QDJ-I Model Rail Breakage Monitoring Systemfor Semi-automatic Block Section
香港地铁南港岛项目轨道断裂检测系统概述
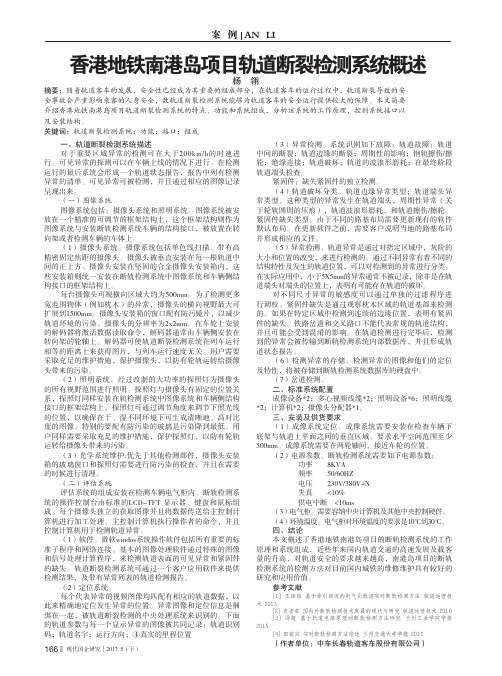
现代国企研究 2017. 5(下)166案 例 AN LI一、轨道断裂检测系统描述对于重要区域异常的检测可在大于200km/h的时速进行。
可见异常的探测可以在车辆上线的情况下进行。
在检测运行的最后系统会形成一个轨道状态报告,报告中列有检测异常的清单。
可见异常可被检测,并且通过相应的图像记录呈现出来。
(一)图像系统图像系统包括:摄像头系统和照明系统。
图像系统被安放在一个精准的可调节的框架结构上,这个框架结构则作为图像系统与安装断轨检测系统车辆的结构接口,被放置在转向架或者检测车辆的车体上。
(1)摄像头系统。
摄像系统包括单色线扫描、带有高精密固定焦距的摄像头。
摄像头被垂直安装在每一根轨道中间的正上方。
摄像头安装在坚固的合金摄像头安装箱内,这些安装箱则统一安装在断轨检测系统中图像系统和车辆侧结构接口的框架结构上。
每台摄像头可视横向区域大约为500mm。
为了检测更多宽范围物体(例如枕木)的异常,摄像头的横向视野最大可扩展到1500mm。
摄像头安装箱的窗口配有防污镜片,以减少轨道环境的污染。
摄像头的分辨率为2x2mm。
在车轮上安装的解码器将激活数据读取命令,解码器通常由车辆侧安装在转向架的轮轴上。
解码器可使轨道断裂检测系统在列车运行相等的距离上来获得图片,与列车运行速度无关。
用户需要采取充足的维护措施,保护摄像头,以防有轮轨运转给摄像头带来的污染。
(2)照明系统。
经过改制的大功率的探照灯为摄像头的所有视野范围进行照明。
探照灯与摄像头有固定的位置关系,探照灯同样安装在轨检测系统中图像系统和车辆侧结构接口的框架结构上。
探照灯可通过调节角度来调节下照光线的位置,以确保在干、湿不同环境下可生成清晰地、高对比度的图像。
特别的要配有防污染的玻璃是污染降到最低。
用户同样需要采取充足的维护措施,保护探照灯,以防有轮轨运转给摄像头带来的污染。
(3)光学系统维护.优先于其他检测部件,摄像头安装箱的玻璃窗口和探照灯需要进行防污染的检查,并且在需要的时候进行清理。
自动化监测技术在青岛地铁13号线施工中的应用

自动化监测技术在青岛地铁13号线施工中的应用Chapter 1: Introduction随着城市化进程的加快,城市交通问题越来越突出。
青岛作为中国的重要沿海城市之一,经济、文化和人口都在不断增加。
为了缓解交通瓶颈,不断完善公共交通系统已成为城市交通建设的重要任务。
青岛市地铁建设逐步向前推进,13号线作为青岛市的重要轨道交通项目之一,在建设过程中,自动化监测技术得到了广泛的应用。
Chapter 2: Application of automation monitoring technology in the construction of Qingdao Metro Line 132.1 Characteristics of Automation Monitoring Technology自动化监测技术是指应用计算机技术、通信技术、仪表技术、传感器技术、图形处理技术、数据库技术等新技术实现监测设备、监测数据的实时采集、实时处理、实时传输、实时显示和自动诊断分析的技术。
监测技术主要用于工程结构物变形、振动、流量、温度、湿度、应变等参数的监测和分析。
2.2 Application of Automation Monitoring Technology in Qingdao Metro Line 13Qingdao Metro Line 13 is a key transportation project in Qingdao. The construction of the project has encountered many technical challenges, such as the complex geological and hydrological conditions, the deep excavation of tunnels, and the highrequirements for construction quality. Therefore, automation monitoring technology is widely used in the construction of Qingdao Metro Line 13.The application of automatic monitoring technology in Qingdao Metro Line 13 can be divided into two parts. Firstly, the monitoring of environmental and geological conditions, and secondly, the monitoring of the construction process.2.2.1 Monitoring of Environmental and Geological ConditionsThe construction of Qingdao Metro Line 13 is affected by many geological and hydrological conditions. For example, the construction area is located in a coastal area with high groundwater levels. Therefore, it is necessary to monitor the groundwater level, pore water pressure, and soil pressure of the construction site in real time to ensure the stability of the construction site. Automatic monitoring systems are used to collect and transmit data to the construction management center in real time. Through the data analysis, the construction team can adjust the construction plan in a timely manner to avoid geological disasters.2.2.2 Monitoring of the Construction ProcessThe construction of Qingdao Metro Line 13 involves various construction technologies, such as tunnel excavation, underground excavation, and construction of stations. In the process of construction, automation monitoring technology can be used to monitor the stability of the excavation face, the deformation of the support structure, the settlement of the ground, and the quality ofthe construction in real time. The monitoring data is transmitted in real time to the construction management center. Through the data analysis, it can provide early warning and take timely measures in case of potential safety hazards.Chapter 3: Advantages of Automation Monitoring Technology in the Construction of Qingdao Metro Line 133.1 Improving the Accuracy of MonitoringThe use of automation monitoring technology can effectively improve the accuracy of monitoring data. In the construction of the subway, it is necessary to monitor various parameters such as deformation, displacement, and strain. The traditional manual monitoring method cannot fully meet the needs of the construction, and the monitoring data is often inaccurate. Automation monitoring technology can improve the accuracy of monitoring by using high-precision sensors and automatic data acquisition systems.3.2 Real-time Monitoring and Early WarningAutomatic monitoring technology can realize real-time acquisition, processing, and transmission of monitoring data, providing timely and accurate information for construction management. By analyzing the data, the construction management center can predict and early warning potential problems and take effective measures to prevent accidents.3.3 Improve the Efficiency of ConstructionBy using automation monitoring technology, it can effectively reduce the number of manual monitoring personnel and the monitoring cycle. The automatic monitoring system can work 24 hours a day and can monitor multiple parameters at the same time. Moreover, the system can analyze data more quickly and accurately than manual monitoring, thus greatly improving the efficiency of construction.Chapter 4: Challenges and Solutions of Automation Monitoring Technology in the Construction of Qingdao Metro Line 134.1 ChallengesThe application of automation monitoring technology in the construction of Qingdao Metro Line 13 has encountered some challenges. For example, the construction site is located in a complex geological environment with high groundwater levels, which causes difficulties in the installation and operation of monitoring equipment. The long construction period also poses a challenge to the maintenance and operation of the monitoring system.4.2 CountermeasuresIn order to overcome these challenges, it is necessary to take corresponding countermeasures. For example, the monitoring equipment should be designed to be waterproof and moisture-proof to ensure its normal operation in a high groundwater level environment. In addition, it is necessary to strengthen themaintenance and management of the monitoring system and make reasonable arrangements for equipment replacement and maintenance.Chapter 5: ConclusionThe construction of Qingdao Metro Line 13 has been a great success, and automation monitoring technology has played an important role in ensuring the safety and quality of the construction project. Through the application of automation monitoring technology, it not only greatly improves the accuracy and efficiency of monitoring but also provides real-time monitoring and early warning, reducing potential safety hazards in the construction process. The application of automation monitoring technology in the construction of Qingdao Metro Line 13 provides a reference for the application of automation monitoring technology in the construction of future rail transit projects.。
轨道精调流程

轨道精调流程下载温馨提示:该文档是我店铺精心编制而成,希望大家下载以后,能够帮助大家解决实际的问题。
文档下载后可定制随意修改,请根据实际需要进行相应的调整和使用,谢谢!并且,本店铺为大家提供各种各样类型的实用资料,如教育随笔、日记赏析、句子摘抄、古诗大全、经典美文、话题作文、工作总结、词语解析、文案摘录、其他资料等等,如想了解不同资料格式和写法,敬请关注!Download tips: This document is carefully compiled by theeditor. I hope that after you download them,they can help yousolve practical problems. The document can be customized andmodified after downloading,please adjust and use it according toactual needs, thank you!In addition, our shop provides you with various types ofpractical materials,such as educational essays, diaryappreciation,sentence excerpts,ancient poems,classic articles,topic composition,work summary,word parsing,copy excerpts,other materials and so on,want to know different data formats andwriting methods,please pay attention!《轨道精调流程》一、准备工作1. 熟悉设计文件:了解轨道的设计标准、技术要求和施工规范。
青岛地铁2号线列车控制及监控系统教材-2017年5月

列车控制及监控系统第一节列车控制及监控系统概述一、功能概述列车控制及监控系统(Train Control and Management System,简称TCMS)是集列车的控制、监控和诊断为一体的集成控制系统,为列车各系统提供实时控制信号,完成对列车的控制,同时,TCMS 也可实现对列车主要设备的运行状态和故障信息进行采集、记录、显示,为司机对车辆的正确驾驶提供信息参考,为车辆检修提供信息提示和数据提取的途径。
二、青岛地铁2号线列车控制及监控系统架构(一)TCMS设备清单表1-1 TCMS设备清单(二)列车网络拓扑结构青岛地铁2号线列车网络拓扑结构如下图所示,EGWM表示TCMS 主机,DDU表示TCMS显示器,DIMe表示数字量输入模块,DXMe表示数字量输入/输出模块,AXMe表示模拟量输入/输出模块,REPA/B 表示中继器,EDRM表示事件记录仪,RCMe表示485-MVB网关,DCU 表示牵引控制单元,BCU表示制动控制单元,SIV表示辅助逆变器,ATC表示信号车载控制单元,PIS表示乘客信息系统,HVAC表示空调控制器,FDS表示烟火报警装置,EDCU7/8表示门控器。
图1-1 列车网络拓扑结构第二节列车控制及监控系统通信接口协议及功能一、与牵引系统的通信接口协议及功能(一)TCMS向DCU发送如下信息:●EGWM生命信号●TCMS时钟信号●DCU自检命令●列车运行模式●列车牵引力、制动力设定值●限速值●轴速度●制动电阻风机测试命令●DCU隔离命令●蓄电池牵引●电制动切除●运行工况●运行方向●车辆有效轮径●车辆有效载荷(二)DCU向TCMS发送如下信息:●DCU生命信号●DCU故障信息●VVVF状态●空转●自检状态●车辆实际牵引、电制动力●电制动回馈能耗●牵引能耗●制动电阻能耗●主断状态(三)TCMS可以配合牵引系统实现以下功能:●DCU通信状态监视●电制动切除功能●驾驶方向选择功能,确定列车的方向选择●DCU隔离功能●时间同步●DCU自检功能●诊断功能,在DDU上显示的DCU的状态和故障信息●轮径值设置功能,通过DDU设置,由TCMS发给各DCU ●激活高加速模式二、与辅助电源系统的通信接口协议及功能(一)TCMS向SIV发送如下信息:●EGWM生命信号●TCMS时钟信号●SIV自检命令●蓄电池牵引(二)SIV向TCMS发送如下信息:●SIV生命信号●SIV故障信息●自检状态●SIV能耗●逆变器状态●线路输入电压●逆变电路输出电压●充电机电路输出电压●蓄电池充电电流●蓄电池温度(三)TCMS可以配合辅助电源系统实现以下功能:●SIV通信状态监视●时间同步●SIV自检功能●诊断功能,在DDU上显示SIV的状态和故障信息三、与信号系统的通信接口协议及功能(一)TCMS向ATC发送如下信息:●EGWM生命信号●TCMS时钟信号●紧急制动施加状态●所有空气制动已施加●牵引、制动指令反馈●空转滑行检测●左/右侧车门全关闭(二)ATC向TCMS发送如下信息:●ATC生命信号●ATC运行模式●ATC触发紧急制动●站点信息(三)TCMS可以配合信号系统实现以下功能:●ATC通信状态监视●时间同步●执行ATO驾驶模式的自动列车控制●站点信息设置四、与制动系统的通信接口协议及功能●EGWM生命信号●TCMS时钟信号●保持制动缓解●运行工况●BCU自检命令(二)BCU向TCMS发送如下信息:●BCU生命信号●BCU故障信息●网关阀状态●自检状态●保持制动施加反馈●轴速度●电制动切除●各架制动风缸、制动缸、空簧、制动管压力(三)TCMS可以配合制动系统实现以下功能:●BCU通信状态监视●时间同步●紧急制动施加检测●保持制动缓解●空压机管理●BCU自检功能●诊断功能,在DDU上显示BCU的状态和故障信息五、与PIDS的通信接口协议及功能●EGWM生命信号●TCMS时钟信号●PIDS自检命令●左、右门全关闭●各车门紧急解锁状态●各车门隔离状态●ATO模式●TCMS紧急广播命令(二)PIDS向TCMS发送如下信息:●PIS生命信号●PIS故障信息●PIS主机主/从状态●自检状态●客室报警器状态●PIS站点信息(三)TCMS可以配合PIDS实现以下功能:●PIS主机通信状态监视●站点信息设置●紧急广播功能●乘客紧急呼叫状态在DDU上显示●烟火报警视频联动●车门紧急解锁视频联动●时间同步●PIS自检功能●诊断功能,在显示器上显示PIS的状态和故障信息六、与空调系统的通信接口协议及功能(一)TCMS向HVAC发送如下信息:●EGWM生命信号●TCMS时钟信号●空调自检命令●停止紧急通风●空调工作模式设置●手动温度设置●空压机启动●各车实际载荷●减载指令(二)HVAC向TCMS发送如下信息:●HVAC生命信号●HVAC故障信息●空调运行模式●空调控制温度●室内、外界温度●减载成功反馈●通风机工作状态●压缩机工作状态●冷凝风机工作状态(三)TCMS可以配合空调系统实现以下功能:●HV AC通信状态监视●HV AC模式设置●HV AC温度设置●控制空调系统顺序启动●时间同步●HV AC自检功能●诊断功能,在显示器上显示HV AC的状态和故障信息七、与车门系统的通信接口协议及功能(一)TCMS向EDCU发送如下信息:●EGWM生命信号●TCMS时钟信号●EDCU自检命令(二)EDCU向TCMS发送如下信息:●EDCU生命信号●EDCU故障信息●EDCU自检状态●各车门状态(三)TCMS可以配合车门系统实现以下功能:●EDCU通信状态监视●各车门状态显示●时间同步●诊断功能,在DDU上显示EDCU的状态和故障信息八、与烟火报警系统的通信接口协议及功能(一)TCMS向FDS发送如下信息:●EGWM生命信号●TCMS时钟信号●全列静音●全列火警复位●自检命令(二)FDS向TCMS发送如下信息:●FDS生命信号●FDS故障信息●自检状态(三)TCMS可以配合烟火报警系统实现以下功能:●FDS通信状态监视;、●火灾警报功能●火警静音功能●火警复位功能●火警探测器状态●时间同步;●自检功能;●诊断功能,在显示器上显示FDS的状态和故障信息第三节列车控制及监控系统设备一、中央控制单元(EGWM:Ethernet GateWay Module)(一)EGWM概述EGWM位于TC车司机室电气柜内,EGWM用来处理列车各系统和模块的通信数据,从而向列车各系统和模块发出控制指令。
Saia-Burgess空调系统用户手册说明书

- 6 -WEEE Directive 2012/19/EC Waste Electrical and Electronic Equipment directiveAt the end of the product life dispose of the packaging and p roduct in a corresponding recycling centre. Do not dispose of the unit with the usual domestic refuse.Do not burn the product !RECOMMENDATIONS AND RULES►Rules regarding electrostatic discharge should be followed. ►If the device is modified in any way, except by the manu -facturer, all warranties concerning operation and safety are invalidated.►Make sure that the local standards and regulations areobserved at all times. Examples of such regulations are VDE 0800 and VDE 0100 or EN 60204-1 for earth grounding.►Use only accessory equipment which comes from or has been approved by Honeywell.►It is recommended that the device be kept at room temper-ature for at least 24 hours before applying power. This is to allow any condensation resulting from low shipping / storage temperatures to evaporate.►The device must be installed in a manner (e.g., in a lockable cabinet) ensuring that uncertified persons have no access to the terminals.►Do not open the device, as it contains no user-serviceable parts inside!►The device is suitable for mounting in fuse boxes conforming to standard DIN 43880, and having a slot height of max. 45 mm.►The device is suitable for panel rail mounting on 35 mmstandard panel rail (both horizontal and vertical rail mounting possible) – see pictures 0G and 0H.STANDARDS, APPROVALS, ETC.PURPOSE OF CONTROL: OPERATING CONTROL and multifunctional non-safety control intended for HVAC in home (residential, commercial, and light-industrial) environments ■24 V models:UL 60730-1, Standard for Automatic Electric Controls for Household and Similar Use, Part 1: General Requirements ■CE-approved■FCC part 15B-compliant.CONSTRUCTION OF CONTROL: Independently mounted electronic control unit with fixed wiring. Panel-mounted on a DIN rail.SHOCK PROTECTION: Class II.POLLUTION DEGREE: 2.RATED IMPULSE VOLTAGE: ■230 V circuits: 2500 V ■ 24 V circuits: 500 V NOTE:K eep AC mains supply/load cables separate from signal wiring!RELAY SPECIFICATIONSCAUTIONRISK OF ELECTRICAL SHOCK OR EQUIPMENT DAMAGES!It is not permitted to combine low voltage and line voltage in the relay block.MU1B-0643GE51 R0418C - 5 -Saia Burgess Controls AGPCD7.LRxx-P5 PG5 ROOM CONTROLLER - MOUNTING INSTRUCTIONS EKeep these instructions together with the device or with the equip-ment documentation!FCette instruction est à conserver avec le contrôleur ou avec la docu-mentation de l’installation !PGuarde estas instruςões junto do regulador ou junto da documentaςão da instalaςão!D Diese Anleitung ist beim Gerät oder in der Anlagendokumentation aufzubewahren!IQueste istruzioni devono essere conservate insieme al lettore o con la documentazione dell´impianto!S Denna instruktion skall förvaras tillsammans med regler eller anlägg-ningsdokumentationen!DKOpbevar denne vejledning sammen med regler eller med anlægsdoku-mentationen!N Denne veiledningen skal oppbev-ares sammen med regler eller anleggs-dokumentasjonen!FITätä ohjetta tulee säilyttää laitteen läheisyydessä tai yhdessä muiden dokumenttien kanssa!ES Conserve estas instrucciones con el recalar con la documentación de la instalación.NL Deze handleiding moet bij de rege-laar, of met de documentatie van de installatie worden bewaard!PLInstrukcję obsługi należy przechowy -wać przy urządzeniu albo w doku -mentacji technicznej.Copyright © 2018 Saia-Burgess Controls AG All Rights ReservedMU1B-0643GE51 R0418CSupportDocumentationMU1B-0643GE51 R0418C - 4 -Saia Burgess Controls AG PCD7.LRxx-P5 PG5 ROOM CONTROLLER - MOUNTING INSTRUCTIONS2. D IN-RAIL MOUNTING PCD7.LRxx-P5 + MOUNTING IRM-RxC3. DISMOUNTING IRM-RxC + DISMOUNTING PCD7.LRxx-P5 from DIN-RAILMU1B-0643GE51 R0418C - 3 -Saia Burgess Controls AG PCD7.LRxx-P5 PG5 ROOM CONTROLLER - MOUNTING INSTRUCTIONS- 2 -Saia Burgess Controls AG PCD7.LRxx-P5 PG5 ROOM CONTROLLER - MOUNTING INSTRUCTIONS MU1B-0643GE51 R0418C。
船用开关柜局部放电异常检测
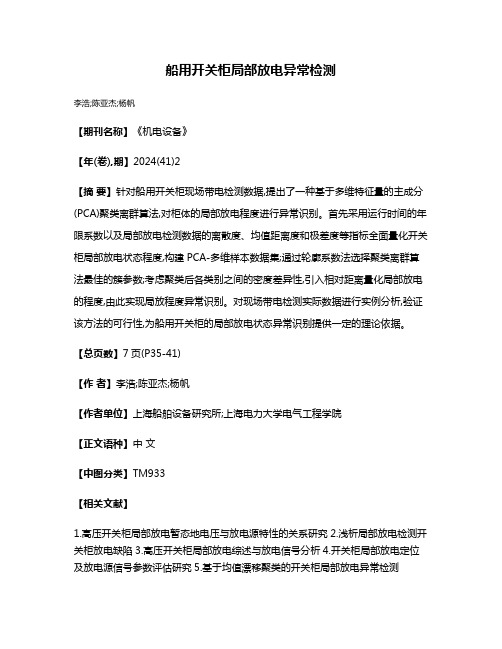
船用开关柜局部放电异常检测
李浩;陈亚杰;杨帆
【期刊名称】《机电设备》
【年(卷),期】2024(41)2
【摘要】针对船用开关柜现场带电检测数据,提出了一种基于多维特征量的主成分(PCA)聚类离群算法,对柜体的局部放电程度进行异常识别。
首先采用运行时间的年限系数以及局部放电检测数据的离散度、均值距离度和极差度等指标全面量化开关柜局部放电状态程度,构建PCA-多维样本数据集;通过轮廓系数法选择聚类离群算法最佳的簇参数;考虑聚类后各类别之间的密度差异性,引入相对距离量化局部放电的程度,由此实现局放程度异常识别。
对现场带电检测实际数据进行实例分析,验证该方法的可行性,为船用开关柜的局部放电状态异常识别提供一定的理论依据。
【总页数】7页(P35-41)
【作者】李浩;陈亚杰;杨帆
【作者单位】上海船舶设备研究所;上海电力大学电气工程学院
【正文语种】中文
【中图分类】TM933
【相关文献】
1.高压开关柜局部放电暂态地电压与放电源特性的关系研究
2.浅析局部放电检测开关柜放电缺陷
3.高压开关柜局部放电综述与放电信号分析
4.开关柜局部放电定位及放电源信号参数评估研究
5.基于均值漂移聚类的开关柜局部放电异常检测
因版权原因,仅展示原文概要,查看原文内容请购买。
- 1、下载文档前请自行甄别文档内容的完整性,平台不提供额外的编辑、内容补充、找答案等附加服务。
- 2、"仅部分预览"的文档,不可在线预览部分如存在完整性等问题,可反馈申请退款(可完整预览的文档不适用该条件!)。
- 3、如文档侵犯您的权益,请联系客服反馈,我们会尽快为您处理(人工客服工作时间:9:00-18:30)。
QDJ-I Model Rail Breakage MonitoringSystemfor Semi-automatic Block SectionNanchang Railway Tianhe Construction Co., Ltd.May 20171. OVERVIEW OF SYSTEMThe QDJ-I model rail breakage monitoring system for semi-automatic block section is no-track-circuit rail breakage monitoring equipment researched, developed and produced independently by the company. Research, development and design of the rail breakage monitoring mainly focus on conducting inspection by ensuring certain current to pass through each rail as a lead wire. In case of physical breakage and electric disconnection of the rail, the loop current is disconnected and alarm messages are sent. Currently, there are multiple rail breakage monitoring schemes, including AC/DC track circuit monitoring, carrier wave monitoring, and ultrasonic wave monitoring. Which rail breakage monitoring scheme costs less but presents high reliability? After going through many times of research and comparison, the research group decided to develop a new energy-saving jointless section track circuit. The purpose of real-time rail breakage monitoring can be achieved by loading carrier signals on rails, and transmitting signals among different field transceivers, with a broken rail differentiation range below 1Km. Besides, this system is also able to monitor and judge the train travel direction and display the whole process of section occupation and clearance. This scheme not only guarantees train travel safety, but also realizes higher efficiency with less personnel, as well as lower cost.2. APPLICATION FIELD AND WORKING PRINCIPLE OF SYSTEM2.1 Application fieldThe section rail breakage monitoring system is used to monitor breakage of rails having no track circuits in real time, and is applicable for both electric and non-electric sections.2.2 Structure and working principle of system2.2.1 System compositionA number of trackside data sending and receiving equipment (“field transceivers” hereinafter) for monitoring overall rail status are installed, using remote cloud as the server and a fixed PC client and a mobile APP as the monitoring points. The information of all the field transceivers is relayed to terminal field transceivers (“managers” hereinafter), which then send the information to the remote server through wireless transceiving devices, so that the users can access the database of the remote server through the fixed client and mobile APP.The manager 1 and field transceivers transmit the data in a relay way to the manager N, the manager N collects the information transmitted from the manager 1 and field transceivers, pack and communicate it to a GPRS module through RS-485, and the GPRS module sends the monitoring data to a control center once every 15 seconds. The control center stores and analyzes the data sent wirelessly from the GPRS module, to provide real-time monitoring data, graphics and alarm messages to the PC client, and send rail breakage alarm messages and rail breakage recovery messages to adesignated phone number. The PC client mainly functions to display database data, analysis and processing results and monitoring curves of the control center, and various user operation and alarm interfaces. In case of rail breakage or monitoring equipment failure, audible and visual alarms are made to warn the person on duty of equipment abnormality and to take prompt measures to prevent accidents.The managers and field transceivers are installed at an interval ≤1KM, and the gauge bars between the rails are all insulated ones. For sections in severe environment, i.e., at low leakage resistance of the track bed, the interval can be adjusted to improve the monitoring precision.The system is mainly composed of the field transceivers, managers, GPRS module, solar power supply, control center, fixed client and mobile client.2.2.2 Working principle of systemThe system finds rail breakage by checking physical and electric disconnection of the rail through carrier current. 13.5KHz FM signals are used, such that the electrical loss of rail transmission is low, and the transmission distance conforms to the requirements.2 managers are set within each section and a field transceiver is set within each kilometer. The manager 1 and field transceivers send information once every 15 seconds in a relay way, the field transceiver 2, field transceiver3 and field transceiver n transmit the information in sequence to the manager through the rail, and the manager checks the electric disconnection status of the rail on the basis of the status of the rail-transmitted/ received signals received from the manager 1, field transceiver 2 and field transceiver n. Then the manager sends the information to the GPRS module through RS485 communication, the GPRS module sends the data to the control center database, and the control center stores and analyzes the data sent from the GPRS module in a wireless way. The client is provided with real-time monitoring data and graphics, and the processed data can be displayed, alarmed, stored, printed, etc. The system client includes the fixed client and mobile client. The fixed client is suitable for the existing computer, through which the cloud server can be logged in. After the server database is logged in by using the fixed client, the processed data can be displayed, alarmed, stored, printed, etc. The mobile client is a mobile APP, through which the cloud server can be logged in to call database data. Both the fixed and mobile clients can be used to monitor the data information of the field transceivers and managers, rail occupancy and clearance status in a section, rail breakage status and system equipment failure information in real time.3. EQUIPMENT CONFIGURATION OF SYSTEM3.1 Control centerThe control center is the place where the rail breakage monitoring data is collected. It includes hardware (like hosts and memories) and backup software, and provides centralized data storage, backup and management services for digitalization. In consideration of the need to manage information of several sections by the railbreakage server, a cloud server with 2-core CPU, 4GB memory, 2M bandwidth and 40GB system disk capacity is used. It also provides network security and management services, including an on-line anti-virus system, invasion detection system, log recording system, network performance monitoring system, etc.3.2 Client configurationFixed client: a Pentuin series computer (or the existing computer);Mobile client: a mobile phone of Android 4.4 version. It is applicable for a phone of Android 4.4 version or above.3.3 Configuration of sampling and monitoring system for section equipment Field transceiver Several (≤1Km/set);Manager 2 sets;Battery Several;Solar panel and charger Several;GPRS module 2 sets.3.4 Field transceiverThe field transceiver mainly functions to monitor the rail status by transmitting carrier signals through the rail, monitor the battery level of itself and failure status of the lightning protection device and of itself, and transmit data of other field transceivers. The field transceiver is composed of a power circuit, CPU, transceiving module 1, transceiving module 2, sleeping/wake-up circuit, etc.Description of the structure block diagram of the field transceiver: the battery provides power for the entire equipment; the CPU having large program memory, large internal RAM, watchdog, power failure detection function and strong interference resistance function is used; the high-precision crystal oscillator is used to provide clock for the CPU to realize accurate time synchronization and sleeping/wakeup; the LED lamp is used to indicate the working status; the CPU communicates with the carrier module through the serial interface; the lightning protection module provides lightning protection to the equipment. See the following diagram for the internal structure of the field transceiver.Structure block diagram of field transceiverThe output line of the field transceiver is connected to the rail through two plug-type power connecting lines. The circuit board and appearance of the field transceiver areas shown below.Circuit board of field transceiverAppearance of field transceiver3.5 ManagerThe manager mainly functions to monitor the rail status by receiving carrier signals transmitted through the rail, pack the collected data transmitted by the field transceivers through the rail, and communicate the data to the GPRS module through RS-485. The manager also monitors the battery level of itself and failure status of the lightning protection device and of itself. Description of the structure block diagram of the manager: the battery provides power for the entire equipment; the CPU having large program memory, large internal RAM, watchdog, power failure detection Solar panel Power processing andbattery status detection module High-precision crystal oscillator LED status indicating lamp Lightningprotection moduleCarrier input/output and protection module Carrier communicationand signal detection module 1 Carrier communicationand signal detectionmodule 2 RS232communicationinterfacefunction and strong interference resistance function is used; the high-precision crystal oscillator is used to provide clock for the CPU to realize accurate time synchronization and sleeping/wakeup; the LED lamp is used to indicate the working status; the CPU communicates with the carrier module through the serial interface; the lightning protection module provides lightning protection to the equipment. The manager has equipment monitoring functions. It can monitor failure of the manager, lightning protection module and battery, make alarms in case of such failure, monitor communication interruption of the GPRS module and make alarms in case of such interruption.The manager receives data from the field transceiver, packs it, and sends it to the GPRS module through the RS-485 interface, and the GPRS module periodically sends the data from the manager to the remote cloud server. See the following diagram for the internal structure of the manager.Structure block diagram of managerThe output line of the manager is connected to the rail through two plug-type power connecting lines. The circuit board and appearance of the manager are as shown below.High-precision crystal oscillatorLightning protection moduleCarrier input/output and protection module Carrier communicationand signal detection module 1 Carrier communicationand signal detectionmodule 2 RS232 communication interface 2 RS485communication interface 1 Wireless GPRS moduleLED statusindicating lampDC-DCVoltage stabilizer Detection module for charging status of standby battery Standbybattery Solar panelCircuit board of manager Appearance of manager4. FUNCTIONAL PARAMETERS AND CHARACTERISTICS OF SYSTEM 4.1 Technical indicators of system(1) Able to monitor rail breakage in non-electric/electric semi-automatic block sections.(2) Missing report rate for rail breakage: 0; alarm accuracy for rail breakage: 99.8%.(3) Distance of reference monitoring unit: ≤1Km.(4) Setting of remote parameters, including alarm interval, track bed parameters, battery level alarm threshold, etc.(5) Remote program upgrade, and remote setting of GPRS target address in alarm host.(6) The control center supports B/S mode, and is developed based on GIS map, having three map modes available: railway-specific map, 3D geographic map and planimetric map. The rail breakage alarm message is uploaded in real time, the map visually shows the section where the broken rail is located and the corresponding kimometers, and makes audible and visual alarms.(7) The client interface also has alarm display function. In the normal condition, the rail section box and equipment box in the client interface are in green; in case of rail breakage, the rail section box is in red, making audible and visual alarms; in case of monitoring equipment failure, the equipment box is in yellow or red, making audible and visual alarms; when a train occupies the section, the rail section box is in blue, and recovers when being cleared.(8) The client interface has data query function. The real-time curve, historical curve, historical data, train passing curve and alarm record can be inquired.(9) The alarm messages can be sent to the phone via SMS.(10) The server stores equipment information and alarm records for 6 months, the system updates the displayed data in real time and displays latest records of ≥100,000.(11) The manager is connected to the GPRS module through the serial interface byRS-485 serial communication with a baud rate of 2,400bps.(11) System data sampling time: 15s; relay transmission.Broken rail identification time: ≤1min; broken rail alarm time: ≤3min (delayed if the rails are occupied). For rail breakage recovery, alarm recovery identification time: ≤1min; alarm elimination time: ≤3min.(13) Equipment self-diagnosis alarm function, including alarms for low voltage (alarms are made if the voltage is down to 5.3V and eliminated if it rises to 5.5V) and failure of the lightning protection module, and alarms for failure of the managers and field transceivers (power failure and line disconnection); alarm time: ≤2min (delayed if the rail is occupied). Alarm recovery time for self-diagnosis: ≤2min.(14) Client working environment: -5℃~+40℃.(15) Service life: field transceivers, managers, solar panel and battery: >5 years.4.2 Technical indicators of manager(1) Static operating current: ≤50mA.(2) Dynamic operating current: ≤400mA.(3) Information receiving distance from field transceiver: ≥0.8Km for track bed resistance of 1.0Ω/Km, and ≥1Km for track bed resistance of 2.0Ω/Km.(4) Carrier center frequency: 13.5KHz±0.5KHz; frequency deviation: 4.0KHz.(5) Instantaneous sending power: ≥0.6W (peak-to-peak value: +2.0V, -2.0V).(6) Maximum number of field transceivers: ≥32.(7) Sampling cycle: ≤15S.(8) Working power: battery: DC5.5V~12V; power supply period without solar power: >7 days.(9) Insulation resistance: ≥25MΩ.(10) Withstand voltage: >1.2KV (AC, 60 seconds, 1mA).(11) Working environment: -40~85℃.(12) Ingress protection rating of equipment casing: IP65.4.3 Field transceiver of field transceiver(1) Static operating current: ≤50mA.(2) Dynamic operating current: ≤400mA.(3) Information receiving distance from field transceiver: ≥0.8Km for track bed resistance of 1.0Ω/Km, and ≥1Km for track bed resistance of 2.0Ω/Km.(4) Carrier center frequency: 13.5KHz±0.5KHz; frequency deviation: 4.0KHz.(5) Instantaneous sending power: ≥0.6W (peak-to-peak value: +2.0V, -2.0V).(6) Sampling cycle: ≤15S.(7) Working power: battery: DC5.5V~12V; power supply period without solar power: >7 days.(8) Insulation resistance ≥25MΩ.(9) Withstand voltage: >1.2KV (AC, 60 seconds, 1mA).(10) Working environment: -40~85℃.(11) Ingress protection rating of equipment casing: IP65.4.4. Technical characteristics(1) Effectiveness①This system monitors rail breakage through transceiving communication with a center frequency of 13.5K.②T he rails are considered as lead wires and the left and right rails are used as loops for information transmission.(2) Reliability①A larm missing and false alarms are prevented by judging between sudden change and gradual change of signal intensity.②T he SPD lightning protection network impairs interference of lightning and HV arc of overhead electric lines to system monitoring and transmission, helping improve the data reliability.(3) SecurityThe system has a framework relatively independent from the measured system. Failure of the latter does not affect normal operation of the former and vice versa. (4) ExpandabilityThe advanced and stable carrier transmission technology will be expanded to more fields to play more roles through further improvement and development.5. SYSTEM ADVANTAGES(1) The system monitors rail breakage through transceiving communication by using FM signals with a center frequency of 13.5K. The electrical loss of rail transmission is low, and the transmission distance conforms to the requirements.(2) Partial functions of jointless section track circuits are realized to monitor the train travel direction, and section occupation and clearance. The rail section box in the client interface is shown in blue, such that the train travel kilometers within the section can be completely mastered, and the train operation conditions can be known.When a train passes through the section, it is not judged whether rail breakage occurs. After the rain has passed, if the section cannot receive information sent from the rail, it is regarded as rail breakage in this section. In this way, the rail breakage alarm precision can be improved, and false alarms can be reduced.(3) The mobile APP is developed to provide a convenient query method for field operators and managers.6. INNOVATION POINTS OF SYSTEM(1) When a train occupies the section, the train wheel pairs are short-circuited from the two rails. Information cannot be received if rail breakage is checked by using the two rails as the transmission medium. This situation is regarded as rail breakage. To reduce false alarms, the sending current of the field transceivers and managers are smartly utilized to differentiate among three statuses of the sending current: short circuit, open circuit and normal status.(2) Partial functions of jointless section track circuits are used to judge between section occupation and clearance. The rail length in the section having no track circuit is divided into equal parts of ≤1.0Km. The field transceivers are installed at this interval. The train occupation/clearance in the rail section box in the client interface is shown in blue to show the train operation conditions. When a train passes through the section, it is not judged whether rail breakage occurs. After the rain has passed, if the section cannot receive information, it is regarded as rail breakage in this section. In this way, the rail breakage alarm precision can be improved, and false alarms can be reduced.7. MEANING OF SYSTEMThe rail breakage monitoring system monitors rail breakage in real time in an all-weather way. It makes audible and visual alarms promptly in case of rail breakage to warn the operators to take prompt measures, so as to prevent train derail and over-turning accidents because of the broken rail.The rail breakage monitoring equipment allows to accurately acquire data about occupation or clearance of the section from the clients. The monitoring data can be called at any time from the database, which provides great convenience for security management and real-time site monitoring of the rail status, and eliminates a blind spot in site security management.8. PROSPECT OF SYSTEMThe QDJ-I model rail breakage monitoring system for semi-automatic block section can be widely used to monitor breakage of rails having no track circuits in real time. It makes alarms promptly in case of rail breakage to warn the operators to take prompt measures, so as to prevent train derail and over-turning accidents because of the broken rail. It brings remarkable social benefits:(1) The rail breakage monitoring system for semi-automatic block section can be built with the least amount of resources to guarantee train travel safety.(2) The broken position of a rail can be quickly found by using this system.(3) The train travel kilometers within the section can be completely mastered by using this system.(4) The rail breakage judgment accuracy is improved and false alarms are minimized in the easiest way.Test Report of Shanghai Institute of Quality Inspection and Technical ResearchTest Report of ICAS Testing Technology Service (shanghai) Co., Ltd.。