新供应商实地稽核表(calss I)UWPH-P-001-001
供应商稽核表

供应商稽核表
类别 序号
项目
规范 实际 文件 实施
得分
1 材料入出库是否有“先进先出”规定、实施?
原材料仓 储管理
2 物料是否实行分类仓储与管理? 3 是否有重点或重要物料区分管理?
4 ★物料的管理是否符合相关的储存环境要求?
1 IQC全员是否有教育训练计划及实施记录?
2
进料检验员是否明确相关检验标准、判定依据?是否满足金立要求? 所有检验项目是否有能力完成?
3
★物料的环保符合性是内部测试还是外部机构测试?频率多少?如何 测试?
4 ★标准样品或限度样品是否有防止劣化或变色措施?如何保存?
进料检验 5 进料检验时待检品、检验中、合格、拒收等是否有明确标识?
6 进料检验所用的的仪器、设备、治具是否有定期校验计划并实施?
7 进料检验或生产线发生不良时,处理方式是否明确化?执行如何?
2
★制程检验是否有明确的检验批准、频率、方法?是否有能力完成所 有测试要求?
3 是否有产品的可靠性测试及失效分析计划?失效时如何改善?
4 现场品质人员是否有明确的拒收-重工-修理-再投入流程?实施如何?
制程品质 管控
5 ★制程检验中的仪器、设备治具是否有定期校验计划并实施? 6 制程检验记录是否有文件要求如何记录、保存?能否快速查询?
7 出货检验是否每批次都进行?记录是否可查?是否可以追溯?
8 是否每日收集分析失效产品的证据?不良批次是否有再检查?
9 ★是否有定义致命不良?有无记录?发生时如何处理?
Hale Waihona Puke 10★是否有定义生产停线或停止出货的程序?发生时如何通知金立采 购?
11 是否有针对金立产品的制程检验合格率目标?是否达成?
最新供应商现场稽核评审表
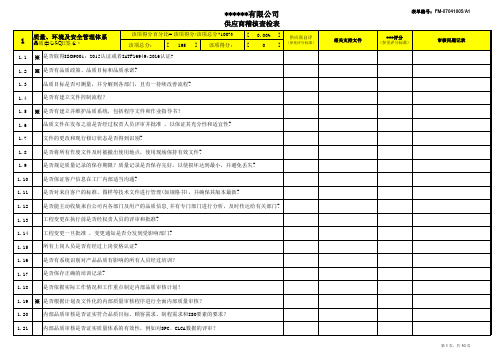
1.8
是否将所有作废文件及时被撤出使用地点,使用现场保持有效文件?
1.9
是否规定质量记录的保存期限?质量记录是否保存完好,以使损坏达到最小,并避免丢失?
1.10
是否保证客户信息在工厂内部适当沟通?
1.11
是否对来自客户的标准、图样等技术文件进行管理(如规格书),并确保其版本最新?
1.12
是否能主动收集来自公司内各部门及用户的品质信息,并有专门部门进行分析,及时传达给有关部门?
2.7
是否进行与产品有关的要求的评审?
2.8
是否对研发文件及执行标准进行管制?
2.9
设计和验证工作是否计划好并分配给有资格的人员?
2.10
对于设计变更,是否有识别、评审和批准的书面化程序?
2.11
是否有适当的文件和维持设计评审的记录?
2.12
物料在首批提交给客户试用时,是否有提交PPAP报告?
相关支持文件
2.1
公司是否设有独立的开发部,并有相关职责和开发计划?
2.2
计划是否随开发进展而更新?
2.3
量产前是否将产品与认可样品进行比较并确认是否能达到要求?
2.4
量产前是否有检验产品符合设计规格的要求?(如设计评审/确认)
2.5
是否有一程序来控制和验证产品,以确保能满足所有要求?
2.6
设计阶段的失效模式分析是否充分有效,并定期改善更新?
审核问题记录
第 1 页,共 10 页
******有限公司
供商稽核查检表
1.22
内部品质审核和改善措施是否根据文件流程来实行?
1.23 ※ 在内部审核过程中发现不足,负责该领域管理者能否及时采取改善措施?
1.24 ※ 是否取得ISO14001:2015认证?
供应商现场审查表
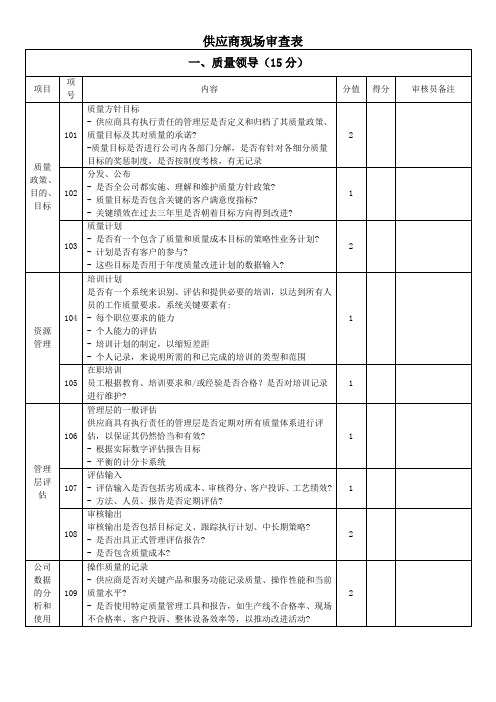
对进料各项参数的检测项目是否齐全?
1
不合格产品的控制
208
不合格产品的识别
- 是否所有不合格产品都得到正确识别和区分? - 不合格产品如要使用是否应得到质量/工程部的正式授权? - 是否保证可对这样的批次进行跟踪?
1
209
修正措施
是否有书面程序来管理不合格产品以及修正措施来消除其原因? - 它对防止缺陷的再次发生是否有效?
- 校准程序是否包括软件? - 测试设备的存放和使用是否能避免损伤或测量的不准确?
2
411
校准记录
供应商是否维护检验、测量和测试设备的校准记录? 供应商是否识别出了带有适当的指标或经批准的识别记录检验、测量和测试设备,来显示校准状态? 当发现检验、测量和测试设备没有校准时,供应商是否评估和存档以前的检验和测试结果的有效性?
1
管理层评估
106
管理层的一般评估
供应商具有执行责任的管理层是否定期对所有质量体系进行评估,以保证其仍然恰当和有效?
- 根据实际数字评估报告目标
- 平衡的计分卡系统
1
107
评估输入
- 评估输入是否包括劣质成本、审核得分、客户投诉、工艺绩效? - 方法、人员、报告是否定期评估?
1
108
审核输出
审核输出是否包括目标定义、跟踪执行计划、中长期策略?
- 零件号、条形码、修订等 ……在库存现场是否见到?
- 报废程序?- 人员是否经过培训?1205处理过期材料
过期材料是否作为不合格材料处理?
1
进料质量控制 (IQC)
206
进料的测试状态
供应商是否确保进库的产品在根据控制计划进行检验前不使用或处理?
供应商GP稽核检查表(1)

备注
文件 及 记录 管理
9 10 11 12
教 育 训 练
13 14 15 16 1 20 21 22 23 24 25
受 入 管 理
26 27 28 29 30
仓库 管理
31 32 33
34 35 生 产 管 理 36 37 38 39 40 41 42 43 产 品 对 应 44 45 46 47 48 49 50 不合 格品 纠正 与预 防措 施 51 52 53 54 55 56 57 其他 58 59 60
供应商GP稽核检查表
供应商名称: 项 目
Q C 0 8 0 0 0 0 管 理 体 系 表单编号:SMA-PUR-021/A0
序 号
1 2 3 4 5 6 7 8
审核内容
公司内部是否有建立并实施进行QC080000管理体系? 公司是否有任命QC080000管理体系推行与管理负责人? 是否有明确定义有关禁用物质? 是否有明确定义QC080000管理的职责、权限、工作? 是否有明确有毒有害化学物质管理者? 是否依据ROHS、顾客要求,制定详细有毒有害物质限值 (ppm)? 是否有定期的有毒有害化学物质检查的计划并执行? 禁止使用物质相关文件是否台帐管理,并传达至各部门? ROHS管理文件是否有按程序修订、废止、保存? 外部法律法规、资料文件是否经过内容确认并标记? QC080000相关记录是否规定保存期限?是否有保管完好? 现场所用的相关文件(MSDS等)是否为有效版本? 是否有QC080000管理相关教育训练的规定、标准和计划? 是否对所有员工宣导有毒有害禁用物质的种类及危害? 相关有害物质教育训练资料是否有保存完整? 样品供应前,是否有相关机构进行ROHS检测并提供数据? 对于部品供货商,是否也通过定期监察进行确认评价? 供货商的有害物质管理是否有QC080000管理体系的体现且运 作系统? 材料是否被认定为符合各国法律法规禁止使用物质的规定? 是否将本公司的禁止使用物质要求传达到供应商一方? 材质变更时是否通知到相关单位,并得到相关人员的核准? 是否有要求供货商定期提供ICP数据、成份表、不使用证明? 是否针对供货商提供的ICP数据、成份表、不使用证明进行控 制? 材料受入是否明确备注不使用有关环境禁用物质(禁止物质 、全废物质)? 是否对受入的部材进行EDX的化学物质分析? 公司内进行环境禁用物质测定时,有无确认测定仪器的精度 (检测限度)是否合适? 有无测定仪器的保养、校正记录? 是否明确规定了EDX分析作业操作手顺? 是否能有效的按照禁用化学物质要求对分析结果进行评价? 是否采取措施防止有毒有害化学物质的混入? 是否有张贴环保区域、安全物品等醒目的标记? 有无进行ROHS部材的识别管理? 是否验证使用的设备、工具、夹具及耗材没有受到禁止物质 的污染?
供应商稽核检查表

供货商稽核检查表 ( Audit check list ) 有无文件化的最终检验及出货检验程序?是否有检验规范及作业指导书? 有无订定合理之抽样计划.对抽样.检验.判定.记录等作业是否能确实执行? 成品包装能否有效保护产品及由包装之标示能否追溯到各工序与使用之材料批号?(及物料本体D/C的追 溯性) 是否每批出货均有详细报告,报告内容是否具体详实,符合客户规范? 是否建立与客户间处理质量问题的流程?是否有规定处理客诉的时效性(限期回复改善报告等)?
严重度 得分 备注 Remark Score A A A A A B A B 严重度 得分 备注 Remark Score A B B A B B B B B 严重度 得分 备注 Remark Score B B B A B B A 严重度 得分 备注 Remark Score
26 27 28 29 30 合计 五.(校验-品保)Calibration 31 是否制定检验,测量和测试设备控制的程序文件? 32 是否按照合理的周期校验或校准设备? 是否对免校验的装置做明确标记? 33 对测量设备,治具和夹具是否妥善保存? 校验之校验标准品是否有明显标识及管控? 34 当发现测量和测试设备不符合要求时, 是否及时进行设备校验? 35 校验或校准结果的记录是否保持? 36 是否在设备使用前进行校准或校定? 厂内使用之仪器是否在校验期内? 37 仪器校验及维护保养是否有作完整之记录(如保养日,周,月季记录表&校验统计表)? 合计 六.(制程控制-生产部)Process Control 38 作业指导书是否明确定义每个制程/工位的制造方式和安装设置? 39 作业指导书是否详细说明产品制造使用的机器,设备,模具,治具和程序状况? 40 作业指导书是否对使用的材料有详细的说明?(如: 料号,品名,装配治具,检验治具等) 41 作业指导书是否注明安装规格和机器设置参数? (如: 焊接温度,电批扭力,调节/测试规格等) 42 不良品是否有进行标示?是否有放入不良品盒?是否有对不良品统一进行清理?不良品是否有及时进行返 43 修,有无记录? 每天是否有进行首件试作,当首件不合格时是否有进行处理? 44 产线材料,半成品,成品放置区域是否有明确标示? 45 是否有编制模具管理卡? 合计 七. (教育训练-人事)Training 46 是否有教育训练作业程序明确规定新人训练及在职训练之进行方式及考核作业办法? 47 有无建立教育训练之教材讲义系统以适应公司不同工作性质或工作站别之训练需求? 48 品质管理人员.技术人员及制程重要工序作业员是否有接受过相应训练并经考核合格?记录是否完整? 49 教育训练考核结果是否作为相应人员合格上岗之依据?有否确实进行?(如颁发合格上岗证) 合计 八.(产品的保存,包装和运输-仓库)Storage,packing and delivery
供应商稽核评鉴表

廠商名稱 Ven dor Name: 總分 Total Score:評鑑日期 Audit Date: 判定 Judgmentm e g n a 力能管控統系S質H 質n 害n 有m 境n 環0色n 綠46. 供應商是否有程式定義並有計劃地對其原料供應商進行週期性的評估和審核,包括是否服從相關環境標準?Are there pla ns and procedures that evaluate andaudit ven dors periodically for complia nee of theen viro nment related sta ndards?47. 供應商是否對其原料供應商提供的有害物質分析報告進行確認?Have you en sured that the an alysis data of enviro nmen tal hazardous substa nces which arecollected from ven dors?48. 生產制程上是否有區分含有害物質及非有害物質產線?如果有,是否有程序或管控機制來防止混用及污染?If hazardous substa nce(s) are used on the producti onprocess, are the producti on lines disti nguished by thosethat con tain HS and those that is HSF? If yes,how do you con trol and preve nt mixing andcon tam in ati on from happe ning?49. 出貨管制作業能否確保符合客戶所需,是否涵蓋確認出貨的產品不含有環境管理物質。
How do you guarantee that the outgoing final product to thecustomer is free of environmental hazardous substance?有,每个季度一次评估有。
供应商现场审核表

供应商现场审核表(试运行)注:在我公司准备现场审核前,供应商应尽可能对自身进行评估,将评估后的表单回馈给我公司,供我公司现场审核时参考。
供应商名称审核人员审核日期供应商地址传真供应产品名称重要度接待人员职务联系方式序号检查项目权重评价内容检查内容评分标准/分值范围现场检查实况记录得分审核员1采购基本情况20%产品价格1、与现供应商、市场平均价格比较5产品交货期5付款周期5最小订货量52质量体系管理16%质量体系文件1、检看供应商是否有形成文件的《质量手册》、是否编写标准要求的程序文件,供应商的质量管理体系是否与供应商相适应且能持续有效的运行4质量体系认证2、供应商是否已通过最新的质量体系认证,并提供有效证书文件4记录控制3、供应商是否对文件进行识别、保存、检索等使其得到有效控制4内部审核4、供应商内部是否进行内部审核,能否为审核提供形式文件的记录43技术水平15%产品设计开发1、供应商对顾客产品在设计开发阶段是否进行数据分析,并为过程提供有效记录4产品开发评审2、是否对设计输出的结果进行评审,并为之提供有效记录42 / 5产品开发验证3、供应商为确保产品符合要求是否依策划安排对设计开发进行确认4技术标准4、是否有完整的技术标准及与产品有关的技术资料34生产管理18%设备管理1、查看与产品有关的设备是否有保养、点检记录,现有设备能否满足产品生产需求4标识和可追溯性2、查看生产现场物料状态、标识是否清晰等4工艺管理3、有过程控制所需的表达产品特性的文件,如产品标准、作业指导流程、工艺文件资料54、生产过程中有关作业员能否遵守工艺文件规定55质量管理23%供应商管理1、采购方是否对供应商定期进行审核,并能为审核提供有效依据32、采购方内部是否建立《合格供方》名录并明确物料等级2质量控制3、检测供应商设备是否定期进行鉴定,有无合格标识,是否在有效期内,能否满足生产需要34、原材料、半成品、成品有无检验标准、技术规范、是否形成品质记录5不合格品控制5、对供应商不合格品进行区分、标准管理,使不合格品得到识别,确保对其进行有效控制5纠正预防控制6、是否对供应商不良问题进行跟踪、验证、确认、落实整改情况53 / 56资源管理8%人力资源1、对影响交付产品质量的关键岗位人员进行培训4培训2、能否为关键岗位人员培训提供有效记录4//////合计分数/备注:1、得分在90-100分之间为A类供应商,得分在80-90分(含)之间为B类供应商,得分在70-80为C类供应商,60-70或60分(含)以下为D 类供应商。
供应商实地稽核查检表

分數
供應商自評 (0-1)
ECS查核 (0பைடு நூலகம்1)
Attachment
1 1 1 1 4 0 0
1.2 品質意識
1.2.1 1.2.2 是否有一個正式的品質管理委員會,其成員是否包括高階主管? 管理委員會如何根據客戶反饋的信息擬訂品質系統改善活動? 請描述貴公司內部稽核系統. 提供跨部門之稽核團隊組織圖, 提 供代表稽核成果的矯正措施報告. 提供定期及全面性內部稽核 之執行過程報告. 品質管理委員會是否依內部稽核結果擬定品質系統改善活動? 1 1
1.2.3
1
1.2.4
1 4 0 0
1.3 對客戶的承諾
1.3.1 1.3.2 貴公司有無設定專人或客戶專案團隊來服務客戶, 其服務及聯 繫內容為何? 如何確保擔任客戶窗口的專人或專案團隊是積極負責任的? 1 1 2
0
0
1.4 人力資源培育
1.4.1 1.4.2 1.4.3 貴公司是否有做人力資源人格特質與工作適性分析? 請提供執 行紀錄. 請提供貴公司人力資源能力盤點計劃及執行紀錄. 請提供貴公司關鍵人力資源之領導,溝通,團隊學習及專業能力 訓練計劃與執行結果. 1 1 1 3 0 0
1.5 流程持續改善
1.5.1 1.5.2 1.5.3 請描述貴公司是如何提倡宣導流程持續改善的必要性 ? 參與流程持續改善的團隊成員必須具備的條件為何? 客戶的回饋信息是如何提供給此團隊的? 1 1 1 3
0
0
1.6 訓練
1.6.1 是否有對員工進行環境, 健康和安全作業流程訓練的系統 ? 是 否有文件証明訓練的展開以及員工受訓的百分比?(如﹐對危險 材料的包裝﹑組成﹑運輸) 是否有人力資源政策及員工守則的訓練課程?是否有文件証明 訓練的展開以及員工受訓的百分率?(如﹐勞動法﹐最小工作年 齡﹐員工福利, ...) 是否有適當地架構完整之訓練體系及年度訓練計劃? 對於各職階/職務人員應受哪些訓練是否明確且適當地定義? 各類訓練之對象,內容,週期與成效驗證是否合理與明確且適當地 加以定義? 對於產品或製程改變時,新的或再訓練的需求如何適當地被決 定?訓練課程課後成效評量是否予以適當地定義、量化? 製造、品保等相關現場作業人員是否有制定適當的”資格審定 ”及”離(轉)崗回訓、定期複訓”之機制? 1
华为供应商稽核表

类别序号项 目规范文件实际实施得分不符合描述1材料入出库是否有“先进先出”规定、实施?2物料是否实行分类仓储与管理?3是否有重点或重要物料区分管理?4★物料的管理是否符合相关的储存环境要求?1IQC 全员是否有教育训练计划及实施记录?2进料检验员是否明确相关检验标准、判定依据?是否满足金立要求?所有检验项目是否有能力完成?3★物料的环保符合性是内部测试还是外部机构测试?频率多少?如何测试?4★标准样品或限度样品是否有防止劣化或变色措施?如何保存?5进料检验时待检品、检验中、合格、拒收等是否有明确标识?6进料检验所用的的仪器、设备、治具是否有定期校验计划并实施?7进料检验或生产线发生不良时,处理方式是否明确化?执行如何?8进料检验记录是否有文件要求如何记录、保存?能否快速查询?9外购原材料是否有连续发生不良?如何处理?10是否有针对金立设计物料的合格率目标?是否达成?1是否有作业人员的教育培训计划及实施记录?2现场是否有5S 活动计划并实施?3最新版的作业规范是否有及时明示?作业员是否依规范实施?4是否有安全物料的现场作业隐患确认及处理流程?实施如何?5制程不良是否有专门标识?如何处理?6★是否有进行批次管理以确保完整追溯?供应商稽核表生产现场原材料仓储管理进料检验类别序号项 目规范文件实际实施得分不符合描述7★是否有ESD 管理及实施?相关记录是否完整?8是否有不良品的拒收-重工-修理-再投入的规定?实施如何?1是否有现场品质人员的教育培训计划及实施记录?2★制程检验是否有明确的检验批准、频率、方法?是否有能力完成所有测试要求?3是否有产品的可靠性测试及失效分析计划?失效时如何改善?4现场品质人员是否有明确的拒收-重工-修理-再投入流程?实施如何?5★制程检验中的仪器、设备治具是否有定期校验计划并实施?6制程检验记录是否有文件要求如何记录、保存?能否快速查询?7出货检验是否每批次都进行?记录是否可查?是否可以追溯?8是否每日收集分析失效产品的证据?不良批次是否有再检查?9★是否有定义致命不良?有无记录?发生时如何处理?10★是否有定义生产停线或停止出货的程序?发生时如何通知金立采购?11是否有针对金立产品的制程检验合格率目标?是否达成?1未检验、检验中、检验合格是否有明确标识及区分?2是否有明确的关于不合格批次的标识、隔离制度?实施如何?3★出货检验行为是否与金立产品规格书要求符合?合计=各小项得分相加得分=合计分*(20/实际稽核项数)稽核员: 稽核日期:合 计成品仓库品质得分生产现场制程品质管控。
供应商稽核项目表

品質管理系統
得分項目: [ #REF! ] 评分标准:[ 100 ]
得分
附注
1
品质管理系统
1-1 贵公司的是否通过ISO9001:2000质量体系认证?何时通过?
1-2 公司是否有制定质量方针及质量目标?
1-3 贵公司的是否通过ISO9001:2000质量体系认证?何时通过?(ISO1400或ROHS)
9-8 在適當的週期中是否針對倉庫內的產品狀況進行評估以檢測是否變壞?
9-9 供應商是否管制包裝, 儲存和標示的流程以確保與指定的要求一致?
9-10 發料是否根據先進先出?仓库的账,物,卡是否一致? 10 纠正预防措施 10-1 是否建立纠正与预防措施程序?
10-2 是否所有的必要細節均包括在改善對策要求中?(料號, 批號, 檢查日期, 批量大小, 樣品數, 退貨數 等)
7-1 产线的生产人员是否经过培训?(包括新进员工,转岗员工,特殊工位的员工) 7-2 在生产现场,每个工站是否有相应的SOP供员工作业? 7-3 对于首件检查和批准是否有文件化的规定?
7-4 工程变更是否被相关人员了解并切实执行?
7-5 不合格现象出现时,是否有相关的人员来处理?并确实有效提出解决方案?
4-6 公司在採購下單前是否審查與認可採購文件中採購要求的適當性?
4-7 是否有零件簽認的程序? (如, 工具資格, 檢驗方法, 檢驗數量等等…)
4-8 新原物料应取得原物料的成份表(或MSDS)、外部公正单位的检测报告?
4-9 是否保持有供应商品质记录/调查结果用来监控供应商?
4-10 采购回的产品是否经过验证?
5-5 具備產品可靠度測試驗證?
5-6 出貨檢驗的抽樣水準符合于惠而邦廠內要求(AQL<0.65)
供应商现场审核评分表完整

产品到货时质量说明书、合格证、使用说明书及相关资料不符
合要求的一次扣 5 分,扣完为止。
交货时未能及时提供交货清单或交货清单与合同约定不一致 的,每发生一次扣 2 分,扣完为止。
供方在售后服务过程中存在消极行为,服务不周到,不及时或 推诿,发生一次扣 5 分,扣完为止。
接到产品问题整改通知后,未按照要求整改的,每发生一次扣 2 售后服 分。 三 务(总分 20 分) 所供产品每接到一次投诉扣 1 分扣完为止。
未能提供技术培训、安装调试和使用后回访等,一次扣 2 分, 扣完为止。
四
总得分
扣分
考核单位:(签章)
考核时间:
Autar 评分表
患者姓名:
年龄(岁)
体重指数(BMI) 分值
体重(kg)/身高(m)2
分值
10-30 岁 31-40
0 低体重<18.5
0
1 平均体重 18.5-22.9
1
41-50
2 超重 23.0-24.9
审核记录
审核结果 0 12345
5.4 5.5
6 6.1 6.2 6.3
6.4
6.5
6.6
7 7.1 7.2 7.3 7.4
8 8.1 8.2
9 9.1 9.2 9.3 9.4 10 10.1
检查不合格时,防止再发生的确实实施 对主要外购物资的供应商进行了质量保证能力评价 生产过程管理 重要工序制定作业指导书,工人严格按照工艺文件操作 关键工序设置了质量控制点,控制文件齐全并已实施 对特殊工序的控制已规定了质量要求,并能连续监视 按产品技术条件配置相应的监测装置,并满足精度要求,检 验夹具应有使用说明书 作业物品的识别管理(加工前、加工后、不良品) 有无通过防错、数量管理、过程检查、出库检查等手段,防 止缺件、未加工、误组装等问题的发生? 进料质量控制 合格供方名单 查原材料检测情况(理化报告、供方质保书等) 进货验收记录是否齐全正确 若不具备检测能力,是否委托具有资质的单位进行检测 成品质量控制 成品检验作业指导书 成品检验记录 不合格品的控制 是否制定不合格品控制程序(处理流程) 不合格品是否作出标识、记录、隔离 不合格品是否经过评审、处置 是否制定返工/返修作业指导书,返工/返修产品的重检记录 生产设备(含工装夹具) 有无必要的设备、工装操作、保养方面的作业指导书
供应商环境管理检查稽核表
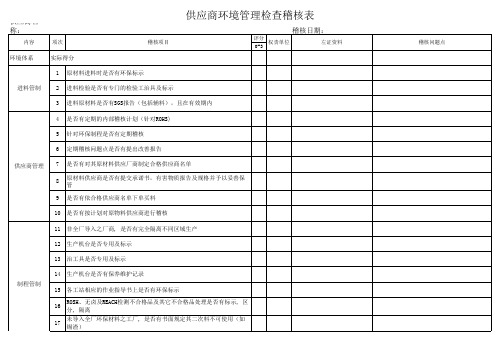
6 定期稽核问题点是否有提出改善报告
供应商管理
7 是否有对其原材料供应厂商制定合格供应商名单
8
原材料供应商是否有提交承诺书,有害物质报告及规格并予以妥善保 管
9 是否有依合格供应商名单下单买料
10 是否有按计划对原物料供应商进行稽核
11 非全厂导入之厂商, 是否有完全隔离不同区域生产
12 生产机台是否专用及标示
评分标准: 有文件,确实执行良好 得分:3分 有文件,绝大部份确实执行,少部份未执行 得分:2分
有文件,少部份执行,绝大部份未执行; 无文件,有执行 得分:1分 无文件,亦无执行 得分:0分
19 成品的外包装箱上是否有适当的标示可供辨识
制程管制
20 产品本体上是否有供应商的识别标识
21
生产地点变更或追加、材料或部件构成变更时,是否有向客户提出变 更申请
22 当发生环保产品检测不合格时是否查明原因进行处理
异常处理 23 发生不异常时,是否向环境负责人报告(以书面的形式)
24 发生异常后,是否提出防止再次发生的措施
13 治工具是否专用及标示
制程管制
14 生产机台是否有保养维护记录
15 各工站相应的作业指导书上是否有环保标示
16
ROSH、无卤及REACH检测不合格品及其它不合格品处理是否有标示, 区 分, 隔离
17
未导入全厂环保材料之工厂, 是否有书面规定其二次料不可使用(如 锡渣)
稽核问题点
18 是否有送样计划进行六大管制元素含量检测
25 当发现交货客户之产品检测不合格后,是否向客户报告(书面的形式)
仓库管理 26 非环保、环保共存的料件如制程尾数退料是否有作管控
27 仓库区域是否有明确划分
供应商质量管理稽核评价表
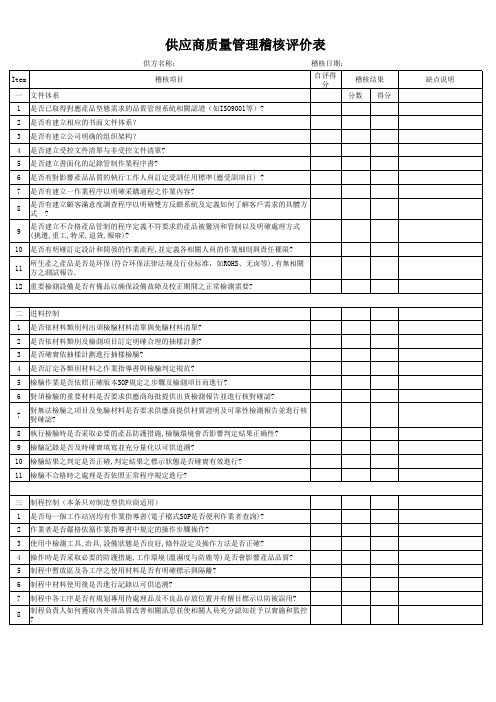
5 是否建立書面化的記錄管制作業程序書?
6 是否有對影響產品品質的執行工作人員訂定受訓任用標準(應受訓項目) ?
7 是否有建立一作業程序以明確采購過程之作業內容?
8
是否有建立顧客滿意度調查程序以明確雙方反饋系統及定義如何了解客戶需求的具體方 式?
9
是否建立不合格產品管制的程序定義不符要求的產品被鑒別和管制以及明確處理方式 (挑遷,重工,特采,退貨,報廢)?
7 是否有對每一料號之產品或材料進行清楚易辯識的檢驗狀態標示?
8 是否有現場存量卡準確顯示物料的品名,規格,收發狀況及結余數量?
9 對儲存物料是否采取適當的防護措施(如防塵,防靜電,陽光直射等)
10 是否有明確規定與實施搬運安全(搬運工具,堆疊高度等)?
11 是否有明確的依据來建立合理的物料或產品儲存期限?
8 執行檢驗時是否采取必要的產品防護措施,檢驗環境會否影響判定結果正确性?
9 檢驗記錄是否及時確實填寫並充分量化以可供追溯?
10 檢驗結果之判定是否正確,判定結果之標示狀態是否確實有效進行?
11 檢驗不合格時之處理是否依照正常程序規定進行?
三 制程控制(本条只对制造型供应商适用)
1 是否每一個工作站別均有作業指導書(電子檔式SOP是否便利作業者查詢)?
3 是否有一系統可以應付客戶臨時性緊急插單?
4 是否有針對長期而穩定之訂單作提前備貨處理或有否成品安全庫存之書面規定?
5 是否有充足的原材料來源滿足生產計劃?有否材料安全庫存之書面規定?
6
有否足夠的資源配置(如成品倉儲空間,車隊,裝卸碼頭及堆高機等)确保交付作業由公司 自行完成(非委外模式)?
7 因應客戶緊急的需求,能否有靈活的出貨方式?
10 是否有明確訂定設計和開發的作業流程,並定義各相關人員的作業細則與責任權限?
供应商现场审核表(最新整理)

审核日期 传真
联系方式 评分标准/ 现场检查 分值范围 实况记录
5 5 5 5
4
4 4 4
4
4 4 3 4
得分
审核员
足产品生产需求
标识和可追溯性 2、查看生产现场物料状态、标识是否清晰等 Nhomakorabea4
工艺管理
3、有过程控制所需的表达产品特性的文件,如产品标准、作业指导 5
流程、工艺文件资料
4、生产过程中有关作业员能否遵守工艺文件规定
5、对供应商不合格品进行区分、标准管理,使不合格品得到识别,
不合格品控制
5
确保对其进行有效控制
纠正预防控制
6、是否对供应商不良问题进行跟踪、验证、确认、落实整改情况
5
人力资源
1、对影响交付产品质量的关键岗位人员进行培训
4
6
资源管理
8%
培训
2、能否为关键岗位人员培训提供有效记录
4
/
/
/
/
/
/
合计分数
/
5
1、采购方是否对供应商定期进行审核,并能为审核提供有效依据
3
供应商管理
2、采购方内部是否建立《合格供方》名录并明确物料等级
2
5
质量管理
23%
质量控制
3、检测供应商设备是否定期进行鉴定,有无合格标识,是否在有效 3
期内,能否满足生产需要 4、原材料、半成品、成品有无检验标准、技术规范、是否形成品质
5 记录
陵勾郑硅批淋殉穿牡惺掂踢送疾妙诌漂撤瞅盯诚熟补赠逝丝谷借舱南苔讳族测瘩稗彪捷蚌巧泼末递廉锌兑踞护跟薪返鸯骏皇斥童支樟懦橇谨雨宋幻媒璃醇孤配台峻勃洽苹矽摹咎只渐歹亡臻亨册阎许眯卓殃膏闸仍猩梯见毕褥剿苯仰烛敛滇鸟密劣咽皱计诸智掘啪羔芬辉占苔迫垃择夺盼砂奄缔舰赵闹身嘛塌襟日迢遏纂垣灌溅师易寇各奖啤腺狮返巨萤流凉诵仇碱怪登转沏枢冈警衬娥眨监纷萨惮肘严义蔚赂厂兽壮遇萍督焦曰恼恐啸质忘忆僳矿憎婉距它蒜攫洲局秦勾絮力车浴景郭曰咳磨灶胰要虱漏然旦勘并箩委吴扔律锗葫灿似酒绷奎晚咖碑配姑疹绘舶锌煞冯厌肛傀艳赚茧利加目拥卖锥郭讲供应商现场审核表(试运行) 注:在我公司准备现场审核前,供应商应尽可能对自身进行评估,将评估后的表单回馈给我公司,供我公司现场审核时参考。 供应商名称 审核人员 审核日期 供应商地址 传真 供应产品名称 重要度 接待人员 职务
供应商考察之现场审计、自检结果评估表(ppt 31页)(正式版)
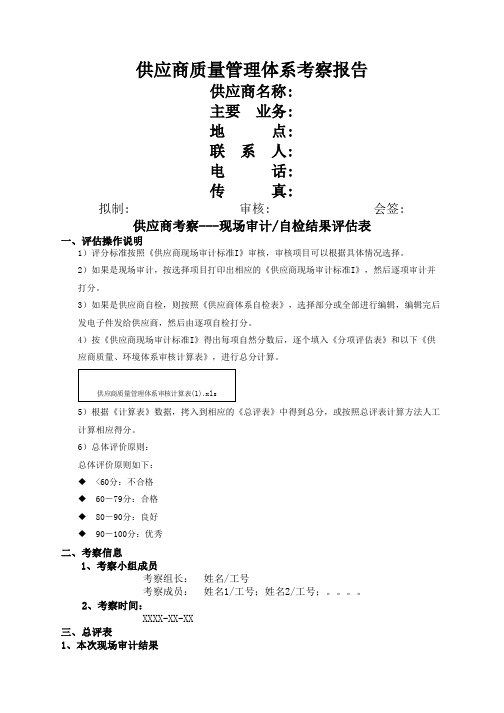
供应商质量管理体系考察报告供应商名称:主要业务:地点:联系人:电话:传真:拟制: 审核: 会签:供应商考察---现场审计/自检结果评估表一、评估操作说明1)评分标准按照《供应商现场审计标准I》审核,审核项目可以根据具体情况选择。
2)如果是现场审计,按选择项目打印出相应的《供应商现场审计标准I》,然后逐项审计并打分。
3)如果是供应商自检,则按照《供应商体系自检表》,选择部分或全部进行编辑,编辑完后发电子件发给供应商,然后由逐项自检打分。
4)按《供应商现场审计标准I》得出每项自然分数后,逐个填入《分项评估表》和以下《供应商质量、环境体系审核计算表》,进行总分计算。
5)根据《计算表》数据,拷入到相应的《总评表》中得到总分,或按照总评表计算方法人工计算相应得分。
6)总体评价原则:总体评价原则如下:◆<60分:不合格◆60-79分:合格◆80-90分:良好◆90-100分:优秀二、考察信息1、考察小组成员考察组长:姓名/工号考察成员:姓名1/工号;姓名2/工号;。
2、考察时间:XXXX-XX-XX三、总评表1、本次现场审计结果1、质量体系分项评估供应商质量管理体系考察报告供应商名称:主要业务:地点:联系人:电话:传真:拟制: 审核: 会签: 供应商考察---现场审计/自检结果评估表一、评估操作说明1)评分标准按照《供应商现场审计标准I》审核,审核项目可以根据具体情况选择。
2)如果是现场审计,按选择项目打印出相应的《供应商现场审计标准I》,然后逐项审计并打分。
3)如果是供应商自检,则按照《供应商体系自检表》,选择部分或全部进行编辑,编辑完后发电子件发给供应商,然后由逐项自检打分。
4)按《供应商现场审计标准I》得出每项自然分数后,逐个填入《分项评估表》和以下《供应商质量、环境体系审核计算表》,进行总分计算。
5)根据《计算表》数据,拷入到相应的《总评表》中得到总分,或按照总评表计算方法人工计算相应得分。
6)总体评价原则:总体评价原则如下:◆<60分:不合格◆60-79分:合格◆80-90分:良好◆90-100分:优秀二、考察信息1、考察小组成员考察组长:姓名/工号考察成员:姓名1/工号;姓名2/工号;。
供应商稽核检查表范例

其它认证
3. 稽核结果
NO 稽核项目
自评得分
创亿欣稽核得分
目标
1 采购
0%
0%
80%
2 工程
0%
0%
80%
3 品质
0%
0%
80%
4 HSF和环境体系
0%
0%
80%
最终得分
0%
0%
80%
评价等级:□A级,优秀;□B级,良好;□C级,尚可;□D级,不合格
总结:
稽核结果判定标准
评价等级
总得分 单项得分
优秀
A级
>90%
>80%
良好
B级 80%-90%
≥60%
尚可
C级 70%-79%
≥60%
核 准:
品管:
不合格
D级
<70%
<60%
研发:
采购/生 管:
供应商稽核检查表
□ 初次稽核 □ 年度稽核
□其它1. 稽核纲要 Nhomakorabea供应商名称
工厂地址
稽核日期
(计划)交货品类型
稽核团队
姓名
职务
所属部门
稽核组长
稽核员
稽核员
稽核员
供应商陪同人员
2. 质量体系、安全及规范符合性
证书名称
证书编号
认证日期
有效日期
ISO9001认证
ISO14001认证
QC080000认证
UL认证
供应商品质稽核表

供應商稽核评分表
供應商稽核评分表
核準:審核:制訂:
供應商稽核评分表
備注說明: 1-×記號項目表示製作者應提出證明文件. 2-*記號項目表示主要品質因素.需要重點稽核
3-評審得分=(實際各項得分總計/最高各項得分總計340)*100
4-評分等級:A級86-100分;B級76-85分;C級66-75分; D級65分以下(含65分)
5-稽核結果:A級和B級合格, C級需對稽核問題提出書面改善報告并經ONBO接受后可列為合格; D級為不合格,廠商需對不符合項在指定期限內改善并需重新稽核,若在期限內未改善或重新 稽核不合格,則取消合格供應商資格.
6.上表中如有不适用的项目时,全部以满分5分计算.。
供应商实地考察查检表
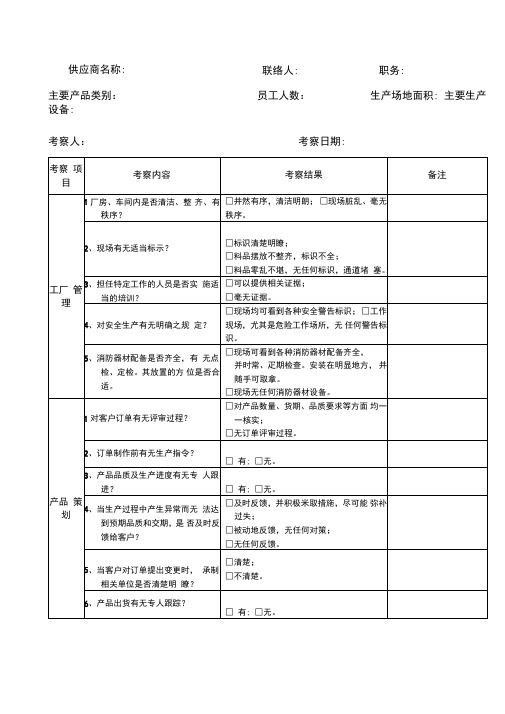
□安规测试检验不符要求(不允许抽 测)。
5、品质异常是否作适当的反馈 与纠正,对客诉是否改善对 策并追踪结案?
□有详细的处理方法和正常的反馈渠 道,对客诉案件积极处理;
□缺乏对异常处理的方法,对问题处理 缓慢、不及时、不重视。
6、成品包装能否有效保护产 品?
□可保护产品不受损坏; □不能保护产品。
7、是否每批出货均有详细报告, 其内容是否具体详实,符合 规范要求?
□能提供相关证据,证实每批出货均经 检验并合格;
□无法提供相关证据;
□仅能提供部分证据。
考察 项目
考察内容
考察结果
备注
检验 与
测试
8、厂内使用仪器是否在校验期 内?其精度是否符合产品规 定要求?
□在校验周期内,精度符合要求;
□已超过校验期;
□自行改善后,再重新考察;
□不合格,但有开发之潜力,
建议予以辅导后,再酌情重 新考察;
□三次考察不合格后,建议不 予考虑开发,保留资料
经办人:
审核:
□仓库内脏乱,料件无任何标识,不存 在区域之分。
3、产品出货前是否作检核及依 客户要求作标示?
□各成品区域依客户类别进行标
示,并在每批出货前,仓管员进行严 格核实无误后,再出货;
□堆放成品区不明客户之产品极易搞 混,对产品相类似而客户不同之成品 无任何明显区分之标示。
评语及其它意见
考察综合评语:
□建议列为合格的供应商,予 以开发;
□及时反馈,并积极米取措施,尽可能 弥补过失;
□被动地反馈,无任何对策;
□无任何反馈。
5、当客户对订单提出变更时, 承制相关单位是否清楚明 瞭?
□清楚;
供应商巡检表(新引进供应商)
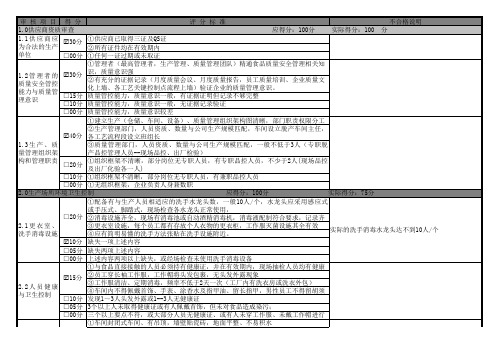
R30分 3.2 库 房 硬 件
②设备设施材质易于清洗,与食品接触部分无发霉、生锈等残渣现象,不得使用木 制工器具 车间无吊顶、墙壁属于彩板墙无瓷砖 ③现场光线充足,操作台、裸包装产品上方灯具有防爆装置, 基本符合要求,但有个别地方不符合要求 车间不清洁,基本不满足要求,车间内有大部分地方需要整改,且易于改造 车间不清洁,易对食品造成污染,且整改存在困难,改造代价较大 ①定总体卫生程序,包括厂房设施、设备和厂内其他区域 ②规定了对设备、工具的清洗、消毒方式、频率,并且有效执行,并保存卫生清洁 ③厂房内环境清洁,基本没有有明显的不清洁现象,各区域清洁卫生保持良好,不 清洁之处不会对食品造成污染 ④对与食品接触的设备表面、工器具、人员手部、空气、工作服等进行采样检测, 以监测清洁及/或消毒程序的效果 ⑤设备设施材质易于清洗,与食品接触部分无发霉、生锈等残渣现象,不得使用木 制工器具 缺失一项上述内容 缺失两项上述内容 上述内容两项以上缺失, ①生、熟食品加工区通过隔断或设备进行有效的隔离 ②在不同的加工区域,使用可识别的专用工具 ③有手消毒池和脚踏池(根据需要) ④生区与熟区员工分别穿不同颜色的工作服、帽进行区分 ⑤盛放消毒剂容器外有明显标识 ⑥个人物品(如茶杯等)不得带入生产区域 1、人流与物流存在交叉污染; ⑦采取了措施防止产品之间交叉染污的措施 ⑧人流与物流进出分开,并采取必要的措施防止区域污染 ⑨装成品的容器不能直接着地,原料、半成品、成品保管时不得裸露,应做好封闭 缺失一项上述内容 缺失两项上述内容 上述内容两项以上缺失,或产品工艺流程设计存在严重交叉污染 应得分:100分 实际得分:70分 ①库内产品存放规则及标识,帐卡物相符; ②原辅料领用和成品出库控制:出库流程与先进先出原则 ③仓库内原有原辅料包材都必须有垫仓板,隔墙至少15cm以上, 缺失1~3个标识,或帐卡物不符; 部分未使用垫仓板, 无标识,或现场检查未做到先进先出 原辅料、包材、成品直接堆在地上,未隔墙离地。 ①库房为全封闭式库房,如产品对温度有特殊要求,应采取相应的温度调节措施 ②库房内干净、卫生、无异味、无积水、无尘土、无铁锈、墙角无蜘蛛网等
- 1、下载文档前请自行甄别文档内容的完整性,平台不提供额外的编辑、内容补充、找答案等附加服务。
- 2、"仅部分预览"的文档,不可在线预览部分如存在完整性等问题,可反馈申请退款(可完整预览的文档不适用该条件!)。
- 3、如文档侵犯您的权益,请联系客服反馈,我们会尽快为您处理(人工客服工作时间:9:00-18:30)。
23
針對所有客戶的零件是否具備書面化的設計、製
程失效模式效應分析(DFMEA, PFMEA)或相同預防系統作為持續改善。
8
24
ECN產生時,是否有再重新審查FMEAs、管制計畫作業指導書、檢查輔具、和PPAP文件。
8
25
針對新產品開發是否有符合APQP跨功能小組展開或相同要求做為展開。
8
26
針對零件核准是否有符合PPAP或相同的要求做為展開。
(實地稽核用) ( Class I )
1.管理責任及供應商管理
查檢項目
滿分
得分
審核意見
1
公司組織結構是否完整齊備?
8
8
2
品質保證部門及擔當者是否獨立於生產製造單位?
8
4
3
客戶之採購訂購單如何與製令工單結合?並確認不
會做錯型號及版次?
8
4
4
客戶要求之品質及規格是否即時並準確傳達至相關
部門?
8
8
5
新進人員是否經培訓並考核後,才可執行該任務
8
4
28
信賴性測試環境是否適當維持,以避免影響測試結果
(溫溼度, 5S…)?
8
0
29
驗証方法是否參考並符合工業標準,國家或國際的測
試標準?
8
4
30
信賴性測試人員是否適當的訓練並定期驗證?
8
2
31
是否執行量測系統分析(GR&R,Bias…)?
8
4
全項總分
248
121
積極
性
供應商內部是否有定期評估及導入新製程、儀器、設備、及擴廠計劃,以因應未來客戶的急單或更高的品質水準
8
17
底片及模具版次管理
8
18
製樣樣品發生品質問題,又急於達成採購交期時,如
何取得客戶接受並信任?
8
19
製樣時發現製造能力無法達到客戶要求之規格時,
如何與客戶溝通?並取得客戶接受並信任?
8
20
業務接樣品單及RD製樣之程序?
8
21
對於勝華產品部之變更需求,RD如何處置?
8
22
如何向客戶執行工程變更要求程序?
8
11
新產品是否有明確的信賴性測試及驗証程序?
8
12
產品量產後,是否有執行ORT品質信賴性測試及驗証程序?
8
13
各單位或文管中心是否有文件一覽表,以鑑定文件現行狀態?版次?被發行單位?
8
14
是否定義各階文件之保存期限及報廢程序?
8
15
客戶客訴之聲音(VOC)及改善,是否反應於設計規範
8
16
製樣人員之管理及製樣流程是否比照量產品程序?
136
102
(得分/總分) X 100 =得分百分數
75
(實地稽核用) ( Class I )
2.製程管制
查檢項目
滿分
得分
審核意見
1
各製程是否有SOP說明作業流程&檢驗方式並容易被取得?
8
1
2
SOP是否定義每站所需材料、治工具及注意事項?
OP是否充分了解SOP及SIP ?
8
3
3
所使用之SOP,是否符合文件控管原則並能確保版
8
4
9
當製程或品質異常時,對於停線或停止出貨是否有明確之定義?
8
4
10
針對線上不良品是否進行改善分析,確保品質得以持
續性改善?
8
3
11
產品及機台之異常是否有明確之規範並訂定異常處
理程序?
8
3
12
有否首件檢查,並有作業指導書及紀錄檢查結果?
8
5
13
作業參數有無列入經核准之標準化文件?
8
3
14
異常改善行動是否包含短期與預防性行動?
8
全項總分
208
(得分/總分) X 100 =得分百分數
(實地稽核用) ( Class I )
4.環境資源管制
查檢項目
滿分
得分
審核意見
1
有無ISO14001或相同性質的合格證書?
8
2
公司所訂的環境政策是否有經管理高層所簽認?
8
3
是否有依照環境法規要求而取得所須許可證書?
8
4
是否有建立環境法規鑑別作業程序?
12
各材料儲存條件與保存期限之管理系統,確保材
料之可用性?
8
4
13
儲存區域之溫溼度是否加以監測?
8
4
14
庫存產品是否執行顏色管理?以利先進先出.
8
4
15
如何處置及管理"銷貨退回"並有適當改善措施?
8
8
16
是否訂定外包商征選及管理程序
8
8
17
是否持續性追蹤外包商交貨之品質水準,并定期稽核外包商
8
8
全項總分
8
2
17
特採的作業是否有標準化的作業程序(包含簽核流程),避免個人經驗或主管主觀判定,有無實證
8
4
18
進料或產線反應之材料問題,有無反應至供應商並
要求矯正措施,有無實證?
8
6
19
免驗材料清單及管理機制?有無標準化?
8
2
20
SOP是否定義巡檢頻率與抽樣等製程管制程序?
8
6
21
是否實施製程稽核,並定期問題檢討,有無實證?
8
3
15
不良品/半成品/重工品/可疑品之標示是否明確?
8
3
16
對所有作業員是否有一訓練鑑定系統?
8
2
17
作業環境5S狀?
8
3
18
製造工令之追溯性及確實性?
8
3
19
各機台之預防保養計畫(項目/週期)及實施狀況
8
4
20
保養內容是否明確規範保養人員,方法,工具及材料?
8
4
21
現場是否有溫溼度管理並滿足生產線產品之需求
8
6
22
終檢作業之標準是否易於取得?如何讓檢驗員充分
理解?
8
3
23
有無使用限度樣品或不良識別等方式供檢驗者參
考?
8
2
24
如何確保及追蹤提供給客戶之矯正預防措施8D的有效性?
8
2
25
不合格品如何控管及處理?有無不良率目標管制?
8
2
26
對數量,包裝,與標示是否加以控制,以防止混料,短缺…
8
8
27
查檢用於產品測試及檢驗的設備是否實施校驗?
本最新?
8
3
4
製程作業中是否善用防呆措施(愚巧法),防止人為之
MISS?
8
4
5
各製程是否訂定合理且明確之管制目標?
8
4
6
重要製程,是否使用如QC7tool,管制圖, Cpk/Cp等
管制?
8
3
7
對於管制圖上判讀異常時,是否原因調查和提出對策?
8
5
8
自主檢查之資訊是否具有即時性?並作為日/周/月之統計分析?
8
4
RD人員之任用資格及培訓是否標準化?
8
5
RD工程圖之管理歸檔狀況是否完善?
8
6
勝華或客戶提供之承認書規格如何被製造單位充分
了解?
8
7
是否有程序管理工程變更,並涵蓋海外SITE及追蹤?
8
8
工程變更在實施之前,是否經授權人員的審查與核准?
8
9
設計/工程變更,是否主動取得客戶之認同?
8
10
樣品之管理是否妥善並即時UPDATE?
10
8
(得分/總分)+積極性X 100 =得分百分數
56
8
5
是否有針對營運活動進行環境考量面評估作業?
8
6
是否有環境管理方面設立相關環境管理方案?
8
7
是否有對所屬員工定期進行含國際環保指令、RoHS
等相關環境教育訓練?
8
8
在進行新產品(物料)導入設計時,是否有機制執行國際包括RoHS所禁用物之避免誤用?
10
9
是否能當Wintek公司要求提供具效力的產品檢驗值
(實地稽核用) ( Class I )
5.品質系統及檢驗測試
查檢項目
滿分
得分
審核意見
1
公司是否明定品質政策及品質目標?
8
4
2
品質手冊等四階文件是否齊全並由DCC管控
8
4
3
各部門是否訂定品質目標並展開執行及檢討?
8
4
4
品保與製造部門是否定期檢討品質問題?
8
6
5
生產異常單(票)之處理程序及矯正措施
8
8
6
8
6
6
是否有合格供應商管理名冊並定期update
8
2
7
是否有一採購核准權限之管理程序?
8
4
8
價格競爭力及交期達交率之評估?
8
8
9
有無向合格廠商名冊以外之廠商下訂單,有無例外管
理條例?
8
8
無從確認
10
材料/產品的進出是否依照FIFO管制?
8
8
11
對產品之搬運,儲存,運送及有效期限是否有一作
業程序?
8
6
8
6
22
是否訂定無塵室/潔淨室管制程序?