预测性维护{维修}又称预知性预见性维护
设备维保的预测性维护与设备管理

案例三
总结词
通过集成传感器和智能化系统,实现对汽车生产线设 备的实时监测和预警,提高生产效率和产品质量。
详细描述
该汽车制造厂在生产线设备上安装了多种传感器,包 括温度、压力、流量等,用于实时监测设备的运行状 态。同时,通过智能化系统的数据分析,可以及时发 现潜在的故障和性能下降趋势。维护团队根据预警信 息进行快速响应,确保设备的稳定运行。这种预见性 维护策略不仅提高了生产效率,还降低了因设备故障 导致的生产损失和产品质量问题。
故障预测准确度挑战
挑战
准确预测设备的故障时间和类型是预测性维 护的核心目标,但实际操作中往往面临预测 精度不高的问题。
解决方案
通过不断优化算法和模型,提高故障预测的 准确度。同时,结合实际运行情况和历史数 据,不断完善和调整预测模型,提高预测精
度。
维修计划优化挑战
挑战
如何根据设备的运行状态和预测的故障风险,制定合理的维修计划和资源配置是另一个 挑战。
案例二:某风电场的发电机组预测性维护方案
总结词
利用传感器和大数据技术,实时监测风电场发电机组的 运行状态,优化维护计划,降低停机时间。
详细描述
该风电场在每个发电机组上安装了传感器,实时收集振 动、温度、电流等数据。通过分析这些数据,可以提前 发现潜在的故障,如轴承磨损、齿轮箱异常等。基于这 些信息,维护团队可以制定针对性的维护计划,确保发 电机组在最佳状态下运行。同时,大数据技术的应用使 得风电场能够更好地预测未来设备的性能和寿命。
温度监测技术
总结词
温度监测技术是通过监测设备运行过程中的温度变化,判断设备是否处于正常工作状态的技术。
详细描述
温度监测技术利用温度传感器采集设备表面的温度数据或者通过间接测量设备内部温度,结合设备正常运行时的 温度范围进行比较,判断设备的运行状态和潜在故障。温度监测技术广泛应用于各种工业设备的监测和预警系统 。
预测性维修概述
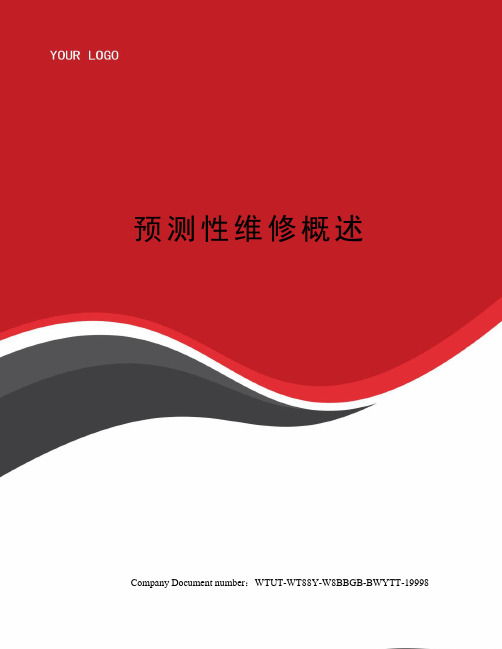
预测性维修概述Company Document number:WTUT-WT88Y-W8BBGB-BWYTT-19998预测性维修(Predictive Maintenance,简称PdM)预测性维修概述预测性维修(Predictive Maintenance,简称PdM)是以状态为依据(Condition Based)的维修,在机器运行时,对它的主要(或)部位进行定期(或连续)的状态监测和故障诊断,判定装备所处的状态,装备状态未来的发展趋势,依据装备的状态发展趋势和可能的故障模式,预先制定预测性维修计划,确定机器应该修理的时间、内容、方式和必需的技术和支持。
预测性维修集装备状态监测、故障诊断、故障(状态)预测、维修决策支持和维修活动于一体,是一种新兴的维修方式。
预测性维修不仅在名字称呼上有不同,在概念的内涵和外延上也有出入,因此又有狭义和广义预测性维修两种概念。
狭义的预测性维修立足于“状态监测”,强调的是“故障诊断”,是指不定期或连续地对设备进行状态监测,根据其结果,查明装备有无状态异常或故障趋势,再适时地安排维修。
狭义的预测性维修不固定维修周期,仅仅通过监测和到的结果来适时地安排维修计划,它强调的是监测、诊断和维修三位一体的过程,这种思想广泛适用于和方式。
广义的预测性维修将状态监测、故障诊断、状态预测和维修决策多位合一体,状态监测和故障诊断是基础,状态预测是重点,维修决策得出最终的维修活动要求。
广义的预测性维修是一个的过程,它将维修管理纳入了预测性维修的范畴,通盘考虑整个维修过程,直至得出与维修活动相关的内容。
(Corrective Maintenance),又称(),是“有故障才维修(Failure Based)”的方式,它是以设备是否完好或是否能用为依据的维修,只在设备部分或全部故障后再恢复其原始状态,也就是用坏后再修理,属于非计划性维修。
()又称定时维修,是以时间为依据(Time Based)的维修,它根据和经验,按规定的时间间隔进行停机检查、解体、更换零部件,以预防损坏、继发性毁坏及生产损失。
设备预防性和预见性维护管理制度
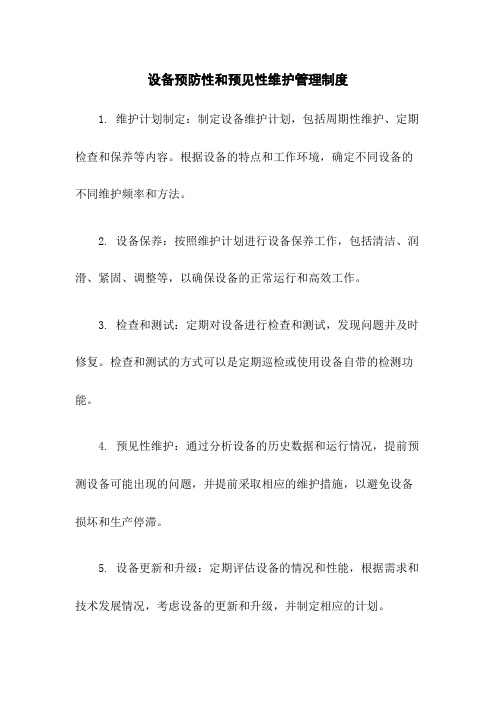
设备预防性和预见性维护管理制度
1. 维护计划制定:制定设备维护计划,包括周期性维护、定期检查和保养等内容。
根据设备的特点和工作环境,确定不同设备的不同维护频率和方法。
2. 设备保养:按照维护计划进行设备保养工作,包括清洁、润滑、紧固、调整等,以确保设备的正常运行和高效工作。
3. 检查和测试:定期对设备进行检查和测试,发现问题并及时修复。
检查和测试的方式可以是定期巡检或使用设备自带的检测功能。
4. 预见性维护:通过分析设备的历史数据和运行情况,提前预测设备可能出现的问题,并提前采取相应的维护措施,以避免设备损坏和生产停滞。
5. 设备更新和升级:定期评估设备的情况和性能,根据需求和技术发展情况,考虑设备的更新和升级,并制定相应的计划。
6. 培训和技术支持:为设备维护人员提供培训和技术支持,使其具备维护设备所需的技能和知识,并及时解答维护过程中遇到的问题。
通过建立和执行这样的预防性和预见性维护管理制度,可以降低设备故障率和维修成本,提高设备的可靠性和工作效率,保证正常的生产运作。
代维资格考试题库

代维资格考试题库1. 什么是代维服务?代维服务是指由专业团队提供的一种服务,包括对设备、设施的维护、保养、修理等,以确保设备的正常运行和延长使用寿命。
2. 代维服务的主要目的是什么?代维服务的主要目的是通过专业的维护和保养,提高设备的可靠性和安全性,降低故障率,减少停机时间,从而提高生产效率和经济效益。
3. 代维服务的主要内容有哪些?代维服务的主要内容包括:定期检查、清洁、润滑、调整、更换磨损件、故障诊断与排除、技术升级改造等。
4. 代维服务的分类有哪些?代维服务可分为预防性维护、预测性维护、紧急维修和全面维护等。
5. 什么是预防性维护?预防性维护是指根据设备的工作特点和使用情况,定期进行的检查、清洁、润滑、调整等工作,以预防设备故障的发生。
6. 什么是预测性维护?预测性维护是指利用先进的监测技术,对设备的工作状态进行实时监测,通过数据分析预测设备可能出现的故障,提前进行维护和修理。
7. 什么是紧急维修?紧急维修是指设备发生故障后,为了尽快恢复生产,采取的快速维修措施。
8. 什么是全面维护?全面维护是指对设备进行全面的检查、维修和升级,以提高设备的综合性能和使用寿命。
9. 代维服务的流程包括哪些步骤?代维服务的流程一般包括:需求分析、服务方案设计、服务实施、质量控制、服务评价和持续改进等。
10. 代维服务的质量控制措施有哪些?代维服务的质量控制措施包括:制定严格的服务标准和操作规程、进行定期的培训和考核、实施现场监督和检查、建立反馈和改进机制等。
11. 代维服务的持续改进方法有哪些?代维服务的持续改进方法包括:收集和分析服务过程中的问题和不足、制定改进计划和措施、实施改进并进行效果评估、建立持续改进的文化和机制等。
12. 代维服务对企业的意义是什么?代维服务对企业的意义主要体现在:提高设备的可靠性和安全性、降低故障率和维修成本、提高生产效率和经济效益、延长设备的使用寿命、提升企业的竞争力等。
13. 代维服务对设备制造商的意义是什么?代维服务对设备制造商的意义主要体现在:提高设备的市场竞争力、增强客户满意度和忠诚度、扩大服务业务和利润来源、收集设备使用数据和反馈、促进产品改进和创新等。
预测性维修及预防性维修

预先维修之路:完美的理论与实现之痛帮助维修人员以计划的和费用有效力的方式完成其任务的维修、监控、诊断和预定的大纲,最基本的困难有很多也是各种各样的。
最佳的选择就在某个地方。
你如何理解字里行间以选择帮助你花最短的时间和最少的努力完成你的工作,并带你到想要到达的地方?“诀窍”似乎是在你的单位如何构成,以及你有什么样的工具以克服在称为实施阶段的困难。
本文提供一些在“沉重打击的锻炼”中遇到的经验教训,以及各个维修单位涉入丰富多彩的商业世界中已经遇到或将要发现的一些预先维修基本原理问题。
维修理论旧理论:损坏、反应、修复的恶性循环许多人将“运转至故障”的情况当为维修。
民间错误地称其为修复性或被动性维修(RM)。
但是这的确完全不是维修。
一家公司或家庭能够以这种没有任何维修部门而是购买重建和新的设备的方式使用其设备、系统和机械。
从一个系统和过程的观点,它是一种类型的维修,但从一个单独部件或机器的观点根本就不是维修。
显而易见的,如今许多公司都有包含管理、工程、监督的维修部门以及专业人员,在其设备、系统或机械丧失功能之后完成其维修任务的75%-85%。
有一些严肃的问题需要提出:经理们是否真的利用其维修部门以获得对其公司资产的最佳管理?维修部门自己(通常包含一些工程师和技术人员、有专业背景的管理人员和适用的工匠)是否建议公司的设备、系统和机械以这种方式使用?我们都知道这两个问题的答案。
然而,我们也知道要想改变使用方式非常困难。
鼓起勇气!许多公司已经改变。
更好的理论:定期的,预防性维修(PM)预防性维修(PM)是从“运转至故障”原理进步来的。
有许多各种各样的PM大纲,但都是基于时间的――它们全部表示在固定时间间隔完成的维修。
在许多情况下,进行彻底改建是由运转时间到出现故障信息的平均值间隔导出的。
预防性理论无法预料在故障平均时间来到之前重建的损坏实际是好的。
然而,由该理论带来的问题有两个方面: 机械的实际情况未加考虑。
自各种设备、系统和机械的平均值变化很大。
如何执行预防性维修维护与预见性维修维护
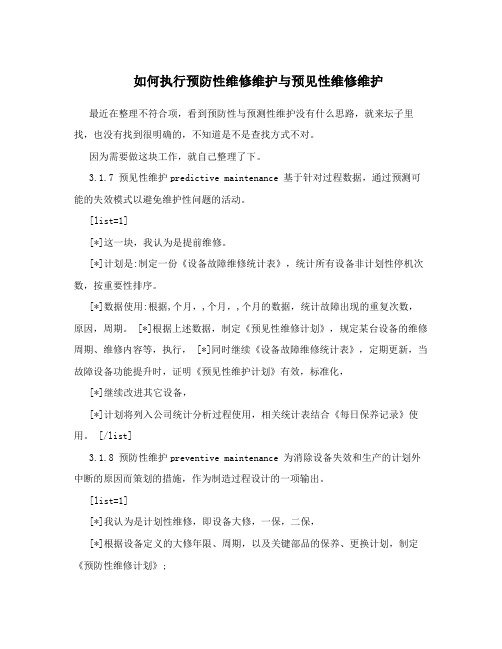
如何执行预防性维修维护与预见性维修维护最近在整理不符合项,看到预防性与预测性维护没有什么思路,就来坛子里找,也没有找到很明确的,不知道是不是查找方式不对。
因为需要做这块工作,就自己整理了下。
3.1.7 预见性维护predictive maintenance 基于针对过程数据,通过预测可能的失效模式以避免维护性问题的活动。
[list=1][*]这一块,我认为是提前维修。
[*]计划是:制定一份《设备故障维修统计表》,统计所有设备非计划性停机次数,按重要性排序。
[*]数据使用:根据,个月,,个月,,个月的数据,统计故障出现的重复次数,原因,周期。
[*]根据上述数据,制定《预见性维修计划》,规定某台设备的维修周期、维修内容等,执行, [*]同时继续《设备故障维修统计表》,定期更新,当故障设备功能提升时,证明《预见性维护计划》有效,标准化,[*]继续改进其它设备,[*]计划将列入公司统计分析过程使用,相关统计表结合《每日保养记录》使用。
[/list]3.1.8 预防性维护preventive maintenance 为消除设备失效和生产的计划外中断的原因而策划的措施,作为制造过程设计的一项输出。
[list=1][*]我认为是计划性维修,即设备大修,一保,二保,[*]根据设备定义的大修年限、周期,以及关键部品的保养、更换计划,制定《预防性维修计划》;[*]定期执行维修保养;[*]为了避免《预防性维修计划》与《预见性维修计划》的冲突,两者中发生冲突的内容及时修订;如《预防性维修计划》里要求,个月换转子,但是《预见性维修计划》要求70天更换,则取消《预防性维修计划》里要求;[*]以年度为基础,更新《预防性维修计划》。
[/list]因系自学,错误时请指正。
预防性维护、预测性维护和周期性检修区别与联系
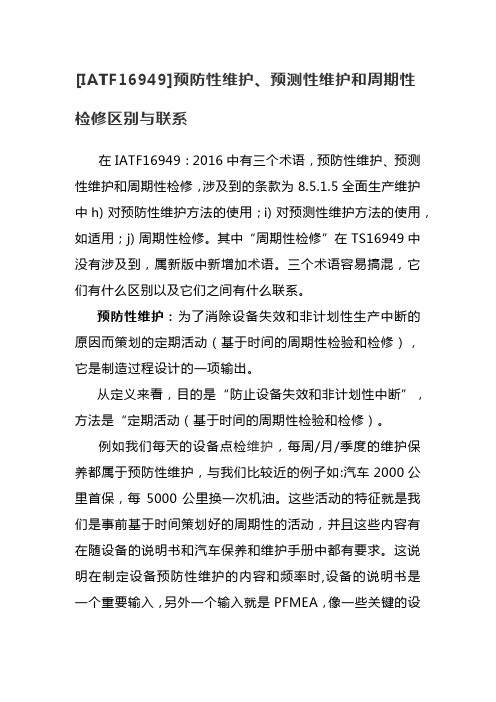
[IATF16949]预防性维护、预测性维护和周期性检修区别与联系在IATF16949:2016中有三个术语,预防性维护、预测性维护和周期性检修,涉及到的条款为8.5.1.5全面生产维护中h) 对预防性维护方法的使用;i) 对预测性维护方法的使用,如适用;j) 周期性检修。
其中“周期性检修”在TS16949中没有涉及到,属新版中新增加术语。
三个术语容易搞混,它们有什么区别以及它们之间有什么联系。
预防性维护:为了消除设备失效和非计划性生产中断的原因而策划的定期活动(基于时间的周期性检验和检修),它是制造过程设计的一项输出。
从定义来看,目的是“防止设备失效和非计划性中断”,方法是“定期活动(基于时间的周期性检验和检修)。
例如我们每天的设备点检维护,每周/月/季度的维护保养都属于预防性维护,与我们比较近的例子如:汽车2000公里首保,每5000公里换一次机油。
这些活动的特征就是我们是事前基于时间策划好的周期性的活动,并且这些内容有在随设备的说明书和汽车保养和维护手册中都有要求。
这说明在制定设备预防性维护的内容和频率时,设备的说明书是一个重要输入,另外一个输入就是PFMEA,像一些关键的设备、工装的一些易损部位,很多时候是要基于PFMEA来进行识别。
预测性维护:通过对设备状况实施周期性或持续监视来评价在役设备状况的一种方法或一套技术,以便预测应当进行维护的具体时间。
从定义来看在没有发生问题的时候,基于对设备状态的一种监控所采取的一些维护性活动,不要等到设备出故障了再去修理,而是在出现这种故障苗头的时候就要去处理它。
怎么去监控设备的状态?一是直接对设备状态进行数据的监控和采集。
如利用红外热像仪,振动分析仪,超声波仪等检测设备,通过检测设备的温度和振动等运行参数,并将测得的参数与设备标准运行状态参数进行比较,从而判断是否需要进行维护,以及如何有针对性的安排维护工作。
二是对于设备的绩效(OEE、MTBF、MTTR等)进行监控。
预防性维护和预见性维护区别

ISO/TS16949:2002标准是这样描述的:
7.5.1.4预防性和预见性维护:
组织应识别关键过程设备,为机器/设备的维护提供资源,并建立有效的、有计划性的全面预防性维护系统,这个系统包括:
---有计划的维护活动
---设备、工装和量具的包装和防护
---可得到关键生产设备的零配件
---将维护目标形成文件并予以评价和改进。
组织应使用预见性维护的方法,以持续改进生产设备的有效性和效率。
我个人理解:
1)预防性维护,好比汽车周期性保养,3000km换机油,到维修站检查,20000km再来一次,对于设备的,每天有日常的保养,可说成一级保养,一般由设备操作人员进行。
每间隔500小时要进行一次二级保养,一般有操作人员和工程部门共同完成,每2000小时大修一次(三级保养),一般由工程部门和设备厂家共同完成。
当然具体的运行时间定多少要看具体情况了。
说简单点,预防性维护就是按计划做一些管理维护,当然不同级别保养内容可能有差异的哦。
2)预见性维护,好比早上起来发动车子发现,转弯有点不顺畅,或者轮胎有点滑,我们感觉好象要出什么事情,马上去维修站,不是计划内的,只是从一些问题发现症状,预计会发生。
说到具体设备比如设备异常噪音、气味、运转异常、不顺畅或SPC控制图一段时期内异常,那么马上应该启动预见性维护程序了。
1。
预防性维护、预测性维护和周期性检修区别与联系
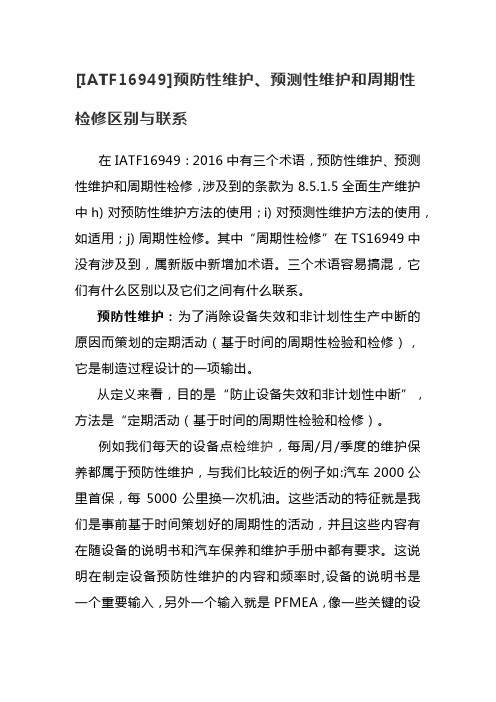
[IATF16949]预防性维护、预测性维护和周期性检修区别与联系在IATF16949:2016中有三个术语,预防性维护、预测性维护和周期性检修,涉及到的条款为8.5.1.5全面生产维护中h) 对预防性维护方法的使用;i) 对预测性维护方法的使用,如适用;j) 周期性检修。
其中“周期性检修”在TS16949中没有涉及到,属新版中新增加术语。
三个术语容易搞混,它们有什么区别以及它们之间有什么联系。
预防性维护:为了消除设备失效和非计划性生产中断的原因而策划的定期活动(基于时间的周期性检验和检修),它是制造过程设计的一项输出。
从定义来看,目的是“防止设备失效和非计划性中断”,方法是“定期活动(基于时间的周期性检验和检修)。
例如我们每天的设备点检维护,每周/月/季度的维护保养都属于预防性维护,与我们比较近的例子如:汽车2000公里首保,每5000公里换一次机油。
这些活动的特征就是我们是事前基于时间策划好的周期性的活动,并且这些内容有在随设备的说明书和汽车保养和维护手册中都有要求。
这说明在制定设备预防性维护的内容和频率时,设备的说明书是一个重要输入,另外一个输入就是PFMEA,像一些关键的设备、工装的一些易损部位,很多时候是要基于PFMEA来进行识别。
预测性维护:通过对设备状况实施周期性或持续监视来评价在役设备状况的一种方法或一套技术,以便预测应当进行维护的具体时间。
从定义来看在没有发生问题的时候,基于对设备状态的一种监控所采取的一些维护性活动,不要等到设备出故障了再去修理,而是在出现这种故障苗头的时候就要去处理它。
怎么去监控设备的状态?一是直接对设备状态进行数据的监控和采集。
如利用红外热像仪,振动分析仪,超声波仪等检测设备,通过检测设备的温度和振动等运行参数,并将测得的参数与设备标准运行状态参数进行比较,从而判断是否需要进行维护,以及如何有针对性的安排维护工作。
二是对于设备的绩效(OEE、MTBF、MTTR等)进行监控。
预见性维护与预防性维护的区别和联系

TS16949:7.5.1.4 预防性和预见性维护组织应识别关键过程设备,为机器/ 设备的维护提供资源,并建立有效的、有计划的全面预防性维护系统。
这个系统至少必须包括:——有计划的维护活动;——设备、工装和量具的包装和防护;——可得到关键生产设备的零配件;——将维护目标形成文件并予以评价和改进;组织应使用预见性维护方法, 以持续改进生产设备的效率和有效性。
预见性维护的定义:3.1.7 基”于过程数据,通过预测可能的失效模式以避免维护性问题(发生)的活动” .预防性维护的定义:3.1.8 为“消除设备故障和生产的计划外中断的原因而策划的措施,作为制造过程设计的一项输出”,由此可见两者的区别。
平时我们做的所谓“三级保养”,是预防性维护,比如日常点检、小修计划与实施、大修计划与实施、等等。
而预见性维护,比如通过人工或监控设施采集数据(温度、黏度、声音、振动、气味、金属含量等),来分析设备的状态,并预测可能失效的模式与时间,提前进行维护,以防止故障发生,实施预见性维护难度比较大,第一是观念问题,第二就是诸如经验数据等缺乏,第三就是分析工具熟悉程度,第四就是分析软硬件不够。
设备FMEA 应用能否当做预见性维护,值得探讨,设备FMEA 的输入考虑了设备以前的失效种类、严重程度、发生频率及可探测度,输出则包含了维护保养的项目、内容、频次、方法等,更重要的输出是易损件的更换计划与备件计划。
即便如此,笔者认为,严格意义上讲,设备FMEA 不算预见性维护,而是预防性维护,理由如下:设备过去虽然可作为设备现在状态的参考,但毕竟无法代替设备现在状态,设备的状态无时无刻在变化,只有实时检测设备相关数据(温度、黏度、声音、振动、气味、金属含量等),经过分析,才能得到设备真正运行状态,也才可能根据分析结果采取相关措施,这才是预见性维护。
设备维护保养可以划分为预防性维护保养和预见性维护保养。
定期检修,更换润滑油,更换零件,大中小修都是预防性保养,预防性保养的周期一般是根据设备说明书中所建议的周期来做.大中小修一般国营厂都是按照苏联的体系来做的,就是八年一大修,三年一中修,一年一小修.另外,就是预见性保养. 预见性保养是预防性保养的延伸, 他要求以最小的成本的维护设备, 有点像精益生产中的JIT, 也就是在设备刚好需要维护时才维护. 可是这怎么做呢? 这就需要有充足的统计数据, 来说明原来的预防性保养的周期是否合理, 比如换油, 可能设备说明书中要求半年一换, 可是随着设备的使用, 这个期限可能会延长,也可能会缩短,你就要根据情况调整维护周期,这就是预见性维护. 可是如何才能知道设备需要维护呢, 有些单位有手段,会对油的成份进行分析来确定设备的磨损情况, 没有这种手段的也可以通过产品质量, 故障频率等来确定预防性维护和预见性维护一般只对设备工装模具,检具自有一套系统, 但我们也可以做预防性维护和预见性维护,区别了防性维护和预见性维护, 就理解怎么做了,以模具为例,预防性维护: 定性的估计这付模具能使用多长时间,而定期进行维护,此周期由经验所得,没有大量的数据支持。
设备维保的预测性维护技术及案例
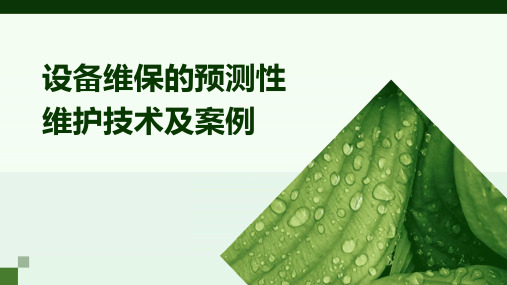
总结词
生产线设备故障预测有助于提高生产效率和降低维护 成本,通过监测生产线设备的运行状态和参数,预测 设备未来故障趋势,提前采取措施进行维修和保养。
详细描述
生产线设备通常由多个设备和系统组成,其运行状态 直接影响生产效率和产品质量。通过安装传感器和监 测系统,实时监测生产线设备的振动、温度、压力等 参数,以及流量、速度等性能指标,结合数据分析技 术,可以预测设备故障趋势,提前进行维修和保养, 确保生产线的稳定运行和产品质量。同时,还可以优 化设备运行参数和工艺流程,提高生产效率和降低能 耗。
技术实施难度与挑战
预测性维护技术需要借助传感器、数据分析工具和算 法等先进技术,实施难度较大,需要专业的技术支持 和培训。
数据安全与隐私保护问题:预测性维护技术需要收集 设备的运行数据和状态信息,涉及到数据安全和隐私 保护问题,需要采取相应的措施保障数据安全和合规 性。
数据安全与隐私保护问题
要点一
数据安全
预测性维护技术涉及大量设备运行数据和敏感信息,需要 采取有效的加密和安全措施,确保数据不被非法获取和使 用。
要点二
隐私保护
在收集和使用设备运行数据时,应尊重用户的隐私权,避 免泄露个人和企业的敏感信息。
THANK YOU
感谢观看
设备维保的预测性 护技术及案例
contents
目录
• 预测性维护技术概述 • 预测性维护技术实施步骤 • 预测性维护技术案例分析 • 预测性维护技术的优势与挑战
01
预测性维护技术概述
定义与特点
定义
预测性维护是一种设备维护策略,通过运用传感器、监测设备和数据分析技术,对设备运行状态进行实时监测和 预测,以确定设备可能出现的故障和性能下降,从而采取相应的维护措施。
预测性维护{维修}又称:预知性、预见性维护{维修})

预测性维护{维修}⼜称:预知性、预见性维护{维修})预测性维护{维修}(Predictive Maintenance,简称PdM)(⼜称:预知性、预见性维护{维修})是以状态为依据(Condition Based)的维护,在机器运⾏时,对它的主要(或需要)部位进⾏定期(或连续)的状态监测和故障诊断,判定装备所处的状态,预测装备状态未来的发展趋势,依据装备的状态发展趋势和可能的故障模式,预先制定预测性维护计划,确定机器应该修理的时间、内容、⽅式和必需的技术和物资⽀持。
预测性维护集装备状态监测、故障诊断、故障(状态)预测、维护决策⽀持和维护活动于⼀体,是⼀种新兴的维护⽅式。
预测性维护不仅在名字称呼上有不同,在概念的内涵和外延上也有出⼊,因此⼜有狭义和⼴义预测性维护两种概念。
狭义的预测性维护⽴⾜于“状态监测”,强调的是“故障诊断”,是指不定期或连续地对设备进⾏状态监测,根据其结果,查明装备有⽆状态异常或故障趋势,再适时地安排维护。
狭义的预测性维护不固定维护周期,仅仅通过监测和诊断到的结果来适时地安排维护计划,它强调的是监测、诊断和维护三位⼀体的过程,这种思想⼴泛适⽤于流程⼯业和⼤规模⽣产⽅式。
⼴义的预测性维护将状态监测、故障诊断、状态预测和维护决策多位合⼀体,状态监测和故障诊断是基础,状态预测是重点,维护决策得出最终的维护活动要求。
⼴义的预测性维护是⼀个系统的过程,它将维护管理纳⼊了预测性维护的范畴,通盘考虑整个维护过程,直⾄得出与维护活动相关的内容。
修复性维护(Corrective Maintenance),⼜称事后维护(Break-down Maintenance),是“有故障才维护(Failure Based)”的⽅式,它是以设备是否完好或是否能⽤为依据的维护,只在设备部分或全部故障后再恢复其原始状态,也就是⽤坏后再修理,属于⾮计划性维护。
预防性维护(Preventive Maintenance)⼜称定时维护,是以时间为依据(Time Based)的维护,它根据⽣产计划和经验,按规定的时间间隔进⾏停机检查、解体、更换零部件,以预防损坏、继发性毁坏及⽣产损失。
【科普】预防性维护与预测性维护

【科普】预防性维护与预测性维护缘起预防性维护与预见性维护1、汽车行业质量管理体系 IATF16949:2016标准3.1.7 预见性维护 predictive maintenance 基于过程数据,通过预测可能的失效模式以避免维护性问题的活动。
3.1.8 预防性维护 prevention maintenance 为消除设备失效和生产的计划外中断的原因而策划的措施,作为制造过程设计的一项输出。
2、数据中心行业实践基本延用汽车行业的定义。
预防性维护:比较常见,也为国内大多数运维及相关人员所熟知。
通常由各零部件、设备、系统的厂家提出相关的固定周期的计划性维护。
部分优先运维团队,也根据自身实际运维经验进行了一些完善和修订。
其特点:一、固定周期,通常一次性制定全年甚至是多年的计划;二、通常仅以设备进行分类,较为优秀者通常会根据项目所在地区,维护团队实力,客户性质,等项目特点而进行适当调整;三、但往往与设备实际运行状态和数据无关。
针对的是一类产品、系统。
而非根据实际设备/产品实际运行状态/性能而特异定制的以制定项目中的指定产品为准的维护。
预见性维护:由于数据中心行业蓬勃发展,行业近年来广受关注,受益于技术进步,预见性维护近来备受重视。
预见性维护是以运行状态(性能)为依据的维修与维护,在设备/系统运行时,对它的主要(或需要)部位进行定期(或连续)的状态监测和故障诊断,判定设备/系统所处的状态,预测设备/系统状态未来的发展趋势,依据设备/系统的状态发展趋势和可能的故障模式,预先制定预测性维护计划,确定设备/系统应该保养/修理的时间、内容、方式和必需的技术和物资支持。
预测性维修集状态监测、故障诊断、故障(状态)预测、维修决策支持和维修活动于一体,结合大数据分析将成为数据中心行业的一种新兴的维护方式。
(早在1999年既已成为汽车行业标准维修方式)广义的预见性维护包含预防性维护,狭义的预见性维护一般排除了常规预防性维护。
[VIP专享]预防性维护与预见性维护区别(非常实用)
![[VIP专享]预防性维护与预见性维护区别(非常实用)](https://img.taocdn.com/s3/m/a3bce053de80d4d8d05a4f38.png)
预防性维护与预见性维护区别(非常实用)汽车体系第一步:先看一下TS标准中的描述7.5.1.4 预防性和预见性维护组织应识别关键过程设备,为机器/设备的维护提供资源,并建立有效的、有计划的全面预防性维护系统。
这个系统至少应包括:— 有计划的维护活动;— 设备、工装和量具的包装和防护;— 可得到关键生产设备的零配件;— 将维护目标形成文件并予以评价和改进。
组织应使用预见性维护方法,以持续改进生产设备的有效性和效率。
第二步:TS标准中的定义3.1.7预见性维护predictive maintenance基于针对过程数据,通过预测可能的失效模式以避免维护性问题的活动。
3.1.8预防性维护preventive maintenance为消除设备失效和生产的计划外中断的原因而策划的措施,作为制造过程设计的一项输出。
第三步:现实问题预防性维护是指有计划的定期设备维护和零配件更换,通常包括保养维护、定期使用检查、定期功能检测、定期拆修、定时更换等几种类型;预见性维护是通过运用各种手段和人的感觉进行数据和信号的采集、分析和判断设备的劣化趋势、故障部位、原因并预测变化发展、提出防范措施,防止和控制可能的故障出现。
预防性及预见性维护要求点检表(ISO/TS16949:2009要求)定义/说明/要求/目的:设备维护是指:为了降低设备失效或功能退化的概率,按预定的时间间隔或规定的标准进行的维护;主要是通过系统性的维护工作消除设备存在的故障征兆,使设备继续保持既定的功能。
关键过程是指:对形成产品质量起决定作用的过程。
预见性维护是指:基于针对过程数据,通过预测可能的失效模式以避免维护性问题的活动。
预防性维护是指:为消除设备失效和生产的计划外中断的原因而策划的措施,作为制造过程设计的一项输出。
组织应识别关键过程设备,为机器/设备的维护提供资源,并建立有效的、有计划的全面预防性维护系统。
预防性维护的目的就是为生产提供稳定的设备。
检查表:编号检查内容1必须识别出关键设备。
预见性维护与预防性维护的区别和联系
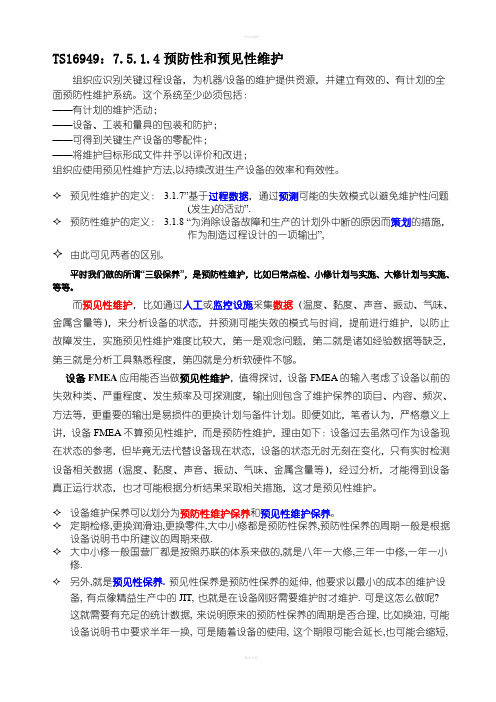
TS16949:7.5.1.4预防性和预见性维护组织应识别关键过程设备,为机器/设备的维护提供资源,并建立有效的、有计划的全面预防性维护系统。
这个系统至少必须包括:——有计划的维护活动;——设备、工装和量具的包装和防护;——可得到关键生产设备的零配件;——将维护目标形成文件并予以评价和改进;组织应使用预见性维护方法,以持续改进生产设备的效率和有效性。
✧预见性维护的定义:3.1.7”基于过程数据,通过预测可能的失效模式以避免维护性问题(发生)的活动”.✧预防性维护的定义:3.1.8 “为消除设备故障和生产的计划外中断的原因而策划的措施,作为制造过程设计的一项输出”,✧由此可见两者的区别。
平时我们做的所谓“三级保养”,是预防性维护,比如日常点检、小修计划与实施、大修计划与实施、等等。
而预见性维护,比如通过人工或监控设施采集数据(温度、黏度、声音、振动、气味、金属含量等),来分析设备的状态,并预测可能失效的模式与时间,提前进行维护,以防止故障发生,实施预见性维护难度比较大,第一是观念问题,第二就是诸如经验数据等缺乏,第三就是分析工具熟悉程度,第四就是分析软硬件不够。
设备FMEA应用能否当做预见性维护,值得探讨,设备FMEA的输入考虑了设备以前的失效种类、严重程度、发生频率及可探测度,输出则包含了维护保养的项目、内容、频次、方法等,更重要的输出是易损件的更换计划与备件计划。
即便如此,笔者认为,严格意义上讲,设备FMEA不算预见性维护,而是预防性维护,理由如下:设备过去虽然可作为设备现在状态的参考,但毕竟无法代替设备现在状态,设备的状态无时无刻在变化,只有实时检测设备相关数据(温度、黏度、声音、振动、气味、金属含量等),经过分析,才能得到设备真正运行状态,也才可能根据分析结果采取相关措施,这才是预见性维护。
✧设备维护保养可以划分为预防性维护保养和预见性维护保养。
✧定期检修,更换润滑油,更换零件,大中小修都是预防性保养,预防性保养的周期一般是根据设备说明书中所建议的周期来做.✧大中小修一般国营厂都是按照苏联的体系来做的,就是八年一大修,三年一中修,一年一小修.✧另外,就是预见性保养.预见性保养是预防性保养的延伸, 他要求以最小的成本的维护设备, 有点像精益生产中的JIT, 也就是在设备刚好需要维护时才维护. 可是这怎么做呢?这就需要有充足的统计数据, 来说明原来的预防性保养的周期是否合理, 比如换油, 可能设备说明书中要求半年一换, 可是随着设备的使用, 这个期限可能会延长,也可能会缩短,你就要根据情况调整维护周期,这就是预见性维护. 可是如何才能知道设备需要维护呢, 有些单位有手段,会对油的成份进行分析来确定设备的磨损情况, 没有这种手段的也可以通过产品质量, 故障频率等来确定。
预防性维护与预见性维护区别

一.设备点检、维护保养的区别是什么?设备点检的目的是为了发现设备异常或隐患,维护(保养)是为了保持设备规定状态所做的工作。
打个比方,你就容易理解了。
定期去牙科检查牙齿或自己不定期检查牙齿(蛀牙、颜色、刷痕磨损等),是点检;自己每天刷牙漱口是维护保养。
另外,根据《设备管理定义和术语》PMS/T 3 的解释,有助于你理解。
3.8 点检checking利用人体的感官(视、听、触、嗅、味)或借助工具、检测设备、仪器等,按照标准(定点、定标、定期、定法、定人“五定”)对设备进行检查或监测,发现设备劣化信息、故障隐患,分析原因并采取改善对策,利用维修窗口进行预防性维修,将设备隐患消灭在萌芽状态的一种管理方法。
注:点检是一种及时掌握设备运行状态,指导设备状态维修的一种科学的管理方法。
3.9 维护servicing为使设备保持规定状态(性能)所需采取的措施。
注:调整、紧固、清扫、润滑“八字”工作方针,是日常维护保养的重要基础工作内容。
3.10 设备维修equipment repair指设备技术状态劣化或发生故障后,为恢复其功能而进行的技术活动。
注1:设备维修,包括各类计划修理和计划外的故障修理及事故修理。
注2:维修模式:通常指一种模式或多种模式的组合,如:定期更换、预防维修、状态维修、事后维修、质量维修、绿色维修、组合维修等。
预防性维护与预见性维护区别汽车体系第一步:先看一下IATF16949标准中的描述7.5.1.4 预防性和预见性维护组织应识别关键过程设备,为机器/设备的维护提供资源,并建立有效的、有计划的全面预防性维护系统。
这个系统至少应包括:—有计划的维护活动;—设备、工装和量具的包装和防护;—可得到关键生产设备的零配件;—将维护目标形成文件并予以评价和改进。
组织应使用预见性维护方法,以持续改进生产设备的有效性和效率。
第二步:IATF16949标准中的定义3.1.7预见性维护predictive maintenance基于针对过程数据,通过预测可能的失效模式以避免维护性问题的活动。
浅谈西门子仪表的预测性维护

浅谈西门子仪表的预测性维护一、前言当今的过程工业,对现场的可靠性要求越来越高,一般都要求仪表设备能满足7/24的连续可靠工作,突发的故障停机会造成极大的损失。
因此,也对设备的维护提出了较高的要求,以最大程度的避免生产的损失和材料的浪费。
根据统计,在1981 年,美国的工厂花费在维护其关键装置系统上的成本超过了 6000 亿美元。
在 1991 年,这种成本已经升至 8000 多亿美元,而在 2000 年更是破记录地达到 12000 亿美元。
这些数据表明,这些成本的三分之一到二分之一由于采用无效的维护管理方法而被浪费掉。
虽然在中国没有这方面的数据统计,但是相信中国目前在这方面的情况和美国当时差不多。
选择错误和原始的维护手段和落后的维护观念是这种无效使用维护支出的主要原因。
在强调经济效益的今天,也有越来越多的用户开始意识到过去那种单纯依靠人的直觉和经验来执行设备维护计划的方式已经不能再满足过程工业的生产需求了。
二、设备维护的模式设备维护一般有三种模式:事后维护、预防性维护和预测性维护。
事后维护,也有人称之为“补救性维护”,“故障后维护”,“运转至出现故障管理”,顾名思义,也就是说设备出现故障时对它进行维修。
这是种“不出故障就不维修”的维护方式,也是最初级最简单也是目前在国内被用户采用最多的维护运行手段。
采用运转至出现故障管理的工厂在机器或系统出现故障之前不会在维护上花费任何资金。
运转至出现故障是一种反应性的管理技术,它会在采取任何维护行动之前等待机器或设备出现故障。
确切地说,这是一种“无维护”管理方法。
它也是最为昂贵的维护管理方法,分析表明,在反应性或事后维护模式下进行维修的成本是有计划或预防性维护模式下进行的相同维护的成本的3 倍。
对维修进行计划安排可使工厂将维修时间和有关的劳动力成本降到最低。
它还提供了一种可减少快速交付和生产下降等负面影响的方法。
与这种维护管理相关的主要费用是:·高备件库存成本;· 高超时劳动力成本;·机器停机时间长;·生产能力低。
预测性维护助力制造设备管理

预测性维护助力制造设备管理随着科技的不断发展和制造业的快速进步,如何保证制造设备的高效运行和延长设备的使用寿命成为了制造业管理者面临的重要问题。
而预测性维护作为一种先进的管理手段,正逐渐受到广泛关注和应用。
本文将讨论预测性维护如何助力制造设备管理,提高设备的可靠性和效率。
1. 概述预测性维护预测性维护,又称为条件化维护或先知性维护,是一种基于设备状况监测和数据分析的维护策略。
其核心理念是通过实时监测设备的工作状态和性能参数,利用数据分析和算法预测设备故障发生的可能性和时间,从而提前采取维护措施,减少设备故障带来的停机时间和损失。
2. 预测性维护的优势相比传统的维修和保养方式,预测性维护具有以下几个优势:(1) 最小化停机时间:通过提前预测设备故障,可以在设备完全失效前对其进行维修,从而最小化停机时间,减少生产损失。
(2) 降低维护成本:预测性维护可以更精确地确定设备维护时机,避免了不必要的维护操作和零配件更换,从而降低了维护成本。
(3) 延长设备寿命:通过定期监测设备的工作状态和性能参数,及时发现并解决潜在问题,可以延长设备的使用寿命,减少更换设备的频率。
3. 实施预测性维护的关键步骤(1) 数据收集:通过传感器、监控设备或其他数据采集手段,实时收集设备的工作状态和性能数据,并建立相应的数据库。
(2) 数据分析:利用数据分析和算法来分析设备数据,寻找数据中的规律和异常,并进一步预测设备的故障概率和时间。
(3) 维护决策:根据预测结果,制定相应的维护策略,确定维护的时机和内容。
(4) 维护执行:根据维护策略,及时对设备进行检修、清洁、润滑等维护操作,确保设备的正常运行。
4. 预测性维护在制造设备管理中的应用(1) 设备状态监测:通过实时监测设备的振动、温度、压力等参数,对设备的状态进行监测,及时发现设备的异常情况。
(2) 故障诊断与预测:通过数据分析和算法,对设备数据进行处理,判断设备是否存在故障,并预测故障的可能性和时间。
设备维修策略简介
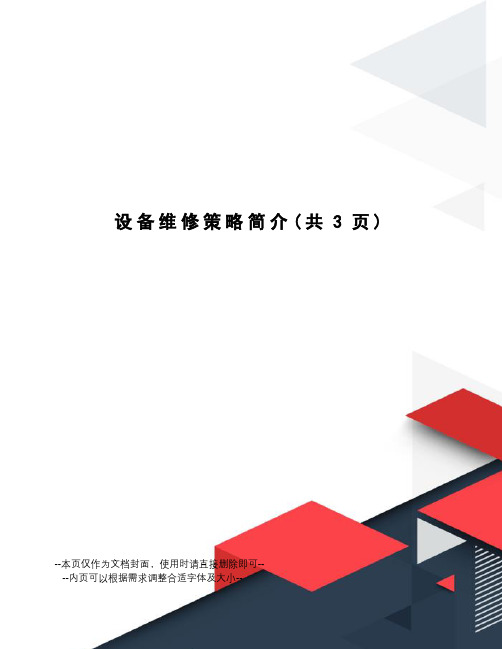
设备维修策略简介(共3页)--本页仅作为文档封面,使用时请直接删除即可----内页可以根据需求调整合适字体及大小--设备维修策略简介视情维修也叫预测性维修(视情维修(Condition Based Maintenance,CBM;Predictive Maintenance,简称PdM)。
是我们在中文翻译时对同一类型的维修工作的不同叫法。
预测性维修基于装备状态监测、故障诊断、故障(状态)预测、维修决策支持和维修活动于一体,是一种新兴的经济效果最佳的维修策略(后面统称预测性维修)。
预测性维修不仅在名字称呼上有不同,在概念的内涵和外延上也有出入,因此又有狭义和广义预测性维修两种概念。
狭义的预测性维修立足于“状态监测”,强调的是“故障诊断”,是指不定期或连续地对设备进行状态监测,根据其结果,查明装备有无状态异常或故障趋势,再适时地安排维修。
狭义的预测性维修不固定维修周期,仅仅通过监测和诊断到的结果来适时地安排维修计划,它强调的是监测、诊断和维修三位一体的过程,这种思想广泛适用于流程工业和大规模生产方式。
广义的预测性维修将状态监测、故障诊断、状态预测和维修决策多位合一体,状态监测和故障诊断是基础,状态预测是重点,维修决策得出最终的维修活动要求。
广义的预测性维修是一个系统的过程,它将维修管理纳入了预测性维修的范畴,通盘考虑整个维修过程,直至得出与维修活动相关的内容。
有故障维修(Break-down Maintenance),是“有故障才维修(Failure Based)”的方式,它是以设备是否完好或是否能用为依据的维修,只在设备部分或全部故障后再恢复其原始状态,也就是用坏后再修理,属于非计划性维修。
预防性定时维修(Preventive Maintenance)又称定时维修,是以时间为依据(Time Based)的维修,它根据生产计划和经验,按规定的时间间隔进行停机检查、解体、更换零部件,以预防损坏、继发性毁坏及生产损失。
- 1、下载文档前请自行甄别文档内容的完整性,平台不提供额外的编辑、内容补充、找答案等附加服务。
- 2、"仅部分预览"的文档,不可在线预览部分如存在完整性等问题,可反馈申请退款(可完整预览的文档不适用该条件!)。
- 3、如文档侵犯您的权益,请联系客服反馈,我们会尽快为您处理(人工客服工作时间:9:00-18:30)。
预测性维护{维修}又称预知性预见性维护预测性维护(又称预知性预见性维护)
预测性维护,也被称为预知性预见性维护,是一种基于数据和分析
的维护策略,旨在提前识别和解决潜在的设备故障和问题,从而最大
程度地减少停机时间和维护成本。
预测性维护通过监测设备的运行状
态和性能参数,使用数据分析和模型预测技术,以及使用先进的传感
器和监测设备等手段,帮助企业实现高效、可靠和可持续的设备维护
管理。
一、预测性维护的意义
预测性维护在现代工业和设备运营中具有重要的意义。
首先,它能
够提高设备的可用性和可靠性。
传统的定期维护往往是基于时间或使
用寿命来安排的,这种维护方式无法准确预测设备的真实状态和故障
潜在风险,并且容易导致设备停机时间过长。
而预测性维护借助先进
的传感器和监测设备,可以实时监测设备的运行状态和性能指标,及
时发现设备问题,并针对性地进行维护和修复,从而提高设备的可用
性和可靠性。
其次,预测性维护可以降低维护成本和维护工作量。
通过实时监测
设备的运行状态,我们可以提前发现设备存在的问题并及时采取措施。
这样,就可以避免因设备故障而导致的停机和维修时间,减少维修成
本和工作量。
另外,预测性维护还可以帮助企业有效规划维护资源,
提高维护效率和维护质量,降低额外的维护费用。
最后,预测性维护有助于延长设备的使用寿命。
通过持续监测设备的运行状况和性能指标,我们可以提前发现设备存在的问题并及时修复,减少不必要的损伤和磨损。
这样,设备的寿命得以延长,减少了设备更换和更新的频率,进一步降低了成本和资源的浪费。
二、预测性维护的实施步骤
实施预测性维护需要进行以下步骤:
1. 设立监测系统:在设备上安装传感器和监测设备,实时监测设备的运行状态和性能参数。
监测数据可以包括温度、压力、振动、电流等信息。
同时,还需要建立数据采集和存储的系统,确保数据的完整和准确性。
2. 数据分析和建模:利用数据分析和数据建模技术,对监测数据进行处理和分析。
通过建立预测模型和故障诊断模型,可以准确评估设备的运行状况和故障潜在风险。
3. 故障预测和预防:基于建立的预测模型,对设备故障进行预测和预防。
通过监测设备的运行状态和性能参数,判断设备是否存在异常情况,并及时采取维护措施,防止故障的发生和进一步恶化。
4. 维护计划和执行:根据故障预测的结果和设备的维护需求,建立维护计划和执行方案。
维护计划应包括维护时机、维护内容和维护工艺等信息。
执行维护方案时,需确保维护操作准确无误。
5. 监控和评估:维护结束后,需要监控设备的运行状态和性能参数,评估维护效果。
通过持续监控和评估,不断优化维护策略和工艺,提
高维护效率和质量。
三、预测性维护的应用领域
预测性维护可以广泛应用于各个领域的设备和工业系统。
以下是几
个常见的应用领域:
1. 制造业:预测性维护可应用于生产线设备、机械工具、自动化系
统等。
通过实时监测设备的运行状态,可以提前发现设备故障并及时
维修,确保生产线的稳定运行和生产效率的提高。
2. 能源领域:预测性维护可以应用于发电设备、输电线路、能源传
输设施等。
通过监测设备的性能指标,可以提前发现设备的故障和损坏,并及时采取措施,确保能源系统的稳定供应。
3. 运输和物流:预测性维护可以应用于机动车辆、航空器和铁路设
备等。
通过监测车辆的运行状况和性能参数,可以提前发现故障和问题,并及时进行维护和修复,保证交通运输的安全和顺畅。
4. 建筑行业:预测性维护可应用于建筑物的设备和设施,如电梯、
空调系统、消防系统等。
通过实时监测设备的运行状态,可以提前发
现设备故障风险,并及时维护和修复,确保建筑物的可用性和安全性。
四、预测性维护的挑战和前景
尽管预测性维护在实践中已经取得了显著的成果,但仍然存在一些
挑战。
首先,数据采集和处理仍然是一个关键问题。
要实现预测性维
护,需要大量的传感器和监测设备,以及高效的数据采集和处理系统。
此外,还需要建立准确可靠的预测模型和故障诊断模型。
其次,预测性维护的实施需要企业具备足够的专业知识和技术能力。
这包括设备维护管理、数据分析和建模、故障预测和预防等方面的能力。
同时,还需要建立良好的维护计划和执行机制,确保维护工作的
有效进行。
然而,预测性维护的前景仍然非常乐观。
随着传感器和监测设备的
逐渐普及和成本的降低,以及大数据和人工智能等技术的快速发展,
预测性维护将得到更广泛的应用和推广。
预测性维护可以帮助企业提
高生产效率、降低维护成本、延长设备使用寿命,从而提高竞争力和
可持续发展能力。
综上所述,预测性维护在现代工业和设备运营中具有重要的意义。
通过实时监测和数据分析,预测性维护可以提前发现和解决设备故障
和问题,降低维护成本和工作量,延长设备使用寿命。
然而,实施预
测性维护也面临一些挑战,需要企业具备足够的专业知识和技术能力。
随着技术的进步和应用的推广,预测性维护的前景非常乐观,将为企
业带来更大的收益和发展机遇。