冲压件未注公差尺寸极限偏差
未注公差尺寸标准
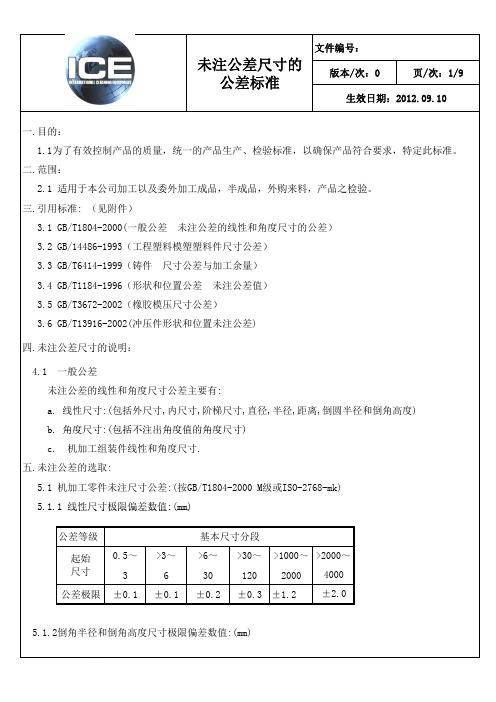
公差等级
起始 尺寸
0.5~ 3
公差极限 ±0.1
>3~ 6
±0.1
基本尺寸分段
>6~ >30~ >1000~ >2000~
30
120 2000 4000
±0.2 ±0.3 ±1.2 ±2.0
5.1.2倒角半径和倒角高度尺寸极限偏差数值:(mm)
未注公差尺寸的 公差标准
文件编号:
版本/次:0
页/次:2/9
基本 尺寸
0.5~3
3~6
6~30
30~120 120~ 400 >400
材料 厚度
≤1 1~4 ≤4 >4 ≤4 >4 ≤4 >4 ≤4 >4 ≤4 >4
冲裁圆 角半径 极限 偏差 ±0.15 ±0.30 ±0.40 ±0.60 ±0.60 ±1.00 ±1.00 ±2.00 ±1.20 ±2.40 ±2.00 ±3.00
公差等级
起始 尺寸
公差极限
≤100 0.6
基本长度分段
>100~ >300~ >1000~
300 1000 3000
0.6
0.8
1
取两面要素中的较长的一边为基准,较短的一边作为被测要素. 5.2.6 同轴度,圆跳动和全跳动未注公差数值: (mm/um)
5.2.6.1 在极限情况下,同轴的未注公差可以和下表中规定的径向跳动的未注公差相等。 5.2.6.2.圆跳动的未注公差按下表选取: mm
成型圆角 基本尺寸 半径
极限偏差
≤3 3~6 6~10 10~18 18~30 >30
+1.00 -0.30 +1.50 -0.50 +2.50 -0.80 +3.00 -1.00 +4.00 -1.50 +5.00 -2.00
未注自由公差规定
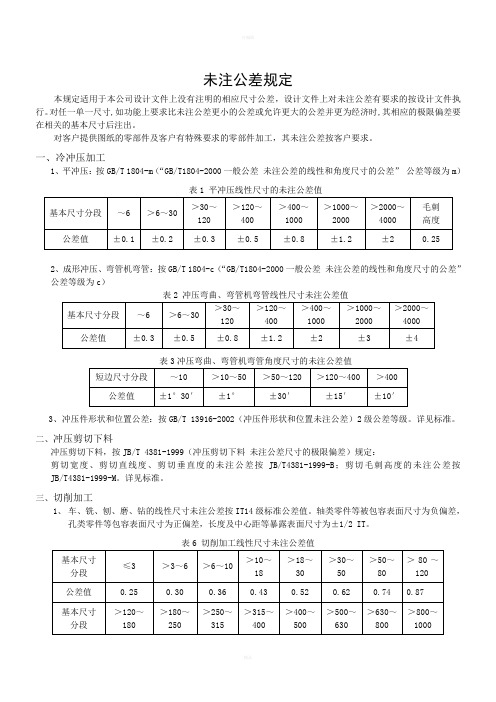
未注公差规定本规定适用于本公司设计文件上没有注明的相应尺寸公差,设计文件上对未注公差有要求的按设计文件执行。
对任一单一尺寸,如功能上要求比未注公差更小的公差或允许更大的公差并更为经济时,其相应的极限偏差要在相关的基本尺寸后注出。
对客户提供图纸的零部件及客户有特殊要求的零部件加工,其未注公差按客户要求。
一、冷冲压加工1、平冲压:按GB/T 1804-m(“GB/T1804-2000一般公差未注公差的线性和角度尺寸的公差”公差等级为m)2、成形冲压、弯管机弯管:按GB/T 1804-c(“GB/T1804-2000一般公差未注公差的线性和角度尺寸的公差”公差等级为c)3、冲压件形状和位置公差:按GB/T 13916-2002(冲压件形状和位置未注公差)2级公差等级。
详见标准。
二、冲压剪切下料冲压剪切下料,按JB/T 4381-1999(冲压剪切下料未注公差尺寸的极限偏差)规定:剪切宽度、剪切直线度、剪切垂直度的未注公差按JB/T4381-1999-B;剪切毛刺高度的未注公差按JB/T4381-1999-M。
详见标准。
三、切削加工1、车、铣、刨、磨、钻的线性尺寸未注公差按IT14级标准公差值。
轴类零件等被包容表面尺寸为负偏差,孔类零件等包容表面尺寸为正偏差,长度及中心距等暴露表面尺寸为±1/2 IT。
表6 切削加工线性尺寸未注公差值2、车、铣、刨、磨、钻的形位公差未注公差按GB/T1184-K(“形状和位置公差未注公差值”中的K级公差)规定。
详见标准。
四、焊接结构参照GB/T19804-2005(焊接结构的一般尺寸公差和形位公差)制定。
五、塑料件塑料模塑件的未注公差,参照GB/T 14486-2008(塑料模塑件尺寸公差)中未注公差制定。
六、模压橡胶制品模压橡胶制品(不包含精密的环形密封圈)的未注公差按GB/T3672.1-2002(橡胶制品的公差第1部分:尺寸公差)中的M3级公差F规定值。
QCT汽车冷冲压加工零件未注公差尺寸的极限偏差
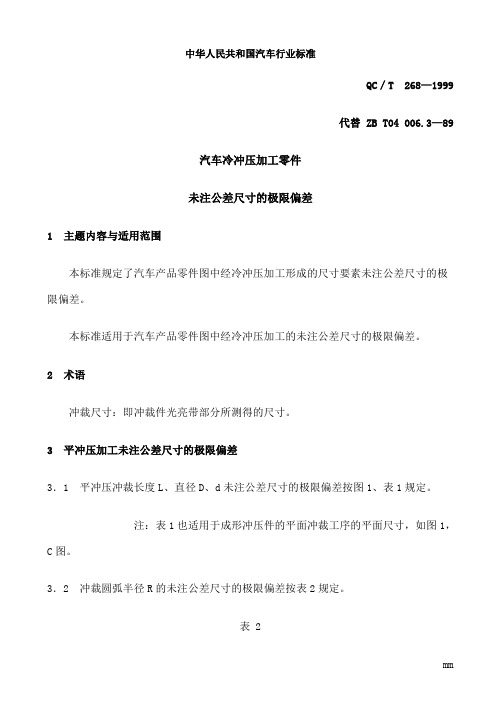
中华人民共和国汽车行业标准QC/T 268—1999代替 ZB T04 006.3—89汽车冷冲压加工零件未注公差尺寸的极限偏差1 主题内容与适用范围本标准规定了汽车产品零件图中经冷冲压加工形成的尺寸要素未注公差尺寸的极限偏差。
本标准适用于汽车产品零件图中经冷冲压加工的未注公差尺寸的极限偏差。
2 术语冲裁尺寸:即冲裁件光亮带部分所测得的尺寸。
3 平冲压加工未注公差尺寸的极限偏差3.1 平冲压冲裁长度L、直径D、d未注公差尺寸的极限偏差按图1、表1规定。
注:表1也适用于成形冲压件的平面冲裁工序的平面尺寸,如图1,C图。
3.2 冲裁圆弧半径R的未注公差尺寸的极限偏差按表2规定。
表 2mm3.3 图样上未注明两冲裁边构成的内部和外部棱角圆角半径r(如图1)的值时,r 应不大于公称料厚的70%。
3.4 冲裁角度未注公差的极限偏差按图2、表3规定。
注:当构成角度的短为未给出尺寸的虚边时(图 2c),则按实际存在的边长L确定。
表 34 成形弯曲件的尺寸公差4.1 弯曲长度L、卷圆直径d未注公差尺寸的极限偏差按图3、表4规定。
表 4mm4.2 管子弯曲处允许其外径变形,变形量(最大直径与最小直径之差)按表5规定。
表 5mm注:当管子有联管螺母等零件装配时,变形后的尺寸应保证其在弯曲处顺利通过。
4.3 弯曲角度未注公差的极限偏差按图4、表6规定。
表 65 成形拉延未注公差尺寸的极限偏差5.1 拉延直径d1(图1c)未注公差尺寸的极限偏差按表1放大一级。
5.2 拉延零件深度H未注公差尺寸的极限偏差按图5、表7规定。
表 7mm5.3 加强筋、加强窝高度h未注公差尺寸的极限偏差按图6、表8规定。
表 8mm5.4 成形件圆弧半径r(图3、图5、图6)未注公差尺寸的极限偏差按表9规定。
表 9mm注:若图样上未注明圆弧半径r值,r应不大于公称料厚。
5.5 成形拉延件允许有局部材料减薄或增厚,变薄后的最小厚度为:t最小=0.8t公称-△式中:t最小——材料的最小厚度,mm;t公称——材料的公称厚度,mm;△——材料厚度下偏差的绝对值,mm。
qct268-1999汽车冷冲压加工零件未注公差尺寸的极限偏差

QC/ T 268—1999代替ZB T04 —89汽车冷冲压加工零件未注公差尺寸的极限偏差1主题内容与适用范围本标准规定了汽车产品零件图中经冷冲压加工形成的尺寸要素未注公差尺寸的极限偏差。
本标准适用于汽车产品零件图中经冷冲压加工的未注公差尺寸的极限偏差。
2术语冲裁尺寸:即冲裁件光亮带部分所测得的尺寸。
3平冲压加工未注公差尺寸的极限偏差3.1平冲压冲裁长度L、直径D d未注公差尺寸的极限偏差按图1、表1规定。
注:表1也适用于成形冲压件的平面冲裁工序的平面尺寸,如图 1 , C图。
3.2冲裁圆弧半径R的未注公差尺寸的极限偏差按表2规定。
mm3.3图样上未注明两冲裁边构成的内部和外部棱角圆角半径r (如图1)的值时,r应不大于公称料厚的70%。
3. 4冲裁角度未注公差的极限偏差按图2、表3规定。
注:当构成角度的短为未给岀尺寸的虚边时(图2c ),则按实际存在的边长L确定。
4成形弯曲件的尺寸公差4.1弯曲长度L、卷圆直径d未注公差尺寸的极限偏差按图3、表4规定。
表4mm4.2管子弯曲处允许其外径变形,变形量(最大直径与最小直径之差)按表5规定表5mm4.3弯曲角度未注公差的极限偏差按图4、表6规定。
5成形拉延未注公差尺寸的极限偏差5.1拉延直径di (图1c)未注公差尺寸的极限偏差按表1放大一级5.2拉延零件深度H未注公差尺寸的极限偏差按图5、表7规定。
mm5.3加强筋、加强窝高度h未注公差尺寸的极限偏差按图6表8规定mm5. 4成形件圆弧半径r (图3、图5、图6)未注公差尺寸的极限偏差按表9规定mm注:若图样上未注明圆弧半径值,应不大于公称料厚。
5.5成形拉延件允许有局部材料减薄或增厚,变薄后的最小厚度为:t最小=公称-△式中:t最小——材料的最小厚度,mmt公称— -一材料的公称厚度,mm△――材料厚度下偏差的绝对值,mm6冲压件的孔边距、孔中心距和孔组距的未注公差尺寸的极限偏差6.1带料、扁条料等型材冲孔对边缘距离未注公差尺寸的极限偏差按图7、表10规定表10mm6.2与同一零件连接的组孔中心距未注公差尺寸的极限偏差按图8、表11规定表11mm6.3与不同零件连接的孔组间距未注公差尺寸的极限偏差按图9、表12规定12表表13mm注:)对不同直径孔的孔距极限偏差,按直径的算术平均值确定。
五金行业冲压件未注公差标准gbt15055-2007

五金行业冲压件未注公差标准gbt15055-2007 GB/T15055-2007冲压件未注公差尺寸极限偏差检索表 1. 冲裁尺寸:经冲孔、落料及其他分离工序加工而成冲压件的线性尺寸。
2. 成型尺寸:经弯曲、拉深及其他工序加工而成冲压件的线性尺寸。
3. 冲裁圆角半径:经冲孔、落料及其他分离工序加工而成冲压件圆角半径的线性尺寸。
4. 冲裁角度:在平板或成形件平面处,经冲裁加工而成的角度尺寸。
5. 弯曲角度:经弯曲成形而形成冲压件的角度尺寸。
下面是赠送的几篇网络励志文章需要的便宜可以好好阅读下,不需要的朋友可以下载后编辑删除~~谢谢~~出路出路,走出去才有路“出路出路,走出去才有路。
”这是我妈常说的一句话,每当我面临困难及有畏难情绪的时候,我妈就用这句话来鼓励我。
很多人有一样的困惑和吐槽,比如在自己的小家乡多么压抑,感觉自己的一生不甘心这样度过,自己的工作多么不满意,不知道该离开还是拔地而起去反击。
你问我,我也不知道你应该怎么选择,人生都是自己的,谁也无法代替你做怎样的选择。
有一个和我熟识的快递员,我之前与他合作了三年。
最开始合作的时候,他负责收件和送件,我搬家的时候,他帮我安排过两次公司的面包车,有时候他送件会顺路把我塞在他的三蹦子里当货物送回我家。
他时常跟我提起在老家农村种地的生活,以及进城之前父母的担忧及村里人为他描绘的可怕的城里人的世界。
那时候的他,工资不高、工作辛苦、老婆怀孕、孩子马上就要出生了,住在北京很郊区的地方。
一定有很多人想说:“这还在北京混个什么劲儿啊~”但他每天都乐呵呵的,就算把快递送错了也乐呵呵的。
某天,他突然递给我一堆其他公司的快递单跟我说:“我开了家快递公司,你看得上我就用我家的吧。
”我有点惊愕,有一种“哎呦喂,张老板好,今天还能三蹦子顺我吗”的感慨。
之后我却很少见他来,我以为是他孩子出生了休假去了。
再然后,我就只能见到单子见不到他了。
某天,我问起他们公司的快递员,小伙子说老板去上海了,在上海开了家新公司。
冷冲压件未注公差尺寸

冷冲压件未注公差尺寸的极限偏差的控制一、课题原因:1、要解决的问题:质量检验需要进行零部件合格与否的判定。
对于图纸标注有公差要求的尺寸,我们可以根据测量结果直接进行判定。
对于没有标注公差要求的尺寸,其极限偏差也必须控制在一个合理的范围之内。
本部分内容要解决的就是经冷冲压加工形成的汽车零部件在产品图中未注公差尺寸的极限偏差控制范围问题。
为了避免产生争议或者发生影响生产的误判,我们有必要进行标准的统一。
2公司给定的冲压件相关标准见上表。
尺寸方面,我们的企业标准是CA/C BG-2-82《冷冲压件未注公差尺寸的公差》和GB/T 13914-2002 《冲压件尺寸公差》。
CA/C BG-2-82对于一汽集团冲压件质量控制起到了重要作用。
GB/T 13914-2002规定了冲压件的尺寸公差等级。
如果产品图纸能够确定相应的等级,则无须按照自由公差来进行质量控制。
还有一个标准——QC/T 268-1999《汽车冷冲压加工零件未注公差尺寸的极限偏差》。
作为汽车行业标准,其中较详细地规定了汽车产品零件图中经冷冲压加工形成的尺寸要素未注公差尺寸的极限偏差的相关要求。
为了统一标准,我们以CA/C BG-2-82为主体、选用汽车行业标准QC/T 268-1999为补充,来作为判定的依据。
3、补充说明:后面的内容,是以CA/C BG-2-82为主体、以QC/T 268-1999为补充。
如有冲突,按照CA/C BG-2-82《冷冲压件未注公差尺寸的公差》执行!CA/C BG-2-82《冷冲压件未注公差尺寸的公差》正式版本以Windchill系统里面的文件为准!冲压车间及冷加工车间生产的冲压件、机加工车间生产的折弯及钻孔件、冷加工车间生产的弯管件,都按本讲义宣贯的标准内容执行!二、CA/C GB-2-82的适用范围本标准适用于本厂冲压件,产品图纸中未注明公差的尺寸公差。
不适用于参考尺寸,几何结构尺寸,按主模型制造的零件尺寸,工序间尺寸和总成装配尺寸。
未注公差尺寸的极限偏差的控制

控制。) 5、毛刺
规定允许毛刺高度的标准为 JB/T 4129-1999《冲压件毛刺高度》。我公司 实际要求为:①下工序凸焊螺母用孔毛刺高度不大于 0.1δ(δ 为料厚);②所 有工件毛剌不大于 0.2mm 高度。这个要求要远高于 JB/T 4129-1999。
(冲压件毛刺系指板料冲裁时留在冲压件成品件断面口上的毛刺。)
如有冲突,按照 CA/C BG-2-82《冷冲压件未注公差尺寸的公差》执行!
隐含在设计文件中的要求
1、冲切尺寸:即冲裁件光亮带部分所测得的尺寸。
对全部高中资料试卷电气设备,在安装过程中以及安装结束后进行高中资料试卷调整试验;通电检查所有设备高中资料电试力卷保相护互装作置用调与试相技互术关,系电,通力根1保过据护管生高线产中敷工资设艺料技高试术中卷0资不配料仅置试可技卷以术要解是求决指,吊机对顶组电层在气配进设置行备不继进规电行范保空高护载中高与资中带料资负试料荷卷试下问卷高题总中2体2资,配料而置试且时卷可,调保需控障要试各在验类最;管大对路限设习度备题内进到来行位确调。保整在机使管组其路高在敷中正设资常过料工程试况1卷中下安,与全要过,加度并强工且看作尽护下可1都关能可于地以管缩正路小常高故工中障作资高;料中对试资于卷料继连试电接卷保管破护口坏进处范行理围整高,核中或对资者定料对值试某,卷些审弯异核扁常与度高校固中对定资图盒料纸位试,置卷编.工保写况护复进层杂行防设自腐备动跨与处接装理地置,线高尤弯中其曲资要半料避径试免标卷错高调误等试高,方中要案资求,料技编试术写5、卷交重电保底要气护。设设装管备备置线4高、调动敷中电试作设资气高,技料课中并3术试、件资且中卷管中料拒包试路调试绝含验敷试卷动线方设技作槽案技术,、以术来管及避架系免等统不多启必项动要方高式案中,;资为对料解整试决套卷高启突中动然语过停文程机电中。气高因课中此件资,中料电管试力壁卷高薄电中、气资接设料口备试不进卷严行保等调护问试装题工置,作调合并试理且技利进术用行,管过要线关求敷运电设行力技高保术中护。资装线料置缆试做敷卷到设技准原术确则指灵:导活在。。分对对线于于盒调差处试动,过保当程护不中装同高置电中高压资中回料资路试料交卷试叉技卷时术调,问试应题技采,术用作是金为指属调发隔试电板人机进员一行,变隔需压开要器处在组理事在;前发同掌生一握内线图部槽 纸故内资障,料时强、,电设需回备要路制进须造行同厂外时家部切出电断具源习高高题中中电资资源料料,试试线卷卷缆试切敷验除设报从完告而毕与采,相用要关高进技中行术资检资料查料试和,卷检并主测且要处了保理解护。现装场置设。备高中资料试卷布置情况与有关高中资料试卷电气系统接线等情况,然后根据规范与规程规定,制定设备调试高中资料试卷方案。
qrt jj 122007 产品零件未注公差尺寸的极限偏差 第2部分 冷冲压加工零件

>120 ±38′ ±30′
5 成形拉延未注公差尺寸的极限偏差 5.1 拉延直径 d1(图 1c)未注公差尺寸的极限偏差按表 1 放大一级。 5.2 拉延零件深度 H 未注公差尺寸的极限偏差按图 3、表 7 的规定。
3
H H
H H
r r
Q/RT JJ 1.2—2007
r r
图3
材料厚度
≤1 >1~2 >2~4 >4~6
±0.40
±0.50
>18~50
±0.50
±0.60
>50~160
±0.60
±0.70
>160~400
±0.80
±1.00
>400
±1.40
±1.60
>3~6
±0.40 ±0.50 ±0.70 ±0.90 ±1.20 ±1.80
㎜
>6~10
— ±0.60 ±0.80 ±1.10 ±1.60 ±2.00
3 平冲压加工未注公差尺寸的极限偏差
3.1 平冲压冲裁长度 L、直径 D、d 未注公差尺寸的极限偏差按图 1、表 1 规定。
L
D
D
D
R
L
LL
L
r
d
R
L
L
L
L
(a)
(b)
图1
L
d1
d
(c)
1
表1
厚度
≤3
基本尺寸
极限偏差
(L、D、d)
孔类
轴类
非孔、轴类
孔类
≤3 >3~6 >6~10 >10~1>80~120 >120~180 >180~250 >250~315 >315~400 >400~500 >500
3.3 图样上未注明两冲裁边构成的内部和外部棱角圆角半径 r(如图 1)的值时,r 应不大于公称料厚 的 70%。 3.4 冲裁角度未注公差的极限偏差按表 3 规定。
冲压件尺寸公差

平板冲裁 成形冲压
1-3 4-6 1-3 4-6
极限偏差的选择: 孔(内形)尺寸的极限偏差取以上公差值冠以“+”号为上偏差,下偏差为0; 轴(外形)尺寸的极限偏差取以上公差值冠以“-”号为下偏差,上偏差为0; 孔中心距,孔边距,弯曲,拉深及其他成形方法而成的长度、高度的极限偏差,取 以上公差值的一半以“±”号分别作为上、下偏差。
公差等级 极限偏差
≤3 +1.00 -0.30
公差等级
f m c v
公差等级
≤10 ±1°00′ ±1°30′ ±2°00′
表4 未注公差成型圆角半径线性尺寸的极限偏差 >3~6 >6~10 >10~18 >18~30 +1.50 +0.25 +3 +4.00 -0.50 -0.80 -1.00 -1.50 表5 未注公差冲裁角度尺寸的极限偏差 短边长度 >10~25 >25~63 >63~160 >160~400 ±0°40′ ±0°30′ ±0°20′ ±0°15′ ±1°00′ ±1°30′ ±0°40′ ±1°00′ ±0°30′ ±0°40′ ±0°20′ ±0°30′
图纸
技术要求: 1.包括公差在内的零件要求以图纸为准,未 注尺寸参考三维数据。 2.未注尺寸公差执行GB/T 15055-2007m级。 3.毛刺高度按JB/T 4129-1999m级。 4.托架零件,材料为08钢,料厚3mm,中批 量生产,要求表面无划痕,孔不允许严重 变形。
冲压件材料的选用
在进行产品的设计时,正确、合理地选择材料是保证产品的最佳性能、工 作寿命、使用安全和经济性的基础。金属材料选用的一般原则如下: 所选用的材料必须满足产品零件工作条件的要求 所选用的材料必须满足零件产品工艺性能的要求 所选材料应满足经济性的要求
冲压件检验规范标准
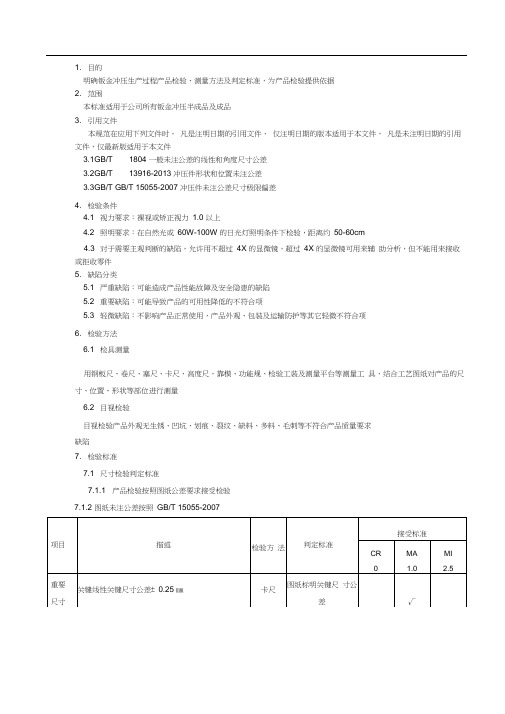
1. 目的明确钣金冲压生产过程产品检验、测量方法及判定标准,为产品检验提供依据2. 范围本标准适用于公司所有钣金冲压半成品及成品3. 引用文件本规范在应用下列文件时,凡是注明日期的引用文件,仅注明日期的版本适用于本文件,凡是未注明日期的引用文件,仅最新版适用于本文件3.1GB/T 1804 一般未注公差的线性和角度尺寸公差3.2GB/T 13916-2013 冲压件形状和位置未注公差3.3GB/T GB/T 15055-2007 冲压件未注公差尺寸极限偏差4. 检验条件4.1 视力要求:裸视或矫正视力1.0 以上4.2 照明要求:在自然光或60W-100W 的日光灯照明条件下检验,距离约50-60cm4.3 对于需要主观判断的缺陷,允许用不超过4X 的显微镜,超过4X 的显微镜可用来辅助分析,但不能用来接收或拒收零件5. 缺陷分类5.1 严重缺陷:可能造成产品性能故障及安全隐患的缺陷5.2 重要缺陷:可能导致产品的可用性降低的不符合项5.3 轻微缺陷:不影响产品正常使用,产品外观、包装及运输防护等其它轻微不符合项6. 检验方法6.1 检具测量用钢板尺、卷尺、塞尺、卡尺、高度尺,靠模、功能规、检验工装及测量平台等测量工具,结合工艺图纸对产品的尺寸、位置、形状等部位进行测量6.2 目视检验目视检验产品外观无生锈、凹坑、划痕、裂纹、缺料、多料、毛刺等不符合产品质量要求缺陷7. 检验标准7.1 尺寸检验判定标准7.1.1 产品检验按照图纸公差要求接受检验7.1.2 图纸未注公差按照GB/T 15055-2007装配孔孔径尺寸D1 ≤30 ㎜孔径尺寸D2 ≥30 ㎜位置度卡尺功能规D1 ﹢0.3 ㎜D2 ﹢0.5 ㎜± 0.25 ㎜一般过孔孔径尺寸D1 ≤30 ㎜孔径尺寸D2 ≥30 ㎜位置度卡尺功能规D1 ﹢0.5 ㎜D2 ﹢1 ㎜± 0.5 ㎜形状位置冲压件形状位置未注公差参考GB/T13916-2013检具满足装配检具适用性方料长宽尺寸卡尺卷尺1:切板方料长度尺寸L ±0.5㎜2: 开料对角线尺寸偏差≤0.5 ㎜轮廓扭曲变形1:前壳成型后扭曲变形量≤2㎜2:后壳成型后扭曲变形量≤1㎜直缝 焊检 验参 考点 深度 翻孔 翻边 高度 后壳 凸点 高度 翻孔不均匀高度尺寸不符合图纸要求7.2 外观检验判定标准卡尺卡尺1: 厚度 3.0 ㎜板料后壳打点高度0.3-0.5 ㎜2 :厚度 4.0 ㎜板料后壳打点高 度1.3 ± 0.1 ㎜1:焊缝目视检验标准点打点深 度 0.3-0.5 ㎜2:计算方法,大点深度约等于1/2 直径1:翻孔净高度3+1 ㎜ 2:端盖翻边高度 h ± 0.5 ㎜项目描述锈蚀是冲压件长期存放或者存放不当导致对产品功能、强度、耐疲劳度产生影响。
冲压件公差

1
±0.25 ±0.40 ±0.60 ±1.00
4
±0.50 ±0.80 ±1.30 ±2.00
—
±0.80 ±1.30 ±2.00 ±3.20
1
±0.30 ±0.50 ±0.80 ±1.30
4
±0.60 ±1.00 ±1.60 ±2.50
—
±1.00 ±1.60 ±2.50 ±4.00
1
±0.45 ±0.70 ±1.10 ±1.80
4
±1.40 ±2.00 ±2.80 ±3.90
—
±1.80 ±2.60 ±3.60 ±5.00
注:对于0.5及0.5以下的尺寸应标公差。
3.2 未注公差成形尺寸的极限偏差按表2规定。
基本尺寸
大于
至
0.5
3
表2 未注公差冲裁尺寸的极限偏差
mm 材料厚度
公差
大于
至
f
m
—
1
±0.15 ±0.20
1
4
3
6
1
4
—
1
6
30
4
—
1
30
120
4
—
1
120
400
4
—
1
400
1000
4
—
1
1000
2000
4
—
1
2000
4000
4
4
±0.20 ±0.30 ±0.40 ±0.55
—
±0.30 ±0.40 ±0.60 ±0.80
1
±0.15 ±0.20 ±0.30 ±0.40
4
±0.30 ±0.40 ±0.55 ±0.75
制图的技术要求

机械制图常用技术要求技术要求(冲压件) 1.锐边去毛刺,冲压切口粗糙度6.3. 2.冲件表面氧化处理:H.Y.或(表面镀锌钝彩.Zn8.DC.). 3.未注公差尺寸的极限偏差按GB/T 1804-92 m级. 技术要求(铸件) 1.铸件不得有气孔、夹渣、裂纹等缺陷. 2.未注明铸造斜度为1~2.5%%d. 3.铸造公差按GB6414-86 CT6. 4.未注明铸造圆角为R1~R2.5. 5.未注公差尺寸的极限偏差按GB/T 1804-92 m级. 6.未注形位公差按GB/T1184-96 H级. 7.去毛刺,未注倒角0.5x45%%D. 技术要求(锻件) 1.未注锻造圆角半径为R1~R2.2.未注锻造斜度为1~1.5%%D,锻造公差为IT15级.3.锻件组织应致密,不得有折叠、裂纹等缺陷,并去飞边. 4.去锐边毛刺,直角处倒钝. 5.未注公差尺寸的极限偏差按GB/T 1804-92 m级. 6.未注形位公差按GB/T1184-96 H级. 技术要求(活塞件) 1.未注公差尺寸的极限偏差按GB/T 1804-92 m级. 2.未注形位公差按GB/T1184-96 H级. 3.去毛刺,未注倒角0.5x45%%D. 4.表面磷化处理. 技术要求(橡胶件) 1.零件表面应光洁.(模具表面粗糙度应在Ra0.4以上) 且不允许有气泡.杂技级凸凹等缺陷. 2.合模缝不允许错位,合模飞边的凸起级厚度不得大于0.02mm. 3.邵氏A型硬度65%%P5. 4.去净飞边. 技术要求(塑料件) 1.成形前材料应预热干燥. 2.成形后制件应光整不得有扭曲变形现象.3.未注圆角为R0.5.4.外表面应光滑,其粗糙度不大于Ra0.4. 且不得有划伤,刻痕等缺陷.5.未注尺寸公差按GB/T 1804-92 m级. 技术要求(弹簧件) 1.旋向:左旋. 2.总圈数:no=12 3.工作圈数:no=10 4.钢丝硬度:HRC42~48. 5.表面氧化处理:H.Y.(俗称发黑) 6.单端并紧磨平.再如:ν如果是整机安装后的技术要求还应该增加:整机的的性能指标,最后的喷漆要求。
QCT汽车冷冲压加工零件未注公差尺寸的极限偏差

中华人民共和国汽车行业标准QC/T 268—1999代替 ZB T04 006.3—89汽车冷冲压加工零件未注公差尺寸的极限偏差1 主题内容与适用范围本标准规定了汽车产品零件图中经冷冲压加工形成的尺寸要素未注公差尺寸的极限偏差。
本标准适用于汽车产品零件图中经冷冲压加工的未注公差尺寸的极限偏差。
2 术语冲裁尺寸:即冲裁件光亮带部分所测得的尺寸。
3 平冲压加工未注公差尺寸的极限偏差3.1 平冲压冲裁长度L、直径D、d未注公差尺寸的极限偏差按图1、表1规定。
注:表1也适用于成形冲压件的平面冲裁工序的平面尺寸,如图1,C图。
3.2 冲裁圆弧半径R的未注公差尺寸的极限偏差按表2规定。
表 2mm3.3 图样上未注明两冲裁边构成的内部和外部棱角圆角半径r(如图1)的值时,r应不大于公称料厚的70%。
3.4 冲裁角度未注公差的极限偏差按图2、表3规定。
注:当构成角度的短为未给出尺寸的虚边时(图 2c),则按实际存在的边长L确定。
表 34 成形弯曲件的尺寸公差4.1 弯曲长度L、卷圆直径d未注公差尺寸的极限偏差按图3、表4规定。
表 4mm4.2 管子弯曲处允许其外径变形,变形量(最大直径与最小直径之差)按表5规定。
表 5mm注:当管子有联管螺母等零件装配时,变形后的尺寸应保证其在弯曲处顺利通过。
4.3 弯曲角度未注公差的极限偏差按图4、表6规定。
表 65 成形拉延未注公差尺寸的极限偏差5.1 拉延直径d1(图1c)未注公差尺寸的极限偏差按表1放大一级。
5.2 拉延零件深度H未注公差尺寸的极限偏差按图5、表7规定。
表 7mm5.3 加强筋、加强窝高度h未注公差尺寸的极限偏差按图6、表8规定。
表 8mm5.4 成形件圆弧半径r(图3、图5、图6)未注公差尺寸的极限偏差按表9规定。
表 9mm注:若图样上未注明圆弧半径r值,r应不大于公称料厚。
5.5 成形拉延件允许有局部材料减薄或增厚,变薄后的最小厚度为:t 最小=0.8t 公称-△式中:t 最小——材料的最小厚度,mm ; t 公称——材料的公称厚度,mm ; △——材料厚度下偏差的绝对值,mm 。
零部件尺寸未注公差验收标准
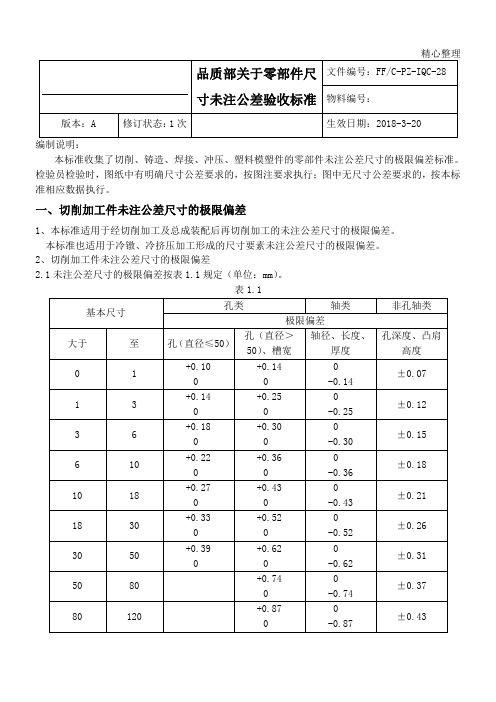
编制说明:本标准收集了切削、铸造、焊接、冲压、塑料模塑件的零部件未注公差尺寸的极限偏差标准。
检验员检验时,图纸中有明确尺寸公差要求的,按图注要求执行;图中无尺寸公差要求的,按本标准相应数据执行。
12车、铣、刨、磨、钻的线性尺寸未注公差按IT14级标准公差值。
轴类零件等被包容表面尺寸为负偏差,孔类零件等包容表面尺寸为正偏差,长度及中心距等暴露表面尺寸为±1/2IT。
切削加工线性尺寸未注公差值表1.2注:对于不同直径孔的中心距极限偏差,d按直径的算术平均值确定。
2.3与不同零件连接的孔间距的极限偏差按图1.2表1.3规定(单位:mm)。
表1.32.4未注公差尺寸的倒角(B、H)和圆角半径(R)的极限偏差按表1.4规定(单位:mm)。
表1.42.5螺纹长度未注公差尺寸的极限偏差按表1.5规定(单位:mm)。
2.3钢模锻造非孔轴类尺寸未注公差尺寸的极限偏差按表2.3规定(单位:mm)。
表2.3三、铸造零件未注公差尺寸的极限偏差1、适用范围:本标准适用于砂型铸造、金属型、低压铸造、熔模铸造、压力铸造的零件的未注公差尺寸的极限偏差。
2、铸件未注公差尺寸的极限偏差2.1砂型铸造未注公差尺寸的极限偏差按表3.1的规定(单位:mm)。
表3.12.2金属型及低压铸造未注公差尺寸的极限偏差按表3.2规定(单位:mm)。
表3.22.4压力铸造未注公差尺寸的极限偏差按表3.4规定(单位:mm)。
表3.4表4.1注:大批量生产方式的焊接件取A级公差,小批量单件生产的焊接件取B级公差。
2.2角度未注公差的极限偏差按表4.2规定(单位:mm)。
1.2未注公差冲裁圆角半径的极限偏差按表5.2规定(单位:mm)。
表5.21.4未注公差弯曲角度的极限偏差按表5.4规定(单位:mm)。
表5.4使用说明:a、本标准一般情况下推荐使用f或m级,冲压件有特殊要求的按产品规定要求执行;b、一般情况下,被包容的零件尺寸取下偏差,包容零件尺寸取上偏差;2、冲压件形状和位置未注公差2.1直线度、平面度未注公差冲压件的直线度、平面度设五个公差等级,其未注公差值按图5.1表5.5规定(单位:mm),平面度未注公差应选择较长边为主参数。
技术要求大全

机械设计技术要求大全一、冲压件1.锐边去毛刺,冲压切口粗糙度6.3.2.冲件外表氧化处理:H.Y.或(外表镀锌钝彩.Zn8.DC.)3.未注公差尺寸的极限偏差按GB/T15055(f精密、m中等、c粗糙、v最粗〕4.冲压件形状和位置未注公差按GB/T 13916-2000。
直线度、平面度设五个等级〔1、2、3、4、5〕同轴度、对称度设四个等级〔1、2、3、4〕5.平冲ST1至ST11级,成形冲FT1至FT10。
二、铸件1.铸件外表上不允许有冷隔、裂纹、缩孔和穿透性缺陷及严重的残缺类缺陷〔如欠铸、机械损伤等〕。
2.未注明铸造斜度为1~°。
3.铸造公差按GB6414-86 CT6。
4.未注明铸造圆角为R1~。
5.铸件应清理干净,不得有毛刺、飞边,非加工外表上的浇铸冒口应清理与铸件外表齐平。
6.铸件非加工外表上的铸字和标志应清晰可辨,位置和字体应符合图样要求。
7.铸件非加工外表的粗糙度,砂型铸造R,不大于50μm。
8.铸件上的型砂,芯砂,芯骨应去除干净。
9.铸件有倾斜的部位、其尺寸公差带应沿倾斜面对称配置。
10.对错型、凸台铸偏等应予以修正,到达圆滑过渡,一定保证外观质量。
11.铸件非加工外表的皱褶,深度小于2mm,间距应大于100mm。
12.机器产品铸件的非加工外表均需喷丸处理或滚筒处理,到达清洁度Sa21/2级的要求。
13.铸件必须进行水韧处理。
三、锻件1.未注锻造圆角半径为R1~R2。
2.未注铸造斜度为1~°,锻造公差为IT15级。
3.锻件组织应致密,不得有折叠、裂纹等缺陷,并去飞边。
4.去锐边毛刺,直角处倒钝。
5.每个钢锭的水口、冒口应有足够的切除量,以保证锻件无缩孔和严重的偏折。
6.锻件应在有足够能力的锻压机上锻造成形,以保证锻件内部充分锻透。
7.锻件不允许有肉眼可见的裂纹、折叠和其他影响使用的外观缺陷。
局部缺陷可以去除,但清理深度不得超过加工余量的75%,锻件非加工外表上的缺陷应清理干净并圆滑过渡。