生产加工过程中关键控制点
生产过程中关键控制点注意事项

生产过程中关键控制点注意事项一、投料口1、投料工是否按照中控要求更换粉碎筛片并且检查筛片是否完好;2、投料工在投料过程中,必须严格按照现场品控员和收货组规定的区域领用投放原料,投料过程中必须将混入其中的线绳、石块、杂质以及霉变、结块原料选出;3、每种原料投完后必须将作业现场清理干净后方可进行下一种原料的投放;4、若需搭配取料必须按现场品控员规定的比例进行搭配;5、投料时须将袋内原料清理干净,残余量不得超过20g/件;6、投料工在下班之前须将所投的每种原料堆放区及投料口彻底清理,严禁将散原料扫入堆垛区域;7、投料工在投料时,不准划破外包装袋,只能从缝袋处拆缝包线,拆下的标签线绳及时放入杂物箱内;8、投返工料时,标签需回收,及时交给原料库管保管。
二、仓顶工1、仓顶工必须根据工艺要求,及时更换分级筛,并在仓顶巡视检查分配器等设备运行是否正常,防止出现串仓、溢仓现象,2、每4小时清理永磁筒、初清筛一次,对筛出的结块原料及时分类清理后从仓口投入原料仓内,3、必须抽样检查粉碎细度是否达标(100%过20目标准筛),每隔30分钟检查一次,4、仓顶工须随时监控是否有串仓、溢仓、粉碎细度不合格及花料等情况出现。
三、中控员1、现场品控员每天必须检查中控员输入的配方是否正确,是否按规定添加回机料、油脂等,若要求在原料仓内进行搭配的原料是否按规定执行,2、是否按工艺参数表执行混合时间,3、每次换核心料前是否明确告之投药工,4、制粒之前是否通知制粒工更换相应的环模。
四、小药投料口1、药品和其它手称原料投入生产前要进行抽查重量并做好记录。
(原料重量小于5Kg,允许误差0.1Kg;原料重量5—25Kg,允许误差0.15 Kg;原料重量25—80 Kg允许误差0.25Kg)。
2、小料口错投、漏投、多投药物时,应立即上报并停止生产。
五、制粒工1、制粒工是否按要求更换环模和筛子,2、严格保证调质温度,喂料频率,检查制粒机切刀是否调节适当,是否锋利,设备、溜管、锅巴料是否清理干净,3、每隔10分钟抽样检查物料粉碎细度,颗粒长短均匀度,含粉率,色泽是否正常。
重要工序质量控制及关键工序控制点
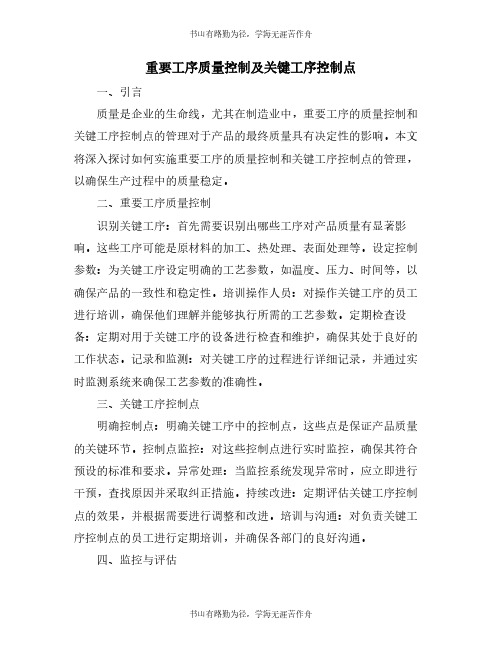
重要工序质量控制及关键工序控制点一、引言质量是企业的生命线,尤其在制造业中,重要工序的质量控制和关键工序控制点的管理对于产品的最终质量具有决定性的影响。
本文将深入探讨如何实施重要工序的质量控制和关键工序控制点的管理,以确保生产过程中的质量稳定。
二、重要工序质量控制识别关键工序:首先需要识别出哪些工序对产品质量有显著影响。
这些工序可能是原材料的加工、热处理、表面处理等。
设定控制参数:为关键工序设定明确的工艺参数,如温度、压力、时间等,以确保产品的一致性和稳定性。
培训操作人员:对操作关键工序的员工进行培训,确保他们理解并能够执行所需的工艺参数。
定期检查设备:定期对用于关键工序的设备进行检查和维护,确保其处于良好的工作状态。
记录和监测:对关键工序的过程进行详细记录,并通过实时监测系统来确保工艺参数的准确性。
三、关键工序控制点明确控制点:明确关键工序中的控制点,这些点是保证产品质量的关键环节。
控制点监控:对这些控制点进行实时监控,确保其符合预设的标准和要求。
异常处理:当监控系统发现异常时,应立即进行干预,查找原因并采取纠正措施。
持续改进:定期评估关键工序控制点的效果,并根据需要进行调整和改进。
培训与沟通:对负责关键工序控制点的员工进行定期培训,并确保各部门的良好沟通。
四、监控与评估监控计划:制定详细的监控计划,明确监控的频率、方法和技术要求。
数据收集与分析:收集关键工序和关键控制点的相关数据,对其进行分析,以评估其性能和效果。
定期评估:定期对整个生产过程进行全面评估,确保所有工序都符合质量要求。
反馈机制:建立有效的反馈机制,使管理层能及时了解生产过程中的问题,并采取相应的措施。
持续改进:根据监控和评估的结果,持续优化生产过程,提高产品质量和生产效率。
五、质量管理体系建设质量方针与目标:制定明确的质量方针和目标,为整个质量管理工作提供指导。
组织结构与职责:建立完善的组织结构,明确各部门和人员的职责和工作关系。
2生产工艺操作程序关键控制点
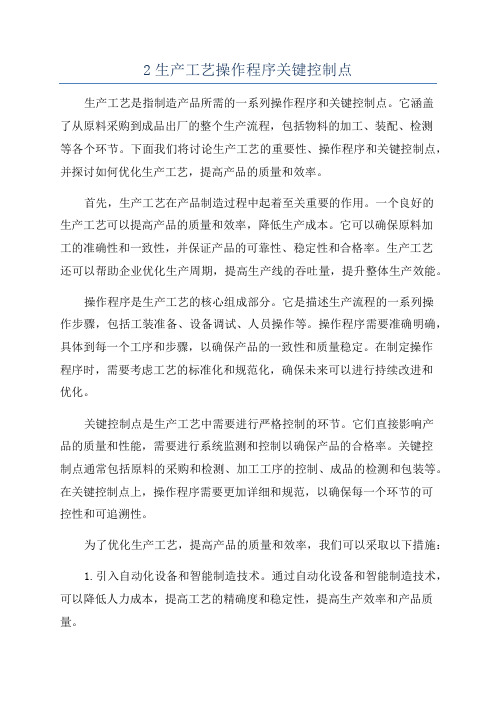
2生产工艺操作程序关键控制点生产工艺是指制造产品所需的一系列操作程序和关键控制点。
它涵盖了从原料采购到成品出厂的整个生产流程,包括物料的加工、装配、检测等各个环节。
下面我们将讨论生产工艺的重要性、操作程序和关键控制点,并探讨如何优化生产工艺,提高产品的质量和效率。
首先,生产工艺在产品制造过程中起着至关重要的作用。
一个良好的生产工艺可以提高产品的质量和效率,降低生产成本。
它可以确保原料加工的准确性和一致性,并保证产品的可靠性、稳定性和合格率。
生产工艺还可以帮助企业优化生产周期,提高生产线的吞吐量,提升整体生产效能。
操作程序是生产工艺的核心组成部分。
它是描述生产流程的一系列操作步骤,包括工装准备、设备调试、人员操作等。
操作程序需要准确明确,具体到每一个工序和步骤,以确保产品的一致性和质量稳定。
在制定操作程序时,需要考虑工艺的标准化和规范化,确保未来可以进行持续改进和优化。
关键控制点是生产工艺中需要进行严格控制的环节。
它们直接影响产品的质量和性能,需要进行系统监测和控制以确保产品的合格率。
关键控制点通常包括原料的采购和检测、加工工序的控制、成品的检测和包装等。
在关键控制点上,操作程序需要更加详细和规范,以确保每一个环节的可控性和可追溯性。
为了优化生产工艺,提高产品的质量和效率,我们可以采取以下措施:1.引入自动化设备和智能制造技术。
通过自动化设备和智能制造技术,可以降低人力成本,提高工艺的精确度和稳定性,提高生产效率和产品质量。
2.强化质量控制和质量保证体系。
建立完善的质量控制和质量保证体系,包括质量管理体系、质检标准和流程等,确保产品满足客户的要求和标准。
3.进行全面的数据分析和过程监测。
通过全面的数据分析和过程监测,可以及时发现生产中的异常和问题,及时采取措施进行调整和改进,提高生产工艺的稳定性和一致性。
4.实施员工培训和技能提升计划。
通过培训和技能提升计划,提高员工的专业素质和操作技能,确保他们熟练掌握操作程序和操作技巧,提高工艺的可控性和可靠性。
关键工序质量控制点

关键工序质量控制点一、引言关键工序质量控制点是指在生产过程中对关键工序进行质量控制的重要节点。
通过在关键工序中设立质量控制点,可以及时发现和纠正产品质量问题,确保产品质量的稳定和可靠性。
本文将详细介绍关键工序质量控制点的定义、目的、设立原则和具体操作步骤。
二、定义关键工序质量控制点是指在生产过程中对影响产品质量的关键环节进行控制的特定位置或者时间点。
通过对这些关键工序进行监控和控制,可以确保产品在整个生产过程中的质量稳定性和一致性。
三、目的1. 提高产品质量:通过对关键工序进行质量控制,可以及时发现和解决工艺问题,确保产品质量符合要求。
2. 减少质量风险:关键工序质量控制点的设立可以匡助企业预防和降低质量风险,减少不良品率和客户投诉。
3. 提高生产效率:通过对关键工序进行监控和控制,可以提高生产效率,减少生产过程中的浪费和重复工作。
四、设立原则1. 选择关键工序:根据产品特点和生产工艺,选择对产品质量影响较大的关键工序作为控制点。
2. 确定控制参数:根据产品质量要求和工艺要求,确定关键工序的控制参数,如温度、压力、速度等。
3. 制定控制标准:根据产品质量要求和工艺要求,制定关键工序的控制标准,如合格品率、不良品率等。
4. 设立监测方法:选择适当的监测方法,如抽样检验、实时监测、自动化控制等,对关键工序进行监测和控制。
5. 制定纠正措施:当关键工序浮现异常情况时,应及时采取纠正措施,防止不良品的产生和扩散。
五、操作步骤1. 识别关键工序:通过对生产工艺的分析,确定对产品质量影响较大的关键工序。
2. 确定控制参数:根据产品质量要求和工艺要求,确定关键工序的控制参数,并建立相应的记录表格。
3. 制定控制标准:根据产品质量要求和工艺要求,制定关键工序的控制标准,并明确合格品率和不良品率等指标。
4. 设立监测方法:根据关键工序的特点和要求,选择适当的监测方法,如抽样检验、实时监测等。
5. 建立监测记录:建立关键工序的监测记录表格,记录关键工序的监测结果和控制措施。
重要工序质量控制及关键工序控制点

重要工序质量控制及关键工序控制点一、引言在生产过程中,重要工序的质量控制是确保产品质量的关键环节。
本文将详细介绍重要工序质量控制的标准格式文本,包括工序描述、质量控制要求、关键工序控制点等内容。
二、工序描述1. 工序名称:XXX工序2. 工序描述:XXX工序是生产过程中的关键工序,它涉及到XXX的加工、XXX的装配等步骤。
该工序的质量控制直接影响产品的性能和可靠性。
三、质量控制要求1. 质量目标:确保产品在XXX方面的质量达到标准要求。
2. 检验方法:采用XXX检验方法进行质量检验。
3. 检验标准:根据产品的设计要求和相关标准,制定相应的检验标准。
4. 技术要求:XXX工序的操作人员必须具备相应的技能和经验,严格按照工艺流程进行操作。
5. 设备要求:确保使用的设备符合相关的质量标准,且设备的维护保养工作得到有效执行。
6. 环境要求:确保工作环境符合相关的卫生、安全和环境保护要求。
四、关键工序控制点1. 控制点一:XXX- 描述:XXX是XXX工序中的关键步骤,直接影响产品的XXX性能。
- 控制方法:XXX- 控制标准:XXX2. 控制点二:XXX- 描述:XXX是XXX工序中的关键步骤,直接影响产品的XXX性能。
- 控制方法:XXX- 控制标准:XXX3. 控制点三:XXX- 描述:XXX是XXX工序中的关键步骤,直接影响产品的XXX性能。
- 控制方法:XXX- 控制标准:XXX4. 控制点四:XXX- 描述:XXX是XXX工序中的关键步骤,直接影响产品的XXX性能。
- 控制方法:XXX- 控制标准:XXX五、总结重要工序质量控制及关键工序控制点是确保产品质量的重要手段。
通过制定质量控制要求和关键工序控制点,可以保证产品在关键工序中的质量达到标准要求,提高产品的性能和可靠性。
在实际生产中,要严格按照质量控制要求和控制点进行操作和检验,确保产品的质量稳定和可靠。
关键控制点管理制度

关键控制点管理制度关键控制点(Key Control Point,KCP)管理制度是一种质量控制措施,它确定了在生产过程中需要特别关注的关键控制点以确保产品符合质量要求。
这种制度可以帮助组织在生产过程中及时发现和纠正不符合质量要求的情况,从而提高产品的质量水平和客户满意度。
本文将详细介绍关键控制点管理制度的概念、作用、要点和实施步骤。
关键控制点管理制度是一种预防性的质量管理手段,通过预先设定关键控制点并采取相关控制措施,可以最大限度地减少产品质量问题的发生。
关键控制点通常是制造过程中的一些关键步骤或环节,对其进行有效的监控和管理可以对产品质量的最终结果产生重要影响。
1.预防产品质量问题的发生:通过对关键控制点实施严格的监控和管理,可以及时发现和纠正潜在的质量问题,防止其进一步扩大,保证产品的一致性和可靠性。
2.提高产品的质量水平:关键控制点管理制度可以帮助组织识别和优化制造过程中的关键环节,确保每个环节都按照标准操作程序进行,从而提高产品的质量水平和稳定性。
3.提高客户满意度:通过有效的关键控制点管理,可以减少不合格品和客户投诉的风险,提高产品质量的一致性和可靠性,从而提升客户对产品的满意度和忠诚度。
实施关键控制点管理制度需要注意以下几个要点:1.确定关键控制点:在确定关键控制点时,需要充分考虑产品的特性和制造过程中可能出现的质量问题,确定能够对最终产品质量产生重要影响的关键环节。
2.制定控制措施:对于每个关键控制点,需要制定相应的控制措施,明确相关员工的职责和要求,确保每个环节都按照标准操作程序进行。
3.设立监控机制:对于关键控制点,需要建立相应的监控机制,以确保其有效运行。
监控可以通过检查、记录和统计等方式进行,及时发现和纠正不符合要求的情况。
4.进行周期性评估:关键控制点管理制度需要进行周期性评估,以确保其适用性和有效性。
评估可以包括关键控制点的设置是否合理、控制措施是否有效等方面。
1.确定关键控制点:通过对产品和制造过程进行分析,确定可能对产品质量产生重要影响的关键环节。
生产过程中的质量控制关键点

生产过程中的质量控制关键点在现代工业生产中,质量控制是确保产品符合规格标准并满足客户需求的重要环节。
质量控制的关键点有很多,下面将从原材料选择、工艺流程、人员培训和设备维护等方面进行探讨。
一、原材料选择原材料是产品质量的基础。
在生产过程中,选择合适的原材料对于产品的质量至关重要。
首先,原材料应符合国家和行业的标准要求,具备相应的质量检测报告。
其次,原材料的供应商应具备良好的信誉度和质量控制体系,确保原材料的可追溯性和供应的稳定性。
最后,生产企业需要加强对原材料的检验和抽样分析,确保原材料的质量稳定可靠。
二、工艺流程控制工艺流程是产品成型的关键环节。
对于需要进行多道工序的产品来说,如何掌握每个工序的质量控制点非常重要。
首先,生产企业应建立完善的工艺流程控制体系,明确每个工序的具体要求,制定相应的操作规程和标准作业指导书。
其次,对于关键控制工序,应加强监控和抽样检验,确保产品在关键工序的质量合格。
最后,生产企业应注重对工艺流程的持续改进,通过改进和优化工艺,提高产品的一致性和稳定性。
三、人员培训人员是质量控制的决定性因素。
只有具备一定的专业知识和技能的员工才能在生产过程中正确操作和控制质量。
因此,生产企业应加强对员工的培训和教育。
首先,培训内容应包括质量控制的基本知识、操作规程和质量分析方法等。
其次,培训应以实际操作为主,通过实际案例和实验演示来让员工掌握质量控制的关键点和技巧。
最后,生产企业应提供良好的培训环境和机会,鼓励员工参与岗位轮换和技能提升,从而不断提高员工的质量控制能力。
四、设备维护设备是保障产品质量的重要保障。
只有设备处于良好的工作状态,才能保证产品的正常生产和质量稳定。
因此,生产企业应加强对设备的日常维护和保养。
首先,制定科学合理的设备维护计划,明确每个设备的维护周期和维护内容。
其次,加强设备的巡检和保养,及时发现和解决设备故障,确保设备的正常运行。
最后,注重设备的更新和升级,引进先进的设备和技术,提高生产线的自动化程度和生产效率,从而提升产品质量和竞争力。
重要工序质量控制及关键工序控制点

重要工序质量控制及关键工序控制点引言在生产过程中,重要工序的质量控制是确保产品质量的关键。
要实施有效的质量控制,需要明确关键工序的控制点,并采取相应的控制措施。
本文将介绍重要工序质量控制的重要性,并一些常见的关键工序控制点。
重要工序质量控制的意义重要工序可以理解为生产过程中对产品质量影响最大的环节。
在这些工序中,质量问题的发生可能会导致产品缺陷、不良品率上升甚至客户投诉。
对于重要工序的质量控制非常重要。
通过对重要工序的质量控制,可以实现以下目标:1. 提高产品质量:通过对重要工序进行严格的质量控制,可以减少质量问题的发生,提高产品的一致性和稳定性。
2. 减少成本:质量问题往往会导致不良品的产生,进而增加了废品处理和维修成本。
通过对重要工序的质量控制,可以减少不良品率,降低相关成本。
3. 提高客户满意度:质量问题可能导致客户投诉,从而影响客户的满意度和忠诚度。
通过对重要工序的质量控制,可以保证产品的质量达到客户的期望,提升客户满意度。
关键工序控制点下面了一些常见的关键工序控制点,这些控制点在不同的生产过程中可能有所区别。
1. 原材料检验:在生产开始之前,需要对原材料进行检验,确保其符合质量要求。
这包括外观检查、尺寸检测、化学成分分析等。
2. 加工参数控制:在加工过程中,需要控制一些关键参数,如温度、压力、速度等。
这些参数的控制可以影响产品的质量特性,需要根据实际情况确定合适的控制范围。
3. 在线检测:在生产过程中,可以设置一些在线检测点,对产品进行实时监测。
这样可以及时发现质量问题,防止不良品的产生。
4. 中间检验:在生产过程中的关键节点,需要进行中间检验。
这些检验可以验证前一步骤的质量控制效果,并及时发现问题。
常见的中间检验包括尺寸检测、成品外观检查等。
5. 最终检验:在产品制造完成之后,需要进行最终检验。
这个环节是确保产品质量的一道关口,包括外观检查、功能性测试等。
6. 过程记录和分析:对于关键工序,需要进行过程记录和分析。