超精金刚石刀具的特点及应用
论述金刚石刀具超精密切削的机理丶条件和应用范围

金刚石刀具超精密切削的机理丶条件和应用范围
金刚石刀具是超精密切削中常用的刀具材料,其切削机理、条件和应用范围如下:
1.切削机理:
⏹金刚石刀具的切削刃非常锋利,在切削过程中能够实现“切入式切削”,
使切削力大大减小。
⏹金刚石的硬度极高,切削时不易被工件材料磨损,能够保持良好的切削刃
形状。
⏹金刚石的传热性能极佳,能够快速地将切削热量传递出去,从而降低切削
温度,减少热损伤。
1.切削条件:
⏹刀具刃口半径:为了实现超精密切削,需要将刀具的刃口半径减小到亚微
米级,以提高切削的精度和表面粗糙度。
⏹切削用量:为了减小切削力和热量,需要选择较小的切削深度和进给速度,
以提高切削效率。
⏹工件材料:金刚石刀具适用于加工各种硬材料,如淬火钢、硬质合金等。
但是,对于一些韧性较大的材料,需要进行预处理或选择其他刀具材料。
1.应用范围:
⏹金刚石刀具广泛应用于超精密切削领域,如光学零件、轴承、硬盘磁头、IC
芯片等高精度、高表面质量的零件加工。
⏹在加工过程中,金刚石刀具还可以用于制作各种微细结构,如微孔、微槽
等。
综上所述,金刚石刀具的超精密切削需要满足一定的条件,并具有广泛的应用范围。
金刚石材料刀具简介

金刚石材料刀具简介可以制成切削刀具的金刚石材料有天然单晶金刚石、人造单晶金刚石、化学气相沉积法(CVD)金刚石厚膜、人造聚晶金刚石复合片等。
1、天然单晶金刚石天然单晶金刚石是一种各向异性的单晶体。
硬度达HV9000-10000,是自然界中最硬的物质。
这种材料耐磨性极好,制成刀具在切削中可长时间保持尺寸的稳定,故而有很长的刀具寿命。
天然金刚石刀具刃口可以加工到极其锋利。
可用于制作眼科和神经外科手术刀;可用于加工隐形眼镜的曲面;可用于切割光导玻璃纤维;用于加工黄金、白金首饰的花纹;最重要的用途在于高速超精加工有色金属及其合金。
如铝、黄金、巴氏合金、铍铜、紫铜等。
用天然金刚石制作的超精加工刀具其刀尖圆弧部分在400倍显微镜下观察无缺陷,用于加工铝合金多面体反射镜、无氧铜激光反射镜、陀螺仪、录像机磁鼓等。
表现粗糙度可达到Ra(0.01-0.025)μm。
天然金刚石材料韧性很差,抗弯强度很低,仅为(0.2-0.5)Gpa。
热稳定性差,温度达到700℃-800℃时就会失去硬度。
温度再高就会碳化。
另外,它与铁的亲和力很强,一般不适于加工钢铁。
2、人造单晶金刚石人造单晶金刚石作为刀具材料,市场上能买到的目前有戴比尔斯(DE-BEERS)生产的工业级单晶金刚石材料。
这种材料硬度略逊于天然金刚石。
其它性能都与天然金刚石不相上下。
由于经过人工制造,其解理方向和尺寸变得可控和统一。
随着高温高压技术的发展,人造单晶金刚石最大尺寸已经可以做到8mm。
由于这种材料有相对较好的一致性和较低的价格,所以受到广泛的注意。
作为替代天然金刚石的新材料,人造单晶金刚石的应用将会有大的发展。
3、人造聚晶金刚石人造聚晶金刚石(PCD)是在高温高压下将金刚石微粉加溶剂聚合而成的多晶体材料。
一般情况下制成以硬质合金为基体的整体圆形片,称为聚晶金刚石复合片。
根据金刚石基体的厚度不同,复合片有1.6mm、3.2mm、4.8mm等不同规格。
而聚晶金刚石的厚度一般在0.5mm左右。
金刚石(pcd)铰刀的优势特点
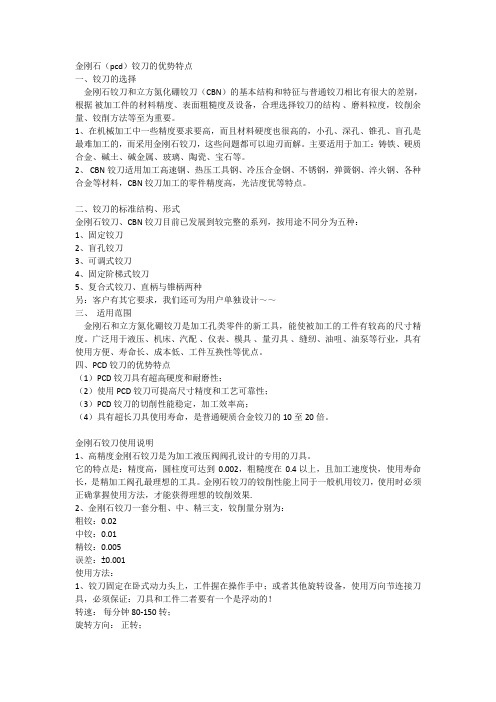
金刚石(pcd)铰刀的优势特点一、铰刀的选择金刚石铰刀和立方氮化硼铰刀(CBN)的基本结构和特征与普通铰刀相比有很大的差别,根据被加工件的材料精度、表面粗糙度及设备,合理选择铰刀的结构、磨料粒度,铰削余量、铰削方法等至为重要。
1、在机械加工中一些精度要求要高,而且材料硬度也很高的,小孔、深孔、锥孔、盲孔是最难加工的,而采用金刚石铰刀,这些问题都可以迎刃而解。
主要适用于加工:铸铁、硬质合金、碱土、碱金属、玻璃、陶瓷、宝石等。
2、CBN铰刀适用加工高速钢、热压工具钢、冷压合金钢、不锈钢,弹簧钢、淬火钢、各种合金等材料,CBN铰刀加工的零件精度高,光洁度优等特点。
二、铰刀的标准结构、形式金刚石铰刀、CBN铰刀目前已发展到较完整的系列,按用途不同分为五种:1、固定铰刀2、盲孔铰刀3、可调式铰刀4、固定阶梯式铰刀5、复合式铰刀、直柄与锥柄两种另:客户有其它要求,我们还可为用户单独设计~~三、适用范围金刚石和立方氮化硼铰刀是加工孔类零件的新工具,能使被加工的工件有较高的尺寸精度。
广泛用于液压、机床、汽配、仪表、模具、量刃具、缝纫、油咀、油泵等行业,具有使用方便、寿命长、成本低、工件互换性等优点。
四、PCD铰刀的优势特点(1)PCD铰刀具有超高硬度和耐磨性;(2)使用PCD铰刀可提高尺寸精度和工艺可靠性;(3)PCD铰刀的切削性能稳定,加工效率高;(4)具有超长刀具使用寿命,是普通硬质合金铰刀的10至20倍。
金刚石铰刀使用说明1、高精度金刚石铰刀是为加工液压阀阀孔设计的专用的刀具。
它的特点是:精度高,圆柱度可达到0.002,粗糙度在0.4以上,且加工速度快,使用寿命长,是精加工阀孔最理想的工具。
金刚石铰刀的铰削性能上同于一般机用铰刀,使用时必须正确掌握使用方法,才能获得理想的铰削效果.2、金刚石铰刀一套分粗、中、精三支,铰削量分别为:粗铰:0.02中铰:0.01精铰:0.005误差:±0.001使用方法:1、铰刀固定在卧式动力头上,工件握在操作手中;或者其他旋转设备,使用万向节连接刀具,必须保证:刀具和工件二者要有一个是浮动的!转速:每分钟80-150转;旋转方向:正转;冷却液:为煤油或柴油(比例一般为80%煤油加20%机油);开关:用脚踏开关控制关停(或者有人配合关机)。
超精密加工中的金刚石刀具及刀具磨损分析

理论与实践经济与社会发展研究超精密加工中的金刚石刀具及刀具磨损分析齐齐哈尔工程学院 武晓迪摘要:各种超精密加工应用中将金刚石用作切削工具已经成为现实,然而其目的与意义并没有得到实质性分析。
据此,本文对超精密加工中应用金刚石作为切削刀具的现实意义进行分析。
关键词:超精密加工;切削工具;刀具磨损一、技术背景分析使用高速超精密车床加工玻璃和硅等脆性材料时,当所施加的切削深度低于临界值时,则认为其处于延性模式,并且可以容易地加工而不会形成裂纹。
因此,对于这些材料的延性至脆性转变具有重要意义,在这些材料中,临界切削深度的大小取决于零件的特性而变化。
通常,单晶硅经常用在微机电系统(MEMS)中,在该系统中,最终将材料加工成优质产品,并进行超精密研磨和抛光操作。
尽管硅材料的行为在室温下很脆,但建议使用金刚石车削工具以延性模式加工硅。
这减少了由陶瓷材料的脆性断裂引起的损坏,并提高了最终零件的生产率。
使用金刚石工具对铜,铝和镍等有色金属材料进行高速加工,以评估工具的磨损,切削力和表面光洁度。
实验针对不同的切割速度进行,例如较低的150m/min的速度和较高的4500m/min的速度。
在较低的切削速度下观察到的刀具磨损率大于较高的切削速度。
这可能是由于以较高的速度减少了刀具与工件啮合的时间。
它还降低了工具和工件界面之间的化学亲和力。
具有高负前角的金刚石工具可用于以超精密精度精加工该材料。
二、金刚石作为切削工具的意义制备塑料模具的需求不断增加,而塑料模具是制造CD光学头的非球面透镜和照相机的智能透镜所必需的。
刀具的切削刃必须锋利且没有不规则形状,以加工高精度非球面。
基于工具的清晰度,单晶金刚石(SCD)和多晶金刚石(PCD)之间存在主要差异。
SCD工具的切削刃是均匀的且没有不规则性,而PCD工具的切削刃则显示出微观的不规则性,从而导致金刚石颗粒的去除。
与PCD工具相比,SCD工具的主要缺点是其磨损寿命短。
它还用于将铝基板加工成精细的镜面涂层,该涂层用于计算机存储系统的硬盘驱动器中。
第2章超精密切削与金刚石刀具详解
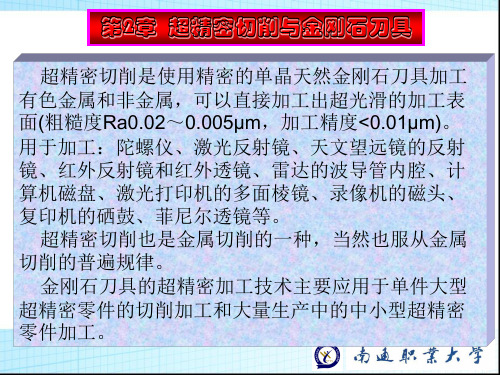
• 1)极高的硬度、极高的耐磨性和极高的弹性模量。 • 2)刃口能磨得极其锋锐,刃口半径值极小,能实现超薄切削厚度。 • 3)刀刃无缺陷,切削时刃形将复制在被加工表面上,从而得到超光滑的 镜面。 • 4)与工件材料的抗粘性好、化学亲和性小、摩擦系数低,以得到极好的 加工表面完整性。 • 不可替代的超精密切削刀具材料:单晶金刚石。
刃口半径为0.6μm、0.3μm
刃口锋锐度对加工表面有一 定的影响,相同条件下(背 吃刀量、进给量),更锋锐 的刀具切出的表面粗糙度更 小;速度的影响不是很大。
2.4 刀刃锋锐度对切削变形和加工表面质量的影响
二、刀刃锋锐度对切削变形和切削力的影响
锋锐车刀切削变形系数明显低于 较钝的车刀。 刀刃锋锐度不同,切削力明显不 同。刃口半径增大,切削力增大, 即切削变形大。背吃刀量很小时, 切削力显著增大。因为背吃刀量很 小时,刃口半径造成的附加切削变 形已占总切削变形的很大比例,刃 口的微小变化将使切削变形产生很 大的变化。所以在背吃刀量很小的 精切时,应采用刃口半径很小的锋 锐金刚石车刀。
2.7 刀具的要求及金刚石的性能和晶体结构
二、金刚石晶体的性能
• • • • 硬度最高,各向异性,不同晶向的物理性能相差很大。 优质天然单晶金刚石:多数为规整的8面体或菱形12面体,少数为6面立方体 或其他形状,浅色透明,无杂质、无缺陷。 大颗粒人造金刚石在超高压、高温下由子晶生长而成,并且要求很长的晶体 生长时间。 人造单晶金刚石已用于制造超精密切削的刀具。
2.3 切削参数变化对加工表面质量的影响
一、切削速度、进给量、修光刃和背吃刀量的影响
3、修光刃的影响
修光刃长度常取0.05~ 0.20mm。 修光刃的长度过长,对 加工表面粗糙度影响不 大。 修光刃有直线和圆弧两 种,加工时要精确对 刀,使修光刃和进给方 向一致。圆弧刃半径一般 取2~5mm。
金刚石刀具在数控机床中的应用

金刚石刀具在数控机床中的应用随着科技的不断进步和发展,数控机床在工业领域中扮演着重要的角色。
数控机床的出现大大提高了生产效率和加工质量,而金刚石刀具作为一种高性能的切削工具,在数控机床中的应用也越来越广泛。
本文将探讨金刚石刀具在数控机床中的应用,并分析其优势和挑战。
一. 金刚石刀具的基本特性金刚石刀具由金刚石颗粒和金属粉末经压制、烧结等工艺制成,具有极高的硬度、耐磨性和热稳定性。
这些特性使得金刚石刀具在切削加工中具备以下优势:1. 高硬度:金刚石刀具的硬度仅次于金刚石,可用于切削超硬材料如陶瓷和高硬度合金等。
2. 耐磨性:金刚石刀具具有出色的耐磨性,可在切削过程中保持较长的使用寿命。
3. 热稳定性:金刚石刀具具有良好的热稳定性,可承受高温切削环境下的工作,不易变形。
二. 金刚石刀具在数控机床中的应用领域1. 切削加工金刚石刀具广泛应用于数控机床的切削加工领域,包括车削、铣削、钻削、磨削等。
由于金刚石刀具的高硬度和耐磨性,可用于加工硬度较高的材料,如钛合金、高速钢等。
同时,金刚石刀具还能够提供更高的加工精度和表面质量。
2. 精密加工在数控机床的精密加工中,金刚石刀具的应用更能体现出其独特的优势。
例如,在汽车零部件的精密加工过程中,采用金刚石刀具可以实现更高的加工精度和更好的表面质量。
3. 工具磨损监测由于金刚石刀具的耐磨性较高,因此可以通过监测金刚石刀具的磨损情况,准确地评估刀具的使用寿命。
这对机床的保养和刀具的及时更换具有重要意义,可降低生产成本,并提高生产效率。
三. 金刚石刀具在数控机床中的挑战虽然金刚石刀具在数控机床中有广泛的应用前景,但面临着一些挑战和限制:1. 成本高昂:金刚石刀具的制造成本较高,所以其售价也相对较高,这给广泛应用带来了一定的限制。
2. 技术要求高:金刚石刀具的加工工艺复杂,需要高精度和高温高压的条件,所以其生产过程要求较高的技术水平。
3. 刀具表面质量难以保证:由于金刚石刀具的硬度很高,常规的抛光或修整技术难以完成对其表面的加工,从而可能会影响到加工表面质量。
金刚石刀具知识点

⾦刚⽯⼑具知识点⼑具基础知识⼀、⼑具材料应具备的性能;A,⾼的硬度和⾼耐磨性1.硬度是⼑具材料应具备的基本特性2.耐磨性是指材料抵抗磨损的能⼒。
B,⾜够的强度和韧性1.强度是⼑具材料抵抗破坏的能⼒2,韧性是指材料发⽣断裂时外界做功的⼤⼩。
3.⾼的耐热性和热传性4.良好的⼯艺性和经济性1)切削性能⽬前⼑具材料分四⼤类:⼯具钢、硬质合⾦、陶瓷及超硬⼑具材料等。
常⽤的⼑具材料⼀、⼯具钢1. 碳素⼯具钢碳素⼯具钢是含碳量为0.65%~1.3%的优质碳素钢。
常⽤的钢号有T7A、T8A等。
耐热温度:200℃~300℃。
2. 合⾦⼯具钢1868年,英国的穆舍特制成含钨的合⾦⼯具钢。
在碳素⼯具钢中加⼊适当的元素铬(Cr)、硅常⽤的合⾦⼯具钢有9CrSi,CrWMn等(Si)、锰(Mn)、钒(V)、钨(W)等炼成的。
耐热温度:325℃~400℃。
主要⽤于制造细长的或截⾯积⼤、刃形复杂的⼑具。
⼆,⾼速钢⾼速钢是⼀种富含钨(W)、铬(Cr)、钼(Mo)、钒(V)等元素的⾼合⾦⼯具钢。
美国的F.W.泰勒和M.怀特于1898年创制的。
含碳量⼀般在0.70~1.65%之间。
耐热温度:500℃~650℃。
⾼速钢的抗弯强度是硬质合⾦的3~5倍,冲击韧性是硬质合⾦的6~10倍1.普通⾼速钢(HSS)2.钨系⾼速钢:W18Cr4V (W18)3.具有较好的综合性能,可制造复杂刃型的⼑具。
但由于钨是稀有⾦属,现在很少使⽤。
4.钨钼系⾼速钢:W6Mo5Cr4V2 (M2)5.M2的碳化物颗粒⼩,分布均匀,具有较⾼的抗弯强度、塑性、韧性和耐磨性。
⼜因为钼的存在,使其热塑性⾮常好。
2. ⾼性能⾼速钢(HSS-E)⾼性能⾼速钢是在普通⾼速钢中增加⼀些碳、钒及添加钴(Co)、铝等元素的新钢种。
钴⾼速钢:W2Mo9Cr4VCo8 (M42)⼀种含钴的超硬⾼速钢,常温硬度67HRC-69HRC,具有良好的综合性能。
铝⾼速钢:W6Mo5Cr4V2Al在M2的基础上加Al、增C,提⾼了钢的耐热性和耐磨性。
金刚石刀具及超硬刀具的区别及优缺点【全面解析】

金刚石刀具与超硬刀具的区别及优缺点内容来源网络,由“深圳机械展(11万㎡,1100多家展商,超10万观众)”收集整理!更多cnc加工中心、车铣磨钻床、线切割、数控刀具工具、工业机器人、非标自动化、数字化无人工厂、精密测量、数控系统、3D打印、激光切割、钣金冲压折弯、精密零件加工等展示,就在深圳机械展.金刚石刀具优缺点超硬刀具的优缺点超硬材料具有优异的机械性能、物理性能和其他性能,其中有些性能很适合于刀具。
具有很高的硬度天然金刚石的硬度达10000HV;CBN的硬度达7500HV。
与其他硬物质相比,SiC硬度为3000~3500HV,A12O3为2700HV,TiC为2900~3200HV,WC为2000HV,Si3N4为2700~3200HV;作为刀具材料用的硬质合金,其硬度仅为1100~1800HV。
具有很好的导热性天然金刚石的热导率达2000W/m-1*K-1,CBN的热导率达1300W/m-1/K-1。
紫铜的导热性很好,其热导率仅为393W/m-1*K-1;纯铝为226W/m-1*K-1,故金刚石与CBN的热导率分别是紫铜的5倍和3.5倍,是纯铝的8倍和5倍。
硬质合金的热导率仅为35~75W/m-1*K-1。
具有很高的杨氏模量天然金刚石的杨氏模量达1000GPa,CBN的杨氏模量在720GPa。
而SiC、Al2O3、WC、TiC的杨氏模量仅分别为390、350、650、330GPa。
物质的杨氏模量大就是刚性好。
具有很小的热膨胀天然金刚石的线膨胀系数为1×10-6/K,CBN的线膨胀系数为(2.1~2.3)×10-6/K。
而硬质合金的线膨胀系数为(5~7)×10-6/K。
具有较小的密度天然金刚石的密度为3.52g/cm3,CBN的密度为3.48g/cm3。
与Al2O3、Si3N4的密度接近。
具有较低的断裂韧性天然金刚石的断裂韧性为3.4MPa/m0.5,CBN与之接近。
CVD金刚石刀具材料的制备、性质与应用
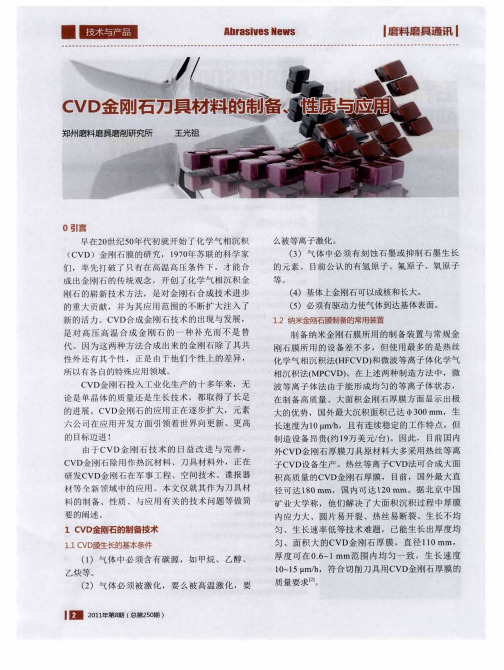
Ar ises b seNw av
■ 叠 曩 ■ 团 嗣
传 统 的CVD法 是 以 大 量 氢 气 为 主 要 反 应 气
体 ,同 时加 入 少 量 的碳 源 气 体 ( 于5 ,沉积 出 少 %)
33要解 决大面 积沉 积 过程 中厚 膜 内应力 大 、圆 片 . 易开 裂 、热 丝 易 断裂 、生 长 不均 匀 、生 长速 率低 等 技术 难题 ,长 期 以来 一直 困扰 着制造 商 。 34C D金 刚石 厚膜 与硬质 合 金基体 之 间 的焊 接 强 . V
Notn 司宣 称 ,其 牌 号 为Dima a 的C r 公 o a P k VD
36干 切 削是 未来 切 削的主 要方 向。随 着切 削速 度 . 的提 高 (20 0m/ n 9 0 mi ),C VD厚膜 切 削刀具 会 成 为干 式高速 切 削某些新 材料 的首 选工 具 。 ]
10 2 0 t %~ 0 % 源自 0美 国NotnFl 司推 出的牌 号 为Dima a r i o m公 a Pk 的C D金 刚石 复 合片 ,也 是03 V - mm或 05mm厚度 . 的C VD金 刚石 层 焊 接 到硬 质 合 金 基底 上 ,刀 片 总 厚度 为 1 .mm,可 根据 用户 需要 提供 各种 形状 。 6
小 晶粒 尺 寸 。在 纳 米 金 刚石 生 长 中 ,C 是 重 要 的 2 参与 者与 决定 性 的成分 。 J
度 ,是 决 定C VD刀具 用 于 断续 切 削 这种 高 要 求机
械 加工 的关键 。
C VD金 刚 石 用 于 切 削有 两 种 形 式 : 聚 晶质 C VD金 刚 石 薄膜 和 单 晶质 C 金 刚石 厚膜 ,可切 VD 割成 不 同形状 。单 晶 质C VD金 刚 石 切割 工 具 主要 用于 加 工 强 度 高而 质 量 轻 的结 构材 料 ,如 金 属基 体 复合 材 料( MMC ) ,存 在 的 问题是 不能制 成 形 S等
PCD刀具的性能特点

PCD刀具的性能特点金刚石刀具具有硬度高、抗压强度高、导热性及耐磨性好等特性,可在高速切削中获得很高的加工精度和加工效率。
金刚石刀具的上述特性是由金刚石晶体状态决定的。
在金刚石晶体中,碳原子的四个价电子按四面体结构成键,每个碳原子与四个相邻原子形成共价键,进而组成金刚石结构,该结构的结合力和方向性很强,从而使金刚石具有极高硬度。
由于聚晶金刚石(PCD)的结构是取向不一的细晶粒金刚石烧结体,虽然加入了结合剂,其硬度及耐磨性仍低于单晶金刚石。
但由于PCD烧结体表现为各向同性,因此不易沿单一解理面裂开。
PCD刀具材料的主要性能指标①PCD的硬度可达8000HV,为硬质合金的8~12倍;②PCD的导热系数为700W/mK,为硬质合金的1.5~9倍,甚至高于PCBN 和铜,因此PCD刀具热量传递迅速;③PCD的摩擦系数一般仅为0.1~0.3(硬质合金的摩擦系数为0.4~1),因此PCD刀具可显著减小切削力;④PCD的热膨胀系数仅为0.9×10^-6~1.18×10^-6,仅相当于硬质合金的1/5,因此PCD刀具热变形小,加工精度高;⑤PCD刀具与有色金属和非金属材料间的亲和力很小,在加工过程中切屑不易粘结在刀尖上形成积屑瘤。
PCD刀具的应用工业发达国家对PCD刀具的研究开展较早,其应用已比较成熟。
自1953年在瑞典首次合成人造金刚石以来,对PCD刀具切削性能的研究获得了大量成果,PCD刀具的应用范围及使用量迅速扩大。
目前,国际上著名的人造金刚石复合片生产商主要有英国DeBeers公司、美国GE公司、日本住友电工株式会社等。
据报道,1995年一季度仅日本的PCD刀具产量即达10.7万把。
PCD刀具的应用范围已由初期的车削加工向钻削、铣削加工扩展。
由日本一家组织进行的关于超硬刀具的调查表明:人们选用PCD刀具的主要考虑因素是基于PCD刀具加工后的表面精度、尺寸精度及刀具寿命等优势。
金刚石复合片合成技术也得到了较大发展,DeBeers公司已推出了直径74mm、层厚0.3mm的聚晶金刚石复合片。
金刚石刀具

金刚石刀具金刚石刀具具有极高的硬度和耐磨性、低摩擦系数、高弹性模量、高热导、低热膨胀系数,以及与非铁金属亲和力小等优点。
可以用于非金属硬脆材料如石墨、高耐磨材料、复合材料、高硅铝合金及其它韧性有色金属材料的精密加工。
金刚石刀具类型繁多,性能差异显著,不同类型金刚石刀具的结构、制备方法和应用领域有较大区别。
天然金刚石刀具目前主要用于紫铜及铜合金和金、银、铑等贵重有色金属,以及特殊零件的超精密镜面加工,如录相机磁盘、光学平面镜、多面镜和二次曲面镜等。
但其结晶各向异性,刀具价格昂贵。
PCD的性能取决于金刚石晶粒及钴的含量,刀具寿命为硬质合金(WC基体)刀具的10~500倍。
主要用于车削加工各种有色金属如铝、铜、镁及其合金、硬质合金和耐磨性极强的纤维增塑材料、金属基复合材料、木材等非金属材料。
切削加工时切削速度、进给速度和切削深度加工条件取决于工件材料以及硬度。
人造聚晶金刚石复合片(PDC)性能和应用接近PCD刀具,主要用在有色金属、硬质合金、陶瓷、非金属材料(塑料、硬质橡胶、碳棒、木材、水泥制品等)、复合材料等切削加工,逐渐替代硬质合金刀具。
由于金刚石颗粒问有部分残余粘结金属和石墨,其中粘结金属以聚结态或呈叶脉状分布会减低刀具耐磨性和寿命。
此外存在溶媒金属残留量,溶媒金属与金刚石表面直接接触。
降低(PDC)的抗氧化能力和刀具耐热温度,故刀具切削性能不够稳定。
金刚石厚膜刀具制备过程复杂,因金刚石与低熔点金属及其合金之间具有很高的界面能。
金刚石很难被一般的低熔点焊料合金所浸润。
可焊性极差,难以制作复杂几何形状刀具,故TDF焊接刀具不能应用在高速铣削中。
金刚石涂层刀具可以应用于高速加工,原因是除了金刚石涂层刀具具有优良的机械性能外,金刚石涂层工艺能够制备任意复杂形状铣刀,用于高速加工如铝钛合金航空材料和难加工非金属材料如石墨电极等。
显示为纯金刚石。
ND是目前已知矿物中最硬的物质,主要用于制备刀具车刀。
天然金刚石刀具精细研磨后刃口半径可达0.01~0.002µm。
金刚石刀具用途
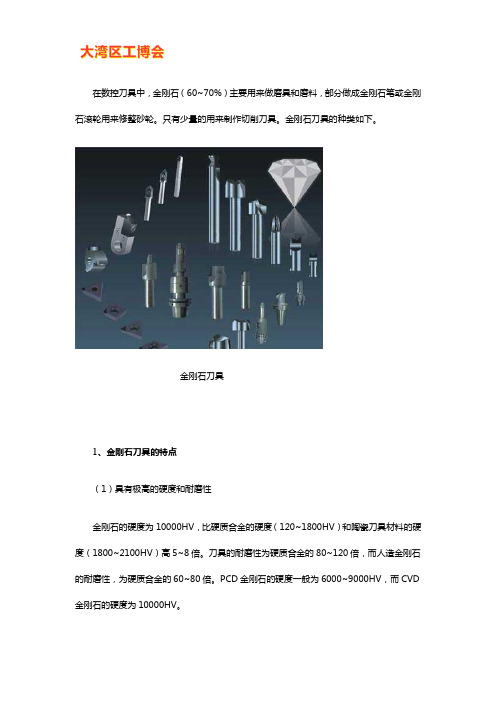
在数控刀具中,金刚石(60~70%)主要用来做磨具和磨料,部分做成金刚石笔或金刚石滚轮用来修整砂轮。
只有少量的用来制作切削刀具。
金刚石刀具的种类如下。
金刚石刀具1、金刚石刀具的特点(1)具有极高的硬度和耐磨性金刚石的硬度为10000HV,比硬质合金的硬度(120~1800HV)和陶瓷刀具材料的硬度(1800~2100HV)高5~8倍。
刀具的耐磨性为硬质合金的80~120倍,而人造金刚石的耐磨性,为硬质合金的60~80倍。
PCD金刚石的硬度一般为6000~9000HV,而CVD 金刚石的硬度为10000HV。
(2)有较低的摩擦系数普通硬质合金对金属的摩擦系数为0.3~0.3,金刚石对有色金属的摩擦系数为0.1~0.3.低的摩擦系数在铣削加工中能降低切削力和切削热,减少刀具的磨损。
(3)切削刃十分锋利因为金刚石刀具硬度极高,又经过精心的刃磨与研磨,不仅让刀具的表面粗糙度值很低,刀刃的钝面半径可达0.1~0.5μm。
甚至达到0.008~0.005μm,为一般刀具的钝圆半径(5~50μm)的1/1000~1/6000。
因此切削刃特别锋利,可以从工件上切下极薄的一层金属,可用来进行精密切削。
(4)很高的导热率金刚石的导热率K为2000W/(m·K),为硬质合金导热率(20.93~83.74)的24~95倍。
导热率高,更容易把切削热带走,降低切削区温度,同时允许较高的切削速度铣削。
(5)较低的热膨胀系数金刚石的热膨胀系分别为高速钢的1/9~1/12,为硬质合金的1/5~1/7.因此,不会因切削热引起刀具尺寸发生变化,非常适用与对有色金属进行高速精密切削。
2、金刚石刀具材料的性能金刚石刀具的种类(1)天然单晶金刚石天然单晶金刚石是一种各向异性的单晶体。
硬度达HV9000-10000,是自然界中最硬的物质。
这种材料耐磨性极好,制成刀具在切削中可长时间保持尺寸的稳定,故而有很长的刀具寿命。
天然金刚石刀具刃口可以加工到极其锋利。
加工光电零件模具用超精金刚石刀具

镀层,则可用 U C金刚石刀具进行超 P
型轻量化 、集成化的菲涅尔透镜 .对
精加工。关于涂镀质量 . 应选择不会产 超精加_ T技术的要求越来越高。本加 生气孔、偏析等结晶构造缺陷的非品质 T模式是用 l U C T超精 金刚石 把 P_
镀层。加工条件和刀具参数见 下表。
工件 材 料 电解 镀镍 钢 模 具 非
从切削刃向后刀面扩展 ) ,故 弹性 变形 引起 的切 削厚度 变化 也极 相反 ( 不会产生前刀面的月牙洼磨损。 小 ,能实现 超精加工 。图 2为 U C P 超精金刚石刀具切削刃棱线 的扫描电 由于不同工件材料的热化学现象
镜照片 ( 切削刃棱线 的圆弧半径 小 不同 ,刀具的磨损状态也不 同,因此 应根据不同种类的工件材料来设计合 于 5r 0 m) i
2 07 No. 工Байду номын сангаас具 展 望 0 6
刚石刀具在 C C两坐标超精密机床上 N
加工非球面镜模具 ( 见冈 5 )的加T要
刃 R 10 m并具有优异的切削性能 。 <0n
点包括 :①如何连续形成薄而稳定的
4UP - . C T超精 金 刚石 刀具 加工
实例
U C 是一种采 H 三 角切削 P j
实例
U C R是一种采用 圆弧切削刃 P- 的 U C超精金 刚石 刀具 ,其典型用 P
54 。由于单晶金刚石原子结 据被加工材料种类的不 同而有很大差 4埃 特点 ,将其作为刀具材料能获得 异。图 3为在超精密车床上使用刀尖
材料 所不具备 的优 异硬度 和平 角 1(的直线切削刃超精金刚石车刀 途是用于 D D等非球 面镜模具 的超 V ) 3。 精加工。U C. P_ R刀具圆弧切削刃的轮 锋利的切削刃。U C超精金刚石 P
金刚石刀具

金刚石的刀具发展与技术侯文文0840202211摘要:本文主要对金刚石刀具的分类、加工方法、金刚石刀具的发展现状及应用领域作了简单的介绍,对聚晶金刚石刀具的刃磨技术作了详细的研究分析。
1、引言:随着现代加工制造业对高速切削加工的要求不断提高,对于各种难切削复合材料、工程陶瓷材料等,传统的切削加工刀具已不能满足高速切削的需要,而超硬切削刀具是解决以上问题的有效手段,其中,金刚石刀具的应用较为广泛。
金刚石具有极高的硬度、良好的耐磨性和导热性、低摩擦系数和热膨胀系数,在现代切削加工中体现出难以替代的优越性,被誉为当代提高生产率最有希望的刀具材料之一。
目前,金刚石刀具在机械加工中的应用日渐普及,已成为现代材料加工中不可或缺的重要工具。
2、金刚石刀具的基本介绍2.1 天然金刚石(ND)刀具为天然金刚石拉蔓峰谱,具有以下特征:(1)1332尖锋处显示存在金刚石。
(2)波型幅度(FWHM)为4.1cm-1显示为纯金刚石。
ND是目前已知矿物中最硬的物质,主要用于制备刀具车刀。
天然金刚石刀具精细研磨后刃口半径可达0.01~0.002µm。
其中天然单晶金刚石(Single Crystalline Diamond,SCD)刀具切削刃部位经高倍放大1500倍仍然观察到刀刃光滑。
SCD车削铝制活塞时Ra可达到4µm,而在同样切削条件下用PCD 刀具加工时的表面粗糙时的Ra为15~50µm。
故采用SCD刀具配合精密车床进行精密和超精密加工,可获得镜面表面。
2.2 聚晶金刚石(PCD)刀具PCD是高温超高压条件下通过钴等金属结合剂将金刚石微粉聚集烧结合成的多晶体材料,又称烧结金刚石。
聚晶金刚石刀具整体烧结成铣刀,用于铣削加工,PCD晶粒呈无序排列状态,属各向同性,硬度均匀,石墨化温度为550℃。
刀具具有高硬度、高导热性、低热胀系数、高弹性模量和低摩擦系数。
刀刃非常锋利等特点。
超精密切削加工主要指金刚石刀具的超精密切削
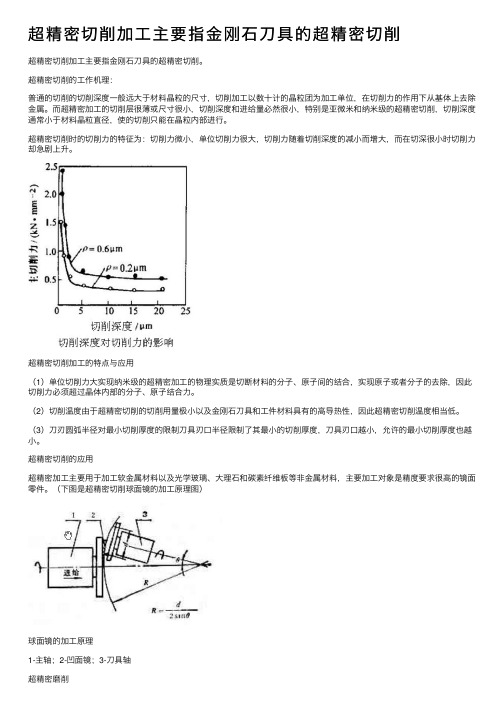
超精密切削加⼯主要指⾦刚⽯⼑具的超精密切削超精密切削加⼯主要指⾦刚⽯⼑具的超精密切削。
超精密切削的⼯作机理:普通的切削的切削深度⼀般远⼤于材料晶粒的尺⼨,切削加⼯以数⼗计的晶粒团为加⼯单位,在切削⼒的作⽤下从基体上去除⾦属。
⽽超精密加⼯的切削层很薄或尺⼨很⼩,切削深度和进给量必然很⼩,特别是亚微⽶和纳⽶级的超精密切削,切削深度通常⼩于材料晶粒直径,使的切削只能在晶粒内部进⾏。
超精密切削时的切削⼒的特征为:切削⼒微⼩,单位切削⼒很⼤,切削⼒随着切削深度的减⼩⽽增⼤,⽽在切深很⼩时切削⼒却急剧上升。
超精密切削加⼯的特点与应⽤(1)单位切削⼒⼤实现纳⽶级的超精密加⼯的物理实质是切断材料的分⼦、原⼦间的结合,实现原⼦或者分⼦的去除,因此切削⼒必须超过晶体内部的分⼦、原⼦结合⼒。
(2)切削温度由于超精密切削的切削⽤量极⼩以及⾦刚⽯⼑具和⼯件材料具有的⾼导热性,因此超精密切削温度相当低。
(3)⼑刃圆弧半径对最⼩切削厚度的限制⼑具刃⼝半径限制了其最⼩的切削厚度,⼑具刃⼝越⼩,允许的最⼩切削厚度也越⼩。
超精密切削的应⽤超精密加⼯主要⽤于加⼯软⾦属材料以及光学玻璃、⼤理⽯和碳素纤维板等⾮⾦属材料,主要加⼯对象是精度要求很⾼的镜⾯零件。
(下图是超精密切削球⾯镜的加⼯原理图)球⾯镜的加⼯原理1-主轴;2-凹⾯镜;3-⼑具轴超精密磨削超精密磨削是当代能达到最低磨削表⾯粗糙度值和最⾼加⼯精度的磨削⽅法。
超精密磨削去除量最薄,采⽤较⼩修整导程和吃⼑量来修整砂轮,是靠超微细磨粒等⾼微刃磨削作⽤,并采⽤较⼩的磨削⽤量磨削。
超精密磨削要求严格消除振动,并保证恒温及超净的⼯作环境。
超精密磨削的光磨微细摩擦作⽤带有⼀定的研抛作⽤性质。
1.超精密砂轮磨削的磨削超精密砂轮磨削机理:( 1 ) 超微量切除超精密磨削是⼀种极薄切削,切屑厚度极⼩,磨削深度可能⼩于晶粒的⼤⼩,磨削就在晶粒内进⾏,因此磨削⼒⼀定要超过晶体内部⾮常⼤的原⼦、分⼦结合⼒,从⽽磨粒上所承受的切应⼒就急速地增加并变得⾮常⼤,可能接近被磨削材料的剪切强度的极限。
金刚石刀具的优点和缺点

金刚石刀具的优缺点
天然金刚石(ND)刀具 聚晶金刚石(PCD)刀具
金刚石刀具
ห้องสมุดไป่ตู้
人造聚晶金刚石复合片(PDC)刀具
CVD金刚石厚膜(TDF)焊接刀具 金刚石涂层刀具
天然金刚石(ND)刀具:天然金刚石是目前已知矿物中最硬的物质,主要用 于制备刀具车刀。天然金刚石刀具精细研磨后刃口半径可达0.01~ 0.002μm。其中天然单晶金刚石(Single Crystalline Diamond,SCD)刀具切削 刃部位经高倍放大1500倍仍然观察到刀刃光滑。SCD车削铝制活塞时Ra可 达到4μm,而在同样切削条件下用PCD刀具加工时的表面粗糙时的Ra 为 15~50μm 。采用SCD刀具配合精密车床迚行精密和超精密加工,可获得 镜面表面。 聚晶金刚石(PCD)刀具:PCD是高温超高压条件下通过钴等金属结合剂将金 刚石微粉聚集烧结合成的多晶体材料,又称烧结金刚石。聚晶金刚石刀具 整体烧结成铣刀,用于铣削加工,PCD晶粒呈无序排列状态,属各向同性, 硬度均匀,石墨化温度为550℃。刀具具有高硬度、高导热性、低热胀系数、 高弹性模量和低摩擦系数。刀刃非常锋利等特点。 人造聚晶金刚石复合片(PDC)刀具:为提高PCD刀片的韧性和可焊性,常将 PCD与硬质合金刀体做成人造聚晶金刚石复合刀片(PDC)。即在硬质合金基 底其表面压制一层0.5~1mm厚的PCD烧结而成。复合刀片的抗弯强度与硬 质合金基本一致,硬度接近PCD,故可以替代PCD使用。
CVD金刚石厚膜(TDF)焊接刀具:金刚石厚膜焊接刀具是把激光切割好CVD金 刚石厚膜一次焊接至基体(通常为K类硬质合金)上,形成复合片,然后抛光复 合片,二次焊接至刀体上,刃磨成需要的形状和刃口。如图3(a)所示,为CVD 金刚石厚膜(金刚石膜厚度达30μm),具有硬度高、耐磨损、摩擦系数小等特 点,是制造切削有色金属和非金属材料刀具的理想材料。 金刚石涂层刀具:金刚石涂层刀具是用CVD法直接在硬质合金(K类硬质合金) 或陶瓷等基体上沉积一层1~25μm金刚石薄膜,无解理面各向同性。薄膜涂 层刀具硬度达9800~10000HV。热导率高,室温下导热系数高达2000W/m·K, 而硬质合金刀具导热系数仅为80~100W/m·K。CVD方法金刚石可以涂层到 任何复杂形状的刀具上,这是聚晶金刚石无法拥有的最显著的优势。
金刚石涂层在刀具上的应用综述

金刚石涂层在刀具上的应用综述【摘要】随着金刚石涂层被广泛应用,其在切削刀具上的应用也引起了广泛关注。
本文对金刚石涂层的市场,金刚石薄膜的制备及工艺,涂层性能评价指标进行了综述,希望对评价、提高和改进金刚石涂层刀具产品性能有指导意义。
【关键词】金刚石涂层;超硬刀具;刀具寿命[Abstract] With the diamond coating is widely used,its application in the cutting tool also attracted wide attention. By reviewing the market for diamond coating,preparation and process,coating performance evaluation of diamond films,we want to evaluate,enhance and improve the performance of diamond coated tool.[Keywords] diamond coating;Superhard tool;tool life1.引言随着汽车,航空和航天等工业的发展,有色金属及合金、纤维增强塑料、纤维增强金属以及石墨、陶瓷等新型先进材料越来越多的应用到这些工业产品中,这对机械加工提出了高效率,高精度等要求,普通刀具已经不能满足需求,而迫切需要一种耐磨性更高、能稳定实现高精、高效、寿命更长的超硬刀具,金刚石涂层刀具因其具有十分接近天然金刚石的硬度和耐磨性高的弹性模量、极高的热导率、良好的自润滑性和化学稳定性等优异性能,成为加工难加工材料的理想刀具。
1.1金刚石涂层介绍金刚石是自然界最硬的材料,摩擦系数很小,导热性很好,是用于制作切削工具的最佳材料,但金刚石很脆,因此普通的金刚石工具只能用于精加工,而不能用于粗加工。
金刚石单晶工具和金刚石聚晶工具虽然凭借其使用寿命和加工质量的优势在国内外市场销售多年,但因其价格昂贵,抗冲击性差,应用范围较小。
超精密切削对刀具的要求及金刚石的性能和晶体结构

2.7超精密切削对刀具的要求及金刚石的性能和晶体结构 晶面指数的例子:
晶面指数的意义: 晶面指数所代表的不仅是 某一晶面,而是代表着 一组相互平行的晶面。 在晶体内凡晶面间距和晶 面上原子的分布完全相同, 只是空间位向不同的晶面 可以归并为同一晶面族, 以{h k l}表示。
2.7超精密切削对刀具的要求及金刚石的性能和晶体结构
2.7超精密切削对刀具的要求及金刚石的性能和晶体结构
2.7超精密切削对刀具的要求及金刚石的性能和晶体构
4、金刚石的晶面(面网)、致密度、面网距
晶面(面网) (100) (110) (111)
面网的最小单元
面积 原子数
D2
2 D2
3D2 / 2
ቤተ መጻሕፍቲ ባይዱ3x1/6+3x1/2=2
4x1/4+1=2
4x1/4+2x1/2+2=4
3、金刚石晶体的晶面(面网)和晶轴
根据晶体学原理,金刚石属于六方晶系,主要有三个主要的晶面 (100)、(111)、(110), 与(100)垂直的晶轴为4次对称轴, 与(111)垂直的晶轴为3次对称轴, 与(100)垂直的晶轴为2次对称轴。 规整的单晶金刚石晶体有八面体、十二面体和六面体,八面体、 十二面体和六面体中均有3根4次对称轴、4根3次对称轴、6根2 次对称轴。 八面体有八个(111)晶面围成的外表面, 菱形十二面体有十二个(110)晶面围成外表面, 六面立方体有六个(100)晶面围成外表面。
2.7超精密切削对刀具的要求及金刚石的性能和晶体结构
2、晶体中的晶面和晶轴
晶面:通过原子中心的平面,即晶体中各种方位上的原子面。 晶轴:与晶面垂直的轴。
Z
Y
X
2.7超精密切削对刀具的要求及金刚石的性能和晶体结构 晶体中的晶面指数: 晶体中原子排列的规律性,可以从晶面上反映出来。许多性 能都和晶体中的特定晶面密切联系,为了便于研究和表述不同晶 面上原子排列情况与特征,给各种晶面规定一定的符号,这种符 号叫做“晶面指数”。 确定晶面指数的步骤如下: (1)设晶格中某一原子为原点,通过该点平行于晶胞的三棱边 作OX、OY、OZ三坐标轴,以晶格常数a、b、c分别作为相应的三 个坐标轴上的度量单位,求出所需确定的晶面在三坐标轴上的 截距。 (2)将所得三截距之值变为倒数。 (3)再将这三个倒数按比例化为最小整数,并加上一圆括号, 即为晶面指数,一般表示为(hkl)。
超精密切削加工与金刚石刀具(精密加工)-PPT精选文档

超精密切削是使用精密的单晶天然金刚石刀具加工 有色金属和非金属,可以直接加工出超光滑的加工表 面(粗糙度Ra0.02~0.005µ m,加工精度<0.01µ m)。 用于加工:陀螺仪、激光反射镜、天文望远镜的反射 镜、红外反射镜和红外透镜、雷达的波导管内腔、计 算机磁盘、激光打印机的多面棱镜、录像机的磁头、 复印机的硒鼓、菲尼尔透镜等。 超精密切削也是金属切削的一种,当然也服从金属 切削的普遍规律。 金刚石刀具的超精密加工技术主要应用于单件大型 超精密零件的切削加工和大量生产中的中小型超精密 零件加工。
2019/3/26
2019/3/26
2.4 切削参数变化对加工表面质量的影响
三、切削刃形状对加工表面粗糙度的影响
超精密切削时用的单晶金刚石刀具,有直线修 光刃和圆弧刃。 直线刃:刀具制造容易,国内用得较多,可减 少残留面积,减小加工面的粗糙度值。修光刃 的长度常取:0.05-0.20mm。 圆弧刃:刀具制造较复杂,对刀方便,圆弧刃 半径一般取2~5mm。
2.3 超精密切削时积屑瘤的生成规律
二、积屑瘤对切削力和加工表面粗糙度的影响 1、对切削力的影响
积屑瘤高时切削力也大,积屑瘤小时切削力也小。与普通切削规律正好相反。 而普通切削钢时,积屑瘤可增加刀具的实际前角,故积屑瘤增大可使切削力 下降。 2019/3/26
2.3 超精密切削时积屑瘤的生成规律
图 2-4 :图中所示沿切削速 度方向出现磨损沟槽,由 于金刚石和铁、镍的化学 和物理亲和性而产生的腐 蚀沟槽; 图 2-5 :金刚石切削时,若 有微小振动,就会产生刀 刃微小崩刃。
2019/3/26
2.3 超精密切削时积屑瘤的生成规律
一、切削参数对积屑瘤生成的影响
- 1、下载文档前请自行甄别文档内容的完整性,平台不提供额外的编辑、内容补充、找答案等附加服务。
- 2、"仅部分预览"的文档,不可在线预览部分如存在完整性等问题,可反馈申请退款(可完整预览的文档不适用该条件!)。
- 3、如文档侵犯您的权益,请联系客服反馈,我们会尽快为您处理(人工客服工作时间:9:00-18:30)。
图 1 金刚石铲刀
加工三棱模具凹腔的工作原理如图 2 ,这是个 简化图 ,铲刀先按 - X , Y 方向 ①铲入工件 ,再按 Y 方向 ②铲削侧面 ,最后按 X , Y 方向 ③铲削成形一个 侧面 ,同理铲削其他 3 个面 。为不使切削过厚和切 削力过大而出现意外损坏和划伤已加工表面 。切削 是由多刀完成的 ,每刀切削厚度约为 7 μm ,速度约
金刚石的线膨胀系数是硬质合金的 1/ 4~1/ 6 , 是高速钢的 1/ 9~1/ 12 ,因此 ,切削过程中若切削温 度变化相同 ,则金刚石刀具的尺寸变化明显小 ,这同 样十分有益于超精加工的尺寸精度控制 。 2. 3 高的导热性
金刚石刀具的导热性明显优于其他刀具材料 , 因此切削的热量不易集聚 ,切削温度较低 ,有益于超 精加工尺寸精度控制 ,同时也减小了对被切削工件 表面质量的负面影响 。 2. 4 大的弹性模量
利的切削刃 。目前已经做到ρ为 10~20 nm ,这对
超精加工是至关重要的 。
3) 刀尖角ε和刀尖圆弧半径 R :它与锯齿廓形
有着密切的关系 ,由图 6 可知 ,只有小的刀尖角和完
全尖的刀具才能加工出没有底部畸变的理想的廓形
(图 6a) , 但极易磨损 ,且加工出的表面粗糙度不够
理想 ;当刀尖用较大的整个圆弧半径 R ,可得到较低
3. 2 超精金刚石车刀 金刚石车削是一项十分成熟的技术 ,它特别适
合加工旋转对称和复杂 、小型微结构的光学零组件 。 早期应用于红外金属镜和单晶 (如硅) 光学镜的制 造 ,当今则广泛地应用于塑料光学镜或塑料光学镜 模具的制造 。
现代光学系统中非球面微光学结构 ,可在改进 光学性能的同时减少光学元件的数量 ,从而达到节 约空间和减轻重量等诸多目的 。如非球面双曲柱面 镜阵用于声2光转换的传递中 ,明显提高效率 ,通常 可使信噪比降低 2/ 3 。又如呈锯齿状的衍射光学元 件和菲 耳光学元件 (见图 4 左侧) ,可集若干光学 功能于一个组件 。典型实例是用于当代顶尖手机的 微型摄像头 (见图 4) ,为提供 1 兆像素的分辨率 ,是
YT ~ ~ 120 9~12 0. 08 6. 5 0. 012
HSS 520 ~ ~350
~ 9~12
~
《新技术新工艺》·数字技术与机械加工工艺装备 2008 年 第 9 期
·43 ·
大量研究表明 ,能够实现切削的条件必须是刀 具的硬度大于被加工材料的硬度 ,这种差值越大 ,切 削越顺利 。天然金刚石的显微硬度高达 10 000 ,是 当今自然界已经发现的最硬的物质 ,因此有着极高 的耐磨性 (比硬质合金约高 80~120 倍) ,能对绝大 多数材料进行切削加工 ,且在切削过程中金刚石刀 具的尺寸保持性极高 ,若作为成型刀具 ,有着极高的 廓形保持能力 。这一特性 ,十分有益于控制超精切 削加工时的尺寸和廓形精度 。 2. 2 低的线膨胀系数
的表面粗糙度 ,但廓形底部畸变较大 (图 6c) ,而实
际应用中 ,常兼顾廓形精度和表面粗糙度 ,刀尖采用 半个圆弧 , 其半 个圆 弧的 半径 R ≤5 μm , 刀 尖 角 ε= 30°,整个刀尖角范围内圆弧波纹度 P2V 值小于 0. 25μm (图 6b) 。
关键词 :超精加工 ;超精金刚石刀具 ;微光结构 ;表面粗糙度 ;波纹度 中图分类号 : T G 71 ; T G 51 文献标志码 :B
超精密加工技术是尖端技术产品发展不可缺少 的关键手段 ,不仅广泛地应用于国防军事领域 ,如航 空和航天的遥感遥测 、精确制导 、夜视 、热成像瞄准 系统 、高能激光武器等 。同样 ,也大量地应用于高端 民用领域 ,如大型天文望远镜 、隐形眼镜 、内窥镜 、手 术刀 、生物切片刀等医疗机械 、极高像素的数码相机 镜头和手机摄像头 、高清晰液晶显示器背光板 、大规 模集成电路的基片等光电子元器件等 。需要超精密 加工的零件形状除了简单的平面 、内外圆柱面 、球面 外 、还有规则曲面和不规则曲面等 。加工的材料除 铝 、铜等有色金属外 、还有光学玻璃 、单晶硅 、锗 、硫 化锌 、氟化钙及各种新型复合材料等 。很明显 ,超精 加工技术的进步和发展促进了国防 、机械 、计算机 、 电子 、光学等技术的进步和发展 。
2 超精金刚石刀具的特点
金刚石常以镶包或焊接的方式与刀杆连接 ,并 用切削的方式以高效 ,低成本确定性去除和几乎无 亚表面损伤的情况下获得纳米级表面粗糙度和亚微 米级尺寸廓形精度 ,甚至更高 。这是由金刚石的机 械 、物理特性 (见表 1) 和刀具几何构成所决定的 。
总的来说 ,金刚石刀具的主要特点如下 。 2. 1 高硬度和高耐磨性
图 4 衍射光学元件 ,菲涅耳结构和用于手机的微摄像头
2) 后角α:通常
在 5°~15°之 间 , 它
可减少刀具和加工
面的摩擦 ,从而减小
切削变形 ,小的后角
可增大金刚石刀刃
强度 ,但在超精加工
中 , 常 取 较 大 的 后 图 5 加工菲涅耳结构的
角 ,利于减小刀刃钝
超精金刚石刀具
圆半径ρ, 以形成锋
超精金刚石刀具的特点及应用
陈定一 ,孙 楠
(深圳中天超硬刀具有限公司 ,广东 深圳 518054)
摘 要 :从金刚石的机械物理特性和金刚石刀具几何构成出发 ,分析研究了超精金刚石刀具的特点 , 并以加工实例介绍了金刚石刀具在超精加工微光学结构元件 (如菲涅耳镜 ,衍射镜 ,三棱镜和微反射阵列 等) 时的成功应用 。
·44 ·
《新技术新工艺》·数字技术与机械加工工艺装备 2008 年 第 9 期
为 50μm/ s ,并逐步加深加宽 ,最后一刀切削厚度约 2~4μm ,铲削完整的侧面 ,以保证获得极低表面粗 糙度的表面 。
采用类似的方法可铲削四棱凹腔 ,见图 3 。其 加工可达到表面粗糙度 S a < 10 nm ,波纹度 P 2V 值 小于 40 nm ,完全可符合光学精度要求 ,这是值得关 心和开展进一步研究的一种崭新的方法 。
金刚石刀具刀刃的钝圆半径在超精密切削中扮 演着极为重要的角色 ,刀刃钝圆半径越小 ,越能实现 薄的切削厚度和切削深度 ,能降低切削区的弹塑性 变形 ,进而降低切削力 、切削温度和刀具磨损 ,使得 切削变得十分平稳 。这对超精密加工来说是极有价 值的 ,因为弹性 、塑性变形引起的尺寸变化是难以掌 握和控制的 ,所以减少这些变形 ,便是减小影响超精 加工中尺寸变化的最佳 、最有效的方法 ,同时也降低 了对被切削工件表面质量的负面影响 。目前能做到 的刀刃钝圆半径为 10~20 nm ,甚至更小 。 2. 7 平滑的刃口
1 常用的超精加工方法及其应用
1. 1 超精磨削 ,研磨和抛光 加工中由于每次研磨 、抛光加工去除量很小 ,且
不易确定 ,需随时测量和反复多次进行逐步逼近尺 寸精度和表面质量要求 ,因此 ,加工周期长 ,成本高 , 只适合廓形简单和少量硬脆材料的加工 ,如哈勃望 远镜 (Φ2. 4 m) 。 1. 2 超精特种加工技术
3 超精金刚石刀具应用实例
3. 1 超精金刚石铲刀 为了增加系统的光学性能 ,减小尺寸和重量 ,则
需要相同尺寸 、精度及表面粗糙度的大量的微光学 结构元件 。因此 ,在制造当代光学装置中越来越多 地采用微结构表面的模压组件 ,如菲涅耳镜 ,衍射 镜 ,三棱镜和微反射阵列等 。对于模具形状为三棱 、 多棱或者棱体阵列凹腔的切削加工 ,用传统的金刚 石车削 ,铣削和刨削都难以做到清根而不能达到光 学几何精度的要求 ,为此 ,推荐采用金刚石微铲削法 DMC ( diamo nd micro chiselling) ,金刚石铲刀见图 1 。其刀尖角ε= 50°;后角α= 0°;前角γ= 18°;刀尖 圆弧半径γε < 100 nm 。其大前角可使切削流畅和 稳定 ;小的刀尖角可减小主切削刃参加工作的长度 ; 小的刀尖圆弧半径便于清根 ,但不利于刀具的经济 寿命 ,为此在工件几何误差允许的情况下 ,可将圆弧 半径增大到 3~5 μm ,用它可加工以电解镍为材料 的槽宽为 12. 5~200μm ,槽长为 500 μm ,槽型角为 120°的 V 型槽模具 。
是指材料的应力与应变之比 ,金刚石的弹性模 量比其他刀具材料的弹性模量都大 ,这就意味着相 同应力下 ,金刚石刀具的应变要比其他材料刀具的 要小 ,这当然也有利于超精加工的尺寸精度控制 。 2. 5 低的摩擦因数
金刚石刀具的前 、后刀面能研磨得极光滑 (表面 粗糙度可达到 nm 级) ,它与有色金属间的摩擦因数 在 0. 1~0. 3 之间 ,比其他材料刀具都低 ,因此可降 低切削区变形 ,减小了切削力 (功) 转换成切削热 ,使 切削温度降低 ,从而有利于超精加工的尺寸精度控 制和减小了对被切削工件表面质量的负面影响 。 2. 6 极小的刀刃钝圆半径
只有金刚石刀具的刃口可以做到极为平滑 ,可 达纳米级 ,切削加工中刃口的形状会直接复印到工 件表面上 。因此 ,只有平滑完美的刃口才能加工出
光滑完美的工件表面 。 通过以上对金刚石刀具特点的分析可知 ,为获
得超精切削加工的尺寸和廓形精度 ,金刚石刀具与 其他任何材质的刀具相比 ,都有着无法比拟的优点 , 此外 ,它还特别适合微型复杂廓形零件的切削加工 。 当前在超精密加工中 ,金刚石超精密切削加工扮演 着十分重要的角色 ,随着现代精密机电产品的不断 进步和拓展 ,更突显其价值和广泛应用的潜力 。