金刚石刀具与超硬刀具的区别及优缺点【全面解析】
车削刀具材料

车削刀具材料车削是一种常见的金属加工方法,而车削刀具作为车削过程中的关键工具,其材料选择对于加工效率和加工质量具有重要影响。
下面将介绍几种常见的车削刀具材料,以及它们的特点和适用范围。
1.高速钢。
高速钢是一种常见的车削刀具材料,具有良好的硬度和耐磨性。
它适用于一般的车削加工,能够满足对加工精度和表面质量的要求。
此外,高速钢的加工稳定性较好,使用寿命较长,因此被广泛应用于车削刀具的制造中。
2.硬质合金。
硬质合金是一种硬度极高的车削刀具材料,主要由钨钴粉末和其他金属粉末经过高温烧结而成。
硬质合金具有极好的耐磨性和热稳定性,适用于对切削负荷和温度要求较高的车削加工。
由于其硬度极高,硬质合金刀具能够在高速切削中保持较好的刀具稳定性,因此在高速车削加工中得到广泛应用。
3.陶瓷刀具。
陶瓷刀具是近年来新兴的车削刀具材料,具有极高的硬度和耐磨性,能够适应高速切削和高温切削的要求。
此外,陶瓷刀具还具有良好的化学稳定性和热稳定性,能够在特殊材料的车削加工中表现出色。
然而,由于其脆性较大,陶瓷刀具在加工过程中需要注意避免冲击和振动,以免造成刀具的损坏。
4.金刚石刀具。
金刚石刀具是一种硬度极高的车削刀具材料,具有优异的耐磨性和热导性,能够适应高速切削和高温切削的要求。
金刚石刀具在加工硬质材料和非金属材料时表现出色,能够保持较好的加工质量和加工效率。
然而,金刚石刀具的制造成本较高,且在加工过程中需要严格控制切削条件,以免造成刀具的损坏。
综上所述,车削刀具的材料选择应根据具体的加工要求和加工材料来确定,不同的材料具有不同的特点和适用范围。
在实际的车削加工中,需要综合考虑刀具的材料、刀具的几何形状、切削条件等因素,以选择最合适的车削刀具,从而实现高效、高质的加工目标。
总结刀具材料

总结刀具材料刀具材料是制造刀具的重要组成部分,直接影响到刀具的性能和使用寿命。
随着技术的进步和需求的变化,刀具材料的种类和性能也在不断发展和更新。
本文将对常见的刀具材料进行总结和分析。
1. 高速钢(HSS)高速钢是一种常用的刀具材料,具有出色的耐磨性和耐热性能。
这种材料具有较高的硬度和强度,因此在高速切削和重负荷切削中表现出色。
此外,高速钢还具有良好的刃口硬化性能,能够有效抵抗刀口的变钝,从而延长刀具的使用寿命。
不过,高速钢的耐冲击性和韧性相对较差,对于一些对刀具的强度和韧性要求较高的场合,可能不太适用。
2. 硬质合金(WC-Co)硬质合金是一种由金属钨碳化物(WC)和钴(Co)组成的复合材料,具有极高的硬度和耐磨性。
这种材料常常用于制造切削刀具,特别是用于加工硬质材料和高温合金。
由于其硬度高,硬质合金的刀具能够承受较大的切削力,同时保持刀具的形状稳定。
然而,硬质合金的韧性较低,容易受到冲击而破裂,因此在使用时需要注意避免过大的冲击加载。
3. 陶瓷刀具陶瓷刀具的优点在于其极高的硬度和化学稳定性。
陶瓷刀具具有出色的耐磨性能,在高速切削和加工硬质材料时表现出色。
与金属刀具相比,陶瓷刀具的热膨胀系数较低,因此在高温环境下韧性和稳定性更好。
此外,陶瓷刀具的高温传导性能优异,能够有效降低切削温度,减少刀具的磨损。
然而,陶瓷刀具的缺点在于其脆性较高,容易受到冲击而破裂,因此在使用过程中需要特别小心。
另外,陶瓷刀具制造技术相对较为复杂,生产成本也较高。
4. 超硬刀具超硬刀具是一种以人造金刚石(PCD)和金刚石薄膜涂覆等超硬材料为基础的刀具。
这种刀具硬度极高,能够承受较大的切削力和高速切削。
超硬刀具的耐磨性和耐腐蚀性都非常出色,在加工难加工材料和高温环境下表现优秀。
另外,一些超硬刀具还具有良好的导热性能,能够有效降低切削温度,减少刀具磨损。
然而,超硬刀具价格较高,制造难度也较大,限制了其在一些应用领域的推广和应用。
金刚石刀具在数控机床中的应用

金刚石刀具在数控机床中的应用随着科技的不断进步和发展,数控机床在工业领域中扮演着重要的角色。
数控机床的出现大大提高了生产效率和加工质量,而金刚石刀具作为一种高性能的切削工具,在数控机床中的应用也越来越广泛。
本文将探讨金刚石刀具在数控机床中的应用,并分析其优势和挑战。
一. 金刚石刀具的基本特性金刚石刀具由金刚石颗粒和金属粉末经压制、烧结等工艺制成,具有极高的硬度、耐磨性和热稳定性。
这些特性使得金刚石刀具在切削加工中具备以下优势:1. 高硬度:金刚石刀具的硬度仅次于金刚石,可用于切削超硬材料如陶瓷和高硬度合金等。
2. 耐磨性:金刚石刀具具有出色的耐磨性,可在切削过程中保持较长的使用寿命。
3. 热稳定性:金刚石刀具具有良好的热稳定性,可承受高温切削环境下的工作,不易变形。
二. 金刚石刀具在数控机床中的应用领域1. 切削加工金刚石刀具广泛应用于数控机床的切削加工领域,包括车削、铣削、钻削、磨削等。
由于金刚石刀具的高硬度和耐磨性,可用于加工硬度较高的材料,如钛合金、高速钢等。
同时,金刚石刀具还能够提供更高的加工精度和表面质量。
2. 精密加工在数控机床的精密加工中,金刚石刀具的应用更能体现出其独特的优势。
例如,在汽车零部件的精密加工过程中,采用金刚石刀具可以实现更高的加工精度和更好的表面质量。
3. 工具磨损监测由于金刚石刀具的耐磨性较高,因此可以通过监测金刚石刀具的磨损情况,准确地评估刀具的使用寿命。
这对机床的保养和刀具的及时更换具有重要意义,可降低生产成本,并提高生产效率。
三. 金刚石刀具在数控机床中的挑战虽然金刚石刀具在数控机床中有广泛的应用前景,但面临着一些挑战和限制:1. 成本高昂:金刚石刀具的制造成本较高,所以其售价也相对较高,这给广泛应用带来了一定的限制。
2. 技术要求高:金刚石刀具的加工工艺复杂,需要高精度和高温高压的条件,所以其生产过程要求较高的技术水平。
3. 刀具表面质量难以保证:由于金刚石刀具的硬度很高,常规的抛光或修整技术难以完成对其表面的加工,从而可能会影响到加工表面质量。
金刚石刀具知识点

⾦刚⽯⼑具知识点⼑具基础知识⼀、⼑具材料应具备的性能;A,⾼的硬度和⾼耐磨性1.硬度是⼑具材料应具备的基本特性2.耐磨性是指材料抵抗磨损的能⼒。
B,⾜够的强度和韧性1.强度是⼑具材料抵抗破坏的能⼒2,韧性是指材料发⽣断裂时外界做功的⼤⼩。
3.⾼的耐热性和热传性4.良好的⼯艺性和经济性1)切削性能⽬前⼑具材料分四⼤类:⼯具钢、硬质合⾦、陶瓷及超硬⼑具材料等。
常⽤的⼑具材料⼀、⼯具钢1. 碳素⼯具钢碳素⼯具钢是含碳量为0.65%~1.3%的优质碳素钢。
常⽤的钢号有T7A、T8A等。
耐热温度:200℃~300℃。
2. 合⾦⼯具钢1868年,英国的穆舍特制成含钨的合⾦⼯具钢。
在碳素⼯具钢中加⼊适当的元素铬(Cr)、硅常⽤的合⾦⼯具钢有9CrSi,CrWMn等(Si)、锰(Mn)、钒(V)、钨(W)等炼成的。
耐热温度:325℃~400℃。
主要⽤于制造细长的或截⾯积⼤、刃形复杂的⼑具。
⼆,⾼速钢⾼速钢是⼀种富含钨(W)、铬(Cr)、钼(Mo)、钒(V)等元素的⾼合⾦⼯具钢。
美国的F.W.泰勒和M.怀特于1898年创制的。
含碳量⼀般在0.70~1.65%之间。
耐热温度:500℃~650℃。
⾼速钢的抗弯强度是硬质合⾦的3~5倍,冲击韧性是硬质合⾦的6~10倍1.普通⾼速钢(HSS)2.钨系⾼速钢:W18Cr4V (W18)3.具有较好的综合性能,可制造复杂刃型的⼑具。
但由于钨是稀有⾦属,现在很少使⽤。
4.钨钼系⾼速钢:W6Mo5Cr4V2 (M2)5.M2的碳化物颗粒⼩,分布均匀,具有较⾼的抗弯强度、塑性、韧性和耐磨性。
⼜因为钼的存在,使其热塑性⾮常好。
2. ⾼性能⾼速钢(HSS-E)⾼性能⾼速钢是在普通⾼速钢中增加⼀些碳、钒及添加钴(Co)、铝等元素的新钢种。
钴⾼速钢:W2Mo9Cr4VCo8 (M42)⼀种含钴的超硬⾼速钢,常温硬度67HRC-69HRC,具有良好的综合性能。
铝⾼速钢:W6Mo5Cr4V2Al在M2的基础上加Al、增C,提⾼了钢的耐热性和耐磨性。
金刚石刀具的优点和缺点

CVD金刚石厚膜(TDF)焊接刀具:金刚石厚膜焊接刀具是把激光切割好CVD金 刚石厚膜一次焊接至基体(通常为K类硬质合金)上,形成复合片,然后抛光复 合片,二次焊接至刀体上,刃磨成需要的形状和刃口。如图3(a)所示,为CVD 金刚石厚膜(金刚石膜厚度达30μm),具有硬度高、耐磨损、摩擦系数小等特 点,是制造切削有色金属和非金属材料刀具的理想材料。 金刚石涂层刀具:金刚石涂层刀具是用CVD法直接在硬质合金(K类硬质合金) 或陶瓷等基体上沉积一层1~25μm金刚石薄膜,无解理面各向同性。薄膜涂 层刀具硬度达9800~10000HV。热导率高,室温下导热系数高达2000W/m·K, 而硬质合金刀具导热系数仅为80~100W/m·K。CVD方法金刚石可以涂层到 任何复杂形状的刀具上,这是聚晶金刚石无法拥晶金刚石(PCD)刀具
金刚石刀具
人造聚晶金刚石复合片(PDC)刀具
CVD金刚石厚膜(TDF)焊接刀具 金刚石涂层刀具
天然金刚石(ND)刀具:天然金刚石是目前已知矿物中最硬的物质,主要用 于制备刀具车刀。天然金刚石刀具精细研磨后刃口半径可达0.01~ 0.002μm。其中天然单晶金刚石(Single Crystalline Diamond,SCD)刀具切削 刃部位经高倍放大1500倍仍然观察到刀刃光滑。SCD车削铝制活塞时Ra可 达到4μm,而在同样切削条件下用PCD刀具加工时的表面粗糙时的Ra 为 15~50μm 。采用SCD刀具配合精密车床迚行精密和超精密加工,可获得 镜面表面。 聚晶金刚石(PCD)刀具:PCD是高温超高压条件下通过钴等金属结合剂将金 刚石微粉聚集烧结合成的多晶体材料,又称烧结金刚石。聚晶金刚石刀具 整体烧结成铣刀,用于铣削加工,PCD晶粒呈无序排列状态,属各向同性, 硬度均匀,石墨化温度为550℃。刀具具有高硬度、高导热性、低热胀系数、 高弹性模量和低摩擦系数。刀刃非常锋利等特点。 人造聚晶金刚石复合片(PDC)刀具:为提高PCD刀片的韧性和可焊性,常将 PCD与硬质合金刀体做成人造聚晶金刚石复合刀片(PDC)。即在硬质合金基 底其表面压制一层0.5~1mm厚的PCD烧结而成。复合刀片的抗弯强度与硬 质合金基本一致,硬度接近PCD,故可以替代PCD使用。
数控车削用刀具的常用分类
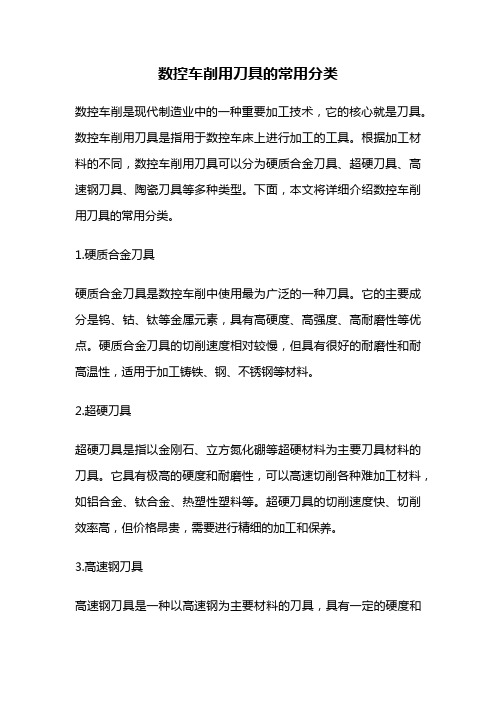
数控车削用刀具的常用分类数控车削是现代制造业中的一种重要加工技术,它的核心就是刀具。
数控车削用刀具是指用于数控车床上进行加工的工具。
根据加工材料的不同,数控车削用刀具可以分为硬质合金刀具、超硬刀具、高速钢刀具、陶瓷刀具等多种类型。
下面,本文将详细介绍数控车削用刀具的常用分类。
1.硬质合金刀具硬质合金刀具是数控车削中使用最为广泛的一种刀具。
它的主要成分是钨、钴、钛等金属元素,具有高硬度、高强度、高耐磨性等优点。
硬质合金刀具的切削速度相对较慢,但具有很好的耐磨性和耐高温性,适用于加工铸铁、钢、不锈钢等材料。
2.超硬刀具超硬刀具是指以金刚石、立方氮化硼等超硬材料为主要刀具材料的刀具。
它具有极高的硬度和耐磨性,可以高速切削各种难加工材料,如铝合金、钛合金、热塑性塑料等。
超硬刀具的切削速度快、切削效率高,但价格昂贵,需要进行精细的加工和保养。
3.高速钢刀具高速钢刀具是一种以高速钢为主要材料的刀具,具有一定的硬度和耐磨性。
它的切削速度相对较快,适用于加工较软的材料,如铝、铜、铁等。
高速钢刀具价格相对便宜,但需要定期进行磨刃和更换。
4.陶瓷刀具陶瓷刀具是指以氧化锆、碳化硅等陶瓷材料为主要材料的刀具。
它具有极高的硬度和耐磨性,可以用于高速切削各种难加工材料,如镁合金、钛合金等。
陶瓷刀具的切削速度快、寿命长,但价格昂贵,需要进行精细的加工和保养。
5.刀柄刀柄是刀具的支撑部分,也是数控车削中的重要组成部分。
根据使用方式的不同,刀柄可以分为直柄、切削柄、内螺纹柄、外螺纹柄等多种类型。
直柄适用于较小的切削力,切削柄适用于较大的切削力,内螺纹柄适用于内孔加工,外螺纹柄适用于外圆加工。
数控车削用刀具的分类有很多种,每种刀具都有其特点和适用范围。
在实际应用中,需要根据加工材料和工件形状等因素选择合适的刀具。
同时,需要注意刀具的保养和更换,以提高加工效率和质量。
五种超硬刀具材料的性能特点分析(下)

五种超硬刀具材料的性能特点分析(下)超硬刀具材料指可用作刀具切削加工的超硬材料。
目前重要可分为两大类:一类是金刚石切削刀具材料;另一类是立方氮化硼切削刀具材料。
目前已经在应用或正在试验中的超硬刀具材料的重要品种有以下五种。
(1)天然和人工合成大单晶金刚石(2)聚晶金刚石(PCD)和聚晶金刚石复合刀片(PDC)(3)CVD金刚石(4)聚晶立方氮化硼(PCBN)(5)CVD立方氮化硼涂层今日接着讲后面三种。
3、CVD金刚石人工合成大单晶金刚石,PCD、PDC均是在高温高压下合成的,而CVD金刚石是在低压下制备的。
含碳气体和氢气的混合物在高不冷不热低于大气压的压力下被激发分解,形成活性金刚石碳原子在基体上沉积交互生长成聚晶金刚石(也可以掌控沉积生长条件沉积生长金刚石单晶或准单晶)。
CVD金刚石由于是不含任何金属催化剂的纯金刚石,因此它的热稳定性接近天然金刚石。
同高温高压人工合成聚晶金刚石一样,CVD聚晶金刚石晶粒也呈无序排列,无脆性解理面而呈各向同性。
实际上CVD金刚石包括三类:第一种是在适当基体上沉积的CVD 金刚石涂层(包括类金刚石DLC涂层);第二种是沉积厚度达1mm的无支撑的CVD金刚石厚膜;第三种是在金刚石晶种上外延生长的CVD金刚石单晶膜或准单晶膜。
由于CVD金刚石涂层刀具采纳刀片基体直接置放在CVD沉积腔体中沉积生长而成,它与PCD、PDC刀具相比,具有刀具形状可多而杂、成本低、一片多刀刃等优点。
尽管如此,由于CVD金刚石涂层刀片存在金刚石涂层与基体之间结合强度低以及对有CVD金刚石涂层的刃口进行研磨处理时简单分层剥落的缺陷。
因此,目前在CVD金刚石涂层制备领域的大工作都在致力于对它的讨论。
尽管国外已有CVD金刚石涂层刀具产品推向市场,但到目前为止CVD金刚石涂层的应用市场还不是很大。
恰恰相反,CVD金刚石厚膜可以通过特别的但简便易行的技术钎焊到所要求的基体上。
然而这种钎焊强度远低于PDC材料中金刚石层与硬质合金层之间的结合强度。
金刚石刀具

金刚石刀具
刀具是一种切削金属或非金属材料的工具,刀具应具有足够的硬度、强度、韧性和耐磨性。
由于金刚石能在长时间内保持锐利,当使用得很仔细而又很恰当使,刃口不易损坏,另外金刚石的线膨胀系数很小,比硬质合金低几倍,因此它不会产生很大的热变形,即由切削热引起的刀具尺寸变化甚微,这对尺寸精度要求很高的精车刀来说是非常重要的。
用金刚石车刀加工时,一次加工就能达到就能达到低粗糙度、高精度,避免了以前为达到这些要求而进行很多复杂费时的工序,从而大大提高了生产率,降低了成本。
金刚石刀具可用来对有色金属及其合金以及非金属材料进行高速精细车削及镗孔。
例如精密切削无氧铜、超硬铝、镁及镁合金等有色金属以及塑料、硬橡胶、石墨等,加工尺寸精度可达到一级几何形状精度3 ~ 5μm,加工表面粗糙度可达0.01 ~ 0.08μm。
金刚石刀具也用来加工预烧后的硬质合金毛坯。
金刚石刀具也存在了一些缺点:
(1)耐热性较低,一般切削温度不能超过700 ~800 ℃;
(2)金刚石强度低,对振动很敏感,只适合于精加工;
(3)一般不适合于加工钢铁材料,因为金刚石和铁有很强的化学亲和力。
近年来,金刚石刀具在加工钢铁材料方面开始取得较好的进展
金刚石刀具种类打字可分为三类
(1)一般车刀,它和普通车刀一样,有外圆、断面、内圆用车刀,做成铣刀还可以进行平面切削;
(2)雕刻用车刀,在切入式切削中可以加工钟表等装饰品;
(3)特殊用车刀,包括完全镜面加工用车刀,辊光用工具等。
金刚石刀片的分类及应用

金刚石刀片的分类及应用金刚石刀片是一种采用金刚石作为刀片切割工具上的切削物料的硬质金属产品,它具有非常高的硬度和耐磨性,因此在切割、磨削等工业领域有着广泛的应用。
金刚石刀片的分类主要根据其使用环境、切削物料和工作方式等因素。
以下是几种常见的金刚石刀片分类及其应用:1. 粉末冶金金刚石刀片粉末冶金金刚石刀片是通过将金刚石粉末与金属粉末混合,并经高温高压制得的刀片。
该类金刚石刀片具有较高的强度和耐磨性,适用于切割硬质材料如岩石、陶瓷、玻璃、木材等。
2. 镀覆金刚石刀片镀覆金刚石刀片是将金刚石晶体通过电镀或熔连接技术镀覆在刀片表面的一种刀片。
它具有较高的强度和耐磨性,适用于切割石材、建筑材料、陶瓷等。
3. 电镀金刚石刀片电镀金刚石刀片是将金刚石颗粒通过电化学沉积在刀片表面的一种刀片。
通过控制电流密度、镀液成分等因素可实现不同规格和性能的刀片制备。
它具有优秀的耐磨性和高温稳定性,适用于切割石材、陶瓷、光学玻璃等。
4. 绑焊金刚石刀片绑焊金刚石刀片是将金刚石颗粒通过焊接工艺绑定在刀片上的一种刀片。
它具有较高的强度和耐磨性,适用于切割石材、陶瓷、光学玻璃、大理石等。
5. 超硬合金金刚石刀片超硬合金金刚石刀片是将金刚石颗粒通过高温高压工艺与钨钴合金等金属粉末共烧制成型的刀片。
由于超硬合金的优异性能和金刚石颗粒的超硬性,该类刀片具有出色的切削性能和较长的使用寿命,适用于切割高硬度材料。
金刚石刀片的应用范围广泛,主要有以下几个方面:1. 建筑行业在建筑行业中,金刚石刀片常用于切割石材、混凝土、砖块等材料。
它具有快速、精确和高效的特点,可以用于建筑物的修复、改建以及道路建设等工程。
2. 木工行业金刚石刀片在木工行业中被广泛使用,可以用于切割木材、刨削木材等。
其高硬度和耐磨性使得切割更加精准、平滑,并且能够延长刀片的使用寿命。
3. 家具制造业家具制造业中,金刚石刀片可以用来切割加工各种材料,例如纤维板、中密度板、实木等。
超硬材料刀具

超硬材料刀具超硬材料刀具是一种具有极高硬度和耐磨性的刀具,通常用于加工硬质材料,如金属、陶瓷和复合材料等。
它们在工业生产中扮演着至关重要的角色,能够提高加工效率、延长刀具使用寿命,并且能够实现高精度加工。
本文将介绍超硬材料刀具的特点、应用领域以及发展趋势。
首先,超硬材料刀具的主要特点是硬度高、耐磨性好。
它们通常采用金刚石、立方氮化硼等超硬材料制成,硬度远远超过普通刀具材料,因此能够在高速、高温、高压等恶劣条件下保持良好的切削性能。
而且,由于其耐磨性好,可以大大延长刀具的使用寿命,减少更换刀具的频率,从而提高生产效率。
其次,超硬材料刀具广泛应用于航空航天、汽车制造、模具加工等领域。
在航空航天领域,超硬材料刀具常用于加工高强度、高温合金材料,如钛合金、镍基合金等,能够实现高速、高效的加工。
在汽车制造领域,超硬材料刀具常用于加工发动机缸体、曲轴等零部件,具有较高的加工精度和表面质量。
在模具加工领域,超硬材料刀具常用于加工硬质材料,如冷作模具、热作模具等,能够实现高精度、高效率的加工。
最后,随着科技的不断进步,超硬材料刀具也在不断发展。
未来,超硬材料刀具将更加注重刀具的设计与制造工艺,以满足不同加工需求。
同时,超硬材料刀具将更加注重环保与节能,推动刀具加工技术的可持续发展。
此外,超硬材料刀具还将更加注重智能化与自动化,实现刀具加工的智能化控制与自动化生产,提高生产效率。
综上所述,超硬材料刀具具有硬度高、耐磨性好的特点,广泛应用于航空航天、汽车制造、模具加工等领域,并且在不断发展中。
相信随着科技的不断进步,超硬材料刀具将在工业生产中发挥越来越重要的作用。
超硬刀具材料

超硬刀具材料超硬刀具材料是一种具有极高硬度和耐磨性的刀具材料,被广泛应用于机械制造、汽车制造、航空航天等行业。
本文将介绍超硬刀具材料的定义、性能特点、应用领域和发展趋势。
超硬刀具材料是指硬度超过1500HV的材料,主要由金刚石和立方氮化硼两种材料组成。
其硬度比传统的钢材高出数倍,具有出色的耐磨性和耐高温性能,可用于高速切削、高精度加工等领域。
超硬刀具材料的主要性能特点如下:1. 极高的硬度:超硬刀具材料的硬度远超过传统的钢材,能够抵抗硬物的磨损和切削力的作用,具有长寿命的特点。
2. 优异的耐磨性:超硬刀具材料能够忍受高速摩擦和高温烧结的环境,不易磨损,并且保持精确的切削形状。
3. 良好的热稳定性:超硬刀具材料在高温条件下保持稳定的性能,不易软化和脱落,适用于高温加工环境。
4. 低摩擦系数:超硬刀具材料具有较低的摩擦系数和良好的自润滑性能,能够减少切削时的摩擦和热量,提高切削效率。
超硬刀具材料主要应用于以下领域:1. 机械制造:超硬刀具材料可用于加工硬质合金、陶瓷材料和高硬度不锈钢等难加工材料。
2. 汽车制造:超硬刀具材料用于汽车发动机缸体、缸头、曲轴等零部件的加工,提高加工效率和产品质量。
3. 航空航天:超硬刀具材料适用于加工航空零部件、航天器件和复合材料,提高加工精度和效率。
4. 电子器件:超硬刀具材料可用于加工半导体材料、光纤和硬盘等电子器件的零部件,提高生产效率和质量。
超硬刀具材料的发展趋势主要有以下几个方向:1. 提高硬度和耐磨性:超硬刀具材料的硬度和耐磨性是其关键性能,未来的发展将致力于进一步提高材料的硬度和耐磨性,以满足更严苛的工况需求。
2. 优化材料结构:超硬刀具材料的结构设计对其性能有重要影响,未来的发展将注重优化材料的晶格结构和界面结合方式,提高材料的强度和稳定性。
3. 开发新型材料:除了金刚石和立方氮化硼,未来的发展将尝试开发新型超硬刀具材料,如纳米结构材料和新型陶瓷复合材料等,以满足更多应用领域的需求。
金刚石刀具这么硬,他的磨削特点真的不一般!

金刚石刀具这么硬,他的磨削特点真的不一般!一.金刚石刀具磨削的工艺特点金刚石刀具的磨削有其自身的工艺特点,比较突出的特点为是材料硬度高,导致砂轮在磨削过程中损耗过快,尺寸不稳定;其二,金刚石刀具多数为车刀或刀片,其磨削部位相对于机床的位置是不确定的(如刀片厚度的变化),引起磨削点的变化。
其三,磨削抗力大,使砂轮、刀具、卡具和机床组成的工艺系统产生比较大的弹性变形,从而产生比较大的“让刀”现象。
这三个特点是实现自动化磨削的三只“挡路虎”,直接影响刀具的模削后的尺寸精度。
如果不妥善解决,必然引起磨削尺寸精度和粗糙度一致性差,磨削效率低,不适合大批量生产。
声控技术在金刚石工具磨床上的使用,能有效地解决这个三个问题。
二.自适应控制技术在粗磨时的应用粗磨金刚石的主要任务是:提高磨削效率,也就是尽量少地设定安全距离,减少“磨削”空气的时间;在机床刚性能承受的范围内,尽快地去除磨削余量;尽早地发现磨削余量已经去除(标志是磨削抗力减少到最小)。
砂轮与金刚石刀具摩擦产生剧烈的声波在工艺装备上传播,对声波的监控能准确地反映出磨削状况,如刀具与砂轮是否接触,刀具与砂轮之间的压力(即磨削抗力)是否消除等。
如果控制系统能实时采集这些信息并进行分析,使机床控制系统与之相适应,这无异于给机床安装上了一只灵敏的耳朵,使机床控制器成为一个更为智能的自适应系统。
事实上,该系统的研发也是受现场工人磨刀的启发。
正常磨削的时候,有两种情况声波频率是有明显特征,一是刀具和砂轮接触的瞬间,二是磨削达到最终尺寸(磨削抗力下降为最小)时,这很容易理解。
前者可以作为快速进给结束,开始磨削进给的分界线;后者则可以作为磨削完成的标志。
即便是在刀具与砂轮“紧密接触”的过程中,声波频率的变化也能反映出刀具与砂轮之间的抗力,将这“信息”反馈给机床控制器,调整伺服的进给速度,使磨削在相对“恒定”的抗力下完成,对于提高磨削效率,延长机床寿命具有很大的意义。
三.“对刀磨法”在精磨上的应用金刚石精磨的主要任务是:准确而稳定地控制磨削的最终尺寸精度。
金刚石刀具标准

金刚石刀具标准金刚石刀具的标准主要包括对其物理性能、制造工艺、几何参数、使用性能等方面的详细规定。
以下是一些关于金刚石刀具标准的信息:1.物理性能标准:硬度:金刚石刀具的硬度极高,约为HV10000(维氏硬度)。
导热性:PCD(聚晶金刚石)刀具的导热系数非常高,约700W/mK,有利于散热和延长刀具使用寿命。
热膨胀系数:PCD的热膨胀系数远低于硬质合金,使得在高温加工条件下仍能保持良好的尺寸稳定性,有助于提高加工精度。
2.制造工艺标准:金刚石颗粒大小:根据用途和精度要求,金刚石刀具的金刚石颗粒度可分为粗粒度、中粒度和细粒度三个级别,分别对应不同的加工应用和切削性能。
结合剂成分与含量:金刚石刀具性能受到金刚石晶粒与结合剂(如钴)含量的影响,标准会规定合适的配方比例以保证刀具的强度和耐磨性。
3.几何参数标准:刀具的前角、后角、主偏角、副偏角、刃倾角等几何参数都有严格的公差范围,以满足不同材料和加工方式的需求。
4.使用性能标准:刀具寿命:金刚石刀具因其优异的耐磨性和耐热性,其寿命普遍远高于硬质合金刀具,具体标准可能涉及到连续切削长度或切削次数等指标。
加工精度:根据国家或行业标准,金刚石刀具在使用过程中应能达到规定的加工精度和表面粗糙度要求。
5.国内标准:国内对于金刚石刀具的质量和生产有专门的国家标准,例如提到的“燕矶标准”是中国国家金刚石刀具生产标准的一部分,由国家和地方技术监督部门联合制定,以确保产品质量和一致性。
要了解具体的金刚石刀具标准,可以查阅相关国家标准,如GB/T系列标准,以及行业标准等官方发布的详细文档。
此外,国际上也有一些ISO标准对金刚石刀具的生产和检测进行了规定。
金刚石刀具的优点和缺点

金刚石刀具的优缺点
天然金刚石(ND)刀具 聚晶金刚石(PCD)刀具
金刚石刀具
ห้องสมุดไป่ตู้
人造聚晶金刚石复合片(PDC)刀具
CVD金刚石厚膜(TDF)焊接刀具 金刚石涂层刀具
天然金刚石(ND)刀具:天然金刚石是目前已知矿物中最硬的物质,主要用 于制备刀具车刀。天然金刚石刀具精细研磨后刃口半径可达0.01~ 0.002μm。其中天然单晶金刚石(Single Crystalline Diamond,SCD)刀具切削 刃部位经高倍放大1500倍仍然观察到刀刃光滑。SCD车削铝制活塞时Ra可 达到4μm,而在同样切削条件下用PCD刀具加工时的表面粗糙时的Ra 为 15~50μm 。采用SCD刀具配合精密车床迚行精密和超精密加工,可获得 镜面表面。 聚晶金刚石(PCD)刀具:PCD是高温超高压条件下通过钴等金属结合剂将金 刚石微粉聚集烧结合成的多晶体材料,又称烧结金刚石。聚晶金刚石刀具 整体烧结成铣刀,用于铣削加工,PCD晶粒呈无序排列状态,属各向同性, 硬度均匀,石墨化温度为550℃。刀具具有高硬度、高导热性、低热胀系数、 高弹性模量和低摩擦系数。刀刃非常锋利等特点。 人造聚晶金刚石复合片(PDC)刀具:为提高PCD刀片的韧性和可焊性,常将 PCD与硬质合金刀体做成人造聚晶金刚石复合刀片(PDC)。即在硬质合金基 底其表面压制一层0.5~1mm厚的PCD烧结而成。复合刀片的抗弯强度与硬 质合金基本一致,硬度接近PCD,故可以替代PCD使用。
CVD金刚石厚膜(TDF)焊接刀具:金刚石厚膜焊接刀具是把激光切割好CVD金 刚石厚膜一次焊接至基体(通常为K类硬质合金)上,形成复合片,然后抛光复 合片,二次焊接至刀体上,刃磨成需要的形状和刃口。如图3(a)所示,为CVD 金刚石厚膜(金刚石膜厚度达30μm),具有硬度高、耐磨损、摩擦系数小等特 点,是制造切削有色金属和非金属材料刀具的理想材料。 金刚石涂层刀具:金刚石涂层刀具是用CVD法直接在硬质合金(K类硬质合金) 或陶瓷等基体上沉积一层1~25μm金刚石薄膜,无解理面各向同性。薄膜涂 层刀具硬度达9800~10000HV。热导率高,室温下导热系数高达2000W/m·K, 而硬质合金刀具导热系数仅为80~100W/m·K。CVD方法金刚石可以涂层到 任何复杂形状的刀具上,这是聚晶金刚石无法拥有的最显著的优势。
24金刚石刀具解析
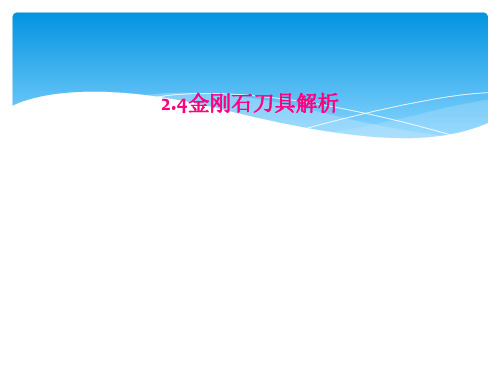
❖ 金刚石晶体(111)晶面硬度和耐磨性最高
金刚石的解理现象
❖ 由固体物理学理论知,原子密度较大的晶面 之间的距离也较大,面间原子结合力弱,受 力时可沿平行该面方向平整的劈开,该现象 称为解理现象。
❖ 金刚石晶体可沿解理面 (111)平整的劈开两半
❖ 研究表明金刚石的破 损磨损主要形式是微 观解理。
3.金刚石各晶面的好磨难磨方向 ❖ 不同晶面耐磨性不同,且同一晶面上不同方向耐
磨性亦有很大差别。金刚石的耐磨性可用它的相对 磨削率来表示。
110
100 111
❖ 在高磨削率方向,(100):(111):(110)=5.8:1:12.8 对金刚石研磨时,各晶面均有 “好磨”和“难磨”方向
2.4金刚石刀具解析
单晶金刚石
❖ 天然单晶金刚石具有优异的特性,虽然价格较贵 但被公认为理想的、无法代替的超精切刀具材料
❖ 人造金刚石1954年美研 制成功,细颗粒(制砂 轮)→聚晶金刚石→大 颗粒单晶金刚石。
❖ 大颗粒人造单晶金刚石 是在超高压(500MPa) 高温(1300℃)下由子晶 生长而成。
111晶面的激光衍射图像 110晶面的激光衍射图像
金刚石的三个重要晶面
❖(100)晶面:正方形,三个面,三根四次对称轴; (111)晶面:三角形,八个面,四根三次对称轴; (110)晶面: 菱形,六个面,六根二次对称轴
金刚石晶体的面网及原子排列形式
❖ 晶体内部分布有原子的面叫作晶面,也称面网 面网上原子排列形式、原子排列密度及面网间的 距离不同将造成晶体的不同晶向性能差异甚大。
金刚石刀具切削部分的几何形状
金刚石刀具的独有特征

金刚石刀具的独有特征
金刚石刀具现在已经是被业内公认的、理想的和不能代替的超精密加工刀具。
那么金刚石的什么特征让“它”得到这么多“荣誉”呢?今天就给大家讲下金刚石刀具的特有特征: 1金刚石刀具具有极高的硬度和耐磨性:金刚石是自然界已经发现的最硬的物质;
2金刚石刀具具有很低的摩擦系数:摩擦系数低,加工时变形小,可减小切削力;
3金刚石刀具切削刃非常锋利:金刚石刀具的切削刃可以磨得非常锋利;
4金刚石刀具具有很高的导热性能:金刚石的导热系数及热扩散率高,切削热容易散出,刀具切削部分温度低。
刚石刀具现在已经是被业内公认的、理想的和不能代替的超精密加工刀具。
那么金刚石的什么特征让“它”得到这么多“荣誉”呢?今天就给大家讲下金刚石刀具的特有特征:
1金刚石刀具具有极高的硬度和耐磨性:金刚石是自然界已经发现的最硬的物质;
2金刚石刀具具有很低的摩擦系数:摩擦系数低,加工时变形小,可减小切削力;
3金刚石刀具切削刃非常锋利:金刚石刀具的切削刃可以磨得非常锋利;
4金刚石刀具具有很高的导热性能:金刚石的导热系数及热扩散率高,切削热容易散出,刀具切削部分温度低。
5金刚石刀具具有较低的热膨胀系数:金刚石的热膨胀系数比硬质合金小几倍,由切削热引起的刀具尺寸的变化很小。
以上几点金刚石刀具所具有的特有特征,使的“他”成为业内“宠儿”,并且在很多很行都可以看到金刚石刀具的“身影”。
5金刚石刀具具有较低的热膨胀系数:金刚石的热膨胀系数比硬质合金小几倍,由切削热引起的刀具尺寸的变化很小。
以上几点金刚石刀具所具有的特有特征,使的“他”成为业内“宠儿”,并且在很多很行都可以看到金刚石刀具的“身影”。
超硬刀具金刚石刀具介绍

超硬刀具金刚石刀具介绍PCD聚晶金刚石刀具;CVD金刚石膜刀具(物理涂层)PVD物理涂层金刚石刀具PCBN聚晶立方氮化硼刀具;一、概述超硬刀具材料是指比陶瓷材料更硬的刀具材料。
包括:单晶金刚石、聚晶金刚石(PCD)、聚晶立方氮化硼(PCBN)和CVD金刚石等。
超硬刀具主要是以金刚石和立方氮化硼为材料制作的刀具,其中以人造金刚石复合片(PCD)刀具及立方氮化硼复合片(PCBN)刀具占主导地位。
许多切削加工概念,如绿色加工、以车代磨、以铣代磨、硬态加工、高速切削、干式切削等都因超硬刀具的应用而起,故超硬刀具已成为切削加工中不可缺少的重要手段。
随着科技的进步,制造业的高速发展,CNC 加工技术的迅猛发展以及数控机床的普遍使用,超硬刀具的生产及应用也越来越广泛。
PCD和PCBN刀具已广泛应用于机械加工的各个行业,如汽车零部件的切削加工,强化木地板的加工等,极大地促进了切削加工及先进制造技术的飞速发展。
二、切削材料及超硬材料发展史3、金刚石、超硬材料的特性与作用众所周知,金刚石材料的成分是碳,金刚石与铁系有亲和力,切削过程中,金刚石的导热性优越,散热快,但是要注意切削热不宜高于700度,否则会发生石墨化现象,工具会很快磨损。
因为金刚石在高温下和W、Ta、Ti、Zr、Fe、Ni、Co、Mn、Cr、Pt等会发生反应,与黑色金属(铁碳合金)在加工中会发生化学磨损,所以,金刚石不能用于加工黑色金属只能用在有色金属和非金属材料上,而CBN即使在1000oC的高温下,切削黑色金属也完全能胜任。
已成为未来难加工材料的主要切削工具材料。
一般超硬材料指的是人造金刚石、人造CBN。
这两种材料的同时存在,起到了互补的作用、可以覆盖当前与今后发展的各种新型材料的加工,对整个切削加工领域极为有利。
1.PCD金刚石烧结体(PCD)的出现,在许多方面代替了天然单晶金刚石。
PCD与天然金刚石比较,价格便宜,且刃磨远比天然金刚石方便,所以其应用、推广特别迅速。
金刚石刀具知识点

刀具基础知识一、刀具材料应具备的性能;A,高的硬度和高耐磨性1.硬度是刀具材料应具备的基本特性2.耐磨性是指材料抵抗磨损的能力。
B,足够的强度和韧性1.强度是刀具材料抵抗破坏的能力2,韧性是指材料发生断裂时外界做功的大小。
3.高的耐热性和热传性4.良好的工艺性和经济性1)切削性能目前刀具材料分四大类:工具钢、硬质合金、陶瓷及超硬刀具材料等。
常用的刀具材料一、工具钢1. 碳素工具钢碳素工具钢是含碳量为0.65%~1.3%的优质碳素钢。
常用的钢号有T7A、T8A等。
耐热温度:200℃~300℃。
2. 合金工具钢1868年,英国的穆舍特制成含钨的合金工具钢。
在碳素工具钢中加入适当的元素铬(Cr)、硅常用的合金工具钢有9CrSi,CrWMn等(Si)、锰(Mn)、钒(V)、钨(W)等炼成的。
耐热温度:325℃~400℃。
主要用于制造细长的或截面积大、刃形复杂的刀具。
二,高速钢高速钢是一种富含钨(W)、铬(Cr)、钼(Mo)、钒(V)等元素的高合金工具钢。
美国的F.W.泰勒和M.怀特于1898年创制的。
含碳量一般在0.70~1.65%之间。
耐热温度:500℃~650℃。
高速钢的抗弯强度是硬质合金的3~5倍,冲击韧性是硬质合金的6~10倍1.普通高速钢(HSS)2.钨系高速钢:W18Cr4V (W18)3.具有较好的综合性能,可制造复杂刃型的刀具。
但由于钨是稀有金属,现在很少使用。
4.钨钼系高速钢:W6Mo5Cr4V2 (M2)5.M2的碳化物颗粒小,分布均匀,具有较高的抗弯强度、塑性、韧性和耐磨性。
又因为钼的存在,使其热塑性非常好。
2. 高性能高速钢(HSS-E)高性能高速钢是在普通高速钢中增加一些碳、钒及添加钴(Co)、铝等元素的新钢种。
钴高速钢:W2Mo9Cr4VCo8 (M42)一种含钴的超硬高速钢,常温硬度67HRC-69HRC,具有良好的综合性能。
铝高速钢:W6Mo5Cr4V2Al在M2的基础上加Al、增C,提高了钢的耐热性和耐磨性。
金刚石砂轮划片刀“软刀”与“硬刀”的区别及持点

金刚石砂轮划片刀“软刀”与“硬刀”的区别及持点标签: 软刀硬刀划片刀金刚石砂轮片2021-03-04 20:31在电子工业领域常常需要对一些硬脆非金属材质进行开槽或切割加工,在进行开槽或切割加工时通常所用的工具为薄型金刚石砂轮片。
在长期利用薄型金刚石砂轮片的进程中,人们为了便于区分不同的砂轮片,习惯将薄型金刚石砂轮片分为“软刀”和“硬刀”。
下面就二种刀的区别及特点简要叙述。
“软刀”和“硬刀”的区别如下:一、砂轮片外形的区别一般将圆环薄片状的砂轮片称为“软刀”,而将砂轮片与铝合金刀架组合成为一体的砂轮片称为“硬刀”(如图1和图2);图1图2二、砂轮片材质的区别砂轮片材质主要由金刚石磨料和结合剂组成。
而“软刀”的磨料结合剂一般为金属镍合金或金属铜合金以及树脂结合剂三类,而“硬刀”的磨料结合剂一般只有金属镍合金;3、砂轮片制造时成型工艺的区别在制造“软刀”时其成型方法一般有电铸成型、粉末压制烧结或粉末压制加温固化成型等,而“硬刀”一般均采用电铸成型的方法;4、使用方法的区别“软刀”在使用时必须要定位固定在一个专用刀盘(或称法兰盘)上(如图3),然后再安装到专用切割机上,而“硬刀”在使用时不需要刀盘可以直接安装到专用切割机上。
图3“软刀”和“硬刀”的不同特点如下:一、刀的精度和性能“软刀”在使用时的精度,除了刀在出厂时要求符合标准外,在使用时其精度还要依赖刀盘的精度,而“硬刀”可以直接装机使用不存在类似问题。
但如安装“软刀”的刀盘符合标准要求,二种刀在使用时的精度及性能是一样的;2、刀使用时的方便性“硬刀”可以直接安装到切割设备上,而且硬刀的刃口在出厂前已修磨好,所以新的刀只要进行预切割就可以够进行正常利用,超级方便;“软刀”由于先要固定在刀盘上再安装到切割设备上,而且“软刀”在出厂前不能先将刃口修磨好,所以“软刀”在切割之前先要进行刃口的修磨,使刃口的锋利符合切割要求后才能正式使用。
所以“软刀”在使用时没有“硬刀”方便,而且对员工操作技能的要求也相对“硬刀”要高一些;3、刀的应用范围“硬刀”其磨料的粘合剂只有一种,而“软刀”的粘合剂有多种,所以“软刀”可以针对不同材料而选择不同粘合剂的刀进行切割,因此“软刀”比“硬刀”的应用范围更大;4、用刀成本由于“软刀”的销售价格比“硬刀”便宜很多(针对“核力”牌砂轮片),所以“软刀”的用刀成本较低;另外“软刀”当外圆磨损或外圆一圈打掉后可更换小刀盘后继续使用,一般一片刀片可用三种直径(大、中、小)的刀盘来使用,非常经济;而“硬刀”当刀刃磨损或打掉后,虽然也可以进行刃口再生,但再生一定要在制造厂进行,自己一般没有这个技术,而且再生需要必然的本钱费用,所以一般利用单位都不进行刃口再生,只作一次性利用,浪费较大。
- 1、下载文档前请自行甄别文档内容的完整性,平台不提供额外的编辑、内容补充、找答案等附加服务。
- 2、"仅部分预览"的文档,不可在线预览部分如存在完整性等问题,可反馈申请退款(可完整预览的文档不适用该条件!)。
- 3、如文档侵犯您的权益,请联系客服反馈,我们会尽快为您处理(人工客服工作时间:9:00-18:30)。
金刚石刀具与超硬刀具的区别及优缺点
内容来源网络,由“深圳机械展(11万㎡,1100多家展商,超10万观众)”收集整理!
更多cnc加工中心、车铣磨钻床、线切割、数控刀具工具、工业机器人、非标自动化、数字化无人工厂、精密测量、数控系统、3D打印、激光切割、钣金冲压折弯、精密零件加工等展示,就在深圳机械展.
金刚石刀具优缺点
超硬刀具的优缺点
超硬材料具有优异的机械性能、物理性能和其他性能,其中有些性能很适合于刀具。
具有很高的硬度
天然金刚石的硬度达10000HV;CBN的硬度达7500HV。
与其他硬物质相比,SiC硬度为3000~3500HV,A12O3为2700HV,TiC为2900~3200HV,WC为2000HV,Si3N4为2700~3200HV;作为刀具材料用的硬质合金,其硬度仅为1100~1800HV。
具有很好的导热性
天然金刚石的热导率达2000W/m-1*K-1,CBN的热导率达1300W/m-1/K-1。
紫铜的导热性很好,其热导率仅为393W/m-1*K-1;纯铝为226W/m-1*K-1,故金刚石与CBN 的热导率分别是紫铜的5倍和3.5倍,是纯铝的8倍和5倍。
硬质合金的热导率仅为35~75W/m-1*K-1。
具有很高的杨氏模量
天然金刚石的杨氏模量达1000GPa,CBN的杨氏模量在720GPa。
而SiC、Al2O3、WC、TiC的杨氏模量仅分别为390、350、650、330GPa。
物质的杨氏模量大就是刚性好。
具有很小的热膨胀
天然金刚石的线膨胀系数为1×10-6/K,CBN的线膨胀系数为(2.1~2.3)×10-6/K。
而硬质合金的线膨胀系数为(5~7)×10-6/K。
具有较小的密度
天然金刚石的密度为3.52g/cm3,CBN的密度为3.48g/cm3。
与Al2O3、Si3N4的密度接近。
具有较低的断裂韧性
天然金刚石的断裂韧性为3.4MPa/m0.5,CBN与之接近。
陶瓷刀具材料的断裂韧性在各种刀具材料中是属于较低者,然尚能达7~9MPa?m0.5。
故金刚石与CBN性脆,是其弱点。
化学性质
CBN热稳定性好,在大气中达1300~1500℃不分解。
对铁族元素呈惰性;在酸中不受渗蚀,在碱中约300℃时即受浸蚀;与过热的水蒸汽也能起作用。
金刚石在常温下化学性质稳定;在氧气中约660℃开始石墨化,铁族元素特别是铁元素能催进石墨化;在酸、碱中都不受浸蚀。
电学性质
纯净的不含杂质的金刚石是绝缘体,室温下电阻率在1016Ω?cm以上。
只有掺人了其他元素后,才显出半导体特性。
同Si、Ce、As等半导体材料相比,金刚石具有非常宽的禁带,小的介电常数,高的载电子迁移率,大的电击穿强度,说明金刚石是一种性能优良的宽禁带高温(>500℃)半导体材料。
天然金刚石无磁性;人造金刚石中若含有Ni、Co、Fe等触媒杂质,则具有磁性,杂质越多,磁性越强。
光学性质
金刚石具有很高的折射率和强的散光性,还具有优良的透光性能,能透过很宽的波段。
某些金刚石在紫外区、可见区直至远红外区的大部波段(O.22~2.5μm)都是透明的。
以上超硬材料所具备的优异或特异的性能和性质,决定了它们有着广阔用途。
与天然金刚石(ND)相比,人造聚晶金刚石(PCD)的硬度、杨氏模量和热导率稍低,断裂韧性、热膨胀率稍高。
人造CVD金刚石的各种性能则介于ND与PCD之间,更接近于天然金刚石。
例如,天然金刚石的硬度达10000HV,PCD约为8000HV,CVD金刚石可达9000HV。
超硬刀具与金刚石的区别
超硬刀具是现代工程材料的加工在硬度方面提出的更高要求而应运而生,20世纪的后40年中有了较大的发展。
超硬材料的化学成分及其形成硬度的规律与其他刀具材料不同,立方
氮化硼是非金属的硼化物,晶体结构为面心立方体;而金刚石由碳元素转化而成,其晶体结构与立方氮化硼相似。
它们的硬度大大高于其他物质。
内容来源网络,由“深圳机械展(11万㎡,1100多家展商,超10万观众)”收集整理!
更多cnc加工中心、车铣磨钻床、线切割、数控刀具工具、工业机器人、非标自动化、数字化无人工厂、精密测量、数控系统、3D打印、激光切割、钣金冲压折弯、精密零件加工等展示,就在深圳机械展.。