连轧机减速箱振动故障诊断
轧钢机械振动监测与故障诊断分析论文

轧钢机械的振动监测与故障诊断分析【摘要】轧钢机械作为轧钢厂中至关重要的设备,通过其运行状态的振动监测和故障诊断能够及时发现轧钢机械的运行故障先兆,避免意外事故的发生,确保轧钢机械安全、可靠运行。
本文主要对轧钢机械振动监测测点的选择、监测的方法、监测周期的选择进行了探讨,并根据振动监测技术地对轧钢机械的常见故障进行了相应的诊断与分析。
【关键词】轧钢机械;振动监测;故障诊断轧钢机械是轧钢厂中至关重要的机械设备,是一种大型的旋转机械。
人们在长期的实践与观察中发现,轧钢机械在发生故障之前会有异常的振动表现出来。
因此,为了及时发现轧钢机械的运行故障先兆,避免意外事故的发生,需要对轧钢机械的重点部位,如旋转轴、齿轮传动件、联轴器、滑动和滚动轴承等进行动态振动监测和故障诊断,以便准确地掌握故障发生的原因,从而更好地维护和检修轧钢机械设备,提高轧钢机械设备的使用率,确保轧钢机械安全、可靠运行。
1.轧钢机械的振动监测1.1测点的选择由于轧钢机械在运行时其转速处于不恒定状态中,功率则在空载与满负荷周期间不断地波动,因而可能出现的故障类型也相对较多。
因此检测设备、点检时间、点检方式及测点的选择对于故障诊断的正确性有着至关重要的作用。
为了确保监测数据具有一定的可比性,在测定数据时需要遵循以下的原则进行操作:第一,每次测量机器的工况需保持一致,且所使用的测量仪器及测量方法都应保持一致。
第二,每次需在同一点测点进行测量,这样不会由于激振源到测点的传递函数不同,而造成测量的结果存在很大的差距。
第三,测量的参数应保持一致,通常而言,频率超过1000hz的振动,其数据采集器的输出参数应以加速度为主,频率在100-1000hz范围内的振动,其数据采集器的输出参数应以速度为主,而频率在10-100hz范围内的振动,其数据采集器的输出参数应以位移为主。
在监测振动的过程中,轧钢机械的监测结果受测点的影响,因此在选择测点时应把握以下原则:第一,测点宜选择在信号反应相对敏感的部位,如机座,轴承座等部位。
轧钢机械振动故障的分析及诊断

轧钢机械振动故障的分析及诊断振动故障在轧钢机械实际运行的过程中,是一个较为常见的问题。
如果对发生故障的地方,采取专业的仪器进行检测,就能够让诊断更具有准确性,将发生故障的原因找出,进而方便工作人员实施有效的手段,对存在的问题进行及时的解决。
基于此,本文主要将详细的分析轧钢机械振动故障的数据采集、频谱分析以及故障诊断,对有关的问题进行探讨。
标签:轧钢机械;振动故障;数据采集;故障诊断一旦振动故障的情况在轧钢机械运行的过程中发生,就会影响轧钢机械的生产质量,同时也会对其的安全性造成影响,虽然这种影响看似非常普通,但实则非常重要,在轧钢机械生产和运行的过程中,振动故障也是需要加强重视的重要部分,同时也是对维护设备工作的重点内容。
在监测和诊断振动故障上,主要可以通过安装监测系统在轧钢机械设备的方法来实施,严格的监控振动幅度,以此来保证准确、及时的对振动故障发生的原因进行判断。
在诊断和处理轧钢机械振动故障时,要对判断的标准进行不断的优化,同时做好数据采集的工作,之后全面的对频谱进行分析,只有按照上述这样的方法,才能够确保准确的对振动发生的故障进行诊断,有效的维护和控制轧钢机械生产活动。
1 判断轧钢机械振动故障的标准判断轧钢机械振动发生故障的判断标准,主要判断的标准分为三种,也就对故障相对的判断、故障定量的评判以及故障类比的评判。
事实上,需要结合多个方面的因素,对故障发生的原因进行判断,比如机械工作过程中状态突然发生的变化等。
因此,这项工作在具体实施的过程中,不但非常复杂,而且还存在一定的困难性。
基于此可知,在判断轧钢机械振动故障时,经常需要采取较为严格的标准进行判断,而较好的方法就是将时间轴作为基准,从而实施比较分析,在一样测试位置的情况下,获取到比较重要的数据,然后将其和正常情况下的数据进行对比,从而发现轧钢机械在实际运行过程中存在的故障情況。
在进行诊断期间,需要严格的监督和控制每个环节,只有这样才能够准确的获取数据,并及时的诊断出故障的发生,这对工作人员在最短时间内发生问题是非常有帮助的,同时为工作人员解决问题争取了更多的时间。
减速器故障振动的监测与诊断
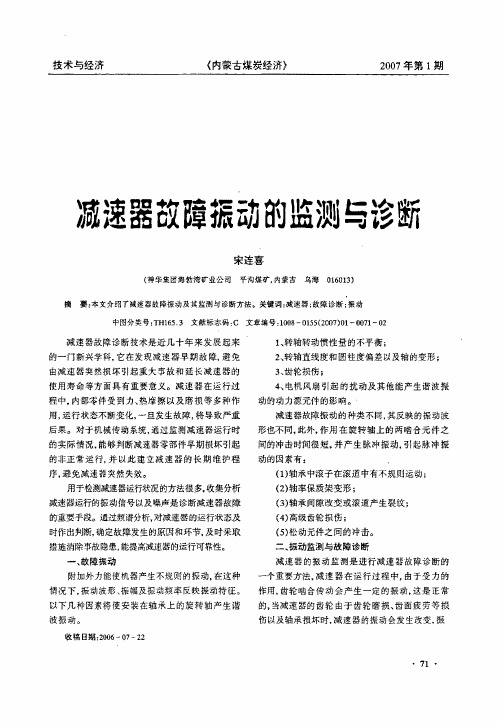
动的振幅、 频率、 速度及加速度等值均会发生变化。 齿数有关的啮合周期. 从而影响减速器的固 有颇率、 当齿轮所有的 轮齿 均匀磨损, 而使齿侧隙 增加时, 啮合频率及基频率分量的变化。 会 使振动加剧, 而且产生的冲击振动的振幅比 其他振 (4)当齿轮轴出现不平衡, 对中性不好和松动等 动大得多。 冲击振动的振幅具有几乎相同的振频, 缺陷时, 当 将出现减速器固有频率的低次频波。 发生齿轮轮齿折摄、 局部齿面磨损等局部异常时, 会 (5)当齿轮有角速度波动时, 会出现调 颜现象。 在高颇域产生非线性振动的跳跃现 即脉冲振动。 象, (6}当齿圈偏心时, 除振幅增大外, 现与偏 将出 减速器某些特征测点处的振动响应频谱可作为某些 心有关的高频调幅信号。 故障诊断的依据。以下是各类故障在频域中的显 轴承故障一般作为产生脉冲振动的因素, 而不 示。 作为产生谐波振动的因素。轴承发生故障时, 将产 ( 1) 当齿轮磨损时, 频率的振幅大小会变化, 生脉冲 高 振动, 脉冲的强度反映了撞击的程度。 通过 次 频率分量的幅道将明显增大。 检测袖承内 滚子与滚道撞击产生的振动 即可 判断 (2)当齿廓有 变形或齿根有裂纹时, 啮合频率的 轴承的 工作状态. 脉冲振动值随着轴承损伤程度的 幅值变大, 频分量也增加。 其谐 恶化而增加。
减速器 故障诊断技术是近几十年来发展起来 的一门新兴学科, 它在发现减速器早期故障, 避免
由减速器突然损坏引起重大事故和延长减速器的
1、 转轴转动惯性量的不平衡; 2、 转轴直线度和圆柱度偏差以及轴的变形;
使用寿命等方面具有重要意义。减速器在运行过 程中, 内部零件受到力、 热摩擦以及磨损等多种作 用, 运行状态不断变化, 一旦发生故障, 将导致严重
技术与经济
( 内蒙古煤炭经济》
棒材连轧主减速机振动监测与故障分析
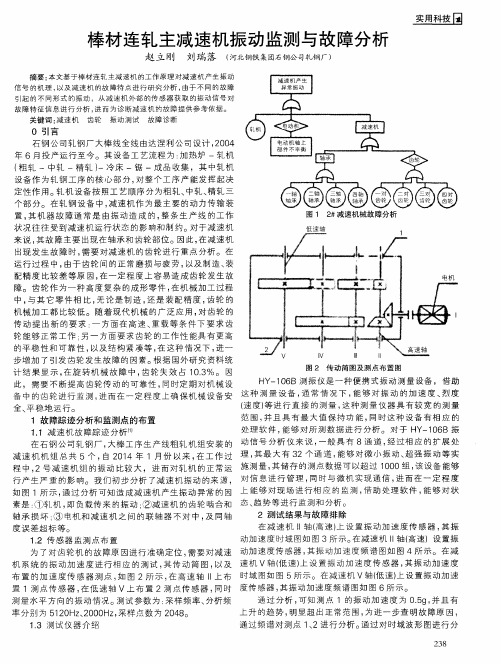
 ̄ F L # J l I
√离 l 部 件 不 平 衡 l … 。 丁 t
轴 承 轮
图 1 2 #减 速机 械 故 障分 析
图 2 传 动简 图及 测 点 布 置 图
H Y 一1 0 6 B测振 仪是 一种 便携 式振 动测 量 设备 ,借 助 此 ,需 要 不 断提高 齿 轮传 动 的可 靠性 , 同时定 期 对机 械设 通常情况下 , 能 够 对 振 动 的加 速 度 、 烈 度 备 中 的齿 轮进 行监 测 , 进 而在 一定 程度 上确 保 机械 设 备安 这种 测 量 设 备 , ( 速度 ) 等 进 行 直接 的测 量 , 这种 测 量 仪器 具 有较 宽 的测 量 全、 平 稳 地运 行。 范 围, 并 且具 有 最 大值 保 持功 能 , 同 时这 种 设备 有 相 应 的 处理 软 件 , 能够 对 所测 数 据 进行 分析 。 对 于 H Y 一 1 0 6 B振 一 般具 有 8通 道 , 经 过相 应 的扩 展 处 在 石钢 公司 轧钢 厂 , 大 棒工 序 生产 线粗 轧机 组 安装 的 动 信 号 分析 仪 来 说 , 其最大有 3 2个 通 道 , 能够 对微 小 振动 、 超 强 振 动 等 实 减 速 机 机 组 总共 5个 , 1 9 2 0 1 4年 1月份 以来 , 在 工 作 过 理 , 施 测量 , 其储 存 的测 点数据 可 以超过 1 0 0 0组 , 该 设备 能 够 程 中, 2号减 速 机 组 的振 动 比较 大 ,进 而 对轧 机 的正 常运 同 时与微 机 实 现通 信 , 进 而 在 一定 程 度 行 产生 严 重 的影 Ⅱ 向 。 我 们初 步 分析 了减 速机 振 动 的来 源 , 对信 息 进行 管 理 ,
棒材连 轧主减 速机振 动监测与故障分析
轧机主减速机振动测试与故障分析
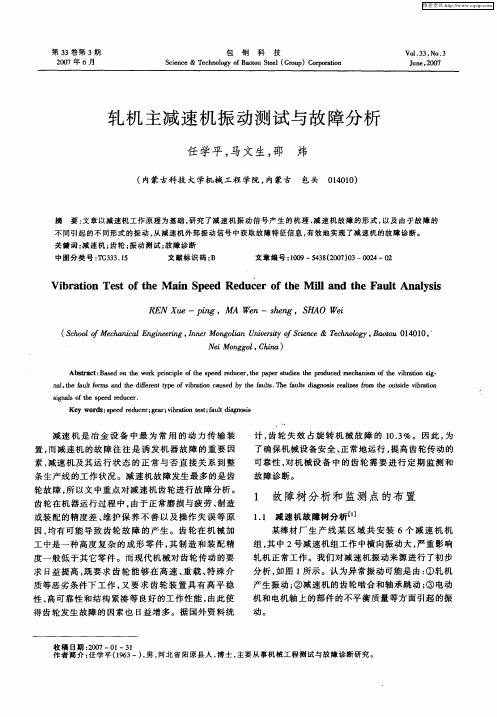
Ab t a t Ba e n te wo k pi cpe o h p e l u e , e p p rsu i ste po u e c a im fte vb ai n sg sr c : s d o h r rn il fte s e d  ̄d c r t a tde r d c d me h ns o irto i- h e h h h l te f l fr n e dfee ttp fvb a o a sd b e fu t T e fut a n ssraie rm h u ie vbain a , aut oms a d t i rn y o ir t n c u y t a s. h a s d g oi e lzs fo te o t d i rt h h e i e h l l i s o ss  ̄ o he s . d l t e . in ft e  ̄dl r pe c Ke r s:p ed rd c r g a ; ir t n ts ;a l da noi y wo d s e e u e ; e r vbai e t fu ti g ss o
( colfM ca i l n i e n Inr n oa n e i c ne Tcnl y B o u04 1 , Sho o eh n a E gn r g,n gl nU i rt o i c & eho g , a t 10 0 i ) e Mog o , h a n
计 , 轮 失 效 占旋 转 机 械 故 障 的 1 . %。因 此 , 齿 03 为 了确 保机械设 备 安全 、 正常地 运行 , 提高 齿轮传 动 的 可靠性 , 机 械设 备 中 的齿 轮 需要 进 行 定 期监 测 和 对 故障诊 断 。
1 故 障树 分析 和 监测 点 的布 置
轧钢机械设备的振动故障诊断分析 李侯军

轧钢机械设备的振动故障诊断分析李侯军摘要:轧钢机械是完成由原料到成品的整个轧钢工艺过程中使用的机械设备。
在生产实践中由于工作强度较大,即使具有操作方便和结构合理的优势,也难免会出现振动故障。
而振动故障不仅会对轧钢产品质量带来影响,同时还会威胁到轧钢机械的生产安全,并对机械的使用寿命产生巨大影响。
因此,对轧钢机械的安全技术维护和运行管理就成为轧钢工作中的重点。
通过装配在轧钢机械设备中的检测和监控系统不断监测振动的幅度和频率,及时发现和定位存在于轧钢机械的振动故障,通过数据采集、频谱分析,发现关于轧钢机械振动故障的规律,并制定相应的判断标准,以指导轧钢机械的安全生产。
关键词:轧钢机械设备;振动故障;诊断分析一、轧钢机械设备的振动故障标准分类轧钢机械振动故障种类繁多,每种都有着较为显著的特征。
根据这些故障振动性质以及振动方式的不同,可以将诊断故障分为以下几类。
(1)转子振动异常。
在轧钢机械设备的运行中,转子的安装能够影响到设备的环境温度和负荷情况。
如果转子在安装的过程中操作人员出现安装失误,那就就会让设备的环境温度产生剧烈浮动,最终转子出现振动异常,直接导致转子松动的现象,有时还会产生转轴松动,无论是哪种都会导致转子的损坏,严重的还会损坏轴承。
总之损坏转子的频率会产生变化,相应的设备就会出现振动故障的现象。
(2)电机振动故障。
电机振动故障同样是由转子引起的,在工作人员安装转子的过程中,一定要注意转子的对称性,转子不对称,那么电子和转子的之间的电压就会极不稳定,设备也就不能稳定的运行。
轧钢机械设备就会不断出现摩擦的现象,时间久了就会产生松动,最后出现异常,导致设备的振动故障。
(3)齿轮机械振动故障。
轧钢机械设备作为重型工业设备,工作时带来的压力是巨大的。
在设备当中的齿轮机械如果缺乏定期的维护保养,长时间工作下就不能承受轧钢机械设备带来的巨大压力。
具体表现为齿轮的波动幅度远远超过了齿轮本身的负载能力,齿轮表面短时间内就会出现磨损,降低使用寿命,严重的甚至还会出现断裂问题,齿轮出现故障,轧钢机械设备就会产生剧烈的诊断故障,无法良好运行。
减速器振动问题分析

减速器振动问题分析减速器振动问题分析减速器振动问题是指在减速器运行过程中出现的振动现象。
振动是指物体在某一时刻或一段时间内由于受到外部力的作用而发生的周期性的往复运动。
减速器振动问题可能会影响到减速器的正常运行,甚至导致设备故障。
解决减速器振动问题的步骤如下:第一步:观察和描述振动现象。
在遇到减速器振动问题时,首先要仔细观察和描述振动的性质。
这包括振动的频率、振幅、方向和持续时间等。
通过观察和描述,可以初步了解振动的特点,为后续的分析提供基础。
第二步:检查和调整设备安装。
减速器的振动问题可能与设备的安装有关。
因此,需要检查减速器的安装情况,确保减速器和相关设备之间的连接牢固可靠。
如果发现安装不当或连接松动的情况,应及时进行调整和修复。
第三步:检查和维护减速器本身。
减速器内部的零部件可能会因磨损、松动或失效而引起振动。
因此,需要对减速器内部进行检查和维护。
这包括检查轴承、齿轮、油封等零部件的状态,并进行必要的更换和维修。
第四步:分析和处理外部干扰。
减速器振动问题可能还与外部干扰有关。
例如,设备周围的振动源、电磁干扰、液压冲击等都可能对减速器的振动产生影响。
在这种情况下,应采取相应的措施来减少或消除外部干扰,以降低减速器的振动水平。
第五步:采取振动控制措施。
如果以上步骤仍无法解决减速器的振动问题,可以考虑采取振动控制措施。
这包括使用减振器、增加结构刚度、优化设备设计等方法来减少振动的传递和影响。
总之,在解决减速器振动问题时,需要逐步进行观察、检查、分析和处理。
通过系统的分析和处理,可以找出振动问题的根本原因,并采取相应的措施来解决问题,确保减速器的正常运行。
轧钢机械振动故障的分析及诊断

轧钢机械振动故障的分析及诊断摘要:轧钢机械长时间在生产运行中会出现各种故障,对设备的稳定运行、正常生产和产品质量产生不利影响。
最常见的故障之一是机械振动,如不及时排除,将引发其他故障,导致轧钢生产质量、效率和安全性大幅度下降。
因此,必须加强对轧钢机振动原因的分析研究,对所出现的问题及时处理,以保证设备的稳定运行。
关键词:轧钢机械;振动故障;诊断引言对于轧钢企业生产运作来说,原材料由钢坯到成品的一系列生产过程都离不开轧钢机械的支持,在这些生产流程中,轧钢机械设备的生产时间较长,生产强度较大,这也代表着机械设备很容易会产生故障。
若轧钢机械出现故障问题时,技术人员不仅要根据原定的故障判断标准来分析设备的振动故障源,还要结合具体的振动数据分析机械设备出现振动故障的原因,确保故障问题能够针对其根源入手。
由于轧钢机械故障问题会影响轧钢生产的效率与质量,带来严重的经济损失,因此对轧钢机械振动故障的成因进行分析,重点分析不同类型故障及其形成原因,也有助于以后设备管理和故障维修提供参考依据。
1.轧钢机械设备的振动故障分类和原因分析1.1 转子异常振动转子的异常振动主要包括装配质量不足和轴弯曲。
在轧制机械设备中,如果转子装配不当,就会发生转子的异常振动,导致设备负荷和设备工作温度特别是轴承温度不能保持稳定。
最终会出现转子异常振动进一步加剧的现象,甚至会产生连接松动、脱落等问题,转子松动会进一步影响轴的稳定性,严重损坏转子和轴承,转子损坏时,频率难以保持稳定,进而导致设备损坏。
转子装配质量不过关容易发生在每次大修后的试运转阶段。
转轴弯曲也会造成转子异常振动,轧机的各级转轴的受力较大,冲击载荷也很大,容易过载造成弯曲,转轴弯曲后也会造成转子异常振动,转轴弯曲容易发生在停机待用期间。
1.2 电气故障引起的电机振动电机各相电流严重不平衡、转子条松动和定子线圈松动等电气原因都可能引起电机的振动。
电气故障除了引起电机振动,一般还伴随着电机发热增大和工作温度升高,进一步恶化电气故障,引起更严重的电气事故甚至造成电机烧坏。
基于轧钢机械振动故障的诊断研究

神经网络是一种模拟人脑神经元连接方式的计算模型,具有自学习和
自适应能力。将神经网络应用于轧钢机械振动故障诊断,可以有效地
识别和分类轧钢机械的故障。
02
神Hale Waihona Puke 网络模型采用前馈神经网络、深度神经网络、卷积神经网络等模型进行轧钢机
械振动故障诊断,通过训练神经网络模型,可以使其具有对振动信号
进行分类和预测的能力。
03
案例应用
某轧钢厂在生产过程中,电机驱动系统出现异常振动,通过采用基于
神经网络的振动故障诊断方法,成功地识别出发电机轴承故障,避免
了电机损坏和生产中断。
基于混合模型的振动故障诊断案例
案例概述
混合模型是将多种不同模型的优点结合起来,形成一种综合性的模型,以提高轧钢机械振 动故障诊断的准确性和鲁棒性。
自动化诊断
借助自动化技术和人工智能算法 ,实现轧钢机械振动故障的自动 诊断和分类。
智能维护
通过远程监测和自动化诊断,实 现轧钢机械振动故障的智能维护 和优化管理。
06
基于轧钢机械振动故障的诊断的应用 前景
在线监测与远程诊断的应用
实时监测和预警
通过在线监测和远程诊断系统,可以实时 监测轧钢机械的运行状态,及时发现振动 故障等潜在问题,并发出预警,从而避免 生产中断和设备损坏。
特征提取与信号分析
特征提取
从经过预处理的振动信号中,提取能够反映轧钢机械振动故障的特征,如频率、 振幅、相位等。
信号分析
对提取到的特征进行深入分析,如时域分析、频域分析、时频分析等,以全面了 解轧钢机械的振动状态和故障类型。
基于机器学习的故障检测模型设计
模型选择
根据实际需求和数据特点,选择适合的机器学习模型,如神经网络、支持向量机、决策树 等。
浅谈轧钢机械振动故障的诊断
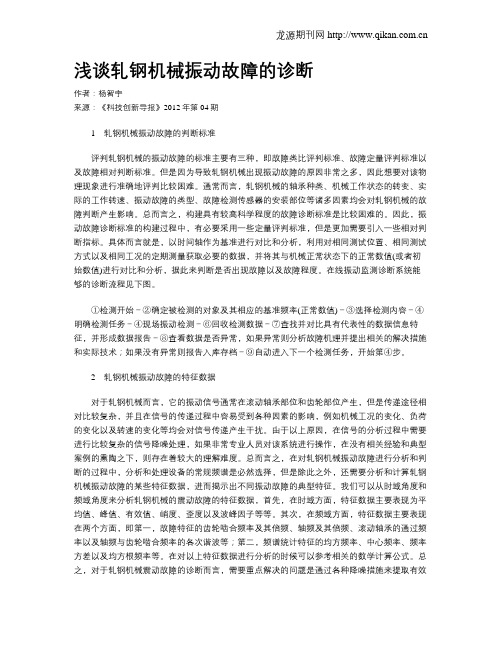
浅谈轧钢机械振动故障的诊断作者:杨智宇来源:《科技创新导报》2012年第04期1轧钢机械振动故障的判断标准评判轧钢机械的振动故障的标准主要有三种,即故障类比评判标准、故障定量评判标准以及故障相对判断标准。
但是因为导致轧钢机械出现振动故障的原因非常之多,因此想要对该物理现象进行准确地评判比较困难。
通常而言,轧钢机械的轴承种类、机械工作状态的转变、实际的工作转速、振动故障的类型、故障检测传感器的安装部位等诸多因素均会对轧钢机械的故障判断产生影响。
总而言之,构建具有较高科学程度的故障诊断标准是比较困难的。
因此,振动故障诊断标准的构建过程中,有必要采用一些定量评判标准,但是更加需要引入一些相对判断指标。
具体而言就是,以时间轴作为基准进行对比和分析,利用对相同测试位置、相同测试方式以及相同工况的定期测量获取必要的数据,并将其与机械正常状态下的正常数值(或者初始数值)进行对比和分析,据此来判断是否出现故障以及故障程度。
在线振动监测诊断系统能够的诊断流程见下图。
①检测开始-②确定被检测的对象及其相应的基准频率(正常数值)-③选择检测内容-④明确检测任务-④现场振动检测-⑥回收检测数据-⑦查找并对比具有代表性的数据信息特征,并形成数据报告-⑧查看数据是否异常,如果异常则分析故障机理并提出相关的解决措施和实际技术;如果没有异常则报告入库存档-⑨自动进入下一个检测任务,开始第④步。
2轧钢机械振动故障的特征数据对于轧钢机械而言,它的振动信号通常在滚动轴承部位和齿轮部位产生,但是传递途径相对比较复杂,并且在信号的传递过程中容易受到各种因素的影响,例如机械工况的变化、负荷的变化以及转速的变化等均会对信号传递产生干扰。
由于以上原因,在信号的分析过程中需要进行比较复杂的信号降噪处理,如果非常专业人员对该系统进行操作,在没有相关经验和典型案例的熏陶之下,则存在着较大的理解难度。
总而言之,在对轧钢机械振动故障进行分析和判断的过程中,分析和处理设备的常规频谱是必然选择,但是除此之外,还需要分析和计算轧钢机械振动故障的某些特征数据,进而揭示出不同振动故障的典型特征。
轧钢机械的振动监测与故障诊断

ห้องสมุดไป่ตู้
4 应严 密 监 视受 损 轴承 直 至更 换 .对 可疑 的 、 . 状
态 不 良的轴 承 , 颁 提供额 外 的监测 时 间 , 强监控 : 必 加
三 、 测 点 的 选 择
要 保证 信 号正 确传输 ,必 须正确 选择 测点 。
6 振 动监 测要 坚持 按 周 期进 行 ,及 时分 析数 据 , .
维普资讯
状态 监测与 技术 诊断
中 教俺工 3 阖 程 蚴.
锄 ⑩
磨
魏
鳓
■ 喻 颖
I 要】给 出轧 钢机 械设 备 的故 障诊 断方 法 ,即用 量化 的方法 来判 断轧钢 机械 的运转 状 态 ,并根 摘
据 监 测 数 据 判 断 故 障 的 部 位 、 原 因 ,为 轧 钢 机 械 设 备 的 检 修 提 供 依 据 。
【 美键词】轧钢机 械
振动 监测 故 障诊 断
现 代化 轧钢企 业连 轧 、半连 轧生 产 线所 用 的轧机 其 特 点为制 造 、安装 精度 高 ,对 操作 、维护 工人 素 质 要 求也 高 。为 了更好 地维 护和检 修轧 钢 机械 设备 .可
对 轧 机 的 重 点 部 位 进 行 动 态 振 动 监 测 , 记 录 每 天 酌 振
不 变 。 电 机 、 减 速
动烈 度 即可 ,即被测 点振 动速 度 的均 方根值 ,单 位 是 mⅡ s S 推荐在 1 — 0 H l 。IO / 0 10 0 z的宽频 带 内测量 。 把 故障 时所测 振值 与平 常监 测 数据或 I0 3 2推 S 27 荐 的 振 动 极 限值 作 比较 ,便 可 判 断 故 障 的 部 位和 原 因。另外 .振动 的大小 与被 测物 的尺 寸 、转速及 底 座 刚度等有关 。 过 强 的振 动 主要 有 三 个 原 因 : ( )机 械 松 动 ; 1 ( )不对 中 ; ( )失 去 平衡 。测点 选 择 正确 ,测 得 2 3
探析轧钢机械振动原因与故障处理王勇

探析轧钢机械振动原因与故障处理王勇发布时间:2021-08-17T06:30:35.477Z 来源:《中国科技人才》2021年第13期作者:王勇[导读] 本文主要围绕轧钢机械振动的原因和故障处理进行分析,以供参考。
江苏甬金金属科技有限公司江苏省南通市 226300摘要:轧钢机械在工作中常见的一些故障,一般都是由振动故障引起的,振动故障是否能够被及时发现和处理,直接关系到轧钢机械整体安全平稳作业。
本文主要围绕轧钢机械振动的原因和故障处理进行分析,以供参考。
关键词:轧钢机械振动;原因;故障处理一、轧钢机械常见振动故障类型及原因分析1、电机振动故障及原因电机装置是轧钢机械设备中的核心部分,其运行状态与轧钢设备生产效率和质量安全密不可分,如果电机装置运行状态异常很容易导致轧钢机械设备出现振动。
比如,电机如果自身发生故障导致运行失稳,或者电机装置安装过程中转子不符合对称标准,都会导致轧钢机失稳。
此外,如果电机中转子电压和定子电压处于不均衡状态,并且此时电机运行速度较高,设备就会出现轴系振动的情况,振幅过大甚至会引发元件断裂松动的情况。
2、滚动轴振动故障及原因如果轧钢机中滚动轴装置在使用中出现异常也容易导致设备发生振动,滚动轴装置是确保轧钢机设备正常使用的关键元件,如果滚动轴受到比较严重的磨损,或者自身发生形变,都会导致轧钢机在使用过程中出现比较明显的振动问题。
3、转子振动故障及原因由转子装置振动引发轧钢机械运行失稳的情况是比较常见的,其主要原因可归纳为以下几个方面,首先,轧钢机在实际运行期间其中转子元件是处于持续转动的状态,转子的转速还比较高,在这种高负荷运行的状态中很容易导致转子元件出现老化严重的情况,这样一来就容易造成振动。
其次,部分技术人员安装转子元件的时候没有遵守操作规范导致细节上出现失误,元件间隔距离和安装点位等都存在偏差,在这种情况下如果启动轧钢机械就容易导致设备振动,难以正常使用。
即使轧钢机设备正常启动之后没有出现比较明显的振动故障,转子元件的老化速度也会加快,设备使用一段时间就会出现振动故障。
轧钢机械振动故障诊断之浅见

轧钢机械振动故障诊断之浅见根据轧钢机械振动故障诊断的实际情况来看,在线振动监测诊断系统的合理应用,可以达到快速、准确、及时的效果。
因此,对轧钢机械振动故障诊断有比较深入的了解,对于保障轧钢机械的运行安全和功能等有着极大作用。
1 轧钢机械振动故障的判断标准在充分利用各种先进设备、技术对轧钢机械的运行情况进行检测的情况下,对当前轧钢机械振动故障的诊断情况进行全面分析来看,比较常用的判断标准主要有如下三种:一是故障类比评判标准;二是故障定量评判标准;三是故障相对评判标准,在保证轧钢机械振动稳定性、可靠性等方面有着极大作用。
在受到环境、经济、生产条件等多种因素影响的情况下,轧钢机械可能出现各种振动故障,因此,想要准确进行各种物理现象的评判有着比较大的难度。
目前,轧钢机械的工作状态、轴承种类、实际运转速度、故障检测传感器的安装部位、振动故障的类型等都会给故障判断带来不同程度的影响。
所以想要制定出科学的故障诊断标准,有着非常大的难度。
在实践过程中,振动故障诊断标准的科学构建,需要注重定量评判标准的运用,还要有机结合相对判断指标等,才能在以时间轴为基准的情况下,充分利用相同的测试方式、测试位置和工况定期测量等,获取相关数据,从而在对比与分析正常数值和测试数据等的基础上,确定轧钢机械的具体故障情况。
根据实践诊断情况来看,在线振动监测诊断系统的合理应用,主要包括如下九个流程:一是检测;二是确定被检测对象和基准频率;三是选择检测内容;四是明确检测任务;五是现场进行检测;六是回收相关数据;七是查找和对比重要的数据信息,并形成其报告;八是检查数据,如果存在异常情况,则需要对其进行可靠分析,才能制定出可行的解决措施和采用合适的技术,如果没有异常情况则需将报告存入档案库中;九是继续进行下一个对象的检测,按照第四步继续操作。
2 轧钢机械振动故障的特征数据分析在轧钢机械运用范围不断扩大、性能不断提高的过程中,一般情况下,振动信号是存在于齿轮部位和滚动轴承部位等位置,并且传递途径具有一定复杂性,信号很容易受到影响,如负荷变化、机械工况变化等,都会使振动信号受到一定干扰。
诌议轧钢机械振动故障诊断

诌议轧钢机械振动故障诊断在轧钢机械的工作过程中,振动故障是一种常见的故障类型。
对振动故障的分析及诊断对于保证轧钢机械的安全运行显得非常必要。
本文从研究轧钢机械的振动故障的判断标准出发,对振动故障特征数据的采集、分析处理及诊断作了进一步探讨。
希望对提高轧钢机械振动故障诊断的准确性,保障轧鋼机械安全高效运转有所帮助。
标签:轧钢机械;振动故障;故障诊断0 引言轧钢机械的振动故障对轧钢机械的正常安全运转有着基础性的影响。
在实际的工作中,现在较为普遍的故障诊断方法通常是在轧钢机械设备中安置检测和监控系统,通过及时发现和定位振动频率及幅度来判断振动故障所在,并通过振动数据的采集、频谱的分析来发现轧钢机械振动故障的规律,制定一系列对应的判断标准,从而指导轧钢机械的安全生产。
1 轧钢机械振动故障的判断标准在正式进行轧钢机械振动故障诊断时,要依据一定的故障判断标准,在具体的轧钢机械维护和管理中,一般引入定性和定量的方法对轧钢机械振动故障进行准确判断。
目前判断轧钢机械的故障标准一般有三种,即故障类比评判标准、故障相对判断标准及故障定量判断标准[1]。
引起轧钢机械振动故障的原因很多,要想对其进行准确的判断还较为困难,通常情况下,影响轧钢机械振动故障判断的原因有以下几种:一是机械工况的变化;二是机械实际的运行速度;三是故障类型;四是故障检测传感器安装设置。
因此,要实现对故障的科学诊断是很困难的,在实际的故障判断中除了参考一些量化标准,还要对一些相对指标进行判断。
因此,当前对轧钢机械振动故障的判断标准还引入了数据采集、频谱分析等方法,不仅提高了轧钢机械振动故障判断标准的有效性,还提升了轧钢机械振动故障判断标准的可行性。
2 轧钢机械振动故障的诊断流程在具体的轧钢机械振动故障诊断中,一般遵循以下流程:轧钢机械振动故障检测开始→确定要被检测的对象及其对应的基准频率(正常参数)→选择轧钢机械振动故障检测内容→明确轧钢机械振动故障的检测任务→对轧钢机械故障进行现场检测→回收轧钢机械振动故障的检测数据→对轧钢机械振动故障数据信息进行特征分析,形成数据报告→查看数据是否异常,作出轧钢机械振动的故障判断[2]。
减速器故障诊断方法

减速器故障诊断方法1. 嘿,听好了啊!观察法可是个好办法哟!就好比你看到一个人脸色不对,就能猜到他可能不舒服一样。
看看减速器有没有奇怪的响声、异常的振动,那很可能就是出问题啦!比如咱厂里那台减速器,有次就发出了“嘎吱嘎吱”的声音,这不就赶紧去检查啦!2. 还有啊,温度检测法呢!就像人发烧了肯定身体有状况呀。
用手摸摸减速器,或者拿温度计测测,温度高得不正常,那可就得小心啦!上次我隔壁车间的那台减速器就烫得吓人,立马就知道不对劲啦!3. 朋友们,别忘了听声音诊断法呀!减速器正常工作的声音和有问题时的声音那差别可大了去了!就好像健康人说话和生病时说话能一样吗?有回我听到减速器发出的声音很沉闷,果然是出问题啦!4. 哇塞,振动检测法也超重要的呀!就像地震了能感觉到大地在晃动一样明显。
如果减速器的振动不对劲,那肯定有毛病呀!咱那次大检修前,那台减速器的振动就很奇怪呢!5. 你们知道吗,油液分析法也很管用呢!这就跟检查血液似的。
看看减速器里的油液状况,有没有杂质、变质啥的。
有回发现油液特别脏,哎呀,不好,减速器可能有麻烦了!6. 诶呀,无损检测法也不能小瞧啊!这可是很高级的呢,不用拆减速器就能发现问题哟。
就像不用打开盒子就能知道里面东西好坏一样神奇吧?上次他们用这个方法,很快就找出了减速器里的一个小裂缝。
7. 别忘了还有频谱分析法呢!这就像是给减速器做个全面的身体检查,通过分析频谱来判断问题。
我们车间那台重要的减速器有阵子不对劲,就是靠这个方法找出问题所在的呀!8. 还有啊,模型分析法也很牛的呀!就好像给减速器建了个模型一样。
通过对比正常和异常的模型,就能知道哪里出问题啦。
之前有个很难发现的毛病,就是靠这个找到的呢!9. 最后啊,经验判断法也不能少呀!老工人的经验那可宝贵了。
他们就像医生一样,一看一听就知道减速器大概是啥情况呢!咱厂的老李师傅,那经验,厉害得很!总之,这么多方法,大家可得好好记住,遇到减速器故障就能派上用场啦!。
薄板坯连铸连轧设备的故障诊断与排除方法

薄板坯连铸连轧设备的故障诊断与排除方法薄板坯连铸连轧设备在钢铁行业中扮演着重要的角色,其主要作用是将钢水连铸成坯料后,经过连轧机组进行成品板材的加工。
然而,由于设备长时间运行,以及受到各种环境和工艺条件的影响,故障难免发生。
本文将介绍薄板坯连铸连轧设备常见故障的诊断与排除方法,帮助企业快速定位并解决设备故障,提高生产效率和质量。
一、设备无法启动或停机故障的诊断与排除1.检查电源供应是否正常:查看电源线路是否正常连接,检查主电源开关和控制电源开关是否接通。
2.检查主控系统状态:观察主控屏幕是否正常工作,若显示正常,则检查系统软件是否正常运行;若显示异常,则进行软件重启或系统更新。
3.检查安全保护装置:检查安全保护装置是否触发,如防火门、紧急停机按钮、过载保护开关等,及时修复或更换受损部件。
4.检查机械部件:检查各传动部件是否受损或过热,若有异常情况,及时进行维护和更换。
二、设备温度过高或过低故障的诊断与排除1.检查润滑情况:检查设备的润滑系统是否正常工作,润滑油是否充足,若不足则及时添加;同时检查润滑油管路是否通畅。
2.检查散热器:检查散热器是否受到阻塞或堵塞,导致冷却不良。
若发现问题,清洗或更换散热器。
3.检查冷却水供应:确保冷却水供应充足,检查水泵和管道是否正常工作。
4.检查温度传感器:检查温度传感器是否准确,如发现异常,校准或更换传感器。
三、设备振动或噪音问题的诊断与排除1.检查设备基础:检查机器基础是否牢固,如有松动或破损,及时修补。
2.检查传动部件:检查各传动部件是否安装正确,是否损坏,需修复或更换受损的部件。
3.检查润滑情况:确保各润滑点的润滑油充足、清洁,如有异常,进行必要的维护和清洁。
4.检查轴承:检查轴承是否受损,需要更换的轴承及时更换。
同时,注意调整轴承的预紧力。
四、设备控制系统故障的诊断与排除1.检查控制电源:检查控制电源是否正常供电,如有异常,检测电路并修复。
2.检查输入输出模块:检查输入输出模块是否正常工作,如有模块损坏,则更换受损的模块。
轧机液压系统的振动诊断

轧机液压系统的振动诊断摘要:主要介绍了轧机中的液压系统的振动的类型、原因,以及抑制液压系统振动的对策,对轧机的液压系统的振动故障的避免和解决作了积极的探索.关键词:轧机;液压;振动故障一、轧机液压系统的故障诊断方法对于CSP热轧机液压系统而言,由于液压管道内油液处于流动状态,液压元件的内部情况和外部密封件的损坏情况不易被察觉到,这给工作人员进行诊断维修带来了巨大的困难。
尤其当机械、液压、电气等故障交织在一起时,极难诊断。
液压系统故障诊断常用的方法有主观诊断法、基于数学模型与信息处理诊断方和智能诊断法。
1.1主观诊断法主观诊断法是对液压设备维修经常采用的方法,主要依靠研究人员的感官和简单的诊断仪器,采取轧机液压系统振动抑制措施应该从两个方面着手:一方面在液压系统设计和相关机械结构设计时,要采取有效的技术措施进行防范;另一方面,在液压系统和相关机械系统安装和运行过程中,要严格按照操作规程进行安装和操作并定期进行维护保养。
1.1.1尽量选择运转平稳、噪声低的电动机、液压泵,使用弹性联轴器进行连接.安装调试时,确保具有良好的同心度。
1.1.2尽可能采用立式油泵电机组,把泵浸入油中,并在泵组安装面加橡胶垫以及泵出口安装液压软管减振。
1.1.3合理设计油箱容积,保证在吸油后最低液面时有足够油量,并设置隔板将吸、回油管隔开。
1.1.4按设计规范安装管夹,减少管路急转弯,并设置具有一定刚度的管路支架,将管路卡牢,以及在管路的各高点处设置具有排气装置的测压接头。
1.1.5做好管路连接处的密封设计,消除泄露。
1.1.6在容易产生压力冲击处设置蓄能器。
1.1.7采取适当的动态补偿措施,维护系统稳定。
1.1.8定期检查管路接头的密封性能,对油液进行抽样检测结合液压专家的实践经验,判断产生故障的部位以及原因,并提出故障排除的方法。
主观故障诊断法分为感官诊断法、逻辑逼近分析法、参数测量比较法、方框图分析法以及鱼刺图分析法等。
轧钢机械振动故障的诊断

轧钢机械振动故障的诊断摘要:伴随我国当前工业经济发展速度进一步加快,重型机械设备的使用量越来越大,也给重型轧钢机械设备的使用性能提出了更高的要求。
轧钢主要指的是应用不断旋转的轧辊产生的压力来对钢锭钢胚的形状进行改变的整个过程,一定要有效的监管和诊断轧钢机械设备,让机械设备的运行效率和质量大幅度提高,让设备的使用寿命延长,本文重点对轧钢机械设备振动故障特征进行分析,并且深入讨论振动故障的诊断流程和判断标准,对轧钢机械设备的性能进行改良,确保设备能够高效、科学、稳定的运行。
关键词:轧钢机械;振动故障;数据采集;故障诊断引言一旦振动故障的情况在轧钢机械运行的过程中发生,就会影响轧钢机械的生产质量,同时也会对其的安全性造成影响,虽然这种影响看似非常普通,但实则非常重要,在轧钢机械生产和运行的过程中,振动故障也是需要加强重视的重要部分,同时也是对维护设备工作的重点内容。
在监测和诊断振动故障上,主要可以通过安装监测系统在轧钢机械设备的方法来实施,严格的监控振动幅度,以此来保证准确、及时的对振动故障发生的原因进行判断。
在诊断和处理轧钢机械振动故障时,要对判断的标准进行不断的优化,同时做好数据采集的工作,之后全面的对频谱进行分析,只有按照上述这样的方法,才能够确保准确的对振动发生的故障进行诊断,有效的维护和控制轧钢机械生产活动。
1轧钢机械振动特征的重要性1.1能够对轴承的磨损情况进行动态的掌握在轧钢机械当中,磨损是非常常见的一种失效形式,可能会导致径向间隙出现变化,进而造成传感器缝隙的电压改变,加速度传感器无法对这种变化进行准确的判断,导致无法动态监测转轴和探头之间的空隙。
某些转轴的表面带有毛刺,系统会进行相应的滤波处理将干扰排除,因为出现一些个别的振动,可能会导致晃动等特殊情况,因此以间隙电压变化为判断依据通常条件下使用的是间隙的平均值。
1.2对轴承转速进行动态观测特征频率指的主要是故障的频率,由于在故障信号分析的过程中,是随机选用的因子,不可能和理论计算出来的频率完全一致。
轧机主减速机振动测试与故障分析
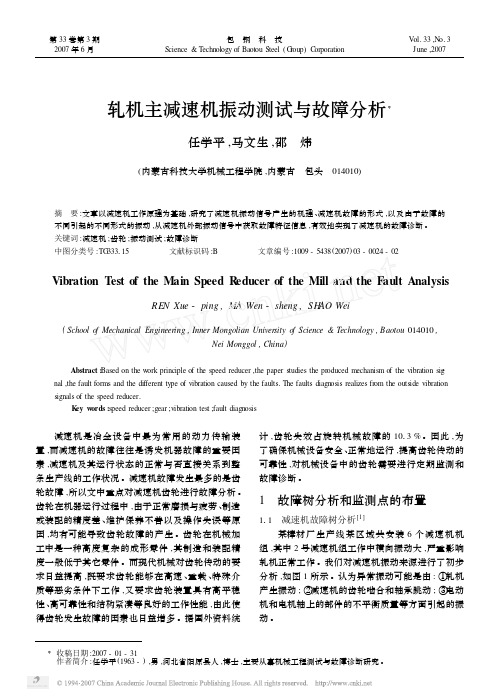
轧机主减速机振动测试与故障分析Ξ任学平,马文生,邵 炜(内蒙古科技大学机械工程学院,内蒙古 包头 014010)摘 要:文章以减速机工作原理为基础,研究了减速机振动信号产生的机理、减速机故障的形式,以及由于故障的不同引起的不同形式的振动,从减速机外部振动信号中获取故障特征信息,有效地实现了减速机的故障诊断。
关键词:减速机;齿轮;振动测试;故障诊断中图分类号:TG333115 文献标识码:B 文章编号:1009-5438(2007)03-0024-02 Vibration Test of the Main Speed R educer of the Mill and the F ault AnalysisREN Xue-ping,MA Wen-sheng,SH AO Wei(School o f Mechanical Engineering,Inner Mongolian Univer sity o f Science&Technology,Baotou014010,Nei Monggol,China) Abstract:Based on the w ork principle of the speed reducer,the paper studies the produced mechanism of the vibration sig2 nal,the fault forms and the different type of vibration caused by the faults.The faults diagnosis realizes from the outside vibration signals of the speed reducer. K ey w ords:speed reducer;gear;vibration test;fault diagnosis 减速机是冶金设备中最为常用的动力传输装置,而减速机的故障往往是诱发机器故障的重要因素,减速机及其运行状态的正常与否直接关系到整条生产线的工作状况。
减速机振动的原因及处理方法

减速机振动的原因及处理方法减速机在运转中剧烈振动,并发出较大噪声。
有时因振动厉害,使机体产生微裂纹,并由此扩展为裂缝,导致减速机漏油和机壳报废。
振动剧烈,还会破坏减速机正常工作状态,导致基础失效、地脚螺栓断裂、齿面胶合、齿轮崩齿、齿圈移位、齿轮轴断裂、轮辐辐板开焊、轮辐损坏、轴承损坏、柱销断裂、运转不平稳等恶性故障。
(1) 齿轮方面故障及处理方法①齿轮的齿面磨损、胶合、点蚀、磨偏和出台(尤其是小齿轮转速快极易磨损)引起减速机振动。
处理方法:及时更换严重磨损的齿轮。
一般可采用反向运行方法解决齿面严重胶合。
②各齿轮的啮合面接触不良和受力不均,使齿轮的轴向窜动频繁,发生轮齿断裂或齿圈断裂,以及轮辐裂纹等,引起减速机振动。
处理方法:更换坏损件;调整齿圈与轮辐门配合;更换齿面磨损超限的齿轮;调整轴承间隙;改善齿轮润滑等。
③高速轴和中速轴的滑键磨损出台,轴上的小齿轮联接螺栓有松动或断裂等引起减速机振动。
处理方法:更换滑键和已断螺栓,紧固松动螺栓。
④齿轮加工粗糙及轴与轴承的磨损,在正常运转中出现齿圈非工作面受力,引起减速机振动。
处理方法:更换符合加工精度和粗糙度要求的零部件;撤换已磨损的轴与轴承。
⑤齿轮与轴的配合过盈量大,使得轴在配合处断裂引起减速机振动。
处理方法:更换断轴,调整齿轮与轴的配合过盈量。
⑥齿轮与轴的轴孔配合公差如孔过大时,造成齿轮和轴不同心,或者齿轮与轴装配不当产生松动现象,引起减速机振动。
处理方法:调整齿轮与轴的轴孔配合公差;精心装配,防止松动。
⑦输出轴大齿轮的轮心与齿圈松动,侧压板活动或压板螺栓有松动或折断,以及大齿轮的静平衡差或不平衡,引起减速机振动。
处理方法:紧固轮心与齿圈;紧固压板螺栓,更换折断螺栓;改善大齿轮平衡状态。
对D110A型减速机采用现场不解体车削平衡轮轨道面,消除疲劳层和凹坑,增加定位圈厚度来补偿轨道面,解决轨道面出现的疲劳层和回坑。
(2) 轴承方面故障及处理方法①轴承磨损或轴承间隙过大,引起减速机振动。
- 1、下载文档前请自行甄别文档内容的完整性,平台不提供额外的编辑、内容补充、找答案等附加服务。
- 2、"仅部分预览"的文档,不可在线预览部分如存在完整性等问题,可反馈申请退款(可完整预览的文档不适用该条件!)。
- 3、如文档侵犯您的权益,请联系客服反馈,我们会尽快为您处理(人工客服工作时间:9:00-18:30)。
2 8日至 2 0 0 8年 1 2 l 0月 7E相继发生 1 9次前瓦轴 ( 1轴瓦 ) 振
…
幅值 突增 ,最 大增 至 Xl2 1 Y = 1 ̄ ( =1 m、 1 24 m 轴振动标准 : ≤
81 0 m为优 良, 6  ̄ x ≤15 m机组 报警 , 0 m机 组跳车 ) 0 8 ≥3 0 。2 0 年 1 0月 2 5日, 经检查该机组运行参数历史 曲线发现 , 机组调峰
测点 2的振 动 值 。
倍谐频 幅值较大 ,而且在齿轮啮合频率及其谐频两边都 出现了
输入轴 的转频 , 6 8 z 即 . H 的转 频 , 5 边带 的幅值与啮合频率 比较 ,
相对较高 。 1 齿轮啮合频率 的两边 , 在 倍 边带族甚至比齿轮 啮合 频率还要高 。 这些现象判 断齿 轮齿 面磨损严重 , 从 齿轮渐开线齿
2 o o 40 0
Hz
{
10 .
05 00 . O 60 0 80 0 l0 00
的迹 象 。
a水平 方 向 )
2 0 1 5
时, 随着 机 组 负 荷 的 变 化 , 组 轴 振 动 幅值 、 向位 移 量 均 有 明 机 轴 显变 化 。 2振 动原 因分 析 . 1轴 瓦 振动 特 点 如 下 :
:
发 电 机
图 1 汽 轮 发 电机 组 构 成 简 图
() 2 轴振幅值 由小到大再 由大到小 , 动幅值的变化时间大 振
20 0 9年 4月份 , 现场巡检 中发现第 三机 架减速箱振动过 在 大, 减速箱输入 轴轴承处振 动值 较大 , 并伴 随着很 大的轰 鸣声 , 脚下有非 常明显的振感 , 于是 , 随后 的几天 内 , 在 对该减 速箱进 行 了重点监测 。 1 表 列出了维修前后轧制 3 0 14合金时测点 1和
的齿轮 啮合频率处 ,其幅值非常大 ,相对于测点 l 水平方 向来
说, 其振动幅值在 其 3 以上。为了解释这一现象 , 倍 对上下箱体
进行振动测试 , 现振动值 以箱体 的结合 面为分界线 , 发 振动烈度 相差较大 , 因此 , 造成垂 直方 向振动值大 的原因 , 可能是 由于 很 箱体 的紧 固螺栓预紧力不够。而且在齿轮啮合频率 的两边有很 明显的边带族 , 明齿轮有偏心或磨损的现象 , 说 以及齿轮有磨损
连 轧机减速箱振动故ห้องสมุดไป่ตู้诊 断
王光平
摘要 对热轧连轧机 减速 箱振动 大进行监测 , 根据 时域频谱 图和振动数据 进行诊 断分析 , 出原 因所在并采取相应措施 , 找 保证
连轧机 减速箱 振动 分 析 B
设 备 的 正 常运 行 。 关键词 中图分 类 号 T 1 31 H 1. 文献标识码
廓 已经 受 到 严 重 的破 坏 , 面 可 能点 蚀 严 重 。 齿
图 2为 20 0 9年 4月一次监测的测点 1 频谱 图 ,从 图 2 水 a 平方 向可 以看 出,齿轮 1 啮合频率为 2 38 H ,其 2倍 和 3 倍 0. z 6
20 . 15 .
从图 2 b垂直方向的频谱来看 , 其振动能量主要集 中在 1 倍
速 箱一 级 减 速 , 高速 齿轮 齿数 为 3 个 , 速 齿 轮 齿数 为 17个 , 1 低 1 分齿 箱 两 齿 轮 齿数 为 2 个 ; 入 和 输 出联 轴器 均 为 鼓 形齿 齿 轮 8 输 图 1 第 三 机架 传 动 及 测 点 布 置示 意 图 联轴 器 。测 点 1 于高 速 输 入 轴 , 点 4位 于减 速 箱 输 出轴 。 位 测
B
1轴瓦 2轴 瓦 3袖瓦 4 瓦 嗨6
中图 分类 号
T 1. H131
文献 标 识 码
1 组 运行 中存 在 的 问题 . 机 大庆 石 化 分 公 司热 电 厂 5 汽 轮 发 电 机组 为 5 MW 抽 汽 凝 0 汽式 汽 轮 机组 ( 1 , 号 C 0 9/3 图 )型 5 — 01 。该 机 组 于 20 0 8年 4月
叶轮转频 ( 2 、 图 ) 速度 峰值 44 mms 说 明机组主油 泵 出现 问 .9 /,
题。 同时频谱 图出现碰摩频率 ( 3 C = 22 H 、 2 2 H )速 图 , 1 1. zC = 5 z , 5
图 设 嗣 与 修 20 4 置 理 维 0 № 1
一
.
. .
盔
盔 蓬 立
维 修 人 员 面对 的一 个 重要 课 题 。
/I 齿 } 箱 j 分
减 速
箱
一
一
联轴 器
2
连轧机第三机架传 动及测点布置如 网 1 所示 ,由两 台直流 电机 串联 , 每台电机功率 19 .k 转速 2 0/ i/ 0/ i; 4 1 W, 4 5r n5 r n 减 m 0 m
汽 轮发 电机 组振 动 分 析及 处 理
张洪奎 孙 晓霞
摘要 针对汽轮机组(0 w) 5 M 长期存在 的轴 瓦振动 问题 , 进行故障诊 断及频谱分析 , 出振动故障原因, 找 采取 了有效措施 , 最终
解决了汽轮机组振动 问题 , 保证 了热电厂设备 的安全 、 平稳 、 长周期 、 满负荷运行。 关键词 汽轮机组 故 障诊断 频谱分析
热 轧 连 轧机 在 产 品 的 轧 制 和新 产 品 的 开发 方 面 ,比如 印刷
行业使用 的铝制印刷版 , 以及高速列车上使用 的高强度 的 5 8 03 铝合金等 , 都起着举足轻重的作用 。因此 , 对于连轧机的状态监 测尤为重要 , 如何保证设备的正常运转和铝产品的正常轧制 , 是
约 在 1— 0 n 5 3mi。
() 3 每次发生轴振突增的周期不定 , 幅值一次比一次大。
从 采 集 的频 谱 分 析 , 谱 图 中 出 现 7 ( 1 3 0 z主 油 泵 频 ×C = 5H )
() 1轴振幅值 突增都发生于机组调峰及调整负荷 、 抽汽量调
整, 主蒸汽压力及其变化时。