熔铝炉烟气余热梯级利用系统
焙烧炉烟气余热回收及利用技术

2023年 5月下 世界有色金属17冶金冶炼M etallurgical smelting焙烧炉烟气余热回收及利用技术罗振勇(贵阳铝镁设计研究院有限公司,贵州 贵阳 550081)摘 要:本文介绍了一种氧化铝厂气态悬浮焙烧炉烟气余热回收以及将回收的烟气余热用于氧化铝生产的节能新技术。
本技术采用喷淋冷却塔对高温焙烧炉烟气进行喷淋冷却,通过直接换热方式,烟气中的水蒸汽释放其潜热,大部分热量回收进入喷淋循环水中。
升温后的循环水再与经过真空闪蒸后的蒸发原液进行热交换,使真空闪蒸后的原液温度升高,温度升高后的蒸发原液再返回进行真空闪蒸,最终蒸发原液浓度得到提高,降低了蒸发工段低压蒸汽消耗,节约了氧化铝生产的综合能耗。
本文对焙烧炉烟气余热回收及利用技术进行了热平衡计算和运营成本估算,分别从技术和经济角度分析了本技术应用于氧化铝生产企业的可行性。
关键词:焙烧炉;烟气余热;水蒸汽潜热;回收及利用中图分类号:X706 文献标识码:A 文章编号:1002-5065(2023)10-0017-3The Recovery and Utilization of Waste Heat Technology for Calciner Flue GasLUO Zhen-yong(Guiyang Aluminium and Magnesium Design and Research Institute Co.,Ltd.,Guiyang 550081,China)Abstract: This paper introduces a new energy saving technology of gas suspension calciner in alumina plant, this technology can recycle the waste heat of flue gas and apply it to production of alumina. The water cooling tower was used to spray cooling the high temperature flue gas of calciner by direct heat exchange. The latent heat was discharged from water vapor in flue gas, and the heat was recycled into spray water. The warming recycled water transfer heat to spent liquor after vacuum flashing. The concentration of spent liquor was higher than before. And then the low pressure steam consumption was lower than before, the comprehensive energy consumption of alumina production was saved. The heat balance calculation and operating cost estimation for the technology were provided in this paper. The feasibility which the technology was applied to alumina industries was analyzed from technical and economic point of view.Keywords: Calciner; Waste Heat of Flue Gas; Latent Heat of Water Vapor; Recovery and Utilization收稿日期:2023-03作者简介:罗振勇,男,生于1982年,满族,辽宁开原人,硕士研究生,工程师,研究方向:氧化铝生产工艺设计及研究。
211169313_铝熔炼炉蓄热式燃烧系统节能改造项目
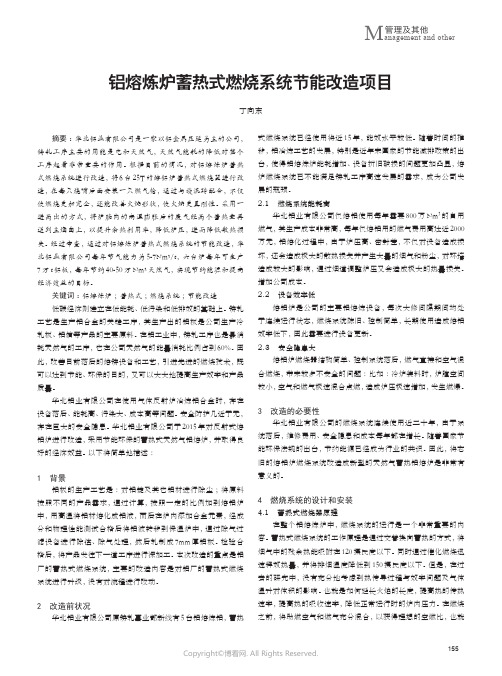
管理及其他M anagement and other 铝熔炼炉蓄热式燃烧系统节能改造项目丁向东摘要:华北铝业有限公司是一家以铝金属压延为主的公司,铸轧工序主要的用能是电和天然气,天然气能耗的降低对整个工序起着非常重要的作用。
根据目前的情况,对铝熔炼炉蓄热式燃烧系统进行改造,将6台25T的熔铝炉蓄热式燃烧器进行改造,在每只烧嘴后面安装一只燃气枪,通过与旋流砖配合,不仅使燃烧更加完全,还能改善火焰形状,使火焰更具刚性。
采用一进两出的方式,将炉膛内的高温膨胀后的废气经两个蓄热室再送到主烟囱上,以提升余热利用率,降低炉压,进而降低散热损失。
经过审查,通过对铝熔炼炉蓄热式燃烧系统的节能改造,华北铝业有限公司每年节气能力为5-7Nm³/t,六台炉每年可生产7万t铝板,每年节约40-50万Nm³天然气,实现节约能源和提高经济效益的目标。
关键词:铝熔炼炉;蓄热式;燃烧系统;节能改造低碳经济则建立在低能耗、低污染和低排放的基础上。
铸轧工艺是生产铝合金的关键工序,其生产出的铝板是公司生产冷轧板、铝箔等产品的主要原料。
在铝工业中,铸轧工序也是最消耗天然气的工序,它在公司天然气的能量消耗比例占到60%。
因此,改善目前落后的熔铸设备和工艺,引进先进的燃烧技术,既可以达到节能、环保的目的,又可以大大地提高生产效率和产品质量。
华北铝业有限公司在使用气体反射炉冶炼铝合金时,存在设备落后、能耗高、污染大、成本高等问题。
安全防护几近于无,存在巨大的安全隐患。
华北铝业有限公司于2015年对反射式熔铝炉进行改造,采用节能环保的蓄热式天然气铝熔炉,并取得良好的经济效益。
以下将简单地描述:1 背景铝板的生产工艺是:对铝锭及其它铝材进行除尘;将原料按照不同的产品需求,通过计算,按照一定的比例加到熔铝炉中,用高温将铝材熔化成铝液,而后在炉内添加合金元素,经成分和物理性能测试合格后将铝液转移到保温炉中,通过除气过滤设备进行除渣、除气处理,然后轧制成7mm厚铝板。
熔铝炉烟气余热利用研究

民营科技2018年第9期科技创新熔铝炉烟气余热利用研究王立坤(哈尔滨松江电炉厂有限责任公司,黑龙江哈尔滨150000)要想提高熔铝炉的工作效率,我们就必须要不断提高熔铝炉燃料的利用效率,企业必须要建立余热资源回收系统,这样熔铝炉的烟气的利用效率才能得到提升。
在对熔铝炉烟气进行研究的时候,我们可以利用助燃空气以及烟气预热燃料、铝锭来对熔铝炉的烟气进行回收,这样企业节能减排的目标才能得到实现,熔铝炉烟气的回收效率才能得到提升。
对某企业容量为2t的熔铝炉燃烧系统进行测试,结果显示,熔铝炉炉顶出口烟气温度为1060℃。
在投入铝锭量为460kg/h,成品铝粉量为452kg/h时,熔铝炉炉顶排出烟气的流量达1072m3/h,烟气带走的热量比例高达67%,占热损失的82%,造成熔铝炉能量大量损失,铝粉生产能耗高。
为此,针对小型熔铝炉烟气余热回收利用进行研究,以达到降低油耗,节约能源,提高能量利用效率的目的。
1烟气余热回收利用方式1.1高温烟气余热回收。
一般情况下企业熔铝炉的温度都是非常高的,这对熔铝炉回收造成的影响是非常大的,但是这也在一定程度上标明烟气其本身所含有的能量是非常高的,在对高温烟气进行回收的施时候,我们采用的一般都是余热回收系统来对其进行回收,这样就可以将熔铝炉烟气能量最大程度上的转化为机械能,企业的经济效益和工作效率才能得到提升。
如果熔铝炉烟气的温度高于600℃的话,那么熔铝炉的烟气体积大概就在5000m3/h左右,这些烟气在进行处理的时候主要被用余热锅炉块进行回收,其可以产出非常压力非常高的热水和蒸汽,在企业生产的过程中可以用热交换器来对其进行转换,让其产生热空气或者是热水,也可以利用燃气轮机来进行发电,这样不尽可以提高熔铝炉燃料的利用效率,同时还可以降低企业生产的成本。
企业还可以将余热锅炉中产生的能量转化为压力非常高的蒸汽,将这些蒸汽应用在水泵、拖动压缩机等机械设备中,这样不仅可以提高企业自身的经济效益。
铝冶炼烟气净化余热利用技术的探讨
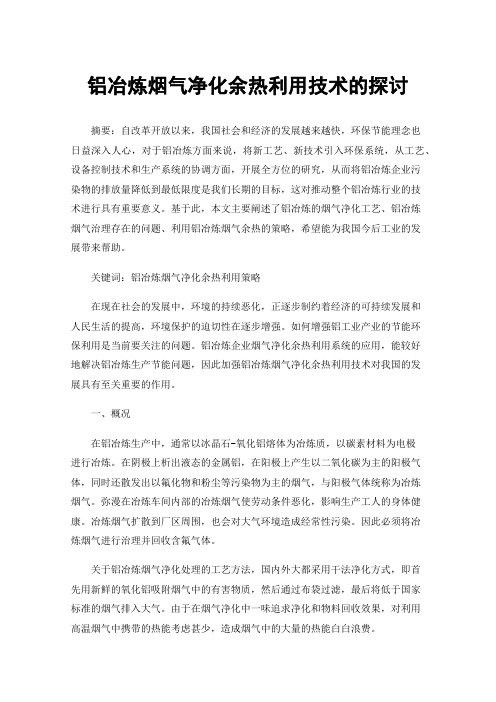
铝冶炼烟气净化余热利用技术的探讨摘要:自改革开放以来,我国社会和经济的发展越来越快,环保节能理念也日益深入人心,对于铝冶炼方面来说,将新工艺、新技术引入环保系统,从工艺、设备控制技术和生产系统的协调方面,开展全方位的研究,从而将铝冶炼企业污染物的排放量降低到最低限度是我们长期的目标,这对推动整个铝冶炼行业的技术进行具有重要意义。
基于此,本文主要阐述了铝冶炼的烟气净化工艺、铝冶炼烟气治理存在的问题、利用铝冶炼烟气余热的策略,希望能为我国今后工业的发展带来帮助。
关键词:铝冶炼烟气净化余热利用策略在现在社会的发展中,环境的持续恶化,正逐步制约着经济的可持续发展和人民生活的提高,环境保护的迫切性在逐步增强。
如何增强铝工业产业的节能环保利用是当前要关注的问题。
铝冶炼企业烟气净化余热利用系统的应用,能较好地解决铝冶炼生产节能问题,因此加强铝冶炼烟气净化余热利用技术对我国的发展具有至关重要的作用。
一、概况在铝冶炼生产中,通常以冰晶石-氧化铝熔体为冶炼质,以碳素材料为电极进行冶炼。
在阴极上析出液态的金属铝,在阳极上产生以二氧化碳为主的阳极气体,同时还散发出以氟化物和粉尘等污染物为主的烟气,与阳极气体统称为冶炼烟气。
弥漫在冶炼车间内部的冶炼烟气使劳动条件恶化,影响生产工人的身体健康。
冶炼烟气扩散到厂区周围,也会对大气环境造成经常性污染。
因此必须将冶炼烟气进行治理并回收含氟气体。
关于铝冶炼烟气净化处理的工艺方法,国内外大都采用干法净化方式,即首先用新鲜的氧化铝吸附烟气中的有害物质,然后通过布袋过滤,最后将低于国家标准的烟气排入大气。
由于在烟气净化中一味追求净化和物料回收效果,对利用高温烟气中携带的热能考虑甚少,造成烟气中的大量的热能白白浪费。
二、铝冶炼的烟气净化工艺2.1工艺流程干法净化工艺流程从功能上主要包括冶炼槽集气、吸附反应、气固分离、氧化铝输送、机械排风五个部分。
冶炼槽产生的烟气经密闭集气罩收集,通过直径600m。
第三代烟气余热梯级利用方案的选择与应用

2020.2 EPEM93随着国家节能形势日益严峻,国家发改委在《煤电节能减排升级与改造行动计划(2014-2020)》中要求:全国新建燃煤发电机组平均供电煤耗低于300g/kWh ;到2020年现役燃煤发电机组改造后平均供电煤耗低于310g/kWh,其中现役60万千瓦及以上机组(除空冷机组外)改造后平均供电煤耗低于300g/kWh。
经调研,目前在役的600MW 等级以下火电机组除部分通过开拓供热提高热电比的方式降低煤耗外,其余大部分电厂都实施了不同程度的节能技术改造,其改造遵循改善设备技术指标,提高机、炉侧效率和优化系统运行方式的原则。
在具体的技术改造方面,又以给水泵变频升级改造、汽轮机通流改造、汽轮机冷端优化和烟气余热利用改造为主流技术路线[1,2]。
1 改造机组基本情况改造机组容量328.5MW,配套意大利进口的亚临界压力控制循环锅炉。
锅炉型式:亚临界参数、一次中间再热、单炉膛、平衡通风,固态排渣,露天布置,全钢构架、控制循环汽包炉。
运转层以下锅炉钢架范围内封闭,炉顶设大罩壳。
脱硫系统采用的工艺为石灰石—石膏湿法脱硫工艺,一炉一塔布置方式。
锅炉改造前在空预器出口至除尘器入口间的烟道内安装有低温省煤器系统,利用烟气余热加热凝结水,低温省煤器凝结水取自#4低加进口,回水至除氧器(表1、表2)。
2 改造机组存在的主要问题由于锅炉实际燃用煤种偏离设计煤种,导致锅第三代烟气余热梯级利用方案的选择与应用神华国能天津大港发电厂有限公司 董 帅摘要:在回收热量一定的情况下,第三代烟气余热梯级利用系统能够最大限度的发挥节能效果,是烟气余热利用节能改造的首选技术方案。
关键字:烟气;余热利用;第三代;空预器旁路;给水加热器炉空预器出口的排烟温度远远高于原设计值,使锅炉排烟温度冬季满负荷工况下达到150℃,夏季基本达到160℃左右,严重影响了机组整体经济性。
另外,加装的低温省煤器布置空间不合理,磨损严重,泄露频繁发生,投入率及经济性均不能保证。
铝熔炉烟气余热回收系统设计与试验
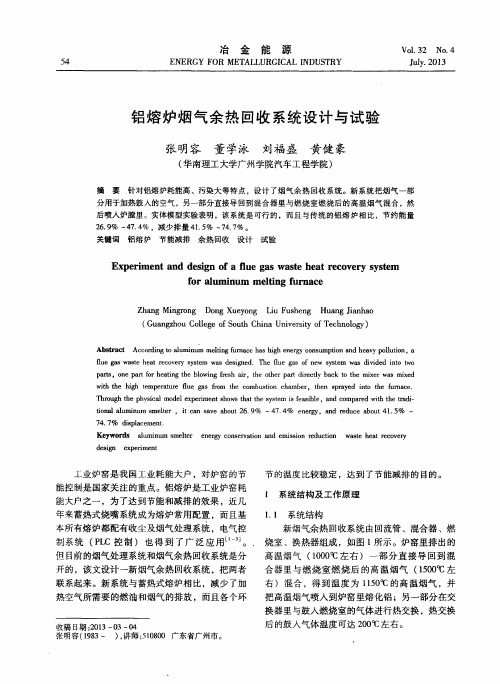
上 业炉窑 是我 国工 业耗 能大户 ,对炉 窑 的节
节 的温度 比较 稳定 ,达 到 了节 能减排 的 目的 。 1 系统 结构 及工作原 理
能控制 是 国家 关 注的重 点 。铝 熔炉 是工业 炉窑耗 能大户 之一 ,为 了达到 节能 和减排 的效果 ,近几 年来蓄 热式烧 嘴 系统 成 为熔炉 常用 配置 ,而且基 本所有 熔炉都 配有 收尘 及烟气 处理 系统 ,电气控 制 系统 ( P L C控 制 ) 也 得 到 了 广 泛 应 用 ¨ 。j 。
Ab s t r a c t A c c o r d i n g t o Mu mi n u m me l t i n g f u r n a c e h a s h i g h e n e r g y e o n s u mp t i o n a n d h e a v y p o l l u t i o n, a l f u e g a s w st a e h e a t r e c o v e r y s y s t e m w a s d e s i g n e d .T h e l f u e g a s o f n e w s y s t e m wa s d i v i d e d i n t o t w o p a r t s ,o n e p a r t f o r h e a t i n g t h e b l o w i n g f r e s h a i r ,t h e o t h e r p a r t d i r e c t l y b a c k t o t h e mi x e r w a s mi x e d it w h t h e h i g h t e mp e r a t u r e l f u e g a s f r o m t h e c o mb u s t i o n c h a mb e r ,t h e n s p r a y e d i n t o t h e f u na r c e . T h r o u g h t h e p h y s i c a l mo d e l e x p e r i me n t s h o w s t h a t t h e s y s t e m i s f e a s i b l e ,a n d c o mp a r e d it w h t h e t r a d i — t i o n a l lu a mi n u m s me l t e r,i t C n a s a v e a b o u t 2 6 . 9 % ~4 7 . 4 % 7 4 . 7 % d is p l a e e me n t . Ke y wo r d s a l u mi n u m s me l t e r e n e r y g c o n s e r v a t i o n nd a e mi s s i o n r e d u c t i o n w a s t e h e a t r e c o v e r y d e s i g n e x p e r i me n t e n e r y ,a g n d r e d u c e a b o u t 41 . 5 % ~
铝冶炼烟气净化余热利用技术的探讨

铝冶炼烟气净化余热利用技术的探讨摘要:自改革开放以来,我国社会和经济的发展越来越快,环保节能理念也日益深入人心,对于铝冶炼方面来说,将新工艺、新技术引入环保系统,从工艺、设备控制技术和生产系统的协调方面,开展全方位的研究,从而将铝冶炼企业污染物的排放量降低到最低限度是我们长期的目标,这对推动整个铝冶炼行业的技术进行具有重要意义。
基于此,本文主要阐述了铝冶炼的烟气净化工艺、铝冶炼烟气治理存在的问题、利用铝冶炼烟气余热的策略,希望能为我国今后工业的发展带来帮助。
关键词:铝冶炼烟气净化余热利用策略在现在社会的发展中,环境的持续恶化,正逐步制约着经济的可持续发展和人民生活的提高,环境保护的迫切性在逐步增强。
如何增强铝工业产业的节能环保利用是当前要关注的问题。
铝冶炼企业烟气净化余热利用系统的应用,能较好地解决铝冶炼生产节能问题,因此加强铝冶炼烟气净化余热利用技术对我国的发展具有至关重要的作用。
一、概况在铝冶炼生产中,通常以冰晶石-氧化铝熔体为冶炼质,以碳素材料为电极进行冶炼。
在阴极上析出液态的金属铝,在阳极上产生以二氧化碳为主的阳极气体,同时还散发出以氟化物和粉尘等污染物为主的烟气,与阳极气体统称为冶炼烟气。
弥漫在冶炼车间内部的冶炼烟气使劳动条件恶化,影响生产工人的身体健康。
冶炼烟气扩散到厂区周围,也会对大气环境造成经常性污染。
因此必须将冶炼烟气进行治理并回收氟化盐和氧化铝。
关于铝冶炼烟气净化处理的工艺方法,国内外大都采用干法净化方式,即首先用新鲜的氧化铝吸附烟气中的有害物质,然后通过布袋过滤,最后将低于国家标准的烟气排入大气。
由于在烟气净化中一味追求净化和物料回收效果,对利用高温烟气中携带的热能考虑甚少,造成烟气中的大量的热能白白浪费。
二、铝冶炼的烟气净化工艺2.1工艺流程干法净化工艺流程从功能上主要包括冶炼槽集气、吸附反应、气固分离、氧化铝输送、机械排风五个部分。
冶炼槽产生的烟气经密闭集气罩收集,通过直径600m。
烟气余热深度梯级利用方案分析

烟气余热深度梯级利用方案分析摘要:当前,烟气余热主要用于预热助燃空气、加热热网水和加热凝结水等用途。
最有前途和潜力的节能措施包括传统低压省煤器系统和余热深度利用及减排系统。
关键词:烟气余热;梯级利用;方案分析1引言烟气余热深度利用及减排系统是一种全新的系统,并且已经在某些燃气锅炉设备成功的应用,节能效果也超过国家的标准要求。
这个系统的特点是,它包括四个换热设备:第一级、第二级低温换热器,高温换热器和空气换热器。
高温换热器和第一级低温换热器依次布置于空预器和除尘器之间烟道内,第二级低温换热器布置于引风机出口和脱硫吸收塔之间烟道内,空气换热器布置于送风机出口风道内。
高温换热器利用空预器后的烟气热量加热凝结水,组成一个高效低压的省燃气器系统。
空气换热器和第一、二级低温换热器可以形成闭式循环,第一级低温换热器能将烟气温度减至95℃,根据相关研究,飞灰的比电阻随温度降低而降低,除尘的效率随之增高,粉尘排放浓度随之降低。
第二级换热器可以将脱硫塔的入口温度降至85℃左右,最大限度的降低脱硫工艺水耗和回收烟气余热。
将空气换热器放置在送风机出口风道,同时把第一、二级低温换热器的低品质的烟气余热进行回收,它的用途就是加热冷二次风,这样如果冷二次风温度提高之后,空气预热器温度发生变化,才有利于降低空气预热器的冷端低温腐蚀情况,减少空气预热器的堵塞,提升烟气品质,提高锅炉的效率。
烟气余热热度利用及减排系统还有一个优点就是各个模块都能单独的调节,根据周围环境温度等因素调节控制烟温,确保在机组各负荷工况下投入该系统时安全、经济运行。
深度利用烟气余热达到节燃气节水,从而实现深度节能。
2烟气余热深度热力学特性不同燃料燃烧后产生的烟气中水含量不同,因而起始冷凝温度也不同。
下边本文将基于对某天然气成分进行计算分析,得出过剩空气系数从l变化到1.3时,烟气冷凝起始温度在60.5~6l℃问变化。
烟气冷凝回收是一个变温过程。
从起始冷凝温度开始,冷凝点随着水分的凝结而降低。