大红山铜矿废石充填工艺的实践
钻孔充填工艺在大红山铜矿的应用
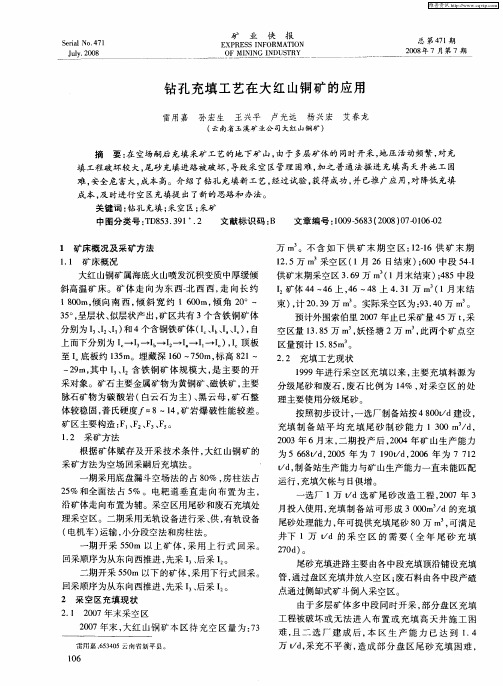
矿
S ra . e ilNo 471
业
快
报 §R一 r Y一 r
EXPRES NF S I ORM ATI ON
一
总 第4 1 7 期
2 0 年 7月第 7期 08
J l. 0 8 uy 2 0
钻 孔充 填 工 艺在 大 红 山铜 矿 的应 用
回采顺序 为从 东 向西推 进 , 采 I、 采 I。 先 ,后
尾砂 充填 进路 主要 由各 中段 充填 顶沿铺 设 充填 管, 通过 盘 区充填井 放人 空 区 ; 石料 由各 中段 产碴 废 点 通过侧 卸式 矿斗 倒人 采空 区 。
二期开采 5 0 以下的矿体, 5m 采用下行式 回采 。 回采 顺序 为从 东 向西推 进 , 采 I、 采 I。 先 后 2 采空区充填现状
12 采 矿 方法 .
根 据 矿 体赋 存 及 开采 技 术条 件 , 大红 山铜 矿 的 采矿 方法 为空场 回采 嗣后 充填 法 。
一
期 采用底 盘 漏斗空 场 法 的 占 8 % , 柱 法 占 0 房
t , / 制备站生产能力与矿 山生产能力一直未能匹配 d 运行 , 充填 欠 帐与 日俱增 。
至 I底板约 15 3m。埋藏深 10— 5m, 高 8 1 6 70 标 2一 2 m, 中 I、 9 其 ,I 铁 铜 矿 体 规 模 大 , 主 要 的 开 :含 是
一
19 进行采 空 区充 填 以来 , 99年 主要 充填 料 源 为 分 级尾 砂和 废 石 , 石 比例 为 1% , 采空 区 的 处 废 4 对 理 主要 使用 分级 尾砂 。 按 照初 步设 计 , 一选 厂制备 站按 480/ 0 td建设 , 充填制 备站平 均 充填 尾砂制 砂能 力 130m / , 0 。d 20 03年 6月末 , 期 投 产 后 ,04年矿 山 生产 能 力 二 20
大红山铜矿_矿石可选性研究报告

目录前言.......................................................... 错误!未定义书签。
一、实验样品的采取............................................ 错误!未定义书签。
二、实验样品的制备............................................ 错误!未定义书签。
三、原矿性质研究.............................................. 错误!未定义书签。
分析 ........................................................ 错误!未定义书签。
............................................................ 错误!未定义书签。
............................................................ 错误!未定义书签。
............................................................ 错误!未定义书签。
............................................................ 错误!未定义书签。
............................................................ 错误!未定义书签。
............................................................ 错误!未定义书签。
............................................................ 错误!未定义书签。
浅谈铜矿充填采矿工艺技术改造
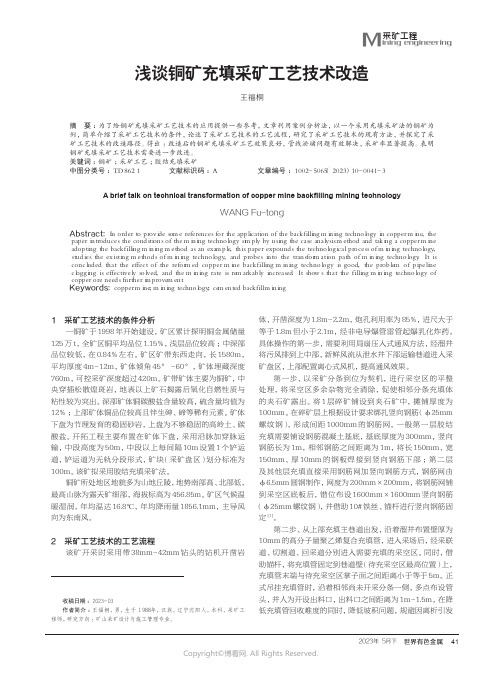
2023年 5月下 世界有色金属41采矿工程M ining engineering浅谈铜矿充填采矿工艺技术改造王福桐(山西中条山集团胡家峪矿业有限公司,山西 运城 043704)摘 要:为了给铜矿充填采矿工艺技术的应用提供一些参考,文章利用案例分析法,以一个采用充填采矿法的铜矿为例,简单介绍了采矿工艺技术的条件,论述了采矿工艺技术的工艺流程,研究了采矿工艺技术的现有方法,并探究了采矿工艺技术的改造路径。
得出:改造后的铜矿充填采矿工艺效果良好,管线淤堵问题有效解决,采矿率显著提高。
表明铜矿充填采矿工艺技术需要进一步改进。
关键词:铜矿;采矿工艺;胶结充填采矿中图分类号:TD862.1 文献标识码:A 文章编号:1002-5065(2023)10-0041-3A brief talk on technical transformation of copper mine backfilling mining technologyWANG Fu-tong(Shanxi Zhongtiao Mountains Group Hujiayu Mining Co.,Ltd., Yuncheng 043704,China)Abstract: In order to provide some references for the application of the backfilling mining technology in copper mine, the paper introduces the conditions of the mining technology simply by using the case analysis method and taking a copper mine adopting the backfilling mining method as an example, this paper expounds the technological process of mining technology, studies the existing methods of mining technology, and probes into the transformation path of mining technology. It is concluded that the effect of the reformed copper mine backfilling mining technology is good, the problem of pipeline clogging is effectively solved, and the mining rate is remarkably increased. It shows that the filling mining technology of copper ore needs further improvement.Keywords: copper mine; mining technology; cemented backfill mining收稿日期:2023-03作者简介:王福桐,男,生于1988年,汉族,辽宁沈阳人,本科,采矿工程师,研究方向:矿山采矿设计与施工管理专业。
大红山铜矿矿石损失率及贫化率优化实践

大红山铜矿矿石损失率及贫化率优化实践胡川【摘要】损失率、贫化率是评价矿山生产技术及管理水平的关键指标,目前,国内已将工业矿和低品位矿资源全部纳入计算评价范围.大红山铜矿自投产以来,矿体开采矿石损失贫化一直偏高,场内损失率居高不下,甚至出现负损失的情况.为合理确定损失率和贫化率,更新了传统损失率、贫化率含义及计算方法,对720、485中段部分采场重新进行了损失率计算,考虑含有用组分的围岩混入和顶板垮落情况,避免了负损失的出现;通过对285中段B48-68线方案优化,将设计开发利用资源储量全部纳入损失率计算范畴后,矿块设计总损失增大7%,设计回采品位由0.338%提升到0.389%,废石混入率由48.9%降低至40%,贫化率由36.7%降低至27%,使得该矿块资源经济效益最大化.损失率和贫化率是一对相辅相成相互制约又相互矛盾的技术指标,只有结合矿山实际,合理确定损失率、贫化率,才能有效降低采选成本,减小尾矿排放量及排放成本.【期刊名称】《现代矿业》【年(卷),期】2019(000)006【总页数】4页(P90-92,107)【关键词】损失率;贫化率;控制措施【作者】胡川【作者单位】云铜集团技术中心矿山研究院【正文语种】中文矿山开采的损失率、贫化率指标是矿山技术工作的主要内容,也是体现矿山生产技术水平的关键指标[1-2]。
在开发过程中,可能会因为各种原因导致矿石损失和贫化,但是部分矿石的损失贫化是可以通过技术手段控制的[3-5]。
降低矿石的损失和贫化,不但可以减少矿床有用组分的损失,增加有用组分的产量,还可以降低采矿选矿成本,减小尾矿排放量及排放成本,提高企业经济效益[6],同时在社会效益、环境效益方面也具有重要的意义。
1 矿山概况大红山矿区开发建设始于上世纪80年代,1993年大红山铜矿一期工程开工建设,1997年7月建成投产。
二期工程于2003年6月建成投产,西部矿段采矿工程2016年9月建成投产。
充填采矿法在铜矿的应用探究
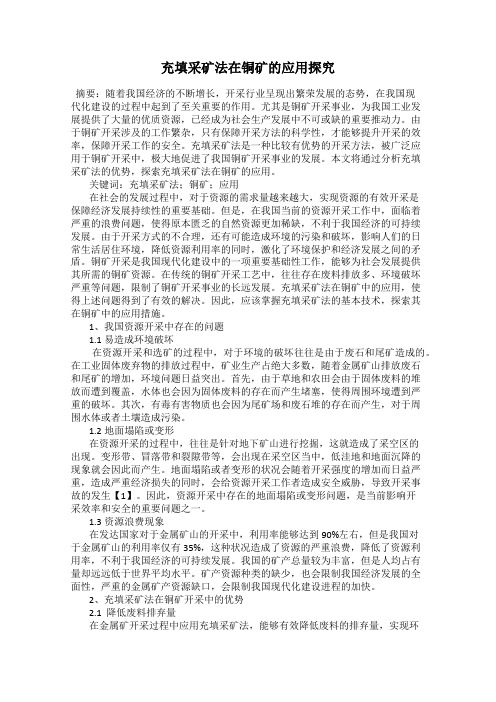
充填采矿法在铜矿的应用探究摘要:随着我国经济的不断增长,开采行业呈现出繁荣发展的态势,在我国现代化建设的过程中起到了至关重要的作用。
尤其是铜矿开采事业,为我国工业发展提供了大量的优质资源,已经成为社会生产发展中不可或缺的重要推动力。
由于铜矿开采涉及的工作繁杂,只有保障开采方法的科学性,才能够提升开采的效率,保障开采工作的安全。
充填采矿法是一种比较有优势的开采方法,被广泛应用于铜矿开采中,极大地促进了我国铜矿开采事业的发展。
本文将通过分析充填采矿法的优势,探索充填采矿法在铜矿的应用。
关键词:充填采矿法;铜矿;应用在社会的发展过程中,对于资源的需求量越来越大,实现资源的有效开采是保障经济发展持续性的重要基础。
但是,在我国当前的资源开采工作中,面临着严重的浪费问题,使得原本匮乏的自然资源更加稀缺,不利于我国经济的可持续发展。
由于开采方式的不合理,还有可能造成环境的污染和破坏,影响人们的日常生活居住环境,降低资源利用率的同时,激化了环境保护和经济发展之间的矛盾。
铜矿开采是我国现代化建设中的一项重要基础性工作,能够为社会发展提供其所需的铜矿资源。
在传统的铜矿开采工艺中,往往存在废料排放多、环境破坏严重等问题,限制了铜矿开采事业的长远发展。
充填采矿法在铜矿中的应用,使得上述问题得到了有效的解决。
因此,应该掌握充填采矿法的基本技术,探索其在铜矿中的应用措施。
1、我国资源开采中存在的问题1.1 易造成环境破坏在资源开采和选矿的过程中,对于环境的破坏往往是由于废石和尾矿造成的。
在工业固体废弃物的排放过程中,矿业生产占绝大多数,随着金属矿山排放废石和尾矿的增加,环境问题日益突出。
首先,由于草地和农田会由于固体废料的堆放而遭到覆盖,水体也会因为固体废料的存在而产生堵塞,使得周围环境遭到严重的破坏。
其次,有毒有害物质也会因为尾矿场和废石堆的存在而产生,对于周围水体或者土壤造成污染。
1.2地面塌陷或变形在资源开采的过程中,往往是针对地下矿山进行挖掘,这就造成了采空区的出现。
点柱式上向分层充填法在大红山铁矿的优化调整与应用

点柱式上向分层充填法在大红山铁矿的优化调整与应用点柱式上向分层充填法是一种高效的矿山回采工艺,该方法主要是针对金属矿石,如黄金、银、铜、铅、锌等,其优点在于有效地回收了矿石细粒、低品位、难选和难回收的矿石。
在大红山铁矿应用该方法的过程中,需要进行优化调整,以提高铁矿石的回收率和抗压性,同时避免因为回采过程的决策和实际操作中不当的因素引起的不良现象。
大红山铁矿是中国重要的铁矿石储备基地之一,是我国大型铁矿石精选工程的样板项目,该矿床的矿石特征为矿物粒度大小分布不均匀,品位较低且含杂质较多。
点柱式上向分层充填法通过优化矿石选别、选区划分、充填方式和在采矿过程中的实际操作中的一系列措施,直接影响铁矿石的回采效果和经济效益。
大红山铁矿中,在选矿过程中将矿石按照品位、矿物组成和粒度等特征进行选择后,采用点柱式上向分层充填法,将浸出液从井下提取,通过管道输送至充填面,再泵送至充填柱内。
在充填柱内,浸出液与矿石颗粒混合,最终生成稳定的充填体。
这种方法主要是通过充填体的形成来支撑矿体的稳定,使得回采区域不发生塌陷和移动,同时能够回收矿石,达到矿山回采的目的。
在实际应用中,大红山铁矿在点柱式上向分层充填法的优化调整方面,主要是针对两方面进行的:一是优化矿石选别和选区划分的方法,二是优化充填方式和实际操作的措施。
在矿石选别和选区划分的方法上,大红山铁矿主要采用了基于深度的矿石品位分层采矿的方法,即充填体向下构建,在下部采集低品位的矿石,在上部采集高品位的矿石。
同时,建立了快速识别低品位矿区和高品位矿区的方法,以准确划分不同的选矿区域,有效地提高了回收率并降低了充填成本。
在优化充填方式和实际操作的措施上,大红山铁矿主要采用了合理安排充填顺序和选用合适粒度的充填物,以提高充填体的强度和稳定性。
在决定充填体的粒度分布时,还采用了水分对充填物粘合性和强度的影响进行了评估,以确保充填体的密度和力学特性。
总之,点柱式上向分层充填法在大红山铁矿的优化调整与应用,采用了一系列的措施以取得最佳的效果。
机械化点柱式上向水平分层充填法在大红山铜矿的应用
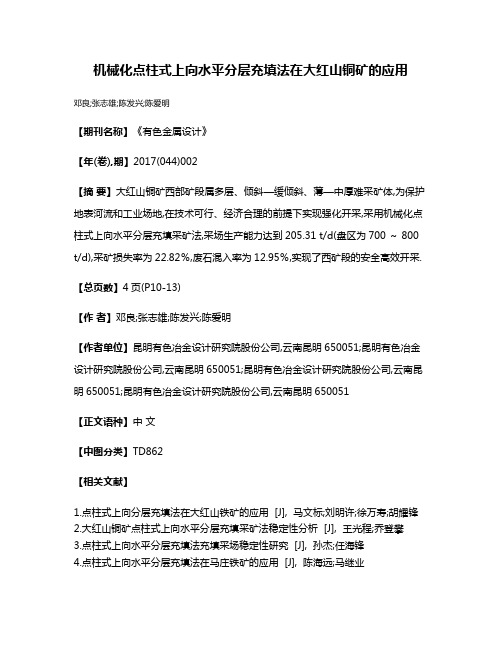
机械化点柱式上向水平分层充填法在大红山铜矿的应用邓良;张志雄;陈发兴;陈爱明
【期刊名称】《有色金属设计》
【年(卷),期】2017(044)002
【摘要】大红山铜矿西部矿段属多层、倾斜—缓倾斜、薄—中厚难采矿体,为保护地表河流和工业场地,在技术可行、经济合理的前提下实现强化开采,采用机械化点柱式上向水平分层充填采矿法,采场生产能力达到205.31 t/d(盘区为700 ~ 800 t/d),采矿损失率为22.82%,废石混入率为12.95%,实现了西矿段的安全高效开采.【总页数】4页(P10-13)
【作者】邓良;张志雄;陈发兴;陈爱明
【作者单位】昆明有色冶金设计研究院股份公司,云南昆明650051;昆明有色冶金设计研究院股份公司,云南昆明650051;昆明有色冶金设计研究院股份公司,云南昆明650051;昆明有色冶金设计研究院股份公司,云南昆明650051
【正文语种】中文
【中图分类】TD862
【相关文献】
1.点柱式上向分层充填法在大红山铁矿的应用 [J], 马文标;刘明许;徐万寿;胡耀锋
2.大红山铜矿点柱式上向水平分层充填采矿法稳定性分析 [J], 王光程;乔登攀
3.点柱式上向水平分层充填法充填采场稳定性研究 [J], 孙杰;任海锋
4.点柱式上向水平分层充填法在马庄铁矿的应用 [J], 陈海远;马继业
5.南京铅锌银矿无污染充填法——点柱上向水平分层充填法 [J], 金铭良;傅跃;郭三军
因版权原因,仅展示原文概要,查看原文内容请购买。
点柱式上向分层充填法在大红山铁矿的优化调整与应用

点柱式上向分层充填法在大红山铁矿的优化调整与应用
点柱式上向分层充填法是一种常见的充填工艺技术,其在大红山铁矿中的应用也十分
广泛。
本文将探讨该工艺在大红山铁矿的优化调整与应用。
首先,点柱式上向分层充填法是一种将一定比例的水泥、石子和废矿渣等材料进行混
合制成矿浆,然后通过输浆管将矿浆输送到深部矿井中,通过充填装置将矿浆充填到矿井
内的空腔和回采区域,使其成为一个稳定的支撑和加固体系。
该工艺适用于矿石热力条件、性质和地质情况较为复杂的矿井,可以有效地提高回采率和矿石利用率,降低回采成本和
环境污染。
在大红山铁矿的应用上,点柱式上向分层充填法也遇到了一些问题,例如混凝土强度
不足、工艺难以控制和充填质量不稳定等问题。
为了解决这些问题,需要进行工艺优化和
调整,以提高充填质量和效益。
一方面,要加强对充填材料的选择和配置,并结合矿石的物理和化学特性进行优化。
另一方面,要完善充填工艺流程,并进行现场调整和监控,及时跟踪充填效果和质量。
同时,对于充填质量不稳定的问题,可以加强对充填工艺的科学研究和探索,寻求更适宜的
工艺流程和方法。
在大红山铁矿的实践中,点柱式上向分层充填法通过优化工艺和流程,有效地提高了
充填质量和效益,降低了回采成本和环境污染,取得了良好的效果。
同时,该工艺也为矿
山的可持续发展提供了一种新的思路和方法。
总之,点柱式上向分层充填法在大红山铁矿的优化调整和应用中,有着重要的意义和
作用。
我们应该继续对该工艺进行深入研究和探索,并推广应用到更多的矿山地质条件中,以促进矿山的可持续发展和环境保护。
废石充填工艺在大红山铜矿的应用研究

2 4 尾 砂 充填 系统缺 陷 . 充 填 制 备 站 按 现 选 矿 能 力 48 0td 置 的 , 0 / 设 制砂能 力 只有 13 0I。 d 0 I 左右 ;而现 在选 矿 能力 已 T/
维普资讯
3 2
矿 业 工 程
铜矿 体 (。 和 4个 含 铜 铁 矿 体 (c b I、I、I) I 、I 、
I、I ) 自上 而下 分别 为 I— I一 I— I一 I— I a o, c 。 b a l
+ I o。
大 红 山铜 矿 采 矿 工 艺 为空 场 嗣 后尾 砂 充填 法 ,
19 9 7年 7 月 ~ 2 0 年 1 月 共 采 出 铜 矿 石 06 2
表 1 19 "2 0 9 7 - 0 6年 废 石 产 出及 地 表 碴 量 统 计 / 。 - , m
20 0 4年 大 红 山铜 矿 经 过 科 学 论 证 ,针 对 提 升
20 0 6年 末井 下 待 充 采 空 区 为 7 O万 m。 。按 此 采 充速 度 ,到 2 0 0 7年 末预计 欠 充空 区量 8 O万 m。 ,
I矿 体 ,充 填结 束后 再采 I矿体 。 。
18 0m,倾 向南 西 ,倾 斜 宽 约 16 0m,倾 角 2 。 0 0 O
~
2 采 空 区和 充 填 系 统 现 状
2 1 废 碴 生 产 现 状 .
3。 5 ,呈层 状 、似 层 状 产 出 ,矿 区共 有 3个 含 铁
1 概 况
1 1 矿体 赋存 条 件 .
矿床 类 型为海 底火 山 喷发沉 积 变质 中厚 缓倾 斜 高 温 矿 床 。 矿 体 走 向 为 东 西 ~ 北 西 西 , 长 约
发 展 方 向 ) 空 场 嗣 后 充 填 采 矿 法 、房 柱 法 、 留矿 法 。回采顺 序 中段 由下 向上 ( 期 5 0标 高 以下 由 二 5 上 向下 ,5 0标 高 以上 由下 向上 ) 5 ,矿 体 先 采 上 层
采矿工程及矿体充填工程施工组织设计

玉溪大红山矿业有限公司第九作业区Ⅰ号铜矿带150万吨/年采矿工程及Ⅲ、Ⅳ矿体充填工程施工组织设计铜陵中都矿建云南分公司公司大红山项目部二〇一一年十月目录第一章工程概况 (3)第二章编制依据与原则 (9)第三章施工准备和大临设施 (10)第四章掘进工程施工方案和技术措施 (12)第五章采矿工艺 (17)第六章出矿进度安排及三级矿量平衡的措施 (24)第七章III IV矿体充填工程 (26)第八章辅助系统 (27)第九章工期承诺和保证措施 (28)第十章项目组织机构、劳动力计划和材料投入计划 (30)第十一章机械设备设施投入计划 (32)第十二章质量承诺和保证措施 (32)12.3.3.1确保混凝土强度等级的技术措施 (34)第十三章安全生产和文明施工措施及违约承诺 (38)附图附表 (41)附件一质量管理体系 (41)附件二安全环境管理体系 (41)附件一 (48)质量管理体系 (48)附件二 (59)安全环境管理体系 (59)第一章工程概况1.1矿区地理和交通大红山铁矿是昆钢集团公司的重要铁矿石原料基地,矿山位于云南省玉溪市新平彝族、傣族自治县戛洒镇。
矿区往东有公路通往新平县城(81km)、玉溪市(165km),昆明市(271km),往西有公路至楚雄市(178km)、昆明市(344km)。
从矿区经新平、玉溪至昆钢本部公路距离260km,至戛洒生活区10.5km,对外交通方便。
1.2概述及采充范围大红山铁矿I号铜矿带150万t/a采矿工程是大红山铁矿800万t/a扩产工程的一部分,初步设计为云南华昆工程技术股份公司和中冶长天国际工程有限责任公司编制的《大红山铁矿I号铜矿带及三选厂铜系列150万t/a采选工程初步设计》。
大红山铁矿I号铜矿带150万t/a采矿工程的建设于07年展开,基建探矿工程已完成,并提交了《Ⅰ号铁铜矿带首采区基建探矿地质报告》,开拓工程已完成大部分,基建采切工程基本结束。
从基建探矿提交的探矿资料看,矿体大部分变得层数较多,且层间距有厚有薄,矿体局部地段较厚大。
大红山铜矿废石充填工艺的实践
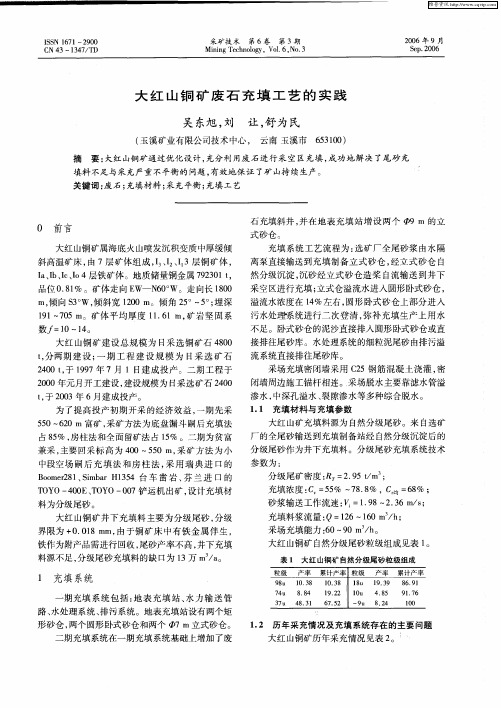
斜高温矿床 , 7层矿体组 成, 、 、 3层铜矿体 , 由 III :
I、 、 、 a I I 14层铁矿体 。地质储量铜金属 720 , b c0 93 1 t 品位 0 8% 。矿体走向 E .1 w—N 0 w。走向长 10 6。 80
m, 向 S 。 , 倾 3w 倾斜 宽 10 20m。倾 角 2 。~ 。埋 深 5 5;
维普资讯
吴东旭 , : 大红山铜 矿废石充填 _ 艺的实践 等 T -
表 2 大红 山铜矿 历年采充情况
13 9
下层矿体 , 下层矿体 出矿结束后两层矿体 同时充填 的开拓布置 回采工艺 。两层矿体原则上先采上层矿 体, 上层矿体 出矿结束后再回采下层矿体 , 下层矿体
表 1 大红 山铜矿 自然分级尾砂粒级 组成
粒级 产率
9u 8 7u 4 3u 7 1. 8 0 3 8 8 .4 4.l 8 3
界限为 + . 1 m 由于铜矿床 中有铁金属伴生 , 0 08 m, 铁作为附产品需进行 回收, 尾砂产率不高 , 井下充填
料源 不足 , 级尾 砂充 填料 的缺 口为 1 分 3万 m / 。 a
然分级沉淀 , 沉砂经立式砂仓造桨 自流输送到井下 采空 区进行 充填 ; 式仓溢 流水 进入 圆形 卧式砂 仓 , 立
溢流 水浓度 在 1 %左右 , 4 圆形 卧式 砂 仓 上部 分进 入
11 75m 9 ~ 0 。矿体平均厚度 1. 1I, 1 6 1 矿岩坚 固系 3
数 /=1 0~1。 4
路 、 处理 系统 、 污系统 。地 表充 填站设 有两个 矩 水 排 形 砂仓 , 两个 圆形 卧式 砂仓 和两 个 7m立 式砂 仓 。 二 期充填 系统 在一 期充 填 系统基 础上 增加 了废 1 2 历年 采 充情况 及 充填 系统存 在 的主 要 问题 . 大红 山铜矿 历年 采充 情况 见 表 2 。’
充填采矿法在大红山铁矿的应用

充填采矿法在大红山铁矿的应用充填采矿法是一种很符合持续发展理念、绿色矿山理念的实用技术,目前在大红山铁矿I号铜矿带深部150万t/a采矿工程、III、IV号矿体和280m小富矿体等处取得了良好的效果,不但可以减少尾矿和采切废石的排放,而且有效的降低生产成本和提高安全性能。
还有二道河矿段100万ta采矿工程未“三下”开采,也必须采用充填采矿法,目前正在建设配套的充填系统。
标签:充填采矿法;绿色环保;安全高效1.大红山地质和采矿方法简介1.1地质简介大红山铁矿根据矿体平面分布、产出部位、埋藏深度、构造边界等因素,可划分为浅部铁矿、深部铁矿、曼岗河北岸铁矿、哈姆白祖铁矿和Ⅰ号铁铜矿带等五个地段。
五个地段经勘探查明有五个主要含矿带,共计71个矿体,其中大型矿体3个、中型矿体7个、小型矿体61个。
共计有铁矿石总储量45825.34万t (未包含熔岩铁矿)/55790万t(含熔岩铁矿),TFe品位36.32%/33.41%,其中表内34112.75万t,TFe品位40.94%,表外11712.59万t,Tfe品位23.05%。
铜矿石总储量约7567.15万t,铜平均品位0.53%,伴生铁品位TFe20.09%。
根据矿体产出层位和部位,由下而上划分为7个含矿带,其中有工业矿体的矿带5个(Ⅰ、Ⅱ、Ⅲ、Ⅳ、Ⅴ)。
矿体的产出层位,上部以铁矿为主,下部以铜矿为主。
Ⅱ矿带为主要铁矿带,Ⅳ、Ⅴ矿带为铁矿,Ⅰ、Ⅲ矿带为铁铜矿带。
各矿体的空间位置如下:1.2采矿方法简介1.2.1无底柱分段崩落法采矿法大红山铁矿中部采区、南翼采区和主采区等400万t/a一期已回采结束的采区及西翼采区、西上采区、东上采区等400万t/a二期正在进行的采矿工程均采用无底柱分段崩落采矿法。
主矿体整体回采顺序自上而下开采,其中主采区合采部分矿体较为厚大,从矿体中部朝南北向拉槽,边角部分辅助拉槽形成补偿空间,矿块回采时整体向切割槽两翼及侧翼后退式回采,多分段梯段式同时出矿,上分段回采工作面超前下分段回采工作面大于一个分段的距离。
点柱式分层充填采矿法在大红山Ⅰ号铜矿带中的应用
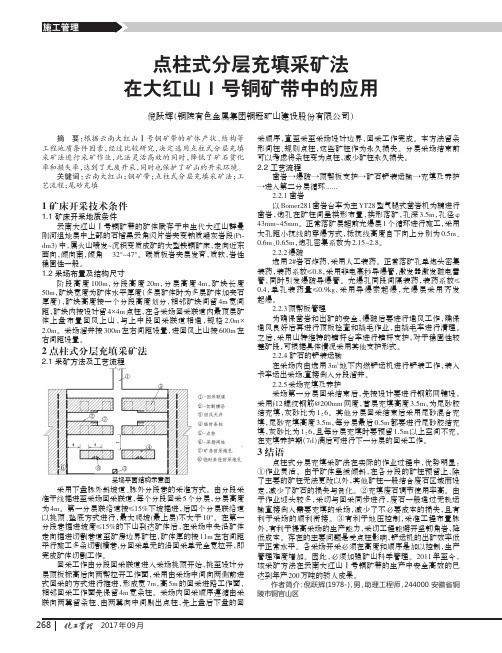
2017年09月点柱式分层充填采矿法在大红山Ⅰ号铜矿带中的应用倪跃辉(铜陵有色金属集团铜冠矿山建设股份有限公司)摘要:根据云南大红山Ⅰ号铜矿带的矿体产状、结构等工程地质条件因素,经过比较研究,决定选用点柱式分层充填采矿法进行采矿作业,此法灵活高效的同时,降低了矿石贫化率和损失率,达到了无废开采,同时也保护了矿山的开采环境。
关键词:云南大红山;铜矿带;点柱式分层充填采矿法;工艺流程;尾砂充填1矿床开采技术条件1.1矿床开采地质条件云南大红山Ⅰ号铜矿带的矿体赋存于中生代大红山群曼刚河组地层中上部的石榴黑云角闪片岩夹变钠质凝灰岩段(Pt⁃dm3)中,属火山喷发~沉积变质成矿的大型铁铜矿床,走向近东西向,倾向南,倾角32°~47°。
碳质板岩夹层发育,质软,岩性稳固性一般。
1.2采场布置及结构尺寸阶段高度100m ,分段高度20m ,分层高度4m ,矿块长度50m ,矿块宽度为矿体水平厚度(多层矿体时为多层矿体加夹石厚度),矿块高度按一个分段高度划分,相邻矿块间留4m 宽间距,矿块内按设计留4×4m 点柱,在各采场回采联道内最顶层矿体上盘布置回风上山,与上中段回采联道相通,规格2.0m×2.0m 。
采场溜井按300m 左右间距设置,进回风上山按600m左右间距设置。
2点柱式分层充填采矿法2.1采矿方法及工艺流程采场平面结构示意图采用下盘脉外斜坡道、脉外分段巷的采准方式。
由分段采准干线掘进至采场回采联道,每个分段回采5个分层,分层高度为4m 。
第一分层联络道按≤15%下坡掘进,后四个分层联络道以挑顶、垫底方式进行,最大爬坡(最上层)不大于10°。
在第一分段巷掘进坡度≤15%的下山到达矿体后,在采场中央沿矿体走向掘进切割巷道至矿房边界矿柱,矿体厚的按11m 左右间距平行施工多条切割横巷,分回采单元的沿回采单元全宽拉开,即完成矿体切割工作。
回采工作由分段回采联道进入采场挑顶开始,挑至设计分层顶板标高后向两帮拉开工作面,采用由采场中间向两侧前进式回采的方式进行推进,形成宽7m ,高5m 的回采进路工作面,相邻回采工作面先保留4m 宽条柱。
大红山铁矿Ⅱ1-2矿体两步骤回采嗣后充填采矿法应用
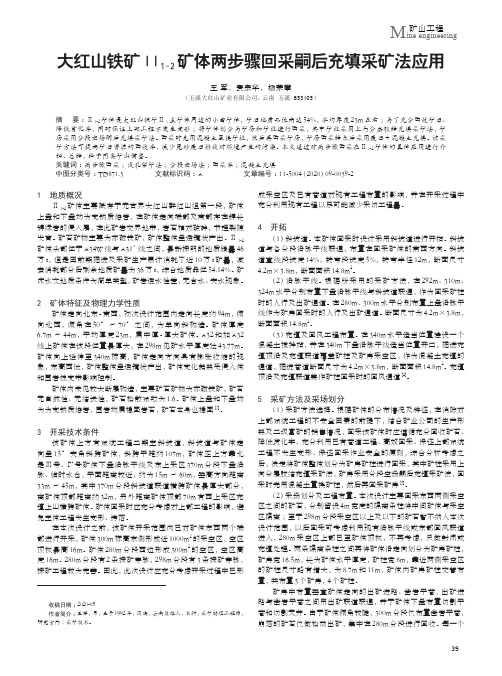
39M ine engineering矿山工程大红山铁矿II 1-2矿体两步骤回采嗣后充填采矿法应用王 军,麦宗华,杨荣攀(玉溪大红山矿业有限公司,云南 玉溪 653405)摘 要:Ⅱ1-2矿体是大红山铁矿Ⅱ1主矿体周边的小富矿体,矿石地质品位高达54%,平均厚度23m 左右;为了充分回收矿石、降低贫化率,同时保证上部工程不发生变形;将矿体划分为矿房和矿柱进行回采,其中矿柱采用上向分层胶结充填采矿法,矿房采用分段空场嗣后充填采矿法。
回采时先用混凝土置换矿柱,然后再回采矿房,矿房回采结束后采用废石+混凝土充填。
该采矿方法可提高矿石资源的回收率,减少尾砂废石排放对环境产生的污染。
本文通过对两步骤回采在Ⅱ1-2矿体的具体应用进行介绍、总结,给予同类矿山借鉴。
关键词:两步骤回采;浅孔留矿法;分段空场法;回采率;混凝土充填中图分类号:TD871.3 文献标识码:A 文章编号:11-5004(2020)09-0039-2 收稿日期:2020-05作者简介:王军,男,生于1992年,汉族,云南楚雄人,本科,采矿助理工程师,研究方向:采矿技术。
1 地质概况Ⅱ1-2矿体主要赋存于元古界大红山群红山组第一段,矿体上盘和下盘均为变钠质熔岩,在矿体走向端部及南部存在辉长辉绿岩的侵入层,在此矿岩交界地带,岩石相对破碎,节理裂隙发育。
矿石矿物主要为赤磁铁矿,矿体整体呈透镜状产出。
Ⅱ1-2矿体头部位于A34W 线与A31’线之间,最新探明的地质储量46万t,但是因前期掘进及采矿生产累计消耗了近10万t 矿量,减去消耗部分后剩余地质矿量为36万t,综合地质品位54.14%。
矿床水文地质条件为简单类型,矿岩透水性差,无含水、突水现象。
2 矿体特征及物理力学性质矿体走向北东-南西,初次设计范围内走向长度约94m,倾向北西,倾角在50°~70°之间,为单向斜构造。
矿体厚度6.7m ~44m,平均厚度23m,属中厚-厚大矿体。
大红山铜矿选矿新工艺试验研究

大红山铜矿选矿新工艺试验研究通过对粗精矿、精I尾矿和扫选精矿进行了MLA测试,查出了选矿流程中的中矿粒度微细且单体解离不足,当前生产的中矿返回二段磨会造成流程负荷加重、不利于选矿指标提高。
对此,经小型试验研究,采取对浮选中矿进行再磨后返回粗选进行处理的工艺,铜精矿品位提高了0.69个百分点,铜回收率提高了1.61个百分点。
标签:中矿再磨选矿试验新工艺选矿流程1原矿性质1.1原矿多元素分析从原矿多元素分析结果可以看出,原矿中SiO2、TFe含量较高,且含有少量有价金属金和银。
1.2原矿铜物相分析原矿铜物相分析结果表明:氧化率为6.06%,其中结合铜占全铜1.10%,游离铜占全铜4.96%;硫化铜为93.94%,其中原生铜占全铜77.96%,次生铜占全铜15.98%,属硫化铜矿。
2可选性试验研究2.1现场工艺条件开路试验2.2现场工艺条件闭路试验2.2.1粗精矿不磨闭路流程试验(试验流程及工艺条件见图2)2.2.2粗精矿再磨闭路流程试验(试验流程及工艺条件见图3)2.3现场工艺条件试验小结(1)开路试验结果表明,现场最佳工艺条件为:原矿磨矿细度-200目70%,丁黄药+丁铵黑药(30+10)g/t,730A(起泡剂)35g/t;(2)粗精矿不磨闭路试验取得的试验指标为:铜精矿产率 1.61%,铜精矿品位20.61%,铜回收率91.08%;(3)粗精矿再磨闭路试验取得的试验指标为:铜精矿产率 1.43%,铜精矿品位23.33%,铜回收率91.85%;2.4精Ⅰ尾矿可选性试验研究开路试验流程及工艺条件(见图4)。
开路试验最佳药剂条件:CTP(抑制剂)20g/t,Y-89(捕收剂)15g/t,730A (起泡剂)5g/t,以此最佳条件所得的精Ⅰ尾矿再磨细度试验结果如表3所示。
由表4可知,精Ⅰ尾矿再磨与不磨相比,精矿2回收率有所提高,精Ⅰ尾矿再磨至(-620目95%)以上,精矿2的铜品位和回收率变化不大,后续试验精Ⅰ尾矿再磨细度选取-620目95%。
大红山铜矿实习报告

大红山生产实习报告学院:国土资源工程学院班级:采矿工程xxx 班姓名:xxx学号:xxxxxxxxxxxx实习地点:大红山铜矿、大红山铁矿昆明理工大学国土资源工程学院资开系目录第1章前言 (1)1.1 实习目的和任务 (1)1.2 矿山地理位置及交通 (1)1.3 矿区人文及经济气候概况 (2)第2章矿山地质条件及开采技术条件 (4)2.1 矿山地质条件 (4)2.2 地层 (6)2.3 地质构造 (8)2.4矿床勘探及矿体赋存条件 (11)2.5开采技术条件 (15)第3章矿床开拓 (16)3.1I期工程开拓方式 (17)3.2I I期工程开拓方式 (18)3.3矿井通风 (19)3.4中段运输方式 (20)第4章采矿方法 (21)4.1I期采矿方法 (21)4.2I I期采矿方法 (23)第5章选矿流程 (24)第6章心得体会 (25)第1章前言1.1 实习目的和任务采矿专业生产实习,是在学生学完本专业主干课程——金属矿床地下开采及部分专业课的基础上,为更多地接触矿山生产,理论结合实际,而进行的一项基本实践训练,是采矿工程专业本科生必须进行的一个实践环节,内容以金属矿床地下开采为主。
此次实习的目的便是通过深入矿山了解与实地观察,进一步了解矿山生产现状、开拓系统以及所使用的采矿方法,学习矿山生产建设中的经验及劳动操作技能,增长才干,培养理论联系实际和独立工作能力,加深巩固学过的专业知识,更好地完成地下开采课程设计以及其它后续课程。
同时,再次学习与熟练掌握地质报告的编写,为日后学习以及工作打下理论与实践的基础。
1.2矿山地理位置及交通大红山铜矿位于云南省新平县戛洒镇境内,地理座标东经101°39′,北纬24°06′,在紧靠哀牢山脉东侧的戛洒江(红河、元江的上游)东岸。
矿区有公路通往新平县城。
矿区距新平县戛洒镇12K m ,从戛洒经326省道至新平,再由大新二级公路进入玉元高速至玉溪共182 K m ;至昆明264 K m 。
大红山实习报告
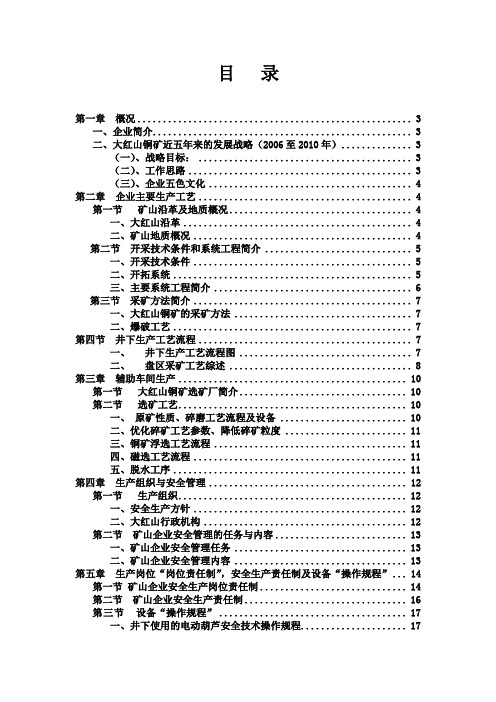
目录第一章概况 (3)一、企业简介 (3)二、大红山铜矿近五年来的发展战略(2006至2010年) (3)(一)、战略目标: (3)(二)、工作思路 (3)(三)、企业五色文化 (4)第二章企业主要生产工艺 (4)第一节矿山沿革及地质概况 (4)一、大红山沿革 (4)二、矿山地质概况 (4)第二节开采技术条件和系统工程简介 (5)一、开采技术条件 (5)二、开拓系统 (5)三、主要系统工程简介 (6)第三节采矿方法简介 (7)一、大红山铜矿的采矿方法 (7)二、爆破工艺 (7)第四节井下生产工艺流程 (7)一、井下生产工艺流程图 (7)二、盘区采矿工艺综述 (8)第三章辅助车间生产 (10)第一节大红山铜矿选矿厂简介 (10)第二节选矿工艺 (10)一、原矿性质、碎磨工艺流程及设备 (10)二、优化碎矿工艺参数、降低碎矿粒度 (11)三、铜矿浮选工艺流程 (11)四、磁选工艺流程 (11)五、脱水工序 (11)第四章生产组织与安全管理 (12)第一节生产组织 (12)一、安全生产方针 (12)二、大红山行政机构 (12)第二节矿山企业安全管理的任务与内容 (13)一、矿山企业安全管理任务 (13)二、矿山企业安全管理内容 (13)第五章生产岗位“岗位责任制”,安全生产责任制及设备“操作规程” (14)第一节矿山企业安全生产岗位责任制 (14)第二节矿山企业安全生产责任制 (16)第三节设备“操作规程” (17)一、井下使用的电动葫芦安全技术操作规程 (17)第六章事故预防与控制的对策 (18)第一节爆破事故预防 (18)第二节爆破事故控制的对策 (20)一、3E基本对策 (20)二、一些常见爆破事故的处理对策: (20)第七章生产系统安全评价 (21)第一节安全评价的工作程序 (21)第二节安全评价制度 (21)第八章职业安全管理健康体系 (21)第一节职业安全管理健康体系 (21)第二节职业安全管理健康体系作用和意义 (22)第九章安全法规及事故救援预案 (22)第一节矿山安全法规 (22)第二节事故应急救援预按 (23)第十章实习体会和建议 (23)一、实习体会 (23)二、实习建议.................................. 错误!未定义书签。
玉溪矿业有限公司大红山铜矿采矿工艺概述

玉溪矿业有限公司大红山铜矿采矿工艺概述第一节矿山沿革及地质概况1、交通位置大红山铜矿位于新平县老厂乡,地理位置东经101°39′,北纬24°06′,靠哀牢山山脉东侧,戛洒江东岸,海拔标高600-1850米,相对高差1250米,属侵蚀剥蚀山地地形,地势陡峻,河谷发育。
矿区距新平县城102km,距玉溪市219km,距昆明市322km,归玉溪市所辖。
2、矿山沿革及地质概况大红山是1959年发现的大型铁铜矿床,于60年代开始普查勘探,1983年11月进行详勘。
易门矿务局(玉溪矿业有限公司)于1989年9月开始施工主控工程—主副斜井,1993年开始基建探矿,一期于1997年7月1日建成投产,二期于2003年6月26日建成投产。
大红山矿区包括铁矿和铜矿两部分,铁矿主要分布在曼岗河以东(昆钢),铜矿主要分布在曼岗河以西(大红山铜矿)。
全矿分两段建设,以550划界,一期回采550米以上,采用有轨开采方式上行式回采,二期回采550米以下,采用无轨开采方式下行式回采。
大红山铜矿属海底火山喷发沉积变质中厚缓倾斜高温矿床。
矿体走向为东西--北西西,走向长约1800米,倾向南西,倾斜宽约1600米,倾角20—35°,呈层状、似层状产出,矿区共有3个含铁铜矿体I3、I2、I1)和四个含铜铁矿体(Ic、Ib、Ia、I0),自上而下分别为Ic→I3→Ib→I2→Ia→I1→I0),Ic顶板至I0底板约135米。
埋藏深度160-750米,标高821—-29米,其中I3、I2含铁铜矿体规模大,是主要的开采对象,矿石主要金属矿物为黄铜矿、磁铁矿,主要脉石矿物为碳酸岩(白云石为主)、黑云母,矿石整体较稳固,f=8-14,矿岩爆破性能较差。
矿区主要构造:F1、F2、F3、F5。
开采范围:根据1989年地质一大队提交的《云南新平县大红山铁、铜矿区铜矿首采区勘探地质报告》,并经云南省矿产储量委员会批准,铜矿区开采范围:东南自曼岗河,西北至A210线,北东自矿体隐伏头,西南至F3断层,A192线--A210线,—29m--800m标高范围内为铜矿区的开采范围。
- 1、下载文档前请自行甄别文档内容的完整性,平台不提供额外的编辑、内容补充、找答案等附加服务。
- 2、"仅部分预览"的文档,不可在线预览部分如存在完整性等问题,可反馈申请退款(可完整预览的文档不适用该条件!)。
- 3、如文档侵犯您的权益,请联系客服反馈,我们会尽快为您处理(人工客服工作时间:9:00-18:30)。
大红山铜矿废石充填工艺的实践吴东旭,刘 让,舒为民(玉溪矿业有限公司技术中心, 云南玉溪市 653100)摘 要:大红山铜矿通过优化设计,充分利用废石进行采空区充填,成功地解决了尾砂充填料不足与采充严重不平衡的问题,有效地保证了矿山持续生产。
关键词:废石;充填材料;采充平衡;充填工艺0 前言大红山铜矿属海底火山喷发沉积变质中厚缓倾斜高温矿床,由7层矿体组成,I3、I2、I13层铜矿体,I a、I b、I c、I o4层铁矿体。
地质储量铜金属792301t,品位0.81%。
矿体走向E W—N60°W。
走向长1800 m,倾向S3°W,倾斜宽1200m。
倾角25°~5°;埋深191~705m。
矿体平均厚度11.61m,矿岩坚固系数f=10~14。
大红山铜矿建设总规模为日采选铜矿石4800 t,分两期建设;一期工程建设规模为日采选矿石2400t,于1997年7月1日建成投产。
二期工程于2000年元月开工建设,建设规模为日采选矿石2400 t,于2003年6月建成投产。
为了提高投产初期开采的经济效益,一期先采550~620m富矿,采矿方法为底盘漏斗嗣后充填法占85%,房柱法和全面留矿法占15%。
二期为贫富兼采,主要回采标高为400~550m,采矿方法为小中段空场嗣后充填法和房柱法,采用瑞典进口的Boomer281、Si m bar H1354台车凿岩、芬兰进口的T OY O-400E、T OY O-007铲运机出矿,设计充填材料为分级尾砂。
大红山铜矿井下充填料主要为分级尾砂,分级界限为+0.018mm,由于铜矿床中有铁金属伴生,铁作为附产品需进行回收,尾砂产率不高,井下充填料源不足,分级尾砂充填料的缺口为13万m3/a。
1 充填系统一期充填系统包括:地表充填站、水力输送管路、水处理系统、排污系统。
地表充填站设有两个矩形砂仓,两个圆形卧式砂仓和两个Φ7m立式砂仓。
二期充填系统在一期充填系统基础上增加了废石充填斜井,并在地表充填站增设两个Φ9m的立式砂仓。
充填系统工艺流程为:选矿厂全尾砂浆由水隔离泵直接输送到充填制备立式砂仓,经立式砂仓自然分级沉淀,沉砂经立式砂仓造桨自流输送到井下采空区进行充填;立式仓溢流水进入圆形卧式砂仓,溢流水浓度在14%左右,圆形卧式砂仓上部分进入污水处理系统进行二次登清,弥补充填生产上用水不足。
卧式砂仓的泥沙直接排入圆形卧式砂仓或直接排往尾砂库。
水处理系统的细粒泥尾砂由排污溢流系统直接排往尾砂库。
采场充填密闭墙采用C25钢筋混凝土浇灌,密闭墙周边施工锚杆相连。
采场脱水主要靠滤水管溢渗水,中深孔溢水、裂隙渗水等多种综合脱水。
1.1 充填材料与充填参数大红山矿充填料源为自然分级尾砂。
来自选矿厂的全尾砂输送到充填制备站经自然分级沉淀后的分级尾砂作为井下充填料。
分级尾砂充填系统技术参数为:分级尾矿密度:RT=2.95t/m3;充填浓度:Cv=55%~78.8%,C v均=68%;砂浆输送工作流速:Vi=1.98~2.36m/s;充填料浆流量:Q=126~160m3/h;采场充填能力:60~90m3/h。
大红山铜矿自然分级尾砂粒级组成见表1。
表1 大红山铜矿自然分级尾砂粒级组成粒级产率累计产率粒级产率累计产率98u10.3810.3818u19.3986.9174u8.8419.2210u 4.8591.7637u48.3167.52-9u8.241001.2 历年采充情况及充填系统存在的主要问题大红山铜矿历年采充情况见表2。
I SS N1671-2900 CN43-1347/T D 采矿技术 第6卷 第3期M ining Technol ogy,Vol.6,No.3 2006年9月Sep.2006表2 大红山铜矿历年采充情况年份年末充填欠帐(m 3)年充填量(m 3)年空区量(m 3)19991407716368020445120002026761070923097682001301050160921461971200247281321400568681820033318332840386158712004387516334356722623 大红山矿充填系统存在的主要问题为:(1)一期废石系统建设滞后,在充填料不足的情况下,充填欠帐越来越严重,采充矛盾十分突出;(2)自然分级尾砂分级效果不理想。
大红山矿目前充填尾砂-18μm 占13.09%,溢流砂中+18μm 尾砂达30.7%,造成可充尾砂流失严重,可供充填的合格分级尾砂产率大大下降,充填料源短缺;(3)充填制备站充填工艺系统的一、二期工程设计是按4800t/d 生产能力所产出尾矿量配置,随着矿山逐年产量的增长,制备站在原有设备的基础上,虽通过增加了一根DN150管道的技改项目,基本满足矿山日处理矿量在5000t/d 所产出尾矿处理分级尾砂量的需要,但不能满足矿山日处理矿量在7000t/d 所产出尾矿处理分级尾砂量的需要;(4)中段废石充填运输系统能力不畅,600m 水平废石充填斜井提升达不到设计生产能力。
2 充填工艺综合研究2.1 多层矿体开采地压控制大红山矿为多层矿体开采,上层I 3矿体已从535m 中段开采到600m 中段,下层I 2矿体也开始回采。
I 3矿体所形成的空区大多已充填结束,I 2矿体开采是否需要充填,进行了全面分析研究并通过三维有限元模拟计算。
从模拟分析采区整体及夹层塑性区分布来看,上、下两层矿体均充填方案明显优于只充上层矿体方案,且对夹层的影响较小,若只充上层矿体方案夹层上有较多塑性区连片的现象,容易造成夹层不稳定,因此要求对下两层矿体采空区都进行充填。
I 2矿体开采时,各中段矿柱受力情况计算结果见表3。
2.2 回采顺序和充填工序的有效结合结合矿山采矿工艺特点,一期在600m 以上中段采用I 3、I 2矿体共用中段运输巷走向上实行连续回采工艺;竖向方向上I 3、I 2矿体同时考虑回采,两层矿体先采上层矿体,上层矿体出矿结束后再回采下层矿体,下层矿体出矿结束后两层矿体同时充填的开拓布置回采工艺。
两层矿体原则上先采上层矿体,上层矿体出矿结束后再回采下层矿体,下层矿体出矿结束后两层矿体同时充填。
上层矿体采空区充满系数可以降低,一般上层矿体充满系数达到50%即可满足生产的需要。
回采顺序为走向上由两翼向中间连续推进回采,由东向西(中部)回采时,区段盘区结束后,即可辙出该区段的巷道的运输设施;倾向上由南向北上行式回采。
表3 各中段间柱应力间柱名称I 2矿体空区充填σ1(MPa )垂直方向(MPa )I 2矿体空区空场σ1(MPa )垂直方向(MPa )550中段26盘区东矿柱-10.569-28.559-12.473-34.137550中段36盘区东矿柱-10.569-34.113-12.473-34.137550中段48盘区东矿柱-10.569-39.666-12.473-40.530550中段62盘区东矿柱-10.569-39.666-12.473-40.530575中段34盘区东矿柱-14.501-34.113-19.187-53.315575中段52盘区东矿柱-12.535-45.219-12.473-53.315600中段36盘区东矿柱-10.569-39.666-10.235-40.530600中段44盘区东矿柱-16.468-34.113-14.711-34.137600中段60盘区东矿柱-16.468-28.559-19.187-40.530根据生产实际情况,采取局部区段降低空区充满系数,缓解采充矛盾。
根据现有的生探资料,在确切撑握矿体赋存条件,在600m 水平B64线以西I 2矿体已尖灭,矿体厚度在4~8m ,属单层矿体开采的条件下,对600m 水平B64线以西I 3矿体实施回采后其采空区不进行充填作业,让其空区顶板自行垮落充填密闭采空区。
为保证顶板垮落期间不造成安全危害,其采空区采取如下措施。
(1)空区充满系数≥30%。
充填井布置在盘区N 端部,用废石充填满充填井,以保护中段或分段矿柱的稳定性。
采用这一措施解决了一期受充填制约而造成中段与中段之间先回采下一中段和上一中段的I 3矿体,两个中段的I 3矿体采充结束后再回采下一中段的I 2矿体。
同中段上实行两步骤回采即跳采,先采充I 3矿体再回采I 2矿体。
在回采过程中出现I 3、I 2矿体开拓系统的运输和充填回风工程互相交织、多中段难以同时作业、I 2矿体回采损失增加等问题。
(2)为解决废石充填在采空区只能形成半个圆锥体,空区废石量受到很大的限制,盘区废石充填量一般在8%~12%这一大难题,通过对地压变化规律的研究和充填机理的研究分析,根据充填回风平巷和空区顶板位置关系(一般高差不低于8m ),采391 吴东旭,等: 大红山铜矿废石充填工艺的实践切盘区在设计时中部优先布置一条充填井回风井,在盘区N端尾部布置两条充填回风井,形成三角形方式进行盘区废石充填。
在充填回风平巷和空区顶板位置为12m以上时,3条井可同时进行废石充填作业;在充填回风平巷和空区顶板位置为8~12m 以上时,先对布置在盘区N端尾部的两条充填回风井进行废石充填,然后再开始进行中间充填进路的废石充填作业工作,实行波浪式的充填推进作业方式。
为确保中间废石充填进路的安全,在空区顶板充填段进路采取了铁道整体固定悬掉的技术措施方案进行确保。
以提高盘区废石充填和达到保护中段或分段矿柱的目的,采用以上工艺盘区设计废石充填率可达35%以上,如575中段62盘区废石充填量为10996m3,占充填量的55.29%。
2.3 提高废石充填率根据充填回风井的布置情况,充填环节上采用充填尾砂和充填废石形成泥石流的方法进行空区充填。
盘区充填过程中废石、尾砂交替充填的措施,增加盘区废石充填量。
一、二期工程可充填的盘区,各条充填井首先充填废石,当废石充到离空区顶板2 m时,用尾砂把废石带入空区再进行废石充填,通过多次的循环交替充填以增加盘区废石充填量。
由于采用无轨设施备具有比较灵活,二期工程生产的废石直接充入采空区。
在现有的开采工艺上,从一分段的二分层施工一条充填措施道联通采空区,作为盘区废石充填的通道,位置为盘区中间矿柱或二分层的铲矿进路的延伸,通过该技术方案的实施,同分层的周边废石可充入充填空区,可使盘区废石充填率达15%~20%。
根据上下段矿体的回采时间关系,利用时间差,在下段矿体出矿的期间,优先在上段矿体施工一条措施道进入下段矿体的采空区,措施道按今后盘区设计中的铲矿进路进行设计,以达到共用的目的。
设计工程位置一般在下段矿体空区的采矿顶板标高及盘区的东中西部。
通过该技术方案的实施,可使盘区废石充填率达60%以上。
结合两种工艺的实施情况和一期充填的生产经验,根据二期生产盘区的条件,针对一些有条件充填盘区采取充填井布置呈三角形布置,同分段上分层布置充填废石措施道,上分段充填废石铲运措施道同时布置的技术方案,该技术方案实施时,第一步先在同分段上分层措施道进行废石充填,废石充填量可占空区充填量的10%~15%;第二步在上分段充填废石铲运措施道进行大量废石充填,废石充填量可占空区充填量的60%以上,完成上两步工艺废石充填量可占空区充填量的70%以上;第三步从充填回风顶沿进行大量废石充填,废石充填量可占空区充填量的20%~25%以上;完成以上三步废石充填工艺,其废石充填量可占空区充填量的90%以上。