烧结矿成品率控制技术研究
探讨提高烧结机烧结矿产量和质量的实践
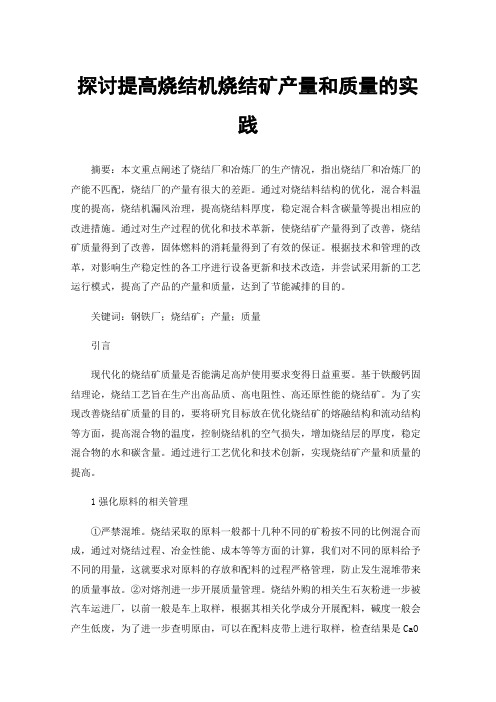
探讨提高烧结机烧结矿产量和质量的实践摘要:本文重点阐述了烧结厂和冶炼厂的生产情况,指出烧结厂和冶炼厂的产能不匹配,烧结厂的产量有很大的差距。
通过对烧结料结构的优化,混合料温度的提高,烧结机漏风治理,提高烧结料厚度,稳定混合料含碳量等提出相应的改进措施。
通过对生产过程的优化和技术革新,使烧结矿产量得到了改善,烧结矿质量得到了改善,固体燃料的消耗量得到了有效的保证。
根据技术和管理的改革,对影响生产稳定性的各工序进行设备更新和技术改造,并尝试采用新的工艺运行模式,提高了产品的产量和质量,达到了节能减排的目的。
关键词:钢铁厂;烧结矿;产量;质量引言现代化的烧结矿质量是否能满足高炉使用要求变得日益重要。
基于铁酸钙固结理论,烧结工艺旨在生产出高品质、高电阻性、高还原性能的烧结矿。
为了实现改善烧结矿质量的目的,要将研究目标放在优化烧结矿的熔融结构和流动结构等方面,提高混合物的温度,控制烧结机的空气损失,增加烧结层的厚度,稳定混合物的水和碳含量。
通过进行工艺优化和技术创新,实现烧结矿产量和质量的提高。
1强化原料的相关管理①严禁混堆。
烧结采取的原料一般都十几种不同的矿粉按不同的比例混合而成,通过对烧结过程、冶金性能、成本等等方面的计算,我们对不同的原料给予不同的用量,这就要求对原料的存放和配料的过程严格管理,防止发生混堆带来的质量事故。
②对熔剂进一步开展质量管理。
烧结外购的相关生石灰粉进一步被汽车运进厂,以前一般是车上取样,根据其相关化学成分开展配料,碱度一般会产生低废,为了进一步查明原由,可以在配料皮带上进行取样,检查结果是CaO含量很低,后期对生石灰粉的取样制度进行不断完善,要求在车上以及卸车以后都进行一次取样以及化验,结算时以CaO含量的最小值为依据,CaO含量不及格的厂家,命令其立即整改,不然拒收。
目前为了提高生石灰粉取样具有绝对的代表性,我们建立了自动取样系统,对整个打灰过程中根据系统的设定自动取样,大大提高了生石灰的合格率与稳定率,同时对生产过程也有积极地作用。
新日铁烧结用矿和烧结技术分析1
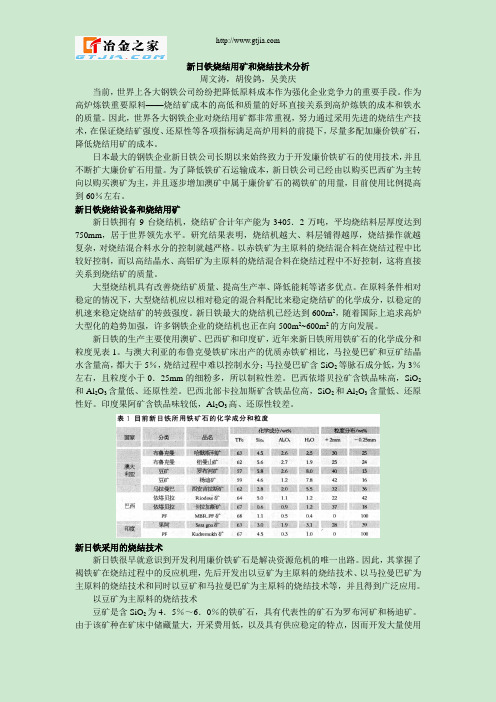
新日铁烧结用矿和烧结技术分析周文涛,胡俊鸽,吴美庆当前,世界上各大钢铁公司纷纷把降低原料成本作为强化企业竞争力的重要手段。
作为高炉炼铁重要原料——烧结矿成本的高低和质量的好坏直接关系到高炉炼铁的成本和铁水的质量。
因此,世界各大钢铁企业对烧结用矿都非常重视,努力通过采用先进的烧结生产技术,在保证烧结矿强度、还原性等各项指标满足高炉用料的前提下,尽量多配加廉价铁矿石,降低烧结用矿的成本。
日本最大的钢铁企业新日铁公司长期以来始终致力于开发廉价铁矿石的使用技术,并且不断扩大廉价矿石用量。
为了降低铁矿石运输成本,新日铁公司已经由以购买巴西矿为主转向以购买澳矿为主,并且逐步增加澳矿中属于廉价矿石的褐铁矿的用量,目前使用比例提高到60%左右。
新日铁烧结设备和烧结用矿新日铁拥有9台烧结机,烧结矿合计年产能为3405.2万吨,平均烧结料层厚度达到750mm,居于世界领先水平。
研究结果表明,烧结机越大、料层铺得越厚,烧结操作就越复杂,对烧结混合料水分的控制就越严格。
以赤铁矿为主原料的烧结混合料在烧结过程中比较好控制,而以高结晶水、高铝矿为主原料的烧结混合料在烧结过程中不好控制,这将直接关系到烧结矿的质量。
大型烧结机具有改善烧结矿质量、提高生产率、降低能耗等诸多优点。
在原料条件相对稳定的情况下,大型烧结机应以相对稳定的混合料配比来稳定烧结矿的化学成分,以稳定的机速来稳定烧结矿的转鼓强度。
新日铁最大的烧结机已经达到600rn2,随着国际上追求高炉大型化的趋势加强,许多钢铁企业的烧结机也正在向500m2~600m2的方向发展。
新日铁的生产主要使用澳矿、巴西矿和印度矿,近年来新日铁所用铁矿石的化学成分和粒度见表1。
与澳大利亚的布鲁克曼铁矿床出产的优质赤铁矿相比,马拉曼巴矿和豆矿结晶水含量高,都大于5%,烧结过程中难以控制水分;马拉曼巴矿含SiO2等脉石成分低,为3%左右,且粒度小于0.25mm的细粉多,所以制粒性差。
巴西依塔贝拉矿含铁品味高,SiO2和Al2O3含量低、还原性差。
烧结矿技术经济指标

烧结矿技术经济指标
一、利用系数,是指单位时间内每m 2有效抽风面积的成品烧结矿质量 有效抽风面积
成品烧结矿台时产量利用系数= 二、台时产量,指每台烧结机每小时的成品烧结矿产量。
烧结机运行总时间
一台烧结机的生产总量台时产量= 三、成品率,指成品烧结矿量占烧结混合料总消耗的百分数。
烧结混合料总消耗量
成品烧结矿量成品率= 四、返矿率,指烧结矿经破碎筛粉所得到的筛下返矿量占烧结混合料总消耗量的百分数。
100⨯=混合料总消耗量
返矿量返矿率% 五、作业率,指烧结机实际作业时间占日历时间的百分数。
100⨯=日历时间
实际作业时间作业率% 六、劳动生产率 指每人每年生产烧结矿的吨数,是烧结厂管理水平和生产技术水平的综合反映。
七、生产成本,指生产每吨烧结矿所需的费用,由原料费和加工费两部分组成。
八、工序能耗,指生产1吨烧结矿所消耗的各种能源总和。
车间烧结矿总产量
标准煤)总能源量(工序能源Kg = 烧结消耗的能源有三种:混合料中的固体燃料,点火用气体燃料和动力,在总能耗中所占比例为:固体燃料约70%,点火燃料和动力各占13%,其它约占4%。
提高烧结机烧结矿产量和质量的实践研究

提高烧结机烧结矿产量和质量的实践研究摘要:按照进一步创新管理与技术的思路,南钢第一烧结厂对于影响生产稳定的每个工艺步骤开展设备更新、技术改造以及试着采取新型的工艺操作方式,提升了烧结矿的产量以及质量,进一步满足了高炉需求以及实现了节能降耗的目标。
关键词:钢铁厂;烧结矿;产量;质量引言随着冶金工业的不断发展,高炉对原材料的需求也日益增加。
烧结和冶炼能力不匹配,烧结矿的生产缺口很大,因此,如何提高烧结矿的产量是各个公司当前的重点工作。
烧结矿作为高炉的主要原材料,其比例在70%以上,因此,烧结矿的质量是否能够满足高炉的使用需求就变得尤为重要。
现代烧结法是在铁酸钙固结原理的基础上,研制出了高品位、高强度、高还原性的高质量烧结矿。
1影响烧结矿产量和质量的因素1.1烧结配料结构影响在烧结生产工艺过程中的混合料是由含铁混匀矿、各种熔剂以及燃料等按照适量配比进行混配而成,而含铁混匀矿是各种铁矿粉、含铁返回料等按照一定的比例混配而成。
烧结配料是要根据各烧结原料的供应情况、储备情况、消耗情况,综合考虑烧结矿的产量和质量指标的需求情况,同时要兼顾烧结矿成本情况。
1.2混合料温度影响通过增加料温可以有效地抑制烧结的过湿性,在料温上升到高于水分凝结的露点温度时,可以防止水分凝结,通过对烧结物料过湿形成的抑制,使其透气性得到改善,从而提高了烧结矿的产量和质量,为厚料层的生产提供了良好的条件。
1.3漏风率与料层厚度在烧结过程中,如果台车出现漏风问题,将会导致烧结矿减产、同时增加耗电成本,台车的治理漏风,是提矿产量,保证矿质量,降低制矿成本措施中最直接有效的一种。
烧结的燃烧是从上到下进行的,座椅材料越致密,中部以及下部的储热效果也就越强。
若能有效地改善烧结部分的透气性,可提高烧结层的生产质量,同时降低固体燃耗。
2提高烧结矿产量和质量的措施2.1优化烧结配矿结构根据国际市场以及港口各种铁矿石市场价格变化,及时进行各种铁矿粉的性价比测算,从而保证在满足烧结矿质量的前提下降低采购成本,实现优化配矿结构,高性价比的进行配矿生产。
探讨提高烧结矿质量的措施

江西冶金职业技术学院毕业论文论文题目:浅谈提高烧结矿的质量的措施姓名:班级:系部:指导老师:时间:1 烧结的起因 32烧结的目的意义 33影响烧结矿质量的因素 33.1烧结矿的品位 33.2 SiO2含量 33.3烧结矿碱度 33.4 MgO%含量 33.5水分 33.6料层厚度 34 提高烧结矿质量的措施 34.1优化入烧原料结构 34.1.1 优化入烧原料结构,稳定控制烧结矿化学成分 34.1.2改善入烧燃料质量 34.2生产高碱度烧结矿 34.3操作技术改进 34.3.1自动配料技术 34.3.2低温点火技术 34.3.3强力造球技术 34.3.4厚料层技术 34.4设备技术改造 34.4.1添加剂仓技术改造 34.4.2混料系统技术改造 34.4.3筛分系统技术改造 3摘要:本文简述了影响烧结矿质量的因素,系统的介绍了提高烧结矿质量的技术措施。
关键词:烧结矿质量技术措施1 烧结的起因烧结生产起源于英国和德国。
大约在1870年,这些国家就开始使用烧结锅,用来处理矿山开采、冶金工厂、化工业厂等废弃物。
1892年美国也出现了烧结锅。
世界钢铁工业第一台带式烧结机于1910年在美国投入生产。
这台烧结机的面积为8.325m2(1.07m×20.269m),当时用于处理高炉炉尘,每天生产烧结矿140t。
它的出现引起了烧结生产的重大变革,从此带式烧结机得到了广泛的应用。
我国铁矿资源十分丰富。
由于历史的原因,建国前钢铁工业十分落后,烧结生产更为落后,1926年3月在鞍山建成四台21.63m2(1.067m×20.269m)带式烧结机,日产量1200t。
1935年,1937年有相继建成四台50m2烧结机,每年产量达19万t。
建国后,我国烧结工业有了很大的发展,1952年鞍钢从苏联引进75m2烧结设备和技术,这套在当时具有国际先进水品的设备,对新中国的烧结工业起到了示范作用。
随着我国钢铁工业的不断发展,一些钢铁公司的烧结厂相继建成投产。
提高烧结机烧结矿产量和质量的实践探析

提高烧结机烧结矿产量和质量的实践探析摘要:钢铁产业的发展对我国社会经济具有重要影响,新时期,钢铁厂如何提高烧结机烧结矿产量和质量,成为现阶段主要研究任务,对此,本文集中分析了具有可行性的提高产量以及质量的实践措施,希望可以为业内人士提供参考。
关键词:钢铁企业;烧结矿;烧结机;产量;质量;实践措施社会经济的飞速发展对钢铁资源需求日益日常,而在技术、管理创新发展趋势下,我国烧结厂有必要从实际出发,积极优化、更新生产工艺、生产设备,不断结合实际需求进行技术改造,从而提高烧结矿的产量以及质量,迎合需求的同时,落实国家提倡的节能降耗目标。
由此可见,本文对提高烧结机烧结矿产量和质量的实践探析,具有十分重要的现实意义。
一、规范原料管理(一)禁止原料混堆分析烧结原料可知,通常情况涉及到了十几种矿粉,并且是按照一定的比例混合。
不同原料用量不同,所以,需要加强管理原料的存放、配料过程,确保不同原料不会混合堆放,进而避免出现质量事故。
(二)加强熔剂质量管理烧结外购的生石灰粉主要是通过汽车运输进厂,以往主要是在车上进行取样,结合相关化学成分,进行配料操作,此种情况非常容易出现碱度低废。
对此,工作人员可以在配料皮带上取样,获取到的检查结果是,氧化钙含量过低[1]。
因此,企业需要制定出完善且全面的生石灰粉取样制度,明确要求,进行两次取样和化验,即车上、卸车后,同时,需要规定出结算结果标准,以氧化钙含量最小值为主,如果化验结果氧化钙含量不合格,企业应当直接命令厂家进行整改,否则拒绝收货。
为了进一步提高生石灰粉取样质量,企业可以积极建设自动取样系统,根据系统的设定对整个打灰过程实施自动取样,这样能够很好的保证生石灰合格率,有利于确保企业生产。
二、科学搭配原料结构(一)合理选择含铁原料为保障烧结质量达到相应的指标要求,有必要合理对原料结构进行搭配,进而提升烧结矿质量。
例如,一些企业通过使用巴西精矿低硫粉,发现其亲水性差,不利于造球,同时,在烧结废气中会产生大量的SO,严重影响到了后续脱硫效2果。
改进烧结生产工艺技术与提高烧结矿质量的研究
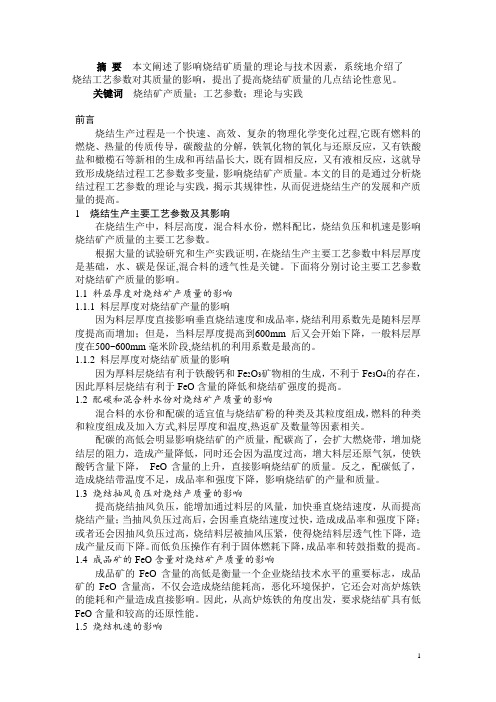
摘要本文阐述了影响烧结矿质量的理论与技术因素,系统地介绍了烧结工艺参数对其质量的影响,提出了提高烧结矿质量的几点结论性意见。
关键词烧结矿产质量;工艺参数;理论与实践前言烧结生产过程是一个快速、高效、复杂的物理化学变化过程,它既有燃料的燃烧、热量的传质传导,碳酸盐的分解,铁氧化物的氧化与还原反应,又有铁酸盐和橄榄石等新相的生成和再结晶长大,既有固相反应,又有液相反应,这就导致形成烧结过程工艺参数多变量,影响烧结矿产质量。
本文的目的是通过分析烧结过程工艺参数的理论与实践,揭示其规律性,从而促进烧结生产的发展和产质量的提高。
1 烧结生产主要工艺参数及其影响在烧结生产中,料层高度,混合料水份,燃料配比,烧结负压和机速是影响烧结矿产质量的主要工艺参数。
根据大量的试验研究和生产实践证明,在烧结生产主要工艺参数中料层厚度是基础,水、碳是保证,混合料的透气性是关键。
下面将分别讨论主要工艺参数对烧结矿产质量的影响。
1.1 料层厚度对烧结矿产质量的影响1.1.1 料层厚度对烧结矿产量的影响因为料层厚度直接影响垂直烧结速度和成品率,烧结利用系数先是随料层厚度提高而增加;但是,当料层厚度提高到600mm后又会开始下降,一般料层厚度在500~600mm毫米阶段,烧结机的利用系数是最高的。
1.1.2 料层厚度对烧结矿质量的影响因为厚料层烧结有利于铁酸钙和Fe2O3矿物相的生成,不利于Fe3O4的存在,因此厚料层烧结有利于FeO含量的降低和烧结矿强度的提高。
1.2 配碳和混合料水份对烧结矿产质量的影响混合料的水份和配碳的适宜值与烧结矿粉的种类及其粒度组成,燃料的种类和粒度组成及加入方式,料层厚度和温度,热返矿及数量等因素相关。
配碳的高低会明显影响烧结矿的产质量,配碳高了,会扩大燃烧带,增加烧结层的阻力,造成产量降低,同时还会因为温度过高,增大料层还原气氛,使铁酸钙含量下降,FeO含量的上升,直接影响烧结矿的质量。
反之,配碳低了,造成烧结带温度不足,成品率和强度下降,影响烧结矿的产量和质量。
烧结机烧结矿产量和质量提升的实践研究
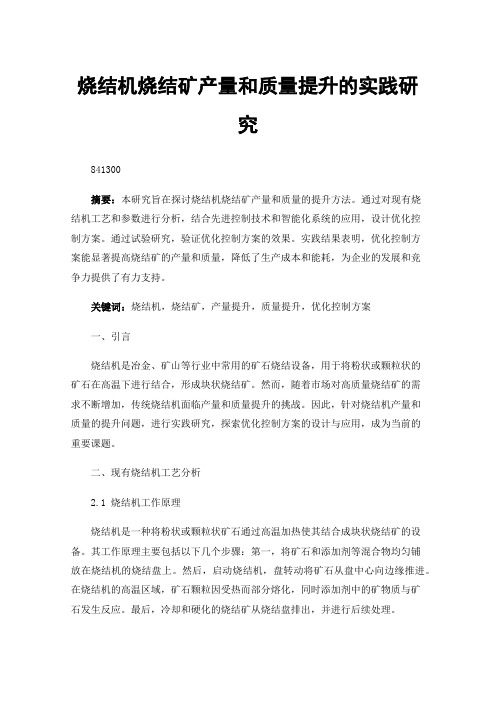
烧结机烧结矿产量和质量提升的实践研究841300摘要:本研究旨在探讨烧结机烧结矿产量和质量的提升方法。
通过对现有烧结机工艺和参数进行分析,结合先进控制技术和智能化系统的应用,设计优化控制方案。
通过试验研究,验证优化控制方案的效果。
实践结果表明,优化控制方案能显著提高烧结矿的产量和质量,降低了生产成本和能耗,为企业的发展和竞争力提供了有力支持。
关键词:烧结机,烧结矿,产量提升,质量提升,优化控制方案一、引言烧结机是冶金、矿山等行业中常用的矿石烧结设备,用于将粉状或颗粒状的矿石在高温下进行结合,形成块状烧结矿。
然而,随着市场对高质量烧结矿的需求不断增加,传统烧结机面临产量和质量提升的挑战。
因此,针对烧结机产量和质量的提升问题,进行实践研究,探索优化控制方案的设计与应用,成为当前的重要课题。
二、现有烧结机工艺分析2.1 烧结机工作原理烧结机是一种将粉状或颗粒状矿石通过高温加热使其结合成块状烧结矿的设备。
其工作原理主要包括以下几个步骤:第一,将矿石和添加剂等混合物均匀铺放在烧结机的烧结盘上。
然后,启动烧结机,盘转动将矿石从盘中心向边缘推进。
在烧结机的高温区域,矿石颗粒因受热而部分熔化,同时添加剂中的矿物质与矿石发生反应。
最后,冷却和硬化的烧结矿从烧结盘排出,并进行后续处理。
2.2 烧结机工艺参数分析烧结机的工艺参数对产量和质量影响深远。
其中,烧结机的烧结温度是关键参数之一,过高的烧结温度可能导致矿石过度熔化,使烧结矿产生粘结现象,影响烧结矿的质量;过低的烧结温度则会导致烧结不完全,影响烧结矿的强度和耐磨性。
此外,烧结机的烧结速度、烧结时间、烧结机料层的厚度等参数也对烧结矿的质量和产量有重要影响。
2.3 存在的问题与挑战在现有烧结机工艺中,普遍存在着一些问题和挑战。
第一,传统烧结机工艺对矿石的加热均匀性有限,导致产量不稳定,质量波动较大。
第二,烧结机工艺参数的调整和优化难度较大,往往需要凭经验和试验进行,效率较低。
改善烧结矿产质量指标的研究

改善烧结矿产质量指标的研究【摘要】本研究就烧结矿的原料性能、燃料破碎质量、燃料分加、烧结矿品位、冶金性能等对烧结矿产质量的影响进行了研究,提出了改善烧结产质量的途径。
【关键词】烧结;改善;产质量;技术0.前言随着高炉铁产量的不断增加,高炉对烧结矿的需求也不断增加;同时,世界范围内钢材市场波动频繁,钢铁企业为了保证效益和增强竞争力对钢材质量的要求必然就会不断的提升。
为满足高炉生产优质生铁的要求,烧结矿的质量也需要不断的改善。
综上所述,从烧结工艺上进行改善烧结矿产质量指标的研究显得意义深远。
因此,本文就改善烧结矿产质量指标从工艺上进行了研究。
1.提高烧结矿产量的研究1.1提高烧结机的利用系数在烧结厂,烧结机是所有设备和工艺的核心,它的利用系数的高低直接或间接的影响烧结矿的产量。
本研究在借鉴前人研究的基础上,从原料性能、和烧结工艺环节上进行了提高烧结机利用系数的研究,取得了显著成效。
1.1.1尽可能降低焦粉的平均粒度借鉴韶钢烧结厂的研究,本研究从焦粉破碎流程及外部局限条件上作了分析和实验。
韶钢烧结厂焦粉的平均粒度一直偏高,小于3mm粒级百分比一直偏低。
参照韶钢烧结厂焦粉粒度条件,为了加强焦粉破碎,可采取以下方法:一、控制购进碎焦的上限粒度,要求小于15mm的焦粉所占比例不得低于90%,杜绝购进大于20mm粒度的碎焦。
二、提高对辊机和四辊机的破碎效率,使经对辊机破碎后的焦粉,其小于8mm 的比例必须占90%以上;经四辊机上辊破碎后,小于5mm的粒级应占80%以上;四辊机下辊破碎完的焦粉,小于3mm的应占72%以上。
通过研究和生产实践,我们可以看出经过努力,焦粉粒度小于3mm的逐年提高,由于细粒度焦粉的提高,改善了焦粉在料层中的燃烧效率,加快了燃烧速度,燃烧前锋变窄,提高了料层的透气性,烧结利用系数得以提高,同时,烧结矿的产量大幅度提高。
1.1.2稳定原料的理化性能原料理化性能的波动,对烧结利用系数极为不利。
烧结系统的控制方案

烧结系统的控制方案1、烧结目的及意义高炉炼铁对含铁原料的要求是:品位高、有害杂质少、还原性好、高温性能优良、强度高、粒度适宜、化学成分稳定均匀。
铁矿粉烧结是目前铁矿粉造块的主要方法,它不仅将粉矿进行造块供高炉炼铁使用,而且通过造块改善铁矿石的冶金性能,使高炉冶炼获得良好的效果。
我国铁矿石多为贫矿和复合矿,必须进行细磨选矿,细磨后铁矿粉必须造块才能被高炉使用。
铁矿粉烧结技术是目前世界上产量最大、使用最广泛的造块方法之一。
2、工艺过程的控制要求2.1烧结工艺概述是指根据原料特性所选择的加工程序和烧结工艺制度。
它对烧结生产的产量和质量有着直接而重要的影响。
本工艺按照烧结过程的内在规律选择了合适的工艺流程和操作制度,利用现代科学技术成果,强化烧结生产过程,能够获得先进的技术经济指标,保证实现高产、优质、低耗。
本生产工艺流程有原料的接受,兑灰,拌合,筛分破碎及溶剂燃料的破碎筛分,配料,混料,点火,抽风烧结,抽风冷却,破碎筛分,除尘等环节组成。
烧结过程示意图如下。
图2-1 烧结过程示意图烧结生产工艺的过程就是将准备好的矿粉、燃料和溶剂,按一定的比例配料,然后再配入一部分烧结机尾筛分的返矿,送到混合机混匀和造球。
混好的料由布料器铺到烧结机台车上点火烧结,烧成的烧结矿经破碎机破碎筛分后,筛上成品烧结矿送往高炉,筛下物为返矿,返矿配入混合料重新烧结,烧结过程产生的废气经除尘器除尘后,由风机抽入烟囱,排入大气。
下面是一些具体的实例控制。
2.2配料的控制要求对配料的基本要求是准确。
即按照计算所确定的配比,连续稳定地配料,把实际下料量的波动值控制在允许的范围内。
当燃料配入量波动0.2%时,就足以引起烧结矿强度与还原性的变化;当矿粉或熔剂配入量发生变化时,烧结矿的含铁量与碱度即随之变化,都将导致高炉炉温、炉渣碱度的变化,对炉况的稳定、顺行带来不利影响。
为保证烧结矿成分的稳定,生产中当烧结机所需的上料量发生变化时,须按配料比准确计算各种料在每米皮带或单位时间内的下料量;当料种或原料成分发生变化时,则应按规定的要求,并准确预计烧结矿的化学成分。
论烧结生产过程控制的精细化和标准化对稳定烧结矿质量的重要性
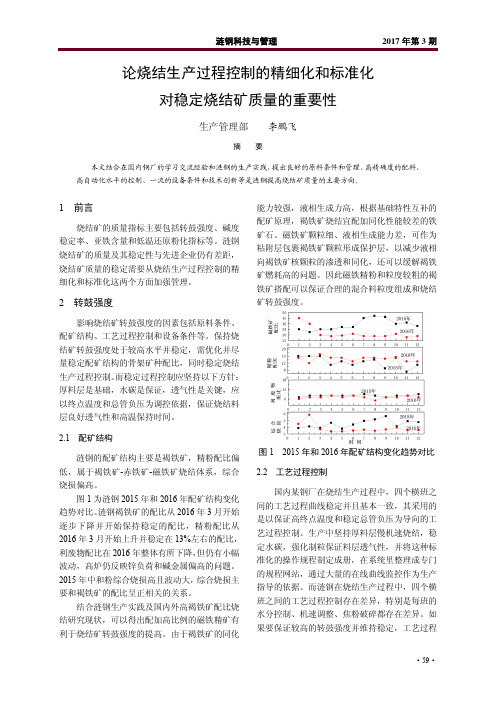
涟钢科技与管理 2017年第3期・59・论烧结生产过程控制的精细化和标准化对稳定烧结矿质量的重要性生产管理部 李鹏飞摘 要本文结合在国内钢厂的学习交流经验和涟钢的生产实践,提出良好的原料条件和管理、高精确度的配料、高自动化水平的控制、一流的设备条件和技术创新等是涟钢提高烧结矿质量的主要方向。
1 前言烧结矿的质量指标主要包括转鼓强度、碱度稳定率、亚铁含量和低温还原粉化指标等。
涟钢烧结矿的质量及其稳定性与先进企业仍有差距,烧结矿质量的稳定需要从烧结生产过程控制的精细化和标准化这两个方面加强管理。
2 转鼓强度影响烧结矿转鼓强度的因素包括原料条件、配矿结构、工艺过程控制和设备条件等。
保持烧结矿转鼓强度处于较高水平并稳定,需优化并尽量稳定配矿结构的骨架矿种配比,同时稳定烧结生产过程控制。
而稳定过程控制应坚持以下方针:厚料层是基础,水碳是保证,透气性是关键,应以终点温度和总管负压为调控依据,保证烧结料层良好透气性和高温保持时间。
2.1 配矿结构涟钢的配矿结构主要是褐铁矿,精粉配比偏低,属于褐铁矿-赤铁矿-磁铁矿烧结体系,综合烧损偏高。
图1为涟钢2015年和2016年配矿结构变化趋势对比。
涟钢褐铁矿的配比从2016年3月开始逐步下降并开始保持稳定的配比,精粉配比从2016年3月开始上升并稳定在13%左右的配比,利废物配比在2016年整体有所下降,但仍有小幅波动,高炉仍反映锌负荷和碱金属偏高的问题。
2015年中和粉综合烧损高且波动大,综合烧损主要和褐铁矿的配比呈正相关的关系。
结合涟钢生产实践及国内外高褐铁矿配比烧结研究现状,可以得出配加高比例的磁铁精矿有利于烧结矿转鼓强度的提高。
由于褐铁矿的同化能力较强,液相生成力高,根据基础特性互补的配矿原理,褐铁矿烧结宜配加同化性能较差的铁矿石。
磁铁矿颗粒细、液相生成能力差,可作为粘附层包裹褐铁矿颗粒形成保护层,以减少液相向褐铁矿核颗粒的渗透和同化,还可以缓解褐铁矿燃耗高的问题。
提高烧结矿成品率
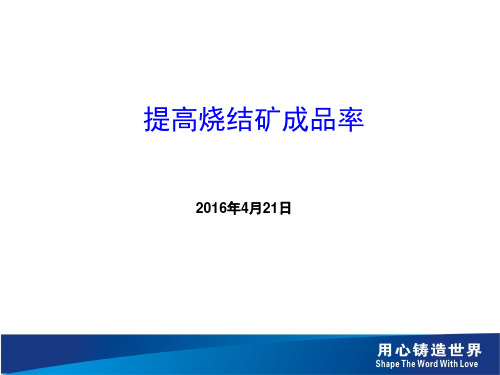
梭布皮带机链 条调整不当
物料湿度控 制不当
法
环
阴雨天物料较为潮湿
露天料场
仪表计量不准
测
影响布料效果因果分析图
因 素 一:
未经岗位培训
现场调查
※ 岗位操作规程齐全,各工段定期按《烧结球团 厂各岗位人员工作标准》对操作工进行岗位操作 培训,并进行理论及实作考试,查看以往培训记录 操作工理论考试平均分数达90分,实作平均分数达 94.5分。
A
A
C
A
16
难以控制
湿度自动加水
选
2、制作专用喷头
C
A
B
B
12
不选
注:A:5分,B:3分,C:1分 制表:李力
日期:2015.9.20
十 对策实施
¢?
制图:李力
改造后
日期:2015.9.20
改造后布料演示
现场实物图
未加设圆盘布料器图
加设圆盘布料器图
效果: 添加圆盘布料器后,料槽料位布置均匀,解决了堵料、断料现象
86
5.88% 84.32%
92
5.88% 90.20%
96
3.92% 94.12%
99
2.94% 97.06%
102
2.94
100%
100%
制表日期:2015.4.23
烧结矿成品率低原因排列图
制图:李力
制图日期:2015.4.23
五 确定目标
目标:烧结矿成品率提升到90%
活动后
烧
结
矿
成
活动前
品
学历 大专 高中 本科 大专 本科 中专
成员简介
职称
改善烧结矿表面点火质量提高成品率的研究

( ) 料 层 厚 度 提 高后 , 保 证 透 气 性 良好 , 5 为 应 对 混 合 料 粒 度 组 成 进 行 合 理 控 制 ,即二 ? < 昆后
( ) 操 作 中根 据 不 同 的煤 气 热 值 、 力 , 2 压 对 煤气 瞬 时 流量 进行 调 整 ,保 证 助燃 风 和 煤 气 比例
合适。
43 由于烧 结 面积 不 同 , 于点 火时 间 和负压 , . 对 也 确 定 了几个 不 同的 方案 分别 进行 摸索
一
( ) 控 制合 适 的 点火 时 间 和 点火 负 压 , 证 3 保
的点 火 温度 。小 于这 一 比例 时 , 温度 能 满 足要 求 ,
烧 结机作 为研 究 对象 。( 20 从 0 8年 8月到 2 0 0 9年 6月 , 烧 结 厂 已经 过 两 次 合并 , 为 炼 铁 厂 的一 原 成 部 分 。本 文 的研 究 内容 均 在原 烧 结 厂混 合 煤 气点 火 的条件 下进 行 ) ( ) 在 现 有原 料 结 构条 件 下 , 1 控制 合适 的点
鑫
关键词 : 表面点火质量 点火温度 点火时间 料层厚度 点火热耗
1 前 言
点 火深 度 。 ( ) 提 高料 层 厚 度 , 保证 烧 结 矿表 面 点火 4 在 质 量 的前 提 下 , 当控 制点 火 温度 , 过 调整煤 气 适 通 流量和 配风 比例来 实现 。
承钢 炼铁 厂 西 区现 有 3 0 烧结 机 ( 一 台 , 6 m2 1) 系 原 5 m 结 机 扩 建 改 造 ,5 m 机 上 冷 却 烧 结 0 烧 10
毕业论文--马钢烧结厂烧结矿质量控制设计

马钢烧结厂烧结矿质量控制设计1.绪论1.1 引言美国著名质量管理专家朱兰(]. M. Juran)1994 年在美国质量管理学会年会上说过,20 世纪将以“生产力的世纪”载入史册, 21 世纪是“质量的世纪。
”他的预言正在逐步地现实。
刚刚跨入21 世纪,人们就感受到自身己置于一种浓厚的竞争氛围中,竞争无处不在。
国家间的竞争正逐渐被市场的竞争、产品的竞争所代替,而市场的竞争又从企业间的竞争发展为供应链间的竞争。
在这场无国界的竞争中,质量扮演着极为重要的角色。
随着社会生产力不断发展,新技术不断涌现,面对日趋激烈的国际、国内市场的竞争,能否提供高质量的产品和服务不仅仅是企业在竞争中能否取得优势的问题,说严重点,它直接关系到企业的生存问题。
每个企业、每种产品和服务,要想在国际市场上占有一席之地,都要面对“超严格的质量要求”,要努力使自己达到世界级的质量水平。
1.2 质量控制研究的背景及意义在我国加入WTO 既成事实的情况下,面对日趋激烈的国际、国内市场的竞争,企业能否提供高质量的产品和服务不仅仅是企业在竞争中能否取得优势的问题,说严重点,它直接关系到企业的生存问题。
因此,我国企业要想在未来的竞争中占有一席之地,必须对产品质量提出更高的要求,且这种高要求应不以高投入为条件。
因此,作为国际上通行的行之有效的质量管理技术 SPC,正在受到越来越多国内企业的重视,并被视为企业降低废品率、提高产品质量、增加企业效益,全面推行 IS09000 和 QS9000 质量管理体系的重要工具。
要提高产品质量,必须对生产、制造各环节进行质量控制,必须大力提倡对质量科学的应用,如对生产线推行和实施各种质量科学技术,用以保证实现生产过程控制中的预防原则。
这方面SPC(Statistical Process Control)即统计过程控制及其系列技术如SPD(Statistical Process Diagnosis)即统计过程诊断和DOE(Design of Experiments)等扮演了重要角色。
通过现场控制FeO技术来保证烧结质量和效益探索

通过现场控制FeO技术来保证烧结质量和效益探索摘要:随着我国社会水平的提升,经济步伐的推进,我国的烧结事业也在这个过程中得到了较大程度的发展。
其中,现场控制FeO技术是我们在实际烧结过程中经常会用到的一种技术,对于稳定控制烧结过程具有非常好的效果。
在本文中,将就现场控制FeO技术来保证烧结质量和效益的方式与意义进行一定的研究。
关键词:现场控制;FeO技术;烧结质量;效益1 引言近年来,我国的烧结事业得到了蓬勃的发展,炼铁厂以及烧结厂无论是在规模上还是数量上都在我国得到了较大的提升。
而在我们烧结矿的过程中,其中FeO的含量是我们一直非常关注的质量指标,其将对于烧结的质量以及企业的整体效益都具有非常大的影响。
对此,就需要我们能够对FeO现场控制技术的意义以及控制方式进行全面的掌握。
2 烧结矿FeO含量影响因素2.1 烧结原料烧结原料是烧结矿中FeO的最主要的来源,但是我们在实际生产过程中,通常都会根据烧结过程汇总所具有含铁原料的配比,并通过加权的方式对混合料中FeO含量进行计算。
其中,含铁原料则是我们对烧结矿FeO含量进行控制的最主要要素。
2.2 烧结配碳量在我们烧结的过程中,在保证烧结矿碱度不变的情况下,矿中FeO的含量会随着配碳量的增加而增加。
经过实践表明,当燃料中配比增加时,烧结矿中的FeO也会随之增加,而这则是因为随着混合料中配碳量的增加而出现较强的还原气氛与温度水平。
3 FeO含量同烧结质量与产量的关系在我们实际生产的过程中,可以发现烧结矿中FeO含量同燃料配比以及生产率都存在一定的联系:当烧结矿碱度为1.4时,FeO含量在烧结矿中的起点较高,而且其所具有的烧结生产率变化情况通常较慢;而如果其中的碱度值为1.7,那么FeO中的含量则会显示出具有不同区间的规律变化,而烧结生产率所具有的起点则较高;而如果碱度值变为2.1,那么矿中所具有的FeO含量更低,且生产率所具有的起点值较高。
而根据这种情况,我们则可以在面对较高碱度时应当选择起点较低的燃料配比作为烧制现场的主要控制方向,从而获得较好的生产率,而对于碱度较低的烧结矿来说,则应当选择中上燃料的配比,来获得更高的生产率。
浅谈烧结生产的过程控制

浅谈烧结生产的过程控制摘要:本文就ISP工艺中烧结的生产实际,谈谈在烧结生产过程中如何加强主要环节、重点工序的控制,以保证烧结生产过程有效有序的平稳进行。
关键词:烧结生产过程控制烧结生产流程长,工序复杂,要抓好整体生产平稳、连续高效,既要做好各岗位的精细操作,更要注重主要环节、工序的生产条件与控制、信息反馈、沟通,这样才能由点及面、有重点突出的做好生产组织,保障生产流程平稳,条件优化、合理受控。
一、抓好精矿的配料精矿的品质决定烧结反应的良好与否,目前我厂采用ISP冶炼方式,其最大特点就是能处理各种品位的铅锌混合矿,但也带来精矿配料的困难,精矿成份波动较频繁,特别是pb、zn、s、sio2等含量的变化。
我厂ISP技改后精矿配料有了很大改善,由最初的圆盘配料改为准确度较高、稳定性较好的电子皮带秤配料,避免了计量不准、岗位劳动环境差的缺点,使精矿化学成份稳定性得到明显提高,其中pb、zn受控合格率达到了90%以上。
精矿仓配料采用堆式横向切割配料方式,在混合过程中做到尽量多抓、不混抓,在电子皮带秤的使用中同时开启两台以上进行配料,进一步稳定料量,减少成份波动。
加强配料与生产调度的协调、信息反馈,根据炉料在烧结过程中的反应,通过小时化验快样获取配料信息,对不利方面及影响因素及时调整、改善。
1、炉料化学成分控制(1)Pb在烧结焙烧过程中是一种硬化剂,与炉料中SiO2形成低熔点PbSiO3;在750—800℃较高温度下焙烧PbS时,当产生一定量氧化产物后,便会出现液相(大部分即是PbSiO3)对炉料起到粘接作用,有利于炉料的烧结焙烧。
提高Pb含量可增加烧结块强度,但过高(Pb>24%)会使烧结块强度急剧下降。
在焙烧中防止PbS转化为PbSO4(难分解物),要加强:a提高烧结焙烧过程的温度(750—900℃)b增加精矿投入量c强氧化气氛d炉气中SO2(SO3)浓度要低。
即要求及时排走。
(2)ZnS焙烧反应ZnS结构致密,在反应中生成的硫酸物和氧化物膜层紧裹在颗粒表面,阻碍反应进行,因此要较长时间、过量空气和较高温度,使其转变为ZnO。
- 1、下载文档前请自行甄别文档内容的完整性,平台不提供额外的编辑、内容补充、找答案等附加服务。
- 2、"仅部分预览"的文档,不可在线预览部分如存在完整性等问题,可反馈申请退款(可完整预览的文档不适用该条件!)。
- 3、如文档侵犯您的权益,请联系客服反馈,我们会尽快为您处理(人工客服工作时间:9:00-18:30)。
and implemented on the based of process and raw materials. Sinter average yield has increased from 69. 02% to 77. 47% .
0
前言
烧结矿成 品 率 是 指 成 品 烧 结 矿 ( 一 般 粒 度 ≥ 5 mm) 占烧结饼量的比率。 烧结矿成品率的提高, 就意味着烧结生产效率的提升。烧结矿成品率的高 不仅直接影响烧结机的生产率, 同时还会影响烧 低, 结矿生产的能源消耗及成本
· 6·
河
南
冶
金
2012 年第 2 期
少了变料次数, 稳定了烧结原料结构。 2. 3 烧结过程工艺参数控制 1 ) 烧结机料层厚度。 增加烧结机料层厚度, 可 有利于烧结 以相对降低表层低强度烧结饼的含量, 原料 矿成品率的提高。 料层厚度的增加要与工艺、 2 条件相适应。400 m 烧结机料层厚度的控制原则 是: 基准料 层 厚 度 700 mm ( 与 烧 结 机 栏 板 平 齐 ) 。 根据原料结构中粉矿配用比例灵活调整。 在工艺、 原料条件许可的情况下, 尽可能保持较高的料层厚 度控制水平。具体控制方法如下: 粉矿配用比例 25% ~ 45% 时, 烧结机料层厚度 700 mm ~ 730 mm, 并适当压料; 粉矿配用 比 例 低 于 25% 时, 烧结机安装松料 器, 料层厚度 700 mm; 粉矿配用比例大于 45% 时, 烧结机料层厚度控 制在 730 mm 以上, 实行超厚料层烧结。 如 2010 年 6 月份, 烧结原料结构配比中粉矿配 最低值达 12. 5% 。在使用该 用比例降低到 22. 0% , 原料结构的混匀料之前, 在烧结机上加装了能够改善 烧结机料层厚度按 700 mm 控 料层透气性的松料器, 制。8 月份, 烧结原料结构配比中粉矿配用比例增加 53% , 到了 最高达 55. 5% 。在使用该原料结构的混 匀料之前, 及时拆除了松料器, 并把烧结机料层厚度 控制在了 750 mm 以上, 实行超高料层烧结。同时, 增 就保证了烧结机使用不 加了压料装置的重量。这样, 同原料结构的混匀料时, 烧结料层透气性的相对稳 定, 为烧结矿成品率的有效控制创造了条件。 2 ) 垂直烧结速度。 在一定的原料条件下, 垂直 烧结速度和烧结矿强度呈负相关关系 。当使用混合 料烧结性能变化时, 可以通过适当控制垂直烧结速 度而对烧结矿强度进行控制, 从而达到稳定烧结矿 成品率的目的。控制垂直烧结速度常用的方法, 一 是控制主抽风机风门开度, 调整烧结机上料量 ( 实 际是控制烧结机生产率 ) ; 二是控制烧结机料层厚 度、 压料程度等。 3 ) 布料和点火。 布料控制重点是料面平整, 无 空洞出现, 压料时要左右均匀, 保持整个烧结料层透 气性的均匀性。台车两侧料面适当压料, 以减轻边 应 缘效应的作用。均匀的布料反映在机尾断面上, 该是红矿层基本控制在一条直线上 。 在点火操作控制上, 除保持适宜的点火温度、 点 还要保持一定的点火深度, 实行微负压点 火强度外, 火。这样, 可以在一定程度上减小烧结机料面裂纹 的程度, 有利于烧结矿返矿的降低。 4 ) 混合料水、 碳含量。 混合料水、 碳的控制内
*
联系人: 高丙寅, 高级工程师, 河南. 安阳( 455004 ) , 安阳钢铁股份有限公司炼铁厂;
2012 年 第 2 期
河
南
冶
金
· 5·
粒而产生的粉末含量, 在烧结机系统设计定型后, 只 有靠改善烧结矿强度的措施来完成 。 2 烧结矿成品率控制的技术措施 控制烧结矿成品率的措施应根据烧结矿返矿产 结合烧结生产的工艺、 原料等具体条件而 生的途径, 制定。烧结生产的工艺、 原料条件不同, 各个影响因 素对成品率的影响程度不同, 采取的具体技术措施 也不尽相同。为了掌握适合安钢工艺、 原料条件实 际的烧结矿成品率控制技术, 提高烧结矿成品率, 安 钢烧结厂在 400 ㎡烧结机系统进行了烧结矿成品率 控制技术的研究。 2. 1 烧结矿强度控制 要控制好烧结矿成品率, 首先要控制好烧结矿 强度这个基础。如果单从提高烧结矿成品率的角度 应该是烧结矿强度即转鼓指数愈高愈好。 但 考虑, 是, 由于影响烧结矿强度的因素很多 , 尤其是在复杂 多变的铁矿粉市场条件和严峻的成本压力下 , 要长 期将烧结矿转鼓指数维持在一个较高的水平上是不 现实的, 故烧结矿强度的波动在所难免。 为了避免 因烧结矿强度波动对烧结矿成品率带来大的影响 , 采取的控制措施是: 1 ) 根 据 烧 结 矿 转 鼓 指 数 波 动 情 况 分 段 控 制。 当转鼓指数≥78% 时, 生产过程工艺参数按正常状 态控制; 转鼓指数在 78% ~ 76% 之间时, 适当增加 提高烧结矿 FeO 控制水平; 当转鼓 固体燃料配比, 指数≤76% 时, 关小烧结机主抽风机风门, 降低垂直 烧结速度, 减小配料室上料量。 2 ) 提高烧结矿转鼓指数的稳定性。 烧结矿转 鼓指数的波动, 必然会引起返矿量的波动, 从而导致 烧结矿成品率的波动。 转鼓指数的波动, 反映出的 信息就是烧结生产过程不稳定。在提高烧结矿转鼓 指数稳定性的措施上, 主要是以稳定烧结生产过程 为主, 并把转鼓指数稳定率作为一项重要的质量指 标进行控制和考核。 2. 2 原料结构优化及控制 烧结矿强度高, 固然对提高烧结矿成品率有好 , 处 但并不能说明烧结矿成品率一定就高 。这一点, 在过去多次的烧结实验室试验中都得到证明 。提高 只能减少烧结生产过程中因转运而增 烧结矿强度, 加的粉末含量, 并不能直接减少烧结饼中原始的粉 末含量。烧结矿 ( 饼 ) 中原始粉末含量与烧结混合 料的烧结性能 ( 液相的性质和数量 ) 有关。 原料结 构决定混合料的烧结性能。 改善混合料的烧结性 能, 必须从原料结构优化入手。 目前, 钢铁市场面临的形势异常严峻, 铁矿粉市
场变幻莫测, 在原料结构优化方面, 不仅要考虑混合 料的烧结性能, 而且要考虑混合料的成本, 二者必须 兼顾。原料结构优化的原则是, 在烧结性能 ( 烧结 原料成本最低。 矿强度 ) 满足生产需要的情况下, 抛开成本, 片面追求混合料烧结性能最优化是没有 意义的。在原料结构优化方面, 主要做法是: 1 ) 依据原料资源条件、 成本控制目标、 炼铁生 产对烧结矿品位的要求及烧结工艺条件等确定原料 结构配比方案。 2 ) 对 原 料 结 构 配 比 方 案 进 行 烧 结 性 能 优 化。 该优化方法采用两种方式, 一是利用历史配矿经验, 限定矿种的适宜配比范围。如磁铁精矿和赤铁粉矿 的配用比例、 某些特定矿种的最高配比量等; 二是进 行实验室试验。 必要时, 进行工业性试验。 通过试 验证烧结混合料的烧结性能, 探索适宜的烧结工 验, 艺参数。这样, 有效避免了烧结性能不确定的配料 方案在使用时, 引起烧结生产过程的波动而导致的 烧结返矿率的升高现象。 3 ) 做好变料操作控制。不同的原料结构, 具有不 对应不同的适宜工艺控制参数。当两 同的烧结性能, 种不同的原料结构的混合料进行变料时, 不可避免地 就会造成烧结生产过程的波动。做好变料操作控制, 可以有效地减小变料时烧结生产过程波动而带来的 成品率的变化。变料操作的控制内容主要包括: 配料 系统对两种不同结构原料的平稳转换过渡 ( 包括堆 尾、 堆头料的处理) 、 变料后合理的烧结工艺参数的确 定以及必要时工艺装备的调整。如在 2010 年 8 月 当烧结原料结构由大比例精矿为主调整为大比例 份, 粉矿为主时, 在对烧结机料层厚度、 燃料粒度、 混合料 水分、 混合料配碳量等工艺参数控制标准调整的同 时, 及时拆除了为适应大比例精矿原料结构烧结时加 装的松料器, 成功实现了两种烧结性能差异较大的原 料结构在生产上的平稳过渡, 稳定了烧结过程, 没有 “大变料” 因 而使烧结矿成品率产生大的波动。 4 ) 稳定原料结构, 尽量减少变料次数。 符合生 产实际的合理烧结工艺参数, 只有在长期生产实践 的探索中才能准确地确定。 因此, 只有稳定原料结 构, 减少变料次数, 才能保持烧结生产过程的长期稳 定以及烧结矿成品率的长期稳定 。在稳定原料结构 方面, 在工序控制上, 就是及时掌握可供利用的原料 资源情况, 在不同烧结生产系统之间合理配置 , 确定 烧结性能 配料方案。对于物理化学成分基本相同, 相近的矿种, 充分发挥原料中和料场的作用, 进行合 并堆放、 使用。这样, 在保证混匀料品质基本不变的 情况下, 既提高了原料中和混匀料场的利用率 , 又减
[1 ]
中经常看到的原矿颗粒, 就是这种现象造成的。 虽被粘结但粘结强度小的颗粒, 主要产生在烧 结机料层的表面和边缘部分。 烧结机上混合料点火烧结后, 由于表面直接和 冷却速度快, 烧结过程中产生的液相还 冷空气接触, 未来得及迁移聚集即被冷却为固相 。此处的烧结饼 且内应力较大, 强度极差。 内部均为薄壁大孔结构, 破碎后, 几乎百分之百变为返矿。 该部分烧结矿层 厚度一般在 30 mm ~ 40 mm 左右, 随烧结过程的垂 直烧结速度、 烧结料烧结性能的不同会有所变化 。 提高烧结机料层厚度, 实行厚料层烧结, 会相对降低 该部分烧结矿占整个烧结饼的比重, 有利于烧结矿 成品率的提高。 鉴于烧结工艺的特点, 烧结机边缘混合料层的 透气性要大于台车中间混合料层的透气性 , 俗称为 “边缘效应” 。由于 “边缘效应” 的存在, 布在台车边 缘的混合料的烧结速度要大于中间混合料的速度 , 这样, 就会产生与表层烧结矿相似的烧结效果。 烧 结机台车愈宽, 边缘烧结矿占整块台车烧结饼的比 重愈小, 对成品率的影响作用相对就愈弱 。显然, 在 “边缘效应” 削弱 上, 大型烧结机比小型烧结机具有 更大的优势。 保持一定的烧结矿强度是提高烧结矿成品率的 基础。提高烧结矿强度, 可以有效提高烧结饼的抗 摔打能力, 减少烧结饼在生产过程中转运摔打而产 生的粉末含量。降低烧结饼在转运和破碎过程中减
2012 年 4 月 第 20 卷 第 2 期
河 南 冶 金 HENAN METALLURGY
Apr. 2012 Vol. 20 No. 2