产品表面外观缺陷的限定标准
电镀产品外观检验标准

【下载本文档,可以自由复制内容或自由编辑修改内容,更多精彩文章,期待你的好评和关注,我将一如既往为您服务】电镀产品外观检验标准1.0 目的为所有电镀的原材料、半成品、成品的外观检验提供依据。
2.0 范围适用于提供给客户的所有的原材料、半成品、成品及返修物料。
3.0 定义A级面:物料的外观面对最终产品的外观、功能、客户使用有重大影响或客户有要求。
B级面:物料装配成产品后,对产品的外观要求、客户使用无影响或此面对功能调试没有影响。
C级面:物料装配成产品后,对参数调试无影响,纯属设计需要或此面有喷漆要求,或非喷漆面不外漏面。
起泡:指因电镀工艺原因产品表面出现的气泡。
过薄:指表面电镀层的平均厚度小于5um。
脱落:指电镀产品表面镀层掉。
漏镀:指电镀产品要求电镀面实际未电镀。
花斑:指电镀前因基体材料腐蚀、或者材料中的杂质、或者材料微孔等原因所造成的、与周围材质表面不同光泽或粗糙度的斑块状花纹外观。
黑点:指电镀产品表面存在的黑色圆点。
发黄:指电镀产品表面的颜色显示黄色状态。
色差:指偏离标准色度的量。
凸起: 指因材料本体或外来物出现高于平面的现象。
水印:指电镀后因清洗水未及时干燥或干燥不彻底所形成的印迹。
砂眼:指表面的疏松针孔。
挂具印:指电镀表面处理生产过程中,因装挂用辅助工具的遮挡而使其与零件相接触的部位局部无膜层的现象。
修补:指因膜层损伤而用涂料所作的局部遮盖。
颗粒:指因材料杂质或外来物的影响而在表面形成的、颜色与正常表面一致的凸起现象。
异物:指由材料、模具、环境或机器设备中的灰尘、夹杂物、污物等影响而形成的与表面不同色的斑点。
打磨:指为了更好的达到表面要求而使用的砂纸抛光的处理方式。
镀前划痕:指电镀或氧化之前因操作不当、或对明显缺陷进行粗打磨等人为造成的基体材料上的划伤或局部磨擦痕迹,一般呈细线型。
浅划痕:膜层表面划伤,但未伤至底层(即底层未暴露);对其它无膜层表面则为:目测不明显、手指甲触摸无凹凸感、未伤及材料本体的伤痕。
产品表面外观缺陷限定标准dkba04000021v2
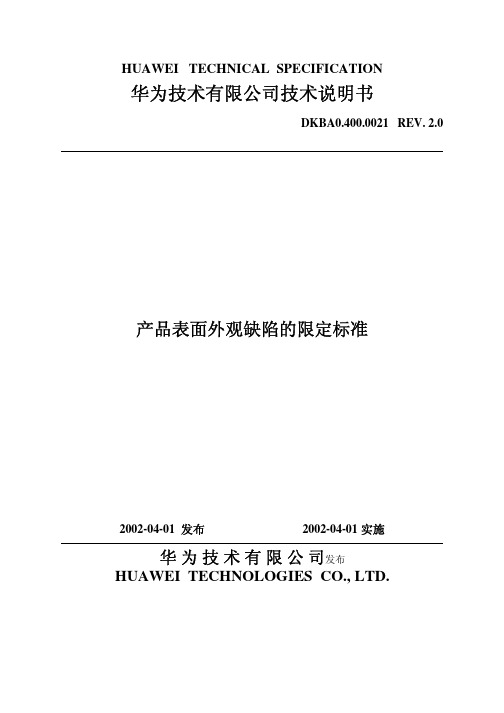
华为技术有限公司技术说明书
DKBA0.400.0021 REV. 2.0
产品表面外观缺陷的限定标准
2002-04-01 发布
2002-04-01 实施
华 为 技 术 有 限 公 司发布
HUAWEI TECHNOLOGIES CO., LTD.
2
DKBA 0.400.0005 压铸件技术规范
3
DKBA 0.400.0011 海绵结构件技术规范
4
DKBA 0.420.0010 橡胶结构件技术规范
5
DKBA 0.450.0011 铝合金喷砂光亮阳极化技术规范
6
DKBA 0.450.0012 铝合金化学氧化技术规范
7
DKBA 0.450.0013 金属零(组)件的粉末喷涂技术规范
4.1.2
华为产品的各部位表面按其在产品中所处位置和质量要求划分为二个等级,即:A级和B级 表面;A级表面中按最终工作状态又可分为外部表面和内部表面。各等级每一面上表面缺陷 的限定标Fra bibliotek详见表 2 。
本文件由华为技术有限公司结构造型设计部提出。 本文件主要起草和解释部门:结构造型设计部 本文件主要起草人:郑玲 本文件主要审核人:曾献科 本文件会签人:黄文源 黄辉 本文件标准化审核人:王丽妍 本文件批准人:陈京
修订记录
发布日期 2001-6-30 2002-3-20
版本号 1.0 2.0
更改说明
新文件
DKBA0.400.0021 REV. 2.0
3.14 凹凸痕:因基材受撞击或校形不良等而呈现出的明显变形、凹凸不平整的现象,手摸时有 不平感觉。
3.15 抛光区:对基材上的腐蚀、划伤、焊接区、铆接区等部位进行机械打磨抛光后表现出的局 部高光泽、光亮区域。
产品外观检验标准

本文件属公司资产,任何人非经许可,不得私自影印
文件名称
产品外观件检验标准
文件编号
版本 号
VER1.0
页次
第1页/共5页
1目的
本标准为公司对塑胶、五金、喷油、丝印件外观及产品组装检验测试的判定提供书面依据。
2适用范围
本标准适用于公司所有材料及产品外观检验和判定,客户特殊要求除外。
6.1.2缺陷定义
任一缺陷与其它缺陷之间的间隙应在2cm以上。
6.1.3外观定义
污点﹕因产品原料内有杂物而在产品表面留有的不可擦拭的杂点(颜色与产品颜色不同)。
凹凸点:本体表面所暴露出来的,与本体表面不在同一水平线的杂点.
气丝:由于种种原因,气体在产品表面留下的痕迹与底面颜色不同并发亮,带有流动样。
√
印刷不良
印刷字体或图案大小不符合规格或印刷有多印﹑漏印﹑位置印错。
√
不允许油墨扩墨大于3mm2﹐拖尾大于0.5mm2,印刷A级面漏白大于1.0mm2。
√
A
牛皮纸﹑内盒允许小于或等于2.0mm的偏位﹐彩盒允许小于或等于1.5mm的偏位..
√
*如果有图案有位置要求﹐则图案位置以不偏过另一面为原则.
√
8 标准说明
6.1塑壳
6.1.1外观面定义
A面:成品机正常放置时,第一眼可以看得到的区域
B面:成品机正常放置时,不在直线范围内,但可以在其它角度看到的一面。
C面:成品机正常放置时,以任何角度观察不到,只有通过旋转成品机后才能观察到的范围,
D面:成品机在正常放置或旋转机器时都看不见,只有通过拆卸零部件才可看到的范围。
√
颜色符合样板或上下限色差范围。
产品表面外观缺陷的限定标准

苏州荣科精密机械有限公司产品表面外观缺陷的限定标准1 范围本规范规定了产品中结构件的表面等级划分及其外观质量要求。
本规范适用于本公司及子公司结构产品表面外观的标准判定,产品的装配生产及结构验收;也可用于指导设计。
本规范同样适用于外购件的验收,当外购个别件不属于本公司专用型号时,也可按供应商的质量标准对其进行验收,具体要求应参照相应外购件的技术说明书等文件。
2 术语2.1 产品:指本公司确定的、处于向本公司客户发货状态下的物品,如整机、模块、散件。
2.2 A级表面:重要外观表面,体现产品外观形象,具有装饰性,可以直接正视到的主要外观表面。
2.3 B级表面:主要外表面,半装饰性的经常可见的外观表面。
2.4 C级表面:次要外表面和内表面,不是以装饰为目的,表面质量要求不高的结构表面。
除A、B级表面外的表面均为C级表面。
2.5 正视:指检查者站立于被检查表面的正面、视线与被检表面呈45-90度而进行观察。
2.6 金属表面:包括电镀、氧化、钝化、以及金属压铸面、金属机械加工面等表面为金属质感的表面,非喷涂面。
2.7 拉丝:是一种砂带磨削加工,通过砂带对金属表面进行磨削加工,去除金属表面缺陷,并形成具有一定粗糙度、纹路均匀的装饰表面。
2.8 喷涂保护面:零件在喷涂过程中,依据图纸要求,对不要求喷涂的表面进行了保护处理的表面。
3 缺陷定义3.1 金属表面3.1.1 模具痕:折弯等模具成型过程中在结构件表面产生的压痕、轻微凹坑等。
3.1.2 磨擦痕:加工过程中板材在机床台面运动过程中产生的轻微划痕,无凹入感。
3.1.3 运动部件摩擦痕:样本架等在运送过程中和基体产生的痕迹。
3.1.4 焊渣:指电镀、氧化前,金属焊接时飞溅到焊缝位置以外区域的、牢固粘附在基材表面的金属点状颗粒。
3.1.5 烧伤:拉丝处理时因操作不当、造成零件表面过热而留下的烧蚀痕迹。
3.1.6 凹坑:由于基体材料缺陷、或在加工过程中操作不当等原因而在材料表面留下的小坑状痕迹。
外观检验标准

产品外观判断标准
电镀件通用检验标准
1 范围
本标准规定了电镀件的检验内容及检验方法,适用于公司来料、半成品的检查。
2 引用标准
GB/T 2828-2003 中华人民共和国国家标准(适用于产品逐批检查)。
3 定义
3.1 A 面:指电镀件正面 . (在使用过程中能直接看到的表面)
3.2 B 面:指电镀件四侧边。
(需将电镀件偏转45~90 °才能看到的四周边)3.3 软划痕:没有深度的划痕。
(无手感)
3.4 硬划痕:硬物摩擦造成的划痕或有深度的划痕。
3.5 批锋:由于注塑等原因造成塑胶边缘突起。
3.6 麻点:由于电镀环境不干净而导致有点状或线状物覆盖于产品表面的缺陷。
3.7 凸点:由于有灰尘造成电镀表面凸点状缺陷。
3.8 沙眼:由于模具压伤后留下的印痕。
4 要求
4 . 1 检验步骤:
包装检验信赖度测试试装检验尺寸检验外观检
4 . 2 检验条件
4.2.1 光源 : 两支 40W 日光灯照射下距物件 1.2 ~ 1.5 米
4.2.2 目视距离:35 ± 5cm
4.2.3 目视角度:检测面与人眼方向成45° ~90°
4.2.4 目视时间 :5 ~ 10S
4 . 3 检验仪器和工具
4.3.1 游标卡尺 [ 准确度: 0.02mm ]
4.3.2 标准菲林
4.3.3 普通刀片 [ 有保护手柄 ]
4.3.4 塞尺
4.3.5 配套卡机面、底壳 [ 工程提供 ]
4.3.6 3M 胶纸
4.3.7 RCA 耐磨测试仪4 . 4 检验细则
4.4.1 检验项目。
华为能源产品结构件表面外观缺陷限定标准

DKBA 华为技术有限公司内部技术规范DKBA 2991-2018.3能源产品结构件表面外观缺陷限定标准Cosmetic Standard for Energy ProductSurfaces2018年03月20日发布2018年03月25日实施华为技术有限公司Huawei Technologies Co., Ltd.修订声明Revision declaration本规范拟制与解释部门:网络能源产品线通信能源系统开发部(此标准解释权在系统开发部,对于标准解释存在歧义以网络能源整机TMG意见为准)本规范的相关系列规范或文件:DKBA04000021产品表面外观缺陷及检测方法定义相关国际规范或文件一致性:无替代或作废的其它规范或文件:无规范号主要起草部门专家主要评审部门专家修订情况DKBA 2991-2012. 4 电源系统开发部:胡荣恒167366整机工程部:杨延平176674整机工程部:王礼新123330整机工程部:韦娟37461能源产品部:刘明涛177027能源产品部:翦威212267能源产品部:胡雄172600能源产品部:黄新锋61371能源产品部:吴才锐172576能源产品部:朱善伦171719能源产品部:刘彪171574能源产品部:黄继常163295能源产品部:张宏翔174609能源产品部:高拥兵174602能源产品部:宋凌179586能源产品部:林伟鸿37885能源产品部:赵福高163643MQE:陈丽娟188628MQE:王海荣127944SQE:孟庆伟145066第一版,无升级更改信息DKBA 2991-2014. 5 能源产品部:胡雄172600能源产品部:刘明涛177027能源产品部:胡荣恒167366能源产品部:杨延平176674能源产品部:陈海平119807能源产品部:杨琦195007能源产品部:翦威212267能源产品部:黄春杰111426能源产品部:陈张锐178882能源产品部:黄继常163295能源产品部:陈本187891MQE:李夏威225540MQE:王海荣127944SQE:孟庆伟145066SQE:廖云涛210817第二版,增加集装箱外观缺陷限定标准(仅喷涂表面),增加能源散热器外观缺陷限定标准,修订装配间隙、喷涂外观等标准2023-03-19 第2页,共29页Page 2 , Total29DKBA 2991-2014.10 能源产品部:胡雄172600能源产品部:胡荣恒167366能源产品部:杨延平176674能源产品部:陈海平119807能源产品部:杨琦195007能源产品部:翦威212267能源产品部:黄春杰111426能源产品部:陈张锐178882能源产品部:黄继常163295能源产品部:陈本187891MQE:黄文源123114MQE:李洋177753MQE:王海荣127944SQE: 董海泉271068SQE: 孟庆伟145066SQE:廖云涛210817第三版,取消2级面不喷涂的预镀锌板涂银漆修补要求;修改螺钉头轻微毛刺要求;增加标签粘贴要求;增加螺纹内部飞粉要求;取消部分缺陷中的累积尺寸要求。
外观件缺陷评定标准10[1].12.16
![外观件缺陷评定标准10[1].12.16](https://img.taocdn.com/s3/m/4a51a02bbd64783e09122bf0.png)
0.1mm, N≤1
≤2
3
无感划伤
不允许
L ≤ 2.5mm , W ≤ L≤2.5mm,W≤0.1mm,
0.1mm, N≤1
N≤2 且 DS≥15mm
4
纤维状毛絮
不允许
L ≤ 0.5mm , W ≤ L≤0.5mm,W≤0.1mm, 0.1mm, N≤2 且 DS N≤2 且 DS≥15mm ≥15mm
图8 外观:表面无划伤、起皮、气泡、、开裂、溜痕、合模线搭接、桃木纹残缺,光泽度均匀,颜色均匀。
序号 不良项目
A 级面
4
飞边
不允许
H≤0.10mm 且不影响 H≤0.20mm 且不影响装
装配
配
5
缩痕
参照限度样本
参照限度样本
不限
6
熔接线
参照限度样本
参照限度样本
不限
7
拖花
参照限度样本
参照限度样本
不限
8
翘曲
参照限度样本
参照限度样本
不限
参照限度样本或△E
9
色差
参照限度样本
>1 时不合格
不限
10
顶白/顶凸
不允许
不允许
不限
11
陷 D≤3mm,凸起+ ≤10mm,凸起+
点缺陷
凹 陷 N ≤ 5 , DS ≥ 凹陷 N≤3,DS≥
100mm
50mm
2
有感划伤(碰伤)
/
D≤0.2mm,N≤1 D≤0.2mm,N≤2
/
L ≤ 0.8mm , W ≤ L≤2mm,W≤0.1mm, N
0.1mm, N≤1
≤2
3
无感划伤
产品表面外观缺陷的限定标准

45-90被检查表面被检查表面图1:“正视”位置示意图1.3 A级表面:从外部能直截了当看到、或日常爱护时能被直截了当看到的表面。
A级表面分为A1、A2 两个表面。
(A1、A2表面划分见表下表)1.4 A1表面:在产品正常工作状态下、能直截了当正视到的产品正前外表面。
1.5 A2表面:在产品正常工作状态下、除A1表面以外的能直截了当正视到的外表面。
1.7 B级表面:除A级以外的所有表面。
1.8 金属表面:包括电镀、氧化、钝化、以及金属压铸面等非喷涂表面。
1.9 打磨:是一种砂带磨削加工,通过砂带对金属表面进行磨削加工,去除金属表面缺陷,并形成具有一定粗糙度、纹路平均的装饰表面。
1.10 基材花斑:电镀或氧化前因基体材料腐蚀、或者材料中的杂质、或者材料微孔等缘故所造成的、与周围材质表面不同光泽或粗糙度的斑块状花纹外观。
1.11 喷涂前划痕:指喷涂或氧化之前因操作不当、或对明显缺陷进行粗打磨等人为造成的基体材料上的一样呈细线型划伤或局部磨擦的痕迹。
1.12 浅划痕:膜层表面划伤,但未伤至底层(即底层未暴露);对其它无膜层表面则为:目测不明显、手指甲触摸无凹凸感、未伤及材料本体的伤痕。
1.13 深划痕:表面膜层划伤,且已伤至底层(即底层已暴露出来);对无膜层表面则为:目测明显、手指甲触摸有凹凸感、伤及材料本体的伤痕。
1.14 凹坑:由于基体材料缺陷、或在加工过程中操作不当等缘故而在材料表面留下的小坑状痕迹。
1.15 凹凸痕:因基材受撞击或校形不良等而出现出的明显变形、凹凸不平坦的现象,手摸时有不平感受。
1.16 打磨区:对基材上的腐蚀、划伤、焊接区、铆接区等部位进行机械打磨抛光后表现出的局部高光泽、光亮区域。
1.17 烧伤:拉丝处理时因操作不当、造成零件表面过热而留下的烧蚀痕迹。
1.18 水印:电镀或氧化后因清洗水未及时干燥或干燥不完全所形成的斑纹、印迹。
1.29 缩水:因材料、工艺等缘故使塑胶或压铸件表面显现凹陷的收缩现象。
DKBA04000021 产品表面外观缺陷的限定标准
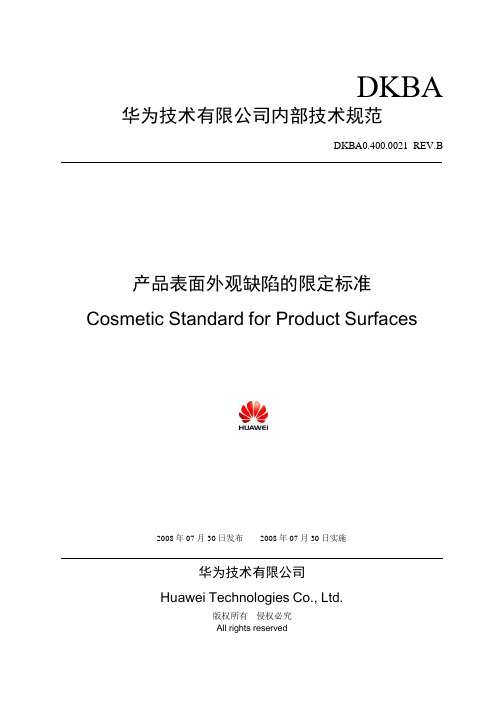
DKBA 华为技术有限公司内部技术规范DKBA0.400.0021 REV.B产品表面外观缺陷的限定标准Cosmetic Standard for Product Surfaces2008 年07 月30 日发布2008 年07 月30 日实施华为技术有限公司Huawei Technologies Co., Ltd.版权所有侵权必究All rights reserved密级:内部公开产品表面外观缺陷的限定标准DKBA0.400.0021修订声明Revision Declaration本规范拟制与解释部门:整机工程部结构造型设计部本规范的相关系列规范或文件:Q/DKBA3250“整机装配质量标准”相关国际规范或文件一致性:无替代或作废的其它规范或文件:无相关规范或文件的相互关系:互相补充密级:内部公开 DKBA0.400.0021产品表面外观缺陷的限定标准密级:内部公开产品表面外观缺陷的限定标准DKBA0.400.0021目录Table of Contents1 外观表面等级定义 (10)1.1 1 级表面 (10)1.2 2 级表面 (10)1.3 3 级表面 (10)2 外观检验条件 (14)2.1 目视检测条件 (14)2.2 检测面积划分 (14)3 对外观的质量要求 (15)3.1 总则 (15)3.1.1 原则 (15)3.1.2 特殊签样 (16)3.1.3 丝印要求 (16)3.2 加工工艺原因导致的问题 (16)3.2.1 毛刺或利边 (16)3.2.2 裂纹 (16)3.2.3 拉丝或喷砂的纹理与光泽 (17)3.2.4 镀锌压铆钉头部钝化膜的受损问题 (17)3.2.5 接刀痕 (17)3.2.6 深孔内壁要求 (17)3.3 材料缺陷导致的问题 (18)3.3.1 铝材晶纹 (18)3.3.2 预镀钢板切口边的锈蚀 (18)3.4 特殊情况 (18)3.4.1 螺钉头 (18)3.5 缺陷的改善 (18)3.5.1 打磨抛光 (18)3.5.2 喷砂或拉丝 (19)4 可接受的缺陷标准 (19)4.1 金属表面 (19)4.1.1 缺陷定义 (19)4.1.2 可接受范围 (25)4.2 喷涂表面 (27)4.2.1 缺陷定义 (27)4.2.2 可接受范围 (35)4.2.3 散热齿变形的可接受范围 (37)4.3 塑料表面 (38)4.3.1 缺陷定义 (38)4.3.2 可接受范围 (42)表目录List of Tables表1、检测条件 (14)表3、可接受表面缺陷总数限定 (16)表4、可接受的缺陷范围 (25)表5、涂层表面缺陷的可接受范围 (35)表6、散热齿变形的可接受范围 (37)表6、塑料表面缺陷的可接受范围 (42)图目录List of Figures图1、机柜外观面等级示意图 (11)图2、插框外观面等级示意图 (12)图3、拉手条外观面等级示意图 (12)图4、模块外观面等级示意图 (13)图5、使用预镀板,表面不喷涂的盒式结构外观面等级示意图 (13)图6、单板上装配的结构件外观面等级示意图 (13)图7、“正视”位置示意图 (14)图8、金属缺料 (15)图9、非金属缺料 (15)图10、塑料破损 (15)图11、拉丝后折弯裂纹 (16)图12、铝板折弯裂纹 (17)图13、孔内涂有保护层 (17)图14、铝材表面的粗晶组织现象 (18)图15、模具痕 (19)图16、磨擦痕 (19)图17、磨擦痕 (20)图18、凹坑 (20)图19、凹痕 (20)图20、打磨痕 (21)图21、镀前划痕 (21)图22、镀前划痕 (21)图23、镀前划痕 (21)图24、镀后划痕 (22)图25、镀后划痕 (22)图27、氧化花斑 (23)图28、镀层起泡 (23)图29、露白 (23)图30、黑点 (23)图31、镀层雾状 (24)图32、水印 (24)图33、电镀后的挂具印 (24)图34、指印 (24)图35、砂眼 (25)图36、局部无铬层 (25)图37、零件间色差 (28)图38、喷涂保护面色差 (28)图39、涂层脱落 (28)图40、孔洞现象 (29)图41、杂质 (29)图42、颗粒 (29)图43、喷涂保护斑点 (30)图44、涂料堆积 (30)图45、毛边 (30)图46、浅划痕 (31)图47、深划痕 (31)图48、打磨痕 (31)图49、模具痕 (32)图50、压铆印 (32)图51、点状熔化焊 (33)图52、焊渣 (33)图53、挂具印 (33)图54、凹坑 (34)图55、焊接凹坑 (34)图56、擦拭印 (35)图57、散热齿变形 (35)图58、零件间色差 (38)图59、水纹 (38)图60、缩水 (39)图61、气泡 (39)密级:内部公开产品表面外观缺陷的限定标准DKBA0.400.0021图62、雾状 (39)图63、涂漆不足 (39)图64、涂漆过多 (40)图65、杂质 (40)图66、颗粒 (40)图67、披锋 (41)图68、凹坑 (41)图69、浅划痕 (41)图70、深划痕 (42)密级:内部公开 DKBA0.400.0021 产品表面外观缺陷的限定标准产品表面外观缺陷的限定标准Cosmetic Standard for Product Surfaces范 围 Scope: 本规范规定了华为技术有限公司结构件的表面等级划分及外观质量要求。
外观检验判定标准

SIP检验规范外观检验判定标准PAGE 页码1/4生效日期2011-7-20CHANGE HISTORY 文件修订履历版本修订内容摘要修订原因作成日期制定部门A0 新文件发行——2011-7-15 梁波QADISTRIBUTION TO DEPTS 分发部门DEPT 部门QTY份数DEPT部门QTY份数DEPT部门QTY份数DEPT部门QTY份数DEPT部门QTY份数QA 1SIP检验规范外观检验判定标准PAGE 页码2/4生效日期2011-7-20一、目的为了加强产品品质及统一本司品质要求,增强客户满意度,特制订本外观检验判定标准。
二、适用范围我司所有产品的外观检验执行标准(具体订单如客户有特别要求时,以客户要求为准)三、相关定义3.1 A级面,B级面,C级面定义见8.1;3.2 色差:待检品表面颜色与资料规定的色卡号(或与签订的色样)对比,有明显的颜色差异。
3.3 批锋/毛边:待检品在制造时存在不是模具设计要求的部分,制造厂商没有处理完全的部分。
3.4 杂色:待检品某个区域内颜色不均匀,或存在其它色纹;3.5 异色点:因材料本身存在杂质而导致待检品表面存在的黑点或异色点;3.6 刮伤/划伤:指待检品由于硬物碰撞或摩擦后表面存在的拉痕,分有感划伤和无感划伤;3.7 (五金件)生锈/变质:指待检品表面由于化学反应而发生腐蚀;3.8 (塑胶件)缩水:指待检品表面发生凹陷的现象。
3.9 脏污:产品表面存在污渍或脏物;3.10 变形:待检品被不明原因造成的外观形状变异;3.11 其它:待检品存在不在以上外观缺陷定义范围内的表面缺陷,依具体情况具体处理。
四、检验使用工具:卡尺,菲林对比卡五、检验方法:目视六、外观判定标准6.1 A级面:6.1.1 异色点:直径不大于0.2mm允许最多有两个点,但点间距不得小于10cm,直径大于0.2mm的异色点不接收;6.1.2 划伤:表面不允许出现有感划伤/拉痕及手指印,无感划伤线径不超过0.1,长度不超过10mm可接收2条,且划伤间距大于10cm;6.1.3 色差:整批及批与批之间不得有色差,对比色卡(或色样),不得低于限度要求;6.1.4 批锋/毛边:不允许出现;6.1.5 缩水/杂色:不允许出现;SIP检验规范外观检验判定标准PAGE 页码3/4生效日期2011-7-206.1.6 脏污/变形/生锈:不允许出现;6.1.7 不允许出现其他未描述的外观不良(如麻点,破裂等)6.2 B级面:6.2.1异色点:直径不大于0.5mm允许最多有四个点,但点间距不得小于10cm,直径大于0.5mm的异色点不接收;6.2.2划伤:表面不允许出现有感划伤/拉痕及手指印,无感划伤线径不超过0.3,长度不超过10mm可接收5条,且划伤间距大于10cm;6.2.3色差:整批及批与批之间不得有明显色差,对比色卡(或色样),不得低于限度要求;6.2.4 批锋/毛边:不允许出现;6.2.5 缩水/杂色:不允许出现;6.2.6 脏污/变形/生锈:不允许出现:6.2.7 不允许出现其他未描述的外观不良(如变形,破裂等)6.3 C级面:6.3.1 异色点:允许有,但不得影响到产品性能;6.3.2 划伤:表面不允许出现有感划伤/拉痕,允许有无感划伤,但不得影响到产品性能6.3.3 色差:允许有,但不得影响到产品性能;6.3.4 批锋/毛边:不允许出现;6.3.5 缩水/杂色:允许有,但不得影响到产品性能;6.3.6 脏污/变形/生锈:不允许出现;6.3.7 不允许出现其他未描述的外观不良(如破裂等)七、允收标准:7.1 原材料依照《来料检验规范(总则)》规定的AQL对来料进行判定;7.2 制程外观全检工位依照6.0外观检验标准进行全检作业,将挑选的不良品经IPQC/IQC确认后退仓;7.3 入库及出货检验标准依照《成品检验规范(总则)》规定的AQL对批量成品灯具进行判定。
外观检验标准
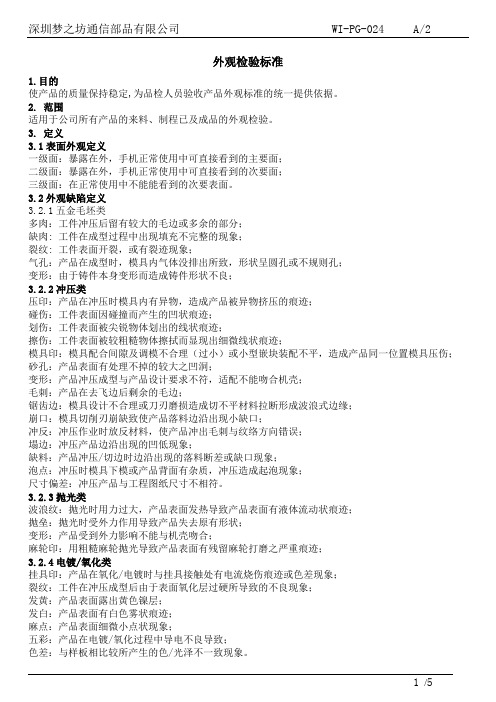
外观检验标准1.目的使产品的质量保持稳定,为品检人员验收产品外观标准的统一提供依据。
2. 范围适用于公司所有产品的来料、制程已及成品的外观检验。
3. 定义3.1表面外观定义一级面:暴露在外,手机正常使用中可直接看到的主要面;二级面:暴露在外,手机正常使用中可直接看到的次要面;三级面:在正常使用中不能能看到的次要表面。
3.2外观缺陷定义3.2.1五金毛坯类多肉:工件冲压后留有较大的毛边或多余的部分;缺肉: 工件在成型过程中出现填充不完整的现象;裂纹: 工件表面开裂,或有裂迹现象;气孔:产品在成型时,模具内气体没排出所致,形状呈圆孔或不规则孔;变形:由于铸件本身变形而造成铸件形状不良;3.2.2冲压类压印:产品在冲压时模具内有异物,造成产品被异物挤压的痕迹;碰伤:工件表面因碰撞而产生的凹状痕迹;划伤:工件表面被尖锐物体划出的线状痕迹;擦伤:工件表面被较粗糙物体擦拭而显现出细微线状痕迹;模具印:模具配合间隙及调模不合理(过小)或小型嵌块装配不平,造成产品同一位置模具压伤;砂孔:产品表面有处理不掉的较大之凹洞;变形:产品冲压成型与产品设计要求不符,适配不能吻合机壳;毛刺:产品在去飞边后剩余的毛边;锯齿边:模具设计不合理或刀刃磨损造成切不平材料拉断形成波浪式边缘;崩口:模具切削刃崩缺致使产品落料边沿出现小缺口;冲反:冲压作业时放反材料,使产品冲出毛刺与纹络方向错误;塌边:冲压产品边沿出现的凹低现象;缺料:产品冲压/切边时边沿出现的落料断差或缺口现象;泡点:冲压时模具下模或产品背面有杂质,冲压造成起泡现象;尺寸偏差:冲压产品与工程图纸尺寸不相符。
3.2.3抛光类波浪纹:抛光时用力过大,产品表面发热导致产品表面有液体流动状痕迹;抛垒:抛光时受外力作用导致产品失去原有形状;变形:产品受到外力影响不能与机壳吻合;麻轮印:用粗糙麻轮抛光导致产品表面有残留麻轮打磨之严重痕迹;3.2.4电镀/氧化类挂具印:产品在氧化/电镀时与挂具接触处有电流烧伤痕迹或色差现象;裂纹:工件在冲压成型后由于表面氧化层过硬所导致的不良现象;发黄:产品表面露出黄色镍层;发白:产品表面有白色雾状痕迹;麻点:产品表面细微小点状现象;五彩:产品在电镀/氧化过程中导电不良导致;色差:与样板相比较所产生的色/光泽不一致现象。
外壳抽检标准
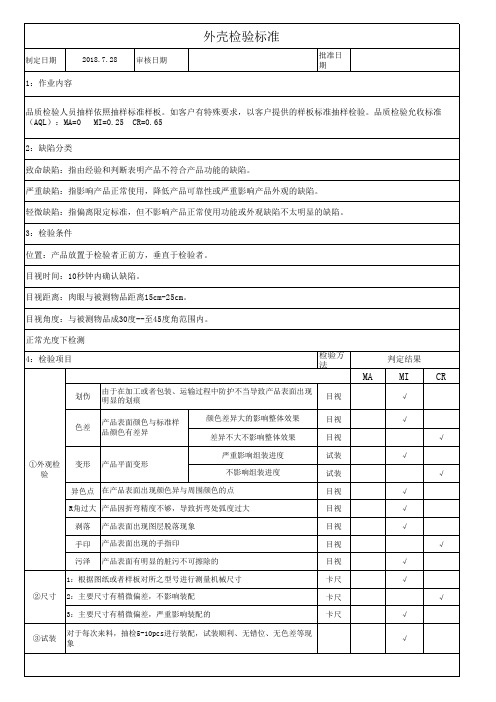
目视
√
R角过大 产品因折弯精度不够,导致折弯处弧度过大
目视
√
剥落 产品表面出现图层脱落现象
目视
√
手印 产品表面出现的手指印
目视
√
污泽 产品表面有明显的脏污不可擦除的
目视
√
1:根据图纸或者样板对所之型号进行测量机械尺寸
卡尺
√
②尺寸 2:主要尺寸有稍微偏差,不影响装配
卡尺
√
3:主要尺寸有稍微偏差,严重影响装配的
轻微缺陷:指偏离限定标准,但不影响产品正常使用功能或外观缺陷不太明显的缺陷。
3:检验条件
位置:产品放置于检验者正前方,垂直于检验者。
目视时间:10秒钟内确认缺陷。
目视距离:肉眼与被测物品距离15cm-25cm。
目视角度:与被测物品成30度--至45度角范围内。
正常光度下检测
4:检验项目
检验方法
判定结果
MA
MI
CR
划伤
由于在加工或者包装、运输过程中防护不当导致产品表面出现 明显的划痕
目视
√
色差
产品表面颜色与标准样 品颜色有差异
颜色差异大的影响整体效果 差异不大不影响整体效果
目视 目视
√ √
①外观检验 变形 产品平面变形
严重影响组装进度 不影响组装进度
试装 试装
√ √
异色点 在产品表面出现颜色异与周围颜色的点
制定日期
2018.7.28 审核日期
1:作业内容
外壳检验标准。如客户有特殊要求,以客户提供的样板标准抽样检验。品质检验允收标准 (AQL):MA=0 MI=0.25 CR=0.65
2:缺陷分类
致命缺陷:指由经验和判断表明产品不符合产品功能的缺陷。
外观检验判定标准
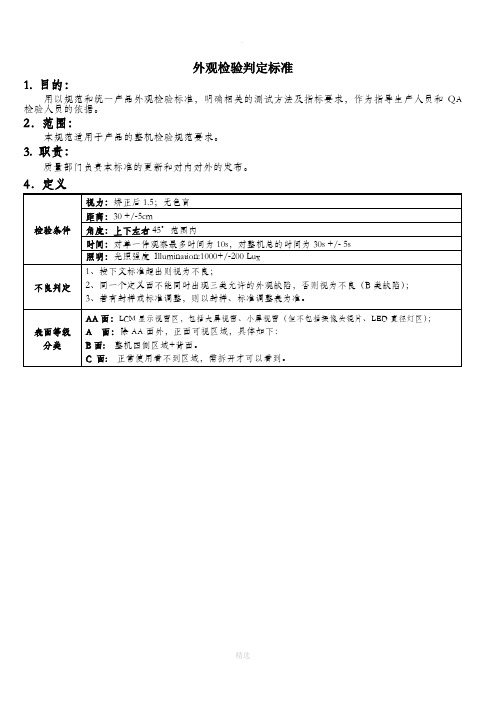
点状
参照点要求执行
N/A
B
线状
显示区:可吹掉异物不允许,不可吹异物参照划痕要求; 装饰区域:S≤0.1mm2
1
B
水纹、油彩
不允许
N/A
B
亮点、暗点
0.05mm²<S≤0.1²mm,允许1点,0.05mm²以内不计
1
B
视窗倾斜
人为装配倾斜不允许,正常装配情况下,
产品装配后单边间隙为0.20mm
参考项:左右两边间隙差不超过0.15mm
时间:对单一件观察最多时间为10s,对整机总的时间为30s +/- 5s
照明:光照强度 Illumination:1000+/-200 Lux
不良判定
1、按下文标准超出则视为不良;
2、同一个定义面不能同时出现三类允许的外观缺陷,否则视为不良(B类缺陷);
3、若有封样或标准调整,则以封样、标准调整表为准。
印刷不良:图文字体缺损,字边模糊等
缺陷分类
A类:产品包装类缺陷:
B类:外观类缺陷,不影响正常使用;
C类:产品功能缺失或未达标,影响客户正常使用或人身安全;
缺陷代码对照表
N:数目D:直径L:长度H:深度W:宽度S:面积DS:间距
N=number
数目
D=diameter
直径(mm)
L=length
长度(mm)
0.10mm<w≤0.2mm,且L≤3mm,允许2,DS≥20mm
2
B
丝印不全
印刷字符移位 字符移位距中心位置≤0.2mm
N/A
B
底部印刷部分 堆漆或漏印等瑕疵D≤0.2mm;N≤2,且两个缺陷的距离DS>15mm
华为产品表面外观缺陷的限定标准

外觀缺陷類型
缺陷所處
表面類型
合格範圍
A級表面
B級表面
顆粒
檢測面積≦6400mm2
所有
不允許
S≦1.0且P≦3或
S≦3.0且P≦2
6400<檢測面積≦48600mm2
S≦0.3且P≦3或
S≦0.5且P≦2或
S≦0.7且P≦1
48600 <檢測面積≦97200mm2
S≦0.5且P≦3或
3
3
定義…………………………………………………………………
3~4
4Hale Waihona Puke 缺陷允收範圍………………………………………………………
4~6
5
基本原則……………………………………………………………
6~7
APPROVED
核准
CHECKED
審核
PREPARED
承辦
ISSUED BY:
出版分發:
BY
簽名
DATE
日期
******修訂履歷******
5.基本原則
5.1原則:產品外觀應美觀,單獨一零/部件的整體視覺效果不能受到破壞,不會給人以劣質產品的印象.
生產者應認真操作、嚴格控制產品質量,避免在生產過程中出現對各種表面的損傷.如果發現上表中
的某一缺陷具有批量性或大面積,即便此缺陷所在表面屬於上表“不限制”範圍,也可以對該產品
不予驗收;如果允許的缺陷出現在重要觀察區,也可以視其對產品形象的影響程度而予以拒收.
(如門板正面)應加以適當的掩飾處理.
5.12拉絲或噴砂表面經壓鉚后在壓鉚區域出現紋理,光澤不完全一致的現(裝飾紋被壓平或有壓過痕
跡),這不屬於缺陷,可以接受.
产品表面外观缺陷的限定标准

产品表面外观缺陷的限定标准公司内部编号:(GOOD-TMMT-MMUT-UUPTY-UUYY-DTTI-产品表面外观缺陷的限定标准正视:指检查者站立于被检查表面的正面、视线与被检表面呈 45-90°而进行的观察(如图1)。
图 1:“正视”位置示意图A级表面:从外部能直接看到、或日常维护时能被直接看到的表面。
A级表面分为A1、A2 两个表面。
(A1、A2表面划分见表下表)A1表面:在产品正常工作状态下、能直接正视到的产品正前外表面。
A2表面:在产品正常工作状态下、除A1表面以外的能直接正视到的外表面。
B级表面:除A级以外的所有表面。
金属表面:包括电镀、氧化、钝化、以及金属压铸面等非喷涂表面。
打磨:是一种砂带磨削加工,通过砂带对金属表面进行磨削加工,去除金属表面缺陷,并形成具有一定粗糙度、纹路均匀的装饰表面。
基材花斑:电镀或氧化前因基体材料腐蚀、或者材料中的杂质、或者材料微孔等原因所造成的、与周围材质表面不同光泽或粗糙度的斑块状花纹外观。
喷涂前划痕:指喷涂或氧化之前因操作不当、或对明显缺陷进行粗打磨等人为造成的基体材料上的一般呈细线型划伤或局部磨擦的痕迹。
浅划痕:膜层表面划伤,但未伤至底层(即底层未暴露);对其它无膜层表面则为:目测不明显、手指甲触摸无凹凸感、未伤及材料本体的伤痕。
深划痕:表面膜层划伤,且已伤至底层(即底层已暴露出来);对无膜层表面则为:目测明显、手指甲触摸有凹凸感、伤及材料本体的伤痕。
凹坑:由于基体材料缺陷、或在加工过程中操作不当等原因而在材料表面留下的小坑状痕迹。
凹凸痕:因基材受撞击或校形不良等而呈现出的明显变形、凹凸不平整的现象,手摸时有不平感觉。
打磨区:对基材上的腐蚀、划伤、焊接区、铆接区等部位进行机械打磨抛光后表现出的局部高光泽、光亮区域。
烧伤:拉丝处理时因操作不当、造成零件表面过热而留下的烧蚀痕迹。
水印:电镀或氧化后因清洗水未及时干燥或干燥不彻底所形成的斑纹、印迹。
产品质量缺陷标准

文件编制部门文件类型页数工程部三级制度文件共8 页第1 页对来料检查、制程检查、出货检查等等在质量检查时要依据公司《AQL 抽样表》 (见附件一)执行抽样检查,同时给出明确的有效的质量检查缺陷判定等级标准;使质量判定标准在统一的水准下使用,提升公司及品牌品质形象,为此特制定本文件。
二、凡本公司质量管控的各环节,在进行质量检查时,遇到产品缺陷判定时均可使用。
未满足与预期或者规定用途有关的要求;即为不良,是产品质量不良等级的严重性的划分点,是产品质量没有达到标准程度的描述;质量缺陷分为四个等级:致命缺陷、严重缺陷、普通缺陷、轻微缺陷;公司在生产时严格控制,必须使“致命缺陷”零发生,为了加严管理,提高品管级别, 引起重视,公司产品缺陷分三级来管理,把“严重缺陷”合并为“致命缺陷”来管理,即“致命缺陷”和“严重缺陷”都为“致命缺陷”; “普通缺陷”称为“严重缺陷”来管理; “轻微缺陷”还称为“轻微缺陷”来管理。
影响安全的所有缺陷;影响产品失去应有功能故障、造成部份功能缺失的或者可能影响到产品的部份功能但可以正常使用到其他产品;造成产品后工序不能装配的或者产品影响装配的或者装配需要另行处理的;产品颜色出错或者产品颜色有较大偏差的;导致产品装配不良或者不能按照正常程序装配的.产品有涉及到外观的气泡、色粉点、黑点的;可能影响到装配,但通过简单后续工艺就能够得到解决的;产品轻微变形但不影响安全、功能、使用和外观的;产品有轻微色差的。
产品有不会涉及到产品整体外观的气泡、黑点等外观缺陷;产品有普通缺陷但被其他配件遮盖且不影响安全、功能、使用及配合的。
页数共8 页第2 页产品应在摹拟实际使用条件的情况下实施检验;产品在做跌落、强迫变形等试验时应使用相关设施并有明确的量化。
产品在做相关理化检验时应根据相关相应的国标、地标行企标实施。
产品在生产单一配件是就应该做产品整体功能及配合度的检验;产品的功能及配合检验应高于该产品的实际使用环境条件;外观检验产品应该在光线良好在环境下实施;实色产品应在距离30CM 摆布平视检验;透明或者半透产品应在距离30CM 透光检验。
外观检验判定标准
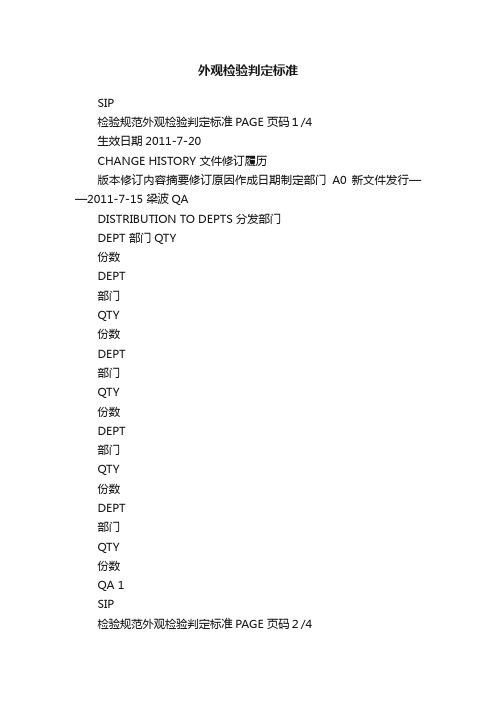
外观检验判定标准SIP检验规范外观检验判定标准PAGE 页码1/4生效日期2011-7-20CHANGE HISTORY 文件修订履历版本修订内容摘要修订原因作成日期制定部门A0 新文件发行——2011-7-15 梁波QADISTRIBUTION TO DEPTS 分发部门DEPT 部门QTY份数DEPT部门QTY份数DEPT部门QTY份数DEPT部门QTY份数DEPT部门QTY份数QA 1SIP检验规范外观检验判定标准PAGE 页码2/4生效日期2011-7-20一、目的为了加强产品品质及统一本司品质要求,增强客户满意度,特制订本外观检验判定标准。
二、适用范围我司所有产品的外观检验执行标准(具体订单如客户有特别要求时,以客户要求为准)三、相关定义3.1 A级面,B级面,C级面定义见8.1;3.2 色差:待检品表面颜色与资料规定的色卡号(或与签订的色样)对比,有明显的颜色差异。
3.3 批锋/毛边:待检品在制造时存在不是模具设计要求的部分,制造厂商没有处理完全的部分。
3.4 杂色:待检品某个区域内颜色不均匀,或存在其它色纹;3.5 异色点:因材料本身存在杂质而导致待检品表面存在的黑点或异色点;3.6 刮伤/划伤:指待检品由于硬物碰撞或摩擦后表面存在的拉痕,分有感划伤和无感划伤;3.7 (五金件)生锈/变质:指待检品表面由于化学反应而发生腐蚀;3.8 (塑胶件)缩水:指待检品表面发生凹陷的现象。
3.9 脏污:产品表面存在污渍或脏物;3.10 变形:待检品被不明原因造成的外观形状变异;3.11 其它:待检品存在不在以上外观缺陷定义范围内的表面缺陷,依具体情况具体处理。
四、检验使用工具:卡尺,菲林对比卡五、检验方法:目视六、外观判定标准6.1 A级面:6.1.1 异色点:直径不大于0.2mm允许最多有两个点,但点间距不得小于10cm,直径大于0.2mm的异色点不接收;6.1.2 划伤:表面不允许出现有感划伤/拉痕及手指印,无感划伤线径不超过0.1,长度不超过10mm可接收2条,且划伤间距大于10cm;6.1.3 色差:整批及批与批之间不得有色差,对比色卡(或色样),不得低于限度要求;6.1.4 批锋/毛边:不允许出现;6.1.5 缩水/杂色:不允许出现;SIP检验规范外观检验判定标准PAGE 页码3/4生效日期2011-7-206.1.6 脏污/变形/生锈:不允许出现;6.1.7 不允许出现其他未描述的外观不良(如麻点,破裂等)6.2 B级面:6.2.1异色点:直径不大于0.5mm允许最多有四个点,但点间距不得小于10cm,直径大于0.5mm的异色点不接收;6.2.2划伤:表面不允许出现有感划伤/拉痕及手指印,无感划伤线径不超过0.3,长度不超过10mm可接收5条,且划伤间距大于10cm;6.2.3色差:整批及批与批之间不得有明显色差,对比色卡(或色样),不得低于限度要求;6.2.4 批锋/毛边:不允许出现;6.2.5 缩水/杂色:不允许出现;6.2.6 脏污/变形/生锈:不允许出现:6.2.7 不允许出现其他未描述的外观不良(如变形,破裂等)6.3 C级面:6.3.1 异色点:允许有,但不得影响到产品性能;6.3.2 划伤:表面不允许出现有感划伤/拉痕,允许有无感划伤,但不得影响到产品性能6.3.3 色差:允许有,但不得影响到产品性能;6.3.4 批锋/毛边:不允许出现;6.3.5 缩水/杂色:允许有,但不得影响到产品性能;6.3.6 脏污/变形/生锈:不允许出现;6.3.7 不允许出现其他未描述的外观不良(如破裂等)七、允收标准:7.1 原材料依照《来料检验规范(总则)》规定的AQL对来料进行判定;7.2 制程外观全检工位依照6.0外观检验标准进行全检作业,将挑选的不良品经IPQC/IQC确认后退仓;7.3 入库及出货检验标准依照《成品检验规范(总则)》规定的AQL对批量成品灯具进行判定。
外观检查标准

外观检查标准外观检查是产品质量控制中的重要环节,通过外观检查可以及时发现产品的表面缺陷和质量问题,确保产品的外观质量符合标准要求。
本文将介绍外观检查的标准和方法,以便文档创作者和质量检验人员能够准确、全面地进行外观检查。
一、外观检查标准。
1. 表面平整度,产品表面应平整光滑,不得有凹凸不平、皱纹、气泡、砂眼等缺陷。
2. 表面颜色,产品表面颜色应均匀一致,不得有色差、色泽不良、色斑等现象。
3. 表面清洁度,产品表面应干净整洁,不得有油污、灰尘、指纹等污染。
4. 表面涂层,如有涂层的产品,应检查涂层的附着力、平整度、厚度等指标是否符合要求。
5. 表面图案和标识,产品表面的图案和标识应清晰可见,不得有模糊、缺失、错位等情况。
二、外观检查方法。
1. 目视检查,通过肉眼观察产品表面,检查其平整度、颜色、清洁度、图案和标识等情况。
2. 使用辅助工具,如放大镜、光源等辅助工具,可以帮助检查人员更清晰地观察产品表面的细节。
3. 仪器检测,对于涂层厚度、颜色差异等需要精密测量的项目,可以借助专业仪器进行检测。
三、外观检查的重要性。
1. 保证产品质量,外观检查是产品质量控制的重要环节,可以及时发现产品的表面缺陷和质量问题,确保产品质量符合标准要求。
2. 提升产品形象,产品的外观质量直接影响消费者的购买决策,良好的外观质量可以提升产品形象,增强市场竞争力。
3. 预防质量事故,通过外观检查,可以及时发现潜在的质量问题,预防质量事故的发生,保障生产安全。
四、外观检查的注意事项。
1. 检查环境,外观检查应在光线充足、无污染的环境下进行,以确保检查结果的准确性。
2. 检查标准,检查人员应熟悉产品的外观质量标准,严格按照标准要求进行检查,确保检查结果的客观性和公正性。
3. 记录和反馈,对于发现的问题,应及时记录并反馈给相关部门,以便及时进行整改和改进。
五、外观检查的改进措施。
1. 完善检查标准,根据实际情况不断完善产品的外观检查标准,确保检查的全面性和准确性。
产品零件部件外观质量要求

C级"和"D级"主要适用于金属表面的要求,如直接可见的腔体外表面、外部盖板的外表面等。如有必要,金属表面也可定为"B级",如有一定装饰性要求的机壳等;
"E级"一般为无外观要求的外表面,但须满足防护性要求;
表面需进行不透明涂覆的产品(零件),涂覆前的表面质量按不同要求在设计时应选"D级"或者"E级";
目视轻微; S(缺陷面积总和)≤被测面积的20%
目视轻微;
S(缺陷面积总和)≤被测面积的30%
目视不严重,面积不限
变色
不限
镀覆、化学处理、涂覆
不允许
轻微,不明显
轻微,较明显
不限
修补
不限
电镀、氧化
颜色、光泽与原膜层目视无明显差异,S≤4 且P≤3
颜色、光泽与原涂层目视允许有轻微差异, S≤20 且P≤3
L≤20且P≤4;或L≤30且P≤2;以及L≤40且P≤1
不限
其它
L≤10且P≤2;或L≤20且P≤1
L≤15且P≤3;或L≤20且P≤2
L≤20且P≤4;或L≤30且P≤2;以及L≤40且P≤1
L≤30且P≤5;或L≤40且P≤3;以及L≤80且P≤1
表面处理前划痕(手感无凹入
不限
拉丝及喷砂面
L≤15且P≤2
不限
喷涂
颜色、光泽与原膜层目视无明显差异,S≤50 且P≤3
颜色、光泽与原涂层目视允许有轻微差异, S≤100 且P≤3
表1 表面缺陷的限定标准(续)
外观缺陷类型
表面大小
缺陷所处表面类型
- 1、下载文档前请自行甄别文档内容的完整性,平台不提供额外的编辑、内容补充、找答案等附加服务。
- 2、"仅部分预览"的文档,不可在线预览部分如存在完整性等问题,可反馈申请退款(可完整预览的文档不适用该条件!)。
- 3、如文档侵犯您的权益,请联系客服反馈,我们会尽快为您处理(人工客服工作时间:9:00-18:30)。
产品表面外观缺陷的限定标准1.2 正视:指检查者站立于被检查表面的正面、视线与被检表面呈45-90°而进行的观察(如图1)。
被检查表面被检查表面图1:“正视”位置示意图1.3 A级表面:从外部能直接看到、或日常维护时能被直接看到的表面。
A级表面分为A1、A2 两个表面。
(A1、A2表面划分见表下表)1.4 A1表面:在产品正常工作状态下、能直接正视到的产品正前外表面。
1.5 A2表面:在产品正常工作状态下、除A1表面以外的能直接正视到的外表面。
1.7B级表面:除A级以外的所有表面。
1.8 金属表面:包括电镀、氧化、钝化、以及金属压铸面等非喷涂表面。
1.9 打磨:是一种砂带磨削加工,通过砂带对金属表面进行磨削加工,去除金属表面缺陷,并形成具有一定粗糙度、纹路均匀的装饰表面。
1.10 基材花斑:电镀或氧化前因基体材料腐蚀、或者材料中的杂质、或者材料微孔等原因所造成的、与周围材质表面不同光泽或粗糙度的斑块状花纹外观。
1.11 喷涂前划痕:指喷涂或氧化之前因操作不当、或对明显缺陷进行粗打磨等人为造成的基体材料上的一般呈细线型划伤或局部磨擦的痕迹。
1.12 浅划痕:膜层表面划伤,但未伤至底层(即底层未暴露);对其它无膜层表面则为:目测不明显、手指甲触摸无凹凸感、未伤及材料本体的伤痕。
1.13 深划痕:表面膜层划伤,且已伤至底层(即底层已暴露出来);对无膜层表面则为:目测明显、手指甲触摸有凹凸感、伤及材料本体的伤痕。
1.14 凹坑:由于基体材料缺陷、或在加工过程中操作不当等原因而在材料表面留下的小坑状痕迹。
1.15 凹凸痕:因基材受撞击或校形不良等而呈现出的明显变形、凹凸不平整的现象,手摸时有不平感觉。
1.16 打磨区:对基材上的腐蚀、划伤、焊接区、铆接区等部位进行机械打磨抛光后表现出的局部高光泽、光亮区域。
1.17 烧伤:拉丝处理时因操作不当、造成零件表面过热而留下的烧蚀痕迹。
1.18 水印:电镀或氧化后因清洗水未及时干燥或干燥不彻底所形成的斑纹、印迹。
1.29 缩水:因材料、工艺等原因使塑胶或压铸件表面出现凹陷的收缩现象。
1.20 气泡:指因工艺原因内部出现的可见空气泡。
1.21 砂眼:焊接或打磨件表面的疏松针孔。
1.22 披锋:压铸件的分模面上出现或残留的毛刺。
1.23 露白:镀锌彩色钝化膜因磨擦而被去除、露出锌层,或因缝隙截留溶液导致的无钝化膜现象,呈现为区别于周围彩色的白色。
1.24 雾状:镀铬、镀镍表面或透明塑胶表面上的模糊、不清晰、不光亮的现象。
1.25 局部无铬层:指镀铬表面因电镀工艺的局限而在凹槽内、深孔内、折弯内角等低电位区出现铬层未电镀上的现象。
1.26 修补:因膜层损伤而用涂料所作的局部遮盖。
1.27 异物:由材料、模具、环境或机器设备中的灰尘、夹杂物、污物等影响而形成的与表面不同色的斑点。
1.28 颗粒:因材料杂质或外来物(如焊渣等)的影响而在表面形成的、颜色与正常表面一致的凸起现象。
1.29 挂具印:指电镀、氧化、或喷涂等表面处理生产过程中,因装挂用辅助工具的遮挡而使其与零件相接触的部位局部无膜层的现象。
1.30 色差:颜色与标准色板样品片/件不兼容所产生的颜色不一致,不均匀。
1.31 图文损伤:印刷图文因局部脱落或擦伤、附着不良、污染等所造成的图形、字迹不完整不清晰现象。
2 对外观的技术要求2.1 总则2.1.1 原则:产品外观应美观,颜色均匀一致,单独一零/部件的整体视觉效果不能受到破坏,不会给人以劣质产品的印象。
生产者应认真操作、严格控制产品质量,避免在生产过程中出现对各种表面的损伤。
2.1.2表面按其在产品中所处位置和质量要求划分为二个等级,即:A级和B级表面;A级表面中按最终工作状态又可分为A1表面和A2表面。
各等级每一面上表面缺陷的限定标准详见表2 。
2.1.3 有签样或图纸上有特殊要求的零部件,其对应的缺陷优先按其样板或技术要求的标准进行判断。
其它结构件表面缺陷的程度不能超出表2的要求,否则为不合格。
表2 中未包括的缺陷均属于不允许范围(但符合零件状态标准的除外)。
(注:表2 中所列的缺陷个数当在每一表面上超过2个时,每2个缺陷之间的距离必须大于10 mm,否则视为同一缺陷,面积以其总和计。
)2.1.4 对于颜色、光泽和纹理,按零件生产要求进行控制。
除非另外指定,最终的光泽、纹理、抛光应同质量部保存的样品片/件所表现的颜色、纹理和光泽相匹配。
当和样品片/件的差异不是很明显时,是可接受的。
机柜、柜门、面板等所表现的颜色、纹理和光泽相匹配表面应在通用整体质量的基础上判断。
颜色、光泽和纹理应同有纹理的表面的样品片/件视觉兼容。
当同样品片/件相比较时,样板的视觉验收有最终权威。
色差在有争议时以色差仪的Delta E值为依据判定。
2.1.5 特殊装饰表面应在相应的零件图纸中(或以签样的形式)规定是否允许表面缺陷、包括是否允许折弯模具压痕等。
2.2 印刷图文对于印刷图文的要求按DMBM0.402.004 执行。
在外部表面上的印刷图文周围20mm 范围内不允许有明显表面缺陷。
其它按表 2 执行。
2.3加工工艺原因导致的问题2.3.1 拉丝或喷砂表面经压铆后在压铆区域出现纹理、光泽不完全一致的现象(装饰纹被压平或有压过痕迹),可以接受。
2.3.2 对于在压铆、焊接的背面所呈现出的轻微凹凸痕迹,属于正常的加工痕;但在要求较高装饰性的表面(如喷有机涂层的外部表面)应加以适当的掩饰处理。
2.3.3 镀彩锌零件先电镀后压铆时,压铆区的电镀层外观在颜色或光泽上有变化、但镀层及钝化膜无损伤,不作为缺陷。
若钝化膜有损伤,可对损伤部位进行涂漆(金色)修补,该修补不受表 2 的面积限制。
2.3.4 对于机械加工过程中形成的正常模具压印,不属于缺陷;但必须保证其与零件边缘轮廓平行或者具有一定的规律性,压痕的程度各方商定,必要时以签样标准加以限制。
2.3.5 冲压过程中产生的接刀痕,只要符合安全和尺寸规定,即可接受。
2.3.6 带有盲孔、或者较深通孔的零件进行电镀或喷涂时,孔内较难镀(喷)上。
因此允许在孔内部、深度大于孔半径的区域没有膜层,但可以涂上油漆(或其它类似的有保护作用的干膜涂料)加以保护,不允许有可见的腐蚀物。
(同时需注意满足尺寸要求)。
2.3.7 表面处理时的挂具印应安排在B级表面。
对于只有A级表面的零件,其挂具印应位于边角位置,并要求其大小控制在S ≤2.0 且P ≤4 (S 及P 的含义见表2 )。
2.4材料缺陷导致的问题2.4.1由于原材料制造原因,铝制零件有时会在化学处理后、在表面呈现出粗晶组织现象(如斑纹状态)。
这种缺陷不允许出现在面板类零件等A1表面,但可用于其它表面(前提是该材料的其它性能符合相关技术要求,如化学成份、机械性能等,而且花纹应比较均匀。
2.4.2 由电镀锌板、电镀锡板(马口铁)或覆铝锌板制作的零件,在其切口断面会出现锈迹。
只要这种锈蚀现象只发生在断面上、而没有延伸到平板面正面区域,且呈零星点状、不成片,则认为可接受。
镀锌钢板在折弯时出现的压痕处膜层损伤,不允许出现在A1部表面。
2.5缺陷的改善2.5.1 对于基材花斑、或镀前划痕、或者焊接后的表面不平整等,均可以采取打磨抛光的方式加以去除,但抛光区不能留下有深度感的打磨条纹(即应采用较细的磨料,表面粗糙度Ra 低于1.0μm),且打磨后的基材必须符合零件尺寸要求。
因抛光区的光泽与周围区域不同,对同一表面上抛光区的面积和数量限制如表2 ;当超出表2限制时,应对整个表面进行抛光处理以使该表面光泽基本均匀一致,同时也应满足本文2.1.1 条的原则:不能在整个表面布满了小面积的抛光区。
2.6特殊情况2.6.1 当型材棱边有磕碰凹痕时,在A级表面上,正视其磕碰凹痕深度不能超过0.7 mm(如图1),宽度不限;数量每条边不多于2 处。
0.7 mm图2:棱边上的磕碰凹痕2.6.2 无色氧化处理的铝表面上的划痕,均当作“镀前划痕”对待。
2.6.3 当用数控冲床进行加工时,由于机床台面对板材的磨擦作用会出现一些轻微的磨擦痕,即外观上此种擦痕较宽,无凹入感。
此类极轻微的擦痕可以出现在A2表面上、不受表2 限制。
2.6.4 螺钉头上若出现槽口明显变形、或表面膜层破损,均不允许。
若槽口边缘出现的轻微毛刺,在A1表面上、不允许;在其它表面,以目视没有明显的变形、或突起、或膜层脱落等缺陷为限。
2.6.5 对无凹入感的镀前划痕,当其与轮廓边平行者,允许L≤300 且P≤2。
(L 及P 的含义见表2 )3 外观检验条件3.1 目视检测条件为:在自然光或光照度在300-600LX 的近似自然光下(如40W 日光灯、距离500mm 处),相距为500-600 mm,观测时间为 5 秒,且检查者位于被检查表面的正面、视线与被检表面呈45-90°进行正常检验(参见图1)。
要求检验者的校正视力不低于1.2 。
3.2检查时,每一表面按其面积或该表面最大外形尺寸划分为不同大小类别,当有两个条件满足时、以大的一类为准。
表面大小划分标准如表1。
当缺陷所在的检测面尺寸超过表2 中对应的最大一类时,则将该面划分为几个这样的最大面对待,且划分方法应保持同一种方式(即始终按面积分,或始终按外形尺寸分)。
表1:表面大小类别划分表2:产品外观缺陷的可接受范围(注①)注①:表中的L表示单个缺陷长度,单位为mm;S表示单个缺陷面积,单位“mm2”;P表示缺陷的数量,单位“个”。
11。