排气焊缝路试断裂问题解决方案
焊缝裂纹修补方案

项 厚度 坡口名称
次 δ(mm)
坡口形式
带钝边 1 50-160 双 U 形
坡口
坡口角 度
β°
(5-12)
坡口尺寸
间隙 b 钝边 p 半径R (mm) (mm) (mm)
说明
0-2.5
6-10
6-10
β=β1,只标出 β 值,允许采用角度不对 称,高度不对称,角度高 度都不对称的双"Y"坡 口
4.2.2、渗透检测:打磨直至缺陷全部消除。符合 JB/T4730-2005Ⅰ级合格。
的背面,首先在预热区一侧使用氧气-乙Байду номын сангаас气焊预热,要求位置必须准确。预
热温度为 125-140℃。层间温度亦控制在 100~150℃范围内。焊接预热时,预
热范围以焊补部位为中心,在半径为 150mm 的范围内,并取较高的预热温度。
4.2.3.4、根据合格的焊接工艺评定制定焊接工艺卡,严格按工艺卡规定的焊
从事无损检测的人员,必须持有劳动部门颁发的锅炉压力容器无损检测技 术等级证书,Ⅰ级无损检测人员可在Ⅱ级或Ⅲ级人员的指导下,进行相应无损 检测操作、记录检测数据、整理检测资料。Ⅱ级和Ⅲ级人员方可评定检测结果 和签发检验报告。 4.2.5、局部热处理
局部热处理时,加热器应严格布置在焊缝及近缝区,并敷盖保温材料进行 保温。加热宽度应为板厚的 6 倍,焊缝每侧的保温宽度应大于板厚的 10 倍。 加热区布置一定量的热电偶,并采用自动控温设备控制升温、保温和降温过程 及温度的显示和记录,同时打印出工艺曲线,并通过温度显示,随时调节各组 加热器的功率,达到温度均匀。
4.2.3、缺陷修补
4.2.3.1、参与修复施焊的焊工必须持有国家技术质量监督部门颁发的焊工合
耐高温排气管汽车排气管焊缝断裂的失效分析

耐高温排气管汽车排气管焊缝断裂的失效分析某汽车用排气管使用不久焊缝处断裂。
对失效排气管焊缝进行化学成分、金相组织和断口的微。
观分析。
发现该排气管焊缝柱状组织粗大,断口微观形貌为沿晶断裂,柱状晶贯穿整个断裂面,断口有较明。
显的脆性特征。
分析认为该排气管属于早期失效,是由于薄壁的排气管焊接时温度过高,导致焊缝柱状组。
织粗大,加之薄壁管冷却又快,致使焊缝产生较大的内应力。
建议改进焊接工艺,控制较低的层间温度,使焊缝组织细化,解决焊缝断裂问题。
某汽车用排气管在使用不久后焊缝处断裂,为此采用了断口分析、显微组织检验和化学成分分析等方法对该排气管的焊缝断裂进行了失效分析。
失效分析中使用了3件样品。
l#样品未使用过,焊接用焊丝为MCW430NbL;2#,3#为使用不久后焊缝处断裂的样品,使用的焊丝为MIG430L,焊接电流为220。
240 A,电压26 V,混合气体V(Ar):V(CO:)为4:1,气体流量25 L/min;焊接方式为手工半自动环究方向为装备环境失效析。
车排气管焊缝断裂的失效分析焊。
排气管是用日本SUS436L铁素体不锈钢制造的壁厚为0.8 inln的薄壁管件。
1分析方法1.1断裂处组织分析1.1.1断口分析对2#,3#样品焊缝用扫描电镜观察断口形貌。
将l#样品从焊缝处纵向压开,用扫描电镜观察断口形貌。
1.1.2显微组织检验按GB/T 13298—1991《金属显微组织检验方法》,用金相显微镜对焊缝断裂处进行金相显微组织分析。
1.2化学成分分析分别用ISO 9556:1989(E)(钢和铁中总碳测定——感应炉燃烧红外线吸收法》,ISO 4935:1989(E)《钢和铁中总硫量测定——感应炉燃烧红外线吸收法》,GB/T 223.11—1991《钢铁及合金化学分析方法过硫酸铵氧化容量法测定铬量》,GB/T 223.26—1991《钢铁及合金化学分析方法过硫酸铵氧化容量法测定钼量》和钼蓝分光光度法,测定母材SUS436L不锈钢和焊缝(焊丝)的碳、硫、铬、钼、磷等化学成分。
工程机械常见焊接开裂与修复技术
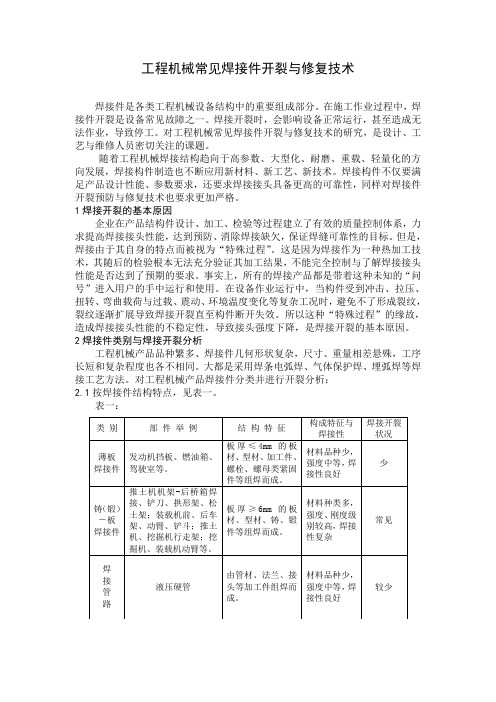
工程机械常见焊接件开裂与修复技术焊接件是各类工程机械设备结构中的重要组成部分。
在施工作业过程中,焊接件开裂是设备常见故障之一。
焊接开裂时,会影响设备正常运行,甚至造成无法作业,导致停工。
对工程机械常见焊接件开裂与修复技术的研究,是设计、工艺与维修人员密切关注的课题。
随着工程机械焊接结构趋向于高参数、大型化、耐磨、重载、轻量化的方向发展,焊接构件制造也不断应用新材料、新工艺、新技术。
焊接构件不仅要满足产品设计性能、参数要求,还要求焊接接头具备更高的可靠性,同样对焊接件开裂预防与修复技术也要求更加严格。
1焊接开裂的基本原因企业在产品结构件设计、加工、检验等过程建立了有效的质量控制体系,力求提高焊接接头性能,达到预防、消除焊接缺欠,保证焊缝可靠性的目标。
但是,焊接由于其自身的特点而被视为“特殊过程”。
这是因为焊接作为一种热加工技术,其随后的检验根本无法充分验证其加工结果,不能完全控制与了解焊接接头性能是否达到了预期的要求。
事实上,所有的焊接产品都是带着这种未知的“问号”进入用户的手中运行和使用。
在设备作业运行中,当构件受到冲击、拉压、扭转、弯曲载荷与过载、震动、环境温度变化等复杂工况时,避免不了形成裂纹,裂纹逐渐扩展导致焊接开裂直至构件断开失效。
所以这种“特殊过程”的缘故,造成焊接接头性能的不稳定性,导致接头强度下降,是焊接开裂的基本原因。
2焊接件类别与焊接开裂分析工程机械产品品种繁多、焊接件几何形状复杂,尺寸、重量相差悬殊,工序长短和复杂程度也各不相同。
大都是采用焊条电弧焊、气体保护焊、埋弧焊等焊接工艺方法。
对工程机械产品焊接件分类并进行开裂分析:2.1按焊接件结构特点,见表一。
表一:2.2按焊接件功能,见表二。
表二2.3按钢材强度级别,见表三。
表三通过以上对焊接件分类与焊接开裂的分析可以看出,焊接件开裂主要集中在工作装置类构件。
这是因为此类焊接件不仅结构复杂、承受大的工作载荷,抗变形能力差,而且采用的钢材品种多、强度级别高,焊接施工难度大。
焊接裂纹的分析与处理
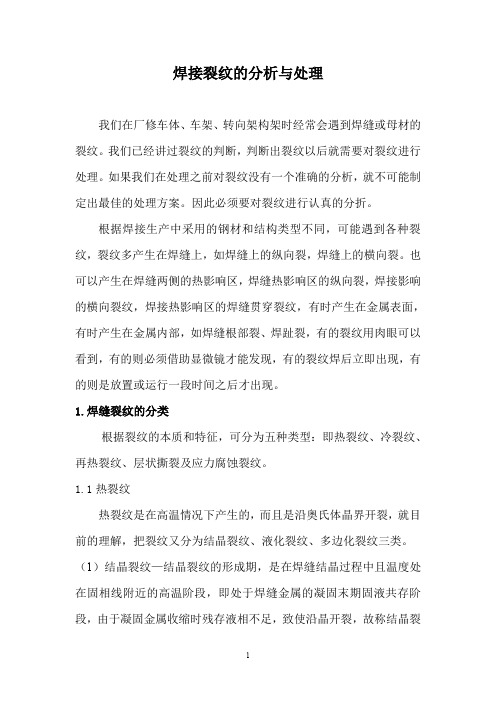
焊接裂纹的分析与处理我们在厂修车体、车架、转向架构架时经常会遇到焊缝或母材的裂纹。
我们已经讲过裂纹的判断,判断出裂纹以后就需要对裂纹进行处理。
如果我们在处理之前对裂纹没有一个准确的分析,就不可能制定出最佳的处理方案。
因此必须要对裂纹进行认真的分折。
根据焊接生产中采用的钢材和结构类型不同,可能遇到各种裂纹,裂纹多产生在焊缝上,如焊缝上的纵向裂,焊缝上的横向裂。
也可以产生在焊缝两侧的热影响区,焊缝热影响区的纵向裂,焊接影响的横向裂纹,焊接热影响区的焊缝贯穿裂纹,有时产生在金属表面,有时产生在金属内部,如焊缝根部裂、焊趾裂,有的裂纹用肉眼可以看到,有的则必须借助显微镜才能发现,有的裂纹焊后立即出现,有的则是放置或运行一段时间之后才出现。
1.焊缝裂纹的分类根据裂纹的本质和特征,可分为五种类型:即热裂纹、冷裂纹、再热裂纹、层状撕裂及应力腐蚀裂纹。
1.1热裂纹热裂纹是在高温情况下产生的,而且是沿奥氏体晶界开裂,就目前的理解,把裂纹又分为结晶裂纹、液化裂纹、多边化裂纹三类。
(1)结晶裂纹—结晶裂纹的形成期,是在焊缝结晶过程中且温度处在固相线附近的高温阶段,即处于焊缝金属的凝固末期固液共存阶段,由于凝固金属收缩时残存液相不足,致使沿晶开裂,故称结晶裂纹,由于这种裂纹是在焊缝金属凝固过程中产生的,所以也称为凝固裂纹。
结晶裂纹的特征:存在的部位主要在焊缝上,也有少量的在热影响区,最常见的是沿焊缝中心长度方向上开裂,即纵向裂,断口有较明显的氧化色,表面无光泽,也是结晶裂纹在高温下形成的一个特征。
(2)液化裂纹—焊接过程中,在焊接热循环峰值温度作用下,在多层焊缝的层间金属以及母材近缝区金属中,由于晶间层金属被重新熔化,在一定的收缩应力的作用下,沿奥氏体晶界产生的开裂,称为“液化裂纹”也称“热撕裂”。
液化裂的特征:①易产生在母材近缝区中紧靠熔合线的地方(部分溶化区),或多层焊缝的层间金属中。
②裂纹的走向,在母材近缝区中,裂纹沿过热奥氏体晶间发展;在多层焊缝金属中,裂纹沿原始柱状晶界发展,裂纹的扩展方向,视应力的最大方向而定,可以是横向或纵向;并在多层焊焊缝金属中,液化裂纹可以贯穿层间;在近缝区中的液化裂纹可以穿越熔合线进入焊缝金属中。
汽车排气管焊缝断裂的失效分析

文献标识码:A
文章编号:1672-9242(2010)03-0014-04
Failure Analysis of Fracture on Weld of Motorcar Vent-pipe
XUAN Wei-fang,WANG Hui,WANG Yi-lin (NO.59 Research Institute of China Ordnance Industry,Chongqing 400039,China)
焊接【K】.北京:机械工业出版社,2001:705.
(上接第9页) 片列入试验报告。
5.6特制槽钢数的选用
出于安全性要求,当被试装备不能直接固定在 安装架上时,需选用特制槽钢过渡。特制槽钢数是 根据被试装备的质量和尺寸以及固定螺孑L间距离进 行选择的,具体选择方法可参考GJB 150.18—86《军 用设备环境试验方法舰船设备的冲击试验》。
microstructure examination and fracture
inspection.It Was detected that the columnar crystal Was big in microstmcture on the position of the weld of vent-pipe.It showed that the fracture was along the crystals on the microstrucmre appearance,columnar cfystals run through fracture surface,fracture
Was rapidly enough to produce big stress.It was suggest that the welding technique should be improved and the lower temperature
焊接件断裂的原因及预防措施

未焊透
缺陷形成原因
防止措施
1、坡口加工 不合适
2、焊接技术 不合适
3、热输入不 合适
1、接头设计必须合适,适当加大坡 口角度,使焊枪能够直接作用到熔 池底部,同时要保持喷嘴到工件的 距离合适;减小钝边高度设置或增 大对接接头中的底层间隙
2、使焊丝保持适当的行走角度,以 达到最大的熔深;使电弧处在熔池 的前沿
谢谢各位同事 晚安
防止措施
1、采用多道焊短 1、在焊接后续焊道之前,清除
路过渡(熔焊渣 掉焊缝边上的渣壳
型夹杂物)
2、减小行走速度;采用含脱氧
2、高的行走速度 剂较高的焊丝;提高电弧电压
(氧化膜型夹杂
物)
气孔
缺陷形成原因
防止措施
1、保护气体覆盖 1、增加保护气流量,排除空气;减小
不足
保护气体流量,防止卷入空气;清除气
2、热输入不足 2、提高送丝速度和电弧电压;减小焊
3、焊接熔池太 接速度
大
3、减面的
合适
熔池边缘停留;焊丝应指向熔池的前沿
5、接头设计不 5、坡口角度应足够大,以便减少焊丝
合理
伸出长度(增大电流),使电弧直接加
热熔池底部;坡口设计为J形或U形
5、减小焊丝的伸出长度
咬边
缺陷形成原因
防止措施
1、焊接速度太高 1、减慢焊接速度
2、电弧电压太高 2、降低电压
3、电流过大
3、降低送丝速度
4、停留时间不足 4、增加在熔池边缘的停留时
5、焊枪角度不正确 间
5、改变焊枪角度使电弧力推
动金属流动
未熔合
缺陷形成原因
防止措施
1、焊缝区表面 1、在焊接之前清理全部坡口面和焊缝 有氧化膜或锈皮 区表面上的轧制氧化皮或杂质
焊接件断裂的原因及预防措施
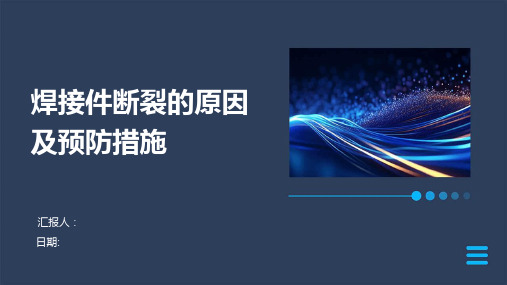
某船舶焊接件断裂事故分析
事故概述
某船舶在航行过程中,焊接部位出现裂纹,导致船舶沉没。
事故原因
焊接过程中,存在夹渣、气孔等缺陷;同时,船舶运营过程中受到交变载荷、腐蚀等因素 的影响,导致裂纹扩展。
预防措施
加强焊接前准备,确保坡口和母材表面清洁;采用合理的焊接工艺参数,避免热影响区硬 化;进行无损检测,及时发现并处理缺陷;合理设计结构,避免交变载荷和腐蚀等因素的 影响。
对焊接设备进行定期维护和保养,确保设备的正常运行和使用寿 命。
建立完善的焊接质量管理体系
制定严格的质量管理制度
01
建立完善的焊接质量管理体系,制定严格的质量管理制度和操
作规程。
强化质量意识
02
加强员工的质量意识教育,让员工充分认识到焊接质量的重要
性。
质量检测与评估
03
对焊接件进行严格的质量检测和评估,确保符合标准和客户要
求。
04
典型焊接件断裂案例 分析
某压力容器焊接件断裂事故分析
事故概述
某压力容器在生产过程中,焊接 部位出现裂纹,导致容器破裂。
事故ห้องสมุดไป่ตู้因
焊接过程中,未能有效清理坡口 和母材表面,存在夹渣、气孔等 缺陷;同时,焊接工艺参数不合
理,导致热影响区硬化。
预防措施
加强焊接前准备,确保坡口和母 材表面清洁;采用合理的焊接工 艺参数,避免热影响区硬化;进 行无损检测,及时发现并处理缺
未焊透
未焊透是指在焊接过程中,接头根部未完全熔透的现象, 未焊透会导致焊接件承载能力下降,容易引发断裂。
夹渣
夹渣是指焊接过程中熔池中的熔渣未完全排除,残留在焊 缝中形成的夹杂物,夹渣的存在会降低焊缝的韧性和塑性 ,影响焊接件的承载能力。
焊缝会出现的问题以及原因和解决方法

焊缝会出现的问题以及原因和解决方法问题问题现象问题分析问题会引发的危害避免措施尺寸偏差焊缝宽度、余高、焊脚尺寸等焊缝尺寸过大或过小。
产生原因:焊条直径及焊接规范选择不当;坡口设计不当;运条手势不良。
危害:尺寸过小,强度降低;尺寸过大,应力集中,疲劳强度降低防止措施:正确选用焊接规范,良好运条咬边由于焊接参数选择不当,或操作方法不正确,沿焊趾的母材部位产生的沟槽或凹陷。
产生原因:操作方法不当,焊接规范选择不正确,如焊接电流太大、电弧过长、运条方式和角度不当、坡口两侧停留时间太长或太短均有产生咬边的可能。
危害:咬边将减少母材的有效截面积、在咬边处可能引起应力集中、特别是低合金高强钢的焊接,咬边的边缘组织被淬硬,易引起裂纹。
防止措施:正确选用焊接规范,不要使用过大的焊接电流,要采用短弧焊,坡口两边运条稍慢、焊缝中间稍快,焊条角度要正确。
气孔焊缝里有洞气孔产生原因:焊件表面氧化物、锈蚀、污染未清理;焊条吸潮;焊接电流过小,电弧过长,焊速太快;药皮保护效果不佳,操作手势不良。
危害:减小焊缝有效截面,降低接头致密性,减小接头承载能力和疲劳强度。
防止措施1、清除焊丝,工作坡口及其附近表面的油污、铁锈、水分和杂物。
2、采用碱性焊条、焊剂,并彻底烘干。
3、采用直流反接并用短电弧施焊。
4、焊前预热,减缓冷却速度。
5、用偏强的规范施焊未焊透有缺口产生原因:坡口、间隙设计不良;焊条角度不正确,操作手势不良;热输入不足,电流过小,焊速太快;坡口焊渣、氧化物未清除。
危害:形成尖锐的缺口,造成应力集中,严重影响接头的强度、疲劳强度等。
防止未焊透的措施:加大焊接电流,加焊盖面焊缝。
夹渣焊接中残留在焊缝中的熔渣产生原因:焊件表面氧化物,层间熔渣没有清除干净;焊接电流过小,焊速太快;坡口设计不当;焊道熔敷顺序不当;操作手势不良。
危害:减小焊缝有效截面,江都接头强度,冲击韧性等。
防止夹渣的措施1、极高焊接操作技术,焊接过程中始终要保持熔池清晰、熔渣与业态金属良好分离。
焊缝出现裂纹处理方法

焊缝出现裂纹处理方法焊接是一种常见的金属连接方式,但难免会出现一些问题。
焊缝出现裂纹是其中一种比较常见的问题。
这会导致焊接强度下降,甚至会影响工件的正常运行和使用寿命。
本文将介绍焊缝出现裂纹的处理方法。
1.预防裂纹的出现首先要做的是预防裂纹的出现。
预防措施包括:(1).选用合适的焊接材料。
应选择符合工件物理性能和化学成分的焊接材料,以确保焊接质量。
(2).确保焊接区域的表面清洁。
在焊接前,应将焊接区域的表面清洁干净,以便进行完美的焊接。
(3).恰当的焊接电流和电压。
应根据焊接材料的性质,在可接受的范围内选择适当的焊接电流和电压。
(4).保持适当的焊接速度。
应保持恰当的焊接速度和焊接温度,以确保焊接均匀和充分。
2.焊缝出现裂纹的处理(1).退火处理。
如果焊缝出现裂纹,可能是焊接后材料产生了内部应力。
应该对焊接件进行退火处理,以消除这些应力。
在退火处理过程中,需要将焊接件放置在还原气体中,加热到一定温度,然后缓慢冷却。
(2).机械加工。
可以通过机械加工把焊缝重新磨平或是用铣床将焊缝变成V形溝后重新焊接,以消除因为焊接引起的问题。
(3).重做焊缝。
如果焊缝的裂纹严重并且处理措施无效,则需要重新焊接。
重新焊接时应使用正确的焊接材料以及合适的焊接参数,以确保焊接质量。
(4).使用补丁或补焊。
对于一些小型的裂缝,可以使用补丁或补焊来修复。
选择合适的补丁或补焊材料,并根据需要进行特定的操作。
以保持金属之间的连续性,从而让修补后的焊缝拥有相同的机械性能和表面光洁度。
3.总结通过以上几种方法,我们可以有效地处理焊缝出现裂纹这一常见问题。
在焊接过程中,我们应遵循正确的焊接流程,并严格控制焊接参数,以保证工件的质量和性能。
对于裂纹的出现,我们要及时采取相应的措施,以避免影响工件的正常使用。
浅析压缩机吸排气管采用钨极氩弧焊出现裂纹原因

徐阳
(重庆美的通用制冷设备有限公司,重庆 401336)
摘 要 :制冷设备主要由换热器、压缩机及电控设备组成,在制冷设备中,主要通过压缩机做功实现制冷剂的循环使用。压缩机
与换热器的连接主要是通过吸排气管分别与两者焊接而成。焊接接头为插入式角焊缝,焊接方法采用钨极氩弧焊。这种插入式
2 焊接试验 2.1 焊接工艺制定
根据母材材质、厚度及焊材直径制定了以下焊接工艺参数 进行试件焊接。 2.2 吸排气管与法兰套焊接试件
吸 排 气 管 直 径 φ108mm,壁 厚 4mm,压 缩 机 法 兰 套 壁 厚 8mm,吸排气管插入法兰套中,接头形式为角焊缝,按上表工艺 参数进行焊接,焊接位置 5F。所得焊接试件如下图 2、图 3 所示。
解决措施。
关键词 :制冷设备 ;钨极氩弧焊 ;泄漏 ;试验
中图分类号 :TH45
文献标识码 :A
文章编号 :11-5004(2019)07-0126-2
商业中央空调主要应用于大型场馆,属于制冷设备中的一 种,其主要有螺杆机、离心机。在制造过程中吸排气管与压缩机 及换热器的焊接难度较大,焊接位置包含了平、立、仰角焊,且 空间狭小,对焊工技术水平要求较高,为质量控制关键点。如若 焊接工艺参数、焊枪角度、接头间隙、焊脚尺寸等控制不当,极 易出现焊接气孔、未熔合等缺陷在压力及应力作用下进而发展 成裂纹导致泄露。鉴于此,特对生产中出现的吸排气管与压缩 机、换热器焊接接头泄露进行了模拟试验及分析,找出接头泄露 原因,并制定预防措施。
1 2
接头间隙
0.5mm~1mm 0mm~0.3mm
焊枪角度
45° ~60° 45° ~60°
某柴油机排气门断裂分析及建议措施

a
b
图1 断裂的排气门形貌
处起源后交汇形成的形貌;裂纹的多处起源区处存在
图4 源区处低倍形貌
图5 源区处放大后形貌
所示为源区进一步放大后的形貌,未观察到图6 源区处放大后形貌图7 疲劳二次裂纹
图2 杆部断口形貌
图3 盘部断口形貌
图8 源区侧表面低倍形貌
图9 源区侧表面放大后形貌
图10 源区侧表面裂纹放大后形貌
图11 断口处的金相组织500×
断口侧表面的裂纹(断口侧面的裂纹形貌所示,裂纹数量较多,深度大多在
右,少数裂纹深度为0.05~0.10mm。
图12 断口侧面的裂纹形貌100×
)化学成分:气门颈部材料化学成分见表
图13 断口处的金相组织500×
)失效柴油机其他排气门的“断裂位置”相同部
图14 未失效气门断口处的金相组织500×
)失效柴油机其他排气门杆部中间位置金相组。
放空阀法兰焊缝断裂失效原因分析

放空阀法兰焊缝断裂失效原因分析摘要:针对某压气站压缩机下游放空阀法兰焊缝断裂的情况,采用外观检测、无损检测、化学分析、金相分析和有限元计算等方法,对该失效法兰进行了失效原因分析。
结果表明:该焊缝断裂属于多源断裂,焊缝上部放空装置较重,在较大风力的作用下,在立管焊缝附近产生很大弯曲载荷,内焊趾处产生应力集中,最终导致裂纹扩展并发生断裂。
结合现场施工和设计情况,提出了防止发生类似事故的建议。
关键词:法兰;断裂;泄漏;金相分析;载荷0 引言站场与阀室是天然气储存、运输系统中必不可少的组成部分,其可靠性在很大程度上影响整条管线系统的安全。
天然气站场和阀室的设备繁多,流程复杂,工况千差万别(如高温、高压、易燃易爆、强腐蚀和有毒介质等),法兰连接多,规格杂,结构和制造标准都有差别,上述各种因素导致法兰潜在失效因素繁多,泄漏的概率大。
因而加强对法兰连接的密封状态、应力状态、腐蚀缺陷和裂纹缺陷的检测评价,变事后维修为事前预防处理,最大程度降低损失,对于管道安全稳定长期运转,具有十分重要的意义。
1 失效事故概况2013年12月25日中午,新疆某天然气压气站运行人员在日常巡检过程中,听见异常气流声音并上报,作业区立即安排值班人员进行全站放空,站场切换至全越站流程,40 min后,站场压力降低到0.3 MPa。
经现场排查发现,3#压缩机出口阀下游管段某处放空立管与法兰连接焊缝断裂,放空阀和立管掉落在附近地面,见图1。
截至19:00完成站场盲板封堵,压缩机组正常运行。
图1 掉落的放空阀装置2 事故调研分析及取样情况2.1 事故调研经调研,该法兰为长颈对焊法兰,连接在3#压缩机组出口管的放空立管上,规格为NPS1,Class900,材质为16Mn,密封形式为环连接面,制造标准为ANSI B 16.5-2009《管法兰与法兰管件》[1];放空立管规格为Φ34.6 mm×4.6 mm,材质为16 Mn,制造标准为GB/T 1591-1988《低合金高强度结构钢》[2]。
中压供汽管道焊缝开裂产生原因分析

中压供汽管道焊缝开裂产生原因分析摘要:中压供汽管道已运行半年突然从焊缝处开裂漏气,从施工、环境、材料、应力及焊口检测等因素进行了综合分析, 认为焊缝泄漏的原因不是施工造成的,而是由于运行人员操作不当,致使强碱溶液混入到中压供汽管道中;同时,由于焊接残余应力和管道承受拉力的永久性存在,在一定温度和压力下,导致强碱溶液对管道薄弱环节焊缝产生快速应力腐蚀,最终破裂发生泄漏。
关键词:供汽管道;焊缝;应力腐蚀;开裂1、焊缝开裂事情经过XX生物质发电项目,2018年11月20日机组已并网发电,中低压供气管道系统(设计压力为1.66MPa、设计温度292℃、管道材质为20#钢)已运行半年多。
2019年5月14日,中压供汽管道突然存在对外冒汽现象,立即对中压供汽管道沿线进行检查,发现中压供汽管道存在有6处对外冒汽的故障点,随后发现故障点逐渐增多,达到30多处。
如下图所示:5月17日,对管道开裂焊缝位置进行了全面处理后投入运行,但没过几天,其供汽管道在上次漏汽位置(已重新焊接处理过的地方)又有漏气现象,并且发现中压供汽管道以及中压联箱存在几处对外冒汽的故障点,随后发现故障点逐渐增多(包括上次焊缝漏汽的地方、新增的焊缝位置、中压联箱焊缝及本体、中压减温器厂家焊口、阀门本体等)。
如下图所示:2、焊缝开裂诸因素分析1)焊口检测分析(1)随机抽样已有焊缝裂纹的23#焊口(透视合格焊口),没有焊缝裂纹的34#、35#焊口进行焊口硬度检测,测量结果如下表:从上表可以看出,焊口和母材的硬度值(20#钢)都在规范许可范围内。
(2)对23#焊口采用超声波进行检测,发现焊口有裂纹缺陷显示;对没有焊缝裂纹的34#、35#焊口采用超声波进行复验,对其中2处深度在4~6mm的反射回波进行了挖补,挖补后采用渗透检测,未发现裂纹缺陷显示。
(3)对76#焊口及母材割取了一段试样管(Ф325X8X450),根据样品断面处发现裂纹从熔合线处由内向外扩散至焊缝表面中心处(见下图);并将试样管送权威机构做进一步的检查分析。
排气挠性软管断裂故障分析与改进

终导致软管断裂。 从绕线式排气管 断口宏观观察, 并无明显的塑性 变形,断口基本 都出现在绕线软 管与排气钢管焊 接处,且断裂位 置不是一次性破 图4绕线式挠·陛软管 坏,完全断裂经 与排气钢管焊接示意图 过一段时间。
弧形,且焊接钢管端口增加涨口、起箍、
缩口、整圆等工序,进一步保证了软管
与钢管之间的无相对摩擦、滑动等风险。 图5绕线式挠性软管与涨口处理后钢管
焊接示意图。
焊接钢管管口
经过涨口处理后的
优点比较明显,钢
管涨口后如图6所
示,其作用主要表
现为:①起到定位 作用,金属软管
外环尺寸16mm;
端口到起箍位置
16mm,若行驶产
因为绕线式挠性软的摩擦切割导致
断裂开口。由此可以判断软管断裂原因
为绕线式挠性软管自身结构存在缺陷的 情况下,叠加装配误差和运动磨损最终
导致绕线式挠性软管断裂。
4改进方案及验证
针对绕线式挠性软管的断裂故障,
提出结构改进方案。首先,在绕线式挠
性软管外增加金属网套,网套的作用即
可以分担金属软管在轴向、径向的静负
荷,还能保证软管波纹部分不直接受到
相对摩擦、撞击等方面的机械损伤。增
加了网套的软管,其强度可以提高十几
倍,屏蔽能力可以到达99.95%。而软 管的延伸率只减小2%~5%,轴向转
动和气密性基本无影响。其次,更改软 管与钢管外环和焊接钢管内环的接头结
构,由原来的直线结构改为端口翻边的
图5绕线式挠性软管与生摩擦,外环起到
再热蒸汽热段放空气管焊缝裂纹的防治措施

再热蒸汽热段放空气管焊缝裂纹的防治措施摘要本文通过介绍300MW机组锅炉再热蒸汽热段管道母材及放空气管道角焊缝,出现大量裂纹的案例,提出再热蒸汽热段放空气管焊缝裂纹的处理方法、防治措施,对同容量同参数,使用相同材质的发电机组检修维护具有一定的参考价值。
关键词300MW锅炉;再热热段;裂纹;防治措施郑州裕中能源有限责任公司新密电厂2×300MW机组所配套的锅炉是上海锅炉厂有限责任公司生产的1025t/h自然循环汽包锅炉,锅炉型号为SG1025/17.5-M888型,单炉膛∏型布置,炉膛由四侧水冷壁组成,水冷壁为膜式全焊接结构,前后侧水冷壁采用双拱形布置,炉膛截面11.89m×12.8m,呈近似正方形,锅筒中心标高64.5m,炉顶管中心线标高60m,炉顶大板梁标高72m,采用四角切圆燃烧,热风送粉,中储式钢球磨煤机制粉系统,露天布置,全钢架悬吊结构,平衡通风,固态机械排渣方式。
#1机组于2006年12月份投产,#2机组于2007年4月份投产。
主蒸汽管道从锅炉高温过热器出口集箱引出,引出管为Φ610×90mm,材质A335P91,经大小头变径为Φ450×41mm,材质A335P91。
在距离第一个弯头垂直焊口约1 500mm处的水平段管子上安装有放空气管(管径Φ42×5.5mm,材质12Cr1MoVG)。
再热蒸汽热段管道分两路从锅炉高温再热器出口集箱引出,引出管均为Φ557.6×24.8mm,材质A335P22,经三通汇合后,管径变为Φ747.5×34mm,材质A335P22。
三通出口焊口至第一个弯头焊口之间水平段管子长度为2450mm,在距离第一个弯头焊口约500mm处的水平段管子上安装有放空气管(管径Φ28×2.5mm,材质12Cr1MoVG)。
再热蒸汽热段管道母材及放空气管道角焊缝出现大量裂纹的位置,就发生在长度为 2 450mm,且距离第一个弯头焊口约 1 000mm范围内的水平段管子上(见图1)。
发动机排气门摩擦焊口断裂失效的原因分析

发动机排气门摩擦焊口断裂失效的原因分析黎志彦;徐得石;王飞华;莫东强【摘要】分析某发动机排气门杆部断裂原因,结果表明:气门因摩擦焊接缺陷导致断裂.采用多方论证的方法,对摩擦焊接缺陷原因进行分析,总结得出产生气门摩擦焊接缺陷的原因:摩擦焊冷机工作和棒料过短,两种因素叠加造成焊接缺陷-微裂纹.【期刊名称】《机电工程技术》【年(卷),期】2019(048)003【总页数】3页(P176-178)【关键词】排气门;摩擦焊接;荧光探伤【作者】黎志彦;徐得石;王飞华;莫东强【作者单位】怀集登云汽配股份有限公司,广东怀集 526400;潍柴动力股份有限公司,山东潍坊 261061;怀集登云汽配股份有限公司,广东怀集 526400;怀集登云汽配股份有限公司,广东怀集 526400【正文语种】中文【中图分类】TK413.4+3Ni-30是由日立和本田开发的可时效硬化的Fe-Ni基合金,以此削减高性能要求的排气门的生产费用。
这个含有约32%Ni的合金替换了由美国(USEV)/Eaton 生产的用于本田Accord车上的排气门。
表1为Ni30合金的化学成分表[1]。
奥氏体不锈钢,其抗氧化、抗蚀性、耐热性较好,但过高的Cr含量会导致高温环境下材料的热稳定性不好[2]。
Ni30材料中添加了Al、Nb、Ti,降低了Cr的含量,保证了合金在长期使用过程中的持久强度[3]。
某公司生产的排气门,是Ni30和45Cr9Si3两种材料通过摩擦焊接组合而成,摩擦焊接工艺在进口120B惯性摩擦焊接机上将气门杆(45Cr9Si3)和头部(Ni30)焊接在一起。
该气门在主机厂生产件批准程序(Production Part Approval Process,PPAP)样件进行200 h台架试验中,有1支气门出现了杆部断裂失效。
相关人员对失效样件进行了分析,确认气门在摩擦焊口断裂。
下文进行具体分析。
1 宏观分析失效气门的照片如图1所示。
2 理化检验检验气门断裂附件的硬度,符合技术要求。
大型油气管道环焊缝失效原因及改进措施
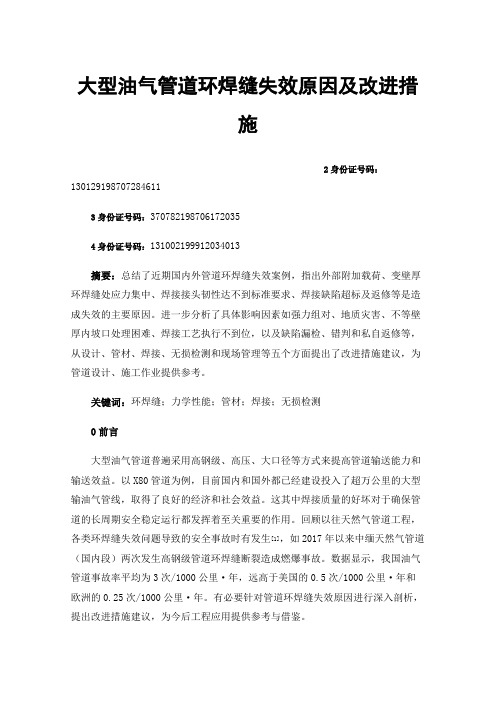
大型油气管道环焊缝失效原因及改进措施2身份证号码:******************3身份证号码:******************4身份证号码:******************摘要:总结了近期国内外管道环焊缝失效案例,指出外部附加载荷、变壁厚环焊缝处应力集中、焊接接头韧性达不到标准要求、焊接缺陷超标及返修等是造成失效的主要原因。
进一步分析了具体影响因素如强力组对、地质灾害、不等壁厚内坡口处理困难、焊接工艺执行不到位,以及缺陷漏检、错判和私自返修等,从设计、管材、焊接、无损检测和现场管理等五个方面提出了改进措施建议,为管道设计、施工作业提供参考。
关键词:环焊缝;力学性能;管材;焊接;无损检测0前言大型油气管道普遍采用高钢级、高压、大口径等方式来提高管道输送能力和输送效益。
以X80管道为例,目前国内和国外都已经建设投入了超万公里的大型输油气管线,取得了良好的经济和社会效益。
这其中焊接质量的好坏对于确保管道的长周期安全稳定运行都发挥着至关重要的作用。
回顾以往天然气管道工程,各类环焊缝失效问题导致的安全事故时有发生[1],如2017年以来中缅天然气管道(国内段)两次发生高钢级管道环焊缝断裂造成燃爆事故。
数据显示,我国油气管道事故率平均为3次/1000公里·年,远高于美国的0.5次/1000公里·年和欧洲的0.25次/1000公里·年。
有必要针对管道环焊缝失效原因进行深入剖析,提出改进措施建议,为今后工程应用提供参考与借鉴。
1失效案例及原因分析1.1国内外失效案例收集到国内2000年以来管道环焊缝失效案例26起,涵盖X52至X80等各种钢级,其中X80管道运行期失效4起,建设期失效3起。
根据不完全统计,北美地区在过去2~3年内发生10次管道失效事故、多数为X70钢级管道环焊缝失效,详见表1。
1.2 失效原因国内管道建设期失效主要原因是:①强力组对应力;②错边超差引起的应力集中;③不等壁厚连接造成较大应力集中;④焊接质量不合格;⑤焊缝韧性低于标准要求。
某发动机排气管悬挂断裂原因分析及改进措施
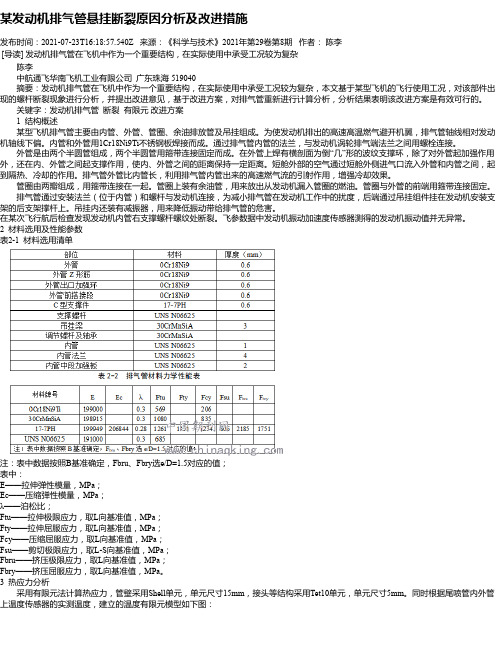
某发动机排气管悬挂断裂原因分析及改进措施发布时间:2021-07-23T16:18:57.540Z 来源:《科学与技术》2021年第29卷第8期作者:陈李[导读] 发动机排气管在飞机中作为一个重要结构,在实际使用中承受工况较为复杂陈李中航通飞华南飞机工业有限公司广东珠海 519040摘要:发动机排气管在飞机中作为一个重要结构,在实际使用中承受工况较为复杂,本文基于某型飞机的飞行使用工况,对该部件出现的螺杆断裂现象进行分析,并提出改进意见,基于改进方案,对排气管重新进行计算分析,分析结果表明该改进方案是有效可行的。
关键字:发动机排气管断裂有限元改进方案1 结构概述某型飞机排气管主要由内管、外管、管圈、余油排放管及吊挂组成。
为使发动机排出的高速高温燃气避开机翼,排气管轴线相对发动机轴线下偏。
内管和外管用1Cr18Ni9Ti不锈钢板焊接而成。
通过排气管内管的法兰,与发动机涡轮排气端法兰之间用螺栓连接。
外管是由两个半圆管组成,两个半圆管用箍带连接固定而成。
在外管上焊有横剖面为倒“几”形的波纹支撑环,除了对外管起加强作用外,还在内、外管之间起支撑作用,使内、外管之间的距离保持一定距离。
短舱外部的空气通过短舱外侧进气口流入外管和内管之间,起到隔热、冷却的作用。
排气管外管比内管长,利用排气管内管出来的高速燃气流的引射作用,增强冷却效果。
管圈由两瓣组成,用箍带连接在一起。
管圈上装有余油管,用来放出从发动机漏入管圈的燃油。
管圈与外管的前端用箍带连接固定。
排气管通过安装法兰(位于内管)和螺杆与发动机连接,为减小排气管在发动机工作中的扰度,后端通过吊挂组件挂在发动机安装支架的后支架撑杆上。
吊挂内还装有减振器,用来降低振动带给排气管的危害。
在某次飞行航后检查发现发动机内管右支撑螺杆螺纹处断裂。
飞参数据中发动机振动加速度传感器测得的发动机振动值并无异常。
2 材料选用及性能参数表2-1 材料选用清单注:表中数据按照B基准确定,Fbru、Fbry选e/D=1.5对应的值;表中:E——拉伸弹性模量,MPa;Ec——压缩弹性模量,MPa;λ——泊松比;Ftu——拉伸极限应力,取L向基准值,MPa;Fty——拉伸屈服应力,取L向基准值,MPa;Fcy——压缩屈服应力,取L向基准值,MPa;Fsu——剪切极限应力,取L-S向基准值,MPa;Fbru——挤压极限应力,取L向基准值,MPa;Fbry——挤压屈服应力,取L向基准值,MPa。
焊缝缺陷的原因和处理方法

焊缝缺陷的原因和处理方法
分类包含主要原因处理方法
裂纹热裂
纹
母材抗裂性能差、焊接材料质量不好、焊接工艺参数选择不当、焊接内应力过大等
在裂纹两端钻止裂孔或铲除裂纹处的焊缝金属,进
行补焊
冷裂
纹
焊接结构设计不合理、焊缝布置不当、焊接工艺措施不合理,焊前未预热、焊后冷却
快等
孔穴气孔
焊条药皮损坏严重、焊条和焊剂未烘烤、母材有油污或锈和氧化物、焊接电流过小、
弧长过长,焊接速度太快等
铲去气孔处的焊缝金属,然后补焊
弧坑
缩孔
焊接电流太大且焊接速度太快、熄弧太快,未反复向熄弧处补充金属等在弧坑处补焊
固体杂质夹渣
焊接材料质量不好、焊接电流太小、焊接速度太快、熔渣密度太小、阻焊熔渣上浮、
多层焊时熔渣未清除干净等
铲除夹渣处的焊缝金属,然后焊补夹钨氩弧焊时钨极与熔池金属接触挖去夹钨处缺陷金属,重新补焊
未熔
合
焊接电流太小、焊接速度太快、坡口角度间隙太小、操作技术不佳等。
铲除未熔合处的焊缝金属好补焊;
未焊透对开敞性好的结构的单面未焊透,可在焊缝背面直接补焊。
对于不能直接焊补的重要焊件,应铲去未焊透的焊缝金属,重新焊接。
形状缺陷咬边
焊接工艺参数选择不当,如电流过大、电弧过长;操作技术不正确,如焊枪角度不对,
运条不当等;焊条药皮端部的电弧偏吹;焊接零件的位置安放不当等。
轻微的、浅的咬边可用机械方法修锉,使其平滑过
渡;严重的、深的咬边应进行补焊。
焊瘤焊接工艺参数选择不正确、操作技术不佳、焊件位置安放不当等铲、锉、磨等手工或机械方法除去多余的堆积金属。
下塌、根部收缩、错边
其它电弧擦伤、飞溅、表面撕裂等。
- 1、下载文档前请自行甄别文档内容的完整性,平台不提供额外的编辑、内容补充、找答案等附加服务。
- 2、"仅部分预览"的文档,不可在线预览部分如存在完整性等问题,可反馈申请退款(可完整预览的文档不适用该条件!)。
- 3、如文档侵犯您的权益,请联系客服反馈,我们会尽快为您处理(人工客服工作时间:9:00-18:30)。
简化载衙或道路处理载荷 ,载荷工况与实际载荷存在一定偏 尤论在汽 车零部件设计开发还是试验阶段都应 当考虑用户 的
差 , 与 道 路 实 验 相 比 ,台 架 模 拟 试 验 速 度 快 、 成 本 低 , 通 常 使 用 要 求 。汽 车 的 耐 久 性 试 验 是 考 核 和 验 证 汽 车 及 零 部 件 耐
久 性 的重 要手 段 ,
剧 于 产 品 设 计 验 证 及 问 题 解 决 方 面 。
某 排 气 系 统 在 整 车 路 试 时 , 出 现 焊缝 断 裂 , 本 文 对 该排
作者简介 :束铭宇 ,硕上, _l 帅.就 职_j:玉柴联 合动力股份 彳f限 气 系 统 焊 缝 断 裂 原 因进 行 分 析 , 对 其 结 构 进 行优 化 设 计 , 并
公 rd,:七婴 从事发动机 能 、噪声 j CAE的研究
最 终 通 过 整 车 验 证 。 我 们 对 优 化 前 后 样 件 进 行路 谱采 集 , 为
ห้องสมุดไป่ตู้
107
汽 车 实 用 技 术
了提 高焊 缝 损 伤 计 算 精 度 , 本 文 没 有 使 用 软 件 中 利 用 理 论 公 应 力 水 平 下 又对 应 着 m 个 不 同疲 劳 寿 命 和 循 环 次 数 ,则 损 伤
验 的 载 荷 工 况 为 实 际 使 用 工 况 ,实 验 结 果 更 准 确 ,通 常 f1]于 汽 车 零 部 件 设 ‘必 须 以市 场 为 导 向 ,设 计 寿 命 “过 大 ”
主 机 厂 的 产 品 认 可 , 台架 模 拟 实 验 的 实 验 载 衙 由 于是 用 经 验 或 “不 足 ” 的 产 晶 通 常 是 不 经 济 日.缺 乏 市 场 竞 争 力 的 ,所 以
RLDA test was done by e·DAQ equipment in Ncode company,And then the welding damage and safe factors was calculated
through test S-N curves byGlyphW orks software,The calculated damage is 1 7.3,It couldn’t meet our target.Then we optimized the hanger design,and did the S-N cur v e and RLDA tests,Recalculated the damage is 0.058 1,meet requirement, Finally the optimized design was submitted to OEM and passed OEM ’S road test. Keywords:Exhaust system;Road load test;S—N Curve;Dam age
式 计 算 的推 荐 寿 命 曲 线 , 而 是 采 用 工 程 寿 命 曲线 试 验 方 法 对 为 : 优 化 前 后 结 构 进 行 寿 命 曲 线 试 验 ,然 后 利 用 :l=程 试 验 S,N 曲 线 对 焊 缝 损 伤进 行 分 析 , 在 考 虑 一 定 安 全 系 数 情 况 下 ,评 估
一
2018年 第2期
10.16638/j.cnki.1671—7988.2018.02.035
排气焊 缝路试 断裂 问题解 决方案
柬 铭 宇
(玉 柴 联 合动 力股 份 有 限 公 司 , 安 徽 芜 湖 241080)
摘 要 :在 某 排 气开 发 项 F1中 ,排 气 系统 路 试 里 程 58%时 ,消 卢 器 m钩 焊 缝 根 部 出现 断 裂 , 丈章 通 过 对 焊缝 质 量 检 查 、焊 缝 寿 命 试验 排 杏 方 式 , 发 现 不 是 焊 缝 质 量 原 凶 , 然 后 利 用 ncode公司 e—DAQ 路 谱 采 集 系 统 对 该 排 气 系 统 吊 钩 焊 缝 进 行 实验 厂 T况 应 变路 谱 采 集 , 并将 实 验 得 到 焊 缝 SN 曲 线输 入 到 ncode公 司 的 GlyphWorks软 件 对 焊缝 路 试 载 荷 损 伤 及 安全 系数 进 行计 算 ,分 析得 到损 伤 为 17.3,不 满 足 要求 ,得 出 失 效 为 设 计 原 ,在对 吊钩 设 汁进 行优 化 后 ,重 新 对 优 化 后 吊钩 进 行 SN 曲线 实 验 干u路 谱 采 集 ,并 计 算 优 化 后 吊钩 损 伤 为 O.058l,满 足耐 久要 求 ,最 后 将 新 设 计方 案提 交主 机 厂路 试 ,最 终通 过路 试验 。 关键词 :排气 系统 ;路谱采集 ;S—N曲线 ;损伤 中图分类号 :U466 文献标识 码 :A 文章编号 :1 671—7988(201 8)02—1 O7一O4
Exhaust System W elding Crack AtRoad Durability Test Problem Solution
Shu M ingyu (Y&C Engine CO.,LTD,Anhui W uhu 241080)
Abstract:At a exhaust system development,When road test reached 58%,M uf l er hanger welding toe cracked.At this paper, W elding quality was be checked,and welding lifetime curve was tested,then we found welding quality meet target.Then
CLC NO.:U466 Document Code:A Article ID:1671—7988(2018)02—107—04
对 汽 车 排 气 系 统 而 言 ,耐 久性 试 验 可 以分 为 道 路 试 验 和
刖 舌
台 架 模 拟 试 验 …『21,两 种 试 验 方 法 各 有 优 缺 点 ,道 路 耐 久 实