乘用车车身结构件被动安全性试验台的研制
4新能源被动安全设计-车身结构设计策略篇
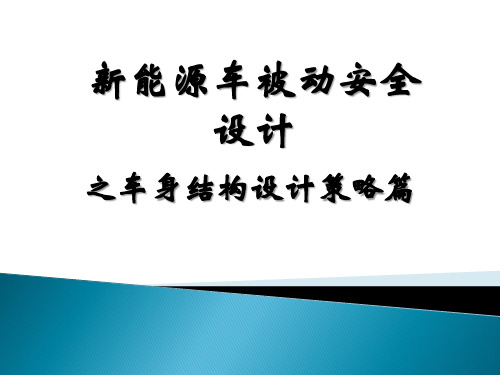
4.2 侧碰方面设计策略-车门防撞梁设计
AE-MDB壁障高度基本越过门槛 梁,需要增加门槛梁上方抵抗刚 度
4.2 侧碰方面设计策略-上下传递路径组合设计
4.2 侧碰方面设计策略-地板横梁设计
4.3 后碰方面设计策略-后碰常规形式
FMVSS 305要求碰撞项
国标GB 20072-2006 50km/h
动力电池传感器加速度曲线
动力电池变形动画
ACCELEROMETER
BR1
BL2
BL1
BL2
附录:CAE分析结果
一、40%偏置碰分析结果 二、100%正碰分析结果 三、侧碰分析结果 四、约束系统假人得分评估
附录:CAE分析结果
50km/h侧碰 优化结果对比:
表1. 侵入速度对比
指标
xx
头部
5.0
4.4 动力电池包框架设计策略
主考察工况冲击载荷 路径横梁加粗
电池包框架设计过程中也要考虑与
车体配合以及载荷的输入,从而到 最佳的传递路径
4.4 动力电池包框架设计策略
柱撞对结构变形考验程度最大。电池包肯定受到挤 压,框架设计非常必要,判定内部模组接触力为零 则风险非常低
4.4 动力电池包框架设计策略-设计示例
指标
A-B柱压缩 腰线 量(mm) 门槛
XX 目标 10.08版 优化方案
98.0
155
41
41.0 <52
69
15
— 结构改进优化后A柱及铰链柱变形改善明显。 — A-B柱压缩量减小,满足目标。
A-B Pillar
优化后变形动画
附录: CAE分析结果
64km/h 40%偏置碰优化结果:
— 纵梁结构刚度提升,前端吸能增加,根部折弯明显改善,变形模式合理。 — 纵梁截面力由90KN提升到130KN;满足当前质量下的纵梁吸能要求。
[讲解]四门两盖耐久试验台(环境舱)试验要求
![[讲解]四门两盖耐久试验台(环境舱)试验要求](https://img.taocdn.com/s3/m/a4da6471f4335a8102d276a20029bd64793e625d.png)
四门两盖性能及耐久试验台(环境舱)技术要求一、概述根据中国汽车技术研究中心《汽车四门两盖性能耐久试验台》技术要求,我司研制出一套便携式四门两盖开启件性能及耐久试验台。
该试验台可在环境仓内对汽车侧门和前、后舱盖的机构及紧固件功能质量进行验证试验。
该试验台适用车型为:M1, M2, N1类车,主要用于车侧门、发动机舱盖、行李箱盖以及商务车侧滑门等的门铰链、限位器、门锁、车门密封条等总成的综合性能及耐久试验。
二、设备特点◆该试验台在设计和实施过程中,在硬件、软件、机械等各方面进行了综合考量,以提高系统的扩展性和柔性,使其能适合用户各现有车型及未来车型四门二盖的性能与耐久试验,在使用过程中可快速切换、方便操作。
◆运用我司的专有技术,该试验台可在(-40℃~+85℃)高低温环境下保持可靠的动作执行及性能测试,可长时间连续工作,性能稳定可靠。
三、设备功能可在环境仓内实现发动机舱盖和行李箱盖的解锁、开启和关闭试验,以及前后侧门的内、外开手柄解锁,内、外开启和关闭试验。
可在环境仓内实时测量侧门的解锁力、开启力和关闭力,并通过测控系统和计算机实时显示各力值与时间的关系曲线,以及开启力、关闭力与门转角的性能曲线。
可在环境仓内实时测量发动机舱盖和行李箱盖的解锁力、开启力和关闭力,并通过测控系统和计算机实时显示各力值与时间的关系曲线。
可在环境仓内实时测量试验过程中电动玻璃升降器、后视镜及门锁的工作电流,并通过测控系统和计算机实时显示各电流值与时间的关系曲线。
动作执行器可在高低温(-40℃~+85℃)环境下保持可靠运行。
四、技术指标a)开门速度:0~3m/s(可调节);b)试验频率:2~10次/分(可调节);c)测量精度:力和电流1%,速度2%;d)设备的检测元件和执行机构可以承受-40℃-+85℃,20%-95%湿度的环境条件;e)气动系统的执行机构可以承受-40℃-+85℃,20%-95%湿度的环境条件,气动控制部分集中管理和布局;f)设备的测控机柜放置在环境室外可以承受-5℃-+40℃,20%-75%湿度的环境条件;g)电气元件集成在可便携移动式测控机柜内,柜内通风良好;h)检测元件、执行结构可以快速推移、定位、固定。
基于LabVIEW的汽车ABS试验台测控系统
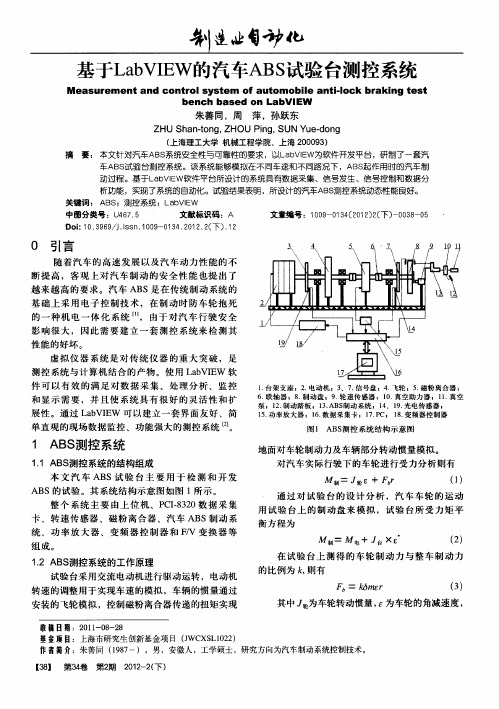
地面对 车轮制 动 力及 车辆 部分转动 惯量 模拟 。
对汽 车实 际行驶 下 的车轮进 行 受力分 析则 有 制= . £+ , , 轮 . () 1
通 过 对 试 验 台 的设 计分 析 ,汽 车 车 轮 的 运 动 用 试 验 台 上 的制 动 盘 来 模 拟 ,试 验 台所 受 力 矩 平
221 电动机 数字式 PD .. I控制设计 为 了使 测 试 系统 达 到 一 个 较 好 的控 制 效 果 ,
块 。 模 块化 使 程 序 结构 清 晰 ,针 对 不 同 的 测 试 对 象 ,编 程 各 自的子 模 块 ,每 个 子 模 块 可 以单 独使
用 ,也 可 以提 供 给 子 程 序 调 用 ,组 成 虚拟 主 控 面 板 。 图 3为 系统软 件 的结构 和功 能框 图 。
性能 的好 坏 。 虚 拟 仪 器 系 统 是 对 传 统 仪 器 的重 大 突破 ,是
测控 系统 与计算 机 结合 的 产物 。使 用 L b I W 软 aV E 件 可 以 有 效 的 满 足 对数 据 采 集 、处理 分 析 、监 控
和 显 示 需 要 ,并 且 使 系 统 具 有 很好 的灵 活 性 和 扩 展性 。通 过 L b E 可 以建立 一 套界 面友 好 、简 a VI W 单直 观 的现场数 据 监控 、功能 强大 的 测控 系统 。
D i1 .9 9 Jis .0 9 1 4 2 1 .( )1 o : 3 6 / . n 1 0-0 3 .0 2 2下 .2 0 s
0 引言
随着 汽 车 的高 速 发展 以及 汽车 动 力性 能 的 不 断 提 高 ,客 观 上 对 汽 车 制 动 的 安全 性 能 也 提 出 了 越 来越 高 的要 求 。汽 车 A BS是 在 传统 制 动 系统 的 基 础 上 采 用 电子 控 制 技 术 ,在制 动 时 防车 轮 抱 死 的 一 种 机 电 一 体 化 系 统 ”, 由于 对 汽 车 行 驶 安 全 影 响 很 大 , 因此 需 要 建 立 一 套 测控 系统 来 检 测 其
汽车被动安全性试验概述

汽车被动安全性试验概述汽车被动安全性是指车辆在发生交通事故时,为乘员提供保护的能力。
被动安全性试验是评估汽车在碰撞、侧翻等事故情况下对乘员的保护能力的重要手段。
汽车被动安全性试验通常包括碰撞试验、侧翻试验、车身刚度试验等内容,通过这些试验可以评估汽车在不同事故情况下的保护能力,为消费者选择安全的汽车提供参考。
碰撞试验是被动安全性试验中最为重要的一项内容。
碰撞试验通常分为正面碰撞试验和侧面碰撞试验两种。
在正面碰撞试验中,汽车以一定的速度撞向障碍物,通过测量车辆变形情况、乘员受力情况等指标来评估汽车在碰撞事故中的保护能力。
而在侧面碰撞试验中,汽车则以一定的速度撞向侧面障碍物,评估汽车在侧面碰撞事故中的保护能力。
这些试验可以帮助消费者了解汽车在不同碰撞情况下的保护水平,选择更安全的汽车。
侧翻试验是另一项重要的被动安全性试验内容。
在侧翻试验中,汽车以一定的速度进行侧翻,通过观察车辆侧翻时的稳定性、车顶强度等指标来评估汽车在侧翻事故中的保护能力。
侧翻事故往往会对乘员造成严重伤害,因此侧翻试验的结果对于消费者选择安全的汽车至关重要。
此外,车身刚度试验也是被动安全性试验中的重要内容之一。
车身刚度试验通过对车身刚度进行测试,评估汽车在碰撞事故中的变形情况以及乘员受力情况。
车身刚度对于汽车在碰撞事故中的保护能力有着重要的影响,因此车身刚度试验也是消费者选择安全汽车时需要考虑的因素之一。
除了上述试验内容外,汽车被动安全性试验还包括了车内安全气囊、安全带等安全装置的测试。
这些安全装置在事故发生时可以为乘员提供重要的保护,因此其性能的测试也是被动安全性试验的重要内容。
总的来说,汽车被动安全性试验是评估汽车在发生事故时对乘员提供保护的重要手段。
通过碰撞试验、侧翻试验、车身刚度试验等内容的测试,可以评估汽车在不同事故情况下的保护能力,为消费者选择安全的汽车提供参考。
消费者在购买汽车时,除了关注汽车的性能、外观等因素外,也需要重视汽车的被动安全性能,选择更安全的汽车,保障自己和家人的安全。
《乘用车悬架系统台架试验标准规范》编制说明范本
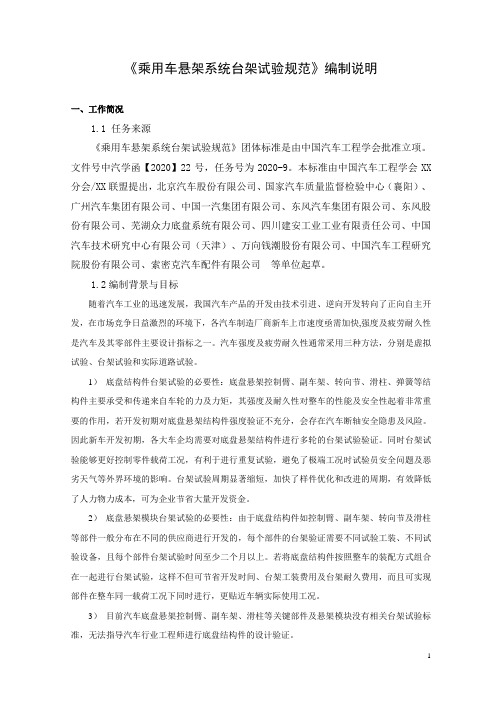
《乘用车悬架系统台架试验规范》编制说明一、工作简况1.1 任务来源《乘用车悬架系统台架试验规范》团体标准是由中国汽车工程学会批准立项。
文件号中汽学函【2020】22号,任务号为2020-9。
本标准由中国汽车工程学会XX 分会/XX联盟提出,北京汽车股份有限公司、国家汽车质量监督检验中心(襄阳)、广州汽车集团有限公司、中国一汽集团有限公司、东风汽车集团有限公司、东风股份有限公司、芜湖众力底盘系统有限公司、四川建安工业工业有限责任公司、中国汽车技术研究中心有限公司(天津)、万向钱潮股份有限公司、中国汽车工程研究院股份有限公司、索密克汽车配件有限公司等单位起草。
1.2编制背景与目标随着汽车工业的迅速发展,我国汽车产品的开发由技术引进、逆向开发转向了正向自主开发,在市场竞争日益激烈的环境下,各汽车制造厂商新车上市速度亟需加快,强度及疲劳耐久性是汽车及其零部件主要设计指标之一。
汽车强度及疲劳耐久性通常采用三种方法,分别是虚拟试验、台架试验和实际道路试验。
1)底盘结构件台架试验的必要性:底盘悬架控制臂、副车架、转向节、滑柱、弹簧等结构件主要承受和传递来自车轮的力及力矩,其强度及耐久性对整车的性能及安全性起着非常重要的作用,若开发初期对底盘悬架结构件强度验证不充分,会存在汽车断轴安全隐患及风险。
因此新车开发初期,各大车企均需要对底盘悬架结构件进行多轮的台架试验验证。
同时台架试验能够更好控制零件载荷工况,有利于进行重复试验,避免了极端工况时试验员安全问题及恶劣天气等外界环境的影响。
台架试验周期显著缩短,加快了样件优化和改进的周期,有效降低了人力物力成本,可为企业节省大量开发资金。
2)底盘悬架模块台架试验的必要性:由于底盘结构件如控制臂、副车架、转向节及滑柱等部件一般分布在不同的供应商进行开发的,每个部件的台架验证需要不同试验工装、不同试验设备,且每个部件台架试验时间至少二个月以上。
若将底盘结构件按照整车的装配方式组合在一起进行台架试验,这样不但可节省开发时间、台架工装费用及台架耐久费用,而且可实现部件在整车同一载荷工况下同时进行,更贴近车辆实际使用工况。
汽车性能试验简介

室内试验台分类
测功机分类
单滚筒 试验台
双滚筒 试验台
平板式 试验台
水力测 功机
电涡流 测功机
直流电 力测功
机
汽车制动性能试验
汽车制动系统包括行车制动装置和停车制动装置两套独立的 装置,其作用是使行驶中的汽车按照驾驶员的要求进行强制减速设 置停车,使已停驶的汽车在各种道路条件下(包括坡道)稳定驻车, 使下坡行驶的汽车速度保持稳定。
试验方法
1)零部件单件试验 考核其设计和工艺的合理性,测试其刚度、强度、磨损和疲 劳寿命以及研究材料的选取是否合适。
2)整车台架试验 试验台架可以模拟实际使用工况,其能消除不需要研究的某 些因数,特别是不受环境的影响,且可以长时间连续进行试验,效 率高,尤其适合于汽车性能的对比试验和可靠性、耐久性试验。在 实际试验中建立台架试验与试车道路试验的当量关系,代替一部分 道路试验。
汽车动力性能试验
1)道路加速度性能试验 汽车的加速性能是指汽车在各种使用条件下迅速增大行驶速
度的能力,是汽车最重要、最基本的使用性能之一。 评价指标:加速度、加速时间、加速距离; 汽车加速性能越好,汽车的动力性越好; 加速性能试验分为: 原地起步加速性能试验 固定挡加速性能试验
汽车动力性能试验
2)车速试验 车速试验包括最低稳定车速试验和最高车速试验。 最低稳定车速通常在直接档下汽车能够稳定行驶的最低车速 最高车速指汽车在无风情况下,在水平良好的路面上汽车能
汽车行驶平顺性试验
汽车平顺性是指避免汽车在行驶过程中所产生的振动和冲击 使人感到不舒服、疲劳甚至损害健康,或使货物损坏的性能。又叫 乘坐舒适性。
新型乘用车法兰试验台的结构设计
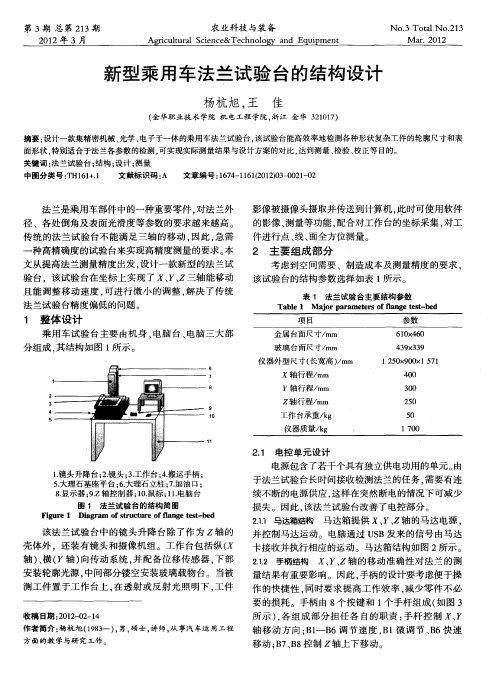
21 0 2年 3月
农 业科 技 与装备
A g iu t rl ce c & Te h l g nd Eq i m e t rc lu a S i n e c no o y a u p n
N O. O a o. 1 3T t N 2 3 l
M a .2 2 r 01
1 整体设计
乘用 车试 验 台主 要 由机身 、 电脑 台 、 电脑 三 大 部 分 组成 . 结构 如 图 1 示 。 其 所
参数
6040 1 x 6 4939 3 x 3
1 2 ×9O 50 0×1 5 71
仪器外型尺寸( 长宽高 )m /m
轴行程/ mm l轴 行 程 / m , m Z轴 行 程/ m m 工作 台承 重 / g k
图 1 法兰试验 台的结构简图
F g r Di g a o t u t r f a g e t b d iu e1 a r m fs r c u e o n e ts - e l f
电源包含了若干个具有独立供电功用的单元。 由 于法 兰试验 台长时 间接 收检测 法 兰的任 务 , 要 有连 需 续 不 断 的电源供 应 , 这样 在突然 断 电 的情 况 下可 减少 损 失 。 因此 , 法兰试 验 台改善 了电控部 分 。 该
轴移动方 向 :1 B B 一 6调 节 速度 . 1微 调 节 、 6快 速 B B 移 动 ;7 B B 、8控制 z轴上 下移 动 。
作者简介 : 杨杭旭 (9 3 ) 男 , 1 8一 , 硕士 , 师, 讲 从事汽车运用工程
方面的教 学与研 究工作 。
2 2
农业 科技 与装 备
安装轮廓光源 。 中间部分镂空安装玻璃载物 台。当被 测 工 件置 于 工作 台上 , 透 射 或 反射 光 照 明下 , 件 在 工
汽车碰撞安全性研究之路
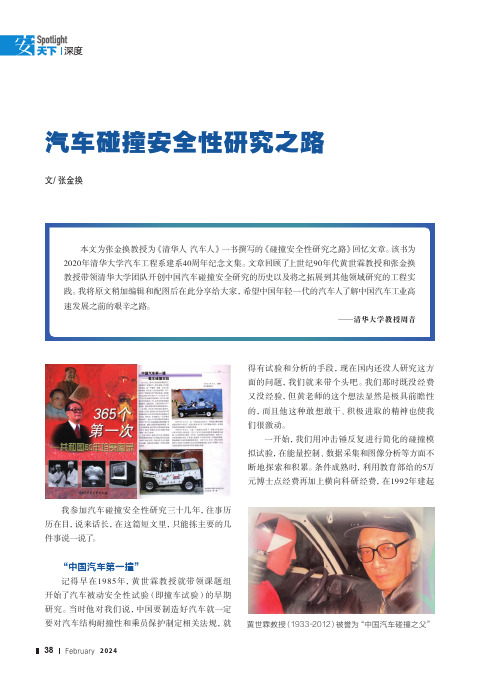
文/ 张金换汽车碰撞安全性研究之路我参加汽车碰撞安全性研究三十几年,往事历历在目,说来话长,在这篇短文里,只能拣主要的几件事说一说了。
“中国汽车第一撞”记得早在1985年,黄世霖教授就带领课题组开始了汽车被动安全性试验(即撞车试验)的早期研究。
当时他对我们说,中国要制造好汽车就一定要对汽车结构耐撞性和乘员保护制定相关法规,就得有试验和分析的手段,现在国内还没人研究这方面的问题,我们就来带个头吧。
我们那时既没经费又没经验,但黄老师的这个想法显然是极具前瞻性的,而且他这种敢想敢干、积极进取的精神也使我们很激动。
一开始,我们用冲击锤反复进行简化的碰撞模拟试验,在能量控制、数据采集和图像分析等方面不断地探索和积累。
条件成熟时,利用教育部给的5万元博士点经费再加上横向科研经费,在1992年建起黄世霖教授(1933-2012)被誉为“中国汽车碰撞之父”38February 2024本文为张金换教授为《清华人 汽车人》一书撰写的《碰撞安全性研究之路》回忆文章。
该书为2020年清华大学汽车工程系建系40周年纪念文集。
文章回顾了上世纪90年代黄世霖教授和张金换教授带领清华大学团队开创中国汽车碰撞安全研究的历史以及将之拓展到其他领域研究的工程实践。
我将原文稍加编辑和配图后在此分享给大家,希望中国年轻一代的汽车人了解中国汽车工业高速发展之前的艰辛之路。
——清华大学教授周青了中国第一座汽车碰撞试验台。
当时的汽车实验室里没有足够大的空间,我们只能把整套实验装置搭建在室外院子里,每次做试验,都要花上一两天的时间进行准备。
大家把牵引用的橡皮绳、自制的缓冲液压缸(最初还使用过汽油桶来控制碰撞的减速度波形)、隔离桶等搬出来,然后做车辆的预处理,布设数据采集设备。
课题组成员不论男女都很能吃苦,还愉快地自称为“拉橡皮绳的”。
就是在这样简陋的条件下,我们在1992年5月31日完成了被中国汽车报记者刘小勇称为“中国汽车第一撞”的中国首次汽车碰撞试验。
一种整车垂直振动试验台的研制与改进

2 技术方 案的确 定
21 国 内外相 关技 术 现状 .
1 试验 台功能定位及主要技术指标
11 功 能定位 .
按照结构和工作原理 , 振动试验 台大体分为电动 振动台、 电液伺服振动台和机械式振动台 3 个大类。 电动振 动台 , 可提供很宽频率范 围的振动 , 但其 振幅 目前最大只能达到 5 nl 0 i 左右 ,不能满足汽车 l l 产品结构应力分析试验要求。
研 制 本试 验 台的最 终 目的 , 为优 化 设 计 服务 。 是
收 稿 日期 :0 2 0 - l 2 1- 6 1 -
作者简介 : 伟( 9 6 ) 男 , 周 16 一 , 广西柳州 人 , 高级工程师 , 士学位 , 学 主要研 究方 向为汽车整车及零部件研 发试验技 术。 16 8
《 装备制造技术}0 2 2 1 年第 9 期
成本高。
传统的机械式振动台, 价格低廉 , 但体积庞大 , 各 激振单元之间的相位控制精度低 , 振动波形失真大 。 近年来 , 随着科技不断进步 , 机械式振动 台也 出 现 了多种技术 改 良, 动系统大幅简化 , 传 设备 占地面 积大幅减少 , 控制精度明显改善。 在 国外 已出现了以伺服电机为动力源 的新型机 械式整车振动试验台。 其技术原理为 : 伺服 电机通过 联轴节 与滚珠螺 杆( 或称 “ 滚珠丝杠 ” 连接 , ) 滚珠 螺 杆 的螺 帽 与平 台通 过 螺 栓相 连 ,于 是 伺 服 电机 的 往 复转动 ,便通过滚珠螺杆转变为平台 的往复直线运 动 。仿 形 凸 台通过 螺 栓 固定 在平 台上 , 动杆 上 的滚 被 子可绕其轴心 自由回转 , 当仿形 凸台左右运动时 , 被 动杆 则 上 下运 动 。改 变 仿形 凸 台 的轮廓 形 状 , 直 接 可 影响到被动杆的振幅和频率 。 该方案 的主要缺点有 : () 1 每做一次上下运动 , 伺服 电机 都需要反转运 动, 高频振动时 , 电机 的动态 响应性 能要求很 高 , 对 电机 的寿命较短。 () 2 为实现不 同的工况 ,需要准备多个仿形 凸 台, 成本较高 。虽然现在 国外有公司引入 了电子凸轮 的技术 , 取消了仿形凸台, 由伺服电机编程模拟 , 改 实 现 了凸轮 运 动轨 迹 ,但 同样 使得 电机 负荷 大 幅上 升 , 据相关用户反馈 , 此类设备 目前还只能用于整车振动 性 能 分析 , 以满 足 整车 振动 疲 劳试验 的苛 刻要 求 。 难 22 本 项 目技术 方 案 - 基于对整车振动试验 台的功 能定 位 ,结合上 述 技术分析 , 目组决定整车振动试验 台的技术方案 , 项 为机 电一体化结构 ,采 用伺服 电机作为激振机构 的 动力源 , 利用其 能实现精准控制的技术 特性 , 保证振 动 的频 率 响应 及 振动 相 位 的准 确性 。 另一方面 , 出于保 证设备可靠性 的考虑 , 激振 单 元采用机械结构 , 将伺服 电机单方向的旋转运动 , 转 化 为激振柱 的往返直线运动 ,从而避免伺服 电机高 速往复旋 转可能引起 的使用寿命降低 。 试验 台的总体布置方案如图 1 。
汽车碰撞模拟实验台设计

1 绪论1.1 课题来源与国内外现状随着科技的进步、经济的发展、人民生活水平的不断提高,汽车己经成为人们学习、工作、生活中不可缺少的代步工具,对人们的生活、生产产生了深刻的影响。
作为一种便捷的现代化交通工具,汽车在给人们带来极大便利的同时,也因其造成的交通事故给人类的生命和财产安全带来了严重威胁。
随着全球汽车保有量的不断增加,交通事故也随之增加,交通事故己经成为全球范围内的一大社会问题。
这是一组让人膛目结舌的数字。
美国的汽车保有量为1.3亿辆,每年道路交通死亡4万人左右;日本的汽车保有量近8000万辆,每年道路交通死亡1.1万人,去年降到8000人。
中国的汽车保有量是3000万辆,每年道路交通死亡近11万人,单车事故率相当于美国的近13倍,日本的近40倍。
除去交通状况等客观因素,一个不可回避的原因就是中国汽车安全系数低,我国交通事故的严重程度由此可想而知。
随着我国道路交通状况的不断改善,我国汽车的保有量不断增加,车速也逐渐提高,交通事故总量和所造成的人员伤亡与财产损失近年来也呈上升趋势。
加强道路交通系统和汽车安全的研究,预防交通事故,是需要全社会共同关注和迫切改善的重要课题[1-2]。
汽车安全性问题与汽车的各种性能等直接或间接有关,对其研究最初是与提高汽车的整车性能的研究交织在一起的。
随着二战后汽车工业的持续发展,到60年代中期,西方发达国家中汽车的保有量和汽车的动力性能有了明显的提高,公路上的车流密度和车流速度己达到了一个空前高的水平,汽车事故发生率空前高涨,汽车安全性受到了公众和政府部门的高度重视。
从这一时期开始,各国相继制定或修订了安全法规,如美国的汽车安全标准FMVSS等[3]。
在这些法规的制约下,以及为了提高汽车产品的竞争力,各大汽车制造商和一些研究机构开展了汽车安全性的专门研究。
汽车安全性研究逐渐从汽车技术研究的其他领域分离出来形成了一个独立的分支。
1.2 汽车安全性的种类汽车安全性可划分为主动安全性和被动安全性[4-5]。
汽车内外饰系统级试验的相关概述

10.16638/ki.1671-7988.2021.05.047汽车内外饰系统级试验的相关概述邓茗馨(华晨宝马汽车有限公司研发部,辽宁沈阳110143)摘要:为了解决汽车内外饰件由于频繁使用和自然环境影响产生的老化问题,产品开发部门需要在研发阶段对产品进行一系列的验证试验。
其中,系统级试验具有测试件零件模块化、适应测试种类多样化、安装状态准确及研发成本低效率高的优点,在研发阶段正在被日益广泛的应用。
文章介绍了系统级试验所涵盖的环境老化试验,振动试验,耐久试验,刚度试验和安全性试验,并阐述了对应的试验目的和试验方法。
关键词:内外饰;环境老化试验;振动试验;耐久试验;刚度试验;安全性试验中图分类号:U467 文献标识码:A 文章编号:1671-7988(2021)05-160-03Overview of System-Level Tests for Automotive Interior and Exterior PartsDeng Mingxin( BMW Brilliance Automotive Ltd. R&D Department, Liaoning Shenyang 110143 )Abstract:For automotive interior and exterior parts, a series of validation tests are required during product development phase, to address the aging issue which is attributed to its environment and frequent daily use. System-level validation test is increasingly applied for its merits on modularization of test parts, versatility of testing types, accurate mounting status, and lower development cost. This paper introduced system-level validation tests including environmental aging test, vibration test, durability test, stiffness and strength test, and safety test. Objectives and methods for each test was preliminarily demonstrated.Keywords: Interior and exterior parts; Environmental aging test; Vibration test; Durability test; Stiffness test; Safety test CLC NO.: U467 Document Code: A Article ID: 1671-7988(2021)05-160-03前言在汽车行业,新车型在量产前需要进行一系列的整车和零件甚至其材料的相关试验,从而确保产品在设计寿命周期内的安全性和功能性。
乘用车四分之一悬架试验台设计

乘用车1/4悬架试验台设计摘要:汽车悬架是乘用车必不可少的机构,不论是乘用车还是商用车,都离不开悬架机构,它关系到乘用车的乘坐平顺性,减缓乘用车车身和车桥的振动,当乘用车受到来自地面的冲击时,或者其他外界的激励,缓和这些外界激励造成的冲击作用,此外还关系到驾驶人员和乘坐人员的安全性与否。
鉴于悬架装置的重要性,此次设计的共振式汽车减振试验台来检测其性能。
首先分析了减振试验台的工作原理,说明了减振试验台的设计要求,再对减振试验台的零部件进行设计分析,然后进行相应的强度校核,并作了技术经济性分析,表明设计的减振试验台符合设计要求。
这种方法的优点在于试验台性能稳定,数据可靠性好,但缺点是检测参数单一,对悬架装置不能形成全面的分析与故障诊断,无法全面反映悬架装置的技术状况。
关键词:减振器;谐振式试验台;谐振频率;谐振振幅The design of passenger car’s suspension test-bedAbstract:Car suspension is essential for passenger cars, whether passenger cars or commercial vehicles, are inseparable from the suspension mechanism, it is related to the passenger ride ride comfort, slow down the car body and axle Vibration, when the passenger car from the impact of the ground, or other external incentives to ease the impact of these external incentives, but also related to the safety of drivers and passengers or not.In view of the importance of suspension devices, the design resonant vehicle vibration reduction test bed to detect its performance. First analyzes the working principle of vibration test rig, vibration test rig is described in the design requirements, and design analysis was carried out on the vibration test rig parts, then the corresponding intensity, and the technical economy analysis, shows that the design of vibration test rig conform to the design requirements. This method is to test the advantages of stable performance, good reliability data, but the disadvantage is that single detection parameters, the suspension could not form a comprehensive analysis and fault diagnosis, can not fully reflect the technical condition of the suspension.Keywords: Suspension resonant;Test stand;Resonant frequency;Resonant amplitude目录摘要 (I)Abstract .................................................................................................................................... I I 1 绪论 .. (1)1.1 国外汽车检测技术发展状况 (1)1.2 中国汽车维修行业的基本情况 (1)1.2.1 汽车维修行业存在的基本问题 (1)1.2.2 汽车维修行业面临的新形势 (2)1.2.3 汽车维修行业的发展趋势 (3)1.3 汽车悬架性能试验技术的发展状况 (3)2 汽车减振试验台的设计 (7)2.1 汽车减振器工作原理 (7)2.2 试验台的设计 (7)2.3 检测台设计注意事项 (8)3 零部件设计 (9)3.1 电机的设计 (9)3.1.1 计算电机的平均转矩 (9)3.1.2 电机的过载能力校验 (10)3.2 偏心轴的设计 (10)3.2.1 轴的受力分析 (10)3.2.2 确定轴颈参数 (11)3.2.3 轴的疲劳强度校核 (12)3.2.4 轴的挠度校核 (12)3.3 轴上键的强度校核 (13)3.4 联轴器的设计 (13)3.5 偏心轴轴承的设计 (14)3.6 轴承座的设计 (14)3.7 飞轮的设计 (14)3.8 滚动导向柱的设计 (15)3.9 弹簧的设计 (16)3.9.1 选择初始数据 (16)3.9.2 弹簧的校核 ............... (16)3.10 传感器的设计 (17)3.11 振动板的设计 (18)3.12 盖板设计 (19)3.12.1 校核盖板的刚度 (19)3.12.2 计算盖板的质量 (19)3.13 驱动盖板的电动机设计 (19)3.14 减速器的设计 (20)3.15 齿轮齿条的设计 (20)3.15.1 齿轮初步设计 (20)3.15.2 齿条的设计 (21)4 技术经济性分析 (22)5 总结与体会 (23)参考文献 (24)致谢 (25)1 绪论1.1 国外汽车检测技术发展状况A.制度化德国的汽车工业走在世界前列,汽车检测技术同样实力强劲,这得益于汽车检测各项技术的制度化,对汽车安全性以及环保性检测有一套行之有效的标准规范,各个汽车检测场都必须遵守这些标准规范以及规章制度,否则会受到严厉的处罚。
吉林大学汽车工程学院
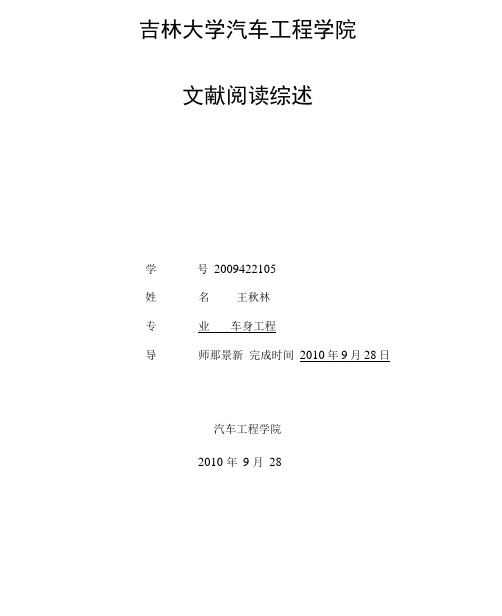
吉林大学汽车工程学院文献阅读综述学号2009422105姓名王秋林专业车身工程导师那景新完成时间2010年9月28日汽车工程学院2010 年9 月28一汽车被动安全性研究概述1汽车安全问题汽车安全、节能和环保问题已成为当今汽车工程领域三大具有重要社会、经济意义的研究热点,并且得到了有关政府部门的高度重视。
汽车安全性一般分为主动安全性、被动安全性、事故后安全性和生态安全性。
主动安全性,又称积极安全性,主要是指汽车防止或减少道路交通事故发生的性能;被动安全性,又称消极安全性,是指交通事故发生后,汽车减轻人员伤害程度或货物损失的能力。
由于汽车被动安全性总是与广义的汽车碰撞事故联系在一起,故又称为“汽车碰撞安全性”;事故后安全性是指汽车能否迅速消除事故后果、同时避免新的事故发生的性能;生态安全性是指发动机排气污染、汽车行驶噪声和电磁波等符合标准、不给环境造成危害的性能。
而习惯上我们把汽车的安全性简单理解为主动安全性和被动安全性两大类。
(1)主动安全性(Active Safety )所谓主动安全性是指在交通事故发生前米取的安全措施,这些措施应尽可能的避免交通事故的发生,是使汽车能够识别潜在的危险因素自动减速,或当突发因素作用时,能够在驾驶员的操纵下避免发生交通事故的性能。
目前,已发展成熟的主动安全性装置和技术主要包括:车轮防抱死制动系统(ABS)、牵引力控制系统(TCS)、主动悬架、四轮转向、四轮驱动、车距雷达报警系统和汽车全球定位导航系统(GPS)等。
但是,汽车主动安全性并不能完全预防大部分交通事故的发生,因此提高汽车本身在发生交通事故时保护乘员、行人免受或减轻伤亡的汽车被动安全性也是汽车安全研究的主要课题。
(2)被动安全性(Passive Safety )所谓被动安全性是指当汽车发生不可避免的交通事故后,能够对车内乘员或车外行人进行保护,以免发生伤害或使伤害减低到最低程度的性能。
汽车被动安全性研究着眼于如何合理地进行车身结构安全性设计,利用车身结构的变形尽可能地吸收能量以减少对乘员的冲击和防止车厢的变形。
上汽乘用车的研发之路专访上汽集团技术中心动力总成分析试验部总监、上海市汽车动力总成重点实验室主任徐政

Q:请您介绍一下上汽1.5T GDI汽油发动机的开发背景?A:先说一下联合开发的背景。
传统发动机和变速器的组合所构成的动力系统是车辆的核心部件,一直都是整车厂的核心技术,一般说来都是作为整车厂的核心技术自己掌握,从这一点讲,我们上汽从成立之初就意识到了这点——核心技术不能受制于人这个理念。
我们上汽从第一款车荣威750开始就搭载了我们自己的发动机。
那时我们收购了罗浮,我们最早的发动机就是从罗浮K系列发动机演变过来的发动机。
之后就开始了发动机的自主研发。
我们在2007年就已经开始了缸内直喷发动机的研发,当时开发的是自然吸气的2.0L 和2.4L发动机。
到了2010年左右的时候,国际上主流发动机的节能减排技术已经发展到具有明显的趋势性,这就是当时福特大规模量产的EcoBoost缸内直喷涡轮增压发动机,也就是发动机的增压与小型化的优势已经凸显出来,成为全球主机厂用来应对日趋严格的排放法规的良策。
同时用来满足市场消费者对追求动力需求与燃油消耗的最佳平衡。
所以各家主机厂都在研发小型化增压发动机。
上汽当时也是希望在发动机技术上实现自主品牌的技术突破,我们规划了从小排量发动机到中等排量的发动机研发规划。
Q:上汽与通用共同开发发动机的情况,上汽主要做了哪些开发内容?A:对于小排量发动机,我们也有这方面的需求,因为这已经成为主流的技术趋势,我们也要尊重这样的技术趋势,开发先进的发动机产品。
而通用汽车公司也是基于同样的技术趋势,需要在它的Ecotec发动机技术基础之上,开发出新一代Ecotec小排量涡轮增压发动机。
我们都有这样的需求,于是作为技术合作伙伴联合开发新一代小排量增压发动机,实现资源共享。
因为通用在北美、欧洲都有很大市场,在中国也有很大市场,这样一来,联合开发就更容易实现,形成了双方联合开发的意愿。
联合开发的模式是基于核心技术联合开发,知识产权全球共享。
我们的团队作为全球开发团队的一部分,参与了小排量涡轮增压发动机的开发。
车身稳定控制液压控制单元性能试验台开发与试验

汽车领域 的三 大核心 技术 : 发动机 控制技 术 、 动 传 控制技 术 以及 底盘 制 动 控制 技 术 。就 目前 而 言 , 些 这 领 域与 国外相 比, 国 尚存 在较 大差距 , 我 仍需要 深入 地
1 0
理论和产 业化研究 。车辆动 态稳定 控制 ( S ) 基 于 DC是
减压 , 防止 车轮抱 死 , 少压 力 波动 。E 减 H泵 将 蓄能 器
油液泵 回主缸 保 证 下 次 制 动正 常 ( B A S功 能 ) 当 然 , ; 即使无 踏板 力它也 能 实 现 自动 增 压 , 为提 供 车 身稳 定 控 制所 需要 的轮缸 压力 ( S D C功能 ) 。
机 构 , }能的好 坏 直接 决 定 了车辆 行 驶 安 全性 。 该 文从 产 业化 角度 对 H U基 础试 验 作 深入 地研 究与 分 苷生 C
析, 主要 涉及 H U的结构 、 C 各部件 典 型特征及 测试 方 法 ; 重点 讨论 H U研发 过程 和 实验 过程 中的 关键 技 术 , C
验 分析 。
2 HC U的 工作原 理
H U是底 盘制 动 中重要 的 执行 元 件 , C 它综 合 了机
械、 电子、 液压 、 控制 、 电磁等学科 , 是一个多学科交叉 的复杂精 密液压 系统 , 于 系统性工 程 J 属 。
液压工 作原 理 图如 图 l 示 。 所
5 2
尽 管制造 商生产 设计 的 H U结 构各有 千秋 , C 但都 包括 以下功 能部件 : 压 阀 、 增 减压 阀 、 限压 阀 、 吸油 阀、
E H泵 、 蓄能器 、 体 等 。常 规 D C阀 的 H U结 构 爆 本 S C
21 0 第 6期 1年
安全车身技术辑粹

I
l
、
由于精心设计 的犀部变形区
乘 客舱在 承 受 巨大; 击力 时也
能够 在很 太 程度 上保 持币 受损
坏
除 了螺 柱 紧圈式 尾郜 棒垃
组 台的铜 质 防撞 葙和 铝质 横 向
构 件 之外 还 包括 行 李箱 底板
区 域的 两 根坚 固 的纵 粱 和横 梁
在牡 生碰 撞时 后轿 的悬 槊副 车絮
也 构成 了能 量 吸收平 面
维普资讯
一
g a安 全车 身 o
很多 人认 为车 身铜 板越 厚越 碗 汽 车也 就越 安生
而丰
口的 G OA安 全 车 身则 是彻 底 否 定这 一 观念 的 例证 = G 0A
clbl u t dn ses  ̄4安 全车 身全 新引 ^ 刚 柔相 G a O ta i A ssm e sn g 济 最安全 的理 念
的坚 固车 身底 部结 构 8 根纵 粱
稳 固乘 客舱 的 主 匝铸铝和挤压型材构成的内部框架加固
4 根横 要 部 件包括 坚 国的 侧裙板
B 柱 车 身底部 了 车窗 框架 内侧 高强 度 锕加 强型 材在
柔和 3 分 通道加 强 件 在车 辆 发生 碰撞 的口裉 横粱 以及 仪表板 下 面的 坚固锕 构件 , 发 生侧 面碰 撞 时增 强 了保护 功 能 .车 门 部
在这 一理 念的指 导 下 丰 田汽 车 6 A车身设 计就 是 充丹 0 强化 汽车乘 具舱 部于 的 睁 性 抗 拉 性 全方位 } l和 发出 乘员 被动 保护 系统 如安 全带 高 水平 地开 而对 于经
安 全气 囊等
常可 能承 受碰 撞的 前保 险杠 和发动 机舱 部 分 则要 设计 出在
汽车被动安全性试验研究
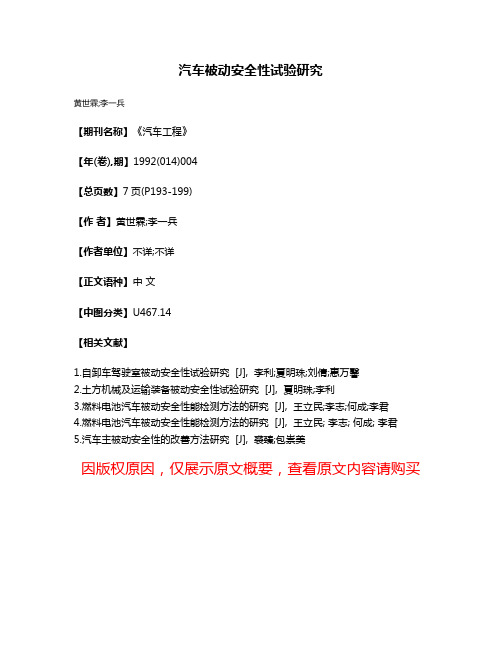
汽车被动安全性试验研究
黄世霖;李一兵
【期刊名称】《汽车工程》
【年(卷),期】1992(014)004
【总页数】7页(P193-199)
【作者】黄世霖;李一兵
【作者单位】不详;不详
【正文语种】中文
【中图分类】U467.14
【相关文献】
1.自卸车驾驶室被动安全性试验研究 [J], 李利;夏明珠;刘倩;惠万馨
2.土方机械及运输装备被动安全性试验研究 [J], 夏明珠;李利
3.燃料电池汽车被动安全性能检测方法的研究 [J], 王立民;李志;何成;李君
4.燃料电池汽车被动安全性能检测方法的研究 [J], 王立民; 李志; 何成; 李君
5.汽车主被动安全性的改善方法研究 [J], 裘臻;包崇美
因版权原因,仅展示原文概要,查看原文内容请购买。
整车模型被动悬架的建模与仿真分析_张海涛
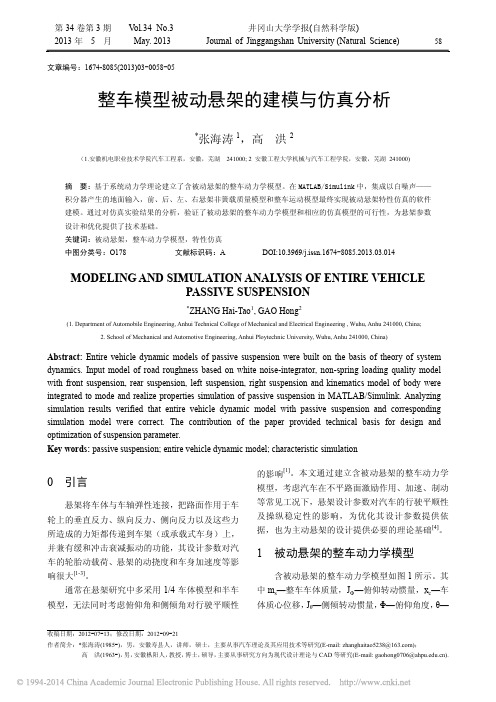
.. . .
..
.
.
xs1 xc b ( B a ) x x b a s2 c xs 3 xc ( L b) ( B a ) xs 4 xc ( L b) a
井冈山大学学报(自然科学版)
59
. . . .
侧倾角度,L—前后轴之间的距离,b—前轴到质心 的距离,B—汽车两轮之间的距离,a—汽车轮胎到 质心的距离,ks1—前左悬架弹簧刚度系数,cs1—前 左悬架减震器的阻尼系数,xt1—前左悬架非簧载质 量的位移, xr1— 前左轮胎地面的扰动输入位移,
J cs1 ( xs1 xt1 )( B a ) cs 2 ( xs 2 xt 2 ) a
Abstract: Entire vehicle dynamic models of passive suspension were built on the basis of theory of system dynamics. Input model of road roughness based on white noise-integrator, non-spring loading quality model with front suspension, rear suspension, left suspension, right suspension and kinematics model of body were integrated to mode and realize properties simulation of passive suspension in MATLAB/Simulink. Analyzing simulation results verified that entire vehicle dynamic model with passive suspension and corresponding simulation model were correct. The contribution of the paper provided technical basis for design and optimization of suspension parameter. Key words: passive suspension; entire vehicle dynamic model; characteristic simulation 的影响[1]。本文通过建立含被动悬架的整车动力学 模型,考虑汽车在不平路面激励作用、加速、制动 等常见工况下,悬架设计参数对汽车的行驶平顺性 及操纵稳定性的影响,为优化其设计参数提供依 据,也为主动悬架的设计提供必要的理论基础[4]。
- 1、下载文档前请自行甄别文档内容的完整性,平台不提供额外的编辑、内容补充、找答案等附加服务。
- 2、"仅部分预览"的文档,不可在线预览部分如存在完整性等问题,可反馈申请退款(可完整预览的文档不适用该条件!)。
- 3、如文档侵犯您的权益,请联系客服反馈,我们会尽快为您处理(人工客服工作时间:9:00-18:30)。
乘用车车身结构件被动安全性试验台的研制*徐兆坤1吴伟蔚1邓子兵1,2何稚华3(1上海工程技术大学汽车工程学院,上海201620)(2上海交通大学机械与动力工程学院,上海200240)(3上海大众汽车有限公司,上海201850)Research and development of passive safety test platform for the passenger vehiclebody in side impact crashes and rollover crashesXU Zhao-kun 1,WU Wei-wei 1,DENG Zi-bing 1,2,HE Zhi-hua 3(1Shanghai University of Engineering Science ,Shanghai 201620,China )(2Shanghai Jiaotong University ,Shanghai 200240,China )(3Shanghai Volkswagen ,Shanghai 201850,China )文章编号:1001-3997(2009)01-0124-03【摘要】试验台不仅能够测试汽车车身的强度、刚度以及抗撞性能,还可用于相当广泛的其他零部件的试验。
试验台不但能测试侧门强度,实时计算并显示平均力、最大力和被测汽车所吸收的能量,而且采用图像测量法精确测量车身刚度,以评价汽车安全性,为研发提供可靠详细的依据。
关键词:试验台;汽车安全性;摄影测量学【Abstract 】It can test not only vehicle body ,but also a broad range of automobile components.Thetest rig has a satisfying performance.In addition to measure and display the data of loading force and ab -sorbed energy in real time ,the device can also provide the information of deformation vector at some pre -defined points by using image processing algorithms.The data can be used in vehicle safety evaluation and in further studies.Key words :Test rig ;Vehicle safety ;Photogrammetry*来稿日期:2008-03-07*基金项目:上海市重点学科建设项目(T1405),并获中国汽车工业科技进步奖(06-04-01)中图分类号:TH16,TP23文献标识码:A1前言汽车碰撞安全性研究已成为汽车安全研究领域的重要内容。
目前,各国所进行的各种汽车碰撞试验主要是确定在碰撞过程中影响乘员生命安全的关键因素,包括车身刚度和强度[1,2]、碰撞过程中的碰撞能量等,其目的是提高碰撞过程中汽车对乘员的保护能力以及通过试验结果分析优化现行汽车安全法规[3],最终达到提高汽车碰撞的兼容性[4]。
根据乘用车碰撞规律研制了用于测试汽车车身及相关零部件(主要是侧门和车顶)的强度、刚度以及抗撞性能的车身结构件碰撞试验台,并且采用数字摄影视觉测量技术测量车身刚度(变形矢量)。
不仅可获得特征点的绝对变形矢量,而且也能获取不同特征点之间的相对变形量,以评价其安全性,为研发提供可靠详细的依据。
2试验台总体设计分别依据美国FMVSS 214和216试验标准确定试验台总体设计方案,如图1所示(加载器为半圆柱体,用于侧门测试情况,更换加载器可以用于车顶等其他部件的试验)。
加载器行程可达600mm ,撞击力可达100kN 。
试验台配置,如图1所示。
2.1加载系统即MTS Microconsole 458.X 控制器和Flex Test Ⅱ试验控制与管理及数据采集系统,MTS 公司液压伺服系统的压力源和液压促动器。
图1试验台总体方案2.2控制系统控制加载系统和数据采集与处理的动作及其同步(包括CCD 摄像机、同步继电器开关、同步闪光灯等)。
2.3数据采集与处理系统即视频采样数字化、压缩、图像分析、数据处理及结果输出等管理系统,控制摄像系统和照明系统。
3试验台关键技术3.1动力及控制系统由于车身,尤其侧门内部结构复杂,内有玻璃升降机构、门锁等,各处强度不一,因此,在撞击过程中,必将产生一个复杂的空Machinery Design &Manufacture机械设计与制造第1期2009年1月124间力系,包括:大小和方向难以确定的轴向力、剪力、弯矩和扭矩,分别作用于被测汽车和加载器上。
作为动力源的液压推柱,如图2所示。
只能承受轴向加载力F d。
根据轴向力平衡公式:F d=F f+F c(1)式中:F c—作用在汽车上的Y方向车身变形反力;F f—轴向摩擦力。
只有当F f→0,才能使F f≈F c,使测试数据较真实反映汽车实际撞击。
因此试验台必须设计一个导向支承装置,以吸收除轴向力以外的所有力、力矩,并且轴向摩擦力F f应尽可能小。
于是汽车在撞击的任意行程s或者任意时刻t所吸收的能量E c(s)为:E c(S)=S乙F c d s≈S0乙F d d s=f(S)(2)或者E c(t)=t乙F c U d t≈t0乙F d U d t=f(t)(3)式中:U—加载器的加载速度。
如图2所示,为试验台主台结构示意图,图中未显示动力源,加载器为车顶试验时所用。
图2试验台主台结构示意图因此加载系统在软件支持下,可实时采集、并在显示屏上显示撞击行程s或时刻t时撞击力F和汽车所吸收的能量E的曲线和数值。
如图3所示,3种车型试验参数,即F与S的变化曲线,如图4所示,3种车型试验过程第1阶段平均力1、第2阶段平均力2和最大力的实测值和标准值的对比。
其中车型1、2分别安装了防撞杆A、B,而车型3没有安装防撞杆。
图33种车型的实测位移S与撞击力F的变化曲线3.2试验台调整系统和刚度保证车身相对于促动器及加载器总成需要三维方向上的平动调整以及绕铅垂轴Z旋转可调,即四维可调自由度。
如果将积木式试验台系统设计成4个几何参数可调的话,不但制造工艺复杂、设备庞大、成本昂贵,而且可调装置刚度很难满足测试要求。
图43种车型的实测值和标准值的比较根据试验台的结构特点,以“不降低刚度、方便实施”为原则,以“需调节的方向与有刚度要求的方向相垂直”为手段将四维自由度分解。
例如,相对而言,主台(促动器及加载器总成等)绕Z轴可调较困难,而具有高度(Z向)可调的一维自由度较易实现,因此对总成中促动器进行Z方向的有级调节,而在加载器内部采用特殊结构,实现Z向(高度方向)无级微量调节,由此在结构上保证了无论有级调节还是无级调节均不影响台架的轴向刚度。
对于车顶试验,根据美国标准FMVSS571.216,平板相对于车顶前倾5°,侧倾25°,由于试验台为综合性试验台,故平板式加载器为铅垂面布置,因此车身必须做相应的调整和定位,车身的调整定位使用的装置,如图5所示。
车辆的底盘固定在调整定位装置的平面上,5个支架支点的移动可调整车身的侧倾和前倾。
图5车顶试验调节定位装置示意图3.3加载系统和图像采集系统的同步控制在进行汽车侧面碰撞试验时,加载系统与图像采集系统这两个系统既没有机械联系,也无电气或信号联系。
为了使完全独立的两个系统的测量结果相互对应,必须进行同步将它们联系在一起。
当液压系统的力传感器信号超过一定阈值,即认为加载头已与车身结构接触,这一时刻作为液压系统力传感器信号的记录起点,同时计算机控制系统发出信号,使闪光灯闪光,闪光灯形成的空白照片即可作为图像采集系统的记录起点。
通过这种方式使图像采集系统与液压加载的信号系统达到同步,有一个共同的起点,为后续的数据分析和处理打下基础。
3.4图像处理系统序列图像运动分析方法可以较为全面地记录整个试验的动态过程,有利于数据分析和处理。
本试验台综合人体工程学、力学原理以及车身制造工艺学等因素布置车身测点,并自主开发图像第1期徐兆坤等:乘用车车身结构件被动安全性试验台的研制*125处理系统软、硬件。
如图6所示,为系统构成,包括视频采样数字化、压缩、图像分析、数据处理及结果输出等管理系统,控制摄像系统和照明系统。
图6试验台图像处理系统图根据摄影测量的原理,一个点的空间坐标(X ,Y ,Z )与它在像平面上的坐标(u ,v )之间通过直接线性变换(DLT )联系在一起:u =L 1X +L 2Y +L 3Z +L 4L 9X +L 10Y +L 11Z +1(4)v =L 5X +L 6Y +L 7Z +L 8L 9X +L 10Y +L 11Z +1(5)其中的参数L 1到L 11反映了物方坐标系和像平面之间的相互关系。
这些参数应该在测量前的标定过程中确定,由于有11个未知数,而1个标定点只含有2个关系式,所以至少需要6个标定点的(X ,Y ,Z )和(u ,v )才能通过最小二乘法完成标定,即确定L 1到L 11。
考虑到光学误差等因素,DLT 变换有很多包含更多参数的修正变换,采用这些变换需要更多的标定点。
通过实测发现,DLT 的测试精度已能满足要求。
很显然一个像平面上的(u ,v )可以对应无数多个空间点的(X ,Y ,Z ),因此无法根据一张图片反求测量点的物方坐标。
所以应该布置2个或2个以上互相不平行的摄像机,这样对于一个测量点,就有(u 1,v 1)、(u 2,v 2)甚至更多的像坐标,代入上面的公式使用最小二乘法就可以解出测量点的物方坐标(X ,Y ,Z )。
计算测量点的一系列物方坐标就获得了这个点的变形轨迹。
使用图像处理系统实现车身标识点的三维测量过程[5],如图7所示。
图7三维测量实现过程布置两台摄像机同时从两个不同方向对目标进行摄像;通过视频文件格式的解析,实现图像帧的提取,然后应用数字图像处理算法对图像帧进行灰度化。
由于在汽车碰撞试验中灯光效果和周围台架设备等因素的影响,使得图像背景比较复杂,采用单一的图像处理算法很难对车身标识点进行识别和提取。
本试验台采用帧差分[6]以及彩色图像分割等算法,实现车身标识点的提取,并且利用目标的相关性[7],跟踪和定位序列图像中的标识点,即提高处理效率,又提高了识别的精度。
为了解决同名点的匹配问题,试验台的车身标识点采用编码标志[7]的方法,实现同名点的自动匹配,提高了测量的自动化操作。
实现的图像三维测量法精确测量车身刚度(变形矢量),即任意时刻特征点的三维坐标。