冷压(冷镦冷挤)加工
冷镦挤压成型工艺

冷镦挤压成型工艺简介冷镦挤压成型工艺是一种常用的金属加工技术,通过将金属材料置于镦头和模具之间,施加高压力并应用冷加工原理使材料在有限空间内变形,从而实现所需的形状和尺寸。
本文将介绍冷镦挤压成型工艺的原理、主要应用领域以及一些注意事项。
工艺原理冷镦挤压成型工艺主要通过镦头和模具对金属材料施加高压力来实现金属的塑性变形。
镦头和模具的形状和尺寸可以根据需要进行设计。
一般来说,镦头上有一个凸起的部分,即挤压面或挤出口,而模具中有一个配合的凹槽。
在挤压过程中,金属材料被挤压进模具中,经过塑性变形后得到所需的形状。
冷镦挤压成型工艺采用冷加工原理,即在常温下进行。
相较于热镦挤压,冷镦挤压不需要将材料加热至较高温度,因此能够节约能源并提高生产效率。
此外,冷镦挤压还能够改善金属材料的强度和硬度,提高产品的精度和表面质量。
应用领域冷镦挤压成型工艺广泛应用于各个行业和领域,特别是在汽车、航空航天、家电、建筑、电子等领域中。
下面介绍一些典型的应用场景:螺栓和螺母螺栓和螺母是冷镦挤压成型工艺的常见应用之一。
通过冷镦挤压,能够将原材料材料经过挤压、滚压等工艺进行成型,最终得到需要的螺纹形状,提高了产品的强度和耐久性。
零件组件冷镦挤压还可用于制造各种零件和组件,如汽车发动机零件、电动工具零件、自行车零件等。
通过冷镦挤压工艺,可以实现对材料形状和尺寸的精确控制,从而满足产品的功能和美观要求。
金属管材冷镦挤压也可以用于制造金属管材。
通过挤压变形,能够提高金属管材的强度和硬度,同时改善内外表面的光洁度和精度,提高管材的使用性能。
注意事项在进行冷镦挤压成型工艺时,需要注意以下几点:1.材料选择:合理选择适合冷镦挤压的金属材料,如低碳钢、不锈钢、黄铜等。
不同材料的挤压性能不同,需要根据产品的要求进行选择。
2.模具设计:模具的设计必须充分考虑产品的形状和尺寸,并结合材料的性能特点进行合理设计。
模具的质量直接影响到产品的质量和成形效果。
冷镦成型工艺

紧固件冷镦成型工艺紧固件成型工艺中,冷镦(挤)技术是一种主要加工工艺。
冷镦(挤)属于金属压力加工范畴。
在生产中,在常温状态下,对金属施加外力,使金属在预定的模具内成形,这种方法通常叫冷镦.实际上,任何紧固件的成形,不单是冷镦一种变形方式能实现的,它在冷镦过程中,除了镦粗变形外,还伴随有正、反挤压、复合挤压、冲切、辗压等多种变形方式。
因此,生产中对冷镦的叫法,只是一种习惯性叫法,更确切地说,应该叫做冷镦(挤).冷镦(挤)的优点很多,它适用于紧固件的大批量生产.它的主要优点概括为以下几个方面: a.钢材利用率高.冷镦(挤)是一种少、无切削加工方法,如加工杆类的六角头螺栓、圆柱头内六角螺钉,采用切削加工方法,钢材利用率仅在25%~35%,而用冷镦(挤)方法,它的利用率可高达85%~95%,仅是料头、料尾及切六角头边的一些工艺消耗。
b.生产率高。
与通用的切削加工相比,冷镦(挤)成型效率要高出几十倍以上。
c.机械性能好.冷镦(挤)方法加工的零件,由于金属纤维未被切断,因此强度要比切削加工的优越得多.d.适于自动化生产。
适宜冷镦(挤)方法生产的紧固件(也含一部分异形件),基本属于对称性零件,适合采用高速自动冷镦机生产,也是大批量生产的主要方法。
总之,冷镦(挤)方法加工紧固件、异形件是一种综合经济效益相当高的加工方法,是紧固件行业中普遍采用的加工方法,也是一种在国内、外广为利用、很有发展的先进加工方法。
因此,如何充分利用、提高金属的塑性、掌握金属塑性变形的机理、研制出科学合理的紧固件冷镦(挤)加工工艺,是本章的目的和宗旨所在。
1 金属变形的基本概念1.1变形变形是指金属受力(外力、内力)时,在保持自己完整性的条件下,组成本身的细小微粒的相对位移的总和。
1。
1.1 变形的种类a.弹性变形金属受外力作用发生了变形,当外力去掉后,恢复原来形状和尺寸的能力,这种变形称为弹性变形.弹性的好坏是通过弹性极限、比例极限来衡量的。
冷镦挤变形工艺冷镦工艺与模具设计

ε =(H0-H1)/H0×100% 式中 H0 —圆柱形试样原始高度;
H1 —试样压缩后在侧表面出现第一条肉眼可见的裂纹时的 试样高度;
变形抗力 (N/mm2)
形过程中,随着变形的增大,由于冷作硬化 作用使金属的硬度和强度随之增大,
电工纯铁
变形抗力也大大增加,而塑性却有所降
低,这将给后道工序带来变形的困难。
金属材料冷作硬化后实际变形抗力如 图1.1-1所示
变形程度 ε(%)
图1.1-1
材料的含碳量越高,其变形抗力越大。所以,在冷加工过程中需适当增加 中间热处理工序,以消除冷作硬化和内应力。否则,继续冷镦加工将是困 难的。
对冷镦用钢的要求: 力学性能的要求 化学成分的要求
金相组织的要求— 一般认为1~4级为粗晶粒,5~8为细晶粒。粗晶粒
材料的冷作硬化敏感性比细晶粒的要大,塑性比细晶粒的要差,适合 冷镦晶粒度以4、5、6级为宜。 材料表面质量的要求 — 钢材表面的缺陷 、表面脱碳。 尺寸精度要求 表面润滑要求
冷镦材料的改制过程
δ= (L1-L0)/L0×100%
式中 L0 — 拉伸试样原始标距长度; L1 —拉伸试样破断后标距长度;
Ψ=(A0-A1)/A0×100%
式中 Ao — 拉伸试样原始截面积; A1 —拉伸试样破断处的截面积;
因此,伸长率和断面收缩率数值越大,表示塑性越好。良 好的塑性材料,有利于进行断压、冷冲、冷镦锻和冷拉拔等成 型工艺。 原则上说,这两个塑性指标,都只能表示材料在单向拉伸条件 下的塑性变形能力。
冷镦机工作原理
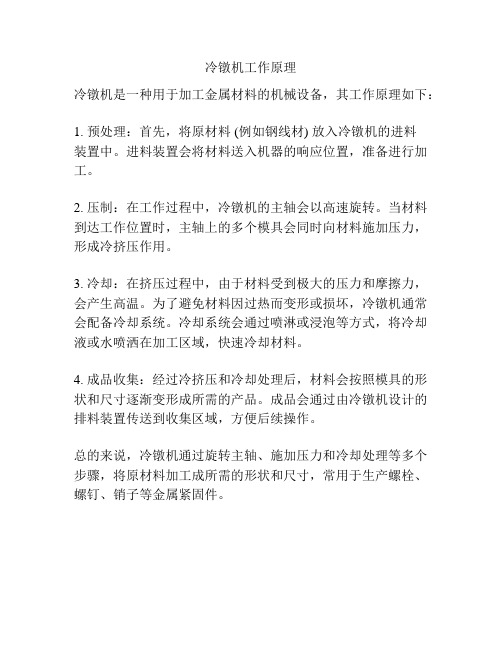
冷镦机工作原理
冷镦机是一种用于加工金属材料的机械设备,其工作原理如下:
1. 预处理:首先,将原材料 (例如钢线材) 放入冷镦机的进料
装置中。
进料装置会将材料送入机器的响应位置,准备进行加工。
2. 压制:在工作过程中,冷镦机的主轴会以高速旋转。
当材料到达工作位置时,主轴上的多个模具会同时向材料施加压力,形成冷挤压作用。
3. 冷却:在挤压过程中,由于材料受到极大的压力和摩擦力,会产生高温。
为了避免材料因过热而变形或损坏,冷镦机通常会配备冷却系统。
冷却系统会通过喷淋或浸泡等方式,将冷却液或水喷洒在加工区域,快速冷却材料。
4. 成品收集:经过冷挤压和冷却处理后,材料会按照模具的形状和尺寸逐渐变形成所需的产品。
成品会通过由冷镦机设计的排料装置传送到收集区域,方便后续操作。
总的来说,冷镦机通过旋转主轴、施加压力和冷却处理等多个步骤,将原材料加工成所需的形状和尺寸,常用于生产螺栓、螺钉、销子等金属紧固件。
冷挤压和冷锻简介

冷镦、冷挤压基础知识介绍发布日期:2007-03-16 浏览次数:54冷挤压是精密塑性体积成形技术中的一个重要组成部分。
冷挤压是指在冷态下将金属毛坯放入模具模腔内,在强大的压力和一定的速度作用下,迫使金属从模腔中挤出,从而获得所需形状、尺寸以及具有一定力学性能的挤压件。
显然,冷挤压加工是靠模具来控制金属流动,靠金属体积的大量转移来成形零件的。
冷挤压技术是一种高精、高效、优质低耗的先进生产工艺技术,较多应用于中小型锻件规模化生产中。
与热锻、温锻工艺相比,可以节材30%~50%,节能40%~80%而且能够提高锻件质量,改善作业环境。
目前,冷挤压技术已在紧固件、机械、仪表、电器、轻工、宇航、船舶、军工等工业部门中得到较为广泛的应用,已成为金属塑性体积成形技术中不可缺少的重要加工手段之一。
二战后,冷挤压技术在国外工业发达国家的汽车、摩托车、家用电器等行业得到了广泛的发展应用,而新型挤压材料、模具新钢种和大吨位压力机的出现便拓展了其发展空间。
日本80年代自称,其轿车生产中以锻造工艺方法生产的零件,有30%~40%是采用冷挤压工艺生产的。
随着科技的进步和汽车、摩托车、家用电器等行业对产品技术要求的不断提高,冷挤压生产工艺技术己逐渐成为中小锻件精化生产的发展方向。
与其他加工工艺相比冷挤压有如下优点:1)节约原材料。
冷挤压是利用金属的塑性变形来制成所需形状的零件,因而能大量减少切削加工,提高材料利用率。
冷挤压的材料利用率一般可达到80%以上。
2)提高劳动生产率。
用冷挤压工艺代替切削加工制造零件,能使生产率提高几倍、几十倍、甚至上百倍。
3)制件可以获得理想的表面粗糙度和尺寸精度。
零件的精度可达IT7~IT8级,表面粗糙度可达R0.2~R0.6。
因此,用冷挤压加工的零件一般很少再切削加工,只需在要求特别高之处进行精磨。
4)提高零件的力学性能。
冷挤压后金属的冷加工硬化,以及在零件内部形成合理的纤维流线分布,使零件的强度远高于原材料的强度。
冷镦基础知识和工艺分析
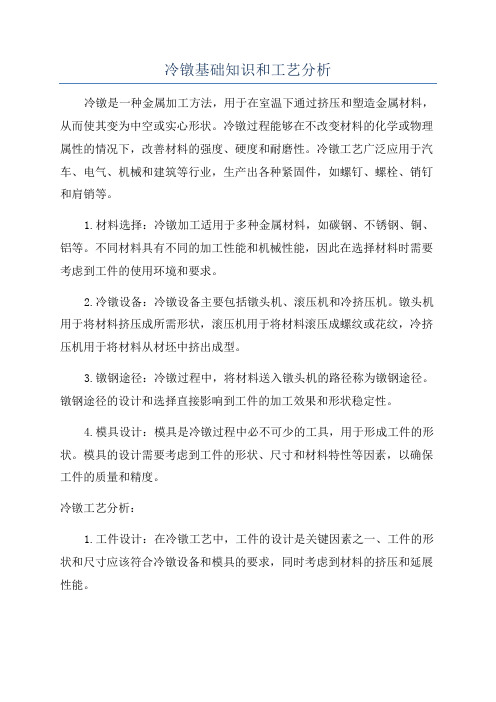
冷镦基础知识和工艺分析冷镦是一种金属加工方法,用于在室温下通过挤压和塑造金属材料,从而使其变为中空或实心形状。
冷镦过程能够在不改变材料的化学或物理属性的情况下,改善材料的强度、硬度和耐磨性。
冷镦工艺广泛应用于汽车、电气、机械和建筑等行业,生产出各种紧固件,如螺钉、螺栓、销钉和肩销等。
1.材料选择:冷镦加工适用于多种金属材料,如碳钢、不锈钢、铜、铝等。
不同材料具有不同的加工性能和机械性能,因此在选择材料时需要考虑到工件的使用环境和要求。
2.冷镦设备:冷镦设备主要包括镦头机、滚压机和冷挤压机。
镦头机用于将材料挤压成所需形状,滚压机用于将材料滚压成螺纹或花纹,冷挤压机用于将材料从材坯中挤出成型。
3.镦钢途径:冷镦过程中,将材料送入镦头机的路径称为镦钢途径。
镦钢途径的设计和选择直接影响到工件的加工效果和形状稳定性。
4.模具设计:模具是冷镦过程中必不可少的工具,用于形成工件的形状。
模具的设计需要考虑到工件的形状、尺寸和材料特性等因素,以确保工件的质量和精度。
冷镦工艺分析:1.工件设计:在冷镦工艺中,工件的设计是关键因素之一、工件的形状和尺寸应该符合冷镦设备和模具的要求,同时考虑到材料的挤压和延展性能。
2.材料预处理:在冷镦加工之前,材料需要进行一些预处理,如清洗、除油和退火等。
这些处理可以减少材料的不均匀性、气泡和应力,提高加工的稳定性和表面质量。
3.加热处理:一些情况下,冷镦工艺需要在加热状态下进行,以提高材料的延展性和塑性。
加热温度和时间的选择需要考虑到材料的特性和工艺要求。
4.加工参数:冷镦过程中的加工参数包括挤压速度、压力和润滑剂的选择等。
这些参数的选择需要经验和试验,以确保加工的稳定性和工件的质量。
5.表面处理:冷镦工艺后,工件的表面需要进行一些处理,如退火、焊接、镀锌等。
这些处理可以进一步改善工件的力学性能和抗腐蚀性能。
总结:冷镦是一种常见的金属加工方法,通过挤压和塑造金属材料,制造出各种紧固件和零部件。
冷镦滚子凸模的冷挤压工艺
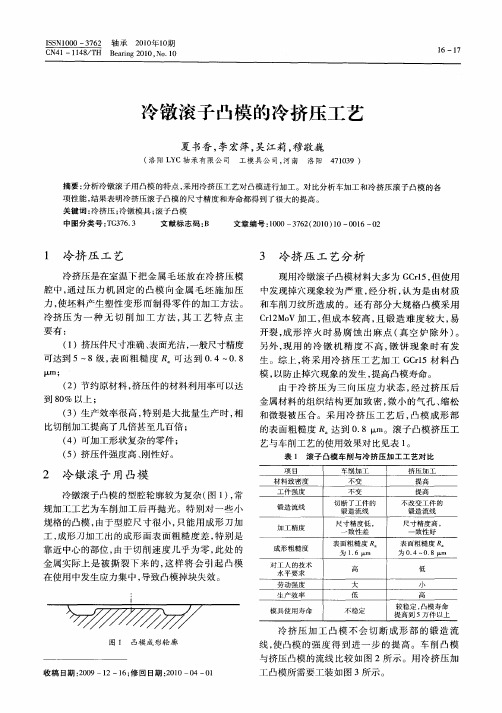
线 , 凸模 的 强 度 得 到 进 一 步 的 提 高 。 车 削 凸模 使 与挤压 凸模 的流线 比较 如 图 2所 示 。用 冷挤 压 加
工 凸模 所需 要工 装如 图 3所示 。
收 稿 日期 :0 9—1 20 2—1 ; 回 日期 :0 0— 4— 1 6修 2 1 0 0
一
( )节 约原材 料 , 压件 的材 料利 用率 可 以达 2 挤
到 8 % 以上 ; 0
( )生 产效 率很 高 , 别 是 大 批 量 生产 时 , 3 特 相 和微 裂被 压 合 。采 用 冷 挤 压 工 艺 后 , 模 成 形 部 凸 比切削加 工 提高 了几倍 甚 至几 百倍 ; ( )可 加工形 状 复杂 的零 件 ; 4
力 , 坯料 产生 塑性 变 形 而 制 得零 件 的加 工 方法 。 使
和车削 刀纹所 造 成 的 。还 有 部 分 大规 格削 加 工 方 法 , 工 艺 特 点 主 ClMo 其 r2 V加 工 , 成 本 较 高 , 锻 造 难 度 较 大 , 但 且 易 要有 : 开裂 , 形 淬 火 时 易 腐 蚀 出 麻 点 ( 空 炉 除 外 ) 成 真 。
规 加工工 艺 为车 削加 工 后 再 抛 光 。特 别 对 一些 小
规 格 的凸模 , 由于型 腔 尺 寸很 小 , 只能 用 成 形 刀加
工, 成形 刀加 工 出的成 形 面表 面 粗 糙 度差 , 特别 是
靠 近 中心 的部 位 , 由于 切 削速 度 几 乎 为零 , 处 的 此 金 属实 际上 是 被 撕 裂 下 来 的 , 样 将 会 引 起 凸模 这
1 冷挤 压 工 艺
冷挤压 是在 室 温下 把 金 属 毛 坯 放在 冷 挤 压 模 腔中, 通过 压 力 机 固定 的 凸模 向金 属 毛 坯 施 加 压
冷镦工艺技术

冷镦工艺技术冷镦工艺技术又称为冷挤压工艺技术,是利用金属材料的可塑性,在冷态下通过金属变形的手段,将金属材料压缩成扁平形状的工艺。
这一技术的主要应用领域包括汽车、机械制造、航空航天等行业,其特点是高效、节能、精度高。
冷镦工艺技术的原理是通过将金属材料放入模具中,利用冷压工艺使其在规定的温度和压力下完成变形。
这一工艺可以使金属材料在不改变化学性质的情况下获得所需的形状和尺寸。
冷镦工艺技术通常包括冷镦成型、冷镦切断、冷镦卷曲等过程。
冷镦成型是指将金属材料通过冷挤压的方式压缩成规定的形状和尺寸。
在冷挤压过程中,金属材料的分子结构会发生变化,使其具有更好的力学性能和表面质量。
冷镦成型的主要特点是:工艺简单、生产效率高、不需要后加工、产品质量稳定。
冷镦切断是指将冷镦后的产品进行切割,使其达到所需的长度和形状。
冷镦切断一般采用剪切的方式进行,剪切刀具会将冷镦后的产品切割成所需的尺寸。
冷镦切断具有高效、精确的特点,不会产生碎屑等废料。
冷镦卷曲是指将冷镦后的产品进行卷曲成所需的形状。
冷镦卷曲通常使用卷曲机进行,将产品放入卷曲机的模具中,通过压力和转动将产品卷曲成所需的形状。
冷镦卷曲的特点是:卷曲成型快速、精准度高、不会损坏产品的化学性质。
冷镦工艺技术的优势主要有以下几个方面:一是生产效率高。
冷镦工艺技术可以实现连续生产,不需要经过冷却和加热等步骤,从而提高生产效率。
二是能耗低。
冷镦工艺技术不需要进行加热处理,可以减少能源的消耗。
三是产品质量稳定。
冷镦工艺技术可以获得高精度的产品,减少产品的缺陷和变形。
四是操作简便。
冷镦工艺技术不需要复杂的设备和工艺,操作简便。
总之,冷镦工艺技术是一种高效、节能、精度高的金属加工技术。
作为金属加工的主要方法之一,冷镦工艺技术在汽车、机械制造等行业具有广泛的应用前景。
通过持续的技术创新和工艺改进,冷镦工艺技术将为各行各业的发展提供更好的支持。
冷镦工艺介绍

冷镦工艺介绍
冷镦是一种金属成形加工技术,也称为冷挤压。
它是一种通过加压来改变金属截面形状的方法,通常应用于制造螺栓、螺钉、螺母和其他紧固件等产品。
冷镦工艺的主要过程包括:
1. 材料准备:选择适当的金属材料,并进行表面处理,以确保其表面平整和清洁。
2. 冷挤压:将金属材料放到冷挤压机中,通过挤压头施加压力,在压力的作用下,金属材料被压缩,经过变形和扭曲,最终形成所需的形状。
3. 冷拉伸:在冷挤压完成后,金属材料经过冷拉伸以进一步增加其强度。
4. 切割:将冷挤压成型的金属材料切割成所需的长度。
冷镦工艺具有高效、精度高、成本低的优点。
与传统的热镦和锻造技术相比,冷镦技术不需要加热金属材料,因此能够减少能源消耗和环境污染。
此外,冷镦还可以在生产过程中避免金属材料的氧化和退火现象,从而提高了制品质量和性能。
总之,冷镦工艺是一种重要的金属成形加工技术,广泛应用于各种工业领域,特别是在紧固件制造领域。
- 1 -。
冷镦和冷挤压

冷镦和冷挤压冷镦与冷挤压基本上是同样条件的变形加工,但在操作方式上是不一样的。
冷墩属于较小型工件的锻造变形,常用于紧固件工业。
而冷挤压则属于较大型工件的挤压变形,用途较广泛。
01什么是冷挤压冷挤压就是把金属毛坯放在冷挤压模腔中,在室温下,通过压力机上固定的凸模向毛坯施加压力,使金属毛坯产生塑性变形而制得零件的加工方法,显然,冷挤压加工是靠模具来控制金属流动,靠金属体积的大量转移来成形零件的。
在挤压设备方面,我国已具备设计和制造各级吨位挤压压力机的能力。
除采用通用机械压力机、液压机、冷挤压力机外,还成功地采用摩擦压力机与高速高能设备进行冷挤压生产。
如果毛坯不经加热就进行挤压,便称为冷挤压。
冷挤压是无切屑、少切屑零件加工工艺之一,所以是金屑塑性加工中一种先进的工艺方法。
如果将毛坯加热到再结晶温度以下的温度进行挤压,便称为温挤压。
温挤压仍具有少无切屑的优点。
冷挤压技术是一种高精、高效、优质低耗的先进生产工艺技术,较多应用于中小型锻件规模化生产中。
与热锻、温锻工艺相比,可以节材30%~50%,节能40%~80%而且能够提高锻件质量,改善作业环境。
目前,冷挤压技术已在紧固件、机械、仪表、电器、轻工、宇航、船舶、军工等工业部门中得到较为广泛的应用,已成为金属塑性体积成形技术中不可缺少的重要加工手段之一。
随着科技的进步和汽车、摩托车、家用电器等行业对产品技术要求的不断提高,冷挤压生产工艺技术己逐渐成为中小锻件精化生产的发展方向。
冷挤压还分正挤压、反挤压、复合挤压、径向挤压等。
02什么是冷镦冷镦工艺是少无切削金属压力加工新工艺之一。
它是一种利用金属在外力作用下所产生的塑性变形,并借助于模具,使金属体积作重新分布及转移,从而形成所需要的零件或毛坯的加工方法。
冷镦工艺最适于用来生产螺栓、螺钉、螺母、铆钉、销钉等标准紧固件。
冷镦工艺常用的设备为专用的冷镦机。
如生产量不太大,也可以用曲柄压力机或摩擦压力机代替。
冷镦工艺由于具有高的生产率,良好的产品质量,并大大减少材料消耗,降低生产成本,改善劳动条件,因此愈来愈广泛地应用在机械制造特别是标准紧固件的生产中,其中应用多工位冷镦机生产的最有代表性的产品,是螺栓、螺钉和螺母。
冷压工艺流程

冷压工艺流程冷压工艺是一种常用的成型工艺,适用于生产各种零部件和产品。
它的工艺流程可以分为准备工作、材料准备、冷镦造型、表面处理和成品检验等几个过程。
首先是准备工作。
在冷压工艺开始之前,需要清洗和准备加工设备和工具。
同时,还需要检查工艺流程和图纸,确保工艺参数和尺寸等是准确无误的。
此外,还需要准备好相应的辅助设备和工装,以便后续的生产使用。
其次是材料准备。
冷压工艺所使用的材料一般是金属材料,如钢、铝、铜等。
在材料准备过程中,首先需要对材料进行切割,按照所需的尺寸进行切割。
然后,还需要对材料进行预处理,以便提高材料的可塑性和加工性能。
预处理的方法可以是热处理、退火或冷却等。
接下来是冷镦造型。
冷镦造型是冷压工艺的核心步骤,也是最关键的一步。
在这一步骤中,需要将材料放入冷镦机中,并通过机械力的作用,将材料进行冷压成型。
冷镦造型的目的是将材料压制成所需的形状和尺寸。
这一步骤需要根据产品的要求和工艺参数来调整冷镦机的压力和速度等参数,以确保产品的质量和精度。
完成冷镦造型后,还需要进行表面处理。
表面处理是为了提高产品的表面质量和防止氧化腐蚀。
常用的表面处理方法有电镀、热处理、喷涂和涂层等。
这些方法可以改善产品的表面光洁度、耐腐蚀性和装饰性。
最后是成品检验。
成品检验是冷压工艺中必不可少的一步,它用于检查产品是否符合要求和标准。
成品检验的项目包括尺寸、形状、表面质量、力学性能等。
通过成品检验可以确保产品的质量和性能达到标准要求,并及时发现和解决可能存在的问题。
总之,冷压工艺是一种重要而常用的成型工艺,它适用于生产各种产品和零部件。
工艺流程包括准备工作、材料准备、冷镦造型、表面处理和成品检验等几个过程。
这些过程的严谨和规范性对于保证产品质量和性能至关重要。
冷压工艺的应用可以提高生产效率、降低生产成本,并且可以生产出高质量的产品。
日本冷间锻造之基础冷锻冷挤压冷镦基础知课件

模具设计要点
根据产品要求和材料特性,设计 合理的模具结构;选择合适的材 料和热处理工艺,提高模具寿命 和精度;考虑润滑条件,合理设
置润滑槽和孔等。
03
冷挤压工艺基础
冷挤压的定义与分类
冷挤压
在室温下,借助压力机的压力,将变形抗力较大且质地较硬 的金属材料通过模具加工成所需形状的零件的塑性加工方法。
冷镦加工要控制好变形量、变形温度和变形速度等参数。
后处理包括去除表面毛刺、修整尺寸和进行表面处理等。
冷镦变形机制与控制
冷镦变形机制
在冷镦过程中,金属坯料在模具中受到压力的作用,产生塑性变形,从而获得所需形状的零件。变形 主要发生在坯料的表层,内部则保持不变。
冷镦变形控制
为了获得高质量的零件,需要对冷镦变形过程进行控制。控制的主要参数包括变形量、变形温度和变 形速度等。通过对这些参数的调整,可以控制金属的流动、应力分布和晶粒细化等过程,从而获得高 精度、高强度和高耐腐蚀性的零件。
模具选用
根据产品类型、材料、精度要求等选择合适的模具。
要点二
工具维护
定期检查工具磨损情况,及时更换磨损件,保持工具 清洁。
典型案例分析
案例一
某机械压力机在生产过程中出现故障, 经过检查发现是机械传动部分磨损导致, 经过维修后恢复正常。
VS
案例二
某液压机在锻造过程中出现漏油现象,经 过检查发现是密封件损坏导致,更换密封 件后恢复正常。
越来越广泛。
本课程旨在介绍日本冷间锻造的 基础知识,为学习者打下坚实的
基础。
课程概述
课程将涵盖冷锻、冷挤压、冷 镦等基础知识的讲解和实际操 作演示。
学习者将了解冷间锻造的基本 原理、工艺流程、材料选择、 模具设计等方面的知识。
名词解释冷加工

名词解释冷加工
冷加工是一种金属加工工艺,它不需要使用热量,而是通过冷却来改变金属的
形状和性能。
它可以改变金属的形状,使其具有更好的性能,从而满足特定的应用要求。
冷加工的主要方法有冷拔、冷压、冷挤压、冷拉伸、冷滚压、冷粘合等。
冷拔
是指将金属材料拉伸成细长的形状,以改变其形状和性能;冷压是指将金属材料压缩成更小的尺寸,以改变其形状和性能;冷挤压是指将金属材料挤压成更小的尺寸,以改变其形状和性能;冷拉伸是指将金属材料拉伸成更长的尺寸,以改变其形状和性能;冷滚压是指将金属材料滚压成更小的尺寸,以改变其形状和性能;冷粘合是指将金属材料粘合在一起,以改变其形状和性能。
冷加工的优点是可以改变金属的形状和性能,从而满足特定的应用要求,而且
不需要使用热量,可以节省能源。
另外,冷加工还可以改善金属的结构,提高金属的强度和耐磨性,从而提高金属的使用寿命。
总之,冷加工是一种金属加工工艺,它可以改变金属的形状和性能,从而满足
特定的应用要求,而且不需要使用热量,可以节省能源,改善金属的结构,提高金属的强度和耐磨性,从而提高金属的使用寿命。
冷镦挤压成型工艺

冷镦挤压成型工艺冷镦挤压成型工艺是一种常见的金属加工方法,主要用于生产各种螺纹和复杂形状的零件。
相较于其他成型工艺,冷镦挤压具有高效、快速、精密等特点,因此在工业生产中被广泛应用。
首先,冷镦挤压工艺需要一台冷镦挤压机。
该机器由一对相互作用的滚轮组成,将金属工件放置在两个滚轮之间进行轴向挤压。
通过调整滚轮的位置和形状,可以实现对工件的不同形状和尺寸的加工。
其次,在具体的工艺过程中,首先将原料金属切割成合适长度。
然后将金属工件放置在冷镦挤压机的进料装置上,通过驱动装置将工件送入挤压机的滚轮区域。
滚轮以高速旋转,对金属工件进行挤压变形。
在挤压过程中,由于工件的镦头被滚轮挤压,金属会沿轴向流动,形成所需的形状。
这个过程中会释放出大量的热量,为了避免过热,需要应用切削液或者冷却装置来冷却工件和滚轮。
同时,适当的润滑剂也需要应用在滚轮表面,以减少摩擦力和磨损。
最后,完成挤压后的工件需要进行后续加工。
通常会进行修整、退火和表面处理等步骤,以达到所需的尺寸、硬度和外观要求。
冷镦挤压成型工艺具有多种优点。
首先,与热镦挤压相比,冷镦挤压不需要加热和冷却的时间,节省了生产时间和能源消耗。
其次,冷镦挤压可以制造出精密的螺纹和零件,尺寸精度高,形状复杂。
此外,冷镦挤压还可以大量生产相同或不同尺寸和形状的工件,提高了生产效率和产品的一致性。
总之,冷镦挤压成型工艺是一种高效、快速、精密的金属加工方法,广泛应用于各个工业领域。
它不仅可以满足不同形状和尺寸的零件需求,还可以提高生产效率和产品质量。
随着科技的不断进步,冷镦挤压工艺将会不断发展和改进,为工业生产带来更多的便利和效益。
冷镦挤压成型工艺是一种常见的金属加工方法,主要用于生产各种螺纹和复杂形状的零件。
相较于其他成型工艺,冷镦挤压具有高效、快速、精密等特点,因此在工业生产中被广泛应用。
冷镦挤压工艺的应用范围非常广泛,适用于包括汽车、电子、航空航天、建筑等行业中的很多产品制造。
冷挤压加工的技术要求
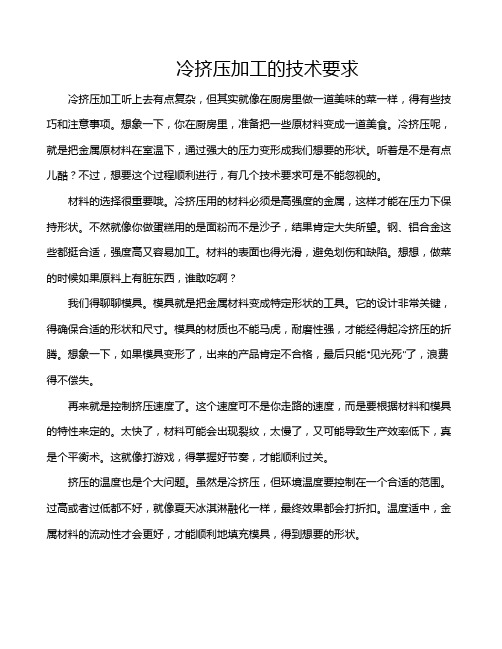
冷挤压加工的技术要求冷挤压加工听上去有点复杂,但其实就像在厨房里做一道美味的菜一样,得有些技巧和注意事项。
想象一下,你在厨房里,准备把一些原材料变成一道美食。
冷挤压呢,就是把金属原材料在室温下,通过强大的压力变形成我们想要的形状。
听着是不是有点儿酷?不过,想要这个过程顺利进行,有几个技术要求可是不能忽视的。
材料的选择很重要哦。
冷挤压用的材料必须是高强度的金属,这样才能在压力下保持形状。
不然就像你做蛋糕用的是面粉而不是沙子,结果肯定大失所望。
钢、铝合金这些都挺合适,强度高又容易加工。
材料的表面也得光滑,避免划伤和缺陷。
想想,做菜的时候如果原料上有脏东西,谁敢吃啊?我们得聊聊模具。
模具就是把金属材料变成特定形状的工具。
它的设计非常关键,得确保合适的形状和尺寸。
模具的材质也不能马虎,耐磨性强,才能经得起冷挤压的折腾。
想象一下,如果模具变形了,出来的产品肯定不合格,最后只能“见光死”了,浪费得不偿失。
再来就是控制挤压速度了。
这个速度可不是你走路的速度,而是要根据材料和模具的特性来定的。
太快了,材料可能会出现裂纹,太慢了,又可能导致生产效率低下,真是个平衡术。
这就像打游戏,得掌握好节奏,才能顺利过关。
挤压的温度也是个大问题。
虽然是冷挤压,但环境温度要控制在一个合适的范围。
过高或者过低都不好,就像夏天冰淇淋融化一样,最终效果都会打折扣。
温度适中,金属材料的流动性才会更好,才能顺利地填充模具,得到想要的形状。
在整个冷挤压的过程中,润滑剂的使用也不能忽视。
它就像做菜时的油,能够减少摩擦,保护模具。
没有润滑剂,材料在挤压时容易产生划痕,甚至损坏模具。
使用合适的润滑剂,不仅能提高产品质量,还能延长模具的使用寿命,真是一举两得。
再说说质量检测。
冷挤压的产品一旦生产出来,得经过严格的检验。
要确保每个产品都符合标准,不能有瑕疵。
就像我们吃东西得看新鲜度一样,产品的质量关乎安全,绝不能马虎。
如果发现有问题,得及时调整生产工艺,确保下次不出错。
冷墩工艺成本计算表
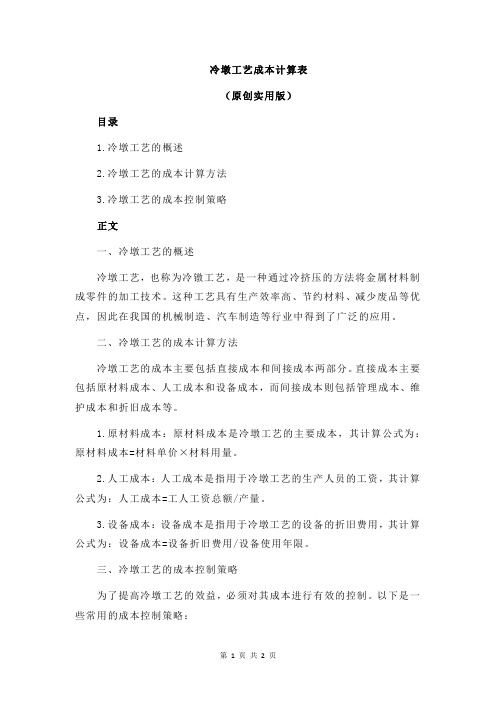
冷墩工艺成本计算表
(原创实用版)
目录
1.冷墩工艺的概述
2.冷墩工艺的成本计算方法
3.冷墩工艺的成本控制策略
正文
一、冷墩工艺的概述
冷墩工艺,也称为冷镦工艺,是一种通过冷挤压的方法将金属材料制成零件的加工技术。
这种工艺具有生产效率高、节约材料、减少废品等优点,因此在我国的机械制造、汽车制造等行业中得到了广泛的应用。
二、冷墩工艺的成本计算方法
冷墩工艺的成本主要包括直接成本和间接成本两部分。
直接成本主要包括原材料成本、人工成本和设备成本,而间接成本则包括管理成本、维护成本和折旧成本等。
1.原材料成本:原材料成本是冷墩工艺的主要成本,其计算公式为:原材料成本=材料单价×材料用量。
2.人工成本:人工成本是指用于冷墩工艺的生产人员的工资,其计算公式为:人工成本=工人工资总额/产量。
3.设备成本:设备成本是指用于冷墩工艺的设备的折旧费用,其计算公式为:设备成本=设备折旧费用/设备使用年限。
三、冷墩工艺的成本控制策略
为了提高冷墩工艺的效益,必须对其成本进行有效的控制。
以下是一些常用的成本控制策略:
1.选择合适的原材料:选择价格合理、质量优良的原材料,可以降低原材料成本。
2.提高生产效率:通过提高生产效率,可以降低人工成本和设备成本。
3.延长设备使用年限:通过合理的设备维护和管理,可以延长设备的使用年限,降低设备成本。
冷镦工艺讲解
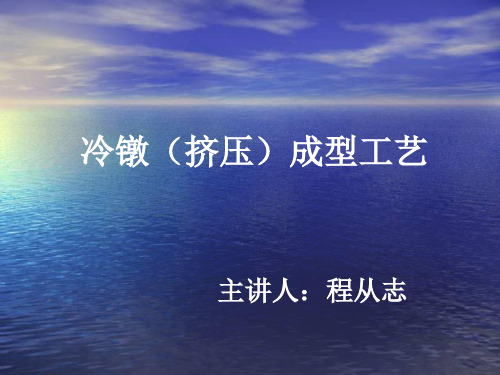
F0、Fk——拉伸试样原始、破断处的截面积。
2021/5/8
5
(2)镦粗试验 又称压扁试验
它是将试样制成高度Ho为试样原始直径Do的1.5倍的圆柱形,然后在 压力机上进行压扁,直到试样表面出现第1条肉眼可观察到的裂纹为 止,这时的压缩程度εc为塑性指标。其数值按下式可计算出:Βιβλιοθήκη cHo Hk Ho
c.机械性能好。冷镦(挤)方法加工的零件,由于金属纤维未被切 断,因此强度要比切削加工的优越得多。
2021/5/8
2
d.适于自动化生产。适宜冷镦(挤)方法生产的紧固件(也含一部 分异形件),基本属于对称性零件,适合采用高速自动冷镦机生产, 也是大批量生产的主要方法。
总之,冷镦(挤)方法加工紧固件、异形件是一种综合经济效益相当 高的加工方法,是紧固件行业中普遍采用的加工方法,也是一种在国 内、外广为利用、很有发展的先进加工方法。因此,如何充分利用、 提高金属的塑性、掌握金属塑性变形的机理、研制出科学合理的紧固 件冷镦(挤)加工工艺,是本章的目的和宗旨所在。
a.金属组织及化学成分对塑性及变形抗力的影响
金属组织决定于组成金属的化学成分,其主要元素的晶格类别,杂质 的性质、数量及分布情况。组成元素越少,塑性越好。例如纯铁具有 很高的塑性。碳在铁中呈固熔体也具有很好的塑性,而呈化合物,则 塑性就降低。如化合物Fe3C实际上是很脆的。一般在钢中其他元素 成分的增加也会降低钢的塑性。
10% 0(公式36-3)
式中 Ho——圆柱形试样的原始高度。Hk——试样在压扁中,在侧表 面出现第1条肉眼可见裂纹时的试样高度。
(3)扭转试验
扭转试验是以试样在扭断机上扭断时的扭转角或扭转圈数来表示的。 生产中最常用的是拉伸试验和镦粗试验。不管哪种试验方法,都是相 对于某种特定的受力状态和变形条件的。由此所得出的塑性指标,只 是相对比较而言,仅说明某种金属在什么样的变形条件下塑性的好坏。
冷压(冷镦冷挤)加工
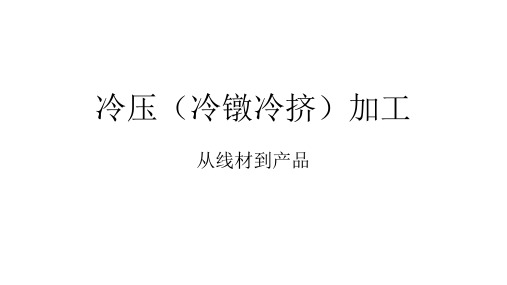
螺母成型机
攻丝机
零件成型机
攻丝机
20
现有设备式样一览表
设备名 机种 NP-425SS 台数 加工尺寸 切断长 月产能力/台 总生产能力
(月产)
1
Φ14(MAX)
14mm(Max) 14mm(Max)
600万个/2班 500万个/2班 约1,900万个
螺母成型机
NF-525SS NF-530SS
2
Φ14(MAX) Φ17(MAX)
棒材
线材
压造成型与切削加工对比
• 以制作螺栓等轴状产品为例,素材都是有内部纤维组织的棒状材 料,用切削方式和镦挤方式加工,前者产品内部的纤维流被切断, 而后者是连续的。 螺栓在使用中,其头部和根部之间的夹角部,受到拉伸应力的作 用,由于切削加工的螺栓,其纤维被切断,易产生冲击损坏或疲 劳损坏。而锻造螺栓具备夹角部强度高的优点。
开放拉伸(reductioning)
在一部分材料尚未进入模腔的 状态下,用冲头挤压材料,从 而对轴部进行拉伸。 这种工艺用于断面减少率较小 的加工。 一般和镦头工艺同时进行。
冷压工艺用以下模具组合制作产品
向后挤压(backward)
切边(trimming)
冲孔(pierce)
将材料置入模具,通过 模冲的挤压,模腔中多 余的材料被向后挤出, 用于 挤孔加工工艺。
冷压成型机(Former)
机体 框架 成型机概略图 曲轴
模体
滑块
马达
模具---模腔
模具---模冲 飞轮
压造成型的好处
• 压造成型机的最大特点就是设备本身具有材料切断功能。 普通冲压式锻机,事先须将棒材做切断、热处理、表面(润滑) 处理,制作出毛坯后,再将毛坯投入锻床。 而压造成型机可以在设备内部将棒材或线材按照所需尺寸切断, 切断的毛坯可在多工位之间搬移(机械手),通过多工序(工位) 加工,完成由粗加工到精加工的全部过程。 这个被称为机械手的搬运装置,也是压造成型机的一大特点。 因此,压造成型机可以实现普通锻机不可比拟的高速生产。
冷挤压和冷镦基础知识介绍
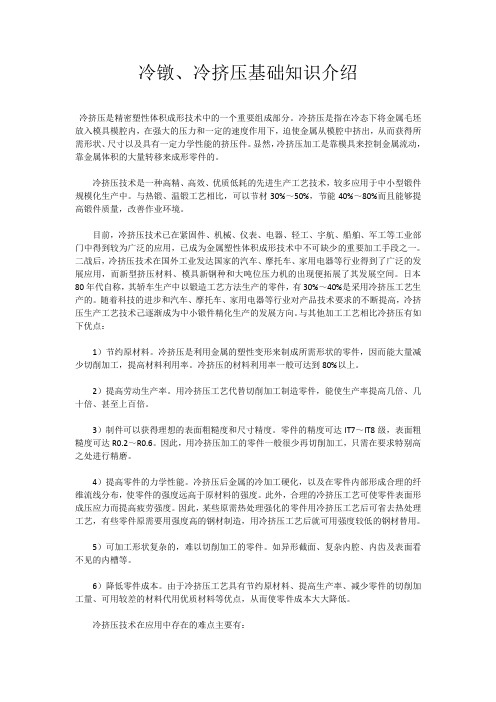
冷镦、冷挤压基础知识介绍冷挤压是精密塑性体积成形技术中的一个重要组成部分。
冷挤压是指在冷态下将金属毛坯放入模具模腔内,在强大的压力和一定的速度作用下,迫使金属从模腔中挤出,从而获得所需形状、尺寸以及具有一定力学性能的挤压件。
显然,冷挤压加工是靠模具来控制金属流动,靠金属体积的大量转移来成形零件的。
冷挤压技术是一种高精、高效、优质低耗的先进生产工艺技术,较多应用于中小型锻件规模化生产中。
与热锻、温锻工艺相比,可以节材30%~50%,节能40%~80%而且能够提高锻件质量,改善作业环境。
目前,冷挤压技术已在紧固件、机械、仪表、电器、轻工、宇航、船舶、军工等工业部门中得到较为广泛的应用,已成为金属塑性体积成形技术中不可缺少的重要加工手段之一。
二战后,冷挤压技术在国外工业发达国家的汽车、摩托车、家用电器等行业得到了广泛的发展应用,而新型挤压材料、模具新钢种和大吨位压力机的出现便拓展了其发展空间。
日本80年代自称,其轿车生产中以锻造工艺方法生产的零件,有30%~40%是采用冷挤压工艺生产的。
随着科技的进步和汽车、摩托车、家用电器等行业对产品技术要求的不断提高,冷挤压生产工艺技术己逐渐成为中小锻件精化生产的发展方向。
与其他加工工艺相比冷挤压有如下优点:1)节约原材料。
冷挤压是利用金属的塑性变形来制成所需形状的零件,因而能大量减少切削加工,提高材料利用率。
冷挤压的材料利用率一般可达到80%以上。
2)提高劳动生产率。
用冷挤压工艺代替切削加工制造零件,能使生产率提高几倍、几十倍、甚至上百倍。
3)制件可以获得理想的表面粗糙度和尺寸精度。
零件的精度可达IT7~IT8级,表面粗糙度可达R0.2~R0.6。
因此,用冷挤压加工的零件一般很少再切削加工,只需在要求特别高之处进行精磨。
4)提高零件的力学性能。
冷挤压后金属的冷加工硬化,以及在零件内部形成合理的纤维流线分布,使零件的强度远高于原材料的强度。
此外,合理的冷挤压工艺可使零件表面形成压应力而提高疲劳强度。
- 1、下载文档前请自行甄别文档内容的完整性,平台不提供额外的编辑、内容补充、找答案等附加服务。
- 2、"仅部分预览"的文档,不可在线预览部分如存在完整性等问题,可反馈申请退款(可完整预览的文档不适用该条件!)。
- 3、如文档侵犯您的权益,请联系客服反馈,我们会尽快为您处理(人工客服工作时间:9:00-18:30)。
大桥精密件制造(广州)有限公司 事业内容
汽车用冷镦压造零件的制造及进口销售业务 生产品种:各种冷镦压造零件 (焊接螺母,法兰螺母,衬套,垫圈等) 工厂主要设备
・ 螺母成型机 4台 NP-425SS(1台) NF-525SS(2台) NF-530SS(1台) ・ 零件成型机 1台 PF-540SS(1台) ・ 打头机 1台 NP-160 (1台) ・ 攻丝机 16台 SUPER-3N(M6~M10) 13台 SUPER-5N(M10 ~ M14) 3台
开放拉伸(reductioning)
在一部分材料尚未进入模腔的 状态下,用冲头挤压材料,从 而对轴部进行拉伸。 这种工艺用于断面减少率较小 的加工。 一般和镦头工艺同时进行。
冷压工艺用以下模具组合制作产品
向后挤压(backward)
切边(trimming)
冲孔(pierce)
将材料置入模具,通过 模冲的挤压,模腔中多 余的材料被向后挤出, 用于 挤孔加工工艺。
约2,000万个
M6~M14
-
70万个/2班
约210万个
21
成品
冷压(冷镦冷挤)加工
从线材到产品
材料(高炉)
1、高炉
矿石、焦炭、 石灰石
2、转炉
氧气
钢水 氧气
3、连铸・制坯
铸模
钢坯
4、开坯
分坯
分坯轧机
5、轧制
轧制
线材轧机
棒材轧机
6、母材
拉丝工厂
材料(拉丝)
母材
酸洗・表面皮膜 (磷化)
拉制(中间)
退火(球状化)
酸洗・表面皮膜 (磷化)
拉制(精拉)
冷压用线材
将多余材料进行切除的加 工,例如用于六角螺栓头 部的六角形成型等。
用模冲进行冲孔,用于冲制螺 母等内孔。
6D6B(6模6冲)
2D3B(2模3冲)
冷压后的后续加工工序
1、螺母压造成型后,用攻丝工艺进行螺纹加工。
2、螺栓压造成型后,用搓丝工艺进行螺纹加工。
3、图纸如有要求,还要对零件实施热处理、表面处理、或者进行 切削加工等。
棒材
线材
压造成型与切削加工对比
• 以制作螺栓等轴状产品为例,素材都是有内部纤维组织的棒状材 料,用切削方式和镦挤方式加工,前者产品内部的纤维流被切断, 而后者是连续的。 螺栓在使用中,其头部和根部之间的夹角部,受到拉伸应力的作 用,由于切削加工的螺栓,其纤维被切断,易产生冲击损坏或疲 劳损坏。而锻造螺栓具备夹角部强度高的优点。
冷压成型机(Former)
机体 框架 成型机概略图 曲轴
模体
滑块
马达
模具---模腔
模具---模冲 飞轮
压造成型的好处
• 压造成型机的最大特点就是设备本身具有材料切断功能。 普通冲压式锻机,事先须将棒材做切断、热处理、表面(润滑) 处理,制作出毛坯后,再将毛坯投入锻床。 而压造成型机可以在设备内部将棒材或线材按照所需尺寸切断, 切断的毛坯可在多工位之间搬移(机械手),通过多工序(工位) 加工,完成由粗加工到精加工的全部过程。 这个被称为机械手的搬运装置,也是压造成型机的一大特点。 因此,压造成型机可以实现普通锻机不可比拟的高速生产。
17mm(Max)
320万个/2班
1 零件成型机 PF-540SS 1 Φ22(MAX) 70mm(Max) 180万个/2班 180万个/2班
打头机NP-1601Φ20(MAX)170mm(Max)
46万个/2班
46万个/2班
SUPER-3N 攻丝机 SUPER-5N
13 3
M6~M10
-
160万个/2班
螺母成型机
攻丝机
零件成型机
攻丝机
20
现有设备式样一览表
设备名 机种 NP-425SS 台数 加工尺寸 切断长 月产能力/台 总生产能力
(月产)
1
Φ14(MAX)
14mm(Max) 14mm(Max)
600万个/2班 500万个/2班 约1,900万个
螺母成型机
NF-525SS NF-530SS
2
Φ14(MAX) Φ17(MAX)
拉制种类
1、直抽・・・酸洗・表面皮膜(磷化) ➡ 拉制(精拉) ➡ 成品
2、1次退火・・・酸洗 ➡ 退火(球化) ➡ 酸洗・表面皮膜(磷化) ➡ 拉制(精拉) ➡ 成品 3、2次退火・・・酸洗 ➡ 退火(球化) ➡ 酸洗 ➡ 拉制(中间) ➡ 退火(球化) ➡ 酸洗・表面皮膜(磷化) ➡ 轧制 (精拉) ➡ 成品
在常温下加工,虽然零件变形 阻力大,但是,零件尺寸精度 好,可以不用额外的精加工。
冷压工艺用以下模具组合制作产品
镦头(upsetting) 冲头挤压材料,使材 料直径变粗,多用于 铆钉或螺栓的头部成 型。
密闭拉伸(forward)
材料完全进入模腔,在密 闭状态下,靠冲头向前挤 压,实现素材拉伸。 可实现较大的拉伸(断面 减小率大)。
锻造的温度区间
【冷锻】 冷锻加工在室温下进行,无须 使用材料加热、冷却装置。 模具、产品冷却用的冷却油对 于使用为挤出、冲孔等加工起 润滑作用而添加的添加剂没有 太大限制。 【温锻】 温锻温度区间通常为300~800℃ 之间,需要加热装置对被加工材 进行加热。 加热温度因材料特性以及零件形 状不同而不同,加热装置因加热 温度不同而不同。一般用电阻加 热器或是感应加热器 素材温度较高时,可能需要对接 触到素材的设备的机构以及部件 实施冷却。 【热锻】 热锻温度区间通常为1,000~1,250℃ 之间,一般使用高频感应加热器对被 加工材进行加热。 设备的送料部位、材料导引部、以及 压造加工部的各机构,需用冷却液进 行循环冷却。冷却液中添加的有水、 防锈剂、防腐剂。 把素材加热到了高温,所以加工时变 形阻力很小,很容易加工。