大连理工大学科技成果——利用复合电沉积的电火花加工电极快速制造技术
大连理工大学科技成果——甲苯-甲醇合成对二甲苯

大连理工大学科技成果——甲苯-甲醇合成对二甲苯一、产品和技术简介:对二甲苯是聚脂纤维的重要原料,也是石油化工的重要原料,对它的需求量日益增长,供不应求。
目前工业上采用甲苯、C9芳烃及混合二甲苯为原料通过歧化、异构化、吸附分离或深冷分离来制取对二甲苯,物料循环量大,设备庞大,操作费用高。
甲苯-甲醇在自制的稀土改性的分子筛催化剂上择形催化直接合成对二甲苯。
主要工艺条件:原料摩尔比甲苯/甲醇=2∶1混合原料质量空速2h-1反应温度460℃反应压力常压载气N2与混合原料摩尔比10此技术与现有生产对二甲苯工艺比较,它取消了二甲苯吸附分离和异构化等复杂工艺过程。
该技术流程简单、污染轻、催化剂综合性能优异、居世界先进水平。
二、应用范围:以甲苯-甲醇合成高纯度对二甲苯是一条新的工艺路线,本技术特点是采用在稀土改性的ZSM-5沸石分子筛催化剂上进行甲苯的选择烃化反应,由于其择形催化作用,可直接得到高纯度的对二甲苯,其含量在混合二甲苯中达98%,甲苯转化率达28%,催化剂单程连续运转300小时,性能稳定,且具有良好的再生性和制备重复性。
三、生产条件:工业可选用两台多段,段间设有激冷的绝热固定床反应器,反应与再生交换进行。
需循环气压缩机,精馏塔(稳定塔、甲苯塔、对二甲苯塔)。
四、成本估算:建设投资比现有甲苯歧化法大大减少。
五、规模与投资:根据实验结果提出工艺流程。
取消二甲苯吸附分离和异构化过程,据西南化工研究院估算,得出甲苯烷基化法建设投资仅为现有甲苯歧化法的40%左右。
六、市场与效益:供不应求。
七、提供技术的程度和合作方式:合作开发,经中试后推广生产。
八、知识产权:自主知识产权。
大连理工大学科技成果——二氧化碳捕集与净化工业化技术

大连理工大学科技成果——二氧化碳捕集与净化工业化技术一、产品和技术简介:随着世界范围内工业化进程的加快,二氧化碳废气的排放量越来越大,既造成了严重的大气污染,形成可怕的温室效应,又浪费了宝贵的碳资源。
因此控制二氧化碳的排放量,对排放的二氧化碳进行回收、固定、利用及再资源化,已成为世界各国特别是发达国家十分关注的问题。
该二氧化碳捕集与净化工业化技术针对不同浓度二氧化碳气源,采用不同的回收技术进行富集和提纯。
复合脱碳溶液用于捕集低浓度二氧化碳气源中的CO2,技术核心是吸收剂对CO2的吸收容量大,解吸量大,解吸温度低,能耗小,抗氧化性能强,不腐蚀设备,操作压力低。
对于高浓度二氧化碳气源,通过吸附精馏技术将吸附法和精馏法结合,使用各种高效吸附剂有效脱除二氧化碳气体中的微量杂质,可以把二氧化碳提纯到99.99%以上,达到和超过国家最新食品添加剂(GB10621-006)和国际饮料协会标准。
二、应用范围和生产条件:该技术可以使用于各种化工厂、发电厂、炼钢厂、矿石分解等尾气的净化提纯。
所得二氧化碳产品广泛实用于人类生活的各行各业:医药、采油驱油剂、焊机保护气、干冰、食品添加剂等。
该技术已在全国成功推广不同气源的二氧化碳回收装置27套,产品二氧化碳包括工业级、食品级。
装置运行稳定,产品供不应求。
三、获得的专利等知识情况:ZL200710011329.8回收混合气体中二氧化碳的符合脱碳溶液200910011874.6一种从含二氧化碳气体中选择性脱除二氧化硫的吸收剂201110230570.6一种用复合脱碳溶液捕集混合气体中二氧化碳的方法ZL200310105015.6脱除二氧化碳中微量乙烯吸附剂ZL03238678.8吸附精馏提纯二氧化碳装置AL200810010905.1吸附精馏技术提纯二氧化碳装置US7,754,102B2 METHOD FOR RECLAIM OF CARBON DIOXIDE AND NITROGEN FROM BOILER FLUE GASZL200710101478.3锅炉烟道气回收净化注井采油装置ZL200710011508.1一种回收废气中二氧化碳用复合脱碳溶液ZL200720011443.6锅炉烟道气加压吸收二氧化碳液化驻京采用装置ZL200920013376.0锅炉烟道气回收二氧化碳液化注井采油装置ZL200920013375.6锅炉烟道气回收全气态注井采油装置ZL200720011439.X锅炉烟道气加压吸收二氧化碳气态注井采油装置ZL200720011438.5蒸汽二氧化碳氮气联注井采油装置四、规模与投资、成本估算:装置规模年产20万吨CO2五、提供技术的程度和合作方式:许可使用六、配图:低浓度二氧化碳富集提纯工艺流程吸附精馏法精制二氧化碳工艺流程七、产业化程度:产业化阶段。
第七届“上银优秀机械博士论文奖”获奖论文
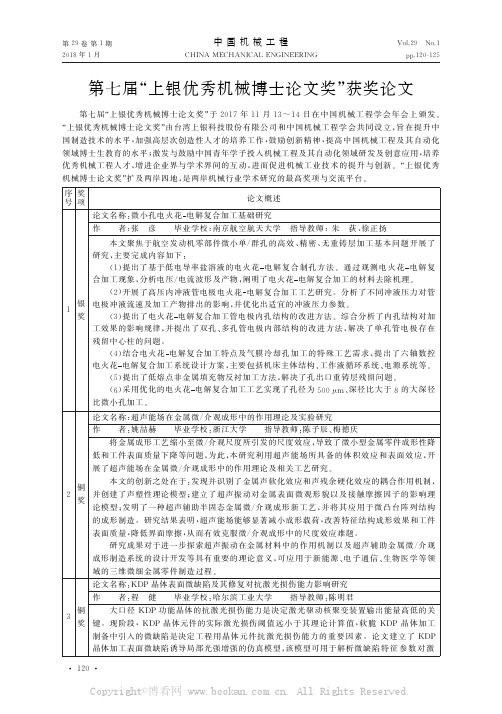
论文名称:铜电致化学抛光机理及性能研究
作 者:单 坤密加工技术在微电子器件和微机电系统制造中具有广泛的需
求.但现有无应力抛光方法无法满足超平滑无 损 伤 铜 表 面 需 求.本 文 针 对 此 难 题,基 于 电 化
展了超声能场在金属微/介观成形中的作用理论及相关工艺研究.
2
铜
奖
本文的创新之处在于:发现并识别了金属声软化效应和声残余硬化效应的耦合作用机制,
并创建了声塑性理论模型;建立了超声振动对金属表面 微 观 形 貌 以 及 接 触 摩 擦 因 子 的 影 响 理
论模型;发明了一种超声辅助半固态金属微/介观 成 形 新 工 艺,并 将 其 应 用 于 微 凸 台 阵 列 结 构
本文聚焦于航空发动机零部件微小单/群孔 的 高 效、精 密、无 重 铸 层 加 工 基 本 问 题 开 展 了
研究,主要完成内容如下:
(
1)提出了基于低电导率盐溶液的电火花 电 解 复 合 制 孔 方 法.通 过 观 测 电 火 花 电 解 复
合加工现象,分析电压/电流波形及产物,阐明了电火花 电解复合加工的材料去除机理.
照下表面损伤点的增长规律及内在物理机制;采用精密 微 铣 削 方 法 对 表 面 微 缺 陷 进 行 修 复 去
除,通过对修复表面诱导的光强分布研究,证实可用精密微铣削修复方法提升晶体元件的抗激
光损伤能力,为晶体元件精密修复中最优修复策略及工艺参数的制定提供了依据;自主研发的
大口径 KDP 晶体修复装备、方法和工艺已获成功应用,该项成果为 我 国 高 功 率 激 光 核 聚 变 装
“上银优秀机械博士论文奖”由台湾上银科技股份有限公司和中国机械工程 学 会 共 同 设 立,旨 在 提 升 中
电火花加工的基本原理及四个阶段
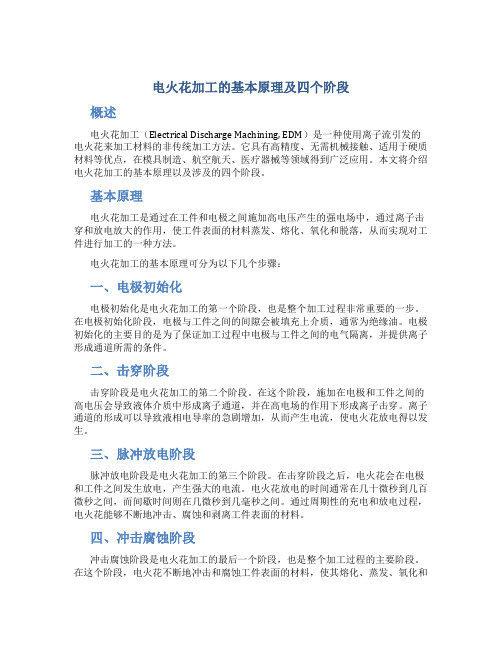
电火花加工的基本原理及四个阶段概述电火花加工(Electrical Discharge Machining, EDM)是一种使用离子流引发的电火花来加工材料的非传统加工方法。
它具有高精度、无需机械接触、适用于硬质材料等优点,在模具制造、航空航天、医疗器械等领域得到广泛应用。
本文将介绍电火花加工的基本原理以及涉及的四个阶段。
基本原理电火花加工是通过在工件和电极之间施加高电压产生的强电场中,通过离子击穿和放电放大的作用,使工件表面的材料蒸发、熔化、氧化和脱落,从而实现对工件进行加工的一种方法。
电火花加工的基本原理可分为以下几个步骤:一、电极初始化电极初始化是电火花加工的第一个阶段,也是整个加工过程非常重要的一步。
在电极初始化阶段,电极与工件之间的间隙会被填充上介质,通常为绝缘油。
电极初始化的主要目的是为了保证加工过程中电极与工件之间的电气隔离,并提供离子形成通道所需的条件。
二、击穿阶段击穿阶段是电火花加工的第二个阶段。
在这个阶段,施加在电极和工件之间的高电压会导致液体介质中形成离子通道,并在高电场的作用下形成离子击穿。
离子通道的形成可以导致液相电导率的急剧增加,从而产生电流,使电火花放电得以发生。
三、脉冲放电阶段脉冲放电阶段是电火花加工的第三个阶段。
在击穿阶段之后,电火花会在电极和工件之间发生放电,产生强大的电流。
电火花放电的时间通常在几十微秒到几百微秒之间,而间歇时间则在几微秒到几毫秒之间。
通过周期性的充电和放电过程,电火花能够不断地冲击、腐蚀和剥离工件表面的材料。
四、冲击腐蚀阶段冲击腐蚀阶段是电火花加工的最后一个阶段,也是整个加工过程的主要阶段。
在这个阶段,电火花不断地冲击和腐蚀工件表面的材料,使其熔化、蒸发、氧化和脱落。
通过不断重复脉冲放电和冲击腐蚀过程,工件的形状和尺寸最终得以加工完成。
总结电火花加工以其高精度、无需机械接触、适用于硬质材料等优点在工业领域得到广泛应用。
在电火花加工的过程中,电极初始化、击穿阶段、脉冲放电阶段和冲击腐蚀阶段是不可或缺的四个阶段。
大连理工大学科技成果——铝合金电弧喷涂防护技术

大连理工大学科技成果——铝合金电弧喷涂防护技术一、产品和技术简介:由于铝合金有较高的强度/重量比,以及良好的塑性和耐海洋大气腐蚀性能,工业上开始大量应用。
在一般的大气环境下,铝合金表面形成的Al2O3保护膜能有效防止构件的腐蚀,但在湿气和电解质存在下,如在海洋大气环境中,大量氯离子的侵入使得铝合金表面出现点蚀现象,甚至是氧化膜的大量脱落,构件的寿命大大缩短。
大连理工大学通过铝合金电弧喷涂涂层及封孔方法的研究,开发出一种操作更加简便,成本更低的新型铝合金防腐蚀方法,解决了较大铝合金构件在湿气和电解质存在下,尤其是海洋大气环境中的长效防腐蚀问题。
铝合金电弧喷涂涂层及封孔技术是采用热喷涂方法,在铝合金表面喷涂一层复合涂层,然后采用不同的封孔方法进行封闭处理,实现铝涂层与基体之间以及封孔涂层与铝涂层之间的紧密结合。
采用的封孔方法简便、经济、高效,可以有效地进行复杂结构件的涂层封孔;同时,还开发了导电封孔技术,在不影响封孔耐蚀效果的同时,使涂层封孔后仍能达到导电抗静电的性能。
满足不同工业应用的需求。
二、应用范围:可用于各种条件(特别是湿气和电解质存在的环境气氛)下铝合金构件的表面防护。
三、生产条件:采用本项目技术进行结构件防护需要电弧喷涂设备1套及相应辅助设备,以及喷涂用金属丝等。
四、规模与投资:电弧喷涂技术具有生产效率高;结合强度高;能源利用率高,能耗少;设备投资低,维护简单,经济效益好;可方便地制备伪合金涂层等特点。
该技术具有可现场操作的特点,而且工件大小和形状不受限制,操作简便,防腐涂层与基体的结合强度高,完全适合工业应用。
该技术成本在10万元以下,主要包括喷涂设备及材料的购置。
五、知识产权情况:具有完全自主知识产权。
六、市场需求与经济效益分析:铝合金目前在工业上广泛使用,使用量仅次于钢,由于其良好的防腐性能,在复杂环境条件下的应用不断扩大,但在传统的防护技术条件下铝合金构件的使用寿命较短,本项目技术可对铝合金构件进行现场防护,使得铝合金构件的使用寿命提高一倍以上。
大连理工大学科技成果——微纳米结构喷印成型系统
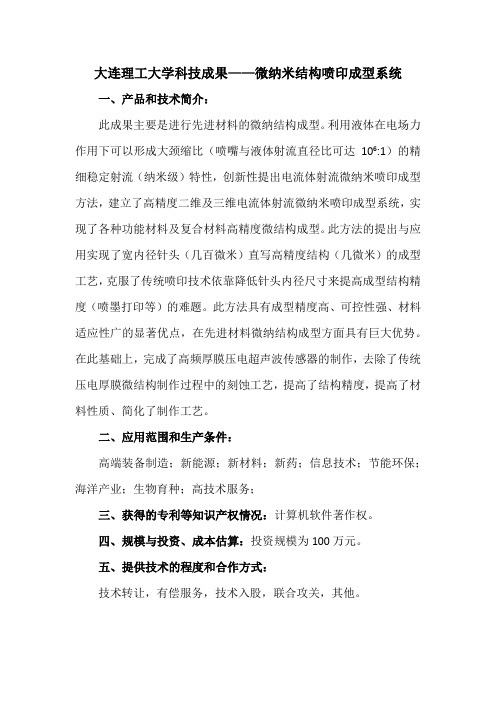
大连理工大学科技成果——微纳米结构喷印成型系统
一、产品和技术简介:
此成果主要是进行先进材料的微纳结构成型。
利用液体在电场力作用下可以形成大颈缩比(喷嘴与液体射流直径比可达106:1)的精细稳定射流(纳米级)特性,创新性提出电流体射流微纳米喷印成型方法,建立了高精度二维及三维电流体射流微纳米喷印成型系统,实现了各种功能材料及复合材料高精度微结构成型。
此方法的提出与应用实现了宽内径针头(几百微米)直写高精度结构(几微米)的成型工艺,克服了传统喷印技术依靠降低针头内径尺寸来提高成型结构精度(喷墨打印等)的难题。
此方法具有成型精度高、可控性强、材料适应性广的显著优点,在先进材料微纳结构成型方面具有巨大优势。
在此基础上,完成了高频厚膜压电超声波传感器的制作,去除了传统压电厚膜微结构制作过程中的刻蚀工艺,提高了结构精度,提高了材料性质、简化了制作工艺。
二、应用范围和生产条件:
高端装备制造;新能源;新材料;新药;信息技术;节能环保;海洋产业;生物育种;高技术服务;
三、获得的专利等知识产权情况:计算机软件著作权。
四、规模与投资、成本估算:投资规模为100万元。
五、提供技术的程度和合作方式:
技术转让,有偿服务,技术入股,联合攻关,其他。
大连理工 导师 课题——纵向科研项目一览表

刘冲
5
2005-2007
20.
一次性电化学生物芯片的优化设计及制作工艺研究
辽宁省博士启动基金
(20041073)
罗怡
4
2005-2007
21.
机械制造企业精益生产模式及其软件系统实现研究
大连市科技计划项目
(2004A1GX091)
王德伦
8
2005-2006
22.
电磁技术和膜技术除垢抗垢方法的应用研究
王德论
80
2006-2009
25.
面向原始创新的模糊前端及概念设计系统化方法与技术
国家高技术研究
发展计划863项目
(2006AA04Z109)
滕弘飞
史彦军
25
2006-2009
12.
××微传感执行网基础研究
国家部委
“十一五”基础科研项目
王立鼎
280
2006-2008
13.
××轴承设计仿真技术研究——滚动轴承计算机数值仿真与试验仿真结果相似度理论研究
高等学校博士学科点
专项科研基金
(20050141010)
刘冲
6
2006-2008
17.
激光诱导等离子体辅助沉积玻璃导电膜机理分析
教育部留学回国人员
科研启动基金
[2005]383
吴东江
3
2006-2007
18.
面向产业化的微流控芯片制造技术及设备
辽宁省基地专项资金计划
王立鼎
50
2006-2008
19.
李庆忠
3
2007-2008
22.
基于NURBSS表达的船舶参数化设计关键技术研究及工程应用
大连理工大学科技成果——超临界萃取-酯交换反应偶合法由原料直接制备生物柴油

大连理工大学科技成果——超临界萃取-酯交换反应偶合法由原料直接制备生物柴油
一、产品和技术简介:
生物柴油作为一种清洁的可替代能源受到越来越多的重视。
以往制备生物柴油的方法存在一些无法避免的弊端,像物理法尽管简单,但产品质量差、存在严重的发动机积碳、润滑油污染等问题,而化学法则工艺复杂、产品分离困难、产生环境污染等。
本课题利用超临界萃取-酯交换反应偶合法由原料直接制备生物柴油,该方法可以在较为温和的条件下由一步法直接从原料制备生物柴油,并且工艺简便,成本低,便于制造成可移动的生产装置,非常适合于就地生产和普及推广。
二、应用范围和生产条件:
目前,生物柴油的应用方式有三种:作为石化柴油润滑性添加剂,一般生物柴油的加入剂量低于5%;作为石化柴油的调和部分,主要应用于运输业、海运业及其他容易造成环境污染的领域(如矿井),研究表明,生物柴油在保持性能不变的同时,还降低了发动机的磨损,多数测试显示20%生物柴油与80%传统柴油相混合的使用效果最好;纯生物柴油作为燃料使用。
通常的标准化学化工实验室即可安装运行,无特殊要求。
三、获得的专利等知识产权情况:
超临界萃取-酯交换反应偶合法由原料直接制备生物柴油的方法,ZL200810010373.1,中国,2011-09-14授权。
四、规模与投资、成本估算:
视用户的具体生产状况。
采用CO2为溶剂,无毒、无污染。
而且CO2可以回收循环利用。
因此本工艺具有潜在的技术经济性。
五、提供技术的程度和合作方式:
转让小试成果,培训人员操作水平达到技术合同要求。
六、配图:
七、产业化程度:中试阶段。
大连理工-康仁科-863课题
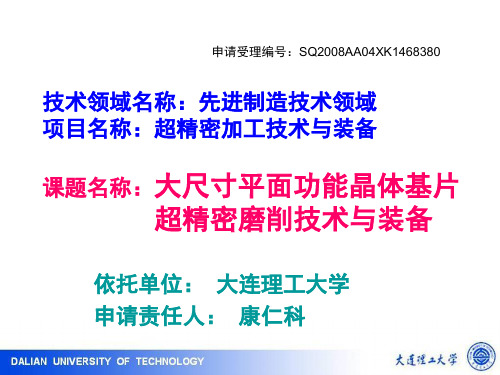
5
微电子制造技术发展趋势之三: 微电子制造技术发展趋势之三:芯片超薄化
减小芯片封装体积 提高3D封装密度 提高 封装密度 提高机械性能 提高散热效率和热稳定性 提高电性能 减小划片加工量 IC芯片厚度的变化趋势(摘自ITRS 2005Edition) IC芯片厚度的变化趋势(摘自 ) 芯片厚度的变化趋势
生产年份 硅片直径 / mm 特征线宽 / nm 减薄厚度(一般用途 减薄厚度 一般用途)/µm 一般用途 减薄厚度(3D封装用 封装用)µm 减薄厚度 封装用 2007 300 65 65 20 2010 300 45 50 10 2013 450 32 40 10
要求硅片背面减薄加工
厚度10µm晶圆 晶圆 厚度
7
超精密磨削技术的应用
• 超精密磨削用于基片制备阶段的平整化加工,取代了研磨和腐蚀工序, 超精密磨削用于基片制备阶段的平整化加工,取代了研磨和腐蚀工序, 可减小加工表面损伤深度,大大减少后续抛光的加工量。 可减小加工表面损伤深度,大大减少后续抛光的加工量。
磨外圆
多线切割
倒圆角
抛光片
单头单片抛光
磨削
11
全 自 动 超 精 密 磨 床
日本东京精密公司PG300/PG200系 列全自动磨床
日本Okamoto公司GNX300型 硅片磨床
德国 G&N公司NANOGRINDER/4 和 Multi-Nano 全自动硅片纳米磨床
美国Strasbaugh公司 7AF型硅片磨床
12
3.3 大尺寸硅片超精密磨削机床发展趋势
厚度50µm闪存芯片 闪存芯片 厚度
18~20层芯片 封装 ~ 层芯片 层芯片3D封装
医学检测芯片
制造半导体照明器件的蓝宝石基片由400μm减薄到100μm以下
大连理工大学科技成果——多相多元催化电解污水处理技术
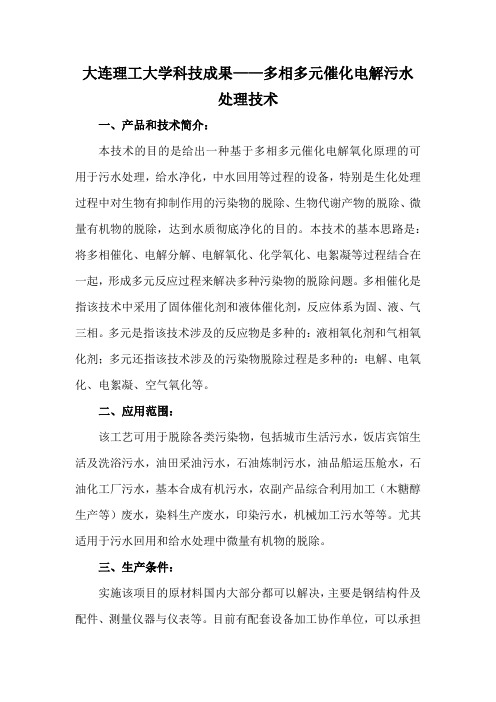
大连理工大学科技成果——多相多元催化电解污水处理技术一、产品和技术简介:本技术的目的是给出一种基于多相多元催化电解氧化原理的可用于污水处理,给水净化,中水回用等过程的设备,特别是生化处理过程中对生物有抑制作用的污染物的脱除、生物代谢产物的脱除、微量有机物的脱除,达到水质彻底净化的目的。
本技术的基本思路是:将多相催化、电解分解、电解氧化、化学氧化、电絮凝等过程结合在一起,形成多元反应过程来解决多种污染物的脱除问题。
多相催化是指该技术中采用了固体催化剂和液体催化剂,反应体系为固、液、气三相。
多元是指该技术涉及的反应物是多种的:液相氧化剂和气相氧化剂;多元还指该技术涉及的污染物脱除过程是多种的:电解、电氧化、电絮凝、空气氧化等。
二、应用范围:该工艺可用于脱除各类污染物,包括城市生活污水,饭店宾馆生活及洗浴污水,油田采油污水,石油炼制污水,油品船运压舱水,石油化工厂污水,基本合成有机污水,农副产品综合利用加工(木糖醇生产等)废水,染料生产废水,印染污水,机械加工污水等等。
尤其适用于污水回用和给水处理中微量有机物的脱除。
三、生产条件:实施该项目的原材料国内大部分都可以解决,主要是钢结构件及配件、测量仪器与仪表等。
目前有配套设备加工协作单位,可以承担设备加工制作安装任务。
部分测量仪表由国外相关专业公司提供。
四、成本估算:该工艺的处理成本主要取决于污染物的浓度和无机盐的浓度,只要无机盐浓度不高(不大于2000mg/L),以处理COD在1000mg/l以下的污水为例,电耗在0.2~0.8KWH/吨水。
五、规模与投资:对处理规模没有限制。
六、市场与效益:该技术的使用,可以使大批污水经过处理后达到回用标准,对于减轻环境污染有不可估量的意义。
每年可节水上百亿吨,对于节约淡水资源、增加工业可用水量有极大的促进作用。
预计今后随着环保要求的日益严格,国内市场需求量逐年增加。
其中染料、印染行业市场需求量较大。
七、提供技术的程度和合作方式:可提供各种不同处理规模的脱硫处理工艺及设备图纸。
Cu—SiC复合电极电火花加工烧结NdFeB永磁体的研究

基 体 构成 的金 属 间化 合 物 l _ 4 ] , 其 化 合 物 之 间 晶体 结 构
复杂 , 滑 移系 很少 , 所 以这 种 材 料具 有 硬 度 高 、 脆 性 大
一
图 1为复 合 电沉 积制 备 的 C u — S i C复 合 电极 材 料
的显 微组 织 。
的特 点 。正基 于这 些 缘 故 , 目前 针 对 钕 铁 硼 加 工 还 是 项 难题 , 采 用 传 统 的切 削加 工 方 式 对 其 加 工 通 常 会 导致 材料 的断裂 、 破碎 或剥落, 成品率极低 , 大 约 只有
1 0 ~2 0 之 间[ 5 ] 。
电火 花 加 工 ( e l e c t r i c a l d i s c h a r g e ma c h i n i n g ,
一 一 ㈩
应 用于 航空 航 天 、 电子、 机 电、 汽车、 声学 、 仪 器 仪 表 和 医疗 等领 域 。
常 温下 钕铁 硼材 料 主要 是 由 Nd 2 F e 1 4 B化 合 物 为
式中, n 为质 量 分数 ; p 为 c u的 密度 ; P 为 S i C
2 材 料 的 制 备
实验采 用硫 酸 铜溶 液 作 为 镀 液 , 镀 液 成 分 有 硫 酸
铜( 含 量为 1 8 0 ~2 2 0 g / L ) 、 硫酸( 含量为 5 0 ~7 0 g / L ) 、 工 艺条 件 为温 度 为 2 0 ~4 0 。 C, 电 流密 度 为 1 ~1 0 A 和 搅拌 速 度 为 3 O ~l O O r / mi n 。 电沉 积 中 阳极 材 料 采 用 含 铜量 为 9 9 . 6 的磷 铜 板 , 阴极 材 料 采 用 不锈 钢 片 。
火花沉积技术国内外研究的最新进展

火花沉积技术国内外研究的最新进展摘要:电火花沉积技术以其节能、汽车材料、环保等优势作为修复研究热点之一,广泛应用于航空军事、能源、电力、医疗矿山冶金等领域,以及精密机械零部件的制造与维修,为了总结这项技术在国内外的基本原理和技术特点,研究的最新进展,对加快这项技术研究及其应用提出了具体建议。
关键词:电火花沉积;进展;原理;工艺特点引言:现代工业的快速发展对材料的耐磨性、耐腐蚀性和耐高温性提出了更高的要求。
在高速、高温、高压、高氧化和高温腐蚀等恶劣条件下,大多数材料损伤发生在材料表面,如高温下的磨损和氧化,这使得材料表面强化技术成为国内外研究的热点之一。
有许多表面强化技术,包括电镀、渗透、热喷涂、EDM、冲浪、激光涂层和气相沉积。
其中,电火花沉积技术是表面强化技术的一个重要组成部分,它具有与基体冶金结合良好、耐磨耐蚀性好、不同材料之间容易沉积、电气材料易于选择等优点,节能、节材、环保,广泛应用于航空航天、汽车、能源、军工、电能、医疗、冶金矿山等领域,以及精密机械零部件的制造和维修得到迅速普及和应用,显示出更广阔的应用前景。
以下重点介绍国内外电火花加工技术的研究现状和进展。
一、电火花表面沉积技术原理及特点沉积工艺如图2所示。
图1电火花表面沉积技术工作原理图图2电火花表面沉积工艺示意图采用分析手段对沉积层进行微观分析。
分析结果表明:沉积层是由电极材料和工件材料通过冶金结合后形成的;沉积强化层组织细密,厚度达5-15um,硬度达到HV 1200以上(相当于HRC72 ),具有优良的物理化学性能和机械性能。
EDM表面沉积技术不仅能有效改善工件的表面性能,而且与传统的表面强化工艺如表面化学热处理、激光镀膜、电镀、,等离子弧和热喷涂的热焊接。
主要体现在以下几个方面:(1) EDM是空气沉积,易实现YG硬质合金、碳钢、黄铜等不同材料的增强层;(2)热输入非常小,电弧的热作用仅发生在工件表面的一小部分,工件的整个基体保持在室温下。
【CN109847752A】通过过渡双金属氧化复合催化材料光电活化过硫酸盐处理氨气并产电的PEC体系

2
CN 109847752 A
说 明 书
1/3 页
通过过渡双金属氧化复合催化材料光电活化过硫酸盐处理氨 气并产电的PEC体系
技术领域 [0001] 本发明属于活化过硫酸盐技术净化气相污染物与恶臭氨气等空气污染废弃物资 源化利用技术领域,提供了一种铜钴双金属氧化复合物做光阴极原位活化过硫酸盐降解氨 气的光电 催化系统 ,实现了在高效去除 氨气污染的同时 利用氨气自含能量产生电 能 ,为基 于过硫酸盐活化的“高级氧化技术”在空气净化领域提供了思路。
化过硫酸盐处理氨气并产电的PEC体系 ( 57 )摘要
本发明提供了一种通过过渡双金属氧化复 合 催化材料光电 活 化过 硫酸盐处理 氨气并 产电 的PEC体系,属于活化过硫酸盐技术净化气相污 染物与恶臭氨气等空气污染废弃物资源化利用 技术领域。铜钴双金属氧化复合物做光阴极原位 活化喷洒在复合物上蒸发浓缩的过硫酸盐,产生 高氧化电 位的硫酸根自由基 ,阳极是由铜棒在 K2SO4电解质溶液中腐蚀形成 ,构建了光电 催化 系统 ,可加快氨气的去除率。在电 催化、光电 催化 体系中CuO-Co3O4催化活化过硫酸盐膜不仅可以 高效去除氨气,同时可以利用氨气自含能量产生 电 能 ,为基于过硫酸盐活化的“高级氧化技术”在 空气净化领域提供了思路。
Cu与Co摩尔比为1:2~1:5分散在超纯水中,并加入过量的1 .5M NaOH溶液调节其pH值达到 10 .0以上;用超纯水洗涤数次后,将沉淀物干燥,研磨,在500℃~800℃条件下煅烧3~6h, 最后得到CuO-Co3O4催化剂;
(2)制备CuO-Co3O4催化活化过硫酸盐膜:将CuO-Co3O4催化剂分散在的硅溶胶中,控制每 mg的CuO-Co3O4催化剂对应每μL的硅溶胶,搅拌均匀,将其涂到预处理后的导电载体上,恒温 烘干,然后取过硫酸钾溶液喷洒与材料表面上,其中过硫酸钾的负载在5 .8~6 .3g/m2,干 燥,得到CuO-Co3O4催化活化过硫酸盐膜;
电火花沉积技术发展及在模具上的应用

电火花沉积技术发展及在模具上的应用电火花沉积技术,节能、省材、环保,应用广泛。
文章介绍了电火花沉积技术的特点、放电机理,分析了其应用现状,并提出相关建议以供参考。
标签:电火花;电火花涂层;压铸模具;热疲劳Abstract:EDM deposition technology is known for energy saving,material saving,environmental protection,and wide use. In this paper,the characteristics and discharge mechanism of EDM are introduced,its application status is analyzed,and some suggestions are put forward for reference.Keywords:EDM;EDM coating;die casting die;thermal fatigue电火花加工是一种常规的材料去除手段,在模具领域得到广泛地应用;电火花表面涂层技术是在电火花加工基础上发展起来的增材制造方法,在可在模具表面形成预防保护的涂层和堆焊修复工具和模具,具有一定的应用前景。
本文从技术基础及应用前景方面着重介绍电火花涂层的制造特点及在精密模具领域的发展潜力。
1 电火花涂层技术的特点电火花涂层是利用金属电极在金属工件表面做相对运动,在工件和电极的微区上产生微电弧,电弧同时熔化工件和电极形成金属熔滴,随后金属熔滴凝固在材料表面形成涂层,该涂层与结合面形成冶金结合。
由于电极和基体的熔化程度受电极极性和工艺参数的程度很大,导致形成的涂层成分和性能千差万别,当负极性连接时(工件接负),电极的熔化程度远高于基体,电极成分进入涂层的比例大幅度增加,因此涂层主要表现为电极的成分和性能,当电极选用特种材料电极时,处理的工件就同时具有了电极材料的性能。
特种加工填空题
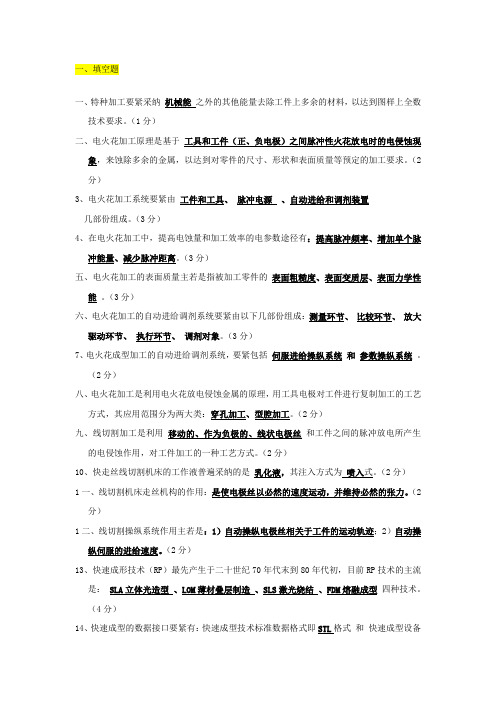
一、填空题一、特种加工要紧采纳机械能之外的其他能量去除工件上多余的材料,以达到图样上全数技术要求。
(1分)二、电火花加工原理是基于工具和工件(正、负电极)之间脉冲性火花放电时的电侵蚀现象,来蚀除多余的金属,以达到对零件的尺寸、形状和表面质量等预定的加工要求。
(2分)3、电火花加工系统要紧由工件和工具、脉冲电源、自动进给和调剂装置几部份组成。
(3分)4、在电火花加工中,提高电蚀量和加工效率的电参数途径有:提高脉冲频率、增加单个脉冲能量、减少脉冲距离。
(3分)五、电火花加工的表面质量主若是指被加工零件的表面粗糙度、表面变质层、表面力学性能。
(3分)六、电火花加工的自动进给调剂系统要紧由以下几部份组成:测量环节、比较环节、放大驱动环节、执行环节、调剂对象。
(3分)7、电火花成型加工的自动进给调剂系统,要紧包括伺服进给操纵系统和参数操纵系统。
(2分)八、电火花加工是利用电火花放电侵蚀金属的原理,用工具电极对工件进行复制加工的工艺方式,其应用范围分为两大类:穿孔加工、型腔加工。
(2分)九、线切割加工是利用移动的、作为负极的、线状电极丝和工件之间的脉冲放电所产生的电侵蚀作用,对工件加工的一种工艺方式。
(2分)10、快走丝线切割机床的工作液普遍采纳的是乳化液,其注入方式为喷入式。
(2分)1一、线切割机床走丝机构的作用:是使电极丝以必然的速度运动,并维持必然的张力。
(2分)1二、线切割操纵系统作用主若是:1)自动操纵电极丝相关于工件的运动轨迹;2)自动操纵伺服的进给速度。
(2分)13、快速成形技术(RP)最先产生于二十世纪70年代末到80年代初,目前RP技术的主流是:SLA立体光造型、LOM薄材叠层制造、SLS激光烧结、FDM熔融成型四种技术。
(4分)14、快速成型的数据接口要紧有:快速成型技术标准数据格式即STL格式和快速成型设备的通用数据接口即CLI格式。
(2分)一、填空题一、电火花加工是将电极形状复制到工件上的一种工艺方式。
- 1、下载文档前请自行甄别文档内容的完整性,平台不提供额外的编辑、内容补充、找答案等附加服务。
- 2、"仅部分预览"的文档,不可在线预览部分如存在完整性等问题,可反馈申请退款(可完整预览的文档不适用该条件!)。
- 3、如文档侵犯您的权益,请联系客服反馈,我们会尽快为您处理(人工客服工作时间:9:00-18:30)。
利用复合电沉积的电火花加工电极快速制造技术
Rapid Tooling Technology for EDM by Using of Composite Electrodeposition
研究背景和课题来源
电火花(EDM)电极的制造作为模具型腔电火花加工中的一个重要环节,对模具制造的质量、周期和成本产生重要影响。
采用铜电铸不仅可以实现EDM电极的快速经济制造,而且在具有复杂型面或微细纹路等特征的EDM电极制造中具有其他方法无法比拟的优越性。
但由于铜电铸电极的抗电蚀性能差,电极极易损耗,严重影响EDM加工的稳定性和加工精度。
因此,研制新型电极材料,提高电极的抗电蚀性能是实现EDM电极快速经济制造的关键。
本方向得到国家自然科学基金重点项目(No.5935110)和辽宁省科学技术基金(No.20062183)的资助。
研究内容与特色
针对铜电铸电极的抗电蚀性能差的问题,提出了复合电沉积法快速制备Cu-ZrB2复合材料EDM电极的新方法,即利用复合电沉积技术制备一种含有导电性难熔微粒ZrB2的Cu-ZrB2复合镀层以提高电极材料的抗电蚀性能。
通过研制新型的铜基电铸液和专用电解液搅拌系统,并将理论建模分析和工艺优化试验相结合,揭示了导电颗粒的脉冲复合共沉积机制和Cu-ZrB2复合镀层的耐电蚀机理,解决了复合电沉积中因导电微粒的尖端效应而严重影响镀层质量的问题。
研究成果
通过理论分析和实验研究,建立了脉冲电流条件下的导电微粒复合共沉积模型,研究了Cu-ZrB2电沉积体系的共沉积规律;通过大量工艺实验,确定了适于电沉积Cu-ZrB2复合材料的铜基电铸液体系,并通过EDM加工性能实验,研究了Cu-ZrB2复合镀层的电蚀除规律及其耐电蚀机理。
与纯铜材料相比,采用新研制的Cu-ZrB2复合镀层,可使电极的相对损耗可降低30%-44%。
导体
基体绝缘体
镀层
固体颗粒
含导电微粒时电沉积方式不同,易引起尖点效应,镀层质量恶化传统电铸铜镀层Cu-ZrB2复合镀层(组织细化)树脂原型导电化处理Cu-ZrB2复合材料电火花电极电火花成形的模具型腔。