数控加工程序编制_加工中心_孔类零件程序编制
数控加工程序编制及操作

2) 铣较大平面
铣较大平面时,为了提高生产效率和提高加 工表面粗糙度,一般采用刀片镶嵌式盘形铣刀, 如图4.9所示。
3) 铣小平面或台阶面
铣小平面或台阶面时一般采用通用铣刀, 如图4.10所示。
4) 铣键槽
铣键槽时,为了保证槽的尺寸精度,一般用 两刃键槽铣刀,如图4.11所示。
5) 孔加工
孔加工时,可采用钻头、镗刀等孔加工类 刀具,如图4.12所示。
数控加工程序编制及操作
1、常用铣削刀具
数控铣床上所采用的刀具, 要根据被加工零件的材料、几何 形状、表面质量要求、热处理状 态、切削性能及加工余量等,选 择刚性好、耐用度高的刀具。常 用刀具见右图。
2、铣刀类型选择
1)加工曲面类零件
加工曲面类零件时,为了保证刀具切削刃与加工轮廓在切 削点相切,而避免刀刃与工件轮廓发生干涉,一般采用球头铣刀 ,粗加工用两刃铣刀,半精加工和精加工用四刃铣刀,如图4.8所示 。
若执行下述程序段 N10 G53 G90 X0 Y0 Z0 N20 G54 G90 G01 X50 Y0 Z0 F100 N30 G55 G90 G01 X100 Y0 Z0 F100 则刀尖点的运动轨迹如图4.31中OAB所示。
b、顺铣和逆铣对加工影响
ቤተ መጻሕፍቲ ባይዱ
在铣削加工中,采用顺铣还是逆铣方式是影响加工表面粗糙度的
重要因素之一。逆铣时切削力F的水平分力FX的方向与进给运动Vf方向相反, 顺铣时切削力F的水平分力FX的方向与进给运动Vf的方向相同。铣削方式的选 择应视零件图样的加工要求,工件材料的性质、特点以及机床、刀具等条件
综合考虑。通常,由于数控机床传动采用滚珠丝杠结构,其进给传动间隙很
3、铣刀结构选择——平装结构
数控加工程序编制铣削编程4孔类零件的程序编制
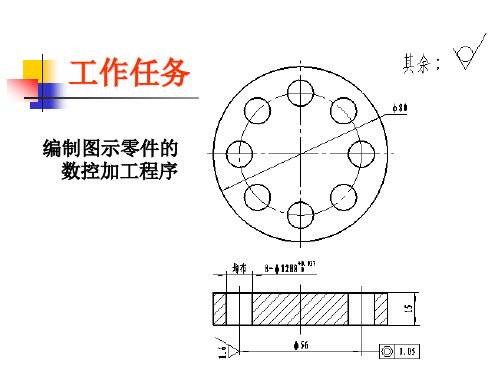
二、相关知识
(四)孔加工循环指令
举例:如图所示,用此程序加 工xy平面上在z轴方向排列的螺 纹孔M12x1。在此,出发点定 为x30y20,第一个孔与此参考 点的距离为20mm,其他的钻 孔相互间的距离也是20mm。 首先执行循环LCYC83加工孔, 然后运行循环LCYC84进行螺 纹切削。钻孔深度为80mm, 攻70mm。
LCYC60循环指令应用
二、相关知识
(四)孔加工循环指令
N10 G0 G54 G71 G17 G90 Tl Dl ;确定工艺参数 N20 S500 M3 y30 x20 z110 ;回到出发点(任意的) N30 R10l=75 R102=2 R103=72 R104=22 ;定义钻孔循环参数 N40 R105=l R107=82 R108=20 R109=10 ;定义钻孔循环参数 N50 R110=30 R111=10 R127=1 ;定义钻孔循环参数 N60 Rl15=83 R116=30 R117=20 R118=20 Rl19=5 R120=90 R121=20 N70 LCYC60 ;调用线性孔循环 N71 M05;
刀具,从而保孔的尺寸精度和表面粗糙度值。
二、相关知识
(三)孔加工刀具的选用
3)钻削速度V、进给量F的选择 F(mm/min)=S(r/min)×f(mm/r) S(r/min)=1000×V/(π×D) (r/min)
钻削进给量F参考值
加工材料
深 径 切削用
刀具直径do(mm)
比
量
灰铸铁
可锻铁、锰铸 铁
l/do
8 10 12 16 20 25 30 35 40
163~229HB (HT100、
HT150)
可锻铸铁 (≤229HB)
数控加工程序编制-加工中心-孔类零件程序编制全解

三、工作任务的完成
(一)数控加工工艺的制订
4.刀具准备,填写刀具卡
序号
1 2 3
4
5 6 7
刀具号
T05 T06 T07
名称 麻花钻 麻花钻 镗刀
T08 镗刀
T09 中心钻 T10 机用铰刀 T11 麻花钻
刀具规格 直径
Φ11.8mm Φ35mm Φ37.5mm
Φ38mm
Φ3mm Φ12mm Φ20mm
2.通过仿真加工,能够修改、优化工艺及程序。
二、相关知识
(一)孔加工工艺知识
孔的加工方法与步骤的选择
序号 加工方案
1钻 2 钻—铰 3 钻—粗铰(扩)—精铰 4 钻—扩 5 钻—扩—铰 6 钻—扩—粗铰—精铰 7 粗镗(扩孔) 8 粗镗(扩孔) —半精镗(精
扩) 9 粗镗(扩) —半精镗(精
扩) —精镗
三、工作任务的完成
(三)工作任务2:螺纹孔加工
G84右螺纹攻丝循环
三、工作任务的完成
(三)工作任务2:螺纹孔加工
例:编写如图所示螺纹孔(右旋螺纹)的加工程序(设Z
轴开始点距工作表面10mm处,切削深度为20mm)。
攻丝加工程序如下:
O2002
N10 G54 M03 S100
N20 G00 Z50. M08
二、相关知识
(二)固定循环功能
3.固定循环指令
G代码 G73 G74 G76 G80 G81 G82 G83 G84 G85 G86 G87 G88 G89
钻削(-Z方向) 间歇进给 切削进给 切削进给 ─── 切削进给 切削进给 间歇进给 切削进给 切削进给 切削进给 切削进给 切削进给 切削进给
T10
机用铰 刀
零件数控车床加工程序的编制

现 以上 图酒 杯 的数 控 车削 为 例 ,分 析怎 样 制 定 加工 工艺 及如 何编 制其 加工 程序 的方 法 。
一
、
分 析 零 件 图
/ ■, / , j 0 ,
零 件 图是 加 工零 件 要严 格遵 守 的技术 文 件 ,分
析零 件 图是 我 们 工 艺 准 备 中首 当其 冲 的重 要 工 作 。
图纸 识读 的准 确 与否 ,将 直 接影 响零 件程 序 编 制及
加工 的结 果 。 件 图上 的尺 寸公 差要 求 ,以确 定 控 制其
尺寸 精度 的加 工工 艺 , 比如 刀具 的选 择及 切 削 用量
图2
的确 定 。分 析 图 中形 状 和位 置公 差 要 求 :在 数 控 车 切 削加 工 中 ,影 响零 件 的形 状 和位 置 度 的主 要 因素 该 加 工路 线是 先用 G 7 5指令 在 径 向迅 速先 切 除 图示 区域 内大 的加 工余 量 ,其 各 点坐 标 可借 助 计 算 机 辅 助计 算 ,很 快捷 。再 用 G 7 3指 令加 工 。这样 可
法 ,则是极 为重要 的一项 工作 。
关 键词 :数 控 车床 ;走 刀路 线 ;程序 编 制
在 数 控 车 削 加 工 中 ,编 制 一 个 零 件 的数 控 程 序 ,其 加 工 路线 的选择 、程序 功 能指 令 的选 择 往 往 举 棋不 定 ,甚 至 同一 个 零 件 已经 加工 完 成 多个 ,尚
低成 本之 目的 。
1 0 /
零 件表 面粗 糙 度 、材 料 与热 处理 、其 它特 殊 处 理及 毛 坯 的要 求 ,件 数 。该 零件 为 铝件 ,粗糙 度 全
部 为R a 3 . 2。这 些都 是不 可忽 视 的参 数 。
加工中心钻孔程序的编制

加工中心的典型程序编制来源:数控产品网添加:2008-08-12 阅读:276次[ 内容简介 ]钻孔程序的编制1.钻孔程序的编制如图1,沿任意一条直线钻等距的孔。
若使用配备FANUC-6M系统的立式加工中心,则加工程序如下:图1 沿直线钻等距孔O1000N10 G92 X400.0 Y300.0 Z320.0 建立加工坐标系N20 M06 T00 换上中心钻N30 G90 G00 X0 Y0 X、Y向定位N40 Z0 Z向定位N50 M03 S500 F30 主轴启动N60 G81 G99 R-4.0 Z-10.0 钻深为5mm的中心孔N70 G91 G00 X20.0 Y10.0 L03 重复3次钻3中心孔N80 M05 主轴旋转停止N90 G28 Z0 经加工原点回机床原点N100 M06 T01 换钻孔刀,返回加工点NIl0 M03 G90 G00 G44 H01 G81 G99 R-5.0 Z-30.0 钻第一个孔,加刀具补偿N120 G91 X-20.0 Y-10.0 L03 重复钻3次孔N130 M05 G28 G49 Z320.0 撤消刀具长度补偿回Z轴N140 M01 参考点N150 M99 P20 返回到N20程序段程序的特点:1)使用G92建立加工坐标系,坐标系的偏置量在程序中进行设置,修改调整更方便。
2)有两次自动换刀,并使用刀具长度补偿,体现加工中心自动加工的功能。
机床起动后主轴上装的是F 10钻头刀具,刀库的零号刀位上应安装有中心钻。
因整个程序只用两把刀,刀库不用转动,原地换刀就可以了。
3)使用中心钻(N60程序段)预钻定位孔,使孔定位准确。
4)使用相对值指令(N70,N120)给出了孔的位置,使固定循环功能重复使用,直到把孔全部钻完。
L03为重复次数。
5)使用了M01(N140)程序暂停。
注意:使用M01时操作面板上的程序暂停开关应放到接通位置,这样在程序执行到M01时面板上的指示灯燃亮,告诉操作者程序处于任选停止,可以装卸零件,待处理工作结束时按循环起动按钮,程序接着执行。
零件加工程序的编制
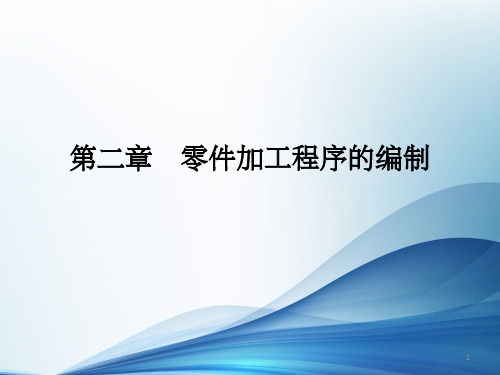
工件原点
Y轴 Z轴
X轴
Z轴偏置量
Y 轴 偏 置 量
X轴偏置量
机床原点
工件原点
立式数控机床的坐标系
卧式数控机床的坐标系
51
二 坐标系
➢设定工件坐标系指令:G54 G55 G56 G57 G58 G59 G59.1 G59.2 G59.3
52
二 坐标系
图2-8 设定工件坐标系举例
53
二 坐标系
图2-9 机床坐标关系
18
二 数控机床的编程方法
自动编程: 定义:编程人员根据零件图纸的要求,按照某个自动编程 系统的规定,将零件的加工信息用较简便的方式送入计算 机,编程系统将能根据数控系统的类型输出数控加工程序。 适用: ① 形状复杂的零件 ② 虽不复杂但编程工作量很大的零件(如有数 千个孔的零件) ③ 虽不复杂但计算工作量大的零件(如非圆曲 线轮廓的计算)
9
一 数控机床程序编制的内容和步骤
铣内圆轮廓,路线为1→A→2→3(偏心圆)→B→4(工件轮廓)→B→5 (偏心圆)→C→6→1。
非圆曲线平面轮廓的铣削同样要切入和切出延伸。
10
一 数控机床程序编制的内容和步骤
铣削内轮廓表面时,切入和切出无法外延,这时铣刀可沿 零件轮廓的法线方向切入和切出,并将其切入、切出点选在零件轮 廓两几何元素的交点处。
Δ c为圆整误差,它表示在编程中,因数据处理、小数圆整而 产生的误差,为减小误差值,一般采用“累计进位法”代替传统的四舍 五入法,可避免产生累积误差。
15
一 数控机床程序编制的内容和步骤
(二)数学处理 先建立一个工件坐标系,根据图纸的要求,计
算出刀具的运动轨迹。 (三)编写零件程序清单
加工路线和工艺参数确定后,编写程序清单。 (四)程序输入
加工中心程序的编制及操作

加工中心程序的编制及操作FANUCSeriesoiMate-MD一、加工中心的结构特点和编程特点VMC系列机床是由CNC(计算机数控装置)控制切削加工的立式加工中心,可进行钻孔、铣削和攻丝等。
VMC680e数控加工中心是配备FANUC系统的三坐标轴CNC数控镗铣床,该加工中心符合ISO标准,适用于中小板材、盘件、壳体零件、模具等复杂零件的加工。
本加工中心可控轴数X\Y\Z三轴;位移脉冲当量0.001mm或0.0001in;最大位移量±999.99mm或999.9999in;数据输入方式为增量方式或绝对方式;准备功能指令GOO~G04、G17~G19、G28、G40~G44、G54~G59、G80~G89、G90、G91,其中G28位自动返回参考点指令,换刀程序段必须用词指令。
辅助功能指令有M00~M09、M17~M19、M30。
1VMC(1)(2)(3)2(1)(2)(3)(4)P1(-50,-50)图(1)%*O0000*N100G21*G54,N124G0Z50.*刀具快速提至安全高度N126M5*主轴停N128G91G28Z0.M9*增量值编程,Z轴返回参考点,关闭冷却液N130G28X0.Y0.*X、Y轴返回参考点(由于没有第四轴这里必须删除A0.)N132M30*程序结束%*下一程序开始二、加工中心的面板及操作(14) (15)(17)(19)(23) (25)(26) (31)功能键(1)按此按键显示位置画面。
(2)按此键显示程序画面。
(3)按此键显示刀偏/设定(SETTING)画面(4)按此键显示系统画面。
(5)按此键显示信息画面。
(44) (45) (46) (47) (48)(49)(54)(57) (58) (60) (61) (62)(6)按此键显示用户宏画面(会话式宏画面)或显示图形画(7)“E-STOP”急停按钮按下后切断主轴及伺服系统电源,控制系统复位。
故障排除后旋转该开关,使其释放。
数控编程的内容及步骤

(6)程序检验 常用的校验方法有人工法、加工仿
真法、空运行法等。
(7)首件试切 首件试切主要用于发现加工误差,并分
析加工误差产生的原因,加以修正。
数控实训
精度及毛胚形状和热处理的分析,确定 工件在数控机床上进行加工的可行性。
(2)确定工艺过程 工艺过程的内容包括确定工件的定
位基准、选用夹具、确定对刀方式和选 择对刀点、制定进给路线并确定加工余 量、切削参数等。
(3)数学处理 工艺方案确定后,就要根据零件的
几何尺寸和加工路线,计算数控加工所 需的编程数据,如计算零件轮廓中的关 键交点、切点等的坐标。
分析零件图纸,确定工艺方案,进 行数学处理,编写程序单,制备控制介 质及程序校验等。其具体步骤如图3.1所 示:
图3.1 数控机床程序编制的步骤
2)程序编制的步骤 :
分析工件图样 确定工艺过程
数学处理 编写零件加工程序单
首件试切 程序检验 制备控制介质
(1) 分析工件图样 通过对工件的材料、形状、尺寸、
数控实训
数控编程的内Байду номын сангаас及步骤
数控编制:是指在数控机床上加工零件 时,根据零件图样的要求,将加工零件 的全部工艺过程及工艺参数、位移数据、 辅助运动,以规定的指令代码及程序格 式编写成加工程序,经过调试后记录在 控制介质上,并用控制介质的信息控制 机床的动作,以实现零件的全部加工过 程。
1)零件加工程序编制的内容:
(4)编写零件加工程序单 准备好编程数据后,下一步需编写
零件加工程序单。
编写程序单之前必须了解数控机床 的性能、编程指令以及数控加工过程, 才能编写出正确、合理的加工程序。
(5)制备控制介质 通常将编写好的程序单记录在控制
数控加工的程序编制
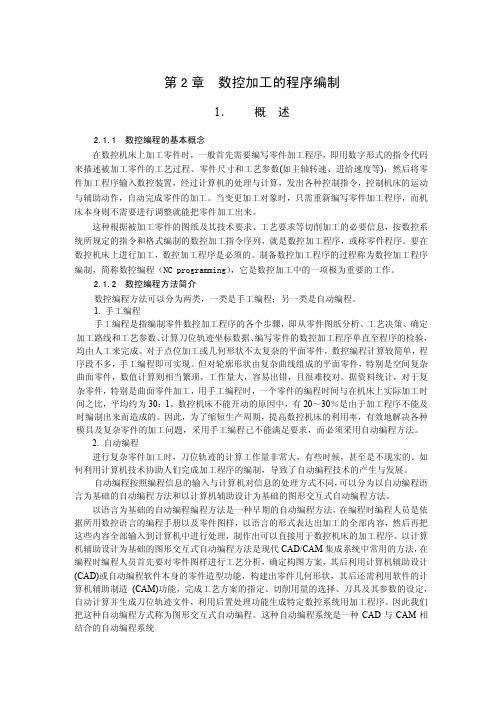
第2章 数控加工的程序编制1.概述2.1.1 数控编程的基本概念在数控机床上加工零件时,一般首先需要编写零件加工程序,即用数字形式的指令代码来描述被加工零件的工艺过程、零件尺寸和工艺参数(如主轴转速、进给速度等),然后将零件加工程序输入数控装置,经过计算机的处理与计算,发出各种控制指令,控制机床的运动与辅助动作,自动完成零件的加工。
当变更加工对象时,只需重新编写零件加工程序,而机床本身则不需要进行调整就能把零件加工出来。
这种根据被加工零件的图纸及其技术要求、工艺要求等切削加工的必要信息,按数控系统所规定的指令和格式编制的数控加工指令序列,就是数控加工程序,或称零件程序。
要在数控机床上进行加工,数控加工程序是必须的。
制备数控加工程序的过程称为数控加工程序编制,简称数控编程(NC programming),它是数控加工中的一项极为重要的工作。
2.1.2 数控编程方法简介数控编程方法可以分为两类,一类是手工编程;另一类是自动编程。
手工编程1.手工编程是指编制零件数控加工程序的各个步骤,即从零件图纸分析、工艺决策、确定加工路线和工艺参数、计算刀位轨迹坐标数据、编写零件的数控加工程序单直至程序的检验,均由人工来完成。
对于点位加工或几何形状不太复杂的平面零件,数控编程计算较简单,程序段不多,手工编程即可实现。
但对轮廓形状由复杂曲线组成的平面零件,特别是空间复杂曲面零件,数值计算则相当繁琐,工作量大,容易出错,且很难校对。
据资料统计,对于复杂零件,特别是曲面零件加工,用手工编程时,一个零件的编程时间与在机床上实际加工时间之比,平均约为30:1。
数控机床不能开动的原因中,有20~30%是由于加工程序不能及时编制出来而造成的。
因此,为了缩短生产周期,提高数控机床的利用率,有效地解决各种模具及复杂零件的加工问题,采用手工编程已不能满足要求,而必须采用自动编程方法。
2. 自动编程进行复杂零件加工时,刀位轨迹的计算工作量非常大,有些时候,甚至是不现实的。
数控车床的程序编制步骤
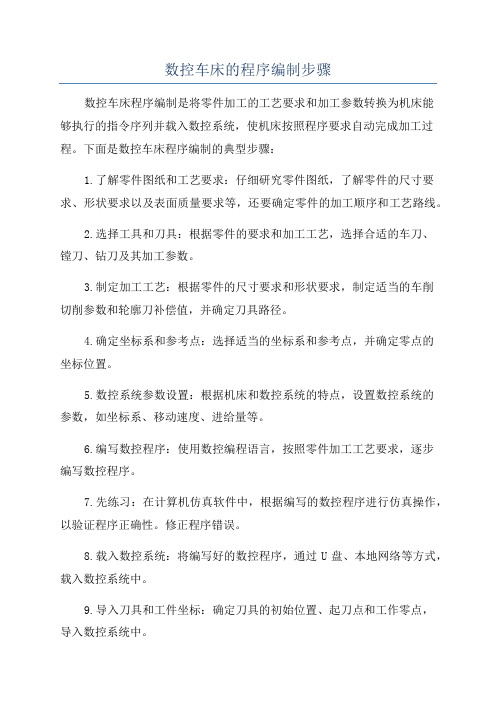
数控车床的程序编制步骤数控车床程序编制是将零件加工的工艺要求和加工参数转换为机床能够执行的指令序列并载入数控系统,使机床按照程序要求自动完成加工过程。
下面是数控车床程序编制的典型步骤:1.了解零件图纸和工艺要求:仔细研究零件图纸,了解零件的尺寸要求、形状要求以及表面质量要求等,还要确定零件的加工顺序和工艺路线。
2.选择工具和刀具:根据零件的要求和加工工艺,选择合适的车刀、镗刀、钻刀及其加工参数。
3.制定加工工艺:根据零件的尺寸要求和形状要求,制定适当的车削切削参数和轮廓刀补偿值,并确定刀具路径。
4.确定坐标系和参考点:选择适当的坐标系和参考点,并确定零点的坐标位置。
5.数控系统参数设置:根据机床和数控系统的特点,设置数控系统的参数,如坐标系、移动速度、进给量等。
6.编写数控程序:使用数控编程语言,按照零件加工工艺要求,逐步编写数控程序。
7.先练习:在计算机仿真软件中,根据编写的数控程序进行仿真操作,以验证程序正确性。
修正程序错误。
8.载入数控系统:将编写好的数控程序,通过U盘、本地网络等方式,载入数控系统中。
9.导入刀具和工件坐标:确定刀具的初始位置、起刀点和工作零点,导入数控系统中。
10.设置工件坐标系:根据图纸和实际加工需求,设置工件坐标系和坐标偏移。
11.调试程序:使用手动操作或自动操作,对数控系统进行调试,确保程序的安全性和准确性。
12.加工实践:进行实际加工操作,监控加工过程中各项参数的变化,并及时调整。
13.检验零件:完成加工后,根据图纸要求进行零件的测量和检验,确保零件质量满足要求。
14.优化程序:根据实际加工情况,调整和优化数控程序,提高加工效率和质量。
15.存档和备份:将编写好的数控程序进行保存和备份,以备后续使用。
总结起来,数控车床程序编制是一项精细的工作,需要熟悉机床、工具和数控系统的基本原理,同时要具备良好的图纸分析和数控编程能力。
通过以上步骤的严格执行,可以确保数控车床加工过程的准确性和安全性。
模块五(项目四)孔类零件.
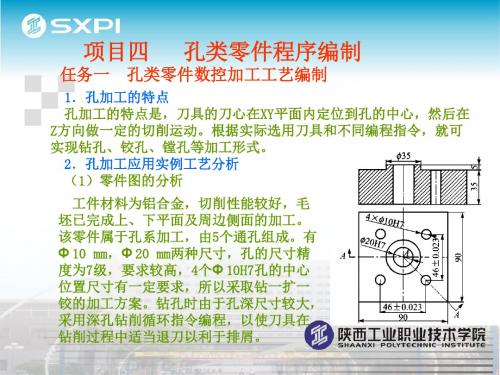
③用Φ 10mm的机用铰刀精铰 4 ×Φ 10 mm的孔至尺寸要求;
④用Φ 13mm的麻花钻将Φ 20mm的孔粗钻至Φ 13mm; ⑤用Φ 19.8mm的麻花钻将Φ 20mm的孔粗钻至Φ 19.8mm;
⑥用Φ 20H7的机用铰刀精铰Φ 20mm的孔至尺寸要求。4个Φ 20 mm孔加工 于XY平面的进给路线,如图所示。
(2)刀具及切削用量的确定 刀具选择:T2:Φ 3 mm的高速钢中心钻,T3:Φ 9.8 mm的高速钢 麻花钻,T4:Φ 10H7的机用铰刀,T5:Φ 13mm高速钢麻花钻,T6: Φ 19.8mm麻花钻,T7:Φ 20H7机用铰刀 (3)工件装夹 选择毛坯底面和两侧面为定位平面,其中底面为主定位面,采用 等高垫铁在平口虎钳口上装夹定位或直接将工件毛坯放在工作台上, 用等高垫铁将工件托起,再用百分表找正工件两侧面进行安装定位, 最后用压板螺母、螺栓、垫圈等元件将工件夹紧。
3.编写加工程序 用 FANUC 0i-MB数控系统的指令及规则编写的加工程序如下:
O3001; N0010 G21; N0020 G17 G40 G49 G69 G80 G90 ; N0030 G54; N0040 T2M6; N0050 S1400 M03; N0060 G00 XO YO ; N0070 G43 G00 Z50 H02; N0080 G00 Z10; N0090 G99 G81 X0 YO Y0 Z-5 R5 F50; N0100 X23 Y23 Z-10 R2; N0110 X-23;N0120 Y-23; N0130 G98 X23; N0140 G80; N0150 GO0 Z50;
N0160 N0170 N0180 N0190 N0200 N0210 N0220 N0230 N0240 N0250 N0260 N0270 N0280 N0290 N0300 N0310 N0320 N0330 N0340 N0350
机床数控技术第3章数控加工程序的编制
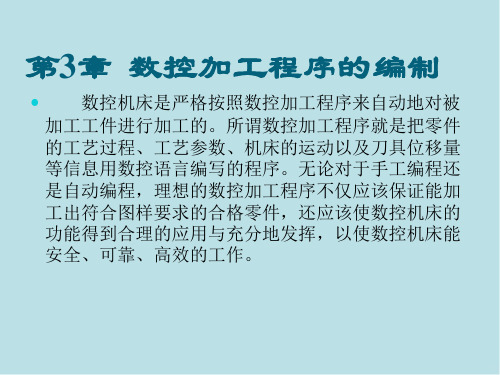
6. 程序校验和首件试切
程序送入数控系统后,通常需要经过试运行和首 件试切两步检查后,才能进行正式加工。通过试运行, 校对检查程序,也可利用数控机床的空运行功能进行 程序检验,检查机床的动作和运动轨迹的正确性。对 带有刀具轨迹动态模拟显示功能的数控机床可进行数 控模拟加工,以检查刀具轨迹是否正确;通过首件试 切可以检查其加工工艺及有关切削参数设定得是否合 理,加工精度能否满足零件图要求,加工工效如何, 以便进一步改进,直到加工出满意的零件为止。
1—脚踏开关 2—主轴卡盘 3—主轴箱 4—机床防护门 5—数控装置 6—对刀仪 7—刀具8—编程与操作面板 9—回转刀架 10—尾座 11—床身
3.2 数控车削加工程序编制
数控车床主要用来加工轴类零件的内外圆柱面、 圆锥面、螺纹表面、成形回转体表面等。对于盘类零 件可进行钻、扩、铰、镗孔等加工。数控车床还可以 完成车端面、切槽等加工。
3. 程序名
FANUC数控系统要求每个程序有一个程序名,
程序名由字母O开头和4位数字组成。如O0001、 O1000、O9999等
3.2.3 基本编程指令
1. 快速定位指令G00
格式:G00 X(U)_ Z(W)_;
说明:
(1) G00指令使刀具在点位控制方式下从当前点以快移速度 向目标点移动,G00可以简写成G0。绝对坐标X、Z和其增 量坐标U、W可以混编。不运动的坐标可以省略。
3.2.1 数控车床的编程特点
(1)在一个程序段中,可以用绝对坐标编程,也可用 增量坐标编程或二者混合编程。
(2)由于被加工零件的径向尺寸在图样上和在测量时 都以直径值表示,所以直径方向用绝对坐标(X)编程时 以直径值表示,用增量坐标(U)编程时以径向实际位移 量的2倍值表示,并附上方向符号。
加工中心的孔加工编程及技巧

《加工中心的孔加工编程及技巧》2005年5月25日加工中心的孔加工编程及技巧摘要:孔加工在数控加工中一直占有重要的地位,如何在加工过程中按照合理的工艺编制出正确的加工程序是非常关键的因素。
关键词:孔加工固定循环子程序极坐标一、引言孔加工在数控加工中一直占有重要的地位。
在合理的加工工艺编制好以后如何编制出正确的程序将直接影响到工件是否加工合格。
复杂的孔加工将用到数控系统中的许多功能。
诸如:孔加工固定循环、子程序、极坐标、坐标旋转等。
因此,如何将这些指令灵活应用在加工的程序中将直接关系到程序的合理性。
二、应用实例下面就以一个定位连接板(图1)作为实例,介绍该类程序的编制及技巧。
1、技术要求:1)零件材料:灰铸铁HT2002)加工部位:加粗部分(φ110,2-φ70H7),8-M12深15,18-φ13深20。
3)加工说明:φ70H7预孔为铸造,余量5mm。
基准面A、B、C、D前工序已完成。
夹具形式不用考虑,φ110孔用铣削方式。
4)数控机床:立式加工中心VMC800;数控系统:FANUC 0iM5)按数控工序卡片编制加工中心程序。
6)程序编制方法:固定循环、子程序、坐标系旋转、极坐标指令等图1 定位连接板2、加工工艺3、加工程序主程序O0001;第0001号程序,加工主程序;建立工件坐标系,并运动到φ70H7孔的中心位置N10T02M6;调用02号刀具(粗镗φ);刀具长度正补偿,并运动到安全高度M03S380;主轴正转M08;打开冷却液;调用粗加工固定循环加工φ70H7孔至φ;在位置继续加工G80;取消固定循环N20T03M6;调用03号刀具(φ40立铣刀铣φ110孔);快速定位到φ110孔的中心位置;刀具长度正补偿,并运动到安全高度M3S420;主轴正转;下刀至第一次的深度位置(粗加工)M98P0501;调用0501号子程序S560;下刀至第二次的深度位置(半精加工)M98P0501;调用0501号子程序M01;检查尺寸。
第二章 数控加工的程序编制

㈤附加坐标系——是指与基本坐标系平行的坐标系。规范规则有两组: 第一组为:U、V、W 其正方向与X、Y、Z相反。 第二组为:P、Q、R 其正方向与X、Y、Z相反。
㈥机床坐标系与工件坐标系 机床坐标系——是数控机床固有的坐标系。其坐标轴的方向和原点是
机床设计时或调试时确定的。是独一的,不可以改动的。 工件坐标系——是加工工件时,由编程人员确定的。该坐标系的坐标
②顺序恢复运转同M00相反〔按下〝循环启动〞键〕
③该指令的运用场所:在加工中随机要使机床中止运动而 要停止某种手动操作的场所。如:随即抽查零件的关键 尺寸。
④停机和恢复顺序都是经过硬件开关来完成的。
〔3〕、M02——顺序完毕指令〔机床中止运动〕
①该指令的功用:是当顺序全部运转终了后,用此指令来 使主轴、进给、冷却全部中止。同时使机床复位,使顺 序前往〝末尾形状〞。
第二种——是与顺序段指令运动完成后末尾〔第3栏中用 〝*〞表示的〕。
5、M代码也有〝不指定〞和〝永不指定〞用来作为机动。 留给用户〔CNC制造商和机床用户〕自行定义新的功用。 但要在运用说明书上说明。
6、几个特殊的M代码 〔1〕M00—顺序中止指令〔暂停〕 ①该顺序的实质:是设定了一个软件〝开关〞,当顺序运
算的。 相对坐标〔増量坐标〕——是指刀具运动的坐标值都是相对运动轨迹
的前一点的坐标计算的。 A、B点的相对坐标:XA=30.0 YA=35.0
XB=12.0 YB=15.0 B点的相对坐标:XB=-18.0 YB=-20.0 ㈧主轴的正转与反转判定 判定方法:用右手螺旋定那么 将右手大姆指顺着主轴指向 工件,四指盘绕主轴轴线。
轴与机床坐标系相平行,坐标轴的方向与机床坐标系相反。工件坐 标系的原点是编程人员为了编程的方便在图纸上
- 1、下载文档前请自行甄别文档内容的完整性,平台不提供额外的编辑、内容补充、找答案等附加服务。
- 2、"仅部分预览"的文档,不可在线预览部分如存在完整性等问题,可反馈申请退款(可完整预览的文档不适用该条件!)。
- 3、如文档侵犯您的权益,请联系客服反馈,我们会尽快为您处理(人工客服工作时间:9:00-18:30)。
四、拓展知识
采用钻孔方式加工3个底孔,然后分别对这些孔进行镗孔、铰孔和攻丝加工。
其程序如下:
AA310.MPF;
主程序
G54 G90 G17 G94 G40;
三、工作任务的完成
(一)数控加工工艺的制订
4.刀具准备,填写刀具卡
序号
1 2 3
4
5 6 7
刀具号
T05 T06 T07
名称 麻花钻 麻花钻 镗刀
T08 镗刀
T09 中心钻 T10 机用铰刀 T11 麻花钻
刀具规格 直径
Φ11.8mm Φ35mm Φ37.5mm
Φ38mm
Φ3mm Φ12mm Φ20mm
(三)工作任务2:螺纹孔加工
1. 任务说明 该工件材料为45#钢,切 削性较好,毛坏已完成上、 下表面及周边侧面的加工, 在本次任务中完成10-M5 螺纹通孔的加工,该螺纹 为右螺纹,如图所示。
三、工作任务的完成
(三)工作任务2:螺纹孔加工
2.攻螺纹循环(G74、G84) (1)右旋螺纹加工循环(G84) 指令格式: G84 X_Y_Z_R_ F_ 从R点到Z点攻丝时,刀具正向进给,主轴正转。到孔 底部时,主轴反转,刀具以反向进给速度退出。G84 指令中进给倍率不起作用;进给保持只能在返回动作 结束后执行。 注意:进给速度F=转速(r/min)×螺矩(mm)
(3)加工工艺与路线设计: 根据该加工内容和图纸要求,螺纹位有一定要求、孔进 行攻丝。故工艺可选为:
钻中心孔→钻孔→攻丝。 (4)工件原点设定:
由于工件为对称圆柱形结构,为简化编程,工件原点 设定在工件中心上表面处。
三、工作任务的完成
(三)工作任务2:螺纹孔加工
(5)零件螺纹孔工序清单
序号 加工内容
N30 G99 G84 X30.0 Y40.0 Z-22.0 R10.0 F150
N40 X90.0
N50 X60.0 Y90.
N70 G80 Z50. N80 M30
G84编程举例
三、工作任务的完成
(三)工作任务2:螺纹孔加工
(2)左旋螺纹加工循环(G74) 指令格式: G74 X_Y_Z_R_ F_ G74 指令用于切削左旋螺纹孔。主轴反转进刀,正转退刀。
在孔底的动作 ───
停刀→主轴正转 主轴定向停止
─── ─── 暂停 ─── 暂停—主轴反转 ─── 主轴停止 主轴正转 暂停→主轴停止 暂停
回退(+Z方向) 快速移动 切削进给 快速移动 ─── 快速移动 快速移动 快速移动 切削进给 切削进给 快速移动 快速移动 手动移动 切削进给
应用 高速深孔钻循环 左旋攻丝循环 精镗循环 取消固定循环 钻孔、点钻循环 钻孔、锪镗循环 深孔钻循环 攻丝循环 镗孔循环 镗孔循环 背镗循环 镗孔循环 镗孔循环
固定循环的动作
二、相关知识
(二)固定循环功能
2.固定循环的几个平面
固定循环的几个平面
孔加工的返回方式
二、相关知识
(二)固定循环功能
3.固定循环指令
G代码 G73 G74 G76 G80 G81 G82 G83 G84 G85 G86 G87 G88 G89
钻削(-Z方向) 间歇进给 切削进给 切削进给 ─── 切削进给 切削进给 间歇进给 切削进给 切削进给 切削进给 切削进给 切削进给 切削进给
二、相关知识
(一)孔加工工艺知识
孔的加工方法与步骤的选择
序号 加工方案
1钻 2 钻—铰 3 钻—粗铰(扩)—精铰 4 钻—扩 5 钻—扩—铰 6 钻—扩—粗铰—精铰 7 粗镗(扩孔) 8 粗镗(扩孔) —半精镗(精
扩) 9 粗镗(扩) —半精镗(精
扩) —精镗
精度等 级 11~13 9 7~8 11 8~9 7 11~13
G74循环
三、工作任务的完成
(三)工作任务2:螺纹孔加工
3. 工作任务2的完成 (1)刀具的选择: 由于 孔系的位置也有一定要求,故选用 T1:A4中心钻 T2:φ4.2mm T3:M5mm细牙丝锥 (2)夹具及装夹方式的选择:
由于工件毛坯为圆柱形,决定采用1台三爪卡盘。
三、工作任务的完成
(三)工作任务2:螺纹孔加工
(二)固定循环功能
(2)带停顿的钻孔循环(G82) 指令格式:
G82 X_Y_Z_P_R_F_
G82循环
该指令除了要在孔底暂停外,其它动作与G81相同。暂 停时间由地址P给出。此指令主要用于加工盲孔,以提 高孔深精度。
二、相关知识
(二)固定循环功能
(3)断屑式深孔加工循环(G73)
指令格式: G73 X_Y_Z_Q_R_F_
材料
高 速 钢
硬质合 金
高 速 钢
刀具补偿
长度
半径
H05
H06
H07
H08
H09 H10 H11
三、工作任务的完成
(一)数控加工工艺的制订
a)直柄麻花钻 b)锥柄麻花钻 c)粗镗刀
d)粗镗刀 e)中心钻
f)铰刀
g)麻花钻
三、工作任务的完成
(一)数控加工工艺的制订
5.编排加工工艺,填写工序卡
工步号
二、相关知识
(二)固定循环功能
G76循环
二、相关知识
(二)固定循环功能
(6)背镗孔(G87) 指令格式: G87 X_ Y_ Z_ R_ Q_ F_
刀具运动到孔中心位置后,主轴定向停止 然后向刀尖相反方向偏移Q值,然后快速运动 到孔底位置,接着返回前面的位移量,回到孔 中心,主轴正转,刀具向上进给运动到Z点,主 轴又定向停止,然后向刀尖相反方向偏移Q值, 快退。刀具返回到初始平面,再返回一个位移 量,回到孔中心,主轴正转,继续执行下一段 程序。
G87循环
三、工作任务的完成
(一)数控加工工艺的制订
1.选定毛坯
使用的练习毛坯尺寸为160mm×120mm×30mm,已完成上、下表 面及周边侧面的加工,并符合尺寸与表面粗糙度要求。
2.夹具选择
该零件可选用加工中心通用夹具――平口虎钳进行装夹。
3. 加工工艺与路线设计
(1)Φ12mm孔的孔位有一定要求、孔径公差、粗糙度要求比较高。 故工艺可选为:钻中心孔→钻孔→铰孔。 (2)Φ20mm孔孔径为自由公差,故直接钻孔加工。 (3)Φ38mm孔的孔径公差、粗糙度要求比较高。故工艺可选为: 钻孔→扩孔→粗镗孔→精镗孔。
机用铰
T10 刀
300
钻孔加工
8
Φ20mm孔
T11 麻花钻
150
进给量 (mm/r)
80 20 80
40
120
80
50
30
背吃刀量 (mm)
三、工作任务的完成
(二)编写数控加工程序
1.确定工件坐标系 在Φ38mm孔中心建立工件坐标系,Z轴原点设在顶面上。 2.根据加工工艺编写程序
三、工作任务的完成
三、工作任务的完成
(三)工作任务2:螺纹孔加工
G84右螺纹攻丝循环
三、工作任务的完成
(三)工作任务2:螺纹孔加工
例:编写如图所示螺纹孔(右旋螺纹)的加工程序(设Z
轴开始点距工作表面10mm处,切削深度为20mm)。
攻丝加工程序如下:
O2002
N10 G54 M03 S100
N20 G00 Z50. M08
0.5D
20~40
0.15~0.25
0.5D
40~60
Байду номын сангаас
0.05~0.20
0.5D
45~90
0.05~0.40
≤2.5
6~12
0.3~1
0.10~0.30
6~12
P
0.5P
80~250
0.10~0.50
0.5~2.0
80~250
0.05~0.30
0.3~1
二、相关知识
(一)孔加工工艺知识
孔加工消除间隙方法进给路线
工步内容
刀具号 刀具名 主轴转速
称
(r/min)
1
钻Φ38mm孔
T05 麻花钻
550
2
扩Φ38mm孔
T06 麻花钻
150
粗镗
3
Φ38mm孔
T07 镗刀
850
精镗
4
Φ38mm孔
T08 镗刀
1000
点钻加工
5
Φ12mm孔
中心钻 T09
1200
钻孔加工
6
Φ12mm孔
麻花钻
T05
550
铰孔加工
7
Φ12mm孔
二、相关知识
(二)固定循环功能
1)孔循环取消(G80) 指令格式:G80 取消所有孔加工固定循环模态。 2)钻孔加工循环(G81、G82、G73、G83) (1)钻孔、点钻循环(G81) 指令格式:
G81 X_Y_Z_R_F_
G81循环
二、相关知识
(二)固定循环功能
例1. 编写如图所示孔的加工程序(设Z轴开始点距工作表面5mm处,切
孔加工导入量与超越量
超越量ΔZ‘:
当钻通孔时,通常取ZP+(1~3)mm,ZP为钻尖高度(通常取0.3倍钻 头直径);
铰通孔时,通常取3~5 mm;
镗通孔时,通常取1~3 mm。 导入量ΔZ通常取2~5mm。
二、相关知识
(二)固定循环功能
1.固定循环六个动作 常用的固定循环指令能完成的工作有:钻孔、攻螺纹和 镗孔等。 1)在XY 平面定位 2)快速移动到R点平面 3)孔的切削加工 4)孔底动作 5)返回到R点平面 6)返回到起始点。
G88循环
二、相关知识
(二)固定循环功能
(5)精镗循环(G76) 指令格式: G76 X_ Y_ Z_ R_ Q_ F_