转炉炼钢流程中的脱磷工艺
铁水转炉吹氧脱磷工艺-概述说明以及解释

铁水转炉吹氧脱磷工艺-概述说明以及解释1.引言1.1 概述铁水转炉吹氧脱磷工艺是钢铁生产中常用的一种去除磷元素的工艺方法。
在铁水中磷元素的含量对钢铁的性能有着重要影响,因此需要采取相应措施进行去除。
吹氧脱磷工艺通过向铁水中吹入氧气,利用氧气与磷元素的化学反应,在高温条件下将磷元素氧化移除,从而减少磷元素含量,提高钢铁的质量和性能。
本文将详细介绍铁水转炉吹氧脱磷工艺的原理、步骤以及其在钢铁生产中的应用。
通过对该工艺的深入探讨,可以更好地了解吹氧脱磷的作用机制和优势,为钢铁生产提供技术支持和参考。
1.2 文章结构1.3 目的本文旨在深入探讨铁水转炉吹氧脱磷工艺,通过对该工艺的原理、步骤、优势以及应用前景进行分析,旨在说明吹氧脱磷工艺在钢铁生产中的重要性和价值。
同时,通过总结工艺的特点和优势,为相关行业提供参考,促进该工艺的广泛应用,提高生产效率,降低成本,推动钢铁行业的可持续发展。
2.正文2.1 铁水转炉工艺概述:铁水转炉是一种用于炼钢的高炉,它是一种旋转的容器,通常由耐火材料和金属外壳构成。
在钢铁冶炼过程中,铁水转炉扮演着至关重要的角色。
铁水转炉工艺通常用于生产高品质的钢铁,其主要特点是操作简单,生产效率高,并能够满足不同规格和质量要求的钢铁生产。
在铁水转炉中,主要通过向铁水中吹入氧气使其氧化,从而提高炉内温度,促使不同元素的相互作用,达到脱除杂质的目的。
铁水转炉通常配有各种喷嘴和氧气喷嘴,以确保充分的氧化反应和高效的燃烧过程。
铁水转炉工艺的优点包括:1. 生产效率高:铁水转炉可以持续生产,操作简单,生产效率高。
2. 能够生产高品质钢铁:通过吹氧脱磷等工艺,可以去除杂质,生产高品质的钢铁。
3. 适用范围广:铁水转炉可以生产各种规格和质量要求的钢铁,适用性广泛。
总的来说,铁水转炉工艺在钢铁冶炼领域具有重要的地位,其优点包括高效、高质以及适用范围广泛,为钢铁行业的发展做出了重要贡献。
2.2 吹氧脱磷的原理2.3 吹氧脱磷的步骤:吹氧脱磷是铁水转炉炼钢过程中的关键环节之一,其步骤主要包括以下几个方面:1. 吹氧开始: 在铁水转炉底部喷入高纯度氧气,形成氧吹。
转炉熔渣气化脱磷循环炼钢关键技术开发及应用

转炉熔渣气化脱磷循环炼钢关键技术开发及应用转炉熔渣气化脱磷循环炼钢关键技术开发及应用近年来,随着工业化进程的不断发展,钢铁行业作为重要的基础产业之一,对环境保护和资源利用提出了更高的要求。
炼钢过程中的熔渣是一种含有大量磷元素的高温废弃物,若不能有效处理,将对环境造成严重的污染。
为了解决这一问题,转炉熔渣气化脱磷循环炼钢技术应运而生。
本文将深入探讨该技术的关键技术开发及应用。
一、转炉熔渣气化脱磷循环炼钢技术的概念与原理转炉熔渣气化脱磷循环炼钢技术是一种通过将炼钢过程中产生的熔渣进行气化处理,将熔渣中的磷元素转化为磷酸氢盐,并通过回收再利用的方式达到脱磷的目的的一种技术。
该技术主要包括气化反应、循环过程和脱磷回收等关键步骤。
在气化反应阶段,炼钢转炉熔渣经过预处理后注入气化炉中,与高温气体发生反应,产生气体燃料和磷酸氢盐。
这一阶段实质上是一种高温熔融质和气体的化学反应过程,需要掌握适当的气化温度和反应剂的选择。
在循环过程中,磷酸氢盐在炉内高温环境中发生水解反应,释放出磷酸和H2O。
磷酸部分被回收,用于炼钢过程中的脱磷处理,而水分则通过水蒸汽的形式排出。
这一过程实质上是一种有效的循环利用,使得磷元素得到了最大程度的回收再利用。
在脱磷回收阶段,磷酸与转炉熔渣中的磷元素发生反应,形成难溶性的磷酸盐,并通过物理分离的方式进行回收。
脱磷回收的效率与磷酸的浓度、反应时间和反应温度等因素密切相关,要实现高效的脱磷回收,需要综合考虑这些因素的影响。
二、转炉熔渣气化脱磷循环炼钢技术的关键技术开发转炉熔渣气化脱磷循环炼钢技术的关键技术开发主要包括反应器设计、催化剂研发、废气处理以及磷酸盐回收等方面。
反应器设计是该技术的核心环节。
反应器设计需要考虑到温度、压力、反应物料的流动性以及反应过程中产生的废气排放等因素,以确保反应器能够稳定运行,同时兼顾能效和安全性。
催化剂的研发对于反应过程中的效率和选择性具有重要影响。
催化剂的选择应考虑到催化活性、选择性和稳定性等因素,以提高反应速率和产物质量,并减少不良反应的产生。
顶吹转炉脱磷热力学分析和工艺优化
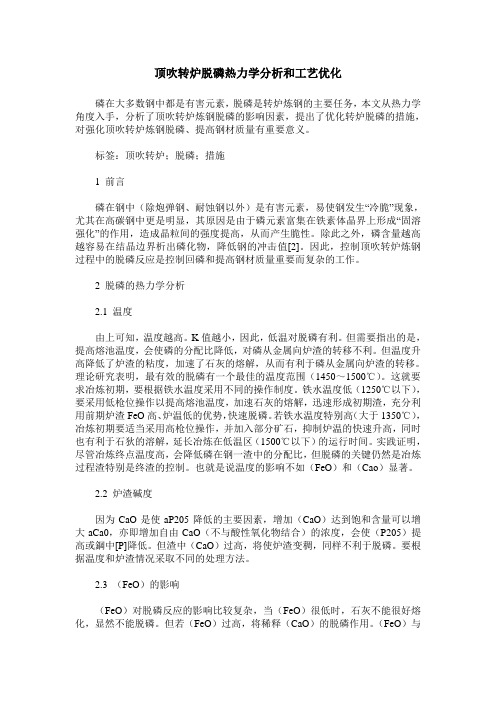
顶吹转炉脱磷热力学分析和工艺优化磷在大多数钢中都是有害元素,脱磷是转炉炼钢的主要任务,本文从热力学角度入手,分析了顶吹转炉炼钢脱磷的影响因素,提出了优化转炉脱磷的措施,对强化顶吹转炉炼钢脱磷、提高钢材质量有重要意义。
标签:顶吹转炉;脱磷;措施1 前言磷在钢中(除炮弹钢、耐蚀钢以外)是有害元素,易使钢发生“冷脆”现象,尤其在高碳钢中更是明显,其原因是由于磷元素富集在铁素体晶界上形成“固溶强化”的作用,造成晶粒间的强度提高,从而产生脆性。
除此之外,磷含量越高越容易在结晶边界析出磷化物,降低钢的冲击值[2]。
因此,控制顶吹转炉炼钢过程中的脱磷反应是控制回磷和提高钢材质量重要而复杂的工作。
2 脱磷的热力学分析2.1 温度由上可知,温度越高。
K值越小,因此,低温对脱磷有利。
但需要指出的是,提高熔池温度,会使磷的分配比降低,对磷从金属向炉渣的转移不利。
但温度升高降低了炉渣的粘度,加速了石灰的熔解,从而有利于磷从金属向炉渣的转移。
理论研究表明,最有效的脱磷有一个最佳的温度范围(1450~1500℃)。
这就要求冶炼初期,要根据铁水温度采用不同的操作制度。
铁水温度低(1250℃以下),要采用低枪位操作以提高熔池温度,加速石灰的熔解,迅速形成初期渣,充分利用前期炉渣FeO高、炉温低的优势,快速脱磷。
若铁水温度特别高(大于1350℃),冶炼初期要适当采用高枪位操作,并加入部分矿石,抑制炉温的快速升高,同时也有利于石狄的溶解,延长冶炼在低温区(1500℃以下)的运行时间。
实践证明,尽管冶炼终点温度高,会降低磷在钢一渣中的分配比,但脱磷的关键仍然是冶炼过程渣特别是终渣的控制。
也就是说温度的影响不如(FeO)和(Cao)显著。
2.2 炉渣碱度因为CaO是使aP205降低的主要因素,增加(CaO)达到饱和含量可以增大aCa0,亦即增加自由CaO(不与酸性氧化物结合)的浓度,会使(P205)提高或鋼中[P]降低。
但渣中(CaO)过高,将使炉渣变稠,同样不利于脱磷。
吹炼过程中的脱磷和脱硫
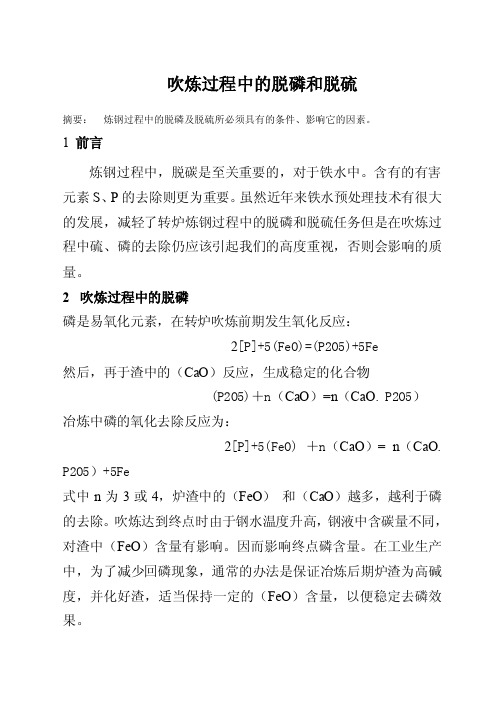
吹炼过程中的脱磷和脱硫摘要:炼钢过程中的脱磷及脱硫所必须具有的条件、影响它的因素。
1前言炼钢过程中,脱碳是至关重要的,对于铁水中。
含有的有害元素S、P的去除则更为重要。
虽然近年来铁水预处理技术有很大的发展,减轻了转炉炼钢过程中的脱磷和脱硫任务但是在吹炼过程中硫、磷的去除仍应该引起我们的高度重视,否则会影响的质量。
2吹炼过程中的脱磷磷是易氧化元素,在转炉吹炼前期发生氧化反应:2[P]+5(FeO)=(P2O5)+5Fe然后,再于渣中的(CaO)反应,生成稳定的化合物(P2O5)+n(CaO)=n(CaO. P2O5)冶炼中磷的氧化去除反应为:2[P]+5(FeO) +n(CaO)= n(CaO. P2O5)+5Fe式中n为3或4,炉渣中的(FeO)和(CaO)越多,越利于磷的去除。
吹炼达到终点时由于钢水温度升高,钢液中含碳量不同,对渣中(FeO)含量有影响。
因而影响终点磷含量。
在工业生产中,为了减少回磷现象,通常的办法是保证冶炼后期炉渣为高碱度,并化好渣,适当保持一定的(FeO)含量,以便稳定去磷效果。
为了去磷,吹炼过程中,应根据去磷的热力学条件,首先要搞好前期渣,尽快形成高氧化性的炉渣,以利于前期低温去磷。
而在吹炼后期要控制好炉渣碱度和渣中的(FeO),以利于后期高温、高碱度、高(FeO)脱磷。
当脱磷反应达到平衡时,用浓度来表示的平衡常数为:Kp= (P2O5)/[p]2(FeO)5(CaO)4常用磷在炉渣和金属中的分配比来表示脱磷能力,其表示方法很多。
常用L p=(P2O5)或Lp= (P2O5)/ [p].Lp越大,炼钢过程中脱磷能力也越大。
平衡常数和温度的关系:Lg=51875/T-33.16从脱磷反应的反应式、平衡常数及温度关系,可知影响脱磷的因素有:2.1炉渣碱度的影响。
由分配比公式可知:渣中的CaO越高,分配比越高,脱磷能力就越强。
CaO的脱磷作用在于:它能使P2O5生成稳定的磷酸钙。
转炉炼钢脱磷工艺理论与实践
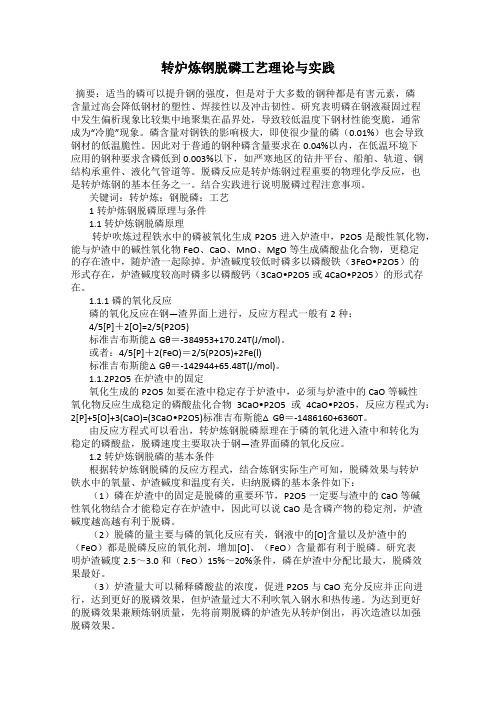
转炉炼钢脱磷工艺理论与实践摘要:适当的磷可以提升钢的强度,但是对于大多数的钢种都是有害元素,磷含量过高会降低钢材的塑性、焊接性以及冲击韧性。
研究表明磷在钢液凝固过程中发生偏析现象比较集中地聚集在晶界处,导致较低温度下钢材性能变脆,通常成为“冷脆”现象。
磷含量对钢铁的影响极大,即使很少量的磷(0.01%)也会导致钢材的低温脆性。
因此对于普通的钢种磷含量要求在0.04%以内,在低温环境下应用的钢种要求含磷低到0.003%以下,如严寒地区的钻井平台、船舶、轨道、钢结构承重件、液化气管道等。
脱磷反应是转炉炼钢过程重要的物理化学反应,也是转炉炼钢的基本任务之一。
结合实践进行说明脱磷过程注意事项。
关键词:转炉炼;钢脱磷;工艺1转炉炼钢脱磷原理与条件1.1转炉炼钢脱磷原理转炉吹炼过程铁水中的磷被氧化生成P2O5进入炉渣中,P2O5是酸性氧化物,能与炉渣中的碱性氧化物FeO、CaO、MnO、MgO等生成磷酸盐化合物,更稳定的存在渣中,随炉渣一起除掉。
炉渣碱度较低时磷多以磷酸铁(3FeO•P2O5)的形式存在,炉渣碱度较高时磷多以磷酸钙(3CaO•P2O5或4CaO•P2O5)的形式存在。
1.1.1磷的氧化反应磷的氧化反应在钢—渣界面上进行,反应方程式一般有2种:4/5[P]+2[O]=2/5(P2O5)标准吉布斯能△Gθ=-384953+170.24T(J/mol)。
或者:4/5[P]+2(FeO)=2/5(P2O5)+2Fe(l)标准吉布斯能△Gθ=-142944+65.48T(J/mol)。
1.1.2P2O5在炉渣中的固定氧化生成的P2O5如要在渣中稳定存于炉渣中,必须与炉渣中的CaO等碱性氧化物反应生成稳定的磷酸盐化合物3CaO•P2O5或4CaO•P2O5,反应方程式为:2[P]+5[O]+3(CaO)=(3CaO•P2O5)标准吉布斯能△Gθ=-1486160+6360T。
由反应方程式可以看出,转炉炼钢脱磷原理在于磷的氧化进入渣中和转化为稳定的磷酸盐,脱磷速度主要取决于钢—渣界面磷的氧化反应。
提高转炉冶炼前期脱磷效率的工艺操作
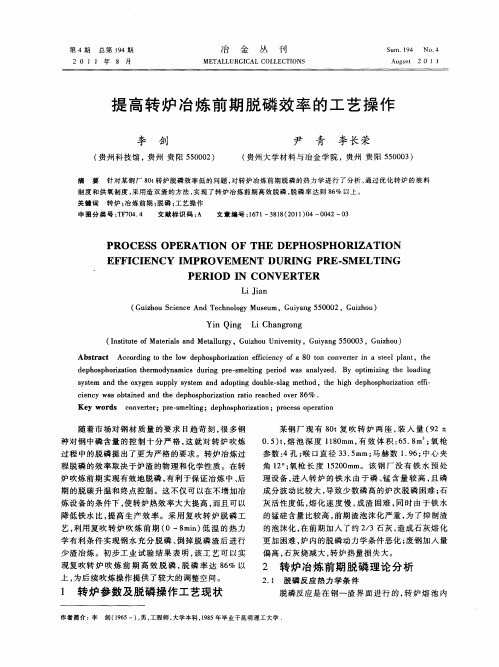
摘 要
尹 青
李 长 荣
( 贵州 大学材 料与 冶金 学院 , 州 贵 阳 5 0 0 ) 贵 5 0 3
针 对某 钢 厂 8 t 炉 脱 磷 效 率 低 的 问 题 , 转 炉 冶 炼 前 期脱 磷 的 热力 学 进 行 了 分 析 , 过 优 化 转 炉 的 装 料 0转 对 通
PRo CES S oPERATI oN F THE o DEPH o S PH o RI ZATI oN EFFI ENCY M PRo VEM ENT CI I DURI NG PRE. M ELTI S NG PERI oD N I CoNVERTER
L in iJa
程脱 磷 的效 率取决 于炉 渣 的物 理 和化学性 质 。在转
炉 吹炼前 期 实现 有效地脱 磷 , 有利 于保证 冶炼 中、 后
理 设备 , 进人 转炉 的 铁 水 由 于磷 、 含 量 较 高 , 磷 锰 且
期 的脱碳 升 温和 终点控 制 。这 不仅 可 以在不 增加 冶
炼设 备 的条 件下 , 使转 炉热效 率大 大提高 , 且可 以 而
极好 的优势 , 同时通 过 加 大前 期 熔 池 搅 拌 强 度 来 获
升高 , 铁水 中的碳 开始 氧化 , 此时 如果 炉 渣 中 的 F O e
钢 水 温度 。
熔 渣 中的 4 a P0 为 固态 , C O・ 其活度系数可近似 看作 1 由于 4 a ・ 与 P0 , CO P0 的摩尔 分数相 同 , 式 () 3 中的 ac .o o P 。 2可代之 以 置c .o或 P P o2 2 。而 当将 o 熔渣 中 口。的活度 系数近似看作 1 , 有 : 。 时 则
转炉脱磷及深脱磷
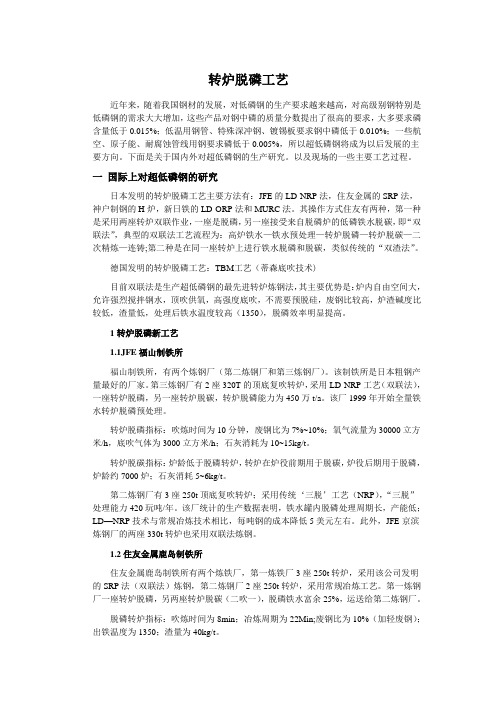
转炉脱磷工艺近年来,随着我国钢材的发展,对低磷钢的生产要求越来越高,对高级别钢特别是低磷钢的需求大大增加,这些产品对钢中磷的质量分数提出了很高的要求,大多要求磷含量低于0.015%;低温用钢管、特殊深冲钢、镀锡板要求钢中磷低于0.010%;一些航空、原子能、耐腐蚀管线用钢要求磷低于0.005%,所以超低磷钢将成为以后发展的主要方向。
下面是关于国内外对超低磷钢的生产研究。
以及现场的一些主要工艺过程。
一国际上对超低磷钢的研究日本发明的转炉脱磷工艺主要方法有:JFE的LD-NRP法,住友金属的SRP法,神户制钢的H炉,新日铁的LD-ORP法和MURC法。
其操作方式住友有两种,第一种是采用两座转炉双联作业,一座是脱磷,另一座接受来自脱磷炉的低磷铁水脱碳,即“双联法”,典型的双联法工艺流程为:高炉铁水—铁水预处理—转炉脱磷—转炉脱碳—二次精炼—连铸;第二种是在同一座转炉上进行铁水脱磷和脱碳,类似传统的“双渣法”。
德国发明的转炉脱磷工艺:TBM工艺(蒂森底吹技术)目前双联法是生产超低磷钢的最先进转炉炼钢法,其主要优势是:炉内自由空间大,允许强烈搅拌钢水,顶吹供氧,高强度底吹,不需要预脱硅,废钢比较高,炉渣碱度比较低,渣量低,处理后铁水温度较高(1350),脱磷效率明显提高。
1转炉脱磷新工艺1.1JFE福山制铁所福山制铁所,有两个炼钢厂(第二炼钢厂和第三炼钢厂)。
该制铁所是日本粗钢产量最好的厂家。
第三炼钢厂有2座320T的顶底复吹转炉,采用LD-NRP工艺(双联法),一座转炉脱磷,另一座转炉脱碳,转炉脱磷能力为450万t/a。
该厂1999年开始全量铁水转炉脱磷预处理。
转炉脱磷指标:吹炼时间为10分钟,废钢比为7%~10%;氧气流量为30000立方米/h,底吹气体为3000立方米/h;石灰消耗为10~15kg/t。
转炉脱碳指标:炉龄低于脱磷转炉,转炉在炉役前期用于脱碳,炉役后期用于脱磷,炉龄约7000炉;石灰消耗5~6kg/t。
转炉脱磷的影响因素及方法

转炉脱磷的影响因素及方法作者:唐天合来源:《科学与技术》2018年第21期摘要:近些年,钢铁市场对于低磷钢以及超低磷钢等品种钢的要求越来越苛刻,尤其是对钢中磷含量要求也进一步提高,所以严格控制好钢水中磷的含量是转炉炼钢的关键,脱磷是碱性炼钢过程中的重要任务之一,对于大多数的钢种而言,磷是一种有害的元素,随着磷含量的增加会引起钢的“冷脆”现象,提高钢的韧脆转变温度,并使焊接性能降低,冷弯性能变差,此外,磷在钢锭中会产生严重的偏析行为影响钢的性能与质量,所以要在冶炼阶段严格控制好终点磷的含量,保证炼钢的正常进行,本文分别讲述了脱磷的影响因素以及脱磷的方法。
关键词:转炉脱磷;碱度;温度1.转炉脱磷工艺概述转炉脱磷工艺主要包括:SRP工艺、多功能转炉脱磷工艺、COMI炼钢工艺脱磷工艺以及复吹转炉深脱磷工艺,其中复吹转炉深脱磷工艺又包括两路双联工艺、单渣工艺以及单炉新双渣工艺。
在炼铁过程中,原料中的磷几乎全部浸入铁水中,转炉和炉渣为脱磷提供了良好的脱磷环境。
在转炉冶炼过程中,可以通过控制主要脱磷影响因素达到良好的脱磷效果。
通常在转炉脱磷初期阶段,溶池温度较低,磷含量较高,热力学条件较好,但是由于此阶段炉渣的流动性较弱、炉渣碱度较低,动力学条件较差,因此需要通过改善动力学条件来配合热力学条件来加速脱磷,即提高炉渣流动性、炉渣碱度等;在转炉脱磷处理后期,钢水磷经过前阶段的脱磷之后,磷含量降低,炉渣流动性较高,具备良好的动力学条件,然而溶池温度较高,热力条件较差,不利于脱磷的进行,此时可以通过提高炉渣的碱度来改善热力学条件。
2.转炉脱磷影响因素分析2.1温度的影响通常转炉脱磷中的“温度”专指“溶池温度”,一般情況下,需要从两方面考虑温度对转炉脱磷效果的影响。
一方面,当熔池温度较低时,从热力学原理上分析,低温将有助于脱磷反应正常进行,但是当温度过低时,石灰在表面容易形成一层冷凝外壳,并未熔化,并降低化渣速度和炉渣流动速度,碱度降低,最终降低脱磷反应速度;另一方面,熔池温度升高过程中也会对脱磷效果产生影响。
钢液脱磷、脱硫 炼钢过程

二、钢液的脱硫
炼钢原料S含量较高,如铁水、生铁块和石灰(石灰窑内 从燃料中吸收S),常超过钢种要求。
S在钢液中无限溶解,不可能自行溢出。在生产中必须采 用相应的手段进行脱S,以满足钢种要求。
钢液的脱硫主要是通过两种途径来实现,即炉渣脱硫和气 化脱硫。在一般炼钢操作条件下,炉渣脱硫占主导。氧化渣 脱硫占总脱硫量的90%,气化脱硫占10%左右。因此,主要 分析炼钢渣与金属间的脱硫反应。
钢液脱磷、脱硫
《转炉炼钢生产》
一、钢液的脱磷
脱磷反应是炼钢过程的基本反应之一,也是一个必要的冶金反应。 磷是一个有害元素,其含量越低越好。在脱氧合金化和炉外精炼过 程中,会发生一定量的回磷现象。而减少其含量是降低危害的唯一 措施。
从理论上来说,钢水的脱磷包括两种方法:氧化脱磷和还原脱磷。 还原脱磷成本高(用Ca脱磷)、工艺复杂,目前处于理论研究 阶段,在生产中基本不使用还原脱磷。在转炉、电炉和铁水预处理 工艺中,主要采用氧化法脱磷工艺。
二、钢液的脱硫
•渣量。增加渣量,降低了渣中(S2-)浓度,促使脱硫反应进行。 •金属液成分的影响。金属液中[C] 能增加硫的活度系数f[S],降低氧 活度,有利于脱硫,铁水含硅高时对脱硫不利,虽然[Si]能使金属中 f[FeS]增大,但它低偿不了生成的SiO2对降低碱度和影响石灰熔化的 负作用。 •脱硫的有利条件:高温,高碱度,低(FeO),大渣量。
一、钢液的脱磷
从 CaO-P2O5 相 图 中 可 以 看 出 3CaO·P2O5 为 最 稳 定 , 4CaO·P2O5次之。可以认为存在于碱性渣中的应是3CaO·P2O5 。
由于3CaO·P2O5和4CaO·P2O5的反应生成自由能值很相近,在 热力学分析时,有两种磷酸盐得出的结论基本上是一致的。在实 验室条件下,达到平衡时的反应产物通常是4CaO·P2O5 。
转炉炼钢脱磷工艺的探讨

转炉炼钢脱磷工艺的探讨【摘要】本文从脱磷的热力学分析入手,对冶炼过程中温度、炉渣碱度、渣中(FeO),等对磷含量的影响进行了探讨。
同时探讨了回磷的原因、影响的因素和防止的措施。
【关键词】转炉炼钢;脱磷工艺;探讨磷在钢中是以【Fe3P】或【Fe2P】形式存在,一般以【P】表示。
磷含量高时,会使钢的朔性和韧性降低,即使钢的脆性增加,这种现象低温时更严重,通常把它称为“冷脆”。
且这种影响常常随着氧,氮含量的增加而加剧。
磷在连铸坯中的偏析仅次于硫,同时它在铁固溶体中扩散速度又很小。
不容易均匀化,因而磷的偏析和难消除。
由于炼铁过程为还原性气氛,脱磷能力较差。
因此脱磷是炼钢过程的重要任务之一。
在20世纪90年代中后期,为解决超低磷钢的生产难题,世界上各大钢厂都曾经进行过转炉铁水脱磷实验研究。
1、铁水预处理方法1.1喷吹苏打粉处理日本住友公司鹿岛厂开发的“住友碱精炼法”是成功用于工业生产的苏打精炼法。
工艺流程:从高炉流出的铁水先经脱硅处理,即将高炉铁水注入混铁车内,用氮气输送和喷吹烧结矿粉,喷入量为每吨铁水40公斤,最大供粉速度为每分钟400公斤,最大吹氧量为每分钟50立方米,脱硅量约为0.4%。
脱硅处理后的铁水硅含量可降到0.1%以下。
然后用真空吸渣器吸出脱硅渣,进行脱磷处理,以氮气为载气向铁水中喷入苏打粉,苏打粉用量为每吨18公斤,最大供粉量为每分钟250公斤,最大吹氧量为每分钟50立方米,处理后铁水中【P】≤0.001%,【S】≤0.003%,再用真空吸渣器吸出脱磷渣,并将其送到苏打回收车间,经水浸后可回收约80%的Na2O,最后将处理过的铁水倒入转炉冶炼。
1.2喷吹石灰系熔剂处理由于石灰系熔剂具有成本低,对环境污染小的优点,因此受到重视,并不断对其深入研究,以使其满足精炼铁水的需要。
工艺流程:向高炉铁沟中加入铁磷进行脱硅处理,加入量为每吨铁水27公斤,处理后铁水含硅量由0.5%降到0.15%,氧的利用率为80%-90%。
转炉脱磷少渣炼钢工艺技术发展与现状概述

转炉脱磷少渣炼钢工艺技术发展与现状概述引言钢铁是现代社会重要的基础材料之一,而磷是钢铁中的一个有害杂质。
传统的炼钢工艺中,磷的含量往往难以控制,导致钢材性能下降。
为了解决这个问题,转炉脱磷少渣炼钢工艺被广泛应用。
本文将对转炉脱磷少渣炼钢工艺的发展与现状进行概述。
转炉脱磷少渣炼钢工艺的原理转炉脱磷少渣炼钢工艺是通过将含有磷的原料在高温下与氧化剂反应,将磷转化为易脱离熔渣的磷酸盐,从而实现脱磷的目的。
其基本原理如下:1.熔融脱磷:在高温条件下,钢中的磷溶解于熔渣中,通过加入适量的熔剂,形成易分离的磷酸盐熔渣。
2.氧化脱磷:在高温条件下,将空气、氧气或含氧气的气体通入转炉中,氧化钢中的磷,将其转化为磷酸盐。
3.过渡氧化脱磷:在转炉炉脱磷过程中,通过在转炉中加入适量的铁素体,将磷转化为铁磷,再将其转化为磷酸盐。
转炉脱磷少渣炼钢工艺的发展历程转炉脱磷少渣炼钢工艺起源于20世纪50年代,经过多年的研究和改进,逐渐成熟并得到广泛应用。
其发展历程主要包括以下几个阶段:1.早期工艺的发展:早期的转炉脱磷少渣炼钢工艺主要采用人工喷镁的方式进行脱磷,但由于操作不稳定、生产效率低等问题,限制了其在实际生产中的应用。
2.化学脱磷工艺的应用:20世纪60年代,化学脱磷工艺开始应用于转炉脱磷少渣炼钢中。
该工艺是通过加入一定比例的化学试剂,如石灰石、白云石等,与熔渣中的磷反应,形成易分离的磷酸盐。
3.氧化脱磷工艺的引入:20世纪70年代,随着氧气和氧气枪在炼钢工艺中的应用,氧化脱磷工艺得到了推广。
该工艺是通过在转炉中加入氧气,氧化钢中的磷,将其转化为磷酸盐。
4.过渡氧化脱磷工艺的发展:20世纪80年代,随着对转炉脱磷少渣炼钢工艺的进一步研究和优化,过渡氧化脱磷工艺得到了广泛应用。
该工艺是通过在转炉中加入铁素体,将磷转化为铁磷,再将其转化为磷酸盐。
5.现代工艺的创新与应用:近年来,随着科技的进步和钢铁工业的发展,转炉脱磷少渣炼钢工艺逐渐采用自动化控制、机器学习等现代技术,提高了工艺的稳定性和生产效率。
2脱磷8-2(转炉脱磷)
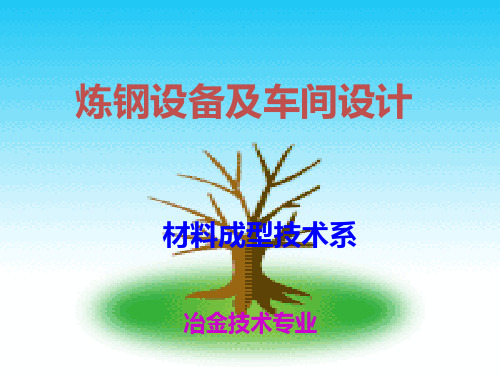
制。
对于含磷较高的铁水,入炉前应进行预处理使之 达到单渣法操作的要求,合理又经济。
§3 转炉脱磷工艺
二、吹炼过程中磷含量的变化规律
转炉炼钢过程中,钢液中的含磷量是逐渐降低的。
但是操作过程中,各种工艺参数的变化对脱磷反应
会有不同的影响。 1.枪位变化对脱磷反应的影响
脱磷反应:
2[P]+5(FeO)+4(CaO)=(4CaO· 2O5)+5[Fe] P 2[P]+5(FeO)+3(CaO)=(3CaO· 2O5)+5[Fe] P
个阶段:吹炼初期、吹炼中期、吹炼后期。 A 吹炼初期 吹炼的最初阶段,硅、锰与氧的亲和力比磷大, 所以要等到铁液中硅、锰含量降到足够低时磷才开
始氧化。因此吹炼的最初阶段脱磷速度不大。
§3 转炉脱磷工艺
二、吹炼过程中磷含量的变化规律
2.吹炼过程中磷含量的变化规律及分析
A 吹炼初期
吹炼初期熔池温度较低,这对于脱磷是一个有利 条件,如果能保证迅速形成高碱度、高氧化铁含量、 流动性良好的炉渣,可以使脱磷过程快速进行。 因此,该阶段应适当提高枪位,使渣中氧化铁含
Na2CO3 + 氧化剂
脱磷反应: 2[P]+3(Na2O)+5(FeO) ==(3Na2OP2O5)+5Fe
§3 转炉脱磷工艺
四、铁水预脱磷
1.脱磷剂 (2)石灰系脱磷剂 脱磷剂组成: CaO + 氧化剂 + 助熔剂
脱磷反应:
2[P]+5(FeO)+3(CaO) == (3CaOP2O5)+5Fe
但其去磷效率较低,一般情况去磷率为90%左右。
§3 转炉脱磷工艺
转炉炼钢脱磷最佳温度
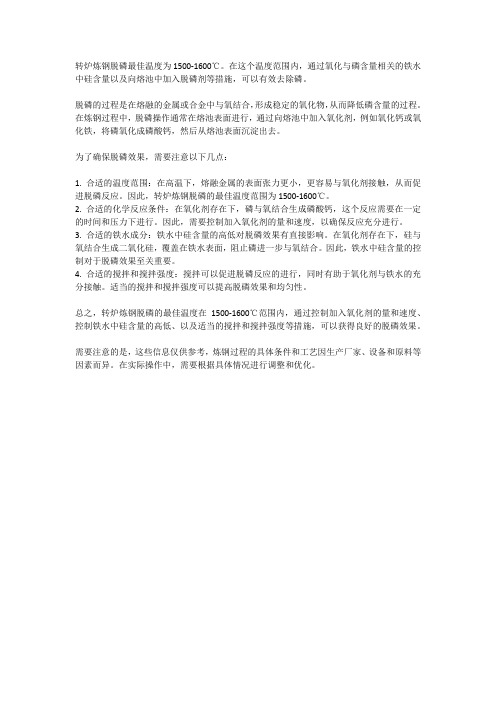
转炉炼钢脱磷最佳温度为1500-1600℃。
在这个温度范围内,通过氧化与磷含量相关的铁水中硅含量以及向熔池中加入脱磷剂等措施,可以有效去除磷。
脱磷的过程是在熔融的金属或合金中与氧结合,形成稳定的氧化物,从而降低磷含量的过程。
在炼钢过程中,脱磷操作通常在熔池表面进行,通过向熔池中加入氧化剂,例如氧化钙或氧化铁,将磷氧化成磷酸钙,然后从熔池表面沉淀出去。
为了确保脱磷效果,需要注意以下几点:
1. 合适的温度范围:在高温下,熔融金属的表面张力更小,更容易与氧化剂接触,从而促进脱磷反应。
因此,转炉炼钢脱磷的最佳温度范围为1500-1600℃。
2. 合适的化学反应条件:在氧化剂存在下,磷与氧结合生成磷酸钙,这个反应需要在一定的时间和压力下进行。
因此,需要控制加入氧化剂的量和速度,以确保反应充分进行。
3. 合适的铁水成分:铁水中硅含量的高低对脱磷效果有直接影响。
在氧化剂存在下,硅与氧结合生成二氧化硅,覆盖在铁水表面,阻止磷进一步与氧结合。
因此,铁水中硅含量的控制对于脱磷效果至关重要。
4. 合适的搅拌和搅拌强度:搅拌可以促进脱磷反应的进行,同时有助于氧化剂与铁水的充分接触。
适当的搅拌和搅拌强度可以提高脱磷效果和均匀性。
总之,转炉炼钢脱磷的最佳温度在1500-1600℃范围内,通过控制加入氧化剂的量和速度、控制铁水中硅含量的高低、以及适当的搅拌和搅拌强度等措施,可以获得良好的脱磷效果。
需要注意的是,这些信息仅供参考,炼钢过程的具体条件和工艺因生产厂家、设备和原料等因素而异。
在实际操作中,需要根据具体情况进行调整和优化。
转炉脱磷造渣工艺
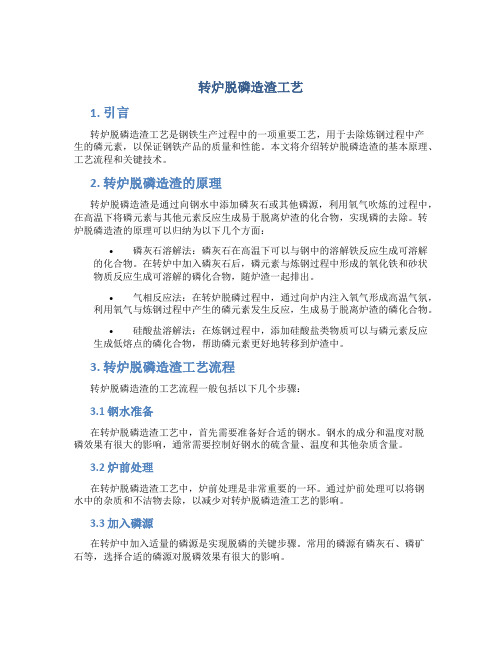
转炉脱磷造渣工艺1. 引言转炉脱磷造渣工艺是钢铁生产过程中的一项重要工艺,用于去除炼钢过程中产生的磷元素,以保证钢铁产品的质量和性能。
本文将介绍转炉脱磷造渣的基本原理、工艺流程和关键技术。
2. 转炉脱磷造渣的原理转炉脱磷造渣是通过向钢水中添加磷灰石或其他磷源,利用氧气吹炼的过程中,在高温下将磷元素与其他元素反应生成易于脱离炉渣的化合物,实现磷的去除。
转炉脱磷造渣的原理可以归纳为以下几个方面:•磷灰石溶解法:磷灰石在高温下可以与钢中的溶解铁反应生成可溶解的化合物。
在转炉中加入磷灰石后,磷元素与炼钢过程中形成的氧化铁和砂状物质反应生成可溶解的磷化合物,随炉渣一起排出。
•气相反应法:在转炉脱磷过程中,通过向炉内注入氧气形成高温气氛,利用氧气与炼钢过程中产生的磷元素发生反应,生成易于脱离炉渣的磷化合物。
•硅酸盐溶解法:在炼钢过程中,添加硅酸盐类物质可以与磷元素反应生成低熔点的磷化合物,帮助磷元素更好地转移到炉渣中。
3. 转炉脱磷造渣工艺流程转炉脱磷造渣的工艺流程一般包括以下几个步骤:3.1 钢水准备在转炉脱磷造渣工艺中,首先需要准备好合适的钢水。
钢水的成分和温度对脱磷效果有很大的影响,通常需要控制好钢水的硫含量、温度和其他杂质含量。
3.2 炉前处理在转炉脱磷造渣工艺中,炉前处理是非常重要的一环。
通过炉前处理可以将钢水中的杂质和不洁物去除,以减少对转炉脱磷造渣工艺的影响。
3.3 加入磷源在转炉中加入适量的磷源是实现脱磷的关键步骤。
常用的磷源有磷灰石、磷矿石等,选择合适的磷源对脱磷效果有很大的影响。
3.4 氧气吹炼在加入磷源后,转炉中开始进行氧气吹炼处理。
氧气的注入可以改变钢水中的气氛,促进磷元素与其他元素的反应,生成易于脱离炉渣的化合物。
3.5 炉渣处理转炉脱磷造渣过程中产生的炉渣需要进行处理。
一般情况下,炉渣会经过冷却、处理、分离等步骤,将渣中的磷元素尽可能去除,以保证炉渣的质量和性能。
4. 转炉脱磷造渣的关键技术转炉脱磷造渣的关键技术包括以下几个方面:4.1 磷源选择选择合适的磷源对于脱磷工艺的效果至关重要。
转炉双联法脱磷技术

1.5、转炉双联法与常规冶炼的比较
23
24
25
26
转炉双联法与常规冶炼的比较
由表2可见,转炉双联法冶炼工艺主要有点:
●降低能源消耗; ●降低熔剂和其他物料的消耗; ●减少渣量,金属收得率高,减轻渣处理工作量; ●缩短转炉的冶炼周期、 ●提高转炉炉龄和提高锰矿中锰的收得率等方面,
27
1.6、本章小结
双联法工艺转炉的主要配置特点
(8)转炉出钢方法 ●转炉炉前的主操作平台可考虑开孔,脱磷炉出脱磷 铁水后,脱磷铁水要马上兑入脱碳转炉内,其最 短捷的工艺路线是在转炉炉前的操作平台上开孔, 从孔中吊起脱磷铁水罐即可就近兑入脱碳炉。 ●在二个转炉的操作平台的合适位置上各开一个铁水 吊装孔,并设置盖板。脱磷转炉前的平台孔打开, 并设活动栏杆,脱碳转炉前的平台孔被盖板盖住。
4
1.1、转炉法铁水脱磷的发展过程
⑤这一技术得到推广 住友金属和歌山厂、川崎制铁水岛厂、NKK福山厂以及新日铁室 兰厂等均采用转炉双联法冶炼工艺进行大规模生产。典型的转炉 法工艺流程为:高炉铁水→铁水脱硫预处理→转炉脱磷→转 炉脱碳→二次精炼→连铸。
⑥宝钢
● 2002年11月11日 宝钢一炼钢2号300t转炉应用转炉脱磷、少渣 冶
②吨钢减少10kg的石灰消耗 ③住友金属采用了炉渣处理后通过炉顶料仓加入脱磷炉,
返回量为10~15kg/t ④新日铁君津厂和福山厂是采用留渣作业。 ⑤宝钢一炼钢采用的是将脱碳炉炉渣通过废钢料槽随废钢一道加
入到脱磷炉中。
12
1.3、双联法工艺转炉配置特点
转炉采用双联法冶炼工艺的风险较小,因 为其设备配置和工艺布置同传统转炉炼钢车间 基本一致。双联法冶炼工艺使用与否相当灵活, 转炉不进行双联作业也可改为常规操作。
转炉脱磷工艺的发展

转炉脱磷工艺的发展郝旭东1,2,李建新2,张临峰2,张兴中2,李 坚1(1.昆明理工大学材料与冶金工程学院,云南昆明650093;2.钢铁研究总院先进钢铁流程及材料国家重点实验室,北京100081)摘 要:简述了用转炉脱磷工艺进行铁水预处理的发展情况及其特点,介绍了其发展趋势,并简要介绍了转炉脱磷工艺在我国的应用发展。
关键词:转炉;脱磷;铁水预处理中图分类号:TF704.4 文献标识码:A 文章编号:100121447(2008)0520052204The development of hot metal pretreatment technologies in BOFHAO Xu 2dong 1,2,L I Jian 2xin 2,ZHAN G Lin 2feng 2,ZHAN G Xing 2zhong 2,L I Jian 1(1.Faculty of Materials and Metallurgical Engineering ,Kunming University of Science and Technology ,Kunming 650093,China ;2.The State Key Laboratory for Advanced Iron and Steel Process and Product s ,Cent ral Iron and Steel Research Instit ute ,Beijing 100081,China )Abstract :A brief int roduction is given to t he develop ment of hot metal pret reat ment technologies in BOF.The feat ure and tendency of develop ment of hot metal p ret reat 2ment technologies in BO F in recent years ,as well as t heir f ut ure application pro spect s in China are also discussed in t his paper.K ey w ords :BOF ;dep hosp horization ;hot metal p retreat ment technology作者简介:郝旭东(1983-),男,山西原平人,硕士生,主要从事转炉炼钢方面的研究. 一般情况下,磷在钢铁产品中是有害杂质,需在炼钢时设法尽可能多地去除掉。
探析转炉脱磷影响因素及其工艺发展
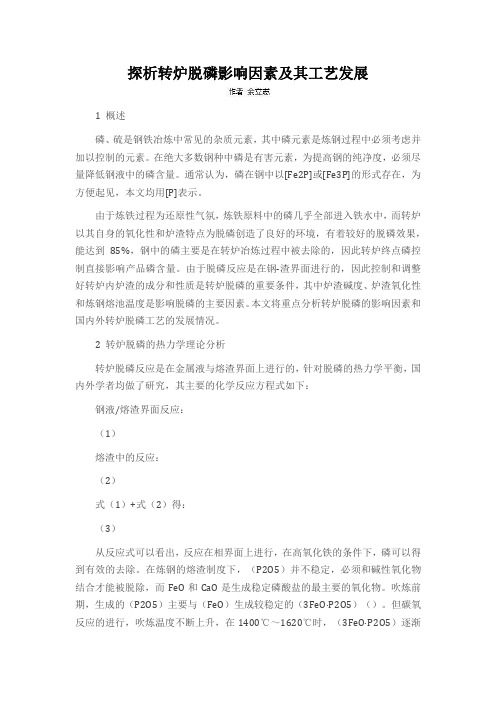
探析转炉脱磷影响因素及其工艺发展1 概述磷、硫是钢铁冶炼中常见的杂质元素,其中磷元素是炼钢过程中必须考虑并加以控制的元素。
在绝大多数钢种中磷是有害元素,为提高钢的纯净度,必须尽量降低钢液中的磷含量。
通常认为,磷在钢中以[Fe2P]或[Fe3P]的形式存在,为方便起见,本文均用[P]表示。
由于炼铁过程为还原性气氛,炼铁原料中的磷几乎全部进入铁水中,而转炉以其自身的氧化性和炉渣特点为脱磷创造了良好的环境,有着较好的脱磷效果,能达到85%,钢中的磷主要是在转炉冶炼过程中被去除的,因此转炉终点磷控制直接影响产品磷含量。
由于脱磷反应是在钢-渣界面进行的,因此控制和调整好转炉内炉渣的成分和性质是转炉脱磷的重要条件,其中炉渣碱度、炉渣氧化性和炼钢熔池温度是影响脱磷的主要因素。
本文将重点分析转炉脱磷的影响因素和国内外转炉脱磷工艺的发展情况。
2 转炉脱磷的热力学理论分析转炉脱磷反应是在金属液与熔渣界面上进行的,针对脱磷的热力学平衡,国内外学者均做了研究,其主要的化学反应方程式如下:钢液/熔渣界面反应:(1)熔渣中的反应:(2)式(1)+式(2)得:(3)从反应式可以看出,反应在相界面上进行,在高氧化铁的条件下,磷可以得到有效的去除。
在炼钢的熔渣制度下,(P2O5)并不稳定,必须和碱性氧化物结合才能被脱除,而FeO和CaO是生成稳定磷酸盐的最主要的氧化物。
吹炼前期,生成的(P2O5)主要与(FeO)生成较稳定的(3FeO·P2O5)()。
但碳氧反应的进行,吹炼温度不断上升,在1400℃~1620℃时,(3FeO·P2O5)逐渐分解,使磷又回到钢液当中。
为了有效地彻底脱磷,必须用石灰造高碱度钢渣,使磷在高碱度下生成更稳定的磷酸盐渣3CaO·(P2O5)或4CaO·(P2O5),其中4CaO·(P2O5)()更稳定,3CaO·(P2O5)次之,但通常达到平衡时的反应产物是4CaO·(P2O5)。
100t顶吹转炉双渣深脱磷工艺研究与实践
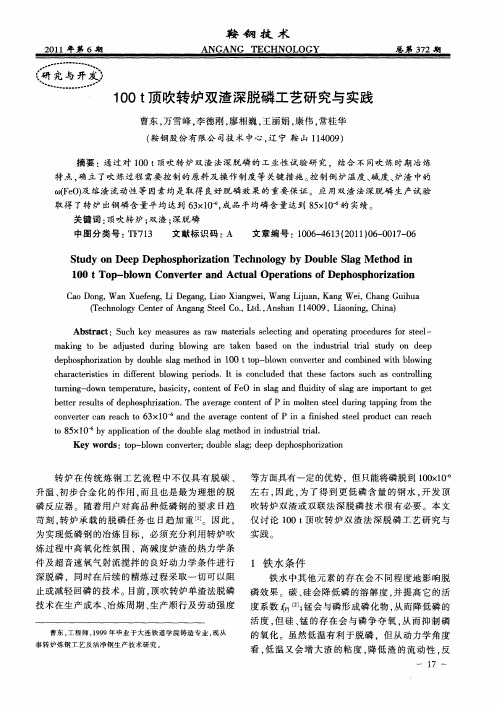
C oD n , nX ee g L e ag La ag e, n i a , agWe, hn uh a a o g Wa u f , i gn , io nw iWa gLj n K n i C a gG iu n D Xi u
(ehooyCne o nagSel o, t. nhn14 0 , ioig C ia T cnlg et f gn te C .Ld, sa 0 9 Lann, hn) r A A 1
St dy o e De ho pho ia i n Te h l g ub e S a e ho n u n De p p s rz to c no o y by Do l l g M t d i
1 0 t p bo n e tra d Acu lOp r to so p o p o ia in 0 To - lwn Co v re n t a e a in fDe h s h rz t o
一】 Biblioteka 7《 钢 技 术 ) 0 1年 第 6期 鞍 ) 1 2 曹 东 等 :0 顶 吹 转 炉 双 渣 深 脱 磷 工 艺 研 究 与 实 践 1 0t
第 3 2期 7
而 阻碍 磷 的脱除 。因此 , 最佳 脱磷 条件 是合 适 的铁 盾 须加 以综 合 考虑 。铁 水条 件如 表 1 示 , 所 可见 , 水 成分 范 围及 温度 范 围( 4 0 15 0℃) 1 5 ̄ 0 。在 实 际 无 论是 铁水 成分 还 是铁水 温 度 , 波动 范 围均 较大 , 必 脱 磷操 作过 程 中 ,现 场操 作人 员 对 于 1 z 多矛 因此 。 须通 过优 化工艺 参数 来实 现低磷 目标 。  ̄ 诸 22
一
由 图 1可 以看 出 .在 保 证 碱 度 R 的 前 提
炼钢脱磷剂配方

炼钢脱磷剂配方炼钢是一种重要的冶金工艺,其中脱磷是一个关键的步骤。
脱磷剂是用于去除炼钢过程中产生的磷元素的一种化学物质。
本文将介绍一种常用的炼钢脱磷剂配方及其作用。
一、脱磷剂的作用炼钢过程中,原料中的磷元素会对钢的性能产生负面影响。
磷元素会降低钢的强度和韧性,增加钢的脆性,同时还会对钢的冷加工性能产生不利影响。
因此,需要在炼钢过程中加入脱磷剂,将磷元素从钢中去除,以提高钢的质量和性能。
二、炼钢脱磷剂的配方常用的炼钢脱磷剂配方是以石灰、氧化铁和氟化钙为主要原料,配合其他助剂进行调配。
具体配方如下:1. 石灰:石灰是一种常用的脱磷剂原料,它可以与磷形成不溶性的磷酸钙沉淀,从而将磷元素去除。
石灰的质量比例通常为20%~30%。
2. 氧化铁:氧化铁是另一种常用的脱磷剂原料,它可以与磷形成稳定的化合物,将磷元素固化在炉渣中。
氧化铁的质量比例通常为10%~20%。
3. 氟化钙:氟化钙是一种重要的助剂,它可以提高脱磷剂的脱磷效果。
氟化钙的质量比例通常为5%~10%。
4. 其他助剂:为了进一步提高脱磷剂的性能,可以添加一些其他助剂,如硅酸盐、氧化镁等。
这些助剂的质量比例通常为5%~10%。
以上是一种常用的炼钢脱磷剂配方,不同的钢种和工艺条件可能需要调整配方中各个原料的比例,以达到最佳的脱磷效果。
三、脱磷剂的使用方法脱磷剂在炼钢过程中的使用方法通常有两种:一种是直接加入到炉渣中,另一种是加入到炼钢炉中。
1. 直接加入到炉渣中:这种方法适用于转炉炼钢和电炉炼钢等工艺。
在炼钢过程中,将脱磷剂按照一定比例加入到炉渣中,通过与炉渣中的磷元素反应,将磷元素转移到炉渣中。
2. 加入到炼钢炉中:这种方法适用于炼铁转炉炼钢等工艺。
在炼钢过程中,将脱磷剂按照一定比例加入到炼钢炉中,通过与炼钢炉中的磷元素反应,将磷元素转移到炉渣中。
无论是直接加入到炉渣中还是加入到炼钢炉中,都需要根据具体的工艺条件和脱磷要求来确定脱磷剂的使用方法和使用量。
- 1、下载文档前请自行甄别文档内容的完整性,平台不提供额外的编辑、内容补充、找答案等附加服务。
- 2、"仅部分预览"的文档,不可在线预览部分如存在完整性等问题,可反馈申请退款(可完整预览的文档不适用该条件!)。
- 3、如文档侵犯您的权益,请联系客服反馈,我们会尽快为您处理(人工客服工作时间:9:00-18:30)。
磷 在渣. %P
:
a ̄
7 C . ・ y4 a Q ) ( OP 0 2
欲提 高熔 渣 的脱磷 能力 ,必须增 大K 、 p ae、aa、f]口 F 0 co t 降低1 C .O) 由止 可 失 p , P 5 ( O2 , 4 匕 l J 利 于脱磷 反应 的基 本热 力学 条件 , 即低温 , 高 氧化 性 、高碱度 的炉 渣 【 3 。 1 低温 度 :脱磷 反应 是强 放热 反应 , ) KD 温 度 升 高 而 急 剧 减 小 。 在 10  ̄ 随 4 0C、
3 高碱 度 : 中的酸 性氧化 物如 SO2 ) 渣 i 对脱 磷 不利 , 高熔渣 碱 度是 提 高脱磷 率 的 提 有 效 途 径 ,增 加 渣 中 碱 性氧 化物 C O的 比 a 例 ,可 以增大 a ,降低 丫CO 25 co (a.o) 4 P ,使得三 p 增 大 。 熔渣碱 度 应控 制在 合适 的范 围 , 但 碱 度过 高 时渣 的流 动性差 而 不利 于脱磷 。 4 大 渣 量 :在 钢渣 成 分 一 定 的情 况 ) 下 ,增 大渣 量意 味着稀 释 了P05 2 的浓度 , 所 以增 加渣 量 可增 大脱磷 量 【。 o J 脱 磷 反应 是 典型 的渣 界 面 反应 ,渣 钢 的形 成 速 率对 脱 磷 有 关 键影 响 。熔 渣 形成 后 ,在渣 钢 界面上 的磷 的氧 化速 率很 快 , 脱 磷速 率 由界 面两侧 的传 质控 制 , 即反钢 液 中 【] P 的传 质 和渣相 中 的(2 ) Po5的传质 。 磷反 脱 应 在相 界面 进 行 , 炉渣 的状 态和 流动 性及其 与 铁 水 的接触 时 间 ,搅 拌程 度 等 动 力 学条 件 ,明显地 影响着 传质 速度 , 从而 影 响脱磷 反应 的速度 。 当热 力学条 件 发生 不利 的变化 时 ,如温 度升 高 、(e ) F O 降低 等原 因,都会 发 生 回磷 。在满足 热力 学条 件 的 同时 . 还必 须 创 造 良好 的脱 磷 反 应 的动 力 学 条 件 , 因 此 , 于脱 磷 反应 的动力 学 条件 是确 保脱磷 利 过 程 中渣 有 良好 的流 动性 , 并在 脱磷 前期加 强熔 池 的搅 拌 。
转炉 炼钢 流程 中 的脱 磷工 艺
胡加 学 李 东
摘 要 : 随 着 用 户 对 低 磷 钢 和 超 低 磷 钢 的 需 求 曰益 增 加 , 铁 水 脱 磷 己成 为 转 炉 冶 炼 低 磷 钢 流 程 中 最 为 关 键 的 工 序 。本 文 综 述 了 目前 国 内外 转 炉 炼 钢 流 程 铁 水 脱 磷 工 艺 的 发 展 现 状 和 部 分 工 厂 的操 作 参 数 ,分 析 比较 了 各种 工 艺 的 优 缺 点 ,并 论 述 了铁 水 预 脱 磷 工 艺对 于 转 炉 炼 钢 的 重 要 意 义 。 在炼 铁过 程 中 , 原料 中磷 的氧化 物被还 原, 磷几 乎全 部进 入铁 水 。 于绝 大多数 钢 对 种 来说 , 是有 害元 素 , 容 易在 晶界偏析 , 磷 它 降低钢 的低温 冲击 韧性 ,增加 冷脆 性 ,引起 腐蚀 疲 劳 、焊接 开裂 等 。近 年来 ,用户对低 磷 钢和 超低磷 钢 的需求 明显 增加 , 部分钢 种 如 深 冲 钢和 高级 别 管线 钢 等对 磷 含 量 要求 苛 刻 , 统 的转 炉炼 钢工 艺流程 越来 越难 以 传 满 足低 成本地 冶炼 低磷 钢 的要求 , 得 日本 使 钢 铁 企 业形 成 了一 系列 以铁 水 预处 理 为基 础 的“ 高炉炼 铁一 铁水 预 处理 ( 脱硅 、脱硫 、 脱 磷 )一 转 炉 少渣 炼 钢 ( 碳 升温 )一 钢 脱 水 炉 外 精 炼 ( 杂 、除气 、深 脱 硫 、调 整 除 合 金 成 份 )一 连铸 ” 的钢铁冶 金优 化工 艺 , 开 始 了纯净钢 冶炼 的先 河 。 目前 国内外 已建 立起 大规 模 的纯净 钢生 产系 统 , 铁水 预处理 正 向深度 脱磷 、深 度脱硫 发 展[ 1 1。 , 2
1 氧 化脱 磷 原理
具 有 氧化 性 的碱 性 炉渣 在 铁 水 中的 典 型脱 磷 反应为 :
2P + 5F O + 4Ca : (C O‘25 [】 (e ) ( O) 4 a P 0) +5F 】 [e Eg - -2 4 5 +8 .5 r - 0 4 0 35 T
其平 衡常 数
2 转炉炼 钢 流程 中的脱磷 工 艺
转 炉炼 钢 生产 普通 钢 种 的常 规 工 艺流 程 是 : 高 炉 铁 水 一 常 规 (轻 ) 硫 脱 ( 100 %) 复 吹 转 炉 ( 磷 、 脱 碳 、 升 [<. S 2 一 脱 温) 钢水精 炼( 一 脱氧 、 气体 、去夹 杂) 去 一普 通钢 水 ,脱磷 是转 炉 的任 务之 一 。 国内外对汽 车板 、管 线钢 、深 冲板等 高