液态金属成形过程及控制
三种液态成形方法
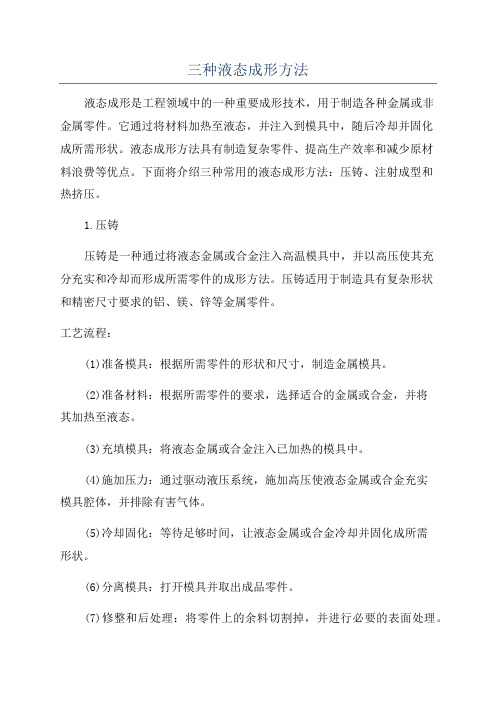
三种液态成形方法液态成形是工程领域中的一种重要成形技术,用于制造各种金属或非金属零件。
它通过将材料加热至液态,并注入到模具中,随后冷却并固化成所需形状。
液态成形方法具有制造复杂零件、提高生产效率和减少原材料浪费等优点。
下面将介绍三种常用的液态成形方法:压铸、注射成型和热挤压。
1.压铸压铸是一种通过将液态金属或合金注入高温模具中,并以高压使其充分充实和冷却而形成所需零件的成形方法。
压铸适用于制造具有复杂形状和精密尺寸要求的铝、镁、锌等金属零件。
工艺流程:(1)准备模具:根据所需零件的形状和尺寸,制造金属模具。
(2)准备材料:根据所需零件的要求,选择适合的金属或合金,并将其加热至液态。
(3)充填模具:将液态金属或合金注入已加热的模具中。
(4)施加压力:通过驱动液压系统,施加高压使液态金属或合金充实模具腔体,并排除有害气体。
(5)冷却固化:等待足够时间,让液态金属或合金冷却并固化成所需形状。
(6)分离模具:打开模具并取出成品零件。
(7)修整和后处理:将零件上的余料切割掉,并进行必要的表面处理。
2.注射成型注射成型是一种通过将液态或半液态塑料材料注入模具中,并在成型温度下固化成所需形状的成形方法。
注射成型适用于制造塑料零件,广泛应用于电子、汽车、日用品等领域。
工艺流程:(1)准备模具:根据所需零件的形状和尺寸,制造塑料模具。
(2)准备材料:选择适合注射成型的塑料树脂,并将其加热至液态或半液态。
(3)充填模具:将液态或半液态塑料注入已加热的模具中。
(4)冷却固化:等待足够时间,让塑料在模具中冷却并固化成所需形状。
(5)分离模具:打开模具并取出成品零件。
(6)修整和后处理:将零件上的余料切割掉,并进行必要的表面处理。
3.热挤压热挤压是一种通过将液态金属在高温和高压下通过模孔挤压成型的成形方法。
热挤压适用于制造具有长直形截面或复杂截面的杆、管和型材等零件。
工艺流程:(1)准备模具:根据所需零件的形状和尺寸,制造高温合金模具。
液态模锻的原理方法和应用

液态模锻的原理方法和应用1. 液态模锻的原理液态模锻是一种先进的金属成形技术,主要利用金属在液态状态下的流动性来实现成形。
其原理主要包括以下几个方面:•金属液态流动性:金属在液态状态下具有较好的流动性,可以在模具内部均匀流动,填充整个模腔。
•压力控制:通过施加一定的液态压力,使金属在模具中流动,并填充模腔。
压力的大小和施加方式对成形质量有重要影响。
•温度控制:液态模锻需要在一定的温度范围内进行,通常要求金属保持在其液态区域内,以保证成形过程的顺利进行。
•冷却控制:液态模锻后,还需要对成形件进行冷却处理,以获得所需的性能和形状。
2. 液态模锻的方法液态模锻的方法有多种,根据实际需求和成形材料的特性选择不同的方法。
下面给出几种常用的液态模锻方法:2.1 直接模锻法直接模锻法是最常用的液态模锻方法之一,其工艺流程简单,适用于各种金属材料。
具体步骤如下:1.预热金属料:将金属料加热至其液态温度以上,使其达到液态状态。
2.填充模具:将液态金属料注入预热好的模具中,使其填充整个模腔。
3.施加压力:在金属料注入模具后,施加一定的液态压力,使金属料在模具内流动并填充模腔。
4.冷却处理:待金属料填充完毕后,进行冷却处理,以获得所需的性能和形状。
2.2 间接模锻法间接模锻法是液态模锻中的另一种常用方法,主要用于形状复杂的零件。
主要步骤如下:1.制备模具:根据所需零件的形状和尺寸,制备相应的模具。
模具可以分为上模和下模两个部分。
2.加热金属料:将金属料加热至其液态温度以上,使其达到液态状态。
3.填充模具:将液态金属料注入上模中,然后合上下模,使金属料填充整个模腔。
4.施加压力:在金属料填充完毕后,施加一定的液态压力,以保证金属料在模具中充分流动,并填充整个模腔。
5.冷却处理:待金属料填充完毕后,进行冷却处理,以获得所需的性能和形状。
2.3 复合模锻法复合模锻法是一种较为复杂的液态模锻方法,主要用于特殊材料或特殊形状的零件。
液态金属
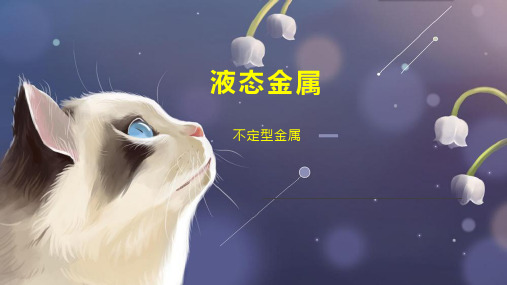
发
液态金属2015年3月,由清华大学教授、中国科学院理化技术研究所双聘研究员刘静带领的中科院理化技术 研究所、清华大学医学院联合研究小组,发现了一种异常独特的现象和机制,即液态金属可在吞食少量物质后以 可变形机器形态长时间高速运动,实现了无需外部电力的自主运动。
谢谢观看
研究
和简单的非金属液体有许多共同点,20世纪60年代以来对它研究较多。但人们对它的结构细节仍不清楚。熔 融金属的X射线或中子散射可得其径向分布函数g(r),它在平均意义上描述熔体结构。当r<σ(σ为原子有效直径, 图1),g(r)=0,说明原子似硬球,不能互相贯穿,r大于2~3nm时,原子完全无规排列,g(r)→1。原子周围最近 邻的原子数叫配位数Z,其中ρ0是熔体粒子数密度。绝大多数金属熔化时体积约增大5%,原子序数Z减小,金属 键不变。少数“反常金属”(如Ga、Ge、Bi、Sb等)熔化时体积约收缩5%,Z增加,共价键部分地变为金属键。 各种金属熔化后结构趋于相近,Z在9~12左右。熔体的Z和r1随温度上升而稍改变,但g(r)基本特点不变。
技术
中国液态金属变形技术
《不同构象之间的液态金属多变形性》论文,揭示出室温液态金属具有可在不同形态和运动模式之间转换的 普适变形能力。比如,浸没于水中的液态金属对象可在低电压作用下呈现出大尺度变形、自旋、定向运动,乃至 发生液球之间的自动融合、断裂-再合并等行为,且不受液态金属对象大小的限制;较为独特的是,一块很大的金 属液膜可在数秒内即收缩为单颗金属液球,变形过程十分快速,而表面积改变幅度可高达上千倍;此外,在外电 场作用下,大量彼此分离的金属液球可发生相互粘连及合并,直至融合成单一的液态金属球;依据于电场控制, 液态金属极易实现高速的自旋运动,并在周围水体中诱发出同样处于快速旋转状态下的漩涡对;若适当调整电极 和流道,还可将液态金属的运动方式转为单一的快速定向移动。研究表明,造成这些变形与运动的机制之一在于 液态金属与水体交界面上的双电层效应。以上丰富的物理学图景革新了人们对于自然界复杂流体、软物质特别是 液态金属材料学行为的基本认识。这些超越常规的物体构象转换能力很难通过传统的刚性材料或流体介质实现, 它们事实上成为用以构筑可变形智能机器的基本要素,为可变形体特别是液体机器的设计和制造开辟了全新途径。
第9章液态金属在特殊条件下的凝固及成形2概述
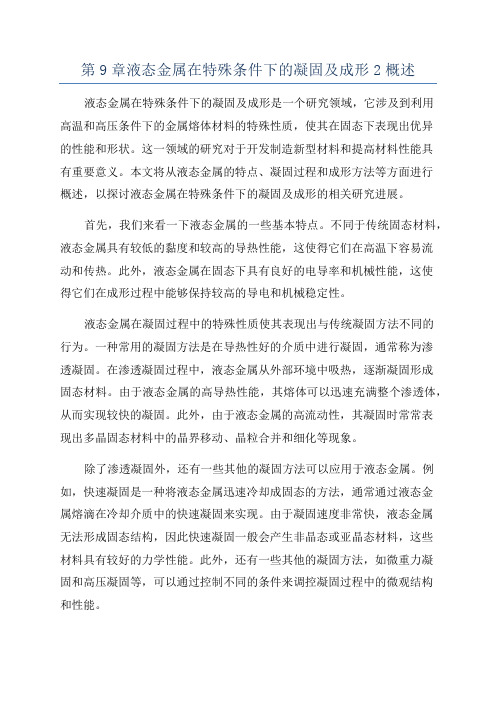
第9章液态金属在特殊条件下的凝固及成形2概述液态金属在特殊条件下的凝固及成形是一个研究领域,它涉及到利用高温和高压条件下的金属熔体材料的特殊性质,使其在固态下表现出优异的性能和形状。
这一领域的研究对于开发制造新型材料和提高材料性能具有重要意义。
本文将从液态金属的特点、凝固过程和成形方法等方面进行概述,以探讨液态金属在特殊条件下的凝固及成形的相关研究进展。
首先,我们来看一下液态金属的一些基本特点。
不同于传统固态材料,液态金属具有较低的黏度和较高的导热性能,这使得它们在高温下容易流动和传热。
此外,液态金属在固态下具有良好的电导率和机械性能,这使得它们在成形过程中能够保持较高的导电和机械稳定性。
液态金属在凝固过程中的特殊性质使其表现出与传统凝固方法不同的行为。
一种常用的凝固方法是在导热性好的介质中进行凝固,通常称为渗透凝固。
在渗透凝固过程中,液态金属从外部环境中吸热,逐渐凝固形成固态材料。
由于液态金属的高导热性能,其熔体可以迅速充满整个渗透体,从而实现较快的凝固。
此外,由于液态金属的高流动性,其凝固时常常表现出多晶固态材料中的晶界移动、晶粒合并和细化等现象。
除了渗透凝固外,还有一些其他的凝固方法可以应用于液态金属。
例如,快速凝固是一种将液态金属迅速冷却成固态的方法,通常通过液态金属熔滴在冷却介质中的快速凝固来实现。
由于凝固速度非常快,液态金属无法形成固态结构,因此快速凝固一般会产生非晶态或亚晶态材料,这些材料具有较好的力学性能。
此外,还有一些其他的凝固方法,如微重力凝固和高压凝固等,可以通过控制不同的条件来调控凝固过程中的微观结构和性能。
液态金属在凝固后可以通过不同的成形方法来加工成所需的形状和尺寸。
一种常用的成形方法是利用热压成形,即将固态的金属材料加热到一定温度,然后施加压力使其塑性变形并保持固态结构。
另一种方法是利用粉末冶金成形,即将液态金属凝固成粉末,然后通过压制和烧结等方法来制备复杂形状的金属制品。
液态金属凝固成形的方法
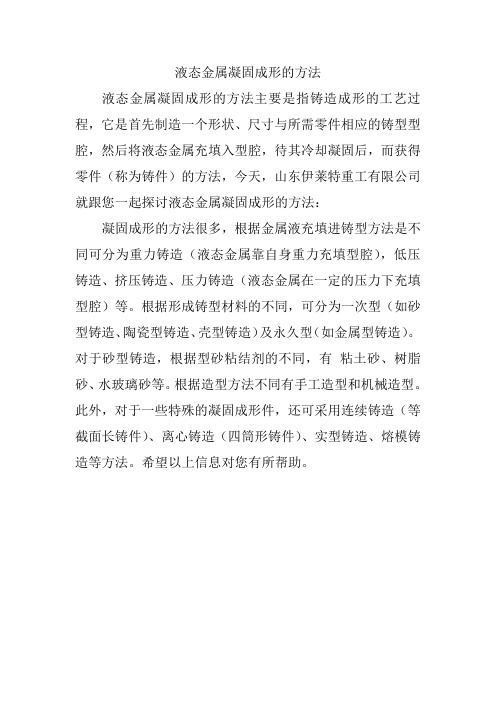
液态金属凝固成形的方法
液态金属凝固成形的方法主要是指铸造成形的工艺过程,它是首先制造一个形状、尺寸与所需零件相应的铸型型腔,然后将液态金属充填入型腔,待其冷却凝固后,而获得零件(称为铸件)的方法,今天,山东伊莱特重工有限公司就跟您一起探讨液态金属凝固成形的方法:
凝固成形的方法很多,根据金属液充填进铸型方法是不同可分为重力铸造(液态金属靠自身重力充填型腔),低压铸造、挤压铸造、压力铸造(液态金属在一定的压力下充填型腔)等。
根据形成铸型材料的不同,可分为一次型(如砂型铸造、陶瓷型铸造、壳型铸造)及永久型(如金属型铸造)。
对于砂型铸造,根据型砂粘结剂的不同,有粘土砂、树脂砂、水玻璃砂等。
根据造型方法不同有手工造型和机械造型。
此外,对于一些特殊的凝固成形件,还可采用连续铸造(等截面长铸件)、离心铸造(四筒形铸件)、实型铸造、熔模铸造等方法。
希望以上信息对您有所帮助。
材料成形工艺-液态金属铸造成形工艺基础

5
第一章 液态金属铸造成形工艺基础
一、基本工艺要素及其控制
一、基本工艺要素及其控制
★ 铸造的基本工艺要素:
成分
温度
熔融金属液
结构
材质
温度
预先制备的铸型
6
第一章 液态金属铸造成形工艺基础
一、基本工艺要素及其控制
一、基本工艺要素及其控制
1、金属液应满足以下要求:
成分符合要求——各元素含量在标称范围内 合金液含气量、杂质含量在允许范围内
3、铸型与金属之间的相互作用
3.2、热作用: 冷却速度超出适当的工艺窗口 导致亚稳相的形成
型壁表面变形开裂 铸件表面质量差、夹砂结疤
金属液热量迅速导入铸型表层 热击——铸型破裂或表面龟裂
17
第一章 液态金属铸造成形工艺基础
一、基本工艺要素及其控制
3、铸型与金属之间的相互作用
3.2、热作用不良导致的缺陷:
应当注意气孔缺陷与疏松缺陷的差别和关联。
20
第一章 液态金属铸造成形工艺基础
一、基本工艺要素及其控制
3、铸型与金属之间的相互作用
铸件中气孔的形成:
卷入气孔的形成
气孔的一般分布区域
21
第一章 液态金属铸造成形工艺基础
一、基本工艺要素及其控制
一、基本工艺要素及其控制
4、常用铸造合金及其熔炼:
黑色金属——
14
第一章 液态金属铸造成形工艺基础
一、基本工艺要素及其控制
一、基本工艺要素及其控制
3、铸型与金属之间的相互作用:
机械作用: 金属液在进入型腔时对铸型的冲刷作用; 金属液充入型腔后对铸型壁面的压力作用; 铸型对金属凝固收缩而产生的阻碍作用。
热 作 用: 金属热量向铸型的换热传输作用。
液态金属在特殊条件下的凝固及成形
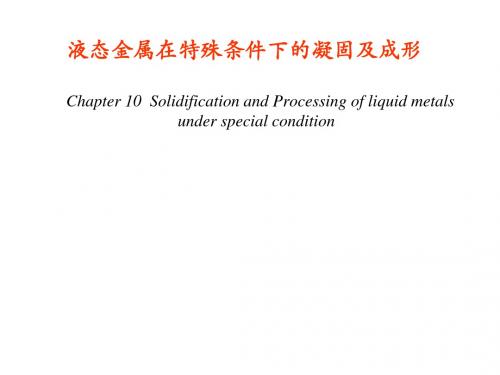
能人为地控制。
• 3) 快速凝固法 (H. R. S法)
• 铸型加热器始终加热, 在凝固时,铸件与加 热器之间产生相对移 动。
• 与P. D法相比可以大大 缩小凝固前沿两相区, 局部冷却速度增大, 有利于细化组织,提 高机械性能。
H. R. S法示意图
2、定向凝固技术的应用 (1)柱状晶的生长
(一种顺序凝固组织)
• (2)单晶生长
• 根据熔区的特点分为正常凝固法和区熔法。
• 1) 正常凝固法
• 有坩埚移动、炉体移动及晶体提拉等单向凝固方法 • 或将“籽晶”放在坩埚底部,当坩埚向下移动时,“籽晶”
处开始结晶,随着固—液界面移动,单晶不断长大。 • 主要缺点是晶体和坩埚壁接触,容易产生应力或寄生成核
图 晶体提拉示意图
• (3) 区域提纯
• 区域熔化是获得超纯材料的极有效的手段,由于区域熔化 的发明,才出现了半导体工业。
• 当正常凝固,固—液界面前沿加强搅拌时,可以使试样的 起始凝固端的纯度提高,而整个试样溶质分布是极不均匀 的。
CE CL Csm C0 k0C0
0
CE Csm C0 k0C0
炉丝
熔体
挡板
坩埚 炉管
a)
b)
图 坩埚移动单向凝固示意图
a)垂直式 b)水平式
图 自生粒晶法生产单晶叶片
1-铸件 2-选晶段 3-起始段
通过x、y、z三个方向选晶,从而确保一个柱晶顺利进入铸件
z
y 0 x
图2-42 选晶段示意图
等轴晶
定向柱状晶 单晶体
提拉杆 籽晶 晶体
熔体
液态模锻工艺介绍)

壳层在较大温差下迅速结晶形成,壳体较薄,尚未有枝晶
形成,组织致密、晶粒细小,性能高。 P0/ P(0 液锻力),仅起
压平液面的作用,其在合金液内部产生的压强(比压力) p/
近似为0。
压平后的液面高度
H0
V液H 0
A0
V液 A0
液态模锻工艺基础
P 凸第模二接阶触段液-面压后力,下液结锻晶力从P0’~P0,0/ 在其P0内部产生压强p,
凸
式
冲
头
加
压 凹
式
冲
头
加
压
液态模锻工艺方法选择
壁厚差别大的零件 壁厚均匀的零件 形状复杂的零件
正挤压液锻 反挤压液锻 复合挤压间接液锻
六、液态模锻成形方式选择原则
杯形件 小型,形状复杂
凸式冲头 上端面有凸台并带有内腔和孔
间接液态模锻
复合式冲头
六、液态模锻凹模结构形式
六、液态模锻凹模结构形式
七、液态模锻工艺基础
五、液态模锻分类
1、按金属流动方式
(1)静压液锻
合金液不产生大量的流动,液锻形状主要靠浇注时定 型。压力的作用主要是加速(影响)合金液的凝固并产 生塑性变形。分单、双向静压液锻。
单向液锻 h/d≤5 双向液锻 h/d>5
液态模锻分类 (2)挤压液锻
液锻时,浇入的合金液在凸模作用下迅速流动、充型,接 着在高压下凝固和产生少量的塑性变形 (1)正挤压液锻。 (2)反挤压液锻。(3)复合挤压液锻。
塑性成形方法
优点 塑性成形方法
缺点
零件组织致密,强度、 塑性高
高质量的零件表面和尺 寸精度
不能成形较复杂外形状 的零件
受施压和取件的约束, 只能成形与施压方向一 致,简单形状的内孔, 不能成形零件的侧内孔
金属液态成形

材料成形技术基础第一章 金属液态成形金属液态成形(铸造):将液态金属在重力或外力作用下充填到型腔中,待其凝固冷却后,获得所需形状和尺寸的毛坯或零件的方法。
液态成形的优点:(1)适应性广,工艺灵活性大(材料、大小、形状几乎不受限制)(2)最适合形状复杂的箱体、机架、阀体、泵体、缸体等(3)成本较低(铸件与最终零件的形状相似、尺寸相近)主要问题:组织疏松、晶粒粗大,铸件内部常有缩孔、缩松、气孔等缺陷产生,导致铸件力学性能,特别是冲击性能较低。
分类:铸造从造型方法来分,可分为砂型铸造和特种铸造两大类。
其中砂型铸造工艺如图1-1所示。
图1-1 砂型铸造工艺流程图第一节金属液态成形工艺基础一、熔融合金的流动性及充型液态合金充满型腔是获得形状完整、轮廓清晰合格铸件的保证,铸件的很多缺陷都是在此阶段形成的。
(一)熔融合金的流动性1.流动性 液态合金充满型腔,形成轮廓清晰、形状和尺寸符合要求的优质铸件的能力,称为液态合金的流动性。
流动性差:铸件易产生浇不到、冷隔、气孔和夹杂等缺陷。
流动性好:易于充满型腔,有利于气体和非金属夹杂物上浮和对铸件进行补缩。
螺旋形流动性试样衡量合金流动性,如图1-2所示。
在常用铸造合金中,灰铸铁、硅黄铜的流动性最好,铸钢的流动性最差。
常用合金的流动性数值见表1-1。
表1-1 常用合金的流动性(砂型,试样截面8㎜×8㎜)2. 影响合金流动性的因素(1) 化学成份 纯金属和共晶成分的合金,由于是在恒温下进行结晶,液态合金从表层逐渐向中心凝固,固液界面比较光滑,对液态合金的流动阻力较小,同时,共晶成分合金的凝固温度最低,可获得较大的过热度,推迟了合金的凝固,故流动性最好;其它成分的合金是在一定温度范围内结晶的,由于初生树枝状晶体与液体金属两相共存,粗糙的固液界面使合金的流动阻力加大,合金的流动性大大下降,合金的结晶温度区间越宽,流动性越差。
Fe-C合金的流动性与含碳量之间的关系如图1-3所示。
液态成形工艺技术

液态成形工艺技术液态成形工艺技术是一种将液体材料注入模具中,通过各种方式使其固化成形的技术。
液态成形工艺技术包括压铸、注塑、压力真空成型等。
这些技术广泛应用于工业生产中,能够生产高精度、高性能的零部件和产品。
液态成形工艺技术的基本原理是通过将液体材料注入模具中,并施加一定的压力,使其充满整个模腔。
在一定的温度和时间下,液体材料会逐渐固化,从而得到所需的成品。
压铸是一种常见的液态成形工艺技术。
在压铸中,液态金属被注入到模具中,并经过高压力的作用,使其充满整个模腔,然后在一定的时间内进行冷却固化。
最终,通过打开模具,可以得到精确的金属零部件。
注塑是另一种常见的液态成形工艺技术。
在注塑中,熔融的塑料被注入到模具中,并且根据模具的形状和尺寸,塑料材料会逐渐固化。
注塑工艺技术可以生产各种塑料制品,如塑料壳体、包装材料等。
注塑工艺技术具有生产效率高、成本低等优点,因此在工业生产中得到广泛应用。
压力真空成型是一种利用压力和真空力来注入液态材料进行成形的技术。
在压力真空成型中,将液态材料放入模具中,并在一定的压力和真空条件下,使其充满整个模腔,并在固化过程中保持形状。
压力真空成型技术适用于各种不同材料的成形,如橡胶、塑料、陶瓷等。
液态成形工艺技术具有许多优点。
首先,液态成形工艺技术可以生产高精度的零部件和产品,尺寸和形状的精准度较高。
其次,液态成形工艺技术可以实现大规模的生产,生产效率较高。
此外,液态成形工艺技术具有良好的表面质量和产品性能,可以生产出高质量的产品。
然而,液态成形工艺技术也存在一些局限性。
首先,液态成形工艺技术对模具的要求较高,模具制造成本较高。
其次,对液态材料的选择和控制有一定的技术要求,不同的液态材料需要不同的成形工艺。
此外,液态成形工艺技术在处理高温材料和特殊材料时存在一定的困难。
总之,液态成形工艺技术是一种重要的加工技术,能够生产出高精度、高性能的零部件和产品。
随着材料和工艺的不断创新,液态成形工艺技术将在工业生产中发挥越来越重要的作用。
材料液态成形工艺

第一节 金属铸造工艺简介
2.收缩导致的铸件缺陷
(1)缩孔和缩松 铸件在凝固过程中,由于金属液态收缩和凝
固收缩造成的体积减小得不到液态金属的补充 ,在铸件最后凝固的部位形成孔洞。其中容积 较大而集中的称缩孔,细小而分散的称缩松。 缩孔和缩松的形成过程示意图分别见图7-6和 图7-7。使铸件的凝固按薄壁-厚壁-冒口的 顺序先后进行,让缩孔移入冒口中,从而获得 致密的铸件,如图7-8所示。
第一节 金属铸造工艺简介
(2)铸造应力、变形和裂纹
铸造应力按其形成原因的不同,分为热应力、 机械应力等。
减少铸造应力就应设法减少铸件冷却过程中各 部位的温差,使各部位收缩一致,如将浇口开在 薄壁处,在厚壁处安放冷铁,即采取同时凝固原 则,如图7-9所示。
铸造应力是导致铸件产生变形和开裂的根源。 图7-10为“T”形铸件在热应力作用下的变形情 况,虚线表示变形的方向。
,易产生浇不足、冷隔和粘砂等缺陷。铸钢的收缩性大 ,产生缩孔、缩松、裂纹等缺陷的倾向大 。
3.铸造有色金属 常用的有铸造铝合金、铸造铜合金等。它们大都具有
流动性好,收缩性大,容易吸气和氧化等特点,特别容 易产生气孔、夹渣缺陷。
六、新型材料-金属间化合物及其铸造性能 特点
第三节 砂型铸造
第三节 砂型铸造
根据造型材料不同,可将铸造方法分为砂型铸造 (Sand Casting Process) 和 特 种 铸 造 (Special Casting Process)两类。
图7-1所示为砂型铸造工艺过程示意图。
第一节 金属铸造工艺简介
第二节 铸造工艺基础知识
一、液态金属的充型能力
液态金属的充型能力(Mold Filling Capacity)是指液 态金属充满铸型型腔,获得形状完整、轮廓清晰铸件的能 力。
材料成型原理与工艺(01)-液态金属成形概论
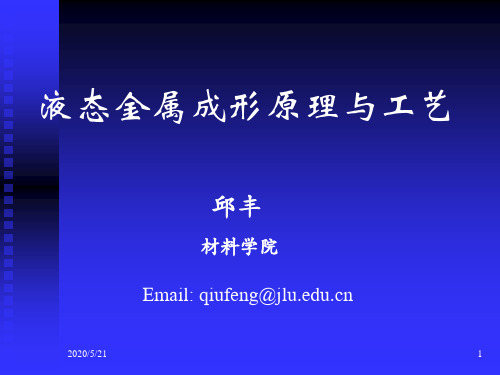
夹杂物的排除: 夹杂物的排除:
金属液静止处理、真空浇注,加熔剂, 金属液静止处理、真空浇注,加熔剂,过滤法
2012-1-8
凝固区域
固相区、凝固区、液相区
凝固方式
逐层凝固方式 体积凝固(糊状凝固方式) 体积凝固(糊状凝固方式) 中间凝固方式
2012-1-8 22
如果合金的结晶温度范围很宽,且铸件的温度分布较 为平坦,则在凝固的某段时间内,铸件表面并不存在 固体层,而液、固并存的凝固区贯穿整个断面。由于 这种凝固方式与水泥类似,即先呈糊状而后固化,故 称为糊状凝固。球墨铸铁、高碳钢、锡青铜和某些黄 铜等都是糊状凝固的合金。 中间凝固方式 大多数合金的凝固介于逐层凝固和糊状 凝固之间,称为中间凝固方式。中碳钢、高锰钢、白口 铸铁等具有中间凝固方式
气压保温浇包
15
采用德国KW公司技术的新二线主机,发动机缸体造型生产线。
罗兰门第制芯中心
2012-1-8 16
二、液态金属在铸型中的流动
1、 液态金属充型能力的基本概念 、
液态金属充满铸型型腔,获得形状完整、轮廓清晰的铸件的能力, 叫做液态金属充填铸型的能力,简称液态金属的充型能力。 液态金属充填铸型一般是在纯液态下充满型腔的,也有边充型边结晶的 情况,在充型过程中当液态金属中形成晶粒堵塞充型通道时,流动则停 止,造成铸件“浇不足”缺陷。 液态金属的充型能力(实验-螺旋形试样):
2012-1-8
18
思考题 1 1. 液态金属成形的概念是什么?液态金属 液态金属成形的概念是什么? 成形具有哪些优点? 成形具有哪些优点? 2. 液态金属成形生产过程。 液态金属成形生产过程。
液态金属成型工艺的研究与应用

液态金属成型工艺的研究与应用导言液态金属成型工艺是一种利用金属在高温状态下具有流动性的特点来进行加工和成型的技术。
它具有高精度、高效率、可塑性强等优点,并在航空航天、汽车制造、电子设备等领域得到广泛应用。
本文将探讨液态金属成型工艺在材料科学与工程中的研究和应用。
一、液态金属成型的基本原理液态金属成型是利用金属在高温状态下的流动性,通过控制金属的温度和形状来进行成型工艺。
通常液态金属成型工艺包括:压铸、浇铸、挤压、注射成形等。
压铸是将金属液体注入模具中,在高压下迅速冷却固化得到零件的一种工艺。
它具有制造复杂形状零件的优势,并且能够实现高度自动化和大规模生产。
浇铸是将金属液体注入到模具中,通过冷却后得到铸件的工艺。
它是一种常用的金属成型工艺,可以制造各种形状和尺寸的零件,广泛应用于汽车制造和航空航天等领域。
挤压是将金属材料加热至液态,通过挤压机的作用将液态金属迫入模具中,然后冷却固化成型。
挤压工艺适用于制造长条形零件或中空零件。
注射成形是将金属液体注射到模具中,通过冷却后得到零件的工艺。
它具有高精度和高稳定性的优势,常用于制造微小和复杂形状的零件。
二、液态金属成型的优势和应用液态金属成型工艺具有以下几个优势:1. 高精度:液态金属成型可以制造出高精度的零件,满足现代产品对精度的要求。
2. 高效率:液态金属成型工艺可以实现连续生产,提高生产效率,节省时间和成本。
3. 可塑性强:液态金属成型可以加工各种复杂形状的零件,具有较强的可塑性和可变性。
液态金属成型工艺在多个领域得到广泛应用:1. 航空航天领域:液态金属成型工艺可以用于制造飞机的发动机部件、燃烧室等关键零件,提高飞行器的性能和安全性。
2. 汽车制造领域:液态金属成型可以用于制造汽车发动机、车身结构和底盘等部件,提高汽车的性能和安全性。
3. 电子设备领域:液态金属成型工艺可以用于制造电子产品的外壳、散热器和连接器等零件,提高产品的可靠性和美观度。
三、液态金属成型的研究进展液态金属成型工艺的研究一直是材料科学与工程领域的热点。
液态金属成型

gx −
1 ∂P +ν ρ ∂x
∂ 2u ∂ 2u ∂ 2u ∂ u ∂u ∂u ∂u ∂ x2 + ∂ y2 + ∂ z2 = ∂t + u ∂x + v ∂y + w∂z
∂ 2v ∂ 2v ∂ 2v ∂ v 1 ∂P ∂v ∂v ∂v gy − +ν + + 2 = + u + v + w 2 2 ρ ∂y ∂x ∂y ∂z ∂y ∂z ∂t ∂x gz − 1 ∂P +ν ρ ∂z ∂ 2w ∂ 2w ∂ 2w ∂ w ∂w ∂w ∂w ∂ x2 + ∂ y2 + ∂ z2 = ∂t + u ∂x + v ∂y + w ∂z
五、实验报告 分析总结铝合金的熔炼处理工艺流程,比较精炼处理、 变质处理、 振动以及冷却条件对 铝合金组织及性能的影响。
实验二、液态成型过程 CAE 实验 一、基础理论 计算机辅助工程( Computer Aided Engineering,简称 CAE)技术是一门以 CAD/CAM 技术水平的提高为发展动力,以高性能计算机及图形显示设备的推出为发展条件,以计算 力学和传热学、 流体力学等的有限元、 有限差分、 边界元、 结构优化设计及模态分析等方法为 理论基础的新技术。目前液态成型 CAE 主要以铸件的温度场模拟和流动场模拟为主,软件 水平已经达到实用化,国内外均有商品化软件出现。国外主要有德国的 MagmaSoft、美国的 ProCAST、 Flow3D、 韩国的 AnyCAST 等,国内主要有华中科技大学的华铸 CAE、 清华的 FTStar、华北工学院的 CastSoft 等。 1)温度场模拟 温度场模拟主要是利用传热学原理,分析铸件的传热过程,模拟铸件的冷却凝固进程 ,
液态金属成型

液态金属成型金属液态成型论文作者:刘永星摘要:金属液态成型又称为铸造,是将液态金属在重力或外力作用下充填到型腔中,待其冷却凝固后,获得所需形状和尺寸的毛坯或零件,即铸件的方法,它是成形毛坯或机器零件的重要方法之一。
工程材料除切削加工以外有各种成型方法,包括金属液态成型、金属塑性成形、材料连接成型、粉末冶金成型以及塑料、橡胶、陶瓷等非金属材料成型及复合材料成型等。
材料成型技术主要讲述金属材料成型和非金属材料成型,现对金属液态成型进行详细论述。
关键词:金属液态成型、成型方法、生产流程、成型原理、选择成型依据一、金属液态成形金属材料在液态下成形,具有很多优点:(1)最适合铸造形状复杂、特别是复杂内腔的铸件。
(2)适应性广,工艺灵活性大。
(3)成本较低。
但液态成形也有很多不足,如铸态组织疏松、晶粒粗大,铸件内部常有缩孔、缩松、气孔等缺陷产生,导致铸件力学性能、特别是冲击性能低于塑形成行件;铸件涉及的工序很多,不易精确控制,铸件质量不稳定;由于目前仍以砂型铸造为主,自动化程度还不够高,工作环境较差;大多数铸件只是毛坯件,需经过切削加工才能成为零件。
砂型铸造是将熔融金属浇入砂质铸型中,待凝固冷却后,将铸型破坏,取出铸件的铸造方法,是应用最为广泛的传统铸造方法,它适用于各种形状、大小及各种常用合金铸件的生产。
砂型铸造的工艺过程称为造型。
造型是砂型铸造最基本的工序,通常分为手工造型和机器造型两大类。
手工造型时,填砂、紧实和起模都用手工和手动完成。
其优点是操作灵活、适应性强、工艺装备简单、生产准备时间短。
但生产效率低、劳动强度大、铸件质量不易保证。
故手工造型只适用于单件、小批量生产。
机器造型生产率很高,是手工造型的数十倍,制造出的铸件尺寸精度高、表面粗糙度小、加工余量小,同时工人劳动条件大为改善。
但机器造型需要造型机、模板以及特质砂箱等专用机器设备,一次性投资大,生产准备时间长,故适用于成批大量生产,且以中、小型铸件为主。
第一节 金属的液态成形原理

决定凝固方式的因素: (1)结晶温度范围 (2)铸件断面温度场分布变化
二 液态合金的充型能力
充型: 液态合金填充铸型的过程. 充型能力 : 液态合金充满铸型型腔 , 获得形状完整 , 轮廓清晰的铸件的能力
若充型能力不足,易产生:
1)浇不足: 不能得到完整隙或凹坑 , 机械性能下 降.
2) 共晶成分流动性好:恒温凝固,固体层表面光滑,且熔点 低,过热度大;
3) 非共晶成分流动性差: 结晶在一定温度范围内进行,初 生树枝状晶阻碍液流 。 常用铸造合金中,铸铁的流动性最好,铸钢的流动性最差。
逐层凝固(好)
糊状凝固(差)
不同成分合金流动性
(过热度)
碳钢
铸铁
碳钢随着结晶温 度范围的增加而 流动性变差;亚 共晶铸铁随含碳 量的增加流动性 提高。
纵向温度分布曲线
冷铁
同时凝固— 整个铸件几乎同时凝固。
同时凝固特点:不需冒口,节约金属且工艺简单;铸件均 匀冷却,减小热应力,不易形成内应力、变形和裂纹等缺 陷,但心部缩松有时难以避免,故用于收缩小的合金和各 种合金的薄壁铸件。如灰铸铁,锡青铜,铝硅合金等。 (1)这是由于薄壁铸件的铸型冷却作用强,薄壁断面温 度梯度大,倾向于逐层凝固。因此收缩小的灰铸铁可消除 缩孔,获得致密铸件;而收缩较大的薄壁铸钢、有色合金 铸件会出现轴线缩松,但其表层组织致密。
温度
固
液
表层
中心
铸件的凝固方式
2)糊状凝固
• 结晶温度范围很宽 的合金,从铸件的 表面至心部都是固 液两相混存。 • 铸件断面上布满小 晶体,将金属液分 割开,致充型和补 缩能力变差。
温度
固
液
表层
中心
铸件的凝固方式
液态成型工艺课程设计
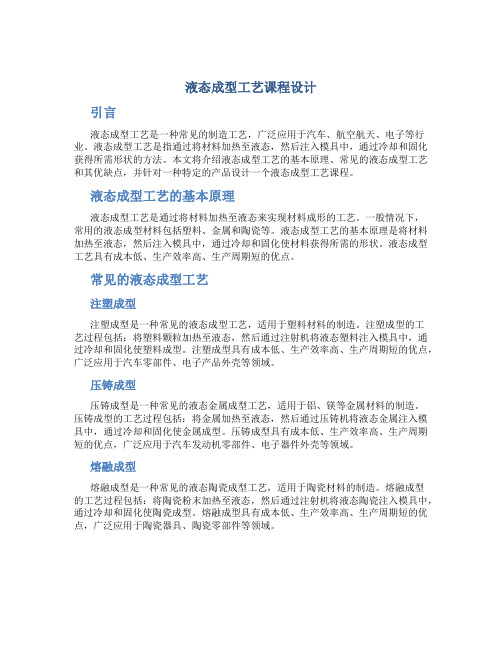
液态成型工艺课程设计引言液态成型工艺是一种常见的制造工艺,广泛应用于汽车、航空航天、电子等行业。
液态成型工艺是指通过将材料加热至液态,然后注入模具中,通过冷却和固化获得所需形状的方法。
本文将介绍液态成型工艺的基本原理、常见的液态成型工艺和其优缺点,并针对一种特定的产品设计一个液态成型工艺课程。
液态成型工艺的基本原理液态成型工艺是通过将材料加热至液态来实现材料成形的工艺。
一般情况下,常用的液态成型材料包括塑料、金属和陶瓷等。
液态成型工艺的基本原理是将材料加热至液态,然后注入模具中,通过冷却和固化使材料获得所需的形状。
液态成型工艺具有成本低、生产效率高、生产周期短的优点。
常见的液态成型工艺注塑成型注塑成型是一种常见的液态成型工艺,适用于塑料材料的制造。
注塑成型的工艺过程包括:将塑料颗粒加热至液态,然后通过注射机将液态塑料注入模具中,通过冷却和固化使塑料成型。
注塑成型具有成本低、生产效率高、生产周期短的优点,广泛应用于汽车零部件、电子产品外壳等领域。
压铸成型压铸成型是一种常见的液态金属成型工艺,适用于铝、镁等金属材料的制造。
压铸成型的工艺过程包括:将金属加热至液态,然后通过压铸机将液态金属注入模具中,通过冷却和固化使金属成型。
压铸成型具有成本低、生产效率高、生产周期短的优点,广泛应用于汽车发动机零部件、电子器件外壳等领域。
熔融成型熔融成型是一种常见的液态陶瓷成型工艺,适用于陶瓷材料的制造。
熔融成型的工艺过程包括:将陶瓷粉末加热至液态,然后通过注射机将液态陶瓷注入模具中,通过冷却和固化使陶瓷成型。
熔融成型具有成本低、生产效率高、生产周期短的优点,广泛应用于陶瓷器具、陶瓷零部件等领域。
液态成型工艺课程设计课程目标本液态成型工艺课程的目标是培养学生对液态成型工艺的基本原理和常见工艺的了解,以及掌握液态成型工艺在产品设计和制造中的应用能力。
通过本课程的学习,学生将能够独立完成一个液态成型产品的设计和制造。
课程内容第一章:液态成型工艺概述•液态成型工艺的定义和分类•液态成型工艺的优缺点及应用领域•液态成型工艺与传统加工方法的比较第二章:注塑成型工艺•注塑成型工艺的基本原理和流程•注塑成型机的结构和工作原理•注塑成型工艺中的关键技术和操作要点第三章:压铸成型工艺•压铸成型工艺的基本原理和流程•压铸机的结构和工作原理•压铸成型工艺中的关键技术和操作要点第四章:熔融成型工艺•熔融成型工艺的基本原理和流程•熔融成型机的结构和工作原理•熔融成型工艺中的关键技术和操作要点第五章:液态成型工艺在产品设计中的应用•液态成型工艺在产品设计中的优势和局限性•液态成型工艺与产品设计的关系•液态成型工艺在不同行业的实际应用案例课程教学方法本液态成型工艺课程采用理论教学与实践教学相结合的教学方法。
金属材料八大成形工艺

金属材料八大成形工艺金属材料成形方法是零件设计的重要内容,也是制造者们极度关心的问题,金属成形工艺的八大工艺:铸造、塑性成形、机加工、焊接、粉末冶金、金属注射成型、金属半固态成型、3D打印。
01铸造液态金属浇注到与零件形状、尺寸相适应的铸型型腔中,待其冷却凝固,以获得毛坯或零件的生产方法,通常称为金属液态成形或铸造。
工艺流程:液体金属→充型→凝固收缩→铸件工艺特点:1)可生产形状任意复杂的制件,特别是内腔形状复杂的制件。
2)适应性强,合金种类不受限制,铸件大小几乎不受限制。
3)材料来源广,废品可重熔,设备投资低。
4)废品率高、表面质量较低、劳动条件差。
铸造分类:(1)砂型铸造(sand casting)砂型铸造:在砂型中生产铸件的铸造方法。
钢、铁和大多数有色合金铸件都可用砂型铸造方法获得。
工艺流程:技术特点:1)适合于制成形状复杂,特别是具有复杂内腔的毛坯;2)适应性广,成本低;3)对于某些塑性很差的材料,如铸铁等,砂型铸造是制造其零件或,毛坯的唯一的成形工艺。
应用:汽车的发动机气缸体、气缸盖、曲轴等铸件(2)熔模铸造(investmentcasting)熔模铸造:通常是指在易熔材料制成模样,在模样表面包覆若干层耐火材料制成型壳,再将模样熔化排出型壳,从而获得无分型面的铸型,经高温焙烧后即可填砂浇注的铸造方案。
常称为“失蜡铸造”。
工艺流程:优点:1)尺寸精度和几何精度高;2)表面粗糙度高;3)能够铸造外型复杂的铸件,且铸造的合金不受限制。
缺点:工序繁杂,费用较高应用:适用于生产形状复杂、精度要求高、或很难进行其它加工的小型零件,如涡轮发动机的叶片等。
(3)压力铸造(die casting)压铸:是利用高压将金属液高速压入一精密金属模具型腔内,金属液在压力作用下冷却凝固而形成铸件。
工艺流程:优点:1)压铸时金属液体承受压力高,流速快2)产品质量好,尺寸稳定,互换性好;3)生产效率高,压铸模使用次数多;4)适合大批大量生产,经济效益好。
- 1、下载文档前请自行甄别文档内容的完整性,平台不提供额外的编辑、内容补充、找答案等附加服务。
- 2、"仅部分预览"的文档,不可在线预览部分如存在完整性等问题,可反馈申请退款(可完整预览的文档不适用该条件!)。
- 3、如文档侵犯您的权益,请联系客服反馈,我们会尽快为您处理(人工客服工作时间:9:00-18:30)。
冒口。
冒口补缩原理
二、选择冒口位置的原则
1.冒口应就近设在铸件热节(hot spot)的上方或侧 旁; 2.冒口应尽量设在铸件最高、最厚的部位; 3.冒口不应设在铸件重要的、受力大的部位; 4.冒口不应选在应力集中处; 5.应尽量用一个冒口补缩几个热节或铸件; 6.冒口不应在加工面上。
金属液过滤器安放位置
泡沫陶瓷过滤器过滤机理
• • 1.“滤饼”机制 复杂的泡沫陶瓷结构,可以高效率 地机械挡渣,当金属液通过结构复 杂的泡沫陶瓷过滤器时,通过过滤 介质的机械分离作用,把大于过滤 器表面孔眼的夹杂物滤除,并使之 沉积在过滤器液态金属流入端,成 为过滤器的一个组成部分。随着夹 杂物在过滤器表面上堆积数量的增 多,逐渐形成了一层“滤饼”,使 金属液流道进一步变细,因而新增 的过滤介质表面可以滤除更为细小 的夹杂物。与此同时,介质内部也 有过滤作用,在贯穿于陶瓷体的众 多小孔中,有的呈现微小狭缝,有 的存在死角,这些变化不同的区域 都是截获夹杂物的可能位置。
第一章
液态金属成形过程及控制
1.1 液态金属的充型及流动 1.2 浇注系统 1.3 凝固过程的工艺分析 1.4 冒口和冷铁
1.1液态金属的充型及流动
• 概述:充型+凝固→铸造成形→质量 一、液态金属充型的水力学特征及在浇注系统中的流动 水力学特征: ①粘性流动←粘度→合金成分,温度,结晶 ②流动的不稳定性 ③散体材料的“多孔管流动”
铸件
1.位置(4)-阶梯式
a)多直浇道式 b)用塞球法控制式 c)控制各 组元比例式 d)带缓冲直浇道 e)带反直浇道式
2.按各单元断面积的比例
• 收缩式:A直﹥ A横﹥ A内 • 扩张式: A直﹤ A横﹤ A内 • 半扩张式: A直﹤ A横﹥ A内
经验的重要
3.浇注系统尺寸的确定(1)
• 按流体力学的经验公式计算浇注系统的最小断面积: ①Amin=G/0.0443γτμ√Hp A-直浇道出口的断面积(开放式)或内浇道的截面积(收 缩式) G-液态金属的质量 γ-液态金属的密度 Τ-浇注时间 μ-流量系数 Hp -金属液的平均静压头 ②各单元截面积之比及结构形式→浇注系统的具体尺寸
冒口和冷铁的设计
2.冒口的补缩原理 1)基本条件 2)选择冒口位置的原则 3)有效补缩距离的确定 3.影响补缩的因素 1)合金种类 2)冷铁 冒口的凝固时间≧铸件(被补缩部分)的凝固时间; 2.有足够的金属液补充铸件的液态及凝固收缩; 3.在凝固前,冒口和被补缩部分存在补缩通道,扩张角向着
金属液的过滤装置
泡沫陶瓷过滤器性能
• 泡沫陶瓷过滤器的孔洞曲折,能有效地阻止非金 属夹杂物流过。 • 主要技术特性:透气率,孔隙率、孔眼大小(或孔 数)和厚度。 • 透气率的适用范围为 (400~8000)X10-7cm2 。透气 率过低,流动阻力大,要求很高的金属压力头, 因而不适用,透气率过高,杂质通过率高,效果 差。当金属液较脏时,应先用粗网过滤,后用细 网过滤,以防夹杂物堵塞孔洞。 • 孔隙率应控制在70%-95%。孔的大小一般用单 位面积的孔数表示(或者用平均孔径表示)。
1.2 浇注系统的设计
(一)类型及应用
按液态金属引入铸型型腔的位置分类; 按浇注系统各单元断面积的比例分类
(二)浇注系统的尺寸计算
1.位置(1)-顶注式
a)简单式 b)刀片式 c)压边式 d)雨淋式 e)搭边式
1.位置(2)-底注式
a)基本式
b)牛角式
c)底雨淋式
1.位置(3)-中间注入式
出气冒口 冒口
浇注系统尺寸的确定(2)
• 用反推法计算浇注系统的截面尺寸:
1.浇注系统的类型和结构型式 ↓ 2.内浇道的数量和总截面积 ↓ 3.内浇道的尺寸 ↓ 4.由浇道截面比确定各单元的尺寸
1.3液态金属凝固收缩过程
1.液态金属凝固过程的工艺特点 *铸件的凝固方式:
*铸件的凝固方向
2.液态成形收缩过程的工艺特点及对 铸件质量的影响
2.表面效应
当金属液流经结构复杂的陶瓷体时, 被分割成许 多细小的流股,增大了金属液中夹杂物与过 滤介质的接触面积及接触几率,由于过滤器 表面具有极微小的凹凸面,凹块尺寸约1— 10μm,具有静电吸附和粘附截流作用。
3.整流效应
金属液流过泡沫陶瓷过滤器时,被 分割成许多细小单元的流股, 其直径较小,从而使雷诺数(Re =vd/r)变小,使液流趋于层流 运动。当金属液处于层流状态 时,由于熔融金属液的密度远 大于夹杂物的密度,因而使夹 杂物有充分的时间上浮除去, 也即泡沫陶瓷过滤器能辅助横 浇道挡渣。浇注系统中放置过 滤器后,金属液流动的阻力增 加,在横浇道中流动的金属液 容易形成充满流动,并使流速 降低,有利于夹杂物上浮,并 滞留在横浇道顶面。
Re数值→充型稳定性 →渣、气等铸件质量问题
液态金属在浇注系统中的流动
1.液态金属在浇口杯中的流动
漏斗式
盆式
水平旋涡及其影响因素
浇口盆
2.在直浇道中的流动
• 水力学流动态 1.充满式:上大下小型 2.非充满式:等截面型
浇口窝
3.在横浇道中的流动
• 搭接式(a)和双重式(b)横浇道 • 横浇道末端延长段的形式
4.在内浇道中的流动-流量分配的不 均匀性
流经内浇道的流量偏差
1
2 3 4
5.金属液在浇注系统中的过滤
• 在铸造生产中,由于非金属夹杂物等铸造缺陷导 致的铸件废品率一般占废品总数的50%—60%。 采用金属液过滤技术,可以有效地减少或消除其 中的非金属夹杂物,净化液态铸造合金。
• • • • • 减少金属中的夹杂物-夹渣缺陷减少 改善了金属的力学性能(疲劳、抗蚀等) 改进了切削性能,延长刀具寿命 提高了铸件表面品质,减少了加工余量 简化了浇注系统结构,提高了工艺出品率
• 缩孔、缩松的形成
缩孔、缩松产生的原因及部位
缩孔、缩松的防止: 冒口、冷铁、补贴-顺序凝固 冷铁-逐层凝固
1.4冒口和冷铁设计
一、冒口:在铸型内用以储存金属液的空腔,有防止缩孔、 缩松、排气和集渣的作用。 1. 种类及形状
常用冒口形状
a)铸钢件
b)铸铁件
1-明顶冒口 2-暗顶冒口 3-侧冒口 4-铸件