中厚板生产坯料设计
中厚板设计

1 产品方案与坯料的选择1.1 产品方案的主要内容产品方案是设计任务书的主要内容之一,是进行车间设计时制定产品生产工艺过程中,确定轧机组成和选择各项设备的主要依据。
制定产品方案的主要原则:(1)满足国民经济发展对轧制产品的需求,特别是根据市场信息解决某些短缺产品的供应和优先保证国民经济重要部门对与钢材的需要。
(2)考虑各类产品的平衡,尤其是地区之间产品的平衡。
要正确处理长远与当前,局部和整体的关系。
做到供应适合,品种平衡。
产销对路,布局合理,要防止不顾轧机特点,不顾车间具体工艺设备条件一哄而上,一哄而下的倾向。
(3)考虑轧机生产能力的充分利用和建厂地区的合理分工。
有条件的要争取轧机的专业化和产品系列化的发展,以利于提高轧机生产技术水平。
(4)考虑建厂地区资源及环境条件,物资和材料等道路运输情况,逐步完善和配套起我国自己的独立的轧钢生产体系。
(5)要逐步解决产品品种和规格老化问题要适应当前对外开放,对内搞活新的经济形式的需要,要根据车间工业设备的情况,力争做到产品结构和产品标准的现代化,有条件的考虑生产一些出口产品,走向国际市场。
产品方案的主要内容包括:(1)车间生产的钢种和生产的规模;(2)各类产品的品种和规格(3)种类产品的数量和其在总量中所占的比例。
各种产品的品种和规格及种类产品的数量和其在总量中所占的比例如表所示表1-1中厚板产品方案(典型产品:1.2金属平衡表成品率的倒数即为金属的消耗系数。
它表示轧制一吨成品需要多少吨原料。
所以成品的数量乘以1金属消耗系数就是金属的需要量。
即:原料需要量=金属消耗系数×成品数量为分析轧钢生产中金属的损失,寻找降低损失的途径。
须编制金属平衡表按本次设计要求。
本设计只列出典型产品的金属平衡表。
单位(万t)表1-2金属平衡表1.3坯料的技术条件1.3.1中厚板的坯料选用中厚板生产采用的原料有扁锭、初扎坯、连铸坯、三种。
中厚板坯料尺寸自动控制研究

21 0 2年EAVY LATE P
V 1 1 No 4 o . 8. .
Au ut 2 2 g s 01
‘23 ・
中厚 板 坯 料 尺 寸 自动 控 制 研 究
张立 超 马有辉 宁利 辉 吴 尚超
( 邯郸 钢铁公 司) 摘 要 中厚板生 产的特 点是批量小 、 规格 多 , 因此坯料尺寸的设计对生产效率、 成材率有着重要的影响。
( adnI nadS e C .t) H n a r n t l o Ld o e
Ab ta t T e me i m d h a y p ae p o u t n fau e ma ac ie ag p cf a o a g .T e d sg fsa s r c h d u a e v lt r d c i e tr s s l b th s ,l re s e i c t n rn e h e in o lb n o l z i i
式 中 : ~氧化 铁 皮 增 重/ g・cl ) K ( r f ; 一
氧 化 速 率 ; 一氧 化 动 力 系 数 , 于 普 碳 钢 , 对 取
4 5 ( 0 ) 一加 热 时 间/ ; . 6 P : H ; s Q一各 钢 种 的激 活 能 , 于 Q 3 B钢 , 13 9 Jm l T一温 度/ 对 25 取 5 . / o ;
K。
在 加热 过程 中 , 内温度 不是恒 定不 变 的 , 炉 而
在坯 料设计 时要 先 分 析 体 积 损 失 的分类 和数 量 ,
dme s n h s a mp ra te e to h r d cin e f i n y a d yed r t . E f i n n c u ae sa e i n a tmai i n i a i o tn f c n te p o u t f c e c o n o i n il a o i f ce t a d a c r t l d sg i u o t i b n c mo e i a f c v a o s i t e mo e n me i m d h a y pa e p o u t n d e e t e w y t u t l d r d u a e v lt r d ci .Au o t o t lo lb d me so a e a sn i l n o tmai c n r fsa i n in c n b — c o c iv d b a so n lsso h aa t r fr h a n u n c ,pa e mi ,c oi g b d a d s e r n me i m n e v he e y me n fa ay i n t e p rmees o e e t g fr a e lt l i l ol e n n h a s i d u a d h a y p ae r ln ln d c mp t rp g a lt o l g pa t i n a o u e r rmmi g o n. Ke wo d Me u a d h a l t rd cin,S a i n in d sg , tma i o t l y rs i d m n e v p ae p o u t y o l b d me s e i Auo t c n r o n c o
中厚板压下规程设计

一.制定生产工艺及工艺制度1.生产工艺:选择坯料——原料清理——加热——除鳞——纵轧一道(使宽度接近成品宽度)——转90˚横轧到底——矫直——冷却——表面检查——切边——定尺——表面尺寸形状检查——力学性能试验——标记——入库——发货2.工艺制度:在保证压缩比的条件下,坯料尺寸尽量小。
加热时出炉温度应在1120˚—1150˚,温度不要过高,以免发生过热或过烧现象;用高压水去除表面的氧化铁皮,矫直时选用辊式矫直机矫直,开始冷却温度一般要尽量接近终轧温度,轧后快冷到相变温度以下,冷却速度大多选用5—10˚C或稍高一些。
切边用圆盘式剪切机进行纵剪,然后用飞剪定尺。
二.选择坯料1.根据生产经验和实践,目前生产中厚板选择连铸坯已成为主流,所以选择连铸坯2.坯料尺寸的确定坯。
(1)坯料厚度的确定:根据经验,压缩比在6—10之间较好,本设计取10,由成品厚度h=13mm知H=10h=130mm。
(2)坯料宽度的确定假设先轧两道,压下量分别为20mm和10mm,且设两道轧后其长度等于宽度。
假设轧后金属烧损不计,考虑切头尾,切边。
在我国切头尾一般为500mm—2500mm取Δl=500mm,切边Δb=100mm,由体积不变定理得Bˊ×Lˊ×[H-(20+10)]=(l+2×500)×(b+2×100)×13因为Bˊ=Lˊ所以Bˊ=Lˊ=(9000+2×500)(1900+2×100)×13/[130-(20+10)]=1650mm(3)坯料长度的确定由H,B,Bˊ,Lˊ由体积不变定理得H×B×L=Hˊ×Bˊ×Lˊ得L=1270mm三.变形量分配1.根据经验,中厚板压下量在Δh=12mm左右,这里取Δh=12mm2.分配各道次压下量,计算各道次变形程度,轧件尺寸及轧制道次(1)由H=130mm,h=13mm,取轧制道次n=12(二辊7道四辊五道)(2)第一道,先用展宽轧制把坯料的宽度B轧成b(或接近b)且不考虑长度变化由体积不变定理得B×L×H=B×L×(H-Δh1)得Δh1=17mm则变形程度ε1=Δh/H×100%=13.08%轧后轧件尺寸为113×1900×1270mm同理其余道次压下量分配,变形程度,轧件尺寸如下表所示四.设计变形工具1.设计二辊(1)辊身长度L:由L=bmax+a bmax=1900mm 当b=1000-2500mm a=150-200mm 取a=200mm所以L=1900+200=2100mm(2)辊径尺寸中厚板轧机L/D=2.2-2.8 取L/D=2.6 得D=808mm 取810mm(3)辊颈尺寸查表3-5 取d/D=0.75(轧钢机械邹家祥主编) 得d=608mm取d=600mm辊颈长度l 取d/l=1 得l=600mm(3)辊头设计因为对于中厚板轧机来说轧辊调整行程比较大,倾角在8˚-12˚间所以应选择万向辊头。
中厚板坯料组板设计

因此 中厚 板 生产必 须 进行 订单 组合 ,即将 合 同订货 的成 品小 板组 合 为轧 制大 板 ,用 同一块 坯料 轧 制 的 方式 ,以解决 市场 小 批量需 求 与轧 机 大批量 高效 生
ye dat i x elnt i . il lan e c le m a
Ke r s s r a t ;l bsz e in; il y wo d : p e d r e sa ied sg yed a
1 前 言
宝 钢集 团新 疆八 一 钢铁 有 限公 司 ( 以下 简 称八
两 种合 同是组 板设 计关 键 , 增加 了组 板设 计 的难度 。
坯 料设 计 的流 程见 图 1 2 3 、 、。
30 mm单 机架 轧 机 投 产后 ,通过 组 板 设 计 的 50
坯料 尺 寸 , 足生 产需 求 , 满 产量 和成 材 率指标 逐 步在
提 高 ,其 中单 定 尺板 的综 合 成材 率 已接 近 9 %, 2 达
结 合 产 品订 单 、 制 规程 来 设 计 中厚 板 生 产 所 需 坯料 , 而达 到成 材 率 最 优 的 目的 。 轧 从 关 键 词 : 展 宽 比 ; 料 组 板 设 计 ; 材 率 坯 成
中 图分 类 号 : G 3 .+ T 35 2 5 文 献标 识 码 : B 文 章编 号 :17 - 4 2 ( 0 0 0 —0 4— 0 6 2 2 4 2 1 )4 0 7 2
到 了 国 内同类 型 单 机架 轧 机 成 材 率 的平 均 水 平 , 这
说 明 目前 八钢 中厚 板采 用 的坯 料组 板设 计 理念 和方
2.2 中厚板生产---轧制工艺部分

(2)狗骨轧制法(DBR法,Dog Bone Rolling) 狗骨轧制法(DBR法 (DBR
与MAS法的补偿原理基本相同,不同之处在于,狗 MAS法的补偿原理基本相同,不同之处在于, 法的补偿原理基本相同 骨轧制法只能解决轧件头尾的“舌形” 骨轧制法只能解决轧件头尾的“舌形”,不能补偿轧件边 部的不均匀变形。 部的不均匀变形。
2
产
(轧制工艺部分) 轧制工艺部分)
2.2 中厚钢板生产工艺
图 中厚板生产工艺流程图
2.2.1 原
料
用于生产中厚钢板的原料有扁钢锭、 用于生产中厚钢板的原料有扁钢锭、 初轧板坯、锻压坯、压铸坯和连铸板坯几种。 初轧板坯、锻压坯、压铸坯和连铸板坯几种。
1、原料尺寸的原则是: 原料尺寸的原则是: (1)原料的厚度尺寸在保证钢板压缩比的前提下应尽可 能小。 能小。 (2)原料的宽度尺寸应尽量大,使横轧操作容易。 原料的宽度尺寸应尽量大,使横轧操作容易。 (3)原料的长度应尽可能接近原料的最大允许长度。 原料的长度应尽可能接近原料的最大允许长度。 钢板的材质是指钢的化学成分. 2、 钢板的材质是指钢的化学成分. 中厚钢板的钢种有:碳素结构钢、优质碳素结构钢、 中厚钢板的钢种有:碳素结构钢、优质碳素结构钢、 碳素工具钢、低合金钢、弹簧钢、 碳素工具钢、低合金钢、弹簧钢、高速工具钢及其他各种 合金钢。 合金钢。不同材质的钢板的材质要求参照其相关标准来规 定。
角轧的优缺点: 角轧的优缺点:咬入条件 减少冲击力, 减少冲击力, 效率低
图
角轧
3 精轧
控制钢板厚度 主要任务 板形 表面质量和性能
2.2.4 平面形状控制
• 平面形状控制:钢板的矩形化控制。 平面形状控制:钢板的矩形化控制。 在成形轧制和展宽轧制阶段, 在成形轧制和展宽轧制阶段,不能认为是平面变 即无宽展变形),轧制中轧件在横向也发生了变形, ),轧制中轧件在横向也发生了变形 形(即无宽展变形),轧制中轧件在横向也发生了变形, 并且变形是不均匀的,轧后钢板的平面形状不再是矩形。 并且变形是不均匀的,轧后钢板的平面形状不再是矩形。
中厚板压下规程设计..
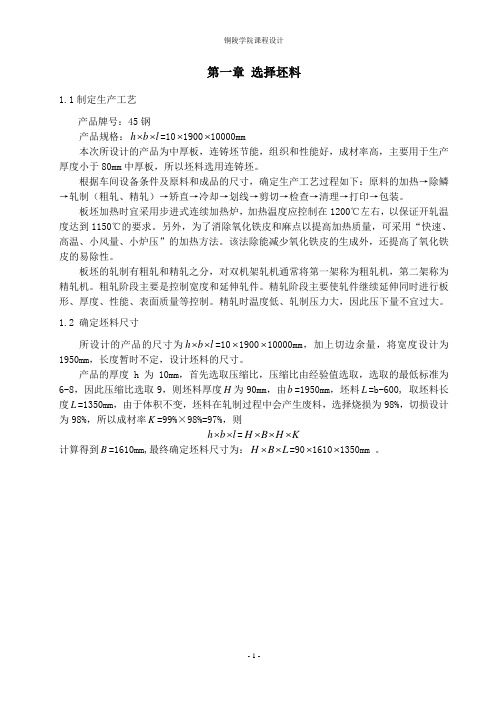
第一章选择坯料1.1制定生产工艺产品牌号:45钢产品规格:l⨯=10⨯1900⨯10000mmbh⨯本次所设计的产品为中厚板,连铸坯节能,组织和性能好,成材率高,主要用于生产厚度小于80mm中厚板,所以坯料选用连铸坯。
根据车间设备条件及原料和成品的尺寸,确定生产工艺过程如下:原料的加热→除鳞→轧制(粗轧、精轧)→矫直→冷却→划线→剪切→检查→清理→打印→包装。
板坯加热时宜采用步进式连续加热炉,加热温度应控制在1200℃左右,以保证开轧温度达到1150℃的要求。
另外,为了消除氧化铁皮和麻点以提高加热质量,可采用“快速、高温、小风量、小炉压”的加热方法。
该法除能减少氧化铁皮的生成外,还提高了氧化铁皮的易除性。
板坯的轧制有粗轧和精轧之分,对双机架轧机通常将第一架称为粗轧机,第二架称为精轧机。
粗轧阶段主要是控制宽度和延伸轧件。
精轧阶段主要使轧件继续延伸同时进行板形、厚度、性能、表面质量等控制。
精轧时温度低、轧制压力大,因此压下量不宜过大。
1.2 确定坯料尺寸所设计的产品的尺寸为l⨯=10⨯1900⨯10000mm,加上切边余量,将宽度设计为bh⨯1950mm,长度暂时不定,设计坯料的尺寸。
产品的厚度h为10mm,首先选取压缩比,压缩比由经验值选取,选取的最低标准为6-8,因此压缩比选取9,则坯料厚度H为90mm,由b=1950mm,坯料L=b-600, 取坯料长度L=1350mm,由于体积不变,坯料在轧制过程中会产生废料,选择烧损为98%,切损设计为98%,所以成材率K=99%×98%=97%,则h⨯⨯=KblH⨯⨯⨯HB计算得到B=1610mm,最终确定坯料尺寸为:L⨯=90⨯1610⨯1350mm 。
H⨯B第二章变形量分配2.1 确定轧制方法先经过二辊轧机纵轧一道,在不考虑切边的情况下,使板坯长度等于成品宽度,然后转90°横轧到所需规格。
2.2 确定道次压下量坯料尺寸:LBH⨯⨯ =90⨯1680⨯1350mm,则总的压下量为90-10=80mm。
中厚板的生产2

中厚板的生产工艺一、制定生产工艺根据车间设备条件及原料和成品的尺寸确定其生产工艺流程如下:原料的选择与加热—>除鳞—>轧制—>矫直—>冷却—>划线—>检查—>清理—>打印—>包装。
1、原料的选择与加热:轧制中厚板所用的厚料有扁钢锭、初轧板坯、连铸坯和压铸板四种。
现在大多都采用连铸坯,我国生产实践表明采用厚150mm的连铸坯生产厚度12mm以下的钢板较理想,为了提高轧机的生产量,板坯的单重和宽度逐渐增大,目前轧坯厚度在80mm~550mm,宽度在1000~2360mm,连铸坯厚度一般为180~300mm,宽度为800~2200mm,长度则取决与加热炉宽度和所需重量。
加热的目的是为了提高塑性、降低变形抗力,加热炉的形式可采用步进式加热炉,加热温度应控制在1250゜C左右,以保证开轧温度达到1200゜C的要求。
另外,为了消除氧化铁皮和麻点以提高加热质量,可采用“快速、高温、小风量、小炉压”的加热方法,该法除能减少氧化铁皮的生成外,还提高了氧化铁皮的易除性。
2、除鳞:除鳞是将坯料表面的炉生和次生氧化铁皮清除干净,以免轧制时压入钢板表面产生缺陷,它是保证钢板表面质量的关键工序。
炉生氧化铁皮采用大立辊侧压并配合高压水的方法清除。
次生氧化铁皮则采用轧机前后高压水喷头,喷高压水的方法来清除。
3、轧制:板坯的轧制分为粗轧和精轧,粗轧其方法有以下几种:a)全纵轧法b)横轧—纵轧法c)角轧—纵轧法d)纵轧—横轧法e)全横轧法根据不同条件,可采用不同的粗轧方法。
但为了调整原料形状,一般还开始纵轧1~2道。
精轧与粗轧之间没有明显的划分界限,在单机架轧机上,一般前期道次为粗轧,后期道次为精轧。
粗轧阶段主要是控制宽度和延伸轧件。
精轧阶段主要是轧件继续延伸同时进行板形、厚度、性能、表面质量等控制。
精轧时温度低,轧制压力大,因此,压下量不宜过大。
4、综合板轧后精整及热处理:中厚板精轧包括矫直、冷却、划线、剪切、检查及清理缺陷,必要时还要进行热处理。
30mm×2100mm×5000mm中厚板生产规程设计

典型产品生产规程设计1 制定生产工艺1.1制定生产工艺选择坯料→原料清理→加热→除磷→横轧两道次(使宽度接近成品宽度)→转90°纵轧到底→矫直→冷却→表面检查→切边→定尺→表面尺寸形状检查→力学性能检测→标记→入库→发货。
1.2制定工艺制度在保证压缩比的情况下,坯料尺寸尽量小,加热时出炉温度应在1120-1300℃,温度不要过高,以免发生过热或过烧现象;用高压水去除表面的氧化铁皮;矫直时采用辊式矫直机矫直,开使冷却温度一般要接近纵轧温度,轧后快冷到相变温度以下,冷却速度大都选用5-10°或稍高一些,切边时用圆盘式剪切机进行纵剪,然后用飞剪定尺。
2 制定压下规程2.1原料设计2.1.1原料的质量按成品钢板的质量和计划成材率计算出原料的质量。
计划成材率指的是在设计原料尺寸时的成材率,计算成材率可以按下面的公式计算。
=()()()()rp twlt t w w l l l s +∆+∆++计划成材率式中t —成品板厚度 W —成品板宽度 L —成品板长度t t +∆—轧制平均厚度 w w +∆—轧制平均宽度rp l —试样长度S —烧损 △t —宽度余量 △w —厚度余量2.1.2原料的尺寸由计算出的原料质量和连铸坯或初轧坯,钢锭的规格范围,考虑到压缩比,横轧时轧机送钢的最小长度,轧机允许最大轧制长度,加热炉允许装入长度等因素,决定原料的厚度、宽度和长度。
在选择原料尺寸时应注意尽可能采用倍尺轧制,即当计算出原料质量小于最大允许原料质量的一半时,应按倍尺轧制考虑选用厚度尺寸。
由于厚板特别是较厚板的订货坯料一般不大,甚至几家用户订货的钢板需要编组在一起进行轧制,因此在选择厚板原料的计算中需要考虑的因素很复杂,而且这些因素互相影响,互相制约。
选择成品尺寸为h ×b ×l=30mm ×2100mm ×5000mm 坯料尺寸:H=220mm B=1600mm取切边为30mm ∆=,切头、尾为50mm δ=,每块板坯轧成n 块成品,n=4 根据体积不变原理有:(b +2∆)×(l ×n +2δ)×h=H ×B ×L 代入数据求得:L=3700mm2.2轧制规程的设计2.2.1坯料的选择中厚板的原料的主体是连铸坯,为了确保成品钢板的综合性能,连铸坯与成品钢板间的最小压缩比保持在6:1以上。
中厚板课程设计

材料成型课程设计中厚板14*2800工艺设计姓名:学号:班级:指导老师:完成时间:2013年1月10日目录1. 设计题目2. 设计目的3. 设计任务4. 设计要求5. 设计方法及步骤5.1 制定生产工艺5.2 制定压下规程5.2.1 确定板坯料的尺寸5.2.2 确定轧制方法5.2.3 分配各道次压下量5.2.4 校核咬入条件5.3 确定速度制度5.3.1 确定速度图形式5.3.2 选择各道咬入、抛出转速5.3.3 计算各道纯轧时间5.3.4 确定各道间隙时间5.3.5 绘制速度图5.4 校核轧机5.4.1 计算各道轧制温度5.4.2 计算各道变形程度5.4.3 计算各道平均变形速度5.4.4 确定各道变形抗力5.4.5 确定各道变形区长度5.4.6 计算各道平均单位压力及各道总压力5.5 校核电机5.5.1 计算各道轧制力矩5.5.2 计算各道附加力矩5.5.3 计算空转力矩5.5.4 计算动力矩5.5.5 确定各道总传动力矩5.5.6 绘制电机负荷图6. 总结与收获7. 参考资料8. 附录8.1 本设计过程中主要为参数计算的Matlab 程序 8.2 Matlab 程序计算结果9. 轧机速度制度图1、电机负荷图2.设计内容一、设计题目:题目内容:用钢种为345Q 、坯料为mm 200*2300*2500的连铸坯轧制产品规格为mm 2800*14的板料的压下规程设计。
主要设备数 项目 粗轧机 精轧机 轧机型式 四辊可逆轧机 PC 轧机 工作辊辊身尺寸mm / 3800950~850⨯φ 3800950~850⨯φ 支撑辊辊身尺寸mm / 37001800~1700⨯φ 37001800~1700⨯φ 工作辊辊颈尺寸mm / 480500⨯φ 420450⨯φ 支撑辊辊颈尺寸mm / 11501200⨯φ 11501200⨯φ 工作辊材质 合金铸铁 合金铸铁 支撑辊材质 铸钢 铸钢 最大轧制压力MN / 70 70 最大轧制力矩m MN */ 2×2.6 2×1.975 最大轧制速度1/-ms 4.239 6.123 最大工作开口度mm / 500 400 主电机功率Km / 2×5000 2×5500 主电机转速rpm / 90~45~0 130~65~0 压下速度/mm s-1 25 15本设计主电机的功率分别选用:粗轧机组 Kw P H 500021⨯= 精轧机组 Kw P H 550022⨯=计算钢种:345Q 坯料:mm 200*2300*2500的连铸坯; 产品规格:2800*14已知条件:开轧温度1200℃,纵轧时开轧温度1150℃;轧机为单机架四辊可逆式,设有大立辊及高压水除鳞装置,机前还设有回转板坯的锥形辊道;工作辊辊身直径850~950毫米,支持辊辊身直径1700~1800毫米、辊颈直径1200毫米,辊身长度3700毫米;工作辊轴承为滚动轴承,支承辊轴承为油膜轴承;轧机最大允许轧制压力70MN ;主电机功率2×5000KW ,转速0~45~90rpm,最大允许扭转力矩2×2.6MN*m。
4300中厚板生产的车间设计(DOC)
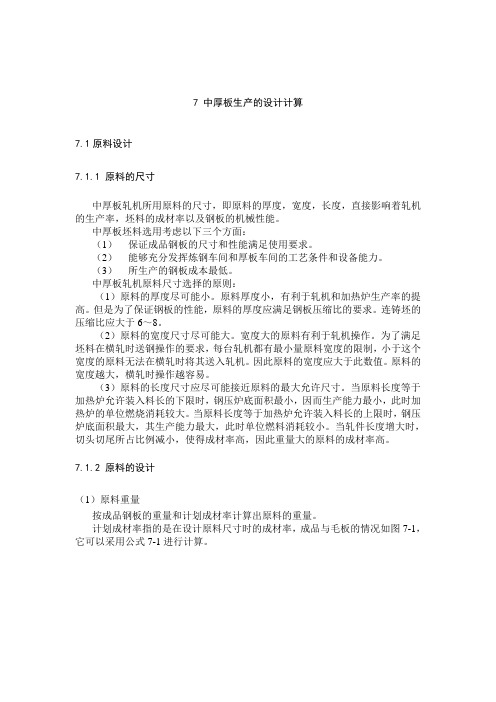
7 中厚板生产的设计计算7.1原料设计7.1.1 原料的尺寸中厚板轧机所用原料的尺寸,即原料的厚度,宽度,长度,直接影响着轧机的生产率,坯料的成材率以及钢板的机械性能。
中厚板坯料选用考虑以下三个方面:(1)保证成品钢板的尺寸和性能满足使用要求。
(2)能够充分发挥炼钢车间和厚板车间的工艺条件和设备能力。
(3)所生产的钢板成本最低。
中厚板轧机原料尺寸选择的原则:(1)原料的厚度尽可能小。
原料厚度小,有利于轧机和加热炉生产率的提高。
但是为了保证钢板的性能,原料的厚度应满足钢板压缩比的要求。
连铸坯的压缩比应大于6~8。
(2)原料的宽度尺寸尽可能大。
宽度大的原料有利于轧机操作。
为了满足坯料在横轧时送钢操作的要求,每台轧机都有最小量原料宽度的限制,小于这个宽度的原料无法在横轧时将其送入轧机。
因此原料的宽度应大于此数值。
原料的宽度越大,横轧时操作越容易。
(3)原料的长度尺寸应尽可能接近原料的最大允许尺寸。
当原料长度等于加热炉允许装入料长的下限时,钢压炉底面积最小,因而生产能力最小,此时加热炉的单位燃烧消耗较大。
当原料长度等于加热炉允许装入料长的上限时,钢压炉底面积最大,其生产能力最大,此时单位燃料消耗较小。
当轧件长度增大时,切头切尾所占比例减小,使得成材率高,因此重量大的原料的成材率高。
7.1.2 原料的设计(1)原料重量按成品钢板的重量和计划成材率计算出原料的重量。
计划成材率指的是在设计原料尺寸时的成材率,成品与毛板的情况如图7-1,它可以采用公式7-1进行计算。
)1)()()((s l l w w t t rp ++∆+∆+ 式中 t ——成品板厚度;w ——成品板宽度;l ——成品板长度;t t ∆+——轧制平均厚度;w w ∆+——轧制平均宽度;rp l ——试样长度;l ∆——长度余量;s ——烧损;t ∆——厚度余量;w ∆——宽度余量。
式中各量的确定方法如下:S ——烧损,即氧化铁皮损失,包括加热炉内生成的氧化铁皮。
4300中厚板生产的车间设计DOC

7 中厚板生产的设计计算7.1原料设计7.1.1 原料的尺寸中厚板轧机所用原料的尺寸,即原料的厚度,宽度,长度,直接影响着轧机的生产率,坯料的成材率以及钢板的机械性能。
中厚板坯料选用考虑以下三个方面:(1)保证成品钢板的尺寸和性能满足使用要求。
(2)能够充分发挥炼钢车间和厚板车间的工艺条件和设备能力。
(3)所生产的钢板成本最低。
中厚板轧机原料尺寸选择的原则:(1)原料的厚度尽可能小。
原料厚度小,有利于轧机和加热炉生产率的提高。
但是为了保证钢板的性能,原料的厚度应满足钢板压缩比的要求。
连铸坯的压缩比应大于6~8。
(2)原料的宽度尺寸尽可能大。
宽度大的原料有利于轧机操作。
为了满足坯料在横轧时送钢操作的要求,每台轧机都有最小量原料宽度的限制,小于这个宽度的原料无法在横轧时将其送入轧机。
因此原料的宽度应大于此数值。
原料的宽度越大,横轧时操作越容易。
(3)原料的长度尺寸应尽可能接近原料的最大允许尺寸。
当原料长度等于加热炉允许装入料长的下限时,钢压炉底面积最小,因而生产能力最小,此时加热炉的单位燃烧消耗较大。
当原料长度等于加热炉允许装入料长的上限时,钢压炉底面积最大,其生产能力最大,此时单位燃料消耗较小。
当轧件长度增大时,切头切尾所占比例减小,使得成材率高,因此重量大的原料的成材率高。
7.1.2 原料的设计(1)原料重量按成品钢板的重量和计划成材率计算出原料的重量。
计划成材率指的是在设计原料尺寸时的成材率,成品与毛板的情况如图7-1,它可以采用公式7-1进行计算。
)1)()()((s l l w w t t rp ++∆+∆+ 式中 t ——成品板厚度;w ——成品板宽度;l ——成品板长度;t t ∆+——轧制平均厚度;w w ∆+——轧制平均宽度;rp l ——试样长度;l ∆——长度余量;s ——烧损;t ∆——厚度余量;w ∆——宽度余量。
式中各量的确定方法如下:S ——烧损,即氧化铁皮损失,包括加热炉内生成的氧化铁皮。
中厚板生产压下规程设计
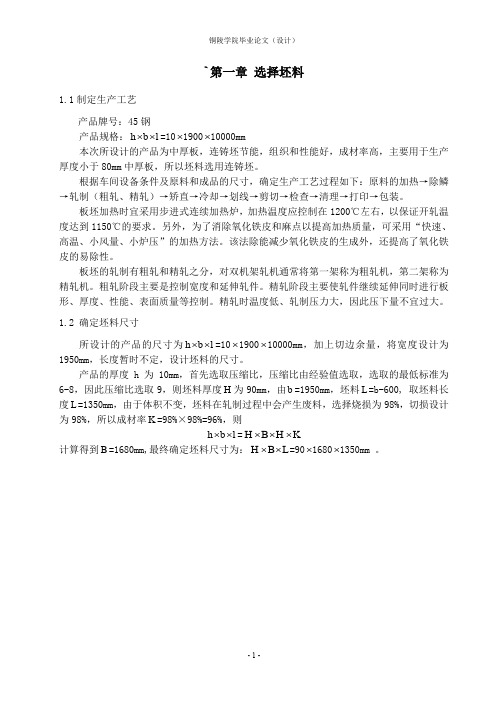
`第一章选择坯料1.1制定生产工艺产品牌号:45钢产品规格:l⨯=10⨯1900⨯10000mmbh⨯本次所设计的产品为中厚板,连铸坯节能,组织和性能好,成材率高,主要用于生产厚度小于80mm中厚板,所以坯料选用连铸坯。
根据车间设备条件及原料和成品的尺寸,确定生产工艺过程如下:原料的加热→除鳞→轧制(粗轧、精轧)→矫直→冷却→划线→剪切→检查→清理→打印→包装。
板坯加热时宜采用步进式连续加热炉,加热温度应控制在1200℃左右,以保证开轧温度达到1150℃的要求。
另外,为了消除氧化铁皮和麻点以提高加热质量,可采用“快速、高温、小风量、小炉压”的加热方法。
该法除能减少氧化铁皮的生成外,还提高了氧化铁皮的易除性。
板坯的轧制有粗轧和精轧之分,对双机架轧机通常将第一架称为粗轧机,第二架称为精轧机。
粗轧阶段主要是控制宽度和延伸轧件。
精轧阶段主要使轧件继续延伸同时进行板形、厚度、性能、表面质量等控制。
精轧时温度低、轧制压力大,因此压下量不宜过大。
1.2 确定坯料尺寸所设计的产品的尺寸为l⨯=10⨯1900⨯10000mm,加上切边余量,将宽度设计为bh⨯1950mm,长度暂时不定,设计坯料的尺寸。
产品的厚度h为10mm,首先选取压缩比,压缩比由经验值选取,选取的最低标准为6-8,因此压缩比选取9,则坯料厚度H为90mm,由b=1950mm,坯料L=b-600, 取坯料长度L=1350mm,由于体积不变,坯料在轧制过程中会产生废料,选择烧损为98%,切损设计为98%,所以成材率K=98%×98%=96%,则h⨯⨯=KblH⨯⨯⨯HB计算得到B=1680mm,最终确定坯料尺寸为:L⨯=90⨯1680⨯1350mm 。
H⨯B第二章变形量分配2.1 确定轧制方法先经过二辊轧机纵轧一道,在不考虑切边的情况下,使板坯长度等于成品宽度,然后转90°横轧到所需规格。
2.2 确定道次压下量坯料尺寸:LBH⨯⨯ =90⨯1680⨯1350mm,则总的压下量为90-10=80mm。
中厚板生产坯料设计

浅谈中厚板生产坯料设计[摘要] 分析中厚板生产坯料设计中坯料质量、坯料尺寸、轧制方式等因素,得出中厚板坯料设计的方法。
[关键词] 中厚板坯料设计方法1、前言中厚板的产品规格变化范围很大,厚度从4mm到150mm,宽度从1000mm到5200mm,长度从3000mm到60000mm,排列组合后可达上万种规格,若在坯料选型上只简单的套用几个规格去生产,那么肯定会造成很大的浪费和产生大量非计划板。
坯料设计又称原料设计,中厚板坯料设计是中厚板生产中的重要环节之一。
中厚板轧机所用的坯料设计即中厚板坯料质量的标准、坯料尺寸(厚度、长度、宽度)和最适合的轧制方式,这些因素直接影响着轧机的生产率、成材率以及钢板的机械性能。
2、坯料设计步骤坯料设计一般步骤先制定符合中厚板轧制使用的连铸坯质量要求和等级,然后根据成品钢板钢种和机械性能要求从大类钢种系列中选择合适钢种,最后根据轧制方法和成品放尺及偏差计算坯料尺寸。
3、中厚板坯料钢种质量要求3.1板坯尺寸及允许偏差:板坯定尺长度偏差: 0~+80mm公称厚度mm 厚度允许偏差mm 公称宽度mm 宽度允许偏差mm 150-200(包括200mm) ±4 1000-1600 0-10mm>200 ±5 >1600 0-15mm3.2连铸板坯外形标准:外形外形允许偏差(mm)横截面脱方厚度:150-200时不大于3mm厚度:>200时不大于4mm镰刀弯每米不大于4mm,总长度上不大于20mm不平度每米不大于10mm,总不平度不大于0.5%l (l为板坯长度) 鼓肚厚度方向鼓肚:厚度尺寸偏差小于0.5%b(b为板坯宽度) 宽度方向鼓肚:宽度尺寸偏差的一半小于3%h(h为板坯厚度)切斜宽度方向切斜值小于10mm,厚度方向切斜值小于5mm凹陷宽度方向凹陷值小于5mm,厚度方向凹陷值小于4mm楔形厚度尺寸楔形值小于2mm、宽度尺寸楔形值小于10mm连铸板坯表面质量要求:连铸板坯表面不得有目视可见的重接、重叠、翻皮、结疤、夹杂、深度或高度大于2mm的划痕、压痕、擦伤、气孔、冷溅、皱纹、耳子、凸块、凹坑和深度大于1mm的裂纹。
中厚板生产课程设计指导书..
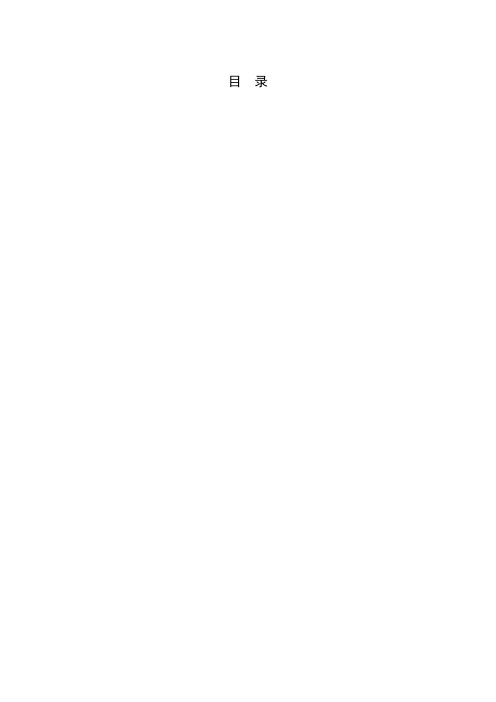
目录1 产品标准和技术要求1.1.1钢材的尺寸、外形及允许偏差钢板和钢带的尺寸、外形及允许偏差见国标GBT/709-2006《热轧钢板和钢带的尺寸、外形、重量及允许偏差》(国标可从网上下载,下同)。
1.1.2技术要求合金牌号和化学成分可查国标,如碳素结构钢可查GB/T700-2006,低合金结构钢可查GB/T1591,优质碳素结构钢 GB/T 699-1999等另外,技术要求可查找GB 3524-2005《碳素结构钢和低合金结构钢热轧钢带》,GB/T4237-2007《不锈钢热轧钢板和钢带》,GB/T8749-2008《优质碳素结构热轧钢带》等。
(1)钢的牌号、化学成分和力学性能见表1-6。
2 生产工艺流程及主要设备参数2.1生产工艺流程根据车间设备条件及原料和成品的尺寸,生产工艺过程一般如下:原料的加热→除鳞→轧制(粗轧、精轧)→矫直→冷却→划线→剪切→检查→清理→打印→包装。
板坯的轧制有粗轧和精轧之分,但粗轧与精轧之间无明显的划分界限。
在单机架轧机上一般前期道次为粗轧,后期道次为精轧;对双机架轧机通常将第一架称为粗轧机,第二架称为精轧机。
粗轧阶段主要是控制宽度和延伸轧件。
精轧阶段主要使轧件继续延伸同时进行板形、厚度、性能、表面质量等控制。
精轧时温度低、轧制压力大,因此压下量不宜过大。
中厚板轧后精整主要包括矫直、冷却、划线、剪切、检查及清理缺陷,必要时还要进行热处理及酸洗等,这些工序多布置在精整作业线上,由辊道及移送机纵横运送钢板进行作业,且机械化自动化水平较高。
2.2 主要生产工艺(1)加热板坯加热目的:中厚板加热目的是提高钢的塑性,降低变形抗力,利于轧制;生成表面氧化铁皮,去除表面缺陷;加热到足够高的温度,使轧制过程在奥氏体化温度区域内完成;在可能的下并可以溶解在后阶段析出的氮化物和碳化物。
一般厚板加热炉的型式有两种:连续式和半连续式。
比较而言,连续式加热炉的产量高、热效率高,装入,抽出方便间歇式加热炉产量一般在10~20t/h,热效率也低。
中厚板生产压下规程课程设计概论
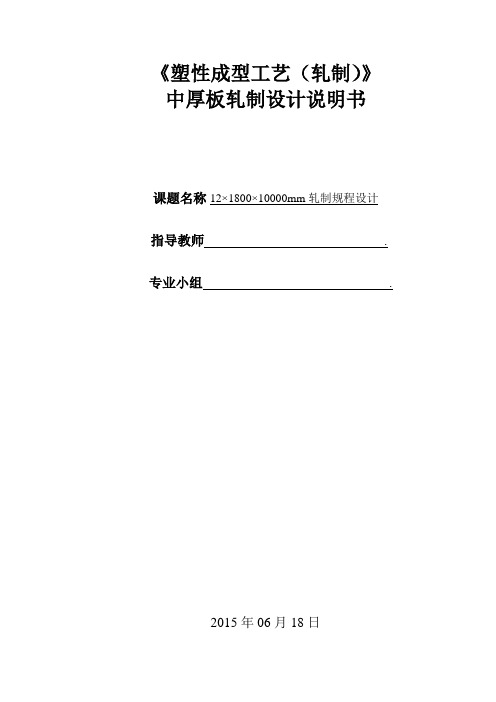
《塑性成型工艺(轧制)》中厚板轧制设计说明书课题名称12×1800×10000mm轧制规程设计指导教师. 专业小组.2015年06月18日目录第一章制定生产工艺及工艺制度 ........................................................... - 3 -一、制定生产工艺及工艺制度 ............................................................................... - 3 -二、坯料选择 ........................................................................................................... - 3 -三、中厚板压下量 ................................................................................................... - 3 -第二章设计变形工具................................................................................ - 5 -一、设计二辊 ........................................................................................................... - 5 -二、设计四辊 ........................................................................................................... - 5 -第三章计算力能参数................................................................................ - 7 -一、选择速度图 ....................................................................................................... - 7 -二、设计轧制速度(n1、n2、n3、a、b)....................................................... - 7 -三、速度图 ............................................................................................................... - 7 -四、计算各道次时间 ............................................................................................... - 7 -五、计算各道次轧制温度 ....................................................................................... - 8 -六、计算各道次变形抗力 ....................................................................................... - 9 -七、选用Sims公式计算各道次轧制力 ................................................................. - 9 -第四章轧辊强度校核............................................................................... - 11 -一、二辊轧机强度校核 ......................................................................................... - 11 -二、四辊轧机强度校核 ......................................................................................... - 12 -第五章主电机容量校核.......................................................................... - 14 -一、绘制力矩图 ..................................................................................................... - 14 -二、计算各机架电机最大输出力矩及等效力矩 ................................................. - 15 -三、校核各机架主电机容量 ................................................................................. - 16 -参考文献.................................................................................................... - 23 -第一章制定生产工艺及工艺制度一、制定生产工艺及工艺制度1.制定生产工艺选择坯料→原料清理→加热→除鳞→纵轧一道(使长度接近成品宽度)→转90°横轧到底→矫直→冷却→表面检查→切边→定尺→表面尺寸形状检查→力学性能试验→标记→入库。
中厚板轧制工艺学 - 副本

中厚板的轧制一、原料准备1.原料种类:扁钢锭、连铸坯、初轧坯、压铸板坯2.原料设计:①厚度尺寸尽可能小;②原料的宽度尺寸尽量大;③原料的长度应尽可能接近加热炉的最大允许长度。
二、原料的加热1.加热的目的①提高钢的塑性,降低变形抗力;②使坯料内外温度均匀;③改变金属的结晶组织,保证生产需要的机械和物理性能。
2.加热的要求①满足工艺规范的需要;②沿长度和断面均匀;③减少加热时氧化烧损3.加热炉型式:按其构造分:连续式加热炉、室状加热炉和均热炉三种。
①连续炉:推钢式(热滑轨式)步进式②室状炉:特重、特轻、特厚、特短的板坯,或多品种、少批量及合金钢,生产灵活。
③均热炉:多用于由钢锭直接轧制特厚板推钢式:优点:设备简单、操作容易掌握、投资少;缺点:钢坯在水梁上滑动产生擦伤;加热时间长,钢坯氧化,脱碳严重;容易粘钢;不能空出炉。
步进式:靠动梁的上、下、前、后平移动作而实现的,故炉长不受限,操作灵活,易于空出炉。
不会造成钢坯划痕,加热效率高。
便于调整坯料间隙和加热时间,易于调整出炉节奏,适应冷装坯,冷热混合坯在炉内的加热条件控制。
加热工艺制度①加热温度:满足轧制工艺规范的温度;②加热速度:单位时间内钢在加热时的温度变化③加热时间:精确确定困难,影响因素多④炉温制度及炉内气氛的选择与控制估算公式:τ=CH H—坯料厚度cmτ—加热时间h C—系数,h/cm低碳钢 0.1~0.15中碳钢 0.15~0.2低合金钢 0.15~0.2高碳钢0.20~0.30高级工具钢 0.3~0.4④加热制度钢在加热炉内加热时的温度变化过程叫钢的加热制度。
一段式加热制度:只有一个加热段;二段式加热制度:加热段+均热段预热段+加热段三段式加热制度:预热段+加热段+均热段多段式加热制度:预热段+多个加热段+均热段三、轧制除磷--粗轧--精轧或成型轧制--展宽轧制--伸长轧制(1)除鳞①除鳞目的:除去表面的氧化铁皮以获得有良的表面质量。
②除鳞原理:利用高压水的强烈冲击作用,去除表面的氧化铁皮。
- 1、下载文档前请自行甄别文档内容的完整性,平台不提供额外的编辑、内容补充、找答案等附加服务。
- 2、"仅部分预览"的文档,不可在线预览部分如存在完整性等问题,可反馈申请退款(可完整预览的文档不适用该条件!)。
- 3、如文档侵犯您的权益,请联系客服反馈,我们会尽快为您处理(人工客服工作时间:9:00-18:30)。
浅谈中厚板生产坯料设计
[摘要] 分析中厚板生产坯料设计中坯料质量、坯料尺寸、轧制方式等因素,得出中厚板坯料设计的方法。
[关键词] 中厚板坯料设计方法
1、前言
中厚板的产品规格变化范围很大,厚度从4mm到150mm,宽度从1000mm到5200mm,长度从3000mm到60000mm,排列组合后可达上万种规格,若在坯料选型上只简单的套用几个规格去生产,那么肯定会造成很大的浪费和产生大量非计划板。
坯料设计又称原料设计,中厚板坯料设计是中厚板生产中的重要环节之一。
中厚板轧机所用的坯料设计即中厚板坯料质量的标准、坯料尺寸(厚度、长度、宽度)和最适合的轧制方式,这些因素直接影响着轧机的生产率、成材率以及钢板的机械性能。
2、坯料设计步骤
坯料设计一般步骤先制定符合中厚板轧制使用的连铸坯质量要求和等级,然后根据成品钢板钢种和机械性能要求从大类钢种系列中选择合适钢种,最后根据轧制方法和成品放尺及偏差计算坯料尺寸。
3、中厚板坯料钢种质量要求
板坯尺寸及允许偏差:板坯定尺长度偏差: 0~+80mm
公称厚度mm 厚度允许偏差mm 公称宽度mm 宽度允许偏差mm
150-200(包括200mm) ±4 1000-1600 0-10mm
>200 ±5 >1600 0-15mm
连铸板坯外形标准:
外形外形允许偏差(mm)
横截面脱方厚度:150-200时不大于3mm
厚度:>200时不大于4mm
镰刀弯每米不大于4mm,总长度上不大于20mm
不平度每米不大于10mm,总不平度不大于%l (l为板坯长度)
鼓肚厚度方向鼓肚:厚度尺寸偏差小于%b(b为板坯宽度)
宽度方向鼓肚:宽度尺寸偏差的一半小于3%h(h为板坯厚度)
切斜宽度方向切斜值小于10mm,厚度方向切斜值小于5mm 凹陷宽度方向凹陷值小于5mm,厚度方向凹陷值小于4mm
楔形厚度尺寸楔形值小于2mm、宽度尺寸楔形值小于10mm 连铸板坯表面质量要求:连铸板坯表面不得有目视可见的重接、重叠、翻皮、结疤、夹杂、深度或高度大于2mm的划痕、压痕、擦伤、气孔、冷溅、皱纹、耳子、凸块、凹坑和深度大于1mm的裂纹。
不得有高度大于2mm的火焰切割瘤,切割端部无毛刺。
连铸板坯横截面不得有影响使用的缩孔、皮下气泡、裂纹。
4、中厚板坯料钢种选择
根据国标中对碳素结构钢、低合金高强度结构钢的标准,结合中厚板成品钢种中普碳钢板、锅炉及压力容器钢板、桥梁用结构钢板的机械性能要求,可以对不同坯料选择进行对应,见下表。
5、中厚板坯料尺寸设计
进行坯料尺寸设计时必须考虑压缩比和展宽比这两个条件。
这是保证产品质量和提高成材率的需要,因此要制定可轧坯料厚度范围和板坯的可展宽范围作为约束条件。
通常为保证钢板的机械性能,必须考虑合适的压缩比。
对于连铸坯来说一般压缩比为6-8较为合适,以此数据来确定所需坯料厚度的下限值;同时在考虑坯料厚度上限值时也不能过厚,否则会增加轧制道次,温度下降,变形抗力增加,轧制变得困难。
展宽轧制时,展宽比在时展宽变化量最小;小于时钢板中间成凹形,大于时钢板中间呈鼓形,为了使轧后钢板成矩形,切边量小,通常在坯料尺寸设计时展宽比为左右,根据实际情况为宜。
宽展比同展宽变化关系图
根据体积不变原理可以得出中厚板坯料计算公式:
l=(h+△h-a) ×(w+△w) ×(l×b+△l)/(h’×b’)
l……坯料实际长度
h……名义成品厚度
w……名义成品宽度值
l……名义成品板子板长
h……厚度放尺量
a…………厚度负偏差
w……宽度放尺量
l……长度放尺量(包括切头尾和试样)
b…………成品倍尺数
h’……坯料实际厚度
b’………坯料实际宽度
由上式可知:减少厚度公差△h,切边量△w,切头尾量△l对提高成材率具有重要意义。
其中减少厚度公差实现负偏差轧制对40mm厚度以下薄规格的板材影响明显;而切边量,切头尾量则随着板厚的增大对板材成材率影响逐渐增大。
结合浦钢实际生产经验得出坯料厚度、宽度、长度放尺量以及根据剪切板和氧割板的不同余量不同,详见下表。
成品厚度(mm) 成品厚度放尺量(mm)
12≥h>6
32≥h>12
80≥h>32
120≥h>80
h>120
成品厚度放尺量表1
展宽比成品宽度放尺量b
α18000 b+10mm
成品厚度成品宽度放尺氧割板
30≤h<80 b-10mm
80≤h<120 b
120≤h b+10mm
成品宽度放尺量表2
厚度规格成品长度放尺量
h≤8 750mm
8<h≤12 650mm
12<h≤25 550(450)mm
25<h≤30 500(400)mm
30<h 300(250)mm
成品长度放尺量表3
在实际计算坯料尺寸时,通常坯料厚度和宽度为名义标准值,只需计算出坯料切割长度就可以完成坯料尺寸设计。
对于坯料的厚度和宽度实际值同名义值之间也有偏差,根据浦钢实际生产数据得出坯料厚度和宽度偏差值,详见下表。
理论坯料厚度(mm) 实际坯料厚度(mm)
180mm、200mm、h-2mm
220mm、250mm h-4mm
坯料厚度偏差表4
理论坯料宽度(mm) 实际坯料宽度(mm)
1000mm 997mm
1150mm 1147mm
1200mm 1197mm
1250mm 1247mm
1300mm 1297mm
1400mm 1397mm
1500mm 1497mm
1550mm 1547mm
1600mm 1597mm
1700mm 1697mm
1800mm 1797mm
坯料宽度偏差表5
应用举例:
已知:成品厚度22mm,厚度允许偏差,厚度放尺查表1得,坯料厚度220mm;成品宽度2500mm,按照展宽比算得坯料宽度1800mm,成品定尺长度8000mm,3倍尺,宽度放尺查表2得110mm;长度放尺查表3得550mm。
l=(h+△h-a) ×(w+△w) ×(l×b+△l)/(h’×b’)
坯料长度=((22+
=*2610*24550/391746
=3614mm
坯料长度计算出来以后,要根据推钢式加热炉的炉筋管间距、轧制时推床转钢最大宽度限制、轧机辊身长度和轧制方式来确定坯料设计的尺寸是否正确。
6、小结
中厚板坯料设计是中厚板生产中的重点,关系成材率和轧成率的高低,因此通过对坯料设计中质量、选材、尺寸的探讨,明白了坯料
设计中的因素,为日后优化坯料设计提供了可鉴之材。
参考文献:
[1] 孙本荣《中厚板生产》
[2] 中国钢铁标准化技术委员会《连续铸钢板坯标准》yb/t 2012-2004 2004。