食品质量管理的先进方法
食品加工行业中的质量控制方法
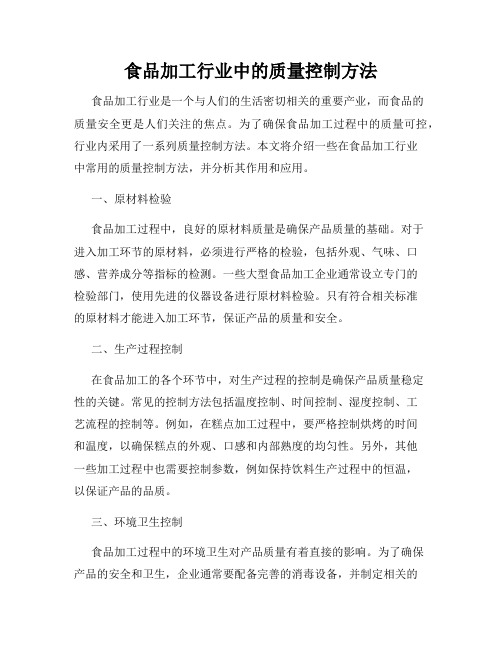
食品加工行业中的质量控制方法食品加工行业是一个与人们的生活密切相关的重要产业,而食品的质量安全更是人们关注的焦点。
为了确保食品加工过程中的质量可控,行业内采用了一系列质量控制方法。
本文将介绍一些在食品加工行业中常用的质量控制方法,并分析其作用和应用。
一、原材料检验食品加工过程中,良好的原材料质量是确保产品质量的基础。
对于进入加工环节的原材料,必须进行严格的检验,包括外观、气味、口感、营养成分等指标的检测。
一些大型食品加工企业通常设立专门的检验部门,使用先进的仪器设备进行原材料检验。
只有符合相关标准的原材料才能进入加工环节,保证产品的质量和安全。
二、生产过程控制在食品加工的各个环节中,对生产过程的控制是确保产品质量稳定性的关键。
常见的控制方法包括温度控制、时间控制、湿度控制、工艺流程的控制等。
例如,在糕点加工过程中,要严格控制烘烤的时间和温度,以确保糕点的外观、口感和内部熟度的均匀性。
另外,其他一些加工过程中也需要控制参数,例如保持饮料生产过程中的恒温,以保证产品的品质。
三、环境卫生控制食品加工过程中的环境卫生对产品质量有着直接的影响。
为了确保产品的安全和卫生,企业通常要配备完善的消毒设备,并制定相关的卫生操作规范。
同时,定期对生产车间进行清洁和消毒,确保生产环境的卫生水平。
对员工的个人卫生也有严格的要求,如佩戴口罩、穿戴工作服等。
四、样品检测食品加工行业中,样品检测是质量控制的重要手段之一。
通过对加工过程中的样品进行检测,可以及时发现问题并进行纠正。
样品检测的方法有很多种,例如常见的微生物检验、化学成分检验、食品安全指标检测等。
食品加工企业通常会委托具备相关资质的专业检测机构进行样品检测,以保证结果的准确性和可信度。
五、质量管理体系为了更好地管理和控制食品加工过程中的质量,行业内许多企业采用质量管理体系,如ISO9001质量管理体系。
质量管理体系可以帮助企业建立一套完整的质量管理体系,包括质量目标的设定、流程的规范、员工培训和绩效评估等。
加强食品安全管理的方法和措施
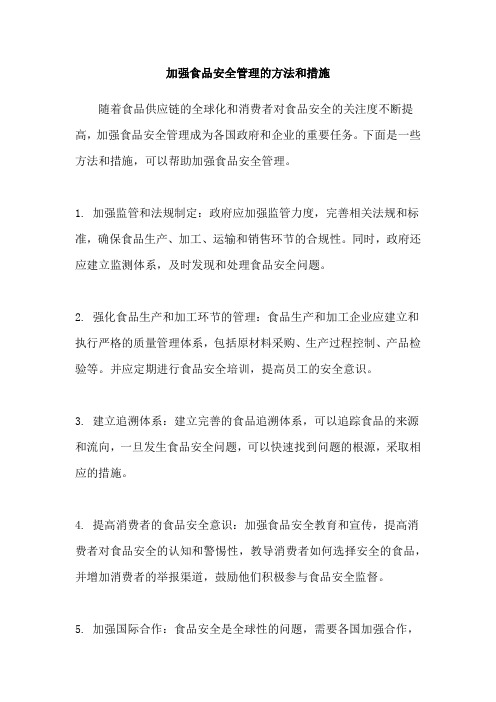
加强食品安全管理的方法和措施
随着食品供应链的全球化和消费者对食品安全的关注度不断提高,加强食品安全管理成为各国政府和企业的重要任务。
下面是一些方法和措施,可以帮助加强食品安全管理。
1. 加强监管和法规制定:政府应加强监管力度,完善相关法规和标准,确保食品生产、加工、运输和销售环节的合规性。
同时,政府还应建立监测体系,及时发现和处理食品安全问题。
2. 强化食品生产和加工环节的管理:食品生产和加工企业应建立和执行严格的质量管理体系,包括原材料采购、生产过程控制、产品检验等。
并应定期进行食品安全培训,提高员工的安全意识。
3. 建立追溯体系:建立完善的食品追溯体系,可以追踪食品的来源和流向,一旦发生食品安全问题,可以快速找到问题的根源,采取相应的措施。
4. 提高消费者的食品安全意识:加强食品安全教育和宣传,提高消费者对食品安全的认知和警惕性,教导消费者如何选择安全的食品,并增加消费者的举报渠道,鼓励他们积极参与食品安全监督。
5. 加强国际合作:食品安全是全球性的问题,需要各国加强合作,
分享信息和经验,共同应对跨国食品安全问题。
国际组织和跨国企业可以共同制定标准和规范,加强食品贸易中的安全保障。
6. 加强技术支持:引入先进的食品安全监测技术和设备,提高食品安全监测的准确性和效率。
利用大数据和人工智能等新技术,可以实时监测食品供应链中的风险,提前预警和处理食品安全问题。
综上所述,加强食品安全管理需要政府、企业和消费者共同努力,通过监管、法规制定、加强食品生产和加工环节的管理、建立追溯体系、提高消费者的食品安全意识、加强国际合作以及引入先进的技术支持等措施,共同确保食品安全和消费者的健康。
食品行业中的质量管理

食品行业中的质量管理食品是人们日常生活中必不可少的物品之一,食品质量安全直接关系到人们的健康和生命安全。
食品行业中的质量管理是保障食品质量安全的关键措施。
食品行业中的质量管理应该从哪些方面入手呢?一、原料质量控制食品生产的原料是影响食品质量的关键因素之一。
控制食品原料的质量是保证食品质量安全的基础。
对采购的原料应进行严格的检查、测试、鉴定等过程,确保原料符合食品生产的规范标准。
同时,应对原料来源和生产过程进行严密的监控。
二、生产过程管控食品生产过程中应加强生产管控,严格按照食品卫生和安全的标准进行操作。
从生产前到生产中再到生产后都应该进行严密的监测和控制,以防止人为操作不当或外界环境因素的影响。
三、质量监测与检测食品行业中的质量管理离不开质量监测与检测。
在生产的不同阶段对食品中的常见污染物和有害物质进行检测,以及对食品的理化性质、营养成分、微生物指标等进行检测和分析,以确保食品的质量安全。
四、质量管理体系建设对于食品生产企业来说,最为关键的就是建立完整的质量管理体系。
建立质量管理体系是对食品生产过程中的每一个环节进行系统的控制,逐一排除不良因素,并要求员工具备严谨的工作态度、稳定的生产技能和一致的服务理念等综合能力的提升。
五、合规政策宣传与培训对于保障食品质量安全的质量安全技术、质量管理法规等知识的传递和培训,则需要政府部门和企业的共同努力以及全社会的认知度提升。
政府部门应该制定出相应的法律和行业准则,定期发布质量安全类相关政策和宣传信息,同时对从业人员和生产企业进行定期培训,强化其质量管理技能,提高食品质量安全的意识。
总之,食品行业中的质量管理是保障食品质量安全的重要手段之一。
通过对原料质量控制、生产过程管控、质量监测与检测、质量管理体系建设和合规政策宣传与培训等方面的改进,可以全面提升食品企业的生产技术和管理水平,从而确保食品质量的可靠性和安全性。
食品质检中的质量控制与质量管理

食品质检中的质量控制与质量管理在现代食品行业中,质量控制和质量管理是确保食品安全和质量的重要环节。
随着人们对食品安全和质量的需求不断增加,食品质检越来越受到关注。
本文将探讨食品质检中的质量控制和质量管理的重要性,并介绍一些相关的方法和措施。
一、质量控制的定义质量控制是指通过各种手段和方法来确保产品质量符合预期标准的过程。
在食品质检中,质量控制是指通过检测、监测和控制食品的质量参数,以确保食品符合相关的卫生、安全和品质标准。
在质量控制的过程中,首先需要建立一套可行的质量标准和检测方法。
这些检测方法可以包括感官评价、生化分析、微生物检测等。
通过对食品的各项指标进行全面的测试和监测,可以及时发现和控制潜在的食品安全问题,确保食品的品质达到消费者的期望。
二、质量管理的重要性质量管理是指通过规范和管理一系列质量活动来提高产品质量的过程。
在食品质检中,质量管理是确保食品安全和质量的关键,它包括了质量计划、质量控制、质量评估和质量改进等环节。
首先,质量管理可以帮助企业建立完善的质量体系和管理流程。
企业可以通过质量管理体系来规范和标准化各项质检工作,包括食品采购、生产过程控制、质量检测等。
同时,质量管理还能帮助企业建立一套食品安全和质量追溯的体系,以便于追踪和解决潜在的质量问题。
其次,质量管理可以提高食品安全和质量的可控性。
通过制定科学的质量标准和控制措施,可以减少食品受到污染和变质的风险。
此外,质量管理还可以通过培训和教育提高员工的质量意识和工作技能,从而进一步提高质检工作的准确性和可靠性。
最后,质量管理可以增强企业的竞争力和信誉度。
高品质的食品不仅能够满足消费者的需求,还能够赢得消费者的信任和口碑。
通过质量管理的严格执行,企业可以建立起良好的品牌形象和声誉,从而提高市场竞争力。
三、质量控制与质量管理的方法和措施1.建立质量控制体系:企业可以根据国家和行业相关的食品安全标准,制定质量控制体系。
该体系应包括食品的采购、加工、储存、运输等环节,以确保每个环节都符合质量要求。
罐头食品质量安全监管措施
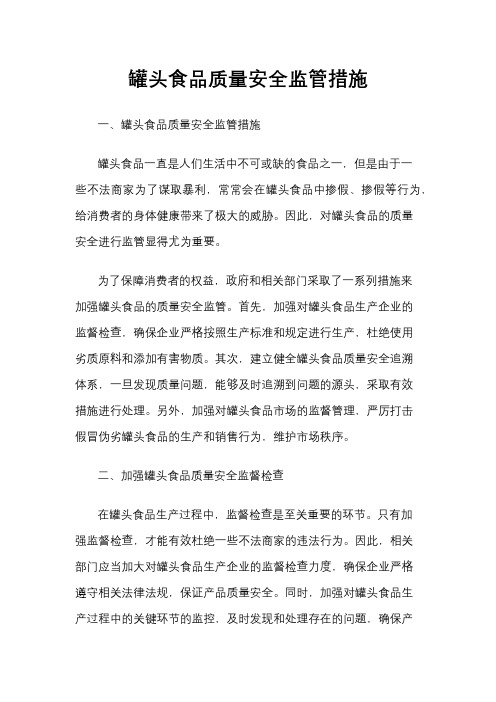
罐头食品质量安全监管措施一、罐头食品质量安全监管措施罐头食品一直是人们生活中不可或缺的食品之一,但是由于一些不法商家为了谋取暴利,常常会在罐头食品中掺假、掺假等行为,给消费者的身体健康带来了极大的威胁。
因此,对罐头食品的质量安全进行监管显得尤为重要。
为了保障消费者的权益,政府和相关部门采取了一系列措施来加强罐头食品的质量安全监管。
首先,加强对罐头食品生产企业的监督检查,确保企业严格按照生产标准和规定进行生产,杜绝使用劣质原料和添加有害物质。
其次,建立健全罐头食品质量安全追溯体系,一旦发现质量问题,能够及时追溯到问题的源头,采取有效措施进行处理。
另外,加强对罐头食品市场的监督管理,严厉打击假冒伪劣罐头食品的生产和销售行为,维护市场秩序。
二、加强罐头食品质量安全监督检查在罐头食品生产过程中,监督检查是至关重要的环节。
只有加强监督检查,才能有效杜绝一些不法商家的违法行为。
因此,相关部门应当加大对罐头食品生产企业的监督检查力度,确保企业严格遵守相关法律法规,保证产品质量安全。
同时,加强对罐头食品生产过程中的关键环节的监控,及时发现和处理存在的问题,确保产品质量符合标准。
三、建立罐头食品质量安全追溯体系建立健全的罐头食品质量安全追溯体系对于保障消费者权益至关重要。
一旦发生质量问题,能够及时追溯到问题的源头,采取有效措施进行处理,避免问题扩大化。
因此,政府和相关部门应当加强对罐头食品生产企业的追溯体系建设,确保产品质量安全可追溯可控制。
四、加强罐头食品市场监督管理加强对罐头食品市场的监督管理,是保障消费者权益的重要举措。
只有严厉打击假冒伪劣罐头食品的生产和销售行为,才能维护市场秩序,保障消费者的合法权益。
因此,政府和相关部门应当加大对罐头食品市场的监督管理力度,加强对市场的巡查检查,严厉打击违法行为,维护市场秩序。
综上所述,加强罐头食品质量安全监管措施,对于保障消费者的健康和权益具有重要意义。
政府和相关部门应当加强监督检查、建立追溯体系、加强市场监督管理,共同努力,确保罐头食品质量安全,让消费者放心食用。
食品行业管理制度的质量控制方法
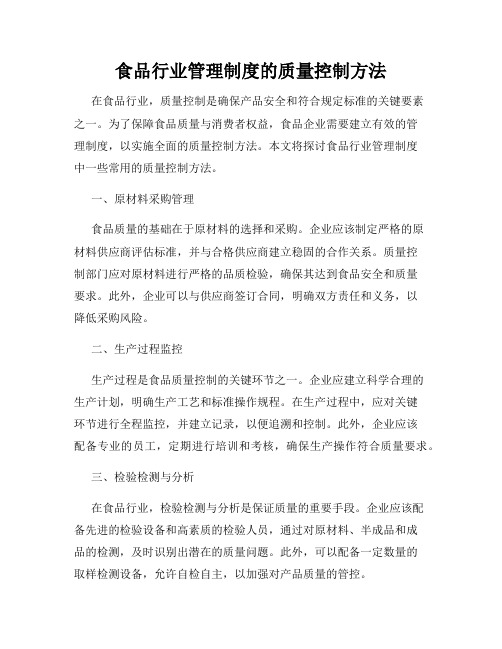
食品行业管理制度的质量控制方法在食品行业,质量控制是确保产品安全和符合规定标准的关键要素之一。
为了保障食品质量与消费者权益,食品企业需要建立有效的管理制度,以实施全面的质量控制方法。
本文将探讨食品行业管理制度中一些常用的质量控制方法。
一、原材料采购管理食品质量的基础在于原材料的选择和采购。
企业应该制定严格的原材料供应商评估标准,并与合格供应商建立稳固的合作关系。
质量控制部门应对原材料进行严格的品质检验,确保其达到食品安全和质量要求。
此外,企业可以与供应商签订合同,明确双方责任和义务,以降低采购风险。
二、生产过程监控生产过程是食品质量控制的关键环节之一。
企业应建立科学合理的生产计划,明确生产工艺和标准操作规程。
在生产过程中,应对关键环节进行全程监控,并建立记录,以便追溯和控制。
此外,企业应该配备专业的员工,定期进行培训和考核,确保生产操作符合质量要求。
三、检验检测与分析在食品行业,检验检测与分析是保证质量的重要手段。
企业应该配备先进的检验设备和高素质的检验人员,通过对原材料、半成品和成品的检测,及时识别出潜在的质量问题。
此外,可以配备一定数量的取样检测设备,允许自检自主,以加强对产品质量的管控。
四、合规管理与风险防控食品行业涉及众多法规标准和政策要求,企业应积极履行合规管理,以确保产品符合相关标准。
食品企业应建立健全的风险评估和风险管理机制,及时识别和评估风险,并采取相应的措施进行控制和防范。
五、售后服务与客户反馈企业在向消费者提供食品过程中,应做好售后服务和客户反馈。
建立客户投诉处理机制,并将客户的反馈作为质量改进的重要参考依据。
根据反馈信息,企业应及时调整生产工艺和改进产品质量,以提高客户满意度。
六、内部审核与持续改进为了确保管理制度的有效执行,企业应定期进行内部审核。
通过审核,可以发现问题和风险,及时进行改进和纠正。
企业应建立持续改进的机制,鼓励员工提出质量改进意见和建议,不断完善管理制度,提高产品质量和综合竞争力。
饮食卫生质量问题制度

饮食卫生质量问题制度一、食品卫生1. 严把食品采购关,坚持食品采购索证制度,禁止采购腐烂变质的食品,对采购的食品要留样备查。
2. 操作人员要讲究仪表形象,勤剪指甲,认真执行《食品卫生法》的相关要求。
3. 食品储存要分类、分架、隔墙、离地存放,生熟食品要加盖,无交叉感染,生熟砧板要分开。
4. 食品加工出售前要检查质量,发现腐烂变质、超过保质期限的食品不得出售。
5. 剩余饭菜应妥善处理,严禁出售和重复使用剩余饭菜。
6. 经常保持厨房的清洁、空气清新,餐室和厨房垃圾及时清运处理。
7. 保持下水道通畅,防止污水横溢和苍蝇滋生。
二、卫生消毒1. 有针对性的科学使用消毒药品,有效预防传染病及其他季节性流行病。
2. 消毒药液和饮水必须坚持定期换药,同时还要进行不定期抽查。
3. 餐具、茶具、毛巾等要“一洗、二清、三消毒、四保洁”,保洁柜经常清理干净,保持清洁存放食品。
4. 个人卫生要做到“四勤”,即勤洗澡、勤理发、勤剪指甲、勤洗衣服。
三、健康检查1. 食堂人员必须进行健康检查,严禁患有传染病的人员进入食堂。
2. 食堂人员必须进行岗前培训,学习有关卫生法规,并上交个人健康保证书。
3. 做好工作人员健康状况的动态监督工作,及时处理有碍食品卫生的行为。
4. 凡有传染病的食堂人员应及时向医院和上级主管部门报告,并立即离开工作岗位进行治疗和观察。
5. 食堂人员每年要进行一次健康检查,对不符合健康要求的人员要立即调离岗位或辞退。
6. 严禁食堂人员在操作时不戴口罩,上班时不穿工作服及在非操作间吸烟、进食等。
7. 严禁食物中毒事件发生。
食物中毒人数超过3人或住院治疗人数超过5人时必须报告上级主管部门和当地防疫部门。
食堂食品质量控制方案
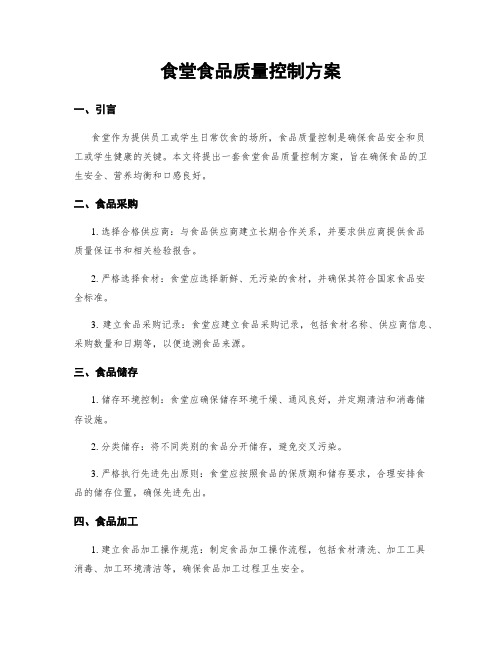
食堂食品质量控制方案一、引言食堂作为提供员工或学生日常饮食的场所,食品质量控制是确保食品安全和员工或学生健康的关键。
本文将提出一套食堂食品质量控制方案,旨在确保食品的卫生安全、营养均衡和口感良好。
二、食品采购1. 选择合格供应商:与食品供应商建立长期合作关系,并要求供应商提供食品质量保证书和相关检验报告。
2. 严格选择食材:食堂应选择新鲜、无污染的食材,并确保其符合国家食品安全标准。
3. 建立食品采购记录:食堂应建立食品采购记录,包括食材名称、供应商信息、采购数量和日期等,以便追溯食品来源。
三、食品储存1. 储存环境控制:食堂应确保储存环境干燥、通风良好,并定期清洁和消毒储存设施。
2. 分类储存:将不同类别的食品分开储存,避免交叉污染。
3. 严格执行先进先出原则:食堂应按照食品的保质期和储存要求,合理安排食品的储存位置,确保先进先出。
四、食品加工1. 建立食品加工操作规范:制定食品加工操作流程,包括食材清洗、加工工具消毒、加工环境清洁等,确保食品加工过程卫生安全。
2. 员工培训:对食品加工人员进行食品安全知识和操作规范的培训,提高员工的食品安全意识和操作技能。
3. 加强质量检验:建立食品加工质量检验制度,对加工过程中的食品进行抽样检测,确保食品质量符合标准。
五、食品供应与销售1. 食品供应环节控制:食堂应确保供应环节的食品质量,包括食品的包装、运输和保温等。
2. 食品销售管理:食堂应建立食品销售记录,包括销售日期、销售数量和销售价格等,以便追溯食品销售情况。
3. 定期食品安全检查:定期对食堂的食品进行安全检查,包括食品质量抽样检测、食品卫生状况检查等,确保食品安全。
六、食品安全事件处理1. 建立食品安全事件处理机制:食堂应建立食品安全事件处理机制,包括食品召回、食品事故应急预案等,以应对可能发生的食品安全事件。
2. 及时报告和处理:对于发生的食品安全事件,食堂应及时向相关部门报告,并采取相应措施进行处理和整改。
食品安全管理中的质量控制措施

食品安全管理中的质量控制措施食品安全是人们关注的重要问题,尤其是在食品质量事故频发的背景下,加强食品安全管理至关重要。
质量控制措施作为食品安全管理的重要环节,不仅涉及到食品的生产过程,还包括食品的储存、运输和销售等环节。
本文将从食品原材料的选择、生产过程的控制、食品检测与监控以及质量管理体系建设四个方面,详细介绍食品安全管理中的质量控制措施。
一、食品原材料的选择食品安全的基础是食品原材料的质量和安全性。
在食品生产过程中,选择质量可靠的食品原材料是第一步。
餐饮企业应建立完善的供应商管理体系,与可靠的供应商建立长期稳定的合作关系,确保食品原材料的来源可追溯。
此外,企业应加强对食品原材料的检验和筛选,建立详细的质量标准和检验流程,严格把关食品原材料的质量与安全。
二、生产过程的控制食品生产过程是保证食品质量的关键环节。
生产过程的控制包括原料加工、食品加工、包装和存储等环节。
在原料加工过程中,应遵循卫生规范,加强对原料的清洗、消毒和处理等工序的控制。
在食品加工过程中,要确保设备设施的卫生安全,加强对食品加工环境的卫生监控。
在包装和存储过程中,要选择符合卫生标准的包装材料,并确保食品的储存条件符合要求,避免发生污染和变质。
三、食品检测与监控食品检测与监控是食品安全管理的重要手段,可以及时发现和解决潜在的食品安全问题。
食品企业应建立完善的食品检测与监控体系,包括建立实验室和引进先进的检测设备,以及培养专业的检测人员。
同时,餐饮企业还应定期开展食品抽检,对所售食品进行质量监控,确保食品的安全性和合规性。
四、质量管理体系建设质量管理体系是保证食品安全和质量的基础。
餐饮企业应建立符合国家和行业标准的质量管理体系,例如ISO9001质量管理体系和HACCP食品安全管理体系等。
质量管理体系建设包括制定质量管理手册和操作规程、培训员工、建立质量记录和文件等。
通过质量管理体系的建设,能够规范食品生产和经营行为,提高食品质量的稳定性和可靠性。
食品质量管理措施

1、我单位保证严格遵守《食品安全法》和《动物检疫法》等相关规定,严格保证食品质量符合国家相关产品质理标准,符合国家各级强制性规范要求。
如浮现因食品质量导致食物中毒的事故发生,我单位承担一切法律责任。
2、我单位保证绝不供应以下食品:(1)腐败变质、油脂酸败、霉变、生虫、污秽不洁、混有异物或者其他感官性状异常,对人体有害的;(2)含有毒、有害物质或者被有害物质污染,对人体身体健康有害的;含有严重超出标准限量的农药残留、兽药残留、重金属、污染物质以及其他危害人体健康的;(3)未经动物部门检疫、检验或者检疫、检验不合格的肉类及其制品;(4)病死、毒死或者不明死因的禽、蓄、兽、水产动物等及其制品;(5)用非食品原料加工的,加入非食品用化学物质或者将非食品当做食品的。
3 、所有配送食材剩余保质期不低于全部保质期的一半。
4、验收标准(1) 家禽:符合GB2707-2022 《食品安全国家标准鲜 (冻) 畜、禽产品》标准。
干冻,无注水,全净膛,表皮完整洁净,按采购人要求规格供货。
(2)蛋类:蛋壳清洁完整,灯光透视时整个蛋呈微红色,蛋黄不见或者略有阴影,打开后蛋黄凸起完整并带有韧性,蛋白澄清透明,稀稠分明。
1、采购食品,应当查验供货者的许可证和食品合格的证明文件。
应当建立食品进货查验记录制度,如实记录食品的名称、规格、数量、生产批号、保质期、供货者名称及联系方式、进货日期等内容。
食品进货查验记录应当真实,保存期限不得少于二年。
实行统一配送经营方式的食品经营企业,可以由企业总部统一查验供货者的许可证和食品合格的证明文件,进行食品进货查验记录。
2、采购各类食品应注意生产日期或者保存期等食品标识,不应采购快到期或者超期食品。
3、采购时应向销售方索取该批产品有效许可证和食品合格的证明文件。
4、禁止采购腐败、霉变、生虫、污秽不洁、混有异物或者其他感官性状异常、可能对人体健康造成危害的食品。
5、禁止采购病死、毒死、死因不明或者有明显致病寄生虫的鲜肉类产品及其制品、酸败油脂、变质乳及乳制品、包装严重污秽不洁、严重破损或者运输工具不洁而造成污染的食品。
食品行业的质量控制目标及实施方法

食品行业的质量控制目标及实施方法食品安全一直是社会关注的焦点之一,为了确保食品行业的质量和安全,制定和实施科学有效的质量控制目标是至关重要的。
本文将探讨食品行业的质量控制目标以及相关的实施方法。
一、质量控制目标食品行业的质量控制目标包括以下几个方面:1. 安全性食品安全是食品行业质量控制的首要目标。
确保食品不含有有害物质,例如重金属、农药残留、致病菌等,并且符合卫生标准和法律法规的要求。
2. 营养价值食品应具备一定的营养价值,以满足人们的营养需求。
通过合理配方和加工工艺,确保食品中的维生素、矿物质、蛋白质等营养成分丰富,并符合相关的标准。
3. 味觉和口感食品的味道和口感直接影响消费者的满意度和选择。
质量控制目标应包括食品的口味、质地、口感等方面,以确保食品在口感上达到消费者的期望。
4. 外观品质食品的外观品质是消费者购买食品时首先注意的特征之一。
外观应包括食品的外观色泽、形状、大小等方面,确保食品具备良好的视觉效果。
二、质量控制实施方法为了实现上述质量控制目标,食品行业采用了一系列的实施方法。
下面列举了几种常见的方法:1. 来源追溯系统通过建立完善的食品来源追溯系统,可以追踪食品的原材料、生产流程、加工环节等信息。
一旦发生质量问题,可以快速定位问题的来源,并进行相应的调查和处理,以保障食品的质量和安全。
2. 食品安全标准制定和实施食品安全标准是保障食品质量的基本要求。
针对不同的食品类型和工艺,制定相应的标准,并进行监督检测。
例如,确定食品中允许的残留农药和重金属的最高限量,以及致病菌的卫生标准等。
3. 检测分析技术食品行业依靠检测分析技术来监测食品的质量和安全。
包括常见的微生物检测、残留物检测、营养成分检测等。
借助先进的仪器设备和方法,可以对食品进行快速、准确的检测,及时发现问题并采取相应的措施。
4. 严格的生产管理食品生产需要确保从原料采购到生产加工的全过程严格符合卫生标准和法规要求。
制订和执行相应的制度和规范,包括原料检验、生产环境卫生、操作规程等,从而保证食品的质量和安全。
饮食质量管理制度
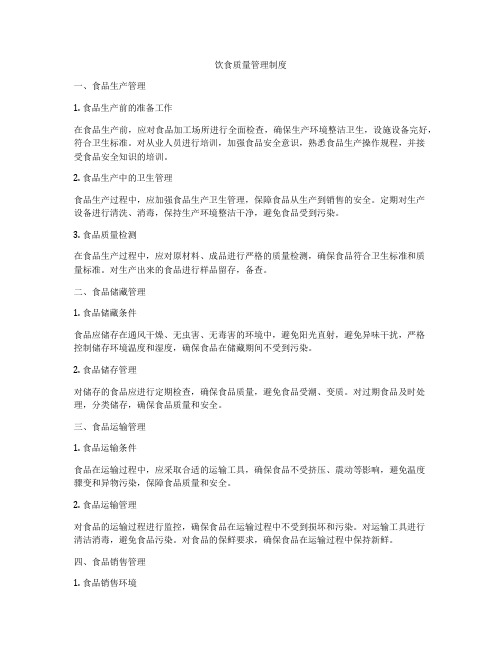
饮食质量管理制度一、食品生产管理1. 食品生产前的准备工作在食品生产前,应对食品加工场所进行全面检查,确保生产环境整洁卫生,设施设备完好,符合卫生标准。
对从业人员进行培训,加强食品安全意识,熟悉食品生产操作规程,并接受食品安全知识的培训。
2. 食品生产中的卫生管理食品生产过程中,应加强食品生产卫生管理,保障食品从生产到销售的安全。
定期对生产设备进行清洗、消毒,保持生产环境整洁干净,避免食品受到污染。
3. 食品质量检测在食品生产过程中,应对原材料、成品进行严格的质量检测,确保食品符合卫生标准和质量标准。
对生产出来的食品进行样品留存,备查。
二、食品储藏管理1. 食品储藏条件食品应储存在通风干燥、无虫害、无毒害的环境中,避免阳光直射,避免异味干扰,严格控制储存环境温度和湿度,确保食品在储藏期间不受到污染。
2. 食品储存管理对储存的食品应进行定期检查,确保食品质量,避免食品受潮、变质。
对过期食品及时处理,分类储存,确保食品质量和安全。
三、食品运输管理1. 食品运输条件食品在运输过程中,应采取合适的运输工具,确保食品不受挤压、震动等影响,避免温度骤变和异物污染,保障食品质量和安全。
2. 食品运输管理对食品的运输过程进行监控,确保食品在运输过程中不受到损坏和污染。
对运输工具进行清洁消毒,避免食品污染。
对食品的保鲜要求,确保食品在运输过程中保持新鲜。
四、食品销售管理1. 食品销售环境食品销售环境应整洁干净,设施设备完好,符合卫生标准,避免异味和污染。
加强对从业人员的培训,提高服务质量,保障消费者的健康。
以上是对饮食质量管理制度的详细介绍,通过建立完善的饮食质量管理制度,可以提高食品质量,确保消费者的健康。
餐饮行业应加强对食品质量管理的重视,注重食品安全和卫生,确保食品质量符合标准,为消费者提供安全、健康的饮食环境。
餐饮产品质量控制方法
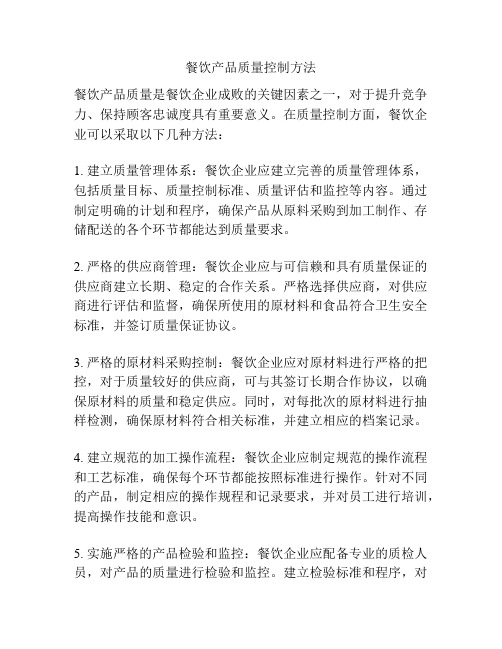
餐饮产品质量控制方法餐饮产品质量是餐饮企业成败的关键因素之一,对于提升竞争力、保持顾客忠诚度具有重要意义。
在质量控制方面,餐饮企业可以采取以下几种方法:1. 建立质量管理体系:餐饮企业应建立完善的质量管理体系,包括质量目标、质量控制标准、质量评估和监控等内容。
通过制定明确的计划和程序,确保产品从原料采购到加工制作、存储配送的各个环节都能达到质量要求。
2. 严格的供应商管理:餐饮企业应与可信赖和具有质量保证的供应商建立长期、稳定的合作关系。
严格选择供应商,对供应商进行评估和监督,确保所使用的原材料和食品符合卫生安全标准,并签订质量保证协议。
3. 严格的原材料采购控制:餐饮企业应对原材料进行严格的把控,对于质量较好的供应商,可与其签订长期合作协议,以确保原材料的质量和稳定供应。
同时,对每批次的原材料进行抽样检测,确保原材料符合相关标准,并建立相应的档案记录。
4. 建立规范的加工操作流程:餐饮企业应制定规范的操作流程和工艺标准,确保每个环节都能按照标准进行操作。
针对不同的产品,制定相应的操作规程和记录要求,并对员工进行培训,提高操作技能和意识。
5. 实施严格的产品检验和监控:餐饮企业应配备专业的质检人员,对产品的质量进行检验和监控。
建立检验标准和程序,对产品进行全面的检测,包括外观、气味、口感等方面,确保产品的各项指标符合要求。
6. 建立回溯体系:餐饮企业应建立产品的回溯体系,确保产品来源可追溯,以便在出现问题时能够迅速定位和解决。
及时记录和保存产品的相关信息,包括原料供应商、加工时间、加工人员等,以备不时之需。
7. 加强员工培训和技能提升:餐饮企业应注重员工的培训和技能提升,提高员工对产品质量的重视和管理意识。
定期组织培训和考核,提高员工的操作技能和质量管理水平,确保每个员工都能够按照标准进行操作。
通过以上几种方法,餐饮企业能够有效控制产品质量,提升竞争力和顾客满意度。
同时,企业应定期进行质量评估和改进,不断完善质量管理体系,以适应市场需求的变化,并不断提升产品质量和服务水平。
食品安全管理与质量控制的要点与方法
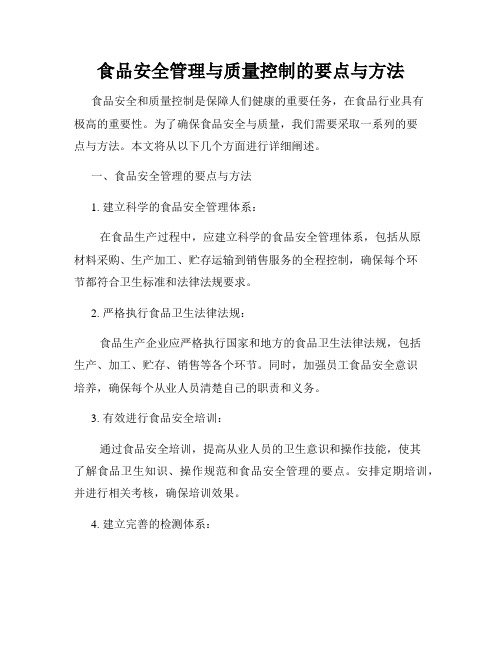
食品安全管理与质量控制的要点与方法食品安全和质量控制是保障人们健康的重要任务,在食品行业具有极高的重要性。
为了确保食品安全与质量,我们需要采取一系列的要点与方法。
本文将从以下几个方面进行详细阐述。
一、食品安全管理的要点与方法1. 建立科学的食品安全管理体系:在食品生产过程中,应建立科学的食品安全管理体系,包括从原材料采购、生产加工、贮存运输到销售服务的全程控制,确保每个环节都符合卫生标准和法律法规要求。
2. 严格执行食品卫生法律法规:食品生产企业应严格执行国家和地方的食品卫生法律法规,包括生产、加工、贮存、销售等各个环节。
同时,加强员工食品安全意识培养,确保每个从业人员清楚自己的职责和义务。
3. 有效进行食品安全培训:通过食品安全培训,提高从业人员的卫生意识和操作技能,使其了解食品卫生知识、操作规范和食品安全管理的要点。
安排定期培训,并进行相关考核,确保培训效果。
4. 建立完善的检测体系:食品安全管理需要进行常规的食品检测,确保食品符合国家的安全指标。
建立完善的检测体系,包括对原材料、生产过程中的监控和成品的检验,确保产品质量。
二、食品质量控制的要点与方法1. 严格控制原材料质量:选择可靠的供应商,建立稳定的供应链,确保原材料的质量和安全。
对于进货的原材料要进行检验,并建立相应的验收标准和程序。
2. 规范生产加工流程:根据产品的特点和生产工艺,制定详细的生产操作规范,包括原材料的配比、加工温度、时间等要点,确保产品的一致性和安全性。
3. 强化生产设备的维护和保养:定期检查和维护生产设备,确保其正常运行和卫生状态良好。
避免设备老化和污染导致的品质问题。
4. 加强质量管理与控制:建立质量管理体系,制定质量控制流程和标准,包括原材料检验、生产过程中的抽检和成品检验等环节,确保产品质量可控。
5. 实施追溯体系:建立食品质量追溯体系,能够追踪产品的生产过程、供应链和销售信息,确保在食品安全事故发生时可以定位问题,采取相应的措施。
食品生产企业如何做好质量管理
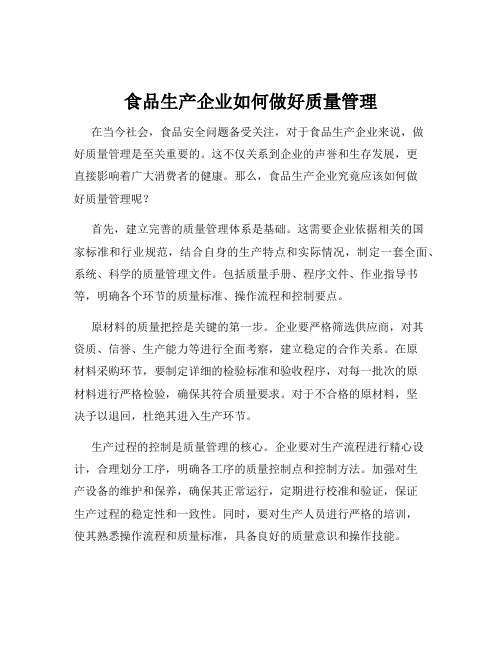
食品生产企业如何做好质量管理在当今社会,食品安全问题备受关注,对于食品生产企业来说,做好质量管理是至关重要的。
这不仅关系到企业的声誉和生存发展,更直接影响着广大消费者的健康。
那么,食品生产企业究竟应该如何做好质量管理呢?首先,建立完善的质量管理体系是基础。
这需要企业依据相关的国家标准和行业规范,结合自身的生产特点和实际情况,制定一套全面、系统、科学的质量管理文件。
包括质量手册、程序文件、作业指导书等,明确各个环节的质量标准、操作流程和控制要点。
原材料的质量把控是关键的第一步。
企业要严格筛选供应商,对其资质、信誉、生产能力等进行全面考察,建立稳定的合作关系。
在原材料采购环节,要制定详细的检验标准和验收程序,对每一批次的原材料进行严格检验,确保其符合质量要求。
对于不合格的原材料,坚决予以退回,杜绝其进入生产环节。
生产过程的控制是质量管理的核心。
企业要对生产流程进行精心设计,合理划分工序,明确各工序的质量控制点和控制方法。
加强对生产设备的维护和保养,确保其正常运行,定期进行校准和验证,保证生产过程的稳定性和一致性。
同时,要对生产人员进行严格的培训,使其熟悉操作流程和质量标准,具备良好的质量意识和操作技能。
在生产过程中,实施严格的监控措施是必不可少的。
通过在线检测、抽样检验等手段,及时发现和解决质量问题。
对于关键控制点,要进行重点监控,确保其处于受控状态。
建立质量追溯体系,对每一批次的产品都能够追溯到原材料的来源、生产过程的操作记录以及检验结果等信息,一旦出现质量问题,能够迅速查明原因,采取有效的召回和整改措施。
加强环境卫生管理也是质量管理的重要环节。
食品生产企业要保持生产车间、仓库等场所的清洁卫生,定期进行消毒和杀虫灭鼠工作。
严格控制生产区域的人员和物流,防止交叉污染。
同时,要对生产用水、空气等进行质量监测,确保符合卫生标准。
质量检验是质量管理的重要手段。
企业要建立独立、权威的质量检验部门,配备专业的检验人员和先进的检验设备。
食品安全管理优化措施

食品安全管理优化措施随着现代社会的飞速发展,食品安全成为人们关注的热点问题。
食品安全问题关系到每个人的生活和健康,因此,优化食品安全管理措施是当务之急。
本文将介绍一些可以采取的食品安全管理优化措施,以期为解决当前的食品安全问题提供一些借鉴。
一、完善监管机制完善监管机制是优化食品安全管理的关键一步。
应建立完善的监督制度,加强对食品生产、加工、运输等环节的监督,确保食品的质量安全。
同时,加强对小作坊、农贸市场等非规范经营场所的监管力度,严厉打击违法行为,提高违法成本,形成强大的震慑力。
二、加强食品生产安全管理加强食品生产安全管理是确保食品安全的基础。
应设立专门的机构负责食品生产安全监管,并对所有食品生产企业进行认定和注册。
此外,加强对食品生产过程的监控,严格执行生产标准,确保食品生产的每一个环节都符合卫生标准,杜绝食品污染。
三、提升食品加工质量食品加工环节是食品安全的重要一环。
应加强对食品加工企业的监管,严格执行生产工艺和卫生标准。
要求企业建立健全的质量管理体系,加强对食品加工过程中可能存在的环境污染、添加剂使用等问题的监控和控制。
只有确保食品加工环节的质量安全,才能保障消费者的健康。
四、加强食品流通环节管理食品流通环节在整个食品供应链中起着连接作用。
应加强对食品流通环节的监督和管理,建立健全食品流通企业的资质认定和监管制度,加强对食品流通过程中可能出现的食品质量安全问题的监测和预防。
同时,要求食品流通企业建立完善的库存管理和追溯体系,提高食品安全的可追溯性。
五、加强食品检验检测工作食品检验检测是确保食品安全的重要手段。
应加强对食品检验检测机构的建设和管理,提高检测仪器设备的先进性和准确度。
同时,加强对食品抽检工作的监督,确保抽检结果的真实可信。
只有加强食品检验检测工作,才能确保食品质量安全。
六、加强食品安全宣传教育加强食品安全宣传教育是提高公众食品安全意识的有效途径。
应加大食品安全知识的普及力度,提高消费者对食品安全的认知和判断能力。
食品企业质量管理措施
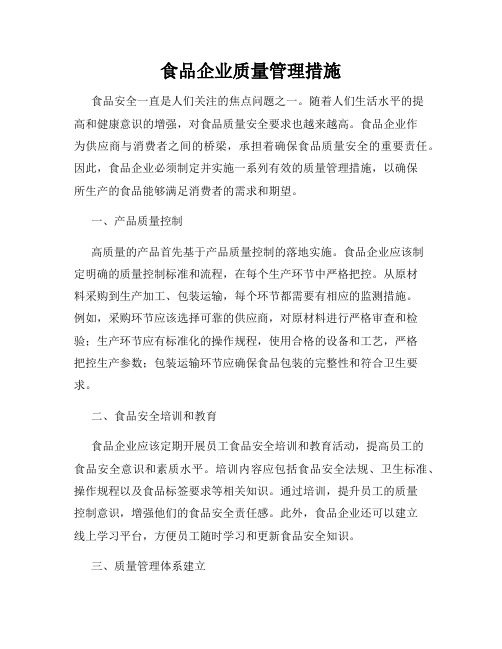
食品企业质量管理措施食品安全一直是人们关注的焦点问题之一。
随着人们生活水平的提高和健康意识的增强,对食品质量安全要求也越来越高。
食品企业作为供应商与消费者之间的桥梁,承担着确保食品质量安全的重要责任。
因此,食品企业必须制定并实施一系列有效的质量管理措施,以确保所生产的食品能够满足消费者的需求和期望。
一、产品质量控制高质量的产品首先基于产品质量控制的落地实施。
食品企业应该制定明确的质量控制标准和流程,在每个生产环节中严格把控。
从原材料采购到生产加工、包装运输,每个环节都需要有相应的监测措施。
例如,采购环节应该选择可靠的供应商,对原材料进行严格审查和检验;生产环节应有标准化的操作规程,使用合格的设备和工艺,严格把控生产参数;包装运输环节应确保食品包装的完整性和符合卫生要求。
二、食品安全培训和教育食品企业应该定期开展员工食品安全培训和教育活动,提高员工的食品安全意识和素质水平。
培训内容应包括食品安全法规、卫生标准、操作规程以及食品标签要求等相关知识。
通过培训,提升员工的质量控制意识,增强他们的食品安全责任感。
此外,食品企业还可以建立线上学习平台,方便员工随时学习和更新食品安全知识。
三、质量管理体系建立食品企业应建立符合国家标准的质量管理体系,如ISO 9001质量管理体系和HACCP食品安全管理体系等。
质量管理体系的建立能够帮助企业提高内部运作效率,确保产品和服务的稳定性和可靠性。
在建立质量管理体系的过程中,食品企业应将质量管理过程全面系统化,包括质量控制、质量保证、质量改进等方面,并通过内部审核和外部认证来保障体系的有效性。
四、设备和设施的维护食品生产中的设备和设施是保证产品质量和食品安全的重要环节。
食品企业应建立设备维护和设施管理的制度,定期对生产设备进行检修和维护,并确保设备能正常运转和卫生洁净。
同时,在设备使用过程中,应采取规范的操作方法和有效的清洁消毒措施,避免交叉污染。
五、食品安全风险评估和监测食品企业应积极开展食品安全风险评估和监测工作。
- 1、下载文档前请自行甄别文档内容的完整性,平台不提供额外的编辑、内容补充、找答案等附加服务。
- 2、"仅部分预览"的文档,不可在线预览部分如存在完整性等问题,可反馈申请退款(可完整预览的文档不适用该条件!)。
- 3、如文档侵犯您的权益,请联系客服反馈,我们会尽快为您处理(人工客服工作时间:9:00-18:30)。
食品质量管理的先进方法
为了提高食品卫生质量,防止食品污染的有害因素对人体的危害,保障人民身体健康,就需要加强食品卫生管理,特别要加强食品企业自身的卫生管理。
食品企业要保证产品的卫生质量,必须建立起本企业的质量控制体系。
质量控制体系主要由两方面内容构成,一是保证产品质量合乎卫生标准,即从产品质量上控制。
二是从生产工艺上制订工艺过程卫生技术标准,使整个生产工艺均符合工艺卫生技术规范,产品质量自然符合食品卫生标准。
即实行产品和工艺双重控制,以保证产品质量。
执行良好的生产规范(GMP)和运用危害分析和关键控制点(HACCP)等食品卫生质量管理先进方法,对保证食品安全卫生,加快改善食品厂的卫生面貌,实现食品卫生管理标准化和规范化,起到积极的重要作用。
一、良好的生产规范(GMP)
制造、加工和销售质量好而安全性高的食品,是食品行业重大的社会责任。
为此,在食品制造过程中,制定严密的日常卫生和质量管理制度,并切实加以实施是至关重要的。
对于食品制度过程中的质量管理,发达国家逐步推广采用GMP方式,并有进一步国际化的趋势。
GMP为GoodManufacturingPractice的缩写,原意为良好的制造实践,比较通用的译法是良好的制造规范或良好生产工艺。
就是说GMP是产品的制造法,是生产过程的管理法规。
1963年美国FnA(食品药物管理局)首先制订了医药品的GMP。
1969年wHo(世界卫生组织)将美国的医药品GMP推荐给有关各国政府,并开始了医药品GMP的制度化。
食品制造与医药品生产在卫生和质量管理方面有许多共同之处。
因此,1969年美国政府发布了“食品制造、加工、包装和贮运中的一般良好制造标准”,即通常所说的食品GMP,作为食品制造的基本法规。
按GMP方式制定的和实施的食品制造标准,主要着眼于以下几个环节:
(一)各种原材料,每一工序中间产品的安全性和保证。
(二)各种污染的防止。
为了避免食品中附着和混入夹杂物、重金属、残留农药、食品中毒的病原菌或有损于食品质量的微生物,必须采取有效措施,切实防止来自工厂设施、操作环境、机械器具、空中沉降细菌和操作人员等方面的污染。
(三)加强工艺技术方面的管理,实行双重检查,建立各工艺的检验制度和质量管理制度,对于误差的防除措施。
(四)商标管理。
(五)管理记录的保存。
保证食品的安全性,提高食品质量,食品工厂的日常卫生管理是很重要的。
美国的GMP采用危害分析和关键控制点(HACCP)方法,把对原材料的危害分析和制造过程的重点管理,作为微生物的管理重点,对整个制造过程进行系统管理。
如上所述,食品GMF是在从原材料到产品的整个食品制造过程中,为了充分进行卫生和质量管理,排除不卫生食品,确保食品的高质量而制定的,这与以产品抽样检查为中心的质量管理制度是大不相同的。
美国低酸性罐头食品的GMP是针对六十年代后期美国相继发生市销罐头食品的肉毒杆菌的中毒事件而制定的罐头制造法规,其内容包括一般事项、机械器具、内容物、罐头容器、卷边、生产过程管理、记录和报告等,其中特别是对罐头生产中的重点工序杀菌和卷边,包括杀菌釜结构、温度管理、卷边部分的检查方法等重点及其管理方法都有极周密的规定。
对于向美国出口的罐头食品必须分别按工厂而且要对每一罐头品种,根据加热杀菌致死值(F0)和传热曲线,计算出加热时间并据此向FnA申报。
其他食品也有自己的GMP。
由此看来,食品GMP既是食品制造规范,又是制造食品所必须遵循的技术标准。
GMP是发达国家食品质量管理的先进方法和成功经验,也是保证食品卫生质量的关键。
目前,世界各国的食品规格或食品卫生法规是大不相同的。
FAO(联合国粮农组织)和WHO 成立了国际食品规格委员会,致力于食品规格的统一和食品卫生法规的协调,以促进国际食品贸易。
预计,食品及其制造和加工技术,食品添加剂和其他食品卫生方面的规格标准,将会逐步实现国际化。
我国已经颁布了《罐头厂卫生规范》、《乳品厂卫生规范》等十五类规范,并以国家标准的形式列于法规之中,要求在全国范围内加以实施。
我国的食品企业卫生规范,相当于国外广泛应用的GMP管理方法。
我国的GMP的颁布和实施,对食品卫生法的进一步贯彻执行,保证食品安全卫生,加快改善食品厂的卫生面貌,实现卫生管理标准化和规范化,保障人民健康,起到积极的重要作用。
二、关键点危险性分析(HACCP)
1980年,世界卫生组织(WHO)和国际食品微生物规格委员会向饮食业推荐了HACCP管理系统。
它是一个预防性的食品安全监控系统。
危害分析和关键控制点(HACCP)的原文为:HazardAnalysisCriticalContr01Point,HACCP亦可译为关键点危险性分析(管理法)或危害分析关键控制环节(体制)。
利用检验手段进行监测对卫生质量控制是最有效的。
使用现代化检测手段,不仅对成品逐批
检验,而且对生产工艺也利用检验手段进行因素分析。
不仅检验成品,还要经常对工器具、工人手、半成品进行微生物学检验。
从检验结果中分析出影响产品卫生质量的因素,再反馈到工艺规程中加以改进。
如此循环反馈不断提高。
美国把这种工艺监测反馈管理方法称之为HACCP。
HACCP方法的要点是:进行危害性分析以确定可引起食品污染的操作方法,判断经过热处理以后的食品中是否还有致病菌存活,以及查明致病菌繁殖到危害消费者健康程度的机会;确定操作过程的关键控制点;实施适当的预防和控制措施;对每个关键控制点的操作进行日常监督。
HACCP的具体实施步骤是:
(一)危害分析的要素和危害分类
危害分析的第一步是就该工厂的每一种产品,绘制工艺流程图。
由于各工厂条件不同,工艺流程不同,即使同一产品也必须分别进行。
若是同一工厂,如设备和工、艺有改变,也应重新进行危害分析。
从一般的危害特性把因素分为如下三类:
1.该产品含有不稳定成分,于一般环境下成为潜在的污染源。
2.加工过程中没有可控制的加热工序,以杀灭有害微生物。
3.在运输、流通过程中或消费者处理过程中,或消费者购买后仍有微生物繁殖的可能性,如微生物繁殖后则食用该食品可能对健康造成危害者。
根据上述三类危害分析的综合因素,将原材料分为I(危害性高)一IY(危害性低)四个等级。
(二)关键控制点(CCP)的确定及管理方法
根据上述危害分析的类别,按产品生产工艺流程,对容易造成微生物污染或增殖,特别是需要严格进行微生物部分确定为关键控制点。
制定原材料及关键工序的控制标准,对各关键控制点进行分析检查。
当对原材料、生产工序和产品的检验发现有问题时,立即针对问题发生原因,制定改进措施,并对生产过程的管理进行调整,以维持良好的生产状态。
HACCP是个系统工程,必须领导重视,全员投入共同协调配合,才能保证HACCP的正常运转,取得预期的效果。
而且HACCP也不是一成不变的,随着科学技术的发展,质量保证措施的落实,危害因素会不断变化,也就是说,最高危害控制后会变成低度危害或没有危害,而原来中度危害相对来说会变成最高危害,不断将危害因素控制,质量才能不断提高,所以HACCP也应象GMP一样,需要不断修整,每修整一次,产品质量就会上一个新台阶。
随着我国各类食品的GMP和HACCP的制定与实施,我国食品卫生水平将会有较大的提高。