注塑模具中常见39大问题的实例讲解
注塑模具试模时几种经常出现问题及解决方法
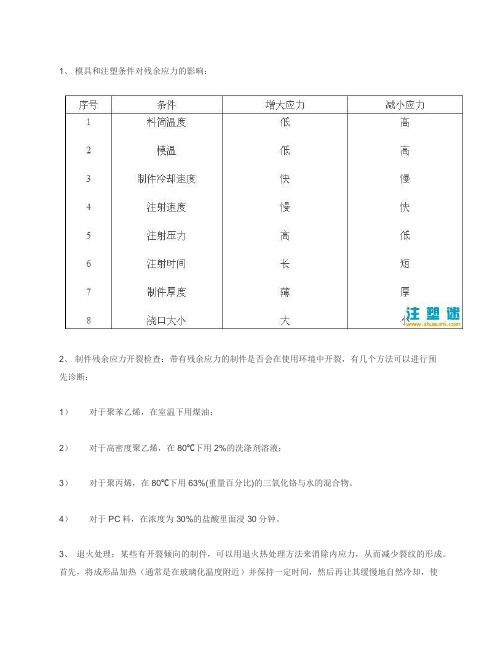
1、模具和注塑条件对残余应力的影响:
2、制件残余应力开裂检查:带有残余应力的制件是否会在使用环境中开裂,有几个方法可以进行预
先诊断:
1)对于聚苯乙烯,在室温下用煤油;
2)对于高密度聚乙烯,在80℃下用2%的洗涤剂溶液;
3)对于聚丙烯,在80℃下用63%(重量百分比)的三氧化铬与水的混合物。
4)对于PC料,在浓度为30%的盐酸里面浸30分钟。
3、退火处理:某些有开裂倾向的制件,可以用退火热处理方法来消除内应力,从而减少裂纹的形成。
首先,将成形品加热(通常是在玻璃化温度附近)并保持一定时间,然后再让其缓慢地自然冷却,使
发生裂纹处的大分子能自由活动、回复原来状态。
这种退火热处理法一般在成形后立即进行。
4、调湿处理:对于尼龙塑件,为了改善内应力分布状况及塑料内的晶体结构,提高制件韧性,保持尺寸相对稳定,可以进行调湿处理,其效果比退火处理更佳。
方法是将制件浸入沸水或醋酸钾水溶液(比例为 1.25:100,沸点121℃)中,浸泡时间视制件最大壁厚而定,从2小时至16小时不等。
注塑过程中常见的问题及解决方案

注塑过程中常见的问题及解决方案一、飞边(披锋)1. 问题描述- 这飞边就像塑料偷偷长出来的小翅膀,在注塑件的边缘或者分型面那里冒出来,看着可闹心了。
就像好好的一块蛋糕,边缘突然多出了一些不规则的奶油坨坨。
2. 解决方案- 首先得检查模具的合模力。
要是合模力不够,那塑料就会像调皮的小孩从门缝里挤出来。
适当增加合模力,把模具紧紧抱住,让塑料乖乖待在该待的地方。
- 模具的磨损也会导致飞边。
就像穿破了的鞋子会漏脚指头一样,磨损的模具缝隙变大了。
这时候就得修模啦,把那些磨损的地方补一补或者磨平。
- 注塑压力也不能太大。
如果压力太大,塑料就像被大力士猛推的水,到处乱流。
降低注塑压力,找到一个合适的值,既能把模具填满,又不会让塑料溢出来。
二、短射(缺料)1. 问题描述- 短射就像给一个杯子倒水,结果没倒满一样。
注塑件看着不完整,有些地方该有塑料的却空着,就像一个没发育好的小怪物。
2. 解决方案- 先看看注塑压力是不是太小。
压力小的话,塑料就像没力气的小蚂蚁,爬不到模具的每个角落。
增加注塑压力,让塑料充满整个模具型腔。
- 塑料的流动性也很关键。
如果塑料太黏,就像浓稠的糨糊,很难流到模具的远端。
这时候可以提高料筒温度,让塑料变得稀一点,流动性更好,就像把糨糊加热变成稀粥一样,能顺利流到各个地方。
- 浇口尺寸也可能有问题。
要是浇口太小,就像一个小得可怜的水龙头,水流不出来多少。
适当扩大浇口尺寸,让塑料能畅快地流进模具。
三、气泡(气穴)1. 问题描述2. 解决方案- 注塑速度可能太快了。
塑料像一阵风呼呼地冲进模具,把空气都裹在里面了。
降低注塑速度,让塑料慢慢流进去,就像散步一样,这样空气就有机会跑出来了。
- 模具的排气也很重要。
如果模具没有排气孔或者排气不良,空气就被困在里面出不来。
在模具上开排气槽或者使用透气钢材料,给空气一条逃跑的路。
- 塑料干燥不彻底也会产生气泡。
如果塑料里有水份,加热的时候就会变成水蒸气,形成气泡。
注塑模具常见问题及解决办法【图解】

塑料模具,是塑料加工工业中和塑料成型机配套,赋予塑料制品以完整构型和精确尺寸的工具。
由于塑料品种和加工方法繁多,塑料成型机和塑料制品的结构又繁简不一,所以,塑料模具的种类和结构也是多种多样的。
注塑模具常见问题及解决办法详细介绍如下:1.浇口脱料困难在注塑过程中,浇口粘在浇口套内,不易脱出。
开模时,制品出现裂纹损伤。
此外,操作者必须用铜棒尖端从喷嘴处敲出,使之松动后方可脱模,严重影响生产效率。
这种故障主要原因是浇口锥孔光洁度差,内孔圆周方向有刀痕。
其次是材料太软,使用一段时间后锥孔小端变形或损伤,以及喷嘴球面弧度太小,致使浇口料在此处产生铆头。
浇口套的锥孔较难加工,应尽量采用标准件,如需自行加工,也应自制或购买专用铰刀。
锥孔需经过研磨至Ra0.4以上。
此外,必须设置浇口拉料杆或者浇口顶出机构。
2.导柱损伤导柱在模具中主要起导向作用,以保证型芯和型腔的成型面在任何情况下互不相碰,不能以导柱作为受力件或定位件用。
在以下几种情况下,注射时动,定模将产生巨大的侧向偏移力:(1).塑件壁厚要求不均匀时,料流通过厚壁处速率大,在此处产生较大的压力;(2).塑件侧面不对称,如阶梯形分型面的模具相对的两侧面所受的反压力不相等。
3.大型模具因各向充料速率不同,以及在装模时受模具自重的影响,产生动定模偏移。
在上述几种情况下,注射时侧向偏移力将加在导柱上,开模时导柱表面拉毛,损伤,严重时导柱弯曲或切断,甚至无法开模。
为了解决以上问题在模具分型面上增设高强度的定位键四面各一个,最简便有效的是采用圆柱键。
导柱孔与分模面的垂直度至关重要.在加工时是采用动,定模对准位置夹紧后,在镗床上一次镗完,这样可保证动,定模孔的同心度,并使垂直度误差最小。
此外,导柱及导套的热处理硬度务必达到设计要求。
4.动模板弯曲模具在注射时,模腔内熔融塑料产生巨大的反压力,一般在600~1000公斤/厘米。
模具制造者有时不重视此问题,往往改变原设计尺寸,或者把动模板用低强度钢板代替,在用顶杆顶料的模具中,由于两侧座跨距大,造成注射时模板下弯。
注塑模成型过程中的常见缺陷及解决方法

注塑模成型过程中的常见缺陷及解决方法
1 注塑模成型过程中的缺陷
注塑模是指将塑料以液体状态注入模具内,并承受模具内设计好的形状而成型的加工工艺。
这种加工工艺的缺陷主要体现在:(1)内应力
由于冷凝和冻结等原因,塑料在冷却期内会形成一定的内应力,这些内应力会折断或变形塑料制品,影响其成型的精度和尺寸的准确性;
(2)开裂
由于注塑模具的温度失去平衡,容易引起塑料表面开裂,影响塑料制品的外观质量;
(3)射脂
由于过大的模具压力,塑料在冷却过程中产生弹性变形,导致部分塑料夹在模具内,出现射脂现象,从而影响塑料制品的精度;
(4)易燃体
一些易燃物质在注塑模具成型过程中,受到热源的热量,容易引发火灾。
2 注塑模成型过程中的解决方法
(1)改善冷凝条件
合理设计模具内的冷凝段,增加冷却水的循环流量,加快冷却速度,降低内应力,减少变形现象;
(2)模具润滑
模具润滑能有效减少注塑模具生产过程中开裂的几率;
(3)改变模具温度
根据注塑塑料特性,采取合理的模具温度,确保合理的射出压力,有效减少射脂;
(4)加强安全防护
增强环境湿度,禁止一切产生火花的设备进入生产现场,防止火灾。
总之,正确处理注塑模具成型过程中的缺陷和解决方法,能有效
改善塑料制品的成型精度,改善它们的外观、可靠性和使用寿命,能
为有效利用注塑技术提供有效援力。
注塑模具问题点汇总清单

注塑模具问题点汇总清单一、外观问题1. 飞边(披锋)- 这模具做出来的产品边缘毛毛糙糙的,就像人没刮干净胡子似的。
在合模的地方或者一些薄壁处,老是有多余的塑料跑出来,形成飞边,影响产品的外观,也可能会刮伤人呢。
2. 缩水痕- 产品表面有那种凹下去的小坑洼,就像人脸上突然长了麻子一样。
在产品壁厚比较厚的地方,冷却的时候不均匀,就容易出现这种缩水痕,看起来可丑了。
3. 流痕- 那些像波浪一样的纹路在产品表面,就像有人在塑料还没干的时候乱划了几笔。
塑料在模具里流动的时候不顺畅,就产生了这种流痕,让产品看起来很不精致。
4. 气泡- 产品里面有像小珠子一样的空洞,就像面包没发好里面有大气泡一样。
注塑的时候,空气没排干净或者塑料里有水分,就会产生这种气泡,感觉产品就像个空心萝卜。
5. 熔接痕- 产品表面有一条明显的线,就像衣服上缝了一道歪歪扭扭的补丁。
不同的塑料流在模具里汇合的时候没融合好,就出现了熔接痕,把产品的美观都破坏了。
6. 表面光泽度不一致- 有的地方亮晶晶的,有的地方却雾蒙蒙的,就像人穿了件一半是绸缎一半是粗布的衣服。
可能是模具表面的光洁度不一样,或者脱模剂喷得不均匀造成的。
二、尺寸问题1. 尺寸偏差过大- 做出来的产品大小跟设计的不一样,有的地方大得像个胖子,有的地方小得像个瘦子。
可能是模具的型腔尺寸没加工准确,或者注塑的时候温度、压力等工艺参数影响了塑料的收缩率。
2. 形状变形- 本来应该是方方正正的产品,结果变成了歪歪扭扭的四边形,就像被人捏过的橡皮泥。
可能是模具的结构不合理,在脱模的时候对产品施加了不均匀的力,或者冷却不均匀导致产品变形。
三、结构问题1. 脱模困难- 产品在模具里就像被胶水粘住了一样,死活不愿意出来。
可能是拔模斜度不够,或者模具的表面粗糙度太大,摩擦力太大,让产品卡在里面出不来。
2. 模具零件损坏- 像那些顶针啊、滑块啊,有时候会断掉或者磨损得很厉害。
就像人的牙齿掉了或者磨平了一样,顶针断了就没法正常顶出产品,滑块磨损了可能会导致合模不严或者产品表面划伤。
塑料模具设计常见问题及改进方法

塑料模具设计常见问题及改进方法塑料模具设计在工程制造过程中起着非常重要的作用。
一个优秀的塑料模具设计能够提高生产效率、降低生产成本,同时还能保证产品的质量和精度。
在塑料模具设计过程中,也会存在一些常见问题,这些问题如果得不到有效的解决,就会导致生产过程中出现质量问题、生产效率低下等一系列问题,对整个工程制造过程产生负面影响。
对于塑料模具设计中的常见问题,我们需要及时识别并进行改进,以保证生产过程的顺利进行。
常见问题一:产品结构复杂造成模具设计困难在实际生产中,由于产品结构复杂,例如产品内部有很多空间复杂轮廓,产品的角度较大等原因,会导致模具设计困难。
这时模具的设计和制造就需要更高的技术要求和复杂的加工工艺,会增加模具设计和制造的难度和成本。
改进方法:1. 在产品设计阶段就应该考虑到成型工艺和模具设计,设计工程师、模具工程师、生产制造工程师应该密切合作,共同完成产品设计和模具设计。
2. 在模具设计阶段,应充分考虑产品的结构特点,尽量将产品分解为简单的几何体,减少模具制造难度。
3. 选择合适的材料和加工工艺,比如采用CNC加工、3D打印等技术,能够更快速地完成复杂结构的模具制作。
常见问题二:模具寿命短,易损坏在生产过程中,模具容易出现磨损、疲劳、裂纹等问题,导致模具寿命缩短,需要频繁更换模具,增加了生产成本,降低了生产效率。
改进方法:1. 选择高质量的模具材料,比如优质的工具钢、耐磨材料等,能够提高模具的抗磨损性能和抗疲劳性能,延长模具的使用寿命。
2. 对模具进行合理的热处理,提高模具的硬度和韧性,增加模具的抗疲劳和抗裂纹能力。
3. 在设计阶段就考虑到模具的结构和加工工艺,尽量减少模具的受力集中和磨损部位,增加模具的使用寿命。
常见问题三:模具精度不高,影响产品质量模具的精度直接关系到产品的质量和精度,如果模具精度不高,就会导致产品尺寸不准确,表面粗糙,甚至出现开裂、变形等问题。
常见问题四:模具开发周期长,影响项目进度模具的设计和制造周期较长,会影响整个项目的进度,延误产品的上市和交付时间。
注塑模具常见问题分析

注塑模具常见问题分析?变色焦化出现黑点的原因分析造成注塑制品变色焦化出现黑点的主要原因是塑料或添加的紫外线吸收剂、防静电剂等在料筒内过热分解,或在料筒内停留时间过长而分解、焦化,再随同熔料注入型腔形成。
分析如下:1.机台方面:(1)由于加热控制系统失控,导致料筒过热造成分解变黑。
(2)由于螺杆或料筒的缺陷使熔料卡入而囤积,经受长时间固定加热造成分解。
应检查过胶头套件是否磨损或里面是否有金属异物。
(3)某些塑料如ABS在料筒内受到高热而交联焦化,在几乎维持原来颗粒形状情形下,难以熔融,被螺杆压破碎后夹带进入制件。
2.模具方面:(1)模具排气不顺,易烧焦,或浇注系统的尺寸过小,剪切过于厉害造成焦化。
(2)模内有不适当的油类润滑剂、脱模剂。
3.塑料方面:塑料挥发物过多,湿度过大,杂质过多,再生料过多,受污染。
4.加工方面:(1)压力过大,速度过高,背压过大,转速过快都会使料温分解。
(2)应定期清洁料筒,清除比塑料耐性还差的添加剂。
出现分层剥离的原因分析造成注塑制品出现分层剥离原因及排除方法:1.料温太低、模具温度太低,造成内应力与熔接缝的出现。
2.注射速度太低,应适当减慢速度。
3.背压太低。
4.原料内混入异料杂质,应筛除异料或换用新料。
肿胀和鼓泡的原因分析有些塑料制件在成型脱模后,很快在金属嵌件的背面或在特别厚的部位出现肿胀或鼓泡。
这是因为未完全冷却硬化的塑料在内压的作用下释放气体膨胀造成。
解决措施:1.有效的冷却。
降低模温,延长开模时间,降低料的干燥与加工温度。
2.降低充模速度,减少成形周期,减少流动阻力。
3.提高保压压力和时间。
4.改善制件壁面太厚或厚薄变化大的状况。
透明缺陷的原因分析熔斑、银纹、裂纹聚苯乙烯、有机玻璃的透明制件,有时候透过光线可以看到一些闪闪发光的细丝般的银纹。
这些银纹又称烁斑或裂纹。
这是由于拉应力的垂直方向产生了应力,使聚合物分子在流动方向取向,使得取向部分与未取向部分折射率不同,光线透过两者界面时发生折射产生银纹。
常见注塑件缺陷及解决的方法
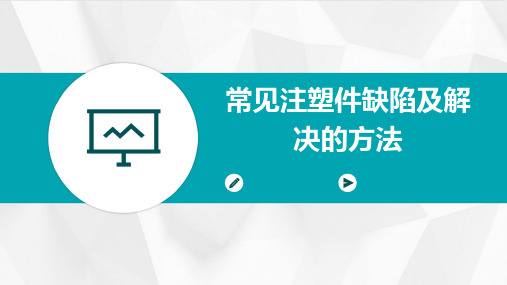
充填不足
01
总结词
充填不足是指注塑件在成型过程中未能完全填满 模具型腔,导致部分区域出现缺料或凹陷。
02
详细描述
充填不足通常是由于注射速度慢、注射压力不足、 模具温度过高或塑料流动性差等原因引起的。
缩痕
总结词
缩痕是指注塑件表面出现凹陷或收缩痕迹,影响 外观和尺寸精度。
详细描述
缩痕通常是由于塑料冷却过程中收缩率不均、模 具温度不均匀或注射压力不足等原因引起的。
常见注塑件缺陷及解 决的方法
目录
• 常见注塑件缺陷 • 注塑件缺陷原因分析 • 解决注塑件缺陷的方法 • 案例分析
01
常见注塑件缺陷
翘曲与扭曲
总结词
翘曲与扭曲是指注塑件形状发生扭曲或弯曲,不符合设 计要求。
详细描述
翘曲与扭曲通常是由于模具设计不合理、塑料收缩率差 异、注射温度和压力不适当等原因引起的。
环境条件的控制Байду номын сангаас
总结词
保持稳定的环境条件对注塑件的质量至关重 要,包括温度、湿度和清洁度等。
详细描述
确保注塑车间温度、湿度稳定,保持环境清 洁、无尘。定期对设备和环境进行清理和消 毒,防止污染和细菌滋生。同时,要关注天 气变化和季节性温差对注塑件质量的影响,
采取相应的措施进行调节。
04
案例分析
案例一:翘曲与扭曲缺陷的解决
材料选择与控制
总结词
选择合适的材料,控制材料质量是解决注塑件缺陷的重要步骤。
详细描述
根据产品使用要求和工艺特性,选择具有良好流动性和成型性的材料。同时, 要确保材料干燥、清洁,无杂质和污染。定期对材料进行质量检查,确保其性 能稳定。
模具优化与维护
注塑模具出现的问题及原因分析!

注塑制品开裂的原因分析开裂,包括制件表面丝状裂纹、微裂、顶白、开裂及因制件粘模、流道粘模而造成或创伤危机,按开裂时间分脱模开裂和应用开裂。
主要有以下几个方面的原因造成:1.加工方面:(1)加工压力过大、速度过快、充料愈多、注射、保压时间过长,都会造成内应力过大而开裂。
(2)调节开模速度与压力防止快速强拉制件造成脱模开裂。
(3)适当调高模具温度,使制件易于脱模,适当调低料温防止分解。
(4)预防由于熔接痕,塑料降解造成机械强度变低而出现开裂。
(5)适当使用脱模剂,注意经常消除模面附着的气雾等物质。
(6)制件残余应力,可通过在成型后立即进行退火热处理来消除内应力而减少裂纹的生成。
2.模具方面:(1)顶出要平衡,如顶杆数量、截面积要足够,脱模斜度要足够,型腔面要有足够光滑,这样才防止由于外力导致顶出残余应力集中而开裂。
(2)制件结构不能太薄,过渡部份应尽量采用圆弧过渡,避免尖角、倒角造成应力集中。
(3)尽量少用金属嵌件,以防止嵌件与制件收缩率不同造成内应力加大。
(4)对深底制件应设置适当的脱模进气孔道,防止形成真空负压。
(5)主流道足够大使浇口料未来得及固化时脱模,这样易于脱模。
(6)主流道衬套与喷嘴接合应当防止冷硬料的拖拉而使制件粘在定模上。
3.材料方面:(1)再生料含量太高,造成制件强度过低。
(2)湿度过大,造成一些塑料与水汽发生化学反应,降低强度而出现顶出开裂。
(3)材料本身不适宜正在加工的环境或质量欠佳,受到污染都会造成开裂。
4.机台方面:注塑机塑化容量要适当,过小塑化不充分未能完全混合而变脆,过大时会降解。
注塑制品气泡的原因分析气泡(真空泡)的气体十分稀薄属于真空泡。
一般说来,如果在开模瞬间已发现存在气泡是属于气体干扰问题。
真空泡的形成是由于充注进塑料不足或压力较低。
在模具的急剧冷却作用下,与型腔接角的燃料牵拉,造成体积损失的结果。
解决办法:(1)提高注射能量:压力、速度、时间和料量,并提高背压,使充模丰满。
注塑模具各类问题原因分析及解决办法
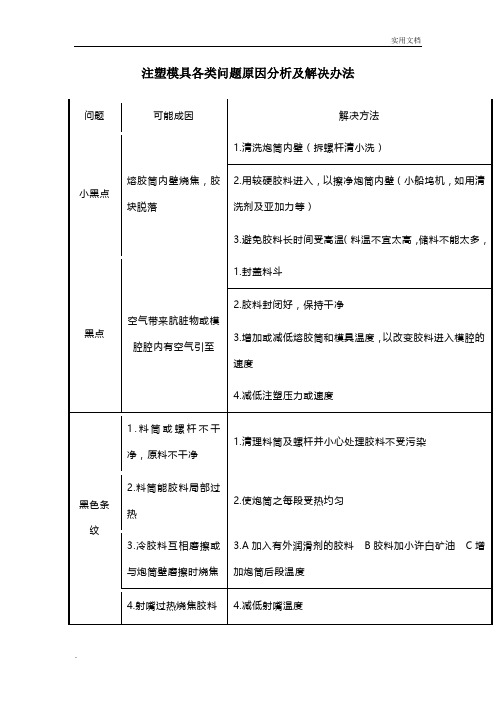
注塑模具各类问题原因分析及解决办法注塑成型过程中,制品收缩凹陷是比较常见的现象。
造成这种情况的主要原因有:机台方面(1)射嘴孔太大造成融料回流而出现收缩,太小时阻力大料量不足出现收缩。
(2)锁模力不足造成飞边也会出现收缩,应检查锁模系统是否有问题。
(3)塑化量不足应选用塑化量大的机台,检查螺杆与料筒是否磨损。
模具方面(1)制件设计要使壁厚均匀,保证收缩一致。
(2)模具的冷却、加温系统要保证各部份的温度一致。
(3)浇注系统要保证通畅,阻力不能过大,如主流道、分流道、浇口的尺寸要适当,光洁度要足够,过渡区要圆弧过渡。
(4)对薄件应提高温度,保证料流畅顺,对厚壁制件应降低模温。
(5)浇口要对称开设,尽量开设在制件厚壁部位,应增加冷料井容积。
塑料方面结晶性的塑料比非结晶性塑料收缩历害,加工时要适当增加料量,或在塑料中加成换剂,以加快结晶,减少收缩凹陷。
加工方面(1)料筒温度过高,容积变化大,特别是前炉温度,对流动性差的塑料应适当提高温度、保证畅顺。
(2)注射压力、速度、背压过低、注射时间过短,使料量或密度不足而收缩压力、速度、背压过大、时间过长造成飞边而出现收缩。
(3)加料量即缓冲垫过大时消耗注射压力,过小时,料量不足。
(4)对于不要求精度的制件,在注射保压完毕,外层基本冷凝硬化而夹心部份尚柔软又能顶出的制件,及早出模,让其在空气或热水中缓慢冷却,可以使收缩凹陷平缓而不那么显眼又不影响使用。
2注塑件震纹的原因分析PS等刚性塑料制件在其浇口附近的表面,以浇口为中心的形成密集的波纹,有时称为震纹。
产生原因是熔体粘度过大而以滞流形式充模时,前端的料一接触到型腔表面便很快冷凝收缩起来,而后来的熔料又胀开已收缩的冷料继续前进过程的不断交替使料流在前进中形成了表面震纹。
解决办法(1)提高料筒温度特别是射嘴温度,还应提高模具温度。
(2)提高注射压力与速度,使其快速充模型腔。
(3)改善流道、浇口尺寸,防止阻力过大。
(4)模具排气要良好,要设置足够大的冷料井。
塑料模具常见问题及解决方法

1、消除制品凹痕的方法2、消除缺料的方法3、消除制品银条痕的方法4、消除制品飞边的方法5、消除制品变形的方法6、消除制品裂纹的方法7、消除制品应力龟裂的方法8、消除制品网装龟裂的方法9、消除制品白化的方法10、消除制品熔合痕的方法11、消除制品内波流的方法12、消除制品产生糊斑的方法13、消除制品产生黑条的方法14、消除制品色不均匀的方法15、消除制品光洁度不良的方法16、消除制品气蚀的方法17、消除制品漩纹的方法18、消除制品脆化的方法19、消除制品使用破碎料产生白化以及脆化的方法20、消除制品内异物不良的方法21、消除制品产生剥离现象的方法22、消除制品尺寸不良的方法23、消除制品小皱纹的方法24、消除制品脱模时的破损以及裂纹的方法25、消除注口料脱模不良的方法26、消除制品上痕迹的方法27、消除制品透明度不良的方法28、消除制品浇口断裂的方法29、消除制品厚度偏差的方法30、消除模具错位的方法31、防止模具胀裂的方法32、防止模具导柱折断的方法33、防止模具咬合的方法34、防止模具生锈的方法35、如何使残留在模具内注口料脱出的方法36、如何使残留在模具内制品出来的方法37、补救外观不良制品的方法38、制品翘曲的矫正方法39、消除制品上热压印不明的方法40、消除制品剥落的方法41、成型缺陷的对策表42、同一材料异色的替换作业43、不同材料的替换作业44、常见塑料材料的简单判别45、常见塑料材料的注塑温度和预干燥温度46、浇口的大小同成型性能的关系47、什么是注塑成型的五要素48、一般的模具构造49、模具的注口,流边和浇口50什么是捏和性螺杆51何谓注塑机52何谓注塑机的注塑量53何谓注塑机的可塑化能力54何谓成形收缩率55何谓成形所必要的锁模力56制品脱模的方法57在固定侧使制品脱模的方法58模具冷却的方法59制品厚度的范围60加强筋同凸起部的设计方法61设计容器类制品时地注意点62透明塑料有那些东西63有既透明又耐冲击性的塑料吗?64耐冲击性最好的塑料是ABS吗?65有耐热性的塑料吗?66耐摩性好的塑料材料那些67倾向于刚性用途的材料是那些68要求制品具有弹性时用什么样的材料69有那些材料是可以镀的70耐燃性的材料有那些71耐药品性的塑料有那些72有必要于干燥的塑料有那些73在料筒内容易分解的塑料有那些74要求成形模具温度高的塑料是那些75流动性太好的塑料在成形上的注意点76成形后必须清除料筒的塑料是那些77塑料的热特性同其它材料的比较78塑料的化学特性同其它材料的比较79塑料的电气特性同其它材料的比较80塑料的老化性能同其它材料的比较81塑料的加工精度同其它材料的比较82塑料的强度同其它材料的比较83塑料使用的可塑剂有那些东西84塑料使用的安定剂有那些东西85塑料使用的润滑剂有那些东西86塑料使用的填充剂有那些东西87塑料使用的色料有那些东西88塑料使用的发泡剂有那些东西89什么叫体积电阻90什么叫表面电阻91什么叫电弧阻抗92什么叫诱电率93什么叫热变形温度94塑料的分子构造同机械性能的关系怎么95塑料的分子构造同耐热性的关系怎么96塑料的分子构造同耐湿性的关系怎么97塑料的分子构造同耐热性的关系怎么98什么是SP值99高分子的结晶化度同溶解度参数的关系怎样100转移点同分子构造的关系怎样101什么叫溶化指数102支配成形性的要点有那些参数103模具内的压力是怎样地变化104树脂温度同射出压对浇口长度有什么影响105成形工程中材料密度是怎样地变化106结晶性塑料在成形上的注意点107配向是怎么样的现象108成形性能同分子量、分子构造的关系怎么样109塑料的流动性特性同流变学110何谓标准注嘴111何谓延长注嘴112何谓溶化型注嘴113何谓搅拌型注嘴114何谓阀控式注嘴115何谓热流道注嘴116注嘴接触应怎么样117模具的普通制作方法时那些118应如何加工模具型腔内带有的花纹119何谓电铸模具120何谓铜合金铸造模具121何谓滚切模具122何谓陶瓷式成型法(肖式精密铸造法) 123何谓电火花加工124何谓L位置注塑机125何谓折缘注塑机126何谓旋转式注塑机127何谓高速注塑机128何谓排气式注塑机129何谓低压注塑机130何谓流动型注塑机131何谓发泡专用注塑机132何谓外壳专用注塑机133何谓压缩成型机134何谓夹层发泡注塑机135何谓锤打式注塑机136注塑机注塑制品的制作程序137注塑制品的设计程序138常见注塑机的所属设备139制品的成本同日期待决定方法140模具的制作顺序141电视机外壳使用有那些特性的材料142电冰箱内装饰品使用那些特性的材料143洗衣机的小部件使用那些特性的材料144照相机的小部件使用那些特性的材料145贮存器具使用那些特性的材料146小汽车部件使用那些特性的材料147精密齿轮使用那些特性的材料148家具使用那些特性的材料149注塑成型的发展方向50、常见塑料材料的中、英名称和简写1、消除制品凹痕的方法一、产生凹痕的原因1-1制品各部分厚度不同1-2模具内在压力不足1-3模具冷却不充分1-4由于冷却时间不足而产生的变形二、相关联的知识2-1 在生产制品过程中,凹痕是不良现象中发生频率最高的,注入模具的塑料在冷却时发生体积收缩,早冷却部分即表面首先硬化,内部就会产生气泡,所谓凹痕,就是冷却慢的部分在气泡收缩的方向产生了显眼的凹面。
注塑模具在使用过程中常出现的问题

注射
浇口衬套 浇口、流道 浇口、
靠近浇口处 合模面 变厚或飞边
小顶杆 小顶杆托板
动模的变形(一般动模侧的变形比定模侧多 动模的变形 一般动模侧的变形比定模侧多) 一般动模侧的变形比定模侧多
4、模具温度不合适造成不良产品 、模具温度不合适造成不良产品
模具温度过低, 模具温度过低,则造成填 充不足,表面模糊不清, 充不足 , 表面模糊不清 , 产 生熔接痕等毛病 ; 生熔接痕 等毛病;过高则成 等毛病 型周期加长, 引起收缩 收缩等 型周期加长 , 引起 收缩 等 , 应根据树脂及成型品形状选 择适当的模具温度且使温度 择适当的模具温度且使 温度 恒定。 恒定。
一般来说,聚碳酸酯、聚甲基丙烯酸甲酯( 一般来说,聚碳酸酯、聚甲基丙烯酸甲酯( 有机 玻璃)等高粘度树脂的模具温度高 聚乙烯、 模具温度高;聚乙烯 玻璃 ) 等高粘度树脂的 模具温度高 聚乙烯 、 苯乙烯 等低粘度树脂的模具温度低, 等低粘度树脂的模具温度低,特别需要注意稳定温度 的树脂为尼龙、聚甲醛、聚丙烯等结晶性树脂。 的树脂为尼龙、聚甲醛、聚丙烯等结晶性树脂。利用 尼龙 这种树脂精密成型时,应尽力将模具温度变动辐度控 这种树脂精密成型时, 制到± ℃以下。 制到±5℃以下。 结晶性树脂在高温模具慢慢冷却和在低温模具急 结晶性树脂 在高温模具慢慢冷却和在低温模具急 剧冷却时,收缩情况有所不同,慢慢冷却收缩大, 剧冷却时,收缩情况有所不同,慢慢冷却收缩大,急 剧冷却收缩小。 剧冷却收缩小。
分型面
顶杆
确定可紧贴着移动侧,另外, 确定可紧贴着移动侧,另外,型芯 冷却好,可紧紧抱住型芯,故情况良好。 冷却好,可紧紧抱住型芯,故情况良好。 固定侧脱模斜度小 难于开模, 脱模斜度小, 固定侧脱模斜度小,难于开模, 应尽可能用硬的材料,仔细研磨。 应尽可能用硬的材料,仔细研磨。
注塑模具常见的问题

开模技术输出1、常用的注塑模具钢有哪些?P20(美国)-618(瑞典)-3Cr2Mo(中国)- NAK-80(日本)预硬塑胶模具钢,一般要求大小塑胶模,适合PA、POM、PS、PE、PP、ABS 塑料。
718(瑞典)-P20+Ni(美国)-3Cr2Mo+ Ni(中国)-SNCM(日本)超级预硬塑胶模具钢,用于大型长寿命塑胶注塑模,如家电制品、电脑外壳等模具。
高表面光洁度的塑胶制品模具吹塑模由于硬度高,可用于塑胶模具中的滑块成型工具;视生产需要可施加火焰硬化或氮化处理的模具零件,718模具钢用途与P20类型模具钢材相同,但由于淬透性更好,性能更优越,可以制作尺寸大的、高档次的塑料模具成形零件,718H特硬。
H13(美国)-4Cr5MoSiV1(中国)-SKD61(日本)是热作模具钢,执行标准GB/T1299—2000。
;牌号4Cr5MoSiV1;合金工具钢简称合工钢,是在碳工钢的基础上加入合金元素而形成的钢种。
其中合工钢包括:量具刃具用钢、耐冲击工具用钢、冷作模具钢、热作模具钢、无磁模具钢、塑料模具钢。
H13模具钢用于制造冲击载荷大的锻模,热挤压模,精锻模;铝、铜及其合金压铸模。
2、什么是热流道和冷流道?冷流道:是指模具入口与产品浇口之间的部分。
塑料在流道内靠注塑压力和其本身的热量保持流动状态,流道作为成型物料的一部分,但并不属于产品。
所以在我们设计模具的时候既要考虑填充效果,又要考虑怎样通过缩短、缩小流道来节省材料,理想情况是这样,但实际应用中则很难达到两全其美。
热流道:作为注塑模具系统的一个常用部件,是通过加热的办法来保证流道和浇口的塑料保持熔融状态。
由于在流道附近或中心设有加热棒和加热圈,从注塑机喷嘴出口到浇口的整个流道都处于高温状态,使流道中的塑料保持熔融,停机后一般不需要打开流道取出凝料,再开机时只需加热流道到所需温度即可。
因此,热流道工艺有时称为热集流管系统,或者称为无流道模塑。
热流道系统的优点1、当产品的壁厚较薄时,确保熔体能充分到达远离浇口(进胶口)的部分,大大减小产品变形程度,大大提高产品表面质量及产品的一致性;2、流道内压力损耗小,熔体流动性好,密度容易均匀,避免注塑件变形、批峰以及尺寸不稳定和色差等缺陷;3、全部或大部分消除料把(水口料),不需人工剪切水口,无需再粉碎,提高物料的利用率,节约能源,提高了生产效率(常见的缩水、填充不足、熔接痕、颜色不均、飞边、翘曲现象也可以明显改善或消除);4、消除了废料带来的附加热量,模具的冷却周期仅为塑料的冷却时间,缩短了加工周期;5、热流道均为自动切断浇口,改善浇口外观,提高了自动化作业程度;6、精确控制熔体塑料温度,消除了材料的降解,使保压时间更合理,降低产品内应力。
注塑成型类产品常见不良分析案例

注塑成型不良的案例分析一、飞边(披锋)系指从模具分型面拼出熔融树脂的现象,在成形作业当中属于最恶劣的情况,特别是当飞边粘在模具面上,残留下来,直接锁模的话,则损伤模具分型面。
一旦出现这种情况,该损伤部分又会导致产生新的飞边,怎么也没办法,所以需特别注意不要出现飞边,1、不得施加过高的射出压力熔融粘度低的树脂,如尼龙、聚丙烯、聚乙烯、聚苯乙烯等,流动性好,往往从模具缝隙出现“边缘鼓出”现象,因此,不得施加过高的射出压力和保压压力。
当有出现飞边的倾向时,应尽早让保压转换用限位开关动作,减少计量。
降低射出压力。
另外,保压压力也有过高的时候,对于这些流动好的树脂,不要从一开始就施加高保压压力。
应边观察成形品的状况,边一点一点提高压力。
2、最初锁模力不足时,当然会产生飞边,不了解所用模具所需锁模力究竟有多大,就不可能作出断。
先利用锁模力调整手柄,增加锁模力试试看。
上图为在模具接触面(分型面)形成的飞边。
飞边主要是发生在分型面,但其它如在小顶杆周围、抽芯周围有时也出现飞边。
所谓纵向飞边,几乎均起因于模具精度不够。
象尼龙之类熔融粘度低的树脂,特别容易产生飞边,如聚碳酸酯之类粘度高的树脂则难于产生飞边。
以最大锁模力锁模,仍然出现飞边时,则应考虑是否是机械能力不足。
此时的判断方法是,当模腔内的压力乘以模腔、流道的投影面积所得的数值未超过机械是大锁模力的话,则不属于机械能力不足。
但需正确估计模腔内压力,然而不能把产品目录所列出的射出压力看作是模腔压力。
射出压力充其量是料筒内的理论压力,树脂流入模具,即被冷却,压力急剧下降。
平均压力从低粘度部件250kg/cm2到高粘度工业部件800kg/cm2左右,这种压力很难估计,虽然大体上有个基准,但要想保证估计精度,还需要凭经验。
3、在模具接触面产生了伤痕、夹有脏东西或是模具平行度差,当然会产生飞边,模具保管不善,则会使安装面打上伤痕,或是生锈,这样都会导致产生飞边。
所以应该养成习惯妥善保管模具。
注塑模具在生产中出现常见问题分析

注塑模具在生产中出现常见问题分析要针对目前成型品产生不良有原因加以分析判断,在成型机,模具及原料方面提供参考因素从而有效的控制不良的产生,降低生产成本。
内容:1 起疮:(银色条纹)成品表面,以CATE为中心,有很多银白色的条痕,基本上是顺着原料的流动方向产生。
这种现象是许多不良条件累积后发生的,有时要抓住真正的原因很困难。
1.1 原料中如果有水分或其他挥发成分,未充分烘干,则表面上就会产生很多银条。
1.2 原料中偶然混入其它原料时,也会形成起疮,其形状呈云母状或针点状,容易与其它原因造成的起疮分别。
1.3 原料或料管不清洁时,也容易发生这种情况。
1.4 射出时间长,初期射入到模穴内的原料温度低,固化的结果,使挥发成分不会排除,尤其对温度敏感的原料,发常会出现这种状况。
1.5 如果模温低,则原料固化快也容易发生(1。
4)之状况,使挥发成分不会排出除。
1.6 模具排气不良时,原料进入时气体不易排除,会产生起疮,像这种状况,成品顶部往往会烧黑。
1.7 模具上如果附着水分,则充填原料带来的热将其蒸发,与熔融的原料融合,形成起疮,呈蛋白色雾状。
1.8 胶道冷料窝有冷料或者小,射出时,冷却的原料带入模穴内,一部分会迅速固化形成薄层,刚开始生产时模温低也会开成起疮。
1.9 原料在充填过程中,因模穴面接触部分急冷形成薄层,又被后面的原料融化分解,形成白色或污痕状,多见於薄壳产品。
1.10 充填时,原料成乱流状能,使原料流径路线延长,并受模穴内结构的影响产生磨擦加之充填速度比原料冷却速度快,GATE位置处于筋骨处或者小容易产生起疮,成品肉厚急剧化的地方也容易产生起疮。
1.11 GATE以及流道小或变形,充填速度快,瞬间产生磨擦使温度急升造成原料分解。
1.12 原料中含有再生料,未充分烘干,射出时分解,则产生起疮。
1.13 原料在料管中停留时间久,造成部分过热分解。
1.14 背压不足,卷入空气(压缩比不足)。
起疮:表一成型机可塑化能力不足。
注塑模具常见问题解决方案

模具加工前对设计图做倒扣、干涉全局检查,对强脱类产品倒扣大小,论证其 可行性分析 TPE、TPU等软胶类产品前模需要做粗纹路,防止注塑过程产生真空而粘模。
深腔、深筋位、孔柱位等容易粘模部位加强EP的布置、特殊部位顶针做延时。
侧向抽芯(滑块、斜顶)大面积的深腔或孔位包胶考虑2次抽芯或者延时抽芯
模具圆弧曲面类分型面加工不到 圆弧曲面类分型面,前、后模距封胶位15-20mm以外做避空。利于CNC加工保
位,采用手工打磨
证精度,减少手工打磨工艺。
模具型腔加工超差
模芯加工完后需要用3次元、投影仪设备进行尺寸检测。
模具结构设计不合理
对半出前、后模的胶位,为防止产品出现逆断差,产品外形周圈将后模比前模做 小0.05-0.1,内部碰穿孔位后模比前模做大0.05,具体可视产品工艺要求进行调整。
模具注塑受力不平衡,偏载
模胚增加直身或者斜度定位锁。
产品周圈分型面和熔胶未端需要加强排气、深筋、深柱超过6-8mm以上需要做 排气镶件。 加大虎口定位面积、模胚增加直身或者斜度定位锁。
模板强度不够,支撑柱太少
模板根据开框深度和模具大小适当加大板的厚度,中小型模具框底部厚度一般取 30-60左右,唧嘴附近、胶位区域因注塑压力相对较大,撑头布置尽量多。
侧向抽芯(滑块、斜顶)大面积的深腔或孔位包胶考虑2次抽芯或者延时抽芯
圆筒、深腔类产品、深筋位、孔柱位视情况做后模先抽、推板或者2次顶出。
2.批峰 断差
原因分析
解决对策
模具碰穿、插穿面尺寸精度超差 碰穿面与插穿面,公模面负公差控制-0.015-0mm;母模面正公差控制+0.015-0
模导向定位精度不够 模具排气不良
注塑模具各类问题原因分析及解决办法
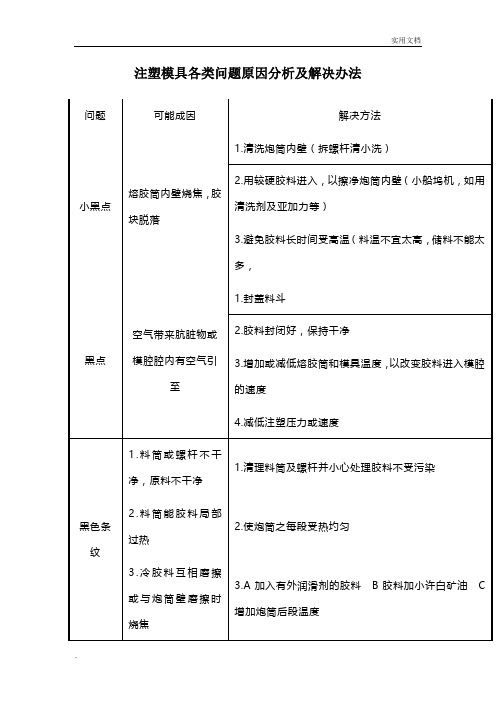
注塑模具各类问题原因分析及解决办法1注塑件收缩凹陷的原因分析注塑成型过程中,制品收缩凹陷是比较常见的现象。
造成这种情况的主要原因有:机台方面(1)射嘴孔太大造成融料回流而出现收缩,太小时阻力大料量不足出现收缩。
(2)锁模力不足造成飞边也会出现收缩,应检查锁模系统是否有问题。
(3)塑化量不足应选用塑化量大的机台,检查螺杆与料筒是否磨损。
模具方面(1)制件设计要使壁厚均匀,保证收缩一致。
(2)模具的冷却、加温系统要保证各部份的温度一致。
(3)浇注系统要保证通畅,阻力不能过大,如主流道、分流道、浇口的尺寸要适当,光洁度要足够,过渡区要圆弧过渡。
(4)对薄件应提高温度,保证料流畅顺,对厚壁制件应降低模温。
(5)浇口要对称开设,尽量开设在制件厚壁部位,应增加冷料井容积。
塑料方面结晶性的塑料比非结晶性塑料收缩历害,加工时要适当增加料量,或在塑料中加成换剂,以加快结晶,减少收缩凹陷。
加工方面(1)料筒温度过高,容积变化大,特别是前炉温度,对流动性差的塑料应适当提高温度、保证畅顺。
(2)注射压力、速度、背压过低、注射时间过短,使料量或密度不足而收缩压力、速度、背压过大、时间过长造成飞边而出现收缩。
(3)加料量即缓冲垫过大时消耗注射压力,过小时,料量不足。
(4)对于不要求精度的制件,在注射保压完毕,外层基本冷凝硬化而夹心部份尚柔软又能顶出的制件,及早出模,让其在空气或热水中缓慢冷却,可以使收缩凹陷平缓而不那么显眼又不影响使用。
2注塑件震纹的原因分析PS等刚性塑料制件在其浇口附近的表面,以浇口为中心的形成密集的波纹,有时称为震纹。
产生原因是熔体粘度过大而以滞流形式充模时,前端的料一接触到型腔表面便很快冷凝收缩起来,而后来的熔料又胀开已收缩的冷料继续前进过程的不断交替使料流在前进中形成了表面震纹。
解决办法(1)提高料筒温度特别是射嘴温度,还应提高模具温度。
(2)提高注射压力与速度,使其快速充模型腔。
(3)改善流道、浇口尺寸,防止阻力过大。
注塑机加工模具常见问题及解决办法
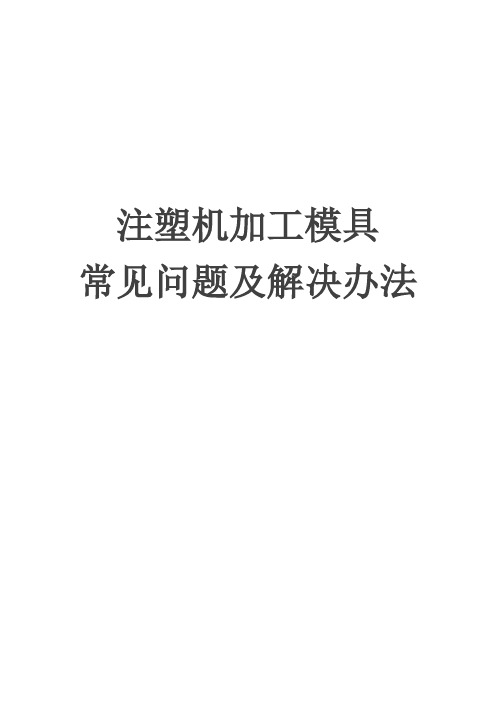
注塑机加工模具常见问题及解决办法问题一:塑胶呈波浪原因:因浇口或其它部分狭窄,熔态塑料推动固化塑件前移时,表面产生波纹。
解决方法:1.增加注直径2.提高注咀及模具温度3.提高料筒高度4.加快注塑速度5.减慢注料速度6.更改模具冷却水进口位,使其远离浇口7.扩大浇口。
问题二::塑件呈银纹形原因:因塑料含水份,混料不均匀,注塑时夹气,添加剂或脱模剂过多。
解决方法:1.加强回压2.减慢注速3.清理料筒4.提高模温5.改浇口位置6.扩大流道及浇口7.烘料8.料门中安装红外线灯。
问题三:塑胶接口不良原因:因塑料温度太低,不能熔化,或因气体排泄不足导致两股以上分流混合而产生发状细线或气泡。
解决方法:1.提高料温2.提高注温3.增加注速4.接缝线外设冷料池5.设放气口6.改变浇口位或浇口7.不要用脱模剂8.转用易流动的低粘度类原料。
问题四:塑件呈现空洞原因:因塑料在熔料固化期间表面接触低温模壁,收缩集中于厚壁段而造成空洞,或因夹气做成空洞。
解决方法:1.提高注压(及二次压力)2.延长注时3.降低料筒固化温度4.消减模壁厚度至6mm以下,必要时设置等壁厚助线,及去除多余壁厚5.扩大浇口6.缩短流道7.调匀模温8.更改浇口位置,排除夹气。
问题五:塑件欠注或缺料原因:因机械注塑及塑化性能不足,料流不良,浇口截面太细,模壁太薄或泄气不良。
解决方法:1.增加注料速率,如仍不足,则需换重型机械2.装防漏注阀式螺杆3.提高注压4.提高料筒、注咀固化及模具温度5.查电热线是否断线6.查注咀是否堵塞,增加循环速度7.提高模具放气能力8.加大浇口截面9.增加产品壁厚10.加设助线,改造料流11.选用低粘度原料12.加润滑剂。
问题六:合模边挤出塑料原因:因料温及注压过高,或锁模力不足。
解决方法:1.降低注压及筒固化温度2.缩短注时3.减少注料速度4.改用高锁模力机5.改造合模表面紧配合及清理合模表面6.转用低粘度料。
问题七:塑件表面呈凹痕原因:因塑件表面误时冷却,因其表面凹痕。
- 1、下载文档前请自行甄别文档内容的完整性,平台不提供额外的编辑、内容补充、找答案等附加服务。
- 2、"仅部分预览"的文档,不可在线预览部分如存在完整性等问题,可反馈申请退款(可完整预览的文档不适用该条件!)。
- 3、如文档侵犯您的权益,请联系客服反馈,我们会尽快为您处理(人工客服工作时间:9:00-18:30)。
注塑模具中常见39大问题的实例讲解
时间:2011-12-18 作者:模具联盟网点击: 3442 评论: 0 字体:T|T
刚开机时产品跑披锋,生产一段时间后产品缺胶的原因及解决方案。
1. 刚开机时注塑机料管内的熔胶由于加热时间长,熔胶粘度低,流动性好,产品易跑披锋,生产一段时间后由于熔胶不断把热量带走,造成熔胶不足,粘度大,流动性差,使产品缺胶。
在生产一段时间后,逐渐提高料管温度来解决。
2.在生产过程中,产品缺胶,有时增大射胶压力和速度都无效,为什么?解决方法?
是因为生产中熔胶不断把热量带走,造成熔胶不足,胶粘度大,流动性差,使产品缺胶。
提高料管温度来解决。
3.产品椭圆的原因及解决方法。
产品椭圆是由于入胶不均匀,造成产品四周压力不匀,使产品椭圆,采用三点入胶,使产品入胶均匀。
4.精密产品对模具的要求。
要求模具材料刚性好,弹变形小,热涨性系数小。
5.产品耐酸试验的目的
产品耐酸试验是为了检测产品内应力,和内应力着力点位置,以便消除产品内应力。
6.产品中金属镶件受力易开裂的原因及解决方法。
产品中放镶件,在啤塑时由于热熔胶遇到冷镶件,会形成内应力,使产品强度下降,易开裂。
在生产时,对镶件进行预热处理。
7.模具排气点的合理性与选择方法。
模具排气点不合理,非但起不到排气效果,反而会造成产品变形或尺寸变化,所以模具排气点要合理。
选择模具排气点,应在产品最后走满胶的地方和产品困气烧的地方开排气。
8.产品易脆裂的原因及解决方法。
产品易脆裂是产品使用水口料和次料太多造成产品易脆裂,或是料在料管内停留时间过长,造成胶料老化,使产品易脆裂。
增加新料的比例,减少水口料回收使用次数,一般不能超过三次,避免胶料在料管内长时间停留。
9.加玻纤产品易出现泛纤的原因及解决方法
是由于熔胶温度低或模具温度低,射胶压力不足,造成玻纤在胶内不能与塑胶很好的结合,使纤泛出。
加高熔胶温度,模具温度,增大射胶压力。
10.进料口温度对产品的影响。
进料口温度的过高或过低,都会造成机器回料不稳定,使加料量不稳定,而影响产品的尺寸和外观。
11.透明产品有白点的原因及解决方法。
透明产品有白点是因为产品内进入冷胶造成,或料内有灰尘造成的。
提高射嘴温度,加冷料井,原料注意保存,防止灰尘进入。
12.什么是注塑机的射出能力?
射出能力※※=射出压力(kg/cm2)×射出容积(cm3)/1000
13.什么是注塑机的射出马力?
射出马力PW(KW)=射出压力(kg/cm2)×射出率(cm3/sec)×9.8×100%
刚开机时产品跑披锋,生产一段时间后产品缺胶的原因及解决方案。
刚开机时注塑机料管内的熔胶由于加热时间长,熔胶粘度低,流动性好,产品易跑披锋,生产一段时间后由于熔胶不断把热量带走,造成熔胶不足,粘度大,流动性差,使产品缺胶。
在生产一段时间后,逐渐提高料管温度来解决。
14.球面丝印后开裂问题.
由于产品表面存在应力,造成丝印后开裂.增加模具温度,减小应力;可用退火的方法消除应力.
15.眼镜架,水口边易断问题.
射胶压力和保压压力大,水口边残存内应力,造成产品易断.尽量减小射胶压力和保压压力,适当提高模具温度来解决.
16.电器外壳,四个装配柱子,打螺丝时爆裂问题.
由于柱子存在夹水线,造成产品装配柱子易暴裂.模具增加排气,适当提高模温,加快射胶速度来减小夹水线.
17.产品变形问题.
产品变形主要是热收缩时不平衡造成产品变形,或由于产品本身内应力作用下使产品变形.
18.透明PC外壳气泡问题。
原料干燥不够;产品存在胶厚薄不均现象,模具排气不良,原料易分解都可能造成产品气泡.
充分干燥原料,增大模具排气,尽量减少胶厚薄不均现象.
19.复印机,磁性材料的啤塑问题。
应采用高模温,快速射胶方法.
20.产品包胶,水口边缩水问题。
模具排气不良,射胶速度慢,保压压力和时间不够,都能造成水口缩水。
增大模具排气,适当提高射胶速度,增加保压压力和时间.
21.产品内应力,造成产品放置一段时间后爆裂问题。
由于产品内残存应力,产品放置一段时间后由于应力的作用,使产品爆裂.
提高啤塑时的模具温度,降低射胶压力,来消除产品应力,产品可用退火的方法消除应力.
22.ABS料在用黑色色母时,造成产品易断裂脱皮问题。
是色母的颜料中用了碳粉过多原因,造成产品脱皮.更换色母颜料.
23.一台180吨14安士机,产品一出四CD盒共120克,外观良好,无批峰,但其中一只重2克,为什么?
模具产品一出四,由于模具进胶不平衡造成其中一只产品啤塑饱满,密度大,出现重2克现象.
24.一台100吨液压曲肘机使用了三年,模具锁紧后,经常打不开。
是由于机器曲肘磨损,造成开模不平衡,所以模具锁紧后,会经常打不开.
25.一台7安士机使用了二年,出现射胶不稳定,一啤批峰一啤缺胶,换过油封和分胶头,系统压力也稳定,就不行。
由于螺杆磨损或损坏,造成回料不匀,所以会出现射胶不稳定.
26.一台150吨新机啤PP水口料半年,原来熔胶最快3秒,而现在要6秒。
由于螺杆磨损,造成回料慢.
27.一啤塑师父在调试一产品,出现缺胶,速度或压力升一点,产品没反应,再升一点就出批峰?
机器锁模机构磨损,造成锁模有间隙,所以会出现披锋.
28.一台机用了二年,啤货时炮筒中间温度偏高,关了电源也没用。
由于螺杆磨损变得粗糙,啤塑回料时磨擦产生热,使炮筒中间温度偏高.
某厂有新旧机十几台,油封经常漏油,换了一段时间又漏?
油温过高使油封易老化损坏,漏油;油缸芯子磨损,造成刮坏油封漏油.
问题18-23请见教材二《注塑机维护保养》相关图解。
29.油泵电机起动电路的讲解。
油泵电机起动是采用星三角起动
30.省电泵原理讲解。
省电泵即为变流量泵,当机器有动作时,压力油通过油阀油缸推动机械动作,再回到油箱,当机器没有动作时,压力油直接回到油箱。
31.电子线路板输入与输出的讲解。
由各个动作感应开关和电子尺等信号输入电子版,电脑通过运算后再输出给油阀,执行动作。
32.略
33.油封顽固性漏油的原因及预防。
油缸芯子磨损刮坏油封,造成顽固性漏油,保持油缸芯子干净,避免磨损预防刮坏油封造成漏油。
34.压力与流量线性对注塑工艺的影响。
压力与流量线性成比例,对注塑工艺的参数准确和稳定有着重要意义。
35.生产周期变慢的原因及改善措施。
生产周期变慢的原因主要是冷却时间延长,和螺杆因磨损使回料时间加长。
改善模具冷却效果,缩短冷却时间,更换磨损的螺杆,使回料时间缩短,加快生产周期。
36.熔胶时发出尖叫声的原因与处理方案。
熔胶时发出尖叫声是由于螺杆与料磨擦发出的或螺杆与炮筒磨擦发出的。
对螺杆抛光处理或电镀,使表面光滑减小磨擦;调整螺杆的中心度使它不与炮筒发生磨擦。
37.锁模平行度的检测与调整方法。
用四个百分表测定机器锁模时哥林柱的拉伸长度,看是否在允许公差内,来检测哥林柱锁模平等度。
然后调整哥林柱大螺母来调整锁模平行度。
38.哥林柱折断的原因与预防措施。
哥林柱折断的原因是由于锁模不平等造成的。
调整锁模平行度来预防哥林柱折断。
39.曲肘磨损的原因分析。
曲肘磨损的原因是,曲肘润滑不良造成的。