TPM全员设备管理讲义
(TPM)设备管理培训资料

设备管理基本原则
• 设备管理基本原则:坚持安全第一、预防为主的原则;坚持设 计、制造与使用相结合的原则;坚持维护与计划检修相结合的 原则;坚持专业管理与群众管理相结合的原则;坚持技术管理 与经济管理相结合的原则。
02 设备前期管理
设备规划与选型
01
02
03
明确设备需求
根据企业生产需求、工艺 流程、产能要求等因素, 确定所需设备的类型、规 格和数量。
报废条件
设备达到或超过规定的使用年限 、技术性能落后、能耗高、效率 低、无修复价值或修复费用过高
等。
报废程序
由使用部门提出申请,经过技术鉴 定、价值评估、审批等程序后办理 报废手续。
报废设备处理
对报废设备进行拆解、回收、处置 等处理,确保处理过程符合环保和 安全要求。
设备资产清查与评估方法
清查目的
建立供应商评价体系,从质量、价格、交货期、 服务等方面综合评价并选择合适的供应商。
采购成本控制
通过集中采购、长期协议、价格谈判等方式,降 低采购成本,提高采购效益。
备件使用与消耗控制
01
备件领用管理
建立备件领用审批流程,确保按 需领用,避免浪费和滥用。
03
备件修复与再利用
对于可修复的备件,积极组织修 复并再利用,降低备件消耗和采
操作规程执行监督
定期检查设备操作人员遵守操作规程 的情况,及时纠正违规行为。
操作规程培训
对设备操作人员进行培训,确保熟练 掌握操作规程。
设备点检制度实施
制定设备点检标准
明确点检部位、点检方法、点检周期等。
点检实施与记录
按照点检计划进行设备点检,并记录点检结 果。
点检计划制定
根据设备点检标准,制定设备点检计划。
全面设备管理TPM培训资料

全面设备管理tpm培训资料pptxx年xx月xx日contents •设备管理tpm概述•设备管理tpm的核心概念•设备管理tpm的实操指南•设备管理tpm的成功案例•设备管理tpm的未来趋势与挑战•总结与展望目录01设备管理tpm概述设备管理TPM(Total Productive Maintenance,全面生产维护)是一种以提高设备综合效率为目标,以全系统的预防维修为过程,以全体人员参与为基础的设备保养和维修管理体系。
TPM是一种科学、高效的设备维护管理方法,旨在通过全员参与,消除设备故障,提高设备效率,降低维修费用,提高企业生产效益。
设备管理tpm的定义1设备管理tpm的重要性23TPM通过对设备的全面维护和保养,减少设备故障,提高设备运行效率,从而提高企业的生产效率和产品质量。
提高设备利用率TPM强调预防性维修,通过早期发现和及时处理设备故障,有效降低维修成本和停机时间。
降低维修成本TPM要求员工全员参与,通过培训和实践提高员工的设备管理和维修技能,增强员工的综合素质。
提高员工素质03TPM现状目前,TPM已经成为众多企业所推崇的设备维护管理模式,广泛应用于制造业、服务业等领域。
设备管理tpm的历史与发展01TPM起源TPM起源于20世纪60年代的日本企业,最初是为了解决设备故障率高、维护困难等问题而提出的。
02TPM发展随着TPM实践的不断深入和应用范围的扩大,TPM逐渐发展成为一种全球性的设备维护管理标准。
02设备管理tpm的核心概念1设备综合效率23设备综合效率是衡量设备性能的重要指标,它反映了设备的有效利用程度和生产效率。
通过对设备综合效率的计算和分析,可以找出设备存在的问题和瓶颈,从而采取针对性的改进措施。
提高设备综合效率的关键在于优化设备配置、改善设备性能、加强设备维护保养等。
设备的全员参与01设备的全员参与是TPM(Total Productive Maintenance,全面生产维护)的核心思想之一,它强调所有员工都参与到设备管理中来。
TPM-全员设备管理与维护(共68张PPT)
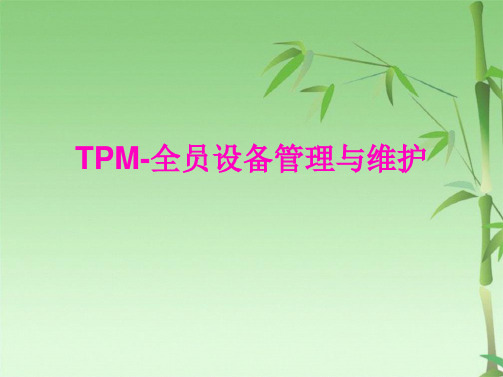
零速度损失
指计划外的设备停 机时间为零。计划
外的停机对生产造成 冲击相当大,使整个 生产品配发生困难, 造成资源闲置等浪费。 计划时间要有一个合 理值,不能为了满足 非计划停机为零而使 计划停机时间值达到 很高。
指由设备原因造
成的废品为零。 “完美的质量需 要完善的机器”, 机器是保证产品 质量的关键,而 人是保证机器好 坏的关键。
挑战比PM奖的受奖 更高的目标
●3年计划
●年度、季度的活动计划,
月度时间表
日本评审PM奖的标准是:
时间开动率≥90%;性能开动率≥95%
合格品率≥99%; 设备综合效率(OEE)≥85%
如何推行TPM
TPM-全面生产维护的规范化
TPM规范化的范畴
1、维修程序规范化
2、备件管理规范化
3、前期管理规范化 4、维修模式规范化
阶段
水平提高
要点
追求生产效率化的极限
PROJECT TEAM 活动
工作岗位小集团活动
STEP 方式, 诊断和合格证
改良保养,计划保养,预防保养
领导的集合教育
成员的传达教育
开发容易制造的制品
开发容易使用的设备
非发生不良的
条件设定和维持管理 生产支援,本部属的效率化
和设备的效率化
构筑灾害 ZERO, 公害ZERO体制
日本中岛清一的TPM的五要素:
◆TPM致力于设备综合效率最大化的目标; ◆TPM在整个设备一生中建立彻底的预防维修体制
◆TPM由各部门共同推行(包括设备的计划、使用操作、维修部门)
◆TPM涉及每个员工,从高层经理(总经理)到现场工人
◆TPM通过动机管理,即通过自主的小组活动使PM体制得到推动。
设备管理与TPM讲座(50页)课件
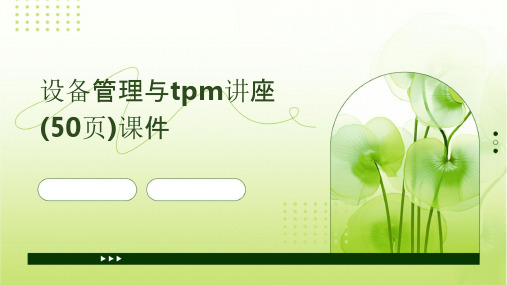
明确设备管理部门和生产使用部门各自的责任。
• 全员
要求从企业最高领导到第一线生产工人都参加设备管理。
Q&A环节 关于设备管理与TPM的常见问题解答
• 全过程:对设备的整个寿命周期进行管理,强调 对设备一生进行管理,并侧重于对设备的维修和 改善。
Q&A环节 关于设备管理与TPM的常见问题解答
TPM的核心理念
TPM强调预防性维护、全员参与和持续改进。它要求企业全 体员工参与到设备维护中,通过有效的设备管理,降低设备 故障率,提高生产效率和产品质量。
TPM的目标与实施步骤
TPM的目标
提高设备综合效率(OEE),降低维 护成本,提高生产效率,减少故障停 机时间。
TPM的实施步骤
1. 初期清扫与零故障目标设定;2. 自 主维护实施;3. 专业保全维修实施;4. 计划保全周期设定及优化;5. 监控与 评估。
设备管理在绿色制造中的作用
在绿色制造中,设备管理需要关注设备的能耗、排放和资源消耗等方面,通过优化设备运 行和维护,降低生产过程中的能耗和排放,提高资源利用效率。
绿色制造与设备管理的融合
绿色制造需要设备管理的绿色化支持,同时设备管理的绿色化也需要绿色制造的推动,两 者相互促进,共同推动制造业的绿色化发展。
TPM与其他设备管理方法的比较
TPM与传统的设备维护管理方法的比较
传统的方法通常更侧重于事后维修和应急维修,而TPM则强调预防性维护和全员 参与,通过减少设备故障和提高设备综合效率来提高生产效益。
TPM与其他设备管理策略的比较
与可靠性为中心的维护(RCM)、全面质量管理(TQM)等其他设备管理策略 相比,TPM更侧重于设备的全面维护和保养,而其他策略可能更侧重于其他方面 如质量管理和可靠性等。
TPM全员设备维护与管理培训讲义

TPM全员设备维护与管理培训讲义1. 简介TPM(全员设备维护与管理)是一种通过维护设备的可靠性和精度来提高生产效率的管理方法。
本文档将介绍TPM的基本概念、操作流程以及培训内容,帮助全员了解和实施TPM。
2. TPM的基本概念TPM是Total Productive Maintenance的缩写,意为全员设备维护与管理。
它的目标是通过消除设备故障和减少生产中的没有价值的时间来提高设备的效率和可用性。
TPM的四大支柱是: - 预防性维护:通过定期检查设备、更换易损件等措施来预防设备故障。
- 细节管理:对设备进行巡检,保持设备的整洁、有序和易于操作。
- 故障隐患消除:对设备故障进行分析,找出根本原因并采取措施消除。
- 提高维护技术:提高维护人员的技能和知识,以更好地管理和维护设备。
3. TPM的操作流程TPM的操作流程包括以下几个步骤:步骤一:设备规划•制定设备的维护计划和目标。
•对设备进行分类和评估,确定关键设备和重点改善项目。
步骤二:故障分析和消除•对设备故障进行分析,找出根本原因。
•制定故障预防计划,采取措施消除故障隐患。
步骤三:维护活动•制定设备的维护计划和标准操作规程。
•进行定期检查、润滑和更换易损件等维护活动。
•培训维护人员,提高其技术和知识水平。
步骤四:细节管理•建立设备巡检和保养记录。
•维护设备的整洁、有序和易于操作。
•采取措施预防设备的污染和损坏。
步骤五:持续改善•回顾和评估设备的维护情况。
•制定改善计划,提高设备的可靠性和精度。
4. TPM的培训内容TPM的培训内容主要包括以下方面:设备维护基础知识•设备类型和分类•设备故障的原因和分类•维护活动和标准操作规程设备的巡检和保养•设备巡检的方法和步骤•设备保养的方法和步骤•巡检和保养记录的管理和分析故障预防和消除•故障分析的方法和步骤•故障预防计划的制定和执行•故障消除的措施和方法维护人员的培训和管理•维护人员的岗位职责和要求•维护人员的技术和知识培训•维护人员的绩效评估和激励措施TPM的实施和改善•TPM的操作流程和步骤•TPM的评估和改善方法•TPM与其他管理方法的整合5. 总结TPM是一种通过维护设备的可靠性和精度来提高生产效率的管理方法。
TPM设备管理理论

Industry
二、TPM全员设备管理
3.TPM全员设备管理所要达到的目标
TPM的目标可以概括为四个“零”,即停机为零、废品为零、事故为零、 速度损失为零。
停机为零:指计划外的设备停机时间为零。计划外的停机对生产造成冲击 相当大,使整个生产品配发生困难,造成资源闲置等浪费。计划时间要有一个 合理值,不能为了满足非计划停机为零而使计划停机时间值达到很高。
可编辑课件
Industry
二、TPM全员设备管理
1.1设备的5种维护方式 ①事后维修----BM(Breakdown Maintenance) 这是最早期 的维修方式,即出了故障再修,不坏不修。 ②预防维护--PM(Preventive Maintenance) 这是以检 查为基础的维修,利用状态监测和故障诊断技术对设备进行预测, 有针对性地对故障隐患加以排除,从而避免和减少停机损失,分定 期维修和预知维修两种方式。 ③改善维护--CM(Corrective Maintenance) 改善维修是 不断地利用先进的工艺方法和技术,改正设备的某些缺陷和先天不 足,提高设备的先进性、可靠性及维修性,提高设备的利用率。
可编辑课件
Industry
二、TPM全员设备管理
1.1设备的5种维护方式 ④维护预防--MP(Maintenance Prevention) 维修预防 实际就是可维修性设计,提倡在设计阶段就认真考虑设备的可靠性 和维修性问题。 从设计、生产上提高设备品质,从根本上防止故障 和事故的发生,减少和避免维修。 ⑤生产维护--PM(Productive Maintenance) 是一种以 生产为中心,为生产服务的一种维修体制。它包含了以上四种维修 方式的具体内容。对不重要的设备仍然实行事后维修,对重要设备 则实行预防维修,同时在修理中对设备进行改善维修,设备选型或 自行开发设备时则注重设备的维修性(维修预防)。
TPM基础知识培训讲义

TPM基础知识培训讲义第一部分:概述TPM(Total Productive Maintenance)全面生产力维护,是一种由日本发展起来的生产管理理论。
TPM的目标是通过减少故障和损失、提高生产效率,实现全面优化的生产过程。
本讲义将带您深入了解TPM 的基础知识,包括TPM的起源、原则和关键要素。
第二部分:TPM的起源1. 日本制造业的发展日本制造业在20世纪六七十年代快速崛起,成为世界制造业的领导者。
然而,由于设备故障频繁和停机时间长,制约了生产效率的提高。
在这样的背景下,TPM理论逐渐兴起。
2. JIPM(日本生产维护协会)JIPM成立于1961年,致力于推广TPM理念。
JIPM制定了TPM 的基本原则和实施步骤,并提供了培训和认证服务。
第三部分:TPM的原则1. 全员参与TPM的实施需要全员参与,从高层管理者到一线员工,每个人都要对设备维护和生产过程负责。
2. 设备维护活动的全面优化TPM强调预防性维护,通过定期保养、润滑和清洁,及时排除设备故障的隐患,延长设备寿命。
3. 生产活动的全面优化TPM要求对生产活动进行全面优化,包括减少生产过程中产生的损失,提高生产效率。
第四部分:TPM的关键要素1. 自主维护自主维护是指由操作员负责执行设备保养和维修工作,提高设备的可靠性和稳定性。
2. 预防性维护预防性维护是指通过定期检查和保养设备,预防设备故障的发生以及提前排除隐患。
3. 故障排除TPM要求快速排除设备故障,并进行彻底分析,找出故障的根本原因,以避免类似问题再次发生。
4. 整备率提高整备率是指设备可用于生产的时间占总时间的比例。
TPM通过减少停机时间和改进维修流程,提高整备率。
5. 生产效能改善TPM通过优化生产活动,消除浪费,提高生产效率和质量。
第五部分:TPM实施步骤1. 制定实施计划开展TPM之前,制定详细的实施计划,确定实施的范围、目标和时间计划。
2. 进行设备基础改善通过改进设备的基础条件,包括设备的可靠性、可维护性和操作性,为后续的活动做好准备。
TPM培训讲义课件142张

• 只要我们坚持做下去,我们也敢于象日本人那样,追求并 期待“零”目标的实现。
第二部分:TPM活动内容
一、自主保全
(一)、什么是自主保全
第一部分:认识TPM
一、什么是TPM
TPM即全员效率维修(Total Productive Maintenance)。 定义:
以最有效的设备利用为目标,以维修预防、预防维 修、改善维修和事后维修综合构成生产维修为总运行体 制,由设备的全程管理部门、使用、维修等所有有关人 员,从最高经营管理者到第一线作业人员全体参与,以 自主的小组活动来推行生产维修,使损失最小化,效益 最大化的活动。 要点:效率最大化、全员参与
自主保全活动就是以操作人员为主,对设备和装置 依据特定的标准,凭五官进行外表层面的检查。通过一 定的教育训练,使之自主开展清扫、点检、加油、紧固 等设备保全活动,及进一步能对微小的故障做简单的修 理和改善。
我们可以尝试开展如下活动: 1)保养(清扫):对设备工作环境进行清洁和整顿。 2)点检:对设备基本工作环境、外部条件、外观等 进行检查。
备等。 个别改善:针对设备缺陷展开的改善活动。 品质保全:通过设备维修活动改善和提高产品品质的活动。 设备前期管理:即从方案规划、采购到投入服役的全程管理。 教育训练:技术及管理培训,不断提高员工技术技能。 安全与卫生:人员操作安全与环境卫生标准。使人机处于良好工
作状态。 间接部门效率化:提高间接业务部门关联业务效率。
四、 TPM的内容
企业经营效率化
核心是全员参与,预防为主 零故障、零灾害、零不良、……零损失
TPM全员生产性维护培训讲义

TPM
TPM的发展史
1951年,美国提出了PM,日本企 业在PM基础上,经改良后,形成 了现在的TPM理论。它以与生产密 切相关的设备为切入点,通过设备, 工作环境的改善来改善人的看法, 想法,进而改善企业的体制。
TPM
TPM的发展史
50年代进行事后保全 60年代进行预防保全 70年代进行全员保全
废品/返工
准备时间
Breakdowns 16%
停机
M in o r
S t g T im e (O .E .E .) 40%
运行时间
World-Class OEE Measurements
Same equipment, 112% more capacity
重点实施事项 在全员中深入 积极开展
保全部门协力 解决发现的问 题,并简化保 全活动 记录点检结果, 并进行对策处 理
针对问题点迅 速进行改善
紧密团结,制 定目标及指标, 激动灵活地解 决问题 实施保全教育, 提高技能,积 极扩展自主保 全活动 适时审视点检 项目、基准及 要领书,并做 适当修正 推测故障点, 为降低MTTR而 实施改善
按时间计算生产量 每人的生产量 设备综合效率
备品的在库金额,在库天数的统计与管理
区分
保全作业
设备故障
保全性 人才育成
TPM目标项
项目
计划保全率 计划保全的达成率 改良设备的件数 突发设备故障的及件数 长时间设备停止的件数 关键设备的平均故障间隔 平均维修时间 个人技能的评价 取得某一资格的人数
TPM
以前一年度的实际情况为基础设定目标 以公司内同类工序的实际为基础设定目标
以同行业好的对手为基础设定目标
区分
安全 品质
TPM--全员生产运作管理

培养理解设备构造, 并能正确点检的能力 工序正确的操作方法, 处理异常的能力 管理4M和品质原因 系的能力 构筑设备及现场管理 的免疫体质
达到理解设备的机能及构造,理解作 用点加工点的水平。 理解工序的性能、调整方法、发生异 常时的对策方法,提高操作可靠性 明确理解设备和品质的关系,在不良 发生之前解决问题 1 ~ 6 STEP的体制化,习惯化
TPM活动的3要素 TPM活动的3 活动的
-板(现况板、活动板、信息传递窗)-硬件软件的方法论 硬件软件的方法论 -物(现场、现物、现象)-实事求是的三现主义 实事求是的三现主义 -人(从工人到最高经营者)-以人为本的三者主义 以人为本的三者主义
预防保全 延长寿命
TPM适合制造类企业 TPM适合制造类企业
集团开展TPM的意义 集团开展TPM的意义 TPM
1. 以构筑企业组织结构,追求最大限度提高经营系统效率为目标。 。 LC全体为对象,确立预防 “灾害、故障、不良”等浪费的体制。 2. 以生产体系的LC LC 。 3. 包括生产、开发、管理等所有部门。 。 总裁到第一线工作人员的全体员工参加。 4. 从总裁 总裁 。 5. 依靠重复小组的活动达到浪费为0。 0 集团展开 TPM 生产保全 预防保全
日期 公司名 时间 08:10-08:40 09:00-10:00 10:00-12:00 12:00-13:00 月 日 13:00-13:30 13:30-16:00 16:00-16:30 16:30-17:00 17:00-18:00 内容 出发(酒店公司) 备注 车接
,共
人左右
与总经理面谈了解公司情况,发放问卷 现场诊断 午餐 问卷整理 发表资料整理 发表诊断结果及答疑 与总经理面谈 返回( 公司 - 酒店) 车送 中层以上干部参加
设备保全TPM讲义ppt课件

三 生产维修体制
生产维修体制:是以生产为中心,为生产服务的一种维修 体制,由以下四种维修方式构成:
预防维护:以预防为主,其出发点是防患于未然,减少故 障和事故,减少停机损失,提高生产效益。 预防维护工作包含的工作有:
除尘和去除其他不洁物 除潮 散热 定期检查电气 定期检查润滑情况 机械调节与更换 采用巡检的方法判断设备的工作状态
设备保全TPM讲义
TPM的发展
一 事后维修
事后维修(BM):日本在战后经济陷入瘫痪,设备破旧 故障多,维修费用高,生产恢复缓慢。
二 预防维修
预防维修(PM):是建立在摩擦学基础上,以预防为 主的维修体制,其出发点是改变原有的事后维修做法, 防患于未然,减少故障和事故,减少停机损失,提高 生产效益。
1.提高(操作,工作)技能 2.改进(工作,精神)面貌 3.改善(企业,运行)环境
TPM推动实作顺序
TPM推进进程分:准备阶段;开始阶段;实施推进阶段; 巩固阶段。 准备阶段:
领导层宣布引进TPM的决心; TPM引进宣传和人员培训; 建立TPM推进机构; 制定TPM基本方针和目标; 制定TPM推进计划;
初 期 管 理
教 育 培 训
品 质 保 全
管 理 部 门 效 率 化
安 全 卫 生 环 境
5
S
自主维修:自己操作的机器设备,自己实施基本的保全 动作。 目的: 让操作者意识到保全的重要性; 提升操作者对设备的关心度; 让操作者的劳动生产力增加; 提升设备的可靠能力; 让操作者具有早期发觉设备异常的能力。
“0”目标 (Zero Defect) -与同行的水平无关 如果追求“0”的目标 在竞争中一定会胜利 -如果同行也追求“0” 那么速度是胜败的关键
5.1TPM-全面生产设备与全员维护-台湾赵智平老师讲解
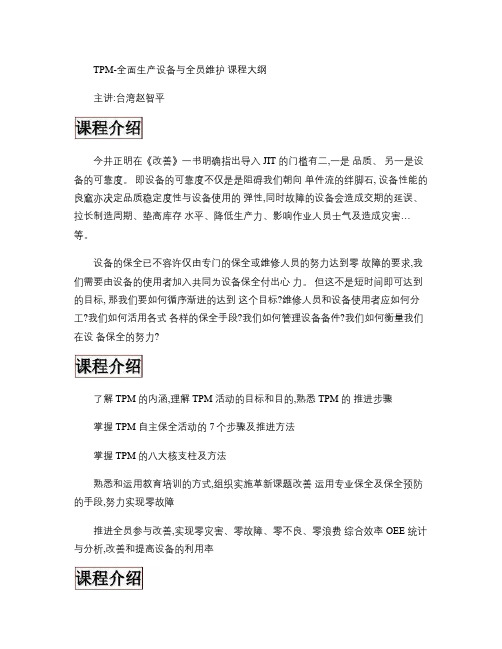
TPM-全面生产设备与全员维护课程大纲主讲:台湾赵智平今井正明在《改善》一书明确指出导入 JIT 的门槛有二,一是品质、另一是设备的可靠度。
即设备的可靠度不仅是是阻碍我们朝向单件流的绊脚石, 设备性能的良窳亦决定品质稳定度性与设备使用的弹性,同时故障的设备会造成交期的延误、拉长制造周期、垫高库存水平、降低生产力、影响作业人员士气及造成灾害…等。
设备的保全已不容许仅由专门的保全或维修人员的努力达到零故障的要求,我们需要由设备的使用者加入共同为设备保全付出心力。
但这不是短时间即可达到的目标, 那我们要如何循序渐进的达到这个目标?维修人员和设备使用者应如何分工?我们如何活用各式各样的保全手段?我们如何管理设备备件?我们如何衡量我们在设备保全的努力?了解 TPM 的内涵,理解 TPM 活动的目标和目的,熟悉 TPM 的推进步骤掌握 TPM 自主保全活动的 7个步骤及推进方法掌握 TPM 的八大核支柱及方法熟悉和运用教育培训的方式,组织实施革新课题改善运用专业保全及保全预防的手段,努力实现零故障推进全员参与改善,实现零灾害、零故障、零不良、零浪费综合效率 OEE 统计与分析,改善和提高设备的利用率企业总经理、副总经理、中高层管理者和生产(制造部经理、主管、设备管理部经理、主管、现场班组长,以及对 TPM 推行感兴趣的人士共计 2天 12小时(上午 9:00-12:00;下午 13:30-16:30第一单元、什么是 TPM一 . 生产部门的 TPM 与全公司的 TPM二 . TPM 的标的三 . 观念与态度四 . 操作人员必须具备的能力五 . 保养人员必须具备的能力六 . 设备必须具备的基本性质七 . 设备可靠度指标第二单元、设备使用的困扰一 . F :弹性 /设备调度; P :生产力; Q :品质; D :交期; S :安全; M :士气; C :成本二 . 设备性能对弹性 /设备调度的影响三 . 设备故障对生产力的影响四 . 设备的七大损失与设备总合效率的关系五 . 设备故障对单件流 /Lean的影响六 . 设备参数输出对品质的影响七 . 设备故障对在制品存货 (WIP与交货期的影响八 . 灾害发生的机构对安全的威胁第三单元、造成设备使用困扰的原因一 . 微缺陷的成长二 . 基本条件与应有状态三 . 故障的浴缸曲线第四单元、推动 TPM 的动机与效益一 . 推动 TPM 的动机分析二 . TPM 成果指标的体系三 . 日本 TPM 优秀奖得奖厂商主要成果第五单元、设备使用方法的研究与改善一 . 减少故障损失的五个对策二 . 设备使用方法的研究与改善三 . PM 分析步骤与实例第六单元、认识并活用各种保全手段一 . 如何设定实施保养的时点二 . 提升可用率,可用的保养活动事后保全定期保全预知保全改良保全保全预防 (MP活动三 . 制造部门与保全部门的基本任务分担四 . 设备备品的管理第七单元、零故障、零灾害的活动一 . 零故障活动的四个阶段阶段 1减少故障间隔的变异阶段 2延长固有寿命阶段 3劣化定期的复元阶段 4预知寿命二 . 迈向零故障、零灾害的过程步骤一整理过去的故障步骤二故障、灾害分析与总点检步骤三强制劣化的排除与待处理劣化的复原●自主保全暂行基准之检讨步骤四弱点 /零灾害研究●危险预知(KYT●设备失效模式与效应分析 (FMEA●抽出点检项目到改良及保全计划步骤五基准书的制订与管理步骤六保全的效率化步骤七预知保全的推展第八单元、 TPM 的八大支柱一 . 八大支柱的地基 - 5S(整理、整顿、清扫、清洁、素养二 . 运转、保全提升训练成功工作的三大条件教育训练的三大支柱训练预定表OJT 工作教导 _四阶段法三 . 自主保全体制自主保全的七步骤四 . 计划保全体制计划保全的基本观念计划保全系统的概念设备计划保全的七步骤与四阶段重点零件计划保全的七步骤与四阶段自主保全与计划保全的比较五 . 效率化改善TPM 推动的组织架构 _重叠式小集团活动个别改善主题的难易度与阶层别品管圈活动与 TPM 小集团的比较六 . 品质保全体系品质保全的必要性与定义推行品质保全的基本观念品质保全、标准化与培训品质保全与各支柱的关系七 . 初期管理体制初期管理活动设备技术体系八 . 间接部门效率化九 . 安全、卫生与环境第九单元、 TPM 的导入与实施一 . TPM 的导入实施步骤二 . TPM 展开计划三 . 改善的机会无所不在!。
TPM培训讲义

--- 1960s --- 1970s
C.M(改良保養,Corrective Maintenance)
M.P(保養預防,Maintenance Prevention)
TPM(全員生產保養,Total Productive Maintenance)
--- 1980s
PdM(預知保養,Predictive Maintenance)
常間
自工程疏失停止
出 勤 時 間負
速 空轉,臨時停機
度
損
速度低減
失
荷
不
時運
良
間轉實損
時質失
不良修整 暖機產率
間運有
轉效
*自責項目中(其他)所包含之時間.
*運轉時間---( 加工數*C.T) *設備基準加工速度與實際加速度之差. *加工數*(實際C.T-基準C.T)
*正常生產時作出不良品之時間. *選別,修理不良品而致設備停止有效稼動之時間. *生產開始時,自故障小停止至回復運轉時,條件
故障的分類及損失結構
損失
結果 故障,停止損失
P
小停損失
Q 換工程調整損失
C 速度低下損失
D 性能低下損失
S 成品不良損失
M
保養費用損失 人員過剩損失
災害發生損失
P:Production Q:Quality
C:Cost
D:Delivery
S:Safety
M:Morale
----------致命故障 MTBF ---------長時間故障 分析 --------- 一般故障
消防演習,健康檢查,預防注射,盤點,試作,原動 力設施之停止等引起設備之停止時間. *計劃的預防保全,改良保養時間. *1700活動,TPM活動日,每日下班之清掃10分鐘. *外注品或他工程部品延遲納入引起之等料.
- 1、下载文档前请自行甄别文档内容的完整性,平台不提供额外的编辑、内容补充、找答案等附加服务。
- 2、"仅部分预览"的文档,不可在线预览部分如存在完整性等问题,可反馈申请退款(可完整预览的文档不适用该条件!)。
- 3、如文档侵犯您的权益,请联系客服反馈,我们会尽快为您处理(人工客服工作时间:9:00-18:30)。
三.最低保養成本模式分析,主要是期望藉由最經濟的成本分 析方法,找出保養的最低成本,以避免在定期保養階段,造 成過度保養的浪費.
簡 介 (二)
四.Q-Component分析(品質構成要因分析),是將構成品質關係 之各項要因一一列舉出,並將其做充分保養,以免造成品質 上的問題.
--- 1980s
TPM(全面生產經營系統,Total Productive Management System).
--- 1990s
豐田生產方式=徹底排除浪費=全員生產保養
豐田的生產方式與TPM的關係
二大支柱
豐田生產方式=徹底排除浪費
豐田生產方式 建立方法
多制程 明確流程 無不良品
(Just-in-Time)生產
TPM 效率化個別改善九步驟
TPM 導入步驟
保養工作的分類與職責劃分
日常點檢表
日常點檢表範例
主管確認
TPM 導入步驟
TPM 導入步驟
TPM 導入步驟
TPM 導入步驟
查核要點
1.TPM的組織運作 2.個別改善 3.自主保養 4.計劃保養 5.品質保養 6.制品,設備的初期管理
7.教育訓練 8.管理,間接部門
(看板)運用手段
生產平準化(多樣化) 批次小準備時間少
零庫存
標準作業
1)Cycle Time 2)作業順序 3)標準化
自動化運用防止停機的技巧--防呆fool proof)
目視管理
Andon
可利用率真(盡量保持設備於可用狀態)
保養確實
縮短準備時間 從作業改善至設備改善
TPM
設備效率化 六大損失的排除
*價格地位
*科技地位
*在業界及顧客中的商譽
•研究發展構面
*產品開發的能力
*創新的能力
•製造構面
*生產力
*設備總合效率
*設備及廠房現代化的程度
*品質
*交期
*規劃及排程的效能
•配銷構面
*配銷管道的好壞及數量的多寡 *配銷的成本 *與經銷廠商的關係 *經銷廠商的關係 *服務客戶的水準
•行政構面
*使用科技設備處理事務的程度 *資訊傳達的能力 *行政成本
各精 條度 件點 的檢
各品 條質 件與 間條 關之 連關 及運
改 善 計 劃 的 實 施
標 準 化 的 實 施
效 果 評 估
(三)TPM 導入步驟
TPM 導入步驟
TPM 導入步驟
1.內部環境分析
•財務構面
•配銷構面
•行銷構面
•行政構面
•同業競爭構面 •管理階層構面
•研究發展構面 •員工構面
TPM全员设备管理讲义
(一)TPM 簡介
TPM的定義
一.以建立追求生產系統效率化極限(總合的效率化) 的企業體質為目標.
二.在現場,現物所構筑的生產系統中,以企業整體生命 周期為對象,追求(零故障),(零不良),(零災害),防止 所有損失於未然.
三.由生產部門開始,而後跨越開發,營業,管理,採購等 部門.
修理整備技術提升 預防保養的實施
改良保養的實施
潤滑管理
預備品的管理
TPM 重點設備判定表
資料整理整頓的基本做法
目的 效率的提升
目標 30秒取得資料
基本條件 •不要的資料廢棄 •定位
實施內容
•不要的資料廢棄 •每月定期整理一次 •資料,檔案的格式統一化 •資料夾分類,歸位 •建立運用規則
(二)TPM 活動常用手法概要
五.所謂PQA,即Perfect Quality Assurance的簡稱,為彌補舊式 QC活動的缺失,達成全面品質提升的手法之一.
六.選擇最經濟的設備投資案,一般以L.C.C.(Life Cycle Cost,生 命周期成本)之分析作為決策參採用 FMEA(失效模式及效應分析)
維修方法 的設定
分解,裝配, 測定,更換 方法的基 準化 使用零件 的共通化 工具器具 的改善專 用化 從結構方 面改善容 易修理的 設備設定 預備品的 保管基準
為延長壽 命,提升強 度的對策 結構,構造 材質,形狀 呎寸精密 度 組合精密 度 組合強度 耐磨耗性 耐腐蝕性 容量…… 動作應力 的減輕對 策 緩衝超過 應力的設 計
運轉 更換
運轉技能
操作 檢點,加油 調整 發現異常征兆
維護技能
檢點,檢查,測定,診斷,修理 整備,故障排除,故障解析
零故障的實施三大方向
人的技術提升
運轉技術提升
操作誤失的防止
設備清掃的實施 日常點檢的實施
零 故 障
設備的改善
營運的系統化
保養技術提升 保養組織的效率化
巡回點檢的實施 故障解析的實施 保養計書的確立
PM分析八步驟
M--Q分析概念圖
管理指標,目標
各
不 良 現 象 的 把 握
品 質 特 性 值 的 決 定
种 與 品 質 有 關 的 要
M
O
Q 之 關 連 作 成
重復分析
•問題點的把握 •重點的決定
因
Machine機械 Ma:Material材料 Q:Quality品質 O:Operation操作 I:Instrument工具
•管理階層構面
*管理階層的素質 *管理階層的士氣 *管理階層的流動率 *可培育為管理人員的人才數目
•員工構面
*流動率 *士氣 *專業知識及技術水準 *目前能力可適應未來趨勢的人才數目 *未來培育的難易度 *勞資關係
2.外部環境分析
•競爭構面 •社會趨勢構面 •經濟趨勢構面 •政治趨勢構面
•競爭構面
*未來整個市場的成長空間 *同業的競爭策略對本公司
影響程度
*新競爭對手對公司的影響
•社會趨勢構面
*支出習慣
*生活型態
*消費意識
*人口
*投入本產業之人口變化
•經濟趨勢構面
*融資利率 *失業率 *貿易收支
*國民生產毛額 *一般薪資水準 *通貨膨脹率
•政治趨勢構面
*稅捐 *產業保護對象及貿易額限制 *環境保護政策
--- 1960s --- 1970s
C.M(改良保養,Corrective Maintenance)
M.P(保養預防,Maintenance Prevention)
TPM(全員生產保養,Total Productive Maintenance)
--- 1980s
PdM(預知保養,Predictive Maintenance)
(5 ~ 10分以上)
突
故
發 型
小
小停止
停
5分以下
止
分
析
精度劣化
障
---機能低下型 劣
磨耗,動搖
腐蝕,變形 溫度及異音
M
M
化
動作不良 Q T
型 ---品質低下型
污穢,塵埃 原料附著
分B
漏氣,漏油, 析 F
滴水
分
析
設備損失結構分析圖
故障對策結構圖
基本條件的 整備
設備清掃 發生源防止 對策 鎖定 防止鬆動 對策 加油 保持加油處 所的乾凈 改善加油 方式 設定清掃, 加油基準
操作失誤的 防止
操作失誤 的原因分 析 操作盤的 設計改善 連結設置 附加 採用“愚巧 法”的對策 目視管理 的實施 操作,調整 方法的基 準化
修理事務的 防止
修理失誤的 原因 容易導致失 誤的零件形 狀及組合方 法之改善 預備品的保 管方法 道具工具的 改善 故障排除的 程序化,容易 化對策 (目視管理)
長期經營目標
長期經營策略
本年度目標 1.附加價值生產性
-- 提升15% 2.勞動生產性 3.庫存金額
-- 減少15% 4.設備總合效率
-- 78% 5.提案件數
-- 每人2件
現狀問題點
基本方針與年度策略展開釋例
TPM基本方針
TPM 導入步驟
TPM 導入步驟
TPM 導入步驟
TPM 導入步驟
工作重點
突發邦聯損失 準備損失 停機損失 速度損失
不良整修損失
暖機損失
TPM的活動 2.TPM活動的八大支柱
一.效率化的個別改善活動. 二.自主保養活動. 三.建立計劃保養體制. 四.品質保養活動. 五.MP設計及初期管理活動. 六.建構教育訓練體系. 七.管理間接部門的效率化. 八.安全,衛生與環境管理.
•製造構面
•財務構面
*本益比 *利潤對銷售收入的比率 *銷售收入對凈交資產的比率 *直接成本和間接費用 *財務商譽(投資人,政府,往來銀行)
•行銷構面
*市場相對占有率 *價格競爭力 *產品行銷範圍 *產品品質(顧客抱怨件數) *對顧客及市場的了解程度 *對客戶的服務的品質
•同業競爭構面
*年度企業排名 *形象地位
9.安全,衛生環境管理 10.TPM的效率及評價
TPM 優 秀 獎 審 查 表
清掃的點檢重點(用眼睛)
設備名: 年月日
清掃的點檢重點 (用耳朵聽,用手摸,用鼻子聞)
設備名: 年月日
重點目標
庫存金額 設備總合效率 生產性 休業災害
降低30% 86%以上 提升50% 0件
TPM 導入步驟
TPM 導入步驟
保全體系概念圖
自主保養 保 養
專門保養
日常點檢
預防保養
定期點檢 設備診斷 改良保養 事後保養
計劃保養 預知保養
教
保養預防
育
訓
練
小集團活動
各部門協力支援
TPM 導入步驟
企業理念與方針
*員工雇用政策 *品質標準的限定 *進口材料的比例限制 *外匯管制及關稅 *公共的支出