电镀不良之原因与对策
电镀过程中镀层不良的描述、原因及对策

电镀过程中镀层不良的描述、原因及对策1、针孔。
针孔是由于镀件外表吸附着氢气,迟迟不开释。
使镀液无法亲润镀件外表,然后无法电析镀层。
跟着析氢点周围区域镀层厚度的添加,析氢点就构成了一个针孔。
特点是一个发亮的圆孔,有时还有一个向上的小尾巴"。
当镀液中短少湿润剂并且电流密度偏高时,容易构成针孔。
2、麻点。
麻点是由于受镀外表不洁净,有固体物质吸附,或许镀液中固体物质悬浮着,当在电场效果下到达工件外表后,吸附其上,而影响了电析,把这些固体物质嵌入在电镀层中,构成一个个小凸点(麻点)。
特点是上凸,没有发亮现象,没有固定形状。
总归是工件脏、镀液脏而构成。
3、气流条纹。
气流条纹是由于添加剂过量或阴极电流密度过高或络合剂过高而降低了阴极电流效率然后析氢量大。
假如当时镀液流动缓慢,阴极移动缓慢,氢气贴着工件外表上升的进程中影响了电析结晶的摆放,构成自下而上一条条气流条纹。
4、掩镀(露底)。
掩镀是由于是工件外表管脚部位的软性溢料没有除掉,无法在此处进行电析堆积镀层。
电镀后可见基材,故称露底(由于软溢料是半通明的或通明的树脂成份)。
5、镀层脆性。
在SMD电镀后切筋成形后,可见在管脚弯处有开裂现象。
当镍层与基体之间开裂,判定是镍层脆性。
当锡层与镍层之间开裂,判定是锡层脆性。
构成脆性的原因八成是添加剂,光亮剂过量,或许是镀液中无机、有机杂质太多构成。
6、气袋。
气袋的构成是由于工件的形状和积气条件而构成。
氢气积在"袋中"无法排到镀液液面。
氢气的存在阻挠了电析镀层。
使堆集氢气的部位无镀层。
在电镀时,只需留意工件的钩挂方向能够防止气袋现象。
如图示工件电镀时,当垂直于镀槽底钩挂时,不发生气袋。
当平行于槽底钩挂时,易发生气袋。
7、塑封黑体中心开"锡花”。
在黑体上有锡镀层,这是由于电子管在焊线时,金丝的向上抛物形太高,塑封时金丝显露在黑体外表,锡就镀在金丝上,像开了一朵花。
不是镀液问题。
8、"爬锡"。
电镀不良及对策
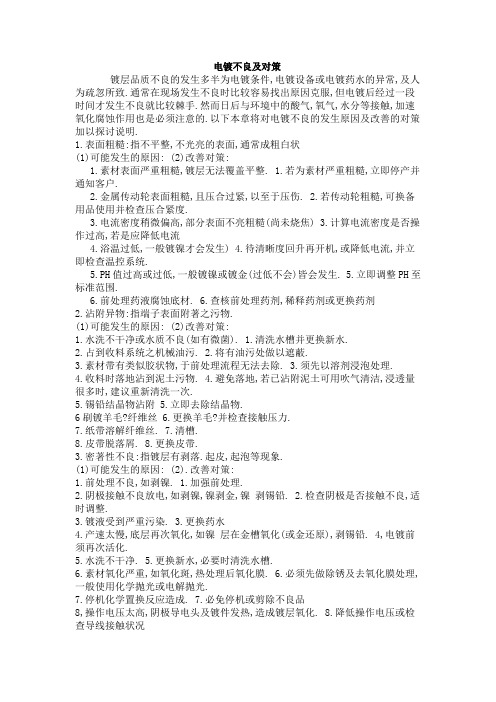
电镀不良及对策镀层品质不良的发生多半为电镀条件,电镀设备或电镀药水的异常,及人为疏忽所致.通常在现场发生不良时比较容易找出原因克服,但电镀后经过一段时间才发生不良就比较棘手.然而日后与环境中的酸气,氧气,水分等接触,加速氧化腐蚀作用也是必须注意的.以下本章将对电镀不良的发生原因及改善的对策加以探讨说明.1.表面粗糙:指不平整,不光亮的表面,通常成粗白状(1)可能发生的原因: (2)改善对策:1.素材表面严重粗糙,镀层无法覆盖平整. 1.若为素材严重粗糙,立即停产并通知客户.2.金属传动轮表面粗糙,且压合过紧,以至于压伤. 2.若传动轮粗糙,可换备用品使用并检查压合紧度.3.电流密度稍微偏高,部分表面不亮粗糙(尚未烧焦) 3.计算电流密度是否操作过高,若是应降低电流4.浴温过低,一般镀镍才会发生) 4.待清晰度回升再开机,或降低电流,并立即检查温控系统.5.PH值过高或过低,一般镀镍或镀金(过低不会)皆会发生. 5.立即调整PH至标准范围.6.前处理药液腐蚀底材. 6.查核前处理药剂,稀释药剂或更换药剂2.沾附异物:指端子表面附著之污物.(1)可能发生的原因: (2)改善对策:1.水洗不干净或水质不良(如有微菌). 1.清洗水槽并更换新水.2.占到收料系统之机械油污. 2.将有油污处做以遮蔽.3.素材带有类似胶状物,于前处理流程无法去除. 3.须先以溶剂浸泡处理.4.收料时落地沾到泥土污物. 4.避免落地,若已沾附泥土可用吹气清洁,浸透量很多时,建议重新清洗一次.5.锡铅结晶物沾附 5.立即去除结晶物.6刷镀羊毛?纤维丝 6.更换羊毛?并检查接触压力.7.纸带溶解纤维丝. 7.清槽.8.皮带脱落屑. 8.更换皮带.3.密著性不良:指镀层有剥落.起皮,起泡等现象.(1)可能发生的原因: (2).改善对策:1.前处理不良,如剥镍. 1.加强前处理.2.阴极接触不良放电,如剥镍,镍剥金,镍剥锡铅. 2.检查阴极是否接触不良,适时调整.3.镀液受到严重污染. 3.更换药水4.产速太慢,底层再次氧化,如镍层在金槽氧化(或金还原),剥锡铅. 4,电镀前须再次活化.5.水洗不干净. 5.更换新水,必要时清洗水槽.6.素材氧化严重,如氧化斑,热处理后氧化膜. 6.必须先做除锈及去氧化膜处理,一般使用化学抛光或电解抛光.7.停机化学置换反应造成. 7.必免停机或剪除不良品8,操作电压太高,阴极导电头及镀件发热,造成镀层氧化. 8.降低操作电压或检查导线接触状况9,底层电镀不良(如烧焦),造成下一层剥落. 9.改善底层电镀品质.10.严重.烧焦所形成剥落 10.参考NO12处理对策.4.露铜:可清楚看见铜色或黄黑色于低电流处(凹槽处)(1)可能发生原因: (2)改善对策:1.前处理不良,油脂,氧化物.异物尚未除去,镀层无法析出. 1.加强前处理或降低产速2.操作电流密度太低,导致低电流区,镀层无法析出. 2.重新计算电镀条件.3镍光泽剂过量,导致低电流区,镀层无法析出 3.处理药水,去除过多光泽剂或更新.4.严重刮伤造成露铜. 4.检查电镀流程,(查参考NO5)5.未镀到. 5.调整电流位置.5刮伤:指水平线条状,一般在锡铅镀层比较容易发生.(1)可能发生的原因: (2)改善对策:1.素材本身在冲压时,及造成刮伤. 1.停止生产,待与客户联系.2.被电镀设备中的金属制具刮伤,如阴极头,烤箱定位器,导轮等. 2.检查电镀流程,适时调整设备和制具.3.被电镀结晶物刮伤. 3.停止生产,立即去除结晶物.6.变形(刮歪):指端子形状已经偏离原有尺寸或位置.(1)可能发生的原因: (2)改善对策:1.素材本身在冲压时,或运输时,即造成变形. 1.停止生产,待与客户联系.2.被电镀设备,制具刮歪(如吹气.定位器,振荡器,槽口,回转轮) 2.检查电镀流程,适时调整设备和制具.3.盘子过小或卷绕不良,导致出入料时刮歪 3.停止生产,适时调整盘子4.传动轮转歪, 4.修正传动轮或变更传动方式.7壓傷:指不規則形狀之凹洞可能發生的原因:改善對策:1)本身在沖床加工時,已經壓傷,鍍層無法覆蓋平整2)傳動輪松動或故障不良,造成壓合時傷到 1)停止生産,待與客戶聯2)檢查傳動機構,或更換備品8白霧:指鍍層表面卡一層雲霧狀,不光亮但平整可能發生的原因:1)前處理不良2)鍍液受污染3)錫鉛層愛到酸腐蝕,如停機時受到錫鉛液腐蝕4)錫鉛藥水溫度過高5)錫鉛電流密度過低6)光澤劑不足7)傳致力輪髒污8)錫鉛電久進,産生泡沫附著造成改善對策:1)加強前處理2)更換藥水並提純污染液3)避免停機,若無法避免時,剪除不良4)立即檢查溫控系統,並重新設定溫度5)提高電流密度6)補足不澤劑傳動輪7)清潔傳動輪8)立即去除泡沫9針孔:指成群、細小圓洞狀(似被鍾紮狀)可能發生的原因:改善對策:1.操作的電流密度太 1.降低電流密度2.电镀溶液表面张力过大,湿润剂不足。
电镀常见的问题及解决方案

电镀常见的问题及解决方案
电镀过程中可能出现的问题及其解决方案如下:
1.针孔或麻点:这是由于前处理不良、有金属杂质、硼酸含量太少、镀液温度太低等原因造成的。
可以使用润湿剂来减小影响,并严格控制镀液维护及流程。
2.结合力低:如果铜镀层未经活化去氧化层,铜和镍之间的附着力就差,会产生镀层剥落现象。
因此,在电镀前应对基材进行适当的预处理,如酸洗、活化等。
3.镀层脆、可焊性差:这通常是由于有机物或重金属物质污染造成的。
添加剂过多会使镀层中夹带的有机物和分解产物增多,此时可以用活性炭处理或电解等方法除去重金属杂质。
4.镀层发暗和色泽不均匀:有金属污染可能是造成这一问题的原因。
应尽量减少挂具所沾的铜溶液,并在发现污染时立即处理。
5.镀层烧伤:这可能是由于硼酸不足、金属盐的浓度低、工作温度太低、电流密度太高、PH值太高或搅拌不充分等原因造成的。
需要检查并调整相关工艺参数,确保其处于合适的范围。
6.沉积速率低:PH值低或电流密度低都可能导致沉积速率低。
应检查并调整镀液的PH值和电流密度,以优化沉积速率。
7.其他问题:如辅助阳极的铜条未与生产板长度一致或已发粗,不允许再使用。
全板及图形镀后板需在24小时内制作下工序。
图形镀上板戴细纱手套,下板戴棕胶手套,全板上板戴橡胶手套,下板戴干燥的粗纱手套。
在处理电镀问题时,需要综合考虑多个因素,包括镀液成分、设备状况、操作条件等。
如遇到难以解决的问题,建议寻求专业人士的帮助。
电镀层附着力不良原因
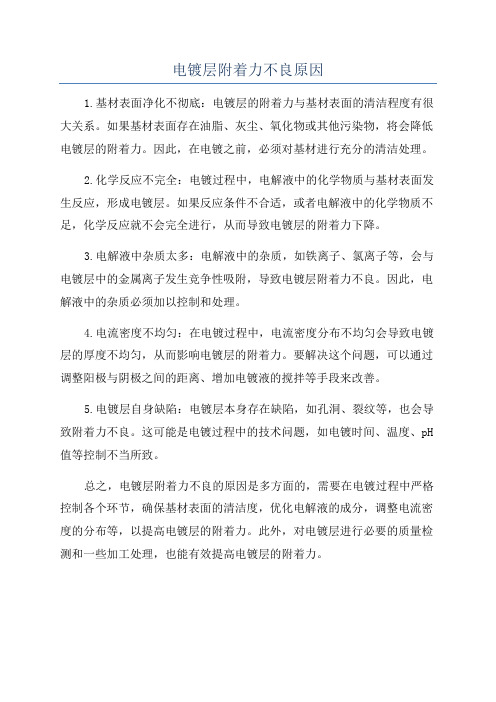
电镀层附着力不良原因
1.基材表面净化不彻底:电镀层的附着力与基材表面的清洁程度有很大关系。
如果基材表面存在油脂、灰尘、氧化物或其他污染物,将会降低电镀层的附着力。
因此,在电镀之前,必须对基材进行充分的清洁处理。
2.化学反应不完全:电镀过程中,电解液中的化学物质与基材表面发生反应,形成电镀层。
如果反应条件不合适,或者电解液中的化学物质不足,化学反应就不会完全进行,从而导致电镀层的附着力下降。
3.电解液中杂质太多:电解液中的杂质,如铁离子、氯离子等,会与电镀层中的金属离子发生竞争性吸附,导致电镀层附着力不良。
因此,电解液中的杂质必须加以控制和处理。
4.电流密度不均匀:在电镀过程中,电流密度分布不均匀会导致电镀层的厚度不均匀,从而影响电镀层的附着力。
要解决这个问题,可以通过调整阳极与阴极之间的距离、增加电镀液的搅拌等手段来改善。
5.电镀层自身缺陷:电镀层本身存在缺陷,如孔洞、裂纹等,也会导致附着力不良。
这可能是电镀过程中的技术问题,如电镀时间、温度、pH 值等控制不当所致。
总之,电镀层附着力不良的原因是多方面的,需要在电镀过程中严格控制各个环节,确保基材表面的清洁度,优化电解液的成分,调整电流密度的分布等,以提高电镀层的附着力。
此外,对电镀层进行必要的质量检测和一些加工处理,也能有效提高电镀层的附着力。
电镀不良的一些情况和解决方法

电镀不良的一些情况和解决方法电镀不良对策镀层品质不良的发生多半为电镀条件,电镀设备或电镀药水的异常,及人为疏忽所致.通常在现场发生不良时比较容易找出塬因克服,但电镀后经过一段时间才发生不良就比较棘手.然而日后与环境中的酸气,氧气,水分等接触,加速氧化腐蚀作用也是必须注意的.以下本章将对电镀不良的发生塬因及改善的对策加以探讨说明.1.表面粗糙:指不平整,不光亮的表面,通常成粗白状(1)可能发生的塬因: (2)改善对策:1.素材表面严重粗糙,镀层无法覆盖平整. 1.若为素材严重粗糙,立即停产并通知客户.2.金属传动轮表面粗糙,且压合过紧,以至于压伤. 2.若传动轮粗糙,可换备用品使用并检查压合紧度.3.电流密度稍微偏高,部分表面不亮粗糙(尚未烧焦) 3.计算电流密度是否操作过高,若是应降低电流4.浴温过低,一般镀镍才会发生) 4.待清晰度回升再开机,或降低电流,并立即检查温控系统.5.PH值过高或过低,一般镀镍或镀金(过低不会)皆会发生. 5.立即调整PH至标准范围.6.前处理药液腐蚀底材. 6.查核前处理药剂,稀释药剂或更换药剂2.沾附异物:指端子表面附着之污物.(1)可能发生的塬因: (2)改善对策:1.水洗不干净或水质不良(如有微菌). 1.清洗水槽并更换新水.2.占到收料系统之机械油污. 2.将有油污处做以遮蔽.3.素材带有类似胶状物,于前处理流程无法去除. 3.须先以溶剂浸泡处理.4.收料时落地沾到泥土污物. 4.避免落地,若已沾附泥土可用吹气清洁,浸透量很多时,建议重新清洗一次.5.锡铅结晶物沾附 5.立即去除结晶物.6刷镀羊毛?纤维丝 6.更换羊毛?并检查接触压力.7.纸带溶解纤维丝. 7.清槽.8.皮带脱落屑. 8.更换皮带.3.密着性不良:指镀层有剥落.起皮,起泡等现象.(1)可能发生的塬因: (2).改善对策:1.前处理不良,如剥镍. 1.加强前处理.2.阴极接触不良放电,如剥镍,镍剥金,镍剥锡铅. 2.检查阴极是否接触不良,适时调整.3.镀液受到严重污染. 3.更换药水4.产速太慢,底层再次氧化,如镍层在金槽氧化(或金还塬),剥锡铅. 4,电镀前须再次活化.5.水洗不干净. 5.更换新水,必要时清洗水槽.6.素材氧化严重,如氧化斑,热处理后氧化膜. 6.必须先做除锈及去氧化膜处理,一般使用化学抛光或电解抛光.7.停机化学置换反应造成. 7.必免停机或剪除不良品8,操作电压太高,阴极导电头及镀件发热,造成镀层氧化. 8.降低操作电压或检查导线接触状况9,底层电镀不良(如烧焦),造成下一层剥落. 9.改善底层电镀品质.10.严重.烧焦所形成剥落 10.参考NO12处理对策.4.露铜:可清楚看见铜色或黄黑色于低电流处(凹槽处)(1)可能发生塬因: (2)改善对策:1.前处理不良,油脂,氧化物.异物尚未除去,镀层无法析出. 1.加强前处理或降低产速2.操作电流密度太低,导致低电流区,镀层无法析出. 2.重新计算电镀条件.3镍光泽剂过量,导致低电流区,镀层无法析出 3.处理药水,去除过多光泽剂或更新.4.严重刮伤造成露铜. 4.检查电镀流程,(查参考NO5)5.未镀到. 5.调整电流位置.5刮伤:指水平线条状,一般在锡铅镀层比较容易发生.(1)可能发生的塬因: (2)改善对策:1.素材本身在冲压时,及造成刮伤. 1.停止生产,待与客户联系.2.被电镀设备中的金属制具刮伤,如阴极头,烤箱定位器,导轮等. 2.检查电镀流程,适时调整设备和制具.3.被电镀结晶物刮伤. 3.停止生产,立即去除结晶物.6.变形(刮歪):指端子形状已经偏离塬有尺寸或位置.(1)可能发生的塬因: (2)改善对策:1.素材本身在冲压时,或运输时,即造成变形. 1.停止生产,待与客户联系.2.被电镀设备,制具刮歪(如吹气.定位器,振荡器,槽口,回转轮) 2.检查电镀流程,适时调整设备和制具.3.盘子过小或卷绕不良,导致出入料时刮歪 3.停止生产,适时调整盘子4.传动轮转歪, 4.修正传动轮或变更传动方式.7压伤:指不规则形状之凹洞可能发生的塬因:改善对策:1)本身在冲床加工时,已经压伤,镀层无法覆盖平整2)传动轮松动或故障不良,造成压合时伤到 1)停止生産,待与客户联2)检查传动机构,或更换备品8白雾:指镀层表面卡一层云雾状,不光亮但平整可能发生的塬因:1)前处理不良2)镀液受污染3)锡铅层爱到酸腐蚀,如停机时受到锡铅液腐蚀4)锡铅药水温度过高5)锡铅电流密度过低6)光泽剂不足7)传致力轮脏污8)锡铅电久进,産生泡沫附着造成改善对策:1)加强前处理2)更换药水并提纯污染液3)避免停机,若无法避免时,剪除不良4)立即检查温控系统,并重新设定温度5)提高电流密度6)补足不泽剂传动轮7)清洁传动轮8)立即去除泡沫9针孔:指成群、细小圆洞状(似被钟扎状)可能发生的塬因:改善对策:1.操作的电流密度太 1.降低电流密度2.电镀溶液表面张力过大,湿润剂不足。
电镀不良原因分析及对策

镀层表面起泡 脱皮
再放入40℃条件下1h,最后再在室温中放置15min。如此循环4次,如果镀层表
面状态和结合力均无变化则为合格
所谓剥离试验,是在制品电镀的样片上切取1!2cm宽的镀层,橇起一头,
用垂直于基体的力拉镀层,并测定剥离镀层时所需的力,其单位为kg/cm。一般剥
离在0.45kg/cm以上则为合格。
可观察到许多微小的凹坑,但手摸时无粗糙感。这种故障产生在酸性镀亮铜工
序中,其产生原因及排除方法如下:
(1)空气搅拌太剧烈。应停用空气搅拌,采用阴极移动,为了防止产生过多的
铜离子,每天下班时应用少量的双氧水经稀释后加入镀液中。
(2)阴极电流密度太大。应适当减小,一般电流密度应控制在2~3A/d㎡。
(3)组合光亮剂的组成不平衡。应适当提高镀液中硫酸含量,降低硫酸铜的含
量,镀液内可添加适量的聚乙二醇和聚二硫二丙烷磺酸钠。
(4)当粗化过度或清洗不良时,敏化和活化反应会构成核状物,导致镀层表
面沉积出凸起的细沙粒状的麻点。对此,应适பைடு நூலகம்调整粗化和水洗工艺条件。
(5)电镀铜时阳极泥混入镀液中,或挂钩接触部位金属脱落混入镀液中。对
此,应严格按照工艺规程进行操作。
(6)使用催化剂时,制品表面未完全分解。应适当调整催化工艺条件。
a、应注意制品的漂浮性。因塑料比重较小,其漂浮性比金属件大,尤其是整 组挂具,在进入镀液时,受浮力影响困难使导电部位脱离电极棒。因此,在设 计时最好采用弹簧或螺钉夹紧,特别是采用自动生产线时更应注意这一问题。
b、应注意制品的变形。由于制品的刚性较差,挂具所用的钢丝直径和触点位 置都会影响到制品的变形。在设计时,应尽量采用托、夹等方法,尽可能避免 撑、插、顶、压。如果必须采用后一类方法时,支撑点尽可能安放在孔内侧的 根部。
电镀中常见的不良原因分析(这些你都能解决了吗)
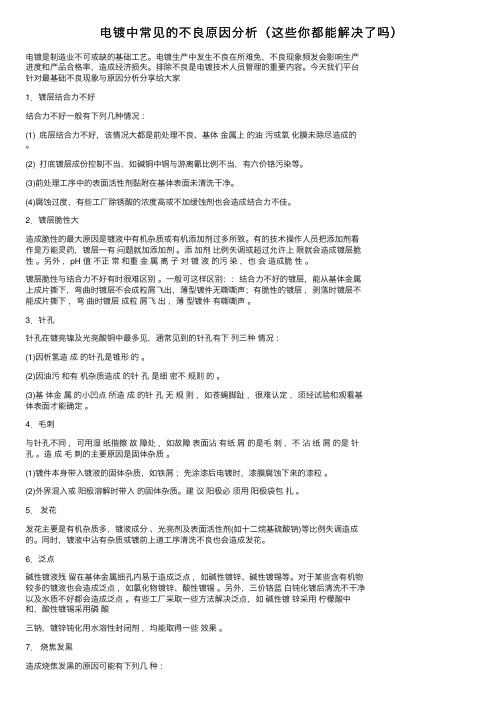
电镀中常见的不良原因分析(这些你都能解决了吗)电镀是制造业不可或缺的基础⼯艺。
电镀⽣产中发⽣不良在所难免,不良现象频发会影响⽣产进度和产品合格率,造成经济损失。
排除不良是电镀技术⼈员管理的重要内容。
今天我们平台针对最基础不良现象与原因分析分享给⼤家1.镀层结合⼒不好结合⼒不好⼀般有下列⼏种情况:(1) 底层结合⼒不好,该情况⼤都是前处理不良、基体⾦属上的油污或氧化膜未除尽造成的。
(2) 打底镀层成份控制不当,如碱铜中铜与游离氰⽐例不当,有六价铬污染等。
(3)前处理⼯序中的表⾯活性剂黏附在基体表⾯未清洗⼲净。
(4)腐蚀过度,有些⼯⼚除锈酸的浓度⾼或不加缓蚀剂也会造成结合⼒不佳。
2.镀层脆性⼤造成脆性的最⼤原因是镀液中有机杂质或有机添加剂过多所致。
有的技术操作⼈员把添加剂看作是万能灵药,镀层⼀有问题就加添加剂。
添加剂⽐例失调或超过允许上限就会造成镀层脆性。
另外,pH 值不正常和重⾦属离⼦对镀液的污染,也会造成脆性。
镀层脆性与结合⼒不好有时很难区别。
⼀般可这样区别::结合⼒不好的镀层,能从基体⾦属上成⽚撕下,弯曲时镀层不会成粒屑飞出,薄型镀件⽆嘶嘶声;有脆性的镀层,剥落时镀层不能成⽚撕下,弯曲时镀层成粒屑飞出,薄型镀件有嘶嘶声。
3.针孔针孔在镀亮镍及光亮酸铜中最多见,通常见到的针孔有下列三种情况:(1)因析氢造成的针孔是锥形的。
(2)因油污和有机杂质造成的针孔是细密不规则的。
(3)基体⾦属的⼩凹点所造成的针孔⽆规则,如苍蝇脚趾,很难认定,须经试验和观看基体表⾯才能确定。
4.⽑刺与针孔不同,可⽤湿纸揩擦故障处,如故障表⾯沾有纸屑的是⽑刺,不沾纸屑的是针孔。
造成⽑刺的主要原因是固体杂质。
(1)镀件本⾝带⼊镀液的固体杂质,如铁屑;先涂漆后电镀时,漆膜腐蚀下来的漆粒。
(2)外界混⼊或阳极溶解时带⼊的固体杂质。
建议阳极必须⽤阳极袋包扎。
5.发花发花主要是有机杂质多,镀液成分、光亮剂及表⾯活性剂(如⼗⼆烷基硫酸钠)等⽐例失调造成的。
电镀件常见不良原因分析
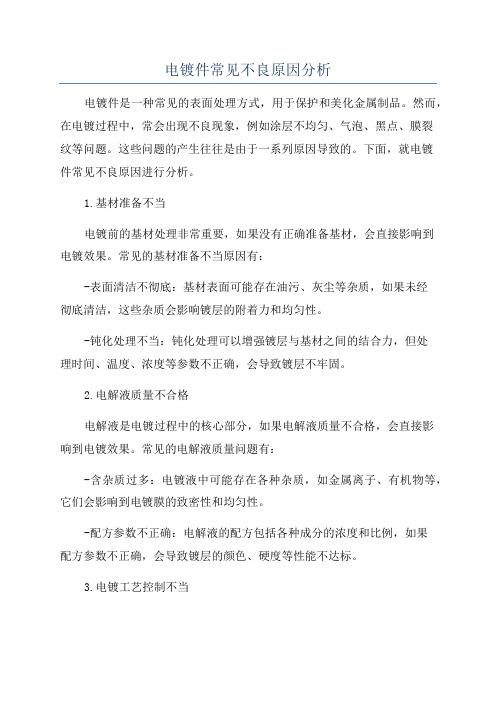
电镀件常见不良原因分析电镀件是一种常见的表面处理方式,用于保护和美化金属制品。
然而,在电镀过程中,常会出现不良现象,例如涂层不均匀、气泡、黑点、膜裂纹等问题。
这些问题的产生往往是由于一系列原因导致的。
下面,就电镀件常见不良原因进行分析。
1.基材准备不当电镀前的基材处理非常重要,如果没有正确准备基材,会直接影响到电镀效果。
常见的基材准备不当原因有:-表面清洁不彻底:基材表面可能存在油污、灰尘等杂质,如果未经彻底清洁,这些杂质会影响镀层的附着力和均匀性。
-钝化处理不当:钝化处理可以增强镀层与基材之间的结合力,但处理时间、温度、浓度等参数不正确,会导致镀层不牢固。
2.电解液质量不合格电解液是电镀过程中的核心部分,如果电解液质量不合格,会直接影响到电镀效果。
常见的电解液质量问题有:-含杂质过多:电镀液中可能存在各种杂质,如金属离子、有机物等,它们会影响到电镀膜的致密性和均匀性。
-配方参数不正确:电解液的配方包括各种成分的浓度和比例,如果配方参数不正确,会导致镀层的颜色、硬度等性能不达标。
3.电镀工艺控制不当电镀工艺过程中的各个环节都需要精确控制,否则会产生不良现象。
常见的电镀工艺控制不当原因有:-电流密度不均匀:电镀过程中,电流密度分布不均匀会导致镀层厚度不均匀,甚至出现孔洞等问题。
-温度控制不准确:电镀过程中的温度控制对于镀层的质量和均匀性非常重要,如果温度控制不准确,会影响到电解液的反应速率和镀层的结构。
4.设备维护不当电镀设备的维护工作也是保证电镀质量的关键。
常见的设备维护不当原因有:-阴极和阳极污染:设备内部的阴极和阳极可能会受到电解液的腐蚀,长期使用后会产生污染物,需要定期清洗和更换。
-设备参数不稳定:设备的电流、温度、电压等参数需保持稳定,如果设备参数不稳定,会导致镀层质量下降。
综上所述,电镀件常见的不良现象往往由基材准备不当、电解液质量不合格、电镀工艺控制不当和设备维护不当等原因导致。
为确保电镀质量,操作人员应遵循正确的工艺流程,提高工作细致性和耐心性,严格控制每个环节的参数和条件,以及定期维护设备,确保设备的正常运行。
电镀不良原因分析及解决方案

镀层呈青绿色
镀层呈灰黑色 镀层色泽发白
镀层色泽不均 镀层粗糙
成因及对策 (1)镀液中铜含量偏高。应在镀液中添加适量锌盐。 (2)阴极电流密度偏低。应适当提高。 (3)镀液温度偏高。应适当降低。 (4)镀液的pH值偏高。应使用碳酸氢钠调整镀液的pH值。 (5)镀液中游离氰化物含量偏低。应补充适量氰化物。 (1)镀液中二价锌离子浓度过高。应补充适量铜盐。 (2)镀液温度偏低。应适当提高。 (3)镀液中游离氰化物含量偏高。应补充适量铜盐。 (1)镀液中游离氰化物含量偏高。应补充适量铜盐。 (2)镀液中有砷等杂质污染。应在大电流密度下进行电解处理。 (1)电流密度偏高。应适当降低。 (2)镀液中二价锌离子浓度太高。应补充适量铜盐。 (3)镀液温度偏低。应适当提高。 (4)镀液中游离氰化物或氨水过多。应补充适量铜盐。 (1)镀液中游离氰化物含量偏低。应补充适量氰化物。 (2)镀液中氨水添加不足。应适当补充。 (1)镀液中氰化物含量偏低。应补充适量氰化物。 (2)阳极不清洁。应清洗阳极。 (3)镀液中杂质太多。应使用活性碳滤出杂质。
电镀加工出现问题的原因及解决办法
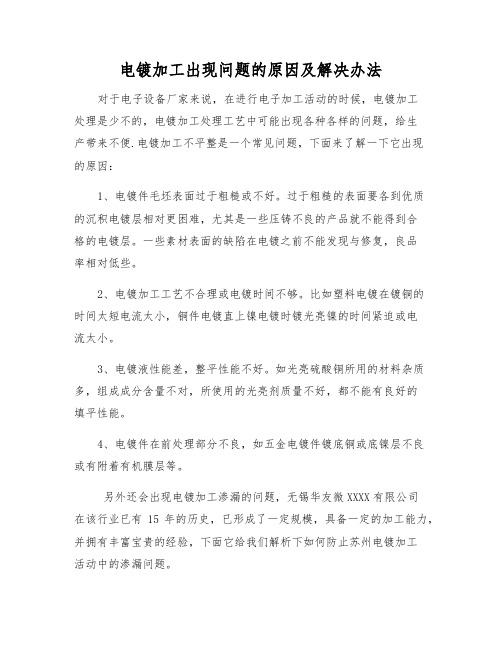
电镀加工出现问题的原因及解决办法对于电子设备厂家来说,在进行电子加工活动的时候,电镀加工处理是少不的,电镀加工处理工艺中可能出现各种各样的问题,给生产带来不便.电镀加工不平整是一个常见问题,下面来了解一下它出现的原因:1、电镀件毛坯表面过于粗糙或不好。
过于粗糙的表面要各到优质的沉积电镀层相对更困难,尤其是一些压铸不良的产品就不能得到合格的电镀层。
一些素材表面的缺陷在电镀之前不能发现与修复,良品率相对低些。
2、电镀加工工艺不合理或电镀时间不够。
比如塑料电镀在镀铜的时间太短电流太小,铜件电镀直上镍电镀时镀光亮镍的时间紧迫或电流太小。
3、电镀液性能差,整平性能不好。
如光亮硫酸铜所用的材料杂质多,组成成分含量不对,所使用的光亮剂质量不好,都不能有良好的填平性能。
4、电镀件在前处理部分不良,如五金电镀件镀底铜或底镍层不良或有附着有机膜层等。
另外还会出现电镀加工渗漏的问题,无锡华友微XXXX有限公司在该行业已有15年的历史,已形成了一定规模,具备一定的加工能力,并拥有丰富宝贵的经验,下面它给我们解析下如何防止苏州电镀加工活动中的渗漏问题。
1、严格防范镀液加温过高。
当镀液加温过高时,镀液会加速蒸发和分解,气雾中含有高浓度的溶质成分。
这时会严重污染环境,尤其是酸、碱气雾,氰化物和铬雾对环境的影响和人体危害会更大。
2、严格防止镀液被排风机吸走。
当电镀加工中,排风机配备不当,镀液液位过高,这时镀液容易被吸走,在槽盖未启开之前极为严重,既引起环境污染,又会造成镀液损耗,出现这种情况时要及时采取措施予以解决,如降低镀液液位,调整吸风口宽度等。
3、防止镀槽、加温(冷却)管渗漏造成污染。
电镀槽或加温(冷却)管渗漏往往会造成严重污染,其渗漏原因随制造材料及不同镀种各有区别。
电镀不良之原因与对策

電鍍没有良之本果與對策之阳早格格创做鍍層品質没有良的發死多数為電鍍條件、電鍍設備大概電鍍藥火的異常,及人為大意所致.常常正在現場發死没有良時比較简单找出本果克服,但是電鍍後經過一段時間才發死没有良便比較棘脚,然而日後與環境中的酸氣、氧氣、火分等交觸,加速氧化腐蝕效率也是必須注意的.以下對電鍍没有良的發死本果及革新的對策加以探討說明.鍍層檢驗正在電鍍業界的鍍層檢驗,普遍包罗中觀檢查、膜薄測試、附著本领測試、抗腐蝕本领測試、抗老化本领測試等.1.中觀檢查:普遍廠家正在檢查中觀比較多使用目視法,較嚴格則會使用4倍大概10倍搁大鏡檢查(正在許多國際標準規範也是如许,如ASTM).建議做業人員先用目視法檢查,一朝瞅到有疑慮的中觀時,再使用搁大鏡觀察.而技術人員則建議必須以50~100倍來檢查(倍數越下,中觀瑕疵越多),以至分解本果時還得借帮200倍以上的顯微鏡.正在電鍍層的中觀判决標準,普遍並無一定的規範,皆需要由買賣雙圆協議.當然表面实足沒有瑕疵最佳,但是這是下難度,没有過普遍人們對色澤均勻這個定義比較能達成共識,果此匯整以下經常發死的一些中觀異常,供參考:(1)色澤没有均,深淺色,異色(如變乌,發紅,發黃,黑霧等)(2)光澤度没有均勻,明明度纷歧,昏暗细糙(3)沾附異物(如火分,毛屑,土灰,油污,結晶物,纖維等)(4)没有服滑,有凸洞,針孔,顆粒物等(5)壓傷,刮傷,磨痕,刮正等各種變形現象及鍍件受損情形(6)電鍍位子没有齊,缺累,過多,過寬等(7)裸露底層金屬現象(8)有起泡,剝降,掉金屬屑等2.膜薄測試:鍍層膜薄測試要领有顯微鏡測試法、電解測試法、X光螢光測試法、β射線測試法、渦流測試法、滴下測試法等.其中以顯微鏡測試法最為正確,没有過需要時間、設備、技術等收援,没有適合檢驗用,普遍用來干分解钻研之用.現正在大部分皆使用X光螢光測試法,果為準確度下,速度快(幾十秒).暂时業界使用XRAY螢光膜薄儀的廠牌有德國的FISCHER、好國的CMI、日本的SEIKO,其測試本理與要领大共小異,但是由於廠牌分歧,几會有少許誤好,只消使用標準片做佳檢量線,做佳定位处事,做佳底材建正,即可將誤好降矮到最小.3.附著本领測試:大概稱為稀著性測試,要领有彎直法、膠帶法、慢热法、切割法、滾壓法等.彎直法比較膠帶法嚴格,有很多場合膠帶法是無法測試鍍層的附著力.若使用膠帶法必須注意一定要使用與Scotch cellophane tape No.600共等粘性膠帶(賽路凡是膠),可則會得来測試效验.4.抗腐蝕本领測試:下表為时常使用的腐蝕試驗要领.說明:√為適用,×為没有適用(1)硝酸蒸汽腐蝕實驗是測試薄金(25μm以上)鍍層的启孔本领,硝酸濃度為70±1%,溫度23±3℃,濕度60%,時間為60分鐘.實驗後鍍層表面没有成有深藍色,乌色腐蝕點及鍍層破裂. (2)两氧化硫蒸汽腐蝕實驗是測試薄金及鈀鎳鍍層的启孔本领,根據AT&T鈀鎳實驗時間為30分鐘,根據ASTM薄金(30μm以上)實驗時間為23±1小時.實驗後鍍層表面没有成有深藍色,乌色腐蝕點及鍍層破裂.(3)鹽火噴霧實驗是測試薄金、鍍鎳層的启孔本领,氯化鈉濃度為5%,實驗溫度為35℃,實驗時間有24小時,48小時,72小時等.實驗後鍍層表面没有成有綠色,红色腐蝕點.(4)硫化氫蒸汽腐蝕實驗是測試金鍍層的启孔本领,實驗時間為 2小時,實驗後鍍層表面没有成有綠色,红色腐蝕點.(5)火蒸氣老化實驗是測試金鍍層的启孔本领,實驗時間為8小時、16小時.實驗後鍍層表面没有成有红色腐蝕點.火蒸氣老化實驗是利用沸騰的純火來蒸烤鍍層,實驗時間為8小時战16小時.暂时業界使用最多為鹽火噴霧實驗战火蒸氣老化實驗.5.抗老化本领實驗:暂时干老化實驗用途,除了觀察表面是可變色,是可有腐蝕斑點中.鍍層中觀檢驗範例一、脚段:正在規範電鍍废品中觀檢驗的要领战判决的標準两、檢驗儀器:1.肉眼.2.20倍搁大鏡.三.檢驗步驟:1.与樣品搁正在深色背景下,用標準红色光源以笔直目标映照. 3.若正在目視下無法判决中觀没有良屬何種没有良現象時,不妨20倍搁大鏡觀察瞭解.四.判决要领:(1)色澤均勻,没有成有深淺色,異色(如變乌,發紅,發黃,黑霧等)的現象.(2)光澤度均勻,没有成有明明度纷歧,昏暗细糙的現象. (3)没有成沾有所有異物(如毛屑,土灰,油污,結晶物,纖維等).(4)仄滑性佳,没有成有凸洞,顆粒物等.(5)没有成有壓傷,刮傷,磨痕等各種變形現象及鍍件受損情形.(6)電鍍位子没有成有没有齊,缺累,過多,過寬等現象. (7)没有成有裸露底層金屬現象.(8)鍍層没有成有起泡,剝降等稀著没有良情形.(9)必須坤燥,没有成沾有火分.稀著本领實驗範例1.合彎實驗法:以1.2~4.0mm的合彎器大概相當於試樣薄度的彎直半徑,將試樣彎直至90度以上,正在以50倍搁大鏡觀察彎直部分的中表面,若無剝離,起皮等現象,即判决為合格.2.膠帶試驗法:使用Scotch cellophane tape No.600大概其余共等粘性的膠帶貼試樣表面,粘貼後以笔直目标赶快撕開,並以目視觀察膠帶上有無剝離金屬,若無所有鍍層剝離現象,即判决為合格.3.慢热試驗法:將試樣正在規定溫度下,加熱30分鐘,然後缓慢热卻於火中(室溫)後烘坤,以50倍搁大鏡觀察,若無起泡,剝離等現象,即判决為合格.4.繞合試驗法:以1mm圓棒對試樣干360度繞合四圈以上,繞合的速度,力量需普遍,正在以50倍搁大鏡觀察,若無剝離,起皮等現象,即判决為合格.。
电镀不良之原因分析及防范措施
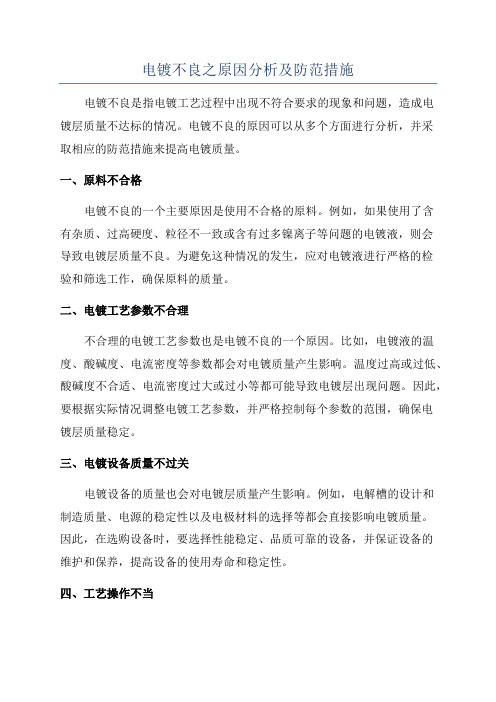
电镀不良之原因分析及防范措施电镀不良是指电镀工艺过程中出现不符合要求的现象和问题,造成电镀层质量不达标的情况。
电镀不良的原因可以从多个方面进行分析,并采取相应的防范措施来提高电镀质量。
一、原料不合格电镀不良的一个主要原因是使用不合格的原料。
例如,如果使用了含有杂质、过高硬度、粒径不一致或含有过多镍离子等问题的电镀液,则会导致电镀层质量不良。
为避免这种情况的发生,应对电镀液进行严格的检验和筛选工作,确保原料的质量。
二、电镀工艺参数不合理不合理的电镀工艺参数也是电镀不良的一个原因。
比如,电镀液的温度、酸碱度、电流密度等参数都会对电镀质量产生影响。
温度过高或过低、酸碱度不合适、电流密度过大或过小等都可能导致电镀层出现问题。
因此,要根据实际情况调整电镀工艺参数,并严格控制每个参数的范围,确保电镀层质量稳定。
三、电镀设备质量不过关电镀设备的质量也会对电镀层质量产生影响。
例如,电解槽的设计和制造质量、电源的稳定性以及电极材料的选择等都会直接影响电镀质量。
因此,在选购设备时,要选择性能稳定、品质可靠的设备,并保证设备的维护和保养,提高设备的使用寿命和稳定性。
四、工艺操作不当不正确的工艺操作也是电镀不良的一个常见原因。
例如,电镀工艺操作的速度太快或太慢,工件的浸泡时间控制不准确等都可能导致电镀层质量不良。
因此,操作人员在进行电镀工艺操作时要严格按照程序进行,并且进行必要的培训和技术指导,提高工艺操作的准确性和稳定性。
综上所述,电镀不良的原因可以从原料、工艺参数、设备质量和工艺操作等多个方面进行分析。
为了防范电镀不良的发生,可以采取以下措施:1.选用优质的原料,并进行严格检验和筛选;2.根据实际情况调整电镀工艺参数,并进行严格的控制;3.选购品质可靠的设备,并保证设备的维护和保养;4.进行工艺操作前进行必要的培训和技术指导,确保操作的准确性和稳定性;5.建立完善的质量控制体系,对电镀过程进行监控和检测,及时处理不良产品;6.加强与供应商的合作,建立长期稳定的合作关系,确保原料和设备质量的稳定性。
电镀不良之原因分析及防范措施

b.水洗不良
a.
1.检查後调整;
2.检查送风机滤纲及各风嘴,管路有无漏气,不良清洁调整;
b. 检查D4、D5槽之水质、水洗步骤,热水洗温度及水质,不良更换。
7.密着不良
(指镀层有剥落、脱皮、起泡等现象)
a.前处理不良,如剥镍;
b.阴极接触不良放电,如剥镍、剥锡铅;
c.镀液受到严重污染;
d.密着不良;
e.电镀时电压过高,造成镀件热氧化、钝化;
f.电流密度过高,致镀层结构不良;
g.搅拌不良,致镀层结构不良;
h.浴温过高,致镀层结构不良;
i.镀层因放置环境较差、时间过久,致镀层氧化、老化;
j.镀层太薄;
k.焊锡温度不正确;
l.镀件形状构造影响;
m.焊剂不纯物过高;
n.镀件材质之影响(锡>锡铅>金>铜>磷青铜>镍>黄铜);
f.重新修正电镀位置,注意电流分布线;
g.检查泸波度是否符合标准,若偏移时须将整流器送修。
15.界面黑线、雾线(通常在半镀锡铅层之界面都会有此现象)
a.阴极反应太大,大量氢氯泡沬浮於液面;
b.阴极搅拌不良;
c.选镀高度调整不均。
a.降低电流;
b.调整PUMP出水量;
c.检查选镀高度,重新修正。
16.镀层暗红
c.停止生产,立即去除结晶物;
d.检查传动机构,或更换备品;
e.电镀过程中尽量减少桶量,减少不良。
3.烧焦、变色
a.电镀电压太高;
b.PH值太高。
a.依电镀作业条件标准做规范作业;
b.由现场专员定稽核PH值,温度。
此份为首顾提供
4.有异物
a.水洗不乾净;
电镀失败原因分析报告
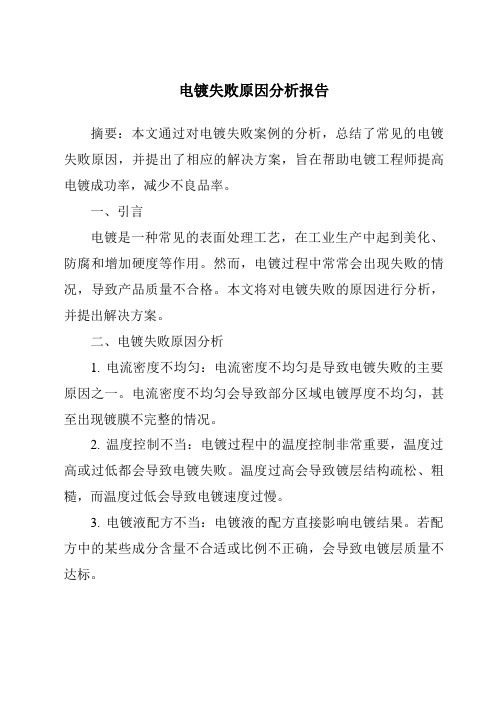
电镀失败原因分析报告摘要:本文通过对电镀失败案例的分析,总结了常见的电镀失败原因,并提出了相应的解决方案,旨在帮助电镀工程师提高电镀成功率,减少不良品率。
一、引言电镀是一种常见的表面处理工艺,在工业生产中起到美化、防腐和增加硬度等作用。
然而,电镀过程中常常会出现失败的情况,导致产品质量不合格。
本文将对电镀失败的原因进行分析,并提出解决方案。
二、电镀失败原因分析1. 电流密度不均匀:电流密度不均匀是导致电镀失败的主要原因之一。
电流密度不均匀会导致部分区域电镀厚度不均匀,甚至出现镀膜不完整的情况。
2. 温度控制不当:电镀过程中的温度控制非常重要,温度过高或过低都会导致电镀失败。
温度过高会导致镀层结构疏松、粗糙,而温度过低会导致电镀速度过慢。
3. 电镀液配方不当:电镀液的配方直接影响电镀结果。
若配方中的某些成分含量不合适或比例不正确,会导致电镀层质量不达标。
4. 表面预处理不彻底:表面预处理是电镀的关键步骤之一,若不进行彻底的表面清洗、脱脂和去除氧化物等处理,会导致电镀层附着力不好。
三、解决方案1. 电流密度均匀化:调整电镀槽设计,使电流在整个工件表面均匀分布,或采用电镀液循环系统,提高电镀液的对流效果,以达到电流密度均匀的目的。
2. 温度控制精确化:安装温度探针,实时监测电镀槽中的温度,并通过控制加热或制冷设备,使温度保持在合适范围内。
3. 优化电镀液配方:根据具体产品要求,调整电镀液中各种成分的含量与比例,确保配方合理,以提高电镀层质量。
4. 提高表面预处理质量:加强表面预处理步骤,确保表面清洁、脱脂和去氧化彻底,可采用多种方法,如超声波清洗、化学脱脂等。
四、结论通过对电镀失败案例的分析,我们总结了电流密度不均匀、温度控制不当、电镀液配方不当和表面预处理不彻底等常见的电镀失败原因,并提出了相应的解决方案。
只有在电镀过程中严格控制这些关键因素,才能提高电镀成功率,降低不良品率,从而保证产品质量。
电镀不良原因分析及对策
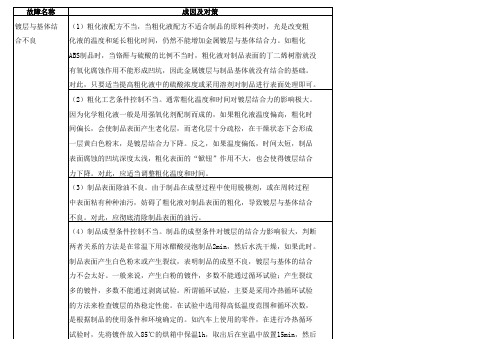
法通过,电镀不上镀层。对此,应首先检查化学镀液,适当延长沉积时间,加
厚化学镀的金属镀层;其次,镀件进入镀槽时,应先用0.1~0.22~3A/d㎡的小电
挂具被金属化
流电镀4~5min,然后将电流逐渐递增至正常工艺规范。 (2)电镀夹具接点太少,夹持部位不当。用作塑料电镀的夹具与镀件的接点, 应比金属件电镀的接点多25%,以减少接触电阻。接点的形式最好不要采用点接 触,而用半环形的线接触,这样可以增强导电性,使电流顺利通过。另外,夹 具应具有良好的弹性,因塑料的比重较小,容易受镀液浮力的作用发生摆动而 影响导电,甚至形成双极性,使镀层溶解。但夹具的弹性也不能过大,否则会 使镀件变形。夹持部位不应选在低电流密度区,因小电流处镀层的沉积速度慢, 相比之下,始终处于难以导电的状态,会影响电镀效果。 (3)化学镀后存放时间太长,镀层表面氧化。经化学镀后的制品,无论存放在 空气或浸放在水中,镀层都会发生氧化,影响导电。对于镀铜层氧化膜,可以 在稀硫酸中进行活化处理,但要损失少量的镀层,增加电镀的困难,不过电镀 还能进行。对于化学镀镍层,因镍的氧化层不易除去,较难活化。对此,可将 镀件先在稀硫酸中活化0.5min,然后带酸入槽电镀5min的暗镍,再镀光亮镍, 则可获得正常镀层。 (1)挂具绝缘不良。应对挂具重新进行绝缘处理。 (2)挂具剥离剂使用不当。应换用适宜的剥离剂。 (3)构架浸入粗化液的深度没有金属化溶液高。应适当降低金属化溶液的液面 高度。 (4)挂具设计不当。塑料电镀时使用的挂具,由于制品本身的特点和工艺的特 殊性,设计时应注意以下问题:
可观察到许多微小的凹坑,但手摸时无粗糙感。这种故障产生在酸性镀亮铜工
序中,其产生原因及排除方法如下:
(1)空气搅拌太剧烈。应停用空气搅拌,采用阴极移动,为了防止产生过多的
常见电镀缺陷和原因分析

常见电镀缺陷和原因分析电镀缺陷是指在电镀过程中(包括准备工作和电镀工艺)出现的不良现象或问题。
下面我将介绍一些常见的电镀缺陷以及可能的原因分析。
1. 镀层不均匀:电镀层在部分区域厚度不均匀或出现斑点、斑纹等现象。
可能的原因包括:- 温度控制不准确:电镀液的温度不稳定、过高或过低,导致镀液在镀件表面的分布不均匀。
- 电镀液流动不均匀:电镀液在镀件上的流动速度不同,导致电流分布不均,进而影响镀层的均匀性。
- 镀液成分不稳定:电镀液中的添加剂、盐类等成分浓度不稳定,导致镀层的形成不均匀。
2. 黑斑或黄斑:镀层表面出现黑色或黄色的斑点。
可能的原因包括:- 杂质污染:电镀液中的杂质(如氧化物、铁离子等)进入镀液中,被还原到镀层表面形成斑点。
- 温度控制不当:电镀液的温度过高,导致镀层表面出现黄色或黑色反应物。
- 电流密度不均匀:镀件表面的电流密度不均匀,导致镀层表面出现黑斑或黄斑。
3. 镀层剥落:镀层与基材之间出现脱落现象。
可能的原因包括:- 镀液准备不当:电镀液的配方和浓度不正确,导致镀液附着力不足。
- 清洗不彻底:镀件在电镀前未进行彻底的清洗,导致表面存在杂质或脱脂剂,影响镀液与基材的结合。
- 电镀时间过短:电镀时间不足,镀层与基材之间的结合力不强,易剥离。
4. 镀层起泡:镀层表面出现气泡现象。
可能的原因包括:- 水分污染:电镀液中存在水分,经电解反应后生成氢气,导致镀液中产生气泡。
- 剧烈搅拌:电镀液在搅拌过程中引入大量气体,导致镀液中产生气泡。
- 电流密度不均匀:镀件表面的电流密度分布不均匀,导致一些区域出现过高的电流密度,进而引发气泡。
5. 镀层色差:镀层表面出现色差现象,包括颜色不均匀、色泽深浅不一等。
可能的原因包括:- 镀液浓度不均:电镀液中添加剂或盐类的浓度不均匀,导致镀层颜色不均匀。
- 电镀液PH值不稳定:电镀液中PH值变化较大,会影响镀层的色泽。
- 镀液渗染:电镀液渗透到基材中,与基材反应产生色差。
电镀常见不良原因
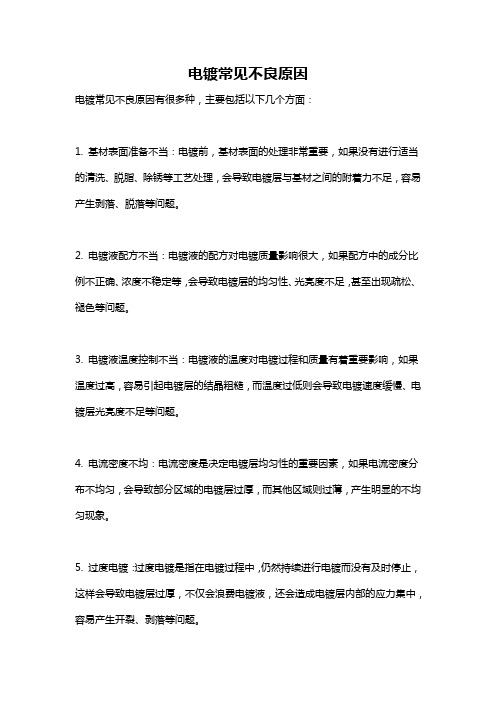
电镀常见不良原因电镀常见不良原因有很多种,主要包括以下几个方面:1. 基材表面准备不当:电镀前,基材表面的处理非常重要,如果没有进行适当的清洗、脱脂、除锈等工艺处理,会导致电镀层与基材之间的附着力不足,容易产生剥落、脱落等问题。
2. 电镀液配方不当:电镀液的配方对电镀质量影响很大,如果配方中的成分比例不正确、浓度不稳定等,会导致电镀层的均匀性、光亮度不足,甚至出现疏松、褪色等问题。
3. 电镀液温度控制不当:电镀液的温度对电镀过程和质量有着重要影响,如果温度过高,容易引起电镀层的结晶粗糙,而温度过低则会导致电镀速度缓慢、电镀层光亮度不足等问题。
4. 电流密度不均:电流密度是决定电镀层均匀性的重要因素,如果电流密度分布不均匀,会导致部分区域的电镀层过厚,而其他区域则过薄,产生明显的不均匀现象。
5. 过度电镀:过度电镀是指在电镀过程中,仍然持续进行电镀而没有及时停止,这样会导致电镀层过厚,不仅会浪费电镀液,还会造成电镀层内部的应力集中,容易产生开裂、剥落等问题。
6. 电流密度过大:如果电流密度设置过大,会导致电镀层过厚、结晶粗糙,甚至出现内部应力过大、变形等问题。
7. 金属离子杂质:电镀过程中,金属离子杂质的存在会对电镀层的质量产生严重影响,容易导致电镀层出现孔洞、起皱、脱落等问题。
8. 电解质污染:如果电解质中存在有机物、杂质等污染物,会影响电镀层的质量,使得电镀层变得不均匀、暗淡、出现结瘤等缺陷。
同时,污染物还会引起电镀过程中的光变化、挥发等问题。
9. 电解质浓度变化:电解质浓度的变化也会对电镀质量产生影响,一方面浓度过低会导致电镀层光亮度不足,另一方面浓度过高则会使得电镀层结晶粗糙、容易脱落。
总之,电镀常见不良原因很多,需要从基材表面准备、电镀液配方、温度控制、电流密度、金属离子杂质、电解质污染、电解质浓度变化等方面进行综合分析和处理,以提高电镀质量。
同时,在电镀过程中,还需要进行严密的监控和控制,保证每一步工艺的准确性和稳定性,以降低不良品率,提高电镀产品的质量和可靠性。
- 1、下载文档前请自行甄别文档内容的完整性,平台不提供额外的编辑、内容补充、找答案等附加服务。
- 2、"仅部分预览"的文档,不可在线预览部分如存在完整性等问题,可反馈申请退款(可完整预览的文档不适用该条件!)。
- 3、如文档侵犯您的权益,请联系客服反馈,我们会尽快为您处理(人工客服工作时间:9:00-18:30)。
電鍍不良之原因與對策
鍍層品質不良的發生多半為電鍍條件、電鍍設備或電鍍藥水的異常,及人為疏忽所致。
通常在現場發生不良時比較容易找出原因克服,但電鍍後經過一段時間才發生不良就比較棘手,然而日後與環境中的酸氣、氧氣、水分等接觸,加速氧化腐蝕作用也是必須注意的。
以下對電鍍不良的發生原因及改善的對策加以探討說明。
鍍層檢驗
在電鍍業界的鍍層檢驗,一般包括外觀檢查、膜厚測試、附著能力測試、抗腐蝕能力測試、抗老化能力測試等。
1.外觀檢查:一般廠家在檢查外觀比較多使用目視法,較嚴格則會使用4倍或10倍放大鏡檢查(在許多國際標準規範也是如此,如ASTM)。
建議作業人員先用目視法檢查,一旦看到有疑慮的外觀時,再使用放大鏡觀察。
而技術人員則建議必須以50~100倍來檢查(倍數越高,外觀瑕疵越多),甚至分析原因時還得借助200倍以上的顯微鏡。
在電鍍層的外觀判定標準,一般並無一定的規範,都需要由買賣雙方協議。
當然表面完全沒有瑕疵最好,但這是高難度,不過一般人們對色澤均勻這個定義比較能達成共識,因此匯整以下經常發生的一些外觀異常,供參考:
(1)色澤不均,深淺色,異色(如變黑,發紅,發黃,白霧等)(2)光澤度不均勻,明亮度不一,暗淡粗糙
(3)沾附異物(如水分,毛屑,土灰,油污,結晶物,纖維等)(4)不平滑,有凹洞,針孔,顆粒物等
(5)壓傷,刮傷,磨痕,刮歪等各種變形現象及鍍件受損情形(6)電鍍位置不齊,不足,過多,過寬等
(7)裸露底層金屬現象
(8)有起泡,剝落,掉金屬屑等
2.膜厚測試:鍍層膜厚測試方法有顯微鏡測試法、電解測試法、X 光螢光測試法、β射線測試法、渦流測試法、滴下測試法等。
其中以顯微鏡測試法最為正確,不過需要時間、設備、技術等支援,不適合檢驗用,一般用來做分析研究之用。
現在大部分都使用X 光螢光測試法,因為準確度高,速度快(幾十秒)。
目前業界使用X-RAY螢光膜厚儀的廠牌有德國的FISCHE
R、美國的CMI、日本的SEIKO,其測試原理與方法大同小異,但由於廠牌不同,多少會有少許誤差,只要使用標準片作好檢量線,作好定位工作,作好底材修正,即可將誤差降低到最小。
3.附著能力測試:或稱為密著性測試,方法有彎曲法、膠帶法、急冷法、切割法、滾壓法等。
彎曲法比較膠帶法嚴格,有很多場合膠帶法是無法測試鍍層的附著力。
若使用膠帶法必須注意一定要使用與Scotch cellophane tape No.600同等粘性膠帶(賽路凡膠),否則會失去測試效果。
4.抗腐蝕能力測試:下表為常用的腐蝕試驗方法。
說明:√為適用,×為不適用
(1)硝酸蒸汽腐蝕實驗是測試厚金(25μm以上)鍍層的封孔能力,硝酸濃度為70±1%,溫度23±3℃,濕度60%,時間為60分鐘。
實驗後鍍層表面不可有深藍色,黑色腐蝕點及鍍層破裂。
(2)二氧化硫蒸汽腐蝕實驗是測試厚金及鈀鎳鍍層的封孔能力,根據AT&T鈀鎳實驗時間為30分鐘,根據ASTM厚金(30μm以上)實驗時間為23±1小時。
實驗後鍍層表面不可有深藍色,黑色腐蝕點及鍍層破裂。
(3)鹽水噴霧實驗是測試薄金、鍍鎳層的封孔能力,氯化鈉濃度為5%,實驗溫度為35℃,實驗時間有24小時,48小時,72小時等。
實驗後鍍層表面不可有綠色,白色腐蝕點。
(4)硫化氫蒸汽腐蝕實驗是測試金鍍層的封孔能力,實驗時間為2小時,實驗後鍍層表面不可有綠色,白色腐蝕點。
(5)水蒸氣老化實驗是測試金鍍層的封孔能力,實驗時間為8小時、16小時。
實驗後鍍層表面不可有白色腐蝕點。
水蒸氣老化實驗是利用沸騰的純水來蒸烤鍍層,實驗時間為8小
時和16小時。
目前業界使用最多為鹽水噴霧實驗和水蒸氣老化實驗。
5.抗老化能力實驗:目前做老化實驗用途,除了觀察表面是否變色,是否有腐蝕斑點外。
鍍層外觀檢驗範例
一、目的:在規範電鍍成品外觀檢驗的方法和判定的標準
二、檢驗儀器:1. 肉眼。
2. 20倍放大鏡。
三.檢驗步驟:
1.取樣品放在深色背景下,用標準白色光源以垂直方向照射。
2.在45度方向距樣品一定的目視距離檢查
3.若在目視下無法判定外觀不良屬何種不良現象時,可以20倍放大鏡觀察瞭解。
四.判定方法:
(1)色澤均勻,不可有深淺色,異色(如變黑,發紅,發黃,白霧等)的現象。
(2)光澤度均勻,不可有明亮度不一,暗淡粗糙的現象。
(3)不可沾有任何異物(如毛屑,土灰,油污,結晶物,纖維等)。
(4)平滑性好,不可有凹洞,顆粒物等。
(5)不可有壓傷,刮傷,磨痕等各種變形現象及鍍件受損情形。
(6)電鍍位置不可有不齊,不足,過多,過寬等現象。
(7)不可有裸露底層金屬現象。
(8)鍍層不可有起泡,剝落等密著不良情形。
(9)必須乾燥,不可沾有水分。
密著能力實驗範例
1.折彎實驗法:
以1.2~4.0mm的折彎器或相當於試樣厚度的彎曲半徑,將試樣彎曲至90度以上,在以50倍放大鏡觀察彎曲部分的外表面,若無剝離,起皮等現象,即判定為合格。
2.膠帶試驗法:
使用Scotch cellophane tape No.600或其他同等粘性的膠帶貼試樣表面,粘貼後以垂直方向迅速撕開,並以目視觀察膠帶上有無剝離金屬,若無任何鍍層剝離現象,即判定為合格。
3.急冷試驗法:
將試樣在規定溫度下,加熱30分鐘,然後急速冷卻於水中(室溫)後烘乾,以50倍放大鏡觀察,若無起泡,剝離等現象,即判定為合格。
4.繞折試驗法:
以1mm圓棒對試樣做360度繞折四圈以上,繞折的速度,力量需一致,在以50倍放大鏡觀察,若無剝離,起皮等現象,即判定為合格。
. .。