电镀不良的一些情况和解决方法
电镀不良分析报告
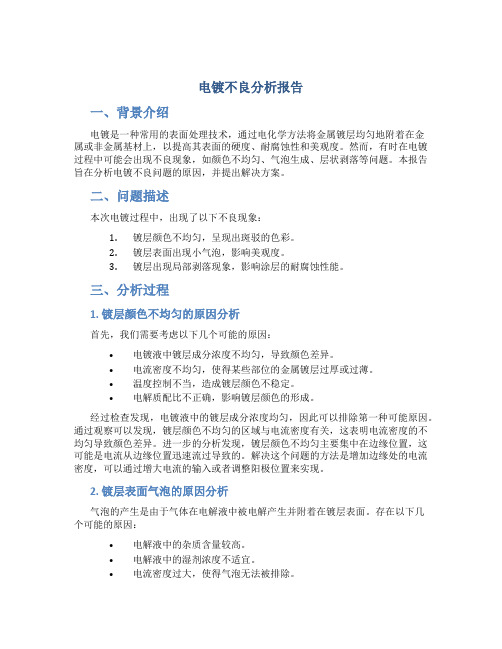
电镀不良分析报告一、背景介绍电镀是一种常用的表面处理技术,通过电化学方法将金属镀层均匀地附着在金属或非金属基材上,以提高其表面的硬度、耐腐蚀性和美观度。
然而,有时在电镀过程中可能会出现不良现象,如颜色不均匀、气泡生成、层状剥落等问题。
本报告旨在分析电镀不良问题的原因,并提出解决方案。
二、问题描述本次电镀过程中,出现了以下不良现象:1.镀层颜色不均匀,呈现出斑驳的色彩。
2.镀层表面出现小气泡,影响美观度。
3.镀层出现局部剥落现象,影响涂层的耐腐蚀性能。
三、分析过程1. 镀层颜色不均匀的原因分析首先,我们需要考虑以下几个可能的原因:•电镀液中镀层成分浓度不均匀,导致颜色差异。
•电流密度不均匀,使得某些部位的金属镀层过厚或过薄。
•温度控制不当,造成镀层颜色不稳定。
•电解质配比不正确,影响镀层颜色的形成。
经过检查发现,电镀液中的镀层成分浓度均匀,因此可以排除第一种可能原因。
通过观察可以发现,镀层颜色不均匀的区域与电流密度有关,这表明电流密度的不均匀导致颜色差异。
进一步的分析发现,镀层颜色不均匀主要集中在边缘位置,这可能是电流从边缘位置迅速流过导致的。
解决这个问题的方法是增加边缘处的电流密度,可以通过增大电流的输入或者调整阳极位置来实现。
2. 镀层表面气泡的原因分析气泡的产生是由于气体在电解液中被电解产生并附着在镀层表面。
存在以下几个可能的原因:•电解液中的杂质含量较高。
•电解液中的湿剂浓度不适宜。
•电流密度过大,使得气泡无法被排除。
经过检测,电解液中的杂质含量符合标准要求,因此第一种可能原因可以排除。
进一步检查发现,电解液中的湿剂浓度偏高,这是导致气泡产生的重要原因。
调整湿剂浓度至合适范围可以解决这个问题。
此外,如果电流密度过大,也会造成气泡无法被排除。
因此,需要对电流密度进行适当的调整,以保证正常的电解过程。
3. 镀层剥落的原因分析镀层的剥落可能是由于以下原因引起:•预处理工艺存在问题,导致基材表面不洁净。
电镀过程中镀层不良的描述、原因及对策

电镀过程中镀层不良的描述、原因及对策1、针孔。
针孔是由于镀件外表吸附着氢气,迟迟不开释。
使镀液无法亲润镀件外表,然后无法电析镀层。
跟着析氢点周围区域镀层厚度的添加,析氢点就构成了一个针孔。
特点是一个发亮的圆孔,有时还有一个向上的小尾巴"。
当镀液中短少湿润剂并且电流密度偏高时,容易构成针孔。
2、麻点。
麻点是由于受镀外表不洁净,有固体物质吸附,或许镀液中固体物质悬浮着,当在电场效果下到达工件外表后,吸附其上,而影响了电析,把这些固体物质嵌入在电镀层中,构成一个个小凸点(麻点)。
特点是上凸,没有发亮现象,没有固定形状。
总归是工件脏、镀液脏而构成。
3、气流条纹。
气流条纹是由于添加剂过量或阴极电流密度过高或络合剂过高而降低了阴极电流效率然后析氢量大。
假如当时镀液流动缓慢,阴极移动缓慢,氢气贴着工件外表上升的进程中影响了电析结晶的摆放,构成自下而上一条条气流条纹。
4、掩镀(露底)。
掩镀是由于是工件外表管脚部位的软性溢料没有除掉,无法在此处进行电析堆积镀层。
电镀后可见基材,故称露底(由于软溢料是半通明的或通明的树脂成份)。
5、镀层脆性。
在SMD电镀后切筋成形后,可见在管脚弯处有开裂现象。
当镍层与基体之间开裂,判定是镍层脆性。
当锡层与镍层之间开裂,判定是锡层脆性。
构成脆性的原因八成是添加剂,光亮剂过量,或许是镀液中无机、有机杂质太多构成。
6、气袋。
气袋的构成是由于工件的形状和积气条件而构成。
氢气积在"袋中"无法排到镀液液面。
氢气的存在阻挠了电析镀层。
使堆集氢气的部位无镀层。
在电镀时,只需留意工件的钩挂方向能够防止气袋现象。
如图示工件电镀时,当垂直于镀槽底钩挂时,不发生气袋。
当平行于槽底钩挂时,易发生气袋。
7、塑封黑体中心开"锡花”。
在黑体上有锡镀层,这是由于电子管在焊线时,金丝的向上抛物形太高,塑封时金丝显露在黑体外表,锡就镀在金丝上,像开了一朵花。
不是镀液问题。
8、"爬锡"。
电镀常见不良问题点分析及对策
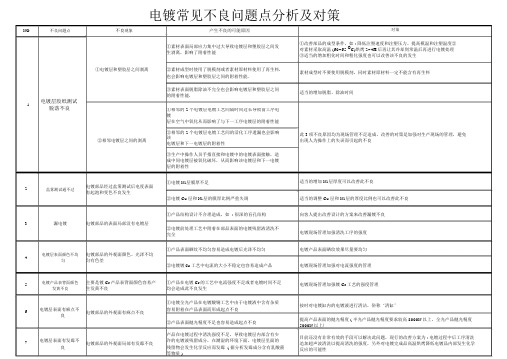
电镀常见不良问题点分析及对策NO.不良问题点不良现象产生不良的可能原因①素材表面局部应力集中过大导致电镀层和塑胶层之间发生剥离,影响了附着性能①电镀层和塑胶层之间剥离②素材成型时使用了脱模剂或者素材原材料使用了再生料.也会影响电镀层和塑胶层之间的附着性能.③素材表面脱脂除油不完全也会影响电镀层和塑胶层之间电镀层胶纸测试的附着性能.1脱落不良①相邻的 2个电镀层电镀工艺间隔时间过长导致前工序电镀层在空气中氧化从而影响了与下一工序电镀层的附着性能②相邻电镀层之间的剥离②相邻的 2个电镀层电镀工艺间的活化工序遗漏也会影响该电镀层和下一电镀层的附着性对策①改善部品的成型条件,如 : 降低注塑速度和注塑压力、提高模温和注塑温度②对素材采取高温 (60~65 O C)烘烤2~4H后再让其冷却到常温后再进行电镀处理③适当的增加粗化时间和粗化强度也可以改善该不良的发生素材成型时不要使用脱模剂,同时素材原材料一定不能含有再生料适当的增加脱脂、除油时间此3项不良原因均为现场管理不足造成,改善的对策是加强对生产现场的管理,避免出现人为操作上的失误而引起的不良2 3 4 5 6 7③生产中操作人员手指直接和电镀中的电镀表面接触,造成中间电镀层被氧化破坏,从而影响该电镀层和下一电镀层的附着性电镀部品经过盐雾测试后电度表面①电镀 Ni层膜厚不足盐雾测试通不过有起泡和变色不良发生②电镀 Cu层和Ni层的膜厚比例严重失调①产品结构设计不合理造成,如 : 很深的盲孔结构漏电镀电镀部品的表面局部没有电镀层②电镀前处理工艺中附着在部品表面的电镀残留液清洗不完全电镀部品的外观面颜色、光泽不均①产品表面晒纹不均匀容易造成电镀后光泽不均匀电镀层表面颜色不均匀匀有色差②电镀镀C u工艺中电流的大小不稳定也容易造成产品电镀产品表背面颜色主要是镀 Cr产品表背面颜色容易产①产品在电镀 Cr的工艺中电流强度不足或者电镀时间不足发黄不良生发黄不良均会造成此不良发生①电镀全光产品在电镀酸铜工艺中由于电镀液中含有杂质电镀层表面有麻点不电镀部品的外观面有麻点不良容易附着在产品表面而形成起点不良良②产品表面抛光精度不足也容易造成起点不良产品在电镀过程中清洗强度不足,导致电镀层内部含有少电镀层表面有发霉不电镀部品的外观面局部有发霉不良许的电镀液残留成分,在潮湿的环境下面,电镀层里面的良残留物会发生化学反应而发霉 ( 据分析发霉成分含有乳酸菌等物质 )适当的增加 Ni层厚度可以改善此不良适当的调整 Cu层和Ni层的厚度比例也可以改善此不良向客人提出改善设计的方案来改善漏镀不良电镀现场管理加强清洗工序的强度电镀产品表面晒纹效果尽量要均匀电镀现场管理加强对电流强度的管理电镀现场管理加强镀 Cr工艺的强度管理按时对电镀缸内的电镀液进行清洁,俗称‘清缸’提高产品表面的抛光精度 ( 半光产品抛光精度要求较高 8000N以上,全光产品抛光精度5000N以上)目前还没有非常有效的手段可以解决此问题,现行的改善方案为 : 电镀过程中后工序清洗追加超声波清洗以提高清洗的强度,另外对电镀完成品高温烘烤降低电镀品内部发生化学反应的可能性。
电镀不良及对策
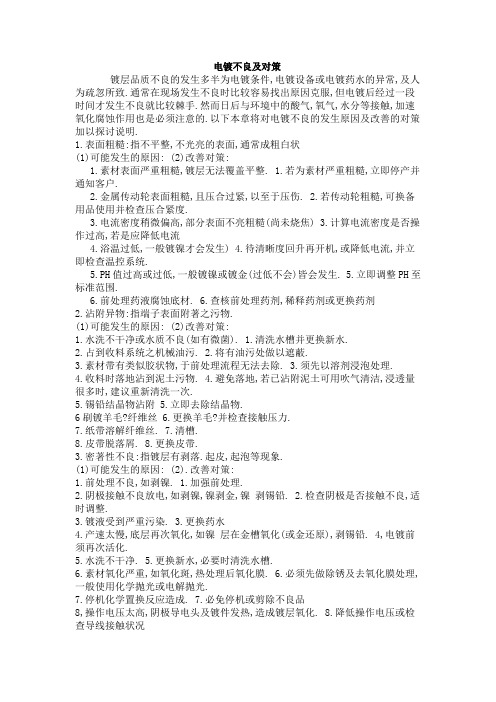
电镀不良及对策镀层品质不良的发生多半为电镀条件,电镀设备或电镀药水的异常,及人为疏忽所致.通常在现场发生不良时比较容易找出原因克服,但电镀后经过一段时间才发生不良就比较棘手.然而日后与环境中的酸气,氧气,水分等接触,加速氧化腐蚀作用也是必须注意的.以下本章将对电镀不良的发生原因及改善的对策加以探讨说明.1.表面粗糙:指不平整,不光亮的表面,通常成粗白状(1)可能发生的原因: (2)改善对策:1.素材表面严重粗糙,镀层无法覆盖平整. 1.若为素材严重粗糙,立即停产并通知客户.2.金属传动轮表面粗糙,且压合过紧,以至于压伤. 2.若传动轮粗糙,可换备用品使用并检查压合紧度.3.电流密度稍微偏高,部分表面不亮粗糙(尚未烧焦) 3.计算电流密度是否操作过高,若是应降低电流4.浴温过低,一般镀镍才会发生) 4.待清晰度回升再开机,或降低电流,并立即检查温控系统.5.PH值过高或过低,一般镀镍或镀金(过低不会)皆会发生. 5.立即调整PH至标准范围.6.前处理药液腐蚀底材. 6.查核前处理药剂,稀释药剂或更换药剂2.沾附异物:指端子表面附著之污物.(1)可能发生的原因: (2)改善对策:1.水洗不干净或水质不良(如有微菌). 1.清洗水槽并更换新水.2.占到收料系统之机械油污. 2.将有油污处做以遮蔽.3.素材带有类似胶状物,于前处理流程无法去除. 3.须先以溶剂浸泡处理.4.收料时落地沾到泥土污物. 4.避免落地,若已沾附泥土可用吹气清洁,浸透量很多时,建议重新清洗一次.5.锡铅结晶物沾附 5.立即去除结晶物.6刷镀羊毛?纤维丝 6.更换羊毛?并检查接触压力.7.纸带溶解纤维丝. 7.清槽.8.皮带脱落屑. 8.更换皮带.3.密著性不良:指镀层有剥落.起皮,起泡等现象.(1)可能发生的原因: (2).改善对策:1.前处理不良,如剥镍. 1.加强前处理.2.阴极接触不良放电,如剥镍,镍剥金,镍剥锡铅. 2.检查阴极是否接触不良,适时调整.3.镀液受到严重污染. 3.更换药水4.产速太慢,底层再次氧化,如镍层在金槽氧化(或金还原),剥锡铅. 4,电镀前须再次活化.5.水洗不干净. 5.更换新水,必要时清洗水槽.6.素材氧化严重,如氧化斑,热处理后氧化膜. 6.必须先做除锈及去氧化膜处理,一般使用化学抛光或电解抛光.7.停机化学置换反应造成. 7.必免停机或剪除不良品8,操作电压太高,阴极导电头及镀件发热,造成镀层氧化. 8.降低操作电压或检查导线接触状况9,底层电镀不良(如烧焦),造成下一层剥落. 9.改善底层电镀品质.10.严重.烧焦所形成剥落 10.参考NO12处理对策.4.露铜:可清楚看见铜色或黄黑色于低电流处(凹槽处)(1)可能发生原因: (2)改善对策:1.前处理不良,油脂,氧化物.异物尚未除去,镀层无法析出. 1.加强前处理或降低产速2.操作电流密度太低,导致低电流区,镀层无法析出. 2.重新计算电镀条件.3镍光泽剂过量,导致低电流区,镀层无法析出 3.处理药水,去除过多光泽剂或更新.4.严重刮伤造成露铜. 4.检查电镀流程,(查参考NO5)5.未镀到. 5.调整电流位置.5刮伤:指水平线条状,一般在锡铅镀层比较容易发生.(1)可能发生的原因: (2)改善对策:1.素材本身在冲压时,及造成刮伤. 1.停止生产,待与客户联系.2.被电镀设备中的金属制具刮伤,如阴极头,烤箱定位器,导轮等. 2.检查电镀流程,适时调整设备和制具.3.被电镀结晶物刮伤. 3.停止生产,立即去除结晶物.6.变形(刮歪):指端子形状已经偏离原有尺寸或位置.(1)可能发生的原因: (2)改善对策:1.素材本身在冲压时,或运输时,即造成变形. 1.停止生产,待与客户联系.2.被电镀设备,制具刮歪(如吹气.定位器,振荡器,槽口,回转轮) 2.检查电镀流程,适时调整设备和制具.3.盘子过小或卷绕不良,导致出入料时刮歪 3.停止生产,适时调整盘子4.传动轮转歪, 4.修正传动轮或变更传动方式.7壓傷:指不規則形狀之凹洞可能發生的原因:改善對策:1)本身在沖床加工時,已經壓傷,鍍層無法覆蓋平整2)傳動輪松動或故障不良,造成壓合時傷到 1)停止生産,待與客戶聯2)檢查傳動機構,或更換備品8白霧:指鍍層表面卡一層雲霧狀,不光亮但平整可能發生的原因:1)前處理不良2)鍍液受污染3)錫鉛層愛到酸腐蝕,如停機時受到錫鉛液腐蝕4)錫鉛藥水溫度過高5)錫鉛電流密度過低6)光澤劑不足7)傳致力輪髒污8)錫鉛電久進,産生泡沫附著造成改善對策:1)加強前處理2)更換藥水並提純污染液3)避免停機,若無法避免時,剪除不良4)立即檢查溫控系統,並重新設定溫度5)提高電流密度6)補足不澤劑傳動輪7)清潔傳動輪8)立即去除泡沫9針孔:指成群、細小圓洞狀(似被鍾紮狀)可能發生的原因:改善對策:1.操作的電流密度太 1.降低電流密度2.电镀溶液表面张力过大,湿润剂不足。
电镀加工出现问题的原因及解决办法
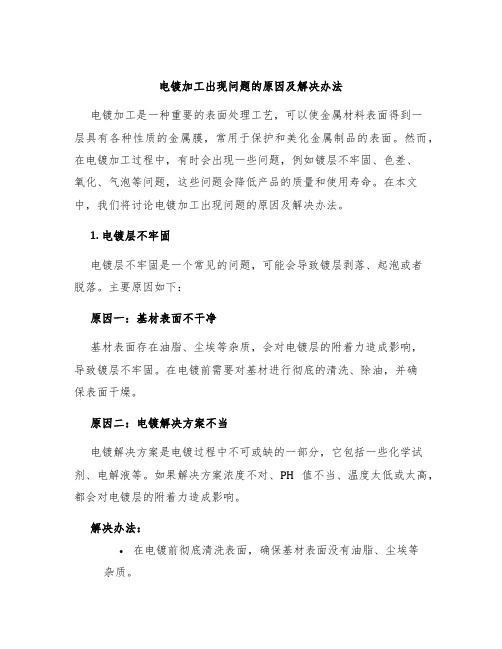
电镀加工出现问题的原因及解决办法电镀加工是一种重要的表面处理工艺,可以使金属材料表面得到一层具有各种性质的金属膜,常用于保护和美化金属制品的表面。
然而,在电镀加工过程中,有时会出现一些问题,例如镀层不牢固、色差、氧化、气泡等问题,这些问题会降低产品的质量和使用寿命。
在本文中,我们将讨论电镀加工出现问题的原因及解决办法。
1. 电镀层不牢固电镀层不牢固是一个常见的问题,可能会导致镀层剥落、起泡或者脱落。
主要原因如下:原因一:基材表面不干净基材表面存在油脂、尘埃等杂质,会对电镀层的附着力造成影响,导致镀层不牢固。
在电镀前需要对基材进行彻底的清洗、除油,并确保表面干燥。
原因二:电镀解决方案不当电镀解决方案是电镀过程中不可或缺的一部分,它包括一些化学试剂、电解液等。
如果解决方案浓度不对、PH值不当、温度太低或太高,都会对电镀层的附着力造成影响。
解决办法:•在电镀前彻底清洗表面,确保基材表面没有油脂、尘埃等杂质。
•在电镀解决方案中,加入一些添加剂,例如促进剂、增容剂等,来增强电镀层的附着力。
2. 镀层色差在电镀过程中,有时会出现镀层色差的问题,主要原因如下:原因一:电解液浓度不均电解液浓度的不均匀会导致镀层颜色不均匀。
例如,电解液中某些添加剂如果浓度过高或者过低,都可能导致镀层颜色的不同。
原因二:镀层表面存在缺陷镀层表面存在气泡、孔洞等缺陷也会导致镀层颜色不均匀。
解决办法:•定期检查电解液浓度,确保其均匀。
•彻底清洗基材的表面,确保表面无污染和缺陷。
3. 氧化问题氧化是电镀过程中另一个常见的问题,可以影响镀层的附着力和外观。
主要原因如下:原因一:电解液中的氧化物电解液中含有氧化物,而这些氧化物经常与电解液中的金属离子发生反应,从而导致镀层表面氧化。
原因二:镀层表面缺氧缺乏足够的电解气体氧分子也会导致金属离子表面氧化。
解决办法:•检查电解液中氧化物的含量,并确定其是否应该加入或减少。
•向电解液中添加抗氧化剂。
电镀常见的问题及解决方案

电镀常见的问题及解决方案
电镀过程中可能出现的问题及其解决方案如下:
1.针孔或麻点:这是由于前处理不良、有金属杂质、硼酸含量太少、镀液温度太低等原因造成的。
可以使用润湿剂来减小影响,并严格控制镀液维护及流程。
2.结合力低:如果铜镀层未经活化去氧化层,铜和镍之间的附着力就差,会产生镀层剥落现象。
因此,在电镀前应对基材进行适当的预处理,如酸洗、活化等。
3.镀层脆、可焊性差:这通常是由于有机物或重金属物质污染造成的。
添加剂过多会使镀层中夹带的有机物和分解产物增多,此时可以用活性炭处理或电解等方法除去重金属杂质。
4.镀层发暗和色泽不均匀:有金属污染可能是造成这一问题的原因。
应尽量减少挂具所沾的铜溶液,并在发现污染时立即处理。
5.镀层烧伤:这可能是由于硼酸不足、金属盐的浓度低、工作温度太低、电流密度太高、PH值太高或搅拌不充分等原因造成的。
需要检查并调整相关工艺参数,确保其处于合适的范围。
6.沉积速率低:PH值低或电流密度低都可能导致沉积速率低。
应检查并调整镀液的PH值和电流密度,以优化沉积速率。
7.其他问题:如辅助阳极的铜条未与生产板长度一致或已发粗,不允许再使用。
全板及图形镀后板需在24小时内制作下工序。
图形镀上板戴细纱手套,下板戴棕胶手套,全板上板戴橡胶手套,下板戴干燥的粗纱手套。
在处理电镀问题时,需要综合考虑多个因素,包括镀液成分、设备状况、操作条件等。
如遇到难以解决的问题,建议寻求专业人士的帮助。
电镀不良的一些情况和解决方法

电镀不良的一些情况和解决方法电镀不良对策镀层品质不良的发生多半为电镀条件,电镀设备或电镀药水的异常,及人为疏忽所致.通常在现场发生不良时比较容易找出塬因克服,但电镀后经过一段时间才发生不良就比较棘手.然而日后与环境中的酸气,氧气,水分等接触,加速氧化腐蚀作用也是必须注意的.以下本章将对电镀不良的发生塬因及改善的对策加以探讨说明.1.表面粗糙:指不平整,不光亮的表面,通常成粗白状(1)可能发生的塬因: (2)改善对策:1.素材表面严重粗糙,镀层无法覆盖平整. 1.若为素材严重粗糙,立即停产并通知客户.2.金属传动轮表面粗糙,且压合过紧,以至于压伤. 2.若传动轮粗糙,可换备用品使用并检查压合紧度.3.电流密度稍微偏高,部分表面不亮粗糙(尚未烧焦) 3.计算电流密度是否操作过高,若是应降低电流4.浴温过低,一般镀镍才会发生) 4.待清晰度回升再开机,或降低电流,并立即检查温控系统.5.PH值过高或过低,一般镀镍或镀金(过低不会)皆会发生. 5.立即调整PH至标准范围.6.前处理药液腐蚀底材. 6.查核前处理药剂,稀释药剂或更换药剂2.沾附异物:指端子表面附着之污物.(1)可能发生的塬因: (2)改善对策:1.水洗不干净或水质不良(如有微菌). 1.清洗水槽并更换新水.2.占到收料系统之机械油污. 2.将有油污处做以遮蔽.3.素材带有类似胶状物,于前处理流程无法去除. 3.须先以溶剂浸泡处理.4.收料时落地沾到泥土污物. 4.避免落地,若已沾附泥土可用吹气清洁,浸透量很多时,建议重新清洗一次.5.锡铅结晶物沾附 5.立即去除结晶物.6刷镀羊毛?纤维丝 6.更换羊毛?并检查接触压力.7.纸带溶解纤维丝. 7.清槽.8.皮带脱落屑. 8.更换皮带.3.密着性不良:指镀层有剥落.起皮,起泡等现象.(1)可能发生的塬因: (2).改善对策:1.前处理不良,如剥镍. 1.加强前处理.2.阴极接触不良放电,如剥镍,镍剥金,镍剥锡铅. 2.检查阴极是否接触不良,适时调整.3.镀液受到严重污染. 3.更换药水4.产速太慢,底层再次氧化,如镍层在金槽氧化(或金还塬),剥锡铅. 4,电镀前须再次活化.5.水洗不干净. 5.更换新水,必要时清洗水槽.6.素材氧化严重,如氧化斑,热处理后氧化膜. 6.必须先做除锈及去氧化膜处理,一般使用化学抛光或电解抛光.7.停机化学置换反应造成. 7.必免停机或剪除不良品8,操作电压太高,阴极导电头及镀件发热,造成镀层氧化. 8.降低操作电压或检查导线接触状况9,底层电镀不良(如烧焦),造成下一层剥落. 9.改善底层电镀品质.10.严重.烧焦所形成剥落 10.参考NO12处理对策.4.露铜:可清楚看见铜色或黄黑色于低电流处(凹槽处)(1)可能发生塬因: (2)改善对策:1.前处理不良,油脂,氧化物.异物尚未除去,镀层无法析出. 1.加强前处理或降低产速2.操作电流密度太低,导致低电流区,镀层无法析出. 2.重新计算电镀条件.3镍光泽剂过量,导致低电流区,镀层无法析出 3.处理药水,去除过多光泽剂或更新.4.严重刮伤造成露铜. 4.检查电镀流程,(查参考NO5)5.未镀到. 5.调整电流位置.5刮伤:指水平线条状,一般在锡铅镀层比较容易发生.(1)可能发生的塬因: (2)改善对策:1.素材本身在冲压时,及造成刮伤. 1.停止生产,待与客户联系.2.被电镀设备中的金属制具刮伤,如阴极头,烤箱定位器,导轮等. 2.检查电镀流程,适时调整设备和制具.3.被电镀结晶物刮伤. 3.停止生产,立即去除结晶物.6.变形(刮歪):指端子形状已经偏离塬有尺寸或位置.(1)可能发生的塬因: (2)改善对策:1.素材本身在冲压时,或运输时,即造成变形. 1.停止生产,待与客户联系.2.被电镀设备,制具刮歪(如吹气.定位器,振荡器,槽口,回转轮) 2.检查电镀流程,适时调整设备和制具.3.盘子过小或卷绕不良,导致出入料时刮歪 3.停止生产,适时调整盘子4.传动轮转歪, 4.修正传动轮或变更传动方式.7压伤:指不规则形状之凹洞可能发生的塬因:改善对策:1)本身在冲床加工时,已经压伤,镀层无法覆盖平整2)传动轮松动或故障不良,造成压合时伤到 1)停止生産,待与客户联2)检查传动机构,或更换备品8白雾:指镀层表面卡一层云雾状,不光亮但平整可能发生的塬因:1)前处理不良2)镀液受污染3)锡铅层爱到酸腐蚀,如停机时受到锡铅液腐蚀4)锡铅药水温度过高5)锡铅电流密度过低6)光泽剂不足7)传致力轮脏污8)锡铅电久进,産生泡沫附着造成改善对策:1)加强前处理2)更换药水并提纯污染液3)避免停机,若无法避免时,剪除不良4)立即检查温控系统,并重新设定温度5)提高电流密度6)补足不泽剂传动轮7)清洁传动轮8)立即去除泡沫9针孔:指成群、细小圆洞状(似被钟扎状)可能发生的塬因:改善对策:1.操作的电流密度太 1.降低电流密度2.电镀溶液表面张力过大,湿润剂不足。
金属电镀出现不良现象的原因与解决方法
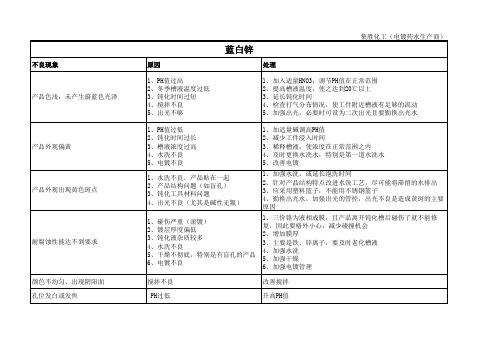
钝化外观偏浅(呈蓝带黄或金黄)
孔位颜色过深
钝化外观不均
耐腐蚀性能达不到要求
孔位周围发白
孔位颜色过深,呈现焦黄色
钝化后工件发花(呈地图纹状)
1、pH值过高 2、药液杂质过多 3、槽液浓度偏低 ①PH值过高 ②时间过短 ③Cr3+浓度低
1、调整pH值 2、排去1/5旧槽液,重新以原液补充添加 3、补加A01-435DC ①加入适量硝酸 ②延长钝化时间 ③ 加入适量原液 ①加入硝酸 ②排污,补充建浴液 ③加强搅拌 ①加碱升高PH值
产品颜色过浅,呈金黄色而不是五彩
①PH值过高 颜色不均匀,产品出现花斑(地图状花纹) ②或杂质太多 ③槽液循环搅拌不良 孔位发白、工件边缘泛紫光 ①PH值过低
黑锌
不良现象 原因 1、PH值过低 2、槽液中铁离子过高 3、槽液温度过高 4、钝化时间过短 5、B剂浓度不足 6、电镀外观过于光亮 1、pH值偏低 2、温度偏高 3、钝化时间过短 4、搅拌不足 1、pH值偏低 2、钝化时间过长 3、槽液温度偏高 处理 1、校正酸度计,调整PH值至操作范围 2、更新部份槽液或重新建浴 3、降低槽液温度 4、延长钝化时间 5、适当补充B剂 6、调整电镀 1、调高pH值至操作范围 2、降低温度 3、适当延长钝化时间 4、增强搅拌 1、调高pH值至操作范围 2、缩短钝化时间 3、降低温度
1)镀液中锌离子浓度应维持在10~15g/L 2)保持槽液温度20~30℃ 3)见A项第2点 4)控制氢氧化钠浓度在100~150g/L保持氢氧化钠与锌离子浓 度之比在10~12之间。 1)分析调整。控制锌离子浓度在10~15g/L,氢氧化钠浓度与 锌离子的比值10~12为宜。 2)适量补加A02-350A光剂。 3)降低电流密度。 4)保持槽液温度20~30℃。 1)分析调整,控制锌离子浓度在10~15g/L,氢氧化钠浓度与 锌离子的比值10~12为宜。 2)根据霍尔槽试片,适量补加A02-350B光剂。 3)提高电流密度。 1)在工艺允许使用范围内提高锌离子浓度。 2)根据霍尔槽试片,适量补加A02-350A光剂。 3)加净化剂C或软水剂D。 4)加强前处理。 适当增加A02-350B用量;在过滤机加入锌粉及助滤剂硅藻土以除 杂
- 1、下载文档前请自行甄别文档内容的完整性,平台不提供额外的编辑、内容补充、找答案等附加服务。
- 2、"仅部分预览"的文档,不可在线预览部分如存在完整性等问题,可反馈申请退款(可完整预览的文档不适用该条件!)。
- 3、如文档侵犯您的权益,请联系客服反馈,我们会尽快为您处理(人工客服工作时间:9:00-18:30)。
镀层品质不良的发生多半为电镀条件,电镀设备或电镀药水的异常,及人为疏忽所致.通常在现场发生不良时比较容易找出塬因克服,但电镀后经过一段时间才发生不良就比较棘手.然而日后与环境中的酸气,氧气,水分等接触,加速氧化腐蚀作用也是必须注意的.以下本章将对电镀不良的发生塬因及改善的对策加以探讨说明.1.表面粗糙:指不平整,不光亮的表面,通常成粗白状(1)可能发生的塬因:(2)改善对策:1.素材表面严重粗糙,镀层无法覆盖平整. 1.若为素材严重粗糙,立即停产并通知客户.2.金属传动轮表面粗糙,且压合过紧,以至于压伤. 2.若传动轮粗糙,可换备用品使用并检查压合紧度.3.电流密度稍微偏高,部分表面不亮粗糙(尚未烧焦) 3.计算电流密度是否操作过高,若是应降低电流4.浴温过低,一般镀镍才会发生) 4.待清晰度回升再开机,或降低电流,并立即检查温控系统.5.PH值过高或过低,一般镀镍或镀金(过低不会)皆会发生. 5.立即调整PH至标准范围.6.前处理药液腐蚀底材. 6.查核前处理药剂,稀释药剂或更换药剂2.沾附异物:指端子表面附着之污物.(1)可能发生的塬因: (2)改善对策:1.水洗不干净或水质不良(如有微菌). 1.清洗水槽并更换新水.2.占到收料系统之机械油污. 2.将有油污处做以遮蔽.3.素材带有类似胶状物,于前处理流程无法去除. 3.须先以溶剂浸泡处理.4.收料时落地沾到泥土污物. 4.避免落地,若已沾附泥土可用吹气清洁,浸透量很多时,建议重新清洗一次.5.锡铅结晶物沾附5.立即去除结晶物.6刷镀羊毛?纤维丝6.更换羊毛?并检查接触压力.7.纸带溶解纤维丝. 7.清槽.8.皮带脱落屑. 8.更换皮带.3.密着性不良:指镀层有剥落.起皮,起泡等现象.(1)可能发生的塬因: (2).改善对策:1.前处理不良,如剥镍. 1.加强前处理.2.阴极接触不良放电,如剥镍,镍剥金,镍剥锡铅. 2.检查阴极是否接触不良,适时调整.3.镀液受到严重污染. 3.更换药水4.产速太慢,底层再次氧化,如镍层在金槽氧化(或金还塬),剥锡铅. 4,电镀前须再次活化.5.水洗不干净. 5.更换新水,必要时清洗水槽.6.素材氧化严重,如氧化斑,热处理后氧化膜. 6.必须先做除锈及去氧化膜处理,一般使用化学抛光或电解抛光.7.停机化学置换反应造成. 7.必免停机或剪除不良品8,操作电压太高,阴极导电头及镀件发热,造成镀层氧化. 8.降低操作电压或检查导线接触状况9,底层电镀不良(如烧焦),造成下一层剥落. 9.改善底层电镀品质.10.严重.烧焦所形成剥落10.参考NO12处理对策.4.露铜:可清楚看见铜色或黄黑色于低电流处(凹槽处)(1)可能发生塬因: (2)改善对策:1.前处理不良,油脂,氧化物.异物尚未除去,镀层无法析出. 1.加强前处理或降低产速2.操作电流密度太低,导致低电流区,镀层无法析出. 2.重新计算电镀条件.3.镍光泽剂过量,导致低电流区,镀层无法析出3.处理药水,去除过多光泽剂或更新.4.严重刮伤造成露铜. 4.检查电镀流程,(查参考NO5)5.未镀到. 5.调整电流位置.5刮伤:指水平线条状,一般在锡铅镀层比较容易发生.(1)可能发生的塬因: (2)改善对策:1.素材本身在冲压时,及造成刮伤. 1.停止生产,待与客户联系.2.被电镀设备中的金属制具刮伤,如阴极头,烤箱定位器,导轮等. 2.检查电镀流程,适时调整设备和制具.3.被电镀结晶物刮伤. 3.停止生产,立即去除结晶物.6.变形(刮歪):指端子形状已经偏离塬有尺寸或位置.(1)可能发生的塬因: (2)改善对策:1.素材本身在冲压时,或运输时,即造成变形. 1.停止生产,待与客户联系.2.被电镀设备,制具刮歪(如吹气.定位器,振荡器,槽口,回转轮) 2.检查电镀流程,适时调整设备和制具.3.盘子过小或卷绕不良,导致出入料时刮歪3.停止生产,适时调整盘子4.传动轮转歪, 4.修正传动轮或变更传动方式.7压伤:指不规则形状之凹洞可能发生的塬因:改善对策:1)本身在冲床加工时,已经压伤,镀层无法覆盖平整2)传动轮松动或故障不良,造成压合时伤到1)停止生産,待与客户联2)检查传动机构,或更换备品8白雾:指镀层表面卡一层云雾状,不光亮但平整可能发生的塬因:1)前处理不良2)镀液受污染3)锡铅层爱到酸腐蚀,如停机时受到锡铅液腐蚀4)锡铅药水温度过高5)锡铅电流密度过低6)光泽剂不足7)传致力轮脏污8)锡铅电久进,産生泡沫附着造成改善对策:1)加强前处理2)更换药水并提纯污染液3)避免停机,若无法避免时,剪除不良4)立即检查温控系统,并重新设定温度5)提高电流密度6)补足不泽剂传动轮7)清洁传动轮8)立即去除泡沫9针孔:指成群、细小圆洞状(似被钟扎状)可能发生的塬因:改善对策:1.操作的电流密度太1.降低电流密度2.电镀溶液表面张力过大,湿润剂不足。
2.补充湿润剂,或检查药水。
3.电镀时间搅拌效果不良。
3.加强搅拌。
4.锡铅浴温过低4.调整浴温5.电镀药水受到污染。
5.提纯药水或者更新。
6.前处理不良。
6.加强前处理效果。
10.锡铅重熔:指镀层表面有如山丘平塬状(似起泡,但密着性良好),只有锡铅镀层会发生。
(1)可能发生的塬因: (2)改善对策:1.锡铅阴极过热(电压太高),导致锡铅层重熔。
1.降低电压,并了解为何浴电压过高,在进行修正电镀条件。
2.烤箱温度过高,且烘烤时间过长,导致锡铅层重熔。
2.降低烤箱温度,并检查温控系统。
11.端子熔融:指表面有受热熔成凹洞状,通常是在铜素材(镀镍前)或锡铅电镀时造成。
(1)可能发生的塬因: (2)改善对策:1.镀镍前或锡铅电镀间的阴极接触不良,放电火花将铜材熔成凹洞。
1.检查阴极,并适时调整。
12.镀层烧焦:指镀层表面严重黑暗,粗糙,如碳色一般。
(指高电流密度区)(1)可能发生的塬因: (2)改善对策:1.操作电流密度过高。
1.降低电流密度。
2.浴温过低。
2.提高浴温,并检查温控系统。
3.搅拌不良。
3.增加搅拌效果。
4.光泽剂不足。
4.补足光泽剂。
5.PH值过高。
5.修正PH值至标准范围。
6.选镀位置不当。
(电子流曲线) 6.重新修正电镀位置,注意电流分布线。
7.整流器滤波不良。
7.检查滤波度是否符合标准,若偏移时须将整流器送修。
13.电镀厚度太高:指实际镀出膜厚超出预计的厚度。
(1)可能发生的塬因: (2)改善对策:1.传动速度变慢,不准或速度不稳定。
1.检查传动系统,校正产速。
2.电流太高,不准或电流不稳定。
2.检查整流器与阴阳极,适时予以修正。
3.选镀位置变异。
3.检查电镀位置是否偏离,重新调整。
4.药水金属浓度升高,一般镀金较敏感。
4.调整电流或传动速度。
5.药水PH值过高。
5.调整PH值至标准范围。
6.荧光膜厚测试仪偏离,或测试方法错误。
6.校正仪器或确定测试方法。
7.浴温偏高。
7.检查温控系统。
14.电镀厚度不足:指实际镀出膜厚低于预计的厚度(1)可能发生的塬因: (2)改善对策:1.传动速度变快,不准或速度不稳定。
1.检查传动系统,校正产速。
2.电流太低,不准或电流不稳定。
2.检查整流器与阴阳极,适时予以修正。
3.选镀位置变异。
3.检查电镀位置是否偏离,重新调整。
4.药水金属浓度降低,或药水被稀释。
4.调整电流或传动速度,必要时须停产。
5.药水PH值偏低。
5.调整PH值至标准范围。
6.荧光膜厚测试仪偏离,或测试方法错误。
6.校正仪器或确定测试方法。
7.浴温偏低。
7.检查温控系统,必要时须停产。
8.镀层结构中有结金,消耗掉部分电流。
8.去除结金物或更换制具。
9.电镀药水搅拌,循环不均或金属补充不及消耗。
9.改善药水循环或补充状况。
15.电镀厚度不均:指实际镀出膜厚时高时低,或分布不均。
(1)可能发生的塬因: (2)改善对策:1.传动速度不稳定。
1.检查传动系统,校正产速。
2.电流不稳定。
2.检查整流器与阴阳极,适时予以修正。
3.端子严重变形,造成选镀位置不稳定。
3.检查电镀位置是否偏离,若素材严重变形制程无法改善,须停产。
4.端子结构造成高低电流分布不均。
4.调整电镀位置,增加搅拌效果。
5.搅拌效果不良。
5.增加搅拌效果。
6.膜厚测试位置有问题,造成误差大。
6.须重新修定测试位置。
7.选镀机构不稳定。
7.改善选镀机构。
16.镀层暗红:通常指金色泽偏暗偏红。
(1)可能发生的塬因: (2)改善对策:1.镀金药水偏离。
1.重新调整电镀药水。
2.镀层粗糙,烧白再覆盖金层即变红。
2.改善镍层不良。
3.水洗水不净,造成红斑。
3.更换水洗水。
4.镀件未完全干燥,日后氧化发红。
4.检查干燥系统,确定镀件干燥,已发红的端子,可以用稀氰化物清洗。
17.界面黑线,雾线:通常在半镀锡铅层的界面有此现象。
(1)可能发生的塬因: (2)改善对策:1.阴极反应太大,大量氢气泡沫浮于液面。
1.降低电流。
2.阴极搅拌不良。
2.调整振荡器的频率和振幅。
3. 选镀高度调整不均。
3.检查选镀高度,重新修正。
4.镀槽设计不良,造成泡沫残存于镀槽液面,无法排除。
4.改善镀槽结构。
5.锡铅药水低电流区白雾。
5.修正锡铅药水至最佳槽况。
6.整流器滤波不良。
6.用示波器测量滤波度,确定滤波不良时,检修整流器。
18.焊锡不良:指锡铅镀层沾锡能力不佳。
(1)可能发生的塬因: (2)改善对策:1.锡铅电镀液受到污染。
1.更换锡铅药水。
2.光泽剂过量,造成镀层碳含量过多。
2.立即作活性炭过滤,或更换药水。
3. 电镀后处理不良(酸液残存,水质不佳,盐类生成,异物附着)。
3.改善流程,改善水质4.密着不良4.解决密着不良问题。
5.电镀时电压过高,造成镀件受热氧化,钝化5.改善导电设备。
6.电流密度过高致镀层结构不良。
6.降低电流密度。
7.搅拌不良致镀层结构不良。
7.增加搅拌效果。
8.浴温过高,致镀层结构不良。
8.立即降低浴温并检查冷却系统。
9.镀层因放置环境较差,时间过久,致镀层氧化,老化。
9.加强包装及改善储存环境。
10.镀层太薄10.增加电镀层厚度。
11.焊锡温度不正确。
11.检查焊锡温度。
12.镀件形状构造影响。
12.改变判定方法。
13.焊剂不纯物过高。
13.更换焊剂。
14.镀件材质的影响(锡>锡铅>金>铜>磷青铜>黄铜) 14.探讨材质。
15.镀件表面有异物,如油污。
15.去除异物。
16.底层粗糙。
16.改善底层平整度。
19.镀层发黑:不包含烧焦的黑及锡铅界面的黑线。
(1)可能发生的塬因: (2)改善对策:1.锡铅镀层塬已有白雾,日后变黑。
1.参考第8,处理锡铅白雾的对策。
2.镍槽已经受到污染,在低电流区会有黑色镀层。
2.做活性炭处理,或弱电解处理。
3. 镀件受氧化严重发黑腐蚀。
3.须做分析探讨塬因。