消除注塑产品缺陷指南
注塑常见缺陷的解决方法

注塑常见缺陷的解决方法注塑是一种常见的制造工艺,可以用于生产各种塑料制品。
然而,在注塑过程中常常会出现一些缺陷,如翘曲、气泡、短射等。
这些缺陷会降低产品的质量,影响使用效果。
因此,解决这些缺陷是注塑加工中重要的一环。
下面是一些常见缺陷的解决方法:1.翘曲:翘曲是指注塑制品的形状变形,不符合设计要求。
翘曲的原因可能是注塑温度过高、材料流动不均匀等。
解决方法包括:优化注塑工艺参数,例如调整注塑温度、压力、速度等;增加型腔冷却方式,以提高产品的冷却效果;使用合适的塑料料种,如改变注塑材料的配方,选择更具平衡性能的材料。
2.气泡:气泡是指注塑制品中出现的气体孔洞,影响了产品的外观和性能。
气泡的形成可能是由于注塑材料中的挥发性成分未完全排除、注塑机排气不良等原因。
解决方法包括:增加注塑所需的压力和温度,以促使挥发性成分完全排出;改善注塑机的排气系统,有效排除气泡。
3.短射:短射是指注塑过程中,塑料流动未能充满整个模具的情况。
短射的原因可能是注塑料温度过低、注塑机压力不足、型腔阻力过大等。
解决方法包括:提高注塑温度和压力,以增加塑料的流动性;改善模具的设计,减少型腔的阻力;检查注塑机的喷嘴和螺杆是否损坏,及时更换。
4.热流线:热流线是指注塑制品表面出现的不均匀纹路,影响产品的外观。
热流线的形成可能是由于塑料流动速度过快、模具温度不均匀等原因。
解决方法包括:调整注塑机的喷嘴和螺杆速度,控制塑料的流动速度;优化模具的冷却系统,使模具温度均匀分布。
5.尺寸偏差:尺寸偏差是指注塑制品的尺寸与设计要求不符,可能是由于模具磨损、注塑工艺参数不恰当等原因。
解决方法包括:定期检查和修复模具,以保证模具的精度;优化注塑工艺参数,例如调整注射时间、压力和温度,以控制产品的尺寸。
总的来说,解决注塑常见缺陷需要综合考虑材料、工艺和设备等方面的因素。
通过不断优化参数和改进工艺,可以改善产品的质量,提高注塑加工的效率。
此外,定期维护和保养注塑设备和模具也是预防和解决缺陷的重要措施。
注塑缺陷描述及解决方案

注塑缺陷描述及解决方案引言概述:注塑技术是一种常用的塑料成型工艺,广泛应用于各个行业。
然而,在注塑过程中,常常会出现一些缺陷,如气泡、热胀冷缩、短射等问题,这些缺陷会影响产品的质量和性能。
本文将从五个大点出发,详细阐述注塑缺陷的描述及解决方案。
正文内容:1.注塑缺陷:气泡1.1 气泡的描述:气泡是注塑过程中常见的缺陷之一。
它们通常出现在产品的内部或表面,给产品的外观和性能带来负面影响。
1.2 气泡的解决方案:1.2.1 调整注塑机的压力和温度,确保塑料完全熔化,减少气体残留。
1.2.2 优化模具结构,增加通气口,促使气泡顺利排出。
1.2.3 使用抗气泡剂或改性剂,减少气泡的生成。
2.注塑缺陷:热胀冷缩2.1 热胀冷缩的描述:热胀冷缩是由于注塑过程中塑料的热胀冷缩性质导致的缺陷。
它会导致产品尺寸不准确,甚至造成产品变形。
2.2 热胀冷缩的解决方案:2.2.1 选择合适的塑料材料,具有较小的热胀冷缩系数。
2.2.2 控制模具温度,使得塑料在注塑过程中均匀冷却,减少热胀冷缩的影响。
2.2.3 使用辅助冷却系统,如冷却水或风扇,加速产品冷却过程,减少热胀冷缩。
3.注塑缺陷:短射3.1 短射的描述:短射是指注塑过程中塑料未能充满模具腔体,导致产品缺陷。
短射通常表现为产品的一部分或整个部分未充实。
3.2 短射的解决方案:3.2.1 检查和调整注塑机的注射速度和压力,确保塑料能够充分填充模具腔体。
3.2.2 检查模具的设计和结构,确保流道和出料口的尺寸和位置合理,避免短射现象。
3.2.3 使用模具温度控制系统,确保塑料在注塑过程中保持适当的温度,减少短射的发生。
4.注塑缺陷:毛刺4.1 毛刺的描述:毛刺是指注塑过程中产生的塑料残留物,通常出现在产品的边缘或表面,影响产品的外观和质量。
4.2 毛刺的解决方案:4.2.1 优化模具设计,增加冷却系统,降低模具温度,减少毛刺的生成。
4.2.2 调整注塑机的注射速度和压力,避免过多的塑料残留。
注塑缺陷原因分析与解决方案

注塑缺陷原因分析与解决方案注塑是一种常见的塑料加工方法,广泛应用于各个行业。
然而,在注塑过程中,可能会出现各种缺陷,如气泡、翘曲、短射等问题,影响产品的质量和性能。
为了解决这些问题,我们需要进行缺陷原因分析,并提出相应的解决方案。
一、缺陷原因分析1. 气泡缺陷气泡是注塑过程中常见的缺陷之一。
其主要原因可能包括以下几个方面:- 塑料材料中含有挥发性物质,如水分、溶剂等,这些物质在高温下蒸发产生气泡。
- 注塑机温度设置不当,过高的温度会使塑料材料中的气体膨胀形成气泡。
- 注塑模具设计不合理,存在气孔或死角,导致塑料充填不均匀,形成气泡。
2. 翘曲缺陷翘曲是注塑产品常见的缺陷之一,其主要原因可能包括以下几个方面:- 注塑机温度不均匀,导致塑料材料在冷却过程中收缩不均匀,引起产品翘曲。
- 注塑模具设计不合理,存在过于薄弱的部位,无法承受注塑过程中的压力,导致产品变形。
- 注塑过程中冷却时间不足,使得产品在脱模后还未完全固化,导致变形。
3. 短射缺陷短射是指注塑产品未能充填满模具而产生的缺陷,其主要原因可能包括以下几个方面:- 注塑机温度设置不当,导致塑料材料粘度过高,无法充填满模具。
- 注塑模具设计不合理,存在过于狭窄的充填道或浇口,导致塑料流动受阻,无法充填满模具。
- 注塑过程中注射速度过快,导致塑料材料无法充填满模具。
二、解决方案1. 气泡缺陷的解决方案- 检查塑料材料的质量,确保其含水量和挥发性物质含量符合要求。
- 调整注塑机的温度,确保塑料材料在注塑过程中不会过热。
- 优化注塑模具的设计,避免气孔和死角的存在,确保塑料充填均匀。
2. 翘曲缺陷的解决方案- 调整注塑机的温度分布,确保塑料材料在冷却过程中收缩均匀。
- 优化注塑模具的设计,增加产品的结构强度,避免过于薄弱的部位。
- 增加注塑过程中的冷却时间,确保产品完全固化后再进行脱模。
3. 短射缺陷的解决方案- 调整注塑机的温度,降低塑料材料的粘度,促进充填。
注塑缺陷原因分析与解决方案
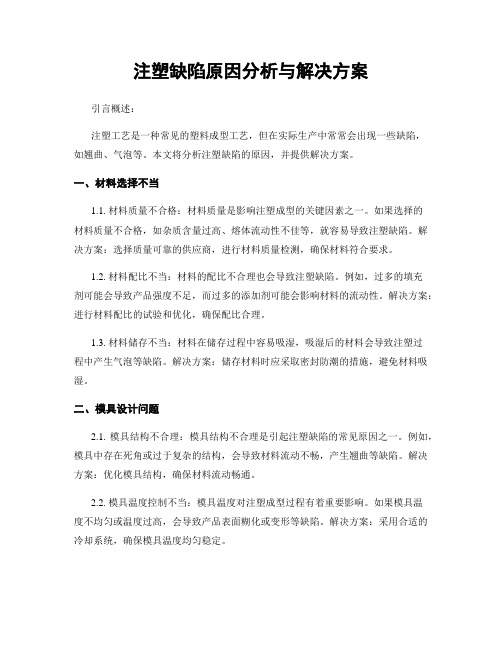
注塑缺陷原因分析与解决方案引言概述:注塑工艺是一种常见的塑料成型工艺,但在实际生产中常常会出现一些缺陷,如翘曲、气泡等。
本文将分析注塑缺陷的原因,并提供解决方案。
一、材料选择不当1.1. 材料质量不合格:材料质量是影响注塑成型的关键因素之一。
如果选择的材料质量不合格,如杂质含量过高、熔体流动性不佳等,就容易导致注塑缺陷。
解决方案:选择质量可靠的供应商,进行材料质量检测,确保材料符合要求。
1.2. 材料配比不当:材料的配比不合理也会导致注塑缺陷。
例如,过多的填充剂可能会导致产品强度不足,而过多的添加剂可能会影响材料的流动性。
解决方案:进行材料配比的试验和优化,确保配比合理。
1.3. 材料储存不当:材料在储存过程中容易吸湿,吸湿后的材料会导致注塑过程中产生气泡等缺陷。
解决方案:储存材料时应采取密封防潮的措施,避免材料吸湿。
二、模具设计问题2.1. 模具结构不合理:模具结构不合理是引起注塑缺陷的常见原因之一。
例如,模具中存在死角或过于复杂的结构,会导致材料流动不畅,产生翘曲等缺陷。
解决方案:优化模具结构,确保材料流动畅通。
2.2. 模具温度控制不当:模具温度对注塑成型过程有着重要影响。
如果模具温度不均匀或温度过高,会导致产品表面糊化或变形等缺陷。
解决方案:采用合适的冷却系统,确保模具温度均匀稳定。
2.3. 模具磨损严重:模具长时间使用后会出现磨损,磨损严重的模具会导致产品尺寸不准确或表面粗糙等缺陷。
解决方案:定期检查和维护模具,及时更换磨损严重的模具部件。
三、注塑工艺参数设置不当3.1. 注射压力过高或过低:注射压力是影响注塑成型的关键参数之一。
如果注射压力过高,会导致产品变形或开裂,而注射压力过低则会导致产品表面光洁度不高。
解决方案:根据产品要求和材料特性,合理设置注射压力。
3.2. 注射速度不合理:注射速度对产品的充填和冷却过程有着重要影响。
如果注射速度过快,会导致产品内部产生气泡或短射,而注射速度过慢则会导致产品表面瑕疵。
注塑制品缺陷的原因分析与解决措施

环境湿度变化大,影响塑料的稳定性和制品的外观。
空气污染
空气中存在灰尘、油雾等污染物,影响制品的外观和 质量。
03
注塑制品缺陷的解决措施
优化模具设计
模具设计合理化
确保模具设计符合产品要求,避免出现倒扣、 侧扣等设计不合理的地方。
避免模具损伤
提高模具的耐用性,避免使用过程中出现磨损 、断裂等问题。
优化浇口设计
合理设计浇口位置和大小,确保塑料能够均匀流入模具型腔。
把关原料质量
严格控制原料成分
确保原料中不含有杂质、异物等不良成分。
定期检测原料性能
对原料的性能进行定期检测,以确保其符合 生产要求。
加强原料存储管理
避免原料在存储过程中受潮、污染等问题。
调整工艺参数
合理调整注塑温度
根据塑料的性质和产品要求,合理调整注塑温度。
201 4
案例三:注塑制品出现银纹的原因及解决方法
原因分析
1. 塑料中含有水分或挥发性物质,导致银纹产 生。
2. 模具温度过低,导致塑料无法完全流动,出 现银纹。
案例三:注塑制品出现银纹的原因及解决方法
• 注射速度过快或压力过低,导致塑料在模具中流动不均匀,出现银纹。
案例三:注塑制品出现银纹的原因及解决方法
注塑制品缺陷的原因
分析与解决措施
汇报人:
日期:
• 注塑制品缺陷概述 • 注塑制品缺陷的原因分析 • 注塑制品缺陷的解决措施 • 注塑制品缺陷案例分析
目录
01
注塑制品缺陷概述
注塑制品常见缺陷
01 02 03 04
翘曲变形 缩痕 气泡 烧焦
注塑制品常见缺陷
01 02
溢边 裂纹
颜色差异
注塑缺陷描述及解决方案

注塑缺陷描述及解决方案注塑是一种常用的塑料加工方法,通过将熔化的塑料材料注入模具中,经过冷却固化后得到所需的塑料制品。
然而,在注塑过程中,可能会出现一些缺陷,影响产品的质量和性能。
本文将详细描述常见的注塑缺陷,并提供相应的解决方案。
一、缺陷描述1. 短射(Short Shot):指注塑过程中塑料未充满模具腔体,导致制品缺少某些部分或整体不完整。
解决方案:可能的原因包括模具温度过低、注塑速度过快、塑料材料不足等。
解决方法包括增加模具温度、调整注塑速度、增加塑料材料供给量等。
2. 翘曲(Warping):指注塑制品在冷却后产生变形,失去原本的平整形状。
解决方案:可能的原因包括模具温度不均匀、冷却时间不足、注塑压力过大等。
解决方法包括优化模具设计、增加冷却时间、减小注塑压力等。
3. 气泡(Air Traps):指注塑制品中出现气泡或空洞。
解决方案:可能的原因包括塑料材料中含有水分、注塑压力不稳定、模具排气不畅等。
解决方法包括使用干燥的塑料材料、调整注塑压力、改善模具排气系统等。
4. 热缩(Shrinkage):指注塑制品在冷却后出现尺寸缩小的现象。
解决方案:可能的原因包括模具温度过高、冷却时间不足、塑料材料收缩率不合理等。
解决方法包括降低模具温度、增加冷却时间、选择合适的塑料材料等。
5. 热裂纹(Hot Cracks):指注塑制品在冷却过程中出现裂纹。
解决方案:可能的原因包括注塑温度过高、冷却速度过快、塑料材料选择不当等。
解决方法包括降低注塑温度、控制冷却速度、选择合适的塑料材料等。
二、解决方案1. 优化模具设计:合理设计模具结构,确保充模充型均匀,避免短射、翘曲等缺陷的发生。
2. 控制注塑工艺参数:包括模具温度、注塑速度、注塑压力等。
通过调整这些参数,可以解决短射、翘曲、气泡等缺陷。
3. 选择合适的塑料材料:不同的塑料材料具有不同的性能和特点,选择合适的材料可以避免热缩、热裂纹等缺陷的发生。
4. 增加冷却时间:适当延长注塑制品的冷却时间,有助于避免翘曲、热缩等缺陷的产生。
注塑缺陷及其解决方法
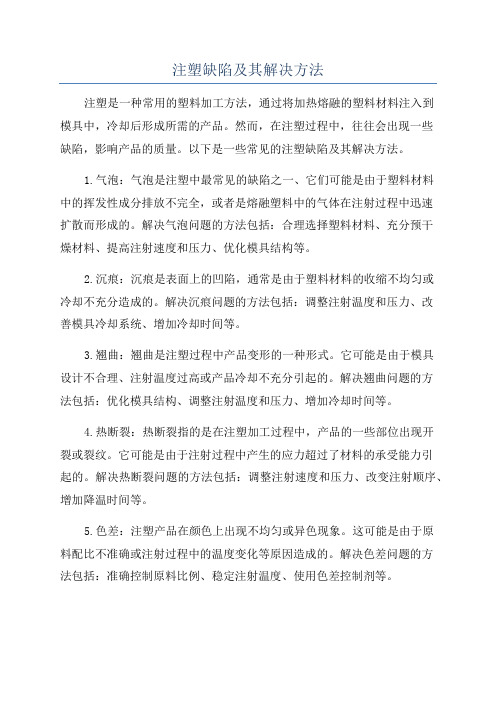
注塑缺陷及其解决方法注塑是一种常用的塑料加工方法,通过将加热熔融的塑料材料注入到模具中,冷却后形成所需的产品。
然而,在注塑过程中,往往会出现一些缺陷,影响产品的质量。
以下是一些常见的注塑缺陷及其解决方法。
1.气泡:气泡是注塑中最常见的缺陷之一、它们可能是由于塑料材料中的挥发性成分排放不完全,或者是熔融塑料中的气体在注射过程中迅速扩散而形成的。
解决气泡问题的方法包括:合理选择塑料材料、充分预干燥材料、提高注射速度和压力、优化模具结构等。
2.沉痕:沉痕是表面上的凹陷,通常是由于塑料材料的收缩不均匀或冷却不充分造成的。
解决沉痕问题的方法包括:调整注射温度和压力、改善模具冷却系统、增加冷却时间等。
3.翘曲:翘曲是注塑过程中产品变形的一种形式。
它可能是由于模具设计不合理、注射温度过高或产品冷却不充分引起的。
解决翘曲问题的方法包括:优化模具结构、调整注射温度和压力、增加冷却时间等。
4.热断裂:热断裂指的是在注塑加工过程中,产品的一些部位出现开裂或裂纹。
它可能是由于注射过程中产生的应力超过了材料的承受能力引起的。
解决热断裂问题的方法包括:调整注射速度和压力、改变注射顺序、增加降温时间等。
5.色差:注塑产品在颜色上出现不均匀或异色现象。
这可能是由于原料配比不准确或注射过程中的温度变化等原因造成的。
解决色差问题的方法包括:准确控制原料比例、稳定注射温度、使用色差控制剂等。
6.熔接线:熔接线是由于注塑模具的设计和操作问题导致两个或多个熔融塑料部分相互连接而形成的。
解决熔接线问题的方法包括:调整模具结构,避免部件交汇点过多,调整注射速度和压力等。
总之,注塑缺陷的解决方法主要包括调整材料配比、优化模具结构、控制注射温度和压力、增加冷却时间等。
同时,及时调整机器参数、进行模具维护和清洁,以保证注塑过程的稳定性和可靠性。
通过以上的措施,可以有效减少注塑缺陷,提高产品质量。
注塑缺陷描述及解决方案

注塑缺陷描述及解决方案注塑是一种常用的塑料加工方法,通过将熔融的塑料材料注入模具中,然后冷却成型,最终得到所需的产品。
然而,在注塑过程中,可能会出现一些缺陷,如气泡、短射、毛刺等,这些缺陷会降低产品质量,影响生产效率。
因此,及时发现并解决注塑缺陷是非常重要的。
首先,气泡是注塑中常见的缺陷之一、气泡通常由以下原因引起:塑料材料中含有水分、注塑机压力不稳定、模具排气不畅等。
为解决气泡缺陷,可以采取以下措施:在使用塑料材料之前对其进行干燥处理,确保材料中不含水分;调整注塑机的压力和速度,保持稳定的注塑过程;对模具进行排气孔设计,确保顺畅排气。
其次,短射是另一种常见的注塑缺陷。
短射通常是由于塑料材料流动性不好、充型不足或注塑机压力不足等原因引起的。
为解决短射问题,可以采取以下措施:选用流动性好的塑料材料,例如增加流动助剂;优化模具的设计,确保充型顺畅;调整注塑机的压力和速度,保证充型充分。
此外,毛刺也是一种常见的注塑缺陷。
毛刺通常是由于模具接缝不严、射出速度过快、注塑机压力过高等原因引起的。
为解决毛刺问题,可以采取以下措施:检查和调整模具接缝,确保接缝紧密;调整射出速度和注塑机压力,控制流动状态,减少毛刺的产生。
此外,还可能出现其他一些注塑缺陷,如烧焦、变色等。
对于这些缺陷,可以通过调整注塑工艺参数、改进模具设计、使用优质的塑料材料等方法加以解决。
总之,注塑缺陷的解决需要综合考虑塑料材料的选择、注塑机的调整以及模具设计等因素。
通过合理的工艺控制和改进,可以有效降低注塑缺陷的发生,提高产品质量和生产效率。
同时,及时发现和解决注塑缺陷也需要经验丰富的操作人员进行实时监控和调整。
注塑产品常见的13种质量缺陷原因分析及解决办法
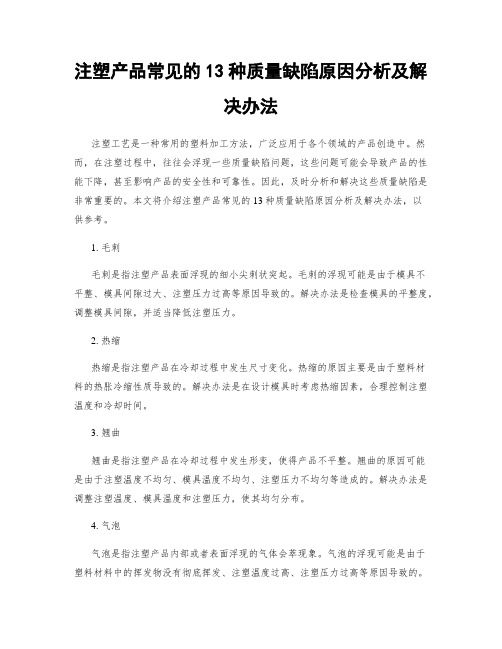
注塑产品常见的13种质量缺陷原因分析及解决办法注塑工艺是一种常用的塑料加工方法,广泛应用于各个领域的产品创造中。
然而,在注塑过程中,往往会浮现一些质量缺陷问题,这些问题可能会导致产品的性能下降,甚至影响产品的安全性和可靠性。
因此,及时分析和解决这些质量缺陷是非常重要的。
本文将介绍注塑产品常见的13种质量缺陷原因分析及解决办法,以供参考。
1. 毛刺毛刺是指注塑产品表面浮现的细小尖刺状突起。
毛刺的浮现可能是由于模具不平整、模具间隙过大、注塑压力过高等原因导致的。
解决办法是检查模具的平整度,调整模具间隙,并适当降低注塑压力。
2. 热缩热缩是指注塑产品在冷却过程中发生尺寸变化。
热缩的原因主要是由于塑料材料的热胀冷缩性质导致的。
解决办法是在设计模具时考虑热缩因素,合理控制注塑温度和冷却时间。
3. 翘曲翘曲是指注塑产品在冷却过程中发生形变,使得产品不平整。
翘曲的原因可能是由于注塑温度不均匀、模具温度不均匀、注塑压力不均匀等造成的。
解决办法是调整注塑温度、模具温度和注塑压力,使其均匀分布。
4. 气泡气泡是指注塑产品内部或者表面浮现的气体会萃现象。
气泡的浮现可能是由于塑料材料中的挥发物没有彻底挥发、注塑温度过高、注塑压力过高等原因导致的。
解决办法是控制注塑温度和压力,选择合适的塑料材料,并进行充分的挤出和干燥处理。
5. 缩孔缩孔是指注塑产品内部浮现的空洞状缺陷。
缩孔的原因可能是由于注塑温度过低、注塑压力不足、模具设计不合理等导致的。
解决办法是提高注塑温度、增加注塑压力,并优化模具设计。
6. 裂纹裂纹是指注塑产品表面或者内部浮现的裂纹状缺陷。
裂纹的浮现可能是由于注塑温度过高、注塑压力过大、冷却时间过短等原因导致的。
解决办法是降低注塑温度、减小注塑压力,并延长冷却时间。
7. 毛边毛边是指注塑产品边缘浮现的不平整现象。
毛边的原因可能是由于模具设计不合理、注塑压力过高、注塑速度过快等导致的。
解决办法是优化模具设计,降低注塑压力,并适当调整注塑速度。
常见注塑件缺陷及解决的方法
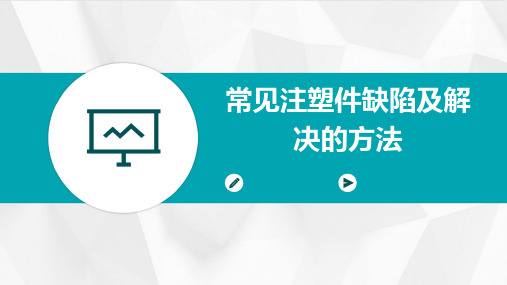
充填不足
01
总结词
充填不足是指注塑件在成型过程中未能完全填满 模具型腔,导致部分区域出现缺料或凹陷。
02
详细描述
充填不足通常是由于注射速度慢、注射压力不足、 模具温度过高或塑料流动性差等原因引起的。
缩痕
总结词
缩痕是指注塑件表面出现凹陷或收缩痕迹,影响 外观和尺寸精度。
详细描述
缩痕通常是由于塑料冷却过程中收缩率不均、模 具温度不均匀或注射压力不足等原因引起的。
常见注塑件缺陷及解 决的方法
目录
• 常见注塑件缺陷 • 注塑件缺陷原因分析 • 解决注塑件缺陷的方法 • 案例分析
01
常见注塑件缺陷
翘曲与扭曲
总结词
翘曲与扭曲是指注塑件形状发生扭曲或弯曲,不符合设 计要求。
详细描述
翘曲与扭曲通常是由于模具设计不合理、塑料收缩率差 异、注射温度和压力不适当等原因引起的。
环境条件的控制Байду номын сангаас
总结词
保持稳定的环境条件对注塑件的质量至关重 要,包括温度、湿度和清洁度等。
详细描述
确保注塑车间温度、湿度稳定,保持环境清 洁、无尘。定期对设备和环境进行清理和消 毒,防止污染和细菌滋生。同时,要关注天 气变化和季节性温差对注塑件质量的影响,
采取相应的措施进行调节。
04
案例分析
案例一:翘曲与扭曲缺陷的解决
材料选择与控制
总结词
选择合适的材料,控制材料质量是解决注塑件缺陷的重要步骤。
详细描述
根据产品使用要求和工艺特性,选择具有良好流动性和成型性的材料。同时, 要确保材料干燥、清洁,无杂质和污染。定期对材料进行质量检查,确保其性 能稳定。
模具优化与维护
注塑缺陷及解决方案

注塑缺陷及解决方案一、包风包风(air traps)是指熔胶波前将模穴内的空气包覆,它发生在熔胶波前从不同方向的汇流,或是空气无法从排气孔或镶埋件之缝隙逃逸的情况。
包风通常发生在最后充填的区域,假如这些区域的排气孔太小或者没有排气孔,就会造成包风,使塑件内部产生空洞或气泡、塑件短射或是表面瑕疪。
另外,塑件肉厚差异大时,熔胶倾向于往厚区流动而造成竞流效应(race-tracking effect),这也是造成包风的主要原因,要消除包风可以降低射出速度,以改变充填模式;或者改变排气孔位置、加大排气孔尺寸。
由于竞流效应所造的包风可以藉由改变塑件肉厚此例或改变排气孔位置加以改善排气问题。
包风的改善方法说明如下:(1) 变更塑件设计:缩减肉厚比例,可以减低熔胶的竞流效应。
(2) 应变更模具设计:将排气孔设置在适当的位置就可以改善排气。
排气孔通常设在最后充饱的区域,例如模具与模具交接处、分模面、镶埋件与模壁之间、顶针及模具滑块的位置。
重新设计浇口和熔胶传送系统可以改变充填模式,使最后充填区域落在适当的排气孔位置。
此外,应确定有足够大的排气孔,足以让充填时的空气逃逸;但是也要小心排气孔不能太大而造成毛边。
建议的排气孔尺寸,结晶性塑料为0.025厘米(0.001英吋),不定形塑料为0.038厘米(0.0015英吋)。
浇口位置不当,浇口位置不当时,塑流有可能包抄空气或气体,形成积风。
更改浇口位置,可以改变充填模式,包风有可能避免。
(3) 调整成形条件:高射出速度会导致喷射流,造成包风。
使用较低的射出速度可以让空气有充足的时间逃逸。
二、短射(充填不足)短射(short shot)是熔胶无法充满整个模穴的现象,特别是薄肉区或流动路径的末端区域。
任何会增加熔胶流动阻力,或是妨碍足量塑料流入模穴的因素,都可能造成短射,包括:(1)成品与模具因素:①肉厚过薄或者流动长度过长(L/t比太高)塑件肉厚过薄常是造成短射的主因,因为薄壁区域流动阻力大,塑料流动容易发生迟滞现象,模具冷却效应明确,因此容易发生短射问题。
注塑缺陷描述及解决方案

注塑缺陷描述及解决方案一、缺陷描述在注塑过程中,可能会出现各种缺陷,影响产品的质量和外观。
以下是常见的注塑缺陷描述:1. 气泡:产品表面或内部出现小气泡,影响外观和强度。
2. 翘曲:产品变形或扭曲,不符合设计要求。
3. 热裂纹:产品表面出现细小的裂纹,通常是由于温度不均匀或冷却不足引起。
4. 毛刺:产品表面出现细小的毛刺,影响外观和触感。
5. 沉砂:产品表面出现沉积物,降低产品质量。
6. 焊痕:产品表面或内部出现焊接痕迹,影响外观和强度。
二、解决方案针对不同的注塑缺陷,可以采取以下解决方案:1. 气泡:a. 检查原料:确保原料干燥,避免含水分过高。
b. 调整注塑工艺参数:如降低注射速度、提高注射压力等。
c. 优化模具设计:减少产品内部空洞,避免气泡产生。
2. 翘曲:a. 优化模具设计:增加产品的支撑结构,减少变形的可能性。
b. 调整注塑工艺参数:如提高注射速度、降低模具温度等。
3. 热裂纹:a. 控制注塑温度:确保注塑温度均匀,避免温度过高或过低。
b. 加强冷却措施:如增加冷却时间、使用冷却剂等。
c. 优化模具设计:减少应力集中区域,避免热裂纹产生。
4. 毛刺:a. 优化模具设计:增加模具的冷却系统,提高冷却效果。
b. 调整注塑工艺参数:如降低注射速度、提高模具温度等。
c. 加工后处理:如打磨、抛光等,去除毛刺。
5. 沉砂:a. 检查原料:确保原料质量,避免含有杂质。
b. 加强清洁措施:定期清洁注塑设备和模具,避免沉砂产生。
6. 焊痕:a. 调整注塑工艺参数:如提高注射速度、降低模具温度等。
b. 优化模具设计:减少焊接痕迹产生的可能性。
三、总结注塑缺陷是在注塑过程中常见的问题,但通过合理的工艺控制和模具设计,可以有效解决这些问题。
在实际生产中,需要根据具体情况选择合适的解决方案,并进行适当的调整和优化,以确保产品的质量和外观达到预期要求。
同时,定期进行设备和模具的维护和清洁,也是预防注塑缺陷的重要措施。
注塑产品缺陷的解决

注意:1放电加工原理,放电加工是利用电能转换成工件热能,使工件急速熔融的一种热性加工方法.放电加工时,电极与工件的间隙中产生过渡电弧放电现象,进而对工件产生热作用,同时,加工中液体由于受到放电压力及热作用产生气化爆发现象,此时工件的熔融部份,将伴随液体气化融入加工液中,工件因放电的作用产生放电痕,如此反复进行,我们所希望的形状便可加工完成了.2线切割原理,铜丝接近工件并未与工件接触,对工件及铜线加上电压而产生电弧和高温9000o C —10000o C,融蚀后将金属残屑吹出,铜丝继续前进,工件冷却后即形成粗糙的被切割面.七、塑胶射出成型产品的外观问题与对策1、塑胶射出成型产品的外观问题积风Air Trap;发赤Blush;毛边Flash;流痕Flow Line or FlowMark;喷流蛇纹Jetting;短射Short Shot;凹陷或缩孔Sink Mark or Vord;条纹Streak;熔接线Weld Line2、积风——Air Trap积风的定义:空气或气体不及排出,被溶胶波前包夹在型腔内.●成品1)壁厚差异太大,产生跑道效应Race Track Effect,壁厚差异太大时,薄壁处塑流迟缓,溶胶循厚壁快速超前,有可能对型腔中空气或气体进行包抄,行程积风.2)CAE可以预测充填模式Filling Pattern和可能的积风点.更改厚度分布,使壁厚尽可能保持均一,以避免积风.●模具1)浇口Gate位置不当:a.浇口位置不当时,塑流有可能包抄空气或气体,形成积风;b. CAE 可以预测充填模式Filling Pattern和可能的积风点.更改浇口位置,可以改变充填模式,积风有可能避免.2)流道Runner或浇口尺寸不当:a.多浇口设计时,流道或浇口尺寸如果不当,塑流有可能赶超空气或气体,形成积风;b. CAE可以预测充填模式Filling Pattern和可能的积风点.更改浇口位置,可以改变充填模式,积风有可能避免.3)排气不良:a.若是排气不良,波前收口处会卷入空气或气体,形成积风;b. CAE可以预测充填模式Filling Pattern和可能的积风点.在可能的积风点加排气口,以避免积风.●射出成形机射速过高时,产生喷流Jetting,有可能卷入气体而形成积风.降低射速,可以稳定塑流,防止喷流,避免积风.3、发赤——Blush发赤的定义:浇口附近产生的云状色变.有时会在塑流通道中形成阻碍处发现.原因是溶胶破折Fracture.●塑料干燥不足,塑料湿气重,加热、混炼、推进时,蒸汽卷入溶胶,进入型腔时,产生银线,发赤现象常伴随产生.●模具1)模温太低;2)溶胶传送系统Melt Delivery System有锐角存在尤其是浇口处有锐角时,容易产生发赤现象.有时只要在进胶处采用较大的圆角半径,即可消除发赤现象.3)冷料井Cold Slug Well太小,注道冷料井的直径应和注道衬套Sprue Bushing出口直径相同,其深度与直径相同或超过直径.4)浇口太小或进料胶处型腔太薄溶胶流量大,短面积小时,剪切速率Shear Rate大,剪切应力往往跟着提高,以至溶胶破折Melt Fracture,产生发赤现象.CAE模拟,可以预测溶胶通过上述狭隘区时的温度、剪切速率和剪切应力,而CAE一般都会提供各种塑料料温、剪切速率和剪切应力的上限.CAE工程师可以根据分析结果做相应的调整,很快可以找出适当的浇口尺寸和进胶处型腔厚度.●射出成形机1)溶胶温度太低;2)射速太快;3)射压太高;4、毛边——Flush毛边的定义:熔融塑料流入分模面,滑块的折动面或配件的间隙所形成的废料.●塑料流动性太大或太小:塑料流动性太大,溶胶太稀,容易渗入型腔各处的间隙,产生毛边;塑胶流动性太小,溶胶太稠,需高压才能填模,模板有可能撑开,溶胶溢出,产生毛边.●模具1)浇口位置不当,使得流长太长,需高压才能填模,模板有可能撑开,溶胶溢出,在浇注系统上游处的分模面产生毛刺.2)合模台阶Land不当,合模台阶应自型腔外缘,向外延伸12mm.再外,动定模就相互分离Relieved,以保持合模台阶处分模面紧贴,不致溢料.3)承板Support Plate跨距太大,模板有可能被型腔内的高压撑开,溶胶溢出,在模板中央处的分模面产生毛刺.可在承板和可动侧安装板之间加间隔块Support Block or Support Pillar,缩短跨距.4)模板太薄,模板有可能被型腔内的高压撑开,溶胶溢出,模板中央处的分模面产生毛刺.5)模具加工或装配不当,型腔边缘形成过大间隙,溶胶溢出,产生毛边.浇道衬套Sprue Bushing不可太长,否则公母模无法合紧,造成溢料,产生毛边.平的分模面的平面度Flatness以0.05mm内为宜.6)排气口太深或太浅:a.排气口太深,溶胶渗出,产生毛边;b.排气口太浅,气体不易排出.加压排气时,模板有可能被撑开,溶胶溢出,产生毛边.7)钢材太软,易生凹陷,凹陷若发生在型腔周围,溶胶渗入,产生毛边.8)模面不清,模面有异物,模板无法密封,造成溢料,产生毛边.9)模温太高,溶胶较稀,容易渗入型腔各处的间隙,产生毛边.●射出成型机1)锁模力Clamp Force不足,模板有可能被型腔内的高压撑开,溶胶溢出,产生毛边.CAE可以预测所需锁模力对时间曲线,设定的锁模力不可以小于曲线重最大的锁模力.2)塑料计量过多,过量的溶胶被挤入型腔,模板可能被型腔内的高压撑开,溶胶溢出,产生毛边.3)料管温度太高,溶胶太稀,容易渗入型腔各处间隙,产生毛边.4)料管温度太低,溶胶太稠,需高压才能填模,模板有可能撑开,溶胶溢出,产生毛边.料温的设定可以参考材料厂商的建议.料管分后、中、前、喷嘴Rear、Center、Front and Nozzle 四区,从后往前的料温设定应逐步提高,每往前一区,增高60o C.若有必要尤其是对热敏感的塑料,可将喷嘴区合前区的料温设定的和中区一样.5)射压过高,模板有可能被型腔内的高压撑开,溶胶溢出,产生毛边.射出可从些许缺料注射Short Shot开始,每次增加3Bar50psi,直到填压过度为止.6)射速过高或过低:a.射速过高时,溶胶太稀,容易渗入型腔各处的间隙,产生毛边;b.射速过低时,溶胶温度降低,溶胶太稠,需高压才能填模,模板有可能撑开,溶胶溢出,产生毛边.每次射压或射速调整的增量以10%为原则.每次调整后,大约要射胶10次才可达到稳定状态.7)保压时间太长,溶胶从高压处向低压处传送,溶胶在型腔各间隙处伺机渗出的或然率提高,有可能产生毛边.8)停留时间太长或太短:a.塑料在料管或热流道中停留时间太长,会使得塑胶变稀,溶胶容易渗入型腔各处的间隙,产生毛边;b.停留时间太短,溶胶温度太低,溶胶太稠,需高压才能填模,模板有可能撑开,溶胶溢出,产生毛边.模具要装在和其射料量相当的射出成型机上.当射料量在料管容量的20到80%之间,塑化适当,毛边不易产生.●操作员习惯不好的操作员过早或过晚开闭成形机的门,塑料运送员不照规定运送塑料等等,都会使得成型结果前后不一致,当料管加热器因不规律的热损失而试图及时补充热量时,塑料温度不易均一,而有热点Hot Spot产生,热点附近流动性好,可能造成毛边.5、流痕——Flow Line or Flow Mark流痕的定义:成型品表面的流动痕迹.●塑料1)流动性不佳流长对壁厚比大的型腔,须以易流塑料充填.如果塑料流动性不够好,溶胶越走越慢,越慢越冷,射压和保压不足以将冷凝的表皮紧压在模面上,留下溶胶在垂直流动方向的凹陷,状似年轮.建议:以不产生溢料的原则下,选用嘴易流动的塑料2)采用成型润滑剂Molding Lubricant不当一般润滑剂含量在1%以下.当流长对壁厚比大时,润滑剂含量须适度提高,以确保冷凝层紧贴在模面上,直到制品定型,流痕无由产生.●模具1)模温太低会使得料温下降太快,射压和保压不足以将冷凝的表皮紧压在模面上,留下溶胶在垂直流动方向的凹陷,状似年轮.2)注道、浇道或浇口太小,留阻提高,如果射压不足,溶胶波前的推进会越来越慢,塑料会越来越冷,射压和保压不足以将冷凝的表皮紧压在模面上,留下溶胶在垂直流动方向的凹陷,状似年轮.3)排气不足,会使得溶胶充填受阻,溶胶波前无法将冷凝得表皮紧压在模面上,留下溶胶在垂直流动方向得凹陷,状似年轮.●射出成形机1)射压和保压不足以将冷凝得表皮紧压在模面上,留下溶胶在垂直流动方向得凹陷,状似年轮.提高射压和保压,冷凝层得以紧压在模面上,直到制品定型,流痕无由产生.2)停留时间不当,塑料在料管内停留时间太短,溶胶温度太低,即使勉强将型腔填满,保压时还是无法将塑胶压实,留下塑胶在垂直流动方向得凹陷,状似年轮.3)填充时间太长,溶胶波前会越走越冷,射压和保压不足以将冷凝得表皮紧压在模面上,留下溶胶在垂直流动方向得凹陷,状似年轮.4)循环时间太短时,塑料在料管内加温不及,溶胶温度低,即使勉强将型腔填满,保压时还是无法将塑胶压实,留下溶胶在垂直流动方向得凹陷,状似年轮.5)料管温度太低时,溶胶温度偏低,射压和保压不足以将冷凝得表皮紧压在模面上,留下溶胶在垂直流动方向得凹陷,状似年轮.6)喷嘴温度太低,塑料在料管内吸收加热带释放得热量以及螺杆转动引起塑料分子相对运动产生得摩擦热,温度逐渐升高.料管中得最后一个加热区为喷嘴,溶胶到此应该达到理想得料温,但须适度加热,以保持最佳状态.如果喷嘴温度设定得不够高,因喷嘴和模具接触,带走得热太多,料温就会下降,射压和保压不足以将冷凝得表皮紧压在模面上,留下溶胶在垂直流动方向得凹陷,状似年轮.6、喷痕蛇纹——Jetting喷痕得定义:自一受限区域例如喷嘴或是浇口,到一较厚和开阔的区域,形成得弯曲折叠似蛇得流痕.●制件壁厚自薄至厚的断差太大,塑流又别无选择的自薄处快速的流向厚处,会使得流动不稳,可能产生喷流.●模具1)浇口位置不当,塑流在型腔有自薄向厚的情形,若薄厚断差大,流速又快,则流动不稳,可能产生喷流.2)浇口非冲击型,冲击型浇口将进胶的溶胶导向一金属面,以释除应力,可稳定塑流,避免喷流.重叠式浇口和潜伏式浇口可设计成冲击型浇口.3)浇口至型腔,断面积突然变大,塑流不稳,容易产生喷流.浇口至型腔,断面积逐渐变化,如突片浇口或是扇形浇口,塑流得以平稳过渡,喷流得以避免.●射出成型机1)溶胶温度太高或是太低,喷流与溶胶进胶后的膨胀效应以及塑胶性质的变化有关.对大部分的塑料而言,温度将度时使得上述的膨胀效应更为明显,而某些材料,反而是当温度提高时膨胀效应更为明显.2)射速太高,采用最佳螺杆前进速度曲线,使熔胶波前能够先以一较慢速度通过浇口,一旦舌形溶胶在浇口下游形成,螺杆速度可以提高.注意:浇口数目的多寡,与充填时每个浇口必须负担的塑胶量有关.浇口数目较少,单位时间每个浇口必须通过的塑胶量也就越多,塑胶的前进速度也就越快.为了避免流速过快,塑胶将印刷膜充蚀,塑胶的流动速度必须降低.浇口数目不能太少,另外,多浇口进胶时,必须考虑塑流平衡的问题.当流动不平衡时,每个浇口通过的塑胶量会随之变化.如果大部分的塑胶都是通过其中某一特定浇口进入型腔,也有可能导致该浇口附近的塑胶膜被充填塑胶冲蚀.7、短射——Short Shot短射的定义:塑料未能充满整个型腔.●塑料流动性不佳,流长对壁厚比大的型腔,必须以易塑料充填.如果塑料流动性不够好,塑胶波前行至半途过冷不前,就会短射.●制件1)壁厚太薄,留阻高,如果射压不足,溶胶波前的推进会越来越慢,在型腔尚未填满前,即因波前固化而造成短射.2)壁厚差异太大,在壁厚部份填满以前,塑流在薄壁处的推进越来越慢,有可能因波前固化而造成短射.●模具1)模温太低会使得溶胶波前在型腔尚未填满前,即已过冷不前,造成短射.2)注道、流道或浇口太小,留阻提高,如果射压不足,溶胶波前的推进会越来越慢,在型腔尚未填满前,即因波前固化而造成短射.3)浇口的数目或位置不当,都会使得流长太长,流阻太大.如果射压不足,溶胶波前的推进会越来越慢,在型腔尚未填满前,即因波前固化而造成短射.4)冷料井未设或设计不当,注道和每一段流道末端应加冷料井.冷料井的尺寸要恰当,上游不可有阻挡物,才不会影响其捕捉冷料的功能.否则任一未捕捉的冷料顺流耳而下,都会有可能堵塞浇口或小的流道,而造成短射.5)排气不足,会使得塑胶充填受阻,甚至产生短射.在每一段流道末端考虑排气,避免流道内的气体进入型腔.型腔排气更不能轻忽.浇口对面的分模面上,考虑加排气孔,对应制品盲孔末端处,考虑加排气顶出销.●射出成型机1)注胶材料不足,注胶的材料不足以填满型腔的每一角落,溶胶固化后自然形成不完全的制品. 2)料管温度太低,在型腔尚未填满前,溶胶波前即已固化不前,成型的制品自然不完全.3)背压不足,背压可以增加相对运动的熔胶分子间的组力和摩擦热.此一摩擦热帮助塑化和促进均匀混炼.背压不足,会使溶胶无法获得足够的热量.冷料在型腔填满前,即已固化不前. 4)射压或射速过低,使得溶胶在过冷前,无力完成型腔充填的任务,短射因而发生.5)射出时间太短,填充动作不会应运而生,短射却随之而来.6)料斗出料口堵塞,料斗出料口即料管进料口,此乃塑料在射出成型机受热的首站.如果塑料在此处的温度接近树脂的软化点就有可能相互结合,形成路障,使得新料难以进入料管,造成缺料,以致短射.7)止回阀间隙太大,止回阀防止料管内螺杆前的溶胶在射出阶段回流.当螺杆前端、止回阀和料管之间的间隙太大时,止回阀的密封功能丧失,螺杆前端的溶胶回流到其上游的螺杆和料管之间,射出量不足,自然发生短射.8)喷嘴太小,流阻提高,如果射压不足,溶胶波前的推进会越来越慢,在型腔尚未填满前,即因波前固化而造成短射.9)射出机料管容量太小,每次射料量应在料管容量的20到80%之间.如果射料量大于容量的80%,下次射料塑化不及,流阻大,可能发生短射.8、凹陷或缩孔——Sink Mark or Void凹陷的定义:成型品表面的局部塌陷或呈酒窝状或呈沟状;缩孔的定义:成形品内部的缩孔.●制件1)肋太厚,肋和底板相遇处也厚,此处塑胶集中,冷却时,周围的肋和板先行固化,此一肋、板交汇处的中央仍然保持液态,后凝的塑胶在先固化的塑胶上收缩,对其周围塑胶有吸入的作用.如果任何一处凝结层较为薄弱一般就在和肋相对的模面处,该处就有可能因为塌陷而形成凹陷.如果凝结层够强,上述肋、板交汇处的中央就会形成缩孔.肋的厚度以底板厚度的50%为宜,甚至可以更薄.2)螺柱孔浅,螺柱底部和底板交汇处太厚,此处塑胶集中,冷却时,此处最后固化,对其周围先行固化的塑胶有吸入的作用.如果任何溢出凝结层较为薄弱一般就在和螺柱相对的模面处,该处就有可能因为塌陷而形成凹陷.如果凝结层够强,上述交汇处的中央就会形成缩孔.●模具1)和肋相对的模面温度太高易形成凹陷,和肋相对的模面温度若较附近高一般的确如此,因为附近溶胶集中,热负荷大,模温居高不下,该处凝结层薄,刚性不够,中央的溶胶固化时,有可能将较薄的凝结层向内拉成凹陷.2)以陶瓷或塑胶入子防止凹陷产生3)注道、流道或浇口太小,流阻提高,如果射压不足,型腔无法填实,溶胶密度小,发生凹陷或缩孔的机率大.4)浇口的数目或位置不当,都会使得流长太长,流阻太大.如果射压不足,型腔无法填实,溶胶密度小,发生凹陷或缩孔的机率大.●射出成型机1)料管温度太高,溶胶密度小,冷却时,贴近型腔表面的溶胶先固化成凝结层,塑胶体积收缩,型腔中央的溶胶密度更小,等到中央的溶胶也逐渐固化时,型腔中央会收缩成孔,缩孔的内壁满布张应力,如果凝结层的刚性不够,就会向内塌陷,形成凹陷.如果凝结层的刚性够,缩孔仍留存在制品之中.2)冷却时间不够易形成凹陷,塑胶凝结层不够厚,无法抵抗内部溶胶固化收缩时产生的拉力,形成凹陷.3)缓冲或保压不足,型腔内的塑胶因为压力偏低或补充料不足而填充不实,密度小,发生凹陷或缩孔的机率大.缓冲变0时,螺杆到底,不再前移.溶胶冷却,收缩时压力降低,螺杆却无法增压,造成保压不足,发生凹陷或缩孔的机率大.4)止回阀失灵,止回阀防止料管内螺杆前的溶胶在射出阶段回流.当螺杆推动定量的料前进时,如果止回阀磨损、破裂或座落不当,溶胶可能滑过螺杆前端、止回阀荷料管之间的间隙,产生回流,使得螺杆推到底,缓冲消失,发生凹陷或缩孔的机率大.9、条纹——Streak条纹的定义:成形品表面沿着流向形成的喷溅状线条.条纹可分为:1热劣解条纹Burn Streak;2水汽条纹Moisture Streak;3色彩条纹Color Streak;4空气条纹Air Streak;5玻织条纹Glass Fiber Streak.1热劣解条纹Burn Streak 分子链缩短产生银线Silver Streak,分子成块变质产生褐线Brown Streak.两者皆可称为热劣解条纹或燃烧条纹.●塑料干燥时温度过高或停留时间过长.●模具(1)浇口太小;(2)浇口或流道不顺畅;(3)排气不足.●射出成型机(1)溶胶温度太高;(2)停留时间过长;(3)射速太快,射压太高;(4)螺杆转速太快,塑化时剪切速率太大.2水汽条纹Moisture Streak 塑胶在储存褐成型过程中,吸收潮气,在溶胶内蒸发成水蒸汽.水蒸汽在接近波前时形成气泡,并逐渐膨胀,气泡到了波前时暴裂,并卷到模面,被拉长成银色条纹状,留影余制件表面.●塑料1干燥不足;2材料储存不当;●模具1模温控制系统漏水;2模面形成凝结水;●射出成型机1溶胶温度太高;2射压太高,射速太快;3螺杆转速太快,塑化时剪切速率太大;4停留时间过长;3色彩条纹Color Streak●塑料1着色时,颜料凝聚成块使得色彩浓度不同.塑胶、成型参数、粘着剂褐其他添加剂都有可能造成这种分布不均的现象;2在自厂以染料染色时,染料颗粒在溶胶内没有完全溶解.●射出成型机颜色对过高的成型温度褐过长的停留时间敏感,以致变色.这种色变若是由于热劣解,可归类为燃烧条纹.5)空气条纹Air Streak●模具(1)充填时空气无法及时逸出,带到产品表面,并且在流动的方向被拉伸;(2)在浮或凹字、肋、拱形物以及凹处下游积聚的空气有可能被后到的溶胶盖住,形成空气条纹或沟状空气囊;●射出成型机(1)螺杆倒退释压时,吸入空气,射出时,空气被卷经浇口,进入型腔,推到模壁浇口附近尤多,并被凝结的塑胶包围,形成空气条纹;(2)螺杆卷入空气;6)玻织条纹Glass Fiber Streak●塑料(1)玻织被波前卷到模壁时,这时玻织四周并没有足够的溶胶包围;(2)玻织褐塑胶的收缩比是1:200,玻织妨碍了塑胶的收缩,使得表面不均.10、熔接线——Weld Line熔接线的定义:溶胶波前相遇时形成的线条.●塑料(1)流动性不佳,流长对壁厚比大的型腔,须以易流塑料充填.如果塑料流动性不够好,溶胶波前越走越慢,越慢越冷,当熔接线形成时,波前温度已经降得太低,接合不良,线条明显.(2)添加辅强料太多,当辅强料得百分比增加时,熔接线得强度降低.未添加辅强料得塑胶所形成得熔接线可维持原材料强度得80-100%.加了辅强料得塑料所形成得熔接线往往无法维持无熔接线部份强度得80%.为了30%玻织得PP,其对头波前形成得熔接线只有其无熔接线部份强度得34%.加了30%玻织得PC,其对头波前形成得熔接线只有其无熔接线部份强度得64%.●制件(1)壁厚太薄或壁厚差异太大;(2)波前遇合角太小,当波前遇合角小于135o时,形成熔接线,大于135o时,形成熔合线.熔接线较之熔合线,两边分子相互扩散得少,品质较差.当遇合角在120o到150o之间时,熔接线表面痕迹逐渐消失.●模具(1)注道、流道或浇口位置不当或太小或太长.注道、流道或浇口位置不当时,熔接线会在外观或强度敏感处产生.注道、流道或浇口太小或太长,流阻提高,如果射压不足,溶胶波前形成熔接线时,温度已经降的太低,接合不良,线条明显.(2)模温太低,溶胶波前形成熔接线时,温度已经降的太低,接合不良,线条明显.提高模温,可以改善熔接线的品质.(3)排气不良,波前收口处会卷入空气或挥发物,熔接线线条明显.有时可在熔接线收口处加一溢料井,成型后再切除之,以改善熔接线的品质.●射出成型机(1)料管温度太低,溶胶波前形成熔接线时,温度太低,接合不良,线条明显.(2)背压不足,背压可以增加相对运动的溶胶分子间的阻力合摩擦热.此一摩擦热帮助塑化和促进均匀混炼.背压不足,会使溶胶无法获得足够的热量.低温溶胶波前形成的熔接线,由于接合不良,线条明显.提高背压,可以改善接合线品质.(3)射压或射速过低,溶胶波前形成熔接线时,温度已经降的太低,接合不良,线条明显.增加射压或射速自然可以改善.。
注塑品外观缺陷原因分析及方案
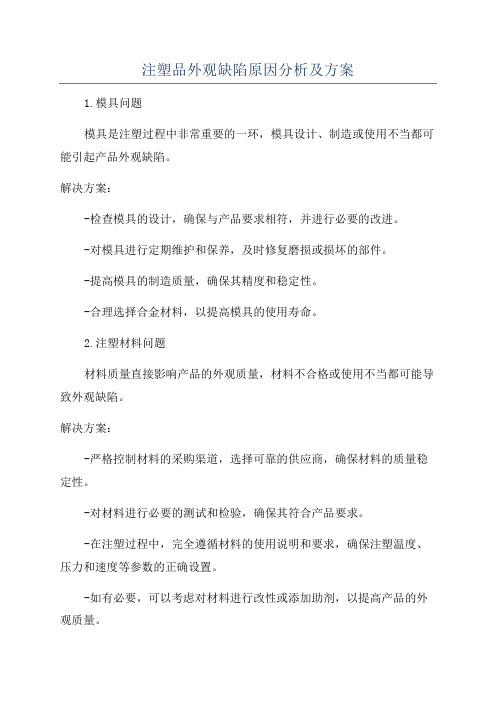
注塑品外观缺陷原因分析及方案1.模具问题模具是注塑过程中非常重要的一环,模具设计、制造或使用不当都可能引起产品外观缺陷。
解决方案:-检查模具的设计,确保与产品要求相符,并进行必要的改进。
-对模具进行定期维护和保养,及时修复磨损或损坏的部件。
-提高模具的制造质量,确保其精度和稳定性。
-合理选择合金材料,以提高模具的使用寿命。
2.注塑材料问题材料质量直接影响产品的外观质量,材料不合格或使用不当都可能导致外观缺陷。
解决方案:-严格控制材料的采购渠道,选择可靠的供应商,确保材料的质量稳定性。
-对材料进行必要的测试和检验,确保其符合产品要求。
-在注塑过程中,完全遵循材料的使用说明和要求,确保注塑温度、压力和速度等参数的正确设置。
-如有必要,可以考虑对材料进行改性或添加助剂,以提高产品的外观质量。
3.工艺参数问题注塑过程中,工艺参数的设置不合理也是导致外观缺陷的常见原因之一解决方案:-根据产品要求和材料特性,合理设置注射压力、注射速度、冷却时间等工艺参数。
-在注塑过程中,定期检查和调整工艺参数,保持其稳定性。
-使用先进的注塑设备和控制系统,提高注塑过程的自动化程度,降低人为因素对工艺参数的影响。
-针对不同的产品和外观缺陷,分析和优化工艺参数,以改善产品的外观质量。
4.操作人员问题操作人员的技术水平和经验不足,也是导致外观缺陷的一个重要原因。
解决方案:-对操作人员进行必要的培训和培养,提高其技术水平和专业知识。
-强调操作的规范性和标准化,遵守操作规程和要求。
-加强团队合作,实施相互监督和互助,减少人为失误的发生。
注塑品外观缺陷的原因分析及解决方案很多,上述只是一部分常见的原因和解决方法。
在实际应用中,还需根据具体情况来综合分析和解决问题。
同时,通过不断的优化和改进,提高注塑过程的质量和效率,减少外观缺陷的发生。
注塑缺陷原因分析与解决方案
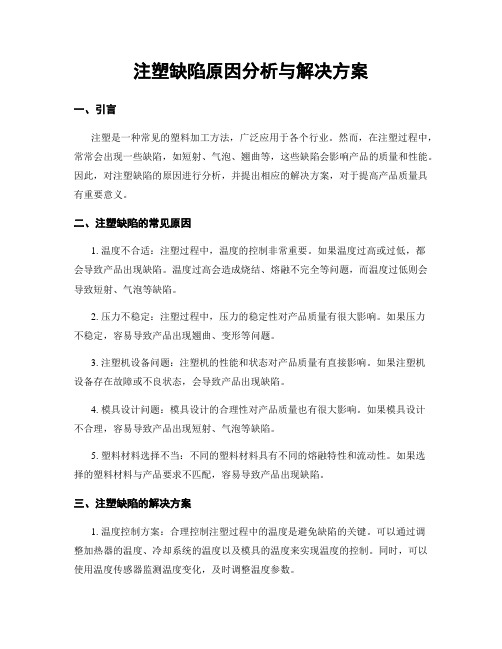
注塑缺陷原因分析与解决方案一、引言注塑是一种常见的塑料加工方法,广泛应用于各个行业。
然而,在注塑过程中,常常会出现一些缺陷,如短射、气泡、翘曲等,这些缺陷会影响产品的质量和性能。
因此,对注塑缺陷的原因进行分析,并提出相应的解决方案,对于提高产品质量具有重要意义。
二、注塑缺陷的常见原因1. 温度不合适:注塑过程中,温度的控制非常重要。
如果温度过高或过低,都会导致产品出现缺陷。
温度过高会造成烧结、熔融不完全等问题,而温度过低则会导致短射、气泡等缺陷。
2. 压力不稳定:注塑过程中,压力的稳定性对产品质量有很大影响。
如果压力不稳定,容易导致产品出现翘曲、变形等问题。
3. 注塑机设备问题:注塑机的性能和状态对产品质量有直接影响。
如果注塑机设备存在故障或不良状态,会导致产品出现缺陷。
4. 模具设计问题:模具设计的合理性对产品质量也有很大影响。
如果模具设计不合理,容易导致产品出现短射、气泡等缺陷。
5. 塑料材料选择不当:不同的塑料材料具有不同的熔融特性和流动性。
如果选择的塑料材料与产品要求不匹配,容易导致产品出现缺陷。
三、注塑缺陷的解决方案1. 温度控制方案:合理控制注塑过程中的温度是避免缺陷的关键。
可以通过调整加热器的温度、冷却系统的温度以及模具的温度来实现温度的控制。
同时,可以使用温度传感器监测温度变化,及时调整温度参数。
2. 压力控制方案:稳定的注塑压力有助于减少产品缺陷。
可以通过调整油压系统的参数、增加油泵的流量以及优化模具结构来实现压力的稳定控制。
3. 注塑机设备维护方案:定期对注塑机设备进行维护和保养,及时排除故障,确保设备处于良好状态。
同时,可以使用高精度的注塑机设备,提高产品质量。
4. 模具设计优化方案:优化模具设计,确保模具结构合理,避免出现短射、气泡等缺陷。
可以通过增加冷却系统、优化流道设计、增加排气系统等方式来改善模具设计。
5. 塑料材料选择方案:根据产品要求,选择合适的塑料材料。
可以通过对不同塑料材料的熔融特性和流动性进行测试,选择最适合的材料,避免出现缺陷。
注塑制品缺陷及解决方法
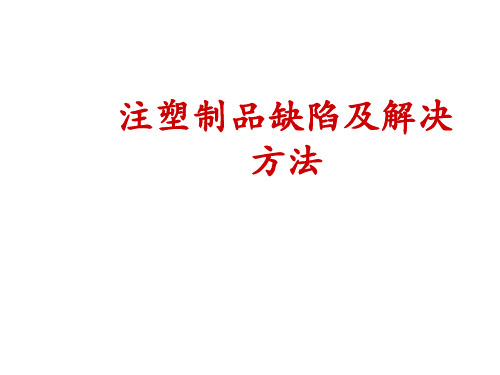
由于浇口个数不足、位臵欠佳导致保压过程压力分布不均 增加个数、改变方式 匀。 抽出模芯方向的抛光不足、抽出倾斜不足。 不能设定充分的保压条件(压力、时间)。 冷媒的流量不足(雷诺指数没有达到紊流域)、与模具热 容量 相比设备性能不足。 重新抛光 更换注塑机或增加锁 模力 更换模温机 更换模温机 提高树脂温度
疲劳破坏 涂装产品的破坏 电镀品的破坏
外力与反复施加负荷的施加方法 外力与涂膜的物性差(冲击、延 伸) 外力与电镀膜的物性差(冲击、 延伸) 外力与成形品的物性下降(劣化) ├不同种类原料的混入
〃消除混入原因 〃使用耐候性原料 〃使用耐热性原料 〃采用适当的成形条件 〃使用抗冲击性材料 〃使用抗冲击性材料 〃降低初期变形(负荷)
高或低(超出树脂流动特性的流动长度)。 高或低(由于浇口附近的树脂过充模(over parking)、浇口密 封不良导致逆流 短或长(浇口附近的树脂过充模(over parking)、浇口密 封不良导致逆流)。 短(原材料强度的温度依赖性)。
控制注塑压力 控制保压压力 控制保压时间 增加冷却时间
四、分层
注塑制品缺陷及解决 方法
一、黑纹、烧焦纹
产生原因: 1)机械原因,例如,由于异常条件造成料筒过热,使树 脂高温分解、烧伤后注射到制品中;或者由于料简内的喷嘴 和螺杆的螺纹、止回阀等部位造成树脂的滞流,分解变色后 带入制品,在制品中带有黑褐色的烧伤痕。 2)模具的原因,主要是因为排气不良所致。 3)在成型条件方面,背压太大会使料筒部分过热,造成 烧伤;螺杆转速过高时,也会产生过热;注射速度过高会引 起过热气体烧伤 4)胶料中含有低温料
十一、漩流纹
低速注射成形
高速注射成形
产生原因: 树脂温度较低的情况,溶融树脂的粘度加大,从 模具注射的树脂粘度进一步提高,造成流动抵抗力加 大,发生漩流现象。 模具温度较低时,注射到模具内部的树脂突然遇 冷,粘度加大而导致出现漩流。 漩流现象多半发生在浇口较小的情况,注射到模 具内部的树脂的流速增大,导致发生漩流现象。 解决方法: 1)成形条件 · 提高树脂温度,降低树脂粘度。 · 使用非结晶性树脂时,将模具温度设定在低于 使用树脂的热变形温度20~30℃左右为宜。 · 降低注射速度。 2)模具 · 为了降低树脂通过浇口时的流速,也可以加大 浇口的横断面积。
常见注塑产品缺陷分析及解决方法

常见注塑产品缺陷分析及解决方法常见注塑产品缺陷分析及解决方法注射模塑缺点和反常现象最终集中在注塑制品的质量上反映出来。
注塑制品缺点可分成下列几点:(1)产品注射不足;(2)产品溢边;(3)产品凹痕和气泡;(4)产品有接痕;(5)产品发脆;(6)塑料变色;(7)产品有银丝、斑纹和流痕;(8)产品浇口处混浊;(9)产品翘曲和收缩;(10)产品尺寸不准;(11)产品粘贴模内;(12)物料粘贴流道;(13)喷嘴流涎。
下面一一叙述其产生的原因及克服的办法。
1.怎样克服产品注射不足产品注料不足往往由于物料在未充满型腔之前即已固化,当然还有其他多种的原因。
⑴设备原因:①料斗中断料;②料斗缩颈部分或全部堵塞;③加料量不够;④加料控制系统操作不正常;⑤注压机塑化容量太小;⑥设备造成的注射周期反常。
⑵注塑条件原因:①注射压力太低;②在注射周期中注射压力损失太大;③注射时间太短;④注射全压时间太短;⑤注射速率太慢;⑥模腔内料流中断;⑦充模速率不等;⑧操作条件造成的注射周期反常。
⑶温度原因:①提高料筒温度;②提高喷嘴温度;③检查毫伏计、热电偶、电阻电热圈(或远红外加热装置)和加热系统;④提高模温;⑤检查模温控制装置。
⑷模具原因①流道太小;②浇口太小;③喷嘴孔太小;④浇口位置不合理;⑤浇口数不足;⑥冷料穴太小;⑦排气不足;⑧模具造成的注射周期反常;⑸物料原因:物料流动性太差。
2.怎样克服产品飞边溢料:产品溢边往往由于模子的缺陷造成,其他原因有:注射力大于锁模力、物料温度太高、排气不足、加料过量、模子上沾有异物等。
⑴模具问题:①型腔和型芯未闭紧;②型腔和型芯偏移;③模板不平行;④模板变形;⑤模子平面落入异物;⑥排气不足;⑦排气孔太大;⑧模具造成的注射周期反常。
⑵设备问题:①制品的投影面积超过了注压机的最大注射面积;②注压机模板安装调节不正确;③模具安装不正确;④锁模力不能保持恒定;⑤注压机模板不平行;⑥拉杆变形不均;⑦设备造成的注射周期反常⑶注塑条件问题:①锁模力太低;②注射压力太大;③注射时间太长;④注射全压力时间太长;⑤注射速率太快;⑥充模速率不等;⑦模腔内料流中断;⑧加料量控制太大;⑨操作条件造成的注射周期反常。
注塑工艺缺陷解决技巧

注塑工艺缺陷解决技巧
注塑工艺缺陷是在注塑过程中常见的问题,下面是一些解决技巧:
1. 确保合适的模具温度:注塑模具温度过高或过低都会导致缺陷。
需要根据不同的塑料材料选择合适的模具温度,并确保模具温度均匀分布。
2. 控制熔融温度和熔融时间:熔融温度和熔融时间对注塑成型质量有很大影响。
过高的温度或过长的时间会导致热分解或气泡产生。
需要根据材料的熔融指导曲线来控制熔融温度和熔融时间。
3. 适当的注射速度和压力:过快或过慢的注射速度都会导致缺陷。
需要根据产品的形状和大小选择合适的注射速度和压力,以确保塑料充填充分均匀。
4. 模具设计优化:合理的模具设计可以减少缺陷的发生。
例如,避免尖角、薄壁和不平衡的结构,使用圆角和倒角等。
5. 选择合适的注塑材料:不同的注塑材料有不同的性能和特点,需要根据产品的要求选择合适的材料。
同时,材料的质量也要保证。
6. 注塑机的维护和保养:定期对注塑机进行检查和保养,确保其正常运行。
包括清洁模具、更换磨损的零件、润滑机械部件等。
7. 实施统计质量控制:建立合理的质量控制体系,包括监控关键工艺参数、进行过程能力分析、实施SPC(统计过程控制)等,及时发现并解决问题。
这些技巧可以帮助解决注塑工艺缺陷,但具体的解决方法还需根据具体情况进行分析和调整。
在实际操作中,需要结合经验和专业知识来进行优化和改进。
注塑常见产品缺陷及解决方法

注塑常见产品缺陷及解决方法注塑是一种常见的塑料加工方法,广泛应用于电子、汽车、家电等行业中。
然而,在注塑过程中,常常会出现一些产品缺陷,影响产品的质量和外观。
下面将介绍一些常见的注塑产品缺陷及相应的解决方法。
1.毛刺毛刺是注塑过程中常见的问题,指的是产品表面出现的细小、锋利的突起物。
毛刺的存在会影响产品的使用体验和外观。
产生毛刺的原因可能是注塑模具精度不高、管道堵塞、注射速度过快等。
解决方法:-加工精度高的注塑模具,尽量减少毛刺的产生。
-定期对注塑机进行维护保养,避免管道堵塞。
-调整注射速度,控制在合适范围内,避免过快导致毛刺问题。
2.气泡气泡是注塑产品中常见的缺陷之一,表现为产品内部或表面出现空洞。
气泡的产生可能是塑料原料中含有气体、熔体温度不稳定、注塑模具设计不合理等原因。
解决方法:-使用优质的塑料原料,尽量避免含气体的原料使用。
-控制熔体温度稳定,防止过热或过冷导致气泡产生。
-根据产品的形状和结构合理设计注塑模具,避免气泡的产生。
3.翘曲翘曲是指注塑产品在冷却后出现变形或弯曲的现象,导致产品无法达到设计要求。
翘曲的原因可能是注塑模具温度不均匀、注射压力不均衡、产品厚度不均等。
解决方法:-调整注塑模具的温度,使其在整个注塑过程中保持均匀的温度。
-调整注射压力,使其在各个位置均匀分布,避免产生翘曲。
-控制产品的厚度,尽量保持均匀,避免局部厚度过大或过小导致翘曲。
4.缩水缩水是指注塑产品在冷却过程中出现体积缩小的现象,导致产品尺寸不达标。
缩水的原因可能是注塑模具设计不合理、冷却系统不良、注射温度过高等。
解决方法:-合理设计注塑模具,避免产品在冷却过程中过度收缩。
-安装冷却系统,使其能够均匀冷却产品,减少缩水现象的发生。
-控制注射温度,尽量避免过高的注射温度导致缩水。
5.出色出色是指注塑产品表面出现凹凸不平、粗糙不光滑的现象,影响产品的外观和质感。
出色的原因可能是注塑模具制造精度不高、注射速度过快、热流道系统不良等。
- 1、下载文档前请自行甄别文档内容的完整性,平台不提供额外的编辑、内容补充、找答案等附加服务。
- 2、"仅部分预览"的文档,不可在线预览部分如存在完整性等问题,可反馈申请退款(可完整预览的文档不适用该条件!)。
- 3、如文档侵犯您的权益,请联系客服反馈,我们会尽快为您处理(人工客服工作时间:9:00-18:30)。
课程名称消除注塑产品缺陷本课程的主要内容有:1、影响注塑制品质量四大素。
2、影响注塑制品质量因素的系统分析。
统分析3、塑料原料的特性。
塑料原料的特性4、制品缺陷分析与诊断。
制品缺陷分析与诊断本课程的学习目的使我们能更深入了解影响注塑制品质量因素的成因,掌握影响注塑制品质量因素的成因掌握影响注塑制品质量因素的成因系统分析工具,了解和掌握塑料原料的特性,掌握并熟解和掌握塑料原料的特性掌握并熟悉制品缺陷的分析与诊断。
从而提高操作技能,能轻而易举的在最短的时间内,最经济的状态下解决制品缺陷间内最经济的状态下解决制品缺陷问题问题。
第一章影响注塑制品响塑制质量四大因素塑件产品不合格的四大因素《1》塑料原料自身的物理性能和化学性能因素。
《2》注塑设备自身的性能、结构配置和故障因素。
障因素《3》注塑工艺参数设置与实际注塑工艺参数需求偏差因素。
《4》模具自身的结构、模具工作温度和模》模具自身的结构模具工作温度和模具故障因素。
第二章影响注塑制品质量因素的分析系统《一》缺陷排列统计与缺陷因素分析缺陷排列统计缺陷因素集聚点分析注塑制品缺陷数据统计表(假设)缺陷总量缺陷名称缺陷数量百分率缺陷排序胶量不足17%缺陷总量:100 件1717 %7筋条走胶不齐4141 %5溢边制品尺寸变化融接痕9999 %1泛白开裂顶白顶高脱模变形缩痕冷料2323 %6色料不均5757 %4气泡光泽不一8282 %3局部烧焦89%暗晕8989 %2材料热降解缺陷因素分析图机器工艺(加工方法)系统压力机筒(射嘴)温度锁模力注射压力流道温度料桶(原料)温度注射速度注射速率模具温度(动模)模具温度(定模)螺杆扭矩螺杆转速实际注射压力实际注射速度(速率)螺杆长径比螺杆几何形状注射段数段压保压段数段压时间螺杆塑化混炼止逆环(封胶效果)残料量用料量(螺杆行程)开模速度顶出速度顶出力回料速度回料背压问题模具投影面积模腔数量再生料比例浇注系统塑件流长颗粒大小水份含量模具排气制件壁厚变化原料流动性添加料含量(比例)模具恒原料收缩率原料熔融度模具恒温型腔表面光洁原料熔融温度模具精度顶针顶管顶块的顶出力分布模具材料塑件制品《二》缺陷表现与形成原因对应表塑件制品缺陷表现与形成原因对应表塑件制品缺陷的缺陷形成的原因塑注射保锁模熔胶喷嘴流模具浇口流模具开脱具模注塑机表现形式化压力度温道浇口温度道温度排气模模稳定性胶量不足X X X X X X X 筋条走胶不齐X X X X X X X X 溢边X X X X X X 制品尺寸变化X X X X X X 融接痕X X X X X X泛白开裂X X X X X顶白顶高X X X脱模变形X X X X X X缩痕X X X X X X 曲翘X X X X X冷料X X色料不均X X气泡X X X光泽不一X X X X X X局部烧焦X X X XX X X X暗晕材料热降解X X X X X第三章塑料原料的特性每种塑料原料都有自己的特性。
它有不同的结构、不同的密度、不同的熔有不同的结构不同的密度不同的熔点、不同的分解点、不同的粘度、不同硬度、不同的韧性等物理性能和对油、硬度不同的韧性等物性能和对油苯、酸、碱、酯、酮、醚、氯化碳氢化合物等不同反应的化学性能。
1)ABS 丙烯腈―丁二烯―苯乙烯共聚物: 非晶体密度: 1.06 ―1.19 g / cm³收缩率: 0.4 ―0.7 %结构106119/³0407物理性能: 坚硬、-40℃仍有韧性、耐高热变形、吸水性低、无毒、可电镀、抗风化力有限。
化学性能:抗酸、碱溶液、碳氢化合物、油、油脂、气油。
不抗丙酮、乙醚、乙苯、氯乙烷、氯化乙烯、苯、苯胺。
易燃、燃烧时火焰明亮有浓烟。
烘料温度(预烘干) :60 ― 80 ℃ 3 h (小时) 熔料温度:220 ― 240℃料筒温度:喂料区40 ― 60 ℃120―1502150―180熔料区1120 150 ℃熔料区2 150 180 ℃熔料区3 180 ― 210 ℃熔料区4200 ― 230 ℃熔料区5 210 ― 230 喷嘴210 ― 230 ℃10001500注射压力:1000 ―1500 bar注射方式:采用多级注射,从慢到快。
高注射速度,可得好的表面光泽。
保压压力:注射压力的30 -60 %,保压时间相对较短。
3060模具温度:30 ― 60 ℃螺杆转速:螺杆转速不易过高,最高转速折合线速度为0.6 / sec ,只要能在冷却时间结束前完成塑化过程即可。
残料量背压:70 -150 bar 计量行程:0. 6 -4.0 D残料量:2 - 6 mm 回收率:可加入30 %没发生热降解回料。
2) ABS / PC丙烯腈―丁二烯―苯乙烯共聚物/ 聚碳酸酯混合物/结构:非晶体密度: 1.5 g / cm³收缩率:0.5 ― 0.7 %物理性能:抗冲击、抗热、抗光、高光泽、可电镀、高弯曲强度。
化学性能:有限的抗水解能力。
不抗酮、酯、氯化碳氢化合物。
烘料温度(预烘干):60 ― 80 ℃4 h (小时) 熔料温度:250 ― 270 ℃料筒温度:喂料区50 ― 70 ℃熔料区1 200 ― 220 ℃熔料区2 230 ― 250 ℃熔料区3 240 260 ℃熔料区4 250 270 ℃3240―2604250―270熔料区5 250 ― 270 ℃喷嘴250 ― 270 ℃注射压力:1000 ― 1500 bar注射方式:采用多级注射,从慢到快。
保压压力:注射压力的40 -50 %。
模具温度:40 ― 80 ℃螺杆转速:螺杆转速不易过高,最高转速折合线速度为0.4 / sec ,螺杆转速不易过高最高转速折合线速度为04/sec背压:50 -100 bar计量行程:0. 6 -4.0 D残料量:2 - 6 mm回收率:可加入20 %没发生热降解回料。
3) PA 6 尼龙6结构: 部分晶体密度: 1.14 g / cm³收缩率: 0.7 ― 2.0 %物理性能: 坚硬、高韧性、含水量在2 -3 %时非常坚韧,干燥时变脆、高抗磨、无毒、良好的颜色淀积易结合。
化学性能:抗油、油脂、气油、碱溶液、溶剂、酮、酯、氯化碳氢化合物。
抗油油脂气油碱溶液溶剂酮酯氯化碳氢化合物不抗臭氧、盐酸、硫酸、双氧水。
可燃、离开明火后仍能继续燃烧、燃烧时起泡有滴落、焰心为蓝色,外沿为黄色。
烘料温度(预烘干) :60―80℃ 4 h (小时) 熔料温度:220 ― 240℃料筒温度:喂料区60 ― 80 ℃熔料区1180 200 ℃熔料区2 210 230 ℃180―2002210―230熔料区3 220 ― 240 ℃熔料区4230 ― 240 ℃熔料区5 230 ― 240 ℃喷嘴230 ― 240 ℃注射压力:1000 ―1800 bar注射方式:采用较快的注射速度。
采用较快的注射速度保压压力:注射压力的40 -50 %,保压时间相对较短。
模具温度:40 80 ℃40―80螺杆转速:较高的螺杆转速,最高转速折合线速度为1. 0 / sec ,只要能在冷却时间结束前完成塑化过程即可。
背压:30 -100 bar 计量行程:0. 5 -3.5 D残料量:2 - 5 mm 30100b053525回收率:可加入10 %没发生热降解回料。
4) PA 66 尼龙66结构: 部分晶体密度: 1.14 g / cm³收缩率: 0.7 ― 2.0 %物理性能: 坚硬、高韧性、含水量在2 -3 %时,非常坚韧,干燥时变脆、高抗磨、无毒、良好的颜色淀积易结合。
化学性能:抗油、油脂、气油、碱溶液、溶剂、酮、酯、氯化碳氢化合物。
不抗臭氧、盐酸、硫酸、双氧水。
可燃、离开明火后仍能继续燃烧、燃烧时起泡有滴落焰为蓝,外沿为黄滴落、焰心为蓝色外沿为黄色。
烘料温度(预烘干) :60―80℃ 4 h (小时) 熔料温度:240 ― 280℃料筒温度:喂料区60 ― 80 ℃熔料区1180 200 ℃熔料区2 220 240 ℃180―2002220―240熔料区3 250 ― 270 ℃熔料区4260 ― 280 ℃熔料区5 260 ― 280 ℃喷嘴260 ― 280 ℃注射压力:1000 ―1800 bar注射方式:采用较快的注射速度。
10001800采用较快的注射速度保压压力:注射压力的40 -50 %,保压时间相对较短。
模具模具温度:40 ― 80 ℃螺杆转速:较高的螺杆转速,最高转速折合线速度为1. 0 / sec ,只要能在冷却时间结束前完成塑化过程即可。
背压:30 100 bar 计量行程:0. 5 3.5 D残料量:2 5 mm 30-100bar05-352-5mm回收率:可加入10 %没发生热降解回料。
5) PC 聚碳酸酯结构: 非晶体密度: 1.2 g / cm³收缩率: 0.6 ―0.8 %物理性能: 坚硬、高抗冲击、耐蠕变温度高、流动性较差、透明性好、良好的颜色淀积性、低吸水性、抗风化。
好的颜色淀积性低吸水性抗风化化学性能:抗油、气油、稀酸、稀碱、酒精。
不抗强酸、强碱溶液、苯。
烘料温度预烘干) 100―120 ℃ 3 h (小时) 熔料温度:270 ― 300℃()()料筒温度:喂料区60 ― 80 ℃熔料区1200 ― 230 ℃熔料区2 230 ― 260 ℃熔料区3 250 ― 280 ℃熔料区4280 ― 300 ℃3250280280300熔料区5 280 ― 300 ℃喷嘴280 ― 300 ℃注射压力:1300 1900 bar1300―1900注射方式:采用多级偏快注射,从慢到快。
保压压力:注射压力的40 -60 %保压。
模具温度:60 ― 100 ℃螺杆转速:中低转速大扭矩,最高转速折合线速度为0.5 / sec ,背压:100 150 bar 计量行程:0. 6 4.0 D残料量: 2 6 mm 100-150bar06-402-6mm 回收率:可加入20 %没发生热降解回料。
PE 聚乙烯PE根据聚合方式的不同,聚乙烯可分为:根据聚合方式的不同聚乙烯可分为低密度聚烯()中密度聚烯低密度聚乙烯( LD –PE )、中密度聚乙烯( MD –PE )、高密度聚乙烯(HD –PE )、线性低密度聚乙烯( LLD -PE )、超高分子量聚(LLD PE)超高分子量聚乙烯( UHMW –PE ) 。
由于性能和价格原因,目前大部分使用的聚乙烯确(PE) 原料为:高密度聚乙烯(HD PE ),所以只介绍其特性(HD–PE)和加工工艺推荐。
6)HD -PE 高密度聚乙烯结构: 部分晶体密度: 0.94 ― 0.95 g / cm³收缩率: 1.2 ― 2.5 %收缩率较大。