ISL6115芯片手册
ZL50112中文资料(Zarlink Semiconductor)中文数据手册「EasyDatasheet - 矽搜」
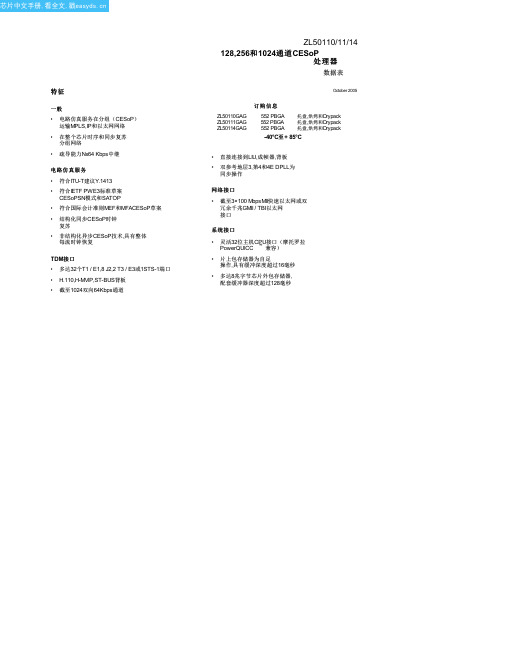
芯片中文手册,看全文,戳
ZL50110/11/14
数据包处理功能
• 灵活多协议数据包封装包括IPv4,IPv6RTP,MPLS,L2TPv3ITU-T Y.1413,IETF CESoPSN模式,IETF SATOP和用户可编程
• 包重测序,允许丢失数据包检测 • 利用出口队列四大类服务优先级可编程机制(WFQ和SP) • 传入分组层2,3,4灵活分类,和5 • 最多支持通过分组交换网络128单独CESoP连接
• 结构感知TDM电路仿真服务在分组交换网络(CESoPSN模式) - 选秀ietfpwe3-cesopsn
该ZL50110/11/14提供高达三倍100 MbpsMII端口或双冗余1000 MbpsGMII / TBI端口.
所述ZL50110/11/14包含一系列每个TDM流强大时钟恢复机制,允许在源时钟频率,可以忠实在目地产生 ,实现更高系统性能和质量.定时使用RTP或类似协议进行,双方自适应和差分时钟恢复方案包括,允许客户选择 正确方案应用.一个外部提供时钟,也可以用于驱动ZL50110/11/14TDM接口.
设备
ZL50114 ZL50110
ZL50111
TDM接口
4 T1,4 E1或1 J 2流或 4 MVIP / ST-BUS流以2.048 Mbps或 1 H.110 / H-MVIP / ST-BUS流在8.192 Mbps
8 T1,8个E1或2 J2流或 8 MVIP / ST-BUS流以2.048 Mbps或 2 H.110 / H-MVIP / ST-BUS流在8.192 Mbps
2.0物理规格. . . . . . . . . . . . . . . . . . . . . . . . . . . . . . . . . . . . . . . . . . . . . . . . . . . . . . . . . . . . . . . . . . 12
ESDH155ADM用户手册

MCL1005多层芯片感应器技术数据说明书
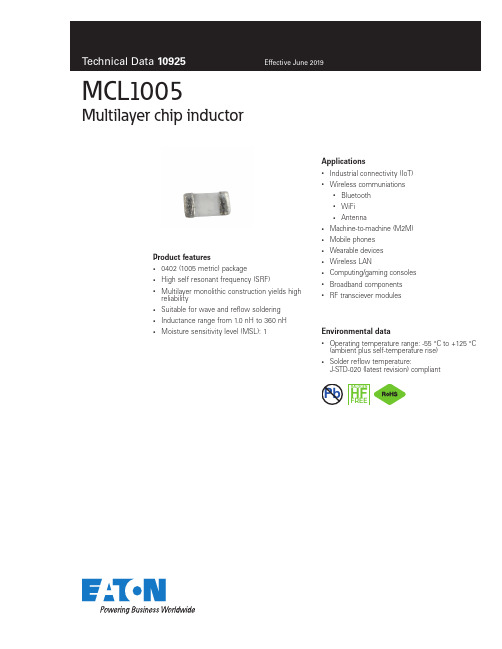
MCL1005 Multilayer chip inductorProduct features• 0402 (1005 metric) package• High self resonant frequency (SRF)• Multilayer monolithic construction yields high reliability• Suitable for wave and reflow soldering• Inductance range from 1.0 nH to 360 nH • Moisture sensitivity level (MSL): 1Applications• Industrial connectivity (IoT)• Wireless communiations• Bluetooth• WiFi• Antenna• Machine-to-machine (M2M)• Mobile phones• Wearable devices• Wireless LAN• Computing/gaming consoles• Broadband components• RF transciever modulesEnvironmental data• Operating temperature range: -55 °C to +125 °C (ambient plus self-temperature rise)• Solder reflow temperature:J-STD-020 (latest revision) compliantPb HALOGENHFFREE2Technical Data 10925Effective June 2019MCL1005Multilayer chip inductor/electronicsProduct specificationsPart numberOCL (nH) ±5%I Rated(mA) maximumDCR (Ω)maximum @ +25°CSRF(MHz) minimumQ(minimum)Test frequency (MHz)Test voltage (mV)MCL1005-1R0-R 1.0 ±0.3nH 4000.1010000810050MCL1005-1R1-R 1.1 ±0.3nH 4000.1010000810050MCL1005-1R2-R 1.2 ±0.3nH 4000.1010000810050MCL1005-1R3-R 1.3 ±0.3nH 4000.1010000810050MCL1005-1R5-R 1.5 ±0.3nH 3000.106000810050MCL1005-1R6-R 1.6 ±0.3nH 3000.126000810050MCL1005-1R8-R 1.8 ±0.3nH 3000.126000810050MCL1005-2R0-R 2.0 ±0.3nH 3000.156000810050MCL1005-2R2-R 2.2 ±0.3nH 3000.156000810050MCL1005-2R4-R 2.4 ±0.3nH 3000.156000810050MCL1005-2R7-R 2.7 ±0.3nH 3000.156000810050MCL1005-3R0-R 3.0 ±0.3nH 3000.206000810050MCL1005-3R3-R 3.3 ±0.3nH 3000.206000810050MCL1005-3R6-R 3.6 ±0.3nH 3000.204000810050MCL1005-3R9-R 3.9 ±0.3nH 3000.204000810050MCL1005-4R3-R 4.3 ±0.3nH 3000.204000810050MCL1005-4R7-R 4.7 ±0.3nH 3000.254000810050MCL1005-5R1-R 5.1 ±0.3nH 3000.254000810050MCL1005-5R6-R 5.6 ±0.3nH 3000.254000810050MCL1005-6R2-R 6.2 ±0.3nH 3000.303900810050MCL1005-6R8-R 6.8 3000.303900810050MCL1005-7R5-R 7.5 3000.403700810050MCL1005-8R2-R 8.23000.403600810050MCL1005-9R1-R 9.13000.403400810050MCL1005-100-R 103000.403200810050MCL1005-120-R 123000.502700810050MCL1005-150-R 153000.502300810050MCL1005-180-R 183000.602100810050MCL1005-200-R 203000.602000810050MCL1005-220-R 223000.601900810050MCL1005-270-R 273000.701600810050MCL1005-330-R 332000.801300810050MCL1005-390-R 39200 1.001200810050MCL1005-430-R 43200 1.101100810050MCL1005-470-R 47200 1.101000810050MCL1005-560-R 56200 1.20750810050MCL1005-680-R 68180 1.40750810050MCL1005-820-R 82150 2.40750810050MCL1005-101-R1001502.607008100501. Test frequency and voltage are for OCL and Q at +25 °C2. Resistance to soldering heat: +260 ±5 °C for 10 ± 1 second3. At low temperature resistance (-55 ±2°C) the inductance change is within ±10% and the Q within ±20%4. At high temperature resistance (+125 ±2°C) the inductance change is within ±10% and the Q within ±20%5. At high temperature load (+125 ±2°C) the inductance change is within ±10% and the Q within ±20%6. Rated I: When rated I is applied to the product, self-temperature rise will be 40 °C or less.7. Part Number Definition: MCL1005-xxx-R MCL1005 = Product code and sizexxx= inductance value in nH, R= decimal point,If no R is present then last character equals number of zeros -R suffix = RoHS compliant3Technical Data 10925Effective June 2019MCL1005Multilayer chip inductor /electronics No part markingAll soldering surfaces to be coplanar within 0.1 millimeters Tolerances are ±0.2 millimeters unless stated otherwisePad layout tolerances are ±0.1 millimeters unless stated otherwise Do not route traces or vias underneath the inductorDimensions (mm)SchematicProduct specificationsPart numberOCL (nH) ±5%I Rated(mA) maximumDCR (Ω)maximum @ +25°CSRF(MHz) minimumQ(minimum)Test frequency (MHz)Test voltage (mV)MCL1005-121-R 120150 2.80600810050MCL1005-151-R 150100 3.20550810050MCL1005-181-R 180100 3.70500810050MCL1005-221-R 220100 4.00450810050MCL1005-271-R 270100 4.50400810050MCL1005-331-R 330507.0035065050MCL1005-361-R360507.50300650501. Test frequency and voltage are for OCL and Q at +25 °C2. Resistance to soldering heat: +260 ±5 °C for 10 ± 1 second3. At low temperature resistance (-55 ±2°C) the inductance change is within ±10% and the Q within ±20%4. At high temperature resistance (+125 ±2°C) the inductance change is within ±10% and the Q within ±20%5. At high temperature load (+125 ±2°C) the inductance change is within ±10% and the Q within ±20%6. Rated I: When rated I is applied to the product, self-temperature rise will be 40 °C or less.7. Part Number Definition: MCL1005-xxx-R MCL1005 = Product code and sizexxx= inductance value in nH, R= decimal point,If no R is present then last character equals number of zeros -R suffix = RoHS compliantPart Number L W T a A B CMCL1005-xxx-R 1.0 ±0.150.50 ±0.150.50 ±0.150.25 ±0.100.85 ±0.100.8 ±0.100.2 ±0.104MCL1005Multilayer chip inductor/electronicsFrequency MHzQ vs frequency5Technical Data 10925Effective June 2019MCL1005Multilayer chip inductor /electronics Solder reflow profileTable 1 - Standard SnPb solder (T c )Package ThicknessVolume mm3 <350Volume mm3 ≥350<2.5 mm)235 °C 220 °C ≥2.5 mm220 °C220 °CTable 2 - Lead (Pb) free solder (T c )Package thicknessVolume mm 3 <350Volume mm 3350 - 2000Volume mm 3 >2000<1.6 mm 260 °C 260 °C 260 °C 1.6 – 2.5 mm 260 °C 250 °C 245 °C >2.5 mm250 °C245 °C245 °CT e m p e r a t u r eT LT PReference J-STD-020Profile featureStandard SnPb solderLead (Pb) free solderPreheat and soak • Temperature min. (T smin )100 °C 150 °C • Temperature max. (T smax )150 °C 200 °C • Time (T smin to T smax ) (t s )60-120 seconds 60-120 seconds Average ramp up rate T smax to T p 3 °C/ second max. 3 °C/ second max.Liquidous temperature (T l ) Time at liquidous (t L )183 °C60-150 seconds 217 °C60-150 seconds Peak package body temperature (T P )*Table 1Table 2Time (t p )** within 5 °C of the specified classification temperature (T c )10 seconds**10 seconds**Average ramp-down rate (T p to T smax ) 6 °C/ second max. 6 °C/ second max.Time 25 °C to peak temperature6 minutes max.8 minutes max.* Tolerance for peak profile temperature (T p ) is defined as a supplier minimum and a user maximum.** Tolerance for time at peak profile temperature (t p ) is defined as a supplier minimum and a user maximum.EatonElectronics Division 1000 Eaton Boulevard Cleveland, OH 44122United States/electronics © 2019 EatonAll Rights Reserved Printed in USAPublication No. 10925 BU-MC19057June 2019MCL1005Multilayer chip inductorTechnical Data 10925Effective June 2019Life Support Policy: Eaton does not authorize the use of any of its products for use in life support devices or systems without the express writtenapproval of an officer of the Company. Life support systems are devices which support or sustain life, and whose failure to perform, when properly used in accordance with instructions for use provided in the labeling, can be reasonably expected to result in significant injury to the user.Eaton reserves the right, without notice, to change design or construction of any products and to discontinue or limit distribution of any products. Eaton also reserves the right to change or update, without notice, any technical information contained in this bulletin.T e m p e r a t u r eTimeT T T T Wave solder profileReference EN 61760-1:2006Profile featureStandard SnPb solderLead (Pb) free solderPreheat • Temperature min. (T smin )100 °C 100 °C • Temperature typ. (T styp )120 °C 120 °C • Temperature max. (T smax )130 °C 130 °C • Time (T smin to T smax ) (t s )70 seconds 70 seconds D preheat to max Temperature150 °C max.150 °C max.Peak temperature (T P )*235 °C – 260 °C 250 °C – 260 °C Time at peak temperature (t p )10 seconds max5 seconds max each wave 10 seconds max5 seconds max each wave Ramp-down rate~ 2 K/s min ~3.5 K/s typ ~5 K/s max ~ 2 K/s min ~3.5 K/s typ~5 K/s max Time 25 °C to 25 °C4 minutes4 minutesManual solder+350 °C, 4-5 seconds. (by soldering iron), generally manual, hand soldering is not recommended.Eaton is a registered trademark.All other trademarks are property of their respective owners.Follow us on social media to get the latest product and support information.。
ISL85005和ISL85005A演示板用户指南说明书
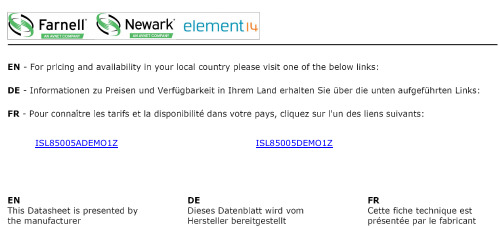
ISL85005ADEMO1Z ISL85005DEMO1ZISL85005DEMO1Z and ISL85005ADEMO1Z Demonstration Boards User GuideDescriptionThe ISL85005 and ISL85005A are 4.5V to 18V input, 5A synchronous buck regulators for applications with input voltage from multi-cell batteries or regulated 5V and 12Vpower rails. These devices also provide an integrated bootstrap diode for the high-side gate driver to reduce the external parts count. The ISL85005DEMO1Z and ISL85005ADEMO1Zplatforms allow quick demonstration of the high performance features of the ISL85005 and ISL85005A buck regulators.SpecificationsThese boards have been configured and optimized for the following operating conditions: •Input voltage ranges from 7V to 15V •5V nominal output voltage •Up to 5A output current capability•Default internally set 500kHz switching frequency •Default internally set 2.3ms soft-start•Operating temperature range: -40°C to +85°CKey Features•Switch selectable EN (enabled/disabled)•Selectable mode (DEM/Forced CCM) (ISL85005DEMO1Z)•Internal and external compensation options•Frequency synchronization option (ISL85005DEMO1Z)•Adjustable soft-start option (ISL85005ADEMO1Z)•Small and compact designRelated Literature•For a full list of related documents please visit our website -ISL85005 and ISL85005A product pagesOrdering InformationPART NUMBER DESCRIPTIONISL85005DEMO1Z Small form-factor demonstration board for ISL85005FRZISL85005ADEMO1ZSmall form-factor demonstration board for ISL85005AFRZFIGURE 1A.ISL85005DEMO1ZFIGURE 1B.ISL85005ADEMO1ZFIGURE 1.BLOCK DIAGRAMSYNC/PG EN FB COMP BOOT VDD VIN VIN PHASE AGND234151*********PHASE PGNDC 3C 4C 5C 6C 8C 9MODE GND = DEM; VCC = FCCM EN PG MODE V INL 1V OUTISL85005R 2C 1R 1PGENFB COMP BOOT VDD VIN VIN PHASE AGND234151110912867PHASE PGNDC 3C 4C 5C 6C 8C 9EN PG V INL 1V OUTISL85005AR 2C 1R 1SS C SSUser Guide 110User Guide 110Connector and Selection Jumper DescriptionsThe ISL85005DEMO1Z and ISL85005ADEMO1Z demonstration boards include I/O connectors and a selection jumper as shown in Table1.Quick Setup GuideRefer to the following Quick Setup Guide to configure and power-up the board for proper operation.1.Set the power supply voltage to 12V, and turn off the powersupply. Connect the positive output of power supply to J3 (VIN) and the negative output to J4 (GND).2.Connect an electronic load to J5 (VOUT) for the positiveconnection and J6 (GND) for the negative connection.3.Measure the output voltage (J5 and J6) with the voltmeter.4.Place scope probes on VOUT and other test points of interest.5.Set EN jumper (J1) to ON position.6.Set the load current to be 0.1A and turn on the power supply,the output voltage should be in regulation with a nominal 5V output.7.Slowly increase the load up to 5A while monitoring the outputvoltage which should remain in regulation with a nominal 5V output.8.Slowly sweep VIN from 7V to 15V, the output voltage shouldremain in regulation with a nominal 5V output.9.Decrease the input voltage to 0V to shut down the regulator. Operation Mode Selection (ISL85005DEMO1Z)The ISL85005DEMO1Z can be configured in either forced Continuous Conduction Mode (CCM) or Diode Emulation Mode (DEM):•In the default configuration of ISL85005DEMO1Z,SYNC/MODE (Pin 1) of ISL85005 is floating, the ISL85005 operates in forced CCM.•To configure the ISL85005 in DEM, short the SYNC/MODE pin to GND by populating a 0Ω resistor for C SS. DEM enables automatic transition from CCM to DCM and higher efficiency at light-load conditions.Frequency Synchronization (ISL85005DEMO1Z)The ISL85005 can be synchronized to an external clock with frequency ranges from 300kHz to 2MHz by applying the external clock to the SYNC/MODE pin on the ISL85005DEMO1Z demonstration board. The external clock should meet the specifications of the pulse width and voltage level described in the datasheet.Adjusting Soft-Start Time(ISL85005ADEMO1Z)With the SS pin floating, the ISL85005A features an internally set 2.3ms of soft-start time. The soft-start time can be set to a desired value by connecting an external capacitor (C SS on the ISL85005ADEMO1Z demonstration board) between the SS pin and AGND. The capacitance can be calculated by Equation1:Evaluating Other Output VoltagesBoth ISL85005DEMO1Z and ISL85005ADEMO1Z have a nominal 5V output voltage. The output voltages are programmable by an external resistor divider formed by R1 and R2 as shown in Figure1 on page1. R1 is usually chosen first, then the value for R2 can be calculated based on R1 and the desired output voltage using Equation2.PCB Layout ConsiderationsThe PCB layout is critical for proper operation of the ISL85005 and ISL85005A. The following guidelines should be followed to achieve good performance.e a multilayer PCB structure to achieve optimizedperformance, a four-layer PCB is recommended for thisdesign.e a combination of bulk capacitors and smaller ceramiccapacitors with lower ESL for the input capacitors and place them as close to the IC as possible.3.Place the VDD decoupling capacitor close to the IC betweenVDD and GND. A 1µF ceramic capacitor is typically used. 4.Place a bootstrap capacitor close to the IC between the BOOTand PHASE pins. A 0.1µF ceramic capacitor is typically used.5.Connect the feedback resistor divider between the outputcapacitor positive terminal and the AGND pin of the IC, and place the resistors close to the FB pin of the IC.6.Connect the EPAD of the IC to the GND planes underneathusing multiple thermal vias to improve thermal performance.TABLE 1.CONNECTORS AND JUMPERREFERENCEDESIGNATOR DESCRIPTIONJ1Selection Jumper for Enable (EN)J3Input voltage positive connectionJ4Input voltage return connectionJ5Output voltage positive connectionJ6Output voltage return connectionC SS nF[] 3.5t SS ms[] 1.6nF–⋅=(EQ. 1)R2R10.8V⋅V OUT0.8V–----------------------------------=(EQ. 2)User Guide 110 ISL85005xDEMO1Z Demonstration BoardFIGURE 2.TOP VIEW SchematicFIGURE 3.ISL85005xDEMO1Z SCHEMATICUser Guide 110 Bill of MaterialsMANUFACTURER PART NUMBER REFERENCEDESIGNATOR QTY DESCRIPTION MANUFACTURERISL85005FRZ(ISL85005DEMO1Z)U11IC-BUCK REGULATOR W/ SYNC/MODE PIN, 12PIN, DFN, 3x4, ROHS INTERSILISL85005AFRZ(ISL85005ADEMO1Z)1IC-BUCK REGULATOR W/ SS PIN, 12PIN, DFN, 3x4, ROHS INTERSILGRM1555C1H120JA01D C41CAP, SMD, 0402, 12pF, 50V, 5%, NP0, ROHS MURATAC7, C8, C SS0CAP, SMD, 0402, DNP-PLACE HOLDER, ROHSGRM188R71E104KA01D C31CAP, SMD, 0603, 0.1µF, 25V, 10%, X7R, ROHS MURATAGRM188R61E105KA12D C91CAP, SMD, 0603, 1µF, 25V, 10%, X5R, ROHS MURATAC1206X7R250-106KNE C1, C22CAP, SMD, 1206, 10µF, 25V, 10%, X7R, ROHS VENKELCL32A476KOJNNNE C5, C62CAP, SMD, 1210, 47µF, 16V, 10%, X5R, ROHS SAMSUNG744314330L11COIL-PWR INDUCTOR, SMD, 6.9mm2, 3.3µH, 9A 9mΩ, WW, ROHS WURTH ELEKTRONIK 1514-2J3, J4, J5, J64CONN-TURRET, TERMINAL POST, TH, ROHS KEYSTONEERJ2RKF20R0R41RES, SMD, 0402, 20Ω, 1/16W, 1%, TF, ROHS PANASONICCR0402-16W-00T R111RES, SMD, 0402, 0Ω, 1/16W, 5%, TF, ROHS VENKELMCR01MZPF2003R7, R142RES, SMD, 0402, 200k, 1/16W, 1%, TF, ROHS ROHMCR0402-16W-4993FT R11RES, SMD, 0402, 499k, 1/16W, 1%, TF, ROHS VENKELRC0402FR-0795K3L R21RES, SMD, 0402, 95.3k, 1/16W, 1%, TF, ROHS YAGEOR3, R80RES, SMD, 0402, DNP, DNP, DNP, TF, ROHS929950-00Jumper1CONN-JUMPER, SHORTING, 2PIN, BLK, OPEN TOP, 2.54mmPITCH,ROHS3MPEC03SAAN J11 3 Positions Header, 100 mil (2.54mm) spacing, Through Hole Tin Sullins Connector Solutions ISL85005xDEMO1Z PCB1PWB-PCB, ISL85005xDEMO1Z, REVA, ROHS AnyUser Guide 110 ISL85005xDEMO1Z PCB LayoutUser Guide 110Intersil Corporation reserves the right to make changes in circuit design, software and/or specifications at any time without notice. Accordingly, the reader is cautioned to verify that the document is current before proceeding.For information regarding Intersil Corporation and its products, see Typical Performance CurvesV IN = 12V, V OUT = 5V, L = 3.3µH, f SW = 500kHz, T A = +25°C, unless otherwise noted.FIGURE 9.START-UP WITH EN, I OUT = 5AFIGURE 10.SHUTDOWN WITH EN, I OUT = 5AFIGURE 11.LOAD TRANSIENT, 0A → 2.5A → 0A, 2.5A/µsV OUT (2V/DIV)I L (2A/DIV)EN (10V/DIV)1ms/DIV200µs/DIV V OUT (2V/DIV)EN (10V/DIV)I L (2A/DIV)50µs/DIVV OUT (100mV/DIV),I OUT (1A/DIV)AC COUPLINGISL85005ADEMO1Z ISL85005DEMO1Z。
PMC-6510说明书(V1.3版)(071210)
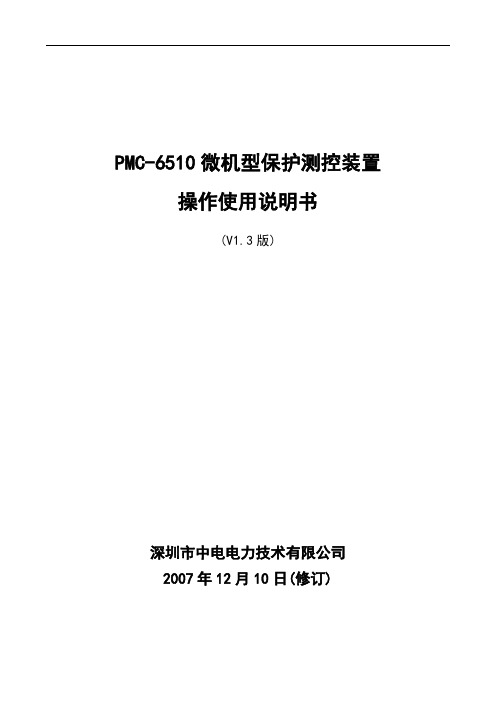
PMC-6510微机型保护测控装置操作使用说明书(V1.3版)深圳市中电电力技术有限公司2007年12月10日(修订)目录1装置简介 (1)1.1概述 (1)1.2产品特点 (1)1.3基本功能 (1)1.4产品使用 (2)2技术指标 (2)2.1工作环境条件 (2)2.2额定参数 (2)2.3精度及误差 (2)2.4遥信分辨率 (3)2.5过载能力 (3)2.6继电器输出 (3)2.7开关量输入 (3)2.8电气绝缘性能 (3)2.9机械性能 (3)2.10电磁兼容性能 (4)3功能说明 (4)3.1保护功能 (4)3.1.1速断保护 (4)3.1.2复合电压元件 (4)3.1.3限时速断 (5)3.1.4定时限过流 (5)3.1.5反时限过流保护 (5)3.1.6过热保护 (6)3.1.7过负荷保护 (6)3.1.8起动时间过长保护 (6)3.1.9堵转保护 (7)3.1.10充电保护 (7)3.1.11零序过流保护(I、II段) (7)3.1.12负序过流保护 (8)3.1.13过压保护 (8)3.1.14低压保护 (8)3.1.15低周减载 (9)3.1.16电容器差压保护 (9)3.1.17绝缘监视 (9)3.1.18TV断线 (9)3.1.19重要遥信处理 (10)3.2测量监视功能 (10)3.2.1测量 (10)3.2.2遥信功能 (10)3.3控制功能 (11)3.4通讯功能 (11)3.5记录功能 (11)3.5.1事件记录 (11)3.5.2故障录波记录 (11)4操作使用说明 (12)4.1按键操作 (12)4.2信号指示灯 (12)4.3默认显示页面 (12)4.4显示结构 (13)4.5画面详细说明 (13)4.5.1数据查询 (14)4.5.2定值查询 (15)4.5.3事件记录 (16)4.5.4参数设置 (18)4.5.5装置维护 (21)4.5.6装置信息 (22)4.5.7定值清单 (23)5安装调试说明 (26)5.1安装 (26)5.1.1装置安装图 (27)5.1.2背板端子布置 (27)5.1.3端子排总体布置: (27)5.1.4模拟量输入 (28)5.1.5工作电源 (28)5.1.6接地线的连接 (28)5.1.7通信接线 (28)5.2开出继电器的应用 (28)5.3开关量输入的应用 (28)5.4通电试验 (28)5.5模拟试验 (29)5.6装置故障分析 (29)6接线原理图 (31)7售后服务承诺 (32)7.1质量保证 (32)7.2装置升级 (32)7.3质保范围 (32)附录1:手册变更信息 (33)危险和警告本设备只能由专业人士进行安装,对于因不遵守本手册的说明所引起的故障,厂家将不承担任何责任。
AiP1651中文使用手册

江苏省无锡市蠡园经济开发区滴翠路 100 号 9 栋 2 层
http://www.i-core. cn
邮编:214072
第 5 页 共 11 页 版本:2012-01-B1
表 733-11-I
无锡中微爱芯电子有限公司
Wuxi I-CORE Electronics Co., Ltd.
写SRAM 数据地址自动加1 模式:
DIG1
SG1 SG2 SG3 SG4 SG5 SG6 SG7
a
DPY
b
a
cf d
g
b
ee
c
f
d
g [LEDgn]
DIG2
SG1 S1 SG2 S2 SG3 S3 SG4 S4 SG5 S5 SG6 S6 SG7 S7
滤波 电容与 IC的VDD、GND的回 路应尽 量短
VDD
104 + 100uF
SG1 SG2 SG3 SG4 SG5 SG6 SG7
编号:AiP1651-AX-BJ-81
3.3、电气特性 参数名称
符号
测试条件
规范值
单
最小 典型 最大
位
电气特性(Ta = -40~+85℃,VDD = 4.5 ~ 5.5 V,GND = 0 V)
i-core IOL1
低电平输出电流 IOL2
高电平输出电流
低电平输出电流 高电平输出电流 容许量 输出上拉电阻 输入电流
-50 200 400 -40~+85 -65~+150 245 250
3.2、推荐使用条件(Ta=-40~+85℃,VDD=4.5~5.5V,GND=0V)
单位 V V mA mA mW ℃ ℃
ISL6115芯片手册
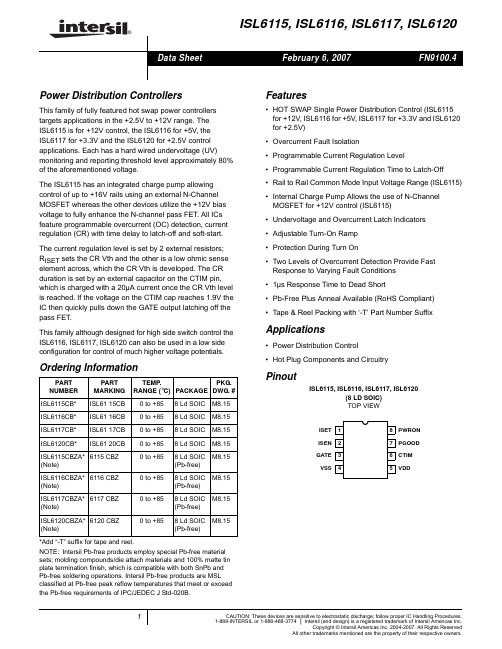
®ISL6115, ISL6116, ISL6117, ISL6120Power Distribution ControllersThis family of fully featured hot swap power controllers targets applications in the +2.5V to +12V range. TheISL6115 is for +12V control, the ISL6116 for +5V, theISL6117 for +3.3V and the ISL6120 for +2.5V control applications. Each has a hard wired undervoltage (UV) monitoring and reporting threshold level approximately 80% of the aforementioned voltage.The ISL6115 has an integrated charge pump allowing control of up to +16V rails using an external N-Channel MOSFET whereas the other devices utilize the +12V bias voltage to fully enhance the N-channel pass FET. All ICs feature programmable overcurrent (OC) detection, current regulation (CR) with time delay to latch-off and soft-start.The current regulation level is set by 2 external resistors;R ISET sets the CR Vth and the other is a low ohmic sense element across, which the CR Vth is developed. The CR duration is set by an external capacitor on the CTIM pin, which is charged with a 20µA current once the CR Vth level is reached. If the voltage on the CTIM cap reaches 1.9V the IC then quickly pulls down the GATE output latching off the pass FET.This family although designed for high side switch control the ISL6116, ISL6117, ISL6120 can also be used in a low side configuration for control of much higher voltage potentials.Features•HOT SWAP Single Power Distribution Control (ISL6115 for +12V, ISL6116 for +5V, ISL6117 for +3.3V and ISL6120 for +2.5V)•Overcurrent Fault Isolation•Programmable Current Regulation Level •Programmable Current Regulation Time to Latch-Off •Rail to Rail Common Mode Input Voltage Range (ISL6115)•Internal Charge Pump Allows the use of N-Channel MOSFET for +12V control (ISL6115)•Undervoltage and Overcurrent Latch Indicators •Adjustable Turn-On Ramp•Protection During Turn On•Two Levels of Overcurrent Detection Provide Fast Response to Varying Fault Conditions•1µs Response Time to Dead Short•Pb-Free Plus Anneal Available (RoHS Compliant)•Tape & Reel Packing with ‘-T’ Part Number Suffix Applications•Power Distribution Control•Hot Plug Components and CircuitryPinoutISL6115, ISL6116, ISL6117, ISL6120(8 LD SOIC)TOP VIEWOrdering InformationPART NUMBERPARTMARKINGTEMP.RANGE (°C)PACKAGEPKG.DWG. #ISL6115CB*ISL61 15CB0 to +858 Ld SOIC M8.15 ISL6116CB*ISL61 16CB0 to +858 Ld SOIC M8.15 ISL6117CB*ISL61 17CB0 to +858 Ld SOIC M8.15 ISL6120CB*ISL61 20CB0 to +858 Ld SOIC M8.15ISL6115CBZA* (Note)6115 CBZ0 to +858 Ld SOIC(Pb-free)M8.15ISL6116CBZA* (Note)6116 CBZ0 to +858 Ld SOIC(Pb-free)M8.15ISL6117CBZA* (Note)6117 CBZ0 to +858 Ld SOIC(Pb-free)M8.15ISL6120CBZA* (Note)6120 CBZ0 to +858 Ld SOIC(Pb-free)M8.15*Add “-T” suffix for tape and reel.NOTE:Intersil Pb-free products employ special Pb-free material sets; molding compounds/die attach materials and 100% matte tin plate termination finish, which is compatible with both SnPb and Pb-free soldering operations. Intersil Pb-free products are MSL classified at Pb-free peak reflow temperatures that meet or exceed the Pb-free requirements of IPC/JEDEC J Std-020B.ISETISENGATEVSS12348765PWRONPGOODCTIMVDDApplication One - High Side ControllerApplication Two - Low Side Controller+12V-+PWRONLOADPGOODOC12348765ISL6115+V supply to be controlledISL6116ISL6117ISL6120LOAD12V REG+VBUSOC12348765PWRONISL6116/7/20Simplified Block Diagram+-I SETI SENGATEV SSV DD CTIMPGOODPWRONCLIMWOCLIMENABLEOC10µAFALLING EDGE DELAY18V+- V REF +- 1.86V12V+-R R SQN QENABLEPOR V DD8VRISING EDGE PULSE+-+-UV18V20µA7.5K+-+-20µAUV DISABLEISL611X Pin DescriptionsPIN #SYMBOL FUNCTIONDESCRIPTION1ISET Current Set Connect to the low side of the current sense resistor through the current limiting set resistor. This pin functions as the current limit programming pin.2ISEN Current SenseConnect to the more positive end of sense resistor to measure the voltage drop across this resistor.3GATEExternal FET Gate Drive PinConnect to the gate of the external N-Channel MOSFET. A capacitor from this node to ground sets the turn-on ramp. At turn-on this capacitor will be charged to V DD +5V (ISL6115) and to V DD (ISL6116, ISL6117, ISL6120) by a 10μA current source.4 VSS Chip Return 5V DD Chip Supply 12V chip supply. This can be either connected directly to the +12V rail supplying the switched load voltage or to a dedicated V SS +12V supply.6CTIMCurrent Limit Timing CapacitorConnect a capacitor from this pin to ground. This capacitor determines the time delaybetween an overcurrent event and chip output shutdown (current limit time-out). The duration of current limit time-out is equal to 93k Ω x C TIM .7 PGOODPower Good IndicatorIndicates that the voltage on the ISEN pin is satisfactory. PGOOD is driven by an open drain N-Channel MOSFET and is pulled low when the output voltage (VISEN) is less than the UV level for the particular IC.8 PWRON Power ONPWRON is used to control and reset the chip. The chip is enabled when PWRON pin is driven high to a maximum of 5V or is left open. After a current limit time out, the chip is reset by a low level signal applied to this pin. This input has 20μA pull up capability.Absolute Maximum Ratings T A = +25°C Thermal InformationV DD . . . . . . . . . . . . . . . . . . . . . . . . . . . . . . . . . . . . . . -0.3V to +16V GATE. . . . . . . . . . . . . . . . . . . . . . . . . . . . . . . . . . . -0.3V to V DD+8V ISEN, PGOOD, PWRON, CTIM, ISET. . . . . . . -0.3V to V DD + 0.3V ESD Classification. . . . . . . . . . . . . . . . . . . . . . . . . . . . . . . . . . . 5kV Operating ConditionsV DD Supply Voltage Range. . . . . . . . . . . . . . . . . . . . . . +12V ±15% Temperature Range (T A) . . . . . . . . . . . . . . . . . . . . . . . 0°C to +85°C Thermal Resistance (Typical, Note 1)θJA (°C/W) SOIC Package. . . . . . . . . . . . . . . . . . . . . . . . . . . . . 98 Maximum Junction Temperature (Plastic Package) . . . . . . .+150°C Maximum Storage Temperature Range. . . . . . . . . .-65°C to +150°C Maximum Lead Temperature (Soldering 10s) . . . . . . . . . . . .+300°C (SOIC - Lead Tips Only)CAUTION: Stresses above those listed in “Absolute Maximum Ratings” may cause permanent damage to the device. This is a stress only rating and operation of the device at these or any other conditions above those indicated in the operational sections of this specification is not implied.NOTES:1.θJA is measured with the component mounted on a high effective thermal conductivity test board in free air. (See Tech Brief, #TB379.1 fordetails.)2.All voltages are relative to GND, unless otherwise specified3.G.N.T. Guaranteed by design and characterization but Not Tested.Electrical Specifications V DD = 12V, T A = T J = 0°C to +85°C, Unless Otherwise SpecifiedPARAMETER SYMBOL TEST CONDITIONS MIN TYP MAX UNITS CURRENT CONTROLISET Current Source I ISET_ft18.52021.5μA ISET Current Source I ISET_pt T J = +15°C to +55°C192021μA Current Limit Amp Offset Voltage Vio_ft V ISET - V ISEN-606mV Current Limit Amp Offset Voltage Vio_pt V ISET - V ISEN, T J = +15°C to +55°C-202mV GATE DRIVEGATE Response Time To Severe OC pd_woc_amp V GATE to 10.8V-100-ns GATE Response Time to Overcurrent pd_oc_amp V GATE to 10.8V-600-ns GATE Turn-On Current I GATE V GATE to = 6V8.41011.6μA GATE Pull Down Current OC_GATE_I_4V Overcurrent4575-mA GATE Pull Down Current (3)WOC_GATE_I_4V Severe Overcurrent0.50.8-A ISL6115 Undervoltage Threshold12V UV_VTH9.29.610V ISL6115 GATE High Voltage12VG GATE Voltage V DD + 4.5V V DD + 5V-V ISL6116 Undervoltage Threshold5V UV_VTH 4.0 4.35 4.5V ISL6117 Undervoltage Threshold3V UV_VTH 2.4 2.6 2.8V ISL6120 Undervoltage Threshold2V UV_VTH 1.8 1.85 1.9V ISL6116, 17, 20 GATE High Voltage VG GATE Voltage V DD - 1.5V V DD-V BIASV DD Supply Current I VDD-35mAV DD POR Rising Threshold V DD_POR_L2H VDD Low to High7.88.49VV DD POR Falling Threshold V DD_POR_H2L VDD High to Low7.58.18.7VV DD POR Threshold Hysteresis V DD_POR_HYS V DD_POR_L2H - V DD_POR_H2L0.10.30.6V PWRON Pull-Up Voltage PWRN_V PWRON Pin Open 2.7 3.2-V PWRON Rising Threshold PWR_Vth 1.4 1.7 2.0V PWRON Hysteresis PWR_hys130170250mV PWRON Pull-Up Current PWRN_I91725μADescription and OperationThe members of this family are single power supply distribution controllers for generic hot swap applications across the +2.5V to +12V supply range. The ISL6115 is targeted for +12V switching applications whereas theISL6116 is targeted for +5V, the ISL6117 for +3.3V and the ISL6120 for +2.5V applications. Each IC has a hardwired undervoltage (UV) threshold level approximately 17% lower than the stated voltages.These ICs feature a highly accurate programmable overcurrent (OC) detecting comparator, programmablecurrent regulation (CR) with programmable time delay to latch off, and programmable soft-start turn-on ramp all set with a minimum of external passive components. The ICs alsoinclude severe OC protection that immediately shuts down the MOSFET switch should a rapid load current transient such as a near dead short cause the CR Vth to exceed theprogrammed level by 150mV. Additionally, the ICs have a UV indicator and an OC latch indicator. The functionality of the PGOOD feature is enabled once the IC is biased, monitoring and reporting any UV condition on the ISEN pin.Upon initial power up, the IC can either isolate the voltage supply from the load by holding the external N-ChannelMOSFET switch off or apply the supply rail voltage directly to the load for true hot swap capability. The PWRON pin must be pulled low for the device to isolate the power supply from the load by holding the external N-channel MOSFET off. With the PWRON pin held high or floating the IC will be in true hot swap mode. In both cases the IC turns on in a soft-start mode protecting the supply rail from sudden in-rush current.At turn-on, the external gate capacitor of the N-Channel MOSFET is charged with a 10μA current source resulting in a programmable ramp (soft-start turn-on). The internal ISL6115 charge pump supplies the gate drive for the 12V supply switch driving that gate to ~V DD +5V, for the other three ICs the gate drive voltage is limited to the chip bias voltage, VDD.Load current passes through the external current senseresistor. When the voltage across the sense resistor exceeds the user programmed CR voltage threshold value, (see T able 1 for R ISET programming resistor value and resulting nominal current regulation threshold voltage, V CR ) thecontroller enters its current regulation mode. At this time, the time-out capacitor, on C TIM pin is charged with a 20μA current source and the controller enters the current limit time to latch-off period. The length of the current limit time to latch-offduration is set by the value of a single external capacitor (see T able 2) for CTIM capacitor value and resulting nominal current limited time out to latch-off duration placed from the CTIM pin (pin 6) to ground. The programmed current level is held until either the OC event passes or the time out period expires. If the former is the case then the N-Channel MOSFET is fully enhanced and the C TIM capacitor isdischarged. Once CTIM charges to 1.87V, signaling that the time out period has expired an internal latch is set whereby the FET gate is quickly pulled to 0V turning off the N-Channel MOSFET switch, isolating the faulty load.This IC responds to a severe overcurrent load (defined as a voltage across the sense resistor >150mV over the OC Vth set point) by immediately driving the N-Channel MOSFET gate to 0V in about 10μs. The gate voltage is then slowly ramped up turning on the N-Channel MOSFET to the programmed current regulation level; this is the start of the time out period.Upon a UV condition the PGOOD signal will pull low when tied high through a resistor to the logic or VDD supply. This pin is a UV fault indicator. For an OC latch off indication, monitor CTIM, pin 6. This pin will rise rapidly from 1.9V to VDD once the time out period expires.See Figures 12 to 16 for waveforms relevant to text.The IC is reset after an OC latch-off condition by a low level on the PWRON pin and is turned on by the PWRON pin being driven high.CURRENT REGULATION DURATION/POWER GOOD C TIM Charging CurrentC TIM _ichg0V CTIM = 0V162023μA C TIM Fault Pull-Up Current (Note 3)-20-mA Current Limit Time-Out Threshold Voltage C TIM _Vth CTIM Voltage 1.3 1.8 2.3V Power Good Pull Down CurrentPG_IpdV OUT = 0.5V-8-mAElectrical SpecificationsV DD = 12V, T A = T J = 0°C to +85°C, Unless Otherwise Specified (Continued)PARAMETERSYMBOLTEST CONDITIONSMINTYPMAX UNITSTABLE 1.R ISET RESISTORNOMINAL OC VTH10k Ω200mV 4.99k Ω100mV 2.5k Ω50mV 750Ω15mVNOTE:Nominal Vth = R ISET x 20μA.TABLE 2.C TIM CAPACITORNOMINAL CURRENT LIMITED PERIOD0.022μF 2ms 0.047μF 4.4ms 0.1μF9.3msNOTE:Nominal time-out period = C TIM x 93k Ω.Application ConsiderationsDuring the soft-start and the time-out delay duration with the IC in its current limit mode, the V GS of the external N-Channel MOSFET is reduced driving the MOSFET switch into a (linear region) high r DS(ON) state. Strike a balance between the CR limit and the timing requirements to avoid periods when the external N-Channel MOSFET s may be damaged or destroyed due to excessive internal power dissipation. Refer to the MOSFET SOA information in the manufacturer’s data sheet.When driving particularly large capacitive loads a longer soft-start time to prevent current regulation upon charging and a short CR time may offer the best application solution relative to reliability and FET MTF.Physical layout of R SENSE resistor is critical to avoid the possibility of false overcurrent occurrences. Ideally, trace routing between the R SENSE resistors and the IC is as direct and as short as possible with zero current in the sense lines (See Figure 1).Using the ISL6116 as a -48V Low Side Hot Swap Power ControllerTo supply the required V DD , it is necessary to maintain the chip supply 10 to 16V above the -48V bus. This may be accomplished with a suitable regulator between the voltage rail and pin 5 (VDD). By using a regulator, the designer may ignore the bus voltage variations. However, a low-costalternative is to use a Zener diode (See Figure 2 for typical 5A load control); this option is detailed below.Note that in this configuration the PGOOD feature (pin 7) is not operational as the I SEN pin voltage is always < UV threshold.See Figures 17 to 20 for waveforms relevant to -48V and other high voltage applications.Biasing the ISL6116Table 3 gives typical component values for biasing the ISL6116 in a ±48V application. The formulas andcalculations deriving these values are also shown below.When using the ISL6116 to control -48V, a Zener diode may be used to provide the +12V bias to the chip. If a Zener is used then a current limit resistor should also be used. Several items must be taken into account when choosing values for the current limit resistor (R CL ) and Zener Diode (DD1):•The variation of the V BUS (in this case, -48V nominal)•The chip supply current needs for all functional conditions •The power rating of R CL .•The current rating of DD1Formulas1.Sizing R CL :R CL = (V BUS,MIN - 12)/I CHIP 2.Power Rating of R CL :P RCL = I C (V BUS,MAX - 12)3.DD1 Current Rating:I DD1 = (V BUS,MAX - 12)/R CLCORRECTTO ISEN ANDCURRENT SENSE RESISTORINCORRECTFIGURE 1.SENSE RESISTOR PCB LAYOUTR ISETTABLE 3.TYPICAL VALUES FOR A -48V HOT SWAPAPPLICATION SYMBOLPARAMETERR CL 1.58k Ω, 1WDD112V Zener Diode, 50mA Reverse CurrentV BUSLOAD12348765ISL6116PWRONNCFIGURE 2.-48VR CL DD112V1.58k Ω1W0.01µF0.047µF1.47k Ω0.0051%0.001µF2k Ω1%ExampleA typical -48V supply may vary from -36 to -72V. Therefore,V BUS,MAX = -72V V BUS,MIN = -36V I CHIP = 15mA (max)Sizing R CL :R CL = (V BUS,MIN - 12)/I C R CL = (36 - 12)/0.015R CL = 1.6k Ω [Typical Value = 1.58k Ω]Power Rating of R CL :P RCL = I C (V BUS,MAX - 12)P RCL = (0.015)(72 - 12)P RCL = 0.9W [Typical Value = 1W]DD1 Current Rating:I DD1 = (VBUS,MAX - 12)/R CL I DD1 = (72 - 12)/1.58k ΩI DD1 = 38mA [Typical Value = 12V rating, 50mA reverse current]Typical Performance CurvesFIGURE 3.VDD BIAS CURRENTFIGURE 4.ISET SOURCE CURRENTFIGURE 5.C TIM CURRENT SOURCEFIGURE 6.C TIM OC VOLTAGE THRESHOLD4.54.03.53.02.52.020305080100TEMPERATURE (°C)5.0S U P P L Y C U R R E N T (m A )104060709020.2TEMPERATURE (°C)I S E T C U R R E N T µA )20305080100104060709020.019.019.219.419.619.820.5020.3220.0019.66C T I M = 0V , C U R R E N T S O U R C E (µA )TEMPERATURE (°C)20305080100104060709019.5020.1619.82C TIM - 0V1.891.881.871.861.851.83C T I M O C V O L T A G E T H R E S H O LD (V )TEMPERATURE (°C)2030508010010406070901.84FIGURE 7.ISL6115/6116 UV THRESHOLD FIGURE 8.ISL6117/6120 UV THRESHOLDFIGURE 9.GATE CHARGE CURRENT FIGURE 10.GATE DRIVE VOLTAGE, VDD = 12VFIGURE 11.POWER ON RESET VOLTAGE THRESHOLD FIGURE 12.ISL6115 +12V TURN-ONTEMPERATURE (°C)I S L 6115, 12V U V T H R E S H O L D (V )203050801001040607090I S L 6116, 5V U V T H R E S H O L D (V )9.769.749.754.374.354.36ISL6116ISL6115TEMPERATURE (°C)I S L 6117, 3.3V U V T H R E S H O L D (V )203050801001040607090I S L 6120, 2.5V U V T H R E S H O L D (V )2.702.651.8601.8501.855ISL61172.60ISL6120TEMPERATURE (°C)203050801001040607090G A T E C H A R G E C U R R E N T (μA )9.69.79.89.910.010.110.217.20017.18317.16617.15017.13317.10012.0011.9911.9811.9711.9611.9511.94TEMPERATURE (°C)I S L 6116,17,20 G A T E D R I V E (V )I S L 6115, G A T E D R I V E (V )20305080100104060709017.116P O W E R O N R E S E T (V )TEMPERATURE (°C)2030508010010406070908.08.58.18.28.38.4VDD LO TO HIVDD HI TO LO5V/DIV. 0.5A/DIV 1ms/DIVGATE VOUTPWRONIOUTPGOODFIGURE 13.ISL6116 +5V TURN-ON FIGURE 14.ISL6115 ‘LOW’ OVERCURRENT RESPONSEFIGURE 15.ISL6115 ‘HIGH’ OVERCURRENT RESPONSE FIGURE 16.ISL6116 ‘HIGH’ OVERCURRENT RESPONSEFIGURE 17.+50V LOW SIDE SWITCHING CGATE = 100pF FIGURE 18.-50V LOW SIDE SWITCHING CGATE = 1000pF2V/DIV 0.5A/DIV 1ms/DIV GATEVOUTPWRONIOUTPGOOD5V/DIV 0.5A/DIV 1ms/DIVCTIMIOUTPGOODVOUTGATE5V/DIV 0.5A/DIV 1ms/DIVIOUTGATECTIMPGOODVOUT 2V/DIV 0.5A/DIV 1ms/DIVIOUTPGOOD CTIMGATEVOUT5ms/DIVVDRAIN 10V/DIV.+50VPWRON 5V/DIV.0V0VVGATE 5V/DIV.IOUT 1A/DIV.5ms/DIVIOUT 1A/DIV.0V0VVGATE 5V/DIV.EN 5V/DIV.-50VVDRAIN 10V/DIV.ISL6115EVAL1 BoardThe ISL6115EVAL1 is configured as a +12V high side switch controller with the CR level set at ~1.5A. (See Figure 21 for ISL6115EVAL1 schematic and Table 4 for BOM). Bias and load connection points are provided along with test points for each IC pin.With the chip to be biased from the +12V bus beingswitched, through B2, GND B5, the load connected between B3 and B4 and with jumper J1 installed the ISL6115 can be evaluated. PWRON pin pulls high enabling the ISL6115 if not driven low.With R2 = 750Ω the CR Vth is set to 15mV and with the 10m Ω sense resistor the ISL6115EVAL1 has a nominal CR level of 1.5A. The 0.047μF delay time to latch-off capacitors results in a nominal 4.4ms before latch-off of outputs after an OC event.Also included with the ISL6115EVAL1 board are one each of the ISL6116, ISL6117 and ISL6120 for evaluation.ISL6116EVAL1 BoardThe ISL6116EVAL1 is default configured as a negative voltage low side switch controller with a ~2.4A CR level. (See Figure 22 for ISL6116EVAL1 schematic and Table 4 for BOM and component description). This basic configuration is capable of controlling both larger positive or negative potential voltages with minimal changes.Bias and load connection points are provided in addition to test points, TP1-8 for each IC pin. The terminals, J1 and J4 are for the bus voltage and return, respectively, with the more negative potential being connected to J4. With the load between terminals J2 and J3 the board is now configured for evaluation. The device is enabled through LOGIN, TP9 with a TTL signal. ISL6116EVAL1 includes a level shifting circuit with an opto-coupling device for the PWRON input so that standard TTL logic can be translated to the -V reference for chip control.When controlling a positive voltage, PWRON can be accessed at TP8.The ISL6116EVAL1 is provided with a high voltage linear regulator for convenience to provide chip bias from ±24V to ±350V. This can be removed and replaced with the zener & resistor bias scheme as discussed earlier. High voltage regulators and power discrete devices are no longer available from Intersil but can be purchased from other semiconductor manufacturers.Reconfiguring the ISL6116EVAL1 board for a higher CR level can be done by changing the R SENSE and R ISET resistor values as the provided FET is 75A rated. Ifevaluation at >60V, an alternate FET must be chosen with an adequate BV DSS .FIGURE 19.+350V LOW SIDE SWITCHING CGATE = 100pF FIGURE 20.+350V LOW SIDE SWITCHING CGATE = 1000pF2ms/DIV+350V0VIOUT 1A/DIVVDRAIN 50V/DIVVGATE 5V/DIVPWRON 5V/DIV2ms/DIV+350V0VIOUT 1A/DIVPWRON 5V/DIVVGATE 5V/DIV.VDRAIN 50V/DIVFIGURE 21.ISL6115EVAL1 HIGH SIDE SWITCH APPLICATIONFIGURE 22.ISL6116EVAL1 NEGATIVE VOLTAGE LOW SIDECONTROLLER56874321ISL6115Q1R2R3C1C2R4D1R5D2JP1V BIAS V+ B2DD1+12VC3R1LOAD -+PWRON 3.3VB1B5B3B4U156874321ISL6116Q2R2R7C1R5D2C3R1LOADDD13.3V+VBUS-VBUSOT1R9R8HI J2J3 LOR6R11R10ONOFF 0-5VU1J1J4PWRONTP8LOGIN TP9R G 1TABLE 4.BILL OF MATERIALS, ISL6115EVAL1, ISL6116EVAL1COMPONENT DESIGNATORCOMPONENT NAMECOMPONENT DESCRIPTIONQ1HUF76132SK811.5m Ω, 30V, 11.5A Logic Level N-Channel Power MOSFET or equiv.Q2HUF7554S3S10m Ω, 80V, 75A N-Channel Power MOSFET or equiv.R1Load Current Sense ResistorDale, WSL-2512 10m Ω 1W Metal Strip ResistorHigh Side R2Overcurrent Voltage Threshold Set Resistor 750Ω 805 Chip Resistor (Vth = 15mV)Low side R2Overcurrent Voltage Threshold Set Resistor 1.21k Ω 805 Chip Resistor (Vth = 24mV)C2Time Delay Set Capacitor 0.047μF 805 Chip Capacitor (4.5ms)C1Gate Timing Capacitor 0.001μF 805 Chip Capacitor (<2ms)C3IC Decoupling Capacitor 0.1μF 805 Chip Capacitor R3Gate Stability Resistor 20Ω 805 Chip Resistor R7Gate to Drain Resistor 2k Ω 805 Chip ResistorJP1Bias Voltage Selection Jumper Install if switched rail voltage is = +12V ±15%. Remove and provide separate +12V bias voltage to U1 via TP5 if ISL6116, ISL6117, ISL6120 being evaluated.R4, R5LED Series Resistors 2.32k Ω 805 Chip Resistor D1, D2Fault Indicating LEDs Low Current Red SMD LEDDD1Fault Voltage Dropping Diode 3.3V Zener Diode, SOT-23 SMD 350mW OT1PWRON Level Shifting Opto-Coupler PS2801-1 NECR8Level Shifting Bias Resistor 2.32k Ω 805 Chip Resistor R9Level Shifting Bias Resistor 1.18k Ω 805 Chip Resistor R10Level Shifting Bias Resistor 200Ω 805 Chip Resistor RG1HIP5600ISHigh Voltage Linear Regulator R6Linear Regulator RF1 1.78k Ω 805 Chip Resistor R11Linear Regulator RF215k Ω 805 Chip ResistorTP1-TP8Test Points for Device Pin Numbers 1-8All Intersil U.S. products are manufactured, assembled and tested utilizing ISO9000 quality systems.Intersil Corporation’s quality certifications can be viewed at /design/qualityIntersil products are sold by description only. Intersil Corporation reserves the right to make changes in circuit design, software and/or specifications at any time without notice. Accordingly, the reader is cautioned to verify that data sheets are current before placing orders. Information furnished by Intersil is believed to be accurate and reliable. However, no responsibility is assumed by Intersil or its subsidiaries for its use; nor for any infringements of patents or other rights of third parties which may result from its use. No license is granted by implication or otherwise under any patent or patent rights of Intersil or its subsidiaries.For information regarding Intersil Corporation and its products, see Small Outline Plastic Packages (SOIC)NOTES:1.Symbols are defined in the “MO Series Symbol List” in Section2.2 of Publication Number 95.2.Dimensioning and tolerancing per ANSI Y14.5M -1982.3.Dimension “D” does not include mold flash, protrusions or gate burrs. Mold flash, protrusion and gate burrs shall not exceed 0.15mm (0.006inch) per side.4.Dimension “E” does not include interlead flash or protrusions. Inter-lead flash and protrusions shall not exceed 0.25mm (0.010 inch) per side.5.The chamfer on the body is optional. If it is not present, a visual index feature must be located within the crosshatched area.6.“L” is the length of terminal for soldering to a substrate.7.“N” is the number of terminal positions.8.Terminal numbers are shown for reference only.9.The lead width “B”, as measured 0.36mm (0.014 inch) or greater above the seating plane, shall not exceed a maximum value of 0.61mm (0.024 inch).10.Controlling dimension:MILLIMETER. Converted inch dimensionsare not necessarily exact.M8.15 (JEDEC MS-012-AA ISSUE C)8 LEAD NARROW BODY SMALL OUTLINE PLASTIC PACKAGESYMBOLINCHESMILLIMETERS NOTESMIN MAX MIN MAX A0.05320.0688 1.35 1.75-A10.00400.00980.100.25-B 0.0130.0200.330.519C 0.00750.00980.190.25-D 0.18900.1968 4.80 5.003E 0.14970.1574 3.80 4.004e 0.050 BSC 1.27 BSC-H0.22840.2440 5.80 6.20-h 0.00990.01960.250.505L 0.0160.0500.401.276N887a0°8°0°8°-Rev. 1 6/05。
L series IPM 应用手册

第5代IPM应用手册Part 2第5代IPM应用手册L系列L系列智能功率模块 系列智能功率模块 应用和设计手册61第5代IPM应用手册1. L系列IPM的 概 念1.1 IPM的优点IPM自从三菱电机最初开发和量产以来,其有用性已经得到广泛认可并占据了功率器件的一个分支。
越来越多 的制造商开发了同样概念的产品。
本应用手册介绍的L系列IPM具有如下优点。
L系列IPM通过采用低功耗IGBT减少了噪声的产生,实现了高性能和环保的两者兼顾。
另外,由于同系列IPM 600V/1200V产品封装相同,从而也有助于实现装置的小型化。
TM 由于采用CSTBT ,实现了低功耗。
影响噪声产生的输出电流在小电流范围内时放慢开关速度,以此降低IPM 放射噪声。
因此不需要噪声滤波器,使得装置的小型化和高性能化成为可能。
小型・新封装◆ ◆ ◆ 50~150A/600V, 25~75A/1200V的模块开发了新的小型封装。
~75A的模块,除了主端子是螺丝型的模 块外,还有一部分节省空间的针型引脚的模块产品线。
450~600A/600V, 200~450A/1200V容量级的模块第一次开发出内含6单元IGBT的小型封装。
200~300A/600V, 100~150A/1200V在开发了新封装的同时,也实现了与原来的S-DASH系列的兼容。
低功耗◆ 采用了第5代1μm IGBT硅片(CSTBT ),降低了功耗,可以减小了散热器的体积。
TM缩短了项目开发周期◆ 内置IGBT的栅极驱动电路。
控制电源只需+15V(不需要反向偏压电源),简化了周边电路的设计。
实现了控制电路CMOS化,降低了控制电路的电力功耗。
内置故障检测和保护电路(短路过电流、过温、控制电源欠压)。
这样就减少了原来的设计 >> 试制 >> 评价 >> 再设计的多次循环工作。
◆不需要防静电措施◆ 和双极性TTL一样使用,不需要另外针对IGBT模块的措施。
U6115PDF内置三极管5W开关电源
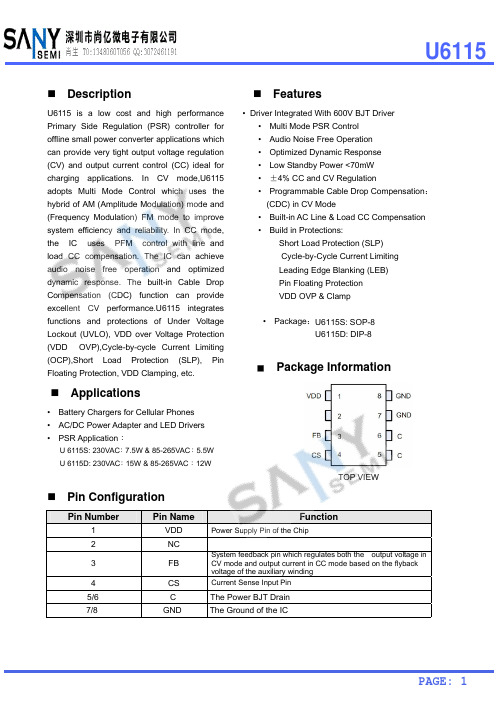
PAGE: 3
U6115
Short Load Protection (SLP) Threshold Short Load Protection (SLP) Debounce Time
Demagnetization Comparator Threshold Minimum OFF time Maximum OFF time Maximum Cable Drop compensation current
Value
7-24 -40 to 85 -65 to 150 70 35
Unit
V ºC ºC kHz KHz
Electrical Characteristics (TA = 25°C, VDD=20V, if not otherwise noted)
Parameter Supply Voltage Section(VDD Pin) Start-up current into VDD pin Operation Current Standby Current
VFB_SLP TFB_SHORT VFB_DEM T Off_min T Off_max ICable_max
(Note 3)
0.6
v
ms
10
25 2 5 60
mV us ms uA
Current Sense Input Section (CS Pin)
CS Input Leading Edge Blanking Time Current limiting threshold Over Current Detection and Control Delay
Features
• Driver Integrated With 600V BJT Driver • Multi Mode PSR Control • Audio Noise Free Operation • Optimized Dynamic Response • Low Standby Power <70mW • ±4% CC and CV Regulation • Programmable Cable Drop Compensation: (CDC) in CV Mode • Built-in AC Line & Load CC Compensation • Build in Protections: Short Load Protection (SLP) Cycle-by-Cycle Current Limiting Leading Edge Blanking (LEB) Pin Floating Protection VDD OVP & Clamp
瑞萨电子ISL2110、ISL2111 100V、3A 4A Peak高频半桥驱动器说明书
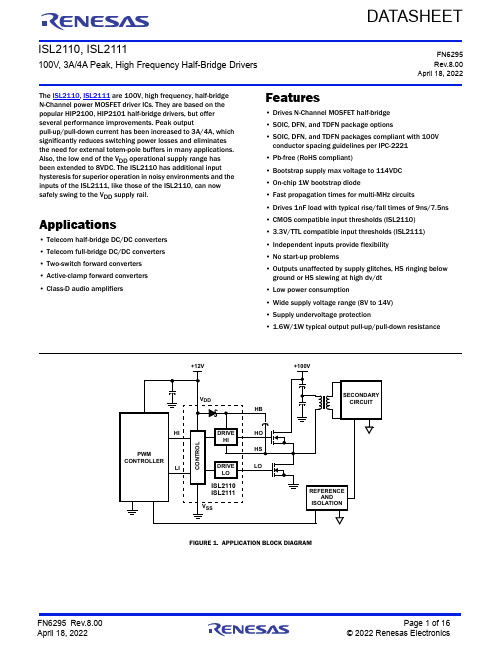
FN6295Rev.8.00April 18, 2022ISL2110, ISL2111100V, 3A/4A Peak, High Frequency Half-Bridge DriversDATASHEETThe ISL2110, ISL2111 are 100V, high frequency, half-bridge N-Channel power MOSFET driver ICs. They are based on the popular HIP2100, HIP2101 half-bridge drivers, but offer several performance improvements. Peak outputpull-up/pull-down current has been increased to 3A/4A, which significantly reduces switching power losses and eliminates the need for external totem-pole buffers in many applications. Also, the low end of the V DD operational supply range has been extended to 8VDC. The ISL2110 has additional input hysteresis for superior operation in noisy environments and the inputs of the ISL2111, like those of the ISL2110, can now safely swing to the V DD supply rail.Applications•Telecom half-bridge DC/DC converters •Telecom full-bridge DC/DC converters •Two-switch forward converters •Active-clamp forward converters •Class-D audio amplifiersFeatures•Drives N-Channel MOSFET half-bridge •SOIC, DFN, and TDFN package options•SOIC, DFN, and TDFN packages compliant with 100V conductor spacing guidelines per IPC-2221•Pb-free (RoHS compliant)•Bootstrap supply max voltage to 114VDC •On-chip 1W bootstrap diode•Fast propagation times for multi-MHz circuits•Drives 1nF load with typical rise/fall times of 9ns/7.5ns •CMOS compatible input thresholds (ISL2110)•3.3V/TTL compatible input thresholds (ISL2111)•Independent inputs provide flexibility •No start-up problems•Outputs unaffected by supply glitches, HS ringing below ground or HS slewing at high dv/dt •Low power consumption•Wide supply voltage range (8V to 14V)•Supply undervoltage protection•1.6W/1W typical output pull-up/pull-down resistanceFIGURE 1.APPLICATION BLOCK DIAGRAMSECONDARY CIRCUIT+100VC O N T R O LCONTROLLERPWMLIHIHO LOV DDHSHB+12V V SSREFERENCEAND ISOLATIONDRIVE LODRIVE HIISL2110ISL2111Functional Block DiagramFIGURE 2.FUNCTIONAL BLOCK DIAGRAMUNDER VOLTAGEV DDHILI V SSDRIVERDRIVERHBHOHSLOLEVEL SHIFTUNDER VOLTAGEEPAD (DFN Package Only)ISL2111ISL2111*EPAD = Exposed Pad. The EPAD is electrically isolated from all other pins. For best thermal performance, connect the EPAD to the PCB power ground plane.Application DiagramsSECONDARY ISOLATIONPWM+48V+12VCIRCUITFIGURE 3.TWO-SWITCH FORWARD CONVERTERISL2110ISL2111SECONDARY CIRCUITISOLATIONPWM+48V+12VFIGURE 4.FORWARD CONVERTER WITH AN ACTIVE-CLAMPISL2110ISL2111Ordering InformationPART NUMBER (Notes2, 3)PARTMARKINGPACKAGE DESCRIPTION(RoHS COMPLIANT)PKG.DWG. #CARRIER TYPE(Notes1)TEMP RANGEISL2110ABZ 2110ABZ 8 Ld SOIC M8.15Tube-40 to +125°CISL2110ABZ -T Reel, 2.5kISL2110AR4Z2110AR4Z 12 Ld 4x4 DFN L12.4x4A TubeISL2110AR4Z-T Reel, 6kISL2111ABZ2111ABZ 8 Ld SOIC M8.15TubeISL2111ABZ-T Reel, 2.5kISL2111AR4Z2111AR4Z 12 Ld 4x4 DFN L12.4x4A TubeISL2111AR4Z-T Reel, 6kISL2111ARTZ2111ARTZ 10 Ld 4x4 TDFN L10.4x4TubeISL2111ARTZ-T Reel, 6kISL2111BR4Z2111BR4Z 8 Ld 4x4 DFN L8.4x4TubeISL2111BR4Z-T Reel, 6kNOTES:1.See TB347 for details about reel specifications.2.These Pb-free plastic packaged products employ special Pb-free material sets, molding compounds/die attach materials, and 100% matte tin plateplus anneal (e3 termination finish, which is RoHS compliant and compatible with both SnPb and Pb-free soldering operations). Pb-free products are MSL classified at Pb-free peak reflow temperatures that meet or exceed the Pb-free requirements of IPC/JEDEC J STD-020.3.For Moisture Sensitivity Level (MSL), please see device information page for ISL2110, ISL2111. For more information on MSL, see TB363.Pin ConfigurationsISL2111ARTZ (10 LD 4x4 TDFN)TOP VIEW ISL2110AR4Z, ISL2111AR4Z(12 LD 4x4 DFN)TOP VIEW2 3 4 1 59 8 7 10 6VDD HB HO HS NC LOVSSLIHINCVDDNCNCHBHOLOVSSNCNCLIHS HI234151110912867EPAD**EPAD = EXPOSED PADISL2110ABZ, ISL2111ABZ(8 LD SOIC)TOP VIEWISL2111BR4Z (8 LD 4x4 DFN)TOP VIEWPin Configurations56874321VDD HB HO HSLO LI HIVSS 23417658VDD HB HO HSLO VSS LI HIEPAD**EPAD = EXPOSED PADPin DescriptionsSYMBOL DESCRIPTIONVDD Positive supply to lower gate driver. Bypass this pin to VSS.HB High-side bootstrap supply. External bootstrap capacitor is required. Connect positive side of bootstrap capacitor to this pin. Bootstrap diode is on-chip.HO High-side output. Connect to gate of high-side power MOSFET.HS High-side source connection. Connect to source of high-side power MOSFET. Connect negative side of bootstrap capacitor to this pin. HI High-side input LI Low-side inputVSS Chip negative supply, which will generally be ground.LO Low-side output. Connect to gate of low-side power MOSFET.NC No connectEPADExposed pad. Connect to ground or float. The EPAD is electrically isolated from all other pins.Absolute Maximum Ratings Thermal InformationSupply Voltage, V DD, V HB - V HS (Notes4, 5) . . . . . . . . . . . . . . . 0.3V to 18V LI and HI Voltages (Note5) . . . . . . . . . . . . . . . . . . . . . . .-0.3V to V DD + 0.3V Voltage on LO (Note5). . . . . . . . . . . . . . . . . . . . . . . . . . .-0.3V to V DD + 0.3V Voltage on HO relative to HS (Repetitive Transient < 100ns). . . . . . . . .-2V Voltage on LO relative to GND (Repetitive Transient < 100ns). . . . . . . .-2V Voltage on HO (Note5) . . . . . . . . . . . . . . . . . . . . . .V HS - 0.3V to V HB + 0.3V Voltage on HS (Continuous) (Note5). . . . . . . . . . . . . . . . . . . . . -1V to 110V Voltage on HB (Note5) . . . . . . . . . . . . . . . . . . . . . . . . . . . . . . . . . . . . . .118V Average Current in V DD to HB Diode . . . . . . . . . . . . . . . . . . . . . . . . . 100mA Maximum Recommended Operating ConditionsSupply Voltage, V DD. . . . . . . . . . . . . . . . . . . . . . . . . . . . . . . . . . . . . 8V to 14V Voltage on HS . . . . . . . . . . . . . . . . . . . . . . . . . . . . . . . . . . . . . . . . -1V to 100V Voltage on HS . . . . . . . . . . . . . (Repetitive Transient < 100ns) -5V to 105V Voltage on HB . . . . . . . . . . .V HS+7V to V HS+14V and V DD - 1V to V DD+100V HS Slew Rate. . . . . . . . . . . . . . . . . . . . . . . . . . . . . . . . . . . . . . . . . . . .<50V/ns Thermal Resistance (Typical)θJA (°C/W)θJC (°C/W) 8 Ld SOIC (Notes6, 9) . . . . . . . . . . . . . . . . . 954610 Ld TDFN (Notes7, 8) . . . . . . . . . . . . . . . 40 2.512 Ld DFN (Notes7, 8) . . . . . . . . . . . . . . . . 39 2.58 Ld DFN (Notes7, 8). . . . . . . . . . . . . . . . . . 40 4.0 Max Power Dissipation at +25°C in Free Air8 Ld SOIC (Notes6, 9). . . . . . . . . . . . . . . . . . . . . . . . . . . . . . . . . . . . . . .1.3W 10 Ld TDFN (Notes7, 8) . . . . . . . . . . . . . . . . . . . . . . . . . . . . . . . . . . . . .3.0W 12 Ld DFN (Notes7, 8) . . . . . . . . . . . . . . . . . . . . . . . . . . . . . . . . . . . . . .3.1W 8 Ld DFN (Notes7, 8). . . . . . . . . . . . . . . . . . . . . . . . . . . . . . . . . . . . . .3.1W Storage Temperature Range. . . . . . . . . . . . . . . . . . . . . . . .-65°C to +150°C Junction Temperature Range . . . . . . . . . . . . . . . . . . . . . . .-55°C to +150°C Pb-Free Reflow Profile. . . . . . . . . . . . . . . . . . . . . . . . . . . . . . . . . . see TB493CAUTION: Do not operate at or near the maximum ratings listed for extended periods of time. Exposure to such conditions may adversely impact product reliability and result in failures not covered by warranty.NOTES:4.The ISL2110 and ISL2111 are capable of derated operation at supply voltages exceeding 14V. Figure 24 shows the high-side voltage derating curvefor this mode of operation.5.All voltages referenced to V SS unless otherwise specified.6.θJA is measured with the component mounted on a high-effective thermal conductivity test board in free air. See Tech Brief TB379 for details.7.θJA is measured in free air with the component mounted on a high-effective thermal conductivity test board with “direct attach” features. See TechBrief TB379.8.For θJC, the “case temp” location is the center of the exposed metal pad on the package underside.9.For θJC, the “case temp” location is taken at the package top center.Electrical Specifications V DD = V HB = 12V, V SS = V HS = 0V, no load on LO or HO, unless otherwise specified.PARAMETERS SYMBOL TEST CONDITIONST J = +25°C T J = -40°C to +125°CUNIT MIN(Note10)TYPMAX(Note10)MIN(Note10)MAX(Note10)SUPPLY CURRENTSV DD Quiescent Current I DD ISL2110; LI = HI = 0V- 0.100.25-0.30mA V DD Quiescent Current I DD ISL2111; LI = HI = 0V- 0.300.45-0.55mA V DD Operating Current I DDO ISL2110; f = 500kHz- 3.4 5.0- 5.5mA V DD Operating Current I DDO ISL2111; f = 500kHz- 3.5 5.0- 5.5mA Total HB Quiescent Current I HB LI = HI = 0V-0.100.15-0.20mA Total HB Operating Current I HBO f = 500kHz- 3.4 5.0- 5.5mA HB to V SS Current, Quiescent I HBS LI = HI = 0V; V HB = V HS = 114V-0.05 1.50-10µA HB to V SS Current, Operating I HBSO f = 500kHz; V HB = V HS = 114V- 1.2---mA INPUT PINSLow Level Input Voltage Threshold V IL ISL2110 3.7 4.4- 3.5-V Low Level Input Voltage Threshold V IL ISL2111 1.4 1.8- 1.2-V High Level Input Voltage Threshold V IH ISL2110- 6.67.4-7.6V High Level Input Voltage Threshold V IH ISL2111- 1.8 2.2- 2.4V Input Voltage Hysteresis V IHYS ISL2110- 2.2---VInput Pull-Down Resistance R I-210-100500k ΩUNDERVOLTAGE PROTECTION V DD Rising Threshold V DDR 6.1 6.67.1 5.87.4V V DD Threshold Hysteresis V DDH -0.6---V HB Rising Threshold V HBR 5.5 6.1 6.8 5.07.1V HB Threshold Hysteresis V HBH-0.6---VBOOTSTRAP DIODELow Current Forward Voltage V DL I VDD-HB = 100µA -0.50.6-0.7V High Current Forward Voltage V DH I VDD-HB = 100mA -0.70.9-1V Dynamic Resistance R DI VDD-HB = 100mA-0.71-1.5ΩLO GATE DRIVER Low Level Output Voltage V OLL I LO = 100mA-0.10.18-0.25V High Level Output Voltage V OHL I LO = -100mA, V OHL = V DD - V LO -0.160.23-0.3V Peak Pull-Up Current I OHL V LO = 0V -3---A Peak Pull-Down Current I OLLV LO = 12V-4---AHO GATE DRIVER Low Level Output Voltage V OLH I HO = 100mA-0.10.18-0.25V High Level Output Voltage V OHH I HO = -100mA, V OHH = V HB - V HO -0.160.23-0.3V Peak Pull-Up Current I OHH V HO = 0V -3---A Peak Pull-Down CurrentI OLHV HO = 12V-4---AElectrical SpecificationsV DD = V HB = 12V, V SS = V HS = 0V, no load on LO or HO, unless otherwise specified. (Continued)PARAMETERSSYMBOL TEST CONDITIONST J = +25°CT J = -40°C to +125°CUNIT MIN (Note 10)TYP MAX (Note 10)MIN (Note 10)MAX (Note 10)Switching SpecificationsV DD = V HB = 12V, V SS = V HS = 0V, No Load on LO or HO, unless otherwise specified.PARAMETERSSYMBOL TESTCONDITIONS T J = +25°CT J = -40°C to +125°C UNIT MIN (Note 10)TYP MAX (Note 10)MIN (Note 10)MAX (Note 10)Lower Turn-Off Propagation Delay (LI Falling to LO Falling)t LPHL -3250-60ns Upper Turn-Off Propagation Delay (HI Falling to HO Falling)t HPHL -3250-60ns Lower Turn-On Propagation Delay (LI Rising to LO Rising)t LPLH -3950-60ns Upper Turn-On Propagation Delay (HI Rising to HO Rising)t HPLH -3850-60ns Delay Matching: Upper Turn-Off to Lower Turn-On t MON 18--16ns Delay Matching: Lower Turn-Off to Upper Turn-On t MOFF 16--16ns Either Output Rise Time (10% to 90%)t RC C L = 1nF -9---ns Either Output Fall Time (90% to 10%)t FC C L = 1nF -7.5---ns Either Output Rise Time (3V to 9V)t R C L = 0.1µF -0.30.4-0.5µs Either Output Fall Time (9V to 3V)t F C L = 0.1µF-0.190.3-0.4µs Minimum Input Pulse Width that Changes the Output t PW ----50ns Bootstrap Diode Turn-On or Turn-Off Timet BS-10---nsNOTE:10.Parameters with MIN and/or MAX limits are 100% tested at +25°C, unless otherwise specified. Temperature limits established by characterizationand are not production tested.Timing DiagramsFIGURE 5.PROPAGATION DELAYSFIGURE 6.DELAY MATCHINGt HPLH ,t LPLHt HPHL ,t LPHLHI , LIHO , LOt MONt MOFFLIHILOHOTypical Performance CurvesFIGURE 7.ISL2110 I DD OPERATING CURRENT vs FREQUENCY FIGURE 8.ISL2111 I DD OPERATING CURRENT vs FREQUENCYFIGURE 9.I HB OPERATING CURRENT vs FREQUENCYFIGURE 10.I HBS OPERATING CURRENT vs FREQUENCYFIGURE 11.HIGH LEVEL OUTPUT VOLTAGE vs TEMPERATURE FIGURE 12.LOW LEVEL OUTPUT VOLTAGE vs TEMPERATURE0.11.010.0FREQUENCY (Hz)I D D O (m A )T = +25°CT = -40°CT = +125°CT = +150°C10k100k1.103k10k100k1.103k0.11.010.0FREQUENCY (Hz)I D D O (m A )T = +25°CT = -40°CT = +150°CT = +125°CFREQUENCY (Hz)I H B O (m A )0.011.010.0T = +25°CT = -40°CT = +125°CT = +150°C10k100k1.103k0.1FREQUENCY (Hz)I H B S O (m A )0.011.010.0T = -40°CT = +125°CT = +150°C10k100k1.103k0.1T = +25°C-505010015050100150200250300TEMPERATURE (°C)V O H L , V O H H (m V )V DD = V HB = 12VV DD = V HB = 14VV DD = V HB = 8V-505010015050100150200V O L L , V O L H (m V )TEMPERATURE (°C)V DD = V HB = 12VV DD = V HB = 14VV DD = V HB = 8VFIGURE 13.UNDERVOLTAGE LOCKOUT THRESHOLD vsTEMPERATUREFIGURE 14.UNDERVOLTAGE LOCKOUT HYSTERESIS vsTEMPERATUREFIGURE 15.ISL2110 PROPAGATION DELAYS vs TEMPERATURE FIGURE 16.ISL2111 PROPAGATION DELAYS vs TEMPERATUREFIGURE 17.ISL2110 DELAY MATCHING vs TEMPERATURE FIGURE 18.ISL2111 DELAY MATCHING vs TEMPERATURETypical Performance Curves (Continued)V D D R , V H B R (V )-50501001506.7TEMPERATURE (°C)V HBRV DDR6.56.36.15.95.75.55.3V D D H , V H B H (V )-50501001500.70TEMPERATURE (°C)V HBHV DDH0.650.600.550.500.450.4025303540455055t L P L H , t L P H L , t H P L H , t H P H L (n s )-5050100150TEMPERATURE (°C)t LPHLt HPHLt LPLHt HPLH25303540455055t L P L H , t L P H L , t H P L H , t H P H L (n s )-5050100150TEMPERATURE (°C)t LPHLt HPHLt LPLHt HPLH4.04.55.05.56.06.57.07.58.0t M O N , t M O F F (n s )-5050100150TEMPERATURE (°C)t MOFFt MON4.04.55.05.56.06.57.07.58.08.59.09.510.0t M O N , t M O F F (n s )-50050100150TEMPERATURE (°C)t MOFFt MONFIGURE 19.PEAK PULL-UP CURRENT vs OUTPUT VOLTAGE FIGURE 20.PEAK PULL-DOWN CURRENT vs OUTPUT VOLTAGEFIGURE 21.ISL2110 QUIESCENT CURRENT vs VOLTAGE FIGURE 22.ISL2111 QUIESCENT CURRENT vs VOLTAGEFIGURE 23.BOOTSTRAP DIODE I-V CHARACTERISTICSFIGURE 24.V HS VOLTAGE vs V DD VOLTAGETypical Performance Curves (Continued)48101200.51.01.52.02.53.03.5V LO , V HO (V)I O H L , I O H H (A )2648101201.52.02.53.03.54.04.5V LO , V HO (V)I O H L , I O H H (A )261.00.505101520102030405060708090100110120V DD , V HB (V)I D D , I H B (µA )I HBI DD05101520V DD , V HB (V)I D D , I H B (µA )20406080100120140160180200220240260280300320I HBI DD0.30.40.50.60.70.81.10-30.010.101.00FORWARD VOLTAGE (V)F O R W A R D C U R R E N T (A )1.10-41.10-51.10-61213141516020406080100120V H S T O V S S V O L T A G E (V )V DD TO V SS VOLTA GE (V)Revision History The revision history provided is for informational purposes only and is believed to be accurate, but not warranted. Please visit our website to make sure you have the latest revision.DATE REVISION CHANGEApril 18, 2022FN6295.8Updated the Ordering information table to comply with the new standard, updated notes.In Absolute Maximum Ratings, added Voltage on HO relative to HS and Voltage on LO relative to GND.Updated POD M8.15 to the latest version: “Added the coplanarity spec into the drawing.”Removed Related Literature and About Intersil sections.Mar 16, 2017FN6295.7Corrected the branding of FG ISL2111BR4Z in the order information table from "211 1BR4A" to "2111BR4Z".Added Revision History table and About Intersil information.Updated L10.4x4 Package Outline Drawing from Rev 1 to Rev 2. Change since Rev 1 is:“Tiebar note update from ‘Tiebar shown (if present) is a non-functional feature’ to ‘Tiebar shown (ifpresent) is a non-functional feature and may be located on any of the 4 sides (or ends)’”.Updated L12.4x4A Package Outline Drawing from Rev 1 to Rev 3. Changes since Rev 1 are:“Tiebar note update from ‘Tiebar shown (if present) is a non-functional feature’ to ‘Tiebar shown (ifpresent) is a non-functional feature and may be located on any of the 4 sides (or ends)’”;“Bottom View changed from ‘3.2 REF’ TO ‘2.5 REF’";“Typical Recommended Land Pattern changed from ‘3.80’ to ‘3.75’";“Updated to new POD format by removing table listing dimensions and moving dimensions onto drawing”,and “Added typical recommended land pattern”.Updated M8.15 Package Outline Drawing from Rev 3 to Rev 4. Change since Rev 3 is:“Changed Note 1 from 1982 to 1994“.Updated L8.4x4 Package Outline Drawing from Rev 0 to Rev 1. Change since Rev 0 is:“Tiebar note update from ‘Tiebar shown (if present) is a non-functional feature’ to ‘Tiebar shown (ifpresent) is a non-functional feature and may be located on any of the 4 sides (or ends)’”.10 LEAD THIN DUAL FLAT NO-LEAD PLASTIC PACKAGE Rev 2, 4/15TYPICAL RECOMMENDED LAND PATTERNDETAIL "X"SIDE VIEWTOP VIEWBOTTOM VIEWlocated within the zone indicated. The pin #1 identifier may be Unless otherwise specified, tolerance : Decimal ± 0.05The configuration of the pin #1 identifier is optional, but must be between 0.15mm and 0.30mm from the terminal tip.Dimension b applies to the metallized terminal and is measured Dimensions in ( ) for Reference Only.Dimensioning and tolerancing conform to AMSE Y14.5m-1994.6.either a mold or mark feature.3.5.4.2.Dimensions are in millimeters.1.NOTES:4.00 2.600.15(3.80)(4X)(10X 0.30)(8X 0.8)0 .75BASE PLANE CSEATING PLANE0.08C0.10C10 X 0.30SEE DETAIL "X"0.104C A M B INDEX AREA6PIN 14.00ABPIN #1 INDEX AREABSC3.2REF8X 0.806(10 X 0.60)0 . 00 MIN.0 . 05 MAX.C0 . 2 REF10X 0 . 403.00(2.60)( 3.00 )0.05M C 65101Tiebar shown (if present) is a non-functional feature and may be located on any of the 4 sides (or ends).12 LEAD DUAL FLAT NO-LEAD PLASTIC PACKAGE Rev 3, 3/15TYPICAL RECOMMENDED LAND PATTERNDETAIL "X"SIDE VIEWTOP VIEWBOTTOM VIEWlocated within the zone indicated. The pin #1 identifier may be Unless otherwise specified, tolerance : Decimal ± 0.05The configuration of the pin #1 identifier is optional, but must be between 0.15mm and 0.30mm from the terminal tip.Lead width applies to the metallized terminal and is measured Dimensions in ( ) for Reference Only.Dimensioning and tolerancing conform to AMSE Y14.5m-1994.6.either a mold or mark feature.3.5.4.2.Dimensions are in millimeters.1.NOTES:4.00 1.580.15( 3.75)(4X)( 12X 0 . 25)( 10X 0 . 5 )1.00 MAXBASE PLANE CSEATING PLANE0.08C0.10C12 X 0.25SEE DETAIL "X"0.104C A M B INDEX AREA6PIN 14.00ABPIN #1 INDEX AREA2.5REF10X 0.50 BSC6( 12 X 0.65 )0 . 00 MIN.0 . 05 MAX.C0 . 2 REF12X 0 . 452.80( 1.58)( 2.80 )0.05M C 76121Tiebar shown (if present) is a non-functional feature and may be located on any of the 4 sides (or ends).8 LEAD NARROW BODY SMALL OUTLINE PLASTIC PACKAGE8 LEAD DUAL FLAT NO-LEAD PLASTIC PACKAGE Rev 1, 03/15TYPICAL RECOMMENDED LAND PATTERNDETAIL "X"SIDE VIEWTOP VIEWBOTTOM VIEWlocated within the zone indicated. The pin #1 identifier may be Unless otherwise specified, tolerance : Decimal ± 0.05The configuration of the pin #1 identifier is optional, but must be between 0.15mm and 0.30mm from the terminal tip.Dimension applies to the metallized terminal and is measured Dimensions in ( ) for Reference Only.Dimensioning and tolerancing conform to ASME Y14.5m-1994.6.either a mold or mark feature.3.5.4.2.Dimensions are in millimeters.1.NOTES:4.00 2.50 ± 0.100.15( 3.80)(4X)( 8X 0 . 30 )( 6X 0 . 8 )0 .9 ± 0.10BASE PLANE CSEATING PLANE0.08C0.10C8 X 0.30SEE DETAIL "X"0.104C A M B INDEX AREA6PIN 14.00ABPIN #1 INDEX AREABSC2.4REF6X 0.806( 8 X 0.60 )8X 0 . 40 ± 0.103.45 ± 0.10( 2.50)( 3.45 )0.05M C 54810 . 00 MIN.0 . 05 MAX.C0 . 2 REFTiebar shown (if present) is a non-functional feature and may be located on any of the 4 sides (or ends).Corporate HeadquartersTOYOSU FORESIA, 3-2-24 Toyosu,Koto-ku, Tokyo 135-0061, Japan Contact InformationFor further information on a product, technology, the most up-to-date version of a document, or your nearest sales office, please visit:/contact/TrademarksRenesas and the Renesas logo are trademarks of Renesas Electronics Corporation. All trademarks and registered trademarks are the property of their respective owners.IMPORTANT NOTICE AND DISCLAIMERRENESAS ELECTRONICS CORPORATION AND ITS SUBSIDIARIES (“RENESAS”) PROVIDES TECHNICAL SPECIFICATIONS AND RELIABILITY DATA (INCLUDING DATASHEETS), DESIGN RESOURCES (INCLUDINGREFERENCE DESIGNS), APPLICATION OR OTHER DESIGN ADVICE, WEB TOOLS, SAFETY INFORMATION, AND OTHER RESOURCES “AS IS” AND WITH ALL FAULTS, AND DISCLAIMS ALL WARRANTIES, EXPRESS OR IMPLIED, INCLUDING, WITHOUT LIMITATION, ANY IMPLIED WARRANTIES OF MERCHANTABILITY, FITNESS FOR A PARTICULAR PURPOSE, OR NON-INFRINGEMENT OF THIRD PARTY INTELLECTUAL PROPERTY RIGHTS.These resources are intended for developers skilled in the art designing with Renesas products. You are solely responsible for (1) selecting the appropriate products for your application, (2) designing, validating, and testing your application, and (3) ensuring your application meets applicable standards, and any other safety, security, or other requirements. These resources are subject to change without notice. Renesas grants you permission to use these resources only for development of an application that uses Renesas products. Other reproduction or use of these resources is strictly prohibited. No license is granted to any other Renesas intellectual property or to any third party intellectual property. Renesas disclaims responsibility for, and you will fully indemnify Renesas and its representatives against, any claims,damages, costs, losses, or liabilities arising out of your use of these resources. Renesas' products are provided only subject to Renesas' Terms and Conditions of Sale or other applicable terms agreed to in writing. No use of any Renesas resources expands or otherwise alters any applicable warranties or warranty disclaimers for these products.(Rev.1.0 Mar 2020)。
ISL6161芯片手册

®ISL6161Dual Power Distribution ControllerThe ISL6161 is a HOT SWAP dual supply power distribution controller that can be used in PCI-Express applications. T wo external N-Channel MOSFETs are driven to distribute and control power while providing load fault isolation. At turn-on, the gate of each external N-Channel MOSFET is charged with a 10µA current source. Capacitors on each gate (see the T ypical Application Diagram), create aprogrammable ramp (soft turn-on) to control inrush currents. A built in charge pump supplies the gate drive for the 12V supply N-Channel MOSFET switch.Over current protection is facilitated by two external current sense resistors and FETs. When the current through either resistor exceeds the user programmed value the controller enters the current regulation mode. The time-out capacitor, C TIM , starts charging as the controller enters the time out period. Once C TIM charges to a 2V threshold, both theN-Channel MOSFETs are latched off. In the event of a hard and fast fault of at least three times the programmed current limit level, the N-Channel MOSFET gates are pulled low immediately before entering the time out period. The controller is reset by a rising edge on the ENABLE pin.The ISL6161 constantly monitors both output voltages and reports either one being low on the PGOOD output as a low. The 12V PGOOD Vth is ~10.8V and the 3.3V Vth is ~2.8V nominally.Features•HOT SWAP Dual Power Distribution and Control for +12V and +3.3V •Provides Fault Isolation•Programmable Current Regulation Level •Programmable Time Out•Charge Pump Allows the Use of N-Channel MOSFETs •Power Good and Over Current Latch Indicators •Adjustable Turn-On Ramp •Protection During Turn-On•Two Levels of Current Limit Detection Provide Fast Response to Varying Fault Conditions •1µs Response Time to Dead Short•3µs Response Time to 200% Current Overshoot •Pb-free availableApplications•PCI-Express Applications •Power Distribution and Control •Hot Plug, Hot Swap ComponentsPART NUMBER TEMP. RANGE(o C)PACKAGE PKG. DWG. #ISL6161CB -0 to 70 14 Ld SOIC M14.15ISL6161CBZA (See Note)-0 to 7014 Ld SOIC (Pb-free)M14.15*Add “-T” suffix to part number for tape and reel packaging.NOTE:Intersil Pb-free products employ special Pb-free material sets; molding compounds/die attach materials and 100% matte tin plate termination finish, which is compatible with both SnPb and Pb-free soldering operations. Intersil Pb-free products are MSL classified at Pb-free peak reflow temperatures that meet or exceed the Pb-free requirements of IPC/JEDEC J Std-020B.PinoutISL6161 (SOIC)TOP VIEWTypical Application Diagram891011121413765432112VS 12VG V DD ENABLE3VG 3VS12VISEN GND C PUMP C TIM R ILIM PGOOD 3VISENNC 12VS 12VG ENABLEPGOOD 3VG 3VS12VISEN GND C TIM R ILIMC PUMP3ISEN V DDISL616112VR LOADR ILIMC TIMENABLE INPUTC PUMP R SENSE3.3VR LOADR SENSE3.3VOPTIONAL R FILTERC FILTERV DD C GATEC GATEPin DescriptionsAbsolute Maximum Ratings T A=25o C Thermal InformationV DD . . . . . . . . . . . . . . . . . . . . . . . . . . . . . . . . . . . . . . .-0.3V to +16V 12VG, C PUMP . . . . . . . . . . . . . . . . . . . . . . . . . . . . . . . .-0.3V to 21V 12VISEN, 12VS. . . . . . . . . . . . . . . . . . . . . . . . . . -5V to V DD + 0.3V 3VISEN, 3VS. . . . . . . . . . . . . . . . . . . . . . . . . . . . . . . . . .-5V to 7.5V PGOOD, R ILIM. . . . . . . . . . . . . . . . . . . . . . . . . . . . . . . -0.3V to 7.5V ENABLE, C TIM, 3VG. . . . . . . . . . . . . . . . . . . . .-0.3V to V DD + 0.3V ESD Classification. . . . . . . . . . . . . . . . . . . . . . . . . . . .2kV (Class 2) Operating ConditionsV DD Supply Voltage Range. . . . . . . . . . . . . . . . . .+10.5V to +13.2V T emperature Range (T A) . . . . . . . . . . . . . . . . . . . . . . . .0o C to 70o C Thermal Resistance (T ypical, Note 1)θJA (o C/W) SOIC Package . . . . . . . . . . . . . . . . . . . . . . . . . . . . . 67 Maximum Junction T emperature (Plastic Package) . . . . . . . .150o C Maximum Storage T emperature Range. . . . . . . . . . -65o C to 150o C Maximum Lead T emperature (Soldering 10s) . . . . . . . . . . . . .300o C (SOIC - Lead Tips Only)CAUTION: Stresses above those listed in “Absolute Maximum Ratings” may cause permanent damage to the device. This is a stress only rating and operation of the device at these or any other conditions above those indicated in the operational sections of this specification is not implied.NOTES:1.θJA is measured with the component mounted on a high effective thermal conductivity test board in free air. See Tech Brief TB379 for details.2.All voltages are relative to GND, unless otherwise specified.Electrical Specifications V DD = 12V, C VG = 0.01µF, C TIM = 0.1µF, R SENSE = 0.1Ω, C BULK = 220µF, ESR = 0.5Ω, T A = T J = 0o C to 70o C, Unless Otherwise SpecifiedISL6161 Description and OperationThe ISL6161 is a multi featured +12V and +3.3V dual powersupply distribution controller, features include programmable current regulation (CR) limiting and time to latch off.At turn-on, the gate capacitor of each external N-Channel MOSFET is charged with a 10µA current source. These capacitors create a programmable ramp (soft turn-on). Acharge pump supplies the gate drive for the 12V supply control FET switch driving that gate to 17V .The load currents pass through two external current sense resistors. When the voltage across either resistor quickly exceeds the user programmed Current Regulation voltage threshold (CRVth) level, the controller enters current regulation. The CRVth is set by the external resistor value on R ILIM pin. At this time the time-out capacitor, C TIM , starts charging with a 10µA current source and the controller enters the time out period. The length of the time out period is set by the single external capacitor (see T able 2) placed from the C TIM pin (pin 10) to ground and is characterized by a lowered gate drivevoltage to the appropriate external N-Channel MOSFET . Once C TIM charges to 2V , an internal comparator is tripped resulting in both N-Channel MOSFETs being latched off. If the voltage across the sense resistors rises slowly in response to an OC condition, then the CR mode is entered at ~95% of theprogrammed CR level. This difference is due to the necessary hysteresis and response time in the CR control circuitry . T able 1 shows Rsense and Rilim recommendations and resulting CR level for the PCI-Express add-in card connector sizes specified.Electrical SpecificationsV DD = 12V , C VG = 0.01µF , C TIM = 0.1µF , R SENSE = 0.1Ω, C BULK = 220µF , ESR = 0.5Ω, T A = T J = 0o C to 70o C, Unless Otherwise Specified (Continued)TABLE 1.The ISL6161 responds to a load short (defined as a current level 3X the OC set point with a fast transition) byimmediately driving the relevant N-Channel MOSFET gate to 0V in ~3µs. The gate voltage is then slowly ramped up soft starting the N-Channel MOSFET to the programmed current regulation limit level, this is the start of the time out period if the abnormal load condition still exists. The programmed current regulation level is held until either the OC event passes or the time out period expires. If the former is the case then the N-Channel MOSFET is fully enhanced and the C TIM charging current is diverted away from the capacitor. If the time out period expires prior to OC resolution then both gates are quickly pulled to 0V turning off both N-Channel MOSFETs simultaneously.Upon any UV condition the PGOOD signal will pull low when tied high through a resistor to the logic supply. This pin is a fault indicator but not the OC latch off indicator. For an OC latch off indication, monitor CTIM, pin 10. This pin will rise rapidly to 12V once the time out period expires. See block diagram for OC latch off circuit suggestion.The ISL6161 is reset by a rising edge on the ENABLE pin and is turned on by the ENABLE pin being driven low.ISL6161 Application ConsiderationsIn a non PCI-Express, motor drive application Current loop stabilization is facilitated through a small value resistor in series with the gate timing capacitor. As the ISL6161 drives a highly inductive current load, instability characterized by the gate voltage repeatedly ramping up and down mayappear. A simple method to enhance stability is provided by the substitution of a larger value gate resistor. T ypically this situation can be avoided by eliminating long point to point wiring to the load.With the ENABLE internal pull-up the ISL6161 is well suitedfor implementation on either side of the connector where a motherboard prebiased condition or a load board staggered connection is present. In either case the ISL6161 turns on in a soft start mode protecting the supply rail from sudden current loading.During the Time Out delay period with the ISL6161 in current limit mode, the V GS of the external N-Channel MOSFETs is reduced driving the N-Channel MOSFET switch into a high r DS(ON) state. Thus avoid extended time out periods as the external N-Channel MOSFETs may be damaged or destroyed due to excessive internal powerdissipation. Refer to the MOSFET manufacturers data sheet for SOA information.With the high levels of inrush current e.g., highly capacitive loads and motor start up currents, choosing the current regulation (CR) level is crucial to provide both protection and still allow for this inrush current without latching off.Consider this in addition to the time out delay when choosing MOSFETs for your design.Physical layout of Rsense resistors is critical to avoid inadvertently lowering the CR and trip levels. Ideally trace routing between the Rsense resistors and the ISL6161 is direct and as short as possible with zero current in the sense lines.Open load detection can be accomplished by monitoring the ISEN pins. Although gated off the external FET I DSS will cause the ISEN pin to float above ground to some voltage when there is no attached load. If this is not desired 5K resistors from the xISEN pins to ground will prevent the outputs from floating when the external switch FETs are disabled and the outputs are open.For PCI-Express applications the ISL6161 and theISL6118 provide the fundamental hotswap function for the +12V & +3.3V main rails and the +3.3V aux respectively as shown in Figure 13.NOTE:Nominal CR Vth = Rilim x 10µA.TABLE 2.NOTE:Nominal time-out period in seconds = C TIM x 200k Ω.TABLE 1. (Continued)FIGURE 1.SENSE RESISTOR PCB LAYOUTTypical Performance CurvesFIGURE 2.SUPPLY CURRENTFIGURE 3.R ILIM SOURCE CURRENTFIGURE 4.C TIM CURRENT SOURCE FIGURE 5.C TIM OC VOLTAGE THRESHOLDFIGURE 6.12V UV THRESHOLD FIGURE 7.3.3V UV THRESHOLD8.28.07.87.67.47.2-40-20020406080TEMPERATURE (o C)8.4S U P P L Y C U R R E N T (m A )-30-1010305070104103-40-2002040608010270503010-10-30105TEMPERATURE (o C)C U R R E N T (µA )-40-20204060-30-10103050708010.710.610.510.410.3C T I M C U R R E N T S O U R C E (µA )TEMPERATURE (o C)-40-200204060-30-1010305070802.042.022.001.981.961.94C T I M O C V O L T A G E T H R E S H O LD (V )TEMPERATURE (o C)TEMPERATURE (o C)12V U V T H R E S H O L D (V )20406080-40-20010.9210.90210.88610.8720406080-40-2002.8752.87252.8702.86752.865TEMPERATURE (o C)3.3V U V T H R E S H O L D (V )FIGURE 8.12V, 3V GATE DRIVE FIGURE 9.PUMP VOLTAGEFIGURE 10.OC VOLTAGE THRESHOLD WITH R LIM = 5k ΩFIGURE 11.OC VOLTAGE THRESHOLD WITH R LIM = 10k ΩFIGURE 12.POWER ON RESET VOLTAGE THRESHOLDTypical Performance Curves (Continued)12V VG3.3VG20406080-400-2017.3617.3417.3217.3017.2817.2611.93511.93011.92511.92011.91511.91011.90511.900TEMPERATURE (o C)3.3V G A T E D R I V E (V )12V G A T E D R I V E (V )20406080-400-20V O L T A G E (V )TEMPERATURE (o C)17.617.417.216.816.617.0CHARGE PUMP VOLTAGE NO LOADCHARGE PUMP VOLTAGE 100µA LOAD20406080-400-20TEMPERATURE (o C)V O L T A G E T H R E S H O L D (m V )54.554.053.553.052.512 OC Vth3.3 OC Vth20406080-400-20V O L T A G E T H R E S H O L D (m V )12 OC VTth3.3 OC VthTEMPERATURE (o C)102.5102.0101.5101.0100.5-40-20020406080-30-101030507010.210.09.89.6P O W E R O N R E S E T (V )TEMPERATURE (o C)V DD LOW TO HIGHV DD HIGH TO LOWAll Intersil U.S. products are manufactured, assembled and tested utilizing ISO9000 quality systems.Intersil Corporation’s quality certifications can be viewed at /design/qualityIntersil products are sold by description only. Intersil Corporation reserves the right to make changes in circuit design, software and/or specifications at any time without notice. Accordingly, the reader is cautioned to verify that data sheets are current before placing orders. Information furnished by Intersil is believed to be accurate and reliable. However, no responsibility is assumed by Intersil or its subsidiaries for its use; nor for any infringements of patents or other rights of third parties which may result from its use. No license is granted by implication or otherwise under any patent or patent rights of Intersil or its subsidiaries.For information regarding Intersil Corporation and its products, see ISL6161Small Outline Plastic Packages (SOIC)NOTES:1.Symbols are defined in the “MO Series Symbol List” in Section2.2 ofPublication Number 95.2.Dimensioning and tolerancing per ANSI Y14.5M -1982.3.Dimension “D” does not include mold flash, protrusions or gate burrs. Mold flash, protrusion and gate burrs shall not exceed 0.15mm (0.006inch) per side.4.Dimension “E” does not include interlead flash or protrusions. Interlead flash and protrusions shall not exceed 0.25mm (0.010 inch) per side.5.The chamfer on the body is optional. If it is not present, a visual index feature must be located within the crosshatched area.6.“L” is the length of terminal for soldering to a substrate.7.“N” is the number of terminal positions.8.Terminal numbers are shown for reference only.9.The lead width “B”, as measured 0.36mm (0.014 inch) or greater above the seating plane, shall not exceed a maximum value of 0.61mm (0.024 inch).10.Controlling dimension:MILLIMETER. Converted inch dimensionsare not necessarily exact.M14.15 (JEDEC MS-012-AB ISSUE C)14 LEAD NARROW BODY SMALL OUTLINE PLASTIC PACKAGESYMBOLINCHESMILLIMETERS NOTESMIN MAX MIN MAX A0.05320.0688 1.35 1.75-A10.00400.00980.100.25-B 0.0130.0200.330.519C 0.00750.00980.190.25-D 0.33670.34448.558.753E 0.14970.1574 3.80 4.004e0.050 BSC 1.27 BSC-H 0.22840.2440 5.80 6.20-h 0.00990.01960.250.505L 0.0160.0500.401.276N14147α0o8o0o8o-Rev. 0 12/93。
ISL6225.pdf

®ISL6225Dual Mobile-Friendly PWM Controller with DDR Memory OptionThe ISL6225 dual PWM controller delivers high efficiency and tight regulation from two voltage regulating synchronous buck DC/DC converters. The ISL6225 PWM power supply controller was designed especially for DDR DRAM, SDRAM, and graphic chipset applications in high performance desknote PCs, notebook PCs, sub-notebook PCs, and PDAs.Automatic mode selection of constant-frequency synchronous rectification at heavy load, and hysteretic diode-emulation at light load, assure high efficiency over a wide range of conditions. The hysteretic mode of operation can be disabled separately on each PWM converter if constant-frequency continuous-conduction operation is desired for all load levels. Efficiency is further enhanced by using the lower MOSFETr DS(ON) as the current sense element.Voltage-feed-forward ramp modulation, average current mode control, and internal feedback compensation provide fast response to input voltage and output load transients. Input current ripple is minimized by channel to channel PWM phase shift of 0°, 90°, or 180° determined by input voltage and status of the DDR pin.The ISL6225 can control two independent output voltages adjustable from 0.9V to 5.5V or, by activating the DDR pin, transform into a complete DDR memory power supply solution. In DDR mode, CH2 output voltage VTT tracks CH1 output voltage VDDQ. CH2 output can both source and sink current, an essential power supply feature for DDR memory systems. The reference voltage VREF required by DDR memory is generated as well.In dual power supply applications the ISL6225 monitors the output voltage of both CH1 and CH2. An independent PGOOD (power good) signal is asserted for each channel after the soft-start sequence has completed, and the output voltage is within ±10% of the set point. In DDR mode CH1 generates the only PGOOD signal.Built-in overvoltage protection prevents the output from going above 115% of the set point by holding the lower MOSFET on and the upper MOSFET off. When the output voltage decays below the overvoltage threshold, normal operation automatically resumes. Once the soft-start sequence has completed, under-voltage protection may latch the ISL6225 off if either output drops below 75% of its set point value.Adjustable overcurrent protection (OCP) monitors the voltage drop across the r DS(ON) of the lower MOSFET. If more precise current-sensing is required, an external current sense resistor may be used.Features•Provides regulated output voltage in the range of 0.9V-5.5V -High efficiency over wide load range-Synchronous buck converter with hysteretic operation atlight load-Inhibit Hysteretic mode on one, or both channels •Complete DDR memory power solution-VTT tracks VDDQ/2-VDDQ/2 buffered reference output•No current-sense resistor required-Uses MOSFET r DS(ON)-Optional current-sense resistor for precision overcurrent •Under-voltage lock-out on V CC pin•Dual input voltage mode operation-Operates directly from battery 5V to 24V input-Operates from 3.3V or 5V system rail-VCC from 5V only•Excellent dynamic response-Combined voltage feed-forward and average currentmode control•Power-good signal for each channel•300kHz switching frequency-180° channel to channel phase operation for reduced input ripple when not in DDR mode-0° channel to channel phase operation in DDR mode forreduced channel interference-90° channel to channel phase operation for reduced input ripple in DDR mode when VIN is at GND.•Pb-Free Available (RoHS Compliant)Applications•Mobile PCs•PDAs•Hand-held portable instrumentsOrdering InformationPART NUMBER TEMP. (°C)PACKAGEPKG.DWG. # ISL6225CA-10 to 8528 Ld SSOP M28.15 ISL6225CAZ (Note1)-10 to 8528 Ld SSOP (Pb-free)M28.15 ISL6225CAZA (Note1)-10 to 8528 Ld SSOP (Pb-free)M28.15 NOTES:1.Intersil Pb-free products employ special Pb-free material sets; moldingcompounds/die attach materials and 100% matte tin plate termination finish, which are RoHS compliant and compatible with both SnPb and Pb-free soldering operations. Intersil Pb-free products are MSLclassified at Pb-free peak reflow temperatures that meet or exceed the Pb-free requirements of IPC/JEDEC J STD-020.2.Add “-T” for Tape and Reel.N O T R E C O M M EN D E D FO R N E WD E S I G NSR E C O M M E N D E DR E P L A CE M E N T:I S L6227O R I S L6539PinoutISL6225SSOP-28TOP VIEWGND LGATE1PGND1PHASE1UGATE1BOOT1ISEN1EN1VOUT1VSEN1OCSET1SOFT1DDR VIN VCC PGND2PHASE2UGATE2BOOT2EN2VSEN2OCSET2SOFT2PG2/REF PG1LGATE2ISEN2VOUT228272625242322212019181716151234567891011121314Absolute Maximum Ratings Thermal InformationBias Voltage, V CC . . . . . . . . . . . . . . . . . . . . . . . . . . . . . . . . . .+ 6.5V Input Voltage, V IN. . . . . . . . . . . . . . . . . . . . . . . . . . . . . . . . . . +27.0V PHASE, UGATE Voltage . . . . . . . . . . . . . . GND-5V (Note 3) to 33V BOOT, ISEN Voltage . . . . . . . . . . . . . . . . . . . . GND-0.3V to +33.0V BOOT with respect to PHASE. . . . . . . . . . . . . . . . . . . . . . . . .+ 6.5V All Other Pins. . . . . . . . . . . . . . . . . . . . . . GND -0.3V to V CC + 0.3V ESD Classification. . . . . . . . . . . . . . . . . . . . . . . . . . . . . . . . .Class 2 Recommended Operating ConditionsBias Voltage, V CC . . . . . . . . . . . . . . . . . . . . . . . . . . . . . .+5.0V ±5% Input Voltage, V IN . . . . . . . . . . . . . . . . . . . . . . . . . . .+5.0V to +24.0V Ambient Temperature Range. . . . . . . . . . . . . . . . . . . .-10°C to 85°C Junction Temperature Range. . . . . . . . . . . . . . . . . . .-10°C to 125°C Thermal Resistance (Typical, Note 4)θJA (°C/W) SSOP Package. . . . . . . . . . . . . . . . . . . . . . . . . . . . 78 Maximum Junction Temperature (Plastic Package) . . . . . . . .150°C Maximum Storage Temperature Range. . . . . . . . . . .-65°C to 150°C Maximum Lead Temperature (Soldering 10s) . . . . . . . . . . . . .300°C (SSOP - Lead Tips Only)CAUTION: Stresses above those listed in “Absolute Maximum Ratings” may cause permanent damage to the device. This is a stress only rating and operation of the device at these or any other conditions above those indicated in the operational sections of this specification is not implied.NOTES:3.200ns transient.4.θJA is measured with the component mounted on a high effective thermal conductivity test board in free air. See Tech Brief TB379 for details. Electrical Specifications Recommended Operating Conditions, Unless Otherwise Noted.PARAMETER SYMBOL TEST CONDITIONS MIN TYP MAX UNITS V CC SUPPLYBias Current I CC LGATEx, UGATEx Open, VSENx forced aboveregulation point, DDR = 0, VIN > 5V- 2.2 3.2mA Shut-down Current I CCSN--30µAV CC UVLORising V CC Threshold V CCU 4.3 4.65 4.75V Falling V CC Threshold V CCD 4.1 4.35 4.45VV INInput Voltage Pin Current (Sink)I VIN10-30µA Input Voltage Pin Current (Source)I VINO--15-30µA Shut-down Current I VINS--1µA OSCILLATORPWM1 Oscillator Frequency F C255300345kHz Ramp Amplitude, pk-pk V R1V IN = 16V, by design-2-V Ramp Amplitude, pk-pk V R2V IN = 5V, by design- 1.25-V Ramp Offset V ROFF By design-0.5-V Ramp/V IN Gain G RB1V IN ≥ 3V, by design-125-mV/V Ramp/V IN Gain G RB21 ≤ V IN ≤ 3V, by design-250-mV/V REFERENCE AND SOFT-STARTInternal Reference Voltage V REF-0.9-V Reference Voltage Accuracy-1.0-+1.0% Soft-Start Current During Start-up I SOFT--5-µA Soft-Start Complete Threshold V ST By design- 1.5-VPWM CONVERTERS Load Regulation0.0mA < I VOUT1 < 5.0A; 5.0V < V BATT < 24.0V -2.0-+2.0%VSEN pin bias current I VSEN By design 5080120nA V OUT pin input impedance I VOUT V OUT = 5V405565k ΩUndervoltage Shut-Down Level V UVL Fraction of the set point; ~2µs noise filter 70-85%Overvoltage Shut-Down V OVP1Fraction of the set point; ~2µs noise filter110-130%GATE DRIVERSUpper Drive Pull-Up Resistance R 2UGPUP V CC = 4.5V -815ΩUpper Drive Pull-Down Resistance R 2UGPDN V CC = 4.5V - 3.25ΩLower Drive Pull-Up Resistance R 2LGPUP V CC = 4.5V -815ΩLower Drive Pull-Down ResistanceR 2LGPDNV CC = 4.5V- 1.83ΩPOWER GOOD AND CONTROL FUNCTIONS Power Good Lower Threshold V PG-Fraction of the set point; ~3µs noise filter -13--7% Power Good Higher Threshold V PG+Fraction of the set point; ~3µs noise filter. Guaranteed by design.12-16% PGOODx Leakage Current I PGLKG V PULLUP = 5.5V --1µA PGOODx Voltage Low V PGOODI PGOOD = -4mA-0.50.85V EN - Low (Off)--0.8V EN - High (On)2.5--V CCM Enforced (Hysteretic Operation Inhibited)VOUTX pulled low--0.1V Automatic CCM/Hysteretic Operation Enabled VOUTX connected to the output0.9--V DDR - Low (Off)--0.8V DDR - High (On) 2.5--V DDR REF Output Voltage V DDREF DDR = 1, I REF = 0...10mA 0.99*V OC2V OC2 1.01*V OC2V DDR REF Output CurrentI DDREFDDR = 1. Guaranteed by design.-1016mAElectrical SpecificationsRecommended Operating Conditions, Unless Otherwise Noted. (Continued)PARAMETERSYMBOLTEST CONDITIONSMINTYPMAXUNITSFunctional Pin DescriptionGND (Pin 1)Signal ground for the IC.LGATE1, LGATE2 (Pin 2, 27)These are outputs of the lower MOSFET drivers.PGND1, PGND2 (Pin 3, 26)These pins provide the return connection for lower gate drivers. These pins are connected to sources of the lower MOSFETs of their respective converters.PHASE1, PHASE2 (Pin 4, 25)The PHASE1 and PHASE2 points are the junction points of the upper MOSFET sources, output filter inductors, and lower MOSFET drains. Connect these pins to the respective converter’s upper MOSFET source.UGATE1, UGATE2 (Pin 5, 24)These pins provide the gate drive for the upper MOSFETs. BOOT1, BOOT2 (Pin 6, 23)These pins power the upper MOSFET drivers of the PWM converter. Connect this pin to the junction of the bootstrap capacitor with the cathode of the bootstrap diode. Anode of the bootstrap diode is connected to the VCC pin.ISEN1, ISEN2 (Pin 7, 22)These pins are used to monitor the voltage drop across the lower MOSFET for current feedback and overcurrent protection. For precise current detection these inputs can be connected to the optional current sense resistors placed in series with the source of the lower MOSFETs.EN1, EN2 (Pin 8, 21)These pins enable operation of the respective converter when high. When both pins are low, the chip is disabled and only low leakage current <1µA is taken from V CC and V IN. These pins are to be connected together and switched at the same time.VOUT1, VOUT2 (Pin 9, 20)These pins when connected to the converters’ respective outputs provide the output voltage inside the chip to reduce output voltage excursion during HYS/PWM transition. When connected to ground, these pins command forced converters operate in continuous conduction mode at all load levels.VSEN1, VSEN2 (Pin 10, 19)These pins are connected to the resistive dividers that set the desired output voltage. The PGOOD, UVP, and OVP circuits use this signal to report output voltage status. OCSET1 (Pin 11)A resistor from this pin to ground sets the overcurrent threshold for the first controller.SOFT1, SOFT2 (Pin 12, 17)These pins provide soft-start function for their respective controllers. When the chip is enabled, the regulated 5µA pull-up current source charges the capacitor connected from the pin to ground. The output voltage of the converter follows the ramping voltage on the SOFT pin.DDR (Pin 13)This pin, when high, transforms dual channel chip into complete DDR memory solution. The OCSET2 pin becomes an input to provide the required tracking function. The channel synchronization is changed from out-of-phase to in-phase. The PG2/REF pin becomes the output of the VDDQ/ 2 buffered voltage that is used as a reference voltage by the second channel.VIN (Pin 14)Provides battery voltage to the oscillator for feed-forward rejection of the input voltage variation.When connected to ground via 100kΩ resistor while the DDR pin is high, this pin commands the out-of-phase 90o channels synchronization for reduced inter-channel interference.PG1 (Pin 15)PGOOD1 is an open drain output used to indicate the status of the output voltage. This pin is pulled low when the first channel output is not within±10% of the set value.PG2/REF (Pin 16)This pin has a double function depending on the mode the chip is operating. When the chip is used as a dual channel PWM controller (DDR = 0), the pin provides a PGOOD2 function for the second channel. The pin is pulled low when the second channel output is not within±10% of the set value.In DDR mode (DDR = 1), this pin serves as an output of the buffer amplifier that provides VDDQ/2 reference voltage applied to the OCSET2 pin.OCSET2 (Pin 18)In a dual channel application (DDR = 0), a resistor from this pin to ground sets the overcurrent threshold for the second controller.In the DDR application (DDR = 1), this pin sets the output voltage of the buffer amplifier and the second controller and should be connected to the center point of a divider from the VDDQ output.VCC (Pin 28)This pin powers the controller.Generic Application Circuits+V IN V OUT1V OUT2+1.80V+1.20V+3.3V TO +24VL1Q1Q2OCSET1DDRFIGURE 1.ISL6225 APPLICATION CIRCUIT FOR TWO CHANNEL POWER SUPPLYPWM1PWM2L2Q3Q4C2OCSET2VCC EN2EN1+5VENABLE +C1+FIGURE 2.ISL6225 APPLICATION CIRCUIT FOR COMPLETE DDR MEMORY POWER SUPPLY+VIN VDDQVTT +2.50V+1.25V+3.3V TO +24VL1Q1Q2OCSET1DDRPWM1PWM2L2Q3Q4OCSET2VCC ENABLE EN2EN1+5VVREF +1.25VPG2/VREFC1+C2+DescriptionOperationThe ISL6225 is a dual channel PWM controller intended for use in power supplies for graphic chipset, SDRAM, DDR DRAM or other low voltage power applications in modern notebook and sub-notebook PCs. The IC integrates two control circuits for two synchronous buck converters. The output voltage of each controller can be set in the range of 0.9V to 5.5V by an external resistive divider. Out-of-phase operation with 180 degree phase shift reduces input current ripple.The synchronous buck converters can operate from either an unregulated DC source such as a notebook battery with a voltage ranging from 5.0V to 24V, or from a regulated system rail of 3.3V or 5V. In either mode of operation the controller is biased from the +5V source.The controllers operate in the current mode with input voltage feed-forward for simplified feedback loop compensation and reduced effect of the input voltage variation. An integrated feedback loop compensation dramatically reduces the number of external components.Depending on the load level, converters can operate either in a fixed-frequency mode or in a hysteretic mode. Switch-over to the hysteretic mode operation at light loads improves the converters' efficiency and prolongs battery run time. The hysteretic mode of operation can be inhibited independently for each channel if a variable frequency operation is not desired.The ISL6225 has a special means to rearrange its internal architecture into a complete DDR solution. When DDR input is set high, the second channel can provide the capability to track the output voltage of the first channel. The buffered reference voltage required by DDR memory chips is also provided.InitializationThe Power-On Reset (POR) function continually monitors the bias supply voltage on the V CC pin and initiates soft-start operation after the input supply voltage exceeds 4.5V. Should this voltage drop lower than 4.0V, the POR disables the chip.Soft-StartWhen soft-start is initiated, the voltage on the SOFT pin starts to ramp gradually due to the 5µA current sourced into the external soft-start capacitor. The output voltage starts to follow the soft-start voltage.When the SOFT pin voltage reaches a level of 0.9V, the output voltage comes into regulation while the soft-start pin voltage continues to rise. When the SOFT voltage reaches 1.5V, the power good (PGOOD), the mode control, and the fault functions are enabled, as depicted in Figure 3.This completes the soft-start sequence. Further rise of pin voltage does not affect the output voltage. During the soft-start, the converter always operates in continuous conduction mode independently of the load level or FCCM pin potential.The soft-start time (the time from the moment when EN becomes high to the moment when PGOOD is reported) is determined by the following equation.The time it takes the output voltage to come into regulation can be obtained from the following equation.Having such a spread between the time when the output voltage reaches the regulation point and the moment when PGOOD is reported allows for a fault-safe test mode by means of an external circuit that clamps the SOFT pin voltage on the level 0.9V < V SOFT < 1.5V.Output Voltage ProgramThe output voltage of either channel is set by a resistive divider from the output to ground. The center point of the divider is connected to VSEN pin as shown in Figure 4. The output voltage value is determined by the following equation. Where 0.9V is the value of the internal reference. The VSEN pin voltage is also used by the controller for the power good function and to detect Undervoltage and Overvoltage conditions.FIGURE 3.START UPCh3 1.0VCh4 5.0VT SOFT 1.5V Csoft×5µA----------------------------------=T RISE0.6T SOFT×=V O0.9V R1R2+()•R2---------------------------------------------=Automatic Operation Mode ControlIn nominal currents the synchronous buck converter operates in continuous-conduction constant-frequency mode. This mode of operation achieves higher efficiency due to the substantially lower voltage drop across the synchronous MOSFET compared to a Schottky diode. In contrast, continuous-conduction operation with loadcurrents lower than the inductor critical value results in lower efficiency. In this case, during a fraction of a switching cycle, the direction of the inductor current changes to the opposite, actively discharging the output filter capacitor.To maintain the output voltage in regulation, the discharged energy should be restored during the consequent cycle of operation by the cost of increased circulating current and losses associated with it.The critical value of the inductor current can be estimated by the following expression:To improve converter efficiency at loads lower than critical, the switch-over to variable frequency hysteretic operation with diode emulation is implemented into the PWM scheme. The switch-over is provided automatically by the mode control circuit that constantly monitors the inductor current and alters the way the PWM signal is generated.The voltage across the synchronous MOSFET at themoment of time just before the upper-MOSFET turns on is monitored for purposes of mode change. When the converter operates at currents higher than critical, thisvoltage is always negative. In currents lower than critical, the voltage is always positive. The mode control circuit uses a sign of voltage across the synchronous devices to determine if the load current is higher or lower than the critical value.To prevent chatter between operating modes, the circuit looks for eight contiguous signals of the same polarity before it makes the decision to perform a mode change. The same algorithm is true for both CCM-hysteretic and hysteretic-CCM transitions.Hysteretic OperationWhen the critical inductor current is detected, the converter enters hysteretic mode. The PWM comparator and the error amplifier that provided control in the CCM mode are inhibited and the hysteretic comparator is now activated. A change is also made to the gate logic. In hysteretic mode the synchronous rectifier MOSFET is controlled in diodeemulation mode, hence conduction in the second quadrant is prohibited.FIGURE 4.OUTPUT VOLTAGE PROGRAMR2R1UGATE LGATE ISL6225L1Q1Q2C1VOUT VSEN VIN R CSISENOCSETR OCCzI HYS V IN V O –()V O•2F SW L O V IN•••-----------------------------------------------------=FIGURE 5.CCM - HYSTERETIC TRANSITIONPWMHYSTERETIC1 2 3 4 5 6 7 8VOUTIINDPHASEOPERATIONMODE OFttttCOMPFIGURE 6.HYSTERETIC - CCM TRANSITIONPWMHYSTERETIC1 23 4 5 6 7 8VOUTIINDPHASECOMPOPERATIONMODE OFttttThe hysteretic comparator initiates the PWM signal when the output voltage gets below the lower threshold and terminates the PWM signal when the output voltage rises above the upper threshold. A spread or hysteresis between these two thresholds determines the switching frequency and the peak value of the inductor current. The transition to constant frequency CCM mode happens when the inductor current increases above the critical value:Where, ∆V hys= 15mV, is a hysteretic comparator window, ESR is the equivalent series resistance of the output capacitor. Because of different control mechanisms, the value of the load current where transition into CCM operation takes place is usually higher compared to the load level at which transition into hysteretic mode had occurred. V OUT pin and Forced Continuous Conduction Mode (FCCM)The controller has the flexibility to operate a converter in fixed-frequency constant conduction mode (CCM), or in hysteretic mode. Connecting the V OUT pin to GND will inhibit hysteretic mode; this is called forced constant conduction mode (FCCM). Connecting the V OUT pin to the converter output will allow transition between CCM mode and hysteretic mode.When the V OUT pin is connected to the converter output, a circuit is activated that smooths the transition from hysteretic mode to CCM mode. While in hysteretic mode, this circuit prepositions the PWM error amplifier output to a level close to that needed to provide the appropriate PWM duty cycle required for regulation. This is a much more desirable state for the PWM error amplifier at mode transition, as opposed to being in saturation which requires a period of time to slew to the required level.Such dual function of the V OUT pin enhances applicability of the controller and allows for lower pin count.Feedback Loop CompensationTo reduce the number of external components and remove the burden of determining compensation components from a system designer, both PWM controllers have internally compensated error amplifiers. To make internal compensation possible several design measures where taken.First, the ramp signal applied to the PWM comparator is proportional to the input voltage provided via the VIN pin. This keeps the modulator gain constant when the input voltage varies. Second, the load current proportional signal is derived from the voltage drop across the lower MOSFET during the PWM time interval and is added to the amplified error signal on the comparator input. This effectively creates an internal current control loop. The resistor connected to the ISEN pin sets the gain in the current feedback loop. The following expression estimates the required value of the current sense resistor depending on the maximum load current and the value of the MOSFET’s r DS(ON).Due to implemented current feedback, the modulator has a single pole response with -1 slope at a frequency determined by the load,where: Ro is load resistance and Co is load capacitance. For this type of modulator, a Type 2 compensation circuit is usually sufficient.Figure 7 shows a Type 2 amplifier and its response along with the responses of the current mode modulator and the converter. The Type 2 amplifier, in addition to the pole at origin, has a zero-pole pair that causes a flat gain region at frequencies between the zero and the pole:This region is also associated with phase ‘bump’ or reduced phase shift. The amount of phase shift reduction depends on how wide the region of flat gain is and has a maximum value of 90o. To further simplify the converter compensation, the modulator gain is kept independent of the input voltage variation by providing feed-forward of V IN to the oscillator ramp.I CCM∆V hys2ESR•---------------------≈R CSI MAX r DS ON()⋅75µA---------------------------------------------100Ω–=F PO12πR O C O⋅⋅---------------------------------=F Z12πR2C1⋅⋅-------------------------------6kHz==F P12πR1C2⋅⋅-------------------------------600kHz==FIGURE 7.FEEDBACK LOOP COMPENSATIONR1R2C1C2F POF Z FPF CMODULATOREATYPE 2 EAG EA = 14dBG M = 18dBCONVERTERThe zero frequency, the amplifier high-frequency gain, and the modulator gain are chosen to satisfy most typical applications. The crossover frequency will appear at the point where the modulator attenuation equals the amplifier high frequency gain. The only task that the system designer has to complete is to specify the output filter capacitors to position the load main pole somewhere within one decade lower than the amplifier zero frequency. With this type of compensation plenty of phase margin is easily achieved due to zero-pole pair phase ‘boost’. Conditional stability may occur only when the main load pole is positioned too much to the left side on the frequency axis due to excessive output filter capacitance. In this case, the ESR zero placed within 10kHz...50kHz range gives some additional phase ‘boost’. Some phase boost can also be achieved by connecting capacitor C z in parallel with the upper resistor R1 of the divider that sets the output voltage value, as shown in Figure4.Gate Control LogicThe gate control logic translates generated PWM signals into gate drive signals providing necessary amplification, level shift, and shoot-trough protection. Also, it bears some functions that help to optimize the IC performance over a wide range of the operational conditions. As MOSFET switching time can very dramatically from type to type and with the input voltage, the gate control logic provides adaptive dead time by monitoring real gate waveforms of both the upper and the lower MOSFETs.Dual-Step ConversionThe ISL6225 dual channel controller can be used either in power systems with a single-stage power conversion when the battery power is converted into the desired output voltage in one step, or in the systems where some intermediate voltages are initially established. The choice of the approach may be dictated by the overall system design criteria or simply to be a matter of voltages available to the system designer, like in the case of PCI card applications. When the power input voltage is a regulated 5V or 3.3V system bus, the feed-forward ramp may become too shallow, which creates the possibility of duty-factor jitter especially in a noisy environment. The noise susceptibility when operating from low level regulated power sources can be improved by connecting the VIN pin to ground. The feed-forward ramp generator will be internally reconnected from the VIN pin to the V CC pin and the ramp slew rate will be doubled. Application circuits for dual-step power conversion are presented in Figures 11 through 15.ProtectionsThe converter output is monitored and protected against extreme overload, short circuit, Overvoltage, and Undervoltage conditions.A sustained overload on the output sets the PGOOD low and latches-off the whole chip. The controller operation can be restored by cycling the VCC voltage or an enable (EN) pin. Overcurrent ProtectionBoth PWM controllers use the lower MOSFET’son-resistance {r DS(ON)} to monitor the current for protection against shorted outputs. The sensed current from the ISEN pin is compared with a current set by a resistor connected from the OCSET pin to ground.Where, I OC is a desired overcurrent protection threshold and R CS is the value of the current sense resistor connected to the I SEN pin.If the lower MOSFET current exceeds the overcurrent threshold, a pulse skipping circuit is activated. The upper MOSFET will not be turned on as long as the sensed current is higher then the threshold value. This limits the current supplied by the DC voltage source. This condition keeps on for eight clock cycles after the overcurrent comparator was tripped for the first time. If after these first eight clock cycles the current exceeds the overcurrent threshold again in a time interval of another eight clock cycles, the overcurrent protection latches and disables the chip. If the overcurrent condition goes away during the first eight clock cycles, normal operation is restored and the overcurrent circuit resets itself sixteen clock cycles after the overcurrent threshold was exceeded the first time, Figure 8. R OCSET9.6V R CS100Ω+()•I OC R•DS ON()---------------------------------------------------------=FIGURE 8.OVERCURRENT PROTECTION WAVEFORMS312SHUTDOWN ILVOUTCH3 1.0AΩPGOODM 10.0µsCH2 100mVCH1 5.0V8 CLK。
IXYS 电路保护芯片数据手册说明书
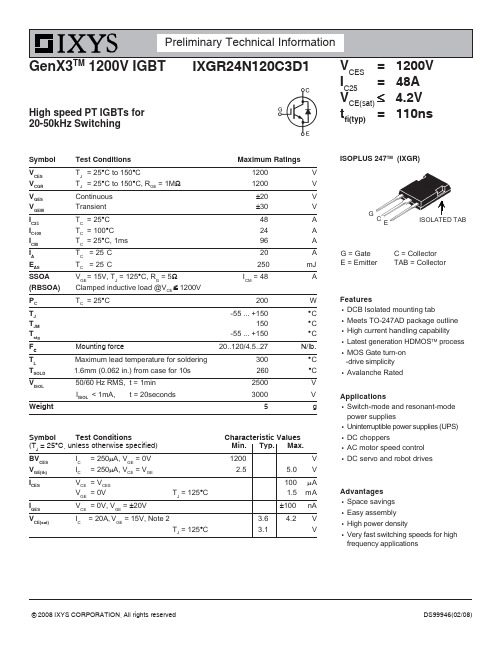
Symbol Test ConditionsMaximum RatingsV CES T J = 25°C to 150°C1200 V V CGR T J = 25°C to 150°C, R GE = 1M Ω1200 V V GES Continuous ±20 V V GEM Transient ±30VI C25T C = 25°C 48A I C100T C = 100°C 24A I CM T C = 25°C, 1ms 96AI A T C = 25°C 20 A E AST C = 25°C250 mJSSOA V GE = 15V, T J = 125°C, R G = 5ΩI CM = 48A(RBSOA)Clamped inductive load @V CE ≤ 1200V P C T C = 25°C200W T J -55 ... +150 °C T JM 150°C T stg -55 ... +150°C F CMounting force 20..120/4.5..27 N/lb.T L Maximum lead temperature for soldering 300°C T SOLD 1.6mm (0.062 in.) from case for 10s 260 °CV ISOL 50/60 Hz RMS, t = 1min2500 V I ISOL < 1mA, t = 20seconds 3000 VWeight5gSymbol Test ConditionsCharacteristic Values (T J = 25°C, unless otherwise specified) Min. Typ. Max.BV CES I C = 250μA, V GE = 0V 1200 V V GE(th)I C= 250μA, V CE = V GE2.5 5.0 VI CES V CE = V CES 100 μA V GE = 0VT J = 125°C1.5 mAI GES V CE = 0V, V GE = ±20V±100 nAV CE(sat)I C = 20A, V GE = 15V, Note 2 3.6 4.2 VT J = 125°C 3.1 VGenX3TM 1200V IGBTIXGR24N120C3D1V CES = 1200V I C25= 48A V CE(sat)≤ 4.2V t fi(typ)= 110nsHigh speed PT IGBTs for 20-50kHz SwitchingG = Gate C = Collector E = Emitter TAB = CollectorISOPLUS 247TM (IXGR)ISOLATED TABGCEFeatures•DCB Isolated mounting tab•Meets TO-247AD package outline •High current handling capability •Latest generation HDMOS TM process •MOS Gate turn-on -drive simplicity •Avalanche RatedApplications•Switch-mode and resonant-mode power supplies•Uninterruptible power supplies (UPS)•DC choppers•AC motor speed control •DC servo and robot drivesAdvantages •Space savings •Easy assembly •High power density•Very fast switching speeds for high frequency applicationsIXYS reserves the right to change limits, test conditions, and dimensions.Notes:1. Switching times may increase for V CE (Clamp) > 0.8 • V CES , higher T J or increased R G .2. Pulse test, t ≤ 300μs; duty cycle, d ≤ 2%.PRELIMINARY TECHNICAL INFORMATIONThe product presented herein is under development. The Technical Specifications offered are derived from data gathered during objective characterizations of preliminary engineering lots; but also may yet contain some information supplied during a pre-production design evaluation. IXYS reserves the right to change limits, test conditions, and dimensions without notice.IXYS reserves the right to change limits, test conditions, and dimensions.IXYS reserves the right to change limits, test conditions, and dimensions.20060010000400800120140160180200220040801201600.00.51.01.52.0K f T VJC -di F /dt02004006008001000040801200.00.40.81.2V FRdi F /dtV2006001000040080010203040506010010000123450123410203040506070I RMQ rI F A V F-di F /dt-di F /dtA/μs A V μC A/μs A/μs t rrnst fr A/μs μs Q rI RMFig. 21.Forward current I F versus V FFig. 23.Peak reverse current I RMFig. 22.Reverse recovery charge Q rFig. 25.Recovery time t rr versus -di F /dt Fig. 26.Peak forward voltage V FR andFig. 24.Dynamic Parameters Q r , I RM。
2SA1158 蜂鸟型 NPN 接地型 电阻 200 欧姆 芯片数据手册说明书
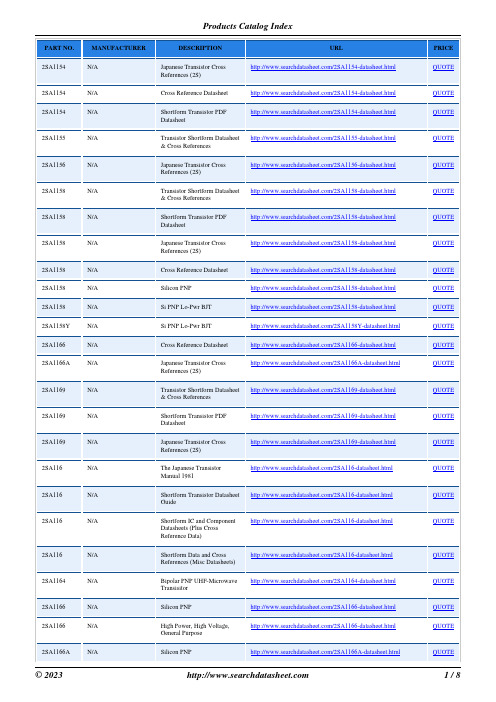
2SA1155
N/A
Transistor Shortform Datasheet /2SA1155-datasheet.html & Cross References
2SA1156
N/A
Japanese Transistor Cross References (2S)
2SA1166A
N/A
Silicon PNP
/2SA1166A-datasheet.html
© 2023
PRICE QUOTE QUOTE QUOTE QUOTE QUOTE QUOTE QUOTE QUOTE QUOTE QUOTE QUOTE QUOTE QUOTE QUOTE QUOTE QUOTE QUOTE QUOTE QUOTE QUOTE
2SA1158
N/A
Shortform Transistor PDF Datasheet
/2SA1158-datasheet.html
2SA1158
N/A
Japanese Transistor Cross References (2S)
/2SA1158-datasheet.html
2SA1169
N/A
Si PNP Power BJT
/2SA1169-datasheet.html
2SA1177
N/A
Transistor Shortform Datasheet /2SA1177-datasheet.html & Cross References
Japanese Transistor Cross References (2S)
/2SA1185-datasheet.html
2SA1186
SMA661AS 全集成 GPS LNA 芯片说明说明书
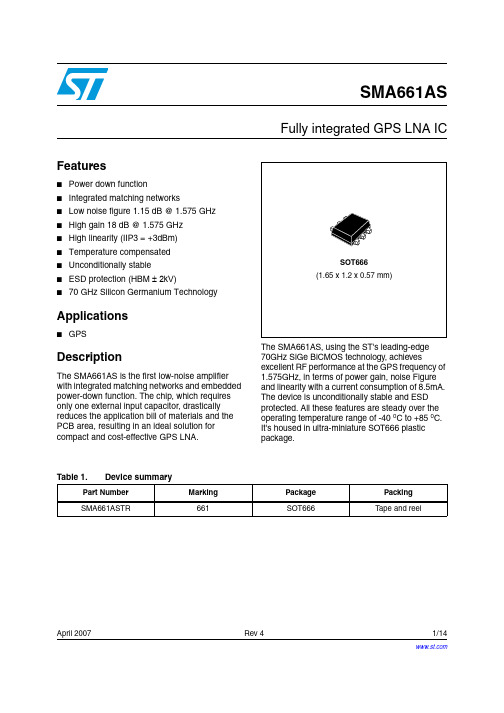
April 2007 Rev 41/14SMA661ASFully integrated GPS LNA ICFeatures■Power down function ■Integrated matching networks■*****************************■*********************■High linearity (IIP3 = +3dBm)■Temperature compensated ■Unconditionally stable ■ESD protection (HBM ± 2kV )■70 GHz Silicon Germanium TechnologyApplications■GPSDescriptionThe SMA661AS is the first low-noise amplifier with integrated matching networks and embedded power-down function. The chip, which requires only one external input capacitor, drastically reduces the application bill of materials and the PCB area, resulting in an ideal solution for compact and cost-effective GPS LNA.The SMA661AS, using the ST's leading-edge 70GHz SiGe BiCMOS technology, achievesexcellent RF performance at the GPS frequency of 1.575GHz, in terms of power gain, noise Figure and linearity with a current consumption of 8.5mA. The device is unconditionally stable and ESD protected. All these features are steady over the operating temperature range of -40 o C to +85 o C. It's housed in ultra-miniature SOT666 plastic package.Table 1.Device summaryPart Number Marking Package Packing SMA661ASTR661SOT666Tape and reelContents SMA661ASContents1Pins description and circuit schematic . . . . . . . . . . . . . . . . . . . . . . . . . . 32Electrical specifications . . . . . . . . . . . . . . . . . . . . . . . . . . . . . . . . . . . . . . 42.1Absolute maximum ratings . . . . . . . . . . . . . . . . . . . . . . . . . . . . . . . . . . . . . 42.2Electrical characteristics . . . . . . . . . . . . . . . . . . . . . . . . . . . . . . . . . . . . . . . 4 3Typical performance . . . . . . . . . . . . . . . . . . . . . . . . . . . . . . . . . . . . . . . . . 5 4Evaluation board description . . . . . . . . . . . . . . . . . . . . . . . . . . . . . . . . . . 85Package and packing informations . . . . . . . . . . . . . . . . . . . . . . . . . . . . 105.1Package informations . . . . . . . . . . . . . . . . . . . . . . . . . . . . . . . . . . . . . . . . 105.2Packing informations . . . . . . . . . . . . . . . . . . . . . . . . . . . . . . . . . . . . . . . . 11 6Revision history . . . . . . . . . . . . . . . . . . . . . . . . . . . . . . . . . . . . . . . . . . . 132/14SMA661AS Pins description and circuit schematic 1 Pins description and circuit schematicTable 2.Pins descriptionPin No.Pin Name1RF IN2GND3PD4RF OUT5GND6V CC3/14Electrical specifications SMA661AS4/142 Electrical specifications2.1Absolute maximum ratings2.2 Electrical characteristics(T a = +25 °C, V CC = 2.7 V , Z L = Z S = 50 ohm, unless otherwise specified; measuredaccording to Figure 13 at pin level)Table 3.Absolute maximum ratingsSymbol ParameterConditions ValueUnit V cc Supply voltage 3.3VT stg Storage temperature-60 to +150o C T a Operating ambient temperature -40 to +85oCV ESD Electrostatic Discharge HBM (ALL PINs)± 2000V V ESDElectrostatic DischargeMM (ALL PINs)± 200VTable 4.Electrical characteristicsSymbolParameters Test ConditionsMin.Typ.Max.Unit f Frequency 1575MHz V cc Supply voltage 2.42.73V I cc Current Consumption8.5mA I PD Power Down ModeCurrent Consumption V PD ≤ V PDL10nA G p Power gain 18dB NF Noise figure 1.15dB IIP2Input IP2f1 = 849 MHz, f2 = 2424 MHz, Pin = -30 dBm0.5dBm IIP3Input IP3f1 = 1574.5 MHz, f2 = 1575.5 MHz, Pin = -30 dBm3dBm ISL Reverse Isolation -28dB RLin Input Return Loss f = 1500-1650 MHz 10dB RLout Output Return Loss f = 1500-1650 MHz10dB V PDL (1)1.The device is switched to OFF state Power Down Low State0.5V V PDH (2)2. The device is switched to ON statePower Down High State1.0VStability100 - 10000 MHzUnconditionally stableSMA661AS Typical performance5/143 Typical performance(Vcc = 2.7 V , ZL = ZS = 50 ohm, unless otherwise specified; measured according to Figure 13 at pin level)Figure 3.Power Gain vs. Frequency Figure 4.Input Return Loss vs. FrequencyFigure 5.Noise Figure vs. Frequency Figure 6.Reverse Isolation vs. FrequencyFigure 7.Output Return Loss vs. Frequency Figure 8.IIP3 vs. TemperatureTypical performance SMA661AS6/14Note:S-Parameter are available on request.Figure 9.Current Consumption vs. TemperatureFigure 10.Gain Power Down vs. TemperatureFigure 11.Power Down Current vs.TemperatureSMA661ASTypical performance7/14Figure 12.Stability1 2 3 4 5 6 7 8 9 100 -Kf (GHz)0 0.511.522.533.544.55KEvaluation board description SMA661AS8/144 Evaluation board descriptionTable 5.Evaluation board bill of materialComponentValue Type Manufacturer Function C11µF (electrolytic)Case_A Various Supply Filter C247 pF 0603Murata (GRM188)RF Bypass C333 nF 0603Murata (GRM188)Input dc block / IIP3 improvementC547 pF 0603Murata (GRM188)RF Bypass C6 1 µF (electrolytic)Case_A Various Supply Filter J1- 142-0711-841(SMA_Female)Johnson RF Input connector J2- 142-0711-841(SMA_Female)Johnson RF Output connector U1-SOT666STMicroelectronicsSMA661AS GPS LNA Substrate-FR418mm x 20mm x 1.1mmVariousLayer = 3 (see Figure 14 & 15)SMA661ASEvaluation board description9/14Figure 14.Evaluation Board LayoutFigure 15.Evaluation Board Cross SectionNote:Gerber files of the SMA661AS evaluation board are available on request.Layout recommendation:Both lines from pin 2 and pin 5 to GND plane have to be as short as possible to maximize the performances. Therefore a via hole under the IC is highly recommended.18 mm20 mmPackage and packing informations SMA661AS10/145 Package and packing informations5.1 Package informationsIn order to meet environmental requirements, ST offers this device in ECOPACK® package.This package has a Lead-free second level interconnect. The category of second Level Interconnect is marked on the package and on the inner box label, in compliance with JEDEC Standard JESD97. The maximum ratings related to soldering conditions are also marked on the inner box label. ECOPACK is an ST trademark.ECOPACK specifications are available at: .Table 6.SOT666 (Lead-free) mechanical dataDIM.mm.MIN.TYPMAX.A 0.450.60A30.08018b 0.170.27b10.270.34D 1.50 1.70E 1.50 1.70E1 1.101.30e 0.50L10.19L20.100.30L30.10SMA661ASPackage and packing informations11/145.2 Packing informationsPackage and packing informations SMA661AS12/14Sprocket holeson the rightSprocket holeson the left661661661661Sprocket hole CavitySMA661AS Revision history13/146 Revision historyTable 7.Document revision historyDate RevisionChanges15-Jul-20051Initial release.20-Oct-20052Added: Evaluation Board Schematic & Layout.07-Jul-20063Changed to new template.Added packing informations.04-Apr-20074Updated noise figure and high gain values. Updated Figure 3 and Figure 5.SMA661AS14/14Please Read Carefully:Information in this document is provided solely in connection with ST products. STMicroelectronics NV and its subsidiaries (“ST”) reserve the right to make changes, corrections, modifications or improvements, to this document, and the products and services described herein at any time, without notice.All ST products are sold pursuant to ST’s terms and conditions of sale.Purchasers are solely responsible for the choice, selection and use of the ST products and services described herein, and ST assumes no liability whatsoever relating to the choice, selection or use of the ST products and services described herein.No license, express or implied, by estoppel or otherwise, to any intellectual property rights is granted under this document. If any part of this document refers to any third party products or services it shall not be deemed a license grant by ST for the use of such third party products or services, or any intellectual property contained therein or considered as a warranty covering the use in any manner whatsoever of such third party products or services or any intellectual property contained therein.UNL ESS OTHERWISE SET FORTH IN ST’S TERMS AND CONDITIONS OF SAL E ST DISCL AIMS ANY EXPRESS OR IMPL IED WARRANTY WITH RESPECT TO THE USE AND/OR SAL E OF ST PRODUCTS INCL UDING WITHOUT L IMITATION IMPL IED WARRANTIES OF MERCHANTABILITY, FITNESS FOR A PARTICULAR PURPOSE (AND THEIR EQUIVALENTS UNDER THE LAWS OF ANY JURISDICTION), OR INFRINGEMENT OF ANY PATENT, COPYRIGHT OR OTHER INTELLECTUAL PROPERTY RIGHT. UNL ESS EXPRESSL Y APPROVED IN WRITING BY AN AUTHORIZED ST REPRESENTATIVE, ST PRODUCTS ARE NOT RECOMMENDED, AUTHORIZED OR WARRANTED FOR USE IN MILITARY, AIR CRAFT, SPACE, LIFE SAVING, OR LIFE SUSTAINING APPLICATIONS, NOR IN PRODUCTS OR SYSTEMS WHERE FAILURE OR MALFUNCTION MAY RESULT IN PERSONAL INJURY, DEATH, OR SEVERE PROPERTY OR ENVIRONMENTAL DAMAGE. ST PRODUCTS WHICH ARE NOT SPECIFIED AS "AUTOMOTIVE GRADE" MAY ONLY BE USED IN AUTOMOTIVE APPLICATIONS AT USER’S OWN RISK.Resale of ST products with provisions different from the statements and/or technical features set forth in this document shall immediately void any warranty granted by ST for the ST product or service described herein and shall not create or extend in any manner whatsoever, any liability of ST.ST and the ST logo are trademarks or registered trademarks of ST in various countries.Information in this document supersedes and replaces all information previously supplied.The ST logo is a registered trademark of STMicroelectronics. All other names are the property of their respective owners.© 2007 STMicroelectronics - All rights reservedSTMicroelectronics group of companiesAustralia - Belgium - Brazil - Canada - China - Czech Republic - Finland - France - Germany - Hong Kong - India - Israel - Italy - Japan - Malaysia - Malta - Morocco - Singapore - Spain - Sweden - Switzerland - United Kingdom - United States of America。
SLC611加力传感器全球认可的准确性和安全性说明书
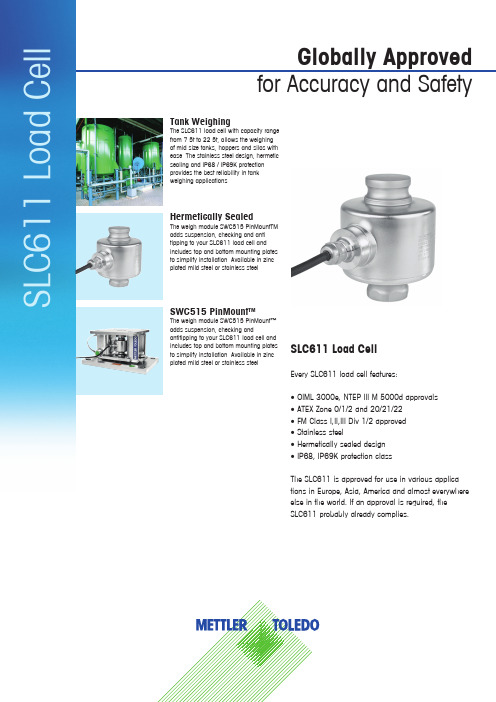
S L C 611 L o a d C e l lSLC611 Load CellEvery SLC611 load cell features:• OIML 3000e, NTEP III M 5000d approvals • ATEX Zone 0/1/2 and 20/21/22• FM Class I,II,III Div 1/2 approved • Stainless steel• Hermetically sealed design • IP68, IP69K protection classThe SLC611 is approved for use in various applica-tions in Europe, Asia, America and almost everywhere else in the world. If an approval is required, the SLC611 probably already complies.SLC611 Load Cell Specifications2METTLER TOLEDO Data Sheet SLC611 Load Cell ©02/2020Parameter unit of measureSpecifications Model No.SLC611Rated Capacity (R.C.)t (klb nominal)7.5 (16.5)15 (33)22.5 (49.6)Rated Output mV/*****. 2 ± 0.1%Zero load Output %R.C.≤ 1Combined Error 1), 2)%R.C.≤ 0.018Repeatability Error %A.L. 3)≤ 0.01Creep, 30 minute%A.L. ≤ 0.017Min. Dead Load Output Return (DR), 30 min %A.L.≤ 0.017Temperature Effect on Min. Dead Load Output %R.C./°C (.../°F)≤ 0.0018 (0.0010)Sensitivity 2)%A.L./°C (.../°F)≤ 0.001 (0.0006)Temperature RangeCompensated °C (°F)–10 ~ +40 (–14 ~ +104)Operating –40 ~ +65 (–40 ~ +149)Safe Storage–40 ~ +80 (–40 ~ +176)OIML/European Approval 4)OIML Cert. No.R60/2000-CN1-14.10European Cert. No.TC8669Class C3nmax 3000Y 7800PLC0.7Humidity Symbol CH Min. dead load kg (lb)0 (0)Z3000Barometric Pressure Effect Vmin/kPa< 1NTEP Approval 4)Number 15-011Class III M nmax 5000Vmin kg (lb)0.96 (2.12)1.92 (4.24)2.88 (6.36)Min. dead loadkg (lb)0 (0)ATEX Approval 4)Number DEKRA 15ATEX0015 XRatingII 1 G Ex ia IIC T6...T4 Ga / II 1 D Ex ia IIIC T100°C DaII 3 G Ex nA IIC T6...T4 Gc / II 3 G Ex ic IIC T6...T4 Gc / II 3 D Ex tc IIIC T100°C DcEntity ParametersUi = 25V, li = 600mA, C i = 6nF, Li = 30µH, P i = 1.25W (T4), 0.86W (T5), 0.51W (T6)Factory Mutual Approval 4)Number, USA 3013511Number, Canada 3028342CRating, USA IS / I, II, III / 1 / ABCDEFG / T5NI / I, II, III, / 2 / ABCDFG / T6Rating, CanadacFM IS/I, II, III / 1 / ABCDEFG / T5 TA= -40°C to +55°C; NI / I / 2 / ABCD /T6 Ta = -40°C to +55°C, DIP /II,III/2/FGCASComplyEntity Parameters Vmax = 25V, Imax = 600mA, Pi = 1.25W, Ci = 4nF 4), Li = 20µH 4)Sys. Drawing No, USA 30105817Sys. Drawing No, Canada30105818Excitation Voltage Recommended V AC/DC 5 ~ 15Max.20Terminal ResistanceExcitation Ω1150 ± 50Output 1000 ± 2Insulation Resistance @50VDC MΩ> 5000Breakdown Voltage V AC > 500MaterialSpring Element stainless steel Enclosure 304 stainless steel Cable entry fitting 304 stainless steel Cable Polyurethane (PU) & FEP3SLC611 Load Cell Dimensions mm1) Error due to the combined effect of non-linearity and hysteresis2) Typical values only. The sum of errors due to Combined Error and Temperature Effect on Sensitivity comply with the requirements of OIML R60 and NIST HB44.3) A.L. = Applied Load4) See certificate for complete information5) % of Applied Load (A.L.) per mm (in) displacement of the top button relative to the bottom button 6) Maximum horizontal displacement of the top button relative to the bottom buttonParameter unit of measure SpecificationsProtectionType welded IP Rating IP68, IP69K NEMA RatingNEMA 6/6PLoad Limit Safe %R.C.200Ultimate300Safe Dynamic Load %R.C.70Fatigue Life **********.1000000Direction of Loading compressionRestoring Force5)%A.L./mm (../in) 3)2.4 (61)3.4 (87)Max Horizontal Travel 6)± mm (in)8 (0.31)7 (0.27) 5 (0.2)**************.,nominal mm (in)0.20 (0.008)0.37 (0.015)0.49 (0.019)Weight, nominal kg (lb) 1 (2.2)Cable Length m (ft)12, 20 (39.4, 65.6)Diameter mm (in)5.2 (0.20)Drawing No.Dimensions 30220610To-Scale30220594SLC611 Load Cell Order InformationWeighing ElectronicsMETTLER TOLEDO offers a complete family of electronics from simple weighing to application solutions for filling, stock control, batching, formulation, counting, and checkweighing.Full ConnectivityMETTLER TOLEDO supplies various data communication interfaces that enable our sensors and instruments to communicate with your PLC, MES, or ERP systems.Global ApprovalsThe SLC611 is provided with all listed approvals. No need tothink about options and additional charges. Simplifies the conduct of global business, order processing and service-part stocking.Visit for more informationOur extensive service network is among the best in the world and ensures maximum availability and service life of your product.SLC611 Load Cell Cable ColorsColour FunctionGreen + Excitation Black – Excitation White + Signal Red – Signal YellowShieldBolded entries are stockedOrder InformationItem No.ClassCable, Material / LengthPU / 12 m (39.4ft)PU / 20 m (65.6ft)FEP / 12 m (39.4ft)FEP / 20 m (65.6ft)7.5 t / 16.5 klb C3/III M n:53005806030058064301057813010578615 t / 33 klb C3/III M n:53005806130058065301057833010578822.5 t / 49.6 klbC3/III M n:530058062300580663010578430105789Mettler Toledo GmbH CH-8606 Greifensee SwitzerlandTel. +41 44 944 22 11Fax +41 44 944 30 60Subject to technical changes© 02/2020 Mettler-Toledo GmbH MarCom SwitzerlandMTSI Document-No: 30242848。
OWI 产品说明书:IC5、IC6、IC570V40、IC570V10、IC670V10 和 IC6
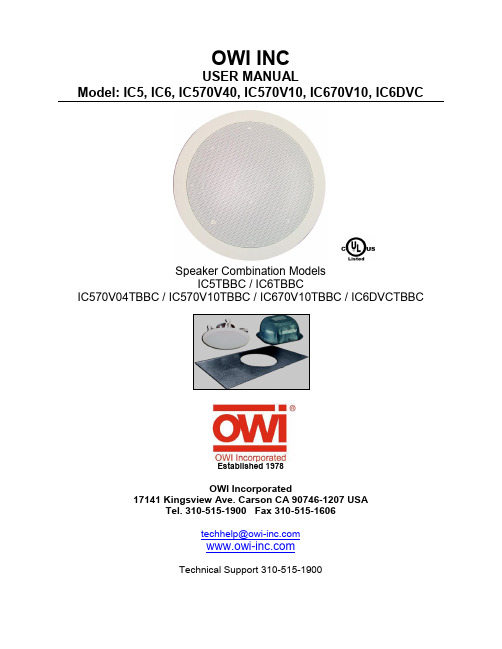
OWI INCUSER MANUALModel: IC5, IC6, IC570V40, IC570V10, IC670V10, IC6DVCSpeaker Combination ModelsIC5TBBC / IC6TBBCIC570V04TBBC / IC570V10TBBC / IC670V10TBBC / IC6DVCTBBCEstablished 1978OWI Incorporated17141 Kingsview Ave. Carson CA 90746-1207 USATel. 310-515-1900 Fax 310-515-1606********************Technical Support 310-515-1900PROPRIETARY NOTICEThe OWI Inc. product information and design disclosed herein were originated by and are the property of OWI Inc. OWI Inc. reserves all patent, proprietary design, manufacturing, reproduction, use and sales rights thereto, and to any article disclosed therein, except to the extent right(s) are expressly granted to others.COPYRIGHT NOTICEThis manual is Copyright 2014 by OWI Inc. All rights reserved. Reproduction in whole or in part without written prior permission from OWI, Inc. is prohibited.UNPACKING AND INSPECTION NOTICEImmediately upon receipt of the equipment, inspect the shipping container and the contents carefully for any discrepancies or damage. Should there be any, notify the freight company and OWI, Inc. or the dealer where purchased at once.LIMITED WARRANTY1. This product has been thoroughly tested and inspected at the factory. It is warranted for one year from thedate of purchase.IT IS THE OWNERS’ RESPONSIBILITY TO ESTABLISH THE DATE OF PURCHASE BY ACCEPTABLE EVIDENCE AT TIME SERVICE IS SOUGHT.2. Any unit, which in the judgment of OWI INC, is defective or develops defects under normal use will be replacedor repaired without cost within the warranty period.3. This warranty will be considered void if the unit is dropped, misused, abused and altered in any manner,overdriven with e xcess amplification exceeding manufacturer’s specification, improperly serviced or accidentally damaged.4. OWI Inc. shall have no liability whatsoever for consequential damages. The sole responsibility at the discretionof OWI Inc. under this warranty shall be limited to the repair of the product or replacement thereof. Any and all implied warranties including the implied warranty of merchantability are limited to the duration of this express limited warranty.OWI, Inc. is NOT liable for incidental or consequential damages of any kind.5. IMPORTANT: This warranty is void unless the attached card is completed and mailed to OWI Inc. within 10days following the date of purchase. Units must be sent to OWI Inc. or to the dealer where purchased. RETURN SHIPPING INSTRUCTIONS, Obtain a RETURN AUTHORIZATION from:OWI Inc., 17141 Kingsview Ave, Carson, CA 90746.Phone (310) 515-1900, Fax (310) 515-1606FCC Notice: This equipment has been tested and found to comply with the limits for a Class A digital device, pursuant to part 15 of the FCC Rules. These limits are designed to provide reasonable protection against harmful interference when the equipment is operated in a commercial environment. This equipment generates, uses, and can radiate radio frequency energy and, if not installed and used in accordance with the instruction manual, may cause harmful interference to radio communications. Operation of this equipment in a residential area is likely to cause harmful interference in which case the user will be required to correct the interference at his or own expense.Modifications not expressly approved by the manufacturer could void the user’s authority to be operated under FCC rules.Table of ContentsIMPORTANT SAFETY INSTRUCTIONS____________________________________________________________________________________________________CAUTIONRISK OF ELECTRIC SHOCK - DO NOT OPEN____________________________________________________________________________________________________ NOTE: Installation is to be completed by a qualified electrical technician according to NEC/CEC code and applicable local codes.CAUTION: The power supply is not to be used in air handling spaces.CAUTION: To reduce the risk of electric shock: Do not remove the cover or back: No user-serviceable parts inside: refer servicing to qualified personnel.The lighting flash with arrowhead within an equilateral triangle is intended to alert the user to the presence of unins ulated “dangerous voltage” within the product’s enclosure that may be of sufficient magnitude to constitute a risk of electric shock to persons.The exclamation point within an equilateral triangle is intended to alert the user of the presence of important operating and maintenance (servicing) instructions in the literature accompanying the appliance.The apparatus shall not be exposed to dripping or splashing and that no objects filled with liquids, such as vases, shall be placed on the apparatus.IMPORTANT SAFETY INSTRUCTIONS1. Read these instructions. All the safety and operation instructions should be read before this OWIproduct is operated.2. Keep these instructions - The safety and operating instructions should be kept for future reference.3. Heed all warnings - All warnings on this product and in these operating instructions should befollowed.4. Follow all instructions - All operating and other instructions should be followed.5. Do not use this apparatus near water - for example, near a bathtub, washbowl, kitchen sink, laundrytub, in a wet basement, near a swimming pool, or a swamp.6. Clean only with dry cloth.7. Do not block any ventilation openings. Install in accordance with the manufacturer’s instructions. -This OWI product should be situated so that its location or position does not interfere with its proper ventilation. For example, the component should not be situated on a bed, sofa, rug, or similar surface that may block any ventilation openings, or placed in a built-in installation such as a bookcase or cabinet that may impede the flow of air through ventilation openings.8. Do not install the unit near any heat sources such as radiators, heat registers, stoves or otherapparatus (including amplifiers) that produce heat.9. Do not defeat the safety purpose of the polarized or grounding-type plug. A polarized plug has twoblades with one wider than the other. A grounding type plug has two blades and a third grounding prong. The wider blade or the third prong is provided for your safety. If the provided plug does not fit into your outlet, consult an electrician for replacement of the obsolete outlet.10. Protect the power cord from being walked on or pinched particularly at plugs, conveniencereceptacles, and the point where they exit the apparatus.11. Only use attachment/accessories specified by the manufacturers.Portable Cart Warning12. Use only with the cart, stand, tripod, bracket or table specified by the manufacturer, or sold with theapparatus. When a cart is used, use caution when moving the cart/apparatus combination to avoid injury from tip-over.13. Unplug this apparatus during lightning storms or when unused for long periods of time.14. Refer all servicing to qualified service personnel. Servicing is required when the apparatus has beendamaged in any way, such as power-supply cord or plug is damaged, liquid has been spilled or objects have fallen into the apparatus, the apparatus has been exposed to rain or moisture, does not operate normally, or has been dropped. The user should not attempt to service this OWI product beyond those means described in this operating manual. All other servicing should be referred to the OWI Service Department.15. WARNING: To reduce the risk of fire or electric shock, do not expose this apparatus to rain ormoisture.16. To prevent electric shock, do not use this polarized plug with an extension cord, receptacle or otheroutlet unless the blades can fully be inserted to prevent blade exposure.17. Exposure to extremely high noise levels may cause permanent hearing loss. Individuals varyconsiderably in susceptibility to noise-induced hearing loss, but nearly everyone will lose some hearing if exposed to sufficiently intense noise for a period of time. The U.S. Government’s Occupational Safety and Health Administration (OSHA) has specified the permissible noise level exposures shown in the following chart. According to OSHA, any exposure in excess of these permissible limits could result in some hearing loss. To ensure against potentially dangerous exposure to high sound pressure levels, it is recommended that all persons exposed to equipment capable of producing high sound pressure levels use hearing protectors while the equipment is in operation. Ear plugs or protectors in the ear canals or over the ears must be worn when operating the equipment in order to prevent a permanent hearing loss if exposure is in excess of the limits set forth here.18. OWI recommends that this apparatus be placed on a switched power outlet, one that switches bothsides and has contact separation of at least 3 millimeters.End of IMPORTANT SAFETY INSTRUCTIONSMODEL IC5 / IC6 / IC6DVCSPEAKER SPECIFICATIONS:MODEL IC5 MODEL IC6 MODEL IC6DVCMODEL IC570V04 / IC570V10 / IC670V10SPEAKER SPECIFICATIONS:MODEL IC570V04 MODEL IC570V10 MODEL IC670V10INSTALLATION:Speaker PlacementBefore installing your OWI speakers, consider the placement carefully, taking into effect the location of electrical, plumbing and other fixtures.Placement in CeilingOWI speakers should be ideally located above the primary listening area.Placement in WallOptimum sound will be achieved when your OWI speakers are installed at ear level or slightly higher and the listening area is no closer to the speakers than the distance between the speakers themselves.Mounting your OWI SpeakersDetermine the best area to mount your OWI speakers. It will be necessary to run your speaker wires to that location. This location must be free of obstructions, such as electrical conduits, HVAC ducts, or water lines.Be sure the mounting surface is between 3/8 and 1 1/4 inches thick and there is at least a 3 1/2inch clearance behind the mounting surface and no wall studs or other objects block the back of the speaker.Remove the round cardboard disc from the cutout template supplied and keep it for later use as a paint mask, if you decide to paint your speakers.Use the template to mark the position for the mounting hole at the selected location. If you are not certain that no obstruction exists (electrical wiring. plumbing. etc.), you should start by cutting a small hole in the center of your penciled mounting hole with a drywall or keyhole saw, cutting at a 45 degree angle towards the inside of the hole. Cutting a small hole at this angle will make drywall repair much easier. Once you have determined there are no obstructions in your desired mounting location, start cutting the finished hole at a 900angle to the wall/ceiling surface.Route the speaker wires from your amplifier to your opening. Avoid routing the speaker wire near electrical wires. If you have to run them parallel, make certain to space the speaker wires at least 2 feet from the AC line. Do not nail or staple the speaker wire.Preparing your OWI Speakers for MountingInsert a paper clip into one of the grille openings, then pull upwards to remove the grille.Be sure to position the four Mounting Tabs on your OWI speaker inward then insert the four screws (supplied) from the front of the speaker into the screw opening.Attach the speaker wires to the speaker terminals.Insert your OWI speaker into the opening and tighten the four screws. As you tighten the screws, the tabs will automatically flip into an outward position thereby clamping the drywall between the feet and the flange of the speaker. BE CAREFUL NOT TO OVER TIGHTEN, OVER TIGHTENING MAY WARP THE BAFFLE, CRACK THE WALL, CAUSE THE FLANGE TO DISTORT AND MAKE THE GRILL DIFFICULT TO INSTALL.Push the grille firmly into the slot in the speaker baffle.Painting your OWI SpeakersThe speakers' other surfaces are primed to accept ordinary latex wall paint or aerosol spray paint. The surface of the speaker behind the grille should remain black and must not be painted. It is necessary to mask this area with the center of the template that you have cut out.The grille can be painted as well, but great care must be taken not to clog the holes in the grille as this will greatly reduce the sound quality of the speakers. It is recommended that only light spray painting using 5 parts thinning agent to 1 part paint be used. Do not paint the grilles while they are attached to the speaker.Proper Wire Gauge SelectionThe gauge of wire required is determined by the distance between your amplifier/receiver and the speakers. Use the following chart as a guide:Length Minimum GaugeLess than 10 feet 18 - 20 Gauge 10 to 100 feet 16 to 18 Gauge Over 100 feet 14 GaugeOWI SPEAKER SYSTEM LIMITED WARRANTY REGISTRATION(Save this portion for your records)1. Your OWI Speaker System has been thoroughly tested and inspected at the factory.It is warranted for 5 years from date of purchase.IT IS THE OWNERS’ RESPONSI BILITY TO ESTABLISH THE DATE OF PURCHASE BY ACCEPTABLE EVIDENCE AT TIME SERVICE IS SOUGHT.2. WHAT WE WILL PAY FOR AND WHAT YOU MUST PAY FOR:OWI INC. will repair or replace unit(s) covered by this warranty, without charge to the consumer for labor or materials. YOU ARE RESPONSIBLE FOR ANY INSTALLATION OR REMOVAL CHARGES AND FOR ANY INITIAL SHIPPING CHARGES if the unit(s) must be shipped for warranty service.However, we will pay the return shipping charges to any destination within the U.S.A. if the repairs are covered by the warranty.3. Any unit which in the judgment of OWI Inc. is defective or develops defects under normal use will bereplaced or repaired without cost within the warranty period.4. This warranty will be considered void if unit has been dropped, misused, abused, altered in anymanner, overdriven with excessive amplification exceeding manufacturer’s specification, improperly serviced or accidental damage.5. OWI Inc. shall have no liability whatsoever for consequential damage. The sole responsibility anddiscretion of OWI Inc. under this warranty shall be limited to the repair of the product or replacement thereof.6. IMPORTANT: This warranty is void unless the attached card is completed and mailed to OWI Inc.within 10 days following the date of purchase. Units must be sent to OWI Inc. or to the dealer where purchased.OWI INCORPORATED Date Purchased: ________________________17141 Kingsview Ave Model Number: ________________________Carson, CA 90746-1207 USA Serial Number: ________________________(Keep this part for your record)-------CUT AND MAIL----------------------------------------------------OWI INCORPORATED17141 Kingsview AveCarson, CA 90746-1207 USALIMITED WARRANTYModel Number:_________________________________Model Name: __________________________________Serial No. _____________________________________Date of Purchase: Month: __________ Day ____ Year ______Owner’s Name: ______________________________________Address: ________________________________________City: _______________________ State __________ Zip_______Dealer’s Name: _________________________ City______________ State ________Purchased from (please check one):Video ____, Electronic ____, Mailorder ___, Mass Merchandiser ___, Installer ___Others (please specify) __________________________________________________Remarks: __________________________________________________________________________________________________________________________________Established 1978OWI Incorporated17141Kingsview Ave. Carson CA 90746-1207 USA Tel. 310-515-1900 Fax 310-515-1606www.owi-inc.om。
ISL6251(笔记本)电池充放电管理芯片引脚定义(图)
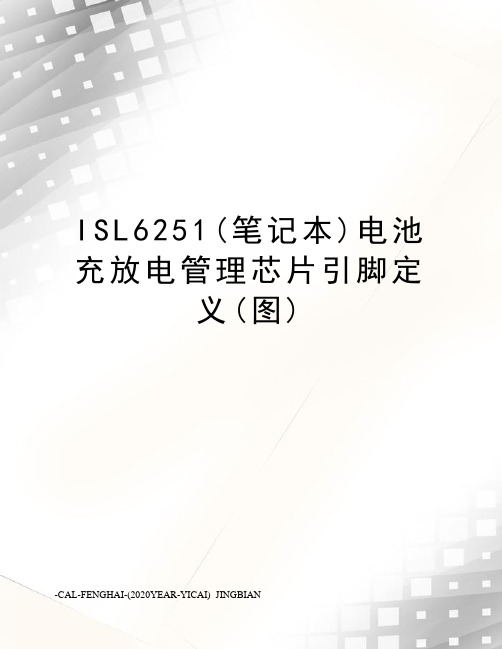
I S L6251(笔记本)电池充放电管理芯片引脚定义(图)-CAL-FENGHAI-(2020YEAR-YICAI)_JINGBIANISL6251AHRZ (笔记本)电池充放电管理芯片引脚定义21,22脚CSOP/CSON:是电池的充电电流感应正/负输入。
在CSOP的差动电压和CSON是用于检测电池的充电电流,并与充电电流限制门限调节充电电流。
该CSON管脚也可以用作电池的反馈电压来执行电压调节。
19,20脚CSIP/CSIN: 是AC适配器电流传感正/负输入。
CSIP的两端的差分电压和CSIN是用于检测AC适配器电流,并与AC适配器电流限制相比,调节AC适配器电流。
24脚DCIN: 是内部5V LDO输入。
它连接到AC适配器的输出。
连接DCIN一个0.1μF的陶瓷电容。
2脚ACSET:是一个AC适配器检测输入。
连接到从适配器输入电阻分压器。
23脚CACPRN:是AC适配器开漏输出。
ACPRN是低电平时ACSET比通常1.26V较高,高电平时ACSET比一般1.26V低。
3脚 EN:是充电使输入。
连接中文高使充电控制功能,连接中文的充电功能低禁用。
使用的热敏电阻来检测并暂停热电池充电。
7脚ICM:是适配器的电流输出。
该引脚输出产生的电压成正比适配器的电流。
13脚PGND:是电源地。
连接PGND到的低侧MOSFET栅极驱动器低电压端MOSFET源。
1脚VDD:是一个内部LDO输出电源IC的模拟电路。
连接一个1μF陶瓷电容接地。
15脚VDDP:是低端MOSFET栅极驱动器电源电压。
4.7Ω电阻连接到VDD和1μF陶瓷电容,电源地。
5脚ICOMP:是一个电流环误差放大器输出。
6脚VCOMP:是一个循环放大器的输出电压。
4脚CELLS:这个引脚用于选择电池电压。
细胞=内径为4型电池组,电池=接地为3S号电池,电池=浮法为2秒电池组。
11脚VADJ:调整电池的稳压电压。
VADJ =参考电压为4.2V的5%; VADJ =为4.2V/cell浮动; VADJ =接地为4.2V的5%。
MPXV6115VC6U;MPXV6115VC6T1;中文规格书,Datasheet资料
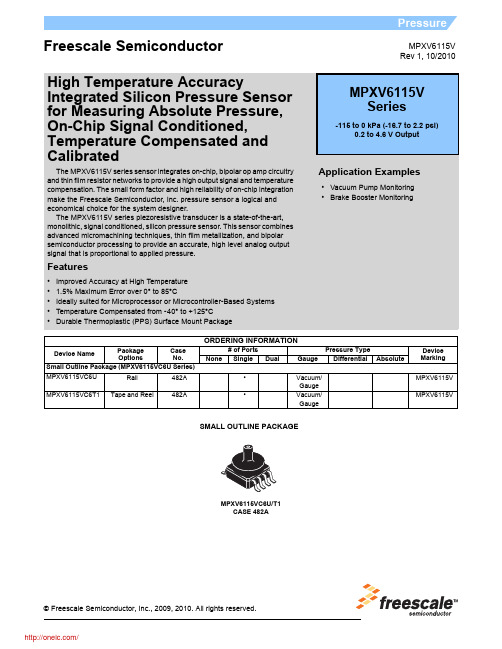
Symbol Pmax Tstg TA Io+ Io-
Value 400 -40 to +125 -40 to +125 0.5 -0.5
1. Exposure beyond the specified limits may cause permanent damage or degradation to the device. 2. Maximum Output Current is controlled by effective impedance from Vout to Gnd or Vout to VS in the application circuit.
Pressure
Operating Characteristics
Table 1. Operating Characteristics (VS = 5.0 Vdc, TA = 25°C unless otherwise noted, P1 > P2)
Characteristic
Symbol
Min
Typ
Pressure Range Supply Voltage(1)
POP
-115
—
VS
4.75
5.0
Supply Current
Full Scale Output(2) @ VS = 5.0 Volts
Io
—
6.0
(0 to 85°C)
VFSO
4.534
4.6
Full Scale Span(3) @ VS = 5.0 Volts
None Single Dual
Gauge Differential Absolute
•
- 1、下载文档前请自行甄别文档内容的完整性,平台不提供额外的编辑、内容补充、找答案等附加服务。
- 2、"仅部分预览"的文档,不可在线预览部分如存在完整性等问题,可反馈申请退款(可完整预览的文档不适用该条件!)。
- 3、如文档侵犯您的权益,请联系客服反馈,我们会尽快为您处理(人工客服工作时间:9:00-18:30)。
®ISL6115, ISL6116, ISL6117, ISL6120Power Distribution ControllersThis family of fully featured hot swap power controllers targets applications in the +2.5V to +12V range. TheISL6115 is for +12V control, the ISL6116 for +5V, theISL6117 for +3.3V and the ISL6120 for +2.5V control applications. Each has a hard wired undervoltage (UV) monitoring and reporting threshold level approximately 80% of the aforementioned voltage.The ISL6115 has an integrated charge pump allowing control of up to +16V rails using an external N-Channel MOSFET whereas the other devices utilize the +12V bias voltage to fully enhance the N-channel pass FET. All ICs feature programmable overcurrent (OC) detection, current regulation (CR) with time delay to latch-off and soft-start.The current regulation level is set by 2 external resistors;R ISET sets the CR Vth and the other is a low ohmic sense element across, which the CR Vth is developed. The CR duration is set by an external capacitor on the CTIM pin, which is charged with a 20µA current once the CR Vth level is reached. If the voltage on the CTIM cap reaches 1.9V the IC then quickly pulls down the GATE output latching off the pass FET.This family although designed for high side switch control the ISL6116, ISL6117, ISL6120 can also be used in a low side configuration for control of much higher voltage potentials.Features•HOT SWAP Single Power Distribution Control (ISL6115 for +12V, ISL6116 for +5V, ISL6117 for +3.3V and ISL6120 for +2.5V)•Overcurrent Fault Isolation•Programmable Current Regulation Level •Programmable Current Regulation Time to Latch-Off •Rail to Rail Common Mode Input Voltage Range (ISL6115)•Internal Charge Pump Allows the use of N-Channel MOSFET for +12V control (ISL6115)•Undervoltage and Overcurrent Latch Indicators •Adjustable Turn-On Ramp•Protection During Turn On•Two Levels of Overcurrent Detection Provide Fast Response to Varying Fault Conditions•1µs Response Time to Dead Short•Pb-Free Plus Anneal Available (RoHS Compliant)•Tape & Reel Packing with ‘-T’ Part Number Suffix Applications•Power Distribution Control•Hot Plug Components and CircuitryPinoutISL6115, ISL6116, ISL6117, ISL6120(8 LD SOIC)TOP VIEWOrdering InformationPART NUMBERPARTMARKINGTEMP.RANGE (°C)PACKAGEPKG.DWG. #ISL6115CB*ISL61 15CB0 to +858 Ld SOIC M8.15 ISL6116CB*ISL61 16CB0 to +858 Ld SOIC M8.15 ISL6117CB*ISL61 17CB0 to +858 Ld SOIC M8.15 ISL6120CB*ISL61 20CB0 to +858 Ld SOIC M8.15ISL6115CBZA* (Note)6115 CBZ0 to +858 Ld SOIC(Pb-free)M8.15ISL6116CBZA* (Note)6116 CBZ0 to +858 Ld SOIC(Pb-free)M8.15ISL6117CBZA* (Note)6117 CBZ0 to +858 Ld SOIC(Pb-free)M8.15ISL6120CBZA* (Note)6120 CBZ0 to +858 Ld SOIC(Pb-free)M8.15*Add “-T” suffix for tape and reel.NOTE:Intersil Pb-free products employ special Pb-free material sets; molding compounds/die attach materials and 100% matte tin plate termination finish, which is compatible with both SnPb and Pb-free soldering operations. Intersil Pb-free products are MSL classified at Pb-free peak reflow temperatures that meet or exceed the Pb-free requirements of IPC/JEDEC J Std-020B.ISETISENGATEVSS12348765PWRONPGOODCTIMVDDApplication One - High Side ControllerApplication Two - Low Side Controller+12V-+PWRONLOADPGOODOC12348765ISL6115+V supply to be controlledISL6116ISL6117ISL6120LOAD12V REG+VBUSOC12348765PWRONISL6116/7/20Simplified Block Diagram+-I SETI SENGATEV SSV DD CTIMPGOODPWRONCLIMWOCLIMENABLEOC10µAFALLING EDGE DELAY18V+- V REF +- 1.86V12V+-R R SQN QENABLEPOR V DD8VRISING EDGE PULSE+-+-UV18V20µA7.5K+-+-20µAUV DISABLEISL611X Pin DescriptionsPIN #SYMBOL FUNCTIONDESCRIPTION1ISET Current Set Connect to the low side of the current sense resistor through the current limiting set resistor. This pin functions as the current limit programming pin.2ISEN Current SenseConnect to the more positive end of sense resistor to measure the voltage drop across this resistor.3GATEExternal FET Gate Drive PinConnect to the gate of the external N-Channel MOSFET. A capacitor from this node to ground sets the turn-on ramp. At turn-on this capacitor will be charged to V DD +5V (ISL6115) and to V DD (ISL6116, ISL6117, ISL6120) by a 10μA current source.4 VSS Chip Return 5V DD Chip Supply 12V chip supply. This can be either connected directly to the +12V rail supplying the switched load voltage or to a dedicated V SS +12V supply.6CTIMCurrent Limit Timing CapacitorConnect a capacitor from this pin to ground. This capacitor determines the time delaybetween an overcurrent event and chip output shutdown (current limit time-out). The duration of current limit time-out is equal to 93k Ω x C TIM .7 PGOODPower Good IndicatorIndicates that the voltage on the ISEN pin is satisfactory. PGOOD is driven by an open drain N-Channel MOSFET and is pulled low when the output voltage (VISEN) is less than the UV level for the particular IC.8 PWRON Power ONPWRON is used to control and reset the chip. The chip is enabled when PWRON pin is driven high to a maximum of 5V or is left open. After a current limit time out, the chip is reset by a low level signal applied to this pin. This input has 20μA pull up capability.Absolute Maximum Ratings T A = +25°C Thermal InformationV DD . . . . . . . . . . . . . . . . . . . . . . . . . . . . . . . . . . . . . . -0.3V to +16V GATE. . . . . . . . . . . . . . . . . . . . . . . . . . . . . . . . . . . -0.3V to V DD+8V ISEN, PGOOD, PWRON, CTIM, ISET. . . . . . . -0.3V to V DD + 0.3V ESD Classification. . . . . . . . . . . . . . . . . . . . . . . . . . . . . . . . . . . 5kV Operating ConditionsV DD Supply Voltage Range. . . . . . . . . . . . . . . . . . . . . . +12V ±15% Temperature Range (T A) . . . . . . . . . . . . . . . . . . . . . . . 0°C to +85°C Thermal Resistance (Typical, Note 1)θJA (°C/W) SOIC Package. . . . . . . . . . . . . . . . . . . . . . . . . . . . . 98 Maximum Junction Temperature (Plastic Package) . . . . . . .+150°C Maximum Storage Temperature Range. . . . . . . . . .-65°C to +150°C Maximum Lead Temperature (Soldering 10s) . . . . . . . . . . . .+300°C (SOIC - Lead Tips Only)CAUTION: Stresses above those listed in “Absolute Maximum Ratings” may cause permanent damage to the device. This is a stress only rating and operation of the device at these or any other conditions above those indicated in the operational sections of this specification is not implied.NOTES:1.θJA is measured with the component mounted on a high effective thermal conductivity test board in free air. (See Tech Brief, #TB379.1 fordetails.)2.All voltages are relative to GND, unless otherwise specified3.G.N.T. Guaranteed by design and characterization but Not Tested.Electrical Specifications V DD = 12V, T A = T J = 0°C to +85°C, Unless Otherwise SpecifiedPARAMETER SYMBOL TEST CONDITIONS MIN TYP MAX UNITS CURRENT CONTROLISET Current Source I ISET_ft18.52021.5μA ISET Current Source I ISET_pt T J = +15°C to +55°C192021μA Current Limit Amp Offset Voltage Vio_ft V ISET - V ISEN-606mV Current Limit Amp Offset Voltage Vio_pt V ISET - V ISEN, T J = +15°C to +55°C-202mV GATE DRIVEGATE Response Time To Severe OC pd_woc_amp V GATE to 10.8V-100-ns GATE Response Time to Overcurrent pd_oc_amp V GATE to 10.8V-600-ns GATE Turn-On Current I GATE V GATE to = 6V8.41011.6μA GATE Pull Down Current OC_GATE_I_4V Overcurrent4575-mA GATE Pull Down Current (3)WOC_GATE_I_4V Severe Overcurrent0.50.8-A ISL6115 Undervoltage Threshold12V UV_VTH9.29.610V ISL6115 GATE High Voltage12VG GATE Voltage V DD + 4.5V V DD + 5V-V ISL6116 Undervoltage Threshold5V UV_VTH 4.0 4.35 4.5V ISL6117 Undervoltage Threshold3V UV_VTH 2.4 2.6 2.8V ISL6120 Undervoltage Threshold2V UV_VTH 1.8 1.85 1.9V ISL6116, 17, 20 GATE High Voltage VG GATE Voltage V DD - 1.5V V DD-V BIASV DD Supply Current I VDD-35mAV DD POR Rising Threshold V DD_POR_L2H VDD Low to High7.88.49VV DD POR Falling Threshold V DD_POR_H2L VDD High to Low7.58.18.7VV DD POR Threshold Hysteresis V DD_POR_HYS V DD_POR_L2H - V DD_POR_H2L0.10.30.6V PWRON Pull-Up Voltage PWRN_V PWRON Pin Open 2.7 3.2-V PWRON Rising Threshold PWR_Vth 1.4 1.7 2.0V PWRON Hysteresis PWR_hys130170250mV PWRON Pull-Up Current PWRN_I91725μADescription and OperationThe members of this family are single power supply distribution controllers for generic hot swap applications across the +2.5V to +12V supply range. The ISL6115 is targeted for +12V switching applications whereas theISL6116 is targeted for +5V, the ISL6117 for +3.3V and the ISL6120 for +2.5V applications. Each IC has a hardwired undervoltage (UV) threshold level approximately 17% lower than the stated voltages.These ICs feature a highly accurate programmable overcurrent (OC) detecting comparator, programmablecurrent regulation (CR) with programmable time delay to latch off, and programmable soft-start turn-on ramp all set with a minimum of external passive components. The ICs alsoinclude severe OC protection that immediately shuts down the MOSFET switch should a rapid load current transient such as a near dead short cause the CR Vth to exceed theprogrammed level by 150mV. Additionally, the ICs have a UV indicator and an OC latch indicator. The functionality of the PGOOD feature is enabled once the IC is biased, monitoring and reporting any UV condition on the ISEN pin.Upon initial power up, the IC can either isolate the voltage supply from the load by holding the external N-ChannelMOSFET switch off or apply the supply rail voltage directly to the load for true hot swap capability. The PWRON pin must be pulled low for the device to isolate the power supply from the load by holding the external N-channel MOSFET off. With the PWRON pin held high or floating the IC will be in true hot swap mode. In both cases the IC turns on in a soft-start mode protecting the supply rail from sudden in-rush current.At turn-on, the external gate capacitor of the N-Channel MOSFET is charged with a 10μA current source resulting in a programmable ramp (soft-start turn-on). The internal ISL6115 charge pump supplies the gate drive for the 12V supply switch driving that gate to ~V DD +5V, for the other three ICs the gate drive voltage is limited to the chip bias voltage, VDD.Load current passes through the external current senseresistor. When the voltage across the sense resistor exceeds the user programmed CR voltage threshold value, (see T able 1 for R ISET programming resistor value and resulting nominal current regulation threshold voltage, V CR ) thecontroller enters its current regulation mode. At this time, the time-out capacitor, on C TIM pin is charged with a 20μA current source and the controller enters the current limit time to latch-off period. The length of the current limit time to latch-offduration is set by the value of a single external capacitor (see T able 2) for CTIM capacitor value and resulting nominal current limited time out to latch-off duration placed from the CTIM pin (pin 6) to ground. The programmed current level is held until either the OC event passes or the time out period expires. If the former is the case then the N-Channel MOSFET is fully enhanced and the C TIM capacitor isdischarged. Once CTIM charges to 1.87V, signaling that the time out period has expired an internal latch is set whereby the FET gate is quickly pulled to 0V turning off the N-Channel MOSFET switch, isolating the faulty load.This IC responds to a severe overcurrent load (defined as a voltage across the sense resistor >150mV over the OC Vth set point) by immediately driving the N-Channel MOSFET gate to 0V in about 10μs. The gate voltage is then slowly ramped up turning on the N-Channel MOSFET to the programmed current regulation level; this is the start of the time out period.Upon a UV condition the PGOOD signal will pull low when tied high through a resistor to the logic or VDD supply. This pin is a UV fault indicator. For an OC latch off indication, monitor CTIM, pin 6. This pin will rise rapidly from 1.9V to VDD once the time out period expires.See Figures 12 to 16 for waveforms relevant to text.The IC is reset after an OC latch-off condition by a low level on the PWRON pin and is turned on by the PWRON pin being driven high.CURRENT REGULATION DURATION/POWER GOOD C TIM Charging CurrentC TIM _ichg0V CTIM = 0V162023μA C TIM Fault Pull-Up Current (Note 3)-20-mA Current Limit Time-Out Threshold Voltage C TIM _Vth CTIM Voltage 1.3 1.8 2.3V Power Good Pull Down CurrentPG_IpdV OUT = 0.5V-8-mAElectrical SpecificationsV DD = 12V, T A = T J = 0°C to +85°C, Unless Otherwise Specified (Continued)PARAMETERSYMBOLTEST CONDITIONSMINTYPMAX UNITSTABLE 1.R ISET RESISTORNOMINAL OC VTH10k Ω200mV 4.99k Ω100mV 2.5k Ω50mV 750Ω15mVNOTE:Nominal Vth = R ISET x 20μA.TABLE 2.C TIM CAPACITORNOMINAL CURRENT LIMITED PERIOD0.022μF 2ms 0.047μF 4.4ms 0.1μF9.3msNOTE:Nominal time-out period = C TIM x 93k Ω.Application ConsiderationsDuring the soft-start and the time-out delay duration with the IC in its current limit mode, the V GS of the external N-Channel MOSFET is reduced driving the MOSFET switch into a (linear region) high r DS(ON) state. Strike a balance between the CR limit and the timing requirements to avoid periods when the external N-Channel MOSFET s may be damaged or destroyed due to excessive internal power dissipation. Refer to the MOSFET SOA information in the manufacturer’s data sheet.When driving particularly large capacitive loads a longer soft-start time to prevent current regulation upon charging and a short CR time may offer the best application solution relative to reliability and FET MTF.Physical layout of R SENSE resistor is critical to avoid the possibility of false overcurrent occurrences. Ideally, trace routing between the R SENSE resistors and the IC is as direct and as short as possible with zero current in the sense lines (See Figure 1).Using the ISL6116 as a -48V Low Side Hot Swap Power ControllerTo supply the required V DD , it is necessary to maintain the chip supply 10 to 16V above the -48V bus. This may be accomplished with a suitable regulator between the voltage rail and pin 5 (VDD). By using a regulator, the designer may ignore the bus voltage variations. However, a low-costalternative is to use a Zener diode (See Figure 2 for typical 5A load control); this option is detailed below.Note that in this configuration the PGOOD feature (pin 7) is not operational as the I SEN pin voltage is always < UV threshold.See Figures 17 to 20 for waveforms relevant to -48V and other high voltage applications.Biasing the ISL6116Table 3 gives typical component values for biasing the ISL6116 in a ±48V application. The formulas andcalculations deriving these values are also shown below.When using the ISL6116 to control -48V, a Zener diode may be used to provide the +12V bias to the chip. If a Zener is used then a current limit resistor should also be used. Several items must be taken into account when choosing values for the current limit resistor (R CL ) and Zener Diode (DD1):•The variation of the V BUS (in this case, -48V nominal)•The chip supply current needs for all functional conditions •The power rating of R CL .•The current rating of DD1Formulas1.Sizing R CL :R CL = (V BUS,MIN - 12)/I CHIP 2.Power Rating of R CL :P RCL = I C (V BUS,MAX - 12)3.DD1 Current Rating:I DD1 = (V BUS,MAX - 12)/R CLCORRECTTO ISEN ANDCURRENT SENSE RESISTORINCORRECTFIGURE 1.SENSE RESISTOR PCB LAYOUTR ISETTABLE 3.TYPICAL VALUES FOR A -48V HOT SWAPAPPLICATION SYMBOLPARAMETERR CL 1.58k Ω, 1WDD112V Zener Diode, 50mA Reverse CurrentV BUSLOAD12348765ISL6116PWRONNCFIGURE 2.-48VR CL DD112V1.58k Ω1W0.01µF0.047µF1.47k Ω0.0051%0.001µF2k Ω1%ExampleA typical -48V supply may vary from -36 to -72V. Therefore,V BUS,MAX = -72V V BUS,MIN = -36V I CHIP = 15mA (max)Sizing R CL :R CL = (V BUS,MIN - 12)/I C R CL = (36 - 12)/0.015R CL = 1.6k Ω [Typical Value = 1.58k Ω]Power Rating of R CL :P RCL = I C (V BUS,MAX - 12)P RCL = (0.015)(72 - 12)P RCL = 0.9W [Typical Value = 1W]DD1 Current Rating:I DD1 = (VBUS,MAX - 12)/R CL I DD1 = (72 - 12)/1.58k ΩI DD1 = 38mA [Typical Value = 12V rating, 50mA reverse current]Typical Performance CurvesFIGURE 3.VDD BIAS CURRENTFIGURE 4.ISET SOURCE CURRENTFIGURE 5.C TIM CURRENT SOURCEFIGURE 6.C TIM OC VOLTAGE THRESHOLD4.54.03.53.02.52.020305080100TEMPERATURE (°C)5.0S U P P L Y C U R R E N T (m A )104060709020.2TEMPERATURE (°C)I S E T C U R R E N T µA )20305080100104060709020.019.019.219.419.619.820.5020.3220.0019.66C T I M = 0V , C U R R E N T S O U R C E (µA )TEMPERATURE (°C)20305080100104060709019.5020.1619.82C TIM - 0V1.891.881.871.861.851.83C T I M O C V O L T A G E T H R E S H O LD (V )TEMPERATURE (°C)2030508010010406070901.84FIGURE 7.ISL6115/6116 UV THRESHOLD FIGURE 8.ISL6117/6120 UV THRESHOLDFIGURE 9.GATE CHARGE CURRENT FIGURE 10.GATE DRIVE VOLTAGE, VDD = 12VFIGURE 11.POWER ON RESET VOLTAGE THRESHOLD FIGURE 12.ISL6115 +12V TURN-ONTEMPERATURE (°C)I S L 6115, 12V U V T H R E S H O L D (V )203050801001040607090I S L 6116, 5V U V T H R E S H O L D (V )9.769.749.754.374.354.36ISL6116ISL6115TEMPERATURE (°C)I S L 6117, 3.3V U V T H R E S H O L D (V )203050801001040607090I S L 6120, 2.5V U V T H R E S H O L D (V )2.702.651.8601.8501.855ISL61172.60ISL6120TEMPERATURE (°C)203050801001040607090G A T E C H A R G E C U R R E N T (μA )9.69.79.89.910.010.110.217.20017.18317.16617.15017.13317.10012.0011.9911.9811.9711.9611.9511.94TEMPERATURE (°C)I S L 6116,17,20 G A T E D R I V E (V )I S L 6115, G A T E D R I V E (V )20305080100104060709017.116P O W E R O N R E S E T (V )TEMPERATURE (°C)2030508010010406070908.08.58.18.28.38.4VDD LO TO HIVDD HI TO LO5V/DIV. 0.5A/DIV 1ms/DIVGATE VOUTPWRONIOUTPGOODFIGURE 13.ISL6116 +5V TURN-ON FIGURE 14.ISL6115 ‘LOW’ OVERCURRENT RESPONSEFIGURE 15.ISL6115 ‘HIGH’ OVERCURRENT RESPONSE FIGURE 16.ISL6116 ‘HIGH’ OVERCURRENT RESPONSEFIGURE 17.+50V LOW SIDE SWITCHING CGATE = 100pF FIGURE 18.-50V LOW SIDE SWITCHING CGATE = 1000pF2V/DIV 0.5A/DIV 1ms/DIV GATEVOUTPWRONIOUTPGOOD5V/DIV 0.5A/DIV 1ms/DIVCTIMIOUTPGOODVOUTGATE5V/DIV 0.5A/DIV 1ms/DIVIOUTGATECTIMPGOODVOUT 2V/DIV 0.5A/DIV 1ms/DIVIOUTPGOOD CTIMGATEVOUT5ms/DIVVDRAIN 10V/DIV.+50VPWRON 5V/DIV.0V0VVGATE 5V/DIV.IOUT 1A/DIV.5ms/DIVIOUT 1A/DIV.0V0VVGATE 5V/DIV.EN 5V/DIV.-50VVDRAIN 10V/DIV.ISL6115EVAL1 BoardThe ISL6115EVAL1 is configured as a +12V high side switch controller with the CR level set at ~1.5A. (See Figure 21 for ISL6115EVAL1 schematic and Table 4 for BOM). Bias and load connection points are provided along with test points for each IC pin.With the chip to be biased from the +12V bus beingswitched, through B2, GND B5, the load connected between B3 and B4 and with jumper J1 installed the ISL6115 can be evaluated. PWRON pin pulls high enabling the ISL6115 if not driven low.With R2 = 750Ω the CR Vth is set to 15mV and with the 10m Ω sense resistor the ISL6115EVAL1 has a nominal CR level of 1.5A. The 0.047μF delay time to latch-off capacitors results in a nominal 4.4ms before latch-off of outputs after an OC event.Also included with the ISL6115EVAL1 board are one each of the ISL6116, ISL6117 and ISL6120 for evaluation.ISL6116EVAL1 BoardThe ISL6116EVAL1 is default configured as a negative voltage low side switch controller with a ~2.4A CR level. (See Figure 22 for ISL6116EVAL1 schematic and Table 4 for BOM and component description). This basic configuration is capable of controlling both larger positive or negative potential voltages with minimal changes.Bias and load connection points are provided in addition to test points, TP1-8 for each IC pin. The terminals, J1 and J4 are for the bus voltage and return, respectively, with the more negative potential being connected to J4. With the load between terminals J2 and J3 the board is now configured for evaluation. The device is enabled through LOGIN, TP9 with a TTL signal. ISL6116EVAL1 includes a level shifting circuit with an opto-coupling device for the PWRON input so that standard TTL logic can be translated to the -V reference for chip control.When controlling a positive voltage, PWRON can be accessed at TP8.The ISL6116EVAL1 is provided with a high voltage linear regulator for convenience to provide chip bias from ±24V to ±350V. This can be removed and replaced with the zener & resistor bias scheme as discussed earlier. High voltage regulators and power discrete devices are no longer available from Intersil but can be purchased from other semiconductor manufacturers.Reconfiguring the ISL6116EVAL1 board for a higher CR level can be done by changing the R SENSE and R ISET resistor values as the provided FET is 75A rated. Ifevaluation at >60V, an alternate FET must be chosen with an adequate BV DSS .FIGURE 19.+350V LOW SIDE SWITCHING CGATE = 100pF FIGURE 20.+350V LOW SIDE SWITCHING CGATE = 1000pF2ms/DIV+350V0VIOUT 1A/DIVVDRAIN 50V/DIVVGATE 5V/DIVPWRON 5V/DIV2ms/DIV+350V0VIOUT 1A/DIVPWRON 5V/DIVVGATE 5V/DIV.VDRAIN 50V/DIVFIGURE 21.ISL6115EVAL1 HIGH SIDE SWITCH APPLICATIONFIGURE 22.ISL6116EVAL1 NEGATIVE VOLTAGE LOW SIDECONTROLLER56874321ISL6115Q1R2R3C1C2R4D1R5D2JP1V BIAS V+ B2DD1+12VC3R1LOAD -+PWRON 3.3VB1B5B3B4U156874321ISL6116Q2R2R7C1R5D2C3R1LOADDD13.3V+VBUS-VBUSOT1R9R8HI J2J3 LOR6R11R10ONOFF 0-5VU1J1J4PWRONTP8LOGIN TP9R G 1TABLE 4.BILL OF MATERIALS, ISL6115EVAL1, ISL6116EVAL1COMPONENT DESIGNATORCOMPONENT NAMECOMPONENT DESCRIPTIONQ1HUF76132SK811.5m Ω, 30V, 11.5A Logic Level N-Channel Power MOSFET or equiv.Q2HUF7554S3S10m Ω, 80V, 75A N-Channel Power MOSFET or equiv.R1Load Current Sense ResistorDale, WSL-2512 10m Ω 1W Metal Strip ResistorHigh Side R2Overcurrent Voltage Threshold Set Resistor 750Ω 805 Chip Resistor (Vth = 15mV)Low side R2Overcurrent Voltage Threshold Set Resistor 1.21k Ω 805 Chip Resistor (Vth = 24mV)C2Time Delay Set Capacitor 0.047μF 805 Chip Capacitor (4.5ms)C1Gate Timing Capacitor 0.001μF 805 Chip Capacitor (<2ms)C3IC Decoupling Capacitor 0.1μF 805 Chip Capacitor R3Gate Stability Resistor 20Ω 805 Chip Resistor R7Gate to Drain Resistor 2k Ω 805 Chip ResistorJP1Bias Voltage Selection Jumper Install if switched rail voltage is = +12V ±15%. Remove and provide separate +12V bias voltage to U1 via TP5 if ISL6116, ISL6117, ISL6120 being evaluated.R4, R5LED Series Resistors 2.32k Ω 805 Chip Resistor D1, D2Fault Indicating LEDs Low Current Red SMD LEDDD1Fault Voltage Dropping Diode 3.3V Zener Diode, SOT-23 SMD 350mW OT1PWRON Level Shifting Opto-Coupler PS2801-1 NECR8Level Shifting Bias Resistor 2.32k Ω 805 Chip Resistor R9Level Shifting Bias Resistor 1.18k Ω 805 Chip Resistor R10Level Shifting Bias Resistor 200Ω 805 Chip Resistor RG1HIP5600ISHigh Voltage Linear Regulator R6Linear Regulator RF1 1.78k Ω 805 Chip Resistor R11Linear Regulator RF215k Ω 805 Chip ResistorTP1-TP8Test Points for Device Pin Numbers 1-8All Intersil U.S. products are manufactured, assembled and tested utilizing ISO9000 quality systems.Intersil Corporation’s quality certifications can be viewed at /design/qualityIntersil products are sold by description only. Intersil Corporation reserves the right to make changes in circuit design, software and/or specifications at any time without notice. Accordingly, the reader is cautioned to verify that data sheets are current before placing orders. Information furnished by Intersil is believed to be accurate and reliable. However, no responsibility is assumed by Intersil or its subsidiaries for its use; nor for any infringements of patents or other rights of third parties which may result from its use. No license is granted by implication or otherwise under any patent or patent rights of Intersil or its subsidiaries.For information regarding Intersil Corporation and its products, see Small Outline Plastic Packages (SOIC)NOTES:1.Symbols are defined in the “MO Series Symbol List” in Section2.2 of Publication Number 95.2.Dimensioning and tolerancing per ANSI Y14.5M -1982.3.Dimension “D” does not include mold flash, protrusions or gate burrs. Mold flash, protrusion and gate burrs shall not exceed 0.15mm (0.006inch) per side.4.Dimension “E” does not include interlead flash or protrusions. Inter-lead flash and protrusions shall not exceed 0.25mm (0.010 inch) per side.5.The chamfer on the body is optional. If it is not present, a visual index feature must be located within the crosshatched area.6.“L” is the length of terminal for soldering to a substrate.7.“N” is the number of terminal positions.8.Terminal numbers are shown for reference only.9.The lead width “B”, as measured 0.36mm (0.014 inch) or greater above the seating plane, shall not exceed a maximum value of 0.61mm (0.024 inch).10.Controlling dimension:MILLIMETER. Converted inch dimensionsare not necessarily exact.M8.15 (JEDEC MS-012-AA ISSUE C)8 LEAD NARROW BODY SMALL OUTLINE PLASTIC PACKAGESYMBOLINCHESMILLIMETERS NOTESMIN MAX MIN MAX A0.05320.0688 1.35 1.75-A10.00400.00980.100.25-B 0.0130.0200.330.519C 0.00750.00980.190.25-D 0.18900.1968 4.80 5.003E 0.14970.1574 3.80 4.004e 0.050 BSC 1.27 BSC-H0.22840.2440 5.80 6.20-h 0.00990.01960.250.505L 0.0160.0500.401.276N887a0°8°0°8°-Rev. 1 6/05。