热镀锌盐雾腐蚀的机理
盐雾腐蚀原理

盐雾腐蚀原理自然界的盐雾是强电解质,其中NaCl占电解质的77.8%,电导很大,能加速电极反应使阳极活化,加速腐蚀。
盐雾对产品的腐蚀是以电化学方式进行的,其机理是基于原电池腐蚀,腐蚀过程如下:阳极过程腐蚀电池中电位较负的金属为阳极,发生氧化反应。
金属的阳极溶解过程至少由以下几个连续步骤组成:1)金属原子离开晶格转变为表面吸附原子:Me晶格→Me吸附。
2)电位差导致金属氧化,其反应为Me→Men+→ne-。
放出相等数量的电子。
由此而形成的金属离子既可溶液到电解液中,也可以与侵袭介质中的成分发生反应后淀析于金属上。
3)阳极的过程可一直持续到它所生成的电子被阴极耗尽为止。
阴极发生反应:O2+2H2O+4e→4OH-,在中性或碱性介质中被还原成羟基离子。
羟基离子又可与金属离子发生反应,而在酸性介质中氢离子通过形成游离氢得到还原,氢则作为气体逸出。
4)在电解液中,氯化钠离解成为钠离子和氯离子,部分氯离子、金属离子和氢氧根离子反应生成金属腐蚀物:2nMe++2nCl+2nOH→nMeCl+nMe(OH).盐雾腐蚀的三要素是水、氧和离子。
涂层是一种高聚物薄膜,能不同程度地阻缓上述三要素的通过而发挥腐作用。
一般情况下,只要水中盐的浓度在0.4mol/L以上,钠与氯离子就可以穿过涂膜扩散,因此在喷盐雾的情况下,上述阳极和阴极反应是不能抑制的:离子透过漆膜比水和氧要慢得多,漆膜所含的羟基离解后使其带负电,因而会选择性地吸收阳离子透入漆膜,经研究证实,一般漆膜会大量吸收阳离子(如Na+)透入漆膜,而阴离子(如Cl-)则不易透入。
离子透入漆膜的结果是使漆膜起泡、脱落。
如果被同一种液体浸润的两种不同金属互相电接触,则阴极过程发生在较贵重的金属上,而阳极过程则发生在“较贱的材料”上。
盐雾的腐蚀原理
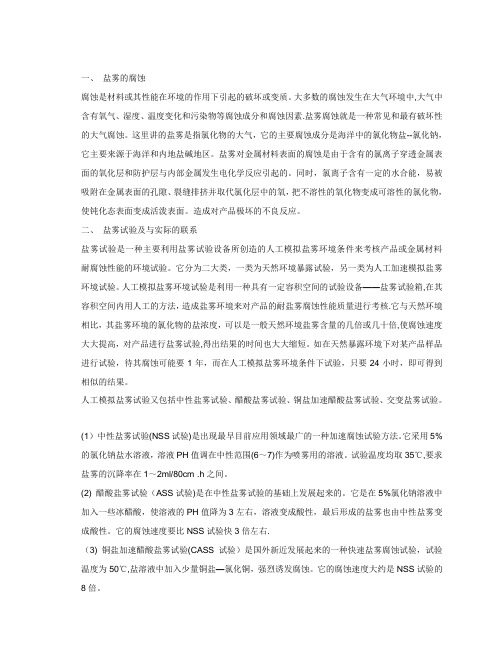
一、盐雾的腐蚀腐蚀是材料或其性能在环境的作用下引起的破坏或变质。
大多数的腐蚀发生在大气环境中,大气中含有氧气、湿度、温度变化和污染物等腐蚀成分和腐蚀因素.盐雾腐蚀就是一种常见和最有破坏性的大气腐蚀。
这里讲的盐雾是指氯化物的大气,它的主要腐蚀成分是海洋中的氯化物盐--氯化钠,它主要来源于海洋和内地盐碱地区。
盐雾对金属材料表面的腐蚀是由于含有的氯离子穿透金属表面的氧化层和防护层与内部金属发生电化学反应引起的。
同时,氯离子含有一定的水合能,易被吸附在金属表面的孔隙、裂缝排挤并取代氯化层中的氧,把不溶性的氧化物变成可溶性的氯化物,使钝化态表面变成活泼表面。
造成对产品极坏的不良反应。
二、盐雾试验及与实际的联系盐雾试验是一种主要利用盐雾试验设备所创造的人工模拟盐雾环境条件来考核产品或金属材料耐腐蚀性能的环境试验。
它分为二大类,一类为天然环境暴露试验,另一类为人工加速模拟盐雾环境试验。
人工模拟盐雾环境试验是利用一种具有一定容积空间的试验设备——盐雾试验箱,在其容积空间内用人工的方法,造成盐雾环境来对产品的耐盐雾腐蚀性能质量进行考核.它与天然环境相比,其盐雾环境的氯化物的盐浓度,可以是一般天然环境盐雾含量的几倍或几十倍,使腐蚀速度大大提高,对产品进行盐雾试验,得出结果的时间也大大缩短。
如在天然暴露环境下对某产品样品进行试验,待其腐蚀可能要1年,而在人工模拟盐雾环境条件下试验,只要24小时,即可得到相似的结果。
人工模拟盐雾试验又包括中性盐雾试验、醋酸盐雾试验、铜盐加速醋酸盐雾试验、交变盐雾试验。
(1)中性盐雾试验(NSS试验)是出现最早目前应用领域最广的一种加速腐蚀试验方法。
它采用5%的氯化钠盐水溶液,溶液PH值调在中性范围(6~7)作为喷雾用的溶液。
试验温度均取35℃,要求盐雾的沉降率在1~2ml/80cm².h之间。
(2) 醋酸盐雾试验(ASS试验)是在中性盐雾试验的基础上发展起来的。
它是在5%氯化钠溶液中加入一些冰醋酸,使溶液的PH值降为3左右,溶液变成酸性,最后形成的盐雾也由中性盐雾变成酸性。
热镀锌盐雾试验
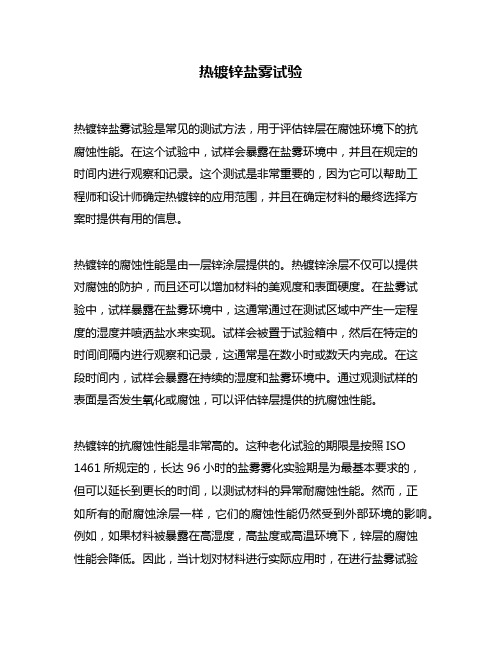
热镀锌盐雾试验热镀锌盐雾试验是常见的测试方法,用于评估锌层在腐蚀环境下的抗腐蚀性能。
在这个试验中,试样会暴露在盐雾环境中,并且在规定的时间内进行观察和记录。
这个测试是非常重要的,因为它可以帮助工程师和设计师确定热镀锌的应用范围,并且在确定材料的最终选择方案时提供有用的信息。
热镀锌的腐蚀性能是由一层锌涂层提供的。
热镀锌涂层不仅可以提供对腐蚀的防护,而且还可以增加材料的美观度和表面硬度。
在盐雾试验中,试样暴露在盐雾环境中,这通常通过在测试区域中产生一定程度的湿度并喷洒盐水来实现。
试样会被置于试验箱中,然后在特定的时间间隔内进行观察和记录,这通常是在数小时或数天内完成。
在这段时间内,试样会暴露在持续的湿度和盐雾环境中。
通过观测试样的表面是否发生氧化或腐蚀,可以评估锌层提供的抗腐蚀性能。
热镀锌的抗腐蚀性能是非常高的。
这种老化试验的期限是按照ISO 1461所规定的,长达96小时的盐雾雾化实验期是为最基本要求的,但可以延长到更长的时间,以测试材料的异常耐腐蚀性能。
然而,正如所有的耐腐蚀涂层一样,它们的腐蚀性能仍然受到外部环境的影响。
例如,如果材料被暴露在高湿度,高盐度或高温环境下,锌层的腐蚀性能会降低。
因此,当计划对材料进行实际应用时,在进行盐雾试验时应该考虑多种因素和环境因素。
总之,热镀锌盐雾试验是一种有效的测试方法,可以帮助工程师和设计师确定材料的最终选择方案。
这个测试不仅可以评估热镀锌涂层的耐腐蚀性能,而且可以提供有用的数据,并为计划进行实际应用的过程提供必要的信息。
但我们需要注意,外部环境的多种因素和条件会影响材料表面的腐蚀性能,因此需要综合多种因素考虑材料的实际应用情况。
热镀锌厚度和盐雾时间对应_概述说明以及解释

热镀锌厚度和盐雾时间对应概述说明以及解释1. 引言1.1 概述热镀锌作为一种常用的防腐蚀技术,在许多工业领域都有广泛应用。
热镀锌处理可以有效地增加金属表面的耐腐蚀性能,并延长其使用寿命。
然而,热镀锌的厚度与材料的耐腐蚀性能之间存在一定的关联,特别是在充满盐分和潮湿环境中。
因此,我们有必要了解热镀锌厚度与盐雾时间之间的对应关系,以更好地评估材料在恶劣环境中的稳定性。
1.2 文章结构本文将按照以下结构组织内容:首先,在第二部分将介绍热镀锌工艺,并探讨热镀锌厚度与耐腐蚀性能之间的关联。
随后,在第三部分将详细介绍我们进行的实验研究,包括实验设计、材料准备以及实验过程。
在第四部分,我们将解释和讨论实验结果,并探讨可能影响热镀锌厚度与盐雾时间对应关系的因素。
最后,在第五部分,我们将总结结果并提出对未来进一步研究方向的建议和展望。
1.3 目的本文旨在通过实验研究,探讨热镀锌厚度与盐雾时间之间的对应关系,并解释其中的机理。
通过了解这一关联性,我们可以更好地评估热镀锌材料在恶劣环境中的耐久性,并为相关工业应用提供指导和建议。
同时,本文还将提供一些可能存在的误差和限制条件分析,以及对未来进一步研究方向的展望。
2. 热镀锌厚度和盐雾时间的相关性:2.1 热镀锌工艺简介:热镀锌是一种常用的金属防腐方法,通过将基材浸入熔融的锌中,形成一层锌铁合金覆盖在基材表面。
这种覆盖层能够有效地保护基材免受腐蚀和氧化。
2.2 热镀锌厚度与耐腐蚀性能的关系:热镀锌厚度是决定其耐腐蚀性能的重要因素之一。
通常情况下,较厚的热镀锌层会提供更好的保护效果,并能延长基材的寿命。
这是因为厚度较大的热镀锌层具有更高的耐侵蚀和阻挡湿气渗透的能力。
2.3 盐雾测试方法简介:盐雾测试是评估金属表面耐腐蚀性能常用的实验方法之一。
该方法通过在特定条件下制造含有各种浓度盐水喷雾环境,模拟真实环境下金属遭受海洋或工业大气环境腐蚀的情况。
在盐雾测试中,将样品暴露在盐雾环境中一定的时间,然后观察和记录其表面的腐蚀情况。
盐雾腐蚀铜机理

盐雾腐蚀铜机理
盐雾腐蚀是指金属受到潮湿空气中盐分(尤其是氯离子)侵蚀的一种腐蚀形式。
当铜表面暴露在富含盐分的潮湿气氛中时,水分中的氧气和氯离子可能与铜反应,形成氧化铜和氯化铜等化合物,导致铜表面的腐蚀。
这种腐蚀过程通常被称为盐雾腐蚀,尤其是在海洋环境或者含有盐的工业大气环境中尤为常见。
盐雾腐蚀铜的主要机理可以简要概括如下:
1. 氯离子/氧气的作用:盐雾中的氯离子对铜具有氧化作用,形成氧化铜。
氧气可以促进氯化铜在铜表面腐蚀的过程。
2. 腐蚀产物:盐雾会导致铜表面形成氯化铜和氧化铜等化合物,这些物质会进一步破坏铜材料的表面结构。
3. 导电性:氯化铜等腐蚀产物可能会提高铜的电导率,同时降低其化学活性,对铜材料的性能造成负面影响。
盐雾腐蚀不仅对铜材料的外观造成损害,还可能降低其
机械性能和导电性能。
由于盐雾腐蚀造成的损害一般为表面腐蚀,因此通常采用表面处理方法(如电镀、涂覆防护层等)来减轻盐雾腐蚀对铜材料的影响。
热镀锌层腐蚀效率

热镀锌层腐蚀效率摘要:一、热镀锌层的概述二、热镀锌层腐蚀的原因三、热镀锌层腐蚀的影响因素四、提高热镀锌层腐蚀效率的方法五、总结正文:热镀锌层是一种广泛应用于钢材防腐的金属涂层,具有优异的耐腐蚀性能。
然而,在实际应用过程中,由于各种原因,热镀锌层的腐蚀效率并不总是能达到预期效果。
本文将对热镀锌层腐蚀效率的相关问题进行探讨。
首先,我们需要了解热镀锌层的概述。
热镀锌层是由锌在高温下镀在钢材表面形成的一种金属涂层。
它具有优良的耐腐蚀性能,主要原因是锌在空气中会发生电化学反应,形成致密的氧化锌保护膜,从而阻止内部金属继续被腐蚀。
接下来,我们来探讨热镀锌层腐蚀的原因。
热镀锌层的腐蚀主要是由内部应力和外部环境共同作用导致的。
内部应力主要包括热应力和冷应力,这些应力可能导致涂层出现裂纹,从而降低其抗腐蚀性能。
外部环境主要包括湿度、温度、大气污染物等,这些因素会影响涂层的氧化锌保护膜的形成和稳定性。
再来分析影响热镀锌层腐蚀效率的因素。
首先是钢材表面处理,如除油、除锈等,这些处理方法会影响热镀锌层的附着力和稳定性。
其次是热镀锌过程的控制,如温度、电流、时间等参数,这些因素会影响热镀锌层的结构和性能。
最后是涂层的维护保养,如定期检查、清洗、涂覆保护剂等,这些措施可以延长热镀锌层的寿命。
针对以上问题,我们可以采取一些方法提高热镀锌层的腐蚀效率。
首先,选择优质的钢材和合适的表面处理方法,以提高热镀锌层的附着力。
其次,优化热镀锌过程的参数,确保热镀锌层的质量和性能。
最后,加强涂层的维护保养,及时发现并处理潜在问题,延长热镀锌层的使用寿命。
总之,热镀锌层腐蚀效率的问题是影响钢材防腐效果的重要因素。
要提高热镀锌层的腐蚀效率,需要从钢材表面处理、热镀锌过程控制和涂层维护保养等方面进行综合考虑和改进。
盐雾生锈原理

盐雾生锈原理
盐雾生锈是一种常见的金属腐蚀现象,特别是在接触海洋环境的金属结构上更为突出。
其实,盐雾生锈是由多种因素共同作用导致的。
主要包括以下几个方面:
1. 盐水中的离子
盐雾中的盐水中溶解了大量的氯化物离子,这些离子可以极大地加速金属的腐蚀进程。
当金属表面处于高湿度的盐雾环境中,盐水中的离子会与金属表面上的氧气发生反应,形成氯化物,进一步腐蚀金属表面。
2. 金属表面的缺陷
金属在制造、运输和安装过程中会留下许多微小的缺陷,如裂纹、疤痕等。
这些缺陷会成为盐雾腐蚀的起点,使金属表面更容易受到盐雾的侵蚀。
3. 电化学反应
在盐水的环境中,金属表面、盐水和空气组成了一个电池系统,金属表面的阳极和阴极之间形成了电化学反应。
盐雾中的盐水溶解了金属表面的阳极部分,导致金属逐渐溶解并产生锈蚀。
4. 氧化还原反应
金属表面的氧化还原反应也是盐雾腐蚀的一个重要原因。
当金属表面暴露在含氧气的盐水中时,金属会发生氧化反应,形成氧化物,加速金属的腐蚀过程。
在海洋环境中,盐雾对金属结构的腐蚀是一个严重的问题,因此在设计和制造金属结构时,需要考虑采取防护措施。
例如,使用防腐涂层、选择耐腐蚀金属、定期维护等方法都可以延缓金属结构被盐雾腐蚀的速度,提高金属结构的使用寿命。
盐雾生锈是一个复杂的物理化学过程,理解其腐蚀原理和采取有效防护措施是保护金属结构的关键。
通过科学的防护设计和有效的维护管理,可以有效延缓金属结构的腐蚀速度,减少损坏,保护金属结构的安全性和稳定性。
盐雾试验原理
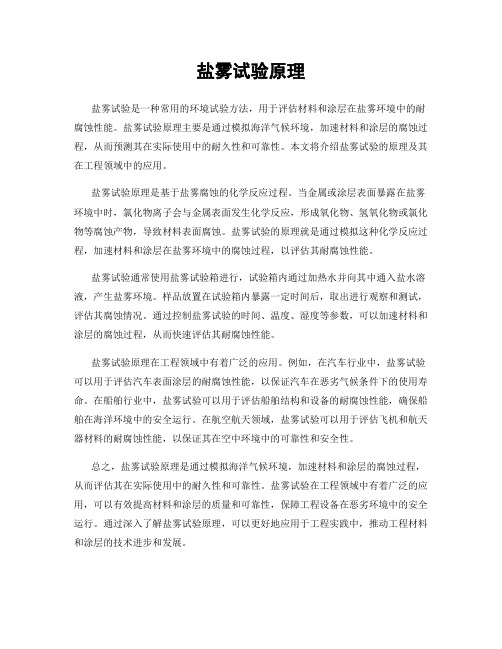
盐雾试验原理盐雾试验是一种常用的环境试验方法,用于评估材料和涂层在盐雾环境中的耐腐蚀性能。
盐雾试验原理主要是通过模拟海洋气候环境,加速材料和涂层的腐蚀过程,从而预测其在实际使用中的耐久性和可靠性。
本文将介绍盐雾试验的原理及其在工程领域中的应用。
盐雾试验原理是基于盐雾腐蚀的化学反应过程。
当金属或涂层表面暴露在盐雾环境中时,氯化物离子会与金属表面发生化学反应,形成氧化物、氢氧化物或氯化物等腐蚀产物,导致材料表面腐蚀。
盐雾试验的原理就是通过模拟这种化学反应过程,加速材料和涂层在盐雾环境中的腐蚀过程,以评估其耐腐蚀性能。
盐雾试验通常使用盐雾试验箱进行,试验箱内通过加热水并向其中通入盐水溶液,产生盐雾环境。
样品放置在试验箱内暴露一定时间后,取出进行观察和测试,评估其腐蚀情况。
通过控制盐雾试验的时间、温度、湿度等参数,可以加速材料和涂层的腐蚀过程,从而快速评估其耐腐蚀性能。
盐雾试验原理在工程领域中有着广泛的应用。
例如,在汽车行业中,盐雾试验可以用于评估汽车表面涂层的耐腐蚀性能,以保证汽车在恶劣气候条件下的使用寿命。
在船舶行业中,盐雾试验可以用于评估船舶结构和设备的耐腐蚀性能,确保船舶在海洋环境中的安全运行。
在航空航天领域,盐雾试验可以用于评估飞机和航天器材料的耐腐蚀性能,以保证其在空中环境中的可靠性和安全性。
总之,盐雾试验原理是通过模拟海洋气候环境,加速材料和涂层的腐蚀过程,从而评估其在实际使用中的耐久性和可靠性。
盐雾试验在工程领域中有着广泛的应用,可以有效提高材料和涂层的质量和可靠性,保障工程设备在恶劣环境中的安全运行。
通过深入了解盐雾试验原理,可以更好地应用于工程实践中,推动工程材料和涂层的技术进步和发展。
盐雾腐蚀原理

盐雾腐蚀原理
盐雾腐蚀是一种常见的金属腐蚀现象,主要发生在海洋环境或者含有较高盐分的地区。
具体原理如下:
1. 盐雾气候条件:盐雾腐蚀主要发生在海洋环境中,其中含有丰富的盐分。
当海水蒸发时,会释放出氯化物和其他盐类物质。
这些盐类化合物在悬浮在空气中形成的微粒中,形成盐雾。
2. 盐雾蒸发过程:当盐雾接触到金属表面时,盐分中的氯化物离子与金属表面的氧气发生反应,形成氯气。
氯气是具有强氧化性的物质,可以与金属表面上的电子结合,造成金属离子的脱落。
3. 金属腐蚀过程:在盐雾的作用下,金属表面被腐蚀,形成金属离子和氯离子。
金属离子可以进一步与盐雾中的其他离子形成溶解的盐类物质。
这种腐蚀过程会不断进行,导致金属表面的损坏和腐蚀。
4. 影响因素:盐雾腐蚀速度受多种因素影响,包括盐分浓度、腐蚀环境中湿度和温度的变化,以及金属表面的处理状态(如是否存在腐蚀保护涂层)等。
在湿度高、温度较高、盐分浓度较大的环境下,盐雾腐蚀速度会更快。
盐雾腐蚀对金属材料的损害是普遍存在的,对于一些采用金属结构的设备、工具和建筑物来说,采取腐蚀保护措施是非常重要的。
常见的腐蚀保护方法包括使用耐腐蚀性能较好的金属、
涂覆腐蚀保护层、采用阴极保护等。
这些措施可以有效延长金属材料的使用寿命,并减少因盐雾腐蚀而导致的经济损失。
盐雾对金属的腐蚀性

盐雾对金属的腐蚀性
简介
盐雾腐蚀是指在高含盐度湿度环境下,由于海水的蒸发会使空气中含有大量盐
分颗粒,这些盐分颗粒能够促进金属表面的氧化反应,从而引起金属的腐蚀。
盐雾对金属的腐蚀性是一种普遍的现象,尤其是在海洋环境和持续暴露在碱性土壤或化学处理过的水中的金属上。
盐雾对金属的腐蚀机理
1.盐雾环境中的氯化物和硫化物等盐分颗粒能够吸附在金属表面,形成
电化学腐蚀的催化剂。
2.盐雾中的水分能够形成电解质溶液,使金属表面形成阳极和阴极,引
发电化学腐蚀反应。
3.盐雾中的氧气和水能够与金属表面形成氧化物,形成金属的氧化腐蚀。
盐雾对不同金属的腐蚀性
1.铁:盐雾对铁的腐蚀性强,会形成铁锈,加速金属的锈蚀速度。
2.铝:盐雾下的铝会形成氧化层,抑制金属进一步腐蚀,但长期暴露下
还是会受到一定腐蚀影响。
3.不锈钢:盐雾对不锈钢的腐蚀性较低,但时间较长下仍会导致表面锈
斑。
盐雾腐蚀的预防方法
1.选择适当的金属材料:在盐雾环境下使用不锈钢等耐蚀性强的金属能
有效减缓腐蚀速度。
2.表面处理:采用镀锌、喷涂防护层等方法对金属表面进行处理,增加
金属的耐蚀性。
3.增加防护:使用防护罩、油漆覆盖等措施保护金属不暴露在盐雾环境
下。
在实际应用中,了解盐雾对金属的腐蚀性能及腐蚀机理,采取有效的预防措施,能够延长金属的使用寿命,减少维护成本,保护设备和结构的安全可靠性。
盐雾试验系列2--盐雾试验的腐蚀机理

盐雾试验的腐蚀机理
盐雾腐蚀是电化学腐蚀,是导电的盐溶液渗入金属内部发生电化学反应,形成“低电位金属一电解质溶液一高电位杂质”的微电池系统,发生电子转移,作为阳极的金属出现溶解,形成新的化合物,即腐蚀物。
海水的主要成分是氯化钠,大约占77.8%。
氯化钠是一种强电解质,极易潮解并在水中完全电离,电解为Cl-离子和Na+离子。
盐雾腐蚀破坏过程中起主要作用的是氯离子Cl-,其半径很小,只有1.81×10-10m,其具有很强的穿透能力,容易穿透金属氧化层和防护层进入金属内部,与里面的金属元素发生电化学反应,破坏金属的钝态,对金属材料造成腐蚀。
同时,氯离子具有一定的水合能,吸附性很强,容易吸附在金属表面的孔隙、裂缝等部位,取代保护金属氧化层中的氧,把不溶性的氧化物变成可溶性的氯化物,使钝化态表面变成活泼表面,从而对产品造成腐蚀。
Cl-、Me+(金属离子)和OH-发生反应后形成金属腐蚀物,反应方程式为:
2nMe++2n Cl-+2n OH-→n MeCl+n Me (OH)
当盐雾沉降到金属表面时,由于水汽的作用,形成一层将整个金属包围的盐水膜,金属表面就相当于浸在氯化钠溶液中,使金属表面构成原电池的两个极,引起电化学反应产生腐蚀。
因此,盐雾对金属材料的腐蚀就是因氯离子穿透金属表面的覆盖层与内部金属发生电化学反应。
注释:铁锈主要由三氧化二铁水合物Fe₂O₂·nH₂O和氢氧化铁(FeO(OH), Fe(OH)₂)组成。
热镀锌盐雾试验

热镀锌盐雾试验
热镀锌是一种常见的防腐处理方法,它可以有效地防止金属材料在潮湿环境下的腐蚀。
然而,即使经过热镀锌处理的金属材料也可能会在恶劣的环境下发生腐蚀。
为了测试热镀锌的防腐性能,盐雾试验被广泛应用。
盐雾试验是一种模拟海洋环境的腐蚀试验方法。
在盐雾试验中,将金属样品放置在盐水喷雾室中,通过喷洒盐水来模拟海洋环境中的腐蚀作用。
在试验过程中,可以通过观察样品的腐蚀情况来评估其防腐性能。
对于热镀锌材料来说,盐雾试验是一种非常有效的测试方法。
热镀锌材料在盐雾环境下的腐蚀速度比普通钢材要慢得多,这是因为锌具有良好的防腐性能。
在盐雾试验中,热镀锌材料的腐蚀速度通常比普通钢材要慢得多,这表明热镀锌材料具有更好的防腐性能。
然而,即使经过热镀锌处理的材料也可能会在盐雾环境下发生腐蚀。
这是因为热镀锌层可能会受到损伤,从而暴露出下面的钢材。
如果钢材没有得到适当的防腐处理,它就会在盐雾环境下迅速腐蚀。
因此,在进行盐雾试验时,需要注意以下几点:
1. 样品的表面应该保持干燥和清洁,以避免表面污染对试验结果的影响。
2. 样品的热镀锌层应该均匀且完整,以确保试验结果的准确性。
3. 在试验过程中,应该定期检查样品的腐蚀情况,并记录下来以便后续分析。
盐雾试验是一种非常有效的测试方法,可以用于评估热镀锌材料的防腐性能。
通过合理的试验设计和操作,可以得到准确的试验结果,并为热镀锌材料的应用提供重要的参考依据。
盐雾时间对镀锌镍合金的影响

盐雾时间对镀锌镍合金的影响盐雾时间对镀锌镍合金的影响一、引言在工业生产和海洋环境中,金属材料常常需要面对盐雾腐蚀的威胁。
镀锌镍合金作为一种常用的防腐材料,其抗盐雾腐蚀性能备受关注。
本文将探讨盐雾时间对镀锌镍合金的影响,以此帮助读者更深入地理解该材料的特性和应用潜力。
二、盐雾腐蚀的机理盐雾腐蚀是指金属材料在盐雾环境中,由于氧化、还原、溶解等电化学反应的作用,导致材料表面出现腐蚀现象的过程。
在盐雾环境下,氯离子等盐类溶液会使得金属表面形成致密的氧化物或氯化物保护层,从而起到一定程度的抗腐蚀作用。
然而,盐雾时间的延长也会加剧镀锌镍合金的腐蚀程度,因为盐雾中的氯离子和其他腐蚀性物质会逐渐渗透到保护层内部,破坏其稳定性。
三、盐雾时间对镀锌镍合金的影响1. 表面腐蚀程度增加:随着盐雾时间的延长,镀锌镍合金表面的腐蚀程度会逐渐增加。
盐雾中的酸性物质会破坏保护层,使得金属表面直接暴露在盐雾环境下,从而加速腐蚀的发生。
2. 材料性能退化:盐雾腐蚀会导致镀锌镍合金的力学性能和化学性能逐渐下降。
腐蚀会使得金属晶界发生脆化、孔洞和裂纹的形成,从而引起材料的强度降低、硬度减小等不良变化。
3. 耐腐蚀性能下降:盐雾时间的延长也会使得镀锌镍合金的耐腐蚀性能下降。
盐雾腐蚀会导致材料表面形成更多的缺陷和孔洞,从而增加了腐蚀介质对材料的侵蚀程度。
4. 结构演化:随着盐雾时间的增加,镀锌镍合金的晶体结构也会发生演化。
晶体的取向、大小和形貌等特征可能会发生变化,进而影响材料的力学和化学性能。
四、我的观点和理解在我的观点和理解中,盐雾时间对镀锌镍合金的影响是显著的。
随着盐雾时间的延长,该材料的抗腐蚀性能逐渐降低,表面腐蚀程度增加,材料性能退化,耐腐蚀性能下降,以及结构发生演化等问题凸显。
在实际应用中,我们需对盐雾时间进行控制,以避免镀锌镍合金遭受严重的腐蚀损害。
五、总结本文探讨了盐雾时间对镀锌镍合金的影响。
随着盐雾时间的延长,金属表面的腐蚀程度增加,材料性能退化,耐腐蚀性能下降,以及结构演化等问题不可忽视。
盐雾试验的原理

盐雾试验的原理
盐雾试验是一种常见的腐蚀性试验方法,用于评估材料和涂层的耐蚀性能。
它模拟了海洋环境中的盐雾腐蚀情况,通过暴露样品在盐水雾化环境中,观察其腐蚀和腐蚀速率,以评估材料的抗腐蚀能力。
盐雾试验的原理主要是利用盐水溶液雾化成盐雾,并将其暴露在样品表面,通过模拟海洋环境中的腐蚀条件,来评估材料的抗腐蚀能力。
盐雾试验的具体原理主要包括以下几个方面:
1. 模拟海洋环境:盐雾试验的原理是通过将盐水溶液雾化成盐雾,暴露在样品表面,模拟海洋环境中的腐蚀条件。
海洋环境中的盐雾含有大量的氯化物离子,对金属材料和涂层具有较强的腐蚀作用,因此盐雾试验可以有效地模拟海洋环境中的腐蚀情况。
2. 加速腐蚀过程:盐雾试验的原理是利用盐水溶液雾化成盐雾,并将其暴露在样品表面,加速腐蚀过程。
盐雾试验中暴露的时间通常较短,但由于盐雾中含有大量氯化物离子,可以加速材料表面的腐蚀速率,从而在短时间内评估材料的抗腐蚀能力。
3. 评估材料耐蚀性能:盐雾试验的原理是通过暴露样品在盐水雾化环境中,观察其腐蚀程度和腐蚀速率,以评估材料的抗腐蚀能力。
通过测量样品的腐蚀程度、腐蚀面积和腐蚀深度等指标,可以客观地评估材料的抗腐蚀性能,为材料的选择
和设计提供参考依据。
总的来说,盐雾试验的原理是通过模拟海洋环境中的盐雾腐蚀条件,加速材料腐蚀过程,评估材料的耐蚀性能。
通过这种方式,可以有效地检测材料的抗腐蚀能力,为材料的选择和设计提供科学依据。
盐雾试验已经成为了广泛应用于材料科学和工程领域的一种重要腐蚀性试验方法。
镀锌件盐雾原因及对策

镀锌件盐雾原因及对策
1镀锌件盐雾及其原因
镀锌件是目前行业部件中应用最为广泛的一种表面处理工艺,镀锌工程广泛应用在农业机械、汽车零部件和家用电器等行业中。
但是在镀锌加工过程中,由于受到外界环境的影响,容易出现件表面出现一层“盐雾”的现象,使镀锌质量受到影响。
镀锌件盐雾的原因是:首先,因为人为污染源发出的二氧化硫、氯气、氯氛等硫族化合物。
其次,在镀锌加工过程中,进去水中含有一定的盐离子,对镀层的腐蚀能力有一定的影响。
最后,为了保证镀锌件的表面光洁度,镀前需要进行水洗,并且镀锌液中也包含有少量的离子,这些都会对镀锌件表面的质量产生不利影响,使其出现盐雾的现象。
2镀锌件盐雾的防治
针对以上原因,下面就可以采取相应的对策来控制盐雾产生:首先,要加强对污染源的监控,有效抑制人为污染源发出的硫族化合物、硝酸盐和氯化物等有害物质出现;其次,应采用合理的镀前处理工艺,降低加工水中的盐离子的含量;最后,加大镀锌前的表面清洗、抛光工作,延长镀锌液的使用寿命,并且及时更换污染较严重的镀锌槽。
另外,在生产过程中,将装配镀锌件的工作放置在盐雾较少的室内环境中进行,以减少外界环境对镀锌件表面的影响,从而有效防治出现盐雾现象。
以上就是针对镀锌件出现盐雾的原因及其防治措施,只有严格按照要求来处理,才能保证镀锌件的质量。
热镀锌钢盐雾腐蚀行为及机理研究

暋2021年8月 暋暋暋暋暋暋暋暋 暋暋暋JournalofShaanxiUniversityofScience& Technology暋暋 暋暋暋暋暋Aug.2021
摘 暋 要 :通 过 研 究 中 性 盐 雾 腐 蚀 研 究 热 镀 锌 钢 的 腐 蚀 行 为 ,明 确 不 同 时 间 周 期 下 热 镀 锌 钢 的 腐 蚀过程及腐蚀机理.模拟中性盐雾加速试验,通 过 失 重 法、SEM、XRD 以 及 拉 曼 光 谱 等 分 析 方 法 ,对 比 不 同 腐 蚀 周 期 对 热 镀 锌 钢 腐 蚀 行 为 的 影 响 .结 果 表 明 :随 着 腐 蚀 周 期 的 增 长 ,热 镀 锌 钢 的 腐 蚀 速 度 呈 现 出 逐 步 增 大 并 最 终 趋 于 平 稳 的 状 态 .腐 蚀 过 程 中 ,腐 蚀 表 面 首 先 出 现 白 色 和 浅 黄色锈迹,随着腐蚀的加剧,腐蚀表面逐渐出现褐红 色 以 及 黑 色 锈 迹,腐 蚀 层 也 逐 渐 由 较 为 致 密转变为蓬松、开裂、剥落,腐蚀产物主要以 ZnCl2、Zn(OH)2、毭-FeOOH、Fe3O4 以及 Fe2O3 为主.热镀锌钢30天的腐蚀过程主要可以分为 三 个 阶 段,分 别 为:镀 锌 层 的 保 护 阶 段,镀 锌 层 的破损阶段以及镀锌层的失效阶段.其中,以镀锌层 的 破 损 阶 段 腐 蚀 速 率 为 最 高,该 阶 段 腐 蚀 产物以黄锈(毭-FeOOH)和红褐色锈(Fe2O3、Fe(OH)3)为主,腐 蚀 产 物 蓬 松,且 出 现 裂 纹,为 下一步的腐蚀提供通道.随着腐蚀周期的增加,碳钢 基 体 逐 渐 暴 露,此 时 腐 蚀 速 率 下 降 且 趋 于 平 稳 ,腐 蚀 产 物 以 红 褐 色 锈 及 黑 锈 (Fe3O4)为 主 ,腐 蚀 产 物 蓬 松 易 脱 落 . 关 键 词 :热 镀 锌 ;中 性 盐 雾 试 验 ;加 速 腐 蚀 试 验 ;湿 热 试 验 中 图 分 类 号 :TG172.3暋 暋 暋 暋 文 献 标 志 码 :A
人造气氛腐蚀试验——盐雾试验揭秘

人造气氛腐蚀试验——盐雾试验揭秘做镀锌板的朋友一定对“盐雾试验”这个词不陌生,并且可能还深受折磨,对其恨之入骨。
今天小编就来说说盐雾试验,让各位以后不再“谈盐色变”!1、为什么要做盐雾试验?昔日曹孟德曰“神龟虽寿,犹有竟时”,就是说王八虽然寿命很长,但总归有挂掉的那天。
钢铁虽然寿命比王八还长,但一样摆脱不掉生老病死的自然规律(别说钢铁了,宇宙还有灭亡的那一天呢)。
钢铁的死亡,叫做失效。
失效的形式多种多样,三大基本形式是断裂、腐蚀和磨损。
盐雾试验,就跟腐蚀有千丝万缕的关系。
为了在选材时能够选出适合设计使用期限的材料,就必须要对材料的寿命进行预测。
在实际项目中,一旦选定并且使用了某种材料,就几乎不可能再中途更改,因此选材前的评价工作就更加重要。
然而钢铁的预期使用寿命一般都很长,如何从腐蚀的角度选择合适的材料呢?实验室的加速腐蚀试验应运而生,盐雾试验就是其中一种。
盐雾试验通过将试件置于一般含氯化钠溶液的细雾之中,有时也改用其他化学物质(欧冶知钢小程序的百科中也有相关介绍,可自行查阅),从而对不同材料的服役预期进行比较。
2、盐雾试验分类对于盐雾试验的要求,我国已制定出比较全面的标准方法。
其中《GB/T 10125-2012 人造气氛腐蚀试验盐雾试验》是一份综合性标准,包含了所有三种盐雾试验,即中性盐雾(NSS)、醋酸盐雾(ASS)和铜加速醋酸盆雾(CASS)试验。
这三种盐雾试验的具体操作方法在这不再赘述,但是他们的适用对象有必要提一下,在《GB/T 10125-2012》的正文部分中有提及:(1)中性盐雾试验适用于:—金属及其合金;—金属覆盖层(阳极性或阴极性);—转化膜;—阳极氧化膜;—金属基体上的有机涂层。
(2)乙酸盐雾试验适用于铜+镍+铬或镍+铬装饰性镀层,也适用于铝的阳极氧化膜。
(3)铜加速乙酸盐雾试验适用于铜+镍+铬或镍+铬装饰性镀层,也适用于铝的阳极氧化膜。
另外,《GB/T 10125-2012》的引言也有必要提醒一下:3、三种盐雾试验方法的优缺点(1)中性盐雾试验适用对象最为广泛,像咱们钢贸商平时接触的镀锌板,也是用中性盐雾试验评价较为合适。
热镀锌盐雾腐蚀的机理

随着汽车工业的发展,汽车用热镀锌钢板的国产化程度不断提高,轿车的发展对热镀锌板的质量、品种和规格提出了更高的要求。
热镀锌板由于使用需要,长期以及Cl-等的腐蚀,影响产品质量,暴露于大气中,易于受到大气中潮湿气、SO2、固缩短产品的使用寿命。
在沿海城市及重工业地区,由于同时受到ph值、NO3体颗粒等影响,热镀锌板的腐蚀速率也会加快,对其耐腐蚀性能提出了更高的要求。
热镀锌板在盐雾实验中,表面锌层首先被腐蚀,腐蚀产物比较疏松,呈白色絮状覆盖在钢板表面,称之为“白锈”。
随着盐雾喷淋时间的延长,镀层逐渐被腐蚀殆尽,随后基板开始腐蚀,腐蚀产物为红色,称之为“红锈”。
由此可见,镀层的厚度与组成是决定红锈产生时间,即镀层腐蚀完毕、基板开始腐蚀所需时间的决定因素。
本章通过盐雾腐蚀实验和电化学实验比较稀土含量对镀锌板耐腐蚀性能的影响,并运用XRD分析腐蚀产物,对实际生产提出指导性意见。
1 镀层厚度的测量结果在镀前处理工艺及冷却方式相同的情况下,镀层厚度与热浸镀时间和锌液成分有关。
图4-1所示为采用传统镀锌液成分(Zn-0.177Al)浸镀时间与钢板表面镀层厚度之间的关系。
浸镀时间增加,镀层也逐渐增厚。
当浸镀时间较短(<2min)时,镀层的连续性较差,容易产生漏镀。
浸镀时间超过120s后,镀层已完全覆盖钢板。
把钢板表面划分为9个区域,用测厚仪在每个区域内取10个测量点进行测量,计算平均值作为此区域的平均厚度值,得到镀层厚度曲线(图4-2)。
结合钢板表面宏观形貌来看,传统镀锌液流动性较差,钢板出锌锅后表面锌液向下流动速率较慢,凝固后表面锌层存在波浪状起伏,两侧厚度差较大,厚度明显不均。
由于钢板出锌锅后采用竖直流平冷却的方式,因此靠近钢板底部的7、8、9三个点的平均厚度要高于其他各点。
整体上看,随着浸镀时间的延长,镀层厚度也呈增加的趋势。
图1 镀层平均厚度与浸镀时间的关系(不含稀土)图2 镀层不同区域内厚度曲线图(不含稀土)(a)厚度曲线;(b)测量区域由3.1.2及3.3.1的计算可知,镀锌液中添加稀土元素后,锌液流动性增加,表面张力降低,锌液与基板间的润湿角减小,因而在样板竖直凝固及冷却过程中,锌液不断向下流动,甚至滴落,最终样板表面的粘锌量较少。
镀锌做盐雾实验标准
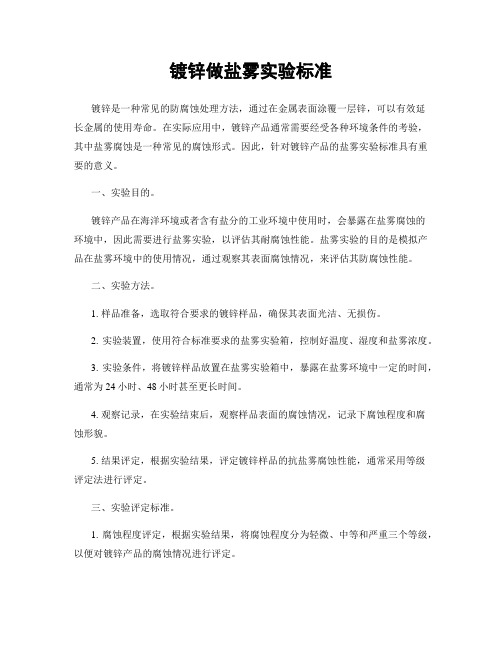
镀锌做盐雾实验标准镀锌是一种常见的防腐蚀处理方法,通过在金属表面涂覆一层锌,可以有效延长金属的使用寿命。
在实际应用中,镀锌产品通常需要经受各种环境条件的考验,其中盐雾腐蚀是一种常见的腐蚀形式。
因此,针对镀锌产品的盐雾实验标准具有重要的意义。
一、实验目的。
镀锌产品在海洋环境或者含有盐分的工业环境中使用时,会暴露在盐雾腐蚀的环境中,因此需要进行盐雾实验,以评估其耐腐蚀性能。
盐雾实验的目的是模拟产品在盐雾环境中的使用情况,通过观察其表面腐蚀情况,来评估其防腐蚀性能。
二、实验方法。
1. 样品准备,选取符合要求的镀锌样品,确保其表面光洁、无损伤。
2. 实验装置,使用符合标准要求的盐雾实验箱,控制好温度、湿度和盐雾浓度。
3. 实验条件,将镀锌样品放置在盐雾实验箱中,暴露在盐雾环境中一定的时间,通常为24小时、48小时甚至更长时间。
4. 观察记录,在实验结束后,观察样品表面的腐蚀情况,记录下腐蚀程度和腐蚀形貌。
5. 结果评定,根据实验结果,评定镀锌样品的抗盐雾腐蚀性能,通常采用等级评定法进行评定。
三、实验评定标准。
1. 腐蚀程度评定,根据实验结果,将腐蚀程度分为轻微、中等和严重三个等级,以便对镀锌产品的腐蚀情况进行评定。
2. 腐蚀形貌评定,观察镀锌样品表面的腐蚀形貌,包括点蚀、线蚀、片状腐蚀等形貌,以便对腐蚀形貌进行评定。
3. 等级评定,根据腐蚀程度和腐蚀形貌,对镀锌样品进行等级评定,通常采用0-10等级进行评定,等级越高表示抗盐雾腐蚀性能越好。
四、实验注意事项。
1. 样品选择,选取符合标准要求的镀锌样品,确保其代表性和可比性。
2. 实验条件,控制好盐雾实验箱的温度、湿度和盐雾浓度,确保实验条件的稳定性和可重复性。
3. 实验操作,严格按照标准要求进行实验操作,确保实验结果的准确性和可靠性。
4. 结果评定,根据实验结果进行等级评定时,要进行多次观察和评定,确保评定结果的客观性和可靠性。
五、实验报告。
1. 实验目的,简要介绍实验的目的和意义。
热镀锌层腐蚀效率
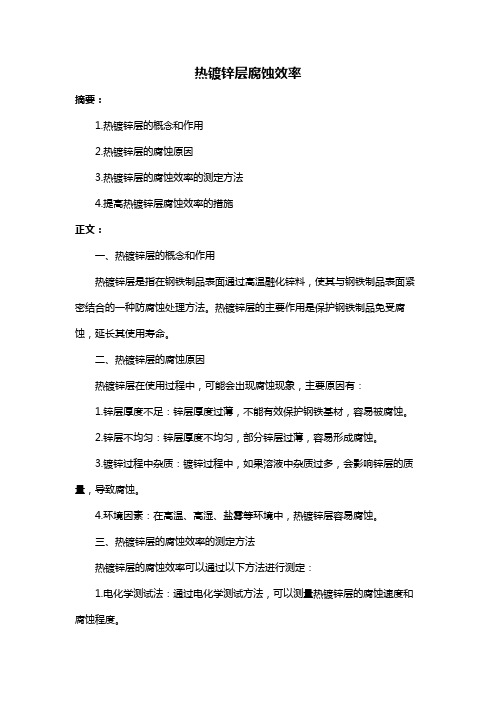
热镀锌层腐蚀效率
摘要:
1.热镀锌层的概念和作用
2.热镀锌层的腐蚀原因
3.热镀锌层的腐蚀效率的测定方法
4.提高热镀锌层腐蚀效率的措施
正文:
一、热镀锌层的概念和作用
热镀锌层是指在钢铁制品表面通过高温融化锌料,使其与钢铁制品表面紧密结合的一种防腐蚀处理方法。
热镀锌层的主要作用是保护钢铁制品免受腐蚀,延长其使用寿命。
二、热镀锌层的腐蚀原因
热镀锌层在使用过程中,可能会出现腐蚀现象,主要原因有:
1.锌层厚度不足:锌层厚度过薄,不能有效保护钢铁基材,容易被腐蚀。
2.锌层不均匀:锌层厚度不均匀,部分锌层过薄,容易形成腐蚀。
3.镀锌过程中杂质:镀锌过程中,如果溶液中杂质过多,会影响锌层的质量,导致腐蚀。
4.环境因素:在高温、高湿、盐雾等环境中,热镀锌层容易腐蚀。
三、热镀锌层的腐蚀效率的测定方法
热镀锌层的腐蚀效率可以通过以下方法进行测定:
1.电化学测试法:通过电化学测试方法,可以测量热镀锌层的腐蚀速度和腐蚀程度。
2.磁性法:通过磁性测厚仪,可以测量热镀锌层的厚度,从而判断其腐蚀效率。
3.镀层重量法:通过称量镀锌前后的重量,可以计算出热镀锌层的腐蚀效率。
四、提高热镀锌层腐蚀效率的措施
要提高热镀锌层的腐蚀效率,可以采取以下措施:
1.控制镀锌厚度:保证热镀锌层的厚度在规定范围内,避免过薄或过厚。
2.优化镀锌溶液:控制镀锌溶液中的杂质含量,提高锌层的质量。
3.控制镀锌工艺:采用适当的镀锌温度和时间,保证锌层的均匀性。
4.选择合适的防腐涂料:在热镀锌层表面涂抹防腐涂料,可以提高其耐腐蚀性能。
- 1、下载文档前请自行甄别文档内容的完整性,平台不提供额外的编辑、内容补充、找答案等附加服务。
- 2、"仅部分预览"的文档,不可在线预览部分如存在完整性等问题,可反馈申请退款(可完整预览的文档不适用该条件!)。
- 3、如文档侵犯您的权益,请联系客服反馈,我们会尽快为您处理(人工客服工作时间:9:00-18:30)。
随着汽车工业的发展,汽车用热镀锌钢板的国产化程度不断提高,轿车的发展对热镀锌板的质量、品种和规格提出了更高的要求。
热镀锌板由于使用需要,-长期暴露于大气中,易于受到大气中潮湿气、SO2以及Cl等的腐蚀,影响产品质量,缩短产品的使用寿命。
在沿海城市及重工业地区,由于同时受到ph值、NO3、固体颗粒等影响,热镀锌板的腐蚀速率也会加快,对其耐腐蚀性能提出了更高的要求。
热镀锌板在盐雾实验中,表面锌层首先被腐蚀,腐蚀产物比较疏松,呈白色絮状覆盖在钢板表面,称之为“白锈”。
随着盐雾喷淋时间的延长,镀层逐渐被腐蚀殆尽,随后基板开始腐蚀,腐蚀产物为红色,称之为“红锈”。
由此可见,镀层的厚度与组成是决定红锈产生时间,即镀层腐蚀完毕、基板开始腐蚀所需时间的决定因素。
本章通过盐雾腐蚀实验和电化学实验比较稀土含量对镀锌板耐腐蚀性能的影响,并运用XRD分析腐蚀产物,对实际生产提出指导性意见。
1 镀层厚度的测量结果在镀前处理工艺及冷却方式相同的情况下,镀层厚度与热浸镀时间和锌液成分有关。
图4-1所示为采用传统镀锌液成分(Zn-0.177Al)浸镀时间与钢板表面镀层厚度之间的关系。
浸镀时间增加,镀层也逐渐增厚。
当浸镀时间较短(<2min) 时,镀层的连续性较差,容易产生漏镀。
浸镀时间超过120s后,镀层已完全覆盖钢板。
把钢板表面划分为9个区域,用测厚仪在每个区域内取10个测量点进行测量,计算平均值作为此区域的平均厚度值,得到镀层厚度曲线(图4-2)。
结合钢板表面宏观形貌来看,传统镀锌液流动性较差,钢板出锌锅后表面锌液向下流动速率较慢,凝固后表面锌层存在波浪状起伏,两侧厚度差较大,厚度明显不均。
由于钢板出锌锅后采用竖直流平冷却的方式,因此靠近钢板底部的7、8、9三个点的平均厚度要高于其他各点。
整体上看,随着浸镀时间的延长,镀层厚度也呈增加的趋势。
图1 镀层平均厚度与浸镀时间的关系(不含稀土)图2 镀层不同区域内厚度曲线图(不含稀土)(a)厚度曲线;(b)测量区域由3.1.2及3.3.1的计算可知,镀锌液中添加稀土元素后,锌液流动性增加,表面张力降低,锌液与基板间的润湿角减小,因而在样板竖直凝固及冷却过程中,锌液不断向下流动,甚至滴落,最终样板表面的粘锌量较少。
因此,添加稀土元素后,样板表面镀锌层厚度普遍小于未添加稀土的样板,对四种不同成分镀锌液钢板的镀层厚度测量结果如图4-3所示。
比较四种钢板的镀层厚度曲线(图4-3a),可以看出,样板A表面镀层最不均匀,厚度值相差最大;添加稀土后,镀层均匀性较好,镀层厚度曲线比较平缓。
随着镀锌液中稀土含量的增加,在相同浸镀时间(2min)下,镀层的平均厚度逐渐降低,同时镀层也更为平整均匀,钢板各测量区域内厚度相差不大,具有比较好的表面效果。
进一步实验表明,当稀土含量大于0.1%时,钢板表面镀层很薄,易于出现漏镀现象,影响热浸镀效果。
图3 镀层厚度与镀锌液成分的关系(浸镀120s)(a)各测量点厚度;(b)平均厚度2 含稀土热镀锌板的耐腐蚀性能研究2.1 热镀锌板的盐雾腐蚀行为热镀锌板在盐雾腐蚀实验中,镀层和基板先后发生氧化腐蚀,参照美国ASTMB-8腐蚀实验方法,记录初次出现红锈的时间,同时根据热镀锌板红色锈点的面积(锈点周围锈迹的面积不计)来计算样板表面红锈的面积百分比。
一般来说,当镀层成分相同时,镀层全部腐蚀所需的时间与镀层的厚度有关。
镀层越厚,全部腐蚀所需的时间越长,基板越难被腐蚀,出红锈时间也越久。
表4-1所示为未添加稀土的热镀锌板镀层厚度与出红锈时间的关系。
表1 镀层厚度与出红锈时间的关系(不含稀土)四种不同镀层成分钢板的盐雾实验照片如图4所示:图4 红锈(a)11天;(b)30天当盐雾实验进行到第11天时,镀层成分为Zn-0.177Al的钢板表面出现红色锈点,约占样板面积的4%,而C、E、G表面均无红锈产生。
最后一块出现红锈的样板E成分为Zn-0.177Al-0.069Re,时间为30天,红锈百分比约为1%。
根据镀层中稀土含量的不同,适当调整浸镀时间,使得七种样板的镀层厚度相近,尽量消除厚度不同对腐蚀时间的影响,进行盐雾实验,此时,镀层表面的成分、结构以及化学活性是钢板出红锈时间和百分比的决定性因素。
其结果如表2所示。
表2 盐雾腐蚀实验结果从实验结果来看,样板 D 、E 的盐雾腐蚀实验结果最好,初出锈时间普遍长 于其他样板,红锈百分比也最低;未添加稀土的样板 A 初出锈时间最短,且红 锈百分比最高,表明稀土对镀层的耐盐雾腐蚀性能有显著的提高作用。
而稀土 含量在 0.045wt%~0.069wt%区间范围内时,样板耐腐蚀能力优于其他成分区间 内的样板。
2.2 盐雾腐蚀产物分析热镀锌板在盐雾实验机内,长期处于高 Cl 浓度的湿热环境中,镀层表面纯 锌层首先发生腐蚀,产生白色锈迹,称为“白锈”。
镀锌层作为热镀锌板防腐 牺牲阳极,在大气环境下容易发生均匀腐蚀,形成致密的碱式碳酸锌(2ZnCO 3 ·3Zn(OH) 2 ),这种碱式碳酸锌比较致密,覆盖在镀层表面起到阻止进一 步发生腐蚀的作用。
而在盐雾实验中,在 NaCl 溶液的浸蚀,局部 Cl 逐渐积累 并在潮湿气氛共同作用下,难溶、密集的 2ZnCO 3 ·3Zn(OH) 2 被疏松、易于溶解的 氯盐化合物所取代,腐蚀产物进一步发生反应,生成 ZnCl 2·4Zn(OH) 2 ,表面形 成的腐蚀产物比较疏松,对镀层的保护作用有限,镀层表面腐蚀和溶解的过程 反复交替进行,镀层逐渐被腐蚀。
对 A 、C 、E 、G 四种样板的腐蚀产物进行 XRD 分析,结果表明四种样板表面 所产生的白锈主要成分均为 Zn 5 (CO 3 ) 2 (OH) 6 和 ZnCl2 ·4Zn(OH) 2 。
当镀层局部腐蚀殆尽后,基板在 Cl-和潮湿气氛作用下发生腐蚀,腐蚀产 物为红色锈点,周围伴随有黄褐色锈迹。
经实验测定,四种样板红锈的主要成 分均为 FeCl3、Fe(OH)3 等。
2.3 极化曲线的测量与计算分析盐雾实验以红锈的出现时间和百分比为评价标准,只有当部分区域内的镀 层腐蚀殆尽时,基板才开始发生腐蚀,产生红锈,是对整个样板表面宏观上耐--腐蚀性能的考察,且其腐蚀条件较为苛刻,腐蚀速率比采用NaCl溶液恒温浸泡等实验方法高。
若以出白锈时间和百分比为依据,根据观察,A、C、E、G四种样板表面在1小时内均被白锈全部覆盖。
因此,盐雾实验不能从微观上体现出这四种样板表层耐腐蚀性能的差异。
极化曲线测定的是镀层表面纯锌层在5%NaCl溶液中的极化行为,结合盐雾实验结果,取A、C、E、G四块样板,用电化学方法测定四种样板极化曲线(图5)。
图5 四种样板的极化曲线同样采用5%NaCl溶液作为腐蚀介质,溶液中阳极及阴极反应如下:阳极:Zn-2e→Zn2+阴极:O 2+2H2O+4e→4OH-其中O2来自于溶解在NaCl溶液中的氧气,镀层表面Zn层在溶液中的腐蚀为吸氧腐蚀,腐蚀速度受到阴极反应中O2的扩散过程控制,图4-6为这种腐蚀速度受到阴极反应扩散控制的典型极化曲线,可以看出,图4-5中四种样板的极化曲线均属于此种类型。
将阳极和阴极曲线延长,根据其延长线交点计算得出该极化反应的自腐蚀电位Ecorr和腐蚀电流Icorr。
结果表明,样板E的自腐蚀电位Ecorr最高,达到-0.9938V,而未添加稀土的样板A自腐蚀电位最低,仅为-0.9997V,四种样板的自腐蚀电位依次为EE>EC>EG>EA(表4-3)。
表3 四种样板的自腐蚀电位计算值图6 腐蚀速度受阴极反应扩散控制的典型极化曲线[58]与盐雾实验生成白锈的机理相似,在5%NaCl溶液中,镀层表面致密的碱式碳酸锌(2ZnCO3·3Zn(OH)2)保护膜受到破坏,发生腐蚀。
在Zn-0.177Al热浸镀液中,不可避免地存在着细微的锌渣和锌灰颗粒,以及一些锌的氧化物、硫化物等。
钢板出锌锅后至镀层完全凝固时,由于不加稀土的热浸镀液黏度较高,流动性较差,部分杂质颗粒被黏附在镀层中,有些甚至存在于镀层表面。
这些杂质破坏了2ZnCO3·3Zn(OH)2保护膜的完整性和致密性,周围还可能伴随着许多微孔,在Cl-的作用下,容易发生点蚀,在杂质区域内产生蚀坑。
添加稀土元素,利用其强脱氧、脱硫作用下反应生成稀土氧化物、硫化物以及硫氧化物,使热浸镀液中的杂质大大减少。
此外,由于稀土提高了热浸镀液的流动性,钢板出锌锅竖直冷却时,锌液能够流过整个钢板表面,在底部富集滴落的同时带走一部分杂质颗粒,进一步减少了镀层中杂质的含量,由图3-1可知,镀层表面光洁平整,其2ZnCO3·3Zn(OH)2保护膜也较为完整致密,因而在5%NaCl溶液中腐蚀速率较慢。
2.4 Kelvin探针微区电位分析为进一步研究稀土元素对镀层表面耐腐蚀性能的影响,运用Kelvin探针对未添加稀土以及添加稀土的两块样板进行微区电位的测量,结果如图7所示。
图7 微区电位分布图(a)Zn-0.177Al;(b)Zn-0.177Al-0.069Re Kelvin探针所反映的是样板表面微小区域(6×4.5mm)内电位的分布情况,具体表现为探针与腐蚀金属电极表面上的薄水膜之间的伏打电位差。
因此,镀层表面的高度差异、晶粒与晶界的区别、杂质微粒的分布等等都会影响Kelvin 探针所测得的功函数值。
图7a中,功函数的值较低,且变化幅度较大(-906meV~-998meV)。
在样板表面测量区域内,微区电位存在严重的分布不均匀性。
而在图4-7b中,功函数的值较高,且变化幅度较小(-803meV~-844meV),样板表面的电位分布较为弥散,没有一定的规律可循。
由此可见,稀土元素的添加,可以提高样板表面的平均电位值,使样板表面电位分布更均匀,极差更小。
从理论上来说,电位较高、分布较均匀的样板,其耐腐蚀性能更好。
3 稀土对耐腐蚀性能的影响机理结合第三章中对含稀土热镀锌层的组织结构观察与分析,在热浸镀液中添加稀土元素,能够显著提高热镀锌钢板的耐腐蚀性能,主要有以下一些原因:3.1 添加稀土元素提高了热浸镀液的流动性,使镀层表面更为平整光洁(图3-1),在大气条件下,镀层所形成的2ZnCO3·3Zn(OH)2保护膜更为致密完整,虽-然在高Cl环境中发生反应生成ZnCl2·4Zn(OH)2,但一定程度上仍起到了延缓腐蚀的作用;3.2 稀土元素易于与O、S等结合,生成的稀土氧化物与硫化物在凝固过程中一部分作为晶核继续生长,一部分表层的颗粒则随着锌液的滴落而除去,同时抑制了热浸镀液中锌渣和锌灰的形成。
未添加稀土的热浸镀液中,则存在着大量锌渣、锌灰以及锌或铝的氧化物、硫化物颗粒,根据晶间区杂质或第二相选择性溶解理论[59],镀层中的夹杂物易于在晶界上偏析,形成表面活性区域,造成表面能的不均匀性,在表层形成很多微孔,且腐蚀产物不能在表面形成连续而均匀的覆盖层,反而容易产生蚀坑,加速了腐蚀的进行;3.3 稀土元素抑制了镀层表面胞状组织的生长,镀层平整性、均匀性较好。