中频炉熔炼球铁配料计算方法修订稿
电炉炼钢的配料计算_装料方法及操作要点
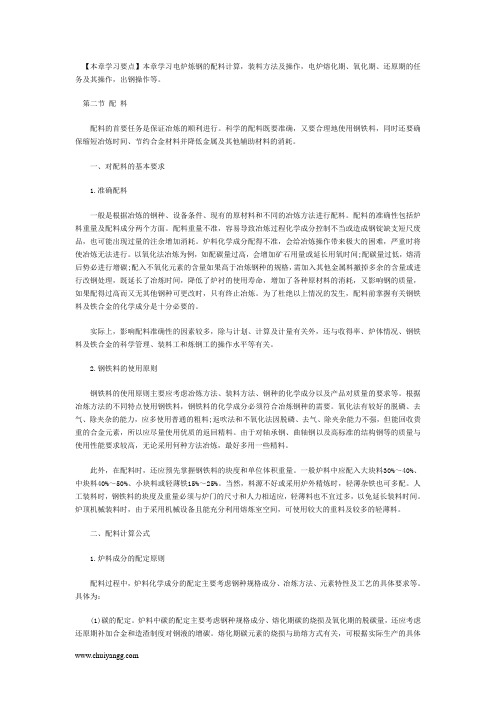
【本章学习要点】本章学习电炉炼钢的配料计算,装料方法及操作,电炉熔化期、氧化期、还原期的任务及其操作,出钢操作等。
第二节配料配料的首要任务是保证冶炼的顺利进行。
科学的配料既要准确,又要合理地使用钢铁料,同时还要确保缩短冶炼时间、节约合金材料并降低金属及其他辅助材料的消耗。
一、对配料的基本要求1.准确配料一般是根据冶炼的钢种、设备条件、现有的原材料和不同的冶炼方法进行配料。
配料的准确性包括炉料重量及配料成分两个方面。
配料重量不准,容易导致冶炼过程化学成分控制不当或造成钢锭缺支短尺废品,也可能出现过量的注余增加消耗。
炉料化学成分配得不准,会给冶炼操作带来极大的困难,严重时将使冶炼无法进行。
以氧化法冶炼为例,如配碳量过高,会增加矿石用量或延长用氧时间;配碳量过低,熔清后势必进行增碳;配入不氧化元素的含量如果高于冶炼钢种的规格,需加入其他金属料撤掉多余的含量或进行改钢处理,既延长了冶炼时间,降低了炉衬的使用寿命,增加了各种原材料的消耗,又影响钢的质量,如果配得过高而又无其他钢种可更改时,只有终止冶炼。
为了杜绝以上情况的发生,配料前掌握有关钢铁料及铁合金的化学成分是十分必要的。
实际上,影响配料准确性的因素较多,除与计划、计算及计量有关外,还与收得率、炉体情况、钢铁料及铁合金的科学管理、装料工和炼钢工的操作水平等有关。
2.钢铁料的使用原则钢铁料的使用原则主要应考虑冶炼方法、装料方法、钢种的化学成分以及产品对质量的要求等。
根据冶炼方法的不同特点使用钢铁料,钢铁料的化学成分必须符合冶炼钢种的需要。
氧化法有较好的脱磷、去气、除夹杂的能力,应多使用普通的粗料;返吹法和不氧化法因脱磷、去气、除夹杂能力不强,但能回收贵重的合金元素,所以应尽量使用优质的返回精料。
由于对轴承钢、曲轴钢以及高标准的结构钢等的质量与使用性能要求较高,无论采用何种方法冶炼,最好多用一些精料。
此外,在配料时,还应预先掌握钢铁料的块度和单位体积重量。
铸造熔炼配料计算方法

铸造熔炼配料计算方法
铸造熔炼配料的计算方法可以按照以下步骤进行:
1. 确定需要铸造的材料及其比例:根据要铸造的零件的要求,确定所需的材料以及其比例。
例如,如果需要铸造一种高强度的合金钢,可能需要使用铁、铬、钼、钢等材料,其中各材料的比例需根据合金设计要求确定。
2. 确定原材料的化学成分:通过化学分析或参考标准规定,确定原材料的化学成分。
这可以通过实验室测试或供应商提供的化学成分报告获得。
3. 计算所需配料的理论化学成分:根据所需材料比例和原材料化学成分,计算出所需配料的理论化学成分。
例如,如果需要铸造一种含有30%铬和5%钼的合金钢,而可用的铬含量为60%,则需要计算出所需铬含量为100%的材料和所需钼含量为100%的材料的配比。
4. 考虑原材料的纯度和可用性:考虑原材料的纯度和可用性对配料进行调整。
如果原材料的纯度低于预期或可用性有限,可能需要调整配比或选择其他材料。
5. 考虑冶炼损耗和浮渣的产生:在计算材料配比时,需要考虑冶炼损耗和浮渣的产生。
这些因素可能会导致所需配比发生变化。
6. 进行实际配比测试:在进行大规模生产之前,建议进行实际
配比测试。
这可以通过小规模试验或实际生产中的抽样测试来完成,以确保所需配比能够满足要求。
铸造熔炼配料的计算方法需要根据具体材料和工艺来确定,因此在实际应用中可能会有一些差异。
建议在进行配料计算时,参考相关的行业标准和专业知识,以确保计算的准确性和可行性。
铸铁熔炼操作规程

加强现场技术管理,规范中频炉熔炼操作。
2;范围适用于中频炉熔炼铸铁的操作。
3:职责3.1原材料准备⑾原生铁、回炉料、增碳剂、废钢、硅铁、锰铁、铜、球化剂、孕育剂的质量标准应符合公司铸造材料标准。
⑿每批外购的生铁、废钢、废机铁、硅铁、锰铁应该分类堆放,不可混杂(生铁、硅铁、锰铁、球化剂、孕育剂应附有对方或本公司的检测报告)⑶炉料应进行破碎,用电子吸盘直接加料尺寸应符合表1,注:用手工加料的不受此限制。
不得混有合金钢废料。
⒂新生铁回炉料、浇冒口表面粘附的泥砂应清除。
⒃铁屑应按材质种类分类堆放,不得混有油污泥砂和抹布等杂物。
⒄根据浇注铁水总量和配料比例,开炉前要备足各种炉料,并且分好类。
3.2修炉⑴每开炉之前,应将炉壁上附着的釉渣进行清理,并检查炉衬的尺寸大小是否符合技术要求。
⑵应仔细对炉衬各部分特别是炉底进行检查,发现有严重侵蚀及裂纹等情况,应用修补炉衬材料进行修补。
⑶将炉领上附着的釉渣进行清理,并按工艺要求进行修整,保证出铁时,铁液不溢出炉外。
3.3 开炉前检查3.3.1每次开炉前一小时,要全面检查以下方面,发现问题要及时排除才能开炉熔化:A)炉体、炉衬、炉领、中频电源漏炉报警装置,内循环和外循环冷却水系统液压倾炉机构等是否正常。
B)炉体各紧固件有无松动和移位;C)水管有无破损漏水等。
3.3.2 炉前地坑和炉体周围不得有积水,地坑内可铺一层干砂。
3.4加料熔化3.4.1 第一炉冷料启动时,其加料量一般为1.5~2.5吨,最好在炉体的中间加入一件重量为150~300公斤的起熔块,两边再用生铁锭或小块废钢填实,装料时禁止站在炉台上往炉丢入铁块,以免将炉体坩埚砸坏。
3.4.2第一炉熔化先用300~500KW左右的小功率送电半小时,使生料逐渐变红,观察炉衬,当生料和炉衬从底部到顶部都变得明亮时,保温半小时,然后进入正常熔化。
3.4.3 加入到电炉内的各种原材料严格按工艺员出具的配料单要求,用电磁吸铁盘或手工分批吊入,计量要求准确,加入顺序为:废钢加入炉底部,然后加入生铁锭和回炉料,并做好记录。
中频炉熔炼球铁配料计算方法
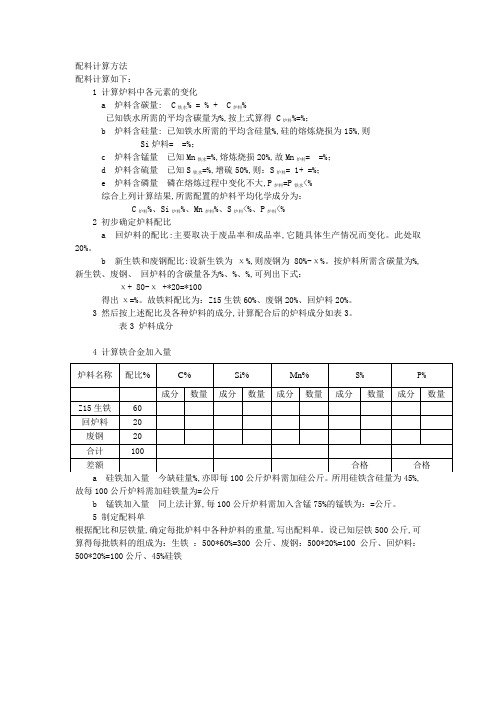
配料计算方法配料计算如下:1 计算炉料中各元素的变化a 炉料含碳量: C铁水% = % + C炉料%已知铁水所需的平均含碳量为%,按上式算得 C炉料%=%;b 炉料含硅量: 已知铁水所需的平均含硅量%,硅的熔炼烧损为15%,则Si炉料= =%;c 炉料含锰量已知Mn铁水=%,熔炼烧损20%,故Mn炉料= =%;d 炉料含硫量已知S铁水=%,增硫50%,则:S炉料= 1+ =%;e 炉料含磷量磷在熔炼过程中变化不大,P炉料=P铁水<%综合上列计算结果,所需配置的炉料平均化学成分为:C炉料%、Si炉料%、Mn炉料%、S炉料<%、P炉料<%2 初步确定炉料配比a 回炉料的配比:主要取决于废品率和成品率,它随具体生产情况而变化。
此处取20%。
b 新生铁和废钢配比:设新生铁为χ%,则废钢为80%-χ%。
按炉料所需含碳量为%,新生铁、废钢、回炉料的含碳量各为%、%、%,可列出下式:χ+ 80-χ +*20=*100得出χ=%。
故铁料配比为:Z15生铁60%、废钢20%、回炉料20%。
3 然后按上述配比及各种炉料的成分,计算配合后的炉料成分如表3。
表3 炉料成分4 计算铁合金加入量故每100公斤炉料需加硅铁量为=公斤b 锰铁加入量同上法计算,每100公斤炉料需加入含锰75%的锰铁为:=公斤。
5 制定配料单根据配比和层铁量,确定每批炉料中各种炉料的重量,写出配料单。
设已知层铁500公斤,可算得每批铁料的组成为:生铁:500*60%=300公斤、废钢:500*20%=100公斤、回炉料:500*20%=100公斤、45%硅铁。
灰球铁铸造工艺规程-副本(2)
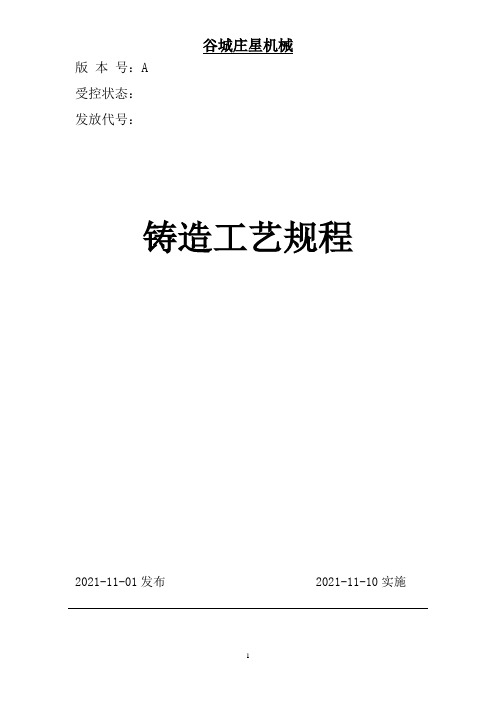
版本号:A受控状态:发放代号:铸造工艺规程2021-11-01发布 2021-11-10实施本规程适用于本公司批量生产各种牌号的灰铸铁件,采用中频炉熔炼,孕育处理生产各种牌号灰铸铁件。
1.1采用孕育法生产各种牌号灰铸铁。
1.2熔炼过程中参照有关熔炼工艺规程执行。
2.1浇注过程中按有关浇注工艺规程执行。
℃,浇注时间每箱15-17秒。
2.3处理后的铁水,一般控制在8-15分钟/内浇注完毕。
2.4对已浇注的铸型按包次插上牌子标志区分。
3.落砂、清理、检验3.1捅箱时,应注意按包次区分,在鳞板上隔离铸件。
3.2从鳞板上下来后,铸件在地上按50型为一组,依次堆放,等检验员依材质检验数据,判定材质合格后,才能上线清理,不合格铸件不能进入清理线。
3.3清理后对铸件再进行一次检验,几何尺寸及外观合格后才能浸漆入库。
铸件质量按有关检查工艺规程执行。
1总那么本规程适用于S114C 型辗轮式混砂机,人工运输,F 脱箱震压造型机造型,湿型浇注。
2型砂配制的内容采用颗粒均匀的圆形或多角天然石英砂即硅砂,粒度采用07/09和08/10的细粒砂。
生产球墨铸铁件时,为适当提高透气率,用05/07和06/08的中粒砂。
湿型砂普遍采用粘结性好的膨润土作为粘结剂,全部采用新原砂配制时,小型铸件膨润土参加量约为5-6%。
铸铁件湿型砂配方成分的显著特点是普遍参加煤粉,煤粉参加量需根据铸件大小,壁的厚薄和煤粉性质而定,铸铁小件参加量为3-4% ;当煤粉参加量到达8%仍出现粘砂缺陷可参加1-2%的重油。
%,冬天取下限,夏天取上限。
配砂所用原材料必须按照工艺要求进行化验,检验合格后,方可使用。
原砂、粘土、煤粉的检验标准详见本公司?铸造原材料技术条件?。
砂处理的各个工艺过程是通过各种砂处理设备来完成的。
2.3.2型砂和芯砂都是将各种物料按一定的配比参加混砂机中经过混制而成。
混砂过程应保证使各种成分均匀,以满足造型造芯的性能要求,其工艺流程如下:混1到2分钟混1到2分钟旧砂新砂水分膨润土、煤粉卸料全部配制混碾时间3-4分钟。
铸造球铁熔铁配料规范
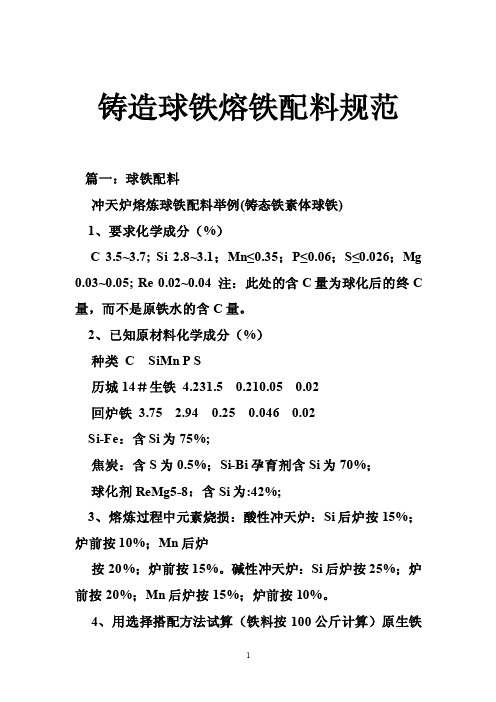
铸造球铁熔铁配料规范篇一:球铁配料冲天炉熔炼球铁配料举例(铸态铁素体球铁)1、要求化学成分(%)C 3.5~3.7; Si 2.8~3.1;Mn≤0.35;P≤0.06;S≤0.026;Mg0.03~0.05; Re 0.02~0.04 注:此处的含C量为球化后的终C 量,而不是原铁水的含C量。
2、已知原材料化学成分(%)种类C SiMn P S历城14#生铁4.231.5 0.210.05 0.02回炉铁3.75 2.94 0.25 0.046 0.02Si-Fe:含Si为75%;焦炭:含S为0.5%;Si-Bi孕育剂含Si为70%;球化剂ReMg5-8:含Si为:42%;3、熔炼过程中元素烧损:酸性冲天炉:Si后炉按15%;炉前按10%;Mn后炉按20%;炉前按15%。
碱性冲天炉:Si后炉按25%;炉前按20%;Mn后炉按15%;炉前按10%。
4、用选择搭配方法试算(铁料按100公斤计算)原生铁65%;回炉铁35%。
5、核算炉料中的含C量C炉料=4.23%×65%+3.75×35%=4.06%由于球铁中碳当量比较高,在冲天炉熔炼条件下要减碳(当碳当量>3.6%时一般要减碳3~8%),如按5.5%计算,则从炉内出来的铁水含C量为:4.06%1×(1-5.5%)=3.84%;同时在球化处理过程中还要降碳0.1~0.2%(原因:○2一部分过饱和C以石墨形式析出,上浮进入熔渣)如球化反应使碳烧损;○按0.15%计算,则铁水最终含C量为:3.84%—0.15%=3.69%(符合3.5~3.7%的要求)6、含Si量的计算铁水最终含Si量包括以下几个部分:1)炉料中的含Si量Si炉料:Si炉料=1.5%×65%+2.94×35%=2.0%,烧损按15%计算,则从炉内出来的铁水含Si量为:2.0%×(1-15%)=1.7%; 2)一次孕育按0.2% 75 Si-Fe(覆盖在球化剂上),进入铁水的硅量Si孕育Ⅰ=0.2%×75%×(1-10%)=0.14%;3)二次孕育按0.4% 75 Si-Fe(在出铁槽加入),进入铁水的硅量Si孕育Ⅱ=0.4%×75%×(1-10%)=0.27%;4)三次孕育按0.2% Si-Bi(浇包孕育),进入铁水的硅量Si孕育Ⅲ=0.2%×70%×(1-10%)=0.13%;5)球化剂加入量按 1.7%,则球化剂进入铁水的硅量Si 球化=1.7%×42%×(1-10%)=0.64%;6)铁水终Si含量为上述1)~5)之和(如果生产管卡,还要计入0.1~0.2%的小颗粒75 Si-Fe浇包四次孕育)即Si 终=1.7%+0.14%+0.27%+0.13%+0.64%=2.88%(符合2.8~3.1%的要求)7、含Mn量的计算炉料中的含Mn量Mn炉料:Mn炉料=0.21%×65%+0.25×35%=0.224%,去掉烧损,则从炉内出来的铁水含Mn量为:0.224%×(1-20%)=0.18%;另外,稀土镁合金中一般允许含Mn≤4%,若以4%计(实际应根据验收化验的具体含量计算),并去掉烧损,则进入铁水的Mn量为:1.7%×4%×(1-15%)=0.058%,铁水中的总Mn量为两者之和即0.18%+0.058%=0.238%,在球化处理过程中由于Mn与S作用和Mn夹渣上浮,一般Mn含量要下降3%~5%,若以4%计算,则铁水的终Mn量Mn 终=0.238%×(1-4%)=0.228%(符合终Mn≤0.35的要求)。
中频炉内成分调整技术操作规程
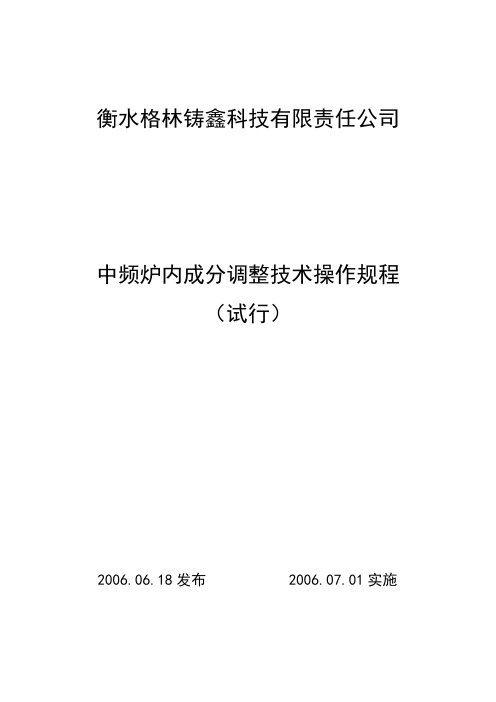
衡水格林铸鑫科技有限责任公司中频炉内成分调整技术操作规程(试行)2006.06.18发布 2006.07.01实施目次1 范围 (1)2 主要设备参数 (1)3 技术操作内容 (1)中频炉熔炼技术操作规程1.范围本规程规定了中频感应炉筑炉、铸铁熔炼及保温技术操作要求及异常情况处理等内容。
本规程适用于衡水格林铸鑫科技有限责任公司中频感应炉各类铸铁熔炼技术操作。
2.主要设备性能2.1 中频感应炉主要规格2.1.1 额定容量5000Kg2.1.2 电源额定功率1000kW,两台电炉无级分配,单台电炉最大功率750kW2.1.3 额定频率200~400Hz2.1.4 额定电压1200~1500V2.1.5 最高工作温度1600℃3.技术操作内容生产过程中,当冲天炉出铁水碳硅锰磷硫等元素不符合工艺要求时,应调整冲天炉所加金属炉料配比;当中频炉内铁水成份不符合要求时,应对中频炉内铁水进行调整。
中频炉内铁水成份的调整是通过加入各种铁合金、生铁、废钢、增碳剂等材料,来实现各有关元素的增减,最终达到符合要求的原铁水成份。
此时,需保证所加材料充分熔化并均匀后方可取样进行元素含量分析,仅当成份符合工艺要求,才可出水进行浇注。
3.1炉内碳硅锰磷硫元素的调整3.1.1碳元素调整3.1.1.1 增碳a. 采用增碳剂,加入量按下面公式计算:X=(C终-C原)*炉内铁水量/(A*η)公式内符号含义:“-、*、/”:代表减、乘、除法X:指需加入的增碳剂量。
单位KgC终:指最终要调整到的铁水含碳量,按百分含量计C原:指还未调整的铁水含碳量,按百分含量计炉内铁水量:指要调整的炉内铁水量,单位KgA:增碳剂中碳的百分含量,按批料化验单(一般按95%左右)η:增碳剂中碳的吸收率,一般按80%左右b. 采用生铁,加入量按下面公式计算:X=(C终-C原)*炉内铁水量/(D-C终)公式内符号含义:“-、*、/”:代表减、乘、除法X:指需加入的生铁量。
球铁配料

冲天炉熔炼球铁配料举例(铸态铁素体球铁)1、要求化学成分(%)C 3.5~3.7; Si 2.8~3.1;Mn≤0.35;P≤0.06;S≤0.026;Mg 0.03~0.05; Re0.02~0.04 注:此处的含C量为球化后的终C量,而不是原铁水的含C量。
2、已知原材料化学成分(%)种类 C Si Mn P S历城14#生铁 4.23 1.5 0.21 0.05 0.02回炉铁 3.75 2.94 0.25 0.046 0.02Si-Fe:含Si为75%;焦炭:含S为0.5%;Si-Bi孕育剂含Si为70%;球化剂ReMg5-8:含Si为:42%;3、熔炼过程中元素烧损:酸性冲天炉:Si后炉按15%;炉前按10%;Mn后炉按20%;炉前按15%。
碱性冲天炉:Si后炉按25%;炉前按20%;Mn后炉按15%;炉前按10%。
4、用选择搭配方法试算(铁料按100公斤计算)原生铁65%;回炉铁35%。
5、核算炉料中的含C量C炉料=4.23%×65%+3.75×35%=4.06%由于球铁中碳当量比较高,在冲天炉熔炼条件下要减碳(当碳当量>3.6%时一般要减碳3~8%),如按5.5%计算,则从炉内出来的铁水含C量为:4.06%×(1-5.5%)=3.84%;同时在球化处理过程中还要降碳0.1~0.2%(原因:○1球化反应使碳烧损;○2一部分过饱和C以石墨形式析出,上浮进入熔渣)如按0.15%计算,则铁水最终含C量为:3.84%—0.15%=3.69%(符合3.5~3.7%的要求)6、含Si量的计算铁水最终含Si量包括以下几个部分:1)炉料中的含Si量Si炉料:Si炉料=1.5%×65%+2.94×35%=2.0%,烧损按15%计算,则从炉内出来的铁水含Si量为:2.0%×(1-15%)=1.7%;2)一次孕育按0.2% 75 Si-Fe(覆盖在球化剂上),进入铁水的硅量Si孕育Ⅰ=0.2%×75%×(1-10%)=0.14%;3)二次孕育按0.4% 75 Si-Fe(在出铁槽加入),进入铁水的硅量Si孕育Ⅱ=0.4%×75%×(1-10%)=0.27%;4)三次孕育按0.2% Si-Bi(浇包孕育),进入铁水的硅量Si孕育Ⅲ=0.2%×70%×(1-10%)=0.13%;5)球化剂加入量按1.7%,则球化剂进入铁水的硅量Si球化=1.7%×42%×(1-10%)=0.64%;6)铁水终Si含量为上述1)~5)之和(如果生产管卡,还要计入0.1~0.2%的小颗粒75 Si-Fe浇包四次孕育)即Si终=1.7%+0.14%+0.27%+0.13%+0.64%=2.88%(符合2.8~3.1%的要求)7、含Mn量的计算炉料中的含Mn量Mn炉料:Mn炉料=0.21%×65%+0.25×35%=0.224%,去掉烧损,则从炉内出来的铁水含Mn量为:0.224%×(1-20%)=0.18%;另外,稀土镁合金中一般允许含Mn≤4%,若以4%计(实际应根据验收化验的具体含量计算),并去掉烧损,则进入铁水的Mn量为: 1.7%×4%×(1-15%)=0.058%,铁水中的总Mn量为两者之和即0.18%+0.058%=0.238%,在球化处理过程中由于Mn与S 作用和Mn夹渣上浮,一般Mn含量要下降3%~5%,若以4%计算,则铁水的终Mn量Mn终=0.238%×(1-4%)=0.228%(符合终Mn≤0.35的要求)。
电炉熔炼球墨铸铁(灰铸铁)元素控制方法
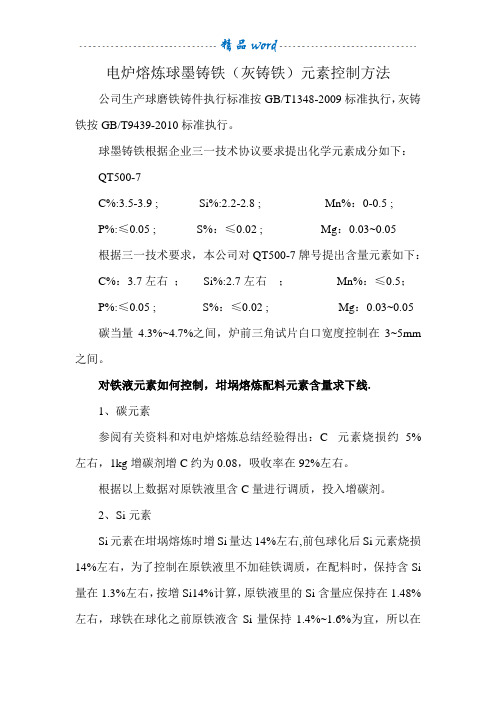
电炉熔炼球墨铸铁(灰铸铁)元素控制方法公司生产球磨铁铸件执行标准按GB/T1348-2009标准执行,灰铸铁按GB/T9439-2010标准执行。
球墨铸铁根据企业三一技术协议要求提出化学元素成分如下:QT500-7C%:3.5-3.9 ; Si%:2.2-2.8 ; Mn%:0-0.5 ;P%:≤0.05 ; S%:≤0.02 ; Mg:0.03~0.05根据三一技术要求,本公司对QT500-7牌号提出含量元素如下:C%:3.7左右;Si%:2.7左右;Mn%:≤0.5;P%:≤0.05 ; S%:≤0.02 ; Mg:0.03~0.05 碳当量4.3%~4.7%之间,炉前三角试片白口宽度控制在3~5mm 之间。
对铁液元素如何控制,坩埚熔炼配料元素含量求下线.1、碳元素参阅有关资料和对电炉熔炼总结经验得出:C 元素烧损约5%左右,1kg增碳剂增C约为0.08,吸收率在92%左右。
根据以上数据对原铁液里含C量进行调质,投入增碳剂。
2、Si元素Si元素在坩埚熔炼时增Si量达14%左右,前包球化后Si元素烧损14%左右,为了控制在原铁液里不加硅铁调质,在配料时,保持含Si 量在1.3%左右,按增Si14%计算,原铁液里的Si含量应保持在1.48%左右,球铁在球化之前原铁液含Si量保持1.4%~1.6%为宜,所以在坩埚内不加硅铁进行调质。
铸件中Si含量要求在2.7%左右,余下Si 含量在前包球化、孕育处理加入,但前包总投Si含量不能<1%为宜。
3、Mn元素新生铁、回炉料、废钢都含有Mn元素,在配料时按5%烧损计算。
若Mn含量过低时,在铁液熔化完出铁水前进行投放,溶化后进行搅拌出锅。
总之,Si和Mn在坩埚内调质都要在最后投放,以免过度烧损。
4、P元素如果原铁液含P高,目前无办法来处理,只有从配料上来控制,少用新生铁,多用废钢来解决。
5、S元素S元素在球墨铁铸件,应当控制在0.015为好。
若原材料含S高,必须加脱硫剂进行脱硫。
铸铁配料计算公式表

铸铁配料计算公式表
以下是常见的铸铁配料计算公式表,用于计算铸铁材料中各种元素或化合物的配料比例:
1. 石墨含量计算:
石墨含量 = (石墨重量 / 总重量) * 100%
2. 硅含量计算:
硅含量 = (硅重量 / 总重量) * 100%
3. 碳当量计算:
碳当量 = 碳含量 + (硅含量 / 3.5) + (磷含量 / 10) + (硫含量 / 32)
4. 硫含量计算:
硫含量 = (硫重量 / 总重量) * 100%
5. 磷含量计算:
磷含量 = (磷重量 / 总重量) * 100%
6. 碳含量计算:
碳含量 = (碳重量 / 总重量) * 100%
以上公式中,总重量指的是铸铁材料的总重量,而各种元素(如碳、硅、磷、硫)的重量指的是这些元素在配料中的重量。
具体的配料比例和配方可能因不同的铸铁材料类型(如灰铁、球墨铸铁)以及工艺要求而有所不同。
因此,在实际应用中,应根据具体的铸铁材料和要求来选择合适的配方和计算公式。
用中频感应电炉熔炼铸铁的几个技术问题

用中频感应电炉熔炼铸铁的几个技术问题王成刚,马顺龙(一汽铸造有限公司技术th■,吉林长春130062)摘要:解答了铸造企业应用rp频感应电炉熔炼铸铁的几个技术问题,提供了有关熔炼工艺、技术特点、合成球铁熔炼方法及发展趋势等方血的参考信息..关键词:铸铁;中频感应电炉;熔炼中图分类号:TG232.3文献标识码:B文章编号:10038345(2012)04—0043—04DOI:1039696issn10038345201204006SeveralTechnicalProblemswithMediumFrequencyInductionFurnaceMeltingofCastIronWANGCheng—gang.MAShun—long(TPchnolngyCenter,Foundryr:n-1.td,ChinaFirstAntfmmhilecⅢ1pCo1,td,Chnngchlm130062,China)Abstract:SeveraltechnicalproblemswithfimndryenterprisesusingmediumfrequencyinductionfumacetomeltcastironswflsexDlai㈣d…domeusefulinfurmalionconcerningthemeltingprof'ess,technicalcharacteristics,mehingprocessanddevelopmenttendencyotsyntheticnodularimnwa8givenKeywords:castiron;mediumfrequencyinductionfurnace;melting1感应电炉简介感应电炉按电流频率分为工频、中频和高频三类,其频率分别为50HZ、50~10000HZ和10000HZ以上。
1.1应用范围111高频炉高频无芯炉容最一般在50kg以下,适用于实验室和小规模生产中熔炼特种钢和特种合金。
中频炉熔炼工艺标准
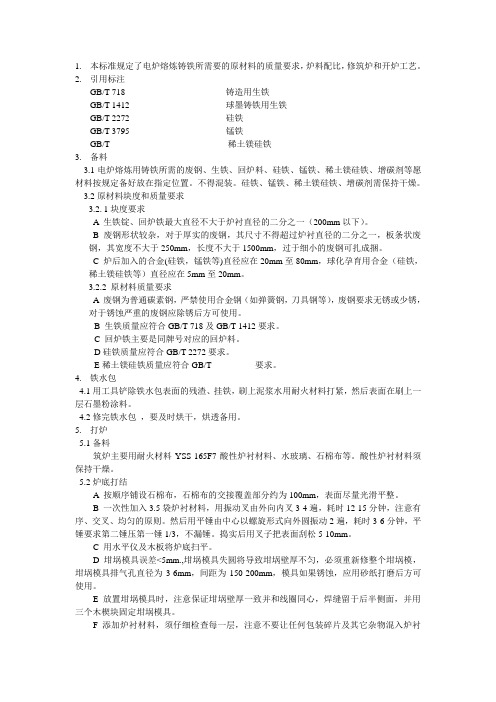
1.本标准规定了电炉熔炼铸铁所需要的原材料的质量要求,炉料配比,修筑炉和开炉工艺。
2.引用标注GB/T 718 铸造用生铁GB/T 1412 球墨铸铁用生铁GB/T 2272 硅铁GB/T 3795 锰铁GB/T 稀土镁硅铁3.备料3.1电炉熔炼用铸铁所需的废钢、生铁、回炉料、硅铁、锰铁、稀土镁硅铁、增碳剂等愿材料按规定备好放在指定位置。
不得混装。
硅铁、锰铁、稀土镁硅铁、增碳剂需保持干燥。
3.2原材料块度和质量要求3.2.1块度要求A 生铁锭、回炉铁最大直径不大于炉衬直径的二分之一(200mm以下)。
B 废钢形状较杂,对于厚实的废钢,其尺寸不得超过炉衬直径的二分之一,板条状废钢,其宽度不大于250mm,长度不大于1500mm,过于细小的废钢可扎成捆。
C 炉后加入的合金(硅铁,锰铁等)直径应在20mm至80mm,球化孕育用合金(硅铁,稀土镁硅铁等)直径应在5mm至20mm。
3.2.2 原材料质量要求A 废钢为普通碳素钢,严禁使用合金钢(如弹簧钢,刀具钢等),废钢要求无锈或少锈,对于锈蚀严重的废钢应除锈后方可使用。
B 生铁质量应符合GB/T 718及GB/T 1412要求。
C 回炉铁主要是同牌号对应的回炉料。
D硅铁质量应符合GB/T 2272要求。
E稀土镁硅铁质量应符合GB/T 要求。
4.铁水包4.1用工具铲除铁水包表面的残渣、挂铁,刷上泥浆水用耐火材料打紧,然后表面在刷上一层石墨粉涂料。
4.2修完铁水包,要及时烘干,烘透备用。
5.打炉5.1备料筑炉主要用耐火材料YSS-165F7酸性炉衬材料、水玻璃、石棉布等。
酸性炉衬材料须保持干燥。
5.2炉底打结A 按顺序铺设石棉布,石棉布的交接覆盖部分约为100mm,表面尽量光滑平整。
B 一次性加入3.5袋炉衬材料,用振动叉由外向内叉3-4遍,耗时12-15分钟,注意有序、交叉、均匀的原则。
然后用平锤由中心以螺旋形式向外圆振动2遍,耗时3-6分钟,平锤要求第二锤压第一锤1/3,不漏锤。
中频炉熔炼球铁配料计算方法

中频炉熔炼球铁配料计算方法球铁配料计算方法主要包括炉内成分计算、原料比例计算和质量平衡计算。
首先,进行炉内成分计算。
炉内成分计算是根据产品要求和原料成分来确定每种原料的投入量。
常见的球铁成分包括铁、碳、硅、锰、磷和硫等。
根据产品要求,确定各种成分的含量范围和理想值。
其次,进行原料比例计算。
原料比例计算是根据炉内成分计算结果,确定每种原料的配比。
常见的球铁原料包括生铁、废钢、铁回收料、铁矿石和细碳粉等。
根据每种原料的成分和含量,计算出每种原料的投入量。
比例计算可以根据质量比或者体积比进行。
质量比计算是根据每种原料的质量来计算比例,常见的计算公式为:配比比例=(目标含量-原料含量)/(目标含量-最小含量)。
体积比计算是根据每种原料的体积来计算比例,常见的计算方法为:配比比例=(目标含量-原料含量)/(目标含量-最小含量)*(原料密度/目标密度)。
最后,进行质量平衡计算。
质量平衡计算是为了验证配料计算方法的准确性和合理性。
质量平衡计算是根据每种原料的投入量和成分计算出炉内化学成分。
比如,根据生铁的含碳量、铁矿石的含碳量以及废钢和细碳粉的投入量,计算出炉内的总碳含量。
然后与目标碳含量进行比较,来评估配料的准确性。
配料计算的准确性和合理性对于球铁熔炼工艺的稳定性和产品质量的提高具有重要影响。
因此,需要根据实际情况和产品要求来确定合理的配料计算方法,并通过质量平衡计算来验证和调整配料比例。
在实际操作中,还应注意原料的储存和搅拌,确保每一次投料的准确性和均匀性,以获得稳定的熔炼效果和优质的球铁产品。
中频炉熔炼操作技术标准

32.9整流变压器容量中频炉熔炼操作技术标准1范围本标准规定了炭素组装车间中频炉熔炼操作技术标准 本标准适用于青海黄河水电公司鑫业分公司22坩埚尺寸 内径$ 700mm熔池高度1150mm坩埚高度 2.3中频电源技术参数 2.5额定工作温度:V 1600 C2.6熔化率:》2.80T/H.台 该指标适用于热炉衬,紧密装料。
32.7耗水量: 单台炉体:35m /h 2.8液压装置 2.8.1最高工作压力 16Mpa 2.8.2使用工作压力 9Mpa 2.8.3工作流量 26L/min 2.8.4输入功率 7.5KW 2.8.5油箱容积 0.6m 2主要设备性能 2.1炉体额定容量3.0T最大容量3.6T 1430mm2.3.1规格型号: 2.3.2输入电压: 2.3.3输入电流: 2.3.4输出直流电压: 2.3.5输出直流电流: 2.3.6输出中频电压: 2.3.7输出频率: 2.3.8输出功率: 2.3.9电源效率:KGPS ----- 0.5/1500 ~660 6 相 50HZ 1360A /2880V 1700A 1250V 500Hz 1500KW98% 2.4额定电气参数 额定功率 1500KW额定频率 500Hz2.9.1 变压器容量1800KV A2.9.2 输入电压6000V2.9.3 输出电压660V/6 相/50Hz2.9.4 整流采用12 脉全控电路。
逆变器采用并联逆变线路。
3 生产工艺技术条件3.1出铁水温度为1400± 50C3.2 浇铸铁水成分:C: 2.8-3.5% Si: 2.0-3.1% Mn : 0.6〜0.9% P: 1.0〜1.8%S:< 0.15% 3.3 电源封闭循环水冷却系统3.3.1冷却水进口温度:<30 C3.3.2冷却水出口温度:v 42C3.3.3 冷却水工作压力: 0.15~0.20MPa33.3.4 封闭循环水流量: 20m3/h3.4 炉体封闭循环水冷却系统3.4.1冷却水进口温度:v 35C3.4.2冷却水出口温度:v 55C3.4.3 炉口进水压力: 0.20~0.30MPa33.4.4 单台炉体水流量:35〜45m3/h3.5 炉体应急冷却循环水系统3.5.1应急水进口温度:v 35C3.5.2应急水出口温度:v 55C3.5.3 应急水进口压力:0.10~0.15MPa33.5.4应急水流量:》20m /h4 启动前的操作准备与检查4.1 开炉前,必须先检查炉村、筑炉情况,发现问题及时处理。
中频炉冶炼不锈钢 造渣工艺【范本模板】
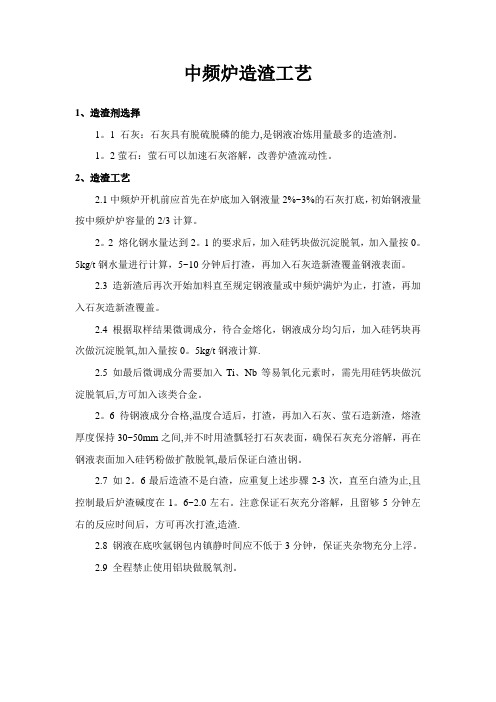
中频炉造渣工艺
1、造渣剂选择
1。
1 石灰:石灰具有脱硫脱磷的能力,是钢液冶炼用量最多的造渣剂。
1。
2萤石:萤石可以加速石灰溶解,改善炉渣流动性。
2、造渣工艺
2.1中频炉开机前应首先在炉底加入钢液量2%~3%的石灰打底,初始钢液量按中频炉炉容量的2/3计算。
2。
2 熔化钢水量达到2。
1的要求后,加入硅钙块做沉淀脱氧,加入量按0。
5kg/t钢水量进行计算,5~10分钟后打渣,再加入石灰造新渣覆盖钢液表面。
2.3 造新渣后再次开始加料直至规定钢液量或中频炉满炉为止,打渣,再加入石灰造新渣覆盖。
2.4 根据取样结果微调成分,待合金熔化,钢液成分均匀后,加入硅钙块再次做沉淀脱氧,加入量按0。
5kg/t钢液计算.
2.5 如最后微调成分需要加入Ti、Nb等易氧化元素时,需先用硅钙块做沉淀脱氧后,方可加入该类合金。
2。
6 待钢液成分合格,温度合适后,打渣,再加入石灰、萤石造新渣,熔渣厚度保持30~50mm之间,并不时用渣瓢轻打石灰表面,确保石灰充分溶解,再在钢液表面加入硅钙粉做扩散脱氧,最后保证白渣出钢。
2.7 如2。
6最后造渣不是白渣,应重复上述步骤2-3次,直至白渣为止,且控制最后炉渣碱度在1。
6~2.0左右。
注意保证石灰充分溶解,且留够5分钟左右的反应时间后,方可再次打渣,造渣.
2.8 钢液在底吹氩钢包内镇静时间应不低于3分钟,保证夹杂物充分上浮。
2.9 全程禁止使用铝块做脱氧剂。
- 1、下载文档前请自行甄别文档内容的完整性,平台不提供额外的编辑、内容补充、找答案等附加服务。
- 2、"仅部分预览"的文档,不可在线预览部分如存在完整性等问题,可反馈申请退款(可完整预览的文档不适用该条件!)。
- 3、如文档侵犯您的权益,请联系客服反馈,我们会尽快为您处理(人工客服工作时间:9:00-18:30)。
中频炉熔炼球铁配料计
算方法
公司标准化编码 [QQX96QT-XQQB89Q8-NQQJ6Q8-MQM9N]
配料计算方法
配料计算如下:
(1)计算炉料中各元素的变化
a) 炉料含碳量:C
铁水% = % + C
炉料
%
已知铁水所需的平均含碳量为%,按上式算得 C
炉料
%=%;
b) 炉料含硅量: 已知铁水所需的平均含硅量%,硅的熔炼烧损为15%,则 Si炉料=()=%;
c) 炉料含锰量已知Mn
铁水=%,熔炼烧损20%,故Mn
炉料
=()=%;
d) 炉料含硫量已知S
铁水=%,增硫50%,则:S
炉料
=(1+)=%;
e) 炉料含磷量磷在熔炼过程中变化不大,P
炉料=P
铁水
<%
综合上列计算结果,所需配置的炉料平均化学成分为:
C
炉料%、Si
炉料
%、Mn
炉料
%、S
炉料
<%、P
炉料
<%
(2)初步确定炉料配比
a) 回炉料的配比:主要取决于废品率和成品率,它随具体生产情况而变化。
此处取20%。
b) 新生铁和废钢配比:设新生铁为χ%,则废钢为80%-χ%。
按炉料所需含碳量为%,新生铁、废钢、
回炉料的含碳量各为%、%、%,可列出下式:
χ+(80-χ)+*20=*100
得出χ=%。
故铁料配比为:Z15生铁60%、废钢20%、回炉料20%。
(3)然后按上述配比及各种炉料的成分,计算配合后的炉料成分如表3。
表3 炉料成分
a) 硅铁加入量今缺硅量%,亦即每100公斤炉料需加硅公斤。
所用硅铁含硅量为45%,故每100公斤炉料需加硅铁量为=公斤
b) 锰铁加入量同上法计算,每100公斤炉料需加入含锰75%的锰铁为:=公斤。
(5)制定配料单
根据配比和层铁量,确定每批炉料中各种炉料的重量,写出配料单。
设已知层铁500公斤,可算得每批铁料的组成为:生铁:500*60%=300公斤、废钢:500*20%=100公斤、回炉料:500*20%=100公斤、45%硅铁。