齿轮齿面沉积膜摩擦磨损性能试验研究
摩擦磨损性能测试试验
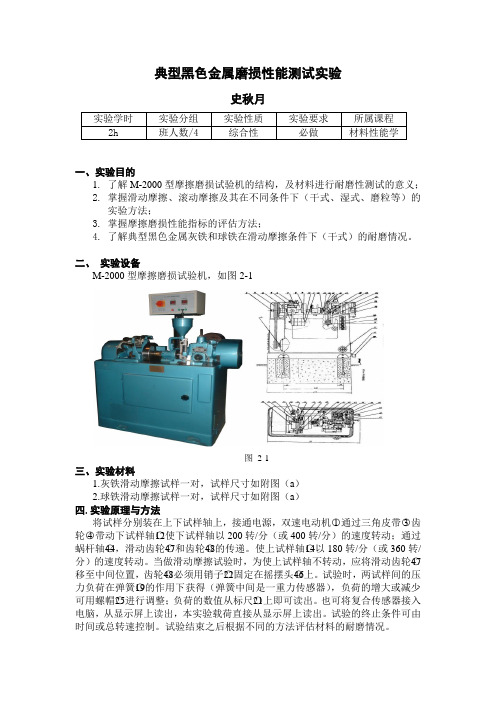
典型黑色金属磨损性能测试实验史秋月实验学时实验分组实验性质实验要求所属课程2h 班人数/4 综合性必做材料性能学一、实验目的1.了解M-2000型摩擦磨损试验机的结构,及材料进行耐磨性测试的意义;2.掌握滑动摩擦、滚动摩擦及其在不同条件下(干式、湿式、磨粒等)的实验方法;3.掌握摩擦磨损性能指标的评估方法;4.了解典型黑色金属灰铁和球铁在滑动摩擦条件下(干式)的耐磨情况。
二、实验设备M-2000型摩擦磨损试验机,如图2-1图2-1三、实验材料1.灰铁滑动摩擦试样一对,试样尺寸如附图(a)2.球铁滑动摩擦试样一对,试样尺寸如附图(a)四.实验原理与方法将试样分别装在上下试样轴上,接通电源,双速电动机○1通过三角皮带○3齿12使下试样轴以200转/分(或400转/分)的速度转动;通过轮○4带动下试样轴○48的传递。
使上试样轴○14以180转/分(或360转/47和齿轮○蜗杆轴○44,滑动齿轮○分)的速度转动。
当做滑动摩擦试验时,为使上试样轴不转动,应将滑动齿轮○47移至中间位置,齿轮○48必须用销子○22固定在摇摆头○46上。
试验时,两试样间的压力负荷在弹簧○19的作用下获得(弹簧中间是一重力传感器),负荷的增大或减少21上即可读出。
也可将复合传感器接入可用螺帽○25进行调整;负荷的数值从标尺○电脑,从显示屏上读出,本实验载荷直接从显示屏上读出。
试验的终止条件可由时间或总转速控制。
试验结束之后根据不同的方法评估材料的耐磨情况。
五、实验内容将加工好的滑动摩擦试样装在实验机上,在给定的条件下(干式、滑动摩擦、压力:200N、时间60min)进行试验,试验结束后将试样取下,评估耐磨性能。
根据所选取磨损试验方法的不同以及材料本质的差异,可以选择不同的耐磨性能评定方法,以期获得精确的试验数据,现简单例举下述几种方法以供参考。
1、称重法:采用试样在试验前后重量之差,本表示耐磨性能的方法,由于两试样之间的摩擦所引起的磨损量,可以采用精度达万分之一的分析天平称量出试样试验前后重量之差非凡获得。
工程机械齿轮的表面改性层及其摩擦磨损性能

工程机械齿轮的表面改性层及其摩擦磨损性能摘要:为了满足工程机械齿轮高硬度、常温和高温耐磨性的要求,采用双层辉光等离子表面改性技术在齿轮钢基体上制备了 W-Mo共渗层,对 W-Mo 共渗层的成分与显微形貌进行了分析,并与齿轮钢基体和固体渗碳层的硬度和耐磨性能进行了对比分析。
关键词:工程机械齿轮;表面改性层;摩擦磨损性能随着中国制造 2025、工业4.0等概念的提出,工程机械制造领域迎来了巨大的发展机遇,由于工程机械齿轮需要长期在高载荷和高转速的苛刻环境中运行,同时工作温度已经提高至 350 ℃及以上,这对齿轮钢的表面性能提出了越来越高的要求。
虽然采用传统热处理的方法可以实现齿轮钢的表面强化,但是提高幅度有限,且在高温作用下会发生软化而降低使用性能等。
一、试验材料及方式方法近年来,随着表面改性技术的快速发展以及齿轮服役环境的日益恶化,高能束表面强化、离子注入等表面处理技术不断应用到齿轮上,虽然各自都取得了一定进展,但是又存在明显局限性,如激光淬火所需的设备大、成本高、扫描区之间存在软带,离子注入深度不足,改性层与基体结合力低等。
双辉等离子表面冶金技术作为一种新型表面改性技术,在高速钢锯条、胶体磨、化工零件和低碳钢上都有成功应用,因此,本文拟以具有高熔点、高硬度的W、Mo元素为原料,采用双辉等离子表面改性技术在工程机械齿轮上制备W-Mo共渗层,其结果对于齿轮钢表面技术的发展以及齿轮服役性能的提高都具有重要的参考意义。
选用商业16Cr3Ni WMo VNb E齿轮钢为试验原料。
在进行表面改性处理前,采用线切割方法加工成 15 mm ×15 mm × 5 mm试样,60 ~ 800号砂纸逐级打磨后,采用金刚石研磨膏抛光后,清水冲洗后置于酒精中超声波清洗,然后吹干备用。
分别对齿轮钢试样进行双辉W-Mo 共渗和固态渗碳: ①采用NMH-3 型双层辉光等离子表面冶金试验炉在试样表面制备W-Mo共渗改性层,源极材料为100 mm × 5 mm的20% W-80% Mo合金靶材,保护气为纯度高于99.6%的高纯氩气,温度 860 ℃、源极电压为 950 V、阴极电压500 V、气压 38 Pa、极间距18 mm,保温时间为 3 h;②在 QNT-12-3 箱式电阻炉中对试样表面进行固体渗碳处理,具体过程包括将试样置于渗碳剂中并加热至 930 ℃保温4 h,之后出炉油淬并进行360 ℃ × 2 h 回火处理,然后空冷至室温。
齿轮表面改性技术研究现状
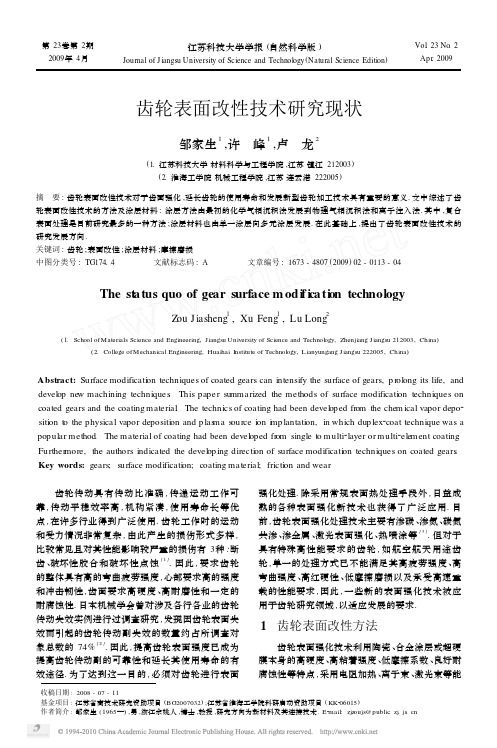
第23卷第2期2009年4月江苏科技大学学报(自然科学版)Journal of J iangsu University of Science and Technol ogy (Natural Science Editi on )Vol .23No .2Ap r .2009齿轮表面改性技术研究现状邹家生1,许 峰1,卢 龙2(1.江苏科技大学材料科学与工程学院,江苏镇江212003)(2.淮海工学院机械工程学院,江苏连云港222005)摘 要:齿轮表面改性技术对于齿面强化,延长齿轮的使用寿命和发展新型齿轮加工技术具有重要的意义.文中综述了齿轮表面改性技术的方法及涂层材料:涂层方法由最初的化学气相沉积法发展到物理气相沉积法和离子注入法.其中,复合表面处理是目前研究最多的一种方法;涂层材料也由单一涂层向多元涂层发展.在此基础上,提出了齿轮表面改性技术的研究发展方向.关键词:齿轮;表面改性;涂层材料;摩擦磨损中图分类号:TG174.4 文献标志码:A 文章编号:1673-4807(2009)02-0113-04收稿日期:2008-07-11基金项目:江苏省高技术研究资助项目(BG2007032);江苏省淮海工学院科研启动资助项目(KK 206015)作者简介:邹家生(1965—),男,浙江余姚人,博士,教授,研究方向为新材料及其连接技术.E 2mail:zjz oujs@public .zj .js .cnThe st a tus quo of gear surface m od i f i ca ti on technologyZou J iasheng 1,Xu Feng 1,Lu Long2(1.School of Materials Science and Engineering,J iangsu University of Science and Technol ogy,Zhenjiang J iangsu 212003,China )(2.College of Mechanical Engineering,Huaihai I nstitute of Technol ogy,L ianyungang J iangsu 222005,China )Abstract:Surface modificati on techniques of coated gears can intensify the surface of gears,p r ol ong its life,and devel op ne w machining techniques .This paper summarized the methods of surface modificati on techniques on coated gears and the coating material .The technics of coating had been devel oped fr om the che m ical vapor depo 2siti on t o the physical vapor depositi on and p las ma s ource i on i m p lantati on,in which dup lex 2coat technique was a popular method .The material of coating had been devel oped fr om single t o multi 2layer or multi 2ele ment coating .Further more,the authors indicated the devel op ing directi on of surface modificati on techniques on coated gears .Key words:gears;surface modificati on;coating material;fricti on and wear 齿轮传动具有传动比准确,传递运动工作可靠,传动平稳效率高,机构紧凑,使用寿命长等优点,在许多行业得到广泛使用.齿轮工作时的运动和受力情况非常复杂,由此产生的损伤形式多样,比较常见且对其性能影响较严重的损伤有3种:断齿、破坏性胶合和破坏性点蚀[1].因此,要求齿轮的整体具有高的弯曲疲劳强度,心部要求高的强度和冲击韧性,齿面要求高硬度、高耐磨性和一定的耐腐蚀性.日本机械学会曾对涉及各行各业的齿轮传动失效实例进行过调查研究,发现因齿轮表面失效而引起的齿轮传动副失效的数量约占所调查对象总数的74%[2].因此,提高齿轮表面强度已成为提高齿轮传动副的可靠性和延长其使用寿命的有效途径.为了达到这一目的,必须对齿轮进行表面强化处理.除采用常规表面热处理手段外,日益成熟的各种表面强化新技术也获得了广泛应用.目前,齿轮表面强化处理技术主要有渗碳、渗氮、碳氮共渗、渗金属、激光表面强化、热喷涂等[3].但对于具有特殊高性能要求的齿轮,如航空航天用途齿轮,单一的处理方式已不能满足其高疲劳强度、高弯曲强度、高红硬性、低摩擦磨损以及承受高速重载的性能要求,因此,一些新的表面强化技术被应用于齿轮研究领域,以适应发展的要求.1 齿轮表面改性方法齿轮表面强化技术利用陶瓷、合金涂层或超硬膜本身的高硬度、高粘着强度、低摩擦系数、良好耐腐蚀性等特点,采用电阻加热、离子束、激光束等能114 江苏科技大学学报(自然科学版)第23卷源作为蒸发源或溅射源,在齿轮表面涂敷一层或多层涂层,以提高齿轮表面硬度,降低摩擦系数,增加耐磨性,延长齿轮使用寿命.利用涂层的这些特性,有望用水基代替油基润滑,不仅节约了成本,还对环境保护和可持续发展有着十分重要的意义.常用的涂层齿轮表面强化技术有:化学气相沉积技术(Che m ical Vapor Depositi on,CVD)、物理气相沉积技术(Physical Vapor Depositi on,P VD)、全方位离子注入技术(Plas ma Source I on I m p lantati on,PSII)等[4].1.1 化学气相沉积法文献[5]对涂层在齿轮上的应用做了开创性的探索研究工作,用CVD法沉积Ti C或Ti N陶瓷膜,通过在有润滑油和干摩擦的条件下,分别研究其摩擦磨损性能,发现镀覆陶瓷涂层后,齿轮副的抗咬合性和抗划伤能力都得到大幅强化.受条件所限,当时使用的CVD技术缺点也十分明显,即处理温度过高,通常保持在900~1100℃范围,超过了绝大多数齿轮材料的热处理温度,导致金相组织发生改变,整体硬度下降,需在表面改性处理后对齿轮重新淬火,增加了成本,尺寸精度也难以控制;且在高温下,基体材料晶粒长大,渗碳层形成氧化脱碳层,导致零件耐摩抗磨性能下降;还存在着渗碳时间长,能量消耗大,污染环境等问题[6].上述原因限制了CVD法制备表面涂层齿轮的应用,对其研究也基本停止.1.2 物理气相沉积法P VD技术作为一种新型的表面改性技术已有多年的实践,其工艺处理温度可控制在500℃以下,解决了C VD法无法克服的高温软化问题.在P VD 技术中,真空蒸镀技术出现较早,但由于膜与基体的结合力不强,多用于装饰和半导体元件.1963年,美国Sandia公司的D.M.Matt ox率先提出离子镀(I on Plating)技术.2年后,I B M公司研制出射频溅射法.离子镀、溅射镀与蒸镀构成了P VD的3大系列.目前,真空离子镀技术获得极大的发展,已广泛应用在刀具、模具、活塞环等部件的处理上.与真空蒸镀和溅射镀等技术相比,离子镀具有结合性能好、绕射性能好、便于使膜材粒子散射在整个工件表面上、可镀材质广、沉积速率快等优点,离子镀还具有结合强度高、可多元成膜、可精确控制温度和涂层厚等优点.近年来,这一技术已应用到齿轮的表面强化处理.通过真空离子镀技术制备的涂层齿轮可大辐降低摩擦系数,提高耐摩擦抗磨损能力,该技术是目前齿轮表面强化技术领域研究的热点和重点.1.3 离子注入法PSII就是将几万至几十万电子伏特的高能离子注入到齿轮表面,使材料表面层的物理、化学和机械性能发生变化,具有注入离子能量高、注入层与基体结合牢固、处理温度低等优点.与C VD和P VD相比,PSII技术的处理温度更低,可控制在120℃对20Cr M o钢齿轮进行表面强化处理,提高表面硬度和耐摩抗磨性[7].该技术处理温度低,齿轮不变形,基体的组织也未发生变化.其缺点是注入层深度不足,厚度仅达0.35~1.5μm,这也限制了其在齿轮表面强化技术上的应用.2 涂层材料的发展2.1 T i N陶瓷涂层离子镀Ti N陶瓷涂层是目前应用最广泛的一种表面改性涂层,具有高硬度、高粘着强度、低摩擦系数、良好的抗腐蚀性等特点,已广泛应用在各个领域,特别是在刀具、模具行业.影响陶瓷涂层在齿轮上应用的主要原因是陶瓷涂层与基体之间的结合力问题.由于齿轮的工作条件和影响因素远比刀具、模具复杂,致使单一的Ti N涂层在齿轮表面处理上的应用受到很大制约.陶瓷涂层具有高硬度、低摩擦系数、耐腐蚀等优点,但脆性大,且难以获得较厚的涂层,故需要硬度高、强度高的基体支撑涂层,才能发挥其特点.所以,陶瓷涂层多用于硬质合金及高速钢表面.而齿轮材料相对于陶瓷材料较软,基体材料与涂层材料性质悬殊,导致涂层和基体结合不牢,对陶瓷涂层支持不足,在使用中容易发生陶瓷涂层的脱落,非但不能发挥陶瓷涂层的作用,甚至脱落的陶瓷涂层颗粒形成磨粒磨损,增加磨损量.目前的解决方法就是采用复合表面处理,改善陶瓷与基体之间结合力.复合表面处理指物理气相沉积涂层与其它表面处理工艺或涂层相结合,采用两种单独的表面/次表面对基体材料表面进行改性,以获得通过单一表面处理工艺所不能达到的复合机械性能.离子氮化和物理气相沉积Ti N复合涂层是目前研究最多的一种.它最早在20世纪80年代由K orhonen等人首先提出[8].文献[9-10]研究了在32Cr2Mo V钢齿轮基体上涂敷Ti N复合涂层,经过正交法实验优化32Cr2MoV钢的复合表面处理工艺.研究表明:等离子氮化基体和Ti N陶瓷复合涂层具有强的结合力,抗摩擦磨损能力得到显著增加.与没有经过离子氮化处理的基体相比,等离子氮化后,第2期邹家生,等:齿轮表面改性技术研究现状115 32Cr2Mo V钢更适合沉积陶瓷涂层.此外,笔者对40Cr钢齿轮材料进行离子氮化和P VD复合镀Ti N涂层研究,结果表明,复合镀膜处理后表面光滑平整,陶瓷涂层与基体的结合力良好,减摩抗磨效果明显.2.2 多层、多组元T i N涂层20世纪90年代,人们通过多层、多组元涂层设计来提高Ti N涂层刀具的性能[11].近几年,在二元Ti N涂层基础上研制出的一些多组元涂层或多层涂层,如Ti-C-N,Ti-C-N-B,Ti-A l-N,Ti-B-N,Ti N/A l2O3等.在Ti N涂层中加入A l,Si等元素可以提高其高温抗氧化性及硬度,加入B元素等可提高其硬度及附着强度,Ti N沉积在Ti衬底上具有较高的附着力和较高的耐腐蚀性等.由于多组元成分的复杂性,对此研究也存在很多争议.在对(Tix ,Cr1-x)N多组元涂层的研究中,研究结果存在争议.有人认为(Tix ,Cr1-x)N涂层是以Ti N为基,Cr只能以置换固溶体的形式存在于Ti N点阵中,不能作为独立的Cr N相存在[12];另外一些研究表明:(Tix ,Cr1-x)N涂层中Cr原子直接置换Ti原子数量有限,其余的Cr则以单质态存在或与N形成化合物[13].相关实验结果表明:涂层中添加Cr能减小表面颗粒尺寸,提高硬度,当Cr的质量百分含量达到31%时,涂层硬度达到最高值,此时涂层的内应力也最大.由于齿轮表面改性技术与刀具、模具相比,研究起步比较晚,但性能要求有共性,可以利用后发优势,充分利用刀模具表面改性新技术,将这一多组元、多层涂层技术应用到齿轮表面改性中,成为齿轮表面改性的发展方向.2.3 其它涂层除了Ti N涂层外,WC/C,B4C膜等其它陶瓷涂层材料在齿轮表面上应用也得到关注.文献[14]利用P VD技术在FEZ-A和FEZ-C齿轮表面沉积WC/C与B4C薄膜,实验表明:P VD镀层显著减少摩擦,不易出现热胶接或胶合,提高2~3个系数的载荷能力.文献[15]尝试利用P VD涂层的优良减摩抗磨性能,取消润滑油,进行干摩擦实验研究,取得了良好的实验效果.目前,超硬膜也日益受到世人瞩目,它是指硬度大于40GPa、具有优异的抗摩擦磨损性能、高热导率、低摩擦系数和热膨胀系数的固体薄膜,主要是非晶金刚石膜和C-N膜.非晶金刚石膜(Amor2 phous D ia mond Fil m)具有非晶特性,没有长程有序结构,含有大量C-C四面体键,所以也常被称为四面体非晶碳膜(Tetrahedral Amor phous Carbon Fil m,ta-C)[16].类金刚石涂层作为一种非晶碳膜,具有诸多类似于金刚石的优良特性.如热导率高、热膨胀系数小、化学稳定性好、高硬度和弹性模量、良好耐磨性及低摩擦系数等.研究表明在齿轮表面涂覆类金刚石膜后,其使用寿命延长了6倍,抗疲劳性能有显著提高.国内有学者对C-N薄膜在20Cr M o钢齿轮上应用做了相关研究,并与P VD法镀Ti N涂层进行比较研究.齿轮的摩擦磨损实验表明:在相同条件下,采用多弧离子镀方法在渗碳淬火齿轮表面镀Ti N涂层时,处理温度高于20Cr M o钢的回火温度,导致齿轮回火,基体硬度降低,抗磨性能急剧降低;而采用磁过滤弧源沉积的方法在齿轮表面沉积的C-N涂层由于其温度低,不会产生回火现象,基体的金相组织和表面硬度基本未改变,显著提高了齿轮的减摩抗磨性[7].合金耐磨涂层也被尝试应用在齿轮上,例如在45#钢齿轮齿面电沉积N i-P-Co合金层,使合金层获得超细晶粒组织,可以显著提高其接触疲劳强度,延长接触疲劳寿命达1.144~1.533倍.当N i-P-Co合金层在400~500℃温度下热处理,合金沉积层结构产生变化,合金层中P原子偏聚富集,与N i生成N i3P,合金沉积层为N i和N i3P的混合物,合金层显微硬度提高[17].还有学者研究在Cu-Cr-P新型合金铸铁齿轮齿面涂镀Cu金属层和N i-W合金涂层,提高其接触疲劳强度.在HT250铸铁齿轮齿面上涂镀N i-W和N i-Co合金涂层,与未涂镀的相比,可以提高铸铁齿轮的耐磨损性能达4~6倍[18219].3 结论齿轮表面改性技术对于齿面强化,延长齿轮的使用寿命和发展新型齿轮加工技术具有重要的意义,已经逐渐成为国内外研究高性能齿轮的热点.但目前的研究仍处在探索阶段,要使齿轮表面改性技术进一步完善并实用化,尚有许多工作需要开展.研究的热点主要集中在以下方面:1)开展齿轮表面涂敷多层复合Ti N陶瓷涂层的工艺研究,以进一步减小涂层内应力,增大涂层厚度,增强涂层附着力,实现涂层齿轮的工业化应用.2)研究新型的多层、多元高硬度、高韧性涂层在齿轮表面的沉积工艺及其对齿轮性能的影响.如将新型Ti-B-N,(Tix,Cr1-x)N等多元复合涂层引入齿轮表面改性工程.3)研究涂层加工过程中的热影响以及不同的116 江苏科技大学学报(自然科学版)第23卷涂层厚度对齿轮尺寸精度、传动性能的影响.4)研究中低合金钢、铸钢等不同材质齿轮的表面改性技术,拓展此项技术的应用范围.参考文献(References)[1]曲敬信,汪鸿宏.表面工程手册[M].北京:化学工业出版社,1998.[2]日本机械学会技术资料出版分科.齿轮强度设计资料[M].李茹贞,赵清慧,译.北京:机械工业出版社,1984.[3]张津,程晓萍.齿轮材料及齿轮表面工程技术发展现状[J].机械工艺师,1999(2):36-39.Zhang J in,Chen Xiaop ing.The status quo of gear material and surface modificati on technol ogy[J].M achinery M anufacturing Engineer,1999(2):36-39.(in Chinese) [4]Lu Long,Lyu S K.A study on the fricti on and wear char2acteristics of C-N coated s pur gear[J].Journal of KSTL E,2004,20(5):272-277.[5]Terauchi Y,Nadanot H,KohnotM,et al.Scoring resist2ance of Ti C and Ti N coated gears[J].Tribology Interna2 tional,1987,20(5):248-254.[6]闻立时,黄荣芳.离子镀硬质膜技术的最新进展和展望[J].真空,2000(1):1-11.W en L ishi,Huang Rongfang.Ne w p r ogress in Ti N2based p r otective coatings deposited by arc i on p lating[J].V acu2 um,2000(1):1-11.(in Chinese)[7]钱文富,曹兴进,卢龙,等.表面处理和涂层技术在齿轮上的应用初探[J].重庆大学学报:自然科学版,2005,28(2):1-4.Q ian W enfu,Cao Xingjin,Lu Long,et al.Surface treat2 ment and coating technol ogies on gears[J].Journal of Chongqing U niversity:N atural Science Edition,2005,28(2):1-4.(in Chinese)[8]Korhonen A S,Sirvi o E H,Sul one M S.Plas ma nitridingand i on p lating with an intensified gl ow discharge[J].Thin Solid Fil m s,1983,107:387-394.[9]李晖,李润方,许洪斌,等.不同表面状态的32Cr2MoV的滑动摩擦试验比较[J].材料导报,2006,20(11):144-146,149.L i Hui,L i Runfang,Xu Hongbin,et al.The analyses of sliding2fricti on ex peri m ent of32Cr2Mo V with different trea2 ted surface[J].M aterials Revie w,2006,20(11):144-146,149.(in Chinese)[10]李晖,李润方,许洪斌,等.32Cr2MoV复合镀Ti N的滑动摩擦试验分析[J].热加工工艺,2006,35(16):42-44,46.L i Hui,L i Runfang,Xu Hongbin,et al.Analysis ofsliding2fricti on experi m ent of dup lex2coated32Cr2MoV[J].Hot W orking Technology,2006,35(16):42-44,46.(in Chinese)[11]Holleck H,Schier V.M ultilayer P VD coatings f or wearp r otecti on[J].Surf Coat Technol,1993,328:76-77.[12]陈军,林国强,陈静,等.电弧离子镀(Ti,Cr)N硬质薄膜的成分、结构与硬度[J].大连理工大学学报,2002,42(5):555-559.Chen Jun,L in Guoqiang,Chen J ing,et posi2 ti on,Structure and hardness of(Ti,Cr)N fil m s deposi2 ted by arc i on p lating[J].Journal of D alian U niversityof Technology,2002,42(5):555-559.(in Chinese) [13]左洪波.离子镀(Ti,Cr)N涂层的组织结构与耐蚀性能的研究[J].哈尔滨理工大学学报,1998,3(6):33-35.Zuo Hongbo.Study on structure and corr osi on resisting p r operty of the coating of i on p lating(Ti,Cr)N[J].Journal of Harbin U niversity of Science and Technology,1998,3(6):33-35.(in Chinese)[14]Franz J,Norbert K.I nfluence of coatings and surfacei m p r ove ments on the lifeti m e of gears[J].D rive Syste mTechnique,2007,21(3):3-13.[15]W alt on D.The wear of unlubricated metallic s pur gear[J].W ear,1998,222:103-113.[16]Lossy R,Pappas D L,Roy R A,et al.Pr operties of a2mor phous dia mond fil m s p repared by a filtered cathodicarc[J].J A ppl Phys,1995,77(9):47-50.[17]李小周,黄华梁.表面电沉积合金层提高碳钢齿轮的接触疲劳强度研究[J].工程设计学报,2002,9(4):211-214.L i Xiaozhou,Huang Hualiang.Research on contact2fa2 tigue strength of45#steel geardrives with N i2P2Co all oycoating[J].Journal of Engineering D esign,2002,9(4):211-214.(in Chinese)[18]温芳,黄华梁,朱江新,等.涂镀合金层的铸铁齿轮耐磨损性能的研究[J].表面技术,2004,33(3):32-34.W en Fang,Huang Hualiang,Zhu J iangxin.Research onthe wear2resisting p r operty of grey cast i orn gear surface with all oy coating[J].Surface Technology,2004,33(3):32-34.(in Chinese)[19]李小周,黄华梁,温芳.涂镀合金层的合金铸铁齿轮的接触疲劳强度研究[J].中国表面工程,2002,15(3):36-39.L i Xiaozhou,Huang Hualiang,W en Fang.Research onthe contact fatigue p r operty of grey cast i orn gear surface with all oy coating[J].China Surface Engineering,2002,15(3):36-39.(in Chinese)(责任编辑:顾 琳)。
齿轮渗碳、渗氮硬化表面耐磨性研究

256管理及其他M anagement and other齿轮渗碳、渗氮硬化表面耐磨性研究李晓喆(太重煤机有限公司,山西 太原 030032)摘 要:在工业化、现代化的过程中,机械传动系统已经逐渐成为现代工业不可缺少的重要技术核心。
作为机械设备的核心构件,齿轮的耐磨性是确保传动系统正常可靠工作的重要指标。
而渗碳与渗氮热处理工艺是当前表面硬化技术中的热点问题,本文分析了不同齿轮表面硬化技术的优缺点,通过渗碳与渗氮热处理加工后的齿轮耐磨性能比较分析,确定了渗氮气体处理方式在低载荷变速齿轮处理温度、耐磨性能方面的优势。
关键词:变速齿轮;渗碳加工;渗氮加工;表面硬化;耐磨性中图分类号:TG156.8;U463.2 文献标识码:A 文章编号:11-5004(2018)06-0256-2传动系统是现代机械工业中的核心机械构件,而齿轮则是增速传动系统中的关键部件。
现代机械中大多数的能量传达都是通过齿轮组来实现的,包括工业减速设备、变速齿轮组等。
而我国齿轮制造工业也在中国现代工业腾飞的过程中,保持了快速发展的态势。
在种类丰富的众多产品中,变速齿轮具有安全性高、结合性好、稳定性强、性价比高等多种有点,在通用机械设备中具有不可替代的作用[1]。
在这种产品发展环境下,必须不断提高变速齿轮的加工制造工艺,提高产品的使用寿命,才能为齿轮制造业的发展提供充足的动力支持。
1齿轮表面强化技术1.1 渗碳技术渗碳热处理工艺能够提高齿轮产品的表面硬度,增强齿轮的耐受摩擦性能,而齿轮工件的基质部分仍然可以保持板条状马氏体组织结构,能够确保齿轮具有较强的韧性,确保变速齿轮本身的物理力学性能指标较高。
所以在渗碳热处理加工的齿轮工件使用过程中,可以耐受较高的荷载力。
传统的渗碳工艺温度保持在930摄氏度,生产工艺的整体周期较长,生产效率相对较低未下。
而在现代工艺的发展环境下,高温渗碳技术为现代齿轮制造提供了新的技术支持,可以有效提高齿轮生产工艺的效率。
齿轮传动中磨损问题研究方法综述

摘
要: 齿轮 传动 是机 器传 递运动 和动 力的一 种 主要 形式 , 如何 减 少齿轮 工 作 中的磨 损 ; 长题。总结 了目 前齿轮接触问题的数值研究方法、 齿轮 磨损问题的研 究历程等 , 并对齿轮磨损问题研 究的发展 方向提 出建议。
节点传递力和位移, 通过数值方法求解出接触节点位移或应力值之后 , 再按规定的位移模式得到整个结构的 位移分布和应力场。有 限元方法是一种有效的结构分析手段 , 国外 已研制了许多成熟的大型有限元分析软 件 , s P A IA、 A T A A S S I da 等。我国在齿轮的有 限元分析方面也开展了不少工作 , 如 . 、 DN M S R N、 N Y 、— es A 如计
维普资讯
第2 8卷
第 3期
河 北 理 工 学 院 学 报
J u n lo b i n t u eo c n lg o r a fHe e si t fTe h oo y I t
Vo . No 3 I28 . Au . 0 6 g 2 0
啮合问题而且可以处理双齿对啮合 问题。白少先¨ 利用有 限元分析方法 , 对双圆弧弧齿锥齿轮的弯曲强度 进行了多方面的研究 , 给出一种接触区载荷分布的计算 方法 , 分析 了齿根弯曲应力的分布规律。包 家汉¨
等利用 A S S N Y 软件 , 研究了一对直齿圆柱齿轮啮合过程中 , 随啮合位置的变化, 齿面接触应力和齿问载荷分 配的情况。太原理工大学 的吴凤林教授 - 利用三维有限元法对准端 面双圆弧齿轮的齿根应力进行 了分析, 1 得出齿根应力与设定螺旋角以及与设定齿厚 比的关系 , 准端面双圆弧齿轮应力沿齿高方向等强度分布。
中图分 类 号 :H 17 1 文献 标识 码 : T 1. A
磨损的测试技术

切槽法:切槽法测磨 损与压痕法十分相似, 用回转刀具刻出月牙 形槽,切槽法排除了 弹性变形回复和四周 鼓起的影响.根据几 何关系,切槽宽度和 磨损深度的关系为:
r-刀刃的回转半径;R-试件 的表面曲率半径,平面时 R=∞,凸面用+,凹面用压痕法和切槽法只适用于磨损量不大而表面光滑的试件. 由于这两种方法都要局部破坏试件的表层, 因而不能用于 研究磨损过程中表面层的组织结构的变化.
定量铁谱分析: 通常先采用铁谱光密度计来测量铁谱片上不
同位置上磨粒沉积物的光密度,从而求得磨粒的尺 寸、大小分布以及微粒总量. 所谓光密度是投射过透明铁谱片的光强度与透射 过含有磨粒的铁谱片的光强度之比,与磨屑的覆盖 面积成正比,那么用光密度值就可以推算铁谱片上 磨屑量的多少.
一般在铁谱片上55mm大磨粒沉积处和49mm小 磨粒沉积处两处测量磨粒的光密度,以AL和AS分别 表示大、小磨粒光密度的读数.通过测出铁谱片上 大、小磨粒的光密度,由此确定大磨粒和小磨粒的 相对含量.
1、摩擦系四数、或摩摩擦擦力磨的损测实量验中的参数测量
① 机械式:
载荷W通过上试件1加到下试件2上
.下试件半径为r旋转,上试件固定. 试样间的摩擦力使下主轴产生一 个力矩,此时与主轴相连的砝码产 生一个偏角,来平衡摩擦力产生的
摩擦力矩,偏角反应了摩擦力矩P
的大小,可以直接从标尺读出,由 此摩擦力矩可以换算出试件上的 摩擦系数μ
例如:正常磨损的磨屑一般呈薄片状; 磨粒和切削磨损形成的磨屑具有螺旋状或卷曲状, 这种磨粒的集中出现是严重磨损过程的表现,若数 目急剧增多,则表面机器损坏即将开始. 氧化磨损或腐蚀磨损形成的磨屑是由化合物组成的, 在有色光作用下不同成分的磨料显示出不同的颜色, 以此确定磨粒的材料类型,进而判断磨损的具体位 置.
齿面微观形态对齿轮耐磨性能影响的试验研究

写一篇齿面微观形态对齿轮耐磨性能影响的试验研究的报告,
600字
齿面微观形态对齿轮耐磨性能影响的试验研究
本文介绍了一项关于齿面微观形态对齿轮耐磨性能影响的试验研究。
首先,本实验从材料方面出发,选择了合金钢作为试验材料。
其次,针对抗磨类材料的齿轮设计,采用了不同的齿面微观形态,分别为齿面圆柱形、椭圆形和多圆柱形。
接下来,实验中采用了特定的齿轮抗磨和摩擦测试设备,并进行了相应的耐磨性能测试。
测试结果表明,在三种不同的齿面微观形态中,多圆柱形的齿面的耐磨性能最好。
因此,多圆柱形齿面的齿轮可以提供良好的抗磨性能。
本试验结果表明,在抗磨类材料的齿轮设计中,多圆柱形的齿面微观形态可以提高齿轮的耐磨性能。
理论上,多圆柱形的齿面可以充分利用抗磨类材料的特性,提高齿轮的耐磨性能。
因此,在齿轮材料设计和应用中,齿面微观形态是一项重要的研究内容,其研究结果可以为更高效的齿轮设计提供参考。
综上所述,本文讨论了一项关于齿面微观形态对齿轮耐磨性能影响的试验研究。
实验结果表明,多锥柱形的齿面的齿轮可以提供良好的抗磨性能。
本实验的结果为更高效的齿轮设计提供了参考,对于齿轮材料设计和应用具有重要的意义。
重载、高速齿轮用a-C-WC薄膜的制备及摩擦学性能研究

重载、高速齿轮用a-C-WC薄膜的制备及摩擦学性能研究重载、高速齿轮用a-C/WC薄膜的制备及摩擦学性能研究摘要:重载和高速齿轮广泛应用于工业生产中,其摩擦学性能对传动系统的性能有着重要影响。
为了提高齿轮的耐磨性和摩擦性能,本研究利用化学气相沉积(CVD)技术制备了一种新型的a-C/WC(亚金刚石/碳化钨)薄膜,并对其制备方法进行了详细介绍。
此外,还对a-C/WC薄膜的物理性质和摩擦学性能进行了系统研究。
研究结果表明,a-C/WC薄膜具有优异的耐磨性、低摩擦系数和良好的化学稳定性,适用于重载和高速齿轮应用。
关键词:重载齿轮、高速齿轮、a-C/WC薄膜、摩擦学性能引言:重载和高速齿轮作为机械传动系统中重要的组成部分,承载着巨大的负载和高速运动的要求。
在实际工作过程中,齿轮常常面临着高温、高压、高速等苛刻的工作环境,因此,其摩擦学性能对传动系统的工作性能和寿命有着重要影响。
传统的涂层材料如TiN、TiCN等在高负载和高温条件下容易发生剥落和氧化等问题,因此迫切需要开发新型的耐磨涂层材料。
实验方法:本研究采用化学气相沉积(CVD)技术制备了a-C/WC薄膜,其制备方法如下:首先,在硬质合金基材表面沉积一层碳化钨(WC)薄膜,然后利用热丝反应炉在500~800°C的温度范围内,将甲烷和乙烯分解成C2H2保护气体,通过控制沉积时间和比例,使碳原子与钨原子发生化学反应,形成a-C/WC复合涂层。
制备的薄膜在光学显微镜下进行表面形貌和厚度的观察,通过扫描电子显微镜(SEM)和透射电子显微镜(TEM)对薄膜的微观结构进行分析。
结果与讨论:经过CVD制备的a-C/WC薄膜具有良好的致密性和适当的结晶度。
薄膜的表面呈现出光滑的形貌,并具有较高的硬度和良好的抗磨性能。
通过摩擦学测试,发现a-C/WC薄膜具有低摩擦系数和良好的耐磨性,其摩擦系数约为0.1左右。
此外,a-C/WC薄膜的磨损机制主要是以微粒疲劳剥落为主,这种疲劳剥落机制可以改善涂层的摩擦学性能。
齿轮啮合面磨损分析报告
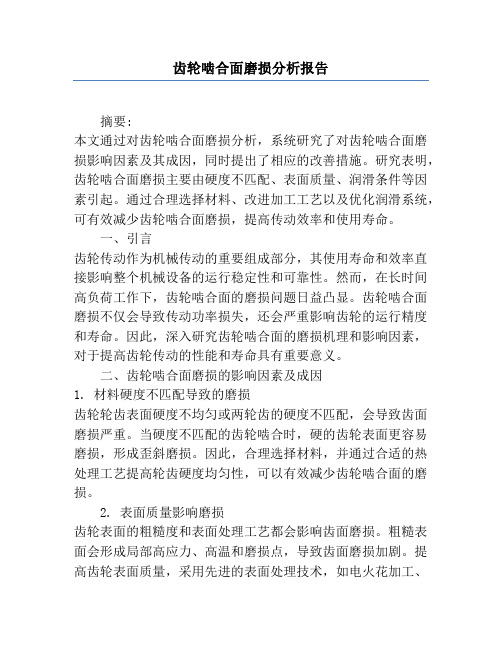
齿轮啮合面磨损分析报告摘要:本文通过对齿轮啮合面磨损分析,系统研究了对齿轮啮合面磨损影响因素及其成因,同时提出了相应的改善措施。
研究表明,齿轮啮合面磨损主要由硬度不匹配、表面质量、润滑条件等因素引起。
通过合理选择材料、改进加工工艺以及优化润滑系统,可有效减少齿轮啮合面磨损,提高传动效率和使用寿命。
一、引言齿轮传动作为机械传动的重要组成部分,其使用寿命和效率直接影响整个机械设备的运行稳定性和可靠性。
然而,在长时间高负荷工作下,齿轮啮合面的磨损问题日益凸显。
齿轮啮合面磨损不仅会导致传动功率损失,还会严重影响齿轮的运行精度和寿命。
因此,深入研究齿轮啮合面的磨损机理和影响因素,对于提高齿轮传动的性能和寿命具有重要意义。
二、齿轮啮合面磨损的影响因素及成因1. 材料硬度不匹配导致的磨损齿轮轮齿表面硬度不均匀或两轮齿的硬度不匹配,会导致齿面磨损严重。
当硬度不匹配的齿轮啮合时,硬的齿轮表面更容易磨损,形成歪斜磨损。
因此,合理选择材料,并通过合适的热处理工艺提高轮齿硬度均匀性,可以有效减少齿轮啮合面的磨损。
2. 表面质量影响磨损齿轮表面的粗糙度和表面处理工艺都会影响齿面磨损。
粗糙表面会形成局部高应力、高温和磨损点,导致齿面磨损加剧。
提高齿轮表面质量,采用先进的表面处理技术,如电火花加工、磨削等,可以有效减少齿轮啮合面的磨损。
3. 润滑条件对磨损的影响良好的润滑条件对齿轮的稳定工作和寿命起着至关重要的作用。
润滑油的种类、粘度和供油方式等因素直接影响齿轮的润滑效果。
如果润滑不良,齿轮啮合面间的磨擦增大,磨损也会加剧。
因此,在齿轮设计和使用过程中,应根据实际工况选择合适的润滑油,并确保润滑系统正常工作。
三、改善措施1. 合理选择材料在齿轮制造过程中,选择适合的材料对于减少齿轮啮合面磨损至关重要。
应根据实际工作条件和要求,选择硬度适中、强度高的材料进行制造,确保齿轮表面硬度均匀,减少硬度差异带来的磨损。
2. 改进加工工艺通过改进加工工艺,提高齿轮表面质量,可以有效减少齿轮啮合面的磨损。
不同润滑条件下碳钢齿轮齿面磨损和点蚀研究

收稿日期:2022-06-11作者简介:张胜男(1988-)ꎬ女ꎬ辽宁铁岭人ꎬ东北大学博士研究生ꎻ孙志礼(1957-)ꎬ男ꎬ山东巨野人ꎬ东北大学教授ꎬ博士生导师.第44卷第7期2023年7月东北大学学报(自然科学版)JournalofNortheasternUniversity(NaturalScience)Vol.44ꎬNo.7Jul.2023㊀doi:10.12068/j.issn.1005-3026.2023.07.008不同润滑条件下碳钢齿轮齿面磨损和点蚀研究张胜男ꎬ孙志礼ꎬ郭凡逸ꎬ王㊀健(东北大学机械工程与自动化学院ꎬ辽宁沈阳㊀110819)摘㊀㊀㊀要:电化学腐蚀会在齿面上形成不含Fe的夹杂物ꎬ夹杂物和Fe基体表面间的缝隙腐蚀可能成为点蚀的萌生位置ꎬ由于润滑油的周期性压力作用ꎬ缝隙不断扩大形成点蚀.不同润滑条件下的磨损和点蚀行为不同:在干摩擦条件下ꎬ点蚀的发生率最低ꎬ磨损最严重ꎬ轮齿表面发生高温氧化腐蚀并在齿面上形成了一层氧化层ꎻ在油润滑条件下ꎬ润滑油以油膜的形式黏附在齿面上ꎬ点蚀的发生率和面积随润滑条件的改善而增加ꎬ磨损程度随润滑条件的改善而减小.在干摩擦条件下齿面磨损为主要失效形式ꎬ充分润滑条件下齿面点蚀变为主要失效形式.润滑油供给量减少时ꎬ磨损深度最小值点会从节点位置向齿根方向发生偏移.关㊀键㊀词:不同润滑条件ꎻ齿面点蚀ꎻ齿面磨损ꎻ碳钢齿轮ꎻFZG齿轮试验中图分类号:TB114 3㊀㊀㊀文献标志码:A㊀㊀㊀文章编号:1005-3026(2023)07-0972-10StudyonToothSurfaceWearandPittingCorrosionofCarbonSteelGearsUnderDifferentLubricationConditionsZHANGSheng ̄nanꎬSUNZhi ̄liꎬGUOFan ̄yiꎬWANGJian(SchoolofMechanicalEngineering&AutomationꎬNortheasternUniversityꎬShenyang110819ꎬChina.Correspondingauthor:ZHANGSheng ̄nanꎬE ̄mail:zhangshengnanneu@163.com)Abstract:TheelectrochemicalcorrosionwillformFe ̄freeinclusionsonthetoothsurfaceꎬandthecrevicecorrosionbetweentheinclusionsandthesurfaceoftheFematrixmaybecometheinitiationpositionofpittingcorrosion.Duetotheperiodicpressureofthelubricatingoilꎬthecreviceswillcontinuetoexpandandformpittingcorrosion.Undertheconditionofdryfrictionꎬtheincidenceofpittingcorrosionisthelowestandthewearisthemostserious.Hightemperatureoxidationcorrosionoccursonthetoothsurfaceandanoxidelayerisformedonthetoothsurface.Undertheconditionofoillubricationꎬthelubricatingoilisadheredtothetoothsurfaceintheformofoilfilmꎬtheincidenceandareaofpittingcorrosionincreasewiththeimprovementoflubricationconditionsꎬandtheweardegreedecreaseswiththeimprovementoflubricationconditions.Undertheconditionofdryfrictionꎬtoothsurfacewearisthemainfailuremodeꎬandunderthesufficientlubricationconditionꎬtoothsurfacepittingbecomesthemainfailuremode.Whenthelubricatingoilsupplydecreasesꎬtheminimumweardepthwillshiftfromthenodepositiontothetoothrootdirection.Keywords:differentlubricationconditionꎻtoothsurfacepittingꎻtoothsurfacewearꎻcarbonsteelgearꎻFZGgeartest㊀㊀齿面磨损和齿面点蚀是齿轮使用寿命的绝对影响因素ꎬ因此对齿轮表面磨损和点蚀的研究受到了国内外学者的长期关注.经过半个多世纪的快速发展ꎬ针对不同工况㊁不同材料制成和不同加工方式获得的齿轮失效形式的研究逐渐深入和细化.啮合面之间有相对滑动ꎬ必然会产生磨损ꎬ对于正常运行的齿轮来说磨损是不可避免的[1].齿轮在啮合过程中齿面受到周期变化的接触应力ꎬ点蚀受接触应力影响是最常见的齿轮故障之一[2].除了齿面磨损和齿面点蚀ꎬ其他几种失效形式在齿轮正常运行条件下发生的必然性较低:发生轮齿折断的前提条件是过载㊁长期工作或偏载[3]ꎻ发生齿面胶合的前提条件是重载和润滑不良[4]ꎬ导致齿面塑性变形的前提条件是齿轮材质较软㊁重载及频繁启动[5].目前ꎬ国内外学者对齿面磨损的研究主要包括:磨损模型的数值仿真[6-7]㊁磨损特性的实验观测[8]㊁材料和加工方法对磨损性能的影响㊁磨损检测方法和评估手段等.考虑现实中齿轮受工作环境的影响ꎬ润滑状态会有所不同ꎬ研究了润滑油量对磨损量的影响.国内外学者对齿面点蚀的研究主要包括:数值模型的建立[9]㊁点蚀失效的故障诊断[10]㊁齿面点蚀的试验研究[11]㊁点蚀对齿轮性能的影响[12]㊁不同工作环境下的齿面点蚀研究[13-15]以及提高抗点蚀性能的手段[16-17].由于在研究点蚀时忽略了润滑油供给条件对其产生的影响ꎬ有必要研究润滑条件对齿面点蚀的影响.点蚀是裂纹逐渐扩展的结果[18-19]ꎬ为了阐明受损表面上的点蚀行为ꎬ有必要研究裂纹的萌生机制.以前的研究都是从力学角度来分析点蚀的成因ꎬGlode㊅z等[20]和Aslantas等[21]早期研究了裂纹的萌生是在与表面有一定距离的最大等效应力处ꎬ为点蚀的萌生理论提供了一种可能性解释.从润滑的角度分析ꎬ油膜会改变齿面间的接触关系和受力情况.润滑可按供油量分类为:充分润滑㊁少油润滑和干摩擦.在充分润滑条件下ꎬ轮齿接触表面完全浸入润滑油中ꎬ碳钢不会直接与大气接触ꎻ在润滑不足的情况下ꎬ润滑油的量不足以在齿面上形成连续的润滑油膜ꎻ在干摩擦条件下ꎬ齿面完全暴露在大气中ꎬ没有润滑油的保护ꎬ因此ꎬ在这种条件下ꎬ齿面点蚀的研究应考虑碳钢在大气中的点蚀行为[22-23]及温度对碳钢腐蚀的影响[24-25].基于FZG齿轮试验ꎬ研究了润滑条件对碳钢齿轮齿面磨损和点蚀行为的影响ꎬ磨损量和点蚀大小分布是衡量齿轮失效的重要参数.在FZG试验机上对AISI1045碳钢齿轮进行不同润滑条件的疲劳试验ꎬ通过XRD和EDS图谱对试验后的轮齿表面的成分进行分析ꎬ借助扫描电镜和三维形貌仪研究了润滑条件对点蚀面积和深度的影响ꎬ三坐标测量仪测量试验前㊁后的齿廓以得到齿廓的磨损量.最后ꎬ讨论了点蚀的萌生及润滑条件对表面成分㊁点蚀扩展和磨损深度的影响.1㊀FZG齿轮失效试验考虑现实中齿轮的工作环境会有充分润滑㊁少油润滑㊁甚至干摩擦的极端状态ꎬ为了更直观地研究润滑条件对齿面磨损和齿面点蚀的影响ꎬ在FZG齿轮试验机上进行了不同润滑条件下的表面疲劳试验ꎬ试验装置如图1所示.FZG齿轮试验机为闭式动力循环系统ꎬ能够为试验齿轮提供固定扭矩.主要组成包括:试验齿轮箱㊁连接轴㊁加载联轴器㊁扭矩测量联轴器㊁陪测齿轮箱等.陪测齿轮箱和试验齿轮箱通过轴连接ꎬ连接轴上有加载联轴器ꎬ将已知质量的载荷挂于负载联轴器的悬臂上以实现该试验机的扭矩施加.齿轮润滑站用于为试验齿轮提供不同流量的润滑油ꎬ通过循环润滑的方式ꎬ可以在齿轮副正常工作时控制润滑量ꎬ从而达到不同程度的润滑效果.为了保证润滑油黏度的变化不会对试验结果产生干扰ꎬ润滑站增加了温度调节装置ꎬ根据润滑油正常黏度的温度范围设定润滑油的工作温度.温度传感器用于实时监测油箱中润滑油的温度.在连续冷却过程中ꎬ当温度低于设定温度时ꎬ润滑油将被实时加热以保持温度不变.考虑到试验精度和时间成本ꎬ本次试验选用L-CKC220中负荷工业齿轮油(生产商:昆仑)作为试验齿轮润滑油ꎬ主要参数如表1所示ꎬ可加速试验齿轮的失效ꎬ且不影响试验精度图1㊀工作原理图和试验台Fig 1㊀Workingprinciplediagramandtestbed(a) 工作原理图ꎻ(b) 试验台.表1㊀L-CKC220主要参数Table1㊀MainparametersofL ̄CKC220ISO黏度等级220运动黏度(40ħ)/(mm2 s-1)218 5闪点(开口)/ħ242倾点/ħ-9379第7期㊀㊀㊀张胜男等:不同润滑条件下碳钢齿轮齿面磨损和点蚀研究㊀㊀㊀㊀选用AISI1045碳钢制造渐开线直齿轮ꎬ齿轮参数如表2所示.在制作齿轮之前ꎬ齿轮粗加工操作中留有2~3mm的余量ꎬ首先在1113K下加热1hꎬ然后水淬ꎬ高温回火1h.实验前对样品进行超声波清洗和干燥.表2㊀试验齿轮参数Table2㊀Testgearparameters齿轮小齿轮大齿轮齿数1624模数/mm4 54 5齿宽/mm2020变位系数0 8635-0 5压力角/(ʎ)2020中心距/mm91 591 5节圆直径/mm73 2109 8啮合角/(ʎ)22 4422 44㊀㊀使用3组每组7对齿轮:1#齿轮为干摩擦试验齿轮ꎬ即先进行简单的浸油处理ꎬ然后添加少量润滑油ꎻ2#齿轮为少油润滑试验齿轮ꎬ即处于干摩擦和充分润滑的中间状态ꎻ3#齿轮为充分润滑试验齿轮ꎬ即确保工作齿面完全浸入润滑油.根据预试验结果ꎬ确定每次试验的润滑油流量.在充分润滑试验中ꎬ齿轮采用浸没润滑ꎬ充分润滑浸没深度设定为齿高的1 5倍左右.少油润滑试验采用循环润滑ꎬ以控制润滑量为充分润滑的25%.通过试验对比ꎬ充分润滑对应的循环润滑流量为1100mL/minꎬ少油润滑的流量为275mL/min.在干摩擦试验中ꎬ为了避免因直接接触摩擦热而产生的胶合ꎬ添加了少量润滑油ꎬ根据预试验结果ꎬ流量为7mL/min.2㊀润滑条件对齿面磨损的影响轮齿的磨损深度是由试验前㊁后的齿廓上各点的坐标变化来确定的.由于参与啮合的齿廓上的各点在接触过程中受力大小不同ꎬ而且受加工精度影响的表面微观形貌不规则ꎬ其微观表面沿齿廓方向分布是高低不平的ꎬ因此磨损深度并不相同.对于不同润滑条件下的磨损深度ꎬ作用在齿面上的正压力及齿面间摩擦系数/润滑油剪切力会受润滑油量的影响发生变化ꎬ导致在不同润滑条件下的磨损深度有所不同.2 1㊀磨损深度的方向定义及计算方法齿轮磨损深度方向的定义准则直接影响磨损行为的判断ꎬ研究将磨损深度定义为参与啮合齿廓上同一半径ri的坐标值变化量ꎬ为周向磨损深度ꎬ图2中箭头方向即为磨损深度方向ꎬsi表示磨损前齿廓上的任一点ꎬ坐标为(xiꎬyi)ꎬSi表示磨损后齿廓上与磨损前对应同一半径的点ꎬ坐标为(XiꎬYi).下文中出现的磨损深度值均是由此种方法计算而得的.图2㊀磨损深度方向示意图Fig 2㊀Schematicdiagramofweardepthdirection㊀㊀磨损深度表达式为h=(xi-Xi)2+(Yi-yi)2.(1)2 2㊀润滑条件对磨损深度的影响由于主动小齿轮受变位系数的影响ꎬ其齿顶圆的弦齿厚非常小ꎬ为了避免齿顶圆被完全磨掉而对测量结果产生影响ꎬ选择大齿轮作为测试对象.通过对试验后齿轮进行观察和随机齿面轮廓测量ꎬ发现每组的7个齿轮具有相似的磨损规律ꎬ且磨损深度曲线的变化规律相似.在每组试验齿轮中随机选择一个大齿轮进行计算ꎬ每个大齿轮上选择相隔120ʎ的3个轮齿进行齿面轮廓测量.图3为充分润滑条件下㊁少油润滑条件下和干摩擦条件下的试验前㊁后齿廓形状测量结果ꎬ从齿面轮廓对比可见ꎬ干摩擦条件下的齿面轮廓变化最图3㊀试验前㊁后齿面轮廓Fig 3㊀Pre ̄andpost ̄testtoothprofile(a) 干摩擦ꎻ(b) 少油润滑ꎻ(c) 充分润滑.479东北大学学报(自然科学版)㊀㊀㊀第44卷㊀㊀㊀㊀明显ꎬ其次为少油润滑ꎬ充分润滑条件下的齿面轮廓变化最小.将试验前㊁后的齿廓相减得到磨损深度的分布规律ꎬ如图4所示.为了方便进行比较ꎬ利用每个齿轮上测得的磨损深度计算齿廓上各点的平均磨损深度曲线.不同润滑条件下的平均磨损深度值对比如图5所示.从润滑条件对齿面磨损的影响角度来看ꎬ干摩擦条件下齿廓上各点的磨损深度最大ꎬ充分润滑条件下齿廓上各点的磨损深度最小.从磨损深度在齿廓上的分布情况来看ꎬ不同润滑条件下的磨损深度在齿廓上具有非常相似的分布规律:磨损深度最大值均出现在单对齿啮合区的下界点附近ꎻ靠近齿根区域的磨损深度大于靠近齿顶区域的磨损深度ꎻ磨损深度最小值点位于节点(r=54 9mm)和最大磨损深度图4㊀不同润滑条件下的磨损深度Fig 4㊀Weardepthunderdifferentlubricationconditions(a) 干摩擦ꎻ(b) 少油润滑ꎻ(c) 充分润滑.之间.由图5可知ꎬ充分润滑条件下的最小磨损深度位置发生在节点附近ꎬ并且轻微偏向于齿根方向ꎬ随润滑条件的恶化ꎬ最小磨损深度的位置逐渐从节点向齿根方向偏移.图5㊀不同润滑条件下的平均磨损深度Fig 5㊀Averageweardepthunderdifferentlubricationconditions㊀㊀齿面磨损深度对比结果说明ꎬ润滑条件对齿面磨损行为有很大影响ꎬ齿轮试验在充分润滑时齿廓上各点的磨损深度都很小ꎬ少油润滑次之ꎬ干摩擦条件下各点的磨损深度最大ꎬ也就是说润滑条件越差齿面磨损越严重.润滑条件能够改变最小磨损深度的位置ꎬ随润滑条件变差ꎬ最小磨损深度的发生位置会从节点向齿根方向偏移.3㊀齿面点蚀萌生的一种可能性点蚀的形成过程受到各种因素的影响ꎬ例如:制造缺陷㊁齿面的物理损坏㊁表面或次表面的应力集中㊁润滑油中的杂质及相对齿面的划痕等都可能成为点蚀萌生的起始点.利用扫描电子显微镜观察和EDS分析试件表面的点蚀行为时发现ꎬ电化学腐蚀会在齿面上形成不含Fe的夹杂物ꎬ夹杂物和Fe基体表面间的缝隙腐蚀可能成为点蚀的萌生位置.本研究所选齿轮的材料为45钢ꎬ其化学成分如表3所示.在每个大齿轮上选择一个轮齿来观察啮合面.在20kV加速电压下进行扫描电子显微镜(SEM)观察和EDS分析.在扫描电子显微镜观察之前ꎬ用去离子水冲洗样品并在N2气流中干燥.3 1㊀齿面夹杂物与点蚀的关系为了确定点蚀的形成与齿面夹杂物之间的关系ꎬ研究了不同润滑条件下齿面典型点蚀坑的表579第7期㊀㊀㊀张胜男等:不同润滑条件下碳钢齿轮齿面磨损和点蚀研究㊀㊀表3㊀试验齿轮化学成分(质量分数)Table3㊀Chemicalcompositionoftestgear(massfraction)%CSiMnCr0 45~0 50 17~0 370 5~0 8ɤ0 25NiCuPSFeɤ0 25ɤ0 25ɤ0 035ɤ0 035余量面化学元素组成.图6为充分润滑㊁少油润滑和干摩擦条件下齿面上典型点蚀坑的SEM图像和相应的EDS图ꎬ箭头方向为相对滑动方向.在每个齿面上都可以观察到Fe的贫瘠区域ꎬ将Fe的贫瘠区域定义为夹杂物ꎬ通过与O元素相应区域的对比可以发现ꎬ这些夹杂物大多为氧化物.可知ꎬ夹杂物的形状不规则且大小不均ꎬ随机分布在齿面上.图6㊀齿面上典型点蚀坑的SEM图像和相应的EDS图Fig 6㊀SEMimagesandcorrespondingEDSimagesoftypicalpittingpitsontoothsurface(a) 充分润滑ꎻ(b) 少油润滑ꎻ(c) 干摩擦.679东北大学学报(自然科学版)㊀㊀㊀第44卷㊀㊀㊀㊀在充分润滑条件下ꎬ可以在一些点蚀的边缘观察到夹杂物(图6a中的区域1ꎬ2ꎬ3ꎬ4ꎬ5)ꎬ但由于萌生点蚀的因素有多种ꎬ因此并非所有的点蚀坑边缘都有夹杂物ꎬ受夹杂物所在位置及受力情况等因素的影响ꎬ并非所有夹杂物都会形成点蚀坑(区域5).在少油润滑条件下ꎬ从图6b可以看出ꎬ与充分润滑呈相同规律.在干摩擦条件下ꎬ夹杂物零星分布在受损齿面上(图6c中区域2ꎬ3ꎬ4ꎬ5)ꎬ由O的检测发现ꎬ与其他润滑条件相比ꎬO的质量分数明显增加ꎬ表明齿面成分发生了变化.相对平坦的表面区域O的质量分数比相对粗糙的表面区域的高很多(图6c中的区域1).干摩擦条件下齿面损伤主要是黏着和磨损ꎬ当发生黏着失效时ꎬ齿面上的材料会被接触的对方齿面带走.因此ꎬ可以判断图6c中的区域1是由于黏着和磨损而新生成的表面.在充分润滑和少油润滑条件下ꎬ齿面夹杂物对点蚀的萌生和分布存在影响ꎬ夹杂物的存在会增加点蚀萌生的可能性ꎻ在干摩擦条件下ꎬ夹杂物的分布和数量与齿面点蚀无关.3 2㊀点蚀萌生机制齿面在润滑条件下的腐蚀机理如图7所示ꎬ齿面腐蚀可分为以下几个阶段:1)O2和H2O的混入:齿轮啮合时由于摩擦热的作用ꎬ两齿面间的润滑油温度升高.润滑油温度越高ꎬ表面的空气湿度越大ꎬ导致溶解在润滑油中的水增加.混入润滑油中的O2和H2O会对齿面产生电化学腐蚀.理论上O2在水膜中呈均匀分布ꎬ当轮齿表面发生电化学腐蚀时ꎬ靠近轮齿表面区域的O2的质量浓度会减少ꎬ导致O2在水膜中的分布形成了一定的浓度梯度ꎬ促使O2向轮齿表面迁移.2)Fe的活性溶解:45钢内部含有大量的铁原子ꎬ当部分轮齿表面被水膜覆盖时ꎬ轮齿内部的铁原子会发生活性溶解ꎬ以游离铁离子的形式存在并依附在轮齿表面或存在于靠近齿面的区域.图7㊀齿面腐蚀机理简示Fig 7㊀Briefdescriptionofthetoothsurfacecorrosionmechanism㊀㊀3)Fe和O2在水膜中发生腐蚀反应:Fe和O2发生电化学腐蚀时ꎬ水膜作为反应的电解质溶液ꎬ齿面为阳极ꎬ溶入水膜中的O2为阴极.阳极上的Fe失去电子并形成Fe2+ꎬ阴极上的O2得到并形成OH-.反应式为阳极:FeңFe2+ꎬ阴极:O2+H2OңOH-ꎬ总反应式:Fe2++OH-ңFeO+H2O.4)FeO的还原反应:Fe与O2反应所生成的FeO不断团聚且附着在齿面上ꎬ部分FeO单独存在并脱离齿面ꎬ随润滑油移动.团聚在齿面上的FeO含量不断增加ꎬFeO会与材料中的还原性物质发生反应.反应式为FeO+MңMO+Fe.M代表还原性大于Fe的物质ꎬMO在齿面逐渐团聚㊁成型ꎬ成为不含Fe的夹杂物.腐蚀速率与水膜中O2的质量分数㊁环境及生成FeO的质量分数有关ꎬFe在水膜中靠近齿面区域的溶解量㊁O2在水膜中的质量分数㊁润滑油的温度㊁FeO在齿面的还原速率等共同影响腐蚀反应速率.摩擦热会使润滑油温度升高ꎬ导致腐蚀反应的活化分子数量增加ꎬ进而加快反应速率.5)点蚀萌生:Fe基体表面与夹杂物之间构成狭窄的缝隙ꎬ缝隙内的有关物质的移动将会受到阻滞ꎬ进而形成浓差电池ꎬ产生缝隙腐蚀.当两齿面接触时ꎬ受到垂直于齿面并指向齿轮内部的法向力.啮合过程使两齿面之间的润滑油受到挤压ꎬ挤压后的润滑油由于自身的流动性ꎬ会在表面寻找薄弱点进行填充ꎬFe基体表面与夹杂物之间的腐蚀缝隙便成为了突破口.由于齿轮机构的工作特性ꎬ润滑油对齿面产生脉冲冲击.润滑油不断挤入Fe基体和夹杂物之间的缝隙ꎬ导致缝隙不断延伸和扩大.相互作用的齿面之间的运动包括相对滑动和滚动ꎬ缝隙将沿法向作用力的方向和相对滑动的相反方向下向前延伸ꎬ当缝隙延伸并扩展到一定长度和深度时ꎬ缝隙中润滑油的不断增加会对被分割的轮齿表面产生向上的推力.随轮齿的周期性啮合ꎬ被分割的部分基体将因脉动法向作用力的消失而失去力学平衡ꎬ受到润滑油垂直于齿面并指向齿轮外部的推力.最后ꎬ被分割的部分基体在润滑油的作用下从齿面被挤压出来.在以后的齿面接触中ꎬ被分割的部分基体将沿着相对滑动的相反方向被撕裂ꎬ掉落的部分将被润滑油带走形成铁屑ꎬ并在齿面上形成凹坑.由此可见ꎬ点蚀萌生机制的理论分析和齿面779第7期㊀㊀㊀张胜男等:不同润滑条件下碳钢齿轮齿面磨损和点蚀研究㊀㊀夹杂物与点蚀关系的观察结果相吻合.以上结果表明ꎬ电化学腐蚀会在齿面上形成不含Fe的夹杂物ꎬ夹杂物和Fe基体表面间的缝隙腐蚀可能成为点蚀的萌生位置.4㊀润滑条件对齿面点蚀的影响4 1㊀齿面点蚀统计齿面发生点蚀时ꎬ点蚀坑不仅形态各异ꎬ发生的位置也不尽相同.依据JB/T5664标准ꎬ可以用齿面点蚀面积与轮齿工作齿面面积的比率来衡量齿面的点蚀程度.为了方便研究不同区域的齿面点蚀行为ꎬ将齿面按照关键研究对象分为几个研究区域ꎬ然后进行点蚀面积与区域面积的比率计算ꎬ以方便不同润滑条件下的同一区域的点蚀行为的相互比较.该方法只用于点蚀行为的比较ꎬ不能用于失效判定.点蚀面积与区域面积的比率为λi=aiAi.(2)式中:Ai为指定区域ꎻai为在区域Ai的点蚀面积总和ꎬi=1ꎬ2ꎬ3ꎬ4.点蚀面积与轮齿工作齿面面积的比率为λ=ðaiðAi.(3)试验齿轮为变位齿轮ꎬ受变位系数取值影响ꎬ节点处于双对齿啮合区域中.根据节点㊁单/双对齿啮合交界及啮入和啮出界线进行区域划分ꎬ可将轮齿工作齿面划分为4个区域ꎬ如图8所示.区域1为齿顶与节线之间的区域ꎬ区域2为节线与单/双齿啮合交界之间的区域ꎬ区域3为两个单/双齿啮合交界之间的区域ꎬ区域4为单/双齿啮合交界与啮出界线之间的区域.根据以上的区域划分和点蚀统计方法对试验后的齿轮齿面进行点蚀统计ꎬ随后研究均是应用此方法进行计算.图8㊀点蚀统计中的区域划分Fig 8㊀Regionaldivisioninpittingstatistics4 2㊀点蚀形貌及齿面氧化层不同润滑条件下的齿轮失效试验ꎬ用三维轮廓仪测量样品的表面形貌ꎬ根据齿面的不同状态分别选择2566μmˑ2569μmꎬ2566μmˑ2569μm和1280μmˑ1281μm区域进行三维轮廓成像.使用X射线衍射(BrukerD8)测定表面产物的相组成ꎬ2θ范围为5ʎ~90ʎ.在不同润滑条件下试验轮齿表面状况如图9所示.在充分润滑条件下ꎬ由于有充足的润滑油供给腐蚀缝隙ꎬ因此充分润滑条件下的点蚀最严重ꎬ且沿整个齿宽均匀分布ꎬ齿面颜色基本没有变化ꎬ见图9a.在润滑不足的情况下ꎬ润滑油不能覆盖整个齿面ꎬ部分腐蚀缝隙会避免润滑油的侵入ꎬ点蚀范围明显缩小ꎬ呈区域性分布ꎬ齿面颜色变化不明显ꎬ见图9b.在干摩擦条件下ꎬ未观察到明显的点蚀行为ꎬ但受损齿面发生高温氧化腐蚀ꎬ导致颜色发生明显变化ꎬ见图9c.图9㊀不同润滑条件下的试验轮齿表面状态Fig 9㊀Surfaceconditionoftestgearteethunderdifferentlubricationconditions(a) 充分润滑ꎻ(b) 少油润滑ꎻ(c) 干摩擦.㊀㊀试样的表面形貌如图10所示ꎬ在充分润滑条件下ꎬ试样表面存在严重点蚀ꎬ且多个点蚀叠加导致损伤直径达1mmꎬ如图10a所示.在少油润滑条件下ꎬ点蚀面积和数量都相对减小ꎬ直径约为879东北大学学报(自然科学版)㊀㊀㊀第44卷㊀㊀0 4mmꎬ并且叠加在一起的概率很小ꎬ如图10b所示.在干摩擦及相同的扫描电镜放大倍数下ꎬ试样表面无明显点蚀ꎬ但表面较粗糙ꎬ如图10c所示.三维形貌测量表明ꎬ在充分润滑条件下ꎬ典型的凹坑深度达到245μmꎬ比少油润滑条件下的130μm严重.图10㊀轮齿表面形貌Fig 10㊀Toothsurfacemorphology(a) 充分润滑ꎻ(b) 少油润滑ꎻ(c) 干摩擦.㊀㊀不同润滑条件下表面疲劳试验后试样表面形成的氧化层的XRD分析如图11所示.曲线1ꎬ2ꎬ3分别为干摩擦㊁少油润滑和充分润滑条件下的测量结果.在干摩擦条件下ꎬ样品表面发现FeOꎬ其他两个样品表面未检测到FeO.少油润滑时ꎬ表面也有可能存在FeOꎬ但其含量低于XRD的检测限.以上结果表明ꎬ在有润滑的条件下ꎬ润滑油将齿面与空气隔离ꎬ并能带走齿轮接触产生的热量ꎬ对齿面起到保护作用.在干摩擦条件下ꎬ轮齿表面不受润滑油保护ꎬ齿轮接触产生摩擦热导致表面温度迅速升高并发生氧化腐蚀.图11㊀轮齿表面XRD分析Fig 11㊀XRDanalysisofgeartoothsurface4 3㊀润滑条件对齿面点蚀的影响通过对齿面点蚀的观察和测量发现ꎬ点蚀凹坑的形状和尺寸不固定ꎬ但其发生位置具有一定的规律性.忽略了由于齿轮轴的对准误差和传动精度存在差异对同种润滑条件下的齿面点蚀分布的影响.选择大齿轮作为观测对象ꎬ通过对试验后齿轮进行观察和随机齿面点蚀统计ꎬ发现每组的7个大齿轮具有相似的点蚀分布规律ꎬ点蚀数量和面积相近.因此ꎬ在每种润滑条件下随机选择3个大齿轮作为测试对象ꎬ每个齿轮上随机选择相差120ʎ的3个轮齿进行测量.按照4 1节所述方法进行点蚀统计ꎬ并对各齿轮的计算结果按照区域取平均值.统计结果如图12所示ꎬ横坐标表示区域编号ꎬ纵坐标表示区域面积中的点蚀面积和非点蚀面积的占比关系.从图中可以看出:充分润滑条件下的点蚀分布在区域2㊁区域3和区域4内ꎬ而且点蚀大部分集中在双对齿啮合区域4内ꎻ少油润滑条件下的点蚀分布在区域3和区域4内ꎬ同样在双对齿啮合区域4内的点蚀面积最大.充分润滑和少油润滑条件下的点蚀面积与轮齿工作齿面面积的比率分别为1 99%ꎬ0 12%ꎬ充分润滑条件下的点蚀面积远大于少油润滑条件下的点蚀面积.随润滑条件的改善ꎬ平均点蚀数量显著增加ꎬ点蚀深度随润滑油的减少而减小.由于干摩擦条件下没有润滑油的作用ꎬ齿面上腐蚀缝隙不能延伸和扩大.由以上研究结果可知ꎬ润滑油的用量会导致表面点蚀行为的差异.在充分润滑条件下ꎬ润滑油将在齿面上形成连续油膜ꎬ当两个齿轮接触时齿面间的油膜厚度大ꎬ夹杂物与Fe基体之间的腐蚀缝隙不断被润滑油填充扩展ꎬ因此点蚀深度和面积相对较大.在润滑不足的情况下ꎬ齿面间的油膜979第7期㊀㊀㊀张胜男等:不同润滑条件下碳钢齿轮齿面磨损和点蚀研究。
齿轮磨损检测方法
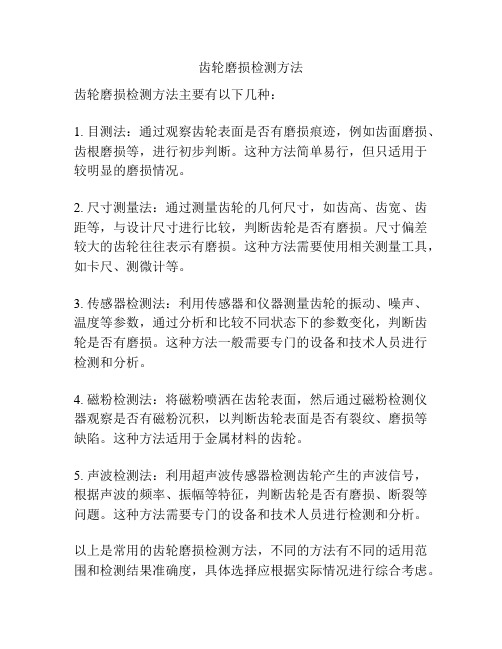
齿轮磨损检测方法
齿轮磨损检测方法主要有以下几种:
1. 目测法:通过观察齿轮表面是否有磨损痕迹,例如齿面磨损、齿根磨损等,进行初步判断。
这种方法简单易行,但只适用于较明显的磨损情况。
2. 尺寸测量法:通过测量齿轮的几何尺寸,如齿高、齿宽、齿距等,与设计尺寸进行比较,判断齿轮是否有磨损。
尺寸偏差较大的齿轮往往表示有磨损。
这种方法需要使用相关测量工具,如卡尺、测微计等。
3. 传感器检测法:利用传感器和仪器测量齿轮的振动、噪声、温度等参数,通过分析和比较不同状态下的参数变化,判断齿轮是否有磨损。
这种方法一般需要专门的设备和技术人员进行检测和分析。
4. 磁粉检测法:将磁粉喷洒在齿轮表面,然后通过磁粉检测仪器观察是否有磁粉沉积,以判断齿轮表面是否有裂纹、磨损等缺陷。
这种方法适用于金属材料的齿轮。
5. 声波检测法:利用超声波传感器检测齿轮产生的声波信号,根据声波的频率、振幅等特征,判断齿轮是否有磨损、断裂等问题。
这种方法需要专门的设备和技术人员进行检测和分析。
以上是常用的齿轮磨损检测方法,不同的方法有不同的适用范围和检测结果准确度,具体选择应根据实际情况进行综合考虑。
粉末冶金非圆齿轮的润滑性能与摩擦磨损行为分析

粉末冶金非圆齿轮的润滑性能与摩擦磨损行为分析摘要:粉末冶金技术被广泛应用于制造非圆齿轮,并具有许多优势,如成本效益、复杂几何形状的制造能力和材料的多样性。
然而,粉末冶金非圆齿轮的润滑性能和摩擦磨损行为是决定其工作可靠性和寿命的重要因素。
因此,对于粉末冶金非圆齿轮的润滑性能和摩擦磨损行为的深入分析具有重要的理论意义和实际应用价值。
引言:粉末冶金非圆齿轮广泛应用于许多领域,如汽车、机械、制造等。
相较于传统的加工方法,粉末冶金技术能够制造出复杂的几何形状,优化材料性能,并有效降低成本。
然而,由于粉末冶金非圆齿轮制造过程中的特殊工艺和材料特性,其润滑性能和摩擦磨损行为的研究仍然是一个热门的领域。
润滑性能的分析:非圆齿轮的润滑性能不仅取决于润滑剂的选择,还受到齿轮表面形态、材料性能和工作条件等因素的影响。
粉末冶金非圆齿轮的表面形态主要由颗粒排列组成,而颗粒之间的接触是非圆齿轮摩擦的主要来源。
因此,细观的表面形貌和微观的接触行为对润滑性能具有重要影响。
未经润滑剂处理的表面形态会导致颗粒间的接触处出现微小凸起,进而增加摩擦损失。
因此,在粉末冶金非圆齿轮的制造过程中,常会利用烧结、热处理等工艺来改善表面形貌,进而提高润滑性能。
此外,润滑剂的选择也是影响润滑性能的关键因素。
低粘度的润滑剂能够更好地填满颗粒间的缝隙,减小颗粒间的接触,从而降低摩擦损失。
摩擦磨损行为的分析:粉末冶金非圆齿轮的摩擦磨损行为主要表现为颗粒间的塑性变形、颗粒脱落和表面磨损等。
由于颗粒之间的接触导致表面形貌的不规则性,摩擦磨损行为在颗粒间的接触区域更加严重。
研究发现,颗粒间的塑性变形是粉末冶金非圆齿轮摩擦磨损的主要机制之一。
由于粉末冶金非圆齿轮在制造过程中使用了高温和高压的工艺,颗粒具有较强的塑性变形能力。
因此,在摩擦过程中,颗粒间会发生塑性变形,从而分散摩擦力和磨损。
另一方面,颗粒的脱落也是摩擦磨损的重要机制之一。
由于粉末冶金非圆齿轮的表面形态不规则,颗粒之间的接触会导致颗粒脱落。
摩擦磨损性能测试试验
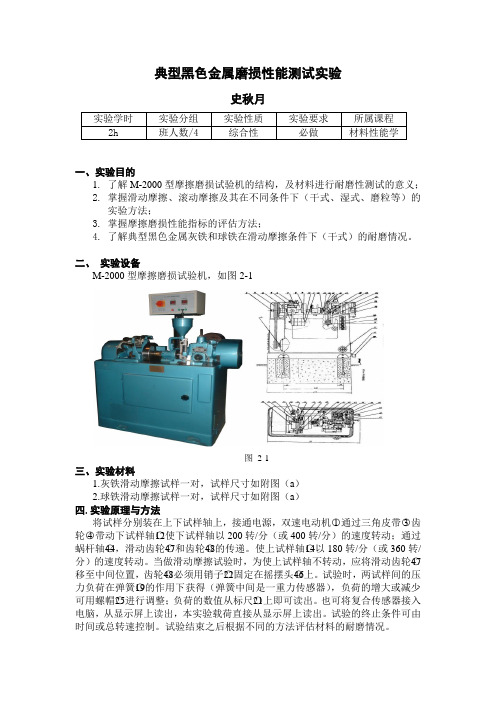
典型黑色金属磨损性能测试实验史秋月实验学时实验分组实验性质实验要求所属课程2h 班人数/4 综合性必做材料性能学一、实验目的1.了解M-2000型摩擦磨损试验机的结构,及材料进行耐磨性测试的意义;2.掌握滑动摩擦、滚动摩擦及其在不同条件下(干式、湿式、磨粒等)的实验方法;3.掌握摩擦磨损性能指标的评估方法;4.了解典型黑色金属灰铁和球铁在滑动摩擦条件下(干式)的耐磨情况。
二、实验设备M-2000型摩擦磨损试验机,如图2-1图2-1三、实验材料1.灰铁滑动摩擦试样一对,试样尺寸如附图(a)2.球铁滑动摩擦试样一对,试样尺寸如附图(a)四.实验原理与方法将试样分别装在上下试样轴上,接通电源,双速电动机○1通过三角皮带○3齿12使下试样轴以200转/分(或400转/分)的速度转动;通过轮○4带动下试样轴○48的传递。
使上试样轴○14以180转/分(或360转/47和齿轮○蜗杆轴○44,滑动齿轮○分)的速度转动。
当做滑动摩擦试验时,为使上试样轴不转动,应将滑动齿轮○47移至中间位置,齿轮○48必须用销子○22固定在摇摆头○46上。
试验时,两试样间的压力负荷在弹簧○19的作用下获得(弹簧中间是一重力传感器),负荷的增大或减少21上即可读出。
也可将复合传感器接入可用螺帽○25进行调整;负荷的数值从标尺○电脑,从显示屏上读出,本实验载荷直接从显示屏上读出。
试验的终止条件可由时间或总转速控制。
试验结束之后根据不同的方法评估材料的耐磨情况。
五、实验内容将加工好的滑动摩擦试样装在实验机上,在给定的条件下(干式、滑动摩擦、压力:200N、时间60min)进行试验,试验结束后将试样取下,评估耐磨性能。
根据所选取磨损试验方法的不同以及材料本质的差异,可以选择不同的耐磨性能评定方法,以期获得精确的试验数据,现简单例举下述几种方法以供参考。
1、称重法:采用试样在试验前后重量之差,本表示耐磨性能的方法,由于两试样之间的摩擦所引起的磨损量,可以采用精度达万分之一的分析天平称量出试样试验前后重量之差非凡获得。
机车牵引齿轮材料摩擦磨损性能试验研究

机车牵引齿轮材料摩擦磨损性能试验研究石莹;姚玉鹏;李宝良【摘要】Taking a certain high-speed locomotive traction gear material of 42CrMo-17CrNiMo6 as the object,the influ-ence of contact load and relative sliding velocity on its friction and wear properties was studied in the pin-on-disk recipro-cating friction and wear tester. The worn surface morphologies were observed on a scanning electron microscope and the friction and wear mechanism of the locomotive gear materials was analyzed. Results show that the friction coefficient of lo-comotive traction gear materials is decreased and then becomes stable gradually with the increasing of normal contact load and relative velocity. The ploughs are generated on the worn surfaces of the locomotive traction gear materials. Due to the increase of the load and velocity,the space of ploughs is widened and the worn surface is smoothed,which causes the de-creasing of the friction coefficient for the locomotive traction gear material.%以某高速机车牵引齿轮材料42CrMo-17CrNiMo6为研究对象,在销盘往复摩擦磨损试验机上研究接触载荷和相对滑动速度对其摩擦磨损性能的影响规律;利用扫描电子显微镜观察磨损表面形貌,进而分析材料摩擦磨损机制。
基于铁谱分析技术的齿轮磨损研究

磨损阶段
续表 1 磨粒特征
过速磨损
过速磨损导致齿轮擦伤或胶合 ,因 此磨粒表面会有一些氧化的痕迹 。大
小磨粒的数量比较低 ,为 1 ζ 500或更 低 ,磨粒的总量高于正常磨损期 。长 度与厚度之比约为 10ζ 1,磨粒不大于 150 μm。
疲劳磨损
疲劳磨损使表面光滑的金属颗粒剥 落 ,且颗粒表面有一些氧化的痕迹 ,长 宽比为 6: 1,长度与厚度之比约为 5: 1。磨粒 长 可 达 150 μm; 大 于 15 μm 的大磨粒主要落在 15~25μm 范围内 。 大小磨粒的数量比很高 ,约为 1: 50或 更高 , 磨 粒 总 量 是 正 常 磨 损 的 3 ~ 5倍 。
图 1 铁谱仪的工作原理 11油样 21导油管 31微量泵 41玻璃基片
51磁场装置 61回油管 71储油杯
— 76 —
过载磨损
低速时齿轮的过载磨损产生的是片 状磨粒 ,长宽比为 2ζ 1,长度与厚度比 为 10ζ 1,磨粒长可达 1 mm ,这取决于 过载 程 度 。过 载 刚 开 始 产 生 不 大 于 150μm 的磨粒 。大小磨粒的数量 也 随之增加 ,磨粒的总量远远高于正常 磨损 ,且磨粒表面常会出现滑动擦痕 。
1 引言
铁谱技术是以磨损颗粒分析为基础的诊断技 术 , 是诊断机器磨损故障的最有效方法 。齿轮副 产生磨粒的特征粒度范围为 1 ~10 μm , 而铁谱技 术的监测区间正好符合这一要求 , 铁谱技术特别 适用于较大磨粒的检测 , 对润滑磨损故障诊断的 机理有着较强的解释性 。尤其对分析异常磨损故 障机理和预防早期 、突发性故障有较大的优势 。
大学机电工程学院 邮 编 : 650093 收稿日期 : 2008 - 11 - 26
齿轮磨损实验报告
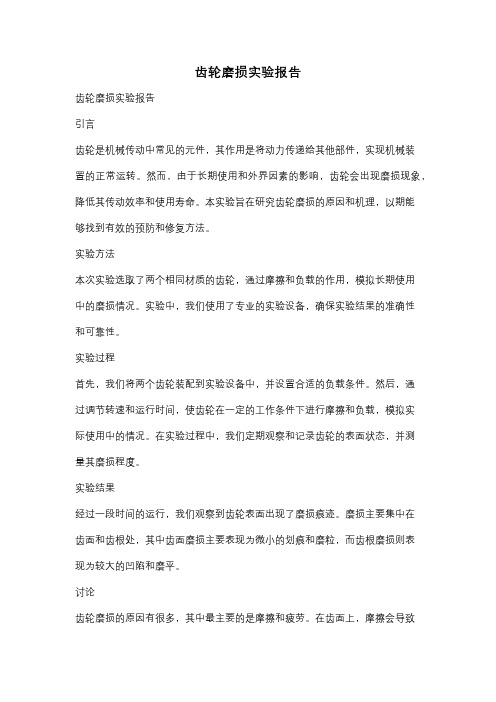
齿轮磨损实验报告齿轮磨损实验报告引言齿轮是机械传动中常见的元件,其作用是将动力传递给其他部件,实现机械装置的正常运转。
然而,由于长期使用和外界因素的影响,齿轮会出现磨损现象,降低其传动效率和使用寿命。
本实验旨在研究齿轮磨损的原因和机理,以期能够找到有效的预防和修复方法。
实验方法本次实验选取了两个相同材质的齿轮,通过摩擦和负载的作用,模拟长期使用中的磨损情况。
实验中,我们使用了专业的实验设备,确保实验结果的准确性和可靠性。
实验过程首先,我们将两个齿轮装配到实验设备中,并设置合适的负载条件。
然后,通过调节转速和运行时间,使齿轮在一定的工作条件下进行摩擦和负载,模拟实际使用中的情况。
在实验过程中,我们定期观察和记录齿轮的表面状态,并测量其磨损程度。
实验结果经过一段时间的运行,我们观察到齿轮表面出现了磨损痕迹。
磨损主要集中在齿面和齿根处,其中齿面磨损主要表现为微小的划痕和磨粒,而齿根磨损则表现为较大的凹陷和磨平。
讨论齿轮磨损的原因有很多,其中最主要的是摩擦和疲劳。
在齿面上,摩擦会导致齿面表面粗糙度增加,从而增加摩擦阻力和能量损耗。
而在齿根处,由于负载的作用,齿根会承受更大的应力,从而导致疲劳破坏和磨损。
除了摩擦和疲劳外,其他因素也可能对齿轮磨损产生影响。
例如,材料的选择和处理会影响齿轮的硬度和强度,从而影响其抗磨损性能。
此外,润滑剂的选择和使用也会对齿轮的磨损情况产生影响,合适的润滑剂可以减少摩擦和磨损。
结论通过本次实验,我们深入了解了齿轮磨损的原因和机理。
磨损主要集中在齿面和齿根处,摩擦和疲劳是主要的磨损机制。
为了减少齿轮磨损,我们可以从材料选择、表面处理、润滑剂使用等方面入手,提高齿轮的抗磨损性能。
此外,定期检查和维护齿轮也是重要的措施,可以及时发现和修复磨损问题,延长齿轮的使用寿命。
展望虽然本次实验对齿轮磨损进行了初步研究,但仍有许多问题需要进一步探索。
例如,不同材料和润滑剂对齿轮磨损的影响,以及不同工况下齿轮磨损的差异等。
低速重载齿轮齿面磨损有限元分析

0 引言
低速重载齿轮速度低,转矩、冲击大,短时超 载严重,工作环境恶劣,长期处于边界润滑状态[1]。 并且由于设计不当、安装误差、材质不均、刚度不 够等因素,很容易发生故障甚至引起重大事故。调 查表明,德国、日本制造的减速机低速重载齿轮寿 命一般为10-15年,俄罗斯的为3-9年,我国制造的 在10年以下,多数为5年左右[2]。因此,低速重载齿 轮的研究对国民经济许多部门的发展意义重大。 低速重载齿轮啮合处压力很高且速度低,传动 过程中不易形成良好的润滑油膜,导致齿面相啮合 金属直接接触而产生粘着,随着齿面相对运动,引 起严重粘着磨损现象,从而导致动载、噪音、齿面 温度升高,造成严重的齿面破坏,使轮齿丧失工作 能力,甚至断裂[3]。以某公司易维护SL1000型采煤 机摇臂传动系统的末级齿轮为例,首先用PRO/E软 件建立该齿轮传动系统的三维实体模型,然后将建 立的正常齿面模型和三种齿面磨损模型分别导入 有限元分析软件ANSYS/LS-DYNA中。最后,依据 实际工况仿真得到的齿轮传动过程中转矩等载荷 数据,对齿轮不同模型进行动态接触有限元仿真分 析,得到低速重载齿轮在正常齿面和齿面磨损条件 下的运动状态与受力情况。这对低速重载齿轮齿面
2
3 结果与分析
3.1 正常齿面模型结果分析 分别截取主、从齿轮在一个啮合周期内啮合初 期和啮合末期的齿面接触有效应力云图5、6,它们 的上两幅图表示主动轮轮齿啮合初期或末期两个 瞬时的齿面接触有效应力云图;下两幅图表示相对 应时刻从动轮轮齿齿面接触有效应力云图。由图可 知,轮齿在啮合传动过程中存在应力集中现象,且 应力主要集中在轮齿节圆附近;齿面受力不均,存 在“边缘效应” 。由于轮齿啮合表面在机械加工过 程中会形成微观不平,导致啮合表面承受载荷的接 触点呈离散状态。齿轮在工作过程中运动不平稳、 受力不均匀及安装制造误差均会导致齿轮传动存 在波动,这也是导致轮齿齿面磨损、胶合等失效形 式的主要原因。
摩擦磨损试验
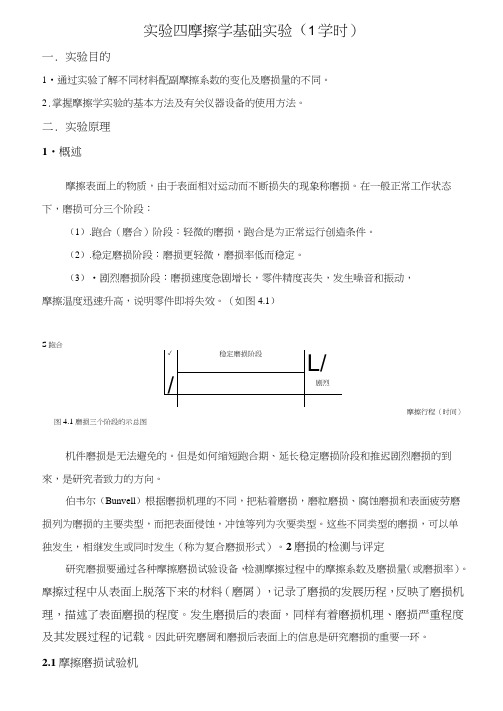
实验四摩擦学基础实验(1学时)一.实验目的1•通过实验了解不同材料配副摩擦系数的变化及磨损量的不同。
2.掌握摩擦学实验的基本方法及有关仪器设备的使用方法。
二.实验原理1•概述摩擦表面上的物质,由于表面相对运动而不断损失的现象称磨损。
在一般正常工作状态下,磨损可分三个阶段:(1).跑合(磨合)阶段:轻微的磨损,跑合是为正常运行创造条件。
(2).稳定磨损阶段:磨损更轻微,磨损率低而稳定。
(3)•剧烈磨损阶段:磨损速度急剧增长,零件精度丧失,发生噪音和振动,摩擦温度迅速升高,说明零件即将失效。
(如图4.1)S跑合摩擦行程(时间〉图4.1磨损三个阶段的示总图机件磨损是无法避免的。
但是如何缩短跑合期、延长稳定磨损阶段和推迟剧烈磨损的到來,是研究者致力的方向。
伯韦尔(Bunvell)根据磨损机理的不同,把粘着磨损,磨粒磨损、腐蚀磨损和表面疲劳磨损列为磨损的主要类型,而把表面侵蚀,冲蚀等列为次要类型。
这些不同类型的磨损,可以单独发生,相继发生或同时发生(称为复合磨损形式)。
2磨损的检测与评定研究磨损要通过各种摩擦磨损试验设备,检测摩擦过程中的摩擦系数及磨损量(或磨损率)。
摩擦过程中从表面上脱落下来的材料(磨屑),记录了磨损的发展历程,反映了磨损机理,描述了表面磨损的程度。
发生磨损后的表面,同样有着磨损机理、磨损严重程度及其发展过程的记载。
因此研究磨屑和磨损后表面上的信息是研究磨损的重要一环。
2.1摩擦磨损试验机磨损试验的目的在于研究各种因素对摩擦磨损的影响,从而合理地选择配对材料,采用有效措施降低摩擦、磨损,正确设计摩擦副的结构尺寸及冷却设施等等。
摩擦磨损试验大体上可分为实验室试验,模拟试验或台架试验,以及使用试验或全尺寸试验三个层次,各层次试验设备的要求各不相同。
(1)实验室评价设备实验室设备主要用于摩擦磨损的基础研究,研究工作参数(载荷、速度等)对摩擦磨损的影响。
可以得到单一参量变化与摩擦磨损过程之间的关系。
高速精密齿轮传动装置的表面处理与涂层技术研究

高速精密齿轮传动装置的表面处理与涂层技术研究一、引言高速精密齿轮传动装置在现代工业中具有重要的应用,广泛应用于航空、航天、汽车、机械等领域。
因其承受高速转动、大扭矩和严苛工况的特点,表面处理和涂层技术显得尤为重要。
本文旨在研究高速精密齿轮传动装置的表面处理与涂层技术,以提高其耐磨性、耐腐蚀性、减少摩擦损失,从而提高齿轮传动装置的使用寿命和效率。
二、表面处理技术1. 碳化处理碳化处理是齿轮传动装置表面处理的一种常见方法。
通过在齿轮表面加入足够碳源,在高温下进行热处理,将碳渗透到表面,形成一层高硬度的碳化物,如碳化铁或碳化钨等。
这种处理可以提高齿轮的硬度和耐磨性,减少齿轮在高速转动时的磨损。
2. 氮化处理氮化处理是另一种常用的表面处理方法。
通过在高温和氮气气氛中进行处理,氮原子渗透到齿轮表面,形成一层氮化物。
氮化物具有较高的硬度和耐磨性,可以显著提高齿轮的表面硬度和磨损性能。
3. 渗氮处理渗氮处理是将氮元素渗透到齿轮表面的一种方法。
这种处理方法可以提高齿轮的硬度和强度,减少齿轮在高速运动时的变形和磨损。
4. 表面涂层表面涂层是一种将涂层材料覆盖在齿轮表面的方法。
常用的涂层材料包括钼二硫化物(MoS2)、氮化硼(BN)、钛氮化物(TiN)等。
这些涂层具有优异的润滑性能和耐磨性,可以有效减少齿轮之间的摩擦损失,提高齿轮传动装置的效率和寿命。
三、涂层技术的研究进展1. 真空沉积技术真空沉积技术是一种常用的表面涂层技术。
该技术通过在高真空条件下沉积涂层材料,可以形成一层均匀、致密且具有良好粘附力的涂层。
但是该技术成本较高,工艺复杂,且涂层厚度有限。
2. 离子束沉积技术离子束沉积技术是近年来发展起来的一种先进的表面涂层技术。
该技术利用离子束轰击齿轮表面,使涂层材料离子化并沉积在表面上。
离子束沉积技术具有高沉积速率、可调控的沉积厚度和较好的涂层质量等优点。
3. 溅射技术溅射技术是一种通过溅射源将材料溅射到齿轮表面的方法。
工程机械齿轮的表面改性层及其摩擦磨损性能

工程机械齿轮的表面改性层及其摩擦磨损性能摘要:本文将在工程机械齿轮的基础上,对工程机械齿轮的表面改性层展开详细分析,并对其摩擦磨损性能进行系统论述。
关键词:工程机械齿轮;表面改性层;摩擦磨损性能1工程机械齿轮表面改性层实验成果分析1.1表面改性层的成分分析以及显微镜下的形貌分析通过对W-Mo共渗层进行能谱分析和表面显微形貌分析,我们得出,在W-Mo共渗层的表面,改性层没有明显的气孔、裂纹以及其他缺陷,可见层分布均匀且细密,但是在改性层的局部,有棱锥性的颗粒分布在其表面,造成这种现象的原因可能是在其共渗过程中,W和Mo的相关元素发生了择优生长的变化而形成的,据能谱分析结果可知改性层表面主要含有41.07wt%W和58.93wt%Mo,与溅射靶材的成分有一定差异,这主要是由于表面改性层的成分除与溅射靶材的成分组成相关外,还与靶材中各元素的扩散系数等有关。
在试验中,当表面改性层的厚度为12毫米时,表面改性层不存在缺陷,且在基体与改性层之间还存在明显的相互扩散层,它们之间的联系较为密切,能够在冶金工程中实现良好的融合。
当表面改性层的扩散层的厚度为3毫米,沉积层的厚度为9毫米时,沉积层中的W 和 Mo这两种元素呈均匀分布的状态;而扩散层中的W 和 Mo元素从沉积层到基体之间则呈现出梯度递减的特征,而铁元素却在不断增加[1]。
1.2工程机械齿轮的摩擦磨损性能分析图1 25度试样磨损程度对照表在工程机械齿轮的摩擦磨损性能的分析上,采用的是固体渗碳试样、齿轮钢基体、和W-Mo共渗试样分别在温度为25、350和500℃时的干摩擦磨损试验结果。
当在25度的温度状态时,固体渗碳试样、齿轮钢基体、和W-Mo共渗这三种试样的摩擦因素并不会因为时间的改变而产生较大的变化幅度,这说明在这一种温度状态下,对工程机械齿轮的磨损程度较小;当测试的温度在350度左右时,固体渗碳试样、齿轮钢基体、和W-Mo共渗这三种试样的波动幅度开始变大,其中齿轮钢基体的变化幅度在这三者中间的波动幅度最为明显;但是当温度升高至500左右时,固体渗碳试样和齿轮钢基体的摩擦因数的波动幅度开始变得极为剧烈。
- 1、下载文档前请自行甄别文档内容的完整性,平台不提供额外的编辑、内容补充、找答案等附加服务。
- 2、"仅部分预览"的文档,不可在线预览部分如存在完整性等问题,可反馈申请退款(可完整预览的文档不适用该条件!)。
- 3、如文档侵犯您的权益,请联系客服反馈,我们会尽快为您处理(人工客服工作时间:9:00-18:30)。
由试样 j的摩 擦 因素 曲线 图 (见 图 3)和 试 样 Ⅱ的 摩 擦 因素 曲线 图 (见 图 4)可 知 :不 同线 速 度 时摩 擦 因 数 曲线 前 部分 值很 小 ,且 比较平 稳 ,前部 分是 膜 层 的摩 擦 因数 ;随着试 验 的进 行 ,不久 后摩 擦 因数 突然 变 为原
收 稿 日期 :20I5 09 24;修 订 日期 :201 6—03~3 J 作 者 简 介 :瞿 志 俊 (1 982)。男 ,江 苏 兴化 人 ,讲 师 ,硕 t, 主要 从 事 数 控 技 术 、机 械 制 造 、 力学 及摩 擦 磨损 方 面 的教 学 与科 研 工 作 。
2016年 第 3期
膜 ,基 材 为 齿 轮 钢 。 采 用 UM F Ⅱ 多功 能 摩 擦 磨 损 试 验 机 对 两 种 试 样 进 行 摩 擦 磨 损 性 能 试 验 研 究 。 结 果 表
明 :试 样 Ⅱ的 摩 擦 磨 损 特 性 比试 样 I的 摩 擦 磨 损 特 性 好 。 关 键 词 :齿 轮 齿 面 ; 沉 积 膜 ;摩 擦 磨 损 性 能
瞿 志 俊 ,等 :齿 轮 齿 面沉 积 膜 摩 擦 磨 损 性 能 试 验 研 究
· 103 ·
来 的几倍 ,原 因是氮化 硅小 球磨 破 了沉积 膜 ,从 而造 成 摩擦 因数 突变 ,突变 后 的摩 擦 因数 是 小球 与试 样 基 体 之 间的摩擦 因数 ,因此摩 擦 因数 突 变 的 时刻 就 是 膜 层 磨 破 的 时 刻 。
第 3期 (总 第 1 96期 ) 2016年 6 月
机 械 工 程 与 自 动 化 M ECHANICAI EN(;-INEERING & AUq、OM ATI()N
文 章 编 号 :1 672—6413(201 6)03 0102—02
NO.3 Jun.
齿 轮 齿 面 沉 积膜 摩 擦 磨 损 性 能试 验 研 究
瞿 志俊 ,王 荣林 ,孙松 丽 , 陆广 华
(南 京 理 工 大 学 泰 州 科 技 学 院 机 械 工 程 学 院 , 江 苏 泰 州 225300)
摘 要 :为 了提 高 齿 轮 齿 面 干 运 转能 力 , 采用 离 子 柬 复 合 沉 积 设 备 ,在 两种 不 同 制 备 工 艺 参 数 下 沉 积 两 种 沉 积
中 图分 类 号 :TH¨7.1:THl32.4l
文 献标 识 码 :A
0 引 言 齿 轮作 为传 动 部 件 在 机 械 行业 中得 到 广 泛应 用 。
齿 轮工 作 时 的受 力和 运 动情 况 十分 复杂 ,由 此 产生 多 种 损伤 形式 ,常 见且 较严 重 的是 断 齿 、破 坏性 点蚀 和破 坏性 胶 合 ,从 而 导致 其 使 用 寿命 缩 短 。在 齿 轮 传 动 过程 中 ,齿面 存 在滚 动摩擦 和 滑动 摩擦 ,齿 面摩 擦会 引 起 齿面 温度 升高 ,过 高 的齿 面 温 度 是 齿 轮胶 合失 效 的主要 原 因l3 J,而且齿 面 摩擦 在点 蚀形 成 、齿根 裂 纹萌 生 与扩 展及 轮齿 断 裂过 程 中起 到 加 速作 用 。因此 为实 现 齿轮 长时 间高 效 可 靠 的运 行 ,齿 轮 不仅 要 具 有 心部 高 的强 度 和耐 冲 击 韧性 ,而 且 齿 面要 有 好 的 耐磨 减摩 特 性 。所 以 ,人 们 将 一 些 新 的表 面 强 化 理 论 及技 术应 用 于 齿轮齿 面 研 究领 域 ,在 齿 轮 齿 面 形 成各 种 耐 磨减 摩 的齿 面膜 层 的摩 擦 磨 损 特性 ,本 文在 f摩 擦 状态 下 进行 销盘 模 式摩 擦 磨 损 试 验 ,获 得 两 种试 样 在 同载荷 、不 同线 速度 下 的摩 擦磨 损特 性 。 1 试 验 部 分 1.1 试 样 制 备
】.2 试 验 方 法
试 验 在 UMT ii多功 能摩 擦 磨损 试 验 机 (见 图 1)
上 进行 。该 试验 采 用 销 盘运 动模 式 ,试 验 时 上试 样 为 4 mrn氮 化 硅 (Si N )小 球 ,下 试 样 为 沉 积 膜 层 试 样 ,
上试样 固定 不动 ,下试 样 旋转 运 动 ,如 图 2所示 。
图 1 uM r~n多功 能 摩 擦 磨 损 试 验 机
图 2 上 、 试 样 之 间 的 销 盘 运 动 模 式
试 验前 用 乙醇 清 浩试 样 摩 擦 表 面 ,在 室 温 条 件 和 干摩 擦 状 态 下 进 行 摩 擦 磨 损 试 验 ,试 验 时 载 荷 为 22 N,分 别在 圆 柱体端 面的不 同半 径上 进行 ,不 同 半径 对 应不 同的线 速度 (见表 1)。每 次 (各 线 速度 )摩擦 磨 损 试验 时 间 由沉积 膜层 磨破 情 况确 定 。 2 结 果 及 分 析 2.1 试样l、试样Ⅱ的摩擦 因数 和沉积膜磨破 所 需时间