8制动试验
制动试验步骤(CRH380)
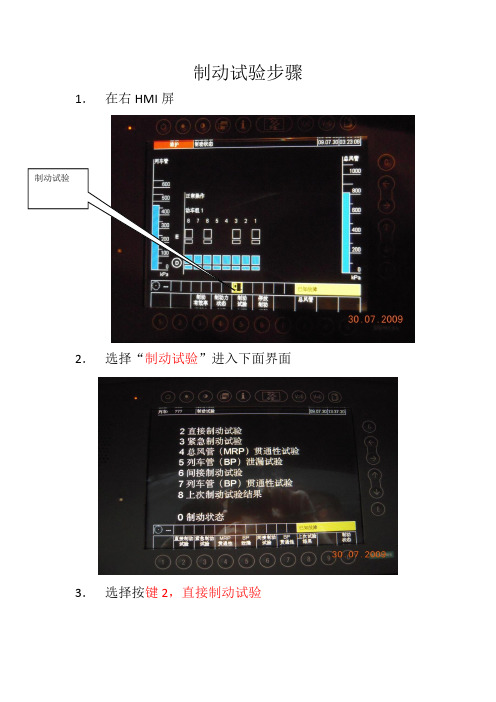
34.按“制动试验”键继续,返回制动试验界面
35.按键7,BP贯通性试验,进入下一界面
36.按“开始试验”进入下一界面
显示内容:
通过后部头车紧急制动阀使BP排风
---检查是否前部头车的BP压力低于260 KPa
37.等待一段时间,显示如下界面
38.等待约几秒,显示如下界面
39.按“停止排风”键停止排风,进入下面界面
显示内容:
通过后部头车紧急制动阀使BP停止排风
---检查是否前部头车的BP压力升高至正常工作压力范围
40.等待几秒,将显示如下界面
41.BP贯通性试验结束,按“制动试验”键继续,返回制动试验界面
42.按“制动状态”键,返回制动主界面
43.按“制动有效率”键,观察制动有效率
44.按“最高限速表”键,进入下一界面
45,按“返回”键
45.按“上次试验结果”,进入如下界面
46.按“显示试验时间”键,进入如下界面
制动试验完成
---检查是否所有制动已施加
制动保持至少10秒
此时,制动管压力将降低
31.等待几秒,将显示下一界面
按“停止排风”键停止BP排风
32.等待约5秒,进入下一界面
显示内容:
通过后部头车的紧急制动阀停止BP排风
---检查是否前部头车的BP压力升高至正常工作压力范围
---检查是否所有制动已缓解
---检查是否所有制动有效
制动试验步骤
1.在右HMI屏
2.选择“制动试验”进入下面界面
3.选择按键2,直接制动试验
4.选择按键1,开始试验
显示内容:
直接制动试验:
按“开始试验”键启动直接制动试验
动车组制动系统检修与调试-CRH2动车组制动系统检修
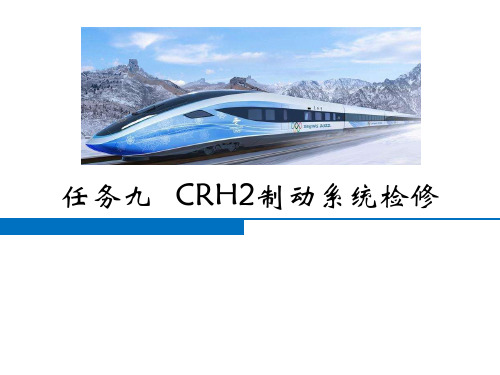
二、制动试验
三)停放制动试验方法 CRH2A统型车与CRH380A统型车才需要做停放制动试验。 1)将制动控制手柄置“运行”位,右旋司机室操纵台“停放制动”旋钮至 “施加”位,施加停放制动;确认动车组产生紧急制动,操作紧急制动复 位,紧急制动不能缓解,通过MON屏确认1、4、5、00车“停放”制动施 加。 2)左旋停放制动旋钮至释放位,确认MON屏制动气缸压力界面1、4、5 、8车“停放”显示消除。操作“紧急复位”按钮,MON屏制动信息界面 “紧急”、“停放”显示消除。
12
三、制动系统二级检修
(一)制动控制装置检查 1)使用四角钥匙、棘轮扳手拆卸制动控制装置相应位置的底板,目视检查底板 无裂纹。 2)目视检查制动控制装置外观状态良好,安装螺栓紧固良好,防松标记无错位 ;手感各配管无漏气。 3)目视检查制动控制装置配线外观良好无破损,配线连接器安装状态良好无松 动。 4)目视检查BCU箱内各电器配件外观状态良好,配线紧固无异常。 5)旋转制动控制装置手柄至开位,打开制动控制装置盖板,目视检查阀类、调 压器、气压开关的外观无异常、安装状态良好,手感各部件无漏气。 6)检查踏面清扫电磁阀外观无破损,安装牢固,连接器安装状态良好无松动。
13
三、制动系统二级检修
(二)风缸检查 1)目视检查主储风缸、供给风缸、控制风缸本体、配管外观无 异常,耳听确认无漏气。 2)目视检查排水阀外观无异常,打开排水阀将各风缸排水,排 水后将排水阀复位。 3)目视检查安全阀铅封状态良好,防松标记无错位。
14
Байду номын сангаас
三、制动系统二级检修
(三)防滑阀检查 1)投入主控钥匙,BCU供电; 2)拨动BCU上拨码开关,如图所示。使SW1=4、SW2=0,SW6向上 ,实行滑行防止阀输出回路自行检测。 3)BCU上拨码开关SW1=4、SW2=0位SW6向上,实行滑行防止阀输 出回路自行检测。判定方法为1至4轴防滑阀应依次排风,闸片动作,共 循环动作两个周期。 4)自检完成后拨动BCU上拨码开关,使SW1=0、SW2=0。 5)关闭制动控制装置盖板。
制动器试验标准

制动器试验标准
制动器试验标准是对制动器进行性能测试和评价的准则和方法。
这些标准通常由国际标准化组织(ISO)或国家标准化组织制定,并被制动系统制造商和相关利益相关者广泛采用。
制动器试验标准可以包括以下内容:
1. 制动力测试:衡量制动器产生的制动力大小和稳定性,通常采用制动力试验机进行。
2. 制动起动性测试:衡量制动器从松开状态到完全制动状态的时间和响应性能。
3. 制动盘温度测试:测试制动盘在连续制动过程中的温度变化情况,以评估制动器的散热性能。
4. 制动器噪音测试:测试制动器在制动过程中产生的噪音水平,以评估制动器的噪声性能。
5. 制动器寿命测试:测试制动器在特定条件下的使用寿命和耐久性。
6. 制动器耐久性测试:测试制动器在不同负荷和使用条件下的耐久性,以模拟实际使用环境。
7. 制动器灵敏度测试:测试制动器对不同输入参数(如制动力、制动温度等)变化的响应灵敏度。
这些标准旨在确保制动器的性能符合设计要求,同时提供一致的测试基准,以便制动器制造商和使用者进行性能比较和选择适合的制动器。
电梯试验方法国标规范

电梯试验方法国标规范电梯试验是电梯行业中非常重要的环节,通过试验可以确保电梯的安全性、可靠性和性能符合国家标准。
下面是电梯试验的一些国标规范。
1.设备检查试验:在电梯安装完成后,需要进行设备检查试验,检查电梯的各项功能是否正常,包括按钮、门、照明等设备。
2.制动试验:制动试验主要是测试电梯的制动系统是否能够可靠地停止电梯运行,检查电梯是否存在制动不良的情况。
3.速度试验:速度试验是测试电梯的运行速度是否在规定范围内,确保电梯的运行速度符合国家标准。
4.过载试验:过载试验主要是测试电梯的载荷能力是否满足规定,检查电梯在承载额定载荷时是否能正常运行。
5.紧急制停试验:紧急制停试验是测试电梯在发生紧急情况时,能否迅速制动并停下。
6.起动试验:起动试验是测试电梯启动时是否平稳,不产生明显的冲击、颠簸等异常情况。
7.开门试验:开门试验是测试电梯的开门是否完全,门是否能够迅速响应,确保乘客的安全。
8.关门试验:关门试验主要是测试电梯的关门速度是否符合国家标准,确保乘客的安全。
9.电气系统试验:电气系统试验主要是测试电梯电气系统的可靠性和性能是否符合国家标准。
10.机械系统试验:机械系统试验主要是测试电梯机械部件的可靠性和性能是否符合国家标准。
11.紧急救援试验:紧急救援试验主要是测试电梯在发生故障时,紧急救援系统是否能正常工作。
在进行电梯试验的过程中,需要按照国家相关标准进行操作,并计量各项试验指标,确保电梯的安全性能符合要求。
此外,还需要对试验过程进行记录,以备验查。
电梯试验是电梯行业中非常重要的一环,通过试验可以保证电梯的安全性和性能符合国家标准。
以上是电梯试验的一些国标规范。
制动系检测

次试验全部完成,提高试验或检测效率。
4)结构简单、安全方便,不需专门的混凝土基础;日常维护 方便、耗电量低。 5)重复性差、占地面积大、需要助跑车道;
(3)惯性式制动试验台
惯性式滚筒制动试验台用旋转飞轮的转动惯量模拟车辆 道路行驶时的平移动能,测试结果与实际工况更为接近。
制动时,轮胎对滚筒表面产生阻力,由于滚筒传动系统具 有一定的惯性,因而滚筒表面将相对于车轮移过一定距离。因 此,惯性式制动试验台可以模拟道路制动试验工况。
(1)反力式制动试验台
(1)驱动装臵 由电动机、减速器和链传动组成。 (2)滚筒装臵 由四个滚筒组成。 每对滚筒独立设臵,有主动
电动机的转动 通过减速器内的蜗轮 蜗杆和圆柱齿轮传动 传递给主动滚筒 通过链传动
滚筒和从动滚筒之分。
传递给从动滚筒
工作过程
(3)测量装臵
主要由测力杠杆、测力传感器和测力弹簧等组成。 测力杠杆一端与传感器连接,另一端与减速器连接 测力杠杆的位移或力
杠杆前端的测力传感器
反映制动力大小的电信号
工 作 过 程
指示与控制装置
(4)举升装置 为了便于汽车出入试验台,在两滚筒之间设有举升装 置,一般由举升器、举升平板和控制开关等组成。
(5)第三滚筒 测量车轮转速;当被检测车轮制动时,转速下降至接近
抱死时,向控制装置发出信号使驱动电机停止转动,以防止
滚筒剥伤轮胎、保护驱动电机。
现用的路试检测检测设备
1.非接触式多功能速度仪
可检测:制动距离、速度、MFDD、减速度、油耗、制动时间
2.制动踏板力计
3.转向盘转动量扭矩检测仪
美国现代便携式制动性能检测设备
VC3000便携式制动性能检测仪
测量参数:
制动器的试验

制动器的试验一、制动器的试验制动器装好以后,必须进行试验。
由于制动器结构不同,制造厂家不同,因而试验方法与标准与不同。
1、2立方以下地下装载机封闭湿式制动器的压力检查:在制动器油液入口处装上气体减压表与压力表(0~0.11MPa ),并向壳体内充气到0.11MPa 为止。
此时关闭压气管,保持3~5min ,如果压力表显示压力下降的趋势,应立即找出原因予以纠正。
2、2立方以上至6立方以下用POSI-STOP 型弹簧制动器总成压力检查:(1)完成总装后用透气塞塞紧。
往制动油液入口充气到0.083MPa 的压力,然后切断进入制动器壳体的空气;(2)让壳体内空气稳定30s ,以补偿空气温度变化,活塞移动和密封唇口的密封;(3)重复加压直至0.083MPa ,至少保持15s ,但不能超过3次加压;(4)如果3次后制动器仍不能保持压力,则拆开检查,确定泄漏原因,并重新装配与试验;(5)用0.552~0.689MPa 的压力替代0.083MPa 的压力重复以上(1)~(5)项的试验;(6)试验得到满意结果后,拆下加压油管,重新装上制动油管,并以常规方法排泄制动器。
二、铲运机制动距离的试验1、铲运机的制动性能是无轨设备的最重要的指标之一,检测方法一般有路试法和台架法。
台架法是利用室内制动性能实验台检测汽车的制动性能,由于其安全易实现的特点,因此绝大多数的铲运机制动性能检测都是采用这种方法。
2、制动距离与车速的关系铲运机应备有行车制动、应急制动(辅助制动)和停车制动系统。
应急制动可以是行车制动系统、停车制动系统具有应急特性或与行车制动、停车制动分开的独立系统。
各制动系统的制动性能为:行车制动的负加速度不小于0.4068g(g 为当地重力加速度,单位为m/s 2),最大反应时间不大于0.35s ,其性能可以使铲运机在按式(1)计算的距离内停车。
在制动初速度等于8km/h 的条件下,行车制动距离应不大于2m: 应急制动的负加速度不小于0.25g( g 为当地重力加速度,单位为m/S 2).最大反应时间不大于0.5s, 其性能可以使铲运机按下式计算的距离内停车。
8T电机车制动距离试验''''

8T蓄电池电机车重载制动距离试验安全技术措施一、试验地点:井下西大巷二、试验前的准备1测量试验地段的坡度。
2.起动(加速)段、最大速度段、计时段及制动段的起始点装设信号灯或明显标志。
3.按照以下要求备足1.5t装满矸石的矿车:8t机车牵引6节4t装满矸石的矿车(附:8t机车牵引车数计算)。
4.指定机车司机,要求工作责任心强、操作技术熟练、持有合格证。
5.检查牵引试验矿车是否完好,轮对转动是否灵活,确保试验过程中不掉道。
6.对试验机车作如下详细的检查:①灯、铃齐全,照明灯光明亮,警铃声音宏亮。
②连接装置、缓冲装置灵活可靠,弹簧无断裂,碰头无裂纹。
机车碰头伸缩长度不小于30mm,矿车碰头伸长为10-30mm。
③制动手轮操作灵活,制动螺栓与螺母无裂纹和磨损,闸瓦厚度不小于15mm,同一制动杆两闸瓦厚度差不大于10mm,闸瓦与车轮踏面的间隙为3-5mm,施闸后应同时贴紧车轮,接触面积大于70%。
④砂箱装满干燥的细砂,砂内应不含有5mm以上的砂粒或杂物,砂管畅通,管口对准轨面中心,操作时能迅速在机车运行前方的轨面上撒砂,停用时,砂箱不应漏砂。
⑤机车的防爆部分要符合防爆性能要求。
7.对试验地段轨道进行整修,轨道质量必须达到优良品。
8.试验地段轨道上的其他车辆及杂物等清理走,保证线路畅通。
9.准备三只秒表,30m皮尺两把及复轨工具等。
10.现场检修工应带齐检修工具。
四、试验方法与步骤:A B C D E说明:图中A(1人):起动指挥兼警戒C(1 人):计时指挥D(1人):计时兼制动指挥E(1人):警戒AB=40米 BC=40米 CD=30米 DE=50米计160米1.试验方法及步骤:①起动指挥在A点指挥机车司机开车起动,当机车运行到B点时,以日常运行的最大速度行驶。
②当机车到C点时,计时指挥人员立即发出开始计时信号,D点计时人员同时按下秒表开始计时。
③当机车到达D点时,计时人员立即按下秒表停止计时,并同时发出制动信号。
项目八 制动机系统的维护与检修

任务一 空气制动系统的认知
一、制动系统概述
3.车辆制动机的种类
轨道电磁制动机在高速乘客列车上与空气制动机 并用。其优点是制动力不受轮轨间的黏着系数限制, 避免车轮滑行,但重量较大,增加了车辆的自重并 加速了钢轨的磨耗。
任务一 空气制动系统的认知
一、制动系统概述
3.车辆制动机的种类
6)线性涡流制动机 当采用线性涡流制动机时,在每一个转向架上设 有可起落的电磁铁,司机操纵制动时,将悬挂在转 向架上导电后起磁感应的电磁铁放下距离轨面上方 几毫米处,
任务一 空气制动系统的认知
二、空气制动系统的组成及作用原理
2)VV120型空气压缩机组 VV120型空气压缩机组如图8-3所示,基本参数见课本 210页表8-1。
任务一 空气制动系统的认知
二、空气制动系统的组成及作用原理
任务一 空气制动系统的认知
二、空气制动系统的组成及作用原理
3)二次冷却器 城轨车辆风源系统所使用的二次冷却器(又称为后冷却 器)均属于表面式换热器。它的冷却方式是冷、热两种流体 分别进入由固体壁面隔开、互不接触的换热器内,热量由热 流体通过壁面传给冷流体,使热流体冷却到必要的温度。一 般城轨车辆上使用的二次冷却器按其传热面形状和结构不同 可分为蛇管式二次冷却器、翅片管式二次冷却器及板翅式二 次冷却器。
任务一 空气制动系统的认知
一、制动系统概述
4.制动机应具备的条件
(9)基础制动装置各部件应有足够的强度,结 构合理,各联结部分灵活耐磨,具有较高的制动效 能;闸瓦耐磨耐热,其摩擦系数应与轮轨黏着系数 相适应。
任务一 空气制动系统的认知
一、制动系统概述4.制动机应备的条件(10)构造简单,便于制造和检修;尽量采用 膜板结构等新技术、新材料,减少研磨件,尽可能 采用标准件、通用件。
Global Spec(轿车盘式制动片中文版)

i全球质量标准轿车盘式制动片的试验标准For Messrs TMD Friction For Messrs Federal Mogul with cooperation by Meinecke / Schog with cooperation by DlugoschFor Messrs Rütgers Automotive For Messrs Honeywell Jurid with cooperation by Leicht / Eisengräber with cooperation by Bräun / Abendroth Prepared on Sep. 12th 2000 Issue status: 08目录页码前言31./2./3. 范围,参考数据,相应的文献 44. 特性数据 55. 产品和功能的描述和检测计划 66. 质量检查 66.1 程序76.2 产品质量的预先计划和试验计划8-9 6.3 活性矩阵106.4 关于理解方法的保护的文献117.1 完整制动片的条件和试验12 7.2. 物理参数13 7.2.1/2/3 密度,多孔性和PH值13-15 7.3. 机械和热性能15 7.3.1. 剪切力和粘接力15-18 7.3.2 冷压缩和热压缩19-23 7.3.3 热传导23-25 7.3.4 盘片膨胀26-27 7.3.5 抗腐蚀性-------背板涂胶27 7.4 摩擦行为,摩擦系数,试验程序28-33 7.5 文献33 7.6 计算制动力矩的公式347.7 附录:衬片的数据表35-388 附录1:根据7.6的制动力矩39-489 附录2: 根据 AK Master的旋转聚集试验49-63前言全球的汽车工业中的客户和供应商之间的关系是变化很快的 ,为了防止越来越激烈的竞争和在成本上的压力, 汽车制造上将越来越多的责任转嫁给了供应商.面对汽车工业的全球化快速发展,全球试验标准对于全球车辆平台和全世界的企业发展, 选择和摩擦片的质量保证来看是必要的和急需的.基于“AK Standard” (参考 Eurospec 1 and 2)工作上,它的成员代表了很大部分的欧洲轿车制动系统和制动片的制造商,the VRI / FEMFM team “AK - QS”和近期的国际试验标准起草了一个全球的检测标准.为了获得大范围的统一和支持, 如下的概念和细节被提交给了国际和国内机构以及相应的全世界范围的企业和公司.试验程序的适应性被描述为应适当的考虑可提供给不同的汽车概念,公司和市场.顾客标准路/车试验和特别的试验可以补充产品的发放.这个建议的基本目标是:- 保护计划阶段和将结果转化到生产中去.- 增加产品的可信度同时可减少检查的费用.- 过程稳定标准上的基本检测频率.-制造过程中的稳定要优先于最终的检测. 要在现场决定过程干涉.-本建议要考虑到的是关于质量控制的大范围的技术革新在本建议中描述的程序是基于QS-9000 / VDA 手册和包含着从定义阶段到参数的确定整个产品质量预计划程序.详情请看第7页的1 – 7.计划要将此建议变为国际标准.1. 目标这些标准描述了发展的系统程序和关于盘式制动片的质量的评估的实验方法.在不同的供应商的试验标准的标准化期间, 目前的试验程序在可重复性和可比较性方面被补充了.一些无意义的试验标准被针对性强的试验标准取代了,还有的一些就取消了.再公差范围的帮助下, 在这些标准中描述的实验方法和试验结果可以对盘式制动片进行快速的评估.经过不同阶段程序的统一处理, 能够保证质量管理标准可被更加清楚的理解并且在客户和供应商之间联系上可能进行全球化执行.2. 范围本标准应用于用液压制动系统的汽车的盘式制动片上.本标准应用于产品开发和目前正在进行的产品质量控制的期间.3. 参考数据,相应文献去了这些标准的要求之外, 如下的文献和标准也要应用:技术图纸和产品特性FMEA (失效模式和结果分析)合法需要 (EU -Guidelines, FMVSS 105 等.)FEMFM特征目录, 现在的版本相应的标准和文献:DIN 53151 Cross-scribingDIN 50021 盐雾试验DIN 53210 锈蚀水平DIN 53209 气泡水平DIN 53167 渗透VDA 621412 涂料试验ISO 6310 压缩性能ISO 6312 剪切性能ISO 9000 f f 质量保证标准VDA 文献 "质量管理 "QS-9000 标准4. 特性数据和参数A BS制动片的热辐射区[ m2 ](假想为一个平的盘)A B 制动片面积[ cm² ]A K 活塞面积[ cm² ]B 制动片的结合物, 剪切试验后的残留原料[ % ]C* 制动系数[ - ]F 力[ N ]F Ab 剪切力[ N ]F B压缩实验中的预压[ kN ]F P压缩实验的试验压力[ kN ]F u* Peripherical force [ N ]G A密度测量中的制动片在空气中的重量[ g ]G B密度测量中的制动片在水中的重量[ g ]G BS制动盘的重量[ N ]dx 最后一个循环的压缩性能[ µm ]dx400 400°C的压缩性能[ µm ]dx RT 室温的压缩性能[ µm ]d1 第一个循环的压缩性能[µm]Md 力矩[ Nm ]P 多孔性[ % ]RT 室温 (18-28°C) [ °C ]S 盘片膨胀,热膨胀[ µm ]S max盘片膨胀最大值[ µm ]T A 起始温度[ °C ]T E 结束温度[ °C ]V 密度测试的制动片体积[ cm³ ]V B 制动片的磨损[ mm, g ]V s制动盘的磨损[ mm, g ]W d热传导[ °C]a 减速[ % ]c 比热[ J/g K ]n 速度[ min -1 ]m 重量[ kg ]t 时间[ s ]密度[ g/cm³ ] p B 制动压力[ bar ]r eff有效摩擦半径[ m ] 热传导系数[ W/m²K ]效率[ % ] µ摩擦系数[ - ]µB 工作摩擦系数[ - ]µF 衰退摩擦系数[ - ]µK 冷却摩擦系数[ - ]µm 平均摩擦系数[ - ]µmax 最大摩擦系数[ - ]µmin 最小摩擦系数[ - ]5. 产品和功能描述盘式制动片是整个制动系统中的重要功能零件. 在制动过程中通过制动钳上活塞的加紧力压向正在转动的制动盘. 汽车的动能就大部分转化为热能. 制动片对于有效性和制动系统给使用者的舒适性又很重要的作用。
《列车制动技术》第八章 列车性能试验

试验项目:
紧急室充气及紧急放风阀漏泄试验:
紧急制动灵敏度及紧急室排风时间试验: 常用制动安定性试验:
三、120阀在705型试验台上的性能试验:
主阀试验:
准备工作:
将主阀与半自动缓解阀组装在一起,主阀
安装面与试验台安装座对正,开控制阀 K1.将主阀抓紧在主阀安装座上;
确认总风源压强在650kPa以上,调压阀调
二、分类: 机车制动试验和车辆制动试验; 制动机性能试验和基础制动性能试验; 三、制动机性能试验: 单个三通阀、分配阀或控制阀在试验台 上的制动性能试验:
制动机性能试验最基本的一步,试验手段
较完善和先进,成批生产制动试验台的厂 家——沈阳机车车辆机械厂。
单个车辆或单个机车的制动性能试验: 即单车试验和机车制动机试验。它们可以 在现车上做,也可以用机车或车辆的制动 装置各个部件组装成的专门试验台来做。 成组车辆或机车车辆组成列车进行的
第六节 单车试验、列车试验、定置试 验、专列静止试验和专列运行试验
一、单车试验: 检查车辆制动机和整个车辆制动装 置在静止状态的性能,合格后才能把车 辆交付运用。
单车试验器
的组成(右图):
操纵阀(简称单阀):有六个作用位置,用
途是控制列车制动管空气压强(充气、排气 或保压),它由回转阀、阀座、阀体和手柄 等组成。回转阀上方通给气阀,回转阀和 阀座的孔路如下图所示:
传动效率试验:
目的:测算基础制动装置的传动效率。
闸调器试验:
目的:测试闸瓦间隙自动调整器的性能。
第二节 闸瓦试验台及闸瓦性能试验
一、闸瓦试验台(1:1试验台): 设计原理:
制动能量等效:
以一个车轮及相应的闸瓦或一个制动盘
制动机检查试验

制动机检查试验制动机检查试验开头,均衡风缸管制动管压力600kpa,工作风缸压力600 kpa,制动缸压力0 kpa,总风缸压力750~900 kpa。
客货车转换法(货车位),单阀自阀手柄运转位,各排风口无泄漏,各螺丝无松脱。
1)自阀减压50kpa保压1分钟,制动缸压力50kpa,每分钟泄漏量不超过20 kpa。
制动缸和工作风缸保压良好。
①下车检查制动缸勾贝,如某一制动缸未伸出(XX制动缸来风管全堵),如某转向架制动缸全未伸出(X转向架制动缸塞门关闭位)。
② 列车管漏,制动缸压力提升。
局减室漏一自阀布满风,自阀直接移至取柄位,不漏为局减室漏。
列车管漏一自阀布满风,自阀直接移至取柄位,待漏至60~70kpa时,自阀移回过减位,起紧急制动。
紧急风缸漏一自阀布满风,自阀直接移至取柄位,待漏至60~70kpa时,自阀移回过减位,不起紧急制动。
③列车管漏,制动缸压力不提升。
安排阀22#总风塞门关一单阀制动区,制动缸压力提升正常。
安排阀与作用阀共用3#塞门关一单阀制动区,制动缸压力不提升。
④ 工作风缸压力下降,制动缸压力下降。
降压风缸漏一自阀布满风移至紧急制动位,保压1分钟,工作风缸压力不下降。
「外漏f自阀运转位,布满风移至取柄位,工作风缸漏。
工作风缸漏y-内漏一自阀运转位,布满风移至取柄位,工作风缸不漏。
⑤ 列车管不漏,制动缸压力不提升。
安排阀侧14#管堵一单阀制动和缓解正常。
作用阀侧14#管堵一单阀制动,制动缸压力不提升。
安排阀侧2#塞门关一单阀制动和缓解正常,自阀紧急制动位,单阀缓解,工作风缸压力下降,自阀回运转位,工作风缸压力不提升。
2)自阀移至最大减压位,排风时间5~7秒,均衡风缸和制动管压力削减140~170kpa,制动缸压力提升至340~360kpa时间7~9秒。
① 制动缸压力达不到340~360kpa。
安排阀侧14#管漏一单阀移至全制位,制动缸压力能达到定压300kpa o作用阀侧14#管漏一单阀移至全制位,制动缸压力达不到定压300kpa。
CRH3型试验程序

附件1:CRH3型动车组检查试验程序一、上车检查1.确认动车组停放股道及型号和止轮器安放状态。
2.库内接车时由在车站始发时的非操纵端上车,如列车门无法电器启动,可通过车门附近的紧急开锁机构在外侧手动开启/关闭列车门。
3.用司机室门钥匙打开驾驶室玻璃门,进入驾驶室4.检查操纵台、付操纵台各开关位于定位;GFX-3A正常显示灯亮。
5.检查操纵台下辅助制动空气塞门和雨刷应急塞门在关闭位。
6.检查控制柜各开关在闭合位。
7.打开安全开关控制柜,确认各旋钮开关定位(垂直位),ATP开关应选择1开位或2开位,接地钥匙在开位。
8.闭合蓄电池开关,确认蓄电池电压表不应低于95V。
9.插入总控钥匙顺时针旋转,方向开关前进或倒车位,激活司机室。
10. MMI屏启动后,通过右侧MMI确认全车停放制动已施加,停放制动指示灯(黄灯)常亮。
11.通过左侧MMI在主页面下,选择软键9进入“开关”选项,按压软键4进入“牵引”页面,确认高压设备切除状态。
并保持该页面。
12.出库前对两端的ETCS进行测试。
二、升弓作业1.扳动受电弓升起开关,确认受电弓升起状态及位置。
此时默认升起的是后端的受电弓,换端后再进行倒弓操作。
保证出库时双弓状态良好。
2.如升弓风压不足时,BCU会自动控制辅助压缩机启动。
司机等待一段时间后再进行一次升弓操作。
3.确认接触网压正常后,等待主断路器“断开”标志由白色变为淡蓝色后,再进行闭合主断路器的操作。
4.主断路器闭合后,主断路器“断开”标志消失。
5.确认所有的辅助供电单元启动正常。
6.确认蓄电池电压表显示120V左右。
7.确认总风MRP压力达到750Kpa以上,紧急制动缓解。
三、ATP、CIR的操作1.进行ATP数据的选择输入和测试:(1)输入司机号按压“回车”键。
(2)选择“等级1”或“等级0”后按压“回车”键。
(3)输入车次号后按压“回车”键。
(4)按规定输入列车参数。
(5)选择F10,“主屏”键。
(6)选择F9,“测试ETCS”键,按压F2“开始测试”键,进行ATP的测试。
制动摩擦片试验项目

制动摩擦片试验项目制动摩擦片试验是对制动系统进行评估和性能测试的重要步骤。
它主要用于测试摩擦片在制动过程中的摩擦性能、磨损情况以及热衰减等参数。
本文将从人类视角出发,详细描述制动摩擦片试验项目的过程和意义。
在进行制动摩擦片试验之前,首先需要准备好试验样品和试验设备。
试验样品通常是摩擦片和制动盘,而试验设备包括制动试验机和相应的测试仪器。
试验过程中,我们需要将试验样品安装到制动试验机上,并通过控制系统模拟真实的制动操作。
试验开始时,制动试验机会施加一定的力或压力来使试验样品开始制动。
通过控制仪器和传感器,我们可以实时监测和记录试验过程中的关键参数,比如制动力、制动时间、摩擦片温度等。
这些数据将被用于后续的分析和评估。
在试验过程中,我们可以通过改变试验条件,比如制动速度、压力等,来模拟不同的制动工况。
通过对不同工况下的试验数据进行对比分析,我们可以评估摩擦片的摩擦性能和磨损情况。
同时,我们还可以通过测量摩擦片的温度变化来评估其热衰减性能。
制动摩擦片试验项目的意义在于确保制动系统的安全和可靠性。
制动系统是车辆行驶过程中的重要保障,而摩擦片作为制动系统的关键部件,其性能直接影响着制动效果和持久性。
通过制动摩擦片试验,我们可以及时了解摩擦片的性能和磨损情况,及时采取措施进行维修或更换,从而保障制动系统的正常运行。
制动摩擦片试验项目是对制动系统进行评估和性能测试的重要环节。
通过模拟真实制动工况,我们可以评估摩擦片的摩擦性能、磨损情况和热衰减性能。
这一过程对于保障制动系统的安全和可靠性至关重要。
通过制动摩擦片试验的结果,我们可以及时采取维修或更换措施,确保车辆的制动效果和持久性。
制动摩擦片试验项目
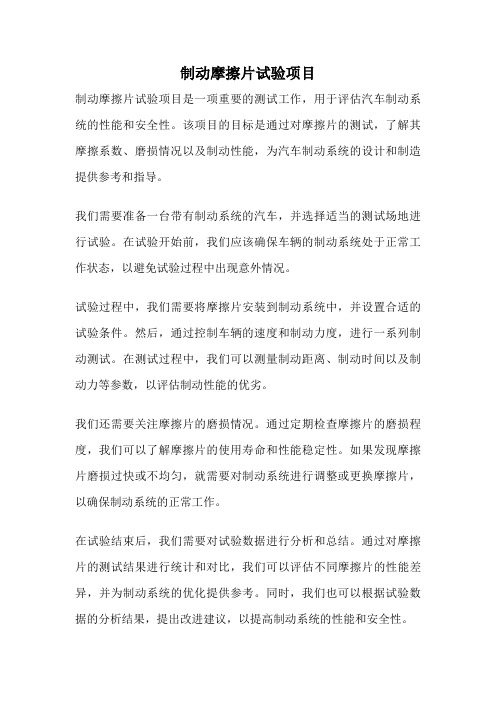
制动摩擦片试验项目
制动摩擦片试验项目是一项重要的测试工作,用于评估汽车制动系统的性能和安全性。
该项目的目标是通过对摩擦片的测试,了解其摩擦系数、磨损情况以及制动性能,为汽车制动系统的设计和制造提供参考和指导。
我们需要准备一台带有制动系统的汽车,并选择适当的测试场地进行试验。
在试验开始前,我们应该确保车辆的制动系统处于正常工作状态,以避免试验过程中出现意外情况。
试验过程中,我们需要将摩擦片安装到制动系统中,并设置合适的试验条件。
然后,通过控制车辆的速度和制动力度,进行一系列制动测试。
在测试过程中,我们可以测量制动距离、制动时间以及制动力等参数,以评估制动性能的优劣。
我们还需要关注摩擦片的磨损情况。
通过定期检查摩擦片的磨损程度,我们可以了解摩擦片的使用寿命和性能稳定性。
如果发现摩擦片磨损过快或不均匀,就需要对制动系统进行调整或更换摩擦片,以确保制动系统的正常工作。
在试验结束后,我们需要对试验数据进行分析和总结。
通过对摩擦片的测试结果进行统计和对比,我们可以评估不同摩擦片的性能差异,并为制动系统的优化提供参考。
同时,我们也可以根据试验数据的分析结果,提出改进建议,以提高制动系统的性能和安全性。
制动摩擦片试验项目是一项重要且复杂的工作。
通过科学的试验设计和数据分析,我们可以全面了解制动系统的性能和摩擦片的特性,为汽车制动技术的发展和改进提供有力支持。
轴重与制动性能检测实施细则

轴重与制动性能检测实施细则一、检测目的与标准GB7258-2004《机动车运行安全技术条件》规定:“6.15”汽车用制动力检验制动性能:1、汽车在制动试验台上检测制动力应符合下表现定的要求。
对空载检验制动力有质疑的,可用下表满载检验制动力要求进行检验:(1)行车制动率标准机动车类型制动力总和与整车重量的百分比轴制动力与轴荷a的百分比空载满载前轴后轴乘用车、总质量不大于3500kg的货车≥60 ≥50 ≥60b ≥20b 其他汽车、汽车列车≥60 ≥50 ≥60b-a 用平板制动检验台检验乘用车时应按动态轴荷计算b 空载和满载状态下测试应满足此要求(2)制动不平衡率合格标准内容要求前轴(左右轮制动力差的最大值/左右轮最大制≤20%动力中的大值)后轴及其他轴(轴制动力≥轴荷*60%时,左右轮制动力差的最大值/左右轮最大制动力中的大值)≤24%后轴及其他轴(轴制动力<轴荷*60%时,左右轮制动力差的最大值/该轴轴荷)≤8%(3)制动协调时间合格标准机动车制动形式协调合格时间液压制动0.35s气压制动0.60s汽车列车、铰接客车、铰接式无轨电车0.80s注:综检站GB18565规定协调时间:对采用液压制动系的车辆不得大于0.35 s;对采用气压制动系的车辆不得大于0.56s。
(4)车轮阻滞力合格标准各车轮的阻滞力占该轴轴荷百分比≤5%(5)驻车制动力合格标准机动车类型合格标准总质量/整备质量≥1.2 驻车制动力总和占整车重量百分比≥20%总质量/整备质量<1.2 驻车制动力总和占整车重量百分比≥15%(6)制动完全释放时间要求(仅对汽车要求):汽车制动完全释放时间(从松开制动踏板到制动消除所需要的时间)不应大于0.80s。
(7)进行制动性能检验时的制动踏板力或制动气压应符合以下要求:(a) 满载检验时①气压制动系:气压表的指示气压≤额定工作气压②液压制动系:踏板力,乘用车≤500N其它机动车≤700N(b) 空载检验时①气压制动系:气压表的指示气压≤600kPa②液压制动系:踏板力,乘用车≤400N其它机动车≤450N两轮、边三轮摩托车和轻便摩托车检验时,踏板力不应大于400 N,手握力不应大于 250 N。
一汽大众tl211标准

按验收标准,试验按 IR (红外线)—光谱.
4.3 施漆方法与漆层厚度(μm)
见表 1
表1
序
系列
涂底漆 单层喷漆 双层喷漆 多层喷漆 单层
号
钢琴漆
1 漆层总厚度 10~50 20~40 30~90 32~135 67~165
2 粘附底漆
2~10 -
2~10
2~10
2~10
或
20~50
3 打底漆/
20~50 -
5.1.2 低温老化
技术要求按表 2 的 Nr 2,必须满足要求.
在热老化之后,用同一个试样完成低温老
化试验
试验时间 24 h
试验温度(-40±3)℃
紧接着在室温下适应环境至少 30 min
塑料外装件的喷漆技术
技术要求
TL 211
共8 页 第 5 页
序号 5.2 5.2.1
6 6.1 6.2 7 8
双层钢琴漆
>90
单层钢琴漆
>90
有光泽单色漆、珠光效应漆和金属漆
>90(-5 有条件地到-10)
其他种漆
根据图纸或表面负荷手册 LAH 983 018
1.2 颜色按 DIN 5033-4,DIN 6174,DIN 6175-2 按 VW 501 95
(适用于首次试样和批量生产颜色)
1.3 结构
测量系统:包括 Wave-scan(视觉扫描)在内,按制造者的说明测量.
双层 钢琴漆 67~165 2~10
20~50
10~35 15~35 10~35 10~35 55~70
塑料外装件的喷漆技术
技术要求
TL 211
共8 页 第 4 页
5 性能要求
- 1、下载文档前请自行甄别文档内容的完整性,平台不提供额外的编辑、内容补充、找答案等附加服务。
- 2、"仅部分预览"的文档,不可在线预览部分如存在完整性等问题,可反馈申请退款(可完整预览的文档不适用该条件!)。
- 3、如文档侵犯您的权益,请联系客服反馈,我们会尽快为您处理(人工客服工作时间:9:00-18:30)。
一、制动性能试验的种类 制动机性能试验 基础制动性能试验
单阀制动性能试验 单车制动性能试验 列车制动性能试验
1
第八章 制动性能试验
一、制动性能试验的种类 制动机性能试验 基础制动性能试验 闸瓦性能试验
制动粘着试验
传动效率试验 闸调器试验 货车手制动机性能试验
2
第八章 制动性能试验
8
环试验 试验分为测力试验和循环试验两部分。 a 测力试验 将手制动机安装在循环试验台上,对手制动 机的手轮输入156N.m的力矩,测试手制动机 链条在不同行程位置的输出拉力。 b 循环试验 试验时对手制动机输入373N.m的力矩。循环 试验共进行4500次,试验分为9个行程,每个 行程进行500次。
4
第八章 制动性能试验
(2)其他各种分配阀的试验 货车120型空气控制阀在WK-120试验台进 行试验。客车104电空阀在104型电空试验 台进行试验。 客车F8型分配阀和F8加电空在F8型电空试 验台进行试验。 (3)各种分配阀的试验,按各自的试验方法 进行,并按相应的技术条件检查其性能是否 符合要求。
二、单阀性能试验 通过试验台试验,检验分配阀的各项性能 要求,并能符合单车及列车的试验要求, 以保证行车安全。 不同形式的客货车三通阀和分配阀要在不 同形式的试验台上进行试验,并要执行各 自的试验规范。
3
第八章 制动性能试验
(1)103和104型分配阀在705型试验台上试 验 要进行主阀试验(包括初充气和充气位漏泄 试验,紧急制动位漏泄试验,制动和缓解灵 敏度试验,局减阀试验,稳定试验);104 阀紧急增压部分试验(已增加垫圈的);紧 急二段阀跃升试验(103阀);全缓解试验; 减速缓解和空车位压力试验(103阀);均 衡灵敏度试验;紧急阀试验(包括紧急时充 气和紧急放风阀漏泄试验,紧急灵敏度及紧 急时排风试验,安定试验)。
5
第八章 制动性能试验
三、单车制动性能试验 单车试验的目的是检查客货车制动机和整 个车辆制动装置在静止状态的性能。 试验按TB/1492-1983《铁路客货车制动机 单车试验方法》进行。要进行制动管漏泄 试验,全车漏泄试验,制动、缓解感度试 验,制动安定试验,阶段缓解试验,紧急 制动试验,紧急制动阀作用试验,手制动 机作用试验。 试验设备有客车或货车单车试验器、压力 表等。
9
明德求索 锲而不舍
10
7
第八章 制动性能试验
四、列车制动性能试验 2.列车运行试验: 列车运行试验的目的是检查列车制动机在运行 状态的性能。 试验参照AAR标准进行。在不同速度等级下进 行紧急制动试验。分别测定列车初速度、列车 减速度,列车制动距离及制动时间、首尾车的 制动管和制动缸压力变化曲线。停车后要检查 制动系统的状态及车轮踏面有无擦伤情况。 试验设备有制动试验车、无线电对讲机、压力 传感器、压力传感器配套用放大器、光线示波 器、制动速度和制动距离测试仪、压力表等。
6
第八章 制动性能试验
四、列车制动性能试验 1.列车定置试验: 列车定置试验的目的是检查整个列车制动机在 静止状态的性能。 试验参照AAR标准进行。试验前要对机车制动 机进行单机性能检查,要检查列车制动系统各 部分漏泄情况。再分别进行漏泄试验、初充气 试验、制动缓解感度试验、制动安定试验、紧 急制动试验、拉车长阀试验等。试验设备有无 线电对讲机、压力传感器、压力传感器配套用 放大器、光线示波器、压力表等。