汽车设计九(制动系设计)
汽车设计课件--制动系设计62页PPT

谢谢!
36、自己的鞋子,自己知道紧在哪里。——西班牙
37、我们唯一不会改正的缺点是软弱。——拉罗什福科
xiexie! 38、我这个人走得很慢,但是我从不后退。——亚伯拉罕·林肯
39、勿问成功的秘诀为何,且尽全力做你应该做的事吧。——美华纳
40、学而不思则罔,思而不学则殆。——孔子
1、不要轻言放弃,否则对不起自己。
2、要冒一次险!整个生命就是一场冒险。走得最远的人,常是愿意 去做,并愿意去冒险的人。“稳妥”之船,从未能从岸边走远。-戴尔.卡耐基。
梦 境
3、人生就像一杯没有加糖的咖啡,喝起来是苦涩的,回味起来却有 久久不会退去的余香。
汽车设计课件--制动系设计 4、守业的最好办法就是不断的发展。 记忆,我不求天长地久的美景,我只要生生世世的轮 回里有你。
毕业设计论文—汽车制动系统的设计
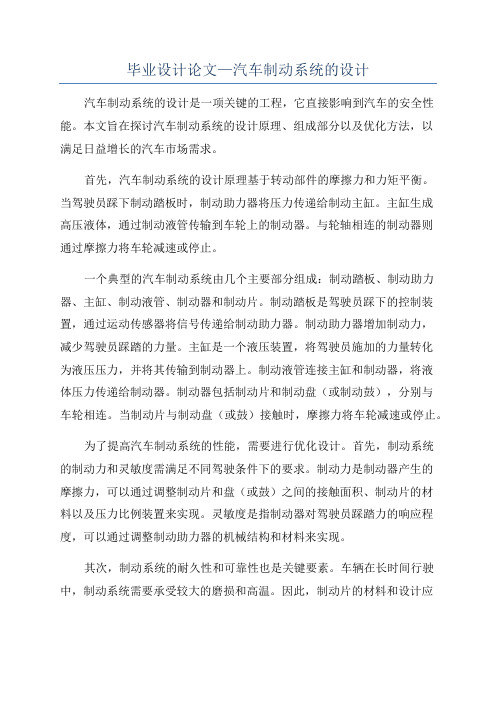
毕业设计论文—汽车制动系统的设计汽车制动系统的设计是一项关键的工程,它直接影响到汽车的安全性能。
本文旨在探讨汽车制动系统的设计原理、组成部分以及优化方法,以满足日益增长的汽车市场需求。
首先,汽车制动系统的设计原理基于转动部件的摩擦力和力矩平衡。
当驾驶员踩下制动踏板时,制动助力器将压力传递给制动主缸。
主缸生成高压液体,通过制动液管传输到车轮上的制动器。
与轮轴相连的制动器则通过摩擦力将车轮减速或停止。
一个典型的汽车制动系统由几个主要部分组成:制动踏板、制动助力器、主缸、制动液管、制动器和制动片。
制动踏板是驾驶员踩下的控制装置,通过运动传感器将信号传递给制动助力器。
制动助力器增加制动力,减少驾驶员踩踏的力量。
主缸是一个液压装置,将驾驶员施加的力量转化为液压压力,并将其传输到制动器上。
制动液管连接主缸和制动器,将液体压力传递给制动器。
制动器包括制动片和制动盘(或制动鼓),分别与车轮相连。
当制动片与制动盘(或鼓)接触时,摩擦力将车轮减速或停止。
为了提高汽车制动系统的性能,需要进行优化设计。
首先,制动系统的制动力和灵敏度需满足不同驾驶条件下的要求。
制动力是制动器产生的摩擦力,可以通过调整制动片和盘(或鼓)之间的接触面积、制动片的材料以及压力比例装置来实现。
灵敏度是指制动器对驾驶员踩踏力的响应程度,可以通过调整制动助力器的机械结构和材料来实现。
其次,制动系统的耐久性和可靠性也是关键要素。
车辆在长时间行驶中,制动系统需要承受较大的磨损和高温。
因此,制动片的材料和设计应具有良好的耐磨和耐高温性能。
此外,制动液管和连接件应具有高强度和密封性,以防止液压泄漏和系统失效。
最后,制动系统的安全性是设计的重要目标。
为了提高系统的安全性,制动系统应具有防抱死制动系统(ABS)和电子制动力分配系统(EBD)。
ABS系统能够避免车轮因制动过度而导致车辆失控,而EBD系统能够根据不同车轮的情况分配适当的制动力,以实现最佳制动性能。
汽车设计课件_8制动系设计(PPT45页)
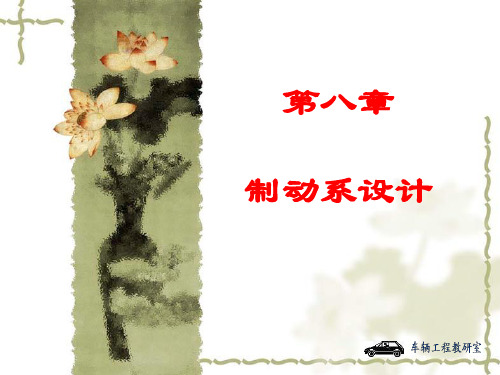
1 B1C1 B1B1 cos1
对于紧蹄的径向变形δ1和压力p1为:
1
p1
p11mmaaxxssinin((aa1111))
2)一个自由度的紧蹄摩擦衬片的径向变形规律
1 B1C1 B1B1 sin 1 A1B1 sin 1d
表面的径向变形和压力为:
3.摩擦衬块外半径R2与内半径R1 外半径R2与内半径R1的比值不大于1.5 ; 若此比值偏大,工作时衬块的外缘与内侧圆周速度相差较多, 磨损不均匀,接触面积减少,导致制动力矩变化大。
§8-4制动器的设计与计算
一、鼓式制动器的设计计算
1.压力沿衬片长度方向的分布规律
1)两个自由度的紧蹄摩擦衬片的径向变形规律
X型管路布置特点:
•结构简单; •直行制动时任一回路失效,剩余总制动力都能保持正常值的50%;
•一旦某一管路损坏造成制动力不对称,此时前轮将朝制动力大的一边 绕主销转动,使汽车丧失稳定性。
•这种方案适用于主销偏移距为负值(达20mm)的汽车上。
HI、HH、LL型管路布置特点: •结构都比较复杂; •LL型和HH型在任一回路失效时,前、后制动力比值均与正常情 况下相同; •LL型和HH型的剩余总制动力可达正常值的50; •HI型单用一轴半回路时,剩余制动力较大, 但此时与LL型相比,紧急制动情况下后轮很容易先抱死。
制动器的制动效能相当高; 倒车制动时,制动效能明显下降;
两蹄片磨损均匀,寿命相同; 结构略显复杂。
3.双向双领蹄式
双领蹄演示
两蹄片浮动,始终为领蹄。
制动效能相当高,而且不变,磨损均匀,寿命相同。
4.双从蹄式
双向双领蹄演示
两块蹄片各有自己的固定支点,而且两固定支点位于 两蹄的不同端。
汽车制动系设计方案.pptx
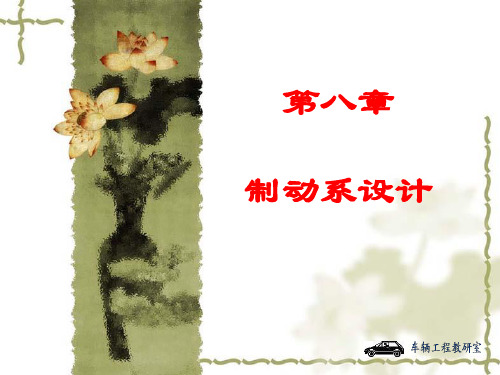
§8-3制动器主要参数的确定
一、鼓式制动器主要参数的确定
1.制动鼓内径D 轿车:D/Dr=0.64~0.74 货车:D/Dr=0.70~0.83
2.摩擦衬片宽度b和包角β 包角一般不宜大于120°。
3.摩擦衬片起始角β0
4.制动器中心到张开力F0作用线的距离e 使距离e尽可能大, 初步设计时可暂定e=0.8R左右。
双从蹄演示
5.单向增力式
两蹄片只有一个固定支点,两蹄下端经推杆 相互连接成一体 。
制动器效能很高,制动器效能稳定性相当差。
单向增力式演示
6.双向增力式
两蹄片端部各有一个制动时不同时使用的共用支 点,支点下方有张开装置,两蹄片下方经推杆连 接成一体 。
制动器效能很高,制动器效能稳定性比较差。
双向增力式演示
二、制动系的分类:
行车制动装置 驻车制动装置 应急制动装置 辅助制动装置
汽车制动系统图组
三、制动系的设计要求:
1)足够的制动能力; 2)工作可靠 ; 3)不应当丧失操纵性和方向稳定性 ; 4)防止水和污泥进入制动器工作表面; 5)热稳定性良好 ; 6)操纵轻便,并具有良好的随动性 ; 7)噪声尽可能小; 8)作用滞后性应尽可能短; 9)摩擦衬片(块)应有足够的使用寿命; 10)调整间隙工作容易; 11)报警装置 。
§8-2制动器的结构方案分析
摩擦式 液力式 -----缓速器 电磁式
一、鼓式制动器
摩擦副结构
鼓式 盘式 带式-----中央制动器
分领从蹄式、双领蹄式、双向双领蹄式、双从蹄式、单向增力式、 双向增力式等几种 。
不同形式鼓式制动器的主要区别:
①蹄片固定支点的数量和位置不同; ②张开装置的形式与数量不同; ③制动时两块蹄片之间有无相互作用。
汽车制动系设计
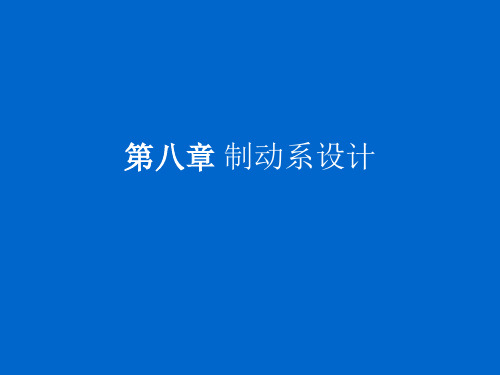
一、比能量耗散率e: 单位衬片(衬块)摩擦面积在单位时间耗 散的能量,单位是W/mm2
e1
ma
v12 4tA1
v22
e2
ma
v12 v22 4tA2
1
t v1 v2 j
紧急制动到停车 v2 0, 1
e1
ma v12 4tA1
制动器效能的稳定性主要取决于其效能因 数对摩擦因数的敏感性,即
第二节 制动器的结构方案分析
二、鼓式制动器 1.鼓式制动器的分类 – 不同型式鼓式制动器的主要区别如下: (1) 蹄片固定支点的数量和位置不同。 (2) 张开装置的型式和数量不同。 (3) 制动时两块蹄片之间有无相互作用。 鼓式制动器可分为领从蹄式、双领蹄式、双
第二节 制
单双 领向 向
从双 双
蹄领 领 式蹄 蹄
式式
双 从 蹄
式
单双 向向 增增 力力
式式
钳盘式
全盘式
固定钳式
浮动钳式
滑动钳式
摆动钳式
第二节 制动器的结构方案分析
一、制动器效能 制动器效能的含义是在单位输入压力或力 的作用下所输出的力或力矩。它常用制动 器效能因数来表示,定义为在制动鼓或制 动盘的作用半径上所得到的摩擦力与输入 力之比
, e2
ma v12 4tA2
(1
)
鼓式制动器:当j=0.6g,v1=100km/h时,e≤1.8W/mm2 盘式制动器:当j=0.6g,v1=100km/h时,e≤6.0W/mm2 二、比摩擦力f0:单位衬片(衬块)摩擦面积的制动器摩擦力 ,
单位是N/mm2
f0
制动系设计汽车设计
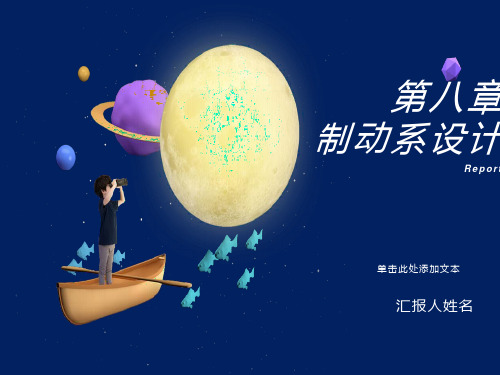
三、摩擦衬片(衬块)
1)具有一定的稳定的摩擦因数。 2)具有良好的耐磨性。 3)要有尽可能小的压缩率和膨胀率。 4)制动时不易产生噪声,对环境无污染。 5)应采用对人体无害的摩擦材料。 6)有较高的耐挤压强度和冲击强度,以及足够的抗剪切能力。 7)摩擦衬块的热传导率应控制在一定范围。
石棉摩阻材料:
§8-4制动器的设计与计算
一、鼓式制动器的设计计算 对于紧蹄的径向变形δ1和压力p1为: 两个自由度的紧蹄摩擦衬片的径向变形规律: 1.压力沿衬片长度方向的分布规律 一个自由度的紧蹄摩擦衬片的径向变形规律 表面的径向变形和压力为: 新蹄片压力沿摩擦衬片长度的分布符合正弦曲线规律
计算蹄片上的制动力矩 法向力 制动力矩
初步设计时 一般 制动踏板工作行程
§8-6制动力调节机构
一、限压阀 限压阀适用于轴距短且质心高,从而制动时轴荷转移较多的轻型汽车,特别是轻型和微型轿车。 二、制动防抱死机构(ABS)
01
02
03
§8-7 制动器的主要结构元件
制动鼓应当有足够的强度、刚度和热容量,与摩擦衬片材料相配合,又应当有较高的摩擦因数。
气压制动:
全液压动力制动
闭式(常压式)
开式(常流式)
操纵轻便、工作可靠、不易出故障、维修保养方便
结构复杂、笨重、成本高;作用滞后时间较长(0.3~0.9s);簧下质量大;噪声大。
真空伺服制动
空气伺服制动
液压伺服制动
0.05~0.07MPa
0.6~0.7MPa
分路系统
全车的所有行车制动器的液压或气压管路分为两个或多个互相独立的回路,其中一个回路失效后,仍可利用其它完好的回路起制动作用。
制造工艺复杂、成本高、容易产生噪声和刮伤对偶
制动系

课程结束! 课程结束!
《汽车设计》 PowerPoint版 版权所有者:南航赵又群 15
二、盘式制动器的设计计算
1、制动器制动力矩 2、衬块的平均半径 3、衬块的有效半径 4、m=R1/R2的选取 5、制造工艺
《汽车设计》 PowerPoint版 版权所有者:南航赵又群 12
§8-4 制动器设计与计算 (p203-210)
三、衬片磨损特性的计算 p207-209 1. 有效因素 2. 能力负荷 3. 评价指标一:比能量耗散率 4. 评价指标二:比摩擦力 四、前、后轮制动器制动力矩的确定 p209 五、应急制动和驻车制动所需的制动力矩 p209210
制动系
《汽车设计》 PowerPoint版
版权所有者:南航赵又群
1
第八章 制动系设计
第八章 制动系设计 8-1 概述 8-2 制动器结构方案分析 8-3 制动器主要参数的确定 8-4 制动器的设计计算 8-5 制动驱动机构 制动力调节机构( 8-6 制动力调节机构(略) 制动器的主要结构元件( 8-7 制动器的主要结构元件(略)
《汽车设计》 PowerPoHale Waihona Puke nt版 版权所有者:南航赵又群 3
§8-2 制动器结构方案分析
(p196-201) p196-201)
分类:
按耗散汽车能量的方式分:摩擦式、液力式、 电磁式和电涡流式等几种。 摩擦式制动器就其摩擦副的结构型式可分为鼓 式、盘式和带式三种。带式的只用作中央制动器。 目前,货车行车制动器大多数用鼓式制动器,并安 装在汽车车轮处。但是,用独立悬架的汽车也有少 数行车制动器安装在驱动桥的半轴上。
《汽车设计》 PowerPoint版 版权所有者:南航赵又群 4
汽车制动系统的设计

摘要汽车是现代交通工具中用得最多,最普遍,也是最方便的交通运输工具。
汽车制动系是汽车底盘上的一个重要系统,它是制约汽车运动的装置。
而制动器又是制动系中直接作用制约汽车运动的一个关健装置,是汽车上最重要的安全件。
汽车的制动性能直接影响汽车的行驶安全性。
随着公路业的迅速发展和车流密度的日益增大,人们对安全性、可靠性要求越来越高,为保证人身和车辆的安全,必须为汽车配备十分可靠的制动系统。
本说明书主要设计了哈飞赛豹轿车制动系统。
首先介绍了汽车制动系统的发展、结构、分类,并通过对鼓式制动器和盘式制动器的结构及优缺点进行分析。
最终确定方案采用液压双回路前盘后鼓式制动器。
除此之外,它还对前后制动器、制动主缸进行设计计算,主要部件的参数选择及制动管路布置形式等的设计过程。
关键字:制动;鼓式制动器;盘式制动器;液压;制动主缸ABSTRACTAutomobile is the modern traffic tools, the most common used most, also be the most convenient traffic transportation. Automobile brake system is automobile chassis to an important system, it is restricted by the car of the movement of the device. And the brake is brake system directly effect the automobile sport in a restricted key device, is the most important safety car parts. The automobile braking performance directly influence the car driving safety. With the rapid development of the industry and highway traffic density increases day by day, the people to the safety and reliability of the demand is higher and higher, to ensure the safety of the person and vehicles, must be equipped with very reliable car brake system.This manual mainly designed saibao hafei car brake system. First this paper reviewed the automobile braking system development, structure, classification, and through to the drum brake disc brake and the structure of the advantages and disadvantages and analyzed. Ultimately determine the scheme adopts hydraulic double circuit qianpan hougu type brake. In addition, it's still around to brake and brake main cylinder design, calculation of the main parts of parameter selection and brake pipe, the design process of decorate a form, etc.Key words: Braking; Brake drum; Brake disc; Hydroid pressure;Braking cylinder目录摘要 (Ⅰ)Abstract (Ⅱ)第1章绪论 (1)1.1汽车制动系的研究的目的和意义 (1)1.2汽车制动系统的研究现状和发展趋势 (1)1.3汽车制动系设的计要求 (5)第2章制动系统总体方案的确定 (7)2.1 制动系统的分类及作用 (7)2.2 制动系统的主要参数的确定及计算 (8)2.2.1 制动力与制动力分配系数 (8)2.2.2 同步附着系数 (9)2.2.3 制动器最大制动力矩 (9)2.2.4 制动器因数 (10)2.3 本章小结 (11)第3章制动驱动机构的设计 (12)3.1 制动驱动机构的结构型式选择 (12)3.2 液压制动驱动机构的设计计算 (13)3.2.1 制动轮缸直径与工作容积 (13)3.2.2 制动主缸直径与工作容积 (14)3.2.3 制动踏板力与踏板的行程 (14)3.3 本章小结 (15)第4章制动器设计和计算 (16)4.1 制动器方案确定 (16)4.1.1鼓式制动器 (16)4.1.2盘式制动器 (18)4.2 鼓、盘式制动器的主要参数的确定 (19)4.2.1 鼓式制动器的结构参数和摩擦系数 (19)4.2.2 盘式制动器主要参数的确定 (20)4.3 制动器的设计与计算 (21)4.3.1 制动蹄摩擦面的压力分布规律及径向变形规律 (21)4.3.2 制动蹄片上的制动力矩 (22)4.3.3 摩擦衬块的磨损特性计算 (23)4.3.4 制动器热容量和温升的核算 (25)4.3.5 盘式制动器制动力矩的计算 (26)4.3.6驻车制动计算 (27)4.4 制动器主要零部件的结构设计 (28)4.4.1 制动鼓 (28)4.4.2 制动蹄 (29)4.4.3 制动底板 (30)4.4.4 制动蹄的支承 (30)4.4.5 制动轮缸 (30)4.4.6 制动盘 (30)4.4.7 制动钳 (31)4.4.8 制动块 (31)4.4.9 摩擦材料 (31)4.4.10 制动器间隙的调整方法及响应机构 (31)4.5 本章小结 (32)结论 (33)参考文献 (34)致谢 (35)附录 (36)第1章绪论1.1汽车制动系的研究的目的和意义汽车制动系是用于使行驶中的汽车减速或停车,使下坡行驶的汽车车速保持稳定以及使已停止的汽车停在原地(包括在斜坡上)驻留不动的机构,汽车制动系直接影响着汽车行驶的安全性和停车的可靠性。
汽车制动系设计方案

功能
制动系统的功能是减缓或停止车辆的行驶,确保安全。
制动系统的工作原理
基础原理
制动系统利用摩擦力来减缓或停止车辆的行驶。当驾驶员踩下制动踏板时,制动 系统会通过摩擦力将车辆的动能转化为热能,从而实现减速或停车。
部件与流程
制动系统的主要部件包括制动踏板、制动液、制动管路、制动器等。当驾驶员踩 下制动踏板时,制动踏板会推动制动液,通过制动管路将压力传递到制动器,从 而产生摩擦力。
研究现状和发展趋势
目前,国内外对于汽车制动系的研究和 应用已经十分广泛,涉及制动器、制动 液、制动管路等多个方面。
制动管路向着轻量化、集成化方向发展 。
制动液向着环保、高性能方向发展;
发展趋势主要表现为
制动器向着盘式、鼓式、电磁式等多种 形式并存的方向发展;
02
制动系统设计基础
制动系统概述
定义
设计方案应考虑制动系统的可靠性, 确保制动器、制动管路等部件的耐用 性和稳定性,避免制动系统在长期使 用中出现故障。
03
操作性分析
设计方案应考虑制动系统的操作便捷 性,包括制动踏板的行程、踏板力度 等,以便驾驶员能够轻松操作制动系 统。
设计方案制造成本估算
材料成本
01
估算制动系统所需原材料的成本,包括制动器、制动盘、制动
制动系统优化方法
仿真分析
利用计算机仿真技术对制动系统进行 建模和分析,预测制动力矩、制动距
离和制动稳定性等性能指标。
结构设计优化
通过对制动系统的结构进行优化设 计,提高制动器的刚度和强度,提
高制动性能和稳定性。
实验测试
通过实验测试对制动系统进行实际 测量和评估,获取制动性能的实际 数据,指导优化设计。
制动系设计

第二节 制动器的结构方案分析
4. 盘式制动器
与鼓式制动器相比盘式制动器具有: ① 热稳定性好 ② 水稳定性好 ③ 制动力矩与汽车运动方向无关 ④ 易于构成双回路制动系 ⑤ 尺寸小、质量小、散热良好 ⑥ 衬块磨损均匀 ⑦ 更换衬块容易;缩短了制动协调时间
⑧ 易于实现间隙自动调整。
第二节 制动器的结构方案分析
第一节 概述
6. 制动系设计应满足的要求
① 具有足够的制动效能(行车制动以制动减速度和制动距离为 评价指标;驻车制动以可靠停使的最大坡度为评价指标)
② 工作可靠 ③ 制动时不应当丧失操纵性和方向稳定性 ④ 防止水和污泥进入制动器工作表面 ⑤ 热稳定性良好 ⑥ 操纵轻便,并具有良好的随动性
第二节 制动器的结构方案分析
作业
如右图所示,车辆的质量为m,制动减速度为a, 地面附着系数为φ,其余参数如图所示,试求车
辆在制动时,前后桥制动器的最大制动力。
本章主要内容
第一节 概述 第二节 制动器的结构方案分析 第三节 制动器的设计 第四节 制动驱动系统
第一节 概述
1. 制动系的功能
① 能够以控制和重复的形式降低车速,在需要时可将车停下来 ② 能够在下坡时保证车辆以稳定车速行驶 ③ 使汽可靠地停在原地或坡道上
第一节 概述
2. ABS防抱死刹车系统
第三节 制动器设计
1. 行车制动
第三节 制动器设计
2. 制动力分配曲线
第三节 制动器设计
3. 驻车制动
第三节 制动器设计
4. 弹簧式盘式制动器
第三节 制动器设计
5. 多片湿式制动器设计
第四节 制动驱动系统
1. 驱动形式
① 机械制动 ② 气压制动 ③ 液压制动
汽车设计课件8制动系设计
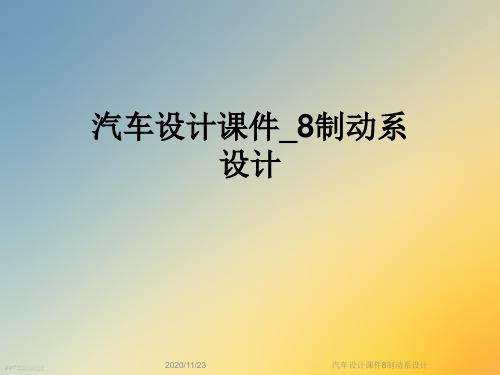
•图d):力多边形求摩擦力的合力F。力F应 与力P垂直。
•图d,e):用索多边形求力F的作用点位置。
•任选一点H,以H点为中心,作线,a,b,…y,
从力f1的延长线任取一点G,作a ′平行于a,
交f2的延长线于J 点,…一直到与f10的延长
线交于K点。过K点作线y ′平行于y,过G点
作线x ′平行于x,两线交于点N,N点即为力
PPT文档演模板
汽车设计课件8制动系设计
•五、应急制动和驻车制动所需的制动力矩
•1.应急制动 •应急制动时,后轮一般都将抱死滑移 •后桥制动力 •后桥制动力距 •2.驻车制动 •上坡停驻时后桥附着力
•下坡停驻时后桥附着力
PPT文档演模板
汽车设计课件8制动系设计
•汽车可能停驻的极限上坡路倾角 •——根据附着力与制动力相等的条件求取
•制动蹄上 的摩擦力 有减小作 用在鼓上 的压力的 趋势,这 类蹄为 “松蹄”。
•制动鼓逆时针旋转 •时的制动力矩曲线
汽车设计课件8制动系设计
•2)解析法 •法向力 •制动力矩
PPT文档演模板
汽车设计课件8制动系设计
•对于紧蹄 •对于松蹄
•液力驱动 •自锁条件:当 •领蹄表面的最大压力
•时不会自锁。
PPT文档演模板
汽车设计课件8制动系设计
•2. 蹄片上的制动力矩的计算
•1).图解法
•图a):将压力分布线AB弧分成若干小单元, 并假设每一单元压力均匀分布且等于该单元 中点上约压力。
•图b):求作用在蹄片小单元上的的径向力Pi =SiFi (中点分布压力乘面积)。 •图c):力多边形求径向力的合力P。
PPT文档演模板
汽车设计课件8制动系设计
§8-2制动器的结构方案分析
汽车制动系统的设计及仿真

汽车制动系统的设计及仿真任务书1.设计的主要任务及目标汽车制动器是制动系中最重要的一个部件,是制动系统中用以产生阻碍汽车运动或运动趋势的力的部件。
凡是利用固定元件与旋转元件工作表面的摩擦而产生制动力矩的制动器都成为摩擦制动器。
摩擦制动器可分为鼓式和盘式两大类。
前者的摩擦副中的旋转元件为制动鼓,其工作表面为圆柱面;后者的旋转元件则为圆盘状的制动盘,以端面为工作表面。
2.设计的基本要求和内容(1)了解汽车制动系统的工作过程。
(2)熟悉汽车制动系统的设计过程和设计参数。
(3)结合汽车制动性能要求设计汽车制动器。
(4)结合三维建模软件,并实现制动器的运动仿真。
3.主要参考文献[1] 王望予.汽车设计[M].北京:机械工业出版社,2004[2] 余志生.汽车理论[M].北京:机械工业出版社,2003[3] 陈家瑞.汽车构造[M].北京:机械工业出版社,2003[4] 林秉华.最新汽车设计实用手册[M],黑龙江:黑龙江出版社,2005[5] 张尉林.汽车制动系统的分析与设计[M].北京:机械工业出社,20024.进度安排注:一式4份,系部、指导教师各1份、学生2份:[毕业设计]及答辩评分表各一份汽车制动系统的设计及仿真摘要:汽车的制动系是汽车行车安全的保证,许多制动法规对制动系提出了许多详细而具体的要求,这是我们设计的出发点。
从制动器的功用及设计的要求出发,依据给定的设计参数,进行了方案论证。
对各种形式的制动器的优缺点进行了比较后,选择了浮动钳盘的形式。
这样,制动系有较高的制动效能和较高的效能因素稳定性。
随后,对盘式制动器的具体结构的设计过程进行了详尽的阐述。
选择了简单液压驱动机构和双管路系统,选用了间隙自动调节装置。
在设计计算部分,选择了几个结构参数,计算了制动系的主要参数,盘式制动器相关零件的设计计算。
关键词: 制动器,同步附着系数,制动盘,制动钳Automobile brake system design and simulationAbstracts:The braking system in a vehicle guaranteed the safety of driving .Many rules and regulations have been made for the braking system in detail, which is the starting of our design.Firstly, I demonstrate the project on the base of the function of the brake, And analysis their strong point and shortcomings .I choose the form of front-disked. In this way, the braking system have higher braking efficiency and high stability of the performance factors. Subsequently, the specific structure of the disc brake design was elaborated in detail.I designed the hydraulic drive system and two-pipe system and selected clearance automatic adjusting device.In the calculate part .I chosen several structural parameters, calculated the main parameters of the braking system drive mechanism.Key words:disc brakes,synchronous attachment coefficient,brake disc,brake caliper目录1 绪论 (1)1.1 课题研究的目的及意义 (1)1.2制动系统研究现状 (1)1.3课题设计思路 (3)2制动系统概述 (4)2.1制动系的类型 (4)2.2汽车制动系统组成 (4)2.3 制动器的组成 (5)2.4 制动器的要求 (5)2.5 制动器的种类 (7)3 汽车参数计算 (14)3.1汽车的基本参数 (14)3.2 制动系的主要参数及其选择 (15)3.3 盘式制动器的结构参数与摩擦系数的确定 (16)3.4 制动衬块的设计计算 (18)3.5 摩擦衬块磨损特性的计算 (19)4 制动器主要零件的结构设计 (21)4.2 制动钳 (21)4.4 摩擦材料 (21)4.5 盘式制动器间隙的调整方法及相应机构 (22)4.6 制动驱动机构的结构型式选择与设计计算 (22)结论 (25)参考文献 (26)致谢 (27)附录 (28)1 绪论1.1 课题研究的目的及意义汽车的设计与生产涉及到许多领域,其独有的安全性、经济性、舒适性等众多指标,也对设计提出了更高的要求。
课程设计制动系设计

课程设计制动系设计一、教学目标本课程旨在通过制动系设计的学习,让学生掌握制动系统的组成、工作原理及其设计方法。
具体目标如下:1.了解制动系统的功能和重要性;2.掌握制动系统的组成部件及其作用;3.理解制动系统的工作原理;4.学习制动系统的设计方法和流程。
5.能够分析制动系统的性能指标;6.能够运用制动系统设计方法进行初步设计;7.能够评估制动系统的安全性和可靠性。
情感态度价值观目标:1.培养学生对汽车工程领域的兴趣和热情;2.培养学生具备安全意识和责任感,注重行车安全;3.培养学生具备创新精神和团队合作意识。
二、教学内容本课程的教学内容主要包括以下几个部分:1.制动系统的功能和重要性;2.制动系统的组成部件及其作用,如制动盘、制动鼓、制动片、制动鞋、制动油管、制动泵等;3.制动系统的工作原理,如液压制动系统、气压制动系统、电子制动系统等;4.制动系统的设计方法,包括制动盘、制动鼓、制动片等的设计计算和选型;5.制动系统的性能评价,如制动效能、制动距离、制动稳定性等;6.制动系统的维修保养和故障诊断。
三、教学方法为了提高教学效果,本课程将采用多种教学方法相结合的方式进行教学:1.讲授法:通过教师的讲解,使学生掌握制动系统的基本概念、原理和设计方法;2.讨论法:学生进行小组讨论,分享学习心得和经验,提高学生的思考和分析能力;3.案例分析法:分析实际案例,使学生更好地理解制动系统的工作原理和设计方法;4.实验法:安排实验室实践环节,让学生亲自动手进行制动系统的拆装和检测,提高学生的动手能力。
四、教学资源为了支持本课程的教学,我们将准备以下教学资源:1.教材:选用权威、实用的制动系统设计教材,为学生提供系统的学习资料;2.参考书:提供相关领域的参考书籍,丰富学生的知识体系;3.多媒体资料:制作课件、视频等多媒体资料,提高学生的学习兴趣和效果;4.实验设备:准备制动系统的实验设备,为学生提供实践操作的机会。
轻型载货汽车设计(制动系设计)

轻型载货汽车设计(制动系设计)摘要制动系至少有两套制动装置即行车制动装置和驻车制动装置。
行车制动装置是用作强制行驶中的汽车减速或停车,并使汽车在下坡时保持适当的稳定车速。
驻车制动装置是用作是汽车停在原地或坡道上。
本设计对鼓式制动器的结构形式进行综合的分析,对六种形式的优缺点作了比较,根据对各种制动器方案对比分析,本设计采用了领从蹄式制动器。
其主要优点是:制动器的效能及稳定性均处于中等水平,但由于其在汽车前进与倒退时的制动性能不变,且结构简单,造价较低,也便于附装驻车驱动机构;易于调整蹄片与制动鼓之间的间隙。
本次设计中,行车制动系采用人力液压式制动;驻车制动的驱动机构为手动驻车;串联双腔制动主缸,双回路结构。
前后制动器都采用领从蹄式鼓式制动器。
设计中根据总体参数和制动器的结构与参数,通过理论推导和计算,对该车制动时的制动力和制动力矩等做了细致的分析。
关键词:制动系统,制动器,行车制动系,应急制动LIGHT TRUCK DESIGN(BRAKE SYSTEM)ABSTRACTBreak system consists of service break arrangement and parking break arangment. Service break system used to force the vehicle to show down and keep a steady speed when downgrading. The parking break system intended to hold the vehicle immovable when parked on an incline.This design carries on the synthesis analysis to the drum type of the brake structural style. It compares the advantages and disadvantages of six kinds of forms, and according to this contrast analysis of the kinds of the brake plan, the horseshoe type’s brake is adopted. Its main merits are that although the brake efficiency and the stability are in the medium level, because the automobile braking performance is invariable when going ahead and going backwards, the construction cost is lower, and it attaches installs in the vehicle’s driving mechanism and adjusts the gap between the brake shoe patch and the brake drum easily. The design uses manual hydraulic break and series connected double cavity general pump. Both the front and rear break is double leading-rear break. According to the vehicle’s parameters and the break’s parameter, after theory analytic and calculating, we analyzed the breaking force and direction stability when breaking specifically.KEY WORD:braking system,brake ,service break system, emergency brake目录第一章概述 (1)第二章制动系的结构形式及其选择 (3)§2.1制动器结构形式简介 (3)§2.2制动器的结构形式选择 (4)§2.3制动驱动机构的结构型式选择 (8)§2.4 液压式制动驱动机构双回路系统方案选择 (10)第三章制动系的主要参数及其选择 (11)§3.1与设计相关的整车参数的确定 (11)§3.2制动力及其分配系数 (11)§3.3同步附着系数 (14)§3.4最大制动力矩 (16)§3.5制动器的结构参数与摩擦系数 (17)第四章制动器的设计计算 (20)§4.1制动器因数的计算 (20)§4.2张开力计算 (22)§4.3摩擦衬片的磨损特性计算 (22)§4.4驻车制动计算 (24)§4.5 汽车制动性能计算 (25)第五章液压制动驱动机构的设计计算 (27)§5.1制动轮缸直径与工作容积的确定 (27)§5.2制动主缸直径与工作容积确定 (28)§5.3制动踏板力F与踏板行程的设计计算 (28)§5.4真空助力器 (29)§5.5制动力分配的调节装置 (31)第六章制动器主要零部件的结构设计与强度计算 (30)§6.1制动器主要零部件的结构设计 (30)§6.2制动器主要零件强度计算 (31)结论 (33)参考文献 (34)致谢 (36)第一章概述制动系是用于使行驶中的汽车以适当的减速度降速行驶直至停车,使下坡行驶的汽车的车速保持稳定以及使已停止的汽车在原地或斜坡上驻留不动的机构。
制动系设计毕业设计
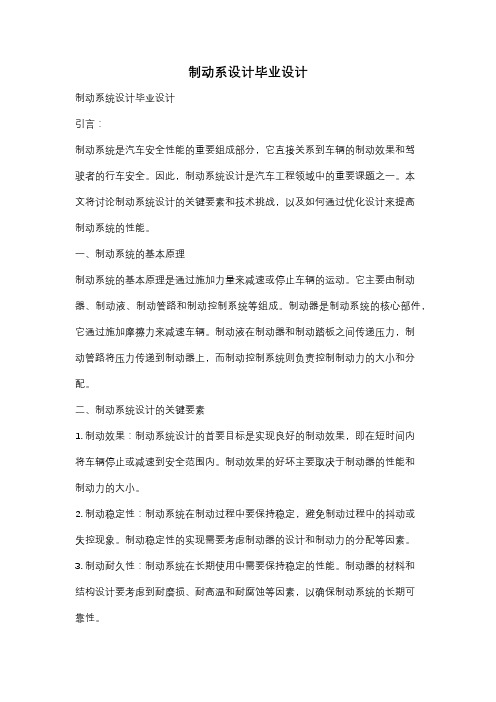
制动系设计毕业设计制动系统设计毕业设计引言:制动系统是汽车安全性能的重要组成部分,它直接关系到车辆的制动效果和驾驶者的行车安全。
因此,制动系统设计是汽车工程领域中的重要课题之一。
本文将讨论制动系统设计的关键要素和技术挑战,以及如何通过优化设计来提高制动系统的性能。
一、制动系统的基本原理制动系统的基本原理是通过施加力量来减速或停止车辆的运动。
它主要由制动器、制动液、制动管路和制动控制系统等组成。
制动器是制动系统的核心部件,它通过施加摩擦力来减速车辆。
制动液在制动器和制动踏板之间传递压力,制动管路将压力传递到制动器上,而制动控制系统则负责控制制动力的大小和分配。
二、制动系统设计的关键要素1. 制动效果:制动系统设计的首要目标是实现良好的制动效果,即在短时间内将车辆停止或减速到安全范围内。
制动效果的好坏主要取决于制动器的性能和制动力的大小。
2. 制动稳定性:制动系统在制动过程中要保持稳定,避免制动过程中的抖动或失控现象。
制动稳定性的实现需要考虑制动器的设计和制动力的分配等因素。
3. 制动耐久性:制动系统在长期使用中需要保持稳定的性能。
制动器的材料和结构设计要考虑到耐磨损、耐高温和耐腐蚀等因素,以确保制动系统的长期可靠性。
4. 制动舒适性:制动过程中产生的噪音、震动和刹车跳动等问题会影响驾驶者的舒适性。
制动系统设计需要考虑减少这些不良影响,提供平稳、静音的制动体验。
三、制动系统设计的技术挑战1. 制动力的分配:在制动系统设计中,如何合理分配制动力是一个关键问题。
前轮制动力过大会导致车辆打滑,后轮制动力过大则会导致车辆失控。
因此,制动系统设计师需要根据车辆的动力学特性和重心位置等因素来优化制动力的分配。
2. 制动器的材料选择:制动器的摩擦材料对制动效果和制动稳定性起着重要作用。
目前常用的制动器材料有有机材料、金属材料和陶瓷材料等。
设计师需要根据车辆的使用条件和性能要求来选择合适的制动器材料。
3. 制动系统的热管理:制动过程中会产生大量的热量,如果不能及时散热,会导致制动器的性能下降甚至失效。
- 1、下载文档前请自行甄别文档内容的完整性,平台不提供额外的编辑、内容补充、找答案等附加服务。
- 2、"仅部分预览"的文档,不可在线预览部分如存在完整性等问题,可反馈申请退款(可完整预览的文档不适用该条件!)。
- 3、如文档侵犯您的权益,请联系客服反馈,我们会尽快为您处理(人工客服工作时间:9:00-18:30)。
制动器效能的稳定性: 效能因数K对摩擦因数f 的敏感性(dK/df).
1.领从蹄式
每块蹄片都有自己的固定支点,而且两固定支点位于两蹄的同一端 . 张开装置: 平衡式 楔块式 凸轮或楔块式 平衡凸块式
非平衡式 活塞轮缸(液压驱动) 制动器的效能和效能稳定性,在各式制动器中居中游 ;两蹄衬片磨损不均 匀,寿命不同.
第八章 制动系设计
第八章
§8-1概述 概述
制动系设计
§8-2制动器的结构方案分析 制动器的结构方案分析 §8-3制动器主要参数的确定 制动器主要参数的确定 §8-4制动器的设计与计算 制动器的设计与计算 §8-5制动驱动机构 制动驱动机构 §8-6制动力调节机构 制动力调节机构 §8-7 制动器的主要结构元件
§8-2制动器的结构方案分析 制动器的结构方案分析
摩擦式 液力式 -----缓速器 电磁式 鼓式 磨擦副结构 盘式 带式-----中央制动器
一,鼓式制动器
分领从蹄式,双领蹄式,双向双领蹄式,双从蹄式,单向增力式,双 向增力式等几种
主要区别: ①蹄片固定支点的数量和位置不同; ②张开装置的形式与数量不同; ③制动时两块蹄片之间有无相互作用. 制动器效能:制动器在单位输入压力或力的作用 下所输出的力或力矩. 制动器效能因数:在制动鼓或制动盘的作用半径R 上所得到摩擦力(M/R)与输入力F0之比,
四,制动鼓(盘)与衬片(块)之间的间隙自动调整装置 产生制动作用的时间增长; 间隙过大 同步制动性能变坏; 增加了压缩空气或制动液的消耗量,并使制动踏板或手柄行程增大 盘式制动器 利用制动钳中的橡胶密封圈的极限弹性变形量,来保持制动时为消除设定 隙所需的活塞设定行程△.
鼓制动器
阶跃式自调装置(适用于双向增力式制动器)
二,分路系统 全车的所有行车制动器的液压或气压管路分为两个或多的互相独立的回路,其 中一个回路失效后,仍可利用其它完好的回路起制动作用.
三,液压制动驱动机构的设计计算 1.制动轮缸直径d的确定
2.制动主缸直径d0的确定 第i个轮缸的工作容积 所有轮缸的总工作容积 初步设计时 主缸活塞行程S0和活塞直径d0 一般 3.制动踏板力Fp 要求:最大踏板力一般为500N(轿车)或700N(货车). 4.制动踏板工作行程 踏板行程(计入衬片或衬块的允许磨损量)对轿车最大应大于 100~150mm,对货车不大于180mm.
二,盘式制动器主要参数的确定 1.制动盘直径D 通常选择为轮辋直径70%~79% 2.制动盘厚度h 实心制动盘厚度可取为10~20mm; 通风式制动盘厚度取为20~50mm; 采用较多的是20~30mm 3.摩擦衬块外半径R2与内半径R1 外半径R2与内半径R1(图8-11)的比值不大于1.5 4.制动衬块面积A 1.6~3.5kg/cm2
§8-1概述 概述
功用: 使汽车以适当的减速度降速行驶直至停车; 在下坡行驶时使汽车保持适当的稳定车速; 使汽车可靠地停在原地或坡道上. 行车制动装置 驻车制动装置 应急制动装置 辅助制动装置
汽车制动系统图组
制动系应满足如下要求: 制动系应满足如下要求:
1)足够的制动能力 . 2)工作可靠 . 3)不应当丧失操纵性和方向稳定性 . 4)防止水和污泥进入制动器工作表面. 5)热稳定性良好 . 6)操纵轻便,并具有良好的随动性 . 7)噪声尽可能小. 8)作用滞后性应尽可能短 9)摩擦衬片(块)应有足够的使用寿命 10)调整间隙工作容易 11)报警装置
§8-7 制动器的主要结构元件
一,制动鼓 制动鼓应当有足够的强度,刚度 和热容量,与摩擦衬片材料相配合, 又应当有较高的摩擦因数. 铸造式: 多选用灰铸造铁, 具有机械加工容易,耐磨热 容量大等优点 轿车壁厚取为7~12mm,货车 取为13~18mm. 组合式:质量小,工作面耐磨,并有较高的摩擦因数 二,制动蹄 轿车和轻型货车的制动蹄广泛采用T形钢辗压 或用钢板焊接制成;重型货车的制动蹄则多用铸 铁或铸钢铸成,断面有工字形,山字形和Ⅱ字形 几种 .制动蹄腹板和翼缘的厚度,轿车为 3~5mm,货车约为5~8mm. 制动蹄和摩擦片可以铆接,也可以粘接.
对于紧蹄 对于松蹄
液力驱动
自锁条件 领蹄表面的最大压力
不会自锁
二,盘式制动器的设计计算
单侧制动块加于制动盘的制动力矩
单侧衬块加于制动盘的总摩擦力
有效半径
m值一般不应小于0.65. 平面度允差为0.012mm,表面粗糙度为Ra0.7~1.3m,两摩擦表面 的平行度不应大于0.05mm,制动盘的端面圆跳动不应大于0.03mm.
§8-3制动器主要参数的确定 制动器主要参数的确定
一,鼓式制动器主要参数的确定 1.制动鼓内径D 轿车:D/Dr=0.64~0.74 货车:D/Dr=0.70~0.83 ZBT24 005-89《制动鼓工作直径及制动蹄片宽度尺寸 系列》 2.摩擦衬片宽度b和包角β 包角一般不宜大于120°. 制动衬片宽度尺寸系列见ZB T24 005-89. 3.摩擦衬片起始角β0 4.制动器中心到张开力F0作用线的距离e 使距离e(图8-7)尽可能大, 初步设计时可暂定e=0.8R左右. 5.制动蹄支承点位置坐标a和c 使a尽可能大而c尽可能小.初步设计时,也可暂定a=0.8R左右.
二,盘式制动器
固定钳式 钳盘式(点盘式制动器 ) 浮动钳式 摆动钳式 全盘式(离合器式制动器 ) 滑动钳式
盘式制动器有如下优点:
热稳定性好;水稳定性好;制动力矩与汽车运动方向无关;易于构成双 回路制动系;尺寸小,质量小,散热良好;衬块磨损均匀;更换衬块容易; 缩短了制动协调时间;易于实现间隙自动调整.
三,衬片磨损特性的计算 摩擦衬片(衬块)的磨损受温度,摩擦力,滑磨速度,制动鼓(制动盘)的 材质及加工情况,以及衬片(衬块)本身材质等许多因素的影响,试验表明,影 响磨损的最重要的因素还是摩擦表面的温度和摩擦力. 双轴汽车的单个前轮及后轮制动器的比能量耗散率
鼓式制动器的比能量耗散率以不大于1.8W/mm2为宜,计算时取减速度 j=0.6g.制动初速度υ1:轿车用100km/h(27.8m/s);总质量3.5t以下的货 车用80km/h(22.2m/s);总质量3.5t以上的货车用65km/h(18m/s). 轿车的盘式制动器在同上的υ1和j的条件下,比能量耗散率应不大于 6.0W/mm2.
next
next
back
�
2.双领蹄式
两块蹄片各有自己的固定支点,而且两固定支点位于两蹄的不同端. 每块蹄片有各自独立的张开装置,且位于与固定支点相对应的一方. 制动器的制动效能相当高; 倒车制动时,制动效能明显下降; 两蹄片 磨损均匀,寿命相同; 结构略显复杂.
3.双向双领蹄式
两蹄片浮动,始终为领蹄. 制动效能相当高,而且不变,磨损均匀,寿命相同.
一个自由度的紧蹄摩擦衬片的径向变形规律
′ δ 1 = B1C1 = B1 B1 sin γ 1 = A1 B1 sin γ 1dγ
表面的径向变形和压力为: δ 1 = R sin adγ p1 = p max sin a 新蹄片压力沿摩擦衬片长度的分布符合正弦曲线规律
2.计算蹄片上的制动力矩 法向力 制动力矩
五,应急制动和驻车制动所需的制动力矩 1.应急制动 应急制动时,后轮一般都将抱死滑移 后桥制动力 前桥制动力 2.驻车制动 上坡停驻时后桥附着力
下坡停驻时后桥附着力
汽车可能停驻的极限上坡路倾角
汽车可能停驻的极限下坡路倾角
§8-5制动驱动机构 制Байду номын сангаас驱动机构
一,制动驱动机构的形式 机械式: 机械效率低,传动比小,润滑点多 结构简单,成本低,工作可靠(故障少), 简单制动 应用于中,小型汽车的驻车制动装置中 液压式: 作用滞后时间较短(0.1~0.3s);工作压 力高(可10~20MPa),结构简单,质量 小;机械效率较高 气压制动: 操纵轻便,工作可靠,不易出故障,维 修保养方便 结构复杂,笨重,成本高;作用滞后时 制动力源 动力制动 间较长(0.3~0.9s);簧下质量大;噪 声大. 开式(常流式) 全液压动力制动 闭式(常压式) 真空伺服制动 0.05~0.07MPa 伺服制动 空气伺服制动 0.6~0.7MPa 液压伺服制动
三,摩擦衬片(衬块) 1)具有一定的稳定的摩擦因数. 2)具有良好的耐磨性. 3)要有尽可能小的压缩率和膨胀率. 4)制动时不易产生噪声,对环境无污染. 5)应采用对人体无害的摩擦材料. 6)有较高的耐挤压强度和冲击强度,以及足够的抗剪切能力. 7)摩擦衬块的热传导率应控制在一定范围. 石棉摩阻材料: 由增强材料(石棉及其它纤维),粘结剂,摩擦性能 调节剂组成 制造容易,成本低,不易刮伤对偶; 耐热性能差,随着温度升高而摩擦因数降低, 磨耗增高和对环境污染 半金属摩阻材料: 由金属纤维,粘结剂和摩擦性能调节剂组成 较高的耐热性和耐磨性,没有石棉粉尘公害 金属摩阻材料: 粉末冶金无机质 耐热性好,摩擦性能稳定 制造工艺复杂,成本高,容易产生噪声和刮伤对偶
§8-4制动器的设计与计算 制动器的设计与计算
一,鼓式制动器的设计计算 1.压力沿衬片长度方向的分布规律 两个自由度的紧蹄摩擦衬片的径向变形规律: ′ δ 1 = B1C1 ≈ B1 B1 cosψ 1 对于紧蹄的径向变形δ1和压力p1为:
δ1 ≈ δ1max sin( a1 + 1 ) p1 ≈ p1max sin( a1 + 1 )
比摩擦力f0 每单位衬片(衬块)摩擦面积的制动器摩擦力
在j=0.6g时,鼓式制动器的比摩擦力f0以不大于0.48N/mm2为宜.与之相 应的衬片与制动鼓之间的平均单位压力pm=f0/f=1.37~1.60N/mm2(设摩擦因 数f=0.3~0.35).
四,前,后轮制动器制动力矩的确定 首先选定同步附着系数φ0, 计算前,后轮制动力矩的比值 根据汽车满载在柏油,混凝土路面上紧急制动到前轮抱死拖滑,计算出前 轮制动器的量大制动力矩M1max; 再根据前面已确定的前,后轮制动力矩的比值计算出后轮制动器的最大制 动力矩M2max.