基于CAE的纸芯空气滤清器注射模反变形设计
CAE知识点总结

CAE知识点总结1.CAE作用:在模具加工前,在计算机上对整个注射成型过程进行模拟分析,准确预测熔体的填充、保压、冷却情况,以及制品中的应力分布、分子和纤维取向分布、制品收缩和翘曲变形等情况,以便设计者能尽早发现问题,及时修改制件和模具设计,而不是等到试模以后再返修模具。
(或者是它能够在产品设计阶段及开模之初,利用计算机对整个成型过程进行分析拟准确预测模具可能出现的问题,并能够为设计者提供可靠地解决方案。
)2.CAE的基本流程:前处理——分析计算——后处理注塑成型CAE的作用:优化塑料制品设计、优化塑料模具设计、优化注射工艺参数。
热注塑成型过程:把塑料原料加入注射机料筒中,经过螺杆的旋转使塑料向前输送,同时机筒加热使其溶化成熔体,储存在注射机筒前端,当螺杆作为加压工具快速向前推进时,塑料熔体已告压通过喷嘴注入磨具型腔中经过冷却、凝固后从磨具中脱出,成为塑料制品。
热注塑成型过称分为以下阶段:(1)塑化阶段(2)注射充模阶段(3)冷却凝固阶段(4)脱模阶段3.注塑成型工艺参数:(1)温度:机筒温度、喷嘴温度、模具温度;(2)压力:塑化压力、注射压力、保压压力;(3)时间(成型周期):注射充模时间、保压时间、冷却时间、预塑时间以及其他辅助时间(开模、脱模、嵌件安放、闭模)。
4.一般CAE软件的结构,分为几个模块?前处理模块---给实体建模与参数化建模,构件的布尔运算,单元自动剖分,节点自动编号与节点参数自动生成,载荷与材料参数直接输入有公式参数化导入,节点载荷自动生成,有限元模型信息自动生成等。
有限元分析模块---有限单元库,材料库及相关算法,约束处理算法,有限元系统组装模块,静力、动力、振动、线性与非线性解法库。
大型通用题的物理、力学和数学特征,分解成若干个子问题,由不同的有限元分析子系统完成。
一般有如下子系统:线性静力分析子系统、动力分析子系统、振动模态分析子系统、热分析子系统等。
后处理模块---有限元分析结果的数据平滑,各种物理量的加工与显示,针对工程或产品设计要求的数据检验与工程规范校核,设计优化与模型修改等。
基于CAD/CAE技术的塑料盖注射模设计

r  ̄ t t p : / / ww w. s z m o l O s . E a n 模具制造立体传媒电子商务平台 r
雩 嘉
基于 C AD / C A E技术 的塑 料 盖 注射 模 设 计
赵 建平 , 刘艳 艳 , 肖 猛
南京理 工大学 紫金 学院( 江 苏南京
a n d s h o r t e n e d t h e p r o d u c t i o n c y c l e .
Ke y wo r d s : CAD/ CAE; s i mu l a t i o n a n a l y s i s ; mo l d d e s i g n ; 3 D p a r t i n g ; EMX
难 以保证 。而运用 C A D / C A E技术 , 不仅 可 以对塑件 程 度 和生 产 率 。
生产工艺条件进行 分析调整 , 模拟注射生产一系列过 程, 对 于产生 问题能及时修改 , 而且还可 以缩 短研 发
周期 , 从 而优化塑件及模具结构 , 为塑件 的最终加 工 成型奠定 了坚实 的基础 。
p l a s t i c c o v e r w a s d e s i g n e d . B a s e d o n C A D / C A E t e c h n o l o g y , t h e d e s i g n m e t h o d o f i n j e c t i o n mo l d
w e r e e x p o r t e d i n t o t h e e x p e t r m o l d b a s e e x t e n s i o n ( E MX ) ,a n d t h e 3 - p l a t e i n j e c t i o n m o l d o f
基于CAE技术的汽车覆盖件模具设计

图1覆盖件成形模拟及模具设计流程
图2 冲J 向 土方
2 覆盖件 拉延 模具 设计 ( 图1) 如
21 设 计 流 程 . 22 拉 延 成 形 模 面 设 计 _
拉延模型面设计 ,是一个在覆盖件产 品三维模型基础上进行边界条 件设计 和数值仿真计算的过程 ,其是根据冲压l 下艺和模具设计知识 ,完 成优选 冲压方向、压料面形状 的确定 、丁艺补充面的设计及拉延筋 设计 等, 依其掌握的经验和知识 ,以获得最佳 的材料流动 ,达到拉延 出合格 的拉延件的 目 的。 1 )冲压方向的确定。冲压方 向的确定是拉延工序设计 中的重要参 数 ,其在保证没有 冲压负角的情形下 ,遵循平均法向原则 、最小拉延深 度原则 、无冲压负角原则等来确定冲压方 向。它表示拉深件在模具 中的 空间位置 ,它不但决定 能否拉延出合格 的覆盖件 ,而且直接影 响到成形 零件的质量和模具结构 的复杂性。该零件在拉延模 中确定的冲压方向 ,
以供参考。
,
关 键词 C E 术 ;汽车覆 盖件 ;拉延模型 面 ;模具设计 A技
中图分 类号 r 文献 标识 码 A 文 童编 号 17 —6 I( 1)9一 180 c 6397 一 00 ]O — 2 2 0 1
汽 车覆 盖件和一般冲压件相 比 ,具有结构尺寸 大 、材 料薄 、精度 高 、形状复杂 、表 面质量高 、配合协调性要求 高 且多为空间曲丽等特 点 ,大多采用薄板冲压成形。从理 论 f讲,汽车覆盖件成形过程涉及 了 _ _ ‘ 几何非线性 、材料非线性 、边界非线性和复杂 的接触摩擦 问题等。而 CE A 技术主要是指对覆盖件进行仿真模拟 ,利用计算机来完成模具的冲 压使用过程 ,并对覆盖件的成形性进行分析 ,通过分析可以解决覆盖件 在生产过程中出现的 回弹、起皱 、托裂等一系列难点 ,并能提供准确的 展开料及各种工艺参数 ,如托延力 、压边力等。随着有限元技术和计算 机技术 的高速发展,基于数值模拟的技术 ( A C E)的戊用大大提高了覆 盖件模具设计制造的可靠性的成功率 ,使冲压模具设 汁和加 定量化, 加快 了冲压工艺方案的确定 ,提高 r冲乐成形质萤 ,使模具开发成本 和
浅谈CAD/CAE/CAM技术在汽车注塑模设计中的应用

或UG 软 件 中的 制造 ( 即uG C A M) 模 块 来实 现 Ma s t e r c a m提 供 刀具选 择 、 加 工 路径规 划、 切 削用量 设定等 功能 , 可 以自动 生成 加工程序 并传输 至数 控机床 , 最 终完 成零 件 的加工 。 U G软件高 度集 成 了C A D 和C A E 系统 , 可以实 现无 图纸
3、 发 展 趋 势
中的 成型过 程 。 对 体 积收缩 , 熔 接痕 , 冷 却效果 以及 变形等 情况进 行预 估 , 在 模 具 设计 中可 以起到 指导 作用 并减 少盲 目性 。 当塑 料模 具设 计好 后 , 有 些零 件
要 对其 进行 力学 的校 对 , 运用 A N S Y S 等软 件可 以对其 进行分 析 、 优化 , 进而判 断其是 否满 足要 求 。 3 、 C A M 技术 与塑 料模 制造
一
.
引 言
计 算机辅 助工程 即c A E 借助有 限元法对 塑料的流动 、 成 型过程进行模 拟和 分析 塑料模 具 的应 力应 变情 况 。 塑料模  ̄ - C A E 主要 包括两 部分 : 一 种是模 流分 析, 比较有代 表性 的软 件 有Mo l c l l f o w ̄ ; 另 一种 是零 件 的受力 分析 , 常 用 的软
型设 计、 模 具设 计 、 加工编 程及 工艺设 计都 以3 D 数据 为基 础 , 实 现数据 共享 , 具
有准确 、 快 速、 简便的优 势 , 不 仅省去 了代码 编辑 、 调试等繁 琐的工 作 , 还 能消 除
加工 工艺编 程设 计的错 误 , 减少 加工 后的修 补和 返工 , 大大提 高模 具制 造效率 和质量 , 降低 成本 。 目前 , 注 射模 的C AM主 要通 过专业 的 C AM.  ̄ 件Ma s t e r c a m
基于CAE技术的塑料模具设计方法

0引言一般塑料制品都是采用模塑成型的基础制造工艺,因此塑料模具是塑料制造行业的主要生产工艺装备,并且在我国国民经济中占有重要作用。
近几年,随着我国汽车、电子、航空等工业领域的迅速发展,对塑料制品的需求量更是急剧增加,因此对塑料制造业效率要求也逐渐提升。
由于塑料模具具有种类多、更新速度快、小批量加工等基本特征,我国的传统塑料模具设计方式已经难以适应新时期工业生产的需求,所以将电子制造技术应用于塑料模具设计就成为塑料制造行业发展的必然趋势。
CAE 技术为塑料制造行业的人员提供了快捷高效地计算机辅助软件,可以帮助塑料模具设计人员从塑料产品开发、模具设计到产品成型进行一系列的设计与完善,从而大大缩短了设计制造周期,提高了效率,降低了企业成本。
1塑料模具CAE 概述CAE (Computer Aided Execution )指的是一种计算机辅助工程技术,是为了深入发展计算机辅助设计工程技术与计算机辅助制造工程技术而出现的一种新的应用软件。
一般可以认为它是一个包括了数值运算技术、信息数据库、多媒体构图学、应用工程分析与仿真模具等元素在内的具有综合性功能的软件系统,而它的核心技术就是对技术工程数据的模具化与信息数据的实现方法。
对于塑料模具设计制造工艺的计算机辅助工程来说,主要是依靠高分子流变学、函数计算与构图形式等基本理论,对制造工艺直接进行数据模拟,这样可以让塑料模具在制造之前能够形象逼真地模拟出塑料产品成型的一系列过程,防止制造过程中塑料模具对最终产品产生影响,及时发现将要出现的问题,为设计与制造过程中条件是否允许提供了较为科学的依据。
基于CAE 计算机辅助技术的塑料模具设计过程(图1)与我国传统的塑料模具设计过程有较大差别,可以说这种新型的生产过程属于典型的并行路线。
在塑料模具设计与制造前,设计人员通过利用计算机CAE 分析软件,在计算机上对将要出来的成型产品进行模拟仿真分析,这样可以科学预测到材料的填充、压缩、冷清及纤维取向分布等情况,进而让工作人员能够迅速了解到需要改进的工艺参数,优化塑料模具工艺过程,将多数出现的问题改正,避免了出来成品之后再修改模具,能够用最短的时间来优化塑料模具的设计过程,从而提高了塑料产品的质量和制造效率。
Moldflow的变形分析及其应用
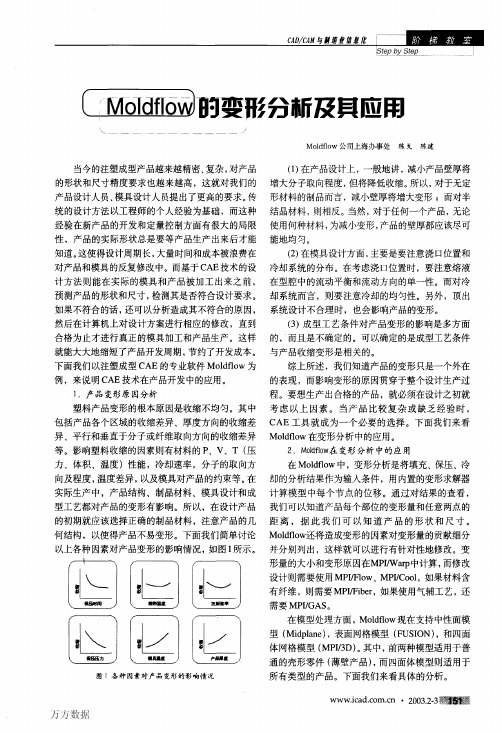
丝里丝型丝皇笪堕堂蕉星些_勉—l篮盈_譬冒_重巨煦鲤鱼触.当今的注塑成型产品越来越精密、复杂,对产品的形状和尺寸精度要求也越来越高,这就对我们的产品设计人员、模具设计人员提出了更高的要求。
传统的设计方法以工程师的个人经验为基础,而这种经验在新产品的开发和定量控制方面有很大的局限性,产品的实际形状总是要等产品生产出来后才能知道。
这使得设计周期长,大量时间和成本被浪费在对产品和模具的反复修改中。
而基于CAE技术的设计方法则能在实际的模具和产品被加工出来之前,预测产品的形状和尺寸,检测其是否符合设计要求。
如果不符合的话,还可以分析造成其不符合的原因,然后在计算机上对设计方案进行相应的修改,直到合格为止才进行真正的模具加工和产品生产。
这样就能大大地缩短了产品开发周期,节约了开发成本。
下面我们以注塑成型CAE的专业软件Moldflow为例,来说明CAE技术在产品开发中的应用。
1.产品变形原因分析塑料产品变形的根本原因是收缩不均匀。
其中包括产品各个区域的收缩差异、厚度方向的收缩差异、平行和垂直于分子或纤维取向方向的收缩差异等。
影响塑料收缩的因素则有材料的P、V、T(压力、体积、温度)性能,冷却速率,分子的取向方向及程度,温度差异,以及模具对产品的约束等。
在实际生产中,产品结构、制品材料、模具设计和成型工艺都对产品的变形有影响。
所以,在设计产品的初期就应该选择正确的制品材料,注意产品的几何结构,以使得产品不易变形。
下面我们简单讨论以上各种因素对产品变形的影响情况,如图1所示。
图1各种因素对产品变形的影响情况分祈及其应用Moldflow公司上海办事处陈戈陈建(1)在产品设计上,一般地讲,减小产品壁厚将增大分子取向程度,但将降低收缩。
所以,对于无定形材料的制品而言,减小壁厚将增大变形;而对半结晶材料,则相反。
当然,对于任何一个产品,无论使用何种材料,为减小变形,产品的壁厚都应该尽可能地均匀。
(2)在模具设计方面,主要是要注意浇口位置和冷却系统的分布。
基于CFD技术的空气自动化净化器滤芯的优化设计

基于CFD 技术的空气自动化净化器滤芯的优化设计Optimization design of filter element of automaticair purifier based on CFD technology黄劲松,骆桂芳,宋瑞仙,唐 朋HUANG Jin-song, LUO Gui-fang, SONG Rui-xian, TANG Peng(湖北工业大学,武汉 430070)摘 要:静电吸附方式会使污染物滞留在滤网上,导致污染物或气体净化效率较低,为了提高净化效果,提出了基于CFD技术的空气自动化净化器滤芯的优化设计。
根据净化器滤芯结构示意图,在清洁、净化和电路三个方面进行优化设计。
在清洁模块中增加静电发生器实现灰尘及滤芯部分灰尘的快速吸附,设置顶盖防止飞尘外溢的作用。
添加超声雾化片,方便水流收集。
在紫外灯管串联一个计时器,防止清洁超时现象发生。
构建CFD模拟分析模型,利用Pro/E软件划分气流通道网格。
模拟速度场,确定流道附近流体流速,并设计净化流程。
由实验结果可知,该滤芯净化污染物或气体效率较高,能够保证室内装修污染物或气体的及时净化。
关键词:CFD技术;空气自动化净化器;滤芯;速度场中图分类号:TQ320.66 文献标识码:A 文章编号:1009-0134(2021)03-0160-04收稿日期:2019-09-08作者简介:黄劲松(1967 -),男,湖北武汉人,副教授,硕士,研究方向为工业设计。
0 引言伴随着自然环境污染的加剧,大气污染问题也越来越受到人们的关注,尤其在我国,部分城市由于季风的影响,冬季空气污染非常严重。
今天的社会,有别于现在的室外空气污染,80%的人都待在室内,室内空气污染来源很多,空气污染的程度远远超过室外空气污染。
甲醛是装修房屋的主要污染物,广泛应用于各类胶粘剂、人造板、油漆、涂料等行业。
人长期吸入含有这些污染物的气体,就会引起各种慢性呼吸道和神经系统疾病。
《基于Moldflow分析的模具预变形技术》

解决了虎皮纹成因,接踵而至的“塑料件注塑成型 后的变形”难题,再次令杨明华和他的团队不得不 再次回到“发现问题—分析问题—解决问题”的应 用模式。而这一次,成都航模由此难题开始着手建 立了自己的标准知识库。
而这背后,离不开Autodesk Simulation Moldflow的 出色表现。
无处遁形的变形
如 此 强 大 的 实 力 背后,缺 不 了“ 软 硬 ”结 合 的 双 管齐下。作为较早一批使用Autodesk Simulation Moldflow的用户之一,成都航模同欧特克公司之间 合作是一路相互成长的过程。“成都航模的CAE分析 室是伴随着Autodesk Simulation Moldflow应用后才 建立起来的。成都航模的CAE分析室担负着为公司 的产品设计和产品开发,提供完善的CAE分析和模 具验证优化等诸多责任。”成都航天模塑股份有限 公司CAE室主任杨明华介绍,正是基于在Moldflow 上的应用合作,奠定了成都航模与欧特克公司之间 的合作基础,并在后来的合作中共同成长。
Autodesk Simulation Moldflow:未来或 将更智能
注塑产品变形分析

模具设计
–顶出设计 • 如果顶出系统布置不平衡,将造成顶出力的不平衡 而使塑件变形。因此,在设计顶出系统时应力求与 脱模阻力相平衡。 • 顶出杆的截面积不能太小,以防塑件单位面积受力 过大(尤其在脱模温度太高时)而使塑件产生变形 。 • 顶杆的布置应尽量靠近脱模阻力大的部位。在不影 响塑件质量(包括使用要求、尺寸精度与外观等) 的前提下,应尽可能多设顶杆以减少塑件的总体变 形(换顶杆为顶块就是这个道理)。
四、CAE分析(Moldflow)在解决产品变形中的运用
1 利用Moldflow分析预测抓手理论变形量 2 利用Moldflow分析预测13KG抓手理论变形量及变形改善 3 Moldflow模流分析辅助解决空气净化器前盖变形问题
一 变形对洗衣机外观,装配的影响
• 注塑件变形是塑料制品常见的缺陷之一,严重影响产品 的外观和装配效果。
产品变形分析
魏 邦 科
技术工艺部 2011年05月
注塑产品常见问题
• 注塑件外观问题
浇口晕、雾斑 、银纹、喷流痕 、波纹 、 缩痕、浮纤、虎皮纹、熔接痕、气孔、拉 毛、顶伤、飞边、成形不足、烧糊等。
• 注塑产品变形问题 • 注塑产品尺寸精度
目
二、变形原因简介 三、变形的预防及解决方案
录
一、常见注塑件变形对洗衣机外观,装配的影响
注射压力,速度对变形影响
• 较高的压力和流速会产生高剪切速率,产生高的残余应力 ,容易翘曲。 • 而较小的注射压力可减少塑料的分子取向倾向,降低其内 应力. • 注射机的注射压力会极大地影响充填时分子的取向程度, 进而引起翘曲变形。 • 减少翘曲,注射压力在可行范围内调到最低,
基于CAE模拟分析的汽车注塑仪表板产品设计

基于CAE模拟分析的汽车注塑仪表板产品设计发表时间:2019-12-24T09:34:26.403Z 来源:《工程管理前沿》2019年第22期作者:尹恩洋[导读] 就目前的汽车仪表盘质量来看,熔接痕与翘曲变形是常见的缺陷摘要:就目前的汽车仪表盘质量来看,熔接痕与翘曲变形是常见的缺陷,在大型的塑料制件中,经常采用多浇口进浇,从而产生熔接痕。
目前,将热流道顺序阀技术应用在汽车仪表盘的制作中,则可以解决上述问题,同时采用CAE模拟软件,可以有效的进行设计与生产的指导。
基于此,本文分析CAE软件对汽车仪表盘注塑成型表面的质量控制。
关键词:汽车仪表盘;注塑成型;质量控制一、汽车仪表板设计重要性的背景当今世界,汽车已经成为走进家家户户的日常交通工具了。
汽车照比过去的几年,无论是价格还是购买方法都更能贴近普通百姓家庭。
汽车的购买量也逐年增大增多。
随着汽车的购买量提升,汽车厂家也逐渐增多,生产的汽车也越来越多元化。
如今,百姓生活水平提升,很多人不仅看汽车的代步功能,更看重汽车的质量和美观。
为了提高竞争力,汽车厂家开始研究更多的汽车技术更新,美观设计,以及提供售后服务等等。
很多汽车企业也看到了一点,提高汽车品牌竞争力,汽车设计方面很重要,而作为可以对汽车整体进行美化和装饰的汽车仪表板则需要更加重视。
汽车仪表板属于汽车设计中的重要部位,除了有美化装饰汽车的作用之外,他还具备很强的功能性,仪表板设计主要包括几个方面,如,仪表板的面板设计、仪表板的仪表面罩设计、仪表板的仪表布置设计和仪表板的操纵按钮布局设计等等。
二、注塑成型过程中存在的问题本文以熔接痕为例,阐述注塑成型中的问题。
通常情况下,熔接痕的形成原因主要有以下几个方面:(1)功能结构。
如果制件表面有槽、孔或者厚度不一,就会在注塑的过程中发生熔接痕。
在厚度不一的情况下,厚度较大的位置受到压力大,流速快,而厚度薄的地方则与之相反。
由于两中溶体的速度差,使之在相遇的过程中发生熔接痕。
注塑模冷却系统设计中的CAE

件有很好配合,表面质量要求较高,零件主要尺 寸为:外圆直径 5 8 m m,内圆直径 1 0 m m ,壁厚 3.2mm ,凸台外径 28mm ,高度 3.2mm。浇口选 在内圆侧壁,以保证外表质量。此零件厚度较 薄,且没有加强筋,在高温注射条件下,很容易 产生零件形状的变形。为了能缩短冷却时间,提 高生产效率,希望在模具上开冷却管道,同时希 望通过冷却介质与零件的热交换,使零件各处在 注射时的温度比较均匀,尽量减少其变形量及其 它缺陷。现冷却管道设计方案有两种,如图 2、 图 3 所示。冷却管道 1 是动定模上各由二条直管 道联连而成,冷却管道2是动定模上各由三条直 管道联接而成。其它设计和注射条件均相同:冷 却管道直径 8mm,距零件表面 12mm ,塑件材料 为聚丙烯(PP),模具材料为 45# 钢,冷却介质 为水,其入口温度为 20℃,流速为 5m/s,料温 235℃等。先作一般的分析:由于浇口开在内圆 侧壁,冷却管道 1 入口比冷却管道 2 入口更接近 浇口,这对温度最高的浇口位置冷却效果好,且 冷却管道1长度较短,使冷却介质在模内升温较 低;由于冷却管道2长度较长,使热交换面积增 大,还可看出冷却管道 2 在零件上的分布较均 匀。上述可见,冷却管道 1 和冷却管道 2 在对模 具降温方面、使零件各处在注射时的温度比较均 匀方面,各自有其有利的因素。根据上述分析难 以选择冷却系统,且选择冷却系统时还有许多其 它因素必须考虑。用CAE软件进行分析,便能得
主要用到的是流动分析模块、冷却分析模 块、翘曲分析模块,其作用是:
MF/Flow 流动分析模块用来分析聚合物在 模具中的流动,并且优化模腔的布局、材料的选 择、填充和保压的工艺参数。可以在产品允许的 强度范围内和合理的充模情况下减少模腔的壁 厚,让熔接线和气泡处于结构和外观允许的位置 上,并且定义一个范围较宽的工艺条件。
CAE技术在光学透镜注射模设计中的应用

中图分类号:P9. ; 306 文献标识码: 文章编号: 0 — 1 (o70— 01 0 T 31 2 Q 2. 2 7T 6 B 1 1 2 820)1 00 — 4 0 6
Ap ia in o pl to f CAE e hn lg i d sg c tc oo y n e in
箱) 瑚 昏. . u ∞, 剐 e . d 13cr 6. r ot o
模拟出塑料熔体在注射成型过程中的流动保压和冷 却过程以及预. 产品中的应力分布、 ? 贝 4 分子取向、 收缩 和翘曲变形等。在塑料透镜模具设计中,应用 C E A 技术帮助预测聚合物熔体在型腔 中的成型过程,及 早发现问题, 及时修改模具设计, 提高一次试模成功 率, 以缩短开发周期 , 降低生产成本, 增强市场竞争
维普资讯
模具工业 20 年 第 3 卷第 1 07 3 期
C E技 术在光学透镜注射模设计 中的应用 A
周应国,陈静波,申长雨,闽志宇
( 郑州大学 橡塑模具国家工程研究中心,河南 郑州 400 ) 502
摘要 : 将注射成型中塑料熔体在型腔 内充填模拟基本理论及熔体前沿跟踪技术应用到具体 的光学透镜 模具设计中。通过对模拟结果的分析与评判,有效预防 了原模具设计方案用于实际生产时可能 出现的 问题, 生产出了合格的产品, A C E技术的可靠性与实用性得到证 实。 关键词 : 注射成型; 充填 ; 模具设计 ; 光学透镜;A C E技术
基于注塑CAE的管件反变形设计
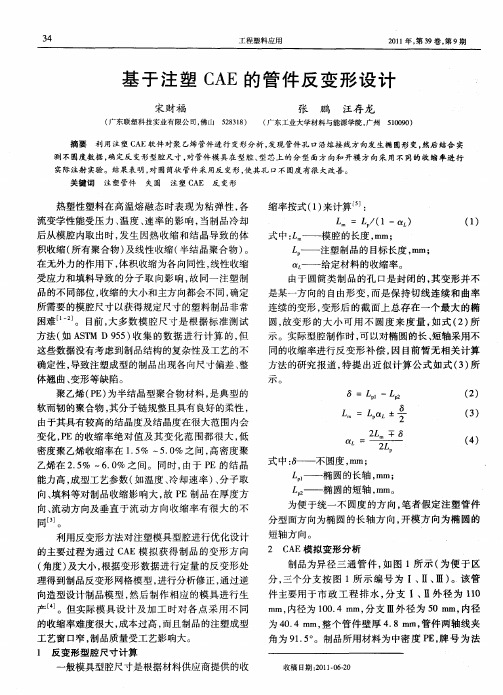
实际注射 实验 。结果表 明, 对圆筒状管件采用反 变形, 其孔 口不圆度有很 大改善。 使
关键 词 注 塑 管件 失 圆 注 塑 C E 反 变形 A
热塑性 塑料 在高 温熔 融态 时 表现 为 粘 弹性 , 各 流变学 性能受 压 力 、 温度 、 速率 的 影 响 , 当制 品冷 却 后从模 腔 内取 出时 , 生 因热 收缩 和 结 晶导 致 的体 发
1 反 变形型腔 尺 寸计算
一
mm, 内径为 104m 分支 Ⅲ外 径 为 5 m, 0 . m, 0m 内径 为 4 . 04mm, 整个 管 件 壁厚 4 8mm, . 管件 两 轴线 夹
角为 9.。 1 5 。制 品所用 材料 为 中密 度 P , 号 为 法 E牌
收稿 1 :0 10 -0 3期 2 1-62
分, 三个分 支按 图 1 所示 编号为 I Ⅱ、 。该管 、 Ⅲ)
件 主要 用于 市 政 工 程 排 水 , 支 I、 分 Ⅱ外 径 为 10 1
向造 型设计制 品模 型 , 后 制作 相 应 的模 具 进行 生 然
产 。但实际模具设计及加工时对各点采用不 同 J
的收缩 率难度 很大 , 成本 过高 , 而且制 品的注 塑成 型 工艺 窗 口窄 , 品质 量受 工艺影 响大 。 制
工程塑料应用
21 , 3 0 1年 第 9卷 , 9期 第
基 于注 塑 C E的 管件 反 变形 设 计 A
宋财福
( 东 联 塑科 技 实 业 有 限 公 司 , 山 广 佛 581) 2 3 8
张
鹏
汪存 龙
5 09 ) 10 0
( 东 工业 大 学 材 料 与 能 源学 院 , 州 广 广
注塑产品变形怎么调机【秘籍】
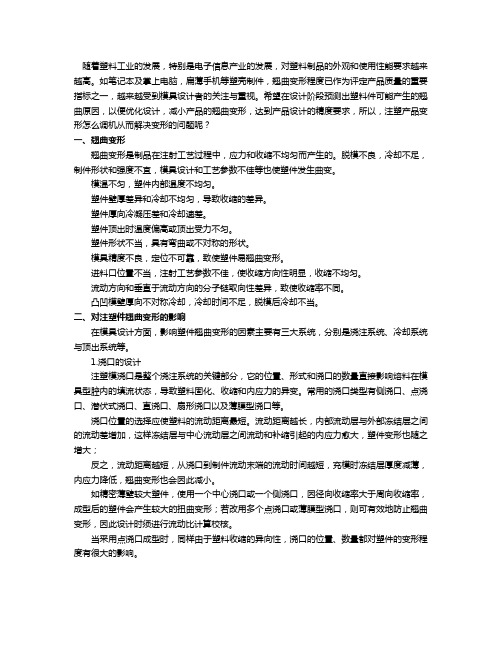
随着塑料工业的发展,特别是电子信息产业的发展,对塑料制品的外观和使用性能要求越来越高。
如笔记本及掌上电脑,扁薄手机等塑壳制件,翘曲变形程度已作为评定产品质量的重要指标之一,越来越受到模具设计者的关注与重视。
希望在设计阶段预测出塑料件可能产生的翘曲原因,以便优化设计,减小产品的翘曲变形,达到产品设计的精度要求,所以,注塑产品变形怎么调机从而解决变形的问题呢?一、翘曲变形翘曲变形是制品在注射工艺过程中,应力和收缩不均匀而产生的。
脱模不良,冷却不足,制件形状和强度不宜,模具设计和工艺参数不佳等也使塑件发生曲变。
模温不匀,塑件内部温度不均匀。
塑件壁厚差异和冷却不均匀,导致收缩的差异。
塑件厚向冷凝压差和冷却速差。
塑件顶出时温度偏高或顶出受力不匀。
塑件形状不当,具有弯曲或不对称的形状。
模具精度不良,定位不可靠,致使塑件易翘曲变形。
进料口位置不当,注射工艺参数不佳,使收缩方向性明显,收缩不均匀。
流动方向和垂直于流动方向的分子链取向性差异,致使收缩率不同。
凸凹模壁厚向不对称冷却,冷却时间不足,脱模后冷却不当。
二、对注塑件翘曲变形的影响在模具设计方面,影响塑件翘曲变形的因素主要有三大系统,分别是浇注系统、冷却系统与顶出系统等。
1.浇口的设计注塑模浇口是整个浇注系统的关键部分,它的位置、形式和浇口的数量直接影响熔料在模具型腔内的填流状态,导致塑料固化、收缩和内应力的异变。
常用的浇口类型有侧浇口、点浇口、潜伏式浇口、直浇口、扇形浇口以及薄膜型浇口等。
浇口位置的选择应使塑料的流动距离最短。
流动距离越长,内部流动层与外部冻结层之间的流动差增加,这样冻结层与中心流动层之间流动和补缩引起的内应力愈大,塑件变形也随之增大;反之,流动距离越短,从浇口到制件流动末端的流动时间越短,充模时冻结层厚度减薄,内应力降低,翘曲变形也会因此减小。
如精密薄壁较大塑件,使用一个中心浇口或一个侧浇口,因径向收缩率大于周向收缩率,成型后的塑件会产生较大的扭曲变形;若改用多个点浇口或薄膜型浇口,则可有效地防止翘曲变形,因此设计时须进行流动比计算校核。
过滤器壳体注塑模具设计

目录第一章绪论 (1)1.1 塑料模现状及发展趋势 (1)1.1.1 我国模具的发展现状 (1)1.1.2 塑料模的行业情况 (1)1.1.3 塑料模发展趋势 (2)1.2 塑件的结构设计 (3)1.2.1 功能结构设计 (3)1.2.2 工艺结构设计 (4)1.2.3 造型结构设计 (4)1.3 Pro/Engineer简单介绍 (5)第二章1441型过滤器下壳体的结构分析 (6)2.1 塑件分析 (6)2.2 塑件材料的选择 (6)2.2.1 ABS的性能和成型特点 (6)2.3 塑料制件的结构工艺性 (7)2.3.1 凸台的设计 (7)2.3.2 壁厚 (7)2.3.3 表面粗糙度 (7)2.3.4 尺寸公差和精度 (7)2.3.5 圆角 (8)2.3.6 孔的设计 (8)2.3.7 脱模斜度 (9)第三章1441型过滤器下壳体的模具设计 (10)3.1注射机的选择及型腔数目的确定 (10)3.2 塑件分析 (10)3.2.1 塑件的质量体积分析及ABS的注射工艺性 (10)3.2.2 型腔数目的确定 (11)3.2.3 注塑机的选择 (11)3.3 分型面的选择 (13)3.4 模具方案的确定 (13)3.5 浇注系统设计和排气系统的设计 (14)3.5.1 浇注系统 (14)3.5.2 冷料穴设计 (15)3.5.3 分流道设计 (16)3.5.4 浇口设计 (17)3.5.5 定位圈和浇口套的选择 (18)3.6 成型零部件设计 (19)3.6.1 成型零件工作尺寸的计算 (20)3.7 凹模型腔侧壁、底板厚度的计算 (21)3.7.1 凹模侧壁厚度的计算 (21)3.7.2 底板厚度的计算 (22)3.7.3 凸模结构设计 (23)3.8 模架的选取 (24)3.8.1 定位销的选择 (25)3.9 脱模机构的设计 (25)3.9.1 脱模方案的选择 (25)3.9.2 脱模力的计算和推杆数目的选择 (25)3.9.3 推杆的稳定性计算 (26)3.10 复位杆设计 (27)3.11 垫块的选择 (27)3.12 导柱与导套的选择 (27)3.13 推出机构的导向 (29)3.14 侧向分型与抽芯机构的设计 (30)3.14.1 侧向分型与抽芯机构的选定 (30)3.14.2 抽芯距的确定与抽芯力的计算 (30)3.14.3 斜导柱的设计 (31)3.14.4 侧滑块的设计 (32)3.14.5 导滑槽设计 (32)3.14.6 楔紧块设计 (33)3.15 吊环螺钉的设计 (33)3.16 温度调节系统的设计 (33)3.16.1 温度调节系统分析 (33)3.16.2 热平衡计算 (34)3.16.3 冷却面积计算 (35)3.16.4 冷却系统设计 (36)第四章模具调试 (37)4.1 模具调试 (37)4.1.1 注射机的选用 (37)4.1.2 模具的安装 (37)4.1.3 成型工艺条件的拟定 (38)第五章模具的经济技术分析 (39)5.1 影响模具价格的因素 (39)5.2 模具价格的计算 (39)结论 (42)致谢 (43)参考文献 (44)第一章绪论1.1 塑料模现状及发展趋势1.1.1 我国模具的发展现状80年代以来,在国家产业政策和与之配套的一系列国家经济政策的支持和引导下,我国模具工业发展迅速,年均增速均为13%,1999年我国模具工业产值为245亿,至2000年我国模具总产值预计为260-270亿元,其中塑料模约占30%左右。
基于CAE技术的汽车座椅配件冲压分析与设计优化

基于CAE技术的汽车座椅配件冲压分析与设计优化诸进才;胡艳娥;李兆飞【摘要】Based on its forming precision and production quantity,the structural characteristics and stamping process of a sheet-metal part for a seat holder of autocar are analyzed,by which a proposal of multi-position progressive die is proposed. Then the sheet-metal part is unfolded automatically by FormingSuite software,and the most dangerous forming region obtained by the analysis results of software simulation is used to modify the original design,which avoids mold design flaws and reduces the number of die repairing. Practice has proved that the multi-position progressive die is reasonable and is an important reference for similar parts when producing by progressive die.% 根据某型号轿车座椅配件的成形精度和生产批量等要求,分析冲压件的结构特点和冲压工艺,提出采用多工位级进模的冲压方案。
然后应用冲压分析软件FormingSuite对钣金件进行自动展开计算,最后基于冲压CAE技术得出最危险的区域并根据分析结果对冲压工艺过程进行调整和优化。
空气滤清器声学性能仿真研究

空气滤清器声学性能仿真研究空气滤清器声学性能仿真研究空气滤清器在进气系统中起到过滤空气和消声这两大作用,受发动机舱空间的限制,进气系统的设计需要进行合理的布置,充分利用有效的空间,因此,通常情况下,进气系统的结构都比较复杂,利用一维仿真很难得到准确的仿真结果。
有鉴于此,发动机进气系统设计普遍采用三维仿真方法,如声学边界元法(Acoustic BEM,ABEM)、声学有限元法(Acoustic FEM,AFEM)。
声学边界元法(ABEM)一般只需建立好进气系统内腔的表面,并采用二维单元划分内腔表面即可建立起三维的边界元模型,由于进气系统属于开口结构,通常采用间接边界元法(Indirect BEM,IBEM),壳体被默认为刚性的。
声学有限元法(AFEM)则需要建立进气系统内腔的空气介质及滤芯模型,并采用三维单元进行网格划分,若材料仅定义成空气,则与声学边界元结果基本一致,壳体被默认为刚性的,将滤芯定义为吸声材料,可以考虑到滤芯对气动噪声的影响。
1.声学材料常数及边界条件设置滤清器空腔声学模态分析模型采用封闭腔体边界条件,即设定腔体四周为没有弹性的硬边界;声传递损失计算用分析模型的边界条件施加方式为,入(出)口侧施加速度边界条件,幅值为-1m/s,出(入)口设置特性阻抗为416.5Rays,其余边界为硬边界;滤清器壳体模态分析中,根据实际工作情况、约束壳体底部三个支点。
2.声学模态计算结果结构模态较为密集,而在能量集中的低频模态区域,声腔模态较少,有利于整体结构的振声性能。
壳体结构模态和空腔声学模态基本没有重合,发生结构与声学模态耦合共振的可能性较小。
从声学模态振型可知,在第5阶模态之后,声腔模态不再是平面波传播,因此,声腔的截止频率约在800Hz。
和结构模态对比,在声腔的第3阶模态频率和结构的第15阶模态频率相近,有共振的可能性。
与方案Ⅰ相比,方案Ⅲ各阶声学模态频率普遍有所降低。
3.空气滤清器声传递损失计算 TL=101gWW=101gSPuSPu=101gSPSP 在高于1500Hz高频区域,通过频率点分布较为密集,且无明显规律可循,但安装滤纸后该区域的传递损失情况会有较大改善,可不必过于注意。
- 1、下载文档前请自行甄别文档内容的完整性,平台不提供额外的编辑、内容补充、找答案等附加服务。
- 2、"仅部分预览"的文档,不可在线预览部分如存在完整性等问题,可反馈申请退款(可完整预览的文档不适用该条件!)。
- 3、如文档侵犯您的权益,请联系客服反馈,我们会尽快为您处理(人工客服工作时间:9:00-18:30)。
在 、l方 向 ( , 即装 配方向 )的变形值控制在 ±15I ' . ll Y 内. n
图 1 空滤 器 三 维 图
Fg 1 Aiftr at i, rie r l p
2 纸 芯 嵌件 简 化 处 理 及 成 型 参数 的预 置
一
般 来说 ,嵌件 与塑 料 的膨 胀 系数 是不 一样 的.在 塑件 与嵌件 的接合 部 附近会产 生变 形 ,在嵌件
效 率 ,降低 成 本 ,所 生 产 的 空滤 器 产 品 质 量 好 ,与采 用 简化 结 构 的模 拟 结 果 相 符 .
[ 关键词] 纸芯嵌件 ;空气滤清 器;注射模具 ;反 变形 ;立式注塑
[ 中图分 类号]T 3 0 6 2 P 1 [ Q 2 .6 ;T 39 文献标志码]A [ 文章编号 ]10 0 8—30 (00 3— 0 4— 5 84 2 1 )0 0 2 0
第 3期
葛 晓宏 ,等 :基 于 C E的纸 芯空 气 滤 清器 注射 模 反 变 形 设 计 A
。 5‘ 2
匹配率 为 8 % ,平 均 纵横 比为 4 1 6 : ,各 项 指 标 均符 合 MO D L W 的分 析 要求 . 材料 选 用 Plpc c L FO o ai y f i 公 司生 产 的型号 为 Cr nC 0 FH 00 ot 330T S 14的 P o 7 P+T (0 ) 塑料 ,根据 该材料 的特 点及企 业生 产 3%
1 纸 芯 空滤 器 产 品分 析
纸芯空滤器 的结构 如 图 1 所示 .该产 品呈长 方形 ,外形 尺寸
为 2 4m × 6 m × 0mm,最小壁厚 13m 2 m 12m 3 . m,最 大壁厚 3ml i. 1
产 品中间部分 为滤纸嵌件 ,纸芯材料 规格番号为 A 16 ,折幅 为 K62 2.8ml 35 i,宽度为 195r 1 l 4 . n ,栅数 为 4 ,滤过 面积为 302 m ; H 7 3 .5c 2 框架 塑料材料 为 7 % 聚丙烯 ( P +3 %滑石 粉 ( a ) 0 P) 0 Tl . c 为保证空滤器 的使用 效果 ,中间的滤 纸不能 出现 破损 ,也不 允许滤纸上有塑料 飞边.为保 证空 滤器 的塑料 框架 与外 接机 构接 触紧密 ,要求框架 四周外表 面光 整 ,尺 寸精度 高 ,因此要 求产 品
第21年9 3期 1 8卷 00 第 月
. 门理 工 学院 学报 厦
J u n l fXime n v ri f e h o o y o r a a n U ie s y o c n l g o t T
V0 . 8 No. J1 3 S p.2 0 e 01
基 于 C E的 纸 芯 空气 滤 清 器 注 射 模 反 变 形 设 计 A
纸芯空气 滤清器是发动机重 要配套附件之一 ,用 于滤除空气 中的硬质灰 尘颗粒 ,向发 动机提供 清洁
空气 ,防止灰尘造成发 动机 缸套 、活塞杆等 主要零 部件 的磨损及发 动机润 滑油 的污 染 ,从 而提高发 动机 的可靠 性 ,延长使用寿命 .空滤器的质量主要决定 于滤纸和成型工艺及模 具装备 . 因此 ,只能从 成型
工 艺及模 具 装 备 方 面进 行 改 良优 化 ,提 高空 滤 器 的质 量 .在此 背 景 下 ,应 生 产 厂 家要 求 ,借助 C E A ( o pt e nier g Cm u r e MddE g en )模拟技术改进模具结构和工艺方案 ,以期降低废品率 ,进而提高产 品质量. n i
状 况 ,初 步拟 定 了如下工 艺参数 ,如表 1所示 .
周 围的制 品往往 会 出现 裂纹 . 当注 射 完成 后 ,塑件 会 在 冷却 水 的作 用 下 逐 步 冷 却 ,在 塑 件 收缩 过 程 中 ,柔性 滤纸 的边缘部 位也 会跟 着一起 收缩 同样 的大小 .而在 注塑 生产 时 ,模 具合模 后会将 滤 纸紧 固 在模 仁之 间 ,边 缘 的滤 纸会 与填 充 的熔 融塑 料接触 结合 ,滤纸对 制 品填充 、冷却 和变 形基本 不构 成影
葛晓宏 ,李 辉 ,范增 伟 ,陈 敏
( 门理 工 学 院材 料 成 形 与模 具 集 成 技 术研 究所 ,福 建 厦 门 3 12 ) 厦 60 4
[ 摘
要 ]基于 C E技 术,对带有 柔性 嵌件 的纸芯 空气滤清 器进行 了填 充、冷却和翘 曲等模 拟分多点进浇方案 ,可避免 熔体直接 冲击纸芯嵌件.针对 空滤 器塑件框 架由于收
缩 引起 的 不 可避 免 的 内凹 变形 ,设 计 了合 理 的 冷 却 方 案 ,提 出 了模 具 型 腔 外 凸 的反 变 形 设 计 方 法 ,使 空 滤
器 安 装 平 面 变 形得 到 合 理 的控 制 . 采 用 立 式 注 塑 机 和 一 个 前 模 、 两 个后 模 的 生 产 组 合 方 式 ,显 著 提 高 成 型
响 .因此 ,在模 拟分析 时不需 要建 立嵌件 模 型.
基 于该 纸芯 空滤器 的特 点 ,本 次分析 采用 双层 面 网格 .经 修整 网格后 ,网格 单元 数 为 两万 多 个 ,
[ 收稿 日期 2 1 0 00~ 8—1 9 [ 修回 日期]2 1 0 0 0— 9—1 6 [ 基金项 目]福建省科技计划重点项 目 (0 8 0 3 ) 2 0 H 0 8 ;福建 省重大项 目 ( 0 0 6 2 ) 2 1 H 0 8 ;厦 门市经发局产 学研项 目 ( X 80 ) H 0 0 3 ;厦门市科 技计 划项 目 (5 2 20 3 2 ) 30 Z 0 80 7 【 作者简介]葛晓宏 (9 4一) 16 ,男 ,江苏建湖人 ,副教授 ,硕士 ,从事材料成形工艺及模 具 C E的研究 . A