合金钢线材问题汇总
合金钢线材的热处理工艺优化与影响因素分析

合金钢线材的热处理工艺优化与影响因素分析随着工业技术和材料科学的不断发展,合金钢在各个行业中得到了广泛应用。
其优异的力学性能和耐热性使其成为诸多结构件、机械零件和工具的首选材料之一。
然而,合金钢的力学性能和性能稳定性很大程度上取决于热处理工艺的选择和优化。
因此,本文将重点探讨合金钢线材的热处理工艺优化与影响因素分析。
一、合金钢线材的热处理工艺在热处理工艺的选择上,合金钢线材主要经历四个阶段,包括退火、正火、淬火和回火。
这些热处理阶段可用于改善钢材的力学性能、提高材料硬度和耐热性以及消除内部应力。
1. 退火退火是合金钢线材热处理工艺中的第一步,其目的是消除冷加工过程中产生的应力和塑性变形,并使晶粒得到再结晶,提高钢材的塑性和韧性。
适当的退火温度和时间对于合金钢线材的后续处理步骤非常重要。
2. 正火正火是通过控制冷却速率和加热温度,使合金钢线材达到所需的力学性能和组织结构。
正火可以增加合金钢的硬度和强度,提高材料的耐磨性和抗拉强度。
然而,正火温度过高或冷却速率过快都会导致材料的过硬化和脆化。
3. 淬火淬火是将合金钢线材迅速冷却到室温以下,以使其组织结构转变为马氏体,增加钢的硬度和强度。
淬火水槽或油槽是常用的淬火介质,通过控制淬火温度和淬火介质来实现所需的力学性能。
4. 回火回火是合金钢线材热处理工艺中的最后一步,通过加热和保温,使淬火后的马氏体转变为较稳定的组织结构,以降低钢材的硬度和脆性,增加韧性和耐用性。
回火温度和时间的选择很大程度上取决于合金钢的成分和所需的性能。
二、合金钢线材热处理工艺的影响因素在优化合金钢线材的热处理工艺时,需要考虑以下几个关键因素:1. 材料成分合金钢的成分对于热处理工艺的选择和优化起着至关重要的作用。
不同的合金元素会影响钢材的相组成和相变温度,从而影响钢材的组织结构和性能。
因此,在进行热处理工艺优化时,需要根据合金钢的具体成分确定合适的处理温度和时间。
2. 加热和冷却速率加热速率和冷却速率是影响合金钢线材组织结构和性能的重要因素。
合金钢常用的维修工艺

合金钢常用的维修工艺合金钢是一种含有高比例合金元素的钢材,常常具有高强度、高硬度、高耐磨性等优异性能。
然而,在使用过程中,由于各种原因,合金钢可能会出现各种损伤和故障,需要进行维修。
下面将介绍合金钢常用的维修工艺。
1. 焊接修复:合金钢常用的维修方法之一就是通过焊接修复来进行。
焊接修复可以使用多种焊接方法,如手工电弧焊、气体保护焊、电阻焊等。
在选择焊接方法时需要考虑合金钢的具体材质和损伤情况。
焊接修复可以对合金钢进行填补,连接或强化。
2. 热处理修复:合金钢在使用过程中可能由于过热或过冷等原因产生缺陷和应力,导致材料性能下降或产生裂纹。
热处理修复可以通过控制温度和冷却速率等方式来改善合金钢的性能。
常用的热处理方法包括退火、正火、淬火和回火等。
3. 加工修复:合金钢在使用过程中可能会有一些机械加工缺陷,如划伤、凹陷、磨损等。
加工修复可以通过机械加工的方式将损坏或磨损的部分去除,然后再进行研磨、打磨、抛光等工序来恢复合金钢的原始形状和光洁度。
4. 粘接修复:合金钢在使用过程中可能会出现破裂或开裂的情况,此时可以使用粘接修复的方法来进行修复。
粘接修复可以使用多种胶黏剂或焊接材料,将合金钢的破裂部分黏合起来。
在选择粘接材料时需要考虑合金钢的材质和工作环境等因素。
5. 表面修复:合金钢的表面可能会出现腐蚀、氧化、磨损等情况,需要进行表面修复。
表面修复可以通过喷涂、涂覆、电镀、阳极氧化等方法来实现。
表面修复可以提高合金钢的耐腐蚀性、耐磨性和美观度。
综上所述,合金钢常用的维修工艺包括焊接修复、热处理修复、加工修复、粘接修复和表面修复等。
在进行维修时,需要根据具体的损伤情况和合金钢的材质选取合适的维修方法,以保证修复效果和性能恢复。
同时,维修过程中需要遵循相关的安全操作规程和操作规范,确保人身安全和设备的正常运行。
线材表面缺陷原因分析及对策

线材表面缺陷原因分析及对策摘要:从设备管理的角度,分析设备问题影响材线表面的各种原因,针对设备存在的问题提出改进措施,表面缺陷得到有效控制。
关键词:线材;表面质量;设备前言线材表面质量是用户对公司实物的第一认知,直接影响到用户对公司产品的满意度。
线材在轧制过程中,设备与线材接触面状况对成品材表面影响极大。
1影响线材表面质量的因素1.1 钢坯表面氧化铁皮影响线材表面质量的原因分析炉温控制不合理,导致钢坯在高温段的停留时间长,钢坯表面氧化严重,经各架轧机轧制后,表面氧化铁皮不能及时脱落,最终嵌入线材表面,形成次材。
空燃配比控制不合理,炉膛为氧化气氛,钢坯表面氧化严重,最终导致线材表面产生缺陷。
高压水除鳞压力不足或是喷嘴安装不正确,不能将钢坯表面的氧化铁皮彻底清除,最终引起成品表面形成麻点、铁皮等缺陷,进而造成次品。
1.2 导卫影响线材表面质量的原因分析由于导卫装配原因,导卫导辊转动不灵活或是导辊对轧件不能起到有效的支撑作用,最终导致轧件表面有划伤、折叠等缺陷。
由于油气润滑以及冷却水系统故障,造成导辊碎裂、粘钢、烧轴承等现象发生,进而导致轧件表面出现划伤。
由于导辊材质原因,在生产过程中有“掉肉”现象发生,进而导致线材表面出现划痕、结疤等缺陷。
由于导卫上线安装原因,导致轧件导入下游轧机时,不能对中相应轧机的孔型,进而导致线材表面出现耳子等缺陷。
1.3 轧辊、辊环影响线材表面质量的原因分析由于轧辊、辊环的质量问题,导致轧辊、辊环在生产过程中有“掉肉”现象发生,进而导致线材表面出现划伤、结疤等缺陷。
由于轧辊、辊环的上线装配原因,各架料型控制不合适,最终导致线材表面出现折叠、耳子等缺陷。
1.4活套轮影响线材表面质量的原因分析活套轮直接与线材表面接触,每条线装机量29个,其运行状态与红钢接触面光洁度对成品线材表面影响非常大。
活套轮高度参数不正确或设定变化范围大,活套轮安装偏离轧制中心线过多,造成辊轮表面磨损不光滑,造成线材表面出现划痕、划伤等问题。
型钢、线材常见缺陷及原因

缺陷名称
缺陷特征
产生原因
结疤
型钢表面上的疤状金属薄块。其大小、深浅不等,外形极不规则,常呈指甲状、鱼鳞状、块状、舌头状无规律地分布在钢材表面上,结疤下常有非金属夹杂物。
由于钢坯未清理,使原有的结疤轧后仍残留在钢材表面上。
表面夹杂
暴露在钢材表面上的非金属物质称为表面夹杂,一般呈点状、块状和条状分布,其颜色有暗红、淡黄、灰白等,机械的粘结在型钢表面上,夹杂脱落后出现一定深度的凹坑,其大小、形状无一定规律。
(1)矫直辊孔型设计不合理。
(2)矫直机调整操作不当。
(3)矫直辊磨损严重。
(4)轧辊磨损或成品孔出口卫板安装不良。
线材常见缺陷
缺陷名称
缺陷特征
产生原因
耳子
盘条表面沿轧制方向的条状凸起称为耳子,有单边耳子,也有双边耳子。在高速线材轧机(连轧)生产中,最终产品头尾两端很难避免耳子的产生。
1)轧槽导卫安装不正及放偏过钢,使轧件产生耳子。
裂纹
顺轧制方向出现在型钢表面上的线形开裂,一般呈直线形,有时呈“Y”形,多为通长出现,有时局部出现。
(1)钢坯有裂缝或皮下气泡、非金属夹杂物,经轧制破裂暴露。
(2)加热温度不均匀,温度过低,轧件在轧制时各部延伸与宽展不一致。
(3)加热速度过快、炉尾温度过高或轧制后冷却不当,易形成裂纹,此种情况多发生在高碳钢和低合金钢上。
(1)孔型设计不良,轧辊车削不正确及轧机调整不当,使轧件进入成品孔时由于金属量不足,造成孔型充填不满。
(2)轧槽错牙或入口导板安装不当,造成轧件某一面缺少金属,再轧时孔型充填不满。
(3)前、后孔磨损程度不一样。
(4)园轧件弯、扭造成进孔不正。
(5)对于工、槽钢,困钢坯不清理,往往出现结疤掉到闭口腿内,在轧制过程中便会出现周期性的腿尖缺肉。
线材产品质量缺陷
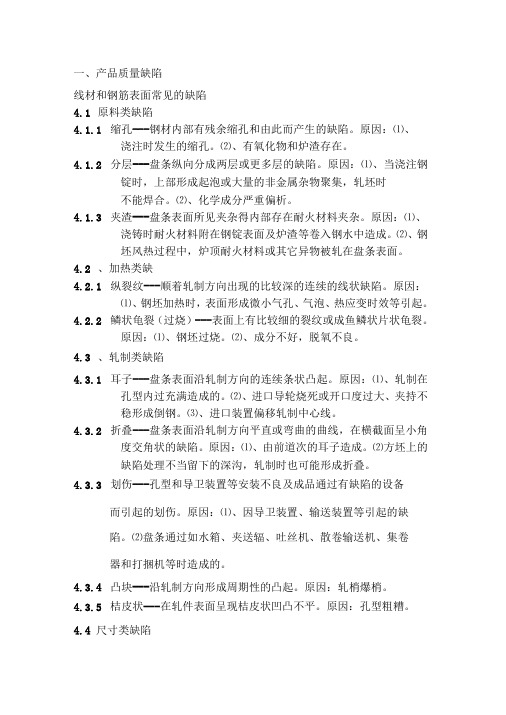
一、产品质量缺陷线材和钢筋表面常见的缺陷4.1原料类缺陷4.1.1缩孔---钢材内部有残余缩孔和由此而产生的缺陷。
原因:⑴、浇注时发生的缩孔。
⑵、有氧化物和炉渣存在。
4.1.2分层---盘条纵向分成两层或更多层的缺陷。
原因:⑴、当浇注钢锭时,上部形成起泡或大量的非金属杂物聚集,轧坯时不能焊合。
⑵、化学成分严重偏析。
4.1.3夹渣---盘条表面所见夹杂得内部存在耐火材料夹杂。
原因:⑴、浇铸时耐火材料附在钢锭表面及炉渣等卷入钢水中造成。
⑵、钢坯风热过程中,炉顶耐火材料或其它异物被轧在盘条表面。
4.2、加热类缺4.2.1纵裂纹---顺着轧制方向出现的比较深的连续的线状缺陷。
原因:⑴、钢坯加热时,表面形成微小气孔、气泡、热应变时效等引起。
4.2.2鳞状龟裂(过烧)---表面上有比较细的裂纹或成鱼鳞状片状龟裂。
原因:⑴、钢坯过烧。
⑵、成分不好,脱氧不良。
4.3、轧制类缺陷4.3.1耳子---盘条表面沿轧制方向的连续条状凸起。
原因:⑴、轧制在孔型内过充满造成的。
⑵、进口导轮烧死或开口度过大、夹持不稳形成倒钢。
⑶、进口装置偏移轧制中心线。
4.3.2折叠---盘条表面沿轧制方向平直或弯曲的曲线,在横截面呈小角度交角状的缺陷。
原因:⑴、由前道次的耳子造成。
⑵方坯上的缺陷处理不当留下的深沟,轧制时也可能形成折叠。
4.3.3划伤---孔型和导卫装置等安装不良及成品通过有缺陷的设备而引起的划伤。
原因:⑴、因导卫装置、输送装置等引起的缺陷。
⑵盘条通过如水箱、夹送辐、吐丝机、散卷输送机、集卷器和打捆机等时造成的。
4.3.4凸块---沿轧制方向形成周期性的凸起。
原因:轧梢爆梢。
4.3.5桔皮状---在轧件表面呈现桔皮状凹凸不平。
原因:孔型粗糟。
4.4尺寸类缺陷4.4.1横肋纵肋偏小---沿轧制方向形成的连续的偏小现象,原因:来料小,孔型充不满。
4.4.2、水平尺寸超标---沿扎制方向形成的连续超标现象。
⑴、来料大。
⑵、进口有倒钢现象。
优特品种钢(合金钢连铸)100问
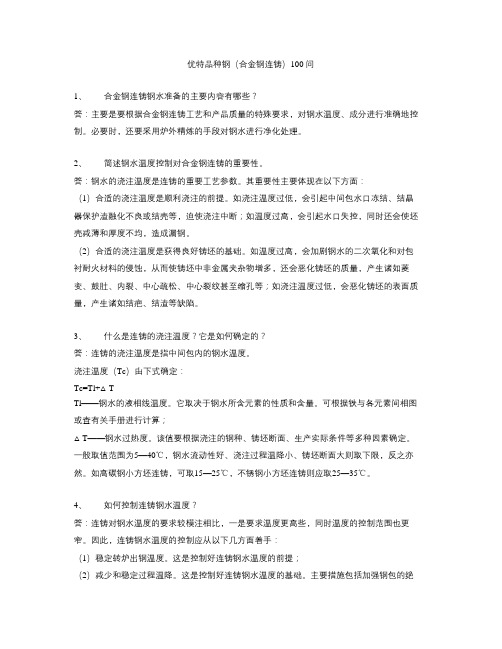
优特品种钢(合金钢连铸)100问1、合金钢连铸钢水准备的主要内容有哪些?答:主要是要根据合金钢连铸工艺和产品质量的特殊要求,对钢水温度、成分进行准确地控制。
必要时,还要采用炉外精炼的手段对钢水进行净化处理。
2、简述钢水温度控制对合金钢连铸的重要性。
答:钢水的浇注温度是连铸的重要工艺参数。
其重要性主要体现在以下方面:(1)合适的浇注温度是顺利浇注的前提。
如浇注温度过低,会引起中间包水口冻结、结晶器保护渣融化不良或结壳等,迫使浇注中断;如温度过高,会引起水口失控,同时还会使坯壳减薄和厚度不均,造成漏钢。
(2)合适的浇注温度是获得良好铸坯的基础。
如温度过高,会加剧钢水的二次氧化和对包衬耐火材料的侵蚀,从而使铸坯中非金属夹杂物增多,还会恶化铸坯的质量,产生诸如菱变、鼓肚、内裂、中心疏松、中心裂纹甚至缩孔等;如浇注温度过低,会恶化铸坯的表面质量,产生诸如结疤、结渣等缺陷。
3、什么是连铸的浇注温度?它是如何确定的?答:连铸的浇注温度是指中间包内的钢水温度。
浇注温度(Tc)由下式确定:Tc=Tl+△TTl——钢水的液相线温度。
它取决于钢水所含元素的性质和含量。
可根据铁与各元素间相图或查有关手册进行计算;△T——钢水过热度。
该值要根据浇注的钢种、铸坯断面、生产实际条件等多种因素确定。
一般取值范围为5—40℃,钢水流动性好、浇注过程温降小、铸坯断面大则取下限,反之亦然。
如高碳钢小方坯连铸,可取15—25℃,不锈钢小方坯连铸则应取25—35℃。
4、如何控制连铸钢水温度?答:连铸对钢水温度的要求较模注相比,一是要求温度更高些,同时温度的控制范围也更窄。
因此,连铸钢水温度的控制应从以下几方面着手:(1)稳定转炉出钢温度。
这是控制好连铸钢水温度的前提;(2)减少和稳定过程温降。
这是控制好连铸钢水温度的基础。
主要措施包括加强钢包的绝热保温和热周转的管理,采取红包出钢,钢液面添加绝热保温材料,钢水包和中间包加盖,必要时可考虑采取加热措施,如上LF炉、中间包等离子加热等;(3)采取必要的温度调整的手段。
线材问题汇总
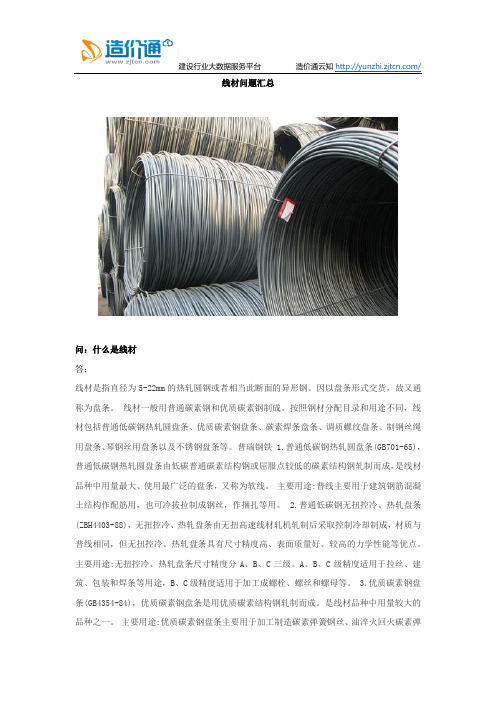
线材问题汇总问:什么是线材答:线材是指直径为5-22mm的热轧圆钢或者相当此断面的异形钢。
因以盘条形式交货,故又通称为盘条。
线材一般用普通碳素钢和优质碳素钢制成。
按照钢材分配目录和用途不同,线材包括普通低碳钢热轧圆盘条、优质碳素钢盘条、碳素焊条盘条、调质螺纹盘条、制钢丝绳用盘条、琴钢丝用盘条以及不锈钢盘条等。
普瑞钢铁 1.普通低碳钢热轧圆盘条(GB701-65),普通低碳钢热轧圆盘条由低碳普通碳素结构钢或屈服点较低的碳素结构钢轧制而成,是线材品种中用量最大、使用最广泛的盘条,又称为软线。
主要用途:普线主要用于建筑钢筋混凝土结构作配筋用,也可冷拔拉制成钢丝,作捆扎等用。
2.普通低碳钢无扭控冷、热轧盘条(ZBH4403-88),无扭控冷、热轧盘条由无扭高速线材轧机轧制后采取控制冷却制成,材质与普线相同,但无扭控冷、热轧盘条具有尺寸精度高、表面质量好、较高的力学性能等优点。
主要用途:无扭控冷、热轧盘条尺寸精度分A、B、C三级。
A、B、C级精度适用于拉丝、建筑、包装和焊条等用途,B、C级精度适用于加工成螺栓、螺丝和螺母等。
3.优质碳素钢盘条(GB4354-84),优质碳素钢盘条是用优质碳素结构钢轧制而成。
是线材品种中用量较大的品种之一。
主要用途:优质碳素钢盘条主要用于加工制造碳素弹簧钢丝、油淬火回火碳素弹簧钢丝、预应力钢丝、高强度优质碳素结构钢丝、镀锌钢丝、镀锌绞线钢丝绳等。
4.优质碳素钢无扭控冷、热轧盘条(ZBH44002-88),优质碳素钢无扭控冷、热轧盘条由无扭高速线材轧机轧制而成,轧制后采取控制冷却处理。
与优质碳素钢盘条相比,具有尺寸精度高、表面质量好,有较高的力学性能。
主要用途:主要用途与优质碳素钢盘条相同。
常用于制造碳素弹簧钢丝、油淬火回火碳弹簧钢丝、预应力钢丝、优质碳素结构钢丝,镀锌钢丝等。
5.制绳钢丝用盘条(YB349-64),制绳钢丝用盘条是优质碳素结构钢热轧圆盘条之一。
主要用途:制绳钢丝用盘条可用35、40、45、55、60、65、70、75、80和85钢号的优质碳素结构钢制造。
线材质量常见五大问题及措施.doc
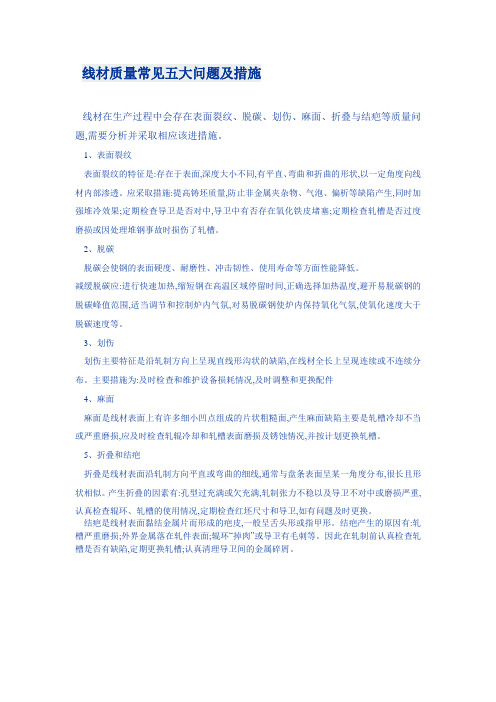
线材质量常见五大问题及措施线材在生产过程中会存在表面裂纹、脱碳、划伤、麻面、折叠与结疤等质量问题,需要分析并采取相应该进措施。
1、表面裂纹表面裂纹的特征是:存在于表面,深度大小不同,有平直、弯曲和折曲的形状,以一定角度向线材内部渗透。
应采取措施:提高铸坯质量,防止非金属夹杂物、气泡、偏析等缺陷产生,同时加强堆冷效果;定期检查导卫是否对中,导卫中有否存在氧化铁皮堵塞;定期检查轧槽是否过度磨损或因处理堆钢事故时损伤了轧槽。
2、脱碳脱碳会使钢的表面硬度、耐磨性、冲击韧性、使用寿命等方面性能降低。
减缓脱碳应:进行快速加热,缩短钢在高温区域停留时间,正确选择加热温度,避开易脱碳钢的脱碳峰值范围,适当调节和控制炉内气氛,对易脱碳钢使炉内保持氧化气氛,使氧化速度大于脱碳速度等。
3、划伤划伤主要特征是沿轧制方向上呈现直线形沟状的缺陷,在线材全长上呈现连续或不连续分布。
主要措施为:及时检查和维护设备损耗情况,及时调整和更换配件4、麻面麻面是线材表面上有许多细小凹点组成的片状粗糙面,产生麻面缺陷主要是轧槽冷却不当或严重磨损,应及时检查轧辊冷却和轧槽表面磨损及锈蚀情况,并按计划更换轧槽。
5、折叠和结疤折叠是线材表面沿轧制方向平直或弯曲的细线,通常与盘条表面呈某一角度分布,很长且形状相似。
产生折叠的因素有:孔型过充满或欠充满,轧制张力不稳以及导卫不对中或磨损严重,认真检查辊环、轧槽的使用情况,定期检查红坯尺寸和导卫,如有问题及时更换。
结疤是线材表面黏结金属片而形成的疤皮,一般呈舌头形或指甲形。
结疤产生的原因有:轧槽严重磨损;外界金属落在轧件表面;辊环“掉肉”或导卫有毛刺等。
因此在轧制前认真检查轧槽是否有缺陷,定期更换轧槽;认真清理导卫间的金属碎屑。
钢材质量常见问题及其防治措施
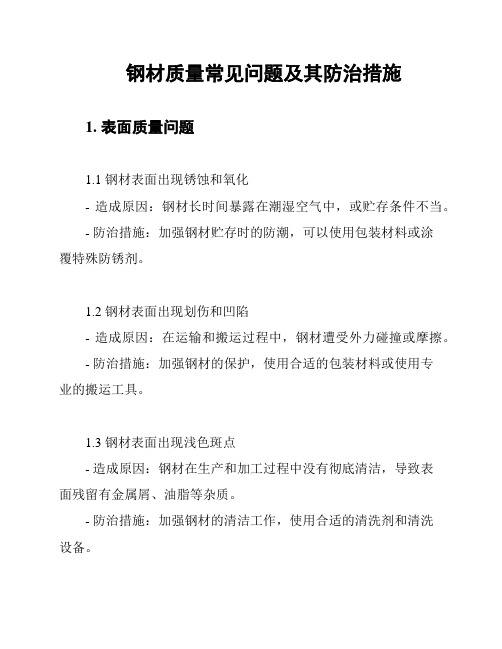
钢材质量常见问题及其防治措施1. 表面质量问题1.1 钢材表面出现锈蚀和氧化- 造成原因:钢材长时间暴露在潮湿空气中,或贮存条件不当。
- 防治措施:加强钢材贮存时的防潮,可以使用包装材料或涂覆特殊防锈剂。
1.2 钢材表面出现划伤和凹陷- 造成原因:在运输和搬运过程中,钢材遭受外力碰撞或摩擦。
- 防治措施:加强钢材的保护,使用合适的包装材料或使用专业的搬运工具。
1.3 钢材表面出现浅色斑点- 造成原因:钢材在生产和加工过程中没有彻底清洁,导致表面残留有金属屑、油脂等杂质。
- 防治措施:加强钢材的清洁工作,使用合适的清洗剂和清洗设备。
2. 钢材尺寸问题2.1 钢材出现尺寸偏差- 造成原因:钢材生产和加工过程中设备不准确或操作不当。
- 防治措施:提高设备精度,加强操作者培训,确保生产和加工过程的准确性。
2.2 钢材尺寸不均匀- 造成原因:钢材生产过程中温度、压力等控制不当。
- 防治措施:加强生产过程中的温度和压力控制,确保钢材的尺寸均匀性。
2.3 钢材出现弯曲或变形- 造成原因:钢材在贮存、运输等过程中承受外力,或生产过程中冷却不均匀。
- 防治措施:加强钢材的保护和包装,控制生产过程中的冷却速度,避免钢材受到外力影响。
3. 钢材化学成分问题3.1 钢材化学成分不合格- 造成原因:原材料不合格或生产过程中控制不当。
- 防治措施:确保原材料的质量,加强生产过程中的化学成分控制和检测。
3.2 钢材含杂质过多- 造成原因:生产过程中杂质的混入或设备不洁净。
- 防治措施:加强生产过程中的杂质控制和设备清洁工作,确保钢材纯净性。
3.3 钢材硬度不达标- 造成原因:生产过程中热处理不当或冷却速度不均匀。
- 防治措施:加强生产过程中的热处理控制,确保钢材的硬度符合要求。
以上是钢材质量常见问题及其防治措施的简要介绍,希望对您有所帮助。
钢材常见五个问题
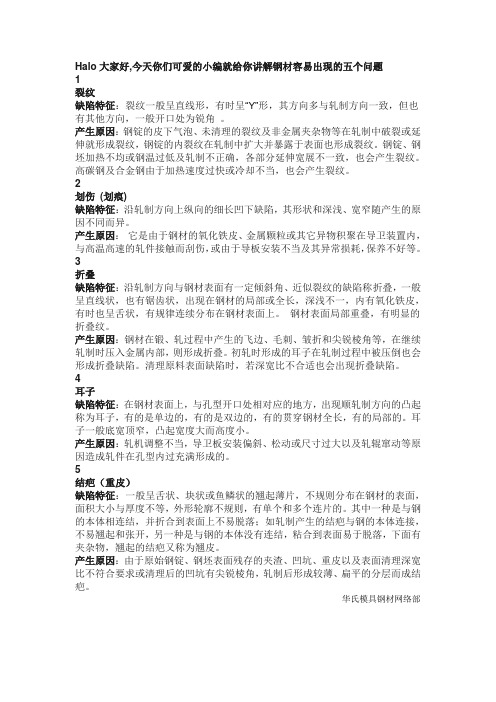
Halo大家好,今天你们可爱的小编就给你讲解钢材容易出现的五个问题1裂纹缺陷特征:裂纹一般呈直线形,有时呈“Y”形,其方向多与轧制方向一致,但也有其他方向,一般开口处为锐角。
产生原因:钢锭的皮下气泡、未清理的裂纹及非金属夹杂物等在轧制中破裂或延伸就形成裂纹,钢锭的内裂纹在轧制中扩大并暴露于表面也形成裂纹。
钢锭、钢坯加热不均或钢温过低及轧制不正确,各部分延伸宽展不一致,也会产生裂纹。
高碳钢及合金钢由于加热速度过快或冷却不当,也会产生裂纹。
2划伤(划痕)缺陷特征:沿轧制方向上纵向的细长凹下缺陷,其形状和深浅、宽窄随产生的原因不同而异。
产生原因:它是由于钢材的氧化铁皮、金属颗粒或其它异物积聚在导卫装置内,与高温高速的轧件接触而刮伤,或由于导板安装不当及其异常损耗,保养不好等。
3折叠缺陷特征:沿轧制方向与钢材表面有一定倾斜角、近似裂纹的缺陷称折叠,一般呈直线状,也有锯齿状,出现在钢材的局部或全长,深浅不一,内有氧化铁皮,有时也呈舌状,有规律连续分布在钢材表面上。
钢材表面局部重叠,有明显的折叠纹。
产生原因:钢材在锻、轧过程中产生的飞边、毛刺、皱折和尖锐棱角等,在继续轧制时压入金属内部,则形成折叠。
初轧时形成的耳子在轧制过程中被压倒也会形成折叠缺陷。
清理原料表面缺陷时,若深宽比不合适也会出现折叠缺陷。
4耳子缺陷特征:在钢材表面上,与孔型开口处相对应的地方,出现顺轧制方向的凸起称为耳子,有的是单边的,有的是双边的,有的贯穿钢材全长,有的局部的。
耳子一般底宽顶窄,凸起宽度大而高度小。
产生原因:轧机调整不当,导卫板安装偏斜、松动或尺寸过大以及轧辊窜动等原因造成轧件在孔型内过充满形成的。
5结疤(重皮)缺陷特征:一般呈舌状、块状或鱼鳞状的翘起薄片,不规则分布在钢材的表面,面积大小与厚度不等,外形轮廓不规则,有单个和多个连片的。
其中一种是与钢的本体相连结,并折合到表面上不易脱落;如轧制产生的结疤与钢的本体连接,不易翘起和张开,另一种是与钢的本体没有连结,粘合到表面易于脱落,下面有夹杂物,翘起的结疤又称为翘皮。
线材常见缺陷
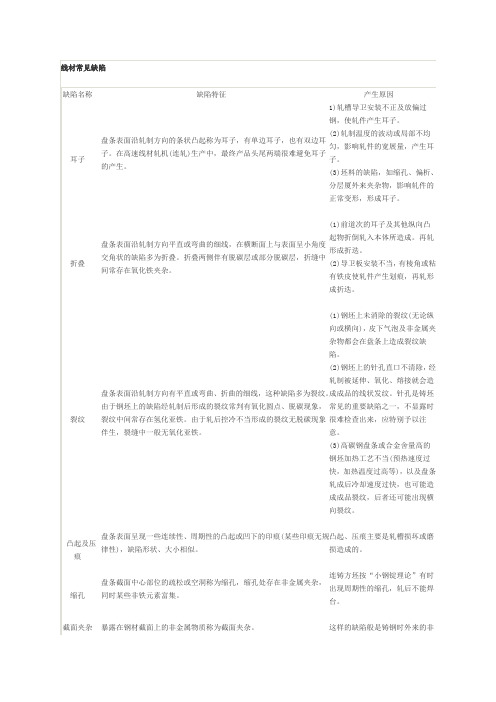
"OkZ
[E)
缺陷名称@Z_V>Cl@%2
缺陷特征aGE} EK_}
产生原因_t_LdQO"_
耳子[fkt3_fS__
盘条表面沿轧制方向的条状凸起称为耳子,有单边耳子,也有双边耳子。在高速线材轧机(连轧)生产中,最终产品头尾两端很难避免耳子的产生。B_4m34)EOE
9Rg|oCP__
Nlc3S_lt;__1=;_%
(2)轧制温度的波动或局部不均匀,影响轧件的宽展量,产生耳子。___Ac_ +fL
(3)坯料的缺陷,如缩孔、偏析、分层厦外来夹杂物,影响轧件的正常变形,形成耳子。*t_Dxw_D7_
"__#%9dWy_
折叠%I_UTi6P l
'`
(2)钢坯上的针孔直口不清除,经轧制被延伸、氧化、熔接就会造成成品的线状发纹。针孔是铸坯常见的重要缺陷之一,不显露时很难检查出来,应特别予以注意。{ daEKac_5
(3)高碳钢盘条或合金舍量高的钢坯加热工艺不当(预热速度过快,加热温度过高等),以及盘条轧成后冷却速度过快,也可能造成成品裂纹,后者还可能出现横向裂纹。<_a$'t_w-8
3Qo_
_a ?*
凸起及压痕^ )_[j_BUT
盘条表面呈现一些连续性、周期性的凸起或凹下的印痕(某些印痕无规律性),缺陷形状、大小相似。u_gMf p_T)
lG_!W__e'?
凸起、压痕主要是轧槽损坏或磨损造成的。dQH9N_sV7g
;ch_z};zY_
缩孔9_Fv V
M9_
盘条截面中心部位的疏松或空洞称为缩孔,缩孔处存在非金属夹杂,同时某些非铁元素富集。o+T %n1$+V
钢材常见质量问题
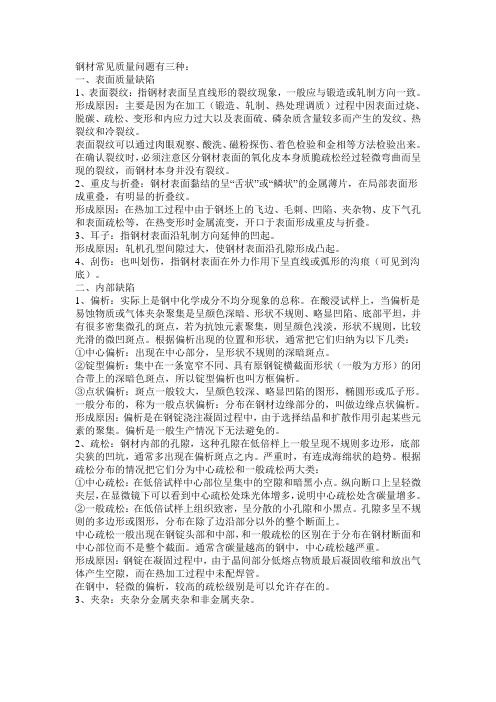
钢材常见质量问题有三种:一、表面质量缺陷1、表面裂纹:指钢材表面呈直线形的裂纹现象,一般应与锻造或轧制方向一致。
形成原因:主要是因为在加工(锻造、轧制、热处理调质)过程中因表面过烧、脱碳、疏松、变形和内应力过大以及表面硫、磷杂质含量较多而产生的发纹、热裂纹和冷裂纹。
表面裂纹可以通过肉眼观察、酸洗、磁粉探伤、着色检验和金相等方法检验出来。
在确认裂纹时,必须注意区分钢材表面的氧化皮本身质脆疏松经过轻微弯曲而呈现的裂纹,而钢材本身并没有裂纹。
2、重皮与折叠:钢材表面黏结的呈“舌状”或“鳞状”的金属薄片,在局部表面形成重叠,有明显的折叠纹。
形成原因:在热加工过程中由于钢坯上的飞边、毛刺、凹陷、夹杂物、皮下气孔和表面疏松等,在热变形时金属流变,开口于表面形成重皮与折叠。
3、耳子:指钢材表面沿轧制方向延伸的凹起。
形成原因:轧机孔型间隙过大,使钢材表面沿孔隙形成凸起。
4、刮伤:也叫划伤,指钢材表面在外力作用下呈直线或弧形的沟痕(可见到沟底)。
二、内部缺陷1、偏析:实际上是钢中化学成分不均分现象的总称。
在酸浸试样上,当偏析是易蚀物质或气体夹杂聚集是呈颜色深暗、形状不规则、略显凹陷、底部平坦,并有很多密集微孔的斑点,若为抗蚀元素聚集,则呈颜色浅淡,形状不规则,比较光滑的微凹斑点。
根据偏析出现的位置和形状,通常把它们归纳为以下几类:①中心偏析:出现在中心部分,呈形状不规则的深暗斑点。
②锭型偏析:集中在一条宽窄不同、具有原钢锭横截面形状(一般为方形)的闭合带上的深暗色斑点,所以锭型偏析也叫方框偏析。
③点状偏析:斑点一般较大,呈颜色较深、略显凹陷的图形,椭圆形或瓜子形。
一般分布的,称为一般点状偏析:分布在钢材边缘部分的,叫做边缘点状偏析。
形成原因:偏析是在钢锭浇注凝固过程中,由于选择结晶和扩散作用引起某些元素的聚集。
偏析是一般生产情况下无法避免的。
2、疏松:钢材内部的孔隙,这种孔隙在低倍样上一般呈现不规则多边形,底部尖狭的凹坑,通常多出现在偏析斑点之内。
不同合金元素对合金钢线材的耐磨性能的影响

不同合金元素对合金钢线材的耐磨性能的影响合金钢是一种添加了合金元素的钢材,它通过改变合金元素的类型和含量来调整钢的性能,使得钢材具有更高的强度、硬度和耐磨性能。
钢材的耐磨性能是指材料在摩擦和磨损作用下的耐久能力,对于一些需要承受高摩擦和磨损的场合,如机械零件、工具和设备等,耐磨性能是至关重要的。
不同合金元素对合金钢线材的耐磨性能具有不同的影响,下面将分析几种常见的合金元素对耐磨性能的影响。
首先,铬元素对合金钢的耐磨性能有着重要影响。
铬是一种重要的合金元素,它能够增加钢材的硬度和耐腐蚀性能,并且形成一种紧密的氧化物表面层,从而提高钢材的抗磨损性能。
研究表明,当合金钢中铬的含量达到一定比例时,钢材的硬度和耐磨性能都会显著提高。
因此,在生产合金钢线材时,适当增加铬元素的含量可以有效提高钢材的耐磨性能。
其次,钼元素也是常用的合金元素之一,它对合金钢的耐磨性能有着重要的影响。
钼能够增加钢材的韧性和抗磨损性能,特别是在高温和高压环境下,其抗磨损性能更为突出。
研究发现,适量添加钼元素可以显著提高合金钢的耐磨性能,尤其是在润滑条件较差的情况下,耐磨性能的提高更为显著。
因此,在生产合金钢线材时,适量添加钼元素是提高钢材耐磨性能的有效手段。
另外,钛元素也可以对合金钢的耐磨性能产生影响。
钛具有强化钢材的效果,可以提高合金钢的硬度和磨损阻力,从而改善耐磨性能。
此外,钛还能抑制晶界腐蚀和晶界松弛,提高钢材的综合性能。
因此,在生产合金钢线材时,适量添加钛元素可以改善钢材的耐磨性能。
此外,还有一些其他的合金元素也会对合金钢的耐磨性能产生一定的影响。
例如,钼、钴、锰等元素都具有一定的强化和抗磨损效果,可以提高钢材的耐磨性能。
然而,不同的合金元素对钢材的耐磨性能影响程度和方式各不相同,并且与其他因素(如碳含量、热处理工艺等)之间相互作用。
因此,在实际应用中,需要根据具体的使用环境和要求,选择合适的合金元素和配比,以实现最佳的耐磨性能。
不同合金元素对合金钢线材性能的影响研究

不同合金元素对合金钢线材性能的影响研究摘要:合金钢线材广泛应用于各个行业,在不同的工况下需要具备不同的性能。
本研究旨在探讨不同合金元素对合金钢线材的性能影响,并通过实验和分析来评估其性能变化。
实验结果表明,合金元素的添加可以显著改善合金钢线材的力学性能、耐磨性和耐腐蚀性。
根据实验数据,我们进一步分析了各种合金元素对合金钢线材性能的影响机制,并提出了一些最佳合金配方的建议。
1. 引言合金钢线材作为一种重要的材料,其性能对于各行业的应用至关重要。
合金元素的添加能够调节线材的宏观性能,包括强度、韧性、硬度、耐磨性和耐腐蚀性等。
因此,研究不同合金元素对合金钢线材性能的影响具有重要的工程意义。
2. 实验方法我们选取了五种常见的合金元素,分别为铬、钼、镍、锰和钛,通过添加不同比例的这些合金元素制备了一系列合金钢线材样品。
然后,进行了一系列力学性能和耐腐蚀性实验,包括拉伸强度测试、硬度测试、冲击韧性测试、耐磨性测试和腐蚀实验等。
实验数据通过统计学方法进行分析和比较。
3. 结果与讨论3.1 力学性能实验结果显示,添加铬、钼、镍、锰和钛等合金元素可以显著提高合金钢线材的拉伸强度和硬度。
其中,添加钢中含钼量的合金元素相较于其他元素添加更显著地提高了钢丝材料的强度和硬度,而添加含镍合金元素则显著提高了钢丝材料的韧性。
3.2 耐磨性合金钢线材的耐磨性能对于一些具有磨损性工况的应用尤为重要。
实验结果显示,添加铬和钼等合金元素可以显著提高合金钢线材的耐磨性能。
其中,铬元素添加比例的增加使得合金钢线材的耐磨性能逐渐提高,而添加含钼的合金元素可以进一步增强钢丝材料的耐磨性。
3.3 耐腐蚀性耐腐蚀性是合金钢线材在腐蚀介质中保持稳定性的重要性能。
实验结果表明,添加镍和钛等合金元素可以显著提高合金钢线材的耐腐蚀性能。
特别是添加含钛的合金元素,可以明显增加钢丝材料在腐蚀介质中的抗腐蚀能力。
4. 影响机制分析根据实验结果,我们推测不同合金元素对合金钢线材性能的影响机制可能是由于其对钢材晶界强化、晶粒细化和相变的影响。
合金钢线材的热导率与电导率测试与分析

合金钢线材的热导率与电导率测试与分析在材料科学领域,热导率和电导率是两个重要的物理性质参数,用于描述材料的导热和导电性能。
对于合金钢线材这样的材料,热导率和电导率的测试与分析对于材料的应用和工程设计具有重要意义。
本文将讨论如何进行合金钢线材的热导率和电导率测试,并对测试结果进行分析。
首先,我们来讨论合金钢线材热导率的测试与分析方法。
热导率是一个描述材料导热性能的量,可以通过热传导实验来测试。
常用的热传导实验方法有热板法和热流法。
热板法是一种常用的测量材料热导率的方法。
该方法通过在待测样品上加热,并测量样品两侧的温度差来计算热传导梯度,从而得到材料的热导率。
在合金钢线材的测试中,我们可以将待测样品固定在两块热板之间,其中一块为加热板,另一块为冷却板。
通过控制加热板的温度和测量两侧的温度差,可以得到合金钢线材的热导率。
另一种常用的热传导实验方法是热流法。
热流法通过在待测样品表面施加一定的热流,通过测量样品各点的温度来计算材料的热导率。
在合金钢线材的测试中,我们可以通过使用热源和热传感器进行测量。
通过控制热源的功率和测量样品各点的温度差,可以得到合金钢线材的热导率。
对于合金钢线材的电导率测试与分析,电导率是一个描述材料导电性能的量,常用的测试方法有四探针法和霍尔效应法。
四探针法是一种常用的测量材料电导率的方法。
该方法通过在待测样品上施加电流,并测量样品上的电压差来计算电阻,从而得到材料的电导率。
在合金钢线材的测试中,我们可以将待测样品夹持在四个电极之间,通过施加一定的电流并测量电压差,计算出合金钢线材的电导率。
霍尔效应法是另一种常用的测量材料电导率的方法。
该方法通过在待测样品上施加磁场,并测量垂直于电流方向的霍尔电压来计算电阻和电导率。
在合金钢线材的测试中,我们可以通过施加磁场并测量霍尔电压,得到合金钢线材的电导率。
对于合金钢线材热导率和电导率的测试结果,我们还需要进行一定的分析。
首先,需要考虑合金钢线材的成分和结构对热导率和电导率的影响。
不同合金元素对合金钢线材的高温蠕变行为的影响

不同合金元素对合金钢线材的高温蠕变行为的影响引言高温下材料的蠕变行为是材料工程中重要的研究领域之一。
合金钢线材作为一种重要的结构材料,在高温环境下必须具备良好的耐久性和稳定性。
因此,了解不同合金元素对合金钢线材高温蠕变行为的影响至关重要。
本文将探讨不同合金元素,如铬、钼、钛和铌对合金钢线材高温蠕变行为的影响。
铬对合金钢线材的高温蠕变行为的影响铬是合金钢中常见的合金元素之一。
它能够提高合金钢的抗蠕变性能。
铬的添加可以通过形成稳定的氧化膜来保护合金钢线材表面,减少氧的渗透,降低了蠕变速率。
此外,铬还可以通过形成固溶强化的效应来增加材料的强度和硬度,从而提高材料的抗蠕变能力。
钼对合金钢线材的高温蠕变行为的影响钼是另一个常见的合金元素,对合金钢线材的高温蠕变行为也有重要影响。
钼的加入可以提高合金钢的高温强度和耐热性。
通过形成稳定的碳化物相,钼可以有效阻止晶粒的生长,从而提高材料的织构和晶界的稳定性。
此外,钼还能够减少晶界的扩散,降低晶界滑移速率,从而降低了合金钢的蠕变速率。
钛对合金钢线材的高温蠕变行为的影响钛是一种轻质强度高的合金元素,其添加对合金钢线材的高温蠕变行为有显著影响。
钛的加入可以有效地改善合金钢的高温强度和韧性。
钛能够与氮形成稳定的氮化物相,使晶粒得以细化,提高材料的晶界强化效应。
此外,钛还能够降低合金钢的晶界扩散速率,减缓材料的蠕变速率。
铌对合金钢线材的高温蠕变行为的影响铌是一种常见的稀有金属元素,在合金钢线材中的应用也比较广泛。
铌的加入可以显著改善合金钢的高温蠕变行为。
铌能够通过形成固溶强化的效应,有效提高合金钢的强度和硬度。
此外,铌还可以促进合金钢的析出强化相的形成,提高其抗蠕变能力。
铌还能够抑制晶粒生长,细化合金钢的晶粒,从而提高材料的高温性能。
结论综上所述,不同合金元素对合金钢线材的高温蠕变行为有着显著的影响。
铬的添加可以提高合金钢的抗蠕变性能,钼可以提高高温强度和耐热性,钛能够改善高温强度和韧性,铌可以显著改善高温蠕变行为。
合金钢线材的磁响应行为与磁控制性能研究

合金钢线材的磁响应行为与磁控制性能研究引言合金钢线材作为一种重要的工程材料,在许多领域应用广泛,具有优异的物理和化学性能。
磁性是合金钢线材的一个重要特性,而磁响应行为和磁控制性能是了解和优化该材料性质的关键。
本文通过研究合金钢线材的磁响应行为和磁控制性能,旨在深入了解该材料的磁性质,为合金钢线材的制备和应用提供理论依据和实验指导。
磁响应行为的研究磁响应行为是合金钢线材磁性质的重要特征之一。
磁性是物质对磁场的响应能力,可以通过测量合金钢线材的磁化曲线来研究其磁响应行为。
常用的磁化曲线包括磁化强度-磁场强度曲线和剩余磁化强度-磁场强度曲线。
通过实验测量得到的磁化强度-磁场强度曲线可以描述合金钢线材的磁性能,如饱和磁化强度、矫顽力和剩余磁化强度等。
通过研究这些磁响应参数,可以了解合金钢线材的磁性质和性能。
磁控制性能的研究磁控制性能是合金钢线材的另一个重要特征,与磁响应行为密切相关。
磁控制性能主要包括磁致伸缩效应和磁阻效应。
磁致伸缩效应是指在外加磁场作用下,合金钢线材的长度发生变化的现象。
通过测量合金钢线材在不同磁场强度下的长度变化,可以研究其磁致伸缩效应。
磁致伸缩效应的大小与合金钢线材的微观结构和磁性有关。
磁阻效应是指合金钢线材在外加磁场作用下,电阻发生变化的现象。
该效应可以通过测量合金钢线材在不同磁场强度下的电阻变化来研究。
磁阻效应广泛应用于传感器和磁控制器件中,研究合金钢线材的磁阻效应有助于优化其设计和性能。
磁控制性能与微观结构的关系合金钢线材的微观结构对其磁控制性能起着重要的影响。
晶体结构、晶粒大小和晶界特征是影响合金钢线材磁性质的关键因素。
晶体结构的研究可以通过X射线衍射等手段进行,了解合金钢线材的晶格参数和晶胞结构。
晶体结构中存在的缺陷和位错对磁性能的影响也是重要的研究内容之一。
晶粒大小是另一个影响磁性能的重要因素。
晶粒尺寸的减小可以提高合金钢线材的磁响应行为和磁控制性能。
晶粒细化技术, 如等通道转角挤压(ECAP)等,可以有效地控制晶粒尺寸和分布。
合金钢线材的氧化皮去除

合金钢线材的氧化皮去除合金钢线材是一种高强度材料,主要用于机械、建筑、电力等领域。
然而,在使用过程中,合金钢线材表面容易形成氧化皮,影响其使用寿命和表面质量。
因此,去除氧化皮是保证合金钢线材质量的重要工序。
本文将介绍一些常见的氧化皮去除方法。
1. 机械抛光法机械抛光法是最传统的氧化皮去除方法之一。
它使用机械力量来切削合金钢线材表面的氧化皮。
这种方法通常使用砂轮、砂布或其他磨料,在旋转的工件上施加压力,以去除氧化皮。
然而,这种方法存在一些缺点。
首先,它需要大量的能源和时间。
其次,机械抛光法容易导致表面形状粗糙和大小不一的划痕,影响合金钢线材的表面质量。
因此,在其他方法可行时,机械抛光法并不是最佳选择。
2. 电解去氧法电解去氧法是一种通过电化学反应去除氧化皮的方法。
该方法涉及使用一个电解槽,并将合金钢线材作为阳极,将电流通过电解槽,并使用腐蚀性液体来溶解氧化皮。
根据溶液的不同,电解去氧法可以分为酸洗法和碱洗法。
酸洗法通常使用盐酸或硫酸溶液,而碱洗法则使用氢氧化钠或氢氧化钾溶液。
在电解去氧法中,盐酸和硫酸溶液更常用,因为它们具有更高的腐蚀性,可以更有效地去除氧化皮。
然而,电解去氧法也存在一些缺点。
首先,它需要大量的能源和设备。
其次,处理过程需要注意安全问题,因为这些液体都具有腐蚀性。
此外,在一些情况下,氧化皮可能会对钢材表面产生微小的凸起,这可能会在处理过程中产生空气泡,并危及工人的安全。
3. 酸洗法酸洗法是一种使用化学酸溶解合金钢线材表面氧化皮的方法。
虽然这种方法比较简单方便,但在实际应用过程中,需要考虑酸洗液的成分、浓度、浸泡时间等因素,以确保去氧效果和处理质量。
常用的酸洗液是盐酸或硫酸,其浓度和浸泡时间需要根据不同的需求进行调整。
但是,酸洗法也有一定的局限性。
首先,酸洗液具有腐蚀性,需要非常小心使用。
其次,酸洗法对于较深层次的氧化皮去除效果不佳。
此外,酸洗液的使用也会对环境造成一定的污染。
4. 其他方法还有许多其他去除合金钢线材氧化皮的方法,例如激光去氧法、气体热镀法、化学水净化法等。
合金钢特点问题回答

合金钢特点合金钢是一种具有优异性能的钢材,其主要特点包括高强度、高耐磨性、高耐腐蚀性、高温强度和良好的可焊性等。
在工业生产中,合金钢已经成为不可或缺的材料之一,广泛应用于航空航天、汽车制造、建筑工程等领域。
一、高强度合金钢由于添加了多种金属元素,使其晶体结构更加致密,同时也增加了其硬度和强度。
因此,在相同重量下,合金钢的承载能力比普通钢更大。
这也是为什么在制造机械设备和工程结构时会选择使用合金钢的原因之一。
二、高耐磨性由于合金钢中添加了铬等耐蚀元素,使其表面形成了一层坚固的氧化物保护层,从而提高了其抗氧化能力和抗腐蚀能力。
同时,在摩擦磨损方面也表现出较好的性能,因此在制造机械零件和切削工具时经常会选择使用合金钢。
三、高耐腐蚀性合金钢中添加的铬等元素可以使其表面形成一层坚固的氧化物保护层,从而提高了其抗氧化能力和抗腐蚀能力。
此外,合金钢还可以通过调整合金元素的配比来改变其耐腐蚀性能,从而满足不同环境下的使用需求。
四、高温强度合金钢中添加了多种金属元素,使其晶体结构更加致密,同时也增加了其硬度和强度。
这些特性使得合金钢在高温环境下仍然具有较好的强度和耐久性。
因此,在制造高温设备和工程结构时经常会选择使用合金钢。
五、良好的可焊性由于合金钢中添加了多种元素,所以在焊接过程中需要选择适当的焊接材料和方法。
但总体来说,相对于其他高强度材料而言,合金钢具有较好的可焊性。
这也是为什么在制造大型机械设备时经常会选择使用合金钢的原因之一。
六、小结综上所述,合金钢具有高强度、高耐磨性、高耐腐蚀性、高温强度和良好的可焊性等特点。
这些特性使得合金钢在航空航天、汽车制造、建筑工程等领域中广泛应用,并成为不可或缺的材料之一。
同时,由于合金钢中添加的元素种类和配比不同,其性能也会有所差异,因此在使用时需要根据具体情况进行选择。
- 1、下载文档前请自行甄别文档内容的完整性,平台不提供额外的编辑、内容补充、找答案等附加服务。
- 2、"仅部分预览"的文档,不可在线预览部分如存在完整性等问题,可反馈申请退款(可完整预览的文档不适用该条件!)。
- 3、如文档侵犯您的权益,请联系客服反馈,我们会尽快为您处理(人工客服工作时间:9:00-18:30)。
1、SCM435 16.0mm——13.0mm无磷化线材减面率较大,线材划伤严重,抽制不了。
2、改制线两次合粗抽、无磷化线材易划伤,生产时需放慢速度,勤检查
3、Ca系拔丝粉润滑性较好,油脂性好,皮膜好,但拉拔后线材表面白粉较多;Na系润滑性较差,但拉拔后线材表面白粉较少
4、333和515拔丝粉的区别:333拔丝粉润滑性好,挂粉较多;515润滑性少差,线材表面粉少。
5、18AΦ16.0——11.4——11.0使用合金钢一号机可以抽(较为勉强),期间断裂过,刚出眼模时线径缩小0.01mm,冷却后缩小0.03mm,后续生产过程中需要注意缩颈,拉拔时尽量使用上限眼模,眼模的角度要较大。
6、对于成品减面率小的线材,球化出现的弯线不能够将之修复,会在线材上出现细小的弯曲现象,客户使用时会造成卡机等现象。
7、对于线材硬度要求不严格的线材,硬度高在客户使用时会造成额外的模具损失,从而成本耗费较高(特别是富奥客户)。
8、新光凯乐10A40.0mm—36.2mm,生产母线时,使用眼模36.2mm,线材刚引出眼模时尺寸为36.15-36.16mm,冷却后线材尺寸为36.03-36.04mm。
技术方面母线尺寸没有较大影响,建议工令排产为36.0(+0.2)mm。
9、新光凯乐10AΦ36.2——35.0(-0.06mm)时,眼模为34.98,刚出眼模线径为34.96mm,盘圈后线径变为34.91—31.92mm;眼模为35.0时,刚出眼模线径为34.98—34.99mm,盘圈后线径变为34.93—34.94mm。
10、新光凯乐10A线材,成品规格为29.5mm,母线规格为29.75mm,首次生产使用34.0mm盘条,减面率为24.72%,使用30.0mm眼模,线材缩丝0.25mm,刚好到达母线规格。
11、新光凯乐10A线材改制线29.5-25.35线材(未改制盘元线材规格应为30.0mm),使用眼模规格为25.42,线材刚出眼模时规格为25.40-25.41,盘卷后冷却测量规格为25.32-25.33,减面率为26.16%,线材缩丝0.08mm左右,成品规格为24.6mm,母线线材刚开始生产时线径缩丝0.07mm,中间部位为0.03-0.05mm左右,后续生产眼模时需注意眼模规格,建议眼模规格为25.42-25.44mm。
12、10A线材32.0—27.10mm,减面率为28.28%,使用27.20mm眼模,线材刚出线筒时,线径为27.18-27.21mm,自线筒盘下后线径变化为27.13-27.14mm。
线材缩丝0.07mm,后续生产眼模使用时建议参考,生产成品时使用眼模尺寸为26.30mm上限眼模,线材盘下后线径表现为26.26mm。
13、含Cr的钢(合金钢车间)在球化时Cr会逐渐的向边缘靠近,在钢中Cr和C的结合能力远远大于Fe和C的结合能力,一个Cr会和二十多个C结合,所以线材中铬含量较高时边缘会出现大量黑色碳化铬;在酸洗披覆时,铬不与酸反应(不锈钢),酸会洗掉钢中的铁基。
磷化膜主要是磷酸铁和磷酸锌等化合物,磷酸盐同样不与铬反应,导致线材表面的磷化不均匀,披覆皂化后会在线材表面产生青色等非常规的磷化膜颜色,线材经过拉拔后就会呈现出非正常的颜色。
14、为防止成品线材出现划伤,成品线材减面率超过0.15mm使用515系拔丝粉(实验)
15、大韩18A26.10-25.50样品线材,抽制成品时使用模具为25.48mm,线材实际线径25.42-25.43,第二次使用模具为25.51mm,线材实际线径为
25.49-25.50mm,自线筒盘下后线材尺寸为25.47-25.48mm。
16、合金钢成品线材前期频繁出现划伤现象,划伤源头处有黑色斑迹,曾初步认为是(1)、酸洗表面冲洗不干净,线材表面存在有黑色颗粒状四氧化三铁,披覆后在拉拔时产生划伤;(2)、酸洗披覆线材表面有异物,皂化池或者磷化池中有杂质附在线材表面,后在拉拔中进入眼模中,在眼模中积累过多造成划伤;(3)、酸洗披覆过薄,表面磷化膜、皂化膜较为稀薄,生产时由于存在减面率不同造成磷化膜、皂化膜破损产生划伤(后续生产中加厚磷化皂化膜对划伤有所减少,且效果明显,已经经过生产证明,但是线材表面白粉较多)
17、合金钢35K线材,盘元尺寸28.0,生产母线尺寸23.5,工艺要求用两次拉拔,首次为26.0,第二次为23.5。
尝试利用一次拉拔进行生产,减面率为29.56%,利用23.57Mm眼模,线材最后线径为23.54-23.55,缩丝0.04mm,后续生产此类线材建议眼模公差为0.04mm,即眼模尺寸为23.54-23.58mm。
18、新光凯乐10A线材34-30.3-29.5,前期为34—29.75—29.5客户反映线材较软,后更改工艺。
生产时由于30.3眼模只有一个,母线尺寸略微胀大,几乎达到30.4mm,生产成品时首次使用眼模29.51mm,线材盘下后缩丝0.03mm,线径尺寸为29.48mm,生产2T后眼模到上限尺寸;后使用29.48mm眼模,线材盘下后缩丝0.03mm,尺寸为29.45.后续生产建议眼模尺寸为29.48mm。
19、新光凯乐10A线材38.0—32.56,使用32.63眼模,线材刚出眼模时线径尺寸为32.63mm,正常生产过程中线径尺寸变化为32.65mm,线材盘下后线径尺寸为32.55,Mm,开头部分为32.53mm
20、合金钢组:14的盘元可以抽到11.95mm,无论什么材质减面率27%。
刘桂炳:45K球化后,10mm以上的减面率为35-40%
赵树林:SCM435、ML40CR:酸洗披覆后(不球化)一次拉拔20%左右,15以下20%,15以上低于20%,拉不动,眼膜也不行,热量大易划伤,有水也不行。
不球化就能拉一次。
SCM435、ML40CR(软化盘元)一次拉拔30-35%,ML40CR 28的能抽到25点多,减面率20%,再大就拉不动,球化后可拉两次。
赵树林与合金钢组长:ML40CR23mm盘条(不软化)可抽到19.8,减面率25.8%,赵树林说不好抽,组长说到极限了。
35K、ML35、45K、38K、10B21、10B30:酸洗披覆后最大一次拉拔40%,34抽到32,减面率11%,再大拉不动。
可拉多次。