厦门特士勒超探说明书
OPTEX HX-40RAM高地外围探测器说明书

N2191-1 BEFORE YOUR OPERATION 11-2 PARTS IDENTIFICATION 222-1 TRANSMITTER PREPARATION 32-2 BATTERY PREPARATION 4DETERMING THE DETECTION LENGTH53-2 MOUNTING THE BATTERY 53-3 MOUNTING THE TRANSMITTER AND THE BATTERY BOX 73-4 MOUNTING THE BRACKET83-5 ADJUSTING THE VERTICAL ANGLE 9101113141516INSTALLATION MANUALThe check ( ) mark indicates recommendation.The cross ( ) mark indicates prohibition.12233228014015TransmitterBattery boxBattery boxTransmitter13Remove the battery box from the mainunit.Mount batteries and put the cover ontothe right position indicated on the side ofthe battery box.Hook the cover firmly by the claws on theright and left sides.Do not contact the ends of the redand black wires to avoid short-circuit.Caution>>4Open the transmitter cover and removethe battery.battery in series.5Dummy batterybattery type.CR123ACR21/2AA1/2AA-Battery Sharing Impossible CaseArrange 3 cells each of CR-123A (recommended) or CR2.After installing the batteries, check theguide on the side and install the cover.Hook the cover firmly by the claws on theright and left sides.Do not contact the ends of the redand black wires to avoid short-circuit.Caution>>3TransmitterAlarm cablePut the alarm wire outsidethrough the wiring holeConnect the alarm cable to thetransmitter and close the cover.4Using the bracket makes it possible to adjust the unit horizontally by ± 90 degrees.In cases where the ground is uneven and therefore not parallel with the base of the unit, it is possible to adjust the unit vertically by ± 20 degree (refer to 3-5)Decide the horizontal angle, and tighten the adjustment screw clockwise.base.Complete the 3-5 “ADJUSTING THE VERTICAL ANGLE”.Remove the cover and the Main unit to tighten the up-down lock screw, and install the Main unit and cover on the base again.Fit the shaft cover into the place.7891011To have the right performance, set the vertical angle parallel to a ground.Decide the wanted detection length at first. If you choose 9.0m/5.5m/4.0m, mask the unwanted lens with masking seals. Refer to the 3-1 for the details.* This is the case to have 12 meters detection length.6Install the base on the bracket.Caution>>Do not tighten the up-down lock screw.--++R E (N o n s h o r t )A R M O U T P U T (N .O .)A R M O U T P U T (C O M )A R M O U T P U T (N .C .)W E R O U T P U T (–) (3 - 7.2V D C )W E R O U T P U T (+) (3 - 7.2V D C )W E R I N P U T (–) (3 - 7.2V D C )W E R I N P U T (+) (3 - 7.2V D C )M P E R O U T P U T (N .O .) *1M P E R O U T P U T (C O M ) *1M P E R O U T P U T (N .C .) *1O U B L E O U T P U TO U B L E O U T P U T“Trouble output” to “ Trouble output + Alarm”.HX-40RAM Main unitINPUTOUTPUTOUTPUTEven if there are continuous alarm events, the alarm is generated only once in the timer period to save the battery life.Dip switch3-IMMUNITY SWITCHTrouble signal output >>Trouble signal at regular intervals is output after trouble condition continues for a certain period.Dip switch4-TROUBLE OUTPUT TYPESelect the contact point output form with the TROUBLE OUTPUT TERMINAL.* This setting is valid only when the “TROUBLE OUTPUT TERMINAL (factory default)” is selected at Dip switch 5.OUTPUTOUTPUT +ALARMDip switch5-TROUBLE OUTPUT (T.O.) TERMINAL-ANTI-MASKING SENSITIVITYCaution >>When turning on the power, do not leave any object with 1 meter from the unit.-LED INDICATIONNOTE: To distinguish a trouble output caused by low battery power, the low battery powerLED display will light up when the cover is opened even if the LED ON/OFF (DIP-SW 6, see p13) is set to OFF.-DETECTION LENGTH ADJUSTMENTTo limit the detection length, apply the appropriate masking seal. Note that there are three different types of seal.Pasting on example for -AREA MASKING* Specifications and design are subject to change without prior notice.The HX-40 series is only a part of a complete system, we cannot accept completeresponsibility for any damages or other consequences resulting from an intrusion. Due to our policy of continuous improvement Optex reserves the right to change specification without prior notice.Unit:mm (inch)Unit:mm (inch)99(3.9)205(8.1)266(10.5)148(5.8)197.5(7.8)92(3.6)Using bracket and hoodWithout bracket and hoodAs a rough indication of battery change timing, enter the battery type and the date it was first used.Battery typeDate (Year/Month)OPTEX INCORPORATED (USA)TEL:+1-909-993-5770Tech:(800)966-7839URL:OPTEX KOREA CO., LTD. (KOREA)TEL:+82-2-719-5971URL:OPTEX SECURITY Sp.z o .o. (POLAND)TEL:+48-22-598-06-55URL:.plOPTEX (DONGGUAN) CO., LTD.SHENZHEN OFFICE (CHINA)TEL:+86-755-33302950URL:OPTEX CO., LTD. (JAPAN)(ISO 9001 Certified) (ISO 14001 Certified)5-8-12 Ogoto Otsu Shiga 520-0101JAPANTEL:+81-77-579-8670FAX:+81-77-579-8190URL:http://www.optex.co.jp/e/OPTEX (EUROPE) LTD. (UK)TEL:+44-1628-631000URL:OPTEX SECURITY SAS (FRANCE)TEL:+33-437-55-50-50URL:。
TS-FTDO2 系列湿度传感器产品使用说明书
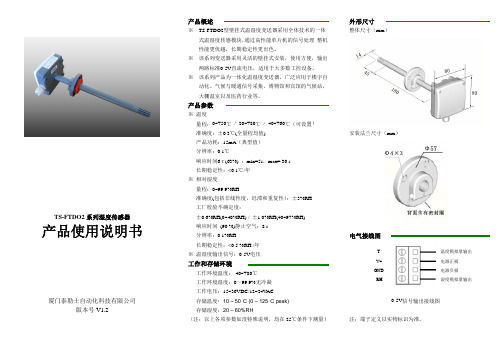
TS-FTDO2系列湿度传感器产品使用说明书厦门泰勒士自动化科技有限公司版本号V1.2产品概述※TS-FTDO2型壁挂式温湿度变送器采用全体技术的一体式温湿度传感模块,通过高性能单片机的信号处理,整机性能更优越,长期稳定性更出色。
※该系列变送器采用灵活的壁挂式安装,使用方便,输出两路标准0-5V直流电压,适用于大多数工控设备。
※该系列产品为一体化温湿度变送器,广泛应用于楼宇自动化、气候与暖通信号采集、博物馆和宾馆的气候站、大棚温室以及医药行业等。
产品参数※温度量程:0~+50℃/-20~+80℃/-40~+60℃(可设置)准确度:±0.3℃(全量程均值)产品功耗:15mA(典型值)分辨率:0.1℃响应时间6τ(63%):min=5s,max=30s长期稳定性:<0.1℃/年※相对湿度量程:0~99.9%RH准确度(包括非线性度,迟滞和重复性):±3%RH工厂校验不确定度:±0.6%RH(0~40%RH)/±1.0%RH(40~97%RH)响应时间(90%)静止空气:8s分辨率:0.1%RH长期稳定性:<0.5%RH/年※温湿度输出信号:0-5V电压工作和存储环境工作环境温度:-40~+80℃工作环境湿度:0~99.9%无冷凝工作电压:15~36VDC/12~24V AC存储温度:10–50°C(0–125°C peak)存储湿度:20–60%RH(注:以上各项参数如没特殊说明,均在25℃条件下测量)外形尺寸整体尺寸(mm)安装法兰尺寸(mm)电气接线图TV+GNDRH0-5V信号输出接线图注:端子定义以实物标识为准。
温度模拟量输出电源正极电源负极湿度模拟量输出电气接线示意图注意:此变送器输出信号为0-5V 直流电压,如采用电压型检测设备,请将检测设备并联接入输出电路中(见典型应用电路中电压表的位置),如采用其它检测设备,请作相应处理。
METTLER TOLEDO金属探测器服务支持包说明书
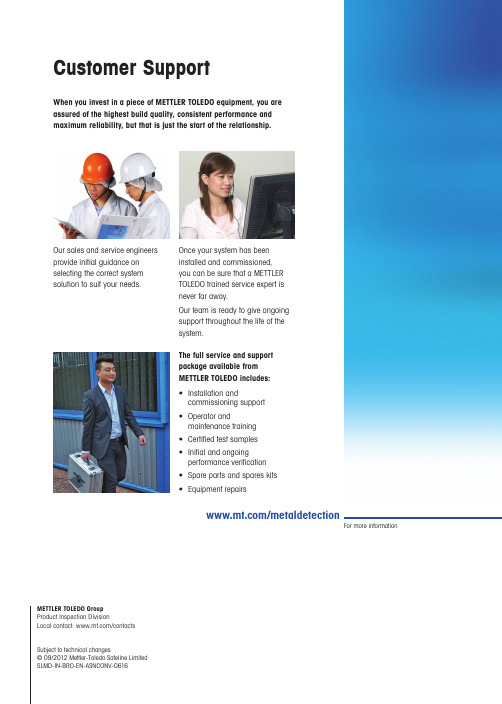
/metaldetectionFor more informationThe full service and support package available from METTLER TOLEDO includes:• Installation andcommissioning support • Operator andmaintenance training • Certified test samples • Initial and ongoing performance verification • Spare parts and spares kits • Equipment repairsWhen you invest in a piece of METTLER TOLEDO equipment, you are assured of the highest build quality, consistent performance and maximum reliability, but that is just the start of the relationship.Our sales and service engineers provide initial guidance on selecting the correct system solution to suit your needs.Once your system has been installed and commissioned, you can be sure that a METTLER TOLEDO trained service expert is never far away.Our team is ready to give ongoing support throughout the life of the system.Customer SupportMETTLER TOLEDO Group Product Inspection DivisionLocal contact: /contactsSubject to technical changes© 09/2012 Mettler-Toledo Safeline Limited SLMD-IN-BRO-EN-ASNCONV-0616Conveyorised Metal Detectors Flexible Configuration Consistent PerformanceMeeting Compliance NeedsM e t a l D e t e c t i o nSeries 40, MB, 60 and 70Flexible Conveyorised Inspection Solutions2Protecting Your CustomersConfigurable to Suit Your ApplicationIn a competitive market place you need to provide your customers with consistent, high quality, contaminant-free products. The Series 40, MB, 60 and 70 Conveyorised Metal Detection range of products provide flexible, inspection solutions to suit a wide range of light to heavy duty food and non-food applications.Tailored to Meet Your Inspection NeedsSystems can be fully configured and built to suit your specific process requirements. Simple stop-on-detection systems through to fully automated detect and reject systems utilising a wide range of product removal devices are available.Conveyorised Metal Detectors provide flexible solutions capable of operating in almost any working environment. This means that whether your product is wet or dry, chilled or frozen, looseor packed, METTLER TOLEDO's range of flexible Conveyorised Metal Detection solutions can address your inspection challenge.C o n v e y o r i s e d M e t a lD e t e c t o r sSeries 40* Conveyorised Metal Detection System with R-Series Profile painted metal detectorSeries 70** Conveyorised Metal Detection System with R-Series Signature metal detector* Series 40 systems are designed for lighter load packages see pages 8 to 9.** Series 70 systems are designed for medium to heavy load packages see pages 10 to 11.Future-Proof Inspection SolutionsDetector apertures, finishes and operational frequencies can be specified to suit your process requirements in order to maximise sensitivity and on line performance. A choice of METTLER TOLEDO metal detection technologies and operating software solutions are available to ensure your quality standards are met.Profile TechnologyThe most advanced metal detection solution available provides the ultimate detection sensitivity to all metals including non-magnetic stainless steels. Profile software also delivers numerous additional features including Product Clustering, Continuous Condition Monitoring and SMS / email communication facilities for maximised process efficiency.Signature TechnologyThe well proven Signature software platformfrom METTLER TOLEDO provides reliablecapability to detect all metal contaminants in amultitude of applications.3C o n v e y o r i s e d M e t a lD e t e c t o r s4Reliable, Consistent PerformanceIn any Working EnvironmentAn Integrated Solution for Dry, Ambient EnvironmentsIn dry, ambient operating environments, painted finishes to both the metal detection head and conveyor frame are sufficient. In some instances a medium duty Stainless Steel (SuS) detector may need to be speci-fied. With IP ratings from a standard IP54 to an IP65 special, systems are capable of withstanding wipe down and light hose down cleaning regimes.Systems of this type can include US Food and Drug Administration (FDA) approved polyurethane (PU) con-veyor belts or can be specified to incorporate modular, polyethylene (PE) belts if required.Suitable for Wet, Chilled and Frozen Products in Extreme EnvironmentsWhen the working environment gets tough, inspection systems need to be specified to equally high standards. The Conveyorised Metal Detection product range can be configured with heavy duty stainless steel detectors rated at IP69K and conveyors sealed up to IP65 standard. Systems of this type are normally designed to include modular polyethylene belts to ensure that the whole system is capable of withstanding high-pressure, hightemperature wash-down regimes and still perform reliably, day after day.The Series 40, MB, 60 and 70 Conveyorised Metal Detection product range can be configured to suit your working environment. This means they deliver consistent performance for maximum process efficiency enabling your business to benefit fromimproved competitiveness and increased productivity with minimum overall operating costs.Conveyors for wet, harsh environmentsR Series Profile detector sealed to IP69K for extreme wash down conditionsSystems include emergency stop buttons as standard5Reliable Performance, Easy IntegrationAll Conveyorised Metal Detection systems are designed and built to exacting standards for long term stability, performance and reliability. Conveyor frames are rigid and robust with fully welded construction. Ledges, flat horizontal surfaces and other dirt traps are minimised ensuring that cleaning is made easy.Effective Product Conveying for Enhanced Process EfficiencyHigh quality motors and drives are utilised to ensure product is transported positively and consistently through the detector. A choice of fixed speed, direct drive motors are available to meet most demands. Alternatively, variable speed drives can be specifiedwhen required.Further Options for a Tailored SolutionOther options can be specified to further aid operational efficiency and product transfer effectiveness including the incorporation of product guides to provide full control of the product as it passes through the system.C o n v e y o r i s e d M e t a lD e t e c t o r s6Fail Safe SystemsFor Complete Peace of MindThe Conveyorised Metal Detection product range can be configured to meet andexceed the demands of all leading retailer and other industry or regulatory standards. An extensive range of options from simple pack sensing devices through to sophisticated closed loop failsafe systems are available.Systems provide a future proof solution with the option to retro-fit failsafe systems at a later stage enabling the system to grow and evolve with your needs and the needs of your customers.Data Collection via USB SticksThe detectors used within the product range can be configured to incorporate ports to support external devices such as USB sticks to collect data. Information gathered can be used to generate data tickets or provide electronic records. When more sophisticated automated data collection is required, systems can incorporate advanced connectivity solutions ranging from a simple serial connection to full Ethernet network connectivity whichcould include wireless functionality.Warning beacons and soundersKey re-set (shown) and push button systems availablePack sensorsDevices and Systems Available Include:• Warning beacons and sounders • Push-button and re-set systems • Pack in-feed sensors• Reject confirmation sensors • Bin-full sensors• Detector head fault warning • Air failure alarm •Shaft encoderSeries 70 Conveyorised System with R-Series Signature metal detectorRemoving the Right Contaminated Product Every TimeOnce identified, metal contaminated product or packs need to be safely and effectively removed from the production line. Rejecting the right pack every time without compromising process efficiency requires the system to be specified correctly with sophisticated timing and process control measures. Important factors to consider can include the need to meet compliance requirements and the characteristics of the product and process, for example, the pack size and line speed.Stop on Detect FunctionalityThe simplest solutions enable the conveyor to be stopped on the detection of metal contamination. Contaminated product can be manually removed before re-starting the system. The effectiveness of these basic systems can be supplemented through the use of optional warning sounders, high visibility beacons and other secure system re-set features.A Choice of Automatic Reject SystemsThe Series 40, MB, 60 and 70 Conveyorised Metal Detection product range can be configured with a host of dynamic, fully automated reject systems. For pack products the reject systems include photo-gated timers to ensure the correct pack is rejected every time. These systems can also be supplemented with the full range of optional warning devices, reject product collectionbins and innovative fail safe systems to further support compliance.Integrated Reject Options Available Include• Air Blast Reject Systems • Pusher Reject Systems*• End Flap Systems*• Sweep Arm Diverter*•Reject BinsAir Blast Reject SystemsPusher Reject SystemsSweep Arm DiverterEnd Flap SystemsRejection Mechanism Capability Table* These systems need be chosen as per configuration and rejection mechanism capability tables.** Reject Bin can only match with Pusher and Air Blast rejections.7Reject BinC o n v e y o r i s e d M e t a lD e t e c t o r s8Series 40 and Series MBConveyorised Inspection SolutionsAvailable in different lengths and widths, Series 40 Conveyorised Systems are designed to be used for light load packed applications with the Series MB solution being utilised in wet harsh processing and packed product line production.Systems are suited for integration into production lines or can be utilised in stand alone applications.Such solutions can form Critical Control Points (CCP's) in a production process to support compliance with local regulatory and international food standards.The system can be designed and built to suit your specific process requirements from simple stop-on-detection, to fully automatic detect and reject systems.Series 40 and Series MB Configuration TablesSeries 40Series MBChoice of Aperture Size••Choice of Conveyor Length and Height ••Conveyor Frame Materials Mild Steel – White Painted •Stainless Steel – Brushed••Fixed Conveyor Speed *•Stop-on-Detection ••Beacon Sounder••Rejection MechanismEnd Flap••Pusher••Sweep Arm Diverter ••Air Blast ••System OptionsProduct Guide ••Pack Sensor••Reject Bin ••Emergency Stop••Variable Conveyor Speed *••* For speed value refer to the conveyor speed tablesSeries MB Conveyorised System with R-Series Profile SuS DetectorSeries 40 and Series MB Product Application RangeSeries 40Series MBApplication Environment Dry product (discrete, small pack)Dry, wet or frozen product (processed, block, pack)Product Size Length≤1000 mm≤1000 mm Width≤200 mm≤400 mm Height ≤150 mm≤300 mm Weight≤10 kg≤30 kgSeries 40 and Series MB Size RangeSeries 40Series MB Conveyor Belt Material PU*Modular PE**Outline Dimensions (mm)Length (Lc)1000~12001200~2000 Width (Ws)800~900800~1100 Height (Hc)550~1000550~1000Maximum Load (kg)1040 MD Aperture Size (mm)Width (Wa)200~300200~500Height (Ha)75~20075~350 Series 40 and Series MB Speed ConfigurationSeries 40 (m/min)Series MB (m/min)Fixed Speed 0.25Kw Not applicable20, 330.55Kw Not applicable16, 19, 25, 35Variable Speed 18~28 18~28 25~4025~40 35~5035~50Note: Speed value tolerance ±10%9 PU* = Polyurethane PE** = PolyethyleneC o n v e y o r i s e d M e t a lD e t e c t o r s10Series 60 and Series 70Conveyorised Inspection SolutionsSeries 60 and Series 70 Configuration TablesSeries 60Series 70Choice of Aperture Size••Choice of Conveyor Length and Height ••Conveyor Materials Mild Steel – White Painted ••Stainless Steel – Brushed••Fixed Conveyor Speed *••Stop on Detection ••Beacon Sounder••Rejection MechanismEnd Flap••Pusher•Sweep Arm Diverter •Function OptionsProduct Guide ••Pack Sensor••Reject Bin •Emergency Stop••Variable Conveyor Speed *••* For speed value refer to the conveyor speed tablesFor larger product applications, the Series 60 and Series 70 Conveyorised Systems provide a flexible conveyor and detection solution well suited to medium and larger packed products.Systems can be integrated efficiently into a production line or utilised for stand alone applications.System design is flexible with a range of configurations enabling diverse solutions to be developed to suit specific process requirements from simple stop-on-detection systems to fully automatic detect and reject mechanisms.Series 70 Conveyorised System with R-Series Signature metal detector11Series 60 and 70 Size RangeSeries 60Series 70Conveyor Belt MaterialPU*PU*Outline Dimensions (mm)Length (Lc)1200~24001200~2400Width (Ws)900~11001100~1400Height (Hc)550~1000550~1000Maximum Load (kg)5050MD Aperture Size (mm)Width (Wa)300~600650~800Height (Ha)75~45075~450Series 60 and 70 Speed ConfigurationSeries 60(m/min)Series 70(m/min)Fixed Speed0.25Kw 20, 27, 35, 41, 4831, 39, 480.55Kw21, 28, 35, 43, 5021, 28, 35, 40, 50Variable Speed18~28 18~28 25~4025~40 35~5035~50Note: Speed value tolerance ±10%Series 60 and 70 Product Application RangeSeries 60Series 70Application EnvironmentDry Product (discrete, big bag, pack)Dry Product (discrete, block, pack)Product SizeLength≤2000 mm ≤2000 mm Width ≤500 mm ≤700 mm Height ≤400 mm ≤400 mm Weight≤30 kg≤30 kgPU* = Polyurethane。
海斯特FORTENSH6.0FT产品说明书
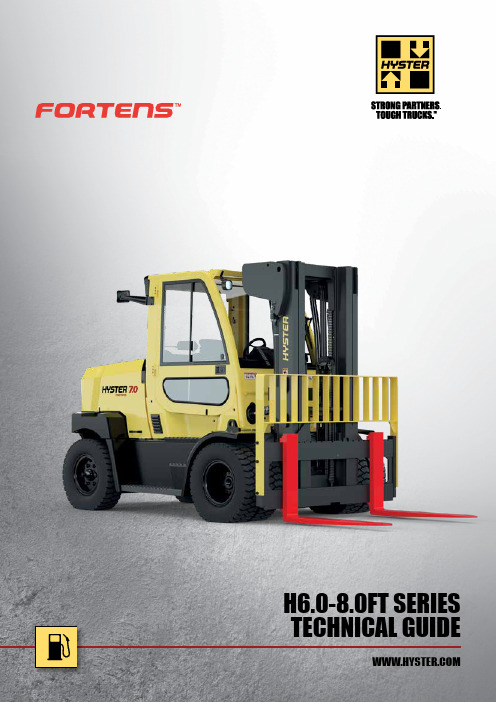
TECHNICAL GUIDEH6.0-8.0FT SERIES2DIMENSIONS h 1sßαh 4h 3h 6m 1h 10yxlc l 1Q1l 5m 2h 7l 2b 2b 1b 11eb 10b 13Wab 5a/2Asta/2H6.0-7.0FTCENTRE OF GRAVITY3h 6h 10h 7y xll 1l 2l 5m 2m 1h 1c Q1sßαh 4h 3b 1b 2b 10b 5eb 13b 11Waa/2Asta/2CENTRE OF GRAVITYH7.0-8.0FTSH6.0FT SPECIFICATIONS 1-11-2H7.0FTS SPECIFICATIONS 1-11-2H8.0FTS SPECIFICATIONS 1-11-27-1Engine manufacturer / modelKUBOTA V3600 62.3KWKUBOTA V3800 81.5KW10-1Operating pressure for attachments bar 155155Parking brakeR A T E D L O A D (k g )STANDARD HOOK TYPE CARRIAGELOAD CENTRE (mm)Load centre - distance from front of forks to centre of gravity of load.Rated load - based on vertical mast.2500350045005500650075008500050010001500H7.0FTH6.0FTH8.0FTSH7.0FTSH7.0FTS9MAST AND CAPACITY INFORMATIONNOTES:Specifications are affected by the condition of the vehicle and how it is equipped, as well as the nature and condition of the operating area. Inform your dealer of the nature and condition of the intended operating area when purchasing your Hyster ® truck.(1) Bottom of forks.(2) W/o load backrest.(3) h 6 subject to +/- 5 mm tolerance. 2549mm for Cab option.(4) Full suspension seat in depressed position. (5) Add 32mm with load backrest.(6) Variable.(7) Measured according to the test cycles and based on the weighting valuescontained in EN12053.All capacities are according to EN1551.MAST TABLES:(1) Deduct 224 with load backrest (2) Add 224 without load backrest (3) Deduct 125 without load backrest (4)Add 125 without load backrestSafety: This truck conforms to the current EU and ANSI requirements.NOTICE:Care must be exercised when handling elevated loads. Operators must be trained and must read, understand and follow the instructions contained in the Operating Manual.All values are nominal values and they are subject to tolerances. For further information, please contact the manufacturer.Hyster products are subject to change without notice.Lift trucks illustrated may feature optional equipment. Values may vary with alternative configurations.Specification data is based on VDI 2198.CERTIFICATION: Hyster lift trucks meet the design and construction requirements of B56.1-1969, per OSHA Section 1910.178(a)(2), and also comply with the B56.1 revision in effect at time of manufacture. Certification of compliance with the applicable ANSI standards appears on the lift truck. Performance specifications are for a truck equipped as described under Standard Equipment on this Technical Guide. Performance specifications are affected by the condition of the vehicle and how it is equipped, as well as by the nature, condition of the operating area, proper service and maintenance of the vehicle. If these specifications are critical, the proposed application should be discussed with your dealer.NOTE: Specifications, unless otherwise listed, are for a standard truck without optional equipment.H6.0FT / H7.0FT / H7.0FTS RATED CAPACITY KG@ 600 MM LOAD CENTREMaximum fork height h 3 + s (mm)Back tilt (°)Lowered height h 1 (mm)Extended height h 4 (mm) (3)Free lift height h 2 + s (m)8.25 x 15-14 Dual pneumatic drive tyresCarriage without sideshift (kg)Carriage with integral sideshift (kg)H8.0FTS H8.0FTS 2-S T A G E L I M I T E D F R E E L I F T 30659°2712435008000796035659°2962485008000795045659°3462585008000793055659°3962685008000790060659°421273500792078103-S T A G E F U L L F R E E L I F T46156°270260771565 (4)8000741055156°300269771865 (4)8000739059656°315274272015 (4)79707360H7.0FTS9 / H8.0FTS RATED CAPACITY KG@ 900 MM LOAD CENTREMaximum fork height h 3 + s (mm)Back tilt (°)Lowered height h 1 (mm)Extended height h 4 (mm) (3)Free lift height h 2 + s (m)8.25 x 15-14 Dual pneumatic drive tyresCarriage without sideshift (kg)Carriage with integral sideshift (kg)H7.0FTS9H8.0FTS H7.0FTS H8.0FTS 2-S T A G E L I M I T E D F R E E L I F T 30659°271243500739067706900632035659°296248500738067606890631045659°346258500736067406880629055659°396268500734067306860628060659°42127350072606650678062003-S T A G E F U L L F R E E L I F T46156°270260771565 (4)688063406430592055156°300269771865 (4)686063206410590059656°315274272015 (4)6840630063905880ERGONOMICS (continued)STD OPT Standard seat belt XHI VIS red seat beltX HI VIS red seat belt with interlock X Air conditioningX Rear drive handle with horn button X Dash mounted 12V auxiliary power outlet XManual lever hydraulic controlsXTouchPoint TMmini lever hydraulic controlsX Joystick X Directional leverXIntegrated directional switch X MonotrolTMX Load weight display XVISIBILITYSTDOPT Dual mirrors side viewX Rear mounted color camera with LCD displayX 2 front and 1 rear LED work lights with stop, tail, indicator & reverse lights X 2 front and 1 rear halogen work lights with stop, tail, indicator & reverse lightsXLED work light protection X Mast mounted LED lights X Hazard warning lights XOPERATIONSTD OPTTurn assist system - H7.0FTS / H7.0FTS9 / H8.0FTS XAudible reverse alarm X Amber strobe lightX Pedestrian awareness light (P .A.L.)X Front pedestrian awareness light (P .A.L.)X Keyswitch start XOperator password startX Push button start with operator password X Push button park brake X Battery disconnect switch X System monitoring package XPremium monitoring packageX Seat switch activated engine, lights and display shutdown system X Signal activated engine shutdown system X Impact monitor with 30s shutdown X Impact monitor with immediate shutdown X Full underbody mesh belly pan X Greasing system for base truck X Optical fuel level sensor X Pressure fuel level sensor X 2 front / 1 rear lifting eyes X Aftermarket-ready telemetry kit X Wireless access card reader X Wireless monitoring - cell XWireless monitoring - wifi X Wireless verification XPACKAGESSTDOPT Cool Truck package which includes belly pan including brake line protection, exhaust wrap, fans in hood key activated and rubber front axle guard XAPPEARANCESTD OPT Hyster yellow paint base truck XSpecial paint colour XSUPPLEMENTAL STDOPT Literature pack X CE certificationX 12 Months / 2,000 Hours manufacturers warranty X36 Months / 6,000 Hours extended warrantyX FEATURES AND OPTIONSSpecial Products Engineering Department (SPED). Contact Hyster for details.www.hyster.eu *********************/HysterEurope @HysterEurope/HysterEuropeSTRONG PARTNERS. TOUGH TRUCKS.TMFOR DEMANDING OPERATIONS, EVERYWHERE.Hyster supplies a complete range of warehouse equipment, IC and electric counterbalanced trucks, container handlers and reach stackers. Hyster is committed to being much more than a lift truck supplier.Our aim is to offer a complete partnership capable ofresponding to the full spectrum of material handling issues: Whether you need professional consultancy on your fleet management, fully qualified service support, or reliable parts supply, you can depend on Hyster.Our network of highly trained dealers provides expert,responsive local support. They can offer cost-effective finance packages and introduce effectively managed maintenance programmes to ensure that you get the best possible value. Our business is dealing with your material handling needs so you can focus on the success of your business today and in the future.HYSTER-YALE UK LIMITED trading as Hyster Europe. Registered Address: Centennial House, Building 4.5, Frimley Business Park, Frimley, Surrey GU16 7SG, United Kingdom.Registered in England and Wales. Company Registration Number: 02636775. ©2020 HYSTER-YALE UK LIMITED, all rights reserved. HYSTER,, STRONG PARTNERS. TOUGH TRUCKS., MONOTROL andare trademarks of HYSTER-YALE Group, Inc.Kubota is a trademark of Kubota Corporation. Grammer is a trademark of Grammer Seating Systems Ltd. Hyster products are subject to change without notice. Forklift trucks illustrated may feature optional equipment.Printed in EU. Part number: 3990331 Rev. 03-01/20HYSTER EUROPECentennial House, Frimley Business Park, Frimley, Surrey, GU16 7SG, England.Tel: +44 (0) 1276 538500。
TriTech DS860系列微波 PIR门激光报警器说明书

Installation Instructionsfor the DS860 SeriesTriTech Microwave/PIR Intrusion Detectors 1.0Specifications•Dimensions (HxWxD): 5 in. x 2.8 in. x 2.2 in.(12.7 cm x 7.1 cm x 5.6 cm)•Input Power:9 to 15 VDC, 16 mA DC nominal(up to 48 mA DC during walk testing ortrouble conditions). Useonly anApproved Limited Power Source.•Standby Power:No internal standby battery.Standby power must be provided byan Approved Limited Power Source.Sixteen mAh required for each hour ofstandby time needed. For UL Listedrequirements, four hours (64 mAh)minimum are required.•Alarm Relay:Silent operating Normally Closedreed relay. Contacts rated 3 watts,125 mA, 28 VDC maximum for DCresistive loads; and protected by a4.7 ohm, 0.5 watt resistor in thecommon "C" leg of the relay. To beconnected to a SELV (Safety Extra-LowVoltage) circuit only. Do not use withcapacitive or inductive loads.•Temperature Range:-40°F to +120°F (-40°C to +49°C).For UL Listed requirements, thetemperature range is +32°F to +120°F(0°C to +49°C), indoor use.•Microwave Frequency:DS860:10.525 GHz (UL Listed)DS860A:10.687 GHz (Export only, not ULListed)DS860B:9.9 GHz (Export only, not UL Listed))•Coverage:Broad (standard):60 ft. by 60 ft. (18 m by 18 m)Long Range (optional):100 ft. by 10 ft. (30 m by 3 m)•Internal Pointability:+2° to –10° Vertical, ±10° Horizontal.•Tamper:Normally Closed (with cover on).Contacts rated at 28 VDC, 125 mAmax. To be connected to a SELV(Safety Extra-Low Voltage) circuitonly. Connect tamper circuit to 24-hourprotection circuit.•Options:B328 Gimbal Mount Bracket, B335Low Profile Swivel Mount Bracket,B338 Ceiling Mount Bracket, OLR92Long Range Barrier LensNOTE:Use of a bracket may reduce range and increase dead zone areas.• Reading Bosch Security Systems, Inc. Product Date Codes For Product Date Code information, refer to the BoschSecurity Systems, Inc. Web site at:/datecodes/•Compliance: This device complies with Part 15 of the FCC Rules and with RSS-210 of Industry and Science Canada.Operation is subject to the following two conditions:(1)this device may not cause harmful interference, and(2)this device must accept any interference received,including interference that may cause undesirableoperation.Changes or modifications not expressly approved by BoschSecurity Systems can void the user’s authority to operate theequipment.2.0Installation ConsiderationsNOTE:The DS860 is not recommended for installationscontaining pets or small animals. Use the DS820 orDS835 for such installations.•Never install the detector in an environment that causes an alarm condition in one technology. Good installations start with the LED OFF when there is no target motion. It should never be left to operate with the tri-color LED in a constant or intermittent green, yellow, or red condition.•Point the unit away from outside traffic (roads/alleys).NOTE:Microwave energy will pass through glass and most common non-metallic construction walls.•Avoid installations where rotating machines (e.g. ceiling fans) are normally in operation within the coverage pattern. Point the unit away from glass exposed to the outdoors and objects that may change temperature rapidly.NOTE:The PIR detector will react to objects rapidly changing temperature within its field-of-view.•Eliminate interference from nearby outside sources.3.0Mounting•Select a location likely to intercept an intruder moving across the coverage pattern. The surface should be solid andvibration-free. Mounting height range is 6 to 8 ft. (1.8 to2.4 m). Recommended mounting height is 7.5 ft. (2.3 m).•Remove the cover. Insert a flathead screwdriver into the locking tab hole at the bottom front of the detector. Pull thecover up and forward.VerticalAdjustScrewTri-colorLEDT erminalStripLEDOn/OffPinsMW0°- 4°- 8°OnOffMicrowaveRange AdjustPIRSensitivitySelection PinsVertical AdjustScaleLook Down LensMIN MAXFace of Lens(masking area) Corner MountKnockout (4)Surface MountKnockout (2)WireEntrancesBracket MountKnockoutVertical AdjustScrew MountCover T ab andLocking Screw HoleWireEntrances•Remove the circuit board from the base. Loosen the Vertical Adjust Screw and slide the circuit board down, then out.•Break away the appropriate thin-wall wire entrance and mounting hole coverings in the base.•Using the base as a template and aligning it so that the detector will be mounted with the terminal block at the top and the PIR lens at the bottom, mark the location of the mounting holes on the mounting surface. Pre-start the mounting screws.Page 2© 2011 Bosch Security Systems, Inc.DS860 Series Installation InstructionsOnOffINTSTD•Route wiring as necessary. Route to the rear of the base and through the wire entrance. Make sure all wiring is unpowered before routing.•Securely attach the base to the mounting surface.•Return the circuit board to the base and tighten the Vertical Adjust Screw.4.0WiringCAUTIONOnly apply power after all connections have been made and inspected. Do not coil excess wiring inside detector.NOTE:Input power must use only an Approved Limited Power Source. Alarm and Tamper Contacts to be connected to a SELV (Safety Extra-Low Voltage) circuit only.9-15 VDCInput–+C NC Alarm RelaySP TSPT Tamper1234Alarm5678Tamper •Terminals 1 (–) & 2 (+): Voltage limits are 9 to 15 VDC. Use no smaller than #22 AWG (0.8 mm) wire pair between the detector and the power source.•Terminals 3 & 4: Alarm relay (reed) contacts rated 3 watts,125 mA, 28 VDC maximum for DC resistive loads and protected by a 4.7 ohm, 0.5 watt resistor.NOTE:Do not use with capacitive or inductive loads.•Terminals 5 and 8: Spare.•Terminals 6 & 7: Tamper contacts rated at 28 VDC, 125 mA.NOTE:Plug the wire entrance hole with the foam plug provided after all wiring connections have been made.5.0LED OperationThe detector uses a tri-color LED to indicate the various alarm and supervision trouble conditions that may exist. See chart below.LEDCauseSteady red Unit alarmSteady yellow Microwave activation (walk test)Steady green PIR activation (walk test)Flashing redWarm-up period after power-up Flashing red (4 pulse sequence)Replace UnitIf the detector experiences a Microwave or PIR self-test failure, it is in need of replacement.NOTE:During walk testing, the LED will light for the first technology (microwave or PIR) and then light red to indicate a detector alarm. The LED will not indicate activation of the second technology by lighting its color.6.0Feature Selection6.1LED On/Off PinsThe ON position allows operation of the tri-color LED. If LEDindication is not desired after setup and walk tests are completed,place in the OFF position. The OFF position does not prevent the LED from indicating supervision trouble conditions. 6.2PIR Sensitivity Selection PinsFor selection, place the plug across the pins marked STD for Standard or INT for Intermediate mode.•Standard Sensitivity: The recommended setting for maximum false alarm immunity. Tolerates environmental extremes on this setting.•Intermediate Sensitivity: The recommended setting for any location where an intruder is expected to cover only a small portion of the protected area. Tolerates normal environments on this setting. This setting will improve your intruder catch performance.7.0Set-up and Walk TestsSelect the vertical starting angle from this chart:To adjust the vertical startingangle for the desired mounting heightand range,loosen thevertical adjustscrew and slidethe board up, topoint the angle down. Note the settings on the vertical adjust scale.•Place the LED plug in the ON position and replace the cover.7.1Establishing PIR Pattern Coverage•Turn the Microwave range adjust to minimum.•Replace the cover and snap it into place. This will close the tamper switch.•Wait two minutes minimum after applying power to start walk tests.NOTE :During the warm-up period, the tri-color LED will flash red until the unit has stabilized (approximately 1 to 2 minutes)and has seen no movement for two seconds. When the tri-color LED stops flashing, the detector is ready to be tested. With no motion in the protection area, the tri-color LED should be OFF. If the LED is on, re-check theprotection area for disturbances affecting the microwave or PIR technologies.•Walk test across the pattern at its farthest edge, then several times closer to the detector. Start walking from outside of the intended protection area, and observe the tri-color LED. The edge of the pattern is determined by the first green, PIR activation of the LED (or the first red activation if the yellow microwave LED activates first).•Walk test from the opposite direction to determine both boundaries. The center of the pattern should be pointed toward the center of the intended protection area.NOTE :The pattern may be moved ±10° horizontally by rotating the lens window left or right.•Slowly bring your arm up and into the pattern to mark the lower boundary on PIR alarm. Perform this task at 10 to 20 ft. (3 to 6m) from the unit. Repeat from above for the upper boundary.The center of the pattern should not be tilted upward .DS860Broad Long Range MountingHeight60 ft.(18 m)100 ft.(30 m)6.5 ft. (2 m)-4°-2°7.5 ft. (2.3 m)-5°-3°8.0 ft. (2.4 m)-6°-3°NOTE:If desired coverage cannot be achieved, try angling the coverage pattern up or down to assure the pattern is notaimed too high or low. The angle of the PIR pattern may bevertically positioned between -10° and +2° by looseningthe Vertical Adjust screw and sliding the circuit board up ordown. Moving the board up will angle the patterndownward.•Tighten the screw snug when positioning is completed.7.2Establishing Microwave CoverageNOTE:It is important to wait one minute after removing/replacing the cover so the microwave portion of the detector cansettle, and to wait at least ten seconds between thefollowing walk testing procedures.•The tri-color LED should be OFF before walk testing.•Walk test across the pattern at the intended coverage’s farthest end. Start walking from outside the intendedprotection area and observe the tri-color LED. The edge of the microwave pattern is determined by the first yellow, microwave activation of the LED (or the first red activation if the green PIR LED activates first).•If adequate range can not be reached, increase the Microwave Range Adjust slightly. Continue walk testing (waiting oneminute after removing/replacing the cover) and adjusting therange until the farthest edge of desired coverage has beenaccurately placed.NOTE:Do not adjust the microwave range higher than required.Doing so will enable the detector to catch movementoutside of the intended coverage pattern.•Walk test the unit from all directions to determine all the Microwave pattern boundaries. Wait at least ten secondsbetween walk tests.7.3Establishing Detector Coverage•The tri-color LED should be OFF before walk testing.•Walk test the unit from all directions to determine the detection boundaries. A detector alarm is signaled by the first redactivation of the tri-color LED after an initial green or yellowactivation.8.0Supervision FeaturesThe supervision features function as follows:•PIR/Microwave: The complete circuit operation of these subsystems is checked approximately every 24 hours. If thePIR or MW subsystem fails, the tri-color LED will flash red 4times per cycle and the unit should be replaced.•Default: If the microwave subsystem fails, the detector will default to PIR technology protection. The PIR signal sensitivity will automatically change from INT to STD.9.0MaintenanceAt least once a year, the range and coverage should be verified. To ensure continual daily operation, the end user should be instructed to walk through the far end of the coverage pattern. This ensures an alarm output prior to arming the system.10.0Coverage PatternsThe DS860 has a standard broad coverage pattern or an optional long-range coverage pattern. The protected coverage area is where the microwave and PIR patterns overlap.An optional Look Down lens is located under the detector. This lens must be unmasked before it is operational. Use caution to remove the black mask only. Do not attempt to remove the white lens assembly. The Look Down lens is not recommended for installations containing pets or small animals. The Look Down zone is shown in black on the Coverage Pattern drawings.Standard Broad Coverage0102030405060Feet0369121518Meters10 ft.0 ft.-5°SIDE VIEWA-IJ-MN-PQ, R3Meters7.5 ft. 2.3 m0369121518Meters0102030405060Feet0 Feet102030102030369369TOP VIEW BACDGHIJKLMNOPEFRQ0Meters Look-DownDS860 Series Installation Instructions© 2011 Bosch Security Systems, Inc.Page 32/11DS860 Series Installation InstructionsP/N: F01U068628-12 Page 4© 2011 Bosch Security Systems, Inc.130 Perinton Parkway, Fairport, New York Long Range Barrier CoverageMeters300Feet 100055TOP VIEW102030405060708090369121518212427001.51.5ABCD Meters300Feet10010SIDE VIEW1020304050607080903691215182124270-3°3Meters ABCD 7.52.3Look-Down 10.1Pattern MaskingThe PIR coverage pattern may be masked using masking tape or electrical tape on the inside (grooved side) of the lens to cover the appropriate pattern areas as shown in the following illustrations.Always walk test for the desired coverage after masking.A B C D E F G H I N J Q K O L R M PDS860 Standard LensA B C DOptional Long RangeBarrier LensNOTE:Masking only eliminates the PIR portion of the coverage and has no effect on the microwave pattern.。
Homder BABeemtDV2w 壁墙探测仪用户指南说明书

Manuals+— User Manuals Simplified.Homder BABeemtDV2w Stud Finder Wall Scanner User Guide Home » Homder » Homder BABeemtDV2w Stud Finder Wall Scanner User GuideContents1 Homder BABeemtDV2w Stud Finder WallScanner2 Multifunction Wall ScannerTH4303 INSTALLING THE BATTERY4 OPERATING TIPS5 SELECTING THE MODE6 TURNING ON/CALIBRATING THE TOOL7 FINDING A STUD8 AC WIRE WARNING9 SCANNING IN METAL MODE10 SCANNING IN AC MODE11 Documents / ResourcesHomder BABeemtDV2w Stud Finder Wall ScannerSCANNING DIFFERENT SURFACESWallpaper: Multifunction wall scanner TH430 functions, normally on walls covered with wallpaper or fabric, unless the materials are metallic foil, contain metallic fibers, or are still wet after application. Wallpaper may need to dry for several weeks after application.Freshly painted walls: May take one week or longer to dry after application.Lath & plaster: Due to Irregularities of i1 plaster thickness, 11 Is difficult for Multifunction wall scanner TH430 to locate studs In Stud modes. Change the Metal Scan mode to locate the nail heads holding wood lath to the studs. II the plaster has metal mesh reinforcement.Multifunction wall scanner TH430 may be unable to detect through that material.Extremely textured walls or acoustic ceilings: When scanning a ceiling or wall with an uneven surface, place tin caroard the surface to be scanned and scan over the caroard in Stud 1 1/2 in. scan If irregular scanning rest. ns are received. switch to the Metal Scan node to locate nails or drywall screws that are up vertically where a stud or joist isWood flooring, subflooring, or gypsum sheathing: Use Stud 1 1/2 in. scan rt)de and rnov•e the tool Sigul In&cator may only display lined bars when the læates a stud through surfers. Multifunction wall scanner TH430 cannot æan for and Pists through concrete or In situations. ry lßng Metal Scan to nails or screws that truly up Mere a stud or joistNote: Sensing depth and accuracy can vary due to moisture, of materials, and wall texture. and paint.SELECTING THE MODEPress the switch to the Stud 1/2 in. scan for finding wood or metal studs within 1/2 in.; Stud 1 in. scan for waging wars within 1 in. thick; Stud 1 1/2 in. scan for watts within 1 1/2 in. thick; Metal Scan for metal; or AC Scan læating live AC wiring. The OWOFF button should pressed peer on the detector before other operations.TURNING ON/CALIBRATING THE TOOLMultifunction wall scanner TH430 can be calibrated anywhere on the wall.Place the Multifunction wall scanner TH430 against the wall before pressing the ON/OFF button.Press the power button, the LCD always displays in Stud 1/2 in. scan mode. Press the Scan button to start calibration, the decreasing bars will disappear and the buzzer will beep one time and the calibration iscorrected. ( keep the tool flat against the wall and begin scanning.)Note: It is important to wait for calibration to complete (2—3 seconds) every time before moving the scanner.Wallpaper: Multifunction wall scanner TH430 functions normally on walls covered with wallpaper or fabric.unless the materials are metallic foil, contain metallic fibers, or are still wet after application. Wallpaper may need to dry for several weeks after application.Freshly painted walls: May take one week or longer to dry after application.Lath & plaster. Due to plaster thickness, it is difficult for Multifunction wall TH430 to locate studs in StudChange to Metal mode to locate the nail heads and Folding lath to the studs. If the star has metal meshreinforcement, the Multifunction wall scanner may be unable to detect through that material.Extremely textured walls or acoustic ceilings: When a wall with the surface. in the surface to cover thecardboard in Stud 1 1/2 in. If mining results are swindle to nails drywall screws that where a or is or gypsum drywall over The Sigtal Indcabt may Limited bars when the tool locates a stud through thick surfaces.Multifunction wall scanner TH430 cannot scan for wood studs and joists through concrete or carpet andpadding. In problematic situations, try using Metal Scan to locate nails or screws that may line up vertically where a stud or joist is positioned.Note: Sensing depth and accuracy can vary due to moisture, content of materials, wall texture, and paint.SELECTING THE MODEPress the mode switch button to the desired mode: Stud 1/2 in. scan for finding wood or metal studs within 1/2 in.; Stud 1 in. scan lor scanning walls within 1 In. thick; Stud 11/2 in. scan for scanning walls within 11/2 in. thick;Metal Scan for locating metal; or AC Scan for locating live AC wiring. The ON/OFF button should be pressed once to power on the detector before other operations.TURNING ON/CALIBRATING THE TOOLMultifunction wall scanner TH430 can be calibrated anywhere on the waitPlace the Multifunction wall scanner TH430 against the wall before pressing the ON/OFF button.Press the power button, the LCD always displays in SttJd 1/2 in. scan mode. Pr? 1he Scan button to start calibration, the decreasing bars will disappear and buzz8f will beep one time and the calibration Is completed. ( keep the tool flat against the wall and begin scanning.)Note: It is important to wait for calibration to complete (2-3 seconds) every time before moving the scanner FINDING A STUDAC WIRE WARNINGSCANNING IN METAL MODENote: For men scanning for studs, use Stud in. scan mode (or Stud I in., Stud 11,2 in. scan mode on thicker welts) to quickly locate me center and edges. use Metal Scan to determine if the previous reading in Stud scan was a wood stud, metal stud, or pØe. In Metal Scan, only metal drywall screws will be found nod the studs, while metal be indicated everywhere on a metal stud or pipe. Metal Scan has interactive cüratim to a#JSt to its sensitivity to metd which can be used to tie the action of metal in MHS. tors, and ceilings. Maximum sensitivity is a deal for quickly finding the approximate location of the rental. However, sensitivity can be reduced by calibrating the tool closer to metal. With reduced sensitivity. The area where metal is will be smaller. But in both cases, the rr•etal target iS is in the me area where the tool indicates new iS present.1. Pres switch to Metal Scan For maximum Rn sensitivity, turn the tool on in the air by holding the Scan button.This will ensure that it calbratæ away from any metal2. (Figure A) Prws the fiat against the wall and slides the scanner across the surface. Mark where you have thehighest metal (the rut on the screen). If is a strong target, the top arrow shows. a will sand. Continue in the sarne until dis*y regex*. Reverse and mark the where the display bars peak reversed The of the two marks Is the of the If the unit induces rental over a refine be scanning area to the metal by fd 3 and 43. (Figure B) To GMG)int of the metal tart. Ean the area again. Release the Scan button and then turn the m, timestarting wall over one of the previous marks. This will reset the to a lower sensitivity and narrow the scan area.4. C) To continue to sensitivity further refine the scanning area, step 3. This can multiple times to narrow the fieldfurther.Note: If any bars are displayed on the screen, metal is present. SrnaN targets or targets deep within the surface may only illuminate some of the bars and rot the center line or audio tone. In this case, use the highest indication to determine tho metal position.SCANNING IN AC MODEAs with Metal Scan Mode, AC Scan Mode has interactive calibration and works in the same manner.1. (Figure A) Press the mode switch button to AC Scan mode. Press the tool flat against the wall, then press theScan button, Wait for the beep to confirm calibration has been completed before moving the tool. Oncecalibration has been completed, slowly slide the scanner across the surface. Mark the location where you get the highest AC indication (the most Middle bars on the screen). If it is a strong target, the top indicated arrow will show, and a steady beep will sound. Continue in the direction until the display bars reduce. Reverse direction and mark the spot where the display bars peak from the reversed direction. The midpoint of the two marks is the location of the center of the live AC wiring. If the unit indicates live electricity over a large area, you can reduce the se live AC Copyfish x2. (Figure B) To further pinpoint the location of the live AC wiring, scan the area again. Release the Scan buttonand then turn the unit back on, this time starting on the wall over one of the previous narks. This will reset the tool to a lower sensitivity and narrow the scan area.3. (Figure C) Scan in both directions as in Step 2. The area indicated should become smaller so you can moreprecisely identify the location of live AC wires. This procedure can be repeated to narrow the field even further.Note: AC Scan will only detect live (hot) unshielded AC wiring. Please refer to the WARNING statement in number 6, AC WARNING Detection, for more important details and warnings about AC detection.HELPFUL HINTS See also number 2, Operating Tips)Documents / ResourcesHomder BABeemtDV2w Stud Finder Wall Scanner [pdf] User GuideDAFO1dU2qbI, BABeemtDV2w, BABeemtDV2w Stud Finder Wall Scanner, BABeemtDV2w, Stud Finder Wall Scanner, Finder Wall Scanner, Wall Scanner, ScannerManuals+,。
Whelen 警览arians 使用说明(样例)说明书
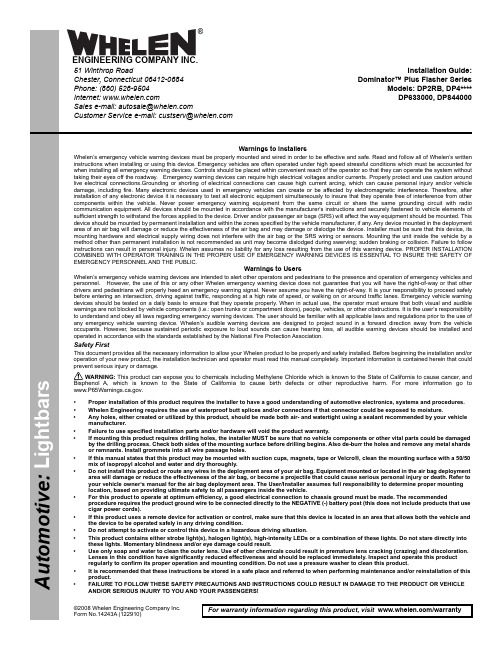
©2008 Whelen Engineering Company Inc.Form No.14243A (122910)A u t o m o t i v e : For warranty information regarding this product, visit /warranty•Proper installation of this product requires the installer to have a good understanding of automotive electronics, systems and procedures.•Whelen Engineering requires the use of waterproof butt splices and/or connectors if that connector could be exposed to moisture.•Any holes, either created or utilized by this product, should be made both air- and watertight using a sealant recommended by your vehicle manufacturer.•Failure to use specified installation parts and/or hardware will void the product warranty.•If mounting this product requires drilling holes, the installer MUST be sure that no vehicle components or other vital parts could be damaged by the drilling process. Check both sides of the mounting surface before drilling begins. Also de-burr the holes and remove any metal shards or remnants. Install grommets into all wire passage holes.•If this manual states that this product may be mounted with suction cups, magnets, tape or Velcro®, clean the mounting surface with a 50/50 mix of isopropyl alcohol and water and dry thoroughly.•Do not install this product or route any wires in the deployment area of your air bag. Equipment mounted or located in the air bag deployment area will damage or reduce the effectiveness of the air bag, or become a projectile that could cause serious personal injury or death. Refer to your vehicle owner’s manual for the air bag deployment area. The User/Installer assumes full responsibility to determine proper mounting location, based on providing ultimate safety to all passengers inside the vehicle.•For this product to operate at optimum efficiency, a good electrical connection to chassis ground must be made. The recommendedprocedure requires the product ground wire to be connected directly to the NEGATIVE (-) battery post (this does not include products that use cigar power cords).•If this product uses a remote device for activation or control, make sure that this device is located in an area that allows both the vehicle and the device to be operated safely in any driving condition.•Do not attempt to activate or control this device in a hazardous driving situation.•This product contains either strobe light(s), halogen light(s), high-intensity LEDs or a combination of these lights. Do not stare directly into these lights. Momentary blindness and/or eye damage could result.•Use only soap and water to clean the outer lens. Use of other chemicals could result in premature lens cracking (crazing) and discoloration. Lenses in this condition have significantly reduced effectiveness and should be replaced immediately. Inspect and operate this product regularly to confirm its proper operation and mounting condition. Do not use a pressure washer to clean this product.•It is recommended that these instructions be stored in a safe place and referred to when performing maintenance and/or reinstallation of this product.•FAILURE TO FOLLOW THESE SAFETY PRECAUTIONS AND INSTRUCTIONS COULD RESULT IN DAMAGE TO THE PRODUCT OR VEHICLE AND/OR SERIOUS INJURY TO YOU AND YOUR PASSENGERS!Warnings to InstallersWhelen’s emergency vehicle warning devices must be properly mounted and wired in order to be effective and safe. Read and follow all of Whelen’s written instructions when installing or using this device. Emergency vehicles are often operated under high speed stressful conditions which must be accounted for when installing all emergency warning devices. Controls should be placed within convenient reach of the operator so that they can operate the system without taking their eyes off the roadway. Emergency warning devices can require high electrical voltages and/or currents. Properly protect and use caution around live electrical connections.Grounding or shorting of electrical connections can cause high current arcing, which can cause personal injury and/or vehicle damage, including fire. Many electronic devices used in emergency vehicles can create or be affected by electromagnetic interference. Therefore, after installation of any electronic device it is necessary to test all electronic equipment simultaneously to insure that they operate free of interference from other components within the vehicle. Never power emergency warning equipment from the same circuit or share the same grounding circuit with radio communication equipment. All devices should be mounted in accordance with the manufacturer’s instructions and securely fastened to vehicle elements of sufficient strength to withstand the forces applied to the device. Driver and/or passenger air bags (SRS) will affect the way equipment should be mounted. This device should be mounted by permanent installation and within the zones specified by the vehicle manufacturer, if any. Any device mounted in the deployment area of an air bag will damage or reduce the effectiveness of the air bag and may damage or dislodge the device. Installer must be sure that this device, its mounting hardware and electrical supply wiring does not interfere with the air bag or the SRS wiring or sensors. Mounting the unit inside the vehicle by a method other than permanent installation is not recommended as unit may become dislodged during swerving; sudden braking or collision. Failure to follow instructions can result in personal injury. Whelen assumes no liability for any loss resulting from the use of this warning device. PROPER INSTALLATION COMBINED WITH OPERATOR TRAINING IN THE PROPER USE OF EMERGENCY WARNING DEVICES IS ESSENTIAL TO INSURE THE SAFETY OF EMERGENCY PERSONNEL AND THE PUBLIC.Warnings to UsersWhelen’s emergency vehicle warning devices are intended to alert other operators and pedestrians to the presence and operation of emergency vehicles and personnel. However, the use of this or any other Whelen emergency warning device does not guarantee that you will have the right-of-way or that other drivers and pedestrians will properly heed an emergency warning signal. Never assume you have the right-of-way. It is your responsibility to proceed safely before entering an intersection, driving against traffic, responding at a high rate of speed, or walking on or around traffic lanes. Emergency vehicle warning devices should be tested on a daily basis to ensure that they operate properly. When in actual use, the operator must ensure that both visual and audible warnings are not blocked by vehicle components (i.e.: open trunks or compartment doors), people, vehicles, or other obstructions. It is the user’s responsibility to understand and obey all laws regarding emergency warning devices. The user should be familiar with all applicable laws and regulations prior to the use of any emergency vehicle warning device. Whelen’s audible warning devices are designed to project sound in a forward direction away from the vehicle occupants. However, because sustained periodic exposure to loud sounds can cause hearing loss, all audible warning devices should be installed and operated in accordance with the standards established by the National Fire Protection Association.Safety FirstThis document provides all the necessary information to allow your Whelen product to be properly and safely installed. Before beginning the installation and/or operation of your new product, the installation technician and operator must read this manual completely. Important information is contained herein that could prevent serious injury or damage.WARNING: This product can expose you to chemicals including Methylene Chloride which is known to the State of California to cause cancer, and Bisphenol A, which is known to the State of California to cause birth defects or other reproductive harm. For more information go to .Installation Guide:Dominator™ Plus Flasher SeriesModels: DP2RB, DP4****DP633000, DP84400051 Winthrop RoadChester, Connecticut 06412-0684Phone: (860) 526-9504Internet: Salese-mail:*******************CustomerServicee-mail:*******************®ENGINEERING COMPANY INC.Specifications:Input Voltage.................................................................................12.8 VDC +/- 20%Input Current for each lighthead / Sim..........................................Peak - .75 AmpsInput Current for each lighthead / Alt..............................................Peak - .3 AmpsFor your lightbar’s input current, multiply by the amount of lightheads in your lightbar.Input Sync................................................................................................Active LowSync Phase.............................................................................Phase I & II @ 400msInput Scan-Lock™.......................................................................+12 VDC @ 20 maInstallation:Note:When routingthe wires, it is veryimportant that youchoose a path thatwill keep the wiresaway from excessiveheat or any vehicleequipment that couldcompromise theintegrity of the wires(ex. trunk lids, doorjams, etc.).Note:Permanent mounting of this product will require drilling. It isabsolutely necessary to make sure that no other vehicle componentscould be damaged by this process. Check both sides of themounting surface before starting. If damage is likely, select adifferent mounting location.IMPORTANT! The lightbar should be a minimum of 16" fromany radio antennas!1.Position the unit in its proposed mounting location. Draw a pencil lineonto the mounting surface along the top and bottom of the extrusionand a “centerline” centered between the two.2.Two 1/4” holes are required to mount this unit. These holes may belocated anywhere along the horizontal centerline that you drew instep one. It’s best to locate the holes as far apart as possible. Markthe hole location onto the mounting surface.ing a 1/4” drill bit, drill a hole in each of the areas scribed in theprevious step.4.Slide the 2 carriage bolts (installed in the rear of the bar) over to the 2mounting holes. Install the rubber gaskets onto the bolts and insertthem into the mounting holes.5.Secure the unit by threading the flat washer and elastic stop nut ontoeach bolt and tightening them firmly.Wiring:As an example, we will synchronize two 2 lighthead Dominators™. The 2lighthead Dominator™ has 4 unique modes for each of the 4 flashpatterns that can be synchronized; Alternating Phase 1, Alternating Phase2, Simultaneous Phase 1 and Simultaneous Phase 2.In Alternating Mode: The left lightbar alternates with the right lightbar.In Simultaneous Mode: The left and right lightbars flash simultaneously.Synchronized lightbars, must be set to the same pattern. Not allpatterns can be synchronized.SET A PATTERN AS DEFAULT: When the desired pattern is displayed,allow it to run for more than 5 seconds. The lighthead will now display thispattern when active.RESET TO THE FACTORY DEFAULT PATTERN: Turn off power andapply +12 volts to the WHITE/VIOLET wire while turning power back on.Note: If you wish to connect the pattern selection wire (WHITE/VIOLET) to a switch, an SPST momentary switch is recommended.Available Scan-Lock™ Flash Patterns:Grey / SYNC:4, 6 & 8 Lamp:1.SignalAlert™ 75etFlash® 753.SingleFlash 3754.SingleFlash 755.ActionFlash™6.ModuFlash™7.ZigZag 608.ZigZag 909.ZigZag 12010.ActionScan™2 Lamp:1.Signal Alert™ 75etFlash® 753.SingleFlash 3754.SingleFlash 755.ActionFlash™6.ModuFlash™7.ActionScan™WARNING: All customer supplied wires that connect to the positiveterminal of the battery must be sized to supply at least 125% of themaximum operating current and FUSED at the battery to carry thatload. DO NOT USE CIRCUIT BREAKERS WITH THIS PRODUCT!Operation: White/Violet / Scan-Lock™Scan-Lock™ allows you to choose from several flash patterns. Tochange a flash pattern, turn on the desired lighthead:CYCLE THROUGH ALL PATTERNS: To cycle forward, apply +12 voltsto the WHITE/VIOLET wire for less than 1 second and release. To cyclebackward,apply +12 volts to the WHITE/VIOLET wire for more than 1second and release.Available Sync Patterns4, 6 & 8 Lamp ArraysSignalAlert™ 75 Alt. - In-Out - Checker Board - Sim. Phase I - Sim. Phase IICometFlash® 75 Alt. - In-Out - Checker Board - Sim. - Phase I - Sim. Phase IISingleFlash 375 Alt. - In-Out - Checker Bd. - Sim. - Phase I - Sim. Phase IISingleFlash 75 Alt. - In-Out - Checker Bd. - Sim. - Phase I - Sim. Phase II2 Lamp Array:SignalAlert 75 Alt - Simultaneous - Phase I - Simultaneous Phase IICometFlash 75 Alt - Simultaneous - Phase I - Simultaneous Phase IISingleFlash 375 Alt - Simultaneous - Phase I - Simultaneous Phase IISingleFlash 75 Alt - Simultaneous - Phase I - Simultaneous Phase IIIMPORTANT! Before returning the vehicle to active service, visuallyconfirm the proper operation of this product, as well as all vehiclecomponents/equipment.。
Tektronix 3T2 时域测试仪校准指南说明书

பைடு நூலகம்00,00 0.000
0.000 000.0
X1 , 2,5 10 , 20 , 50
000.0 00.00
Units us
18 18 ns ng ng
Ic
TYPE 312
Page 1 of 2
General Information This change in the adjustment of the Lead Time , R231 , control is to ensure adequate lead time when the Type 3T2 is operated with the Type 352 .
Section 7
Calibration
Page 7-11
right column , Step 9
Insert new part ( a . ) of Step 9 . a . Set the DISPLAY MODE switch to MANUAL , turn the MANUAL SCAN control
.
8
1 Ons with Trig . Sweep Cal ( 6329 )
9. 10 .
Check 1us , 100us , de 1ms Ranges + 3 % Check Single Sweep
Presets
Range Switch to 10us , lus markers Range Switch to 100ns , 10ns marks
+ 20mv
Range 1 ms
100us 10us
1 us 100ns
Magnifier Decimal
X1 , 2,5 20 , 20 , 50
SITRANS LG240 棒型和绳型测量探头操作说明书

制导雷达SITRANS LG240 Foundation FieldbusPFA 涂层的棒型和绳型测量探头操作说明书 • 01/20202PBD-51041246SITRANS LG240 - 操作说明书44579-ZH-2005223PBD-51041246SITRANS LG240 - 操作说明书44579-Z H -200522目录1关于本技术文献 ............................................................................................................................................51.1 功能 .............................................................................................................................................................................51.2 对象 .............................................................................................................................................................................51.3 所用的图标.. (52)安全注意事项 ...............................................................................................................................................62.1 授权人员 .....................................................................................................................................................................62.2 正确使用 .....................................................................................................................................................................62.3 警告勿滥用.................................................................................................................................................................62.4 一般性安全说明.........................................................................................................................................................62.5 欧盟一致性.................................................................................................................................................................62.6 NAMUR 推荐 (63)产品说明 ......................................................................................................................................................83.1 结构 .............................................................................................................................................................................83.2 操作原理 .....................................................................................................................................................................93.3 包装、运输和仓储 ..................................................................................................................................................103.4 配件 (114)安装 ...........................................................................................................................................................124.1 一般性说明...............................................................................................................................................................124.2 安装说明 . (125)与供电装置相连接 ......................................................................................................................................175.1 为连接作准备...........................................................................................................................................................175.2 连接 ...........................................................................................................................................................................175.3 单腔式外壳的接线图 ..............................................................................................................................................185.4 双腔式外壳的接线图 ..............................................................................................................................................195.5 启动阶段 . (206)用显示和调整模块进行调试 ........................................................................................................................216.1 使用显示和调整模块 ..............................................................................................................................................216.2 操作系统 ...................................................................................................................................................................216.3 更改参数 - 快速调试 ..............................................................................................................................................226.4 更改参数 - 扩展操作 ..............................................................................................................................................236.5 储存设置或更改了的参数 .. (357)用 PACTware 进行调试 .............................................................................................................................367.1 连接电脑 ...................................................................................................................................................................367.2 用 PACTware 更改参数 .........................................................................................................................................367.3 通过快速调试来投入使用 ......................................................................................................................................377.4 储存设置或更改了的参数 .. (388)用其它系统进行调试 ...................................................................................................................................398.1 DD 操作程序............................................................................................................................................................398.2 Field Communicator 375, 475 . (399)诊断与服务 .................................................................................................................................................409.1 维护 ...........................................................................................................................................................................409.2 诊断储存器...............................................................................................................................................................409.3 状态信息 ...................................................................................................................................................................419.4 排除故障 ...................................................................................................................................................................439.5 更换电子插件...........................................................................................................................................................479.6 软件升级 ...................................................................................................................................................................489.7 需要维修时的步骤 .. (48)10 拆卸 ...........................................................................................................................................................4910.1 拆卸步骤 ...................................................................................................................................................................4910.2 废物清除 . (49)4PBD-51041246SITRANS LG240 - 操作说明书44579-ZH-20052211 附件 (50)11.1 技术参数 ...................................................................................................................................................................5011.2 仪表通信 Foundation Fieldbus .........................................................................................................................5811.3 尺寸 ...........................................................................................................................................................................6211.4 商标 (66)用于防爆区域的安全说明请在将仪表用于防爆应用领域时遵守特别针对防爆的安全说明。
DWYER INSTRUMENTS TAC3 口袋式潜在脉冲测速仪规格及操作说明说明书

DWYER INSTRUMENTS, INC.P .O. BOX 373 • MICHIGAN CITY , INDIANA 46361 U.S.A.Phone: 219/879-8000 Fax: 219/872-9057 e-mail:*******************Diode LaserMax. output power: <1 milliwattWavelength: 650 nanometers (visible light)Min. divergence: 1.0 milliradianOutput: Continuous (CW)Laser hazard classifi cation: Class 2Contact info: Country of Origin: USASAFEGUARDS AND PRECAUTIONSLaser hazards• Eye injury from beam - Do not look into the direct or refl ected beam; can cause eye injury up to 25 ft (7.5 m) away.• Visual interference (glare) with pilots and drivers - Interferes with vision up to 525 ft (160 m) away. Can be a distraction up to 1 mile (1.6 km) away. NEVER point any laser towards aircraft or vehicles; it is unsafe and illegal.Safe use guidanceClass 2 lasers are considered safe foraccidental eye exposure. Do not look orstare into beam. Do not aim at aircraft.This is not a toy. Always supervise children.Read and follow all instructions in this manual carefully, and retainthis manual for future reference.Do not use this instrument in any manner inconsistent with these operating instructions or under any conditions that exceed the environmental specifi cations stated.This instrument is not user serviceable. For technical assistance, contact the sales organization from which you purchased the product.In order to comply with EU Directive 2012/19/EU on Waste Electrical andElectronic Equipment (WEEE): This product may contain material which couldbe hazardous to human health and the environment. DO NOT DISPOSE of thisproduct as unsorted municipal waste. This product needs to be RECYCLED in accordance with local regulations, contact your local authorities for more information. Thisproduct may be returnable to your distributor for recycling - contact the distributor for details.1.0 OVERVIEW (1)2.0 FEATURE LOCATIONS (1)3.0 LCD DISPLAY SYMBOLS (2)4.0 TAC3 SPECIFICATIONS (3)5.0 INPUT / OUTPUT (7)6.0 PREPARATION FOR MEASUREMENT (8)6.1 Non-Contact Preparation (8)6.2 Direct Contact Preparation (8)6.3 Connecting External Sensors (9)7.0 TAKING MEASUREMENTS (10)7.1 Non-Contact Measurements (10)7.2 Direct Contact Measurements (10)8.0 TACHometer Mode (11)8.1 TACHometer Setup (11)8.2 TACHometer Operation (13)9.0 RATE Mode (13)9.1 RATE Setup (14)9.2 RATE Operation (16)10.0 TOTALizer Mode (17)10.1 TOTALizer Setup (17)10.2 TOTALizer Operation (20)11.0 TIMER Mode (21)11.1 TIMER Setup (21)11.2 TIMER Operation (22)12.0 BATTERIES (23)13.0 CLEANING (24)14.0 OPTIONS /ACCESSORIES (24)11.0 OVERVIEWThe Model TAC3 is a 32 function tachometer/ratemeter, totalizer/counter, and timer. It is programmable to read in English or Metric units. An input socket accepts remote sensing devices and an output socket allows for pulse output to external indicating devices. The Model TAC3 can be tripod mounted and “Locked-On” for accurate and continuous operation. This tachometer also stores minimum, maximum and last measurement in memory.2.0 FEATURE LOCATIONSAVOID EXPOSURE - LASER BEAM IS EMITTED FROM THIS APERTURE3.0 LCD DISPLAY SYMBOLS24.0 TAC3 SPECIFICATIONSLaser Specifi cations:Classifi cation: Class 2 (per IEC 60825-1:2014)This product complies with IEC 60825-1 Ed.3 and 21 CFR 1040.10 and 1040.11 except for deviations pursuant to Laser Notice No. 50 of June 2007.Maximum Laser Output: <1mWPulse Duration: ContinuousLaser Wavelength: 650 nmBeam Divergence: > 1.0 mradBeam Diameter: 4 x 7 mm typical at 2 metersLaser Diode Life: 8,000 operating hours MTBF (1 year warranty) Non-Contact Specifi cations:Ranges:RPM 5 – 200,000RPS 0.084 – 3,333.3RPH 300-999,990Resolution:Fixed: 1 (10 above 99,999)Auto-ranging: 0.001 to 1.0 (10 above 99,999) Accuracy:±0.01% of reading or resolution limitOperating Range:up to 25 feet (7.62 m) or up to 70 degrees offperpendicular to TAC-5 tape targetContact Specifi cations using optional Remote Contact Assembly: Range:Contact Tips: 0.5 to 20,000 RPM10 cm / 12-inch Wheel: 0.5 to 12,000 RPMResolution:Fixed: 1 (10 above 99,999)Auto-ranging: 0.001 to 1.0 (10 above 99,999) 3Contact Specifi cations (continued):Accuracy:Revs: ±0.05% of reading (RPM) or resolution limit(with no slippage)Linear: ±0.5% of reading or resolution limit (with noslippage)Contact Measurements Ranges:TACHOMETER:Revolutions per Minute (RPM) 0.5 to 20,000 RPMRevolutions per Second (RPS) 0.0833 to 333.33 RPSRevolution per Hour (RPH) 30 to 999,990 RPH RATES: Wheel Circumference:Inches per Second 10 cm:0.033 to 1312.3 IPS12 in:0.100 to 2,400.0 IPSInches per Minute 10 cm: 1.969 to 78,740 IPM12 in: 6.000 to 144,000 IPMInches per Hour 10 cm:118.11 to 999,990 IPH12 in:360.00 to 999,990 IPHFeet per Second 10 cm:0.003 to 109.36 FT/S12 in:0.009 to 200.00 FT/SFeet per Minute 10 cm:0.164 to 6,561.7 FT/M12 in:0.500 to 12,000 FT/MFeet per Hour 10 cm:9.843 to 393,700 FT/H12 in:30.000 to 720,000 FT/HYards per Second 10 cm:0.001 to 36.453 YPS12 in:0.003 to 66.667 YPSYards per Minute 10 cm:0.055 to 2,187.2 YPM12 in:0.167 to 4,000.0 YPM4Contact Measurements Ranges (continued):RATES: Wheel Circumference:Yards per Hour 10cm: 3.281 to 131,233 YPH12 in:10.000 to 240,000 YPHMiles per Hour 10 cm:0.002 to 74.564 MPH12 in:0.006 to 136.36 MPHCentimeters per Second 10 cm:0.084 to 3,333.3 CM/S12 in:0.21 to 3,048.0 CM/SCentimeters per Minute 10 cm: 5.000 to 200,000 CM/M12 in:15.240 to 365,760 CM/MCentimeters per Hour 10 cm:300.00 to 999,990 CM/H12 in:914.40 to 999,990 CM/HMeters per Second 10 cm:0.001 to 33.333 M/SEC12 in:0.003 to 60.960 M/SECMeters per Minute 10 cm:0.050 to 2,000.0 M/MIN12 in:0.153 to 3,657.6 M/MINMeters per Hour 10 cm: 3.000 to 120,000 M/H12 in:9.144 to 219,460 M/HTOTALIZER:Counts: 0 to 999,999Scale Totals in Inches, Feet, Yards, Centimeters or MetersInput: Internal or External optics or linear contact wheel Timer Specifi cations:Minutes:Seconds.Tenths to 99:59.9Accuracy: ±0.2 secondResolution: 0.1 second5Batteries:Battery Life:Edge:Pulse Output:Dimensions:Weight:This product is designed to be safe for indoor use under the following conditions (per IEC61010-1).Installation Category II per IEC 664Pollution Degree Level II per IEC 664Temperature: 40 °F to 105 °F (5 °C to 40 °C)Humidity: Maximum relative humidity of 80% for temperatures up to88 °F (31 °C) decreasing linearly to 50% relative humidityat 100 °F (40 °C). Humidity non-condensing.Specifi cations subject to change without notice.675.0 INPUT / OUTPUTor Input Connector Detail (Stereo plug)Output Connector Detail (Mono plug)86.0 PREPARATION FOR MEASUREMENT6.1 Non-Contact PreparationFor Internal operation (Red laser) or External operation using optional Remote Optical Sensor (TAC2K-91).6.2 Direct Contact PreparationFor External operation ONLY using optional Remote Contact Assembly.1. Clean ShaftAs small as 1/8” wide on side or radius edge2. Apply 1/2” square TAC-5 Refl ective tapeFor Small Shafts:Select and install contact option:1. Contact Tip (Convex tip shown. Use Concave tip for small shafts.)ats96.3 Connecting External Sensorssecurely into fl at on shaft.screw.2. 10 cm Wheel3. 12 inch WheelOR Remote Optical Sensor(TAC2K-91)Remote Contact Assembly(shown with optional 12 inch wheel)7.0 TAKING MEASUREMENTS7.1 Non-Contact Measurements7.2 Direct Contact Measurements10Hand-heldLaserExternal Sensor (TAC2K-91 shown)ORLightWARNING: Making measurements in direct contact with rotating equipment can be dangerous. Keep all loose clothing and hair away from exposed moving machinery. Keep the hand holding the instrument well behind the back end of the Remote Contact Assembly. Properly replace all machinery guards after completing measurement. Do not use for rotation greater than 20,000 RPM.to Remote Contact Assemblyfrom TAC3from TAC3RotationalLinear(Use concave tip for small shafts)ONLY USE MODERATE PRESSURE111.Turn Power ON2.Enter Setup3.Enter selection of Mode 4.Select TACH Mode 5.Save and advanceORRepeat until TACH displayedLast Mode selected isdisplayed1a. To toggle LockOn/OffLast Units selectedare displayed8.0 TACHometer ModeTachometer measures speed or linear rate with respect to time. Time intervals are sceonds, minutes, or hours. Rotational speed can be measured in Revolutions (Revs) per second, per minute, or per hour. The most common measurement is RPM or Revs per minute using the optical tachometer mode.8.1 TACHometer Setup12NONE , 1, 2 or3ORRepeat until desired decimalplaces displayedUnit will remember these settings (including lock on/off) even if turned off and back on.ORRepeat until desired Units displayedDONE , then Unitsselected6.Enter selection of Units7. Select Units8.Save and advance9.Enter selection of number of decimal places10. Select decimalplaces11. Save andadvance12. Exit Setup – Ready tomeasureRPS , RPM orRPH138.2 TACHometer OperationMeasureRecall MaxRecall Min If unit Locked on:Power OFFMax SpeedAutomatic after 90 seconds if unit not Locked onORPress and holdResets Max/MinOR9.0 RATE ModeMeasurement of units in addition to Revs requires the attachment of the Remote Contact Assembly and tips/wheels (TAC3-K Only). With this attachment, the unit can measure RATE inputs-revs, inches, feet, yards, centimeters and meters either per second, per minute or per hour, as well as miles per hour.NOTE: External Remote Contact Assembly must be inserted into inputsocket.149.1RATE Setup1.Turn Power ON2.Enter Setup3.Enter selection of Mode 4.Select RATE Mode 5.Save and advance6.Enter selection of UnitsORToggles between RATE and TOTAL . Select RATE .Last Mode selected isdisplayed1a. To toggle LockOn/OffRotational: C RPS , C RPM or C RPHEXTRN , then scrolling message, then lastUnits selected, FT/S , FT/M , FT/H , YPS , YPM , YPH , MPH , CM/S , CM/M , CM/H , M/SEC , M/MIN , M/H15NONE, 1, 2 or3OR Repeat untildesired decimalplaces displayedOR Repeat untildesired Unitsdisplayed8a. Enterselection ofWheel8b. SelectWheel8c. Save andAdvanceOnly for Linear Units:OROR Togglesbetween 10CMand 12INLast Wheelselected isdisplayed7. Select Units8. Save andadvance9. Enter selectionof number ofdecimal places10. Select decimalplaces11. Save andadvanceRATE Setup (continued):16Unit will remember these settings (including lock on/off) even if turned off and back on.DONE ,USE CONTACT TIP or [wheel selected],then Units selectedORPress and hold12. Exit Setup – Ready tomeasureMeasureRecall MaxRecall MinIf unit Locked on:Power OffResets Max/Min9.2RATE OperationAutomatic after 90 seconds if unit not Locked onOR171.Turn Power ON2.Enter Setup3.Enterselection of Mode 4.Select TOTALModeORRepeat until TOTAL displayed.Last Mode selectedis displayed1a. To toggle LockOn/OffDifferent messages displayed for Internal or External operation.Internal optics or External optical sensor (TAC2K-91):External Remote Contact Assembly:, then scrolling Last Units10.0 TOTALizer ModeTotalizer accumulates input on an ongoing basis, In the simplest form the unit acts as an optical counter, incrementing the display each time an input pulse is sensed. Using the remote contact assembly with various tips and wheels (TAC3-K only), the unit can totalize in revs, inches, feet, yards, centimeters, and meters.10.1 TOTALizer Setup185.Save and advance6.Enterselection of Units7. Select Units8.Save and advanceRotational: REV Linear: INCH, FEET, YARDS , CM , METER Different options displayed for Internal or External operation.Internal or External:External Remote Contact Assembly:COUNTOnlyORRepeat until desired Units displayed Linear UnitsOR8a. Enter selectionof Wheel8b. Select Wheel8c. Save andAdvanceOnly for Linear Units:ORToggles between 10CM and 12INLast Wheel selected isdisplayed19TOTALizer Setup (continued):NONE , 1, 2 or3ORRepeat until desired decimalplaces displayedUnit will remember these settings (including lock on/off) even if turned off and back on.DONE , then COUNTDONE ,USE CONTACT TIP or [wheel selected],then Units selectedUnits = COUNT :Rotational/Linear Units:9.Enter selection of number of decimal places10. Select decimalplaces11. Save andadvance12. Exit Setup – Ready tomeasureMeasureRecall Max or Min Recall Time in secondsIf unit is Locked on: Power Offuntil the last inputsignal measured.ORPress and holdResets Max/Min, Total andMeasurement Time10.2 TOTALizer OperationAutomatic after 90 seconds ifunit not Locked onORNOTE: Pressing once before 90seconds will keepmeasurements inmemory and thedisplay turned onlonger.OR20211.Turn Power ON2.Enter Setup Mode 3.Enter selection of Mode 4.Select TIMER Mode 5.Save and advanceORRepeat until TIMER displayed Last Mode selectedis displayed 1a.To toggle LockOn/OffLast Units selected are displayed11.0 TIMER ModeAccumulates time in minutes, seconds, and tenths of a second. There are two modes of operation. The Manual mode operates like a stopwatch, the timing period being started and stopped by the user. The Auto mode can be stopped and started by the user or a piece of refl ective tape on objects. The user can freeze the display-and view/record a LAP time-at any time without affecting the count.11.1TIMER Setup226.Enter selection of Timer function 7.Select Timer function 8.Save and advance 9. Exit Setup – Ready to measureMeasure:ResetUnit will remember these settings (including lock on/off) even if turned off and back on.DONE , then UnitsselectedManualAutoEach press toggles Start and StopStart and Stop triggered byexternal remote optical sensor (TAC2K-91) or internal opticsWith Timer stopped - Resets time to 00:00.0OR 11.2TIMER OperationMAN orAUTOORToggles between Manual andAutoWith Timer running - Stops at elapsed time to date.To continue, press again.If Timer stopped -Automatic after 90 seconds(if unit not Locked on)Automatic after 99:59.9ORLapPower OffORTIMER Operation (continued):12.0 BATTERIES2313.0 CLEANINGTo clean the instrument, wipe with a damp cloth using mild soapy solution.14.0 OPTIONS /ACCESSORIESTAC2K-91Remote Optical Sensor, includes mounting bracket and 8 foot [2.5 m] cableTAC-5Refl ective Tape, 5 foot [1.5 m] roll, ½ inch [13 mm] wide TAC3-1 Remote Contact Assembly, includes 6 foot [1.8 m] cable, convex and concave tips and 10 cm contact wheel24Printed in the U.S.A.Copyright 2017, all rights reserved1071-4838-6121071-4838-612E-0717。
MESUTRONIC(金属探测器)通用操作手册

INDEXIntroduction介绍 (3)Safety安全 (3)Operation操作 (3)Operating principle 工作原理 (4)Actuation 投入运行 (5)Installation 安裝 (8)Electronic 电子 (8)Detector检测器 (8)Power supply电源 (9)Operation操作 (10)Adjustments调节 (11)Overview operating levels操作面一览 (11)General概述 (13)Operating level 1操作面1 (14)Operating level 2操作面2 (15)Operating level QM操作面QM (19)Maintenance维护 (21)Electronics电子部分 (21)Electrical电气部分 (21)Detector探测器 (21)Cleaning清洁 (21)Faults and Problems故障和问题 (24)General概述 (24)Erorr messages and notice出错信息和提示 (24)Electrical Power电源 (27)Service服务 (28)Technical Data技术资料 (28)Connections连接 (29)Dear customer,to begin with, we would like to thank you for your confidence in our metal detection system. .首先,非常感谢您对我们公司的金属检测系统的信任。
Prior to switching the system on, please read the user manual completely as this provides you with the expertise necessary for optimum operation and adjustment of the system according to your requirements. 激活该系统前,请与专家一起完整阅读这本用户手册,使该系统能够根据您的需要,达到最优操作运行和调节。
Dwyer 160标准探管系列产品说明说明书

3-5/8 [92.08]
Ø1/4 [6.350]
2-35/64 [64.69]
STATIC PRESSURE (8) Ø.040 [1.02] HOLES EQUALLY SPACED
Ø1/4 [6.35]
STATIC PRESSURE CONNECTION
TOTAL PRESSURE Ø1/8 [3.18] HOLE
No. A-397 Step Drill. For fast, convenient installation of Pitot tubes in sheet metal ducts. No center punch needed; automatic de-burring. Drills six sizes from 3/16˝-1/2˝ in 1/16˝ increments.
TOTAL PRESSURE CONNECTION
1/4 COMPRESSION FITTING
COUPLING SUPPLIED PIPE SUPPLIED
BY CUSTOMER
BY CUSTOMER
2-35/64 [64.69]
STATIC PRESSURE
NOTE: CUSTOMER MUST SUPPLY
Standard 5/16˝ Diameter
Model Insertion Length Price
160-8 8-5/8˝
$56.50
160-12 12-5/8˝
58.00
160-18 18-5/8˝
62.50
160-24 24-5/8˝
65.00
160-36 36-5/8˝
73.50
160-48 48-5/8˝
克兰特克特 运动检测技术说明书

Clantect: The Company.Clantect was founded by Professor Steve Daley and Dr Ilias Zazas, who are world leading experts in the field of sound and vibration. In partnership with Southampton University and the Institute of Sound & Vibration Research, Clantect’s ‘Motion Detection T echnology’ has set new standards for accuracy, reliability, flexibility and ease of use, in the detection of clandestine presence on vehicles. Clantect: The Motion Detection Technology.Clantect’s MDT goes way beyond the limitations of other forms of scanning technologies, which are inadequate in the application of the detection of humans in heavy goods vehicles. Equally, manual searches of heavy goods vehicles are both impractical and inefficient - they would involve too many people and would require the lengthy removal of the goods and cargo - it would take too much time to complete this for each vehicle (causing massive traffic hold ups), and, most important, manual searches are not thorough enough and will often miss hidden human presence. The solution is Clantect’s Motion Detection Technology.Clantect’s MDT works by the detection of any ‘vehicle-induced’ vibration, including even the faintest of movements, such as the agitated heartbeat of a human occupant. The system is able to execute and complete a ‘sensory test’, which will detect a hidden intruder very quickly.Clantect’s MDT is deployed and controlled by a ruggedised Computer T erminal, which is positioned in the inspection area for the vehicles. Highly sensitive sensors (normally 2) are attached to the side of the vehicle and perform a ‘sensory test’. If there is any sound and movement detected, the system provides an automated alert to conduct a search of the vehicle. The whole process is automated: very fast and very simple. The Clantect Software manages the processes, capturing and analysing the results of each ‘sensory test’, as well as compiling key data, such as vehicle number plates. There is also the capability for online 4G connectivity to a remote host computer , for data consolidation and management information reporting.Clantect: The System Highlights.• High Accuracy: Clantect uses advanced algorithms, signal processing and systems logic to eradicate any background interference (such as vibration from passing traffic). This ensures that the readings are interpreted correctly. So any even the faintest noise or vibration, emanating from the vehicle, will be detected, such as an agitated heartbeat. Clantect’s highest performing accuracy has been validated by independent authorities.• Ruggedised Durable Equipment: Designed to be used in ‘harsh’ outdoor conditions, e.g. encased in a protective metallic frame, and with MIL-Spec connectors.• Rapid Throughput Times: A complete ‘sensory test’ of a vehicle can be completed in approximately, only a minute. So the daily operations of the border controls and gate stations, particularly traffic flows, are not adversely impacted. • Ease of Use and Operation: The sensors are quickly and easily attached to the exterior of the vehicle, and with no further operator intervention, the system automatically executes a ‘sensory test’ of the vehicle. The Computer T erminal is menu-driven and intuitive, with very minimal data entry: it’s automated from Start to Finish.• Multi-Vehicle Format Configuration: The system can be utilised for different types of heavy goods vehicles: trucks, roll-on/roll-off containers, coaches, cement mixers, tankers, etc.• Automatic Data Capture and Update: The results of the scan are automatically captured and processed, i.e. no manual input nor intervention required. Quick & Simple and Ready for the next vehicle.• Vehicle Number Plate Recognition: The number plates of all vehicles are automatically and instantly recorded on the system. This provides critical data for operational reports (vehicle tracking) and for auditing purposes. • Remote Data Management & Communications: All Clantect terminals can transfer data to and from head-office organisations via 4G networks, both nationally and internationally. This means a rapid and easy consolidation of up to date information into the head office host computers. It also enables the Head Office to access all Clantect T erminals remotely, for operational support and diagnostics.• Multiple Vehicle Scanning: The Clantect system can provide for multi-vehicle scanning from a single terminal, particularly useful for the larger transport inspection bays.• Multiple Language Capability: The system is available in most languages, and is already deployed in multiple countries.• Sensor Health Check & Validation: The Clantect system provides for an automated sensor health check, with built-in alarm and audit reports. This ensures that the sensors are functioning correctly, and highlights any irregularities.• Geophone Testing Station (GTS) module: This is an additional terminal which manages and extends the life-cycle of the Clantect sensors and cable components. This executes tests on the accuracy and throughput of the sensors, and provides management information data, highlighting any key performance issues. • CE Certified: The Clantect system has CE Certification, a key quality assurance.Sea Ports - Military Bases - Research Facilities - Industrial ComplexesRail & Freight T erminals - Prisons and Penitentiaries - Nuclear & Hazardous Waste Plants.Clantect LtdInstitute of Sound and Vibration ResearchSouthampton, SO17 1BJ, UK Phone: +44 (0) 23 8059 3043Email:*****************www Ga t e dC o m p o un ds B or d e r C r o s s in g s R es t r i c t e d A re a s H ig hS e c u r i t y F a cil i t ie s P r i s o n sP o r t s。
XPLORER-TX TS 探测器系列商品说明书
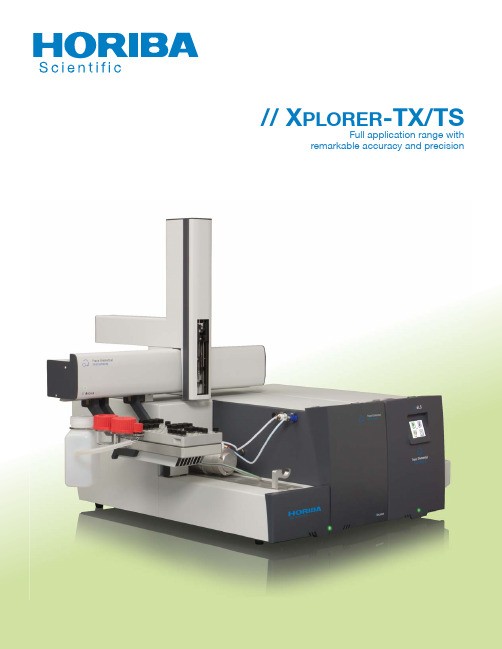
// X PLORER-TX/TSFull application range with remarkable accuracy and precisionKey Features Include:• Ultra-low detection limits, high stability and reliability due to the temperature controlled detectors and feedbackcontrol loop.• Compact design, with the smallest footprint in the market.• Short start-up time. (Less than 15 minutes from standby mode).• Fast and precise measurement of liquids, solids, and gases (including LPGs).• Automation available for each type of measurement. • Intuitive user interface and operational software.• Simultaneous analysis of halogens and sulfur.• Fast and easy switching between modules, resulting in high productivity.• Complies with international standards like: ASTM, ISO, EN and IP .• Fully automated creation of calibration curves from a single stock solution with the optional A RCHIE autosampler.• Fast generation of sample lists and application methods.• Low maintenance due to optimized combustion and the proper conditioning of the produced gases.Con fi guration: X PLORER with GLS*The X PLORER -TX/TS is a microcoulometric combustion analyzer for the analysis of total halogens and total sulfur. The small footprint allows it to blend into every laboratory environment, whether it is in R & D, a re fi nery, a chemical or petrochemical application. This elemental analyzer will perform well. It is robust, precise and ideal for harsh testing environments.Speed & performance with minimal footprintAny Sample MatrixThe XPLORER-TX/TS combustion analyzer handles solid, liquid, gas and LPG samples. Changing from a liquids & gas module to the solids module has never been easier. With the push of one button, the liquids & gas module retracts automatically from the furnace. No clamps or manual locking. The change can be made in less than a minute. Simply choose the pre-loaded sample calibration list and run your samples.Automated or Semi-automatedIn terms of system automation, the choice is yours; semiautomated or fully automated. Select between manual operation for a couple of samples per day or round the clock operation with the autosampler. If the analyzer is operated manually there are two options. For the introduction of liquid samples, there is an integrated automatic syringe driver. It offers full control over the desired volume and speed of injection. For the introduction of solid samples, there is an integrated, software controlled boat drive.When operating the analyzer in full automation, the ARCHIE robotic XYZ auto sampler handles all liquid samples from 105 up to 210 postions. It extracts the samples from 2 mL vials and is able to dilute and generate calibration check standards automatically as well as run routine samples. The GLS module is for the introductionof gas and LPG samples. Using the touch screen as the user interface it can be operated as a method driven gas sampler and also as a stand alone sample introduction unit.Solid samples can be introduced by the stackable NEWTON auto sampler, which simply utilizes gravity introduction for high sample throughput and low cost per analysis. Assorted sample cups are available for various applications. W orking with an auto sampler enhances the overall quality, saves time and signifi cantly reduces the use of spare parts.Higher Productivity through Accurate Analysis Coulometric determination of chlorine and sulfur isan absolute technique using Faraday constant, so no calibration is required. T he accuracy is automaticallyverifi ed using a control standard. The overall analysisof hydrocarbons at ultra-low concentrations offers unprecidented precision.Compliance and RegulationsThe instrument complies with, but is not limited to the following international standards:TX ASTM D4929ASTM D5194ASTM D5808ASTM D7457UOP 779TSASTM D3120ASTM D3246ASTM D3961ArchieIndustrial ApplicationsChemicals• Acetic Acid• Polypropylene & ethylene • Polycarbonate • Aromatics • Resins • Ole fi ns and para fi nes Re fi nery Products • Crude oil • Kerosene • Fuel oil • Gasoline • Diesel fuels • Catalyst • Naptha • Lubricants Gases and LPGs• Independant laboratories • Chemical laboratories • Petrochemical laboratories• Government institutions and research facilities • UniversitiesMeeting the T oughest Standards and RegulationsRegulatory organizations worldwide have set low levels of allowed sulfur concentration in organic fuel for the present and near future. Besides sulfur regulations, knowing the exact concentration of sulfur and chlorine in certain feed stocks has always been important for production processes in the re fi neries. During the re fi nery process organic chlorines combust and will form hydrochloric acid. This formation needs to be avoided to minimize corrosion in the re fi nery process. Therefore, the re fi neries need to monitor and control the total sulfur and total chlorine content in the crude oil feedstock.Reference MethodologyMicrocoulometry is a reference method for the determination of total sulfur content in light liquidhydrocarbons, gasoline, diesels and their additives. It is also the reference method for the determination of total chlorides in crude oil. Microcoulometry fully complies with international standards: ASTM, ISO, IP , and UOP .GLSThe next generation Gas & LPG sampling systemThe GLS is suitable for handling all types of pressurized gases and LPGsfor the analysis of chlorine and sulfur. The GLS combines seamlessly with the X PLORER combustion analyzer using the same software, and is also excellent with other combustion analyzers.A RCHIEThe robotic liquids auto samplerUnlike previous generation liquid samplers, the A RCHIE uses a 100 μL syringe to aspirate and seal the sample with utmost precision and at a controlled speed. The sample can then be introduced into a vertical liquid furnace or be injected in a boat introduction module at controlled speed, forming a perfect complement to the X PLORER analyzer.N EWTONThis auto sampler measures up to 60 solid samples unattendedThe N EWTON is a stackable auto sampler. Housing trays for 20 samples, it is designed for a quick, accurate introduction of solid samples into the X PLORER . It is a user friendly system that is capable of running one, two or three trays of samples in succession unattended. The clean cups which are retracted from the combustion zone, are stored in a stainless steel compartment ready to be reused.Auto SamplersHow does the Chlorine Cell work?Samples are introduced with the appropriate module,into a furnace, where the sample is oxidized at high temperature. The combustion gas, containing halide ions, is led into a sulfuric acid scrubber for a rapid water and interferent removal. The dried and clean gas is led into the temperature controlled titration cell, where the halide ions react with silver ions, present in the titration cell.The amount of charge (the integral of the regeneration current over the measuring time) used to regenerate the lost silver ions, is directly related to the halogen content of the sample.Combustion:R-X + O2∙ HX + CO2+ H2OTitration Cell:HX + Ag+∙ H+ + AgX Ag ∙ Ag+ + e-How does the Sulfur Cell work?Samples are introduced, with the appropriate module, into a furnace, where the sample is oxidized at high temperature. The combustion gas, containing sulfur dioxide (SO2), is led into a sulfuric acid scrubber for rapid water and interferent removal. The dried and clean gas is led into the temperature controlled titration cell, where the sulfur dioxide reacts with T ri-iodine, present in the titration cell.The amount of charge (the integral of the regeneration current over the measuring time) used to regenerate the lost T ri-iodine, is directly related to the sulfur content of the sample.Combustion:RS + O2∙ CO2+ SO2+ H2OTitration cell:SO2+ I3- + H2O ∙ SO3+ 3I- + 2H+3I-∙ I3- + 2e-Sulfur CellChlorine CellHORIBA INSTRUMENTS, INC.9755 Research Drive Irvine, California 92618800-446-7422/us/oil ******************• The contents of this catalog are subject to change without prior notice, and without any subsequent liability to this company.• The color of the actual products may differ from the color pictured in this catalog due to printing limitations.• It is strictly forbidden to copy the content of this catalog in part or in full.• All brand names, product names and service names in this catalog are trademarks or registered trademarks of their respective companies.cam0916X PLORER-TX/TS System Speci fications。
Panametrics-NDT Model 25DL PLUS 超声波精密厚度尺测试手持设备说明书
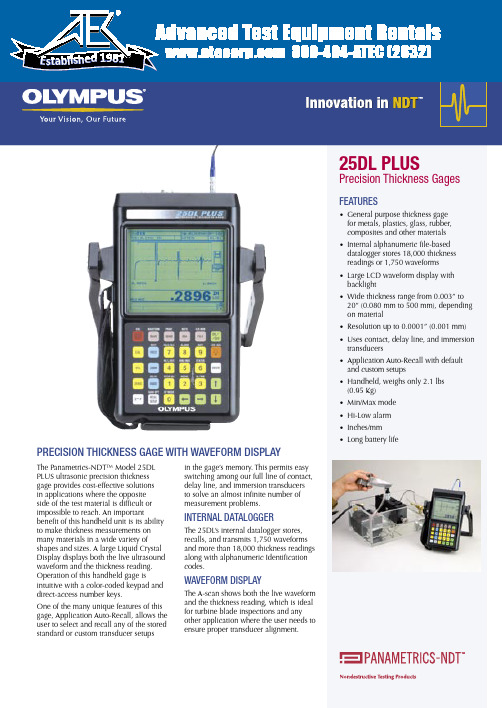
MEASUREMENTSMode 1: Time interval between excita-tion pulse and first backwall echo. Using contact transducers.Mode 2: Time interval between the first interface echo after the excitation pulse and the first backwall echo. Using delay line or immersion transducers.Mode 3: Time interval between successive backwall echoes following the first inter-face echo after the excitation pulse. Using delay line and immersion transducers.Thickness Measurement Range: Steel: 0.006 - 20” (0.15 - 500 mm) Plastic: 0.003 - 2”(0.08 - 50 mm)Thickness range depends on material, transducer, surface condition and setup selected, extended thickness ranges are possible using custom setups.Material Velocity Range: 0.02000 - 0.55110 inch/μS (0.5080 - 13.9979 mm/μS)Resolution, keypad selectable: LOW: 0.01” 0.1 mm STANDARD: 0.001” 0.01 mm HIGH: 0.0001” 0.001 mm Measurement Rate: 4, 8, 12, 16, or 20 measurements per second Transducer Frequency Range: 2.25 - 30 MHzThree Differential Modes: Standard and Percent: Thickness difference and percent difference between actual measurement and reference value. Rate Reduction: Display actual thickness and percent difference from setpoint. Both values can stored in the internal dataloggerMin/Max Mode: Works in conjunction with FAST Mode for rapid location of minimum or maximum thickness reading and associated waveformTwo Alarm Modes: 1) Standard Hi-Low 2) Previous thickness (Absolute or Per-centage). Both with audible and visual indicatorsApplication Auto-Recall: Automatically adjusts internal parameters and zero offset for a wide variety of transducers. Stores 25 standard transducer setups and up to 35 custom transducer setups Other Standard 25DL PLUS Features: Calibration Lock Mode, Internal Diagnostic Test Mode, Metric/EnglishDISPLAYDisplay: Liquid Crystal Display with backlight. Contrast keypad adjustable. Display area 4.0 x 3.39 inch (102 x 86 mm) Backlight: Backlit electroluminescent display with Power Save featureZoom Mode: Expands the horizontal span of the waveform to the minimum range associated with each transducer and au-tomatically centers the measured echoes.Freeze Mode: Freeze and Un-Freeze live A-scan with thicknessDisplay Hold/Blank: Display blanks after last reading or holds readingRectification: RF, half wave positive or negative, and full waveWaveform Display Range and Delay Control: The horizontal span of thewaveform is set at selected intervals with a fully adjustable delayPOWER SUPPLYBattery: 6 V Rechargeable NiCad battery pack. Optional replaceable alkaline “AA” cellsBattery Life: 30 hrs nominal (normaloperation), Nicad. Optional alkaline “AA” cells approximately 70 hours Battery Charge Time: 2 hours using provided chargerCharger: External wall plug-in charger/AC Adapter for 100/115/230 VAC inputs Auto Power On/Off, Low Battery Indica-torGENERALKeypad: Sealed color-coded keypad with tactile and audible feedbackMulti-Language Display: English, French, German, and SpanishOperating Temperature:-10°C to +50°C (+14°F to 122°F)Size: L 9.375” x W 5.45” x D 1.5”, L 238 x W 138 x D 38 mm Weight: 2.1 lbs (0.95 Kg)INTERNAL DATALOGGERIdentify, store, recall, clear, and transmit thickness readings and gage setup infor-mation via the full duplex RS-232 Serial Port. Baud rate, word length, stop bits, and parity are adjustable from keypad.Maximum # of Stored Values: Standard: 18,000 thickness readings or 1,750 waveforms with thickness. Upgrade 1: 36,000 thickness readings or 3,400 waveforms with thickness.Upgrade 2: 54,000 thickness readings or 5,100 waveforms with thickness.Location Codes: 8-character file name plus 16-character alphanumericlocation code input. Multiple Comments per locationFile Structures: 7 standard or custom application-specific file structures Reports: On-gage reporting of: Summary with statistics, Min/Max with locations, and File Comparison. On-screen Com-parison of current and previous readings On-board Statistics Calculator:Permits statistical reporting directly to Serial PrinterSTANDARD INCLUSIONSModel 25DL PLUS Digital Ultrasonic Multi-Mode Thickness Gage, AC or Bat-tery Operation, 50-60 Hz, with Internal Alphanumeric Datalogger. Including: Universal Quick Charger/AC Adapter, Transducer Cable, Test Block, Couplant, RS-232 I/O Cable, Carrying Case, Instruc-tion Manual, Two Year Limited WarrantyOPTIONAL ACCESSORIES36DLP/SPC/KIT Protective Pouch with Neck StrapPlus/RPC Rubber Boot with Gage Stand Win25DL PLUS Interface Program 25DLP/EW Extended Limited Warranty, 3rd Year2214E† 5-Step Test Block, 1018 steel, English Units: .100”, .200”, .300”, .400”, .500”2213E† 5-Step Test Block, Aluminum, English Units: 100”, .200”, .300”, .400”, .500”26DLPLUS/HDC Heavy Duty Shipping Case†Test Blocks are available in metric units.Printed 9/2005© 2005 Olympus NDT, All Rights Reserved.*All specifications are subject to change without notice.Panametrics, Panametrics-NDT and the Panametrics-NDT logo are trademarks of Panametrics Inc.Lexan is a trademark of General ElectricOther company or product names mentioned in this document may be trademarks or registeredtrademarks of their respective companies25DL PLUS SPECIFICATIONS*Olympus NDT, Inc.48 Woerd Ave, Waltham, MA U.S.A.TEL 781-419-3900 • 800 225-8330 in North America e-mail:************************。
Steinel SensIQ EVO 动感探测器 白色- 使用手册说明书

EAN 4007841 029562Article number 029562infrared sensor 3 x100°3 zones scalable2-20m2500 W max. (LED-ready)IP54 2 - 2000 lux 5 sec - 15 min ideal 2 - 5 m energy savingmanufacturer'swarranty steinel-professional.de/garantieCE Function descriptionKing of the infrared motion detectors. The revolutionary sensIQ for indoors and out, ideal for building entrances, loading bays, installation height up to 5 m, quadruple sensor system for optimum coverage over a 300° detection angle, 20 m range (tangential), metre-precision reach setting in 3 different directions, heavy-duty relay for high switching capacity. Remote control and corner wall mount bracket included.Technical specificationsDimensions (L x W x H)172 x 113 x 144 mmWith motion detector YesManufacturer's Warranty 5 yearsSettings viaRemote control, Potentiometers,Smart RemoteWith remote control YesVersion whitePU1, EAN4007841029562Type Motion detectorsApplication, place Indoors, OutdoorsApplication, roommulti-storey / underground car park,outdoors, warehouse, front door, allround the building, courtyard &driveway, IndoorsColour whiteColour, RAL9010Includes corner wall mount YesInstallation site wall, ceiling, cornerLED lamps > 2 W < 8 W250 WLED lamps > 8 W500 WCapacitive load in μF176 µFTechnology, sensors passive infrared, Light sensorMounting height2,00 – 5,00 mMounting height max.5,00 mOptimum mounting height 2 mDetection angle300 °Angle of aperture180 °Sneak-by guard YesCapability of masking out individualsegmentsYesElectronic scalability NoMechanical scalability YesReach, radial r = 4 m (42 m²)Reach, tangential r = 20 m (1047 m²)Switching zones1360 switching zoneshttps://www.steinel.deEAN 4007841 029562Article number 029562 Technical specificationsInstallation Surface wiring, Wall, Ceiling, corner IP-rating IP54Ambient temperature-20 – 50 °CMaterial PlasticMains power supply220 – 240 V / 50 – 60 Hz Switching output 1, resistive2500 WSwitching output 1, number ofLEDs / fluorescent lamps8 pcs.Switching output 1, floating NoFluorescent lamps, electronic ballast500 WFluorescent lamps, series-corrected1800 VAFluorescent lamps, parallel-corrected500 VALED lamps < 2 W100 W FunctionsNormal / test mode, Manual ON /ON-OFFTwilight setting 2 – 2000 lxTime setting 5 s – 15 Min.Basic light level function NoMain light adjustable NoTwilight setting TEACH YesConstant-lighting control NoInterconnection YesType of interconnection Master/master Interconnection via CableAccessoriesEAN 4007841 009151Remote control Smart RemoteEAN 4007841 007638Remote control RC9https://www.steinel.deEAN 4007841 029562Article number 029562Detection Zone Dimension DrawingLight without neutral conductor Light with neutral conductorConnection using two-circuit switch for manual and automaticConnection of 4-fold push-button coupler to DALI2 APC operationhttps://www.steinel.de。
additel 761 超高精度温度感測器数据表 说明书
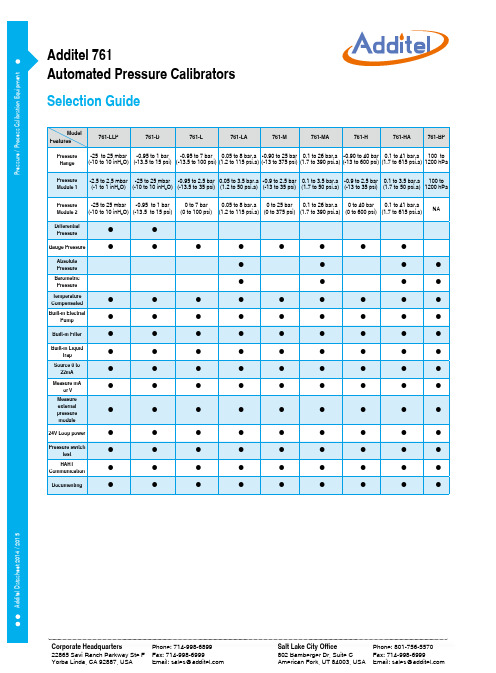
Selection Guide5124122014 2015Fully automated pressure calibrator with built-in pressure generator / controller to as high as 600 psi (40 bar) or as low as 0.01 Pa (0.00004 inH 2O)0.02%FS accuracy Dual pressure modulesBuilt-in filter and liquid trap with venting system prevents contamination of the calibrator Portable (12.4 lb)OVERVIEWWith a built-in high performance electronic pump and precision pressure controller, the 761 series portable automated pressure calibrators provide a turnkey solution for calibration of gauges, transmitters, and switches both in the field and in the laboratory. In a portable package, this calibrator can automatically generate pressures from 90% vacuum to 600 psi (40 bar) with 0.005% FS pressure control stability and 0.02% FS accuracy. To improve the calibrator accuracy, two pressure modules with differing ranges are built-in and integrated with the internal pump and controller.The 761-LLP is specially designed for low pressure calibration, and pressures can be set to as low as 0.01 Pa (0.00004 inH 2O) with a control stability better than 0.05 Pa (0.0002 inH 2O).The 761-BP is designed for barometric gauge calibration. With a quartz pressure sensor, the accuracy of 761-BP can achieve 0.01%FS accuracy.With optional external pressure modules (160 series), the 761 can measure pressures up to 10,000 psi (700 bar) with 0.025%FS accuracy. In addition to the pressure generation, control, and measurement capabilities, the 761 also features HART communication capability, supplies 24V loop power, and reads the current or voltage produced by the pressure transducers. The 761 is a state of the art automated pressure calibrator which brings automated pressure calibration to the field.2014 2015FEATURESPressure RangePressure generated by built-in pump and controlled automatically from 90% vacuum to 600 psi (40 bar)Pressure measured with external pressure modules (160 series) to 10,000 psi (700 bar)Accuracy (Fully temperature compensated)0.02%FS0.05%FS (ADT761-LLP)0.01%FS (ADT761-BP)Control Stability <0.005%FSADT761-LLP: < 0.05 Pa (0.0002 inH 2O)Contamination prevention systemBuilt-in filter and liquid trap with venting system prevent contamination of the calibratorSolid particles can be blocked by built-in filterA small amount of liquid can be collected by the built-in liquid trapBoth solid particles and liquid can be blown out through the venting systemAutomation and Test ProgramFully Automated pressure calibration Task preset and auto run Auto stepEasy to UseUser friendly interfaceIntuitive icon driven menu structureSourcing and Measuring electrical signalsMeasure mA with 0.01% RD + 1.5μA accuracy Measure V with 0.01% RD + 1.5mV accuracy Source/sink 0 to 22mA current24 VDC loop power supplied to pressure transmitter during testAutomated switch testMisuse ProtectionUp to 30V misuse protection on any two sockets Display7" LCD color screen (800X480)Documenting and data logging Task management capabilityInternal memory stores 200 tasks Download tasks and upload resultsHART Communication capability Support HART instrumentationRechargeable battery:Rechargeable battery with up to 8 hours operation between chargesLeak testing:Apply leak test to an external pressure system todetermine the magnitude of pressure variations due to leaksPipeline Protection: Special design the pipeline layout to avoid possible blockage and leakage Portable: Only 12.4 lbMulti Lingual InterfaceEnglish, German, French, Italian, Spanish, Portuguese, Simplified Chinese(Traditional Chinese, Japanese and Russian are available per request)NIST Traceable: NIST traceable calibration with data (included)2014 2015Task ManualBuilt-in User's ManualPressure gauge / transmitter / switch calibrationControl Stability <0.005%FS;ADT761-LLP: < 0.05 Pa (0.0002 inH 2O)Pressure ConnectionsPressure connection: ADT761-L/M/H/LA/MA/HAOne ADT100-761 Hose Test Kit with quick connector 1/8 BSP Female on calibratorTwo 1/4NPT(or 1/2NPT, 1/4BSP, M20×1.5) female hand-tight connectors on the external pressure manifold Pressure connection: ADT761-LLP/BP Stainless steel hose barb fitting External Pressure Module Connection Accepts Intelligent Pressure Module Electrical Connection0.156 inch (Ø4mm) banana sockets Documenting and data logging Task management capabilityInternal memory stores 200 tasks Download tasks and upload results Display7" LCD color screen (800×480)Display rate: 5 readings per secondResolution 4, 5 or 6 digit, user selectablePressure UnitsPa, kPa, MPa, psi, bar, mbar, inH 2O@4°C, mmH 2O@4°C, inH 2O@20°C, mmH 2O@20°C,inHg@0°C, mmHg@0°C, kgf/cm 2, and hPa (ADT761-BP)PowerBattery: Rechargeable Li-ion Polymer battery (included)Li-Battery working time: ~8 hours Recharge time: ~3 hoursExternal Power: 110/220V Power adapter (DC 27 V) (Included)Environmental Specification:Operating temperature: 32°F to 122°F (0°C to 50°C) Compensated Temperature: 32°F to 122°F (0°C to 50°C)Storage temperature: -20°C to 60°C Humidity: <90%, non-condensing European Compliance: CE MarkedCommunicationRS232 (DB9/F, environmentally sealed)Baud rate: 2400, 4800, 9600, 19200, 38400, 57600, 115200Data length: 7 Bits, 8 Bits Stop bit: 1 Bit, 2 Bits Address: from 1 to 121Dimension11.65" X 7.32" X 7.09"(296mm X186mm X180mm)Weight: 16.3 lb (7.4 kg)SPECIFICATIONSSPECIFICATIONSPressure Ranges* One year accuracy (including yearly stability) except ADT761-LLP which is 0.05%FS calibration accuracy and 0.05%FS yearly stability.* * Additel 761 calibrators support 160 series intelligent digital pressure modules that are available for gauge, vacuum and absolute pressure from -15 psi to 10,000 psi (-1 bar to 700 bar). Accuracy from 0.025%FS includes operation over 14°F to 122°F (-10°C to 50°C), one year stability and calibration uncertainty. For detailed specification refer to 160 series pressure modules datasheet.Electrical Measurement and Source Accuracy5124122014 2015ORDERING INFORMATIONPressure port type on External Pressure Manifold: N- 1/4NPT female N2- 1/2NPT female B- 1/4BSP female M-M20X1.5 female* Additel/Land software could be downloaded for free at Model Number。
Omega TQ514 Series数字旋转扭力传感器说明书

e-mail:**************For latest product manuals: TQ514 SeriesDigital Rotating TorqueSensors Shaft-to-Shaft ConfigurationShop online at User’s G ui d e***********************Servicing North America:U.S.A. Omega Engineering, Inc.Headquarters: Toll-Free: 1-800-826-6342 (USA & Canada only)Customer Service: 1-800-622-2378 (USA & Canada only)Engineering Service: 1-800-872-9436 (USA & Canada only)Tel: (203) 359-1660 Fax: (203) 359-7700e-mail:**************For Other Locations Visit /worldwideThe information contained in this document is believed to be correct, but OMEGA accepts no liability for any errors it contains, and reserves the right to alter specifications without notice.Thank YouThank you for purchasing one of Omega Engineering’s digital non-contact Rotary Torque Sensors. We know you will be satisfied with the performance and durability of our products.Intended UseModel TQ514 is a line of shaft-to-shaft rotary torque sensors for measuring the performance of electric drive motors, small DC motors, clutches, fans, etc.This line of sensors incorporates a Full Wheatstone Bridge and transmits the signal to a built-in receiver to produce a high level analog signal without the use of slip rings. Ball bearing supported shafts will provide long life and superior performance.Certificate of Conformance and Calibration TraceabilityOmega certifies that the products described herein meet the specifications and performance requirements described in the pamphlet.Calibration was performed with a test system utilizing a reference load cell or deadweights and an electronic indicator. The system was within current calibration requirements at the time of the test and is traceable to the National Institute of Standards and Technology (NIST).Omega Engineering calibration laboratory is accredited to ISO9000-2008InstallationInstall the sensor so that the label “Active End” is facing the place where torque is to be measured, i.e., to measure the torque applied by a wrench to a bolt, the “Active End” should face the bolt.Important: The sensor’s housing is NOT intended for use as a structural support.Do NOT place any loads on the housing.It is also important that the total stress on the shaft does NOT exceed σmax.To calculate the total stress, use the following equation:σ = A*F x + B*F y + C*F z + D*M x + E*M y + F*M zModel #CapacityExtraneous Load CoefficientsA &BCD &E FTorsional Spring Rate (in #/RAD)Shaft dia (inches)Key Width (inches)σ max (psi)TQ514-003 50 in-oz 1030.0 56.7 223.0 4300.0 182 TQ514-006 100 in-oz 678.0 26.1 102.0 2060.0 556TQ514-012 200 in-oz 435.0 18l0 70.5 997.01660TQ514-030 500 in-oz 214.0 10.9 42.7 380.0 7120 TQ514-062 1000 in-oz 104.0 7.3 28.5 175.0 22900 .375” Flats 18000 TQ514-100 100 in-lb 724.0 79.5 517.0 431.0 6900TQ514-200 200 in-lb 363.0 31.6 259.0 216.0 17300 .749” .1875”TQ514-500 500 in-lb 145.0 9.3 103.0 86.1 59000TQ514-1K 1000 in-lb 72.3 3.8 51.7 43.1 149000TQ514-1.5K 1500 in-lb 55.1 2.8 37.4 33.6 281000 TQ514-2K 2000 in-lb 35.9 2.4 25.7 21.4 378000 .999” .25”84000For example:If you are using a 200 in-lb. sensor to measure 100 in-lb. of torque applied by a 10 lb. fan six inches from the sensor,The total stress on the shaft would be:σ = B*F y + D*M x + F*M zσ = 363*10 + 259*60 + 216*100 = 40,770 psisince σ max for this model is 84,000 psi, this is acceptable.The sensor is supplied with a 10 pin mating connector. When wired, it will contain power in, encoder (when optioned), and analog signal output connections. Therefore, it is recommended that a cable t hat provides a shield around the analog signal wires be used. For example, a cable that provides shielded pairs would suffice, so that the analog signal wires can be shielded from the power supply and encoder wires. Ground the shield at the DAQ system that is monitoring this sensor.The signal output is electrically isolated from the power supply. This is done to prevent ground loops when the signal is fed into a single ended input. This may cause trouble for a differential input due to common mode drift. When using differential inputs, ground the negative input to an analog signal ground on the measuring DAQ system.Shunt CalibrationWhen the shunt pins on the sensor connector are shorted, the sensor electronics will apply a shunt to the strain gage bridge, and shift the voltage output from it’s current position. This is a real shunt of the bridge, not the star bridge shunt that so many rotary transformer systems use. Reference th e calibration sheet for the shunt calibration value. Remove this short to return the sensor to normal operation.Cleaning:The TQ514 is a brushless sensor, and therefore, the only wearing parts are the bearings. For the very low capacities, TQ514-003 and -006 units, these have oiled bearings and will periodically require a drop of high quality light machine oil on each. Only a drop is required. Clean environments will require a drop every 360 straight hours of use. Dirty or otherwise harsh environmen ts may require more frequent oiling. All other capacities have bearings that are permanently lubricated. Do NOT immerse the assembly in the solvent. This may damage the electronics inside the housing.Recalibration:To guarantee accuracy, all sensors should be recalibrated on an annual basis.OMEGA’s policy is to make running changes, not model changes, whenever an improvement is possible. T his affords ourcustomers the latest in technology and engineering.OMEGA is a trademark of OMEGA ENGINEERING, INC.© Copyright 2018 OMEGA ENGINEERING, INC. All rights reserved. T his document may not be copied, photocopied, reproduced, translated, or reduced to any electronic medium or machine-readable form, in whole or in part, without the prior written consent of OMEGA ENGINEERING, INC.FOR WARRANTY RETURNS, please have thefollowing information available BEFORE contactingOMEGA:1. P urchase Order number under which the productwas PURCHASED,2. M odel and serial number of the product underwarranty, and3. Repair instructions and/or specific problemsrelative to the product.FOR NON-WARRANTY REPAIRS, consult OMEGA for current repair charges. Have the following information available BEFORE contacting OMEGA:1. Purchase Order number to cover the COST of the repair,2. Model and serial number of the product, and 3. Repair instructions and/or specific problems relative to the product.RETURN REQUESTS/INQUIRIESDirect all warranty and repair requests/inquiries to the OMEGA Customer Service Department. BEFORE RET URNING ANY PRODUCT (S) T O OMEGA, PURCHASER MUST OBT AIN AN AUT HORIZED RET URN (AR) NUMBER FROM OMEGA’S CUST OMER SERVICE DEPART MENT (IN ORDER T O AVOID PROCESSING DELAYS). The assigned AR number should then be marked on the outside of the return package and on any correspondence.T he purchaser is responsible for shipping charges, freight, insurance and proper packaging to preventbreakage in transit.WARRANTY/DISCLAIMEROMEGA ENGINEERING, INC. warrants this unit to be free of defects in materials and workmanship for a period of 13 months from date of purchase. OMEGA’s WARRANTY adds an additional one (1) month grace period to the normal one (1) year product warranty to cover handling and shipping time. This ensures that OMEGA’s customers receive maximum coverage on each product.If the unit malfunctions, it must be returned to the factory for evaluation. OMEGA’s Customer Service Department will issue an Authorized Return (AR) number immediately upon phone or written request. Upon examination by OMEGA, if the unit is found to be defective, it will be repaired or replaced at no charge. OMEGA’s WARRANT Y does not apply to defects resulting from any action of the purchaser, including but not limited to mishandling, improper interfacing, operation outside of design limits, improper repair, or unauthorized modification. T his WARRANT Y is VOID if the unit shows evidence of having been tampered with or shows evidence of having been damaged as a result of excessive corrosion; or current, heat, moisture or vibration; improper specification; misapplication; misuse or other operating conditions outside of OMEGA’s control. Components in which wear is not warranted, include but are not limited to contact points, fuses, and triacs.OMEGA is pleased to offer suggestions on the use of its various products. However, OMEGA neither assumes responsibility for any omissions or errors nor assumes liability for any damages that result from the use of its products in accordance with information provided by OMEGA, either verbal or written. OMEGA warrants only that the parts manufactured by the company will be as specified and free of defects. OMEGA MAKES NO OTHER WARRANTIES OR REPRESENTATIONS OF ANY KIND WHATSOEVER, EXPRESSED OR IMPLIED, EXCEPT THAT OF TITLE, AND ALL IMPLIED W ARRANTIES INCLUDING ANY W ARRANTY OF MERCHANTABILITY AND FITNESS FOR A PARTICULAR PURPOSE ARE HEREBY DISCLAIMED. LIMITATION OF LIABILITY: The remedies of purchaser set forth herein are exclusive, and the total liability of OMEGA with respect to this order, whether based on contract, warranty, negligence, indemnification, strict liability or otherwise, shall not exceed the purchase price of the component upon which liability is based. In no event shall OMEGA be liable for consequential, incidental or special damages.CONDITIONS: Equipment sold by OMEGA is not intended to be used, nor shall it be used: (1) as a “Basic Component” under 10 CFR 21 (NRC), used in or with any nuclear installation or activity; or (2) in medical applications or used on humans. Should any Product(s) be used in or with any nuclear installation or activity, medical application, used on humans, or misused in any way, OMEGA assumes no responsibility as set forth in our basic WARRANT Y /DISCLAIMER language, and, additionally, purchaser will indemnify OMEGA and hold OMEGA harmless from any liability or damage whatsoever arising out of the use of theProduct(s) in such a manner.Where Do I Find Everything I Need forProcess Measurement and Control?OMEGA…Of Course!Shop online at TEMPERATUREM U Thermocouple, RTD & Thermistor Probes, Connectors,Panels & AssembliesM U Wire: Thermocouple, RTD & ThermistorM U Calibrators & Ice Point ReferencesM U Recorders, Controllers & Process MonitorsM U Infrared PyrometersPRESSURE, STRAIN AND FORCEM U Transducers & Strain GagesM U Load Cells & Pressure GagesM U Displacement TransducersM U Instrumentation & AccessoriesFLOW/LEVELM U Rotameters, Gas Mass Flowmeters & Flow ComputersM U Air Velocity IndicatorsM U Turbine/Paddlewheel SystemsM U Totalizers & Batch ControllerspH/CONDUCTIVITYM U pH Electrodes, Testers & AccessoriesM U Benchtop/Laboratory MetersM U Controllers, Calibrators, Simulators & PumpsM U Industrial pH & Conductivity EquipmentDATA ACQUISITIONM U Communications-Based Acquisition SystemsM U Data Logging SystemsM U Wireless Sensors, Transmitters, & ReceiversM U Signal ConditionersM U Data Acquisition SoftwareHEATERSM U Heating CableM U Cartridge & Strip HeatersM U Immersion & Band HeatersM U Flexible HeatersM U Laboratory HeatersENVIRONMENTALMONITORING AND CONTROLM U Metering & Control InstrumentationM U RefractometersM U Pumps & TubingM U Air, Soil & Water MonitorsM U Industrial Water & Wastewater TreatmentM U pH, Conductivity & Dissolved Oxygen InstrumentsM4944/0818。
TM88使用说明
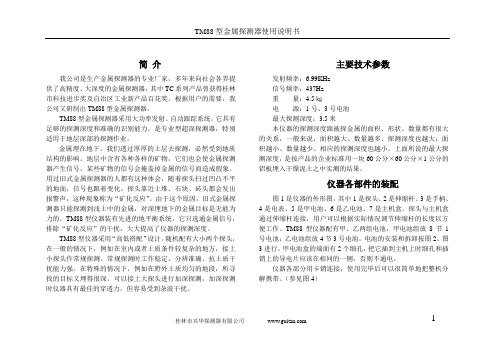
简介我公司是生产金属探测器的专业厂家,多年来向社会各界提供了高精度、大深度的金属探测器,其中TC系列产品曾获得桂林市科技进步奖及自治区工业新产品百花奖。
根据用户的需要,我公司又研制出TM88型金属探测器。
TM88型金属探测器采用大功率发射、自动跟踪系统,它具有足够的探测深度和准确的识别能力,是专业型超深探测器,特别适用于地层深部的探测作业。
金属埋在地下,我们透过厚厚的土层去探测,必然受到地质结构的影响。
地层中含有各种各样的矿物,它们也会使金属探测器产生信号,某些矿物的信号会掩盖掉金属的信号而造成假象。
用过旧式金属探测器的人都有这种体会,随着探头扫过凹凸不平的地面,信号也跟着变化,探头靠近土堆、石块、砖头都会发出报警声,这种现象称为“矿化反应”。
由于这个原因,旧式金属探测器只能探测到浅土中的金属,对深埋地下的金属目标是无能为力的。
TM88型仪器装有先进的地平衡系统,它只选通金属信号,排除“矿化反应”的干扰,大大提高了仪器的探测深度。
TM88型仪器采用“高低搭配”设计,随机配有大小两个探头,在一般的情况下,例如在室内或者土质条件较复杂的地方,接上小探头作常规探测。
常规探测时工作稳定、分辨准确、抗土质干扰能力强。
在特殊的情况下,例如在野外土质均匀的地段,所寻找的目标又埋得很深,可以接上大探头进行加深探测,加深探测时仪器具有最佳的穿透力,但容易受到杂波干扰。
主要技术参数发射频率:6.99KHz信号频率:437Hz重量:4.5㎏电源:1号、3号电池最大探测深度:3.5米本仪器的探测深度跟被探金属的面积、形状、数量都有很大的关系,一般来说,面积越大、数量越多、探测深度也越大;面积越小、数量越少、相应的探测深度也越小。
上面所说的最大探测深度,是按产品的企业标准用一块60公分×60公分×1公分的铝板埋入干燥泥土之中实测的结果。
仪器各部件的装配图1是仪器的外形图,其中1是探头、2是伸缩杆、3是手柄、4是电表、5是甲电池、6是乙电池、7是主机盒。
- 1、下载文档前请自行甄别文档内容的完整性,平台不提供额外的编辑、内容补充、找答案等附加服务。
- 2、"仅部分预览"的文档,不可在线预览部分如存在完整性等问题,可反馈申请退款(可完整预览的文档不适用该条件!)。
- 3、如文档侵犯您的权益,请联系客服反馈,我们会尽快为您处理(人工客服工作时间:9:00-18:30)。
数字式超声波探伤仪使用说明书目录序言 (1)第一章简介 (2)1.1安全提示 (2)1.2概述 (2)1.3 功能特点 (2)1.4 技术参数 (3)1.5 仪器主机 (4)1.6 显示界面简介 (5)1.7按键介绍 (5)1.8 菜单结构 (7)1.9 指示灯 (8)1.10 充电说明 (8)1.10.1 供电方式 (8)1.10.2 充电方式 (8)第二章基本操作 (10)2.1开关机 (10)2.2探头连接 (10)2.3飞梭旋轮操作 (10)2.4探头参数设置 (11)2.5 增益调节 (11)2.6 检测范围调节 (11)2.7 声速和零偏校准 (11)2.8 闸门调节 (12)2.9 读数设置 (12)2.10发射参数调节 (12)2.11回波介绍 (13)2.12 标准设置 (13)2.13 恢复出厂设置 (13)2.14 冻结 (13)2.15 其它参数 (13)2.15.1 AWS标准使用方法: (13)2.15.2 屏幕亮度操作: (14)第三章调校操作及其举例 (15)3.1直探头校准 (15)3.1.1已知材料声速、零点的校准 (15)3.1.2未知材料声速、零点的校准 (16)3.2斜探头校准 (17)3.2.1斜探头材料声速、探头零偏、探头前沿校准 (17)3.3.2斜探头角度/K值的校准 (19)3.3双晶探头校准 (21)第四章DAC/A VG曲线 (22)4.1 DAC曲线 (22)4.1.1 DAC曲线制作 (22)4.1.2 DAC曲线调整 (24)4.1.3 DAC曲线拟合 (25)4.1.4 DAC曲线删除 (25)4. 2 A VG曲线 (25)4.2.1 单点A VG 曲线制作 (26)4.2.2 多点A VG制作 (28)4.2.3 A VG 曲线拟合 (28)第五章探伤辅助功能应用 (29)5.1 动态记录 (29)5.2 波峰记忆 (30)5.3 回波包络 (30)5.4 通讯 (31)5.5 报警 (31)5.6 通道 (31)5.7 波形 (32)5.8 B扫 (34)5.9展宽 (35)第六章检测精度的影响因素及缺陷评估 (36)6.1使用超声探伤仪的必要条件 (36)6.2影响检测精度的因素 (36)6.3缺陷评估方法 (36)6.3.1缺陷边界法 (36)6.3.2回波显示比较法 (36)第七章维修与保养 (38)7.1使用注意事项 (38)7.2保养与维护 (38)一般故障及排除 (38)附录 (39)附录1:名词术语 (39)附录2:与超声波探伤有关的国家标准与行业标准 (40)序言感谢您使用我公司的超声波探伤仪产品,您能成为我们的用户,是我们莫大的荣幸。
数字式智能超声波探伤仪采用国际先进的集成电路技术和新型TFT彩色显示器件,其各项性能指标均达到或超过国际先进水平。
仪器采用人工智能技术,功能强劲,使用方便。
为了您能尽快熟练掌握该款超声波探伤仪,请务必仔细阅读本操作手册以及随机配送的其它相关资料,以便您更好地使用探伤仪。
请您仔细核对随机资料是否齐全、所得仪器及配件与装箱单是否一致,如果有不妥之处,您可拒收仪器。
购买仪器后,请您认真仔细地阅读仪器的相关资料,以保证您获得应有的权利和服务。
这款数字式超声波探伤仪是设计先进、制造精良的高科技产品,在研发和制造过程中经过了严格的技术评测,具有很高的可靠性。
即使如此,您仍可能会在使用中遇到一些技术问题,为此我们在本手册中进行了详尽说明和示例,以方便您的使用。
如果您在仪器使用过程中遇到问题,请查阅本操作手册相关部分,或者直接与我公司联系。
感谢您的合作。
第一章简介本仪器是一款便携式、全数字式超声波探伤仪,能够快速、无损伤、精确地进行工件内部多种缺陷(焊接、裂纹、夹杂、气孔等)的检测、定位和评估。
既可以用于实验室,也可以用于工程现场。
本仪器能够广泛地应用在制造业、钢铁冶金业、金属加工业、化工业等需要缺陷检测和质量控制的领域,也广泛应用于航空航天、铁路交通、锅炉压力容器等领域的在役安全检查与寿命评估。
1.1安全提示◇本仪器为工业超声波无损探伤设备,不可以用于医疗检测;◇使用本仪器的人员必须具备专业无损检测知识,以保证安全操作;◇本仪器必须在仪器允许的环境条件下使用,尤其不可在强磁场、强腐蚀的环境下使用;◇在使用过程中请按照本手册的介绍正确使用,保证安全操作,避免不必要的损失;◇出现故障请与本公司联系,切勿自行拆卸修理。
声明:本公司对由于误操作造成的任何后果不负任何责任,请您严格按照本手册的介绍正确使用本仪器。
1.2 概述的功能/性能如表1所示。
表1功能列表型号SUB110显示屏TFTDAC曲线●A VG曲线●内置标准●闸门报警●曲线报警●波形冻结●通道10波形100录像5min×10自动校准●脉冲幅度固定噪声抑制●波峰记忆●回波包络●厚度B扫●自动增益●PC软件●电池模块 11.3 功能特点◇仪器特点超探仪产品是全数字式超声波探伤仪,高速度、高精度、高效率、可靠性高、综合性能好、实时操作。
采用先进技术,现场性能卓越。
大容量电子硬盘,可永久性保存。
多通道探伤,可通道另存,便于探伤。
大容量波形存储,可波形调用。
高速、长时间探伤过程录像。
全中文显示,菜单式操作,多个快捷键,数码飞梭旋钮。
操作便捷,技术领先。
真彩色液晶显示屏,可根据环境选择仪器配色方案,屏幕亮度可自由设定。
可拆卸式电池供电,可在线充电,亦可脱机充电。
可边工作边充电。
电池更换方便。
可长时间在野外作业而无忧虑。
其体积小,重量轻,便于携带。
◇发射脉冲脉冲幅度和宽度可调,使探头工作在最佳状态。
阻抗匹配可选,满足灵敏度及分辨率的不同工作要求。
四种工作方式:直探头,斜探头,双晶,透射探伤。
◇放大接收实时采样:高速ADC,充分显示波形细节。
检波方式:全波、正半波、负半波、射频。
闸门:双闸门读数,支持时间闸门与声程闸门。
增益:0-110dB多级步距可调。
可分别调节基本增益、扫查增益、表面补偿,方便探伤设置。
支持增益锁定,支持自动增益。
◇报警类型闸门进波、闸门失波、曲线进波、曲线失波4种类型可选◇数据存储设有存储快捷键,便于操作。
可存储10个探伤通道;100个波形存储;10段5分钟录像。
可快速另存、调用、回放与删除。
◇探伤功能波峰记忆:实时检索缺陷最高波,记录缺陷最大值回波包络:对缺陷回波进行波峰轨迹描绘,辅助对缺陷定性判断。
B型扫描:实时扫查、横截面显示,可显示工件缺陷形状,使探测结果更直观。
DAC、A VG:直/斜探头锻件探伤找准缺陷最高波自动计算Φ值,可分段制作。
动态记录:快捷检测实时动态记录波形,存储、回放。
缺陷定位:水平值L、深度值H、声程值S。
缺陷定量:根据设定基准灵活显示。
缺陷定性:通过包络波形,人工经验判断。
◇实时时钟记录日期、时间跟踪记录,并存储。
◇通讯接口高速USB接口提供传输。
◇屏幕保护待机时,仪器屏幕会降低亮度或自动关闭,可使仪器省电,延长使用寿命1.4 技术参数本仪器的技术参数详见表2。
表2 技术参数列表检测范围0~9999mm声速范围1000~9999m/s增益范围0dB~110dB显示延迟-20µs~+3400µs探头零偏0µs~99.99µs工作频率0.5~15MHz电噪声水平≤10%探头阻尼100Ω、150Ω、200Ω、500Ω重复频率10~1000Hz灵敏度余量>62dB(深200mm,Ф2平底孔)分辨力>40dB(5P14)线性抑制0~80%(数字抑制)垂直线性误差≤3%水平线性误差≤0.1%动态范围≥32dB脉冲类型方波脉冲强度固定脉冲宽度50~300ns环境温度-10℃~﹢50℃环境湿度20%~95%RH工作时间≥ 20 hours电源电压DC:7.2V; AC:220V尺寸220×175×59(mm)重量 1.3 kg (含电池)1.5 仪器主机探伤仪外观如图1.1所示,图中标出各部分名称。
图1.11-键盘2-手持护带3-TFT真彩数字显示屏4-电源指示灯5-报警指示灯6-数码飞梭旋钮7-支架8-USB通讯口9-复位关机孔10-充电插孔11-接收端口12-收/发端口13-防护盖1.6 显示界面简介探伤仪主要有两种显示界面,分别为:回波界面和设置界面。
回波界面主要由回波显示区 ,主菜单区,子菜单区和基本信息显示区等构成,如图1.2,1.3,1.4和1.5所示。
回波显示区闸门子菜单主菜单状态条标志状态显示区增益显示区声速和探头频率图1.2 主界面当前通道水平投影深度当前闸门内波高声程当前闸门图1.3 状态条补偿增益扫查增益基本增益当前基本增益图1.4 增益显示 图1.5 标志状态显示1.7按键介绍本仪器键盘设计有按键和数码飞梭旋轮两种操作方式,键位如图1.6所示。
探伤人员对探伤仪发出的所有控制指令,均通过键盘操作或旋轮操作完成。
键盘操作或旋轮操作过程中,探伤仪根据不同的状态自动识别各键的不同含义,执行操作人员的指令。
图1.6 仪器按键键位图功能选择键下移键确认键上移键电源指示灯报警指示灯“基本”功能组键“调校”功能组键“存储”功能组键“系统”功能组键“功能”功能组键闸门快捷键增益快捷键通道快捷键K 值快捷键“曲线”功能组键展宽快捷键显示屏色彩快捷键参数列表显示键标准列表显示键自动增益键波峰记忆快捷键动态回波记录键冻结键电源开/关键数码飞梭旋轮旋轮键主要用于数值增减、步距选择等功能。
操作方式左旋、右旋:数值增减单击:轻轻按下旋轮,马上松开,让旋轮弹起,用于选择步距如上面的“仪器按键键位图”,按键区分为三部分,第一部份为第一行功能选择键行,由H1、H2、H3、H4、H5五个键组成。
通过这五个按键可以选择显示屏下方主菜单中相对应的功能选项。
第二部份为第二行的三个基本操作按钮,分别为“上移”、“确认”、“下移”键,通过单击“上移”和“下移”键,可在屏幕右侧的子菜单中的不同参数之间进行切换,单击“确认”键,可对完成的操作进行确认,进入下一步操作。
第三部份为功能组及快捷功能区域。
在2.8功能组键操作和2.9功能快捷键操作中会详细介绍。
1.8 菜单结构基本调校存储系统曲线功能范围检测范围探头探头类型通道通道选择显示屏幕亮度DAC 曲线制作AVG 曲线制作扫描B扫模式材料声速探头频率通道存储配色方案基本增益基本增益B扫方向显示延迟探头前沿通道清空测点波高测点波高扫描周期探头零偏晶片尺寸通道另存闸门起始闸门起始A扫显示闸门闸门选择校准自动校准波形波形选择标度网格显示调整曲线调整调整曲线调整焊缝焊缝参数闸门起始手动设置波形存储标度单位测点顺序测点顺序闸门宽度前端距离波形调用水平标度测点波高测点波高闸门高度探头零偏波形清空起始闸门起始闸门增益基本增益角度自动校准录像录像编号报警按键声音偏移判废线RL 偏移上AVG线孔径当量孔径增益步距手动设置录像制作蜂鸣报警定量线SL 中AVG线闸门起始扫查增益探头角度录像回放闪光报警评定线EL 下AVG线晶片直径表面补偿探头K值录像清空报警类型报警基准报警曲线探头频率读数读数方式发射发射强度清除所有通道AWS AWS功能设置缺陷类型设置曲线基准测裂纹裂纹测深自动捕捉脉冲宽度所有波形缺陷直径基准孔径端点A 检测方式重复频率所有录像缺陷长度晶片直径端点B探头阻尼恢复出厂关闭系统当量基准探头频率起始闸门回波检波方式设置工件厚度预留信息当前日期显示曲线显示显示曲线显示曲面工件外径噪声抑制自动波高当前时间曲线类型曲线类型工件内径波形填充波峰记忆软件版本曲线拟合曲线拟合曲面修正回波编码回波包络其他信息曲线删除曲线删除1.9 指示灯报警指示灯:当前闸门内回波峰值超出闸门或曲线高度(进波报警),当前闸门内回波峰值低于闸门或曲线高度(失波报警)时,该报警指示灯闪烁报警;电源指示灯:开机状态下仪器电源指示灯亮。