转炉渣铁分离
高炉炼铁中渣铁分离技术研究减少渣铁中的杂质含量

高炉炼铁中渣铁分离技术研究减少渣铁中的杂质含量炼铁过程中,高炉炼铁技术一直是主要的铁矿石还原冶炼方法之一。
然而,高炉炼铁过程中,渣和铁的分离问题一直是一个挑战。
其中,渣铁中的杂质含量是一个严重影响炼铁品质的问题。
本文将探讨高炉炼铁中渣铁分离技术的研究,以减少渣铁中的杂质含量。
一、高炉炼铁过程中渣铁分离问题在高炉炼铁过程中,铁矿石和燃料经过还原反应生成金属铁。
同时,一些杂质元素也存在于铁矿石中,如硫、磷、锰等。
在冶炼过程中,这些杂质元素会被部分还原,并被固定在渣中。
因此,高炉炼铁过程中需要有效地分离渣和铁,减少渣中的杂质含量。
二、渣铁分离技术的研究现状目前,研究学者们一直在寻找各种方法来解决高炉炼铁中的渣铁分离问题。
以下是一些常见的渣铁分离技术:1. 磁选技术磁选技术通过利用渣铁中铁矿石的磁性差异,将铁与渣有效地分离。
这种技术需要使用磁铁或磁场来实现。
2. 重力分离技术重力分离技术利用不同物质的密度差异,通过采用物理或机械设备,使重物质下沉,从而分离渣和铁。
3. 浮选技术浮选技术通过利用物质的表面特性,使一种物质在浮液中浮起,而另一种物质下沉。
这种技术可以用于分离渣和铁。
4. 气浮分离技术气浮分离技术利用气泡在浮液中产生的浮力,将一种物质从另一种物质中分离出来。
这种技术可以用于渣铁分离。
5. 浸出技术浸出技术通过使用溶剂,将需要分离的物质从固体中溶解出来。
这种技术也可以应用于渣铁分离。
以上是一些常见的渣铁分离技术,每种技术都有其优点和局限性。
研究者们正在不断探索创新的渣铁分离技术,以进一步降低渣铁中的杂质含量。
三、减少渣铁中杂质含量的挑战在研究渣铁分离技术的同时,我们也需要面对一些挑战,以减少渣铁中的杂质含量。
1. 操作和成本渣铁分离技术的操作和设备成本是在实际应用中需要考虑的重要因素。
一些高效的技术可能需要更多的经济投入,对实际生产造成一定的影响。
2. 杂质再分布即使通过分离技术成功减少了渣铁中的杂质含量,但在高炉冶炼过程中,杂质的再分布也会产生。
转炉挡渣出钢

转炉挡渣出钢——让钢水更“洁净”随着我国国民经济的发展,对钢材的消费结构正在发生变化,加之众多企业日益关注转炉生产特殊钢,这些都对低成本生产高洁净度钢水提出了越来越高的要求。
就转炉炼钢生产企业而言,为生产IF钢(超低碳钢)、石油管线钢、硅钢、轴承钢、弹簧钢等高附加值产品,减少转炉出钢时的下渣量是提高钢水洁净度,从而提高转炉钢产品的质量和档次,降低其生产成本最有效的途径。
有效挡渣亟待引起高度重视有效防止钢水回磷、回硫。
在转炉出钢时采取有效的挡渣操作,是改善钢水质量的重要举措,既可以减少钢水回磷、回硫,提高合金收得率,减少钢水中夹杂物,提高钢水洁净度,还可为后续精炼创造条件。
当在精炼过程进行造渣脱硫时,因钢水钢渣中含有10%~13%的SiO2和0.8%~1.0%的P2O5,钢水极易发生回硫和回磷现象,导致钢水成分超标形成废品。
减少脱氧剂及合金消耗。
在转炉出钢时采取有效的挡渣操作,不仅可以减少脱氧剂及合金消耗,减少钢包粘渣,延长钢包使用寿命,还可提高转炉出钢口区域耐材的使用寿命,降低炼钢产品的生产成本。
转炉出钢后钢包的钢渣成分与终渣成分基本一致。
若转炉出钢时挡渣效果不好,将导致钢包钢渣量加大。
如果钢水精炼过程中不对钢渣进行脱氧改性,则精炼后钢渣中的氧会扩散到钢中,造成钢中成分烧损,导致成分变差;或在钢中形成新的夹杂物,污染钢水使其质量恶化。
当对钢渣进行脱氧改性时,较大的顶渣量会消耗大量脱氧剂。
钢包钢渣中FeO含量通常为1O%~17%(平均按13%计算),钢水精炼时,以使用铝脱氧剂为例,每100公斤顶渣消耗的铝脱氧剂为3.8公斤。
对于每天产钢100炉的炼钢厂,如果每炉出钢少出200公斤渣,则每年可节省脱氧剂消耗440万元。
挡渣塞成为挡渣产品主流多年来,国内外众多冶金工作者研究开发将钢渣进入量降到最低的技术和方法,除少渣、无渣冶炼工艺外,主要开发了各种挡渣技术和产品,以尽量减少转炉出钢后期涡流带出的钢渣量。
转炉脱磷造渣工艺
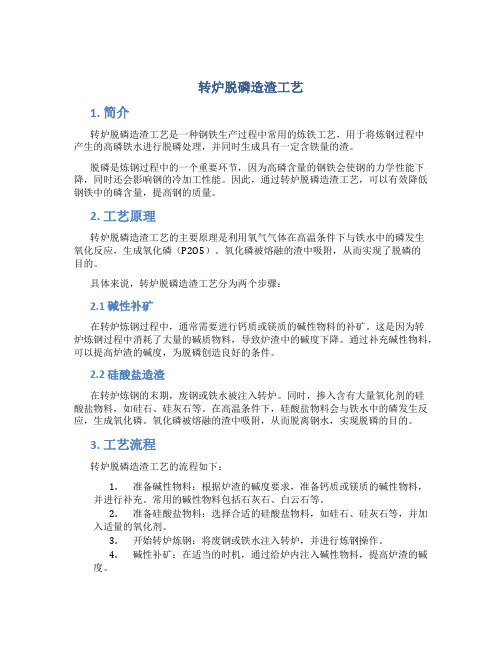
转炉脱磷造渣工艺1. 简介转炉脱磷造渣工艺是一种钢铁生产过程中常用的炼铁工艺,用于将炼钢过程中产生的高磷铁水进行脱磷处理,并同时生成具有一定含铁量的渣。
脱磷是炼钢过程中的一个重要环节,因为高磷含量的钢铁会使钢的力学性能下降,同时还会影响钢的冷加工性能。
因此,通过转炉脱磷造渣工艺,可以有效降低钢铁中的磷含量,提高钢的质量。
2. 工艺原理转炉脱磷造渣工艺的主要原理是利用氧气气体在高温条件下与铁水中的磷发生氧化反应,生成氧化磷(P2O5)。
氧化磷被熔融的渣中吸附,从而实现了脱磷的目的。
具体来说,转炉脱磷造渣工艺分为两个步骤:2.1 碱性补矿在转炉炼钢过程中,通常需要进行钙质或镁质的碱性物料的补矿。
这是因为转炉炼钢过程中消耗了大量的碱质物料,导致炉渣中的碱度下降。
通过补充碱性物料,可以提高炉渣的碱度,为脱磷创造良好的条件。
2.2 硅酸盐造渣在转炉炼钢的末期,废钢或铁水被注入转炉。
同时,掺入含有大量氧化剂的硅酸盐物料,如硅石、硅灰石等。
在高温条件下,硅酸盐物料会与铁水中的磷发生反应,生成氧化磷。
氧化磷被熔融的渣中吸附,从而脱离钢水,实现脱磷的目的。
3. 工艺流程转炉脱磷造渣工艺的流程如下:1.准备碱性物料:根据炉渣的碱度要求,准备钙质或镁质的碱性物料,并进行补充。
常用的碱性物料包括石灰石、白云石等。
2.准备硅酸盐物料:选择合适的硅酸盐物料,如硅石、硅灰石等,并加入适量的氧化剂。
3.开始转炉炼钢:将废钢或铁水注入转炉,并进行炼钢操作。
4.碱性补矿:在适当的时机,通过给炉内注入碱性物料,提高炉渣的碱度。
5.硅酸盐造渣:当转炉炼钢接近末期时,通过给炉内注入硅酸盐物料,利用氧化剂促进磷的氧化反应。
6.淋渣:根据炉内的渣情况,选择合适的时间进行淋渣操作。
淋渣可以通过人工或机械设备进行。
7.渣铁分离:在脱磷过程中,渣中生成的氧化磷会被吸附在渣中,从而脱离钢水。
通过合适的方法,将渣与钢水分离。
8.尾渣处理:处理分离出来的尾渣,并对其进行资源化利用或安全处理。
转炉渣处理试验方案

转炉渣处理试验方案©2009 广州市绿易化工科技有限公司一.实验背景柳钢转炉炼钢产生的钢渣,主要来源由生铁炉料带入的杂质,以及加入的造渣剂如石灰石、萤石、硅石等,以及氧化剂、脱硫产物和被侵蚀的炉衬材料等生成,另外还夹带有一定量的单质铁等。
钢渣的主要成分是钙、铁、硅、镁、铝、锰、磷、氧等组成,转炉渣经过磁选后,其主要成分含量如表一表一转炉渣成分磁选后的钢渣,其中高价值金属的含量低,处理较困难,虽然现已开发较多的处理方法,如作为溶剂回炉、作为水泥的掺和剂、作为路基回填的原料等,但由于钢渣的产量大,以上领域所需的量有限,造成大量钢渣积压堆放于渣场,不仅占用有限的土地资源,对环境造成影响。
从钢渣的成分来看,其含有和水泥相类似的硅酸三钙、硅酸二钙及铁铝酸盐等活性矿物质,具有水硬胶凝性,最广阔的用途在于作为水泥生产的熟料,但是由于其中铁含量较高,且含有游离钙、镁等,不能直接作为水泥生产的熟料使用,因此,开发一种工艺,使钢渣能够直接作为水泥生产的熟料使用,是处理转炉渣的较好方法。
二.试验工艺1. 工艺流程图设定的转炉渣处理流程图如图1:磁选矿硫酸钙再生酸图1 试验工艺流程图2. 实验过程简述使用震动球磨机球磨,将转炉渣磨碎至-100目(其中,少许不能破碎的铁块筛分回收),破碎后的炉渣经过磁选分离出大部分单质铁,磁选尾渣使用再生盐酸浸出,浸出渣经其他混合配料后转水泥制备,浸出液经过鼓气氧化、碳酸钙中和沉淀铁,沉铁渣经洗涤煅烧后制成氧化铁红,除铁后溶液经过控制PH分步沉淀出Mn、Mg,沉淀后的溶液经过净化除杂,硫酸再生后制备再生盐酸,返回盐酸浸出工序,硫酸钙沉淀作为产品出售。
三.试验进度安排1. 实验总体进度安排本次实验的目标是能够比较经济、有效的的使转炉渣转变为能够直接作为生产水泥的熟料的原料,并回收其中的铁、锰、镁等金属,根据所需的工作量,设定的进度表如表二:表二实验总体进度安排其中,第一阶段在广州市绿易化工的办公室完成,包括理论分析、方案选定、市场可行性调研、计算机模拟、经济性评价等内容。
8-转炉“留渣-双渣”少渣炼钢工艺实践
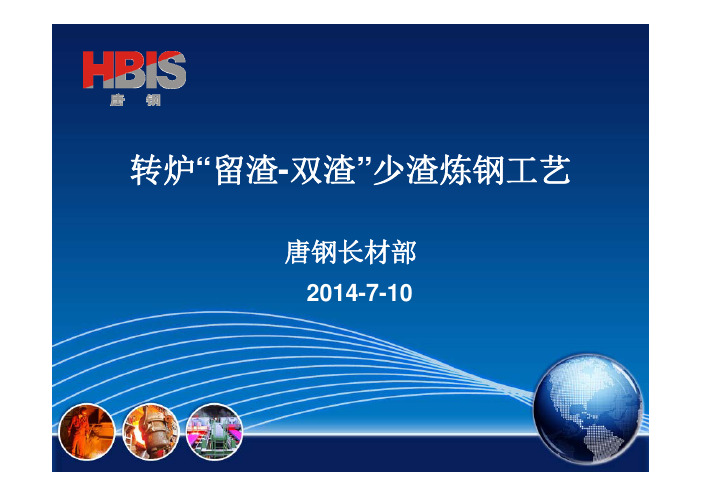
“留渣-双渣”工艺示意图
3.转炉脱磷影响因素
3.脱磷的基本原理
2[P]+5(FeO)+4(CaO)=4CaO·P2O5+5[Fe]
a 4CaO P2 O 5 a a
2 p 5 F eO
Kp
a
4 C aO
% 4CaO P2 O 5 4CaO P O 4 5 4 % P 2 f P2 % F e O 5 F e O % CaO C aO
演变:首钢公司从2011年开始,在首钢首秦和迁钢分别连续试验单
转炉“留渣-双渣”操作,取得较好的效果,目前首钢集团首钢长治, 首钢水钢均推广应用“留渣-双渣”少渣炼钢操作工艺,工艺相对成熟 。
1. 大幅度减少炼钢石灰、白云石等渣料消耗和炼钢渣量; 2. 可以利用出钢后炉渣的物理热,预热废钢; 3. 炼钢终渣含Tfe:15~25%,渣量减少可以降低钢铁料消耗; 4. 双渣倒渣的炉渣主要为脱磷阶段低碱度渣,自由CaO含量低, 可以简化炉渣处理; 5. 常规转炉出钢后留在炉内钢水随炉渣倒出,采用“留渣-少渣”工 艺终点少倒渣、出钢后不倒渣,可以提高钢水收得率。
FeO%
H11Mn2SiA
3A14306-1 3A14306-2 3B14615-1 3B14615-2 3C14935-1 3C14935-2 3A14301-1 3A14301-2 3B14603-1 3B14603-2 3B14612-1 3B14612-1
1 冶炼周期影响
类别 加料 脱磷期 双渣 脱碳期 终点 加废钢 兑铁时间 前期吹炼时间 氮气刹渣 倒渣时间 中后期吹炼 拉碳、补吹时间 等待终点成分 出钢时间 溅渣时间 总冶炼周期 留渣-双渣 1.7 2.4 4.5 2.1 3 8.8 2 1 2.5 2 30 单渣法 1.7 2.2 4.5 / / 8.7 2 1 2.5 2.5 25.1
宝钢钢渣技术
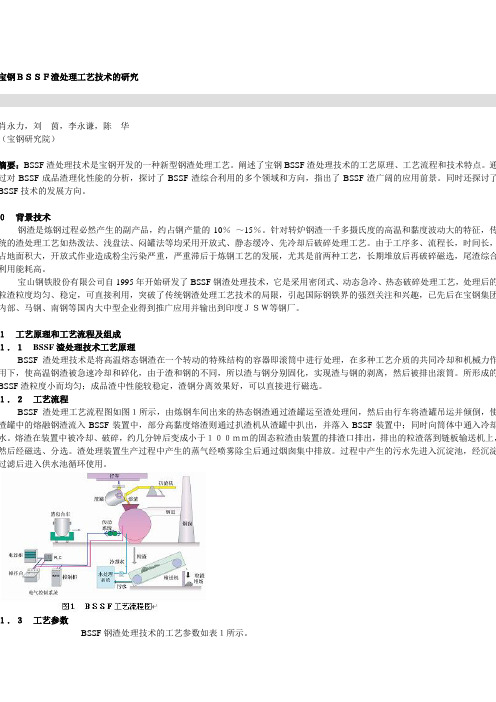
宝钢BSSF渣处理工艺技术的研究肖永力,刘茵,李永谦,陈华(宝钢研究院)摘要:BSSF渣处理技术是宝钢开发的一种新型钢渣处理工艺。
阐述了宝钢BSSF渣处理技术的工艺原理、工艺流程和技术特点。
通过对BSSF成品渣理化性能的分析,探讨了BSSF渣综合利用的多个领域和方向,指出了BSSF渣广阔的应用前景。
同时还探讨了BSSF技术的发展方向。
0背景技术钢渣是炼钢过程必然产生的副产品,约占钢产量的10%~15%。
针对转炉钢渣一千多摄氏度的高温和黏度波动大的特征,传统的渣处理工艺如热泼法、浅盘法、闷罐法等均采用开放式、静态缓冷、先冷却后破碎处理工艺。
由于工序多、流程长,时间长,占地面积大,开放式作业造成粉尘污染严重,严重滞后于炼钢工艺的发展,尤其是前两种工艺,长期堆放后再破碎磁选,尾渣综合利用能耗高。
宝山钢铁股份有限公司自1995年开始研发了BSSF钢渣处理技术,它是采用密闭式、动态急冷、热态破碎处理工艺,处理后的粒渣粒度均匀、稳定,可直接利用,突破了传统钢渣处理工艺技术的局限,引起国际钢铁界的强烈关注和兴趣,已先后在宝钢集团内部、马钢、南钢等国内大中型企业得到推广应用并输出到印度JSW等钢厂。
1工艺原理和工艺流程及组成1.1BSSF渣处理技术工艺原理BSSF渣处理技术是将高温熔态钢渣在一个转动的特殊结构的容器即滚筒中进行处理,在多种工艺介质的共同冷却和机械力作用下,使高温钢渣被急速冷却和碎化,由于渣和钢的不同,所以渣与钢分别固化,实现渣与钢的剥离,然后被排出滚筒。
所形成的BSSF渣粒度小而均匀;成品渣中性能较稳定,渣钢分离效果好,可以直接进行磁选。
1.2工艺流程BSSF渣处理工艺流程图如图1所示,由炼钢车间出来的热态钢渣通过渣罐运至渣处理间,然后由行车将渣罐吊运并倾倒,使渣罐中的熔融钢渣流入BSSF装置中,部分高黏度熔渣则通过扒渣机从渣罐中扒出,并落入BSSF装置中;同时向筒体中通入冷却水。
熔渣在装置中被冷却、破碎,约几分钟后变成小于100mm的固态粒渣由装置的排渣口排出,排出的粒渣落到链板输送机上,然后经磁选、分选。
转炉冶炼出钢挡渣

出钢挡渣随着用户对钢材质量要求的日益提高,需要不断提高钢水质量。
减少转炉出钢时的下渣量是改善钢水质量的一个重要方面。
在转炉出钢过程中进行有效的挡渣操作,不仅可以减少钢水回磷,提高合金收得率,还能减少钢中夹杂物,提高钢水清洁度,并可减少钢包粘渣,延长钢包使用寿命。
与此同时亦可减少耐材消耗,相应提高转炉出钢口耐火材料的使用寿命,还可为钢水精炼提供良好的条件。
转炉吹炼结束向盛钢桶(钢包)内放出钢水而把氧化渣留在炉内的操作。
出钢时使氧化性渣和钢水分离是炉外精炼的要求。
钢包内的二次精炼适于在还原条件下进行。
采用挡渣出钢,避免出钢带渣对提高炉外精炼效果是重要保证。
出钢时,随着钢水面的下降,当钢水深度低于某一临界值时,在出钢口上方会形成漏斗状的汇流旋涡,部分渣子在钢水出完以前就由出钢口流出,这是渣、钢分离不清的根本原因。
另外摇炉过快,有部分渣子由炉口涌出;但这可通过细心操作而避免。
挡渣出钢技术主要是针对汇流旋涡下渣而开发的。
有挡渣球、挡渣塞、高压气挡渣、挡渣阀门、下渣信号检测等各种方法。
挡渣球挡渣球由耐火材料包裹在铁芯外面制成,其密度大于炉渣而小于钢水,因而能浮在渣钢界面处。
出钢时,当钢水已倾出3/4~4/5时,用特定工具伸入炉内将挡渣球放置于出钢口上方。
钢水临近出完时,旋涡将其推向出钢口,将出钢口堵住而阻挡渣子流出。
(图1)为了提高挡渣球的抗急冷急热性能,提高挡渣效率,又研制了石灰质挡渣球。
先在铁芯外包一层耐火纤维,用于起缓冲作用;球的外壳以白云石、石灰等作原料,用合成树脂或沥青等作黏接剂制造。
挡渣球法成功的关键:一是球的密度恰当,即4.3~4.4g/cm3;二是出钢口维护好,保持圆形;三是放置球的位置对准出钢口。
但由于挡渣球的体形,极易随钢流飘浮而离开出钢口,从而失去挡渣作用。
挡渣出钢挡渣塞将挡渣物制成上为倒锥体下为棒状的塞(图2a)。
由于其形状接近于漏斗形,可配合出钢时的钢水流,故比挡渣球效率高。
有的在挡渣塞上部锥体增加小圆槽而下部改为六角锥形(图2b),以增加抑制旋涡的能力。
降低转炉渣中的全铁含量的措施

降低转炉渣中的全铁含量的措施
1. 优化转炉渣的化学成分,调整炉渣中的氧化剂和还原剂含量,以降低全铁含量。
2. 提高转炉渣的温度,加快化学反应速度,促使一部分含铁氧化物还原为金属铁,从而减少全铁含量。
3. 适当增加转炉的冶炼时间,延长铁水与渣的接触时间,有利于全铁的分离和减少在渣中的含量。
4. 采用高效的炼渣剂,如钙、镁等,能与炉渣中的氧化铁发生反应,有效降低全铁含量。
5. 控制转炉的气氛,保持适当的还原性气氛,有利于还原渣中的氧化铁,减少全铁含量。
6. 使用适当的炉渣处理器,能够有效地除去炉渣中的杂质和含铁物质,从而降低全铁含量。
7. 进行颗粒物分离,利用适当的分选设备,分离掉转炉渣中的细小颗粒物,减少全铁的含量。
8. 优化转炉的操作参数,控制转炉的溶解速度、吹氧量等参数,从而降低全铁含量。
10. 定期对转炉渣进行化学分析,及时调整工艺和措施,确保全铁含量的降低效果。
转炉渣铁分离解析

2020/8/11
-VPG-
9
钢冶金学课程报告
谢谢!
2020/8/11
-VPG-
10
魏2宝02森0/8转/1炉1的挡渣出钢技术探讨 2013
-VPG-
7
滑渣法最有效的 控制前期和后期下渣挡渣 成功率可达百分之百,国 内宝钢自 2009 年开始逐 步采用滑板挡渣法 +AMEPA红外下渣检测技 术相结合的挡渣出钢技术, 挡渣成功率达100%,钢 包渣厚可稳定控制在 40mm以下。
2020/8/11
-VPG-
3
3
转炉渣铁分离
转炉出钢期间,根据转炉倾角大小将整个出钢过程分为前期渣、过程渣和后 期渣三个下渣阶段,各下渣阶段大体上分别占转炉出钢到钢包下渣量的30%、 30%和40%。前期下渣和后期下渣如图1所示。
2020/8/11
-VPG-
4
4
转炉渣铁分离
挡渣法分类:
模式 挡渣帽
进行机械封闭,赛头端部喷 信号原件和信号处理器组成,通过测出出
射高压气体。
钢口流量的变化能准确的控制出钢时间。
以机械或液压控制方式开启或关闭出钢口,
将滑板耐火原件安装到出钢
达到挡渣的目的。
口。
-VPG-
5
转炉中的渣铁分离
2020/8/11
-VPG-
6
6
转炉挡渣实例
挡渣帽+挡渣镖:
为有针对性的控制不同阶段的下渣,本钢炼钢厂180t 转炉采用双挡渣 法工艺,即采用挡渣帽挡出钢开始时的前期下渣,再用挡渣镖挡出钢 结束时的后期下渣的方法。这两种挡渣方法的综合使用,使挡渣效果 明显提高,出钢后钢包渣厚一般可控制在80 ~ 90mm,有效降低了钢 水回磷,并为精炼处理等后部工序创造了良好条件。
转炉钢渣处理的工艺方法
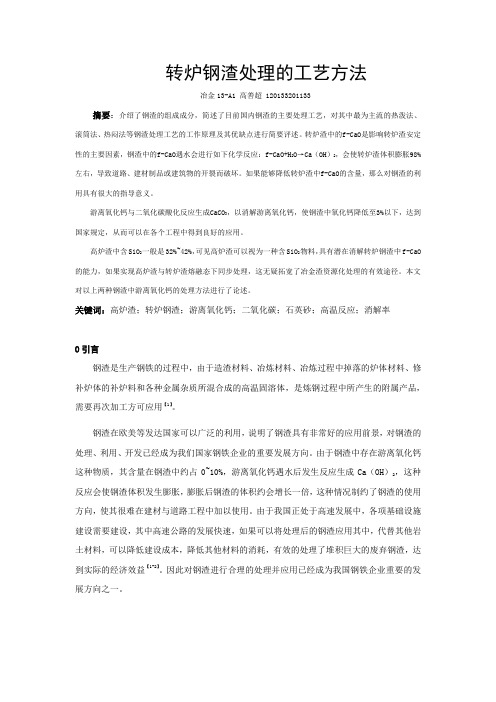
转炉钢渣处理的工艺方法冶金13-A1 高善超 120133201133摘要:介绍了钢渣的组成成分,简述了目前国内钢渣的主要处理工艺,对其中最为主流的热泼法、滚筒法、热闷法等钢渣处理工艺的工作原理及其优缺点进行简要评述。
转炉渣中的f-CaO是影响转炉渣安定性的主要因素,钢渣中的f-CaO遇水会进行如下化学反应:f-CaO+H2O→Ca(OH)2,会使转炉渣体积膨胀98%左右,导致道路、建材制品或建筑物的开裂而破坏。
如果能够降低转炉渣中f-CaO的含量,那么对钢渣的利用具有很大的指导意义。
游离氧化钙与二氧化碳酸化反应生成CaCO3,以消解游离氧化钙,使钢渣中氧化钙降低至3%以下,达到国家规定,从而可以在各个工程中得到良好的应用。
高炉渣中含SiO2一般是32%~42%,可见高炉渣可以视为一种含SiO2物料,具有潜在消解转炉钢渣中f-CaO 的能力,如果实现高炉渣与转炉渣熔融态下同步处理,这无疑拓宽了冶金渣资源化处理的有效途径。
本文对以上两种钢渣中游离氧化钙的处理方法进行了论述。
关键词:高炉渣;转炉钢渣;游离氧化钙;二氧化碳;石英砂;高温反应;消解率0引言钢渣是生产钢铁的过程中,由于造渣材料、冶炼材料、冶炼过程中掉落的炉体材料、修补炉体的补炉料和各种金属杂质所混合成的高温固溶体,是炼钢过程中所产生的附属产品,需要再次加工方可应用【1】。
钢渣在欧美等发达国家可以广泛的利用,说明了钢渣具有非常好的应用前景,对钢渣的处理、利用、开发已经成为我们国家钢铁企业的重要发展方向。
由于钢渣中存在游离氧化钙这种物质,其含量在钢渣中约占0~10%,游离氧化钙遇水后发生反应生成Ca(OH)2,这种反应会使钢渣体积发生膨胀,膨胀后钢渣的体积约会增长一倍,这种情况制约了钢渣的使用方向,使其很难在建材与道路工程中加以使用。
由于我国正处于高速发展中,各项基础设施建设需要建设,其中高速公路的发展快速,如果可以将处理后的钢渣应用其中,代替其他岩土材料,可以降低建设成本,降低其他材料的消耗,有效的处理了堆积巨大的废弃钢渣,达到实际的经济效益【1-2】。
转炉钢渣处理的工艺方法

转炉钢渣处理的工艺方法冶金13-A1 高善超120133201133摘要:介绍了钢渣的组成成分,简述了目前国内钢渣的主要处理工艺,对其中最为主流的热泼法、滚筒法、热闷法等钢渣处理工艺的工作原理及其优缺点进行简要评述。
转炉渣中的f-CaO是影响转炉渣安定性的主要因素,钢渣中的f-CaO遇水会进行如下化学反应:f-CaO+H2O→Ca(OH)2,会使转炉渣体积膨胀98%左右,导致道路、建材制品或建筑物的开裂而破坏。
如果能够降低转炉渣中f-CaO的含量,那么对钢渣的利用具有很大的指导意义。
游离氧化钙与二氧化碳酸化反应生成CaCO3,以消解游离氧化钙,使钢渣中氧化钙降低至3%以下,达到国家规定,从而可以在各个工程中得到良好的应用。
高炉渣中含SiO2一般是32%~42%,可见高炉渣可以视为一种含SiO2物料,具有潜在消解转炉钢渣中f-CaO的能力,如果实现高炉渣与转炉渣熔融态下同步处理,这无疑拓宽了冶金渣资源化处理的有效途径。
本文对以上两种钢渣中游离氧化钙的处理方法进行了论述。
关键词:高炉渣;转炉钢渣;游离氧化钙;二氧化碳;石英砂;高温反应;消解率0引言钢渣是生产钢铁的过程中,由于造渣材料、冶炼材料、冶炼过程中掉落的炉体材料、修补炉体的补炉料和各种金属杂质所混合成的高温固溶体,是炼钢过程中所产生的附属产品,需要再次加工方可应用【1】。
钢渣在欧美等发达国家可以广泛的利用,说明了钢渣具有非常好的应用前景,对钢渣的处理、利用、开发已经成为我们国家钢铁企业的重要发展方向。
由于钢渣中存在游离氧化钙这种物质,其含量在钢渣中约占0~10%,游离氧化钙遇水后发生反应生成Ca(OH)2,这种反应会使钢渣体积发生膨胀,膨胀后钢渣的体积约会增长一倍,这种情况制约了钢渣的使用方向,使其很难在建材与道路工程中加以使用。
由于我国正处于高速发展中,各项基础设施建设需要建设,其中高速公路的发展快速,如果可以将处理后的钢渣应用其中,代替其他岩土材料,可以降低建设成本,降低其他材料的消耗,有效的处理了堆积巨大的废弃钢渣,达到实际的经济效益【1-2】。
钢铁冶炼中的转炉钢渣处理技术

钢铁冶炼中的转炉钢渣处理技术钢铁冶炼是重工业生产中的重要环节之一,其产生的钢渣处理技术对整个工业链的环保安全和经济效益都有着重要影响。
在钢铁冶炼过程中,转炉钢渣处理技术是一种常见的处理方式,本文将对转炉钢渣处理技术进行详细介绍。
一、转炉钢渣生成原因钢铁冶炼过程中,将生铁和废钢放入转炉中进行冶炼,转炉中加入的生料在高温下熔融,氧化生成气体和钢渣。
钢渣是指在钢铁冶炼过程中,从熔炼金属中分离出来的杂质物质,它是熔体和熔渣中的一部分物质。
而转炉钢渣则是指在转炉冶炼过程中产生的钢渣。
二、转炉钢渣组成以及处理方式转炉钢渣主要由氧化物和还原物质组成,包括氧化铁、氧化硅、氧化钙、氧化镁、氧化铝等,还有少量的碳酸盐、硅酸盐、氧化钾、氧化钠等。
不同氧化物的含量和比例不同,对应着钢渣的不同性质。
转炉钢渣处理技术主要包括常规方法和新型方法。
常规方法包括混合熔炼、渣铸、风冷、半干法处理、干法处理等,这些处理方法主要是通过钢渣的物化性质差异,采用相应的方法将其分离,保留其中有用的物质。
渣铸方法是把热钢渣倒入浇铸模型中,冷却后从模具中取出,得到经过初步分离的钢渣块。
这种处理方法不仅可以将有用的物质得到回收利用,还可以减少运输和处理的成本。
风冷方法则是将熔融的钢渣放入钢渣散落区内,通过冷却吹风使其迅速冷却硬化并散落。
这种方法具有成本低、空间占用少、对环境污染小等特点,但处理效率较低。
半干法处理和干法处理是化学方法,将熔融的钢渣加入反应器中,加入石灰石等化学剂,使钢渣成为固态。
这种方式不仅可以减少钢渣的体积,还可以回收其中的有价值的物质。
三、传统转炉钢渣处理存在的问题虽然传统转炉钢渣处理技术在一定程度上解决了钢渣处理的问题,但其存在着许多问题,主要表现在以下几个方面:1、难以满足环保要求。
传统的钢渣处理方法,往往会对环境造成一定的危害,例如渣铸处理方式会在周围环境中产生大量灰尘和噪音,而风冷处理方式则会对空气产生一定的污染。
这种处理方式对环境造成的危害大大降低了其应用范围和市场竞争力。
转炉引渣法渣钢分离实践

( ) 出钢 时 转 炉 连 续 摇 动 ,高 温 环 境 下 隔 1 着 钢渣 和钢 水很 难 确定 出钢 口的准 确位 置 。挡 渣
球 ( )没 有 投 中出钢 口 ,则无 法 实现 挡渣 ; 锥 ( )挡 渣 失 败 后 没 有 合 适 的补 救 办 法 。 钢 2
开始 抬炉 至 出钢 口不 再下 渣过 程 中流 下 的钢 渣引 到钢 包外 侧 的接渣 斗 ,实 现 了有 效 的渣钢 分离 。
1 引渣法渣钢 分离的新思路
传统渣钢分离的切人点都是一个 “ 堵” 字 ,
李树森 :19 9 3年毕业于辽宁科技学 院 ,现在迁钢公司从 事精炼
工 作 ,高 级 工 程 师 。 收 稿/ 0 7 1 -8 2 0 -0 0
能 少 ,以提 高二 次冶 炼效 果 。转炉 渣 钢分 离 的方 法 较多 ,国内主要 有 挡渣 球 挡渣 和 挡 渣 锥挡 渣 2 种 ,国外 有应 用 气动 挡渣 的 ,但 总体 效果 不 够理 想 ,特 别是挡 渣 失败 后无 法挽 救 ,使 钢包 内 渣较
多 ,影 响二 次冶炼 效 果 。 引渣 法渣 钢分 离 既可 以对 其他 方 法挡 渣失 败 进 行补救 。又可 以单独 使 用 ,是对 转 炉渣钢 分 离
包 内 的钢渣 主要 是在 挡 渣失 败 、转炉 钢水 出完 开
始抬 炉 至 出钢 口不再 下渣 的过程 中流人 钢包 的 。
有益 的探 索 和尝试 。
抛开以 “ 堵”字为切人点的思维 ,借鉴大禹 治水的思路 , 在研究渣钢分离工艺时将 “ 引”字 作为 切人 点 ,对 钢渣 进行 引流 ,将 转 炉钢 水 出完
( n e i f c n ea dT c nlg e ig ( hu a gQa ’nI nads e C . t. U i r t o i c n e h o yB in ) S o gn in a o n t l o,Ld ) v sy S e o j r e
转炉钢渣分离方法[发明专利]
![转炉钢渣分离方法[发明专利]](https://img.taocdn.com/s3/m/6de1bd3102d8ce2f0066f5335a8102d276a261cd.png)
(10)申请公布号 (43)申请公布日 2015.01.28C N 104313208A (21)申请号 201410551041.X(22)申请日 2014.10.16C21B 3/04(2006.01)(71)申请人攀枝花钢城集团有限公司地址617023 四川省攀枝花市东区木棉路72号(72)发明人范泽宇 李贤书 钱强(74)专利代理机构成都虹桥专利事务所(普通合伙) 51124代理人刘世平(54)发明名称转炉钢渣分离方法(57)摘要本发明涉及冶金领域,尤其是一种转炉钢渣分离方法。
所要解决的技术问题是提供一种能高效率的实现对转炉钢渣进行分离和回收利用的转炉钢渣分离方法。
转炉钢渣分离方法,其特征在于,包括以下步骤:a 、将转炉钢渣进行热闷处理;b 、将转炉钢渣放入料仓,进行筛分;c 、经过料仓滚筛的筛分后分别得到筛出物和筛下物,其中筛下物放入到双层平筛进行筛分;d 、得到三种规格的物料,再将所述三种规格的物料依次经过半永磁磁辊;e 、所述半永磁磁辊得到精料、尾料、磁选料、尾粉。
本发明实现了对转炉钢渣的深度分离,充分的将转炉钢渣内含有的各组成部分实现回收利用,提高了转炉钢渣的利用率,本发明尤其适用于转炉钢渣中金属铁的分离工艺中。
(51)Int.Cl.权利要求书1页 说明书3页(19)中华人民共和国国家知识产权局(12)发明专利申请权利要求书1页 说明书3页(10)申请公布号CN 104313208 A1.转炉钢渣分离方法,其特征在于,包括以下步骤:a、将转炉钢渣放入渣坑进行热闷处理;b、将热闷后的转炉钢渣放入料仓,所述料仓内设置有料仓滚筛,由料仓滚筛对转炉钢渣进行筛分;c、经过料仓滚筛的筛分后分别得到筛出物和筛下物,其中筛下物放入到上层为60mm~100mm、下层为10mm的双层平筛进行筛分;d、经过双层平筛的筛分得到大小规格分别为60mm~200mm、10mm~60mm、0~10mm三种规格的物料,再将所述三种规格的物料依次经过半永磁磁辊;e、所述半永磁磁辊从60mm~200mm、10mm~60mm规格的物料中吸附得到含铁磁选物,将上述含铁磁选物放入到自磨机进行精选加工获得精料,而60mm~200mm、10mm~60mm规格的物料剩余的尾料用于高炉熔剂;所述半永磁磁辊从0~10mm规格的物料中吸附得到磁选料,所述磁选料用于烧结熔剂,而0~10mm规格的物料剩余的尾粉用于水泥生料或是混合材。
- 1、下载文档前请自行甄别文档内容的完整性,平台不提供额外的编辑、内容补充、找答案等附加服务。
- 2、"仅部分预览"的文档,不可在线预览部分如存在完整性等问题,可反馈申请退款(可完整预览的文档不适用该条件!)。
- 3、如文档侵犯您的权益,请联系客服反馈,我们会尽快为您处理(人工客服工作时间:9:00-18:30)。
2015/10/19
-VPG-
8
丁瑞锋, 王艳红, 冯士超, 潘秀兰. (2014). 大中型转炉出钢挡渣工艺技术研究现状. 上海金属
小结:
转炉出钢挡渣的发展趋势为从有形挡渣向无形挡渣进化,无形挡渣配备下 渣检测装置可实现出钢挡渣过程的全自动控制,这种效果好、可靠的挡渣法将成 为一种发展趋势。
滑板挡渣法
2015/10/19
以机械或液压控制方式开启或关闭出钢口, 达到挡渣的目的。 将滑板耐火原件安装到出钢 口。
-VPG-
5
转炉中的渣铁分离
2015/10/19
-VPG-
6
6
转炉挡渣实例
挡渣帽+挡渣镖:
为有针对性的控制不同阶段的下渣,本钢炼钢厂180t 转炉采用双挡渣 法工艺,即采用挡渣帽挡出钢开始时的前期下渣,再用挡渣镖挡出钢 结束时的后期下渣的方法。这两种挡渣方法的综合使用,使挡渣效果 明显提高,出钢后钢包渣厚一般可控制在80 ~ 90mm,有效降低了钢 水回磷,并为精炼处理等后部工序创造了良好条件。
钢冶金学课程报告
转炉炼钢时的渣铁分离
2015/10/19
-VPG-
1
目 转炉挡渣实例
2015/10/19
-VPG-
2
2
渣铁分离目的
1 1 1
可以减少钢水回磷,提高合金收得率;
2
减少钢中夹杂物,提高钢水清洁度;
3
可以减少钢包粘渣,提高钢包包龄;
4
同时可减少耐材消耗;
5
也可为钢水精炼提供良好的条件。
2015/10/19
-VPG-
3
3
转炉渣铁分离
转炉出钢期间,根据转炉倾角大小将整个出钢过程分为前期渣、过程渣和后 期渣三个下渣阶段,各下渣阶段大体上分别占转炉出钢到钢包下渣量的30%、 30%和40%。前期下渣和后期下渣如图1所示。
2015/10/19 -VPG-
4
对于较小公称容量的转炉,出钢时较多采用挡渣球和挡渣塞进行挡渣。
大中型转炉更多的采用如挡渣镖、气动挡渣法和滑板挡渣法。
2015/10/19
-VPG-
9
钢冶金学课程报告
谢谢!
2015/10/19
-VPG-
10
魏宝森 转炉的挡渣出钢技术探讨 2013
2015/10/19
-VPG-
7
滑板挡渣法
滑动挡渣法最有效的 控制前期和后期下渣挡渣 成功率可达百分之百,国 内宝钢自 2009 年开始逐 步采用滑板挡渣法 +AMEPA红外下渣检测技 术相结合的挡渣出钢技术, 挡渣成功率达100%,钢 包渣厚可稳定控制在 40mm以下。
4
转炉渣铁分离
挡渣法分类:
模式 挡渣帽 操作方法 出钢前将圆锥形铁皮挡渣帽 插入出钢口。 加入出钢口上方区域 工作原理 利用出钢口和挡渣帽之间的摩擦力封闭出 钢口,当转炉倾角足够大前期渣已经完全 通过出钢口区域时钢水可冲开挡渣帽进行 出钢。 挡渣球密度介于钢/渣之间,在出钢结束时 堵住出钢口,以阻止渣流入钢包内。
挡渣球 挡渣塞、镖法
电磁挡渣法 气动挡渣法
挡渣塞为一半球状并伴有一直径较小的导 出钢后期利用机械投掷装置 向棒的耐材制品,半球部分悬浮于渣液界 将挡渣塞导向棒部分插入出 面,随着出钢过程逐渐堵住出钢口,实现 钢口。 抑制涡流和挡渣的作用。 采用磁场使出钢口上方的钢水液面产生的 出钢口安装电磁泵 吸入涡流高度降低,防止炉渣卷入出钢口。 挡渣时,挡渣塞头对出钢口 进行机械封闭,赛头端部喷 射高压气体。 采用了炉渣流出检测装置,由发送和接受 信号原件和信号处理器组成,通过测出出 钢口流量的变化能准确的控制出钢时间。