11种常见的表面处理技术工艺
表面处理标准汇总

2
色漆和清漆-划痕试验
ISO 1518
3
色漆和清漆-弯曲试验(圆柱轴)
ISO 1519
4
色漆和清漆-压痕试验
ISO 1520
5
色漆和清漆-摆杆阻尼试验
ISO 1522
6
色漆和清漆、石油和相关产品闪点测定-闭杯平衡法
ISO 1523
7
色漆和清漆-研磨细度测定
ISO 1524
8
色漆和清漆-划格试验
HG/T 2-1047
3
电泳漆泳透力测定法
HG/T 2-1048
4
电泳漆库仑效率测定法
HG/T 2-1049
5
电泳漆沉积量测定法
HG/T 2-1050
6
电泳漆泳透力测定法(钢管法)
HG/T 2-1051
7
涂料粘度测定法
GB/T 1723
8
涂料细度测定法
GB/T 1724
9
涂料固体含量测定法
GB/T 1725
GB/T 15442.3
28
饰面型防火涂料防火性能分级及试验方法小室燃烧法
GB/T 15442.4
29
粉末涂料烘烤时质量损失测定
GB/T 16592
30
涂料产品检验,运输和储存通则
HG/T 2458
四.安全与环境保护标准
序号
标准名称
标准号
1
涂装作业安全规程涂漆前处理工艺安全及其通风净化
GB 7692
6
钢铁件涂装前除油程度检验方法(验油试纸法)
GB/T 13312
7
涂装前钢材表面锈蚀等级和除锈等级
GB/T 8923
8
11种去毛刺除毛刺方法选择
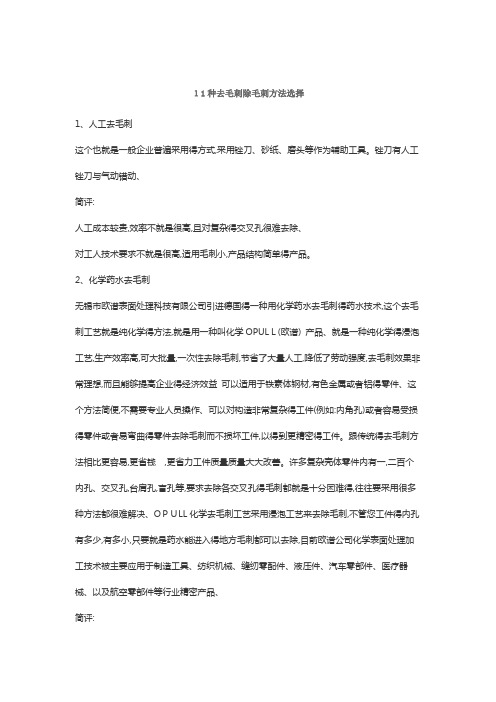
11种去毛刺除毛刺方法选择1、人工去毛刺这个也就是一般企业普遍采用得方式,采用锉刀、砂纸、磨头等作为辅助工具。
锉刀有人工锉刀与气动错动、简评:人工成本较贵,效率不就是很高,且对复杂得交叉孔很难去除、对工人技术要求不就是很高,适用毛刺小,产品结构简单得产品。
2、化学药水去毛刺无锡市欧谱表面处理科技有限公司引进德国得一种用化学药水去毛刺得药水技术,这个去毛刺工艺就是纯化学得方法,就是用一种叫化学OPULL(欧谱) 产品、就是一种纯化学得浸泡工艺,生产效率高,可大批量,一次性去除毛刺,节省了大量人工,降低了劳动强度,去毛刺效果非常理想,而且能够提高企业得经济效益可以适用于铁素体钢材,有色金属或者铝得零件、这个方法简便,不需要专业人员操作、可以对构造非常复杂得工件(例如:内角孔)或者容易受损得零件或者易弯曲得零件去除毛刺而不损坏工件,以得到更精密得工件。
跟传统得去毛刺方法相比更容易,更省钱,更省力工件质量质量大大改善。
许多复杂壳体零件内有一,二百个内孔、交叉孔,台肩孔,盲孔等,要求去除各交叉孔得毛刺都就是十分困难得,往往要采用很多种方法都很难解决、OPULL化学去毛刺工艺采用浸泡工艺来去除毛刺,不管您工件得内孔有多少,有多小,只要就是药水能进入得地方毛刺都可以去除,目前欧谱公司化学表面处理加工技术被主要应用于制造工具、纺织机械、缝纫零配件、液压件、汽车零部件、医疗器械、以及航空零部件等行业精密产品、简评:生产效率高,可大批量,一次性去除毛刺,节省了大量人工,降低了劳动强度,去毛刺效果非常理想,而且能够提高企业得经济效益?、3、冲模去毛刺采用制作冲模配合冲床进行去毛刺。
简评:需要一定得冲模(粗模+精冲模)制作费,可能还需要制作整形模、适合分型面较简单得产品,效率及去毛刺效果比人工佳。
4、研磨去毛刺此类去毛刺包含振动、喷砂、滚筒等方式,目前企业采用较多、简评:存在去除不就是很干净得问题,可能需要后续人工处理残余毛刺或者配合其她方式去毛刺。
(完整版)表面处理标准汇总

试验方法标准 醋酸-盐雾试验
ASTM B287
44
试验方法标准 铜加速的醋酸-盐雾试验(CASS试验)
ASTM B368
45
试验方法标准 用锥形挠曲机试验附着的有机涂层的伸长
ASTM D522
46
试验方法标准 镜面光泽
ASTM D523
47
方法标准 试验色漆、清漆、喷漆和有关产品用钢板的制备
ASTM D609
ISO 8130-9
38
金属的磷酸盐转化膜-确定要求的方法
ISO 9717
39
化学转化膜-铝及铝合金上的漂洗和不漂洗铬酸盐转化膜
ISO 10546
40
人造气氛腐蚀试验-盐雾试验
ISO 9227
41
金属材料上的转化膜-单位面积上膜层质量的测量-重量法
ISO 3892
42
试验方法标准 盐雾试验
ASTM B117
GB 14443
6
污水综合排放标准
GB 8978
国际标准部分
序号
标准名称
标准号
1
色漆和清漆-试验用标准样板
ISO 1514
2
色漆和清漆-划痕试验
ISO 1518
3
色漆和清漆-弯曲试验(圆柱轴)
ISO 1519
4
色漆和清漆-压痕试验
ISO 1520
5
色漆和清漆-摆杆阻尼试验
ISO 1522
6
色漆和清漆、石油和有关产品闪点的测定-闭杯平衡法
ASTM E376
69
试验方法标准 管道涂层的耐冲击性(石灰石落降试验)
ASTM G13
70
试验方法标准 管道涂层的耐冲击性(落锤试验)
11-表面工程技术PPT模板

1 渗钛与离子渗氮复合处理
2 渗碳、渗氮、碳氮共渗与渗硫复合处理
3 液体碳氮共渗与高频感应加热表面淬火的复合强化
4 激光与离子渗氮复合处理
— 10 —
1.3 复合表面处理技术
2.表面覆层技术与其他表面处理技术的复合
表面覆层技术与其他表面处理技术 的复合,即利用各种工艺方法在工件表 面上形成各种覆层,如镀层、涂层、沉 积层或薄膜,经过适当的热处理,使覆 层中的金属原子向基体扩散,或与基体 进行冶金熔合,不仅可增强覆层与基体 的结合强度,同时也能改变表面覆层本 身的成分,防止覆层剥落,并可提高覆 层的强韧性,提高表面的抗擦伤力、耐 磨损和耐腐蚀能力。
— 6—
1.2 表面覆层技术
1.热喷涂
火焰喷涂
等离子喷涂
如 图 4-5 所 示 , 火 焰 喷 涂 借 助 高 速
气流将喷涂的粉末吸入火焰区,加热到
熔融或高塑性状态后喷射到粗糙的基体
表面形成涂层;或将线材或棒材送入氧-
乙炔火焰区加热熔化,借助压缩空气使
其雾化成颗粒,再喷向粗糙的基体表面 形成涂层。
激光表面熔覆是采 用大功率激光束扫 描金属表面,将选 定的材料熔化到金 属表面,形成具有 硬度高、耐磨性好、 抗腐蚀等特性的涂 覆层。
激光表面熔凝是 采用高能量密度 的激光,使材料 表面层快速熔化, 然后依靠材料自 身快速冷却凝固, 从而获得非常细 密的非平衡快速 凝固组织。
激光表面合金化是 利用高能量的激光 束使根据需求加入 的合金涂层与基体 金属表面混合熔化, 在极短的时间内, 形成与基体不同化 学成分和结构的表 面合金层。
热喷涂技术采用气体、液体或电弧、 等离子、激光等作为热源,将金属、合金、 陶瓷、氧化物、碳化物、塑料以及其复合 材料加热到熔融或半熔融状态,通过高速 气流使其雾化,然后喷射、沉积到经过预 处理的工件表面,从而形成附着牢固的表 面层。
螺丝磷化工艺介绍
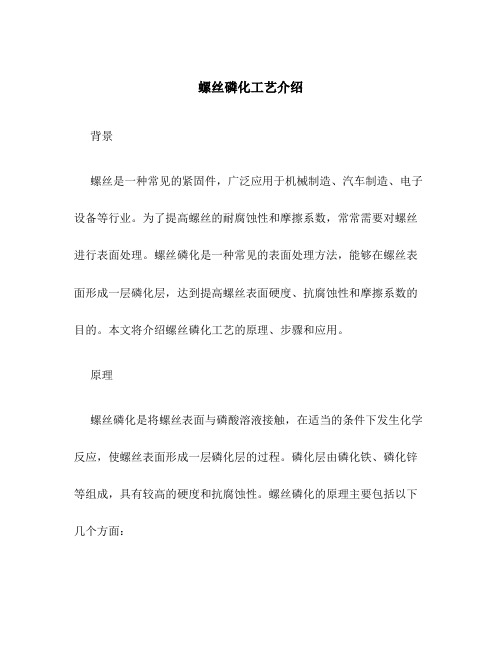
螺丝磷化工艺介绍背景螺丝是一种常见的紧固件,广泛应用于机械制造、汽车制造、电子设备等行业。
为了提高螺丝的耐腐蚀性和摩擦系数,常常需要对螺丝进行表面处理。
螺丝磷化是一种常见的表面处理方法,能够在螺丝表面形成一层磷化层,达到提高螺丝表面硬度、抗腐蚀性和摩擦系数的目的。
本文将介绍螺丝磷化工艺的原理、步骤和应用。
原理螺丝磷化是将螺丝表面与磷酸溶液接触,在适当的条件下发生化学反应,使螺丝表面形成一层磷化层的过程。
磷化层由磷化铁、磷化锌等组成,具有较高的硬度和抗腐蚀性。
螺丝磷化的原理主要包括以下几个方面:1.化学反应:螺丝表面的铁、锌元素与磷酸发生化学反应,生成磷酸铁、磷酸锌等磷化物。
2.反应条件:螺丝的磷化过程需要适宜的温度、PH值和反应时间等条件。
通常情况下,磷化反应在60-100°C的温度下进行,PH值控制在2-4之间。
3.磷化层结构:螺丝磷化层由磷酸铁、磷酸锌等磷化物组成,具有较高的硬度和抗腐蚀性。
磷化层的厚度可以根据需要进行控制,一般为3-8μm。
步骤螺丝磷化的工艺步骤主要包括以下几个环节:1.清洗:将螺丝放入清洗槽中,在适当的温度和清洗剂中进行清洗,去除螺丝表面的油污和杂质。
2.酸洗:将清洗后的螺丝放入酸洗槽中,在适当的温度和酸性溶液中进行酸洗,去除表面氧化物和锈迹。
3.磷化:将酸洗后的螺丝放入磷化槽中,浸泡在适当的磷酸溶液中,使螺丝表面与磷酸发生化学反应,形成磷化层。
4.中和:将磷化后的螺丝放入中和槽中,在适当的温度和碱性溶液中进行中和处理,中和残留在螺丝表面的酸性物质。
5.清洗:将中和后的螺丝进行清洗,去除残留在螺丝表面的碱性物质。
6.干燥:将清洗后的螺丝进行干燥处理,使螺丝表面完全干燥。
应用螺丝磷化广泛应用于机械制造、汽车制造、电子设备等行业,其应用主要包括以下几个方面:1.提高耐腐蚀性:螺丝磷化后,在螺丝表面形成的磷化层能够有效增加螺丝的耐腐蚀性,延长使用寿命。
2.提高摩擦系数:螺丝磷化后,磷化层能够增加螺丝与配合件之间的摩擦系数,改善螺丝的防松性能。
材料表面处理技术

阳极氧化膜无色透明,含锰或硅的铝合金的氧化膜则为浅灰 色或棕灰色。
工艺流程
机械准备(包括抛光)——除油——水洗——浸蚀(或化 学抛光、电化学抛光)——水洗——阳极氧化——水洗——着 色——水洗——封闭——水洗——干燥
阳极氧化膜的着色-化学着色
5~6
5~6
4.5~5.5
6~7
5~6 5~6 5~6 5~6 6.5~7.5 5~6 5~5.5 5~6
5~5.5 4.5~5.5 5~5.5
5.喷砂
是采用压缩空气为动力,以形成高速喷射束将喷料(铜矿 砂、石英砂、金刚砂、铁砂、海砂)高速喷射到被需处理工 件表面,使工件表面的外表面的外表或形状发生变化,由于 磨料对工件表面的冲击和切削作用,使工件的表面获得一定 的清洁度和不同的粗糙度,使工件表面的机械性能得到改善, 因此提高了工件的抗疲劳性,增加了它和涂层之间的附着力, 延长了涂膜的耐久性,也有利于涂料的流平和装饰。
5.喷砂实物
铝轮表面喷砂去氧化皮处理
铝制件去氧化皮、亚光处理
6.真空镀膜
基本原理: 在真空条件下,把镀膜材料加热蒸发,使之汽化沉积在制品 表面上形成固态薄膜。 被镀金属材料可以是金、银、铜、锌、铬、铝等,其中用得 最多的是铝。 主要用于在经予处理的塑料、陶瓷等制品表面蒸镀金属薄膜、 七彩膜仿金膜等,从而获得光亮、美观、价廉的塑料,陶瓷表面 金属化制品。广泛应用于工艺美术、装璜装饰、灯具、家具、 玩具、酒瓶盖、女式鞋后跟等领域。 用户选择在灯具基体上喷底漆、镀铝膜、镀保护膜或灯具基 体在真空室进行前处理(不喷底漆)、镀铝膜、镀保护膜工 艺。
金属转化膜是指金属表面的原子层与某些特定介质的阴离子 反应后,在金属表面生成的膜层。
手机表面处理工艺(绝密)

1. 表面处理工艺1.1 适用于塑胶零件工艺1.1.1 原色(表面没有做任何工艺)优点:省喷涂费用(前后壳、电池盖需3-5块钱)1.1.1.1 光面模具省光,模具电镀 缺点:产品表面不耐磨1.1.1.2 幼纹面模具上晒纹(蚀纹),晒纹的样式是根据纹板1.1.1.3 粗纹面1.1.2 丝印即丝网印刷,移印(厚度0.01)(承印物为不规则的异形表面)1.1.2.1 丝印先做菲林1.1.2.1.1 一次只能印刷一种颜色1.1.2.1.2 两个颜色的图案及字符可选用丝印(印2次)多个图案的采用转印(例如丝印6次,如果第六次出现不良品,前面5次就白印了) 1.1.2.1.3 丝印后会过光油及UV,否则容易脱落金属丝印或者移印需在100-150°高温下干固45分钟1.1.2.1.4 可丝印圆柱形状1.1.2.2 移印由于其在小面积、凹凸面的产品上面进行印刷具有非常明显的优势,弥补了丝网版印刷工艺的不足1.1.2.2.1 移印定义适用于在曲面和平面上印刷,但油墨成本较丝印而言较高 1.1.3 普通喷涂(产品表面越光附着力越差)1.1.3.1 普通喷涂(厚度0.02)1.1.3.2 高光漆1.1.3.3 哑光漆1.1.3.4 流程1.1.3.4.1 除尘(除脂)1.1.3.4.2 底漆1.1.3.4.3 烘干1.1.3.4.4 面漆1.1.3.4.5 烘烤1.1.4 UV漆(高光UV,亚光UV。
底漆+UV厚度≈0.02)为了增加涂层表面的耐磨性,通常产品外表面喷涂底漆后再喷涂一层紫外固化的UV涂料1.1.4.1 UV工艺在手机中的应用UV工艺在手机中应用得最多的是-UV上光油,而且主要目的是保护上一道工序中漆层或镀层;增强外观效果;以及部件真空镀后产品表面的固化等作用。
1.1.4.2 UV漆特点1.1.4.2.1 硬度高。
最高硬度可达5~6H手机壳一般做1~2H左右,太高了胶塑性减弱 1.1.4.2.2 耐磨、耐酸碱、耐盐雾、耐汽油1.1.4.2.3 表面光亮1.1.4.2.4 固化速度快,生产效率高普通喷涂需要烘烤1.1.4.2.5 胶件不易变形1.1.4.2.6 环保1.1.4.3 UV漆缺点1.1.4.3.1 生产设备贵1.1.4.3.2 生产环境要求高10000级以上防尘车间1.1.4.4 普通底漆+UV漆喷涂流程工件表面的清洁→普通底漆喷涂烘干→UV光油的开稀过滤→喷涂施工→55°C~65°C流平3~7分钟→UV灯固化→检验,成品1.1.4.5 UV工艺常见问题及解决1.1.4.5.1 麻点现象 a.油墨发生了晶化现象 b.表面张力值大,对墨层润湿作用不好1.1.4.5.2 条痕和起皱现象 a.UV油太稠,涂布量过大,主要出现在辊涂中1.1.4.5.3 气泡现象 a.所用UV油质量不高,UV油本身含有气泡,多发生在用丝网上光中1.1.4.5.4 桔皮现象 a.UV油粘度高,流平性差。
涂层技术概述
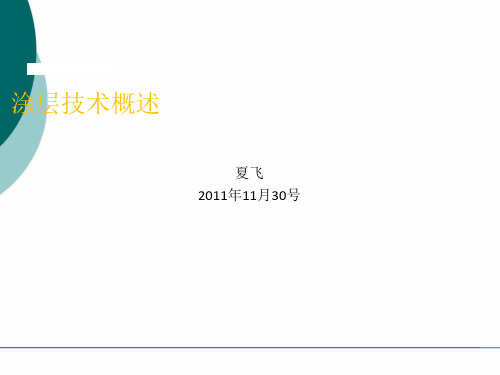
磨痕仪
球坑法是一种简易实用的镀层厚度测试方法,球 磨后,在镀层样品上形成一球坑,通过正确的测 量分析,可快速得出镀层的准确厚度。
基涂球体层
划痕仪
• 用金刚石压头划出划痕,看涂层的破裂情况,用临界载荷评价涂层结合
• 表征涂层 • 耐划伤能力 • 结合力 • 摩擦系数
(如果有配件)
• 分析
• 临界载荷(Lc) • 划痕形貌
• 涂层技术和应用
薄膜和涂层制备方法
1.热喷涂技术
利用热源将喷涂材料加热至溶化或半溶化状态,并以一定的速度喷射沉积到经过预处理的 基体表面形成涂层的方法 分类:低压等离子喷涂、大气等离子喷涂、爆炸喷涂、高速氧焰喷涂、中温喷涂,冷喷涂等 特点:沉积速率快,但表面粗糙,需要后续处理, 适合较厚涂层
2.物理气相沉积技术(PVD)
摩擦磨损
针盘式摩擦实验
✓摩擦系数 ✓磨损寿命 ✓磨损速率
光学显微镜
扫描电子显微镜
Quelle: Wikipedia
பைடு நூலகம்
自然界的矿物分为10个硬度等级,所有的物体应 该在这个范围内
布氏硬度
压头: 球 (硬质合金或淬硬钢)
压头
布氏和维氏硬度
维氏硬度
压头: 金字塔形 (金刚石)
压头
样品
d
样品
1. 定位
显微硬度测量
2. 压痕
3. 硬度计算
纳米压痕方法
✓深分对度之于一一涂般,以层小避硬于免度涂基的层体测厚的量度影,的压响十痕
4.湿法沉积
电镀,化学镀等
价格便宜.
薄膜和涂层示例 刀具涂层
DDP
光学镜片涂层
光学滤镜
光电涂层
表面涂层主要分析方法
表面处理-技术手册

技术手册油漆涂装施工 (1)一、表面处理 (1)二、漆膜厚度 (1)三、干膜厚度的测量 (1)四、涂覆方法 (2)1、刷涂 (2)2、滚涂 (2)3、空气喷涂(传统式) (2)4、空气喷涂(带压力罐) (3)4、高压无气喷涂 (3)5、涂覆时的各种条件 (4)常用换算及公式 (5)一、常用单位的换算 (5)二、涂料用量简单计算 (6)三、湿膜厚度的控制 (6)四、漆膜重量的计算 (6)五、钢板面积的计算 (7)五、管道面积的计算方法 (7)六、钢梁及角钢面积的估算 (8)表面处理 (9)一、前言 (9)二、锈蚀等级标准 (9)1、钢丝刷除锈标准- St (9)2、喷砂除锈标准- Sa (9)三、表面处理方法和设备的确认 (10)1、去除疏松油漆和厚锈 (10)2、机械钢丝刷除锈 (10)3、手工钢丝刷 (10)4、机械砂轮打磨 (10)5、喷砂除锈 (11)6、喷砂除锈注意事项 (11)7、湿喷砂处理/喷砂浆处理 (12)8、高压水喷射 (12)9、施工于完整油漆上的表面处理 (13)10、铝质和镀锌钢材的预处理 (13)11、混凝土墙体表面 (13)11、混凝土地面 (14)12、安全注意事项 (14)四、涂装前的钢铁表面处理 (15)1、喷砂除锈 (15)2、车间底漆的涂装 (15)3、底漆涂装前的准备 (15)五、涂装的注意事项 (15)1.、膜厚的控制 (15)2. 涂料的配制 (16)3、稀释剂的使用 (16)4、涂装的间隔 (16)5、涂膜的异常 (16)6、涂装环境 (16)7、漆膜的完全固化 (17)六、涂料及涂膜产生弊病的原因 (17)1、涂料本身的质量 (17)2、施工基层状况 (17)3、涂装工艺 (17)4、施工操作 (17)5、施工环境 (17)油漆涂装施工金属的腐蚀与破坏都是从表面开始,假如在它的表面与介质之间插入稳定的或耐蚀的物质,使金属表面与介质不能接触,金属的腐蚀便会停止。
模具表面处理种类及规格

Fine Fine Medel Grov
符号 VDI12 VDI15 VDI18 VDI21 VDI24 VDI27 VDI30 VDI33 VDI36 VDI39 VDI42 VDI45
粗糙度 Ra 0.40 Ra 0.50 Ra 0.80 Ra 1.12 Ra 1.60 Ra 2.24 Ra 3.15 Ra 4.50 Ra 6.30 Ra 9.00 Ra 12.5 Ra 18.0
SPIB-1
SPIC-1
SPID-1
SPIA-2
(良好脱模和外观)
SPIB-2
SPIC-2
SPID-2
SPIA-3
(良好脱模,外观无 需高光)
SPIB-3
SPIC-3
SPID-3
火花纹(Thin Fire Texture)
号码
0 1 2 3 4 5 6 7 8 9 10 11 12 13 14 15 16 17 18 19 20
MT Specification
单位:mm
咬花深度
0.0102
0.0254
0.0381
0.0508
0.0762
0.1143
0.0762
0.0762
0.0508
0.0889
0.1524
0.0635
0.0508
0.0635
0.0635
0.0698
0.1016
Ptn.# MT-11000 MT-11010 MT-11020 MT-11030 MT-11040 MT-11050 MT-11060 MT-11070 MT-11080 MT-11090 MT-11100 MT-11110 MT-11120 MT-11130 MT-11140 MT-11150 MT-11160
表面处理简介_防腐

EC painting
Electroplated coating of Tin Y 108
Y 108
Electroplated coating of Zinc with chromating Y 105
Y 105
Electroplated coatings of zinc-iron with chromating Phosphating Y 104 Painting Y 520 Zinc-chromate metal and organic coating painting Y 500 painting Y 511 painting Y 550 painting Y 600 painting Y 650 K1,K2,K3,K4
表面处理简介
防腐工艺
目录
一.表面处理的分类 二.金属腐蚀的介绍 三.防腐表面处理方式分类 四.发黑 五.防锈剂 六.热浸锌 七.电镀 八.钝化 九.理方式 一三.防腐能力排序
表面处理的分类
按照表面处理的功用,大致可以分为以下三类:
防腐表面处理 表面处理方式的目的是为了减缓基层材料的腐蚀速度。主要的处理方式如下:
Fe/Zn-Fe C Y104
Y 520 Y 500 Y 511 Y 550 Y 600 Y 650 K1,2,3,4
STD 121-0009 STD 5771,7 STD 121-0006
STD 5752,53 STD 121-0003 STD 121-0004
STD 121-0012
STD 121-0013 STD 5732,11 STD 5732,12 STD 5732,109 STD 1281,21 STD 5732,108 STD 5732,105 STD 5732,104 STD 5742,104
石材的表面加工处理工艺

石材的表面加工处理工艺荔枝面石材不是火烧面的一种。
但都是表面糙化石材的处理方式。
表面糙化的方式还有:1、自然霹雳面2、蘑菇面3、烧毛面4、机刨面5、喷砂面。
表面纹理的区别是:荔枝面石材就是表面的点是凸出来的那种石材,(火烧面大多是凹进去的)天然石材常见的表面加工(Surface Finishing)方法:1.抛光(Polished):表面非常的平滑,高度磨光,有镜面效果,有高光泽。
花岗岩、大理和石灰石通常是抛光处理,并且需要不同的维护以保持其光泽。
2.亚光(Honed):表面平滑,但是低度磨光,产生漫反射,无光泽,不产生镜面效果,无光污染。
3.粗磨(Rough-Rubbing):表面简单磨光,把毛板切割过程中形成的机切纹磨没即可,感觉是很粗糙的亚光加工。
4.机切(Machine-Cut):直接由圆盘锯砂锯或桥切机等设备切割成型,表面较粗糙,带有明显的机切纹路。
5.酸洗(Pickling):用强酸腐蚀石材表面,使其有小的腐蚀痕迹,外观比磨光面更为质朴。
大部分的石头都可以酸洗,但是最常见的是大理石和石灰石。
酸洗也是软化花岗岩光泽的一种方法。
6.荔枝(Bushhammered):表面粗糙,凹凸不平,是用凿子在表面上密密麻麻的凿出小洞,有一模仿水滴经年累月的滴在石头上的一种效果。
7.菠萝(Picked):表面比荔枝加工更加的凹凸不平,就像菠萝的表皮一般。
8.剁斧(Chiselled):也叫龙眼面,是用斧剁敲在石材表面上,形成非常密集的条状纹理,有些像龙眼表皮的效果。
9.火烧(Flamed):表面粗糙。
这种表面主要用于室内如地板或作商业大厦的饰面,劳动力成本较高。
高温加热之后快速冷却就形成了火烧面。
火烧面一般是花岗岩。
10.开裂(Nature Split):俗称自然面,其表面粗糙,不过不像火烧那样粗糙。
这种表面处理通常是用手工切割或在矿山錾以露出石头自然的开裂面。
11.翻滚(tumbled):表面光滑或稍微粗糙,边角光滑且呈破碎状。
材料表面处理

材料表面处理
材料表面处理是指对材料表面进行改性,以增强其性能、延长使用寿命、改善外观等目的的一系列工艺过程。
材料表面处理在工业生产中起着至关重要的作用,它可以改善材料的表面性能,提高材料的耐腐蚀性、耐磨损性、耐高温性等,从而满足不同工程应用的需求。
首先,材料表面处理的方法有很多种,常见的包括化学处理、物理处理、机械处理等。
化学处理包括酸洗、镀锌、阳极氧化等,物理处理包括喷砂、喷丸、激光熔覆等,机械处理包括打磨、抛光、刻蚀等。
不同的材料和不同的工程要求需要选择不同的表面处理方法,以达到最佳的效果。
其次,材料表面处理的目的主要有三个方面。
一是提高材料的耐腐蚀性能,例如在海洋工程中需要对金属材料进行防腐处理,以延长其使用寿命。
二是改善材料的外观,例如对汽车零部件进行喷涂或镀层处理,以提高其美观度和抗氧化性能。
三是增强材料的机械性能,例如对钢铁材料进行热处理,以提高其硬度和强度。
最后,材料表面处理在实际应用中需要注意一些问题。
首先,要选择合适的表面处理方法,根据材料的特性和工程要求进行合理选择。
其次,要控制好表面处理的工艺参数,包括处理温度、处理时间、处理介质等,以确保处理效果。
最后,要进行质量检验,确保表面处理后的材料符合相关标准和要求。
总的来说,材料表面处理是一项非常重要的工艺过程,它可以改善材料的性能和外观,满足不同工程应用的需求。
在实际应用中,我们需要根据具体情况选择合适的表面处理方法,控制好工艺参数,并进行质量检验,以确保处理效果和产品质量。
希望本文对材料表面处理有所帮助,谢谢阅读。
内孔去毛刺的十一种方法
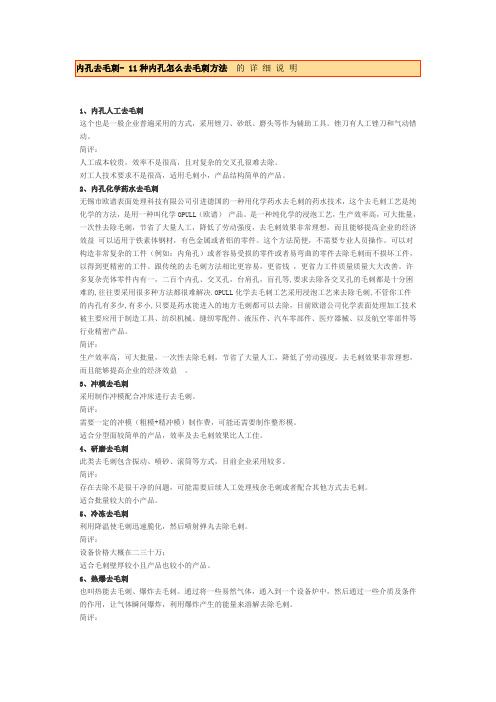
1、内孔人工去毛刺这个也是一般企业普遍采用的方式,采用锉刀、砂纸、磨头等作为辅助工具。
锉刀有人工锉刀和气动错动。
简评:人工成本较贵,效率不是很高,且对复杂的交叉孔很难去除。
对工人技术要求不是很高,适用毛刺小,产品结构简单的产品。
2、内孔化学药水去毛刺无锡市欧谱表面处理科技有限公司引进德国的一种用化学药水去毛刺的药水技术,这个去毛刺工艺是纯化学的方法,是用一种叫化学OPULL(欧谱)产品。
是一种纯化学的浸泡工艺,生产效率高,可大批量,一次性去除毛刺,节省了大量人工,降低了劳动强度,去毛刺效果非常理想,而且能够提高企业的经济效益可以适用于铁素体钢材,有色金属或者铝的零件。
这个方法简便,不需要专业人员操作。
可以对构造非常复杂的工件(例如:内角孔)或者容易受损的零件或者易弯曲的零件去除毛刺而不损坏工件,以得到更精密的工件。
跟传统的去毛刺方法相比更容易,更省钱,更省力工件质量质量大大改善。
许多复杂壳体零件内有一,二百个内孔、交叉孔,台肩孔,盲孔等,要求去除各交叉孔的毛刺都是十分困难的,往往要采用很多种方法都很难解决.OPULL化学去毛刺工艺采用浸泡工艺来去除毛刺,不管你工件的内孔有多少,有多小,只要是药水能进入的地方毛刺都可以去除,目前欧谱公司化学表面处理加工技术被主要应用于制造工具、纺织机械、缝纫零配件、液压件、汽车零部件、医疗器械、以及航空零部件等行业精密产品。
简评:生产效率高,可大批量,一次性去除毛刺,节省了大量人工,降低了劳动强度,去毛刺效果非常理想,而且能够提高企业的经济效益。
3、冲模去毛刺采用制作冲模配合冲床进行去毛刺。
简评:需要一定的冲模(粗模+精冲模)制作费,可能还需要制作整形模。
适合分型面较简单的产品,效率及去毛刺效果比人工佳。
4、研磨去毛刺此类去毛刺包含振动、喷砂、滚筒等方式,目前企业采用较多。
简评:存在去除不是很干净的问题,可能需要后续人工处理残余毛刺或者配合其他方式去毛刺。
适合批量较大的小产品。
表面处理工艺英文缩写

表面处理工艺英文缩写表面处理工艺是指对材料表面进行物理或化学处理,以改变其表面性能或满足特定要求的一种工艺。
在不同的领域,表面处理工艺有许多种类和方法。
为了方便交流和标识,各种表面处理工艺通常都有相应的英文缩写。
防护性表面处理1.耐蚀处理 (AC):Anti-corrosion treatment2.防氧化处理 (AO):Anti-oxidation treatment3.防尘处理 (AD):Anti-dust treatment4.防盐雾处理 (AS):Anti-salt fog treatment5.防风化处理 (AW):Anti-weathering treatment表面改性处理1.表面涂覆处理 (SC):Surface coating treatment2.表面喷涂处理 (ST):Surface spraying treatment3.表面沉积处理 (SD):Surface deposition treatment4.表面合金化处理 (SA):Surface alloying treatment5.表面等离子处理 (SP):Surface plasma treatment表面修饰处理1.表面抛光处理 (SP):Surface polishing treatment2.表面激光处理 (SL):Surface laser treatment3.表面电刷处理 (SB):Surface brush treatment4.表面烧蚀处理 (SE):Surface eroding treatment5.表面喷丸处理 (SW):Surface shot blasting treatment表面功能化处理1.表面涂层处理 (SC):Surface coating treatment2.表面改变电阻率处理 (SR):Surface resistance altering treatment3.表面改变导电性处理 (SC):Surface conductivity altering treatment4.表面改变磁性处理 (SM):Surface magnetism altering treatment5.表面改变光学性质处理 (SO):Surface optics altering treatment其他常见缩写1.热处理 (HT):Heat treatment2.精密表面处理 (SP):Precision surface treatment3.涂覆层厚度测试 (CT):Coating thickness testing4.表面粗糙度测试 (SR):Surface roughness testing5.表面硬度测试 (SH):Surface hardness testing每种表面处理工艺都有其特定的表现效果和适用范围。
铜排镀锡等表面处理工艺

铜排镀锡等表面处理三种工艺铜排镀锡等表面处理三种工艺1. 铜排涂漆1.1。
此工艺属于淘汰落后工艺,现很少使用。
1.2。
三相交流电路的母线均涂黑漆,在显眼处粘贴色标,A相为黄色,B相为绿色,C相为红色,零线或中性线涂淡蓝色漆,安全用的接地线涂交替黄绿双色漆,无法区分极性、相序者涂白漆。
1.3. 直流电路的正极涂棕漆,负极涂蓝色漆,接地中线涂淡蓝色漆。
1.4。
检查母线的涂漆是否均匀,是否有流挂现象。
1.5。
母线涂漆可采用喷漆或刷漆,色泽应均匀,边缘应整齐,不得有漏漆、挂漆现象,母线连接处不得沾漆。
1.6。
同一元件,同一端的各相母线的涂漆界线应无明显不整齐现象。
1。
7。
母线的涂漆界线平齐。
2。
铜排镀锡2。
1. 工艺成熟。
操作周期短,普遍采用.2。
2。
弱点:时间长了表面发暗,人手做不到.不环保!2.3. 工艺流程2。
3。
1。
表面抛光除油等前处理→纯水洗→镀高Pb—Sn合金个自来水洗→纯水洗→镀锡→自来水喷洗→中和(Na2HPO4+Na3PO4)→自来水喷洗→浸硬脂酸→自来水喷洗→热纯水浸洗→烘干。
2。
4. 铜排表面处理工艺抛光:无论是人工还是机械都慢,而且累,粉尘很严重,清理表面氧化皮,微小毛刺.(用石英砂,玻璃丸)。
2。
5. 镀液各成分作用及工艺流程2.6. 光亮硫酸盐镀锡液主要成分为硫酸亚锡和硫酸,生产中其含量随所采用的添加剂不同而不同.2.6。
1。
硫酸亚锡为主盐,含量十般控制在40~100g/L。
但生产实验结果表明,高浓度硫酸亚锡虽然可以提高阴极电流密度,加快沉积速度,但使镀液分散能力明显下降,且使镀层结晶粗、光亮区域变小,甚至大大缩短了镀液的处理周期。
2.6.2。
SnSO4含量控制在20~60g/L为宜,若取下限,可以通过加快镀液循环速度及电极(阴极或阳极)移动速度等办法进行“补偿",仍可镀出优良产品,但不宜过低.2。
7。
硫酸具有降低亚锡离子的活性、防止其水解、提高镀液导电性能及阳极电流效率等作用。
- 1、下载文档前请自行甄别文档内容的完整性,平台不提供额外的编辑、内容补充、找答案等附加服务。
- 2、"仅部分预览"的文档,不可在线预览部分如存在完整性等问题,可反馈申请退款(可完整预览的文档不适用该条件!)。
- 3、如文档侵犯您的权益,请联系客服反馈,我们会尽快为您处理(人工客服工作时间:9:00-18:30)。
11种常见的表面处理
技术工艺
在机械加工及表面处理行业,通常材料需要完成毛坯下料、车削加工、铣削加工、钻孔攻丝、热处理、磨削等一系列加工工序后,还需要进行各种表面处理。
它利用现代物理化学、金属学和热处理学等学科的边缘性新技术来改变零部件表面的状况和性质,使之与内部材料作优化组合,以达到预定性能要求。
目前,表面处理技术可分为:表面强化处理、表面洁化处理、表面装饰处理、表面防蚀处理以及表面修复处理。
其中,常用的表面处理方法包括:热喷涂、喷丸、表面滚压和胀光、离子镀、激光表面强化、抛光、普通电镀、特种电镀、钢铁发蓝、钢铁磷化、铝阳极氧化及着色处理、喷漆与喷塑等。
01 热喷涂
特点:* 工艺灵活,适用范围广。
热喷涂施工对象可大可小,小的可到直径10mm内孔(线爆喷涂),大的可到桥梁、铁塔(火焰线材喷涂或电弧喷涂),可在室内喷涂,也可在户外现场作业;可整体喷涂,也可局部喷涂。
* 基体及喷涂材料广泛,可通过喷涂不同材料,使工件表面获得所需的各种物理和化学性能。
* 工件应力变形小,基体可保持较低的温度,工件产生的应力变形很小。
* 生产效率高,每小时喷涂材料重量从几千克到几十千克,且沉积效率高。
应用:* 防腐蚀:主要用于大型水闸钢闸门、造纸机烘缸、煤矿井下钢结构、高压输电铁塔、电视台天线、大型钢桥梁、化工厂大罐和管道的防腐喷涂。
* 防磨损:通过喷涂修复已磨损的零部件,或在零部件易磨损部位预先喷涂上耐磨材料,如风机主轴、高炉风口、汽车曲轴、机床主轴、机床导轨、柴油机缸套、油田钻杆、农用机械刀片等。
* 特殊功能层:通过喷涂获得表层某些特殊性能,如耐高温、隔热、导电、绝缘、防辐射等,在航空航天和原子能等部门应用较多。
02 喷丸
特点:* 利用高速喷射出的砂丸,对工件表面进行撞击,以提高零部件的部分力学性能和改变表面状态的工艺方法。
* 喷丸通常是直径为0.5-2mm的沙粒或铁丸。
沙粒的材料多为氧化铝或二氧化硅。
表面处理的效果与丸粒的大小、喷射速度和持续时间有关。
* 喷丸用于提高零部件机械强度及耐磨性、抗疲劳和耐蚀性等,还可用于表面消光、去氧化皮和消除铸、锻、焊件的残余应力等。
03 表面滚压和胀光
特点:* 表面滚压是在常温上用硬质滚柱或滚轮施压于施转的工件表面上,并沿母线方向移动,使工件表面塑性变形硬化,以获得光洁和强化的表面。
* 表面胀光(挤光或挤压)是在常温下将直径稍大于孔径的钢球或其他形状的胀光工具挤过工件已加工的内容,以获得光洁和强化的表面。
04
特点:* 离子镀是将镀层材料气化并电离成离子,通过扩散和电场作用,沉积于制件表面,形成与基体牢固结合的满足所需性能的镀层。
* 离子镀的种类很多,其绕射性均很好,能镀覆制件上各个方向的表面,可在金属或非金属表面上镀覆金属或合金,镀层厚度一般为2-3mm。
* 离子镀已广泛用于机械、电子、航空、航天、轻工、光学和建筑等部门,用以制备耐磨、耐蚀、耐热、超硬、导电、磁性和光电转换等镀层。
05 激光表面强化
特点:* 使用聚焦的激光束射向钢件表面,在极短时间内将工件表层极薄的材料加热到相变温度或熔点以上的温度,又在极短时间内冷却,使工件表面淬硬强化。
* 热影响区小,变形小,工件表面清洁,操作方便。
* 主要用于局部强化的零部件,如冲裁模、曲轴、凸轮、凸轮轴、花键轴、精密仪器导轨、高速钢刀具、齿轮及内燃机缸等。
06
特点:抛光是对零部件表面进行修饰的一种光整加工方法,一般只能得到光滑表面,却不能提高甚至不能保持原有的加工精度,随预加工状况不同,抛光后的Ra值可达1.6-0.008μm。
1. 机械抛光:①轮式抛光用高速旋转的柔性抛光轮和极细的磨料对工件表面进行滚压和微量切削实现抛光。
抛光轮用多层帆布、毛毡或皮革叠纸而成,用于较大的零部件。
②滚筒抛光和振动抛光,将工件、磨料和抛光液装入滚筒或振动箱内,滚筒缓慢滚动或振动箱振动,使工件与工件,工件与磨料互相摩擦,加上抛光液的化学作用,除去工件表面油污、锈层,磨去凸峰,从而获得光滑的表面。
用于细小而量大零部件,后者比前者生产率高,抛光效果好。
2. 化学抛光:将金属零部件浸入特制的化学溶液中,利用金属表面凸起部位比凹洼部位溶解速度快的现象,实现零部件表面的抛光。
3. 电化学抛光:电化学抛光与化学抛光类似,不通电是还要以直流电,工件接阳极,产生阳极溶解,也是利用金属表面凸起部位比凹洼部位溶解速度快的现象进行抛光。
07 特种电镀
1. 刷镀:刷镀不用镀槽,旋转的工件接直流电源的负极,镀笔接正极,镀笔前端用脱脂棉包住,浇注的镀液浸贮在脱脂棉套内,镀液中的金属正离子在电场力作用下的工件表面(阴极)获得电子而沉积于表面,形成电镀层。
- 镀层厚度可达0.01-0.05mm,镀层质量好,结合强度高,速度比槽镀快。
- 刷镀设备简单,操作灵活,可进行局部电镀和户外作业。
- 对于大批量中小型零部件或大面积镀覆的工件进行装饰性或尺寸电镀时,刷镀不如槽镀。
- 刷镀主要用于大型零部件的局部电镀或大中型零部件的局部修复。
2. 非金属电镀:是指对塑料、玻璃、陶瓷、纤维等非金属制品电镀。
- 非金属电镀的关键工艺是表面金属化,使非金属基体上生成导电层以便进行导电。
表面金属化的方法有化学镀法、喷涂法、烧渗银法和涂刷法等。
- 塑料电镀是非金属电镀中应用最广泛的一种。
通过电镀可提高塑料制品的强度,防止老化,使其具有导电性、电磁性、焊接性和装饰性外观。
- 非金属电镀制品主要用于汽车、飞机某些装饰性零部件及印刷线路板、电子仪器屏蔽和碳纤维等。
08
特点:* 钢铁发蓝:是对钢铁零部件进行的一种氧化处理,使其表面生成一层极薄的氧化铁氧化膜。
发蓝后呈蓝黑色和深黑色,可提高零件的耐蚀性、润滑性,可改善外观。
* 钢铁磷化:是钢铁零部件在磷化液中处理,在表面沉积形成一层不溶于水结晶型磷酸盐膜。
* 磷化后呈灰色或灰黑色,其耐蚀性比发蓝好,但外观不如发蓝。
磷化主要用于钢铁制件(如枪炮)耐蚀防护和喷漆前处理,以增加漆膜与钢铁工件的附着力及防护性。
09 铝阳极氧化与着色处理
特点:* 阳极氧化是将铝或铝合金制件浸于酸性电解液中,在外电流作用下作为阳极,在制件表面形成与基体牢固结合的防腐蚀氧化膜。
* 阳极氧化前要经过抛光、除油、清洗等预处理,其后要进行冲洗、着色和封闭等处理。
* 阳极氧化的氧化膜可染成黑色、红色、蓝色、绿色、金黄色和茶色等。
* 阳极氧化和着色处理常用于汽车、飞机的某些装饰性零部件及工艺品和日用五金制品作装饰性处理。
10 高压无气喷涂
特点:* 利用低压(0.4-0.6MPa)压缩空气带动高压泵,将涂料加压到10-20MPa的压力,经高压喷枪的特殊喷嘴喷出形成涂层。
* 高压无气喷涂的特点:没有一般压缩空气喷涂时的涂料微粒回溅及漆雾飞扬现象;生产率高,比压缩空气喷涂提高几倍至几十倍。
* 适宜喷涂高粘度涂料,一次可获100-300mm厚度涂层。
11 静电喷涂
特点:* 用静电喷枪使油漆雾化并带上正电荷,与接地的工件间形成高压静电场,静电引力使漆膜沉积在工件表面形成均匀漆膜。
* 静电喷涂比普通喷涂生产率高,成膜质量好。
* 静电喷涂常用于大批量生产中的汽车、自行车、家用机电设备零部件的自动化生产线中。
表面处理工艺各色其式,因应生产线原来的设备、操作员的技术、工件类型和大小,以及生产成本和时间等等,企业管理在多方的考虑因素作出不同选择。
然而,科技日新月异,作为表面处理从业者却不能固步自封,应了解其他方面发展中的技术,在未来规划生产线及至新技术需求作好准备。