箱式双转子在线除气装置
铝合金熔体在线除气、精炼设备供货技术要求

铝合金熔体在线除气、精炼设备供货技术要求1、供货名称及数量(前期上4套除气过滤,后期再上2套)铝合金熔体箱式双转子液压倾翻式在线除气设备6台,水平板式过滤设备6台;2、设备用途铝合金熔体铸造前在线净化处理,经吸附精炼后的铝熔体进入过滤装置,陶瓷过滤板对铝熔体进行二次过滤和梳理整流,吸附粘结夹杂物,实现非吸附精炼,以满足各种挤压铝型材产品对熔体质量(氢含量、非金属夹杂物含量)的最终要求。
3、供货范围整体设备设计、制作、安装;保温炉出水口至铸造机进水口段流槽及施工,涉及土建部份由供货方提供相关土建施工图纸,购买方负责土建施工。
供货方同时负责完成后期设备调试、MES系统建造人员配合工作、操作员工培训工作;同时需要与熔炼炉、铸造机设计方沟通出水和铸造盘高度,保证设备达到最佳使用效果;4、除气设备技术要求1)除气效果:针对1、3、4、5、6、7系铝合金,当除气箱进口铝合金熔体中氢含量≥0.30cm3/100g· Al 时,除气率≥60%;当除气箱进口铝合金熔体中氢含量<0.30cm3/100g·Al时,出口含氢量小于0.12cm3/100g·Al;(上述指标在买方提供99.995%纯氩惰性气源,铝液中Mg ≤1%的条件才可达到);2)除气介质:氩气压力:5-16bar设计流量:200L/min操作流量:120L/min3)在线除气箱要求:3.1、保证惰性气体扩散表面积在铝液中达最大,弥散性最均匀,气泡最小。
3.2、惰性气体在铝液中保持时间最长。
3.3、惰性气体与杂质保持充分接触。
3.4、保证惰性气体产生的涡流最小,铝液表面浮动最小。
3.5、保证铝液形成稳定的潜流,进出口温降最小。
3.6、熔体处理量:≤30T/h ;3.7、保温性能好,箱体外壁允许温升不超过30℃(即外壁温度≤室温+30℃);3.8、足够的升温能力,在工作态时的出口温度比进口温度温升≥2℃;3.9、良好的密闭性,箱体内金属液面上方应维持惰性气氛,以保护转子和金属液尽量少氧化;3.10、足够的容量,以保证充分脱气;3.11、箱体内衬寿命:≥24个月;转子寿命:≥150工作时3.12、有工艺参数显示及智能控制和故障报警,温控精度±3℃;3.13、运行噪音≤60dB;3.14、操作、清理方便,维护简便;3.15、处理结束时,箱体内不滞留或少滞留熔体;3.16、应考虑环保和车间卫生的要求。
几种典型铝合金除气机转子浅析
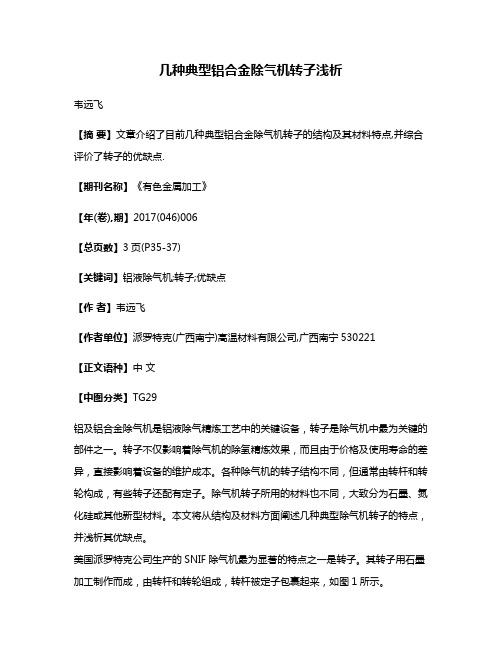
几种典型铝合金除气机转子浅析韦远飞【摘要】文章介绍了目前几种典型铝合金除气机转子的结构及其材料特点,并综合评价了转子的优缺点.【期刊名称】《有色金属加工》【年(卷),期】2017(046)006【总页数】3页(P35-37)【关键词】铝液除气机;转子;优缺点【作者】韦远飞【作者单位】派罗特克(广西南宁)高温材料有限公司,广西南宁530221【正文语种】中文【中图分类】TG29铝及铝合金除气机是铝液除气精炼工艺中的关键设备,转子是除气机中最为关键的部件之一。
转子不仅影响着除气机的除氢精炼效果,而且由于价格及使用寿命的差异,直接影响着设备的维护成本。
各种除气机的转子结构不同,但通常由转杆和转轮构成,有些转子还配有定子。
除气机转子所用的材料也不同,大致分为石墨、氮化硅或其他新型材料。
本文将从结构及材料方面阐述几种典型除气机转子的特点,并浅析其优缺点。
美国派罗特克公司生产的SNIF除气机最为显著的特点之一是转子。
其转子用石墨加工制作而成,由转杆和转轮组成,转杆被定子包裹起来,如图1所示。
除气机旋转除气时,石墨定子在铝液中不转动,对转杆和转轮起保护作用。
转轮通过螺纹安装在转杆底部。
搅拌铝水时,惰性气体通过定子和转杆之间的间隙,从定子底部边缘和转轮顶部边缘凹槽外喷射到铝液中。
通过转轮的剪切力,导致铝液向下循环,从而抵消了自然浮力的影响,使得从转子和定子喷射出来的气泡径向喷射且均匀的分散在铝液中,从而到达最佳的除气精炼效果。
由于定子的保护作用,避免了转杆高速旋转时在与铝液面接触处被铝液冲刷磨损而折断。
美国派罗特克公司的另一系列ILDU除气机转子的材质为新型BTS,如图2所示。
目前大部分除气机转子的材质一般都是石墨、碳化硅或氮化硅。
石墨转子在温度大于700℃时,容易烧损氧化,造成断裂或剥落,从而污染铝液;碳化硅浇铸转子不耐热冲击,在急冷急热冲击下易断裂;氮化硅转子成本太高。
BST转子内部为石墨材料,外部为耐火材料烧结而成,恰好克服了上述三种材料的缺点。
A356铝合金显微组织及断口分析
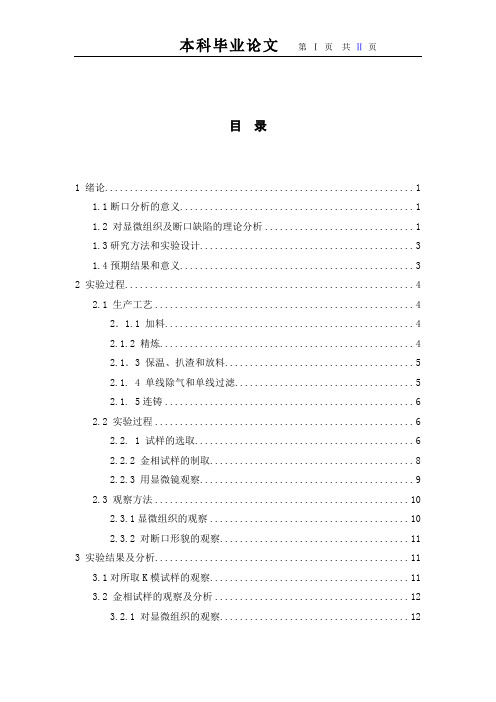
目录1 绪论 (1)1.1断口分析的意义 (1)1.2 对显微组织及断口缺陷的理论分析 (1)1.3研究方法和实验设计 (3)1.4预期结果和意义 (3)2 实验过程 (4)2.1 生产工艺 (4)2.1.1 加料 (4)2.1.2 精炼 (4)2.1.3 保温、扒渣和放料 (5)2.1. 4 单线除气和单线过滤 (5)2.1. 5连铸 (6)2.2 实验过程 (6)2.2. 1 试样的选取 (6)2.2.2 金相试样的制取 (8)2.2.3 用显微镜观察 (9)2.3 观察方法 (10)2.3.1显微组织的观察 (10)2.3.2 对断口形貌的观察 (11)3 实验结果及分析 (11)3.1对所取K模试样的观察 (11)3.2 金相试样的观察及分析 (12)3.2.1 对显微组织的观察 (12)3.2.2 断口缺陷 (15)结论 (23)致谢 (24)参考文献 (25)附录 (27)1 绪论1.1断口分析的意义随着现代科技的发展以及现代工业的需求,作为21世纪三大支柱产业的材料科学正朝着高比强度,高强高韧等综合性能等方向发展。
长久以来,铸造铝合金以其价廉、质轻、性能可靠等因素在工业应用中获得了较大的发展。
尤其随着近年来对轨道交通材料轻量化的要求日益迫切[1],作为铸造铝合金中应用最广的A356铝合金具有铸造流动性好、气密性好、收缩率小和热裂倾向小,经过变质和热处理后,具有良好的力学性能、物理性能、耐腐蚀性能和较好的机械加工性能[2-3],与钢轮毂相比,铝合金轮毂具有质量轻、安全、舒适、节能等,在汽车和航空工业上得到了日益广泛的应用[4]。
然而,由于其凝固收缩,同时在熔融状态下很容易溶入氢,因此铸造铝合金不可避免地包含一定数量的缺陷,比如空隙、氧化物、孔洞和非金属夹杂物等[5-7]。
这些缺陷对构件的力学性能影响较大,如含1%体积分数的空隙将导致其疲劳50%,疲劳极限降20%[8-9]。
所以研究构件中缺陷的性质、数量、尺寸和分布位置对力学性能的影响具有重要意义[10]。
铝DC铸造培训资料

Ni ≤0.002
Cu ≤0.02
Al ≤0.05
Mn ≤0.05
其他单个杂质 ≤0.05
1 样/批
2
表面质量
目视
表面应平整清洁,不允许有残留熔剂、夹渣、冷隔、飞边、氧化燃烧产物及其他 影响使用 的缺陷,但允许有修理痕迹。 单块重量7.5±0.5kg 每年做一次第三方检测 GB/T 3499-2011
ABM氮化硼涂料
耐火泥
应用:耐火泥是用于耐火材料堆砌和修补的材料,广泛用于铝熔铸的
模盘、流道、箱体、水口等部位的维护与修复 优点:1、减少熔融金属温降;2、不沾湿熔融铝,无化学反应,减少 金属粘着的可能性;3、易于操作,可用手或铲子涂抹,易于清除;有 良好的绝热性能,收缩率小,表面强度高;5、避免夹杂,提高铝液质 量。 主要参数
有抗氧化涂层的保护,产品使用时耐高温,耐腐蚀,不熔化,不燃烧, 不产烟气,并能保持自身的完整性。 适用于流槽口、浇包前对金属的过滤。可有效去除铝熔液中的气泡、 夹灰氧化物,以及各种夹杂物等有害杂质,不影响铝合金成份组成,以 保证铝铸件的品质。
陶瓷过滤板
含有适量多的难熔元素;化学成分均匀;气体、非金属夹杂物含量尽 可能低;易于破碎,便于配料。 铝硅为5kg块状,其他均为华夫锭,铝钛硼为卷材 铝铜无色标、铝钛为红色、铝锆为黑色、铝钒为蓝色
NO. 检验项目 检验方法
牌号 Si Fe Cu ≤0.10 Mn
检验标准
Cr Ni Ti ≤0.10 ≤0.10 B V Zr Sn Al 余量
2样/批 全检
添加剂
合金元素含量高,减少了添加剂的使用数量,从而使运输、储存、保
管费用降低; 由于合金组元以粉末形式引入,比表面积大,加之使用数量少,因而, 熔化块,温降小,省时节能; 密度大,在铝液中自沉,有熔剂保护,加之快速溶解,因此,合金元 素的实收率较高,一般均大于95%; 每块添加剂重量恒定,成分含量准确,配料时无需称量、破碎,备料 方便,控制准确。
7075大规格圆铸锭熔铸工艺研究及裂纹解决

7075大规格圆铸锭熔铸工艺研究及裂纹解决张金平;苏银忠【期刊名称】《世界有色金属》【年(卷),期】2014(000)002【总页数】3页(P30-32)【作者】张金平;苏银忠【作者单位】中国铝业股份有限公司连城分公司;中国铝业股份有限公司连城分公司【正文语种】中文通过在圆铸锭进口生产线试制7075硬质合金,成功研制出Φ460、Φ605大规格7075硬质合金圆铸锭,掌握了7075合金的熔铸生产工艺。
本文着重阐述了各工艺参数的确定依据,对铸造裂纹缺陷进行了分析并提出相应的预防措施。
7075属于Al-Zn-Mg-Cu系超硬铝合金,强度高,远胜于任何软钢,属高强度可热处理合金,具有良好的机械性能、耐磨性能、抗腐蚀性能,同时具备可实用性好、抗氧化性好等特点。
广泛应用于航天航空工业、超声波塑焊模具、高尔夫球头、攀岩设备、夹具、模具加工、高端铝合金自行车车架等领域。
7075合金(化学成分表见表1)中Mg含量与Zn含量的和在8.10%~8.70%之间,而Zn含量在5.60%~5.90%之间,成型较困难,且具有较大的裂纹倾向性,笔者针对其生产工艺探讨。
成分控制及熔炼工艺1 成分控制7075合金中Mg、Zn均为主要的合金元素,为增加合金的塑性,降低合金的裂纹倾向性,将Mg含量按中偏上限控制,Zn含量按中偏下限控制,尽可能提高Mg/Zn比。
该合金对热裂纹较为敏感的区域位于热脆性曲线的上升部分,Fe、Si 含量改变时,合金在铸造时产生的共晶量变化由此产生的具有最大热脆性的成分发生转移,为了改善合金抵抗热裂纹的能力,应尽可能降低Si的含量,并使Fe含量大于Si,要求Fe>Si0.15%,这样既可以达到改善合金铸造工艺性能,又不会显著改变它的最终性能。
2 熔炼工艺7075合金中含有Cu、Mg、Zn、Cr、Fe等主要元素,Cu、Mg以纯金属形式加入,Zn以中间合金的形式加入,Cr、Fe以熔剂形式加入。
经实践证明,按照溶解速度快慢和烧损的易难情况加入熔炼炉,比较难溶的合金先加,较易溶解的后加;不易烧损的先加,较易烧损的后加;稳定的先加,不稳定的后加。
三井金属除气设备介绍
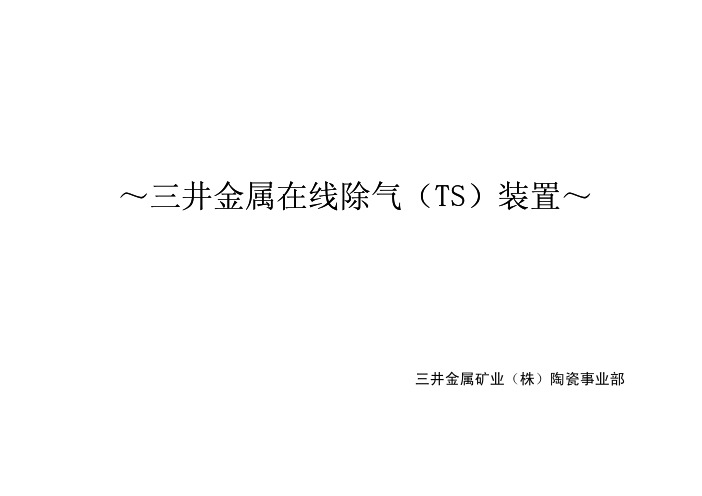
3)在工业炉上的应用
升液管
TB液面探测
热电偶保护套 給湯口
加热器保护套
<红颜色的部位
>
3、浸入式的直接加热方式 直接加热的3个优点
加热效率高 减少铝液表面的氧化 对铝水没有污染
非常感谢!
素材 (用途:除气、过滤设备)
・拉法、联矿生产 (用途:溶解炉、保持炉、除气、 过滤装置)
・高純度アルミ炉内張り材 (用途:溶解炉、保持炉、除气、 过滤装置) ・高純度用としてSi汚染低減 を目的とした素材
采用氮化硅碳化硅或浇注料烧结成预制砖
1-4 除气室内腔阻流板设计
确保铝溶体表面的稳定,可以防止空气及铝溶体表面的氧化物被卷到铝溶体当中。
内腔尺寸 (mm)
685×685 850×850 650×650 750×750 850×850 650×650 750×750 850×850
溶体保持量 (㎏)
700 1000 1300 1700 2100 2000 2650 3100
溶体流速 (㎏/分)
150 200 250 350 450 360 500 750
气泡细微 气孔容易堵塞
SNIF
气泡细微、铝溶 体表面波动小。 昂贵,易损
氮化硅转子的特点
使用超长使用寿命 转子的头部杆部均采用氮化硅材料,真正做到
的陶瓷材料
永不磨损。
转子头部直径200mm、杆部60mm,能够最大
确保铝溶体液面的 限度的减少对溶体的搅拌力。
稳定
转子的同心度控制在1.5mm以内,确保高转速情
10
15
20
Day
氮C化a硅rb转on子 ハイセラ
強度
優
1)氮化硅材料SN的组织构造
5083铝合金大规格扁锭铸造热裂纹缺陷的研究
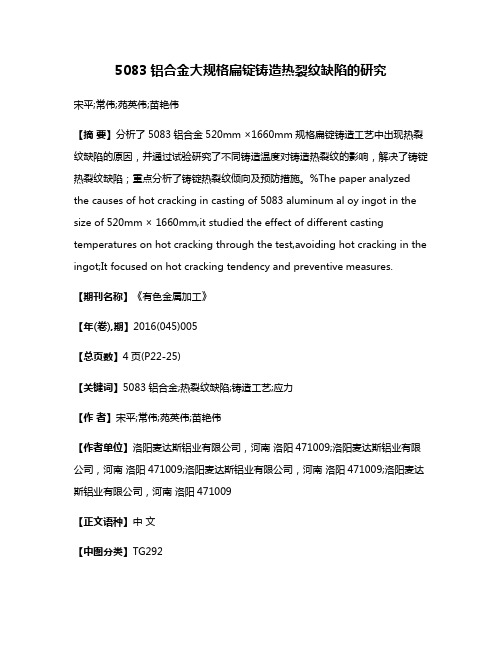
5083铝合金大规格扁锭铸造热裂纹缺陷的研究宋平;常伟;苑英伟;苗艳伟【摘要】分析了5083铝合金520mm ×1660mm规格扁锭铸造工艺中出现热裂纹缺陷的原因,并通过试验研究了不同铸造温度对铸造热裂纹的影响,解决了铸锭热裂纹缺陷;重点分析了铸锭热裂纹倾向及预防措施。
%The paper analyzed the causes of hot cracking in casting of 5083 aluminum al oy ingot in the size of 520mm × 1660mm,it studied the effect of different casting temperatures on hot cracking through the test,avoiding hot cracking in the ingot;It focused on hot cracking tendency and preventive measures.【期刊名称】《有色金属加工》【年(卷),期】2016(045)005【总页数】4页(P22-25)【关键词】5083铝合金;热裂纹缺陷;铸造工艺;应力【作者】宋平;常伟;苑英伟;苗艳伟【作者单位】洛阳麦达斯铝业有限公司,河南洛阳471009;洛阳麦达斯铝业有限公司,河南洛阳471009;洛阳麦达斯铝业有限公司,河南洛阳471009;洛阳麦达斯铝业有限公司,河南洛阳471009【正文语种】中文【中图分类】TG2925083合金属于Al-Mg系合金,具有强度高、耐腐蚀、塑性好、易切削等特点,被广泛应用于高速列车、地铁轻轨、汽车、航空航天、压力容器等领域,是重要的结构材料。
但是由于该合金的合金化程度高,结晶温度范围宽,在半连续铸造结晶过程中具有较大的热裂纹倾向,导致成品率低。
而520mm×1660mm规格的扁锭因整体应力较大,在铸造过程中的裂纹倾向尤其大,虽然我公司在设备厂家调试过程中连续生产了5次,但均未有效地解决热裂纹缺陷的质量难题。
ZYQ-812说明书
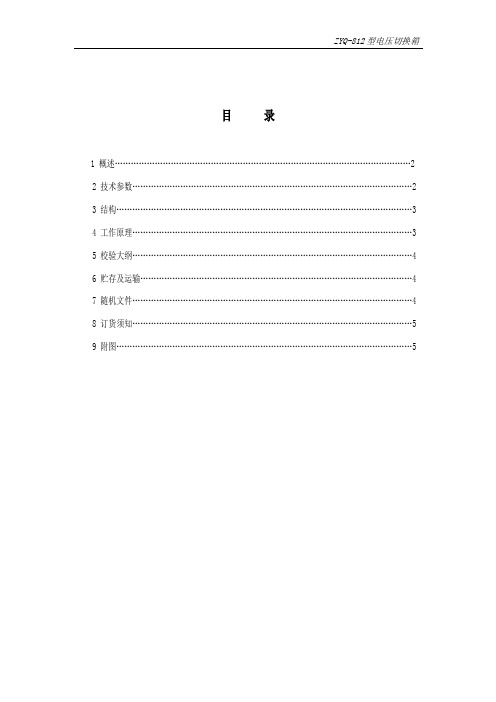
目录1 概述 (2)2 技术参数 (2)3 结构 (3)4 工作原理 (3)5 校验大纲 (4)6 贮存及运输 (4)7 随机文件 (4)8 订货须知 (5)9 附图 (5)1 概述1.1 装置用途该装置适用于双母线接线系统,为保证双母线接线系统上所连接的电气元件在运行时,其一次系统和二次电压系统相对应,以免保护及自动装置发生误动或拒动。
1.2 装置综述装置共一层箱,由两个插件组成,包括两个电压切换插件,均采用插拔式,保证了配置的灵活方便,。
装置可实现电压的自动切换。
2 技术参数2.1 基本数据2.1.1 额定数据额定直流电压:220V或110V;2.1.2 功率消耗在额定直流电压下,直流电压回路功率消耗正常情况下不大于40W。
2.1.3 触点性能在电压不大于250V,电流不大于0.5A,时间常数为5ms±0.75ms的直流有感负荷电路中,断开容量为50W,长期允许通过电流为5A。
2.1.4 装置约重2kg。
2.2 绝缘性能2.2.1 绝缘电阻所有回路对外壳及电气上无联系的各电路之间的绝缘电阻在正常检验的标准大气条件下,不小于100MΩ。
2.2.2 介质强度所有电路对外壳的介质强度应能承受50Hz,2000V,1min试验而无绝缘击穿或闪络现象。
2.3 工作环境条件2.3.1 环境条件-25℃~+40℃,24h内平均温度不超过35℃。
2.3.2 相对湿度最湿月的月平均最大湿度为90%,同时该月的月平均温度为25℃,最高温度为40℃,平均最大相对湿度不超过50%。
2.3.3 大气压力80kPa~110kPa。
2.3.4 安装方式安装位置偏离其它垂直基准面的任一方向不大于5 。
2.3.5 使用地点出现交越频率以下的位移峰值不超过0.035mm,交越频率以上的加速度峰值不超过0.5gh的机械振动,以及加速度不超过5gh的机械冲击。
2.3.6 使用地点不得有爆炸危险的介质,周围介质不含有腐蚀金属和绝缘的气体以及导电介质,不允许充满水蒸气及有较严重的霉菌存在。
铝加工产品熔铸工序节能降耗的方案与措施

铝加工产品熔铸工序节能降耗的方案与措施王国军【摘要】本文介绍了世界社会经济发展对节能降耗的迫切要求和《中国制造2025》国家战略有关对新材料产业绿色和创新的内容,剖析了国内外铝合金压力加工产品铝合金熔铸工序的特点与能源消耗现状,从装备保证条件、工艺技术优化两条主线讲解了铝合金熔铸工序节能降耗的方案和措施,指出了实现铝合金熔铸工序节能降耗的途径和下一步努力的方向.【期刊名称】《世界有色金属》【年(卷),期】2015(000)012【总页数】4页(P41-44)【关键词】铝合金熔铸;节能降耗;装备升级;工艺改进【作者】王国军【作者单位】中铝东北轻合金有限责任公司,黑龙江哈尔滨150060【正文语种】中文【中图分类】TG292《中国制造2025》新材料技术路线图指明了铝合金产业目标:重点突破低能耗短流程、高效高精度加工新技术、新工艺及装备。
高性能大规格材料制备及精密成形工艺与控制、服役性能评价技术。
先进铝合金材料年产销量要达到100万吨。
产业规模要达到500亿。
可见低能耗短流程等节能减排也是我国材料产业的发展方向。
我国的铝加工业发展十分迅速,据《中国有色金属工业发展研究报告》数据显示:1980年的加工材产量不到30万吨,2010年我国铝材一年产量为2026万吨,2014年生产铝材为4845万吨,5年翻了一番多,我国已成为铝加工材名副其实的生产大国,其中山东、河南、广东三省名列三甲;山东一省就有1000万吨以上的产量,发展速度惊人。
铝加工产业能源消耗巨大,而熔铸工序作为铝加工最大的能源消耗工序,是国家实施节能减排的重点领域,逐步淘汰污染严重、能耗超标、陈旧落后的设备,发展合理工业布局,提高设备性能及配置,提升工艺技术水平成为铝合金工业节能环保发展的主流趋势,也是业界研究和关注的焦点。
笔者在铝加工特大型企业工作多年,一直从事工艺创新、科研和新产品开发工作。
为更好地落实国家战略,现综合对国内外铝合金熔铸技术发展现状的了解,从装备升级和工艺改创新进两个主要方面深入分析一下铝合金压力加工产品熔铸工序节能降耗的有效途径。
Hazelett节能工艺探讨

Hazelett节能工艺探讨赵海东【摘要】Hazelett工艺是我国近年引进的铝板带连铸连轧新工艺,具有节能、降耗和低生产成本特点.结合国内首条已投产Hazelett生产线的节能功效,并和传统半连续大扁锭生产法、铸轧法生产铝板带能耗方面进行比较,得出Hazelett工艺是目前最节能的铝板带生产工艺.在当前铝板带市场和经济环境下,最适宜在电解铝厂旁建设投资少、见效快和具有市场竞争力的铝板带生产线.【期刊名称】《有色金属设计》【年(卷),期】2016(043)001【总页数】3页(P14-16)【关键词】Hazelett工艺;铝板带生产线;大扁锭法;铸轧法;节能降耗【作者】赵海东【作者单位】中冶东方工程技术有限公司,山东青岛266555【正文语种】中文【中图分类】TG335.13河南某铝加工企业2008年签订国内首条Hazelett铝板带连铸连轧生产线,自投产以来节能功效突出。
下面综合论述整条生产线工艺节能方面的优势和设计之初采用的节能措施,并通过不同铝板带生产工艺节能方面比较,突出在当前市场和经济环境下,Hazelett铝板带连铸连轧生产线,节能明显[1],是具有发展前景的铝板带生产工艺。
望能够借鉴并大力推广。
Hazelett生产线是一条连续铸造、连续热轧的紧凑式生产线。
生产线以Hazelett双钢带铸造机为核心,将熔炼工艺和热轧工艺串联在一条连续生产线上,改变了传统半连续铝板带生产工艺,类似于钢铁行业ASP或ESP或CSP生产线。
国内尚属首次采用Hazelett连铸连轧生产铝板带工艺,同时也填补了我国铝板带生产的一项空白。
具体工艺流程见图1。
河南Hazelett连铸连轧生产线主要工艺设备配置为:4台120 t铝液混合炉→三转子在线除气→双陶瓷泡沫过滤→1台Hazelett双钢带铸造机→3机架热连轧机→双卷取机。
其中4台120 t铝液混合炉以59 t/h的速度连续给Hazelett铸造机供铝,4台混合炉配置了底置式ABB电磁搅拌器和炉内单转子HD-2 000精炼装置,并采用液压倾动真空罐向炉内兑高温电解铝液。
5系铝合金260mm×1500mm规格直边铸锭熔铸工艺研究

5系铝合金260mm×1500mm规格直边铸锭熔铸工艺研究侯显智;赵涛;滕志贵;王晓峰【期刊名称】《金属世界》【年(卷),期】2013(000)002【总页数】7页(P54-59,73)【作者】侯显智;赵涛;滕志贵;王晓峰【作者单位】东北轻合金有限责任公司,黑龙江哈尔滨150060【正文语种】中文内容导读5系铝合金采用传统的铸造方式生产的铸锭表面偏析瘤较大,在机械加工时必须进行小面刨边和大面铣面,而且铣面较大,不仅影响成品率而且增加生产成本.因此我分厂自主设计、制定了260mmX1500mm规格直边铸锭生产工艺.对5083牌号铝合金进行化学成分的控制,铸造工艺及均匀化退火工艺的改进,铸造成型工具的研发等一系列工艺参数摸索.对最终产品的化学成分,铸锭表面质量,低倍组织,力学性能等各项指标检测.检测结果表明,采用新工艺参数生产的铸锭,铸锭的化学成分,铸锭表面及内部质量,力学性能均良好.保证了成品率,缓解刨边工序的生产窄口问题.5 系铝合金大方铸锭常规的规格为 255 mmX1500 mm,该规格铸锭小面为圆弧型,不仅有利于铸造成型也有利于轧制时顺利咬入,但是传统的铸造方式生产的铸锭表面偏析瘤较大,这样在机加时必须进行小面刨边和大面铣面且铣面较大,不仅影响成品率而且增加生产成本.随着 5 系铝合金 255 mmX1500 mm 规格生产任务的加大,刨边工序已成为了生产的窄口.鉴于这种情况,我分厂自主设计、制作 260 mmX1500 mm规格直边铸锭铸造成型工具,采用低液位铸造方式生产,低液位铸造方式生产的铸锭表面质量好,且该规格铸锭小面为直边,无需进行刨边,但小面为直边的铸锭铸造成型相对难度增加.生产260 mmX1500 mm 规格的 5 系铝合金,90% 以上的产量均为5083 铝合金,为了缓解刨边工序的生产窄口问题,提高成品率,我们展开了对 260 mmX1500 mm 规格的5083 合金直边铸锭熔铸工艺研究.5083 铝合金具有中等强度、良好的耐蚀性、焊接性及易于加工成形等特点,是 Al-Mg 系合金中的典型合金.不同热处理状态的 5083 铝合金板材是压力容器、装甲车辆、船舶、汽车制造业所用的主要材料.本试验主要从铸锭化学成分、铸锭外观质量、显微组织及力学性能等方面对 260 mmX1500 mm 规格的 5083 铝合金进行质量全分析.试验过程合金成分 (见表 1)表 1 5083 合金成分合金成分,质量百分比/%SiFeCu Mn Mg CrNiZnTi Be 杂质 Al 单个合计国家标准 0.40 0.40 0.10 0.40~1.0 4.0~4.9 0.05~0.25 - 0.25 0.150.0004~0.0008 0.05 0.15 余量厂内标准 0.25 0.30 0.10 0.60~0.90 4.4~4.80.05~0.10 - 0.20 0.10 0.05 0.15 余量工艺流程配料→熔炼与净化→铸造→均匀化退火→机加→铸锭试片试验项目检测.◆ 配料完全采用固体料投料,炉料由 40%~45% 的新铝锭 (除调整化学成分的金属外,为 5 系铝合金二、三级废料)、Mg、Mn、Cr、Be 等组成.Mg 以纯金属形式加入,Mn、Cr 以添加剂的形式加入,Be 以中间合金的形式加入.◆ 熔炼与净化工艺熔炼温度700~750℃.720℃以上加 Mn 剂、Cr 剂、Mg 锭,保证铁含量大于硅含量 0.1% ,保温炉补 0.01% 的 Ti,并在熔炼温度范围内导入保温炉、取样、调整化学成分、精炼.铸造前采用氩气体精炼 20 min,静置 20 min,铸造时采用 Alpur (双转子气体精炼装置) 进行在线除气,采用40PPI (PPI 为每英寸上的孔隙数) 陶瓷片过滤器进行净化处理.◆ 铸造工艺铸造在线播种 Al-Ti-0.2B 丝进行晶粒细化,其速度为 440 mm/min.主要的铸造工艺参数见表 2.表 2 5083 铝合金 260mmX1500mm 规格主要铸造参数铸造温度/℃ 填充时间/s 铸造速度/(mm. min-1)金属液位/mm冷却水流量(/m3. h-1) 脉冲水710~730 5060 70 90 开头使用◆ 均匀化退火制度5083 铝合金 260 mmX1500 mm规格均匀化退火制度参见表 3.表 3 5083 铝合金 260mmX1500mm 规格均匀化退火制度合金规格/mm2 制品各区定/℃ 金属温/℃ 保温时间/h 5083铝金 260X1500 板 465 460~470 29检测项目将5083 铝合金 260 mmX 1500 mm 铸锭锯切头尾后选择一端切取一片厚20~30 mm 的试片,沿厚度方向将试片打断,取一半进行各项试验检测[1].铸锭各项检测用试样的位置见图 1.图 1 5083 试片取样位置图铸锭质量分析化学成分按照图 1 所示,由中心向边部 (1-1→1-7) 取样,分析 5083 中化学成分偏析程度,其主要合金元素 Mg、Mn、Cr 化学成分变化趋势如图 2、图 3 和图 4 所示 (注:图中横坐标 1~7 代表铸锭化学成分取样位置),其余杂质元素均符合 5083 铝合金标准化学成分要求,由于控制含量低,基本不会产生偏析,也不会对合金组织与性能产生明显影响[1].从图 2 可以看出,铸锭 Mg元素平均值为 4.49%,最大差值为 0.36%.符合 5083 铝合金化学成分要求.铸锭 Mg 元素含量最大差值较小,说明铸锭 Mg 元素偏析程度较小,这种现象可能由于铸锭较薄,冷却速度较快的缘故.图 2 5083 铝合金 Mg 偏析情况从图 3 可以看出,铸锭 Mn元素平均值为 0.69%,最大差值为 0.02%,符合 5083 铝合金化学成分要求.5083 铝合金化学成分中 Mn 元素含量不是主要元素,含量相对较低,基本上没有产生成分偏析.图 3 5083 铝合金 Mn 偏析情况从图 4 可以看出,铸锭 Cr 元素平均值为 0.083%,最大差值为 0.006%.由于 Cr 元素含量较低,控制相对容易,未见明显成分偏析.图 4 5083 铝合金 Cr 偏析情况综合图 2、图 3、图 4 可以看出,整个铸锭截面上的各主要合金元素偏析程度较低,并且符合 5083 铝合金标准化学成分要求,有利于铸锭力学性能.铸锭表面质量铸锭表面偏析层较薄,无金属瘤、无拉裂、冷隔等表面缺陷.图 5 5083 铝合金不同位置的显微组织低倍组织铸锭低倍组织上无气孔、白斑等缺陷.显微组织从图 5 高倍组织照片可以看出,铸锭从边部到中心 (2-5→2-4→2-3→2-2→2-1,2-7→2-6→2-1) 枝晶网络厚,但枝晶间距逐渐变小较均匀,晶粒从小到大,基本上符合铝合金熔炼过程中的结晶规律[1].从图 5 偏光组织照片可以看出,铸锭从边部到中心 (2-5→2-4→2-3→2-2→2-1,2-7→2-6→2-1) 晶粒大小趋势与高倍组织相似,对比晶粒等级照片可以看出为 1~2 级晶粒组织,与低倍组织检查结果相符.力学性能按照图 1 所示,沿试片中心至边部取样,检测铸锭力学性能,结果如图 6、图 7 和图 8 所示 (图中横坐标1→12 表示3-1→3-12).从图 6 可以看出,铸锭平均值为 265.6 MPa、最大差值为31 MPa.图 6 5083 铝合金抗拉强度检测结果从图 7 可以看出,铸锭平均值为 149.3 MPa、最大差值为 16 MPa.图 7 5083 铝合金屈服强度检测结果从图 8 可以看出,铸锭平均值为 12.2%、最大差值为 8.64%.图 8 5083 铝合金伸长率检测结果试验结果讨论杂质 Fe 和 Si 的控制Fe 与 Mn 形成难熔金属间化合物[2],又脆又硬,会破坏铝基体组织的均匀性,降低合金的耐蚀性,使铸锭轧制时容易开裂,故一般控制 Fe<0.4%.Si 的副作用比 Fe 的更大.Si 与Mg形成 Mg2Si 相,由于 Mg 量过剩时,降低了 Mg2Si 在基体中的溶解度,故不但强化作用不大,而且降低合金的塑性.只有当 Si 接近 0.1%,且 Fe 含量足够大时,上述副作用才能减小.所以要确保 Fe 含量大于 Si 含量,使合金组织中宁可形成极少量不规则的 Al12Fe3Si 相,也要避免形成Mg2Si 相.[3]加 Be对熔体进行保护5083 铝合金 Mg 含量较高,氧化性大,在熔体表面易生成不致密的、疏松多孔的氧化膜,氧化反应向熔体深度处进行,氧化后的熔体铸造的铸锭表面发黑、疏松增加、容易产生夹渣,氧化夹渣易引起应力集中而导致铸锭产生裂纹.因此利用元素 Be 原子半径小、氧化时发热量大和 VBeO/VBe>1 等特点,在 5083 铝合金熔体中加入适量的 Be 保护熔体,阻止氧化.用 A1-Ti-0.2B 丝在线细化晶粒当铸锭中晶粒粗大时,结晶末期存在于晶界和枝晶界上的低熔点金属相粗大,而且分布不均匀,所以塑性低,抵抗拉应力的能力降低,裂纹倾向增加;当晶粒和枝晶细小时,分布在晶界和枝晶界上的低熔点金属相分布均匀,塑性提高,抵抗变形能力增强,裂纹倾向减小.因此,在线播种 Al-Ti-0.2 B 丝细化晶粒.但在 5083 合金中 B>2X10-6 时,熔体中 TiB2 质点容易聚集,在铸锭表面形成竖道皱褶缺陷,会成为裂纹源.因此应控制 B<2X10-6在线播种 Al-Ti-0.2B 进行细化晶粒[3].结束语5083 铝合金260 mmX1500 mm规格的熔铸工艺为:熔炼温度700~750℃,720℃ 以上加 Mn 剂、Cr 剂、Mg 锭,保证铁含量大于硅含量 0.1%,保温炉补 0.01% 的Ti.铸造前采用氩气体精炼 20 min,静置 20 min,铸造时采用 Alpur 进行在线除气,采用 40 PPI 陶瓷片过滤器进行净化处理.铸造在线点 Al-Ti-0.2B 丝440 mm/min,铸造温度控制在710~730℃,填充时间为50 s,铸造速度为 60 mm/min,金属液位高度为 70 mm,冷却水流量为 90 m3/h.采用该熔铸工艺生产的铸锭能够满足后续加工的化学成分、显微组织、和力学性能的要求:1) 在化学成分中,各合金元素偏析较小;2) 在显微组织中,锭晶粒尺寸较为均匀;3) 铸锭综合力学性能较好.参考文献[1] 郑力, 赵涛, 张浩然, 等. 复合材料芯材用新型Al-Mn合金的研制. 金属世界, 2011,(5): 61-62[2] 肖亚庆, 谢水生, 刘静安, 等. 铝加工技术实用手册. 北京: 冶金工业出版社, 2005[3] 郝志刚, 黄晶, 时羽, 等. 5083铝合金大规格扁锭熔铸工艺研究. 轻合金加工技术,2006, (7): 17。
- 1、下载文档前请自行甄别文档内容的完整性,平台不提供额外的编辑、内容补充、找答案等附加服务。
- 2、"仅部分预览"的文档,不可在线预览部分如存在完整性等问题,可反馈申请退款(可完整预览的文档不适用该条件!)。
- 3、如文档侵犯您的权益,请联系客服反馈,我们会尽快为您处理(人工客服工作时间:9:00-18:30)。
箱式双转子在线除气装置MLDU-II(15型)
箱式双转子在线除气装置
●装置由除气箱体、上盖及转子机构、加热系
统、提升机构和控制系统组成。
设备特点Advantages And Benefits
●除气效率高:采用了紧凑式的炉体设计,在
除气箱中使用旋转喷头除气,在箱内形成对
流,使小气泡在铝液中可以得到充分的扩散。
增大了气泡和铝液的接触面;同时采用了密
封式设计,杜绝了外界空气的进入而造成二
次污染,提高了设备的除气效率。
●控制精确:采用了工作站除气的方法,在工
作间隙铝液可以通过电加热维持温度,加热
系统采用浸入式加热装置,加热效率高,采
用硅碳棒加热元件,可控硅控温,控温精度
高,使用方便。
●操作方便:采用一键式切换,设计简单易用,减少了系统的复杂程度,减低设备维护成本,同时在
设备设计上考虑了用户对铸造质量的不同要求,精炼气体流量和转子转速均可调。
●维护保养方便:便于设备维护和转子更换的方便性,旋转喷头部分和加热器部分均可以单独提升,
上盖可以提升并水平旋转,最大限度地方便保养维护的操作。
●操作安全:设备带有连锁机构,避免由于误操作造成伤害。
主要性能参数Technical Specifications
●加热器功率:40KW
●加热方式:浸入式加热。
●温控方式:智能仪表自动控制
●箱体外壁平均温度:≤65℃
●箱体内铝液温度:700-760℃
●保温能力:长时间停机后设计容量的铝液可满足铸造工艺要求。
●炉体内腔容量:<800kg
●旋转喷头转速调节范围:0-350rpm
●金属最大处理量:15t/hr
●静态铝液温度控制精度:≤±2℃。