轴承振动特征分析
电机轴承振动特性试验研究

电机轴承振动特性试验研究摘要:现当今,随着我国经济的快速发展,轴承是电机中重要的支承和旋转元件,直接影响着电机转子系统的旋转性能,进一步影响着电机工作时的稳定性及静音性。
本文首先对电机转子的临界转速进行分析,继而在搭建的电机振动测试系统上开展了轴承振动特性试验研究。
结果表明:当电机在小于临界转速的工况下运行时,电机轴承的振动频率以转频为主;随着电机转速的升高,轴承3个方向的振动加速度有效值均增加,且对x向振动影响最大,z向振动影响最小;电机启动过程中对轴承振动产生明显影响,为避免电机产生过大的振动,应尽量减小达到工作转速所需的时间;电机轴承游隙组变化对振动也会产生一定影响,为了减小电机的振动,非传动端端轴承宜采用CN游隙组;电机轴承采用尼龙保持架相对于冲压钢保持架更有利于运转稳定性;预紧力对振动的影响只能有限的提高,过大或过小的预紧都不利于轴承的稳定性。
关键词:电机轴承;振动特性;试验引言在电机的运转过程中,主要存在其轴承温度与振动幅度异常等现象,使电机的正常工作和生产系统正常运转产生阻碍。
引起此类负面现象产生的因素颇多,为保证电机在生产中中具备更好的运行能力,需要专业人员依据其对应的故障情况来进行调节和修护,最终保证电机的正常运转。
1电机振动及模态分析原理电机振动按照产生机理主要分为三类:一是电磁振动,由气隙磁场产生的单边磁拉力作用于定子铁芯的径向和切向使定子铁芯产生变形振动。
电磁振动产生的原因有三相电压不平衡、电机定转子偏心、定子绕组断路、转子笼条与端环开焊、转子断条等。
二是机械振动,由转子旋转过程中的机械力周期性地作用在电机本体上产生的振动。
机械振动产生的原因有结构整体刚度不足、转子动平衡不良、轴承及基础安装不当、内部风扇损坏以及联轴器对中精度不足等。
三是机电耦合振动,由电机气隙不匀引起单边电磁拉力,其周期性作用又使气隙不均衡进一步加剧,最终作用到电机引起振动。
机电耦合振动产生的原因有定子内径和转子外径圆度不足、转子安装不良引起的轴向窜动等。
轴承振动特征分析

轴承振动特征分析轴承是机械设备中常用的关键元件之一,其质量和工作状态对设备的性能和寿命有着重要的影响。
轴承振动特征分析是评估轴承工作状态和健康状况的重要手段,可以通过振动信号的分析和处理,获取轴承正常和异常工作状态的特征参数,从而判断轴承是否存在异常故障。
1.轴承振动信号采集与分析:通过安装合适的振动传感器(如加速度计、速度计等)在轴承或设备上采集振动信号,并进行信号分析和处理。
常用的分析方法包括时域分析、频域分析和时频域分析等。
在时域分析中,可以观察到振动信号的波形特征,如振幅和频率的变化;在频域分析中,可以通过傅里叶变换将时域信号转换为频域信号,进而分析信号的频谱特征,如频率和幅值的分布;在时频域分析中,可以结合时域和频域的特点,利用小波分析等方法研究信号的瞬态特性和频率特性。
2.轴承故障诊断与判定:通过对轴承振动信号的分析,可以判断轴承是否存在故障,如内圈和外圈的裂纹、滚道的磨损、滚珠的损坏等。
常见的故障特征参数包括峰值、峰值因子、峭度、波形指标、频谱指标等。
例如,当轴承存在内圈裂纹时,振动信号会出现高频峰值,而当存在滚珠损坏时,振动信号会出现冲击信号等。
通过识别和提取这些故障特征参数,可以进行故障类型的判定和诊断。
3.轴承故障预测与预警:根据轴承振动信号的变化规律,可以对轴承的剩余寿命进行预测和评估,从而提前进行维修和更换。
常见的预测方法包括统计模型、神经网络模型、遗传算法等。
通过对大量实际运行数据的分析和建模,可以建立轴承故障预测模型,根据振动信号的变化趋势和特征参数的变化情况,预测轴承的寿命和故障时间,提前进行维修和预防措施,以降低故障风险和成本损失。
4.轴承振动特征分析的应用与发展:轴承振动特征分析已经广泛应用于各个领域,如机械制造、航空航天、电力、石油化工等,对轴承的安全运行和性能提升起到了重要的作用。
未来,随着传感技术、智能化技术等的发展,轴承振动特征分析将更加精细化和自动化,可以实时监测和分析轴承的振动信号,提前预警故障风险和进行状态评估,从而实现设备的智能化管理。
调心球轴承的振动信号分析与故障诊断方法

调心球轴承的振动信号分析与故障诊断方法调心球轴承是现代工业中常见的一种轴承类型,广泛应用于各种机械设备中。
然而,由于工作环境的复杂性和长期工作的损耗,调心球轴承可能会发生故障,影响设备的正常运行。
因此,开发有效的振动信号分析与故障诊断方法对于提高设备的可靠性和安全性具有重要意义。
调心球轴承的振动信号是一种重要的故障特征,可以用于检测和诊断轴承的运行状态和故障类型。
振动信号分析方法是一种常用的技术,通过分析轴承在振动中产生的频谱特征和时域波形,可以判断轴承是否存在故障。
下面将介绍一些常用的振动信号分析与故障诊断方法。
第一种方法是频谱分析。
频谱分析通过将振动信号转换成频谱图,可以直观地观察到频率成分的分布和能量大小。
常用的频谱分析方法包括傅里叶变换、小波变换和功率谱密度估计等。
通过分析频谱图的特征,可以准确地识别出轴承的故障类型,比如滚珠的裂纹、滚道的磨损等。
第二种方法是时域分析。
时域分析直接观察振动信号的波形变化,可以判断轴承是否存在明显的故障振动特征。
常用的时域分析方法包括包络分析、峰峰值分析和自相关分析等。
这些方法可以提取振动信号的幅值、波形形状和周期特征,从而判断轴承是否存在异常。
第三种方法是模式识别。
模式识别是一种利用机器学习算法对振动信号进行分类和诊断的方法。
通过构建合适的特征向量并利用分类算法,可以对轴承的故障类型进行准确诊断。
常用的模式识别算法包括支持向量机、人工神经网络和决策树等。
模式识别方法具有较高的准确性和鲁棒性,在实际应用中已取得了良好的效果。
除了以上方法,还有一些其他的振动信号分析与故障诊断方法,比如相关分析、阶次分析和熵分析等。
这些方法都可以从不同的方面提供有用的信息,帮助判断轴承的工作状态和故障类型。
综上所述,调心球轴承的振动信号分析与故障诊断方法对于提高设备的可靠性和安全性具有重要意义。
通过应用合适的分析方法,可以有效地判断轴承的故障类型,并采取相应的维修和保养措施,延长轴承的使用寿命,提高设备的运行效率。
滚动轴承振动信号特性分析
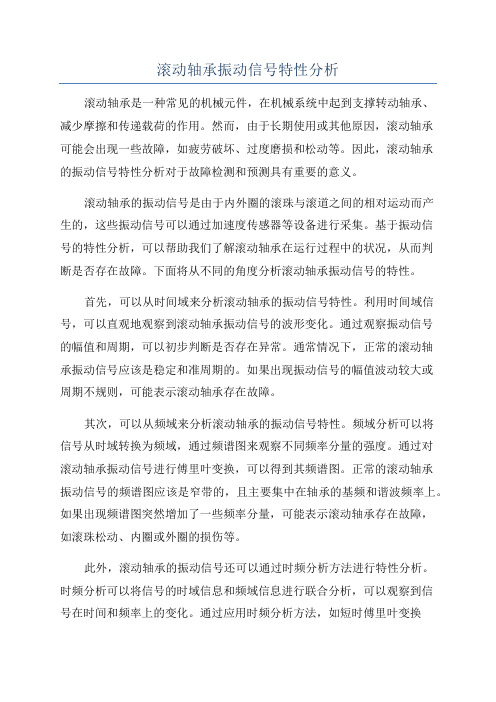
滚动轴承振动信号特性分析滚动轴承是一种常见的机械元件,在机械系统中起到支撑转动轴承、减少摩擦和传递载荷的作用。
然而,由于长期使用或其他原因,滚动轴承可能会出现一些故障,如疲劳破坏、过度磨损和松动等。
因此,滚动轴承的振动信号特性分析对于故障检测和预测具有重要的意义。
滚动轴承的振动信号是由于内外圈的滚珠与滚道之间的相对运动而产生的,这些振动信号可以通过加速度传感器等设备进行采集。
基于振动信号的特性分析,可以帮助我们了解滚动轴承在运行过程中的状况,从而判断是否存在故障。
下面将从不同的角度分析滚动轴承振动信号的特性。
首先,可以从时间域来分析滚动轴承的振动信号特性。
利用时间域信号,可以直观地观察到滚动轴承振动信号的波形变化。
通过观察振动信号的幅值和周期,可以初步判断是否存在异常。
通常情况下,正常的滚动轴承振动信号应该是稳定和准周期的。
如果出现振动信号的幅值波动较大或周期不规则,可能表示滚动轴承存在故障。
其次,可以从频域来分析滚动轴承的振动信号特性。
频域分析可以将信号从时域转换为频域,通过频谱图来观察不同频率分量的强度。
通过对滚动轴承振动信号进行傅里叶变换,可以得到其频谱图。
正常的滚动轴承振动信号的频谱图应该是窄带的,且主要集中在轴承的基频和谐波频率上。
如果出现频谱图突然增加了一些频率分量,可能表示滚动轴承存在故障,如滚珠松动、内圈或外圈的损伤等。
此外,滚动轴承的振动信号还可以通过时频分析方法进行特性分析。
时频分析可以将信号的时域信息和频域信息进行联合分析,可以观察到信号在时间和频率上的变化。
通过应用时频分析方法,如短时傅里叶变换(STFT)和小波变换,可以查看滚动轴承振动信号在时间和频率上的瞬态和局部特性。
这种分析方法可以帮助我们检测滚动轴承振动信号的瞬态特征和突变情况,提高故障检测和预测的准确性。
最后,滚动轴承的振动信号特性还可以通过统计学方法进行分析。
通过统计学参数,如均值、标准差和峭度等,可以观察滚动轴承振动信号的集中程度、离散程度和峰态等特性。
轴承振动特征分析
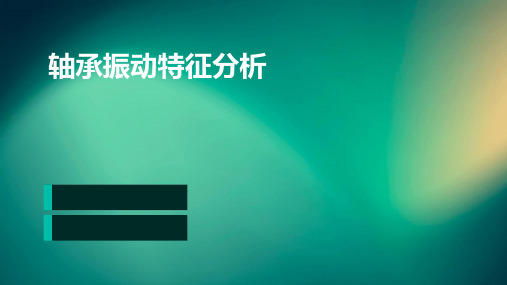
06 结论与建议
结论总结
轴承故障诊断的准确性得 到提高
通过分析振动信号,可以更准确地判断轴承 的运行状态,及时发现潜在的故障。
故障模式识别更加明确
振动特征分析有助于识别轴承的故障模式,如内圈 、外圈或滚动体的故障,为后续的故障原因分析和 修复提供依据。
定量评估轴承性能
通过分析振动信号的频谱、幅值等信息,可 以对轴承的性能进行定量评估,为轴承的维 护和更换提供决策依据。
原因
主要包括轴承座刚度不足、安装 不良、基础松动等。
振动特征分析方法
通过频谱分析、波形分析、轴心 轨迹分析等方法,对轴承座的振 动信号进行采集、处理和分析, 提取出轴承座的振动特征。
实例分析结果
轴承座的振动特征主要表现为低 频振动信号,其频率与轴承座的 结构和基础有关,通过分析这些 特征可以判断轴承座的工作状态 和故障类型。
轴承振动概述
轴承振动是指轴承在运转过程中产生的振动 现象,其产生的原因主要包括轴承内部元件 的相互作用、轴承座的不稳定以及外部激励 等。
轴承振动特征分析主要通过采集轴承的 振动信号,利用信号处理技术提取特征 ,进而对轴承的工作状态进行评估。
轴承振动通常采用振动烈度来描述, 其评价指标包括加速度、速度和位移 等。
02 轴承振动产生的原因
制造误差
材料不均匀
轴承材料内部存在不均匀性,导 致在运转过程中受力不均,引起 振动。
热处理不当
轴承的热处理工艺不佳,导致材 料内部存在残余应力,在运转过 程中产生振动。
装配误差
安装位置不准确
轴承在安装过程中位置不准确,导致运转过程中受力不均, 引起振动。
装配间隙不当
轴承的装配间隙过小或过大,都会影响轴承的正常运转,产 生振动。
机器振动特征分析(2)轴承

转速愈高,预期的寿命愈短。理论的轴承寿命随轴承承受的的负 载的三次方变化。如果设计者只考虑轴承的静载和如皮带拉伸等其他 部件静载,则轴承的理论计算寿命会大打折扣。
缩短滚动轴承寿命的因素
例:
重量为2000磅 908公斤 的转子,转速为6000 公斤) 6000转 在直径为3英尺(半径为18 18英 重量为2000磅(908公斤)的转子,转速为6000转/分,在直径为3英尺(半径为18英 2000 457. 毫米)处的转子上存在一个1盎司(28.35克 的不平衡质量。 寸 =457.2毫米)处的转子上存在一个1盎司(28. 35克 )的不平衡质量。此不平衡质量产 生的离心力计算: 生的离心力计算:
轴承故障原因及其解决
• 腐蚀 –其征兆是在滚道、滚子、保 持架或其他位置出现红棕色 区域 –原因是轴承接触腐蚀性流体 和气体 –严重情况下,腐蚀引起轴承 早期疲劳失效 –除掉腐蚀流体,尽可能使用 整体密封轴承
轴承故障原因及其解决
• 不对中
– 征兆是滚珠在滚道上产生的磨痕与滚道边缘不平行 – 如果不对中超过0.001in/in,会产生轴承和轴承座异常 温升,和保持架球磨损
滚动轴承故障频率计算例
典型的轴承故障发展过程
润滑分析 声发射检测
感官
振动分析
典型的轴承故障发展过程
轴承故障劣化发展不是按线性规律,而是按指数规律变化
灾难性破坏
X
累 积 的 损 伤
1 2 3 4
阶段≈轴承剩余寿命的10-20% 阶段≈轴承剩余寿命的5-10% 阶段≈轴承剩余寿命的1-5% 阶段≈一小时至轴承剩余寿命的1%
d=滚动体直径; D=滚动轴承平均直径(滚动体中心处直径); φ=径向方向接触角; n=滚动体数目; No=轴承外环角速度; No Ni=轴承内环角速度(=轴转速). Ni=
滑动轴承、滚动轴承振动故障症状特征分析与解决处理方法(图文并茂详解)

滑动轴承、滚动轴承振动故障症状特征分析与解决处理方法(图文并茂详解)一、滚动轴承症状特征:(一)、滚动轴承故障发展的第一阶段症状特征:1、超声波频率范围(>250K赫兹) 内的最早的指示;2、利用振动加速度包络技术(振动尖峰能量gSE)可最好地评定频谱。
(二)、滚动轴承故障发展的第二阶段症状特征:1、轻微的故障激起滚动轴承部件的自振频率振动。
2、故障频率出现在500-2000赫兹范围内。
3、在滚动轴承故障发展第二阶段的末端,在自振频率的左右两侧出现边带频率。
(三)、滚动轴承故障发展的第三阶段症状特征:1、出现滚动轴承故障频率及其谐波频率。
2、随着磨损严重出现故障频率的许多谐波频率,边带数也增多。
3、在此阶段,磨损可以用肉眼看见,并环绕轴承的圆周方向扩展。
(四)、滚动轴承故障发展的第四阶段症状特征:1、离散的滚动轴承故障频率消失,被噪声地平形式的宽带随机振动取代之。
2、朝此阶段末端发展,甚至影响1X转速频率的幅值。
3、事实上,高频噪声地平的幅值和总量幅值可能反而减小。
二、滑动轴承症状特征:(一)、油膜振荡不稳定性症状特征:1、如果机器在2X转子临界转速下运转,可能出现油膜振荡。
2、当转子升速到转子第二阶临界转速时,油膜涡动接近转子临界转速,过大的振动将使油膜不能支承轴。
3、油膜振荡频率将锁定在转子的临界转速。
4、转速升高,油膜涡动频率也不升高。
(二)、油膜涡动不稳定性症状特征:1、通常出现在旋转转速的42-48%频率范围内。
2、有时,振动幅值非常大油膜涡动是固有不稳定的,因为它增大离心力,所以增大涡动力。
(三)、滑动轴承磨损/间隙故障症状特征:1、滑动轴承磨损故障后阶段将产生幅值很大的旋转转速频率的谐波频率振动。
2、当存在过大的滑动轴承间隙时,很小的不平衡或不对中将导致很大幅值的振动。
滚动轴承的振动形式及振动机理的研究
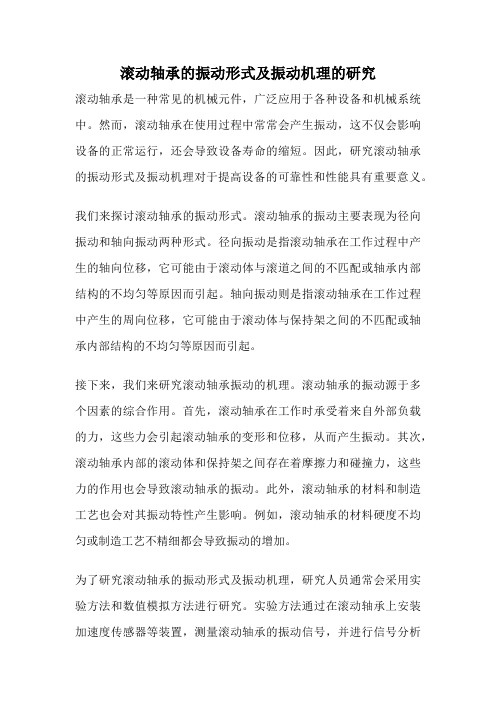
滚动轴承的振动形式及振动机理的研究滚动轴承是一种常见的机械元件,广泛应用于各种设备和机械系统中。
然而,滚动轴承在使用过程中常常会产生振动,这不仅会影响设备的正常运行,还会导致设备寿命的缩短。
因此,研究滚动轴承的振动形式及振动机理对于提高设备的可靠性和性能具有重要意义。
我们来探讨滚动轴承的振动形式。
滚动轴承的振动主要表现为径向振动和轴向振动两种形式。
径向振动是指滚动轴承在工作过程中产生的轴向位移,它可能由于滚动体与滚道之间的不匹配或轴承内部结构的不均匀等原因而引起。
轴向振动则是指滚动轴承在工作过程中产生的周向位移,它可能由于滚动体与保持架之间的不匹配或轴承内部结构的不均匀等原因而引起。
接下来,我们来研究滚动轴承振动的机理。
滚动轴承的振动源于多个因素的综合作用。
首先,滚动轴承在工作时承受着来自外部负载的力,这些力会引起滚动轴承的变形和位移,从而产生振动。
其次,滚动轴承内部的滚动体和保持架之间存在着摩擦力和碰撞力,这些力的作用也会导致滚动轴承的振动。
此外,滚动轴承的材料和制造工艺也会对其振动特性产生影响。
例如,滚动轴承的材料硬度不均匀或制造工艺不精细都会导致振动的增加。
为了研究滚动轴承的振动形式及振动机理,研究人员通常会采用实验方法和数值模拟方法进行研究。
实验方法通过在滚动轴承上安装加速度传感器等装置,测量滚动轴承的振动信号,并进行信号分析和处理,从而得到滚动轴承的振动特性。
数值模拟方法则是利用计算机模拟滚动轴承的工作过程,通过对滚动轴承内部力学和动力学特性的建模和计算,预测和分析滚动轴承的振动行为。
通过研究滚动轴承的振动形式及振动机理,可以帮助人们更好地理解滚动轴承的工作原理和振动特性,为改善滚动轴承的设计和制造提供理论依据和技术支持。
例如,可以通过优化滚动轴承的结构和材料,减小滚动轴承的振动幅值和频率,提高滚动轴承的工作效率和寿命。
此外,还可以通过改进滚动轴承的润滑和冷却方式,减少滚动轴承的热量和摩擦,从而降低滚动轴承的振动水平。
- 1、下载文档前请自行甄别文档内容的完整性,平台不提供额外的编辑、内容补充、找答案等附加服务。
- 2、"仅部分预览"的文档,不可在线预览部分如存在完整性等问题,可反馈申请退款(可完整预览的文档不适用该条件!)。
- 3、如文档侵犯您的权益,请联系客服反馈,我们会尽快为您处理(人工客服工作时间:9:00-18:30)。
8.
9.
当滚动体本身出现故障时,往往会产生不仅滚动体故障频率(BSF),还有 保持架故障频率(FTF);
轴承保持架断裂时,可能出现滚动体旋转故障频率 ;
10. 一个以上滚动体有故障时,将产生有故障的滚动体数目×滚动体故障特征 频率的频率。如果5个滚珠或滚柱上有故障,往往将出现5×BSF的频率。 11. 轴承故障频率允许的振动幅值不能绝对限定。它不仅与具体机器、转速有 关,还与轴承故障频率传递的通路有很大关系。 指示轴承损坏的最明显 的标志就是存在轴承故障频率的谐波频率,尤其是这些频率伴有1×转速 频率或轴承其它故障频率边带,应尽快更换该轴承。
n=滚动体数目; N=轴的转速。 注:1.滚动轴承没有滑动;2.滚动轴承几何尺寸没有变化;3.轴承外环固定不旋转
估算公式
滚动轴承故障频率计算例
典型的轴承故障发展过程
润滑分析 声发射检测 感官
振动分析
典型的轴承故障发展过程
轴承故障劣化发展不是按线性规律,而是按指数规律变化
灾难性破坏
X
累 积 的 损 伤
其它缩短滚动轴承寿命的因素
转子不只承受不平衡,还承受不对中、松动、气蚀或其它故障引起
的动载荷,轴承的实际寿命可能还要短。
其它因素:润滑不当,错误润滑剂,灰尘和其它污染物污染,储存 不当,潮气,运输或使用时嗑碰、刮伤,错用轴承型号,轴承安装
不当等。
最重要的对策是监测滚动轴承的状态,早期发现轴承故障,跟踪其 发展趋势,并知道何时需更换轴承;
1 2 3 4
阶段轴承剩余寿命的10-20% 阶段轴承剩余寿命的5-10% 阶段轴承剩余寿命的1-5% 阶段一小时至轴承剩余寿命的1%
4 1 2 3
通常约百分之八十至九十的轴承寿命
时间
轴承故障发展的四个阶段
I. 初始阶段
1. 噪声正常 2. 温度正常 3. 可以用超声,振动尖峰能量,声发射测量出来,轴承外环有缺陷 4. 振动总量比较小,无离散的轴承故障频率尖峰 5. 剩余寿命大于10%
轴承故障特征频率的特点
12. 评定的低速机器的轴承状态:
评定尤其是低于100转/分转速的机器轴承状态时,推荐采集时域波形和 (FFT)频谱二者。当转速很低时,滚动体滚动通过轴承内外环上缺陷时发 生的脉冲没有足够能量产生清楚的,可以检测出来的FFT谱中的频率,但 是在时域波形中仍然可能清楚的看出来。
轴承故障四个阶段的频谱
Stage 1
no apparent change on typical velocity spectrum
轴承故障原因及其解决
• 污染 – 污染是轴承失效主要原因之一
– 污染的征兆是在滚道和滚动体表面有点痕,导致振 动加大和磨损
– 清洁环境,工具,规范操作。新轴承的储运。 • 润滑油失效 – 滚道和滚子的变色(蓝、棕)是润滑失效的征兆, 随之产生滚道、滚子和保持架磨损,导致过热和严 重故障。 – 滚动轴承的正常运行取决于各部件间存在良好油膜 失效常常由润滑不足和过热引起
轴承故障特征频率的特点
1. 2. 3. 4. 轴承的故障频率与其他故障频率不同 ; 轴承故障频率是转速频率的非整数倍 ; 内外环故障频率的和频=“轴承滚动体通过频率” (滚动体个数 ×RPM) 轴承内环故障频率往往伴有1 X转速频率的边带
轴承故障特征频率的特点
5. 6. 7. 轴承外环故障频率的幅值高于轴承内环故障频率的幅值; 轴承故障一般在发展到滚动体和保持架出现故障之前首先出现的是内环或 外环故障频率; 轴承保持架故障频率(FTF)通常不是以其基频出现 ;
轴承故障原因及其解决
• 腐蚀
–其征兆是在滚道、滚子、保 持架或其他位置出现红棕色 区域 –原因是轴承接触腐蚀性流体 和气体 –严重情况下,腐蚀引起轴承 早期疲劳失效 –除掉腐蚀流体,尽可能使用 整体密封轴承
轴承故障原因及其解决
• 不对中
– 征兆是滚珠在滚道上产生的磨痕与滚道边缘不平行
– 如果不对中超过0.001in/in,会产生轴承和轴承座异常 温升,和保持架球磨损
FTFr≌0.4N
n=滚动体数目; N=轴的转速。
注:1.滚动轴承没有滑动;2.滚动轴承几何尺寸没有变化; 3.轴承外环固定不旋转.
经验公式
滚动轴承故障频率计算(4)
外环故障频率: BPFOe≌N(0.5n-1.2) 内环故障频率: BPFIe≌N(0.5n+1.2) 滚动体故障频率: BSFe≌N(0.2n-1.2/n) 保持架故障频率: FTFe≌N(0.5-1.2/n)
1. 2. 3. 4. 5. 6. 7. 可听到噪声 温度略升高 非常高的超声,声发射,振动尖峰能量,轴承外环有故障 振动加速度总量和振动速度总量有大的增加 在线性刻度的频谱上清楚地看出轴承故障频率及其谐波和边带 振动频谱噪声地平明显提高 剩余寿命小于1%
IV.第四阶段
1. 噪声的强度改变 2. 温度明显升高 3. 超声,声发射,振动尖峰能量迅速增大,随后逐渐减小,轴承外环处在损坏之 前故障状态 4. 振动速度总量和振动位移总量明显增大,振动加速度总量减小 5. 较低的轴承故障频率占优势的振动尖峰,振动频谱中噪声地平非常高 6. 剩余寿命小于0.2%
滚动轴承振动尖峰能量(gSE)报警值。
滚动轴承故障的振动特征
轴承零部件的自振频率
安装在机器上的滚动轴承自振频率范围约为500到2000Hz之 间。自振频率与转速无关,无论轴的转速高低它都处在一个相同 的频率位置。
轴承故障特征频率
滚动轴承故障特征频率就是轴承故障产生的振动频率。 BPFO – 外圈故障特征频率 BPFI – 内圈故障特征频率 BSF – 滚动体故障特征频率 FTF - 保持架故障特征频率
• 正常疲劳失效 –疲劳失效指滚道和滚动体上发生龟 裂,并随之产生材料碎片剥落 –这种疲劳为逐渐发生,一旦开始则 迅速扩展,并伴随明显的振动增加
–更换轴承,和设计有更长疲劳寿命 的轴承
轴承故障原因及其解决
• 反向载荷 –角接触轴承的设计只接受一个方向 的轴向载荷 –当方向相反时,外圈的椭圆接触区 域被削平… –结果是应力增加,温度升高,并产 生振动增大和轴承早期失效
机器振动特征分析(2)
滚动轴承故障
滚动轴承故障
滚动轴承是机器中最精密的部件,公差是其余 部件的十分之一。 由于各种原因,只有10%到20%的轴承能达 到它们的设计寿命
滚动轴承类型
深槽球轴承 针轴承 角接触球轴承
圆柱滚子轴承
球面滚子轴承
圆锥滚子轴承
滚动轴承为什么会过早损坏?
主要因素之一是过大的动载荷即振动。 理论计算滚珠轴承寿命公式,表明为什么作用在轴承上的动载减少轴 承的寿命:
滚动轴承故障频率计算(1)
保持架故障频率: FTF=(1/2){No[1+(d/D)Cos φ] +Ni [1-(d/D)Cos φ]} 滚动体旋转故障频率: BSF=(1/2)(D/d) |No-Ni|{ [1-(d/D)Cos φ]² } 外环故障频率: BPFO=(1/2)n |No-Ni| [1-(d/D)Cosφ] 内环故障频率: BPFI=(1/2)n |Ni- No| [1+(d/D)Cosφ]
随机的超声频率;
轴承零部件的自振频率;
轴承故障特征频率; 轴承故障的和频及差频。
随机的超声频率振动
滚动轴承初始故障时产生的振动,从滚动轴承安装在设备上直到 它们刚发生故障之前,发生的频率范围从约5000Hz到60000Hz超声 频率范围。包括振动尖峰能量(SpikeEneey),高频加速度(HFD), 冲击脉冲(ShockPules)及其他。通常,以总量值评定轴承的状态, 其频谱数据信息更丰富。
转速愈高,预期的寿命愈短。理论的轴承寿命随轴承承受的的负 载的三次方变化。如果设计者只考虑轴承的静载和如皮带拉伸等其他 部件静载,则轴承的理论计算寿命会大打折扣。
缩短滚动轴承寿命的因素
例:
重量为2000磅(908公斤)的转子,转速为6000转/分,在直径为3英尺(半径为18英 寸 =457.2毫米)处的转子上存在一个1盎司(28. 35克 )的不平衡质量。此不平衡质量产 生的离心力计算:
d=滚动体直径; D=滚动轴承平均直径(滚动体中心处直径); φ=径向方向接触角; n=滚动体数目; No=轴承外环角速度; Ni=轴承内环角速度(=轴转速). 注:1.滚动轴承没有滑动;2.滚动轴承几何尺寸没有变化;3.轴承外环和轴承内环都旋转.
滚动轴承故障频率计算(2)
保持架故障频率: FTF=(N/2)[1-(d/D)Cos φ] 滚动体旋转故障频率: BSF=(N/2)(D/d){1-[(d/D)Cos φ]² } 外环故障频率: BPFO=(N/2)n[1-(d/D)Cosφ] 内环故障频率: BPFI=(N/2)n[1+(d/D)Cosφ]
滚动轴承故障特征频率
BPFO BPFI BSF FTF -
Ball Pass Frequency Outer Race Ball Pass Frequency Inner Race Ball Spin Frequency Cage Frequency or Fundamental Train Frequency
II. 第二阶段
1. 噪声略增大 2. 温度正常 3. 超声,声发射,振动尖峰能量有大的增加,轴承外环有缺陷, 4. 振动总量略增大(振动加速度总量和振动速度总量) 5. 对数刻度频谱上可清楚看到轴承故障频率,线性刻度频谱上难得看到,噪声地平 明显提高 6. 剩余寿命5%
轴承故障发展的四个阶段
III. 第三阶段
轴承故障特征频率的特点
13.振动传感器置于尽可能靠近轴承的承载区,尤其是轴承仅支承径向负载时。 14.不合适的轴承负载和安装问题 若轴承负载不合适或安装不恰当,例如,安装新轴承时,如果轴承与轴承 座过盈配合过紧,使轴承“咔入”轴承座中,导致轴承内部间隙发生变化,使 滚动体强制被压向轴承的内外环。出现这种情况,轴承在起动时立即产生轴承 外环和内环的故障频率。 由于安装不当对轴承施加了过大负荷。虽然,可能尚未发生实际损坏,但 是,如果检测不出这种故障问题并采取措施修正,则该轴承将在其预定寿命之 前很早就损坏。 15.轴承润滑不良产生的频率 特征是在900到1600Hz范围内,有3或4个尖峰,尖峰之间的差频在80到 130Hz。润滑良好的轴承可能也包括这些频率分量,然而,它们的幅值非常小, 约为1.27mm/s或更小。当润滑不良时,幅值增大到 2.54到5.08mm/s