硫对镇雄煤气化灰渣析铁过程的影响
小议炉渣脱硫及其影响因素
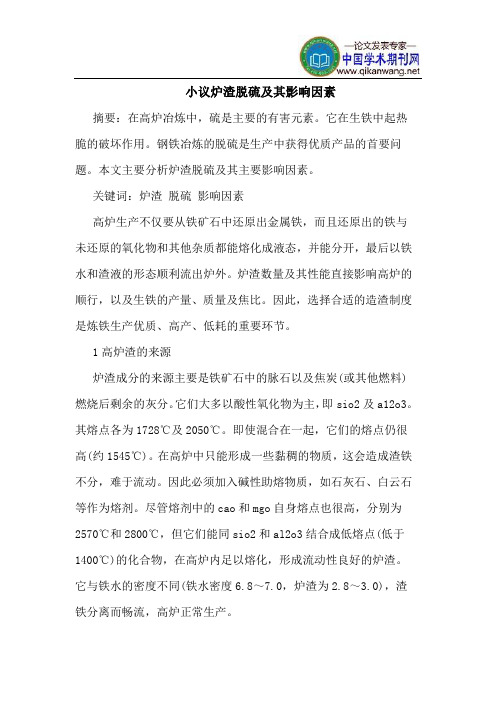
小议炉渣脱硫及其影响因素摘要:在高炉冶炼中,硫是主要的有害元素。
它在生铁中起热脆的破坏作用。
钢铁冶炼的脱硫是生产中获得优质产品的首要问题。
本文主要分析炉渣脱硫及其主要影响因素。
关键词:炉渣脱硫影响因素高炉生产不仅要从铁矿石中还原出金属铁,而且还原出的铁与未还原的氧化物和其他杂质都能熔化成液态,并能分开,最后以铁水和渣液的形态顺利流出炉外。
炉渣数量及其性能直接影响高炉的顺行,以及生铁的产量、质量及焦比。
因此,选择合适的造渣制度是炼铁生产优质、高产、低耗的重要环节。
1高炉渣的来源炉渣成分的来源主要是铁矿石中的脉石以及焦炭(或其他燃料)燃烧后剩余的灰分。
它们大多以酸性氧化物为主,即sio2及a12o3。
其熔点各为1728℃及2050℃。
即使混合在一起,它们的熔点仍很高(约1545℃)。
在高炉中只能形成一些黏稠的物质,这会造成渣铁不分,难于流动。
因此必须加入碱性助熔物质,如石灰石、白云石等作为熔剂。
尽管熔剂中的cao和mgo自身熔点也很高,分别为2570℃和2800℃,但它们能同sio2和al2o3结合成低熔点(低于1400℃)的化合物,在高炉内足以熔化,形成流动性良好的炉渣。
它与铁水的密度不同(铁水密度6.8~7.0,炉渣为2.8~3.0),渣铁分离而畅流,高炉正常生产。
高炉生产中总是希望炉渣愈少愈好,但完全没有炉渣是不可能的(也是不可行的),高炉工作者的责任是在一定的矿石和燃料条件下,选定熔剂的种类和数量,配出最有利的炉渣成分,以满足冶炼过程的要求。
2炉渣的作用2.1成渣的过程煤气与炉料在相对运动中,前者将热量传给后者,炉料在受热后温度不断提高。
不同的炉料在下降过程中其变化不同。
矿石中的氧化物逐渐被还原,而脉石部分首先是软化,而后逐渐熔融、滴落穿过焦炭层,汇集到炉缸。
石灰石在下降过程中受热后逐渐分解,到1000℃以上区域才能分解完毕。
分解后的cao参与造渣。
焦炭在下降过程中起料柱的骨架作用,一直保持固体状态下到风口,与鼓风相遇燃烧,剩下的灰分进入炉渣。
《煤气化灰渣热处理资源化利用》札记

《煤气化灰渣热处理资源化利用》阅读随笔目录一、内容简述 (3)1. 煤气化技术的发展与应用 (3)2. 灰渣处理的现状与挑战 (5)3. 资源化利用的重要性与意义 (6)二、煤气化灰渣的基本特性 (7)1. 灰渣的成分分析 (9)2. 灰渣的物理性质 (10)3. 灰渣的化学性质 (11)三、煤气化灰渣热处理技术 (12)1. 热处理原理及方法 (13)a. 灰渣焚烧 (15)b. 灰渣热解 (16)c. 灰渣气化 (17)2. 热处理工艺流程 (18)a. 预处理工艺 (19)b. 热处理工艺 (21)c. 后处理工艺 (22)四、煤气化灰渣资源化利用途径 (23)1. 建筑材料 (24)a. 灰渣混凝土 (25)b. 灰渣砖 (27)2. 陶瓷与耐火材料 (28)3. 化肥工业原料 (29)4. 路面基础材料 (31)5. 膨胀蛭石与硅酸钙绝热材料 (32)五、煤气化灰渣热处理资源化利用的挑战与对策 (34)1. 技术难题与瓶颈 (35)2. 成本控制与经济效益 (37)3. 政策支持与标准规范 (38)六、案例分析 (39)1. 国内外煤气化灰渣热处理资源化利用的成功案例 (40)2. 案例分析与经验借鉴 (40)七、展望与建议 (42)1. 技术创新与研发方向 (43)2. 政策引导与产业升级 (44)3. 企业合作与市场化运作 (45)八、结语 (47)1. 煤气化灰渣热处理资源化利用的前景展望 (48)2. 对未来研究的展望 (49)一、内容简述《煤气化灰渣热处理资源化利用》主要围绕煤气化过程中产生的灰渣的处理与资源化利用进行阐述。
此书内容深入剖析了煤气化灰渣的性质、成分及其处理现状,详细探讨了如何通过热处理技术实现灰渣的资源化利用。
书中不仅介绍了相关理论知识,还结合实践案例,展示了灰渣资源化利用的实际操作与效果。
通过对此书的阅读,我深感其在能源利用与环境保护之间的平衡中发挥了重要作用。
煤气化渣特性分析及资源化利用途径

煤气化渣特性分析及资源化利用途径目录一、内容概要 (2)1.1 煤气化技术的重要性 (2)1.2 煤气化渣的产生及其危害 (3)1.3 国内外研究现状及发展趋势 (4)二、煤气化渣基本特性分析 (5)2.1 物理特性 (6)2.2 化学成分 (7)2.3 矿物组成 (8)2.4 粒度分布 (10)三、煤气化渣资源化利用途径 (11)3.1 建筑材料 (12)3.2 冶金行业 (13)3.2.1 矿石粉 (14)3.2.2 高炉喷吹料 (16)3.3 化肥工业 (16)3.4 路面基础材料 (18)3.4.1 水泥稳定碎石 (19)3.4.2 沥青混合料 (20)3.5 环保领域 (22)3.5.1 废水处理 (23)3.5.2 废弃物填埋 (24)四、煤气化渣特性影响因素及优化措施 (25)4.1 影响因素分析 (27)4.2 优化措施探讨 (28)五、结论与展望 (29)5.1 结论总结 (30)5.2 发展前景展望 (31)一、内容概要煤气化渣是煤气化过程中产生的固体残渣,其产生量与煤气化工艺、原料煤性质、气化炉操作条件等诸多因素密切相关。
煤气化渣特性分析主要涉及其化学成分、物理形态、热值、灰分以及重金属含量等方面。
在资源化利用方面,煤气化渣具有较高的潜在价值。
其中所含的某些重金属元素如钙、镁、硅等,可以作为陶瓷原料或水泥原料的替代品,用于生产建筑材料;另一方面,煤气化渣中的有机物质在一定条件下可以转化为生物质能源,如沼气或生物柴油等,实现能源的回收和再利用。
煤气化渣还可以作为吸附剂或过滤材料应用于污水处理、废气处理等领域,发挥其吸附、过滤和净化作用。
对煤气化渣进行深入研究,发掘其更多潜在应用价值,对于推动煤炭清洁高效利用、降低环境污染、实现可持续发展具有重要意义。
1.1 煤气化技术的重要性煤气化技术在现代工业中扮演着至关重要的角色,它不仅能够将煤炭转化为高热值的合成气,还能进一步转化为各种化工原料和燃料。
影响生铁质量因素的分析
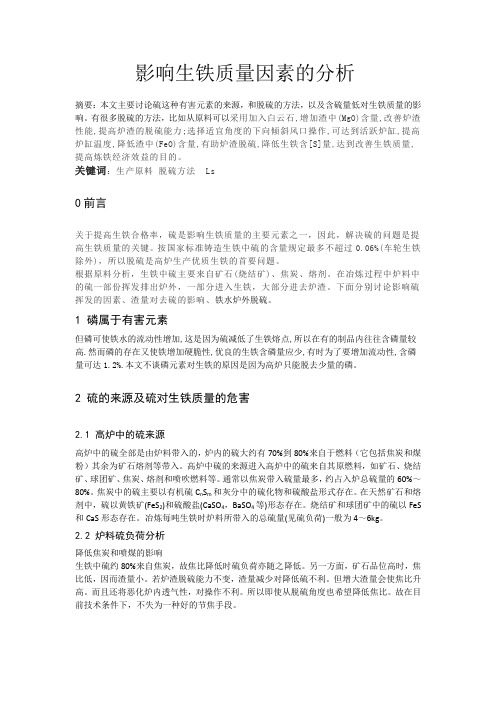
影响生铁质量因素的分析摘要:本文主要讨论硫这种有害元素的来源,和脱硫的方法,以及含硫量低对生铁质量的影响。
有很多脱硫的方法,比如从原料可以采用加入白云石,增加渣中(MgO)含量,改善炉渣性能,提高炉渣的脱硫能力;选择适宜角度的下向倾斜风口操作,可达到活跃炉缸,提高炉缸温度,降低渣中(FeO)含量,有助炉渣脱硫,降低生铁含[S]量,达到改善生铁质量,提高炼铁经济效益的目的。
关键词:生产原料脱硫方法 Ls0前言关于提高生铁合格率,硫是影响生铁质量的主要元素之一,因此,解决硫的问题是提高生铁质量的关键。
按国家标准铸造生铁中硫的含量规定最多不超过0.06%(车轮生铁除外),所以脱硫是高炉生产优质生铁的首要问题。
根据原料分析,生铁中硫主要来自矿石(烧结矿)、焦炭、熔剂。
在冶炼过程中炉料中的硫一部份挥发排出炉外,一部分进入生铁,大部分进去炉渣。
下面分别讨论影响硫挥发的因素、渣量对去硫的影响、铁水炉外脱硫。
1 磷属于有害元素但磷可使铁水的流动性增加,这是因为硫减低了生铁熔点,所以在有的制品内往往含磷量较高.然而磷的存在又使铁增加硬脆性,优良的生铁含磷量应少,有时为了要增加流动性,含磷量可达1.2%.本文不谈磷元素对生铁的原因是因为高炉只能脱去少量的磷。
2 硫的来源及硫对生铁质量的危害2.1 高炉中的硫来源高炉中的硫全部是由炉料带入的,炉内的硫大约有70%到80%来自于燃料(它包括焦炭和煤粉)其余为矿石熔剂等带入。
高炉中硫的来源进入高炉中的硫来自其原燃料,如矿石、烧结矿、球团矿、焦炭、熔剂和喷吹燃料等。
通常以焦炭带入硫量最多,约占入炉总硫量的60%~80%。
焦炭中的硫主要以有机硫C n S m和灰分中的硫化物和硫酸盐形式存在。
在天然矿石和熔剂中,硫以黄铁矿(FeS2)和硫酸盐(CaSO4,BaSO4等)形态存在。
烧结矿和球团矿中的硫以FeS 和CaS形态存在。
冶炼每吨生铁时炉料所带入的总硫量(见硫负荷)一般为4~6kg。
硫在灰铸铁中正面作用与负面作用全解

硫在灰铸铁中正面作用与负面作用全解本文简要介绍了外国学者与专家关于“硫在铸铁生产中的作用”方面有重要参考价值和推广意义的研究成果与论述,讲述了在为用户服务过程中所遇到的一些案例。
前言众所周知,硫元素在铸铁生产中具有不可忽视的双重作用,在一定条件下,它既是使铸件产生脆性,造成表面缺陷和熔渣缺陷,降低机械性能等等方面的有害者,又是提高灰铁铸件,尤其是低硫灰铁铸件,机械性能,增加灰铁共晶晶团数和薄壁球铁铸件球数等等的贡献者。
具有50多年实践经验的Roy Lobenhoter在评论硫的作用时说:生产球铁时,目标是将处理前的硫尽量保持得低些。
但有些专家声称,在球铁中,硫可以非常非常的低,“在某些地方可低到0.001%以下”;但是,我从未看到过令我满意的文件记载。
在灰铁中,如果硫太低,则可能产生问题。
低硫可以导致孕育剂出现奇怪的表现。
而有些“专家”说,硫应高于0.03%,而另外一些专家则说应高于0.05%,我却宁愿它达到0.07%的目标。
Reginald D Forrest“在球化之前基铁的最佳含硫量是多少”一文中指出:在基铁含硫量太低(低于0.008%)的地方,必须增硫,以便使其进入建议的范围(0.008-0.012%S);在用感应炉或转炉进行熔炼的地方,通过有控制地加入硫化铁(黄铁矿)的办法就可以很容易地做到这一点。
为增每0.001%的硫,每吨铁水应当加入30克(0.067磅)FeS;在用冲天炉进行熔炼接着进行脱硫(例如用多孔塞/碳化该)的地方,必须不断地调节(碳化钙加入量或者根据温度和搅拌强度决定的搅拌时间)等措施。
韩国和日本学者SangHak Lee等人在研究硫和稀土对铸铁组织和性能的影响时,得出的下列结论很有参考价值:①在使用高纯生铁的情况下,生成A+D型石墨的RE/S是0~1.25,生成A型石墨的RE/S 是1.25~5.0,生成全白口的RE/S是5.0或以上;②在使用普通生铁的情况下,生成A+D+(B)型石墨的RE/S是0~2.5,生成A型石墨的RE/S为2.5~5,生成全白口的RE/S是5.0或以上;③这两种铁的RE/S 都是在大约2.5时,可以获得弥散均匀的A型石墨而且白口的深度很小。
昭通镇雄某矿区煤中硫的分布特征

昭通镇雄某矿区煤中硫的分布特征摘要:昭通镇雄地区有大量的晚二叠时期原煤资源,其煤类主要是无烟煤和贫煤,煤中硫含量普遍偏高。
通过筛分浮沉试验、显微镜下观察等多种方式研究分析,发现煤中硫以硫铁矿为主,硫铁矿主要赋存于粘土矿物及石英中,少部分硫铁矿充填在胞腔中,通过洗选可将结核状硫铁矿与赋存于粘土矿物及石英中的硫铁矿脱去,但充填在植物胞腔中的硫铁矿难以脱除。
关键词:晚二叠;硫铁矿;煤中硫;Abstract: Zhaotong Shigeo raw coal resources of the Late Permian period, its coal-class anthracite and lean coal, sulfur content in coal is generally high. Screening drifting test, under the microscope a number of ways, and found that sulfur coal to mainly pyrite, pyrite mainly hosted in clay minerals and quartz, and less part of the pyrite filling in the cell cavity. stripped by washing can be nodular pyrite and hosted in clay minerals and quartz, pyrite, but pyrite removal is difficult to fill in the plant cell.Keywords: Late Permian; pyrite; sulfur in coal;1概述昭通镇雄地区有大量的煤炭资源,主要成煤时期为晚二叠世,其煤类以年轻无烟煤及贫煤为主,是国家规划的大型煤炭基地,累计查明全县煤炭地质资源量28.69亿吨,占全省的11.64,煤炭工业是镇雄县的支柱产业[1] 。
还原性气氛下熔渣析铁的影响因素_李寒旭

煤炭学报 JOURNAL OF CHINA COAL SOCIETY
Vol. 39 No. 7 July 2014
李寒旭,辛 宇,张冬梅,等. 还原性气氛下熔渣析铁的影响因素[J]. 煤炭学报,2014,39( 7) : 1372 - 1378. doi: 10. 13225 / j. cnki. jccs. 2014. 0184 Li Hanxu,Xin Yu,Zhang Dongmei,et al. Influencing factors of iron precipitation of slag under reducing conditions[J]. Journal of China Coal Society,2014,39( 7) : 1372 - 1378. doi: 10. 13225 / j. cnki. jccs. 2014. 0184
渣、堵渣的主要原因之一。选取含铁量较高的镇雄煤,运用 X 射线衍射( XRD) 、扫描电子显微镜和
X 射线能谱仪( SEM - EDX) 等测试手段,分析了不同还原性气氛、不同温度下渣样的矿物组成、表
观形貌和微区化学组成,探究了还原性气氛下熔渣析铁的影响因素。结果表明: 还原性气氛下影响
熔渣析铁的因素主要有还原性气氛浓度、反应温度、灰渣中钙长石的含量和硫的含量。还原性气氛
根据国标 GB 212—77 把分析煤样制成 815 ℃ 灰 样,然后 称 取 ( 1. 0 ± 0. 1 ) g 煤 灰 制 成 灰 柱,置 于 KTL1 600高温管式炉按表 3 的气化条件进行高温处 理,达到预定温度后,再用去离子水淬冷,干燥 12 h, 研钵研磨至 200 目下制得渣样。
表 1 镇雄煤煤质分析 Table 1 Basic properties of Zhenxiong coal
硫对灰铸铁组织和性能的影响
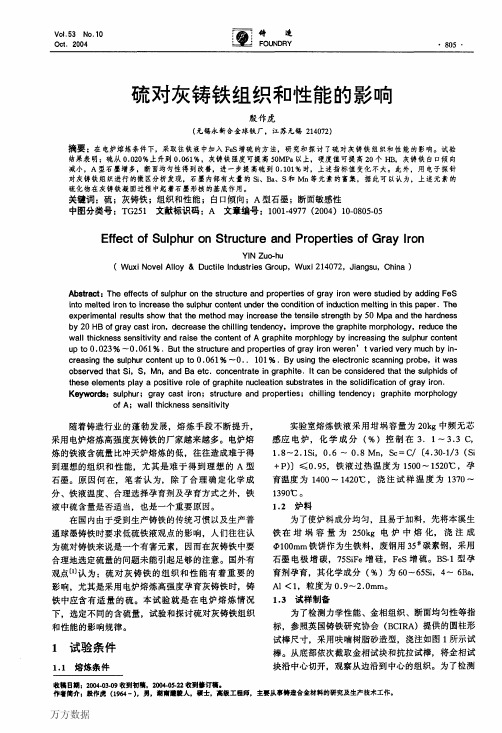
块、激冷试块和热分析试块。三角试块尺寸为底 13mm,高26mm,沿中部敲断,测量白口宽度。激 冷试块尺寸如图3所示,浇注时底部放一块15mm厚 钢板,沿试块中部敲断,测量白口深度。用 多O.5mmNiC卜NiSi热电偶丝,XwZ.200A自动平衡 记录仪测量铁液温度。其中三角试样、激冷试样和热 分析试样砂芯壳都用合脂砂制成。
1390℃。
1.2炉料 为了使炉料成分均匀,且易于加料,先将本溪生
铁在坩埚容量为250kg电炉中熔化,浇注成 西100mm铁饼作为生铁料,废钢用35#碳素钢,采用 石墨电极增碳,75SiFe增硅,FeS增硫。BSl型孕 育剂孕育,其化学成分(%)为60~65Si,4~6Ba, Al<1。粒度为0.9~2.0mm。 1.3试样制备
1 试验条件
1.1熔炼条件
实验室熔炼铁液采用坩埚容量为20kg中频无芯 感应电炉,化学成分(%)控制在3.1~3.3 C, 1.8~2.1Si,0.6~0.8 Mn,Sc=C/[4.30.1/3(Si +P)]≤0.95,铁液过热温度为1500~1520℃,孕 育温度为1400~1420℃,浇注试样温度为137()~
图5a、b、c、d、e、f是硫含量分别为0.023%、 0.061%和0.101%时,030mm试棒中心和边缘部位 的金相照片,从图5可看出,随着硫量的增加,I)型 石墨减少,A型石墨增加,形态变好。进一步增加硫 到0.105%时,试棒边缘开始出现少许D型和E型石 墨。 2.4.2硫对灰铸铁基体组织的影响
(a)含O.023%S 500×
(b)含0.067%S 500×
图6硫对灰铸铁基体组织的影响
Fig.6 The effect of sulphur on gray cast iron base structure
灰分在煤气化过程中的影响及解决方案

53煤气化生产工艺过程中,由原料煤和生产过程中产生的灰分,对气化系统影响较大,如何通过煤种中含有的灰分成分和比例,进而测量灰熔点等数值,更加高效稳定的进行生产,对煤气化的发展和完善有着深远的意义。
一、粉煤气化工艺首先备煤车间将粒度小于13mm的原料煤,通过皮带将煤粉送入碎煤仓,后经给煤机并伴有一定比例的石灰石一起送入磨机中碾磨,制成合格粒度的煤粉。
通过热惰性循环气干燥后,被循环风送入煤粉袋式过滤器中分离,分离出的循环风继续提供动力,煤粉被送到粉煤贮仓中待用。
粉煤贮仓内的煤粉靠重力进入锁斗内,锁斗经过加压输送至煤粉给料罐内,再通过四条煤粉管线,从煤粉给料罐罐体,上吹式送出,通过速度计和密度计测量计算,与经过氧气预热器加热后的高压氧气,一同喷入气化炉内。
在高温高压下瞬间发生氧化反应:(C+O 2=CO 2;C+CO 2=2CO;C+H 2O =CO+H 2;C+2H 2=CH 4;CO+H 2O=CO 2+H 2;C H 4+H 2O=CO+3H 2),生成主要成分为(CO+H 2)的合成气。
气化炉反应室产生的合成气,在激冷段被压缩机K13301送来的激冷气激冷,后经输气管送往激冷罐V13305,在激冷罐内被激冷水冷却、降温和洗涤除灰。
出激冷罐V13305的合成气,进入湿洗单元洗涤、除灰、降温。
合成气经过文丘里洗涤器喷淋水侵湿后,进入湿洗塔被洗涤水进一步洗涤、除灰、降温,温度降低的合成气被送往变换装置。
合格的变换气送至下一工序。
煤粉在高温高压下燃烧形成的液态渣,经过排渣口流入渣池。
熔渣被喷淋水激冷后,固化、淬裂成碎块。
大颗粒的渣迅速下沉,至破渣机处,经过破渣机破碎,变成玻璃状细小颗粒。
小颗粒的渣通过渣锁斗,定期排至捞渣机。
由捞渣机捞出后,通过长短皮带,将渣送往渣场储存。
渣水中残余的细渣及未反应的煤粉颗经过水利旋流器旋分,通过渣浆泵送至澄清单元。
处理后的渣水再次循环利用。
煤气化工序、湿洗工序的高温灰水,通过灰水角阀节流减压后,形成气液两相流。
煤液化残渣中硫的氧化规律

煤液化残渣中硫的氧化规律常卫科;徐洁;孙伟;袁桂梅;陈胜利;张胜振【摘要】利用四氢呋喃溶解煤液化残渣,将煤液化残渣分离为油相和四氢呋喃不溶物固体,之后测定其中各形态硫的含量,发现煤液化残渣中98%(质量分数)的硫存在于四氢呋喃不溶物固体中,且主要以磁黄铁矿的形式存在.故此以四氢呋喃不溶物为原料进行空气氧化,研究其中硫的氧化转化规律.结果表明,干空气氧化四氢呋喃不溶物,四氢呋喃不溶物总合硫量减少,氧化过程中生成硫酸盐和单质硫,其中单质硫在氧化过程中进入气相而脱离四氢呋喃不溶物固体;湿空气氧化四氢呋喃不溶物,四氢呋喃不溶物总合硫量基本不变,反应过程中仅有硫酸盐生成.实验条件下,氧化过程由磁黄铁矿颗粒上覆盖的硫酸盐产物层中的氧扩散控制,扩散活化能为26.25 kJ/mol.【期刊名称】《中国粉体技术》【年(卷),期】2018(024)002【总页数】8页(P44-51)【关键词】煤液化残渣;硫;氧化规律;硫酸盐【作者】常卫科;徐洁;孙伟;袁桂梅;陈胜利;张胜振【作者单位】中国石油大学(北京)重质油国家重点实验室,北京102249;中国石油大学(北京)重质油国家重点实验室,北京102249;中国石油大学(北京)重质油国家重点实验室,北京102249;中国石油大学(北京)重质油国家重点实验室,北京102249;中国石油大学(北京)重质油国家重点实验室,北京102249;北京低碳清洁能源研究所,北京102211【正文语种】中文【中图分类】TQ520.1煤液化残渣是煤在高温、高压条件下直接催化加氢的液化产物经常减压蒸馏后,不能蒸馏出来的物质。
其中含有高沸点有机物、未转化的煤粉、煤中的无机矿物和加入的加氢催化剂(通常是铁)。
煤液化残渣产量高达原煤使用量的20%~30%[1]。
由于在煤液化过程中主要使用铁基催化剂(硫铁矿),并加入硫单质作为助剂[2],在整个工艺过程中硫在残渣中富集,并最后以磁黄铁矿和黄铁矿的形式存在于液化残渣中,导致液化残渣的硫含量超过2.5%(质量分数,下同),高于原煤中硫含量[3-4]。
高炉炼铁过程中的炉渣脱硫技术

资源回收:回收利用废渣, 减少资源浪费
提高产品质量:降低硫含 量,提高钢铁产品质量
经济效益:降低生产成本, 提高企业经济效益
4
炉渣脱硫技术的工艺流程
炉渣的形成与处理
炉渣的形成:高炉炼铁过 程中产生的废渣
炉渣的成分:主要包括铁、 硅、锰、磷等元素
炉渣的处理方法:包括物 理处理、化学处理和生物 处理等
物理处理:包括磁选、浮 选、重选等方法,用于分 离炉渣中的有用成分
化学处理:包括酸浸、碱 浸、氧化还原等方法,用 于改变炉渣的化学性质
生物处理:利用微生物对 炉渣进行生物降解,用于 处理有毒有害成分
脱硫剂的选择与添加
脱硫剂种类:石灰石、白云石、 氧化镁等
脱硫剂添加方式:直接添加、 预混合添加、喷射添加等
硫效率
优化炉渣脱硫 设备,降低能
耗和成本
采用新型脱硫 剂,提高脱硫 效果和稳定性
结合其他环保 技术,实现炉 渣脱硫与废气 治理的协同优
化
6
炉渣脱硫技术的发展趋势和未来展望
新型脱硫剂的研究与开发
研究背景: 随着环保 要求的提 高,传统 脱硫剂逐 渐被淘汰
研究目标: 开发高效、 环保、经 济的新型 脱硫剂
燃料:煤炭、焦 炭等燃料在燃烧 过程中会产生硫 化物
熔剂:石灰石、 白云石等熔剂在 熔化过程中会产 生硫化物
空气:空气中的 硫化物在燃烧过 程中会被氧化, 产生硫化物
硫对高炉炼铁的影响
硫是铁矿石中的 有害元素,会影 响铁的质量和产 量
硫与铁反应生成 硫化铁,降低铁 的熔点,影响铁 的流动性和渗透 性
未来炉渣脱硫技术的发展方向与趋势
提高脱硫效率:通过改进 工艺和设备,提高脱硫效
率,降低能耗和成本。
炼铁高炉炉料中含硫物质的控制

炼铁高炉炉料中含硫物质
的控制
汇报人:
目录
01 02 03 04 05
添加目录项标题 硫对炼铁高炉的影响 控制含硫物质的方法 含硫物质控制的效果 含硫物质控制技术的发展趋势
1
添加目录项标题
2
硫对炼铁高炉的影响
硫在炼铁过程中的作用
硫是铁矿石中的有害元素,会影响铁的质量和产量 硫与铁反应生成硫化铁,降低铁的熔点和强度 硫还会导致炉料结块,影响高炉的透气性和生产效率 控制硫含量可以有效提高铁的质量和产量,降低生产成本
4
含硫物质控制的效果
提高生铁质量
含硫物质控制:减少 生铁中的硫含量,提
高生铁质量
效果:降低生铁中的 硫含量,提高生铁的
强度和韧性
控制方法:采用脱硫 剂、提高炉温、优化
炉料配比等方法
应用:广泛应用于钢 铁生产中,提高生铁
质量和生产效率
延长高炉使用寿命
含硫物质控制 可以有效减少 高炉炉料的腐
蚀和磨损
硫对生铁质量的影响
硫含量过高会导 致生铁质量下降, 影响其力学性能 和耐腐蚀性
硫与铁反应生成 硫化铁,降低生 铁的强度和韧性
硫化铁还会导致 生铁表面形成硫 化物,影响其外 观和加工性能
硫含量过高还会 影响生铁的熔化 性能,增加熔化 难度和能耗
硫对高炉设备的影响
腐蚀性:硫化物对高炉设备造成 腐蚀,影响设备使用寿命
物质的产生和排放
脱硫处理:采用物理 或化学方法去除原料
中的含硫物质
加强质量控制:严格 控制原料质量和生产 过程,确保含硫量在
规定范围内
选择合适的脱硫剂
脱硫剂的作用: 去除炉料中的
含硫物质
常见的脱硫剂: 石灰石、白云 石、氧化镁等
降低生铁含硫量途径的探讨
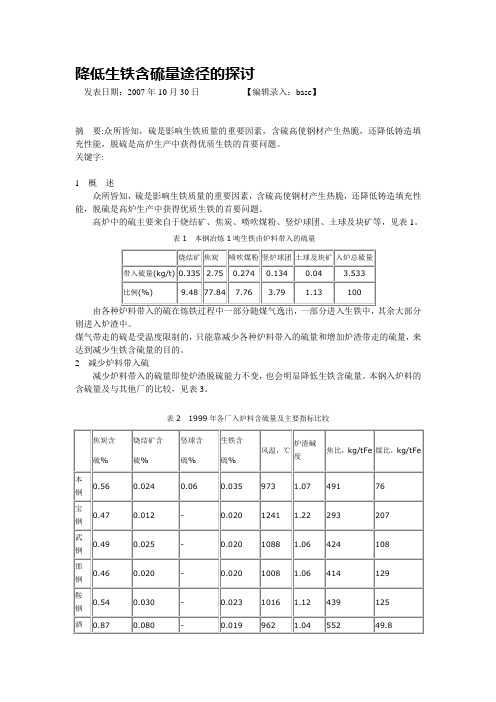
降低生铁含硫量途径的探讨发表日期:2007年10月30日【编辑录入:base】摘要:众所皆知,硫是影响生铁质量的重要因素,含硫高使钢材产生热脆,还降低铸造填充性能,脱硫是高炉生产中获得优质生铁的首要问题。
关键字:1概述众所皆知,硫是影响生铁质量的重要因素,含硫高使钢材产生热脆,还降低铸造填充性能,脱硫是高炉生产中获得优质生铁的首要问题。
高炉中的硫主要来自于烧结矿、焦炭、喷吹煤粉、竖炉球团、土球及块矿等,见表1。
表1本钢冶炼1吨生铁由炉料带入的硫量烧结矿焦炭喷吹煤粉竖炉球团土球及块矿入炉总硫量带入硫量(kg/t) 0.335 2.75 0.274 0.134 0.04 3.533比例(%) 9.48 77.84 7.76 3.79 1.13 100由各种炉料带入的硫在炼铁过程中一部分随煤气逸出,一部分进入生铁中,其余大部分则进入炉渣中。
煤气带走的硫是受温度限制的,只能靠减少各种炉料带入的硫量和增加炉渣带走的硫量,来达到减少生铁含硫量的目的。
2减少炉料带入硫减少炉料带入的硫量即使炉渣脱硫能力不变,也会明显降低生铁含硫量。
本钢入炉料的含硫量及与其他厂的比较,见表3。
表21999年各厂入炉料含硫量及主要指标比较焦炭含硫% 烧结矿含硫%竖球含硫%生铁含硫%风温,℃炉渣碱度焦比,kg/tFe 煤比,kg/tFe本钢0.56 0.024 0.06 0.035 973 1.07 491 76 宝钢0.47 0.012 - 0.020 1241 1.22 293 207 武钢0.49 0.025 - 0.020 1088 1.06 424 108 邯钢0.46 0.020 - 0.020 1008 1.06 414 129 鞍钢0.54 0.030 - 0.023 1016 1.12 439 125 酒0.87 0.080 - 0.019 962 1.04 552 49.8钢表3本钢炼铁原料的含硫量南芬矿粉歪矿粉地方矿粉澳矿粉弓长岭块矿锰矿二铁烧结矿土球二铁竖球TFe% 66.69 65.62 62.52 65.5 39.69 15.74 57.17 54.58 61.55S% 0.038 0.02 0.038 0.011 0.008 0.268 0.024 0.068 0.061从表中可以看出:焦炭带入高炉的硫量最多,直接影响着生铁的含硫量,本钢焦炭的含硫量明显高于宝钢、武钢及邯钢0.08%~0.1%,也高于鞍钢0.02%,而且焦比也高,所以由焦炭带入的硫量就比这些厂家多,生铁含硫量也就高于这些厂家。
高炉热风炉脱硫技术

高炉热风炉脱硫技术高炉热风炉脱硫技术在高炉热风炉中,脱硫是一项关键的技术,旨在降低炉渣中的硫含量,提高高炉冶炼的效率和产品质量。
在过去的几十年里,随着环境保护意识的增强和相关法规的出台,高炉热风炉脱硫技术得到了广泛的关注和研究。
本文将深入探讨高炉热风炉脱硫技术的多个方面,帮助读者更全面、深入地了解这一技术。
我们来了解高炉热风炉脱硫技术的基本原理。
高炉热风炉脱硫主要依靠在高温下进行的化学反应来实现。
一般来说,高炉热风炉中的炉渣中含有一定量的硫,而硫在钢铁冶炼过程中是一个有害元素,会导致钢铁的质量下降。
减少炉渣中的硫含量就成为高炉操作的一个重要目标。
在脱硫过程中,通常会添加一定的脱硫剂,如石灰石、白云石等,来与炉渣中的硫发生反应,生成易挥发的硫化物,通过炉顶排放出高炉系统,从而达到脱硫的目的。
我们来详细了解高炉热风炉脱硫技术中的一些关键问题和解决方案。
首先是脱硫剂的选择。
不同的脱硫剂具有不同的特性,对脱硫效果、炉渣性能等方面都有一定的影响。
在选择脱硫剂时需要考虑到多个因素,如脱硫效果、成本、对炉渣性能的影响等。
其次是脱硫剂的添加方式和时机。
脱硫剂的添加方式可以影响到脱硫效果和炉渣性能,因此需要在实际操作中综合考虑。
另外,脱硫剂的添加时机也是一个关键问题。
在高炉操作中,不同的时期添加脱硫剂会对脱硫效果产生不同的影响,因此需要根据具体情况进行调整。
还有一些其他关键问题,如脱硫剂的用量、炉温控制等,在实际操作中也需要注意。
除了关键问题和解决方案,我们还需要了解高炉热风炉脱硫技术的发展现状和趋势。
随着环境法规的逐渐严格,高炉热风炉脱硫技术也在不断发展和改进。
目前,已经有一些新的脱硫技术得到了应用,如湿法脱硫、氧气富氧脱硫等。
这些新技术不仅能够更好地降低炉渣中的硫含量,还能够减少能源消耗,提高冶炼效率。
一些新的脱硫剂也被引入到高炉热风炉脱硫技术中,以提高脱硫效果和降低成本。
总结回顾一下,高炉热风炉脱硫技术是高炉冶炼过程中的一个关键环节,对提高钢铁质量和保护环境都起到了重要作用。
浅析粉煤气化灰渣综合利用
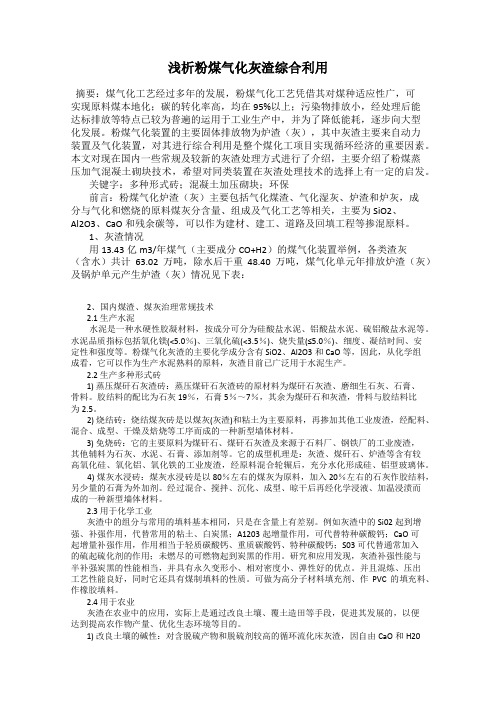
浅析粉煤气化灰渣综合利用摘要:煤气化工艺经过多年的发展,粉煤气化工艺凭借其对煤种适应性广,可实现原料煤本地化;碳的转化率高,均在95%以上;污染物排放小,经处理后能达标排放等特点已较为普遍的运用于工业生产中,并为了降低能耗,逐步向大型化发展。
粉煤气化装置的主要固体排放物为炉渣(灰),其中灰渣主要来自动力装置及气化装置,对其进行综合利用是整个煤化工项目实现循环经济的重要因素。
本文对现在国内一些常规及较新的灰渣处理方式进行了介绍,主要介绍了粉煤蒸压加气混凝土砌块技术,希望对同类装置在灰渣处理技术的选择上有一定的启发。
关键字:多种形式砖;混凝土加压砌块;环保前言:粉煤气化炉渣(灰)主要包括气化煤渣、气化湿灰、炉渣和炉灰,成分与气化和燃烧的原料煤灰分含量、组成及气化工艺等相关,主要为SiO2、Al2O3、CaO和残余碳等,可以作为建材、建工、道路及回填工程等掺混原料。
1、灰渣情况用13.43亿m3/年煤气(主要成分CO+H2)的煤气化装置举例,各类渣灰(含水)共计63.02万吨,除水后干重48.40万吨,煤气化单元年排放炉渣(灰)及锅炉单元产生炉渣(灰)情况见下表:2、国内煤渣、煤灰治理常规技术2.1 生产水泥水泥是一种水硬性胶凝材料,按成分可分为硅酸盐水泥、铝酸盐水泥、硫铝酸盐水泥等。
水泥品质指标包括氧化镁(<5.0%)、三氧化硫(<3.5%)、烧失量(≤5.0%)、细度、凝结时间、安定性和强度等。
粉煤气化灰渣的主要化学成分含有SiO2、Al2O3和CaO等,因此,从化学组成看,它可以作为生产水泥熟料的原料,灰渣目前已广泛用于水泥生产。
2.2 生产多种形式砖1) 蒸压煤矸石灰渣砖:蒸压煤矸石灰渣砖的原材料为煤矸石灰渣、磨细生石灰、石膏、骨料。
胶结料的配比为石灰19%,石膏5%~7%,其余为煤矸石和灰渣,骨料与胶结料比为2.5。
2) 烧结砖:烧结煤灰砖是以煤灰(灰渣)和粘土为主要原料,再掺加其他工业废渣,经配料、混合、成型、干燥及焙烧等工序而成的一种新型墙体材料。
浅析铸铁中硫的功能与控制

浅析铸铁中硫的功能与控制发表时间:2019-11-26T15:34:37.537Z 来源:《中国西部科技》2019年第21期作者:陈宇[导读] 目前,我国的科技发展十分迅速,硫在铁液中主要以自由硫、化合硫和硫夹杂物的形式存在。
本文分析了铸铁中硫的三种存在形式和它们之间的平衡关系,总结了自由硫的表面活性功能、硫化反应功能和抑制吸氮功能对铸铁组织性能的影响。
结合生产实际,汇总了目前硫含量的测定方法和常用增硫脱硫措施,为铸铁中硫的合理控制提供了指导方向。
陈宇广东肇庆动力金属股份有限公司摘要:目前,我国的科技发展十分迅速,硫在铁液中主要以自由硫、化合硫和硫夹杂物的形式存在。
本文分析了铸铁中硫的三种存在形式和它们之间的平衡关系,总结了自由硫的表面活性功能、硫化反应功能和抑制吸氮功能对铸铁组织性能的影响。
结合生产实际,汇总了目前硫含量的测定方法和常用增硫脱硫措施,为铸铁中硫的合理控制提供了指导方向。
关键词:铸铁;硫;增硫剂;脱硫剂引言铸铁具有耐磨、高强度等特点,被广泛应用于纺织、汽车、电力、家电、造船及国防等行业,其在生产实践中的广泛应用,其产品质量直接影响到下游产品的质量和性能。
铸铁碳硫专用标准样品,是具有足够的均匀性和很好的确定了化学成份的物质,它作为成份分析的实物标准,对于验证化学分析方法的可靠性,提高化学成份分析的准确性都有着重要的作用和意义,被广泛应用于测量的质量保证、产品的质量管理、测量方法的评价以及相关法规的科学制定与有效实施。
1影响硫含量的因素1.1炉料因素炉料中废钢配入量越多,铁水增硫率越高。
原因有二。
一是废钢在一定条件下更容易产生铁水,即使其本身的含硫量较低,但在炉内熔化的位置较低时,结合其自身熔点高的特性,加上废钢中碳、硅含量低而产生化学反应,产生较多Fe0,从而加剧了增硫。
二是铁水中含有碳、硅以及锰等元素。
其中,碳和硅能使Fe0还原,从而有助于炉内进行脱硫反应。
然而,锰作用更大,在其特殊性能下能直接引起脱硫反应。
球墨铸铁中硫的影响_来源及含硫量的控制
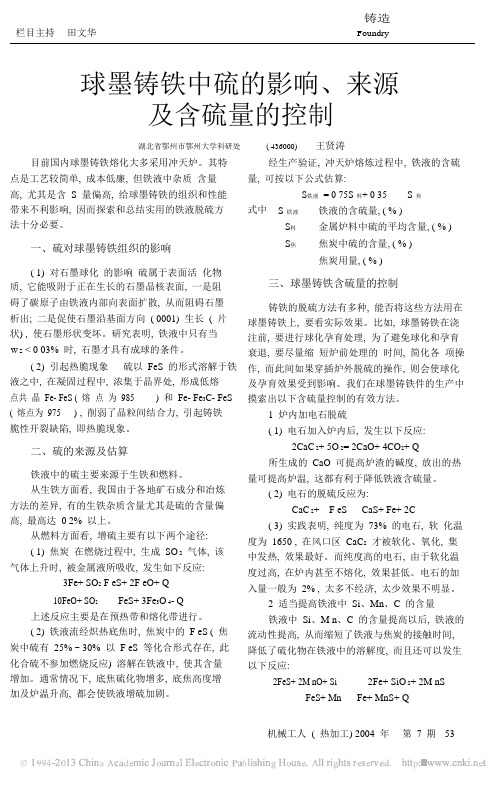
铸造栏目主持田文华Foundry球墨铸铁中硫的影响、来源及含硫量的控制湖北省鄂州市鄂州大学科研处( 436000) 王贤涛目前国内球墨铸铁熔化大多采用冲天炉。
其特点是工艺较简单, 成本低廉, 但铁液中杂质含量经生产验证, 冲天炉熔炼过程中, 铁液的含硫量, 可按以下公式估算:高, 尤其是含S 量偏高, 给球墨铸铁的组织和性能S铁液= 0 75S料+ 0 35 S焦带来不利影响, 因而探索和总结实用的铁液脱硫方法十分必要。
一、硫对球墨铸铁组织的影响式中S铁液S料S焦铁液的含硫量, ( % )金属炉料中硫的平均含量, ( % )焦炭中硫的含量, ( % )焦炭用量, ( % )( 1) 对石墨球化的影响硫属于表面活化物质, 它能吸附于正在生长的石墨晶核表面, 一是阻碍了碳原子由铁液内部向表面扩散, 从而阻碍石墨析出; 二是促使石墨沿基面方向( 0001) 生长( 片状) , 使石墨形状变坏。
研究表明, 铁液中只有当w S < 0 03% 时, 石墨才具有成球的条件。
三、球墨铸铁含硫量的控制铸铁的脱硫方法有多种, 能否将这些方法用在球墨铸铁上, 要看实际效果。
比如, 球墨铸铁在浇注前, 要进行球化孕育处理, 为了避免球化和孕育衰退, 要尽量缩短炉前处理的时间, 简化各项操( 2) 引起热脆现象硫以FeS 的形式溶解于铁作, 而此间如果穿插炉外脱硫的操作, 则会使球化液之中, 在凝固过程中, 浓集于晶界处, 形成低熔及孕育效果受到影响。
我们在球墨铸铁件的生产中点共晶Fe- FeS ( 熔点为985 ) 和Fe- Fe3C- FeS 摸索出以下含硫量控制的有效方法。
( 熔点为975 ) , 削弱了晶粒间结合力, 引起铸铁 1 炉内加电石脱硫脆性开裂缺陷, 即热脆现象。
二、硫的来源及估算铁液中的硫主要来源于生铁和燃料。
从生铁方面看, 我国由于各地矿石成分和冶炼方法的差异, 有的生铁杂质含量尤其是硫的含量偏高, 最高达0 2% 以上。
【热坛讨论】关于球铁原铁水含硫量过低对铸件影响问题

【热坛讨论】关于球铁原铁水含硫量过低对铸件影响问题
【热坛讨论】关于球铁原铁水含硫量过低对铸件影响问题
坛友xyzhlan提出:球铁原铁水含硫量过低对铸件有何影响,如果原铁水含硫量在0.007~0.008%之间,球化处理后,铁水会有哪方面影响,请有这方面经验的人讲讲。
【以下摘录部分坛友参与讨论的回复】
坛友辉精英:这方面,国外研究的比较多,国内研究的很少,主要还是原材料的不同,据挪威技术人员介绍:硫过低会造成形核困难,不易球化,且孕育效果也差。
坛友KAKAKAKA:硫不仅会降低碳在铁水中的溶解度,促进石墨的析出,而且硫和锰反应促进形核。
坛友hedazhuzao:形核能力肯定较差,加硫氧孕育剂会好些,原则上冲天炉加升温炉的双联熔炼的材质更好。
坛友yelei051:我最近也遇到这种问题了,QT700-2,最近几次配料较少量生铁(20%),生铁的硫含量0.015%,其余全废钢,没用回炉料,原铁水S含量在0.012左右,球化处理后S含量在0.006-0.009,球化率一直很差(普遍3-4级),石墨球偏大(5-6级)。
最近几次我在炉内加了一点硫铁,使原铁水S含量0.018-0.020,球化完成后S为0.011。
这几次的球化率普遍好了不少,达不到2级但比3级要好,石墨球明显变小,球大小7级。