Tactile sensor hardware based on programmable SoC
传感器的原理及其应用解读

气敏(嗅觉)传感器
概述: 气味检测是半导体气敏传感器扩大应用的主流方向之一,最有潜力的应 用领域是食品工业和医学,还有家住环境和舒适度的调节系统等。在 开发味敏传感器方面取得的主要成就是在改进提高敏感材料的灵敏度 和选择性方面,针对气味的特征成分,使用了各种掺杂剂,以适应不 同的需要。 应用: 常见的有酒精浓度传感器。 此外,在有些场合还需要分别鉴别出混合气体中的各个成分。
文本 文本 文本
Understanding of sensor:
The sensor is a detection device, can feel the measured information, and can feel the information, according to the law must transform into electric signal or other required information in the form of output, in order to satisfy the information transmission, processing, storage, display, record and control requirements. It is the most important link for realizing automatic detection and automatic control.
触觉传感器
介绍: 将压力转换为电信号输出的传感器。通常把压力测量仪表中的电测式仪 表称为压力传感器。 应用:称重传感器、霍尔传感器。 称重传感器采用金属电阻应变片组成测量桥路,利用金属电阻丝在 张力作用下伸长变细,电阻增加的原理,即金属电阻随所受应变而变 化的效应而制成的(应变,就是尺寸的变化)。 在现代化工业生产以及自动化生产过程中,需要用到各种称重传感器来 监视和控制生产过程中的各个参数,称重传感器的功能是使设备工作 在正常状态或最佳状态,并使生产出来的产品达到最好的质量。可以 说,没有众多的优良的称重传感器,现代化生产也就失去了基础。如 此看来,称重传感器将在这个智能化生产产业中是会有美好的发展前 途。治理超重。
74HC1G14和74HCT1G14高速Si-gate CMOS非门IC数据手册说明书

1. General description74HC1G14 and 74HCT1G14 are high-speed Si-gate CMOS devices. They provide aninverting buffer function with Schmitt trigger action. These devices are capable oftransforming slowly changing input signals into sharply defined, jitter-free output signals.The HC device has CMOS input switching levels and supply voltage range 2 V to 6 V.The HCT device has TTL input switching levels and supply voltage range 4.5 V to 5.5 V.The standard output currents are half of those of the 74HC14 and 74HCT14.2. Features and benefits⏹Symmetrical output impedance ⏹High noise immunity ⏹Low power dissipation⏹Balanced propagation delays⏹SOT353-1 and SOT753 package options ⏹Specified from -40 ︒C to +125 ︒C3. Applications⏹Wave and pulse shapers ⏹Astable multivibrators ⏹Monostable multivibrators4. Ordering information74HC1G14; 74HCT1G14Inverting Schmitt triggerRev. 6 — 27 December 2012Product data sheetTable 1.Ordering informationType numberPackageTemperature rangeName DescriptionVersion 74HC1G14GW -40 ︒C to +125 ︒CTSSOP5plastic thin shrink small outline package;5leads; body width 1.25mmSOT353-174HCT1G14GW 74HC1G14GV -40 ︒C to +125 ︒CSC-74Aplastic surface-mounted package; 5 leadsSOT75374HCT1G14GV5. MarkingTable 2.Marking codesType number Marking code[1]74HC1G14GW HF74HCT1G14GW TF74HC1G14GV H1474HCT1G14GV T14[1]The pin 1 indicator is located on the lower left corner of the device, below the marking code.6. Functional diagram7. Pinning information7.1Pinning7.2Pin descriptionTable 3.Pin descriptionSymbol Pin Descriptionn.c.1not connectedA2data inputGND3ground (0 V)Y4data outputV CC5supply voltage8. Functional descriptionTable 4.Function tableH = HIGH voltage level; L = LOW voltage levelInput OutputA YL HH L9. Limiting valuesTable 5.Limiting valuesIn accordance with the Absolute Maximum Rating System (IEC 60134). Voltages are referenced to GND (ground = 0 V). [1] Symbol Parameter Conditions Min Max UnitV CC supply voltage-0.5+7.0VI IK input clamping current V I <-0.5V or V I>V CC+ 0.5V-±20mAI OK output clamping current V O<-0.5V or V O>V CC+ 0.5V-±20mAI O output current-0.5 V < V O<V CC+0.5V-±12.5mAI CC supply current-25mAI GND ground current-25-mAT stg storage temperature-65+150︒CP tot total power dissipation T amb = -40︒C to+125 ︒C[2]-200mW[1]The input and output voltage ratings may be exceeded if the input and output current ratings are observed.[2]Above 55︒C, the value of P tot derates linearly with 2.5mW/K.10. Recommended operating conditionsTable 6.Recommended operating conditionsVoltages are referenced to GND (ground = 0 V).Symbol Parameter Conditions74HC1G1474HCT1G14UnitMin Typ Max Min Typ MaxV CC supply voltage 2.0 5.0 6.0 4.5 5.0 5.5VV I input voltage0-V CC0-V CC VV O output voltage0-V CC0-V CC VT amb ambient temperature-40+25+125-40+25+125︒C11. Static characteristicsTable 7.Static characteristicsVoltages are referenced to GND (ground = 0 V). All typical values are measured at T amb=25︒C.Symbol Parameter Conditions-40︒C to+85 ︒C-40︒C to+125 ︒C UnitMin Typ Max Min MaxFor type 74HC1G14V OH HIGH-level outputvoltage V I= V T+ or V T-I O= -20μA; V CC=2.0V 1.9 2.0- 1.9-V I O= -20μA; V CC=4.5V 4.4 4.5- 4.4-V I O= -20μA; V CC=6.0V 5.9 6.0- 5.9-V I O= -2.0mA; V CC=4.5V 4.13 4.32- 3.7-V I O= -2.6mA; V CC=6.0V 5.63 5.81- 5.2-VV OL LOW-level outputvoltage V I= V T+ or V T-I O= 20μA; V CC=2.0V-00.1-0.1V I O= 20μA; V CC=4.5V-00.1-0.1V I O= 20μA; V CC=6.0V-00.1-0.1V I O= 2.0mA; V CC=4.5V-0.150.33-0.4V I O= 2.6mA; V CC=6.0V-0.160.33-0.4VI I input leakage current V I=V CC or GND; V CC=6.0V-- 1.0- 1.0μA I CC supply current V I=V CC or GND; I O=0A;V CC=6.0V--10-20μA C I input capacitance- 1.5---pFV T+positive-goingthreshold voltage see Figure7 and Figure8V CC=2.0 V0.7 1.09 1.50.7 1.5V V CC=4.5 V 1.7 2.36 3.15 1.7 3.15V V CC=6.0 V 2.1 3.12 4.2 2.1 4.2VV T-negative-goingthreshold voltage see Figure7 and Figure8V CC=2.0 V0.30.600.90.30.9V V CC=4.5 V0.9 1.53 2.00.9 2.0V V CC=6.0 V 1.2 2.08 2.6 1.2 2.6VV H hysteresis voltage see Figure7 and Figure8V CC=2.0 V0.20.48 1.00.2 1.0VV CC=4.5 V0.40.83 1.40.4 1.4VV CC=6.0 V0.6 1.04 1.60.6 1.6V For type 74HCT1G14V OH HIGH-level outputvoltage V I= V T+ or V T-I O= -20μA; V CC=4.5V 4.4 4.5- 4.4-V I O= -2.0mA; V CC=4.5V 4.13 4.32- 3.7-VV OL LOW-level outputvoltage V I= V T+ or V T-I O= 20μA; V CC=4.5V-00.1-0.1V I O= 2.0mA; V CC=4.5V-0.150.33-0.4VI I input leakage current V I=V CC or GND; V CC=5.5V-- 1.0- 1.0μA12. Dynamic characteristics[1]t pd is the same as t PLH and t PHL .[2]C PD is used to determine the dynamic power dissipation P D (μW).P D =C PD ⨯V CC 2⨯f i +∑(C L ⨯V CC 2⨯f o )where:f i =input frequency in MHz; f o =output frequency in MHz C L =output load capacitance in pF; V CC =supply voltage in Volts ∑(C L ⨯V CC 2⨯f o ) = sum of outputsI CC supply current V I =V CC or GND; I O =0A; V CC =5.5V--10-20μA ∆I CC additional supply currentper input; V CC =4.5V to 5.5V; V I = V CC - 2.1 V; I O =0A--500-850μA C I input capacitance - 1.5---pF V T+positive-going threshold voltagesee Figure 7 and Figure 8V CC =4.5 V 1.2 1.55 1.9 1.2 1.9V V CC =5.5 V1.41.802.11.42.1VV T -negative-going threshold voltagesee Figure 7 and Figure 8V CC =4.5 V 0.50.76 1.20.5 1.2V V CC =5.5 V0.60.901.40.61.4VV Hhysteresis voltagesee Figure 7 and Figure 8V CC =4.5 V 0.40.80-0.4-V V CC =5.5 V0.40.90-0.4-VTable 7.Static characteristics …continuedVoltages are referenced to GND (ground = 0 V). All typical values are measured at T amb =25︒C.Symbol Parameter Conditions-40︒C to +85 ︒C -40︒C to +125 ︒C UnitMin Typ Max Min Max Table 8.Dynamic characteristicsGND = 0 V; t r = t f ≤ 6.0 ns; All typical values are measured at T amb =25︒C. For test circuit see Figure 6Symbol Parameter Conditions -40︒C to +85 ︒C -40︒C to +125 ︒C Unit MinTyp MaxMinMaxFor type 74HC1G14t pdpropagation delay A to Y; see Figure 5[1]V CC = 2.0 V; C L =50pF -25155-190ns V CC = 4.5 V; C L =50pF -1231-38ns V CC = 5.0 V; C L =15pF -10---ns V CC = 6.0 V; C L =50pF-1126-32ns C PDpower dissipation capacitanceV I =GND to V CC [2]-20---pFFor type 74HCT1G14t pdpropagation delay A to Y; see Figure 5[1]V CC = 4.5 V; C L =50pF -1743-51ns V CC = 5.0 V; C L =15pF-15---ns C PDpower dissipation capacitanceV I =GND to V CC -1.5V [2]-22---pF13. WaveformsTable 9.Measurement pointsType number Input OutputV I V M V M74HC1G14GND to V CC0.5 ⨯ V CC0.5 ⨯ V CC 74HCT1G14GND to 3.0 V 1.5 V0.5 ⨯ V CC14. Transfer characteristics waveforms15. Application informationThe slow input rise and fall times cause additional power dissipation, this can becalculated using the following formula:P add=f i⨯(t r⨯∆I CC(AV)+t f⨯∆I CC(AV))⨯V CCWhere:P add=additional power dissipation (μW)f i=input frequency (MHz)t r=rise time (ns); 10% to 90%t f=fall time (ns); 90% to 10%∆I CC(AV)=average additional supply current (μA)∆I CC(AV) differs with positive or negative input transitions, as shown in Figure14 and Figure15.74HC1G14 and 74HCT1G14 used in relaxation oscillator circuit, see Figure16. Remark: All values given are typical unless otherwise specified.16. Package outlineTSSOP5: plastic thin shrink small outline package; 5 leads; body width 1.25 mm SOT353-1Fig 18.Package outline SOT353-1 (TSSOP5)Plastic surface-mounted package; 5 leads SOT753Fig 19.Package outline SOT753 (SC-74A)17. Abbreviations18. Revision historyTable 10.AbbreviationsAcronym Description DUT Device Under Test TTLTransistor-Transistor LogicTable 11.Revision historyDocument ID Release date Data sheet status Change notice Supersedes 74HC_HCT1G14 v.620121227Product data sheet -74HC_HCT1G14 v.5Modifications:•Table 3: Pin number Y output changed from 5 to 4 (errata).74HC_HCT1G14 v.520120924Product data sheet-74HC_HCT1G14 v.4Modifications:•Figure 17 added (typical K-factor for relaxation oscillator).•Legal page updated.74HC_HCT1G14 v.420070717Product data sheet -74HC_HCT1G14 v.374HC_HCT1G14 v.320020515Product specification -74HC_HCT1G14 v.274HC_HCT1G14 v.220010302Product specification -74HC_HCT1G14 v.174HC_HCT1G14 v.119980805Product specification--19. Legal information19.1 Data sheet status[1]Please consult the most recently issued document before initiating or completing a design.[2]The term ‘short data sheet’ is explained in section “Definitions”.[3]The product status of device(s) described in this document may have changed since this document was published and may differ in case of multiple devices. The latest product statusinformation is available on the Internet at URL .19.2 DefinitionsDraft — The document is a draft version only. The content is still under internal review and subject to formal approval, which may result in modifications or additions. Nexperia does not give anyrepresentations or warranties as to the accuracy or completeness of information included herein and shall have no liability for the consequences of use of such information.Short data sheet — A short data sheet is an extract from a full data sheet with the same product type number(s) and title. A short data sheet is intended for quick reference only and should not be relied upon to contain detailed and full information. For detailed and full information see the relevant full data sheet, which is available on request via the local Nexperia salesoffice. In case of any inconsistency or conflict with the short data sheet, the full data sheet shall prevail.Product specification — The information and data provided in a Product data sheet shall define the specification of the product as agreed between Nexperia and its customer, unless Nexperia andcustomer have explicitly agreed otherwise in writing. In no event however, shall an agreement be valid in which the Nexperia product isdeemed to offer functions and qualities beyond those described in the Product data sheet.19.3 DisclaimersLimited warranty and liability — Information in this document is believed to be accurate and reliable. However, Nexperia does not give any representations or warranties, expressed or implied, as to the accuracy or completeness of such information and shall have no liability for the consequences of use of such information. Nexperia takes noresponsibility for the content in this document if provided by an information source outside of Nexperia.In no event shall Nexperia be liable for any indirect, incidental,punitive, special or consequential damages (including - without limitation - lost profits, lost savings, business interruption, costs related to the removal or replacement of any products or rework charges) whether or not such damages are based on tort (including negligence), warranty, breach of contract or any other legal theory.Notwithstanding any damages that customer might incur for any reason whatsoever, Nexperia’s aggregate and cumulative liability towards customer for the products described herein shall be limited in accordance with the Terms and conditions of commercial sale of Nexperia.Right to make changes — Nexperia reserves the right to makechanges to information published in this document, including without limitation specifications and product descriptions, at any time and without notice. This document supersedes and replaces all information supplied prior to the publication hereof.Suitability for use — Nexperia products are not designed,authorized or warranted to be suitable for use in life support, life-critical or safety-critical systems or equipment, nor in applications where failure or malfunction of a Nexperia product can reasonably be expectedto result in personal injury, death or severe property or environmental damage. Nexperia and its suppliers accept no liability forinclusion and/or use of Nexperia products in such equipment or applications and therefore such inclusion and/or use is at the customer’s own risk.Applications — Applications that are described herein for any of these products are for illustrative purposes only. Nexperia makes no representation or warranty that such applications will be suitable for the specified use without further testing or modification.Customers are responsible for the design and operation of their applications and products using Nexperia products, and Nexperiaaccepts no liability for any assistance with applications or customer product design. It is customer’s sole responsibility to determine whether the Nexperia product is suitable and fit for the customer’s applications andproducts planned, as well as for the planned application and use of customer’s third party customer(s). Customers should provide appropriate design and operating safeguards to minimize the risks associated with their applications and products.Nexperia does not accept any liability related to any default,damage, costs or problem which is based on any weakness or default in the customer’s applications or products, or the application or use by customer’s third party customer(s). Customer is responsible for doing all necessary testing for the customer’s applications and products using Nexperia products in order to avoid a default of the applications andthe products or of the application or use by customer’s third partycustomer(s). Nexperia does not accept any liability in this respect.Limiting values — Stress above one or more limiting values (as defined in the Absolute Maximum Ratings System of IEC60134) will cause permanent damage to the device. Limiting values are stress ratings only and (proper) operation of the device at these or any other conditions above those given in the Recommended operating conditions section (if present) or the Characteristics sections of this document is not warranted. Constant or repeated exposure to limiting values will permanently and irreversibly affect the quality and reliability of the device.Terms and conditions of commercial sale — Nexperiaproducts are sold subject to the general terms and conditions of commercial sale, as published at /profile/terms, unless otherwise agreed in a valid written individual agreement. In case an individual agreement is concluded only the terms and conditions of the respective agreement shall apply. Nexperia hereby expressly objects toapplying the customer’s general terms and conditions with regard to the purchase of Nexperia products by customer.No offer to sell or license — Nothing in this document may be interpreted or construed as an offer to sell products that is open for acceptance or the grant, conveyance or implication of any license under any copyrights, patents or other industrial or intellectual property rights.Document status[1][2]Product status[3]DefinitionObjective [short] data sheet Development This document contains data from the objective specification for product development. Preliminary [short] data sheet Qualification This document contains data from the preliminary specification.Product [short] data sheet Production This document contains the product specification.Export control — This document as well as the item(s) described herein may be subject to export control regulations. Export might require a prior authorization from competent authorities.Non-automotive qualified products — Unless this data sheet expressly states that this specific Nexperia product is automotive qualified,the product is not suitable for automotive use. It is neither qualified nor tested in accordance with automotive testing or application requirements. Nexperia accepts no liability for inclusion and/or use ofnon-automotive qualified products in automotive equipment or applications. In the event that customer uses the product for design-in and use in automotive applications to automotive specifications and standards, customer (a) shall use the product without Nexperia’s warranty of theproduct for such automotive applications, use and specifications, and (b) whenever customer uses the product for automotive applications beyond Nexperia’s specifications such use shall be solely at customer’sown risk, and (c) customer fully indemnifies Nexperia for anyliability, damages or failed product claims resulting from customer design and use of the product for automotive applications beyond Nexperia’sstandard warranty and Nexperia’s product specifications.Translations — A non-English (translated) version of a document is for reference only. The English version shall prevail in case of any discrepancy between the translated and English versions.19.4 TrademarksNotice: All referenced brands, product names, service names and trademarks are the property of their respective owners.20. Contact informationFor more information, please visit: For sales office addresses, please send an email to: ***************************21. Contents1 General description. . . . . . . . . . . . . . . . . . . . . . 12 Features and benefits . . . . . . . . . . . . . . . . . . . . 13 Applications. . . . . . . . . . . . . . . . . . . . . . . . . . . . 14 Ordering information. . . . . . . . . . . . . . . . . . . . . 15 Marking. . . . . . . . . . . . . . . . . . . . . . . . . . . . . . . . 26 Functional diagram . . . . . . . . . . . . . . . . . . . . . . 27 Pinning information. . . . . . . . . . . . . . . . . . . . . . 27.1 Pinning . . . . . . . . . . . . . . . . . . . . . . . . . . . . . . . 27.2 Pin description . . . . . . . . . . . . . . . . . . . . . . . . . 28 Functional description . . . . . . . . . . . . . . . . . . . 39 Limiting values. . . . . . . . . . . . . . . . . . . . . . . . . . 310 Recommended operating conditions. . . . . . . . 311 Static characteristics. . . . . . . . . . . . . . . . . . . . . 412 Dynamic characteristics . . . . . . . . . . . . . . . . . . 513 Waveforms . . . . . . . . . . . . . . . . . . . . . . . . . . . . . 614 Transfer characteristics waveforms. . . . . . . . . 715 Application information. . . . . . . . . . . . . . . . . . . 816 Package outline . . . . . . . . . . . . . . . . . . . . . . . . 1117 Abbreviations. . . . . . . . . . . . . . . . . . . . . . . . . . 1318 Revision history. . . . . . . . . . . . . . . . . . . . . . . . 1319 Legal information. . . . . . . . . . . . . . . . . . . . . . . 1419.1 Data sheet status . . . . . . . . . . . . . . . . . . . . . . 1419.2 Definitions. . . . . . . . . . . . . . . . . . . . . . . . . . . . 1419.3 Disclaimers. . . . . . . . . . . . . . . . . . . . . . . . . . . 1419.4 Trademarks. . . . . . . . . . . . . . . . . . . . . . . . . . . 1520 Contact information. . . . . . . . . . . . . . . . . . . . . 1521 Contents . . . . . . . . . . . . . . . . . . . . . . . . . . . . . . 16© Nexperia B.V. 2017. All rights reserved For more information, please visit: Forsalesofficeaddresses,pleasesendanemailto:*************************** Date of release:Mouser ElectronicsAuthorized DistributorClick to View Pricing, Inventory, Delivery & Lifecycle Information:N experia:74HC1G14GV,12574HC1G14GW,12574HC1G14GW,16574HCT1G14GV,12574HCT1G14GW,125。
高灵敏度传感器实现动作识别满足消费电子市场需求

高灵敏度传感器实现动作识别满足消费电子市场需求
彭湃
【期刊名称】《电子技术应用》
【年(卷),期】2007(33)6
【摘要】飞思卡尔半导体在微机电系统(MEMS)传感器设备设计制造领域具有全球领先的地位,通过推出高灵敏度的XYZ三轴加速计,可满足当今智能移动设备领域日益增长的移动感应需求。
从MP3播放器到PDA,再到超小的笔记本电脑,如今的消费者正在越来越多地通过其使用的便携式电子设备的种类以及对这些设备的定制来彰显自己的个性。
便携式设备的设计人员也在不断寻找新途径,以便在不增加设备尺寸的情况下,让.产品具有更大的显示屏和更多的新功能。
设计人员还试图结合移动感应技术以保护易碎的电子组件安全,生产出更加稳定可靠的便携式设备。
【总页数】2页(P17-18)
【作者】彭湃
【作者单位】飞思卡尔半导体中国有限公司,上海分公司,上海,201203
【正文语种】中文
【相关文献】
1.高灵敏度传感器实现动作识别,满足消费电子市场需求 [J],
2.高灵敏度传感器实现动作识别满足消费电子市场需求 [J], 彭湃
3.高灵敏度传感器实现动作识别,满足消费电子市场需求 [J], 飞思卡尔半导体公司
4.高灵敏度传感器实现动作识别满足消费电子市场需求 [J], 飞思卡尔公司
5.高灵敏度传感器实现动作识别,满足消费电子市场需求 [J], 飞思卡尔半导体公司因版权原因,仅展示原文概要,查看原文内容请购买。
意法半导体推出业界首款可同时支持用户接口和手抖补偿功能的角速度传感器

意法半导体推出业界首款可同时支持用户接口和手抖补偿功能
的角速度传感器
佚名
【期刊名称】《《传感器世界》》
【年(卷),期】2012(018)001
【摘要】意法半导体(STMieroelectronics)最新推出了一款数字输出3轴角速度(陀螺仪)传感器L3G41S,可同时支持用户接口功能和手抖补偿功能。
新产品只配备了一个MEMS三轴角速度传感器,通过相关信号电路,可同时支持用户接口功能和手抖补偿功能。
【总页数】1页(P34-34)
【正文语种】中文
【中图分类】TP212
【相关文献】
1.意法半导体(ST)推出世界首款基于 ARM Cortex-M7的STM32 F7系列微控制器 [J],
2.意法半导体(ST)推出世界首款3轴汽车陀螺仪 [J],
3.意法半导体(ST)与FIME携手推出业界首款兼容全球支付标准的Calypso交通卡 [J],
4.意法半导体推出世界首款3轴汽车陀螺仪 [J],
5.意法半导体(ST)推出业界首款高符号率卫星解调器,实现更快速、更经济的宽带服[J],
因版权原因,仅展示原文概要,查看原文内容请购买。
基于EIT技术的柔性触觉传感器的设计

基于EIT技术的柔性触觉传感器的设计程文芳;王晓杰;董帅【摘要】随着机器人技术的日益发展,柔性传感器在机器人皮肤上的应用也得到了新的发展。
本文提出并研究了一种基于导电聚合物压敏电阻效应的柔性触觉传感器的设计,使用由聚二甲基硅氧烷PDMS(Poly Di Methyl Siloxane)和多壁碳纳米管(MWCNTs)混合而成的导电橡胶作为传感器主体,运用EIT(Electrical Impedance Tomography)技术,设计并制作了本系统的硬件电路,并用其检测、传输导电橡胶的边缘电势数据。
最后在计算机中应用工具包EIDORS进行有限元模型和图像重构技术,有效且直观的将导电橡胶上的受力位置表现出来。
实验对1~3个目标分别进行了成像,证明了本设计的可行性。
%The rapid development of robot technology has led to new applications of soft sensors for robotic sensitive skin. In this paper we present a study on the design of flexible tactile sensor based on the piezoresitivity of a new conductive polymer which has been developed by ourselves. The conductive polymer is made by blending PDMS (polydimethylsiloxane,polydimethylsiloxane)with a small amount of multi-walled carbon nanotubes(MWCNTs) which has a high sensitivity in resistance-pressure response. The Electrical Impedance Tomography(EIT)is used to create the flexible tactile sensor. The peripheral hardware circuits based on EIT are designed and manufactured. The data obtained from hardware circuits is processed by computer. The finite element modeling and image recon⁃structue has been performed with a toolkit calledEIDORS. The experiment has been carried out to successfully identify the positions of the targets in 1~3 goals when touching on the sensor surface.【期刊名称】《传感技术学报》【年(卷),期】2016(029)002【总页数】6页(P155-160)【关键词】柔性触觉传感器;EIT;导电橡胶;EIDORS【作者】程文芳;王晓杰;董帅【作者单位】中国科学技术大学自动化系,合肥230027; 中国科学院合肥物质科学研究院先进制造技术研究所,江苏常州213164;中国科学院合肥物质科学研究院先进制造技术研究所,江苏常州213164;中国科学技术大学自动化系,合肥230027; 中国科学院合肥物质科学研究院先进制造技术研究所,江苏常州213164【正文语种】中文【中图分类】TP212.1随着传感器技术的不断发展,适用于机器人“皮肤”的柔性触觉传感系统引起了人们的广泛关注。
2.45 GHz 与5.8 GHz 双频柔性天线的设计

2.45 GHz 与5.8 GHz 双频柔性天线的设计许德成;郭小辉;田小建;刘微;高永慧【摘要】We gave topology and preparation process of a 2.45 GHz and 5.8 GHz flexible wearable monopole dual-band antenna based on polydimethylsiloxane (PDMS)flexible substrate and organo-silicone conductive silver adhesive.The structure of the flexible dual-band antenna was optimized and the performances of the antenna were characterized.The results show that the experimental results are in good agreement with simulation results.The return losses of the dual-band antenna at the center frequency of 2.45 GHz and 5.8 GHz are -26 dB and -28 dB,respectively.%基于聚二甲基硅氧烷(PDMS)柔性基体和有机硅导电银胶,给出柔性双频微带天线的拓扑结构及制备2.45 GHz 与5.8 GHz 柔性可穿戴单极子双频天线流程,并优化天线结构,对天线性能进行实测表征.结果表明,仿真与实测结果基本一致,双频天线在中心频率2.45 GHz 和5.8 GHz 处的回波损耗分别为-26 dB 和-28 dB.【期刊名称】《吉林大学学报(理学版)》【年(卷),期】2016(054)006【总页数】5页(P1413-1417)【关键词】柔性天线;双频;可穿戴;导电银胶;聚二甲基硅氧烷(PDMS)【作者】许德成;郭小辉;田小建;刘微;高永慧【作者单位】吉林大学电子科学与工程学院,长春 130012; 吉林师范大学信息技术学院,吉林四平 136000;合肥工业大学电子科学与应用物理学院,合肥230009;吉林大学电子科学与工程学院,长春 130012;吉林师范大学信息技术学院,吉林四平 136000;吉林师范大学信息技术学院,吉林四平 136000【正文语种】中文【中图分类】TN82随着无线通信技术和可穿戴传感技术的快速发展,使人体中心无线网络逐渐成为一种新兴产业[1],可穿戴电子设备在医疗监护[2-3]、军事[4]、体育训练[5-6]等领域应用广泛. 柔性可穿戴天线是一种可集成于人体衣物中的天线类型,具有低剖面、便于携带以及易于共形等特点. 导电织物[7]、纳米打印[8-9]、石墨烯[10]等材料已应用于新型天线的设计与研究中. 文献[11]基于毛毡和铜箔提出了一种能与服装完全共形的柔性微带天线,经测试验证可满足穿戴系统无线通信的需求,但铜箔与基体之间不易实现紧密黏接,且在穿戴过程中经反复折叠易出现裂纹等弊端. 文献[12]利用三维织物制备出一种可灵活集成于衣物的柔性可穿戴四元天线阵,由于天线辐射贴片与接地面均采用导电织物,因此其表面较粗糙且交叉结构导致电阻率降低,天线增益存在较大损耗.无线局域网(WLAN)因其低成本、网络组建灵活以及扩展能力强等优势,在无线通信领域中应用广泛. 为进一步提升天线辐射贴片和接地平面的电导率,满足可穿戴设备无线通信的需求,本文基于有机硅导电银胶和聚二甲基硅氧烷(PDMS)柔性基体设计并制备一种2.45 GHz和5.8 GHz的双频微带柔性可穿戴天线. 以有机硅导电银胶为辐射贴片/接地平面,PDMS为柔性基体,通过3D打印技术及流体成型技术,即可制备满足WLAN通信系统的要求.1.1 天线结构设计微带天线具有体积小、低剖面、结构紧凑以及易于集成等优点[13-16],为满足可穿戴无线通信系统对柔性天线的需求,本文基于有机硅导电银胶和PDMS柔性基体研制一种新型柔性天线,即2.45 GHz和5.8 GHz双频微带柔性可穿戴天线,其拓扑结构如图1所示,其中柔性介质基体PDMS购于美国道康宁Sylgard®184公司,其介电常数εr=2.65,损耗角tan δ=0.02,位于PDMS基体两面作为辐射贴片和接地平面的有机硅导电银胶YC-02购于南京喜力特胶黏剂有限公司.根据天线中心频率与介质属性估算1/4波长单极子天线的长度,并通过高频结构仿真软件(HFSS)对双频天线结构进行优化,其优化的天线尺寸参数见图1.1.2 柔性天线制备柔性双频微带天线的制备流程如图2所示. 基于3D打印技术和流体成型技术,首先,利用3D打印机(Replicator 2X型,精度100 μm,美国Makerbot公司)制备所需天线模具,将YC-02有机硅橡胶按固定比例均匀搅拌后注入辐射贴片凹槽内固化成型. 其次,将PDMS按固化比例用磁力搅拌机(FDWTC-D型,上海复旦天欣科教仪器有限公司)均匀搅拌后注入柔性基体模具,并于真空干燥箱(DZF-6021型,上海索普仪器有限公司)中抽真空,除去PDMS搅拌时混入的气泡,固化后脱模成型. 接地平面的制备方法类似,将接地平面与PDMS基地底面组装即可获得柔性双频微带天线样品,通过环氧型导电银胶(YC-01,南京喜力特胶黏剂有限公司)将SMA插座与馈电面连接以备天线性能表征.柔性可穿戴双频微带天线的实物如图3所示. 由图3可见,该新型双频微带天线的柔性较好,满足穿戴舒适度的要求. 为进一步降低其电阻率,对固化后的有机硅导电银胶薄膜进行压缩处理,使得银纳米颗粒之间更紧密. 利用SU8020型场发射扫描电子显微镜(日本日立公司)与DMM-200C型金相电子显微镜(上海蔡康光学仪器有限公司)表征有机硅导电银胶,并用4200-SCS型半导体特征分析系统(美国吉时利公司)测试其I-V特性. 结果分别如图4和图5所示.由图4可见,有机硅导电银胶固化后的表面较平滑,且各导电银颗粒之间均匀连接,在物理结构层面为高导电性提供了条件. 由图5可见,I-V特性曲线具有较好的重复性,其电阻率为10-4~10-3 Ω·mm.利用电磁仿真软件(HFSS)对柔性双频微带天线进行性能仿真优化,并制备天线样品,使用矢量网络分析仪(ZNB8型,德国Rohde & Schwarz公司)测试双频天线的特性. 柔性双频微带天线的回波损耗仿真与实测结果如图6所示. 由图6可见,在中心频率2.45 GHz和5.8 GHz处的回波损耗分别为-26 dB和-28 dB,满足工程要求.柔性双频微带天线驻波比的仿真与实测对比结果如图7所示. 由图7可见,在中心频率2.45 GHz和5.8 GHz处的电压驻波比(SWR)分别为1.5和1.8,仿真值均低于1.2,经参数优化后达到良好的阻抗匹配效果. 为进一步验证双频微带天线在弯曲状态下仍可满足通信要求,建立柔性双频微带天线弯曲状态下的仿真模型,选取弯曲半径R=40 mm,分别沿x轴和y轴弯曲,其回波损耗仿真结果如图8所示. 由图8可见,当柔性双频微带天线沿x轴(y轴)弯曲时,其中频频率会沿低频方向发生轻微偏移,但仍能满足工程应用需求.天线方向图是表征天线辐射特性与空间角度关系的图形[17],为验证柔性双频微带可穿戴天线在2.45 GHz和5.8 GHz中心频率的辐射特性,利用图9中所示的暗室对该柔性双频微带可穿戴天线进行远场参数测试,每隔1°由天线测试系统记录一次. 图10为2.45 GHz和5.8 GHz柔性天线的仿真与实测辐射方向图. 由图10可见,其xz与yz平面的方向图仿真结果与实测结果基本一致.综上,本文分别以PDMS和有机硅导电银胶为柔性基体与导电辐射贴片,给出了2.45 GHz与5.8 GHz柔性可穿戴双频天线的拓扑结构及优化后的尺寸参数,并基于3D打印技术制备了柔性双频天线. 通过对天线性能进行实测表征,分析了弯曲状态下回波损耗的变化特点. 结果表明,在中心频率2.45 GHz和5.8 GHz处的回波损耗分别为-26 dB和-28 dB,其驻波比、辐射方向图与仿真结果基本一致.【相关文献】[1] Kamardin K,Rahim M K A,Hall P S,et al. Planar Textile Antennas with Artificial Magnetic Conductor for Body-Centric Communications [J]. Applied Physics A,2016,122(4): 363-371.[2] Nadeem A,Hussain M A,Owais O,et al. Application Specific Study,Analysis and Classification of Body Area Wireless Sensor Network Applications [J]. Computer Networks,2015,83(4): 363-380.[3] Bharadwaj R,Parini C,Alomainy A. Experimental Investigation of 3-D Human Body Localization Using Wearable Ultra-wideband Antennas [J]. IEEE Transactions on Antennas & Propagation,2015,63(11): 5035-5044.[4] Singh N,Singh A K,Singh V K. Design and Performance of Wearable Ultrawide Band Textile Antenna for Medical Applications [J]. Microwave & Optical Technology Letters,2015,57(7): 1553-1557.[5] GUO Xiaohui,HUANG Ying,CAI Xia,et al. Capacitive Wearable Tactile Sensor Based on Smart Textile Substrate with Carbon Black/Silicone Rubber Composite Dielectric [J]. Measurement Science & Technology,2016,27(4): 045105.[6] 郭小辉,黄英,毛磊东,等. 可穿戴式电子织物仿生皮肤设计与应用研究 [J]. 仪器仪表学报,2016,37(4): 938-944. (GUO Xiaohui,HUANG Ying,MAO Leidong,et al. Research on the Design and Application of Wearable Electronic Fabric Bionic Skin [J]. Chinese Journal of Scientific Instrument,2016,37(4): 938-944.)[7] Zeng W,Shu L,Li Q,et al. Fiber-Based Wearable Electronics: A Review ofMaterials,Fabrication,Devices,and Applications [J]. Advanced Materials,2014,26(31): 5310-5336.[8] Song L,Myers A C,Adams J J,et al. Stretchable and Reversibly Deformable Radio Frequency Antennas Based on Silver Nanowires [J]. Acs Applied Materials & Interfaces,2014,6(6): 4248-4253.[9] Su M,Li F,Chen S,et al. Nanoparticle Based Curve Arrays for Multirecognition Flexible Electronics [J]. Advanced Materials,2015,28(7): 1369-1374.[10] Huang X,Leng T,Zhang X,et al. Binder-Free Highly Conductive Graphene Laminate for Low Cost Printed Radio Frequency Applications [J]. Applied Physics Letters,2015,106(20): 203105.[11] 程春霞,张福顺. 柔性微带天线设计与研究 [J]. 微波学报,2014,30(4): 25-28. (CHENG Chunxia,ZHANG Fushun. Design and Research of Flexible Microstrip Patch Antenna [J]. Journal of Microwaves,2014,30(4): 25-28.)[12] 杨福慧,杜成珠. 基于三维织物的四元阵纺织天线 [J]. 电子元件与材料,2014,33(7): 52-54. (YANG Fuhui,DU Chengzhu. Textile Microstrip Four-Element Array Antenna Integrated in Three Dimensional Orthogonal Woven Fabrics [J]. Electronic Components and Materials,2014,33(7): 52-54.)[13] 严冬,汪朋,李帅永,等. 2.45 GHz印刷倒F天线的研究与实现 [J]. 仪器仪表学报,2015,36(10): 2372-2380. (YAN Dong,WANG Peng,LI Shuaiyong,et al. Research and Realization of 2.45 GHz Printed Inverted-F Antenna [J]. Chinese Journal of Scientific Instrument,2015,36(10): 2372-2380.)[14] Chen Y Y,Lin E C,Chen S H,et al. A Flexible Dual-Band Monopole Antenna [J]. International Journal of Advances in Engineering & Technology,2015,8(3): 272-280. [15] Pinapati S P,Kaufmann T,Ranasinghe D C,et al. Wearable Dual-Band Stripline-Fed Half-Mode Substrate-Integrated Cavity Antenna [J]. Electronics Letters,2016,52(6): 424-426.[16] Hamouda Z,Wojkiewicz J L,Pud A A,et al. Dual-Band Elliptical Planar Conductive Polymer Antenna Printed on a Flexible Substrate [J]. IEEE Transactions on Antennas & Propagation,2015,63(12): 5864-5867.[17] Kamyshny A,Magdassi S. Conductive Nanomaterials for Printed Electronics [J]. Small,2014,10(17): 3515-3535.。
飞思卡尔高能效三轴加速度传感器推进消费电子动作传感技术

特 性
◆ 1 2位数 字输 出
MMA 4 0 加速 度 传感 器 是针 对 下 一代 移 动设 备 ( 85Q 如 智 能 手机 和智 能 本 ) 计 的 , 要 求 性 能 、 携 性 和 电池 寿 设 这 便 命 进行 理想 组 合 才 能满 足市 场 需求 。这款 三轴 数 字传 感 器
缓 存 的配 合 使 用 , 终 端 处 理 器 仅 对 要 求 的数 据 进 行 分 使 析; 另外 , 相 同 I 总 线 上 复 用其 他 传 感 器 时 , 有 助 于 在 C 这
电机 系 统 ( MS ME )市 场将 从 2 0 年 的 5 亿 美 元 增 长 到 06 6
8 3亿 美 元 。据 该 公 司 的 调 查 结 果 显 示 , 0 1年 只 有 3 20 的手 机采 用 了加 速 度 传 感 器 , 于 ME 由 MS技 术 的 发 展 以 及 消 费 者对 增 强 型 用 户界 面 的需 求 , 2 1 到 0 0年 , 数 字 预 该
MMA8 5 Q 传 感 器 是 1 40 2位 的 数 字 解 决 方 案 , 用 采 3mm×3mm×lmm 小 体 积 封 装 。 它提 供 智 能 的 数 据 管 理 功 能 ,内 置 3 2段 采 样/ ( Y、 轴 )的 先 入 先 出 轴 X、 Z ( I O)内存 缓 冲 , FF 以提 高 整个 系统 的省 电能 力 , 通 过 减 并 轻 主处 理 器 负 载 来 加 快 响 应 速 度 。嵌 入 式 功 能 和 F F IO
一
双击 、 敲击 、 自由落 体 及震 动检 测 能 力 。
一
作模 式下 ,2 20 A) 4 ~ 5
一
典 型值为 2 A O R 0Hz 低功耗模式) 7 ( D =5 , 典型值为 4 A O R 0 , 2 ( D =10Hz 正常工作模
TACTILE SENSOR

专利名称:TACTILE SENSOR发明人:KURIYAMA TOSHIHIDE 申请号:JP2029384申请日:19840207公开号:JPS60164367A公开日:19850827专利内容由知识产权出版社提供摘要:PURPOSE:To produce a robot hand sensor accurately measuring fluctuation of pressures at low frequency or constant pressures as well as their distribution upon contact surface by a method wherein a piezo-electric body and an insulating gate type field effect transistor are fixed on a base oscillating in the direction perpendicular to their surfaces. CONSTITUTION:A tactile sensor is composed of an oscillating base 1, a p type silicon substrate 2, a high concentration n type silicon source region 3, a high concentration n type silicon drain region 4, insulators 5, a source electrode 6, a gate electrode 7, a drain electrode 8 etc. while a gate electrode 9 is electrically insulated from all elements other than a piezo-electric body 10. When a conventional supersonic wave sensor made of a piezo-electric body and an insulating gate type field effect transistor is fixed on a robot hand as a tactile sensor, the response characteristics to an object is that output is rapidly decreased by time lapse entirely out of proportion to the pressure. On the other hand, this tactile sensor oscillating itself can alternately fluctuate the pressure per object. The alternate amplitude of drain current of the insulating gate type FET may be made accurately proportional to the pressure by means of setting up the oscillating cycle of this sensor sufficiently shorter than the polarization attenuation time of piezo-electric body.申请人:NIPPON DENKI KK 更多信息请下载全文后查看。
剪切式压电加速度传感器工作原理

剪切式压电加速度传感器工作原理The working principle of a shear-type piezoelectric accelerometer involves the use of the piezoelectric effect to convert mechanical motion into an electrical signal. 剪切式压电加速度传感器的工作原理涉及使用压电效应将机械运动转换为电信号。
When the sensor is subjected to an acceleration, mass within the sensor is displaced relative to the housing, causing the piezoelectric material to generate a charge. 当传感器受到加速度作用时,传感器内的质量相对于外壳发生位移,使压电材料产生电荷。
This charge is then measured by external circuitry and can be used to quantify the acceleration. 这个电荷然后被外部电路测量,并可用于量化加速度。
The basic construction of a shear-type piezoelectric accelerometer includes a seismic mass, a support spring, a housing, and a piezoelectric material. 剪切式压电加速度传感器的基本结构包括一个地震质量、支持弹簧、外壳和压电材料。
When subjected to acceleration, the seismic mass is displaced, causing the support spring to deflect, which induces a shear strain in the piezoelectric material. 当受到加速度作用时,地震质量发生位移,导致支持弹簧变形,从而在压电材料中诱导剪切应变。
面向汗液的可穿戴柔性电化学传感器研究进展

第 2 期第 78-91 页材料工程Vol.52Feb. 2024Journal of Materials EngineeringNo.2pp.78-91第 52 卷2024 年 2 月面向汗液的可穿戴柔性电化学传感器研究进展Research progress of wearable flexibleelectrochemical sensors for sweat陈晨,李嘉夕,聂磊*(湖北工业大学机械工程学院现代制造质量工程湖北省重点实验室,武汉 430068)CHEN Chen,LI Jiaxi,NIE Lei*(Hubei Key Laboratory of Modern Manufacturing QualityEngineering,School of Mechanical Engineering,HubeiUniversity of Technology,Wuhan 430068,China)摘要:汗液中含有人体诸多生理信息,如电解质、代谢物、激素、温度等。
基于汗液的可穿戴式传感器可对多模态生物指标实现分子层面上的实时、连续、非侵入式监测,在运动感知、疾病预防以及健康管理等领域具有重大发展潜力,而被广泛研究。
本文阐述了可穿戴汗液传感器集成结构中基底、集汗、传感、电源和决策五大模块,着重强调了纳米结构(如金属基、碳基等材料)在电化学传感敏感材料中表现出的优异性能及应用,最后讨论了可穿戴汗液传感器在微量汗液收集及多参数传感中物理化学变量的可变性等方面存在的挑战。
针对汗液收集和实时校准两个关键问题,提出可穿戴汗液传感未来发展方向包括仿生微流控技术和多参数反馈调控方法,实现微量汗液高效收集及精确检测,将有效推动汗液传感在慢性重大疾病实时预警的应用和发展。
关键词:汗液传感器;可穿戴;电化学;纳米结构;柔性;集成结构doi:10.11868/j.issn.1001-4381.2022.001025中图分类号:TP212.2 文献标识码:A 文章编号:1001-4381(2024)02-0078-14Abstract:Sweat contains many physiological information about the body, such as electrolytes, metabolites,hormones,temperature,etc.Sweat-based wearable sensors enable real-time,continuous,non-invasive monitoring of multimodal bio-metrics at the molecular level,and are widely studied for their significant potential in areas such as motion sensing,disease prevention,and health management.This paper described the five modules of substrate,sweat collection,sensing,power supply and decision making in the integrated structure of wearable sweat sensors,highlighted the excellent performance and applications of nanostructures (such as metal-based and carbon-based materials)in electrochemical sensing sensitive materials, and finally discussed the challenges of wearable sweat sensors in terms of trace sweat collection and variability of physicochemical variables in multi-parameter sensing,meanwhile,future directions of wearable sweat sensing are proposed for two key problems of sweat collection and real-time calibration,including bionic microfluidics and multi-parameter feedback regulation methods to achieve efficient collection and accurate detection of microscopic sweat,promote the application and development of real-time early warning of sweat sensing for chronic major diseases.Key words:sweat sensor;wearable;electrochemistry;nanostructure;flexibility;integrated structure汗液作为实时健康监测的重要生物流体,携带大量传递人体生理信息的物质,如代谢物(葡萄糖、乳酸)、电解质(Na+,Cl-,K+)、激素(皮质醇、多巴胺(DA))等[1]。
OPTICAL TACTILE SENSOR

专利名称:OPTICAL TACTILE SENSOR发明人:TACHI, Susumu,KAJIMOTO, Hiroyuki 申请号:EP01961195.3申请日:20010830公开号:EP1321753B1公开日:20080917专利内容由知识产权出版社提供摘要:The invention relates to a tactile sensor capable of obtaining information for a plurality of degrees of freedom at each point on a surface by introducing multi-channel sensing that uses color or optical spectrum to an optical tactile sensor. An optical tactile sensor is provided with a tactile section and imaging means, the tactile section comprising a transparent elastic body and a plurality of groups of markers provided inside the elastic body, each marker group being made up of a number of colored markers, with markers making up different marker groups having different colors for each group, and behavior of the colored markers when an object touches the elastic body being photographed by the imaging means. Preferably; the marker groups have mutually different spatial arrangements.申请人:TOUDAI TLO LTD地址:JP国籍:JP代理机构:Ebner von Eschenbach, Jennifer更多信息请下载全文后查看。
外文翻译--传感器技术的新进展
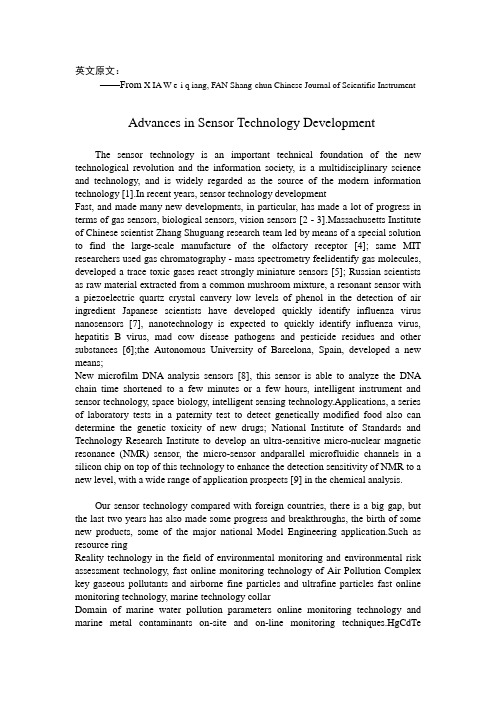
英文原文:——From X IA W e-i q iang, FAN Shang-chun Chinese Journal of Scientific Instrument Advances in Sensor Technology Development The sensor technology is an important technical foundation of the new technological revolution and the information society, is a multidisciplinary science and technology, and is widely regarded as the source of the modern information technology [1].In recent years, sensor technology developmentFast, and made many new developments, in particular, has made a lot of progress in terms of gas sensors, biological sensors, vision sensors [2 - 3].Massachusetts Institute of Chinese scientist Zhang Shuguang research team led by means of a special solution to find the large-scale manufacture of the olfactory receptor [4]; same MIT researchers used gas chromatography - mass spectrometry feelidentify gas molecules, developed a trace toxic gases react strongly miniature sensors [5]; Russian scientists as raw material extracted from a common mushroom mixture, a resonant sensor with a piezoelectric quartz crystal canvery low levels of phenol in the detection of air ingredient Japanese scientists have developed quickly identify influenza virus nanosensors [7], nanotechnology is expected to quickly identify influenza virus, hepatitis B virus, mad cow disease pathogens and pesticide residues and other substances [6];the Autonomous University of Barcelona, Spain, developed a new means;New microfilm DNA analysis sensors [8], this sensor is able to analyze the DNA chain time shortened to a few minutes or a few hours, intelligent instrument and sensor technology, space biology, intelligent sensing technology.Applications, a series of laboratory tests in a paternity test to detect genetically modified food also can determine the genetic toxicity of new drugs; National Institute of Standards and Technology Research Institute to develop an ultra-sensitive micro-nuclear magnetic resonance (NMR) sensor, the micro-sensor andparallel microfluidic channels in a silicon chip on top of this technology to enhance the detection sensitivity of NMR to a new level, with a wide range of application prospects [9] in the chemical analysis.Our sensor technology compared with foreign countries, there is a big gap, but the last two years has also made some progress and breakthroughs, the birth of some new products, some of the major national Model Engineering application.Such as resource ringReality technology in the field of environmental monitoring and environmental risk assessment technology, fast online monitoring technology of Air Pollution Complex key gaseous pollutants and airborne fine particles and ultrafine particles fast online monitoring technology, marine technology collarDomain of marine water pollution parameters online monitoring technology and marine metal contaminants on-site and on-line monitoring techniques.HgCdTeinfrared sensors have been used in China's Fengyun series satellites, oceanic satellites and Shenzhou series flyShip.Beijing University of Aeronautics and Astronautics invented the small precision CMOS celestial sensor technology won the 2008 National Invention and Technology Prize [10].The development of these technologies highlights sensor technology showing toThe high-precision, miniaturization, micro-power consumption and passive, intelligent, high reliability direction of the trend, the following were discussed.The main direction of development of sensor technology to the development of high-precisionAutomated production technology continues to evolve, the requirements of the sensor is also continuously improve the requirements developed with high sensitivity, high accuracy, fast response speed, good interchangeability new sensor to ensure the reliability of production automation.In recent years, the world's major the sensor research institutions using new theories, new methods, new techniques to improve the sensor accuracy achieved outstanding results.American scholars have found a new method to improve the sensitivity of the sensor [11], to take a systematic approach to the various design rules together with a consistent framework to improve the design of the sensor.They compared the traditional planar sensor (p lanar sensor) components with cylindrical single nanotube sensor (cylindrica l sing le-nano tube sensor)Components, the results show the smaller cylindrical sensitivity of the sensor is at least 100 times higher, which is sufficient to prove that the smaller the better the theoretical.University of California at Berkeley and the Berkeley Lab researchers create the world's first fully functional nanotube device, the successful construction of a weighing gold atoms nanoelectromechanical systems (NEMS) [12].This device measured the gold atoms quality for 3125 @ 10 - 22 g.The NEMS mass sensor consists of a single carbon nanotube, double wall, with all the electronic properties, and the increase in hardness.The one end of the carbon nanotubes can be freely, while the other end is connected to one electrode, and the distance relative to the electrode is very near.The DC power from the battery or solar cell on the pair of electrodes connected, cause it to some fluctuations in the resonance frequency of vibration.When an atom or molecule is stored above carbon nanotubes, the resonant frequency of this carbon nanotube will therefore the mass of the atoms or molecules to change, similar to the different weight diver would change the resonance frequency of the diving board.American Oak R idge National Laboratory using silicon micro-electromechanical systems (MEMS) sensor detected 515 fg (femtograms) of the substances, and to create a new world record [13].The use of only 2 Lm Length, 50 nm thick silicon cantilever, by an inexpensive diode laser vibration.The researchers believe that the use of MEMS sensors in theory be able to detect any substances.British the Transense company launched a precision level millionth non-contacttorque sensor Torqsense [14].This sensor is based on the principle of surface acoustic wave (SAW), the size of only 4 mm @ 2 mm @ 015 mm.45b fixed for measuring the torque of the shaft, the two SAW sensor and the shaft was continuously into / half-bridge 0 structure; When the shaft is subject to torque, a pressure receiving a tensile the consolidated two sensors frequency generating / Difference 0 or /superposition 0 signal to derive the respective torque or temperature signal.Epson Toyocom Corporation developed a? 10 Pa (about one ten thousandth atmospheric pressure) of high accuracy and high resolution of 011 Pa and a volume of 1215 ml, weight is 15 g small crystal absolute pressure sensor [15].Tuning-fork type crystal unit is used in the pressure detecting unit, whereby the oscillation frequency of high stability can be obtained, thus achieving the pressure sensor with high precision and high resolution crystal; on top of this using QMEMS technology developed a new original.pressure sensing structure, to make it possible to have both small and high performance.Taiyo Yuden developed a detection sensitivity of 10 @ - 9 (1ppb) gas sensor [16], because of its gas adsorption characteristics, Taiyo Yuden be called / of nanoscale gas sensor 0, and in October 2007show opening / CEATEC JAPAN 20070.The sensor 80Lm @ 500Lm dielectric film is formed on a silicon wafer, using a dielectric film after the adsorbed gas, the resistance value change of the dielectric film, in order to detect the gas.112 development to the miniaturization of various control equipment function more and more, the requirements of the various components of smaller is better, and thus the sensor itself, the volume is as small as possible, which requires a focus on the development of micro-sensors based on new materials and processing technology.French scientist, winner of the 2007 Nobel Prize in Physics Albert # Fil German scientist Peter # Green Berger found / giant magnetoresistance 0 effect [17 - 19], not only can produce more sensitive data read headThe increasingly weak magnetic signals and still be able to be clearly read out and converted into a clear current change.The breakthrough in the technology provides an extremely important technical support for the miniaturization of sensors.Hitachi Metals has developed the world's smallest 3-axis acceleration sensor, external dimensions of 215mm @ 215 mm _AT_ 1mm volume of 6125 mm3 to varistor resin package.The package size smaller than similar products by 30% the volume and weight of 14 mg, 46% lower than similar products, with more than 20,000 gravitational acceleration impact resistance.Japanese scientists have also successfully developed the world's smallest ultra-sensitive tactile sensor, the prospects for a wide range of applications in the field of medical devices.The sensor is embedded in the synthetic resin of approximately 011mm3 a diameter of 1 ~ 10 Lm, long of 300 ~~ 500 Lm, the helical spring-like fine carbon coil element, carbon coil after the contact with the object, will be minor changes in pressure and temperature conversioninto electrical signals.Furthermore, the sensor can also sense / screwed 0, / 0, etc. of friction signal.113 micro-power consumption and passive sensor can not work without power, in the field or in a place far from the grid, often with a battery or solar power, the development of micro-powersensor and passive sensor is an inevitable development direction,In this way, you can saveEnergy and can improve the life of the system.German scientists have developed a sensor, the energy of the fluid (liquid or gas) can have through their own conversion into electricity, which means that the sensor can own / power generation 0, which would greatly facilitate the design and maintenance of the system.The conversion process is carried out in a fixed cavity into electricity, the media fluid (liquid or gas) through the heart as blood flows through here like.Due to the Coanda effect, the flow of fluid is close to the conduit wall; continuous flow generated here periodic pressure fluctuations, to the piezoelectric ceramics, piezoelectric ceramic ultimately by the energy of the fluid is converted into electrical conduction by the feedback member.Generated electricity in the microwatt or milliwatt able to meet the energy demand of the loop running sensor to ensure the sensor reading and outgoing data.British Perpetuum and CAP-XX, Australia developed without battery driven wireless sensor terminal The terminal is equipped with a micro vibration can be converted to energy generators and double-layer capacitor.The vibration of the installation site can be used as energy, power generation, the surplus electric power can be stored in the electric double layer capacitor [23].114 to the intelligent development of increasingly complex with the development of science and technology, the function of the sensor.Its output is no longer a single analog signal, but after the microprocessor processing the digital signal, and some even with a control function.Technology development that the digital signal processor (DSP) will promote the development of many new next-generation products.The technology laboratory R & D of the San Jose Accen ture one is called / 0 of smart dust smart sensing system can automatically monitor and leaf-like objects combustion warning.Once the smart dust sensor point will be near each small dust sprayed into the trees, dust to locate and establish a wireless connection.When spotted possible anomalies detected, it will touch the the nearby dust size device to determine their access to information, and get multiple information from multiple sources, then the sensor will be able to judge a tree dangerous.Once the danger trigger sensor group through its wireless connection to send messages to woodland workers to monitor the sensor network.Ok i recently introduced ultra-small triaxial accelerometer module the ML8950, integrated sensor chip and control IC, the world's thinnest package.Has detected a triaxial accelerometer function can also detect tilt and impact shocks.The controlling IC chip is fitted in the signal amplifying circuit, a control circuit, analog-to-digital converter, and temperature compensation circuit.Furthermore, it is the first with a digital interface triaxial accelerometer module, because it can be directly connected to the CPU, so without the use of analog to digital signal converter device can be embedded in the digital device.115 directly affects the reliability of the sensor to the high reliability electronic device antijamming performance, the development of high reliability, the wide temperaturerange of the sensor will be permanent direction.Improve the temperature range has always been a major issue in the scope of its work, most sensors are - 20 ~ 70e, in the military system requirements Operating temperature - 40 ~ 85e range, while cars boiler occasions require sensor temperature requirements are higher, so the development ofpromising emerging materials (such as ceramic) sensor.Honeyw e ll launch LG1237 absolute pressure sensor is an intelligent, accurate, stable measurement of the product within the pressure range of 015 to 1000 Pa, its service life of 25 years or 100, 000 hours.Product - 55e to 125e, the accuracy rate of over? 0103% F1S1, the device will be with a piezoresistive pressure sensor connected with the DSP of the microprocessor, and can withstand the live level acceleration and vibration.Institute of Precision Engineering, Xi'an Jiaotong University successfully developed an anti-shock 2000e instantaneous ultra high temperature silicon isolated high temperature pressure sensor.The sensors in the environment - 30 ~ 250e pressure measurement, pressure measurement to be completed by the of 1000MPa any of the following range, and can withstand the high temperature of 2000e instantaneous impact, to meet the high-temperature, high-pressure, high-frequency response and instantaneous temperature impact and other harsh environmentspressure measurement.The sensor is an effective solution to the technical problems of sensor failure pressure measurement and instantaneous temperature impact in the field of China's aerospace, petrochemical, automotive and other high-temperature environment.The development of biosensorsIn recent years, with the development of biotechnology, bio-sensor has also been a lot of development.And attaches great importance to the food industry, environmental monitoring, fermentation industry, medicine and a wide range of applications, such as for the detection of food ingredients, food additives, harmful toxins and food freshness [28 - 31].Environmental pollutants, continuous, rapid, on-line monitoring of foreign subcellular lipids fixed made of cellulose acetate membrane and oxygen electrode amperometric biosensor detection of acid rain acid mist sample solution.Widely used microbial sensors take advantage of this electrochemical sensors can be of the number of microbial cells as an effective measurement tool, a continuous, on-line determination of the cell concentration in the fermentation industry.Microbial sensor is not only used in clinical medicine, and is also used in military medicine, through timely and rapid detection of bacteria, viruses, and biological weapons defense.The past two years, China has invested in biosensor research on a lot of manpower and resources, made some pretty good results.For example, successfully developed / protein chip biosensor system 0 and its practical prototype provides a novel label-free protein analysis technology.The water-soluble conjugated polymer is used as a new fluorescent probes, the design of a series of conjugated polymer-based biosensor system.The use of fluorescence resonance energy transfer principle, the development of novel high sensitivity based on the conjugated polymer spent hydrogen peroxide and glucose sensing system.Conjugated through the regulation ofthe electron transfer process of the polymeric system, to achieve a sensitive detection of the nitroxide free radicals and antioxidants.117 quantum mechanics and sensor technology, the development of quantum mechanics provides a theoretical basis for the development of modern science and technology.Development of quantum effects sensitive a measurement of the quantum-sensitive devices, such as resonant tunneling diodes, quantum well lasers and quantum interference components, with high-speed (increased 1,000-fold) than the sensitive electronic devices speed, low-power (more sensitive than electronicdevices reduce energy consumption by 1000 times), efficient, highly integrated, reliable and economic advantages.Therefore, the development of nanoelectronics, may lead to a new revolution in sensor technology and sensor technology to a new stage of development.2 domestic sensor gapIn recent years, China's sensor industry has made great strides, and has formed the basis of a certain industry, but there is still a wide gap compared with developed countries. Scientific research and development behind the international level from 5 to 10 years, 10 to 15 years behind the large-scale production technology. China's chemical industry, the security monitoring sensor market, almost all foreign enterprises occupied. Sensors for military, aerospace and other purposes, the foreign country is an embargo. The level of development of the sensor behind a serious impediment to the development of China's automobile, petrochemical, aerospace and other industries. At present, China has yielded few results of independent intellectual property rights of innovative research results to industrial conversion speed is slow, inefficient, and achieved significant social and economic benefits of the project less; able to represent the national level, but also to achieve large-scale production of small enterprises, high-grade fewer products, low market share; big gap between production technology and equipment from the international level; overall in the tracking state. Sensor devices and systems the comprehensive technical level of China's independent innovation capability is low, sensitive materials, integrated design and manufacturing, industrial design, testing and calibration than backward. Gap with foreign countries mainly in: Device varieties, mainly dependent on imports of high-end products; lower level of automation, intelligent; modular, standardized, low degree of integration; poor stability, reliability is low; Low cost the market less competitive.3 countermeasures and suggestionsAccording to the current situation of the development of sensor technology at home and abroad, our gaps, combined with the needs and priorities of China's science and technology, social and economic development strategy, to give overall consideration to the sensor technology, basic research, applied basic research and applied research. Basic research is mainly focused on sensor mechanism of, from a theoretical point of view to solve a number of key technologies of sensor development, provide important theoretical basis for the study of the sensor. Application of basic research on the basis of the basic research, focusing on key technologies provide important technical support for the sensor market process transformation to the theoretical and experimental prototype. In the sensor applied research, the mainexisting, after the application of the basic research stage proved to be more reliable and mature technology into the application stage of the market-oriented products.For our future sensor development countermeasures, including the following aspects:1) the planning of the national level from the level of national development, the future direction of development of the sensor planning, the plan should focus on the development of a new type of high-precision, low power consumption, miniaturization and miniaturized sensors. Note that the combination of production, learning and research.2) between different industries sensors complement each other and promote each sensor as an information access means in different industries have different characteristics and needs. Similar sensor technology for different industries. Should support complementary advantages between the various sectors, including joint research on common technology, craftsmanship help each other, to form a common development of various industries, thus contributing to the sensorVigorously develop technology.3) vigorously promote the construction and development of the sensor research base, to develop sensor senior professionals to encourage the sensor research leading to the national laboratory, the joint ministerial key laboratories, Key Laboratory of the industry and universities Key Laboratory, the formation of a system national the sensor research base group to provide technical support for the development of the sensor. Meanwhile, laboratory and trained expertise of a number of sensors, provide important protection of personnel for the development of sensor technology research areas.4) To change from passive to active, actively develop high-performance sensor in the the sensor research process to avoid simply copying foreign technology. Sensing technology trends, to carry out a prospective study to break through the bottleneck problem, a technology with independent intellectual property rights, to break down foreignTechnological monopoly, in a place on the international.Development of new sensor new sensor, generally should include: a new principle, fill sensor Blank, biomimetic sensors and other aspects. They are interrelated. The working mechanism of the sensor is based on a variety of effects, and the law of which inspire people to further explore the sensitive functional materials with new effects and novel physical properties sensor device developed new principle, which is the development of high-performance, multi-function, important way of low-cost, miniaturized sensors. Structured sensor developed earlier matures. Complex structure type sensor, the general structure it, the volume is too large, the prices are high. Type sensors of the physical properties of roughly contrast, has many attractive advantages, coupled with past development is not enough. Countries in the world in terms of physical properties sensor invest a lot of manpower and material resources to strengthen research, thus making it a noteworthy developments. The various effects of quantum mechanics developed low sensitivity threshold sensor usedto detect weak signals, the development of one of the new trends. Integrated, multifunctional, integrated intelligent sensor includes two definitions, and one multi-element of the same functions in parallel, about a single sensing element of the same type with integrated technology are arranged on the same plane, aligned in one dimension This is the case for a linear sensor, a CCD image sensor. Another definition of integrated multi-functional integration, upcoming sensor zoom, computing, and temperature compensation, link integration, assembled into a single device. With the development of integrated technologies, various types of hybrid and monolithic integrated pressure sensors have appeared, some of them have become a commodity. Integrated piezoresistive, capacitive pressure sensor, and other types of integrated piezoresistive sensors rapid development and wide application. Sensor multifunction is one of the development. The typical example of the so-called multi-functional monolithic silicon, an American University Sensor Research and Development Center developed a multi-axis force sensor can measure three line speed, of three centrifugal acceleration (angular velocity) and three angular acceleration. The main element is mounted on one substrate by four properly designed cantilever consisting of monolithic silicon structures, 9 are correctly arranged in the respective cantilever piezoresistive sensitive components. Multifunctional not only can reduce production costs, reduce the volume, and can effectively improve the stability of the sensor, reliability and other performance indicators. Integrate a plurality of different functions of the sensing element and integrated processing and evaluation of the results of measurement of these parameters, in addition to measurement of a variety of parameters can be performed simultaneously, but also reflects the overall status of the system under test.From the above it can be seen, integrated solid-state sensor brings many new opportunities, it is also the basis of multi-functional. Combination of sensor and microprocessor, the detection function also has information processing, logical judgment, self-diagnostics, and artificial intelligence of "thinking" it is called intelligent sensors. By means of a semiconductor integrated sensor portion signal pre-processing circuit, the input and output interfaces, microprocessor production on the same chip, large-scale integrated intelligent sensor. Smart sensor is the product of the combination of sensor technology and LSI technology, its implementation will depend on the improvement and development of the sensing technology and semiconductor integrated process level. Such sensors have multi-energy, high-performance, small size, suitable for mass production and ease of use, and can say with certainty, is one of the most important direction sensor.The development of new materials, sensor materials is an important foundation of the sensor technology, sensor technology upgrades support. With the advances in materials science, sensor technology has matured, more and more of its kind, In addition to early use of semiconductor materials, ceramic materials, optical fiber, as well as the development of superconducting materials, the development of the sensor provides a material basis. For example, according to many semiconductor materials silicon substrate easy miniaturization, integration, multi-functional, intelligent, and semiconductor optical heat detectors with high sensitivity, high accuracy, non-contactsexual characteristics, the development of infrared sensors, laser sensors modern sensors, fiber optic sensors, etc.; in the sensitive material, a ceramic material, organic material quickly, different formulations can be used mixed raw material and precision deployment of chemical constituents based on, after the precision molding sintering, to obtain one or a certain types of gas-sensitive material having an identification function, is used to produce a new gas sensor. In addition, the organic polymer sensitive materials is of great concern in recent years new sensitive materials with potential applications, the sensor can be made of the thermistor, photosensitive, gas sensing, humidity, force-sensitive ion-sensitive biological Min et al. Sensor technology continues to evolve, but also to promote the development of newer materials, such as nano materials.U.S. NRC has developed a nano ZrO2 gas sensor, and control of motor vehicle exhaust emissions, cleaning up the environment effect good, relatively broad application prospects. As a result of the production of nanomaterials sensor, has a huge interface can provide a lot of gas channel, and the on-resistance is small, is conducive to the development of miniaturized sensor to the birth of more new material With the continuous advancement of science and technology . Adoption of new technology in the development of new sensors, is inseparable from the adoption of new technology. Within the meaning of the new technology is very broad, and here mainly refers to the development of emerging sensor contact a particularly close microfabrication technology. This technique, also known as micro-machining technology, With the IC process development, it is the ion beam, electron beam, molecular beam, a laser beam, and chemical etching for microelectronics processing techniques in recent years, has been the more more used in the sensor field, such as sputtering, vapor deposition, plasma etching, chemical gas deposition (CVD), epitaxy, diffusion, etching, lithography, etc., so far, a large number of sensors made by the process described above reported at home and abroad. Smart materials smart materials refers to the physical, chemical, mechanical, electrical, and other parameters of the design and control of materials, develop biological material characteristics or superior to biological material properties of artificial materials. Some people think that the material has the following functions can be called smart materials: a judgment on the environment can be adaptive function; possess self-diagnostic function; possess self-healing capabilities; function with self-reinforced (or time base). The most prominent feature of the biological material with time base function, this differential sensor characteristics and its variational sensitive.Conversely, the long-term in a particular environment and get used to this environment, the sensitivity decreased. In general, it can adjust its sensitivity to adapt to the environment. In addition to the biological material, most notably smart material is a shape memory alloy, shape memory ceramics and shape memory polymer. The smart material exploration work has just begun, I believe the near future there will be a lot of development.。
AITEK阿泰克传感器的工作原理
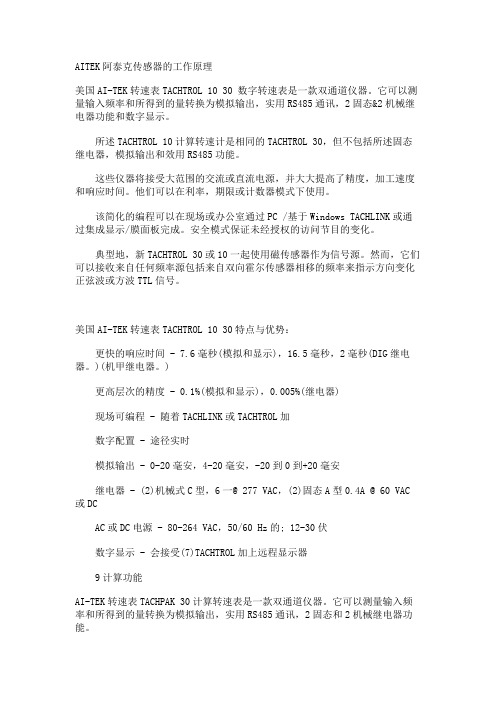
AITEK阿泰克传感器的工作原理美国AI-TEK转速表TACHTROL 10 30 数字转速表是一款双通道仪器。
它可以测量输入频率和所得到的量转换为模拟输出,实用RS485通讯,2固态&2机械继电器功能和数字显示。
所述TACHTROL 10计算转速计是相同的TACHTROL 30,但不包括所述固态继电器,模拟输出和效用RS485功能。
这些仪器将接受大范围的交流或直流电源,并大大提高了精度,加工速度和响应时间。
他们可以在利率,期限或计数器模式下使用。
该简化的编程可以在现场或办公室通过PC /基于Windows TACHLINK或通过集成显示/膜面板完成。
安全模式保证未经授权的访问节目的变化。
典型地,新TACHTROL 30或10一起使用磁传感器作为信号源。
然而,它们可以接收来自任何频率源包括来自双向霍尔传感器相移的频率来指示方向变化正弦波或方波TTL信号。
美国AI-TEK转速表TACHTROL 10 30特点与优势:更快的响应时间 - 7.6毫秒(模拟和显示),16.5毫秒,2毫秒(DIG继电器。
)(机甲继电器。
)更高层次的精度 - 0.1%(模拟和显示),0.005%(继电器)现场可编程 - 随着TACHLINK或TACHTROL加数字配置 - 途径实时模拟输出 - 0-20毫安,4-20毫安,-20到0到+20毫安继电器 - (2)机械式C型,6一@ 277 VAC,(2)固态A型0.4A @ 60 VAC 或DCAC或DC电源 - 80-264 VAC,50/60 Hz的; 12-30伏数字显示 - 会接受(7)TACHTROL加上远程显示器9计算功能AI-TEK转速表TACHPAK 30计算转速表是一款双通道仪器。
它可以测量输入频率和所得到的量转换为模拟输出,实用RS485通讯,2固态和2机械继电器功能。
所述TACHPAK 10计算速度开关是一样的TACHPAK 30,但不包括所述固态继电器,模拟输出和效用RS485功能。
惊人的机器人技术 超越人脑或不再是梦想
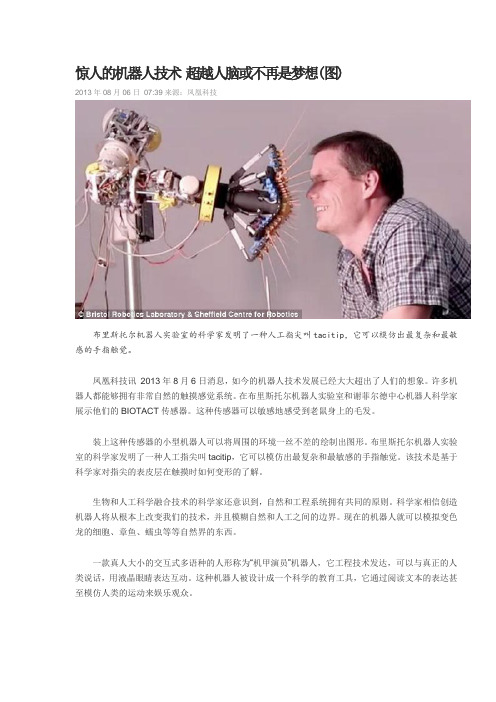
惊人的机器人技术超越人脑或不再是梦想(图)2013年08月06日07:39来源:凤凰科技布里斯托尔机器人实验室的科学家发明了一种人工指尖叫tacitip,它可以模仿出最复杂和最敏感的手指触觉。
凤凰科技讯2013年8月6日消息,如今的机器人技术发展已经大大超出了人们的想象。
许多机器人都能够拥有非常自然的触摸感觉系统。
在布里斯托尔机器人实验室和谢菲尔德中心机器人科学家展示他们的BIOTACT传感器。
这种传感器可以敏感地感受到老鼠身上的毛发。
装上这种传感器的小型机器人可以将周围的环境一丝不差的绘制出图形。
布里斯托尔机器人实验室的科学家发明了一种人工指尖叫tacitip,它可以模仿出最复杂和最敏感的手指触觉。
该技术是基于科学家对指尖的表皮层在触摸时如何变形的了解。
生物和人工科学融合技术的科学家还意识到,自然和工程系统拥有共同的原则。
科学家相信创造机器人将从根本上改变我们的技术,并且模糊自然和人工之间的边界。
现在的机器人就可以模拟变色龙的细胞、章鱼、蠕虫等等自然界的东西。
一款真人大小的交互式多语种的人形称为“机甲演员”机器人,它工程技术发达,可以与真正的人类说话,用液晶眼睛表达互动。
这种机器人被设计成一个科学的教育工具,它通过阅读文本的表达甚至模仿人类的运动来娱乐观众。
另一款称为iCub人形机器人可以伴着音乐跳舞。
它执行一个曲目的舞蹈样动作,证明了它的感知行为的学习能力。
设计这样的机器人的目在于,通过舞蹈展示其情感能力,实现与人类相互理解与互动。
康沃尔工程师威尔·杰克逊制造了一款机器人可以与观众进行互动。
有35个这样的机器人正在代替导游每天重复而沉闷的工作。
它们可以模仿和识别人类的肢体动作,并做出相应的反应。
目前,生产这样的一个机器人需要55000欧元。
(编译/韩林君)《星际迷航》心灵传送或可实现(图)2013年08月06日07:35来源:凤凰科技电影《星际迷航》里的柯克船长和斯波克船长。
凤凰科技讯北京时间8月6日消息,英国每日邮报报道,在流行的科幻电影里,心灵传送使得你能够在两地之间迅速移动。
毕业设计(论文)-基于敏感阵列的触觉传感器结构设计及仿真分析

基于敏感阵列的触觉传感器结构设计及仿真分析摘要触觉是生物体感知外部环境的重要手段,是仿生机器人研究的一个重要内容。
相比于视觉、听觉等其他感知形式,触觉能感知更多信息量,如接触力的大小、柔软性、硬度、弹性、粗糙度、温度和湿度等。
三维力触觉传感器,将在体育运动、医疗康复、机器人等领域发挥重要的作用。
本论文利用材料力学、有限元仿真、模式识别等学科的研究成果,从传感器结构设计的角度出发,研究了基于导电橡胶的三维力柔性触觉传感器的若干理论和技术问题,提出了一种新的三维力柔性触觉传感器模型。
本论文的主要研究内容如下:(1)利用有限元仿真技术,对基于二层双面节点对称交叉分布的柔性触觉阵列传感器结构进行仿真,建立传感器的三维力一电阻仿真数字模型。
(2)提出基于一种新的柔性触觉传感器N型微结构,建立相应的三维力-电阻数学模型,并利用有限元仿真进行模拟和结构优化。
该新型结构首先从结构上对三维力进行了优化,降低了原来高维、多参数传感器信号在实时、精确解耦方面的难度。
关键词:柔性触觉传感器;三维力结构设计; ANSYS仿真分析Design of The Structure Design and Simulation Analysis of Tactile Sensor Based on Sensitive ArrayAbstractTactile is an important sensing for the robots to perceive the external information,in particular,it’s an important research content of bionic robot.Cornered to the visual,auditory and other perceived forms,tactile reception can get more information:surface roughness,temperature flexibility and shape etc..Flexible three-dimensional force tactile sensor play an important role in sports,medical,rehabilitation,robotics and other study fields.This paper made full use of the scientific achievements in the fields of pattern recognition,material mechanics,finite element simulation.In the sensor structure design point of view,we studied some key theoretical and technical problems of the 3D flexible tactile sensor based on the conductive rubber.and present a new 3D force flexible tactile sensor model.The main research contents and innovations are as follows:(1)With finite element simulation,we simulated the structure of flexible tactile sensor array of two layers in symmetric cross distribution,establisheda 3D stress—resistance simulation model of the sensor.(2)Present a new flexible tactile sensor based on the N—type micro structure,established the 3D stress—resistance mathematical model,andsimulated and optimized with finite element simulation.The method decoupling the 3D stress from the structure,reduce the difficulty in decoupling of the high dimensional,multi parameter sensor signals.Keywords:Flexible tactile sensor ;3D force Structure;ANSYS Simulation目录引言......................................................................................................................... - 1 -第1章绪论.............................................................................................................. - 2 -1.1论文研究背景................................................................................................. - 2 -1.1.1研究背景.............................................................................................. - 2 -1.1.2基于敏感阵列的触觉传感器的发展趋势..................................................... - 4 -1.2 论文研究的主要内容 ...................................................................................... - 5 -1.3 论文研究的意义............................................................................................. - 5 -第2章有限元理论及超弹性模型 ................................................................................. - 6 -2.1 ANSYS有限元概述........................................................................................ - 6 -2.1.1几何模型和网络划分.............................................................................. - 6 -2.1.2多物理场.............................................................................................. - 6 -2.1.3流体动力学 .......................................................................................... - 6 -2.1.4 ANSYS工程应用.................................................................................. - 6 -2.2超弹性理论.................................................................................................... - 7 -2.2.1超弹性理论模型 .................................................................................... - 7 -2.3 传感器力学仿真方法 ...................................................................................... - 8 -第3章数学模型理论分析........................................................................................... - 9 -3.1 导电橡胶的导电机理 ...................................................................................... - 9 -3.2 并联电阻模型结构和原理.............................................................................. - 10 -3.2.1 模型结构........................................................................................... - 10 -3.3敏感单元分析............................................................................................... - 11 -3.3.1微结构............................................................................................... - 11 -3.3.2 阵列................................................................................................. - 12 -第4章ANSYS分析与结论....................................................................................... - 15 -4.1 静力学仿真 (15)4.1.1建模 (15)4.1.2ANSYS 有限元网格划分........................................................................ - 15-4.1.3 采用表面印记功能 (16)4.1.4 施加约束...........................................................................................................- 16-4.2仿真结果与分析 (17)总结与展望...............................................................................................................................-2 0-致谢................................................................................................................. - 22 -参考文献................................................................................................................. - 23 -附录B英文文献及其译文 (30)附录 B 主要参考文献的题录及摘要 (51)插图清单图1-1 传感器测试电路图 (2)图1-2 传感器示意图 (3)图1-3 装有传感器的机器手...................................................................................................4图3-1 电阻率随炭黑含量的变化图....................................................................................................9图3-2 传感器行列电阻示图. (10)图3-3 阵列的俯视图 (11)图3-3 微结构示意图 (12)图3-4 阵列示意图 (1)2图4-1 有限元模型 (1)5图4-2 网格划分.................................................................................................................. ...15图4-3 采用表面印记功能.....................................................................................................16图4-4 用fix support 约束表面.. (16)图4-5 X向受力载荷的形变图.............................................................................................17图4-6 Y向受力载荷的形变图 (18)图4-7 Z向受力载荷的形变图 (19)插表清单表2-1 材料的样品库清单 (12)表4-1 X向力受力情况对比表............................................................................................................22表4-2 Y向力受力情况对比表............................................................................................................23表4-3 Z向力受力情况对比表.. (24)引言触觉是指用分布于皮肤上的神经细胞感受来自外界的温度、湿度、压力、振动等感觉。
g-sensor原理

g-sensor原理G-Sensor原理引言:在现代科技中,G-Sensor(重力传感器)是一项非常重要的技术。
它广泛应用于智能手机、平板电脑、游戏手柄等设备中,为用户提供了许多便利。
本文将介绍G-Sensor的原理及其应用。
一、G-Sensor的原理G-Sensor是一种基于微机电系统(MEMS)技术的传感器,主要用于测量物体的加速度。
其原理是基于牛顿第二定律,即物体的加速度与作用在物体上的力成正比,方向与力的方向相同。
G-Sensor利用微机电系统中的微小质量块和微弹簧,通过检测和计算物体的加速度,来实现对物体运动状态的感知。
二、G-Sensor的工作原理G-Sensor内部包含一个微小的质量块,该质量块通过微弹簧与固定的支撑结构相连。
当物体发生加速度变化时,质量块会受到作用力,从而相对于支撑结构发生位移。
位移的大小与物体的加速度成正比,方向与加速度方向相同。
G-Sensor通过测量质量块相对于支撑结构的位移,从而确定物体的加速度。
三、G-Sensor的应用1. 重力感应:G-Sensor可以检测设备的重力方向,从而实现屏幕自动旋转。
当用户将手机横放时,G-Sensor可以感知到重力方向发生变化,然后自动调整屏幕显示方向,以保证用户的使用体验。
2. 倾斜控制:G-Sensor可以检测设备的倾斜角度,从而实现游戏手柄的倾斜控制。
在游戏中,用户可以通过倾斜手机来控制游戏角色的移动或倾斜飞机的方向,增加游戏的乐趣和交互性。
3. 步数计数:G-Sensor可以通过检测设备的振动和运动状态,实现步数的计数。
许多智能手环和智能手表都内置了G-Sensor,可以准确地记录用户的步数和运动轨迹,帮助用户进行健康管理。
4. 震动反馈:G-Sensor可以通过检测设备的振动状态,实现震动反馈功能。
手机、游戏手柄等设备可以根据G-Sensor的反馈信号,产生不同的震动效果,增强用户的触感体验。
5. 倾斜校正:G-Sensor可以用于校正设备的倾斜角度,提高设备的精确度和准确性。
- 1、下载文档前请自行甄别文档内容的完整性,平台不提供额外的编辑、内容补充、找答案等附加服务。
- 2、"仅部分预览"的文档,不可在线预览部分如存在完整性等问题,可反馈申请退款(可完整预览的文档不适用该条件!)。
- 3、如文档侵犯您的权益,请联系客服反馈,我们会尽快为您处理(人工客服工作时间:9:00-18:30)。
(Vbias ¼ 2.5 V). The latter can be obtained with a voltage regulator. Another alternative is the use of the reference Vbias generated on-chip, although one pin is dedicated to providing access to it and the number of columns is reduced by one (three with the PSoC of this Letter). The array is scanned to read the sensor data. This process sets the driving voltage of a row to zero, while the others are set to a high impedance. It takes as many steps as rows in the array, while the columns are read in parallel. Note that the voltage drop at the resistive paths in the notdriven rows is zero and they do not contribute to the output. RG = ((VS/Vbias) − 1)RS min at Fig. 1, where VS is the voltage supply (5 V) and RSmin is the minimum value of RS determined by the pressure range of our application. Another important equation is Vbias((1/Rbias) + (4/RS min)) ≤ IDRV max to guarantee that the current sunk by the row driver does not exceed the limit imposed by the PSoC (IDRVmax).
Tactile sensor hardware based on programmable SoC
F. Vidal-Verdu´, D. Bravo-Ga´lvez and O. Oballe-Peinado
This reported work focuses on the implementation of data acquisition electronics for a piezoresistive tactile sensor. It commonly involves the use of quite bulky electronics not very suitable to be housed in artificial hands, for instance. A very compact implementation because it is not based on a conventional microcontroller but on a programmable system-on-chip (SoC) is presented. This device implements analogue blocks that are not present in standard microcontrollers, so they do not have to be added as extra integrated circuits on the PCB, and a compact implementation based on a single chip plus a few electronic components is obtained.
a Output with electronics in Fig. 1 b (left) With an electronics that does not cancel interferences (right)
Conclusion: The electronics for a piezoresistive tactile sensor based on a single chip plus a few electronic components has been shown. Crosstalk cancellation and some parallelism in data acquisition are achieved by using the resources for signal conditioning on the PSoC.
A direct way to cancel this crosstalk implements one track per taxel in the array [2]. Another popular method for cancelling the interferences due to these parasitic currents is based on grounding and consists in driving the sensor in a way that the voltage drop throughout the parasitic resistive path is zero [3]. This Letter shows a sensor the circuitry of which is based on a programmable system-on-chip (PSoC). This device has analogue blocks inside. When adequately configured, these blocks allow the implementation of the strategy to cancel the crosstalk. This has been done for the sensor shown in this Letter, where a PSoC is used instead of a standard microcontroller that results in more bulky hardware [4].
Introduction: Tactile sensors are designed to be a sort of artificial skin for robots or machines with smart interfaces with humans [1]. These sensors provide an array of force measurements or pressure maps. Many sensors have been proposed, most of them based on piezoresistive, capacitive or optical principles. Piezoresistive sensors are the most popular because their simple construction results in a robust and relatively cheap sensor. On the other hand, these sensors are quite prone to error, and errors owing to drift, hysteresis, nonlinearity or crosstalk are significant. Crosstalk cancellation is a particularly relevant issue in the design of their data acquisition electronics. Crosstalk is due to parasitic current paths. These paths are commonly associated with the fact that these sensors are implemented with continuous sheets of piezoresistive materials that are shared by taxels. However, they are also caused by paths present in an architecture that addresses the sensor in rows and columns because the metal tracks that connect these rows and columns also form parasitic paths.