C620普通车床的数控化改造
普通车床数控化改造
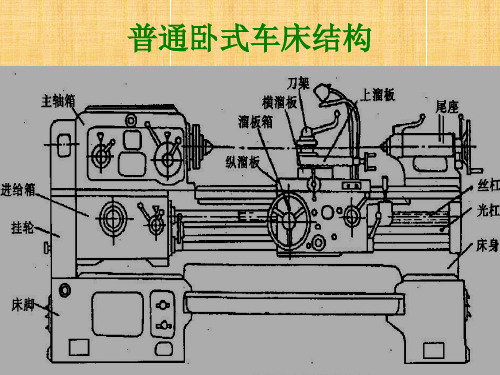
4.螺纹编码器的安装方案
螺纹编码器又称主轴脉冲发生器或 圆光栅。数控车床加工螺纹时,需 要配置主轴脉冲发生器,作为车床 主轴位置信号的反馈元件,它与车 床主轴同步转动。
1、同轴安装 同轴安装是指将编码器直接安装在主
轴后端,与主轴同轴,这种方式结构简单, 但它堵住了主轴的通孔。 2、异轴安装
异轴安装是指将编码器安装在床头箱
二、总体方案的确定
总体方案应考虑车床数控系统的运动方式、 进给伺服系统的类型、数控系统的选择,以 及进给传动方式和执行机构的选择等。
(1)普通车床数控化改造后应具有单坐标 定位,两坐标直线插补、圆弧插补以及螺纹 插补的功能。因此,数控系统应设计成连续 控制型。
(2)根据系统的功能要求,需要扩展 程序存储器、数据存储器、键盘与显示 电路、I/O接口电路、D/A转换电路、串 行接口电路等;还要选择电动机的驱动 电源以及主轴电动机的交流变频器等。 (3)为了达到技术指标中的速度和精 度要求,纵、横向的进给传动应选用摩 擦力小、传动效率高的滚珠丝杠螺母副; 为了消除传动间隙提高传动刚度,滚珠 丝杠的螺母应有预紧机构等。
(4)拆除四方刀架与上溜板总成,在横溜 板上方安装四工位立式电动刀架。 (5)拆除横溜板下的滑动丝杆螺母副,将 滑动丝杆靠刻度盘一段锯断保留,拆掉刻度 盘上的手柄,保留刻度盘附近的两个推力轴 承,换上滚珠丝杠副。 (6)将横向进给伺服电机通过法兰座安装 到横溜板后部的纵溜板上,并与滚珠丝杠的 轴头相联。 (7)拆去三杆(丝杆、光杆与操纵杆), 更换丝杆的右支承。
2.安装电动卡盘
为了提高加工效率,工件的夹紧 与松开采用电动卡盘,选用呼和 浩特机床附件总厂生产的 KD11250型电动三爪自定心卡 盘。卡盘的夹紧与松开由数控系 统发信控制。
C620车床主轴结构改造设计3
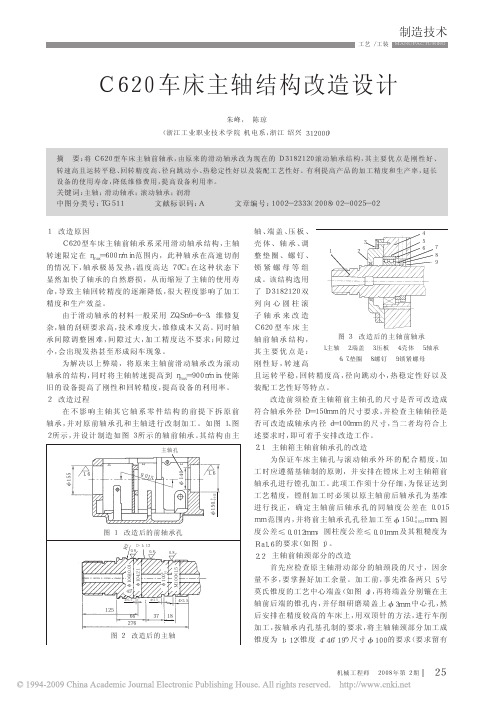
!3 中 心 孔
M100 ×1.5 轴 档 而因严重搅拌现象而使轴承升温; 若供油量过少, 轴承润
!38 !44 !54
调 整 螺 纹 , 1 只 滑不够, 温度也会上升, 所以供油量与喷油的位置决定了
M100 ×1.5 的 调 轴承的合理润滑, 以确保轴承的热稳定性。
70
整螺母和 2 只
( 2) 将主轴箱的润滑油移出贮放在外部, 从而起到冷
莫氏锥度的工艺中心端盖( 如图 4) , 再将端盖分别镶在主
轴前后端的锥孔内, 并仔细研磨端盖上 !3mm 中心孔, 然
后安排在精度较高的车床上, 用双顶针的方法, 进行车削
加工, 按轴承内孔基孔制的要求, 将主轴轴颈部分加工成
锥度为 1: 12( 锥度 4°46′19″) 尺寸 !100 的要求( 要求留有
筒等( 为叙述方便, 统称为大轮) 需要旋转, 此时设备结构 2 磨损分析和优化的设计
又不便安装轴承, 常常在它们下面安装两只托轮进行支
多盘过滤机托轮的工作环境及相关条件: 大轮以
撑 , 如 造 纸 业 的 倾 斜 式 高浓 碎 浆 机 、圆 筒 筛 、多 盘 过 滤 机 n=2r/min 匀速旋转, 直径 !900mm; 托轮直径 !240mm; 托
图 3 改造后的主轴前轴承 1.主轴 2.端盖 3.压板 4.壳体 5.轴承
6, 7.垫圈 8.螺钉 9.锁紧螺母
且运转平稳, 回转精度高, 径向跳动小, 热稳定性好以及
装配工艺性好等特点。
改造前须检查主轴箱前主轴孔的尺寸是否可改造成
符合轴承外径 D=150mm 的尺寸要求, 并检查主轴轴径是
否可改造成轴承内径 d=100mm 的尺寸, 当二者均符合上
45°
普通车床数控化改造总体方案设计
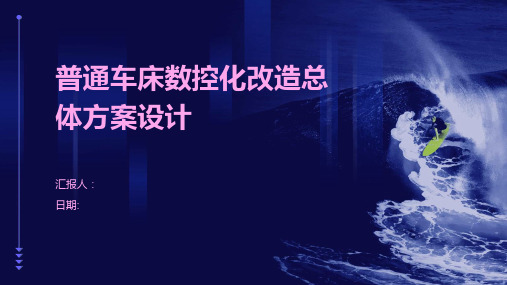
改造后的普通车床可以加工更复杂的 零件和更广泛的材料,拓展了其应用
领域和市场。
提升产品质量
改造后的普通车床加工精度和稳定性 提高,有助于提升产品质量和客户满 意度。
促进产业升级
普通车床数控化改造是机械制造行业 转型升级的重要方向之一,有助于推 动整个产业的升级和发展。
THANKS
感谢观看
伺服系统性能
根据车床的加工需求和改造重点, 选择所需的伺服系统性能,如扭矩 、转速等。
传动系统设计
主传动设计
根据车床的加工需求和改造重点 ,设计主传动系统的结构和性能
参数。
进给传动设计
根据车床的加工需求和改造重点 ,设计进给传动系统的结构和性
能参数。
其他传动设计
根据车床的加工需求和改造重点 ,设计其他必要的传动系统结构
包括机械结构改造、控制系统升级、设备调试等,预计需 要2个月时间。
改造后测试与验收阶段
对改造后的车床进行各项性能测试和安全评估,确保达到 预期效果,预计需要1个月时间。
改造实施费用预算
设备采购费用
根据所选设备的型号和配置,预计设备采购费用为XX万元。
改造施工费用
包括施工所需的人工费、工具费、材料费等,预计改造施工费用为 XX万元。
数控系统功能
根据车床的加工需求和改 造重点,选择所需的数控 系统功能,如车削、铣削 、钻孔等。
数控系统品牌
对比不同品牌数控系统的 性能、价格、可靠性等因 素,选择合适的品牌。
伺服系统设计
伺服系统类型
选择适合普通车床的伺服系统 类型,如步进电机、直流电机
、交流伺服电机等。
伺服系统精度
根据车床的加工精度要求,选择适 度的伺服系统精度。
普通车床数控化改造总体方案设计

普通车床数控化改造总体方案设计随着科技的不断发展,数控机床已经逐渐取代了传统机床成为重要的生产工具,因为其快捷、精准、自动化、高效的特点,越来越受到企业和人们的青睐。
普通车床是加工金属零件必不可少的工具,但是其性能不能够满足复杂零部件的加工要求,所以更加显示了数控机床的实用性和重要性。
今天,我们将介绍一下普通车床数控化改造总体方案设计。
一、数控化改造的优势1、提高生产效率的能力数控机床的控制系统可以对生产过程进行监测,能够及时发现生产中出现的问题并对其修复,为生产提供了坚实的基础。
特别是在复杂加工的过程中,数控机床能够快速切削、加工出想要的产品,节省了工作时间、提高了生产效率。
2、提高零件精度和质量普通车床操作难度较大,要求工人对刀具、工件、加工速度等都能够很好地控制。
而数控机床则可以通过设定刀具的路径和位置、控制加工速度、调节加工深度等,从而保证产品的精度和质量。
3、简化操作流程数控机床的主要优势在于自动化生产,通过使用数控系统,可以避免一些人工操作,对工人的技能要求也较普通车床降低。
这极大地提高了生产效率,降低了对操作人员的要求,从而减少了工作强度。
二、普通车床数控化改造的关键技术1、控制系统控制系统是整个数控化改造过程中的核心部分,其主要作用是控制数控机床的动态加工过程。
控制系统包括数控软件和控制器两个部分,数控软件是用来进行编程的,控制器则是用来执行程序的,两者的相互协调是整个控制系统的关键。
2、运动控制系统运动控制系统是数控机床实现加工运动的重要部分。
它主要包括定位控制系统、运动控制系统和位置检测系统。
定位控制系统是用于控制人工输入的程序和数控系统程序中的切削位置和切削轨迹,运动控制系统用于执行运动控制命令和切削工艺参数,位置检测系统用于检测加工过程的位置精度和误差。
三、普通车床数控化改造的总体方案设计1、优化传动系统在普通车床数控化改造中,需优化其传动部分,以适应新的数控系统。
首先需要更换一些传动零件,例如齿轮等,将其改为钢制齿轮,从而提高了转速和变速的平稳性。
C620车床数控改造设计
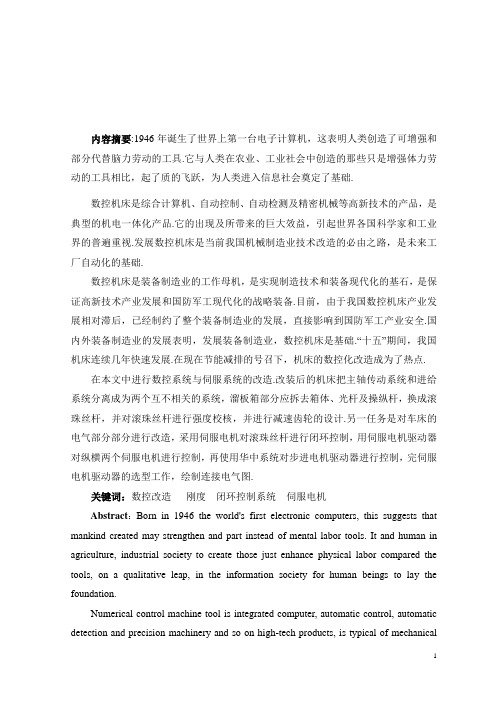
内容摘要:1946年诞生了世界上第一台电子计算机,这表明人类创造了可增强和部分代替脑力劳动的工具.它与人类在农业、工业社会中创造的那些只是增强体力劳动的工具相比,起了质的飞跃,为人类进入信息社会奠定了基础.数控机床是综合计算机、自动控制、自动检测及精密机械等高新技术的产品,是典型的机电一体化产品.它的出现及所带来的巨大效益,引起世界各国科学家和工业界的普遍重视.发展数控机床是当前我国机械制造业技术改造的必由之路,是未来工厂自动化的基础.数控机床是装备制造业的工作母机,是实现制造技术和装备现代化的基石,是保证高新技术产业发展和国防军工现代化的战略装备.目前,由于我国数控机床产业发展相对滞后,已经制约了整个装备制造业的发展,直接影响到国防军工产业安全.国内外装备制造业的发展表明,发展装备制造业,数控机床是基础.“十五”期间,我国机床连续几年快速发展.在现在节能减排的号召下,机床的数控化改造成为了热点.在本文中进行数控系统与伺服系统的改造.改装后的机床把主轴传动系统和进给系统分离成为两个互不相关的系统,溜板箱部分应拆去箱体、光杆及操纵杆,换成滚珠丝杆,并对滚珠丝杆进行强度校核,并进行减速齿轮的设计.另一任务是对车床的电气部分部分进行改造,采用伺服电机对滚珠丝杆进行闭环控制,用伺服电机驱动器对纵横两个伺服电机进行控制,再使用华中系统对步进电机驱动器进行控制,完伺服电机驱动器的选型工作,绘制连接电气图.关键词:数控改造刚度闭环控制系统伺服电机Abstract:Born in 1946 the world's first electronic computers, this suggests that mankind created may strengthen and part instead of mental labor tools. It and human in agriculture, industrial society to create those just enhance physical labor compared the tools, on a qualitative leap, in the information society for human beings to lay the foundation.Numerical control machine tool is integrated computer, automatic control, automatic detection and precision machinery and so on high-tech products, is typical of mechanicaland electrical products. It emerged and brings great benefits, cause the countries all over the world paid attention to scientists and industry. Development in China's current numerical control machine mechanical manufacturing technology reform way, that is the factory automation foundation.Numerical control machine tool is the equipment manufacturing industry machine tools, is to realize manufacturing technology and equipment modernization's cornerstone, is the guarantee of high and new technology industry development and national defense military modernization strategy equipment. At present, as our country's numerical control machine tool industry development is relatively slow, has restricted the development of the equipment manufacturing industry, directly affects the national defense military industry safety. The development of the equipment manufacturing industry at home and abroad show that, the development of the equipment manufacturing industry, numerical control machine tool is the foundation. In the tenth-five period, China machine rapid development for several years. Now in the energy conservation and emissions reduction under the call, numerical control machine tool converted into a hot spot.In this paper the CNC servo system with the reform. Modified machine tool spindle drive system and the system into separate into two irrelevant system, walk the board box part should tear down the body and light pestle and joysticks, change of ball screw, ball screw to check intensity, and the reduction gear design. Another task is to part of the lathe electrical transformed, servo motor ball screw for closed loop control, with servo motor drive to globetrotting two servo motor control, to use the central China system of the stepping motor drive control, the selection of the servo motor drive, draw connection electrical diagrams.Key words:digital modification stiffness closed-loop closed-cycle cyclil control system Servo motor1. 绪论1.1问题的提出1.1.1国外数控机床的发展状况数控机床出现至今已有近60年历史,在这60年中,随着科技、特别是微电子、计算机技术的进步,数控机床得到了广泛的发展.它已经成为现代化企业发展进程中一支凸显业绩的生力军,代表着未来机器制造业的发展方向.目前以美国、德国、日本在数控机床的科研、设计、制造和使用上,技术最先进、经验最多,他们政府重视机床工业,并且重视科研和创新,使他们三国的数控技术处于世界领先地位.数控技术正在发生根本性变革,由专用型封闭式开环控制模式向通用型开放式实时动态全封闭控制模式发展.在集成化基础上,数控系统实现了超薄型、超小型化;在智能化基础上,综合了计算机、多媒体、模糊控制和神经网络等多学科技术,数控系统实现了高速、高精度、高效控制,加工过程中可以自动修正、调节和补偿各项数据,实现了在线诊断和智能化故障处理;在网络化基础上,CAD/CAM与数控系统集成一体,机床联网,实现了中央集中控制群的加工.1.1.2国内数控机床的现状机床作为机械制造业的重要基础装备,它的发展一直引起人们的关注,由于计算机技术的兴起,促使机床的控制信息出现了质的突破,导致了应用数字化技术进行柔性自动化控制的新一代机床-数控机床的诞生和发展.是关键技术,它集微电子、计算机、信息处理、自动检测、自动控制等高新技术于一体,具有高精度、高效率、柔性自动化等特点,对制造业实现柔性自动化、集成化、智能化起着举足轻重的作用.目前,数控技术正在发生根本性变革,由专用型封闭式开环控制模式向通用型开放式实时动态全闭环控制模式发展.在集成化基础上,数控系统实现了超薄型、超小型化;在智能化基础上,综合了计算机、多媒体、模糊控制、神经网络等多学科技术,数控系统实现了高速、高精、高效控制,加工过程中可以自动修正、调节与补偿各项参数,实现了在线诊断和智能化故障处理;在网络化基础上,CAD/CAM与数控系统集成为一体,机床联网,实现了中央集中控制的群控加工.长期以来,我国的数控系统为传统的封闭式体系结构,CNC只能作为非智能的机床运动控制器.加工过程变量根据经验以固定参数形式事先设定,加工程序在实际加工前用手工方式或通过CAD/CAM及自动编程系统进行编制.CAD/CAM和CNC之间没有反馈控制环节,整个制造过程中CNC只是一个封闭式的开环执行机构.在复杂环境以及多变条件下,加工过程中的刀具组合、工件材料、主轴转速、进给速率、刀具轨迹、切削深度、步长、加工余量等加工参数,无法在现场环境下根据外部干扰和随机因素实时动态调整,更无法通过反馈控制环节随机修正CAD/CAM中的设定量,因而影响CNC的工作效率和产品加工质量.由此可见,传统CNC系统的这种固定程序控制模式和封闭式体系结构,限制了CNC向多变量智能化控制发展,已不适应日益复杂的制造过程,因此,对数控技术实行变革势在必行.随着计算机技术的高速发展,传统的制造业开始了根本性变革,各工业发达国家投入巨资,对现代制造技术进行研究开发,提出了全新的制造模式.1.1.3数控未来发展的趋势1.高速高精高效化速度、精度和效率是机械制造技术的关键性能指标.由于采用了高速CPU芯片、RISC芯片、多CPU控制系统以及带高分辨率绝对式检测元件的交流数字伺服系统,同时采取了改善机床动态、静态特性等有效措施,机床的高速高精高效化已大大提高.2.柔性化包含两方面:数控系统本身的柔性,数控系统采用模块化设计,功能覆盖面大,可裁剪性强,便于满足不同用户的需求;群控系统的柔性,同一群控系统能依据不同生产流程的要求,使物料流和信息流自动进行动态调整,从而最大限度地发挥群控系统的效能.3.工艺复合性和多轴化以减少工序、辅助时间为主要目的的复合加工,正朝着多轴、多系列控制功能方向发展.数控机床的工艺复合化是指工件在一台机床上一次装夹后,通过自动换刀、旋转主轴头或转台等各种措施,完成多工序、多表面的复合加工.数控技术轴,西门子880系统控制轴数可达24轴.4.实时智能化早期的实时系统通常针对相对简单的理想环境,其作用是如何调度任务,以确保任务在规定期限内完成.而人工智能则试图用计算模型实现人类的各种智能行为.科学技术发展到今天,实时系统和人工智能相互结合,人工智能正向着具有实时响应的、更现实的领域发展,而实时系统也朝着具有智能行为的、更加复杂的应用发展,由此产生了实时智能控制这一新的领域.在数控技术领域,实时智能控制的研究和应用正沿着几个主要分支发展:自适应控制、模糊控制、神经网络控制、专家控制、学习控制、前馈控制等.例如在数控系统中配备编程专家系统、故障诊断专家系统、参数自动设定和刀具自动管理及补偿等自适应调节系统,在高速加工时的综合运动控制中引入提前预测和预算功能、动态前馈功能,在压力、温度、位置、速度控制等方面采用模糊控制,使数控系统的控制性能大大提高,从而达到最佳控制的目的.1.2 机床数控化改造的必要性应用科学的发展观,我们可以从微观和宏观两个不同的角度看待数字控制技术在当今工业发展中的必要性.1.2.1 微观看改造的必要性从微观上看,数控机床比传统机床有以下突出的优越性,而且这些优越性均来自数控系统所包含的计算机的威力.1.可以加工出传统机床加工不出来的曲线、曲面等复杂的零件.由于计算机有高超的运算能力,可以瞬时准确地计算出每个坐标轴瞬时应该运动的运动量,因此可以复合成复杂的曲线或曲面.2.可以实现加工的自动化,而且是柔性自动化,从而效率可比传统机床提高3~7倍.由于计算机有记忆和存储能力,可以将输入的程序记住和存储下来,然后按程序规定的顺序自动去执行,从而实现自动化.数控机床只要更换一个程序,就可实现另一工件加工的自动化,从而使单件和小批生产得以自动化,故被称为实现了“柔性自动化”.3.加工零件的精度高,尺寸分散度小,使装配容易,不再需要“修配”.4.可实现多工序的集中,减少零件在机床间的频繁搬运.5.拥有自动报警、自动监控、自动补偿等多种自律功能,因而可实现长时间无人看管加工.6.由以上五条派生的好处.如:降低了工人的劳动强度,节省了劳动力(一个人可以看管多台机床),减少了工装,缩短了新产品试制周期和生产周期,可对市场需求作出快速反应等等.以上这些优越性是前人想象不到的,是一个极为重大的突破.此外,机床数控化还是推行FMC(柔性制造单元)、FMS(柔性制造系统)以及CIMS(计算机集成制造系统)等企业信息化改造的基础.数控技术已经成为制造业自动化的核心技术和基础技术.1.2.2 宏观看改造的必要性从宏观上看,工业发达国家的军、民机械工业,在70年代末、80年代初已开始大规模应用数控机床.其本质是,采用信息技术对传统产业(包括军、民机械工业)进行技术改造.除在制造过程中采用数控机床、FMC、FM S外,还包括在产品开发中推行CAD、CAE、CAM、虚拟制造以及在生产管理中推行MIS(管理信息系统)、CIMS等等.以及在其生产的产品中增加信息技术,包括人工智能等的含量.由于采用信息技术对国外军、民机械工业进行深入改造(称之为信息化),最终使得他们的产品在国际军品和民品的市场上竞争力大为增强.而我们在信息技术改造传统产业方面比发达国家约落后20年.如我国机床拥有量中,数控机床的比重(数控化率)到1995年只有1.9%,而日本在1994年已达20.8%,因此每年都有大量机电产品进口.这也就从宏观上说明了机床数控化改造的必要性.1.3研究意义1.3.1机床数控化改造的意义1.节省资金.机床的数控改造同购置新机床相比一般可节省60%左右的费用大型及特殊设备尤为明显.一般大型机床改造只需花新机床购置费的1/3.即使将原机床的结构进行彻底改造升级也只需花费购买新机床60%的费用,并可以利用现有车床.2.性能稳定可靠.因原机床各基础件经过长期时效,几乎不会产生应力变形而影响精度.3.提高生产效率.机床经数控改造后即可实现加工的自动化效率可比传统机床提高 3至5倍.对复杂零件而言难度越高功效提高得越多.且可以不用或少用工装,不仅节约了费用而且可以缩短生产准备周期.在国内,目前各企业有大量普通机床,完全用数控机床替换根本不现实,而且替代又造成很大的浪费,数控改造一次性投入少,而且对机床又增加很多性能.以上几点可以看出,普通机床应走数控改造之路,因此普通机床的数控改造,不但要有必要,而且大有可为,尤其是对一些中小型企业更是如此.机床的数控改造具有很好的理论意义和实际应用价值:1.改造费低,在发挥原有机床的功能同时提高加工精度.2.改造后机床自动化程度提高,减少辅助时间,提高生产效率3.降低工人水平要求,改善劳动条件,有利于身体健康4.改造闲置设、传统设备,提高机床功能和使用价值,减少设备投入.5.改造后可以加工复杂、异形零件,能完成普通机床难以加工或根本不可能加工的复杂曲线、曲面等零件.6.计算机控制,消除人为误差,加工零件精度高、一致性好、尺寸分散度小,使装配容易,无需修配.7.具有柔性化的特点,只需编制零件程序就能加工新零件,可以实现多品种、变批量、高性能加工,不仅能适应中小批量,也适合大批量生产.8.计算机具有记忆与储存功能,可以将输入的程序记住和储存下来,数控机床只要更换一个程序,就可以实现另一个零件的加工自动化,从而使单件和小批量生产得以自动化.9.能适应信息化发展的需要,通过网络可以实现信息通信,具有远程监控、补偿、诊断和自动报警等多种功能,可实现无人看管加工,降低了劳动强度,操作者有空闲时间照料其他操作.1.3.2机床数控化改造的迫切性经济的全球化、市场的国际化,促进了竞争,为求得生存与发展,各企业不仅要提高产品质量,而且必须频繁的改型,缩短生产周期,以满足市场上不断变化的需求.经过数控改造的机床的高精度、高效率、高度柔性化及适合加工精度高以及复杂的零部件,满足当今市场快速多变、竞争激烈和工艺发展的需要.可以说,数控改造技术的应用是机械制造行业现代化的标志,在很大程度上决定了企业在市场竞争中的成败.2. C620机床运动分析2.1传动链分析 电动机带轮床头箱主轴挂论丝杆光杆溜板箱刀架进给箱工件车刀图2-1 C620车床传动系统图图所示为C620型机床传动系统图,传动系统包括主传动链和进给传动链两部分.2.2主传动链主传动链两端是电动机与主轴.它的作用是把动力源(电动机)的运动与动力传给主轴,使主轴带动工件旋转,并使主轴获得变速和转向.2.3进给箱传动链进给箱传动链包括纵向进给与横向进给传动链3. 车床改造的总体方案3.1 C620型普通车床的简易数控改装的设计任务要点1.改装后能实现车削圆弧面、外圆面、端面等回转表面.2.改装后纵向进给精度士0. 0lmm,横向进给精度士0. 005mm,空载快速进给速=2m/min,主切削力P Z=2303N,横向拖板刀架质量W1=465. 5N,大拖板刀架质度V快量W2=1039N.3.改动后不要求保留手动操作功能.4.控制部分要求运动可靠,抗干扰,维修方便.5.改造成本低.3.2总体方案的确定改装后的数控车床应把主轴传动系统和进给系统分离成为两个互不相关的系统,为了便于编程,保证加工精度,要求车床纵向脉冲当量为0.01mm,横向脉冲当量为0.005mm,车床需要改装的部分有:1.挂轮架系统全部拆去.2.进给齿轮箱箱体内的零件全部拆去.3.溜板箱部分应拆去箱体、光杆及操纵杆,并增加支承支架,安装滚珠丝杆.4.纵向导轨选用贴塑的矩形和三角形组合导轨,横向导轨选用贴塑的燕尾形导轨,贴塑为聚四氟乙烯.5.横向溜板上应安装伺服电机,并通过传动齿轮将电机轴与横向滚珠丝杆联接6.刀架体应加装纵、横微调装置以供校刀使用.7.纵向丝杆挂脚应安装伺服电机,并通过传动齿轮与纵向滚珠丝杆联接.伺服电机与丝杆的联接方式要求联接可靠,传动无间隙,无噪音.对于电气部分,采用华中数控对纵、横两个伺服电机进行闭环控制,系统中有时钟电路模块,复位电路,数码显示器接口电路,光电藕合器等.采用内置驱动模块将伺服电机进行驱动,将整个控制系统放在控制柜中,由电缆把控制系统和伺服电机联系起来.4. 纵向进给装置的改造4.1纵向滚珠丝杆的最大轴向载荷的设计计算4.1.1 纵向丝杆的最大轴向载荷因为主切削力P z =2303N =235kgf , 所以纵向进给力为P x =0.5P z=0.5⨯2303=1151.5 N纵向丝杆的最大轴向载荷:P a =KP X +f (P Z +W 2)=1.14⨯1151.5+0.11⨯(2303+1039)=1312.71+367.62=1680.33N=171.5kgk ---系数,k =1.14f ---贴塑导轨摩擦系数,f =0.11W 2---纵向托板重量,W 2=1039N =106kgf4.1.2丝杆最高转速n maxn max ==t v62000=333 r /minv ---空载快速进给速度,v =2m /min =2000mm /mint ---丝杆导程,初设t =6mm4.1.3丝杆寿命(以 106 转为单位1)L =6max1060n T ⋅⋅ =6101500033360⨯⨯=300T ---丝杠使用寿命,T =15000小时n ma ---丝杆最高转速,n ma =333r /min一般考虑运转中有冲击,以及丝杆材料硬度对寿命的影响,则最大动负荷Q 为:Q =h w a f f P L ⋅⋅⋅3 =0.14.15.1713003⨯⨯⨯=1607kgfL ---丝杆寿命,L =300P a ---纵向丝杆的最大轴向载荷,P a =171.5kgff w ---运转系数,f w =1.4f h ---硬度系数,f h =1.04.1.4选择滚珠丝杠副按最大动负载荷Q 选用滚珠丝杆副,使 Q ≤CC ---滚珠丝杆的额定动负荷选用城L 3506型的单螺母滚珠丝杆副,其尺寸如表4-1所示:4.1.5确定丝杆副工作长度LL ≥431l l H l +++1l ---控制系统中需要的行程,l 1 =900 mmH ---螺母安装高度,H =111 mm3l ---由丝杆副防护结构确定的长度,取3l =115 mm4l ---由丝杆副支承所需的长度,取心4l =80L ≥431l l H l +++≥900+111+115+80≥1206滚珠丝杆副的总长度总L ,总L 为丝杆副工作长度L 加上结构长度,取结构长度为165mm ,则: 总L =L +165=1206+165=1371mm滚珠丝杆的长度应满足刚度要求,即:0D l 总=9.32351371=≤45 Do ---滚珠丝杆副的名义直径,Do =35 mm故丝杆副长度可以满足刚度要求.表4-1 滚珠丝杆副的尺寸规格序号 名称 代号 尺寸 单位1 滚珠丝杆副型号 W 1L35062 名义直径 D 0 35 mm3 螺距 t 6 mm4 螺旋升角 λ '7305 滚珠直径 d 0 3.969 mm6 滚道半径 R 2.064 mm7 偏心距 e 0.056 mm8 丝杆外径 d 34 mm9 螺母凸缘外径 D 3 72 mm10 螺母配合外径 D 55 mm11 圆螺母尺寸 M M52×1.5 mm12 二个圆螺母厚度 L 2 20 mm13 螺母座键槽厚度 t 2 58.2 mm14 平键尺寸 b×h×l 6×6×45 mm15 螺母装配总长度 L 111 mm16 额定动负载荷3.5圈1列C 1940 kgf17 额定动负载荷3.5圈1列 C0 7110 kgf4.1.6滚珠丝杆副几何参数的计算丝杆内径1d 为:1d = D 0+2e -2R=35+2×0.056-2×2.064=30.984=3.0984CMD 0---滚珠丝杆副的名义直径,D 0=35mme ---滚珠丝杆副的偏心距,e =0.056 mmR ---滚珠丝杆副的滚道半径,R =2.064mm丝杆接触直径z d 为:z d = D 0-d 0·cos β=35-3.969×cos 045=32.193mm=3.2193cmD 0---滚珠丝杆副的名义直径,D 0=35mmd 0---滚珠丝杆副的滚珠直径,d 0=3.969mmβ---接触角,β=0454.1.7计算传动效率0η0η=()ϕλλ+tan tan=()()''0'0107373+tg tg=0.949=94.9%λ---螺旋升角,λ='730ϕ---摩擦角,滚珠丝杆副的滚动摩擦系数f =0.003~0.004,其摩擦角ϕ≈'104.2纵向滚珠丝杆副的刚度验算滚珠丝杆受工作载荷P a 的作用而引起螺距t 的变化量∆t 1,其值可按下式计算:∆t 1=F E tp a ⋅⋅P a ---工作载荷,P a =1680Nt ---滚珠丝杆的螺距,t =6mm =0.6cmF ---滚珠丝杆的截面积F =421d ⋅π=40984.314.32⨯=7.536cm 21d ---丝杆内径,1d =3.0984cmE ---弹性模数,对钢E =20.6×106N / cm 2∆t 1=F E tp a ⋅⋅ =536.7106.206.016806⨯⨯⨯=6.49×610-cm滚珠丝杆因受扭矩作用而引起的导程变化量∆2t 为∆2t =πϕ2⋅tt ---在滚珠丝杆的螺距,t =6mm =0.6cmϕ---在扭矩M 作用下,滚珠丝杆每一螺距长度两截面上的相对扭转角ϕ=cJ G tM ⋅⋅G ---扭转弹性模数,对钢G =82.4×105N / cm 2M ---滚珠丝杆上的扭矩M =()λtg d P z a ⋅⋅21 =()'0732193.3168021tg ⨯⨯⨯ =147N ·cmP a ---工作载荷,P a =1680Nz d ---丝杆接触直径,z d =3.2193cmλ---螺旋升角,λ='730J c ---滚珠丝杆截面积的惯性拒J c =4132d π=40984.33214.3⨯ =9.04cm 41d ---丝杆内径,1d =3.0984cmϕ=cG t M ⋅⋅ =04.9104.826.01475⨯⨯⨯ =1.19×106-∆2t =πϕ2⋅t =14.321019.16.06÷⨯⨯- =0.113×106-因此滚珠丝杆在工作载荷P a 扭矩M 共同作用下,所引起每一个螺距变形量∆t 为∆t =∆t 1+∆2t=6.49×106-+0.113×106-=6.603×106-cm如果滚珠丝杠长度为1000mm ,其上共有100/t 个螺距,它的螺距变形总误差∆为∆=⋅t100∆t =610603.66.0100-⨯⨯ =11.005μm /m因为选滚珠丝杆精度等级为E 级,计算的总变形误差∆=11.005μm /cm ,小于E 级精度误差15μm /m ,所以刚度合适4.3支承方式及轴承的选择4.3.1支承方式的确定如果螺母座、丝杆的轴承及其支架等刚度不足,将严重影响滚珠丝杆副的传动刚度,因此螺母应有加强筋,以减小受力后的变形,螺母座与床身的接触面积宜大,其联接螺钉的刚度也应高一些,定位销要紧密配合,不能松动.由于丝杆主要承受轴向力,大多采用推力轴承作支撑,这里采用左右各一个推力轴承的支承方式.如下图所示:图4-1 滚珠丝杆支承方式其中最左端与最右端为推力轴承,中间两个为深沟球轴承这种支承方式可以对丝杆进行预拉伸安装,预紧拉伸安装可以诚少或俏除因丝杆自重而产生的弯曲变形,在推力轴承预紧力不小于丝杆最大轴向载荷1/3的条件下,丝杆的拉伸压缩刚度可提高4倍,丝杆不会因温升而升长,温升只能减小预拉伸力,另外,丝杆不承受压力,由于只承受拉力,因而没有压杆稳定性问题.但是预拉伸安装将使轴承发热和摩擦扭矩有所增加.4.3.2轴承选择由于进给丝杆主要承受较大轴向力和较小径向力,所以只需计算推力轴承的额定动载荷C :C =n h f f ×P a P a ---工作载荷,P a =1680Nf n ---速度系数f n =33333100⨯ =0.464n t ---轴承计算转速,n t =n max =333r /minf h ---寿命系数f h =3500T =350015000 =3.107T ---使用寿命,T =15000hC =nh f f ×P a =464.0107.3×1680 =11249.5N参照工具书查找到8106推力轴承,其额定负载为12.5×103N ≥11249.5N ,能满足要求,同时选用深沟球轴承型号为60064.3.3确定滚珠丝杠副的预紧力F P为了消除轴向间隙,增加丝杆副的刚性和定位精度,在丝杆螺母间加以预紧力F P ,然而过大的预紧力将会引起滚珠丝杆的寿命下降以及摩擦力的增大,而预紧力偏小,会在产生的轴向载荷左用下出现间隙,影响定位精度,因此,一般取:F P =5.9Q=5.96.15748 =1658NQ ---最大动负荷,Q =1607kgf =15748.6N取F P =1658N4.3.4确定滚珠丝杆轴的预紧拉伸力F pl为了消除丝杆自重而产生的弯曲变形,补偿因工作温度升高而引起的丝杆伸长,保证滚珠丝杆在正常使用时的定位精度和提高滚珠丝杆的系统刚性,对有快速驱动并有定位精度要求的滚珠丝杆副,其丝杆轴需进行预加拉伸力,决定拉伸力时还应考虑到丝杆两端支承轴承允许的预紧力的大小,一般情况下取:F pl =a p 31=5.17131⨯ =57.2kgfP a =171.5kgf4.4机械传动刚度的计算与校核在忽略支承座和螺母座刚度的情况下,机械传动部的刚度主要为:丝杆轴的支承刚度K k ,滚珠丝杆副的接触刚度K N 和轴承的轴向接触刚度K B ,则机械传动的综合拉压刚度为:∑K =BN K K K K 1111++4.4.1计算丝杆轴的支承刚度K K丝杆轴的支承方式及支承长度如图4-2所示:由于丝杆两端采用推力轴承和深沟球轴承,并且丝杆两端轴向固定支承,丝杆轴的支承刚度K K 的计算公式为:K K =32010114-⨯⎪⎪⎭⎫ ⎝⎛-+⋅K K L L L E D πN /μm D 0---滚珠丝杆副的名义直径,D 0=35mmE ---弹性模数,对钢E =2.06×105N /mm 2L ---丝杆工作长度,取L =1206mmL K ---丝杆作用长度mm丝杆作用长度L K 在这里有两种情况,当工作台处于最做端时,此时L K =96mm ,有最大的拉压刚度K kmax :K kmax =32010114-⨯⎪⎪⎭⎫⎝⎛-+⋅KK L L L E D π=⎪⎭⎫⎝⎛-+⨯⨯⨯⨯961006196141006.23514.352×103-=2379.52N /μm当工作台处于中间位置时,此时L K =603mm ,则有最小的拉压刚度K Kmin :K kmin =32010114-⨯⎪⎪⎭⎫⎝⎛-+⋅K K L L L E D π=420E D π×⎪⎪⎭⎫⎝⎛-+K K L L L 11×310-=⎪⎭⎫⎝⎛-+⨯⨯⨯⨯60312061603141006.23514.352=657N /μm电机961206图4-2 滚珠丝杆支撑方式4.4.2计算滚珠丝杆与螺母副间的接触刚度K nK n =0.77×320∑⨯⨯Z d F P ( N /μm )F P ----预紧力,F P =1658Nd 0---滚珠丝杆副的滚珠直径,d 0=3.969mmZ ∑---滚珠数量Z ∑=Z ×圈数×列数Z ---一圈的滚珠数Z =00d D π=969.33514.3⨯=27.69D 0---滚珠丝杆副的名义直径,D 0=35mmd 0---滚珠丝杆副的滚珠直径,d 0=3.969mmZ ∑=27.69×3.5×1=96.9K N =0.77×329.96969.31658⨯⨯=304 N /μm4.4.3计算轴承的轴向接触刚度K B推力轴承的轴向变形c δ为:c δ=2.4×322Z d P a*θP a ---工作载荷,P a =171.5kgfZ ---推力轴承的滚动体直径,d θ=5.556c δ=2.4×32218556.55.171⨯=6.09μm由于对轴承施加了预紧力,其变形量减少了一半计算:。
C620型普通车床数控化改造设计

目录引言 (5)1 概述 (6)1.1 毕业设计的目的 (6)1.2 设计任务 (7)1.3 设计的必要性 (7)1.3.1 数控改造目的 (7)1.3.2 数控改造的优点 (7)2总体方案设计 (7)2.1 系统的运动方式与伺服系统的选择 (7)2.2 计算机系统 (8)2.3 机械传动方式 (8)2.3.1纵向滚珠丝杠 (8)2.3.2横向滚珠丝杠 (8)2.3.3总体方案 (9)3进给伺服系统设计 (9)3.1纵向进给伺服系统 (10)3.1.1 计算进给牵引力F(N) (10)m3.1.2 计算最大动载荷C (11)3.1.3 滚珠丝杠螺母副的传动效率计算 (11)3.1.4 刚度验算 (12)3.1.5 稳定性校核 (13)3.2横向进给伺服系统 (13)F (13)3.2.1 计算进给牵引力m3.2.2 计算最大动负载C (13)3.2.3选择滚动丝杠螺母副 (14)3.2.4传动效率计算 (14)3.2.5 刚度验算 (14)3.2.6稳定性校核 (16)3.3齿轮传动比计算 (18)3.3.1 纵向进给齿轮箱传动比计算 (18)3.3.2横向进给齿轮箱传动比计算 (19)3.4步进电机的选型 (19)3.4.1纵向进给步进电机 (19)3.4.2横向步进电机 (23)3.4.3 计算步进电机空载启动频率和工作时的频率 (25)4 数控系统硬件电路设置 (26)4.1 数控系统基本硬件组成 (26)4.2 选择 CPU 的类型 (27)4.3 74LS138 CPU 和存储器 (27)4.4 I/O接口电路 (28)4.5 软件环行分配器 (28)4.6 控制系统 (28)4.7 其它辅助电路 (29)参考书目 (30)致谢 (31)图纸简介 .......................................... 错误!未定义书签。
摘要这次毕业设计主要是将一台C620型普通车床进行经济型数控改造设计,由于定位精度高,所以纵、横向导轨均采用贴塑导轨,传动系统采用滚珠丝杠,同时,为提高传动刚度和消除间隙,对丝杠进行预拉伸,传动齿轮采用双片错齿消隙齿轮,驱动元件采用步进电机。
C620普通车床进行数控改造
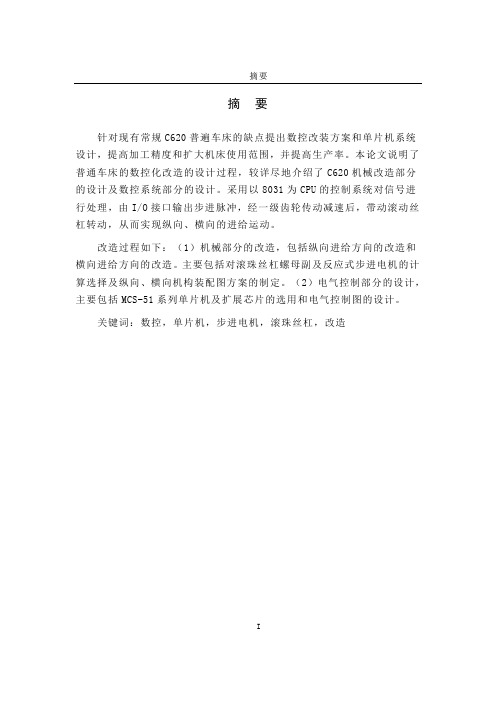
摘要摘要针对现有常规C620普遍车床的缺点提出数控改装方案和单片机系统设计,提高加工精度和扩大机床使用范围,并提高生产率。
本论文说明了普通车床的数控化改造的设计过程,较详尽地介绍了C620机械改造部分的设计及数控系统部分的设计。
采用以8031为CPU的控制系统对信号进行处理,由I/O接口输出步进脉冲,经一级齿轮传动减速后,带动滚动丝杠转动,从而实现纵向、横向的进给运动。
改造过程如下:(1)机械部分的改造,包括纵向进给方向的改造和横向进给方向的改造。
主要包括对滚珠丝杠螺母副及反应式步进电机的计算选择及纵向、横向机构装配图方案的制定。
(2)电气控制部分的设计,主要包括MCS-51系列单片机及扩展芯片的选用和电气控制图的设计。
关键词:数控,单片机,步进电机,滚珠丝杠,改造IABSTRACTABSTRACTTo remedy the defects of ordinary lather C620, a design o f data processing system and its single chip microcomputer system program is put forward to raise the processing precision and extend the machine’s usage, and to improve production rate。
This paper presents the process of designing numerical control reform,and explicitly introduces the design of mechanical and numerical control system reforms。
We adopt control system which has 8031 as cpu to cope with the signal,and output the step pulse through the I/O interface。
利用plc完成C620-1车床plc改造毕业设计
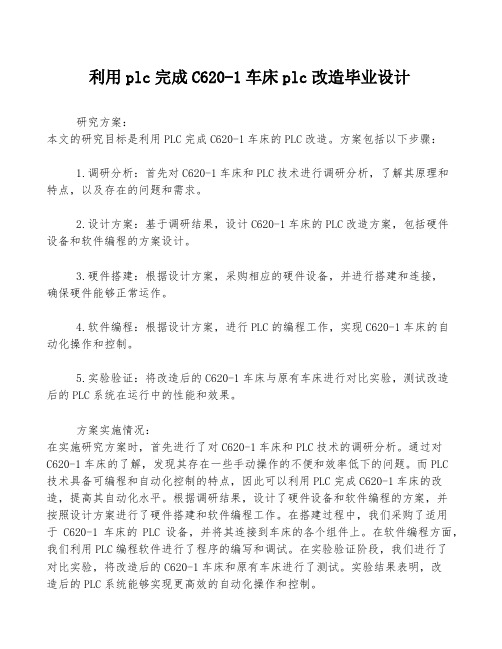
利用plc完成C620-1车床plc改造毕业设计研究方案:本文的研究目标是利用PLC完成C620-1车床的PLC改造。
方案包括以下步骤:1.调研分析:首先对C620-1车床和PLC技术进行调研分析,了解其原理和特点,以及存在的问题和需求。
2.设计方案:基于调研结果,设计C620-1车床的PLC改造方案,包括硬件设备和软件编程的方案设计。
3.硬件搭建:根据设计方案,采购相应的硬件设备,并进行搭建和连接,确保硬件能够正常运作。
4.软件编程:根据设计方案,进行PLC的编程工作,实现C620-1车床的自动化操作和控制。
5.实验验证:将改造后的C620-1车床与原有车床进行对比实验,测试改造后的PLC系统在运行中的性能和效果。
方案实施情况:在实施研究方案时,首先进行了对C620-1车床和PLC技术的调研分析。
通过对C620-1车床的了解,发现其存在一些手动操作的不便和效率低下的问题。
而PLC技术具备可编程和自动化控制的特点,因此可以利用PLC完成C620-1车床的改造,提高其自动化水平。
根据调研结果,设计了硬件设备和软件编程的方案,并按照设计方案进行了硬件搭建和软件编程工作。
在搭建过程中,我们采购了适用于C620-1车床的PLC设备,并将其连接到车床的各个组件上。
在软件编程方面,我们利用PLC编程软件进行了程序的编写和调试。
在实验验证阶段,我们进行了对比实验,将改造后的C620-1车床和原有车床进行了测试。
实验结果表明,改造后的PLC系统能够实现更高效的自动化操作和控制。
数据采集和分析:在实验过程中,我们进行了数据的采集和分析。
具体来说,我们记录了原有车床和改造后车床的自动化程度、生产效率和操作便利性等方面的数据。
通过对比这些数据,我们对改造后的PLC系统的性能进行了评估和分析。
实验结果表明,改造后的C620-1车床在自动化程度、生产效率和操作便利性等方面均有明显提升。
例如,改造后的车床可以通过预设程序实现各种加工工序的自动化控制,大大提高了生产效率和产品质量。
普通车床的数控化改造
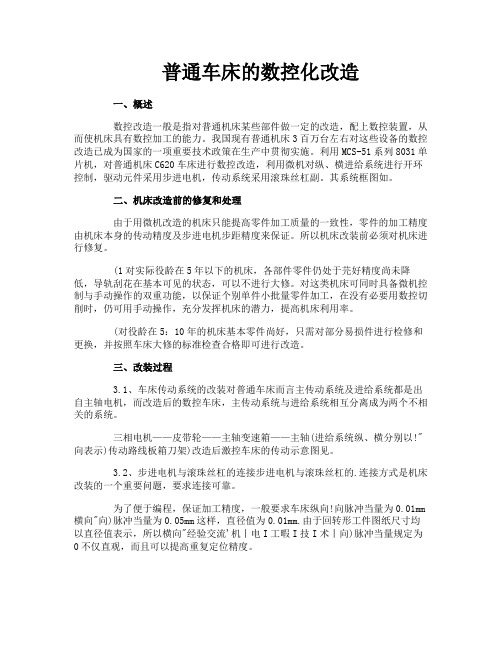
普通车床的数控化改造一、概述数控改造一般是指对普通机床某些部件做一定的改造,配上数控装置,从而使机床具有数控加工的能力。
我国现有普通机床3百万台左右对这些设备的数控改造已成为国家的一项重要技术政策在生产中贯彻实施。
利用MCS-51系列8031单片机,对普通机床C620车床进行数控改造,利用微机对纵、横进给系统进行开环控制,驱动元件采用步进电机,传动系统采用滚珠丝杠副。
其系统框图如。
二、机床改造前的修复和处理由于用微机改造的机床只能提高零件加工质量的一致性,零件的加工精度由机床本身的传动精度及步进电机步距精度来保证。
所以机床改装前必须对机床进行修复。
(1对实际役龄在5年以下的机床,各部件零件仍处于芫好精度尚未降低,导轨刮花在基本可见的状态,可以不进行大修。
对这类机床可同时具备微机控制与手动操作的双重功能,以保证个别单件小批量零件加工,在没有必要用数控切削时,仍可用手动操作,充分发挥机床的潜力,提高机床利用率。
(对役龄在5:10年的机床基本零件尚好,只需对部分易损件进行检修和更换,并按照车床大修的标准检查合格即可进行改造。
三、改装过程3.1、车床传动系统的改装对普通车床而言主传动系统及进给系统都是出自主轴电机,而改造后的数控车床,主传动系统与进给系统相互分离成为两个不相关的系统。
三相电机——皮带轮——主轴变速箱——主轴(进给系统纵、横分别以!"向表示)传动路线板箱刀架)改造后激控车床的传动示意图见。
3.2、步进电机与滚珠丝杠的连接步进电机与滚珠丝杠的.连接方式是机床改装的一个重要问题,要求连接可靠。
为了便于编程,保证加工精度,一般要求车床纵向!向脉冲当量为0.01mm 横向"向)脉冲当量为0.05mm这样,直径值为0.01mm.由于回转形工件图纸尺寸均以直径值表示,所以横向"经验交流'机丨电I工暇I技I术丨向)脉冲当量规定为0不仅直观,而且可以提高重复定位精度。
车床C620的数控改造
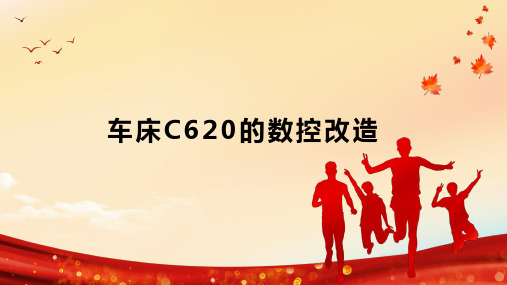
需求分析
3、适应多样化的生产需求:通过编程和控制,可以满足不同种类、不同批量 的生产需求。
4、维护和升级方便:改造后的车床应便于维护和升级,以便在未来适应新的 生产需求和技术发展。
4、维护和升级方便:改造后的 车床应便于维护和升级
2、软件改造
(3)生产管理:结合企业资源规划(ERP)系统,实现生产计划的动态调整 和优化。
三、改造效果分析
三、改造效果分析
经过数控化改造后,C616卧式车床可实现以下性能提升: 1、加工精度:通过选用高精度轴承、刀具和传动系统,以及先进的数控技术, 可大幅提高车床的加工精度。
三、改造效果分析
4、维护和升级方便:改造后的车床应便于维护和升级,以便在未来 适应新的生产需求和技术发展。
4、操作界面改进:设计友好型操作界面,使工人能够方便地操作机床。同时, 增加故障诊断功能,快速定位和解决机床故障。
参考内容
内容摘要
随着科技的不断发展,制造业正在快速变革,向着更高精度、更高效率的目 标迈进。在这个过程中,普通车床的数控化改造成为了制造业转型升级的重要手 段。本次演示将介绍C6140普通车床数控化改造的背景和意义,分析普通车床的 不足,提出数控化改造方案,并举例说明编程方式及改造效果。
四、应用前景展望
总之,C616卧式车床的数控化改造不仅能提升企业的生产效率和产品质量, 还能推动制造业的转型升级,具有较高的实用性和推广价值。在未来,我们应进 一步研究和优化改造方案,为制造业的发展贡献更多力量。
谢谢观看
车床C620的数控改造
01 引言
03 参考内容
目录
02 需求分析
机械c620普通车床的数控改造设计【全套图纸】学士学位论文

绪论内容摘要(CAM中的数控技术)尽管数控机床是开发实用CAM系统的关键所在,但本文描述的数控机床不能应用基于制造系统的计算机中。
必须改进传统的数控机床及自动化机床,以使信息能在监控装置及以计算机就为主的控制系统中传输。
这种改进导致了源于数控概念的三个主要发展、计算机管理数控、群集概念、新形式的适用控制。
计算机管理数控是一个包括DNC(直接数控)和CNC(计算机数控)的一般性概念DNC和CNC是用来在控制性计算机和数控机床间分配编程和计算机职责的方式,两个系统都不改进数控机床控制之外的工艺数据和命令的通讯方法。
群集概念基本上是对多种机床的计算机管理的延伸。
一系列机床(如铣床钻床磨床等),通过送料系统连接起来。
需要时,输料系统能自动向各个机床送料。
这样两级监控就成为必要。
单独的机床用计算机管理数控来控制,群集本身由协调许多群集的生产产量的中央计算机进行管理,其中的分级安排也是显而易见的。
全套图纸,加153893706适应性数控系统是CAM环境中的一部分。
中央计算机获得工艺过程信息以便检测出异常情况(如刀具破损),并加以纠正保护。
另外,也可以把适应性反馈记录下来并加以分析以便实现某一操作的高效生产。
可以从自动化和集成的角度看待在以计算机为机场的制造系统中数控机床的使用。
四级制造自动化可被定义。
独立的NC机床本身实现一个自动化操作循环。
数控加工中心则使整个制造加工过程过程自动化。
外控机床的群集则实现一个完全自动化的制造任务。
最后,CAM系统本身把所有的自动化制造工艺中的低层方法集成起来。
CAM系统的组成计算机付账制造系统的成功与否取决于在所有信息流动中起作用的硬件与软件的集成。
CAM硬件包括数控机床、检测设备,数字计算机和相关设备。
CAM软件是用来监测、处理、以及最终监控制造信息流和CAM硬件的计算机编程系统的相互联系的网络,在这里,软件部分在信息流方面受到检验。
CAM数据库基于制造系统的计算机不仅依靠实时信息,而且还要依靠存储信息,实时数据比如自动控制反馈的信息通常被立即处理,除非要求被储存,一般可以认为是瞬变的信息。
C620-1B车床的数控改造
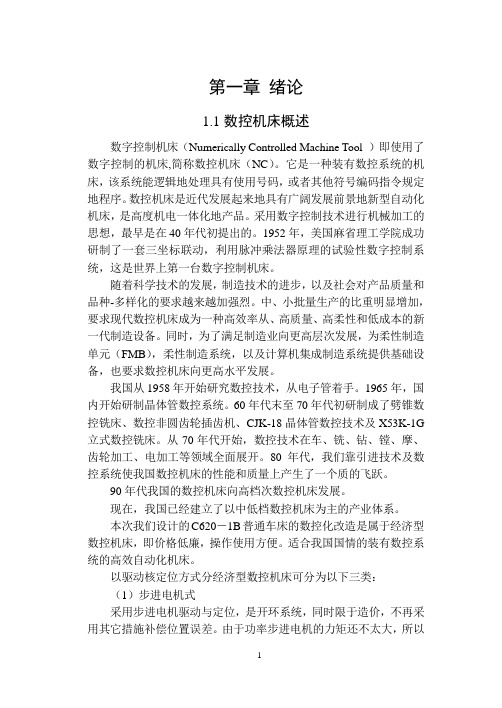
第一章绪论1.1数控机床概述数字控制机床(Numerically Controlled Machine Tool )即使用了数字控制的机床,简称数控机床(NC)。
它是一种装有数控系统的机床,该系统能逻辑地处理具有使用号码,或者其他符号编码指令规定地程序。
数控机床是近代发展起来地具有广阔发展前景地新型自动化机床,是高度机电一体化地产品。
采用数字控制技术进行机械加工的思想,最早是在40年代初提出的。
1952年,美国麻省理工学院成功研制了一套三坐标联动,利用脉冲乘法器原理的试验性数字控制系统,这是世界上第一台数字控制机床。
随着科学技术的发展,制造技术的进步,以及社会对产品质量和品种-多样化的要求越来越加强烈。
中、小批量生产的比重明显增加,要求现代数控机床成为一种高效率从、高质量、高柔性和低成本的新一代制造设备。
同时,为了满足制造业向更高层次发展,为柔性制造单元(FMB),柔性制造系统,以及计算机集成制造系统提供基础设备,也要求数控机床向更高水平发展。
我国从1958年开始研究数控技术,从电子管着手。
1965年,国内开始研制晶体管数控系统。
60年代末至70年代初研制成了劈锥数控铣床、数控非圆齿轮插齿机、CJK-18晶体管数控技术及X53K-1G 立式数控铣床。
从70年代开始,数控技术在车、铣、钻、镗、摩、齿轮加工、电加工等领域全面展开。
80年代,我们靠引进技术及数控系统使我国数控机床的性能和质量上产生了一个质的飞跃。
90年代我国的数控机床向高档次数控机床发展。
现在,我国已经建立了以中低档数控机床为主的产业体系。
本次我们设计的C620-1B普通车床的数控化改造是属于经济型数控机床,即价格低廉,操作使用方便。
适合我国国情的装有数控系统的高效自动化机床。
以驱动核定位方式分经济型数控机床可分为以下三类:(1)步进电机式采用步进电机驱动与定位,是开环系统,同时限于造价,不再采用其它措施补偿位置误差。
由于功率步进电机的力矩还不太大,所以机床的空行程速度较低,一般用于半精加工。
C620一1卧式车床的数控化改造
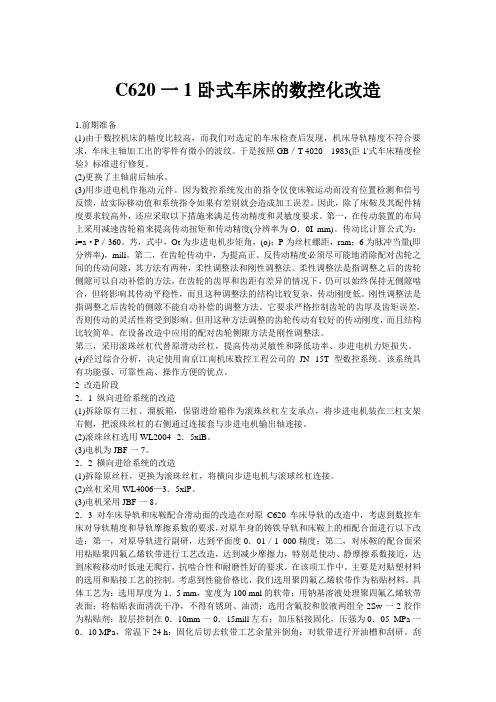
C620一1卧式车床的数控化改造1.前期准备(1)由于数控机床的精度比较高,而我们对选定的车床检查后发现,机床导轨精度不符合要求,车床主轴加工出的零件有微小的波纹。
于是按照GB/T 4020---1983(臣1'式车床精度检验》标准进行修复。
(2)更换了主轴前后轴承。
(3)用步进电机作拖动元件。
因为数控系统发出的指令仅使床鞍运动而没有位置检测和信号反馈,故实际移动值和系统指令如果有差别就会造成加工误差。
因此,除了床鞍及其配件精度要求较高外,还应采取以下措施来满足传动精度和灵敏度要求。
第一,在传动装置的布局上采用减速齿轮箱来提高传动扭矩和传动精度(分辨率为O.0I mm)。
传动比计算公式为:i=a·P/360。
艿,式中,Ot为步进电机步矩角,(o);P为丝杠螺距,ram;6为脉冲当量(即分辨率),mill。
第二,在齿轮传动中,为提高正、反传动精度必须尽可能地消除配对齿轮之间的传动问隙,其方法有两种,柔性调整法和刚性调整法。
柔性调整法是指调整之后的齿轮侧隙可以自动补偿的方法,在齿轮的齿厚和齿距有差异的情况下,仍可以始终保持无侧隙啮合,但将影响其传动平稳性,而且这种调整法的结构比较复杂,传动刚度低。
刚性调整法是指调整之后齿轮的侧隙不能自动补偿的调整方法。
它要求严格控制齿轮的齿厚及齿矩误差,否则传动的灵活性将受到影响。
但用这种方法调整的齿轮传动有较好的传动刚度,而且结构比较简单。
在设备改造中应用的配对齿轮侧隙方法是刚性调整法。
第三,采用滚珠丝杠代替原滑动丝杠,提高传动灵敏性和降低功率、步进电机力矩损失。
(4)经过综合分析,决定使用南京江南机床数控工程公司的JN--15T型数控系统。
该系统具有功能强、可靠性高、操作方便的优点。
2 改造阶段2.1 纵向进给系统的改造(1)拆除原有三杠、溜板箱,保留迸给箱作为滚珠丝杠左支承点,将步进电机装在三杠支架右侧,把滚珠丝杠的右侧通过连接套与步进电机输出轴连接。
ca620车床数控化改造毕业设计说明书

目录0摘要 (3)1引言 (6)第一章设计方案的确定...........................................................................- 7 - 一总体设计方案的确定...................................................................... - 8 - 二机械部分的改造设计与计算.......................................................... - 8 - (一)纵向进给系统的设计选型...................................................... - 8 -(二) 横向进给系统的设计与计算...................... 错误!未定义书签。
第二章步进电动机的选择............................................. 错误!未定义书签。
一步进电动机选用原则............................................... 错误!未定义书签。
二步进电机的选型....................................................... 错误!未定义书签。
(一)C620纵向进给系流步进电机的确定....... 错误!未定义书签。
(二)C620横向进给系流步进电机的确定....... 错误!未定义书签。
(三)110BF003型直流步进电机主要技术参数错误!未定义书签。
(四)110BF004型直流步进电机主要技术参数错误!未定义书签。
第三章经济型数控系统选型............................................. 错误!未定义书签。
第四章电动刀架的选型............................................... 错误!未定义书签。