自动裁床OEE与产能分析
自动裁床品牌分析报告
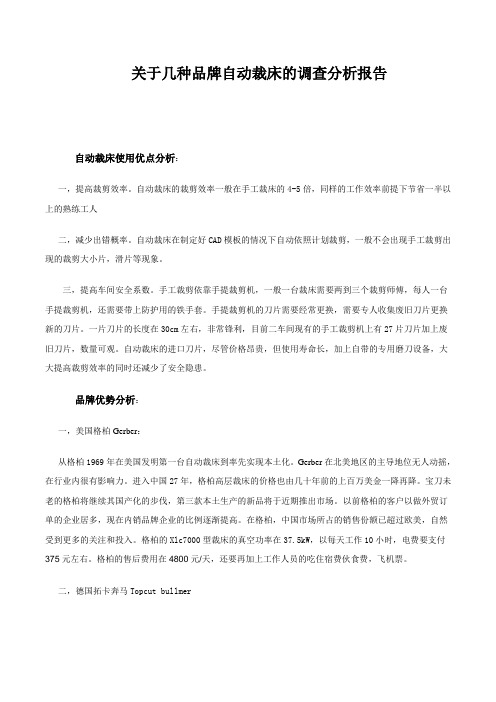
关于几种品牌自动裁床的调查分析报告自动裁床使用优点分析:一,提高裁剪效率。
自动裁床的裁剪效率一般在手工裁床的4-5倍,同样的工作效率前提下节省一半以上的熟练工人二,减少出错概率。
自动裁床在制定好CAD模板的情况下自动依照计划裁剪,一般不会出现手工裁剪出现的裁剪大小片,滑片等现象。
三,提高车间安全系数。
手工裁剪依靠手提裁剪机,一般一台裁床需要两到三个裁剪师傅,每人一台手提裁剪机,还需要带上防护用的铁手套。
手提裁剪机的刀片需要经常更换,需要专人收集废旧刀片更换新的刀片。
一片刀片的长度在30cm左右,非常锋利,目前二车间现有的手工裁剪机上有27片刀片加上废旧刀片,数量可观。
自动裁床的进口刀片,尽管价格昂贵,但使用寿命长,加上自带的专用磨刀设备,大大提高裁剪效率的同时还减少了安全隐患。
品牌优势分析:一,美国格柏Gerber:从格柏1969年在美国发明第一台自动裁床到率先实现本土化。
Gerber在北美地区的主导地位无人动摇,在行业内很有影响力。
进入中国27年,格柏高层裁床的价格也由几十年前的上百万美金一降再降。
宝刀未老的格柏将继续其国产化的步伐,第三款本土生产的新品将于近期推出市场。
以前格柏的客户以做外贸订单的企业居多,现在内销品牌企业的比例逐渐提高。
在格柏,中国市场所占的销售份额已超过欧美,自然受到更多的关注和投入。
格柏的Xlc7000型裁床的真空功率在37.5kW,以每天工作10小时,电费要支付375元左右。
格柏的售后费用在4800元/天,还要再加上工作人员的吃住宿费伙食费,飞机票。
二,德国拓卡奔马Topcut bullmer1,价格本土化。
浙江新杰克控股集团公司接手拓卡奔马后,着手的第一件事就是将原来150~200万的价降至120万左右。
雄心勃勃的拓卡奔马正紧锣密鼓推进国产化进程。
2,质量国际化。
拓卡奔马裁床的德国品质经过市场检验,得到了广泛的认可。
拓卡奔马的员工大都是在本企业服务了三四十年的,技术上可以说已经达到炉火纯青的地步,加上极为认真的工作态度,从而保证了质量好,寿命长。
OEE产能分析课件(PPT 36张)

14000*12=168000
满足
案例B
生产能力分析报告
供应商:XX公司
产品名称及图号:XX轴
项
目
工
序
磨外径
该工序加工
设备
时间(分钟,计划月 含辅助时间)台套② 次数/月
①
磨床
2件/分钟 24000
月调机时间③
时间/每次 (分钟)
总计时间分 钟(品种*次 数/月*时间/
次)
月设备维 修及停工 待料时间 (分钟)
专线和共线的产能分析,区别在于“产能分配百分比”的计 算,其它分析方法一致
28
产能分析问题交流
对以上内容有任何问题 或您在这方面有更深的体会请提出
共同参与交流
29
钓鱼
1、钓鱼方式 2、赢
30
分享共赢 钓鱼方式
传统钓
矶钓
海钓
冰钓
路亚钓
31
分享共赢 鱼竿种类
•
15、只有登上山顶,才能看到那边的风光。
•
16只会幻想而不行动的人,永远也体会不到收获果实时的喜悦。
•
17、勤奋是你生命的密码,能译出你一部壮丽的史诗。
•
1 8.成功,往往住在失败的隔壁!
•
1 9 生命不是要超越别人,而是要超越自己.
•
2 0.命运是那些懦弱和认命的人发明的!
•
21.人生最大的喜悦是每个人都说你做不到,你却完成它了!
•
3、当你还不能对自己说今天学到了什么东西时,你就不要去睡觉。 ——利希顿堡
•
4、人天天都学到一点东西,而往往所学到的是发现昨日学到的是错的。 ——B.V
•
5、学到很多东西的诀窍,就是一下子不要学很多。 ——洛 克
OEE产能报告
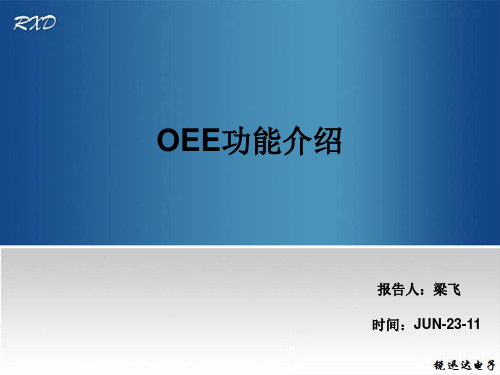
1000 50 1008 1000 219 5000 5000 219 800 1000
7000J-MSD-070BGWWCDMA-TOP 7000J-MSD-070BGW主 板-110530-BOT TEC-21006-00-1A RY-BG200-V4主板-BOT SMTKEPF9XA3 T20KB2 T20KB1 PW8C41MXD1SMT IN9QAAAAB8SMT IN9QAAAAB8SMT
切换工时 上料 程序 调整
大
调 备 等待 故障 调整 养 调整
物料 设备 程序 保
小 工艺 其它 清 尾 生产 小停 保 调整 ( G ) 数 养 止
美赛达 美赛达 博电 东太利 TPV 联想 联想 TPV TPV TPV
MSD1105006 MSD1106004(新产 品) BD1106003 DTL1106003(新产 品) 5500143779-80 4500220761-20 4500220761-10 5500143778-20 5500143777-50 5500143777-30
实际生产报表
SMT 生产日报表
生产日期 : 2011.6.20 班 别 线 体 S1 S2 S3 S3 S4 白 班 S4 S4 S5 S5 S5 客户 订单号 订单量 机 型 拼板 单板 数 点数 2 1 16 2 8 25 4 2 2 2 200 296 23 69 15 2 12 108 23 23 瓶颈工 时 (秒) 61 45 67 35 20 18 20 48 15 15 单小时 目标产 量 94 64 688 165 1152 4000 576 120 384 384 生产 板 数 597 50 1008 868 224 5000 1464 219 800 400 10630 MSD1105006 5500143777-10 MSD1106004(新产 品) BD1106003 DTL1106003(新产 品) DTL1106003(新产 品) 4500220761-10 5500143820-120 5500143820-130 5500143820-110 5500143777-30 5500143777-40 5500143777-80 5500143777-60 1000 1014 50 3000 1000 1000 5000 30 30 960 1000 1800 800 1000 7000J-MSD-070BGWWCDMA-TOP SMTF9A4SX3 7000L-MSD-070BGW主板-110530-TOP TEC-20906-01-10 PY-BG200-V4主板BOT PY-BG200-V4主板TOP T20 KB1 2 1 1 20 2 2 4 32 32 32 2 2 2 2 200 574 333 31 69 82 12 6 6 6 23 23 14 14 61 29 50 77 34 51 22 74 74 74 15 15 10 10 94 99 58 748 169 113 524 1245 1245 1245 384 384 576 576 403 84 50 3000 132 524 3536 30 30 960 600 1800 648 870 12667 23297 实装 点数 : 715002 目标 生产 点数 122754 23680 23728 56777 5760 19333 24192 25920 20608 12365 335117 86557 85506 19181 103967 9741 63902 43462 249 249 8967 14426 41952 14515 16128 508802 实装点数 生产工 时(分 钟) 390 75 90 300 20 145 210 120 140 84 1574 275 90 60 269 50 414 415 2 2 72 98 285 108 120 2260 8 9 9 15 10 30 10 20 5 8 6 6 20 52 75 20 10 5 20 88 20 15 10 16 3 38 45 28 80 88 20 80 30 10 15 8 15 25 35 10 20 5 4 10 10 5 8 22 70 60 40 10 15 10 10 10 10 20 10 5 20 20 20 30 18 5 5 4 30 30 20 20 6 5 30 50 43 10 10 15 15 45
OPE OEE及生产线平衡
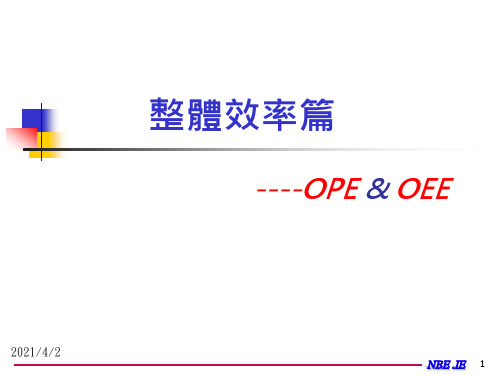
----OPE & OEE
2021/4/2
1
什么是OEE & OPE ?
OEE: 整體設備效率 Overall Equipment Efficiency
OPE: 整體工廠效率 Overall Plant Efficiency
用來衡量工廠經營管理的整體效率,包含: 設計者效率: 設備利用率,生產線平衡率 管理者效率: (設備或生產線)稼動率 作業者效率: 操作效率(或勞動效率)
OEE&OPE反應工廠的綜合能力
2
OEE & OPE如何計算 ?
OEE=產出工時/設備可用工時 OPE=產出工時/人員可用工時 產出工時
=可用時間內產出良品數*單件標准時間 設備可用工時
=投入設備數量*設備可用時間 人員可用工時
=投入作業人數*人員可用時間 可用時間指當班(天)花費到某產品上的時間
二:技術模組化時的重點是什麼? 如何做 好從專案到系統的過渡?
13
注意: 產出工時與可用工時計算的時間長度需要保持一致
3
關於OPE & OEE
可用工時
工
時
良品產出工時 平衡損失 稼動損失 操作損失
結
構
良品產出工時
平衡損失
操作損失
稼動損失
OPE = 平衡率 稼動率 操作效率
改
善 工廠績效 設計者績效 管理者績效 作業者績效
思
維
OPE =
=100%
稼動損失分析對策
設備 異常
作業 失誤
20% 其他
改善對策
損失項目 不良返修
設備異常 作業失誤
改善對策
TOP3管控跟蹤 拉杆加壓痕
关于应用自动裁床的可行性分析报告
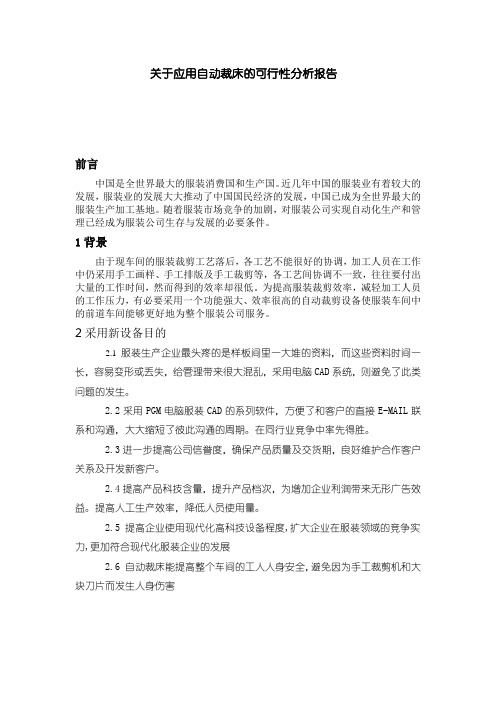
关于应用自动裁床的可行性分析报告前言中国是全世界最大的服装消费国和生产国。
近几年中国的服装业有着较大的发展,服装业的发展大大推动了中国国民经济的发展,中国已成为全世界最大的服装生产加工基地。
随着服装市场竞争的加剧,对服装公司实现自动化生产和管理已经成为服装公司生存与发展的必要条件。
1背景由于现车间的服装裁剪工艺落后,各工艺不能很好的协调,加工人员在工作中仍采用手工画样、手工排版及手工裁剪等,各工艺间协调不一致,往往要付出大量的工作时间,然而得到的效率却很低。
为提高服装裁剪效率,减轻加工人员的工作压力,有必要采用一个功能强大、效率很高的自动裁剪设备使服装车间中的前道车间能够更好地为整个服装公司服务。
2采用新设备目的2.1服装生产企业最头疼的是样板间里一大堆的资料,而这些资料时间一长,容易变形或丢失,给管理带来很大混乱,采用电脑CAD系统,则避免了此类问题的发生。
2.2采用PGM电脑服装CAD的系列软件,方便了和客户的直接E-MAIL联系和沟通,大大缩短了彼此沟通的周期。
在同行业竞争中率先得胜。
2.3进一步提高公司信誉度,确保产品质量及交货期,良好维护合作客户关系及开发新客户。
2.4提高产品科技含量,提升产品档次,为增加企业利润带来无形广告效益。
提高人工生产效率,降低人员使用量。
2.5 提高企业使用现代化高科技设备程度,扩大企业在服装领域的竞争实力,更加符合现代化服装企业的发展2.6 自动裁床能提高整个车间的工人人身安全,避免因为手工裁剪机和大块刀片而发生人身伤害3新旧设备工艺对比3.1描版和软件转换功能:使用CAD后:a.发单客户提供现成的样板,来样,可以通过读图板直接读入到打版软件中,再进行放码,排料,打印,非常方便。
b.如果发单客户本身有CAD系统,可直接发E-MAIL过来,在软件中打开,节省了快递的费用及时间。
并保证了纸样的准确性,大大提高效率。
手工打版时:a.要通过手工把发单客户的来样拓下来,放码,排料等,无法避免因手工的操作而带来的误差,从而影响产品质量。
生产产能分析
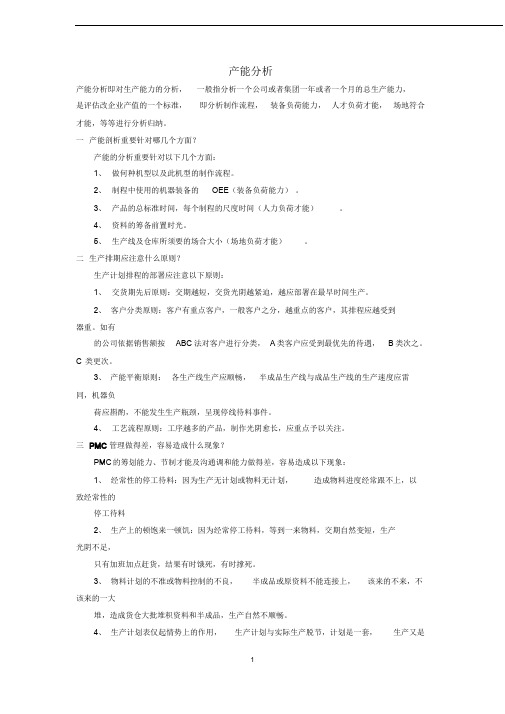
产能分析产能分析即对生产能力的分析,一般指分析一个公司或者集团一年或者一个月的总生产能力,是评估改企业产值的一个标准,即分析制作流程,装备负荷能力,人才负荷才能,场地符合才能,等等进行分析归纳。
一产能剖析重要针对哪几个方面?产能的分析重要针对以下几个方面:1、做何种机型以及此机型的制作流程。
2、制程中使用的机器装备的OEE(装备负荷能力)。
3、产品的总标准时间,每个制程的尺度时间(人力负荷才能)。
4、资料的筹备前置时光。
5、生产线及仓库所须要的场合大小(场地负荷才能)。
二生产排期应注意什么原则?生产计划排程的部署应注意以下原则:1、交货期先后原则:交期越短,交货光阴越紧迫,越应部署在最早时间生产。
2、客户分类原则:客户有重点客户,一般客户之分,越重点的客户,其排程应越受到器重。
如有的公司依据销售额按ABC法对客户进行分类, A 类客户应受到最优先的待遇, B 类次之。
C类更次。
3、产能平衡原则:各生产线生产应顺畅,半成品生产线与成品生产线的生产速度应雷同,机器负荷应斟酌,不能发生生产瓶颈,呈现停线待料事件。
4、工艺流程原则:工序越多的产品,制作光阴愈长,应重点予以关注。
三PMC管理做得差,容易造成什么现象?PMC 的筹划能力、节制才能及沟通调和能力做得差,容易造成以下现象:1、经常性的停工待料:因为生产无计划或物料无计划,造成物料进度经常跟不上,以致经常性的停工待料2、生产上的顿饱来一顿饥:因为经常停工待料,等到一来物料,交期自然变短,生产光阴不足,只有加班加点赶货,结果有时饿死,有时撑死。
3、物料计划的不准或物料控制的不良,半成品或原资料不能连接上,该来的不来,不该来的一大堆,造成货仓大批堆积资料和半成品,生产自然不顺畅。
4、生产计划表仅起情势上的作用,生产计划与实际生产脱节,计划是一套,生产又是一套,生产方案基本不起作用,徒具情势。
5、对销售预测不准或对产能剖析不准,不能针对产能进行合理部署,没有空留余地,生产计划的灵活性不强,生产计划变化频繁,紧迫订单一多,生产计划的执行就成了泡影。
设备OEE培训PPT课件
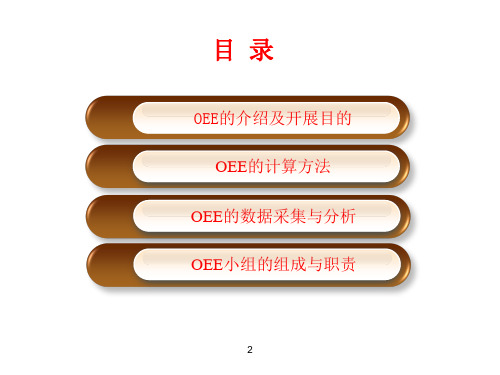
一工厂金工 OEE组长:黄元林
项目责任人 胡楚平
二工厂金工 OEE组长:宋秋阳
一工厂检包 OEE组长:金钱有
19
二工厂检包 OEE组长:刘银火
OEE车间小组结构图
OEE副组长 车间副主任
OEE专员
OEE组员 工程师、领班
1.组长负责整个OEE工作落 实
2.副组长、主管工程师负责 工艺分析与改进方案实施
2.每周进行数据汇总, 分析时间利用率、设 备性能率、产品合格 率指数,找出对应设 备损失
提升步骤
3.针对各项损失做出 改进方案,及时落实 工作
17
四、OEE小组的组成与职责
万丰摩轮设备OEE项目组织结构图
一工厂综合 OEE组长:徐亚忠
一工厂熔铸 OEE组长:张剑辉
二工厂熔铸 OEE组长:陈国云
时间开动率=
* 100%
负荷时间
停
可利用时间
止 损
失 2.空转、间
速
歇停顿
真正利用时间
度 损
失
1.废品、返工
创造价值的
不 良
2.启动、开机
运转时间 损
失
理论循环时间*加工数量
性能开动率=
利用时间
* 100%
加工数量-不合格数量
合格率 =
* 100%
加工数量
10
OEE案例
设某设备某天工作时间为8h, 班前计划停机15min, 故 障停机30min,工装调整25min, 产品的理论加工周期 为0.6 min/件, 一天共加工产品450件, 有20件不合格, 求这台设备的OEE? 根据上面可知: 计划运行时间 =8 x 60 -15 =465 (min) 实际运行时间 =465-30-25=410 (min) 时间开动率 =(410/465)*100%=88.1% 性能开动率 =(450*0.6)/410*100%=65.8% 合格品率 =(450—20)/450*100%=95.5% OEE = 时间开动率x性能开动率x合格品率=55.4%
设备综合效率OEE的分析与改善
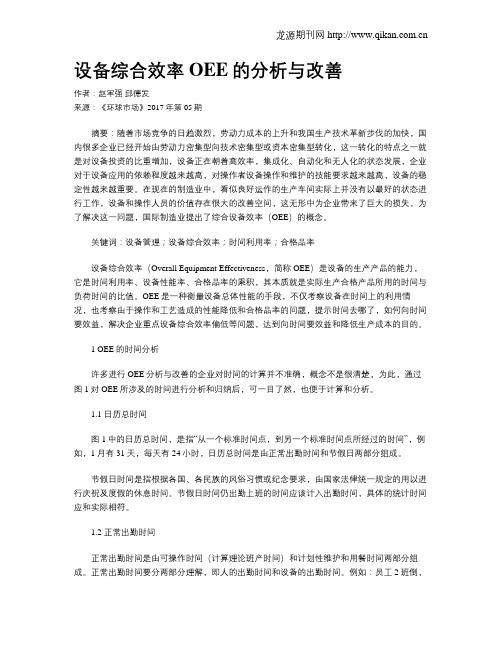
设备综合效率OEE的分析与改善作者:赵军强邱德发来源:《环球市场》2017年第05期摘要:随着市场竞争的日趋激烈,劳动力成本的上升和我国生产技术革新步伐的加快,国内很多企业已经开始由劳动力密集型向技术密集型或资本密集型转化,这一转化的特点之一就是对设备投资的比重增加,设备正在朝着高效率,集成化、自动化和无人化的状态发展,企业对于设备应用的依赖程度越来越高,对操作者设备操作和维护的技能要求越来越高,设备的稳定性越来越重要。
在现在的制造业中,看似良好运作的生产车间实际上并没有以最好的状态进行工作,设备和操作人员的价值存在很大的改善空间,这无形中为企业带来了巨大的损失,为了解决这一问题,国际制造业提出了综合设备效率(OEE)的概念。
关键词:设备管理;设备综合效率;时间利用率;合格品率设备综合效率(Overall Equipment Effectiveness,简称OEE)是设备的生产产品的能力,它是时间利用率、设备性能率、合格品率的乘积,其本质就是实际生产合格产品所用的时间与负荷时间的比值。
OEE是一种衡量设备总体性能的手段,不仅考察设备在时间上的利用情况,也考察由于操作和工艺造成的性能降低和合格品率的问题,提示时间去哪了,如何向时间要效益,解决企业重点设备综合效率偏低等问题,达到向时间要效益和降低生产成本的目的。
1 OEE的时间分析许多进行OEE分析与改善的企业对时间的计算并不准确,概念不是很清楚,为此,通过图1对OEE所涉及的时间进行分析和归纳后,可一目了然,也便于计算和分析。
1.1 日历总时间图1中的日历总时间,是指“从一个标准时间点,到另一个标准时间点所经过的时间”,例如,1月有31天,每天有24小时,日历总时间是由正常出勤时间和节假日两部分组成。
节假日时间是指根据各国、各民族的风俗习惯或纪念要求,由国家法律统一规定的用以进行庆祝及度假的休息时间。
节假日时间仍出勤上班的时间应该计入出勤时间,具体的统计时间应和实际相符。
设备综合效率OEE计算公式和方法
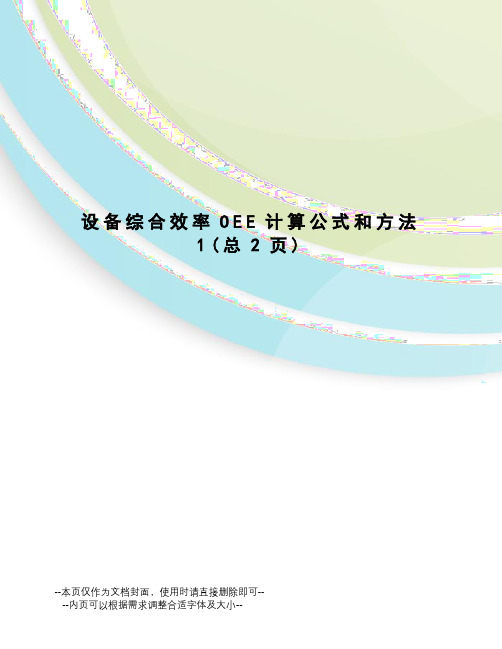
设备综合效率O E E计算公式和方法1(总2页)--本页仅作为文档封面,使用时请直接删除即可----内页可以根据需求调整合适字体及大小--设备综合效率OEE计算公式和方法实例影响设备综合效率的主要原因是停机损失、速度损失和废品损失。
它们分别由时间开动率、性开动率和合格品率反映出来,故得到下面设备综合效率公式:设备综合效率=时间开动率×性能开动率×合格品率这里,负荷时间为规定的作业时间除去每天的停机时间,即负荷时间=总工作时间-计划停机时间工作时间则是负荷时间除去那些非计划停机时间,如故障停机、设备调整和更换刀具、工夹具停机等。
【例1】若总工作时间为8h,班前计划停机时间是20min,而故障停机为20min,安装工夹具时间为20min,调整设备时间为20min。
于是负荷时间=480-20=460min开动时间=460-20-20=400min时间开动率=速度开动率×净开动率这里,理论加工周期是按照标准的加工进给速度计算得到的,而实际的加工周期一般要比理论加工周期长。
开动时间即是设备实际用于加工的时间,也就是工作时间减去计划停机和非计划停机所得时间,或是负荷时间减去非计划停机所得时间。
从计算上看,用简化了的公式也可以得到同样的结果。
之所以用速度开动率和净开动率共同表示性能开动率,是因为从计算过程更容易看出性能开动率的损失原因。
【例2】有400件零件加工,理论加工周期为,实际加工周期为。
则净开动率=×400/400=80%速度开动率==%性能开动率=80%×%=50%【例3】如果仍延用上面的例子,假如设备合格品率为98%,则设备综合效率(全效率)=87%×50%×98%=42. 6%我们把上面的公式和例子总结成以下的序列,得到(A)每天工作时间=60×8=480min。
(B)每天计划停机时间(生产、维修计划、早晨会议等)=20min。
OEE计算案例及其价值介绍
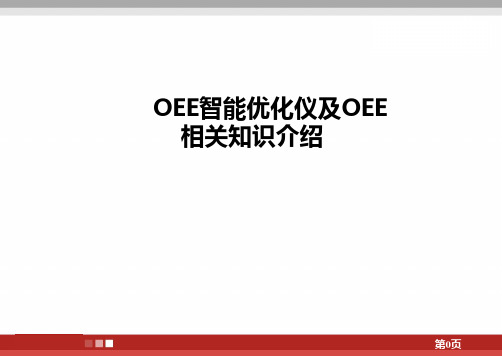
产品质量 低下
OEE衡量的是礁石的大小水平
100%
80% OEE Value
国际先进水平 国内企业
60%
40%
一般管理水平
20%
无管理
0%
第4页
根据文献统计出的各行业OEE水平
行业/设备 钢铁业 化工业 家电制造业 汽车制造业 OEE水平 74% ~ 90% 87% ~ 97% 79% ~ 88% 48% ~ 75%
• OEE指数已成为衡量企业生产效率的重要标准,也是TPM的一个重要手法。
OEE所涵盖的其他 时间损失
传统效率衡量方式 只计算了部分时间 损失
总时间损失
第1页
OEE用在何时?
OEE用于以明确目的有针对性地支持业务目标的实施 – 限制满足客户需求的价值创造流程能力实现的瓶颈机器设 备 – 利用率必须提高的昂贵设备(如注模设备、压铸设备和冲 压设备)
机器运转时间
计划内停工 = 1 小 时 /天 机器故障 = 11.3 小时 换线= 80.5 小时 计划外停工 = 27.4 小时 速度降低 = 12.9 小时 废品 = 50件 返工= 50件
41.8- 12.9 = 28.9
合格品
1000-100 =900
全局设备效率 = 26% x 69% x 90% = 16%
第7页
2. 换线
• 定义:未经调整的全速的由最后一件食品转入第一件新食品的运 作,设备全速运转情况下最后一个良好的旧产品到第一个良好的 新产品间的时间 • OEE优化仪自动统计测量 • 应对措施 – 运用SMED方法即快速换模法来缩短换线时间*(包括运转中 更换原材料,如用新线) – 通过业绩管理来按照标准监控换线时间是否合格 – 实施持续改善行动
自动化机械加工生产线节拍分析
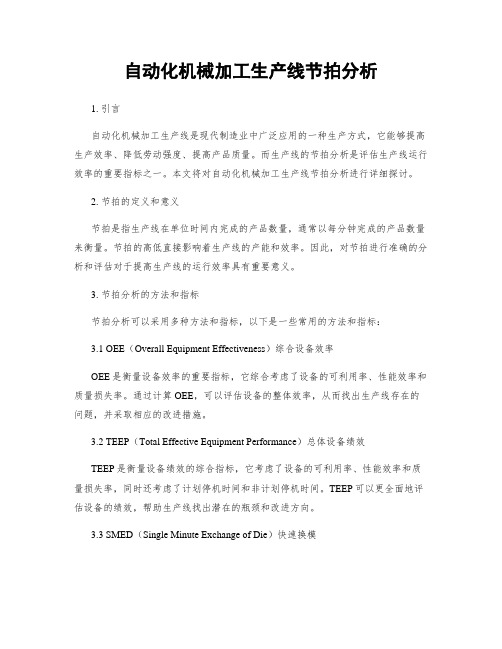
自动化机械加工生产线节拍分析1. 引言自动化机械加工生产线是现代制造业中广泛应用的一种生产方式,它能够提高生产效率、降低劳动强度、提高产品质量。
而生产线的节拍分析是评估生产线运行效率的重要指标之一。
本文将对自动化机械加工生产线节拍分析进行详细探讨。
2. 节拍的定义和意义节拍是指生产线在单位时间内完成的产品数量,通常以每分钟完成的产品数量来衡量。
节拍的高低直接影响着生产线的产能和效率。
因此,对节拍进行准确的分析和评估对于提高生产线的运行效率具有重要意义。
3. 节拍分析的方法和指标节拍分析可以采用多种方法和指标,以下是一些常用的方法和指标:3.1 OEE(Overall Equipment Effectiveness)综合设备效率OEE是衡量设备效率的重要指标,它综合考虑了设备的可利用率、性能效率和质量损失率。
通过计算OEE,可以评估设备的整体效率,从而找出生产线存在的问题,并采取相应的改进措施。
3.2 TEEP(Total Effective Equipment Performance)总体设备绩效TEEP是衡量设备绩效的综合指标,它考虑了设备的可利用率、性能效率和质量损失率,同时还考虑了计划停机时间和非计划停机时间。
TEEP可以更全面地评估设备的绩效,帮助生产线找出潜在的瓶颈和改进方向。
3.3 SMED(Single Minute Exchange of Die)快速换模SMED是一种减少设备换模时间的方法,通过优化设备的换模过程,可以大大缩短换模时间,提高生产线的运行效率。
通过对设备换模时间的分析,可以找出换模过程中的瓶颈和改进点,从而提高生产线的节拍。
3.4 产能利用率产能利用率是衡量生产线产能利用程度的指标,它表示生产线实际产出与理论最大产出之间的比例。
通过分析产能利用率,可以找出生产线存在的产能浪费和瓶颈,从而采取相应的改进措施,提高生产线的节拍。
4. 节拍分析的实施步骤进行节拍分析需要按照以下步骤进行:4.1 收集数据收集生产线的相关数据,包括生产数量、生产时间、设备故障时间、设备换模时间等。
自动裁床产业发展趋势
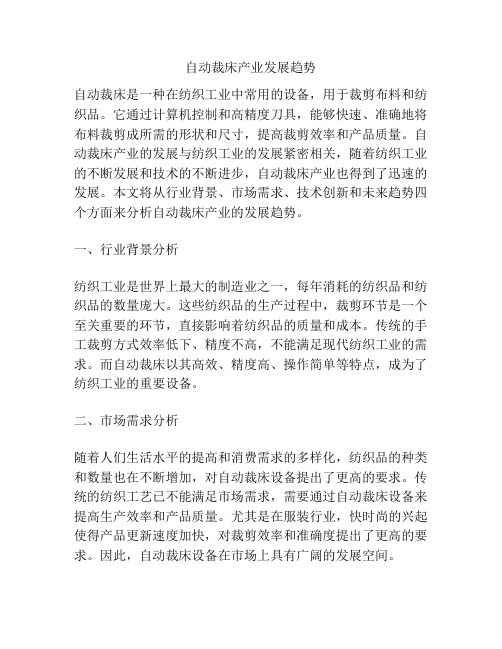
自动裁床产业发展趋势自动裁床是一种在纺织工业中常用的设备,用于裁剪布料和纺织品。
它通过计算机控制和高精度刀具,能够快速、准确地将布料裁剪成所需的形状和尺寸,提高裁剪效率和产品质量。
自动裁床产业的发展与纺织工业的发展紧密相关,随着纺织工业的不断发展和技术的不断进步,自动裁床产业也得到了迅速的发展。
本文将从行业背景、市场需求、技术创新和未来趋势四个方面来分析自动裁床产业的发展趋势。
一、行业背景分析纺织工业是世界上最大的制造业之一,每年消耗的纺织品和纺织品的数量庞大。
这些纺织品的生产过程中,裁剪环节是一个至关重要的环节,直接影响着纺织品的质量和成本。
传统的手工裁剪方式效率低下、精度不高,不能满足现代纺织工业的需求。
而自动裁床以其高效、精度高、操作简单等特点,成为了纺织工业的重要设备。
二、市场需求分析随着人们生活水平的提高和消费需求的多样化,纺织品的种类和数量也在不断增加,对自动裁床设备提出了更高的要求。
传统的纺织工艺已不能满足市场需求,需要通过自动裁床设备来提高生产效率和产品质量。
尤其是在服装行业,快时尚的兴起使得产品更新速度加快,对裁剪效率和准确度提出了更高的要求。
因此,自动裁床设备在市场上具有广阔的发展空间。
三、技术创新分析自动裁床技术是纺织工业中的关键技术之一,随着科技的不断进步和创新,自动裁床设备得到了大幅度的改进和提升。
1. 机械结构创新:传统的自动裁床设备主要采用线条导向运动方式,机械结构相对简单。
随着技术的不断进步,新一代的自动裁床设备采用了伺服电机和精密导轨等先进技术,提高了设备的稳定性和精度。
2. 控制系统创新:传统的自动裁床设备采用的是单机控制系统,操作复杂,容易出错。
现在,先进的自动裁床设备采用了PLC和人机界面等新技术,实现了设备的自动化控制和智能化操作,提高了设备的生产效率和稳定性。
3. 刀具材料创新:传统的自动裁床设备刀具多为硬质合金材料,易磨损,需要频繁更换。
现在,新一代的自动裁床设备采用了特殊的刀具材料,如超硬合金、陶瓷等,具有更长的使用寿命和更高的切削效率。
电控缝纫机自动化生产的成本效益分析与评估
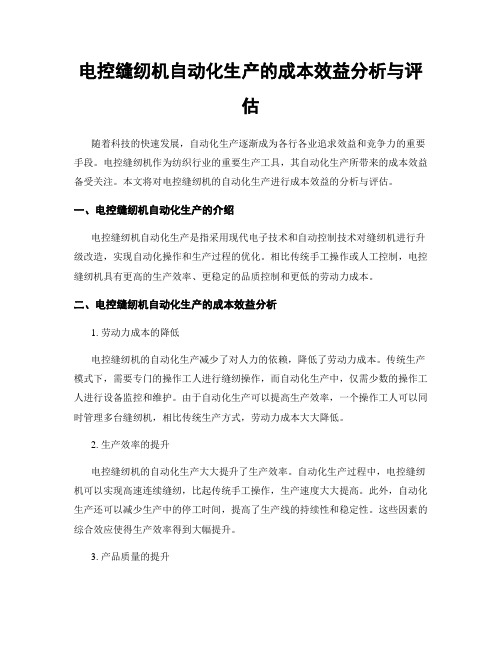
电控缝纫机自动化生产的成本效益分析与评估随着科技的快速发展,自动化生产逐渐成为各行各业追求效益和竞争力的重要手段。
电控缝纫机作为纺织行业的重要生产工具,其自动化生产所带来的成本效益备受关注。
本文将对电控缝纫机的自动化生产进行成本效益的分析与评估。
一、电控缝纫机自动化生产的介绍电控缝纫机自动化生产是指采用现代电子技术和自动控制技术对缝纫机进行升级改造,实现自动化操作和生产过程的优化。
相比传统手工操作或人工控制,电控缝纫机具有更高的生产效率、更稳定的品质控制和更低的劳动力成本。
二、电控缝纫机自动化生产的成本效益分析1. 劳动力成本的降低电控缝纫机的自动化生产减少了对人力的依赖,降低了劳动力成本。
传统生产模式下,需要专门的操作工人进行缝纫操作,而自动化生产中,仅需少数的操作工人进行设备监控和维护。
由于自动化生产可以提高生产效率,一个操作工人可以同时管理多台缝纫机,相比传统生产方式,劳动力成本大大降低。
2. 生产效率的提升电控缝纫机的自动化生产大大提升了生产效率。
自动化生产过程中,电控缝纫机可以实现高速连续缝纫,比起传统手工操作,生产速度大大提高。
此外,自动化生产还可以减少生产中的停工时间,提高了生产线的持续性和稳定性。
这些因素的综合效应使得生产效率得到大幅提升。
3. 产品质量的提升电控缝纫机的自动化生产可以通过精确的控制系统实现高质量的生产。
传统生产方式下,由于人工操作的不确定性,产品质量难以保证。
而自动化生产中,电控缝纫机可以通过精确的设定和监控,实现一致性和稳定性的生产,提高产品的质量和一致性。
4. 维护成本的降低电控缝纫机的自动化生产降低了设备维护的成本。
自动化生产中,电控缝纫机可以实现自动检测和报警系统,及时发现设备故障并进行维修和保养。
相比传统生产方式下,自动化系统的维护更加简便方便,大大降低了设备维修和保养的成本。
三、电控缝纫机自动化生产的评估1. 投资回报率电控缝纫机的自动化生产需要一定的投资成本。
自动裁床OEE与产能分析共25页文档
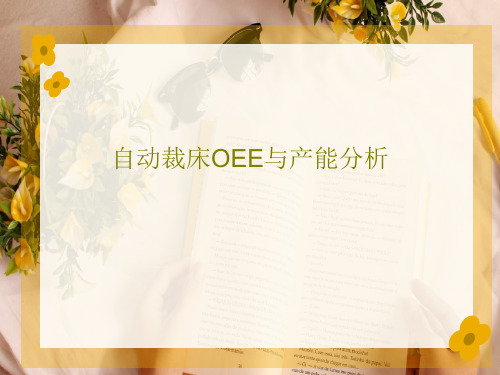
45、自己的饭量自己知道。——苏联
1
0
、
倚
南
窗
以
寄
傲
,
安
。
41、学问是异常珍贵的东西,从任何源泉吸 收都不可耻。——阿卜·日·法拉兹
42、只有在人群中间,才能认识自 己。——德国
43、重复别人所说的话,只需要教育; 而要挑战别人所说的话,则需要头脑。—— 玛丽·佩蒂博恩·普尔
文 家 。汉 族 ,东 晋 浔阳 柴桑 人 (今 江西 九江 ) 。曾 做过 几 年小 官, 后辞 官 回家 ,从 此 隐居 ,田 园生 活 是陶 渊明 诗 的主 要题 材, 相 关作 品有 《饮 酒 》 、 《 归 园 田 居 》 、 《 桃花 源 记 》 、 《 五 柳先 生 传 》 、 《 归 去来 兮 辞 》 等 。
自动裁床OEE与产能分析
6
、
露
凝
无
游
氛
,
天
高
风
景
澈
。
7、翩翩新 来燕,双双入我庐 ,先巢故尚在,相 将还旧居。
8
、
吁
嗟
身
后
名
,
于
我
若
浮
烟
。
9、 陶渊 明( 约 365年 —427年 ),字 元亮, (又 一说名 潜,字 渊明 )号五 柳先生 ,私 谥“靖 节”, 东晋 末期南 朝宋初 期诗 人、文 学家、 辞赋 家、散
基于工作抽样的OEE分析在缝纫线生产管理中的应用
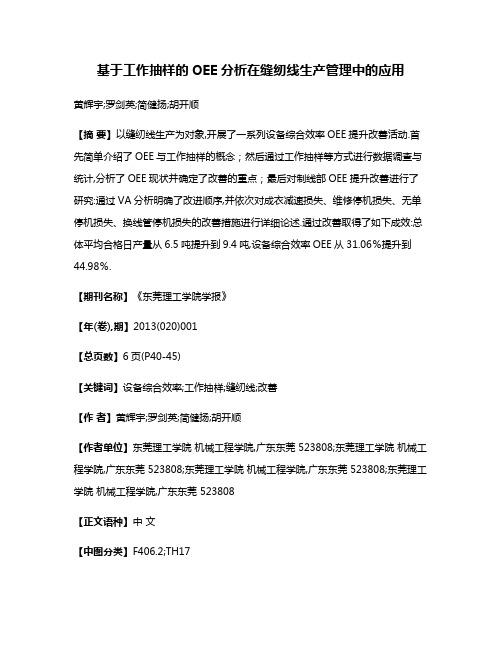
基于工作抽样的OEE分析在缝纫线生产管理中的应用黄辉宇;罗剑英;简健扬;胡开顺【摘要】以缝纫线生产为对象,开展了一系列设备综合效率OEE提升改善活动.首先简单介绍了OEE与工作抽样的概念;然后通过工作抽样等方式进行数据调查与统计,分析了OEE现状并确定了改善的重点;最后对制线部OEE提升改善进行了研究:通过VA分析明确了改进顺序,并依次对成衣减速损失、维修停机损失、无单停机损失、换线管停机损失的改善措施进行详细论述.通过改善取得了如下成效:总体平均合格日产量从6.5吨提升到9.4吨,设备综合效率OEE从31.06%提升到44.98%.【期刊名称】《东莞理工学院学报》【年(卷),期】2013(020)001【总页数】6页(P40-45)【关键词】设备综合效率;工作抽样;缝纫线;改善【作者】黄辉宇;罗剑英;简健扬;胡开顺【作者单位】东莞理工学院机械工程学院,广东东莞 523808;东莞理工学院机械工程学院,广东东莞 523808;东莞理工学院机械工程学院,广东东莞 523808;东莞理工学院机械工程学院,广东东莞 523808【正文语种】中文【中图分类】F406.2;TH17设备综合效率 (Overall Equipment Efficiency,OEE)于1999年由SEMT组织提出,起源于日本汽车行业。
由于实行OEE分析有助于帮助企业降低设备故障和维修成本,延长设备的使用寿命,提高劳动者的工作效率,解决工序上的瓶颈问题,提升产品质量和降低返修率,减少不必要的制造成本,最终提高企业的整体效益[1],因此该技术逐渐从日本推广到欧美,应用范围含盖了通信设备、电子、医药、化工、食品加工等制造行业。
近年来,OEE分析技术在国内制造企业中也逐渐被推广应用,但总体应用水平远不及发达国家。
缝纫线行业属于传统制造行业,竞争环境激烈,成本敏感性高,同时由于其机器自动化程度高,对机器设备利用率要求较高,因此对OEE分析在缝纫线生产管理中的应用进行研究具有重要意义。
- 1、下载文档前请自行甄别文档内容的完整性,平台不提供额外的编辑、内容补充、找答案等附加服务。
- 2、"仅部分预览"的文档,不可在线预览部分如存在完整性等问题,可反馈申请退款(可完整预览的文档不适用该条件!)。
- 3、如文档侵犯您的权益,请联系客服反馈,我们会尽快为您处理(人工客服工作时间:9:00-18:30)。
日产 能提 高率
14% 18.5% 15% 17% 23.3% 18% 20.8% 18%
影响裁床OEE的因素
4.单独裁剪不成台套的面套(配套面套),不能 充分发挥裁床的效率,从而影响性能效率
不成台套的面套的裁剪,同样需经过上料、铺料、裁剪 等所有的工序流程,因此所需生产工时与成套裁剪相同 或略低,但由于一般用料长度短,层数少,不能充分发 挥裁床的利用率
OEE是衡量生产设备使用效率的一个综合指标 是衡量生产设备使用效率的一个综合指标 OEE=设备可利用率×性能效率×产品合格率×100% 设备可利用率=实际运行时间/可运行时间×100% 性能效率=理想循环时间×总工件数/实际运行时间 ×100% 产品合格率=(总工件数—有缺陷工件数)/总工件数×100% 理想循环时间: 理想循环时间: 是指在理想状态下(设备完好,原料合格, 是指在理想状态下(设备完好,原料合格,生产过 程无停顿,操作熟练, 程无停顿,操作熟练,无非工艺要求的操作时间浪费和 多余动作), ),生产出一件合格产品或完成一道工序所需 多余动作),生产出一件合格产品或完成一道工序所需 的最少时间。 的最少时间。
一版中裁片越多、排版长度越长, 一版中裁片越多、排版长度越长,堵料时间越长;
平均每版裁剪因堵料造成延迟1~2分钟,一天平均延迟 10~30分钟
提高裁床OEE的措施
1.在时间允许的情况下,要求采用面料预铺; 2.对于物流投料,物流人员应及时跟踪生产信息,保证 投料到位; 3 .车间铺料工可根据车间铺料看板,了解需铺面料品种、 数量及铺料顺序,预先发现可能短缺的面料,及时通知 仓库; 4 .尽可能减少不成套的面套裁剪的次数,或可将订单安 排在生产任务较少时进行; 5 .物流部下生产订单,应尽量下20倍数的产量,以充分 提高裁床的效率; 6 .适当提高裁床运行速度; 7 .采用较宽垫纸,以减少加垫纸的工作量;
26 %
J116 双排
面 料 60 14 38
37 %
J116 单排
面 料 40 6 18
50 %
J116 一排半
面 料 20 5 26
19 %
J117 五座
04款 全顺
全顺17 座
面 料 40 11 40
27.5 %
平 均 值
边 料 80 15 56
26.7 %
边 料 80 8 29
27.5 %
边 料 60 15 42
全顺17座边料铺料发生皱折
铺布异常情况及处理
割面料外包装袋
处理面料断头
铺布异常情况及处理
面料须边卷入铺布机中
处理面料须边
影响裁床OEE的因素
2.裁床操作工的辅助工作多,影响裁床可 利用率
裁床操作工的工作流程和所需时间比率
送料3% 送料 整料8% 整料 (推料入裁床) (铺塑料覆膜、两侧加铺垫纸、开吸风)
◆铺布机故障及面料缺陷造成铺布与裁剪等待
铺布机故障、面料色差、皱折等(见图)
结论:根据测算,铺布工每天平均需花1~2小时处理出 结论:根据测算,铺布工每天平均需花 小时处理出
现的各种异常情况。 现的各种异常情况。
铺布异常情况及处理 待料
铺布异常情况及处理
04款面料(包括17座、J116边料)产生须边
自动裁床OEE值提升报告 值提升报告 自动裁床
问题提出:
自公司投入自动裁床进行生产以来,相 比于手工裁剪,有其自动化程度高,裁剪质 量稳定,浪费率低的优点,但如何进一步提 高其OEE和生产效率,以更好地发挥自动裁 床在生产中的作用,挖掘设备的潜力,是我 们需要努力的主要方向。
OEE——设备总效率
影响裁床OEE的因素
5.一次裁剪的面套台套数如果不成20倍数,则不 能发挥裁床的效率,倍数越高,性能效率越高
不同铺版方式裁剪时间对照表
可裁最 大层数 PK 面料 五十铃单 排面料 20 20 20 20 每层 台套 2 3 2 2 一次铺 一次裁剪 裁剪时 平均单台 版量(版) 最大台套 间(分) 时间(秒) 1 2 1 2 40 120 40 80 7.5 18 .5 8 14 11 .25 9 .25 12 10 .5
52 7
22 16
27 15
14 4
18 8
16 10
9 12
13 21 20 49 5 1 4 19
46 6
49 3
铺布时间长的原因
1。铺布操作工的辅助工作占据时间过长; 铺布生产工序:
上料 整料 输入数据 铺料 推料至裁床
(循环3~5次/版)
2。铺布工序异常事件多,需花额外时间处理;
异常事件 割面料包装袋 通知缺料并等待 判断并处理设备异常 处理面料圈动松驰 处理面料断头 清理面料须边 处理其他面料缺陷 (色差、面料皱折) 发生的频度 3~5个/版 1~5次/月 1~3次/周 1~5次/天 经常/每天
从表中可以看出,一次裁剪的台套数越大,铺布和裁剪的工作量越 少,裁剪效率越高。
影响裁床OEE的因素
6.分捡裁片的速度跟不上裁剪,造成裁剪堵料,使 裁床停机等待,影响裁床生产效率
在裁剪04款全顺等面套时,由于一版中的裁片(特别是小 裁片)多,分捡裁片所需时间长,无法及时清空裁床,造 成堵料,延迟了下一版面料送入裁床的工序
5月 性能效率
6月 58 % 73.5 % 100% 42.6 %
6月 合格率
7月 49.8 % 71.7 % 100% 35.7 %
7月 OEE
8月 59 % 69.5 % 100% 41 %
8月
平均值 52.6% 75.9% 100% 39.8%
自动裁床运行时间测定表
作业日期:9月19日
项 车 型 PK 边料 80/20 豪华 面料 10/10 14 座 边料 10/10 五十 铃单 排 J116 一排 半 J116 单排 面料 80/20 0.4 边料 80/20 面料 20/10 0.45 边料 20/20 面料 40/20 0.4 边料 40/20 面料 20/20 1.8 边料 20/20 12 座 面料 20/20 1.1 边料 20/20 J117 五座 面料 20/20 0.8 边料 20/20 176 14 332 1 21 2 20 2 25 2 16 7 47 4 2 21 473 70.2% 53% 100% 37.2% 39 8 1 1 1 1 2 2 1 1 2 46 13 64.7% 72.7% 100% 47.1% 35 27 1 2 1 1 1 2 0.5 1 *10 48.5 33 83.5% 33.3% 100% 27.8% 10 16 2 1.5 1 1 1 1.5 0.5 1 3 #25 17.5 46 54% 70.6% 100% 38.1% * 铺料皱折 # 缺面料 5 8 1 1 1 1 1 1.5 1 1 1 9 13.5 59.3% 88.9% 100% 52.7% 40 9 2 1 1.5 1.5 2 1 1 1 5 2 0.5 52 15.5 57.1% 64% 100% 36.6% 1.3 42 10 2 1 1.5 1 2 1 1 1 5 48.5 19 70.4% 64% 100% 45.1% 目 台套/ 台套 理想 循环 层 时间 裁床 运行 时间 10 0.4 44 15 1 1.5 2 1 2.5 1.5 0.5 1 4 1 55 20 83.2% 22.8% 100% 18.9% 样板 设置 1 拖料 1 整料 1 后 整理 1 停机时间 零件 设备 清理 保养 /更换 更换 设备 故障 应运 可利用 性能效 合格率 OEE 行时 率 率 间 15.5 25.5% 59.3% 100% 15.1% 备 注
调样板程序6%(输入程序、对四边、等待程序运行) 调样板程序 自动裁剪70% 自动裁剪 后整理5% (送料至捡料台、收薄膜和垫纸、记录数据) 后整理 裁床清理1% (清理裁头、换刀等) 裁床清理
操作工加铺垫纸
纸宽1.86米
两种不同宽度的裁剪垫纸
纸宽1.80米
两侧加铺垫纸的原因:
由于垫纸的宽度(1.80M)比裁床有效裁剪宽度(1.83M) 小,裁剪时,由于吸风作用,面料表面的塑料薄膜会被 吸进裁床的齿形压板内,造成运行故障
时间/平 均每台套 PK 120单排 J116双排 J117五座 04款15座 全顺17座 物流车 平均值 0.82分钟 0.89分钟 0.77分钟 1.7分钟 4分钟 3.5分钟 1.75分钟 台套/ 8小时 586 540 626 282 120 137 274 时间/平 均每台套 0.67分钟 0.75分钟 0.66分钟 1.45分钟 3.25分钟 2.95分钟 1.45分钟 台套/ 8小时 668 640 720 330 148 162 331
铺04款全顺面料与17座 及J116边料
产生的后果 停机 可能停机 停机 停机 停机 停机 停机
所需处理时间 0.5~1分钟/个 30~40分钟/次 >10分钟/次 1~4分钟/次 1~3分钟/次 >5分钟/次 >15分钟/次
不经常
影响裁床OEE的因素
◆物流面料投料不及时,造成铺料和裁剪等待
操作工处理缺料程序: 操作工处理缺料程序: 操作工发现缺料 通知大班长(或投料工) 大班长通知仓库 仓库安排人员投料 面料 投至生产现场 整个过程所需时间一般不会低于30~40分钟
面料最大 裁床有效可 橡胶压 裁剪宽度 裁剪宽度 皮宽 <175 183 9 裁剪垫 纸宽 186 180 措施 可一侧加垫纸 有时需两侧加垫纸
根据现场测试,避免此问题产生的条件是:
垫纸的宽度至少比裁床有效裁剪宽度每侧宽3公分
影响裁床OEE的因素
3.裁剪运行速度越低,性能效率越低
提高裁床运行速度对裁剪产能的影响对比表(不考虑裁剪待料时间) 现有裁剪速度35 裁剪速度提至45
时间单位:分钟
待料
堵料 1.5