066 攀钢高炉炉前综合技术开发
攀钢开发高炉应用捣固焦技术

攀钢开发高炉应用捣固焦技术
由攀研院、攀钢钒等单位共同研究开发的“捣固焦炭在攀钢高炉上的应用技术研究”项目,日前在成都通过了四川省科技厅组织的技术鉴定。
专家鉴定认为,访项研究成果达到了国内先进水平。
研究高炉应用捣同焦炭技术,是攀钢应对焦煤资源日趋紧张状况,扩大炼焦煤资源适应性的一条重要技术途径。
为此,攀钢专门成立了技术开发项目组。
项目组科技人员针对捣固焦炭取代顶装焦炭后,堆密度增加、气孔率降低,给高炉操作调节带来的诸多问题,对捣固焦炭使用后高炉上下部操作参数变化、不同比例的捣固焦炭对高炉料柱透气性的影响规律、配加不同比例的捣固焦炭对高炉主要技术经济指标的影响规律等方面进行了深入实验研究;总结分析了高炉应用捣固焦炭操作特点,通过采取多项技术措施,取得了捣固焦炭在攀钢钒1、2、3号高炉的成功应用.形成了攀钢高炉应用捣固焦炭的核心技术。
该项目研究成果在高炉应用后,高炉路况稳定运行,仅1号高炉每天的产量就增加了49.5t,焦比降低了14.4kg/t,煤比增加了12 kg/t,具有显著的经济效益。
有关专家指出,该项目的成功实施,不仅使攀钢高炉取得了明显
的增铁节焦效果,而且扩大了攀钢炼焦煤资源适应性,提高了市场竞争力,对今后在大型钢铁联合企业采用捣固炼焦技术及捣固焦炭在高炉上的应用具有较好的借鉴意义。
攀钢1750m3高炉高焦丁比生产实践
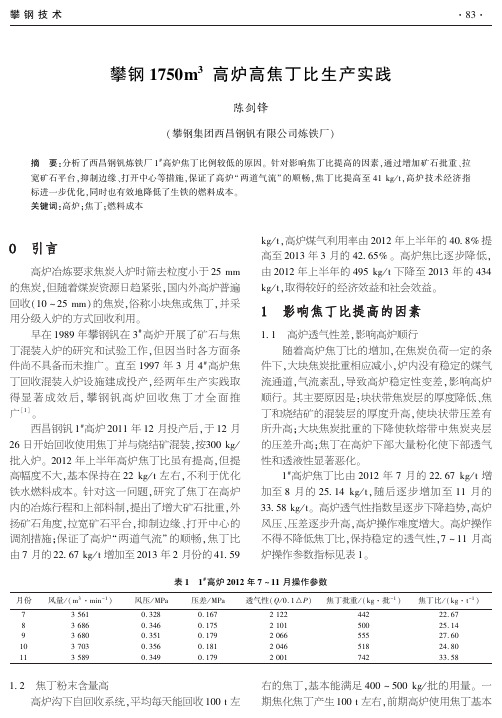
攀钢1750m3高炉高焦丁比生产实践陈剑锋(攀钢集团西昌钢钒有限公司炼铁厂)摘 要:分析了西昌钢钒炼铁厂1#高炉焦丁比例较低的原因㊂针对影响焦丁比提高的因素,通过增加矿石批重㊁拉宽矿石平台,抑制边缘㊁打开中心等措施,保证了高炉 两道气流”的顺畅,焦丁比提高至41kg/t,高炉技术经济指标进一步优化,同时也有效地降低了生铁的燃料成本㊂关键词:高炉;焦丁;燃料成本0 引言 高炉冶炼要求焦炭入炉时筛去粒度小于25mm 的焦炭,但随着煤炭资源日趋紧张,国内外高炉普遍回收(10~25mm)的焦炭,俗称小块焦或焦丁,并采用分级入炉的方式回收利用㊂早在1989年攀钢钒在3#高炉开展了矿石与焦丁混装入炉的研究和试验工作,但因当时各方面条件尚不具备而未推广㊂直至1997年3月4#高炉焦丁回收混装入炉设施建成投产,经两年生产实践取得显著成效后,攀钢钒高炉回收焦丁才全面推广[1]㊂西昌钢钒1#高炉2011年12月投产后,于12月26日开始回收使用焦丁并与烧结矿混装,按300kg/批入炉㊂2012年上半年高炉焦丁比虽有提高,但提高幅度不大,基本保持在22kg/t左右,不利于优化铁水燃料成本㊂针对这一问题,研究了焦丁在高炉内的冶炼行程和上部料制,提出了增大矿石批重,外扬矿石角度,拉宽矿石平台,抑制边缘㊁打开中心的调剂措施;保证了高炉 两道气流”的顺畅,焦丁比由7月的22.67kg/t增加至2013年2月份的41.59kg/t,高炉煤气利用率由2012年上半年的40.8%提高至2013年3月的42.65%㊂高炉焦比逐步降低,由2012年上半年的495kg/t下降至2013年的434 kg/t,取得较好的经济效益和社会效益㊂1 影响焦丁比提高的因素1.1 高炉透气性差,影响高炉顺行随着高炉焦丁比的增加,在焦炭负荷一定的条件下,大块焦炭批重相应减小,炉内没有稳定的煤气流通道,气流紊乱,导致高炉稳定性变差,影响高炉顺行㊂其主要原因是:块状带焦炭层的厚度降低㊁焦丁和烧结矿的混装层的厚度升高,使块状带压差有所升高;大块焦炭批重的下降使软熔带中焦炭夹层的压差升高;焦丁在高炉下部大量粉化使下部透气性和透液性显著恶化㊂1#高炉焦丁比由2012年7月的22.67kg/t增加至8月的25.14kg/t,随后逐步增加至11月的33.58kg/t㊂高炉透气性指数呈逐步下降趋势,高炉风压㊁压差逐步升高,高炉操作难度增大㊂高炉操作不得不降低焦丁比,保持稳定的透气性,7~11月高炉操作参数指标见表1㊂表1 1#高炉2012年7~11月操作参数月份风量/(m3㊃min-1)风压/MPa压差/MPa透气性(Q/0.1△P)焦丁批重/(kg㊃批-1)焦丁比/(kg㊃t-1) 735610.3280.167212244222.67 836860.3460.175210150025.14 936800.3510.179206655527.60 1037030.3560.181204651824.80 1135890.3490.179200174233.581.2 焦丁粉末含量高高炉沟下自回收系统,平均每天能回收100t左右的焦丁,基本能满足400~500kg/批的用量㊂一期焦化焦丁产生100t左右,前期高炉使用焦丁基本㊃38㊃攀钢技术采取搭配使用㊂由于焦化焦丁筛维护力度不够,导致焦丁中粉末含量升高,正常时焦化焦丁粉末在3%~6%,最高达20%以上㊂高炉布料时,将大部分焦丁粉末吹走,进入高炉重力除尘器中,导致瓦斯灰中C含量增加,造成碳资源直接浪费㊂同时高炉在使用焦丁时,焦丁代替焦炭计算焦炭负荷,粉末被吹走后,焦炭负荷增大,导致高炉炉温波动,影响高炉顺行㊂高炉被迫中断使用焦化所产焦丁,导致焦丁比下降㊂2 采取的措施2.1 优化上部料制2.1.1 增加矿石批重1#高炉采用焦丁混入烧结矿中入炉,称料时先称烧结矿进入称量斗,后称焦丁进入称量斗,称量完成后统一排料,在排料过程中可以起到混匀的作用㊂采用与烧结矿混装入炉方式,由于焦丁粒度组成与烧结矿相近(见表2),混装后有利于提高炉料间空隙度,改善块状带矿石层的透气性㊂烧结矿有较好的高温冶金性能,增加煤气流与焦丁的接触量,利于焦丁在炉内中上部消化,防止增加焦粉末进入炉缸,恶化工作环境㊂表2摇焦丁与烧结矿粒度组成粒度/mm焦丁/%烧结矿/%粒度/mm焦丁/%烧结矿/% <5 2.0820~4076.533.70 <10824.31>400.697.54 10~2014.8132.78 但是随着焦丁量的逐步增加,在焦炭负荷一定的情况下,相应减小大块焦量,进入软熔带时,大块焦窗相应变薄,导致焦窗透气性变差㊂为保持大块焦焦窗厚度相应不变,增加矿石批重有利于提高大块焦焦窗厚度,保持焦窗良好的透气性㊂1#高炉矿石批重由2012年4月的40.4t逐步增加至2013年3月的44.0t,高炉透气性指数由2067上升至2237,焦丁比逐步提高㊂2.1.2 外扬角度,拉宽矿石平台随着焦丁比的逐步增加,高炉软熔带大块焦窗相应变薄,煤气流通过软熔带阻力增加,气流向软熔带边沿发展,造成边沿气流增强,炉喉温度上升, 2012年7月焦丁比为442kg/批,平均炉喉温度为60℃,2012年8月焦丁比为500kg/批,平均炉喉温度为80℃,炉喉温度上升20℃㊂为此,高炉采取逐渐外扬角度的措施(见图1)㊂图1 高炉外扬角措施 矿石外角由37°增加至39°,矿石平台由5.5°拉宽至6.5°,并且加重了矿石边沿圈数,由2圈增加至3圈,同时减少了焦炭边沿圈数,由4圈减至1圈㊂9月份平均炉喉温度由100℃左右下降至月底60℃左右㊂如图2所示,高炉边缘气流得到了有效地抑制,且气流平稳无开叉现象,同时增加矿㊁焦内角差,疏导中心气流,保证了高炉 两道气流”的顺畅㊂高炉保持了稳定顺行,高炉料柱透气性㊁高炉煤气利用率得到提高,也相应增加了焦丁比,焦丁比由7月的22.67kg/t增加至2013年2月份的41.59kg/t㊂2.2 降低焦丁粉末含量针对焦化供焦丁粉末含量高的问题,加强与焦化之间的调度联系,及时了解焦化焦丁的产量和实物质量㊂加强岗位操作管理,提升岗位责任心,当皮带系统转焦丁时,实行定点观察焦丁粉末情况,发现问题及时上报调度室㊂调度室联系派出工艺管理人员对焦丁粉末进行跟踪,粉末较高时,延伸到焦化筛分楼处查看焦丁筛子情况,发现筛子间距增大或破损时,联系焦化及时更换筛子㊂同时联系技术质量部㊁焦化等单位,对焦丁进行三家联合取样,分析焦丁粉末含量,督促焦化加强焦丁筛子的管理,减少焦丁粉末含量㊂同时高炉根据焦丁粉末含量,及时调整焦化焦丁的比例,并相应调整焦炭负荷,减小焦丁粉末对高炉顺行的影响㊂2.3 加强沟下监控力度高炉沟下设置有沟下工作人员,加强其岗位责任心,及时观察焦丁质量情况,发现粉末升高时,及时通知高炉操作人员,并取一部分焦丁到高炉操作室,观察其实物质量,让高炉操作者提前做好应对措施㊂㊃48㊃2013年第36卷第5期图2 2012年9月份炉喉温度曲线 同时加强取样分析频次,由原来一个班1次分析,增加到2~3次分析,并及时上传分析结果至MES系统,实现分析结果互享㊂3 取得效果 高炉软熔带是高炉压差损失最大的部位,占料柱总阻损的50%以上,当炉料开始软化,随着体积的收缩,空隙度不断下降,煤气通过时阻损将急剧上升㊂焦丁与烧结矿混装后,改变了原来矿石软熔层不透气的局面,起到了增大 焦窗”的作用;同时,焦丁粒度小,在炉内优先参与熔损反应,减少大块焦的熔损率,使风口焦的平均粒度增大,炉缸的焦炭强度提高,大块焦炭仍保持着良好的料柱骨架作用,从而也降低了高炉滴落带压差,改善煤气流分布,提高高炉透气性;焦丁与烧结矿接触良好,焦丁熔损时产生的CO与矿石发生还原反应,这既强化了煤气的作用,减少了直接还原耗炭,又有利于传热㊁传质和化学反应[2]㊂随着焦丁比的逐步增加,高炉煤气利用率得到提高,焦比逐渐降低,见表3㊂表3 1#高炉焦丁比提高后的技术经济指标时间产量/t焦比/(kg㊃t-1)焦丁量/(kg㊃批-1)焦丁比/(kg㊃t-1)煤气利用/%提高前2012年1~7月119980495.4940022.6740.8提高后2012年8~10月125520490.052025.1441.2 2012年11月124642493.1474233.5841.72012年12月106034492.1889234.7942.22013年2月118479444.3094841.5942.602013年3月129577434.6594141.2342.65平均120850.4470.854808.635.2742.07 备注:指标统计扣除2012年2月与2013年1月㊂4 结语 1)随着焦炭资源紧张,提高高炉焦丁比成为高炉节约燃料成本的有效途径㊂2)通过优化上部料制,确保了高炉长期稳定顺行㊂结合高炉自身情况,采取增大矿石批重㊁拉宽矿石平台㊁外扬角度等措施,保证了高炉 两道气流”的稳定,提高了煤气利用率,实现了高炉焦丁比的提高,大幅度地降低了高炉焦比㊂西昌钢钒1#高炉目前焦丁比达到41kg/t,焦比降至430kg/t,主要经济技术指标达到了较高水平㊂参考文献[1] 刁日升,刘树芳,吴志远.攀钢高炉焦丁混装入炉生产实践[J].钢铁钒钛,2000.[2] 孙伟铭,余乐安.高炉焦丁混装入炉的效果与探索[J].浙江冶金,2008.编辑 余文华收稿日期:2013-08-15㊃58㊃攀钢技术。
攀钢2号高炉顺利开炉与快速达产

BLOW IN SM OOTHLY AND FASTLY OF NO .2 BF AT PAN ZH IH UA IRO N & STEEL GRO UP CO .
Liu Tianwei (Panzhihua New steel and vanadium limit Co.iron plant)
2 开炉 措施
2.1 安装烘炉吹管 ,提高烘炉风量 在高炉烘炉前 ,在 18个风 口中均匀选择 4个风 口和 5个风口分别安装炉底送风点火吹管和烘炉吹 管,这样做有利于加快对高炉炉底砖衬的烘烤。烘 炉以测定炉顶废气湿度为准 ,当炉顶废气湿度与大 气湿度相等时 ,烘炉达到要求 。起初的烘炉原则是 : 在控制炉顶温度≤350℃ 的情况下尽可能采用较大 风量 ,目的在风速、风量较大的情 况下加强热传导, 以便带入 炉内较多 的热量 和从炉 内带走较多的水 份 ,从而缩短烘炉时间。原计划烘炉 84小时,但为 了加快烘炉进度 ,在前 48小时严 格控制0 200 l00
炉 、达 产有着 十 分 重 要 的 意 义 。此 次开 炉 在 总结 历 次开炉总焦 比及近期原燃料质量变化的基础上 ,经 过多种方法的计算与 比较 ,最后确定 了总焦 比及后 续料负荷。待炉况和设 备运 转正 常后 ,逐渐增加焦 炭负荷。按此总焦 比开炉后 ,炉温合适 ,渣铁畅流, 为加快开炉进程打下了坚实的基础 。与冶炼普通矿 不 同的是冶炼 高钛 型钒 钛 矿在 高炉 开炉后 要进行料
O 5 1O 15 25 3O 35 40 45 50 55 60 65 7O 75 80 84
制转换 ,即采用 100%天然块矿开炉逐步过渡到配
图 1 二 高 炉扩 大 性 小 修 烘 炉 曲 线
攀钢高炉开铁口机技术进步

作者简介 : 芳 , 刘树 教高 ; 联系 电话 :8239 0 4 0 1.3 12
维普资讯
四川冶金
第2 9卷
一
能够根据高炉在各个时期炉缸、 炉底的侵蚀情况在 定范 围 内调 节 。
() 2 打开 出铁 口时 , 覆盖 在 出铁 口 区域 炉 缸 内
构——采用 C Q 20 H M 00型冲击钻机 , 具有钻削、 正 向冲打的功能; 操作系统——通过手动阀操作 。 由于设备停放位置影 响炉前安全作业等问题 ,
通过 加 长转臂 , 旋转气 缸 改油 缸 , 消折叠 气 马达 等 取
壁上 的耐火 泥层 ( 俗称 泥包 ) 应 被破 坏 , 不 使铁 口长 期处 于 良好 的工作 状态 。
攀钢2 #、3 #高炉新增热风炉的自动控制简介
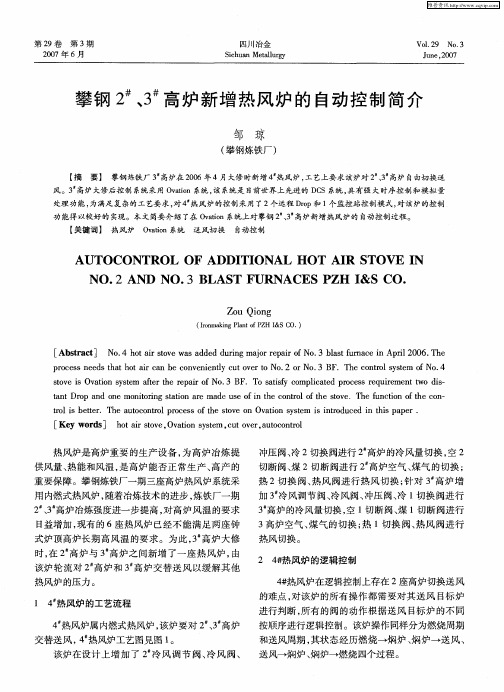
按顺序进行逻辑控制。该炉操作同样分为燃烧周期
和送风 周期 , 状 态 经历 燃 烧 一 焖 炉 、 炉 一 送 风 、 其 焖 送 风一 焖 炉 、 炉一 燃烧 四个 过程 。 焖
该炉在设计上增加 了 2 冷风调 节 阀、 冷风 阀、
处 理 功 能 , 满 足 复 杂 的 工 艺要 求 , 4 热 风 炉 的控 制 采 用 了 2个 远 程 D o 为 对 rp和 1个 监 控 站 控 制 模 式 , 该 炉 的控 制 对
功 能得 以较好 的实现 。本 文简要介 绍 了在 O  ̄o vi n系统上对攀钢 2 、 3 高炉新增热风 炉的 自动控 制过 程。
邹 琼
( 攀钢 炼铁 厂 )
【 摘 要 】 攀钢炼铁厂 3高炉在 20 年 4月 大修 时新增 4热风 炉, 06 工艺上要 求该炉对 2、 高炉 自由切换送 3
风。3 高炉大修后控制 系统采 用 O a o vt n系统 , 系统是 目前世界 上先进的 D S系统 , i 该 C 具有强 大时序控 制和模 拟量
用 内燃 式热 风炉 , 随着 冶炼 技术 的进 步 , 铁 厂一期 炼
冲压阀、 2 冷 切换阀进行 2高炉 的冷风量切换 , 2 空 切断阀、 2 煤 切断 阀进行 2高炉空气、 煤气的切换 ;
热 2切 换 阀 、 风 阀 进 行 热 风 切换 ; 对 3 高炉 增 热 针 加 3冷 风调 节 阀、 风 阀 、 冷 冲压 阀、 l 换 阀进行 冷 切 3高 炉 的冷风 量 切换 , l 断 阀 、 l切 断 阀进 行 空 切 煤
【 关键词 】 热风炉
O ao 统 vi tn系
送 风切 换 自动控 制
攀钢2号高炉优化操作实践

攀钢2号高炉优化操作实践胡方友(攀枝花新钢钒股份有限公司)摘要攀钢2号高炉通过采取调整风口、改善入炉原料质量、优化高炉操作、处理炉前隐患等措施,使各项技术经济指标逐渐得到优化。
关键词高炉强化冶炼顺行攀钢2号高炉有效容积l 200 m3,设有18个风口,1个铁口,2个渣口,3座顶燃式热风炉,采用双钟式炉顶,马基式旋转布料器,2007年底大修后开始第四代炉役的生产。
本文着重分析了2号高炉在2008年期间炉况逐渐变差的原因,并重点总结了在2009年期间针对炉况差而采取的优化措施。
1 炉况差的原因2号高炉投产后,高炉不易接受风量,炉缸活跃度降低,炉内顺行变差,出现了长期、崩滑料的现象,加减风频繁,致使高炉冶炼强度逐渐降低、利用系数降低、焦比升高、铁损增加(见表1)。
究其原因,初步分析有如下几点。
1.1 开炉初期炉型变化不规则。
大修开炉初期,有1座热风炉检修未完工,长期是2 座热风炉送风。
2号高炉采用低风温、低负荷操作,疏松边缘的COCO+OO↓OCCC↓装料制度,风口设置为直径130mm的2个、140mm的16个。
2号高炉2008年上半年东南和东北炉喉煤气CO2分布如图l所示。
可见2号高炉顺行虽好,但是边缘气流并不稳定。
在3座热风炉送风后,逐渐把风温用到1 200℃。
负荷加重以后,多次采取加重边缘的装料制度如OCOC+COCO+OO↓OCCC↓2 OOOO+COCO+2OO↓OCCC↓等,批重从20.8t减到20.3 t,料线2.8 m降到3.0 m。
炉缸1、2、3段水温差和炉身下2层温度都很低,使曲线带变窄成一条直线。
时间从22 h逐渐缩短到19 h,焦炭反应性从33%左右增到38%左右,反应后强度从55%左右降到52%左右,M40从78%降低到76%;喷吹煤粉质量也差,较平时12%左右高,入炉粉末最高达13.12%。
1.3设备的影响高炉砂坝和下渣沟整体上抬,砂坝太高而使砂坝和下渣沟常常糊死,同时后渣带铁多,经常坏渣口,最多的一个月坏了13个,最少的一个月也坏了4个,导致高炉经常因渣铁出不净而带来其他事故和频繁大减风。
攀钢低硫高强耐腐蚀钢炉外精炼技术的应用
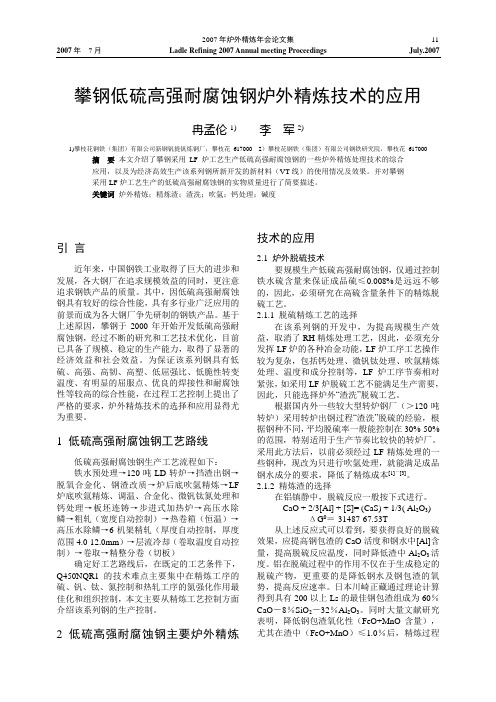
根据脱硫反应式,脱硫过程需通过保证一定量的[Als]来获得低氧势和消耗脱硫产生的氧,以使反应式向右进行。因此,在出钢过程中经过一次脱氧后,在小平台根据钢水氧活度喂入铝线,然后又在LF站加热前根据小平台[Als]补加铝丸(或喂铝线),从而保证了一定量的[Als],也保证了成品[Als]的稳定性。
与钒钢相比,通过微钛(0.01%左右的钛)处理的V-Ti钢具有以下优点:
⑴再加热奥氏体晶粒粗化温度提高到1200-1300℃[6]。
⑵奥氏体再结晶温度低[7]。
这说明与钒钢相比,V-Ti钢更容易获得细小的奥氏体晶粒晶粒,从而达到细化铁素体晶粒的目的。但在钒钢中加入微量钛发挥有利作用的同时,由于在较高的温度下形成TiV(N)颗粒,将削弱钒的沉淀强化作用(降低10-40MPa)[8]。因此,对于V-Ti钢,应考虑钛带来的强度损失,进而精确控制钛含量。
确定好工艺路线后,在既定的工艺条件下,Q450NQR1的技术难点主要集中在精炼工序的硫、钒、钛、氮控制和热轧工序的氮强化作用最佳化和组织控制,本文主要从精炼工艺控制方面介绍该系列钢的生产控制。
2低硫高强耐腐蚀钢主要炉外精炼技术的应用
2.1炉外脱硫技术
要规模生产低硫高强耐腐蚀钢,仅通过控制铁水硫含量来保证成品硫≤0.008%是远远不够的,因此,必须研究在高硫含量条件下的精炼脱硫工艺。
从理论上讲,单纯加入含CaO 90%的活性石灰即可提高钢包渣中CaO含量,但这一措施存在化渣较慢的缺点,为促进化渣一般均要在渣中配入一定量的CaF2或Al2O3、Na2O等助溶剂,并控制渣料粒度。选择CaF2作为精炼渣的助溶剂,为减轻CaF2对钢包内衬的侵蚀,将其加入量控制在10%以下,同时将精炼渣粒度控制在5mm左右。在确定以上配料原则后,根据转炉下渣量、成分,脱氧合金化种类及脱硫对钢包渣成分的要求计算得到精炼渣加入量在1000kg/炉的条件下,精炼渣中的CaO应≥75%,精炼渣的典型化学成分见表1。
攀钢提钒炼钢厂工艺技术及装备进步
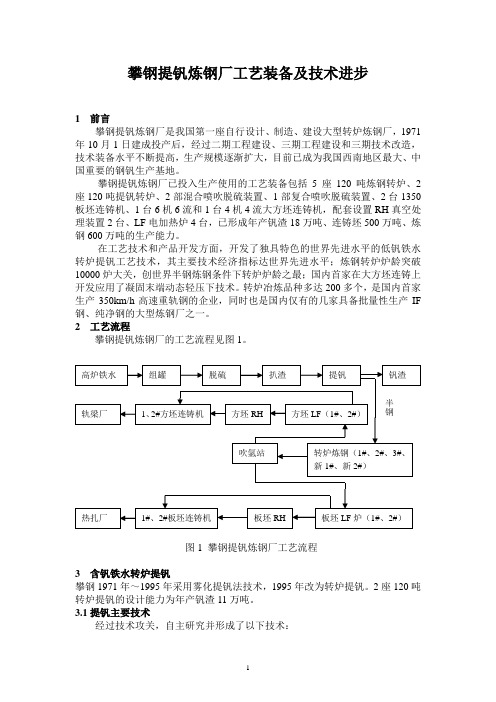
4.3挡渣出钢技术
针对原出钢挡渣采用加球机投放挡渣锥的挡渣效果差,下渣量较大,钢渣中有害成分污染钢水,影响钢坯质量,难以实现“洁净钢”生产。攀钢于2000年12月推广使用了新型的挡渣标挡渣技术,与原挡渣工艺相比,钢包内渣层厚度平均减少23mm,渣层厚度小于100mm的比例从64.98%提高到85.75%以上,为开发高纯净钢种创造了条件。采用新型挡渣工艺,有利于提高钢水质量,稳定脱氧工艺,减少出钢过程的回硫、回磷,该技术达到了国内先进水平。
⑷新转炉一次除尘系统采用了鲁奇公司的新型OG烟气湿法除尘技术,风机抽风量达210000m3/h,该技术是采用环隙式可调喉口,烟气流速最大可达180~190m/s(R—D喉口最高能达120 m/s),反冲水的粒径在75~100μm之间,除尘效果更好。从目前实际使用情况看,含尘浓度小于50~80mg/Nm3,净化效果较好。新转炉还配备了德国鲁奇公司的转炉煤气回收装置,实现了转炉煤气的自动回收,每炉可回收16000Nm3(CO浓度40%~50%)的煤气量,既满足了环保又实现了资源的综合利用。
2工艺流程
攀钢提钒炼钢厂的工艺流程见图1。
图1攀钢提钒炼钢厂工艺流程
3含钒铁水转炉提钒
攀钢1971年~1995年采用雾化提钒法技术,1995年改为转炉提钒。2座120吨转炉提钒的设计能力为年产钒渣11万吨。
3.1提钒主要技术
经过技术攻关,自主研究并形成了以下技术:
(1)渣态调整工艺技术。
(2)多炉出钒渣工艺技术和挡渣出半钢技术。
攀钢新三高炉炉前液压泥炮开口机的遥控改造解读
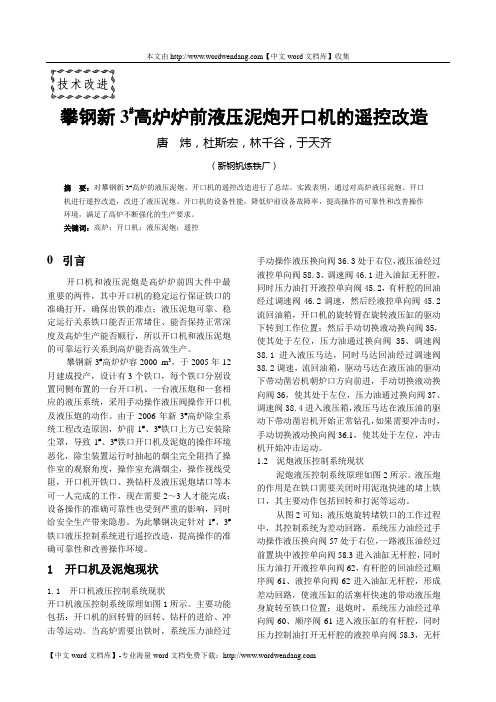
在原操作室新安装一套比例阀组,与远程控制系统相同,所有的控制系统采用开环控制,液压系统的控制采用无线遥控。
改造后的控制方式彻底改变了传统的操作方式,在现场操作中显得更加灵活,可以在出铁场范围内选择最佳操作位置和观察位置;操作方式更加灵活,即可以手动,又可以遥控;和现有控制系统构成冗余液压系统,提高了系统的可靠性;但液压系统的改动量大,对油液的清洁度要求达到AS7~8才能确保系统的稳定性;对维修的要求较高,投资也较高;需要对无线控制液压炮和开口机进行技术研究。
关键词:高炉;开口机;液压泥炮;遥控
1引言
开口机和液压泥炮是高炉炉前四大件中最重要的两件,其中开口机的稳定运行保证铁口的准确打开,确保出铁的准点;液压泥炮可靠、稳定运行关系铁口能否正常堵住、能否保持正常深度及高炉生产能否顺行,所以开口机和液压泥炮的可靠运行关系到高炉能否高效生产。
攀钢新3#高炉炉容2000 m3,于2005年12月建成投产,设计有3个铁口,每个铁口分别设置同侧布置的一台开口机、一台液压炮和一套相应的液压系统,采用手动操作液压阀操作开口机及液压炮的动作。由于2006年新3#高炉除尘系统工程改造原因,炉前1#、3#铁口上方已安装除尘罩,导致1#、3#铁口开口机及泥炮的操作环境恶化,除尘装置运行时抽起的烟尘完全阻挡了操作室的观察角度,操作室充满烟尘,操作视线受阻,开口机开铁口、换钻杆及液压泥炮堵口等本可一人完成的工作,现在需要2~3人才能完成;设备操作的准确可靠性也受到严重的影响,同时给安全生产带来隐患。为此攀钢决定针对1#、3#铁口液压控制系统进行遥控改造,提高操作的准确可靠性和改善操作环境。
发展钒钛球团矿 优化攀钢高炉炉料结构

的 6台烧结机进行所需的简单扩容 ( 包含新 建烧结机 )或取决于能否对现有的 6 ; 台烧结
机进 行 满 足 小 球 烧 结 要求 的技 术 改造 , 面 全
推行小球 烧结 技术 , 幅增产烧 结矿… , 大 1以
满足 对 烧结 矿 的新 增 需 求 , 方 面 本 文 不 予 这 讨 论 。后一 种 解决 办 法不 仅要 考 虑用 什 么原 料来 做 球 团 , 用 什 么样 的工 艺 , 采 能否 做得 出
与脉石 单 体 分 离 , 因此 , 矿 的粒 度 极 细 , 精 适
炉都获得 良好的冶炼效果 , 很难说那 一种结 构有绝对 优势。对我 国来说 ,0世纪 8 2 0年 代以来 的研究证明 , 高碱度烧结矿有利 于提
高其机 械 强 度 、 金 性 能 和产 量 , 此 , 二 冶 因 近 十年来 高 碱 度 烧 结 矿 成 为 发 展 主 流 。 同 时 ,
烧结矿碱度提高后客观上需要一定数量的酸 性炉料与之搭 配, 主要是靠天然生块矿 和 这 酸性球 团矿来解决。大量研究也 证明 , 高碱
度烧 结矿 为 主 +酸性 球 团矿 的炉 料结 构 要优
于高碱度烧结矿 +天然块 矿的炉料结构 , 因
为前~ 种 炉料 为全 熟 料 , 还 原性 、 熔 滴落 其 软
合格球 团, 球团加工成本怎样 , 更重要的是要 考虑 “ 烧结矿 +球 团矿 ” 的炉料结构是 否 比
“ 烧结 矿 +天然 块矿 ” 的炉 料结 构更 有利 于 攀
钢高炉冶炼 。为此 , 我们结合攀钢周边 资源 特点 , 围绕采用什 么原料 、 生产什么球 团、 选 择什么工艺 、 能否生产出合格球 团、 高炉使用 效果诸方面开展 了实验室研究 、 半工业实验 、 调研等工作 , 图弄清攀钢高炉使用酸性球 试 团矿的技术性与经济性 , 为公 司进行相关决 策提供可靠依据 。
攀钢钒富余焦炉煤气综合利用工艺技术运用实践

攀钢钒富余焦炉煤气综合利用工艺技术运用实践摘要:攀枝花钢钒公司现有焦炉6座,其中6米顶装焦炉4座,5.5米捣固焦炉2座,2019年焦炉煤气总发生量为22017924 GJ,焦炉煤气热值~3800kCal/Nm3。
根据现有焦炉煤气用户消耗能力及2019年焦炉煤气产销平衡数据分析,正常情况下焦炉煤气基本能满足产销平衡。
但在出现发电机组检修或炼钢厂、热轧板厂、轨梁厂等用量较大用户检修减量时,则焦炉煤气平衡困难,不可避免的发生阶段性富余放散现象,不仅造成能源浪费且与杜绝无序散排的环保政策不符,带来极大的环保风险问题。
为此,如何利用现有工艺条件,通过少量的经济投入,解决焦炉煤气阶段性富余放散,规避环保风险的问题,具有现实探讨价值。
本文重点针对该问题进行原因分析并提出解决措施。
关键词:富余焦炉煤气利用改造1 焦炉煤气系统现状攀钢钒公司现有焦炉6座,其中6米顶装焦炉4座,5.5米捣固焦炉2座,据统计2019年焦炉煤气总发生量为22017924 GJ,焦炉煤气热值~3800kCal/Nm3,小时发生量~15.75万Nm3。
焦炉的炉顶荒煤气经回收净化后,脱除荒煤气中H2S、焦油雾、氨、苯类、硫化物、氰化物、萘等杂质后,得到以氢气、甲烷、一氧化碳等为主的精制焦炉煤气,然后进入焦炉煤气主管网。
现焦炉煤气主管网配有一座15万M3 POC型干式煤气柜,焦炉煤气主要用户有热电锅炉、轧钢加热炉、冶材石灰窑、冷轧罩式炉及作为民用燃料等。
2 存在的问题根据2019年焦炉煤气产销平衡数据,正常情况下焦炉煤气基本能满足产销平衡。
但在出现发电机组检修或炼钢厂、热轧板厂、轨梁厂等用量较大用户检修减量时,则焦炉煤气平衡困难,难免发生阶段性富余放散现象,浪费同时与无序散排的环保政策不符,带来极大的环保风险问题。
2.1 2019年焦炉煤气产销平衡数据分析通过对2019年焦炉煤气生产、销售数据进行统计(表1)。
表1: 2019年焦炉煤气产销数据统计由上表1可以看出,焦炉煤气主要大的用户有能动公司锅炉、炼铁厂、炼钢厂、轨梁厂、热轧板厂、攀宏钒制品厂、盘江煤焦化公司及民用燃料等。
攀钢高效推进新产品开发
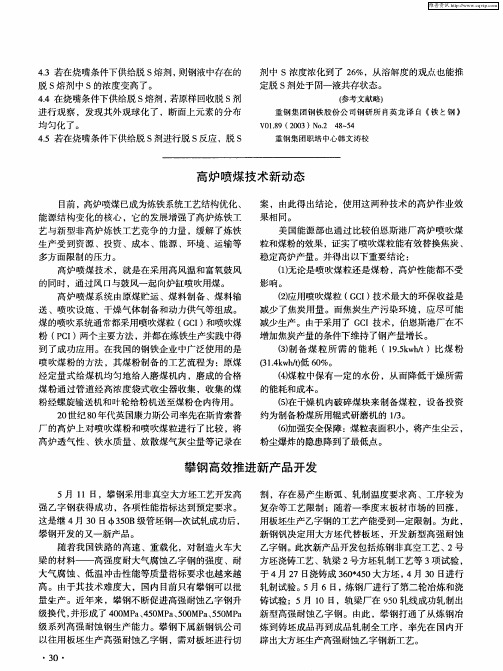
强乙字钢获得成功 ,各项性能指标达到预定要求 。 这是继 4 3 3 0 月 0日 5B级管坯钢一次试轧成功后, 攀钢开发的又一新产品。 随着我 国铁路 的高速 、重载化 ,对制造火车大 梁的材料—— 高强度耐大气腐蚀乙字钢的强度 、耐 大气腐蚀 、低温冲击性能等质量指标要求也越来越 高。由于其技术难度大 ,国内目前只有攀钢可以批 量生产 。近年来 ,攀钢不断促进高强耐蚀 乙字钢升 级换 代 , 并形 成 了 4 0 a 40 a 50 a5 0 a 0 MP 、5 MP 、0MP 、5MP 级系列高强耐蚀钢生产能力 。攀钢下属新钢钒公司 以往用 板 坯 生产 高 强 耐蚀 乙字 钢 ,需对 板 坯 进行 切
重 钢集 团职培 中心韩文 涛校
高 炉 喷 煤 技 术新 动 态
目前 ,高 炉 喷煤 已成 为炼铁 系 统工艺 结构 优化 、 能 源结 构 变 化 的核 心 ,它 的发 展增 强 了高 炉 炼铁 工
艺与新 型非高炉炼铁工艺竞争的力量 ,缓解 了炼铁 生产受到资源 、投资 、成本 、能源 、环境 、运输等 多方 面 限制 的压 力 。 高炉喷煤技术 ,就是在采用高风温和富氧鼓风 的同时 ,通 过风 口与鼓 风一 起 向炉 缸喷 吹用 煤 。 高 炉 喷煤 系统 由原 煤贮 运 、煤料 制 备 、煤料 输 送 、喷吹设施 、干燥气体制备和动力供气等组成 。 煤 的喷 吹 系统通 常 都采用 喷 吹煤粒 ( C )和喷吹煤 GI 粉 (C ) P I 两个主要方法 ,并都在炼铁生产实践中得 到 了成功应用 。在我 国的钢铁企业 中广泛使用的是 喷吹煤 粉的方法 ,其煤粉制备 的工艺流程为:原煤 经定量式给煤机均 匀地给人磨煤机内,磨成的合格
维 熔剂 , 则钢液 中存在的 脱s 熔剂 中 s的浓度变高了。 4 . 4在烧嘴条件下供给脱 s 熔剂 , 若原样回收脱 s 剂 进行观察 ,发现其外观球化 了,断面上元素的分布 均匀 化 了 。 4 . 5若在烧嘴条件下供给脱 s 剂进行脱 s 反应 ,脱 s
066 攀钢高炉炉前综合技术开发
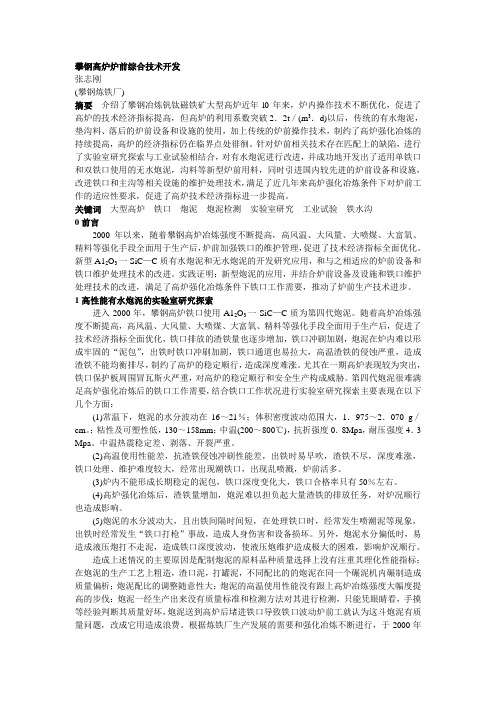
攀钢高炉炉前综合技术开发张志刚(攀钢炼铁厂)摘要介绍了攀钢冶炼钒钛磁铁矿大型高炉近年l0年来,炉内操作技术不断优化,促进了高炉的技术经济指标提高,但高炉的利用系数突破2.2t/(m3.d)以后,传统的有水炮泥,垫沟料、落后的炉前设备和设施的使用,加上传统的炉前操作技术,制约了高炉强化冶炼的持续提高,高炉的经济指标仍在临界点处徘徊。
针对炉前相关技术存在匹配上的缺陷,进行了实验室研究探索与工业试验相结合,对有水炮泥进行改进,并成功地开发出了适用单铁口和双铁口使用的无水炮泥,沟料等新型炉前用料,同时引进国内较先进的炉前设备和设施,改进铁口和主沟等相关设施的维护处理技术,满足了近几年来高炉强化冶炼条件下对炉前工作的适应性要求,促进了高炉技术经济指标进一步提高。
关键词大型高炉铁口炮泥炮泥检测实验室研究工业试验铁水沟0前言2000年以来,随着攀钢高炉冶炼强度不断提高,高风温、大风量、大喷煤、大富氧、精料等强化手段全面用于生产后,炉前加强铁口的维护管理,促进了技术经济指标全面优化。
新型A12O3一SiC—C质有水炮泥和无水炮泥的开发研究应用,和与之相适应的炉前设备和铁口维护处理技术的改进。
实践证明:新型炮泥的应用,并结合炉前设备及设施和铁口维护处理技术的改进,满足了高炉强化冶炼条件下铁口工作需要,推动了炉前生产技术进步。
1高性能有水炮泥的实验室研究探索进入2000年,攀钢高炉铁口使用A12O3一SiC—C质为第四代炮泥。
随着高炉冶炼强度不断提高,高风温、大风量、大喷煤、大富氧、精料等强化手段全面用于生产后,促进了技术经济指标全面优化,铁口排放的渣铁量也逐步增加,铁口冲刷加剧,炮泥在炉内难以形成牢固的“泥包”,出铁时铁口冲刷加剧,铁口通道也易拉大,高温渣铁的侵蚀严重,造成渣铁不能均衡排尽,制约了高炉的稳定顺行,造成深度难涨。
尤其在一期高炉表现较为突出,铁口保护板周围冒瓦斯火严重,对高炉的稳定顺行和安全生产构成威胁。
提高钒钛磁铁矿高炉综合入炉品位的高炉炉料及方法[发明专利]
![提高钒钛磁铁矿高炉综合入炉品位的高炉炉料及方法[发明专利]](https://img.taocdn.com/s3/m/ff051514f90f76c660371ab2.png)
专利名称:提高钒钛磁铁矿高炉综合入炉品位的高炉炉料及方法
专利类型:发明专利
发明人:石军,陆高峰,林文康,邹仕华,曾中兴,李清明,江凌,黄云,毛建林,胡勇,张志强,饶家庭,刘燕,姚国勋,陈剑锋,
朱香
申请号:CN201310612907.9
申请日:20131127
公开号:CN103725812A
公开日:
20140416
专利内容由知识产权出版社提供
摘要:本发明提供一种提高钒钛磁铁矿高炉综合入炉品位的高炉炉料及方法,所述高炉炉料包括64-90wt%的钒钛烧结矿、1-35wt%钒钛球团矿、0-9wt%酸性块矿和1-10wt%高品位块矿,所述高品位块矿中Fe元素的重量百分比为40-65%,SiO的重量百分比为5-15%。
本发明还提供了一种提高钒钛磁铁矿高炉综合入炉品位的方法,所述方法包括将本发明所述高炉炉料进行高炉冶炼。
根据本发明可以提高高炉入炉品位,提高高炉产量,降低焦比,降低高炉炉料的成本。
申请人:攀钢集团西昌钢钒有限公司
地址:615032 四川省凉山彝族自治州西昌市经久工业园区
国籍:CN
代理机构:北京铭硕知识产权代理有限公司
更多信息请下载全文后查看。
攀钢钒高炉炉前液压泥炮开口机的遥控改造
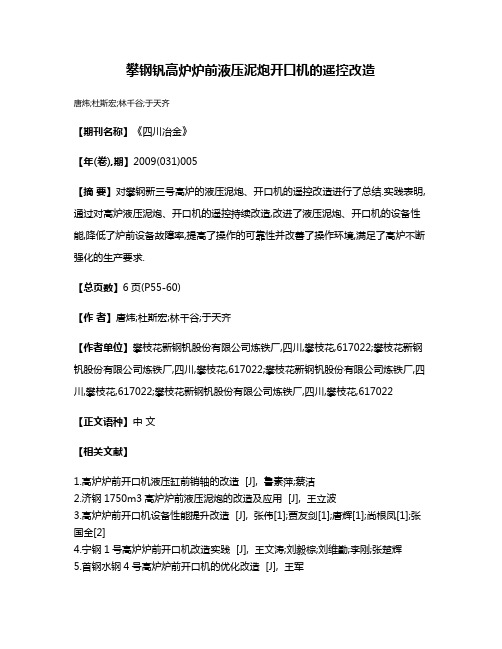
攀钢钒高炉炉前液压泥炮开口机的遥控改造
唐炜;杜斯宏;林千谷;于天齐
【期刊名称】《四川冶金》
【年(卷),期】2009(031)005
【摘要】对攀钢新三号高炉的液压泥炮、开口机的遥控改造进行了总结.实践表明,通过对高炉液压泥炮、开口机的遥控持续改造,改进了液压泥炮、开口机的设备性能,降低了炉前设备故障率,提高了操作的可靠性并改善了操作环境,满足了高炉不断强化的生产要求.
【总页数】6页(P55-60)
【作者】唐炜;杜斯宏;林千谷;于天齐
【作者单位】攀枝花新钢钒股份有限公司炼铁厂,四川,攀枝花,617022;攀枝花新钢钒股份有限公司炼铁厂,四川,攀枝花,617022;攀枝花新钢钒股份有限公司炼铁厂,四川,攀枝花,617022;攀枝花新钢钒股份有限公司炼铁厂,四川,攀枝花,617022
【正文语种】中文
【相关文献】
1.高炉炉前开口机液压缸前销轴的改造 [J], 鲁素萍;蔡洁
2.济钢1750m3高炉炉前液压泥炮的改造及应用 [J], 王立波
3.高炉炉前开口机设备性能提升改造 [J], 张伟[1];贾友剑[1];唐辉[1];尚根凤[1];张国全[2]
4.宁钢1号高炉炉前开口机改造实践 [J], 王文涛;刘毅棕;刘维勤;李刚;张楚辉
5.首钢水钢4号高炉炉前开口机的优化改造 [J], 王军
因版权原因,仅展示原文概要,查看原文内容请购买。
炼铁高炉机械设备的技术性分析 王东
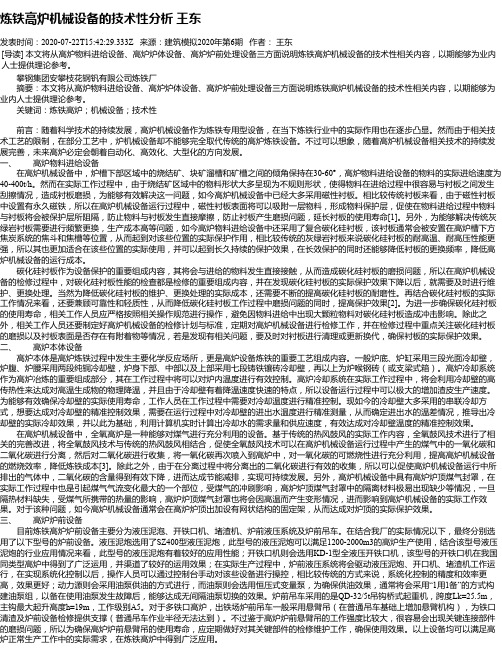
炼铁高炉机械设备的技术性分析王东发表时间:2020-07-22T15:42:29.333Z 来源:建筑模拟2020年第6期作者:王东[导读] 本文将从高炉物料进给设备、高炉炉体设备、高炉炉前处理设备三方面说明炼铁高炉机械设备的技术性相关内容,以期能够为业内人士提供理论参考。
攀钢集团安攀枝花钢钒有限公司炼铁厂摘要:本文将从高炉物料进给设备、高炉炉体设备、高炉炉前处理设备三方面说明炼铁高炉机械设备的技术性相关内容,以期能够为业内人士提供理论参考。
关键词:炼铁高炉;机械设备;技术性前言:随着科学技术的持续发展,高炉机械设备作为炼铁专用型设备,在当下炼铁行业中的实际作用也在逐步凸显。
然而由于相关技术工艺的限制,在部分工艺中,炉机械设备却不能够完全取代传统的高炉炼铁设备。
不过可以想象,随着高炉机械设备相关技术的持续发展完善,未来高炉必定会朝着自动化、高效化、大型化的方向发展。
一、高炉物料进给设备在高炉机械设备中,炉槽下部区域中的烧结矿、块矿溜槽和矿槽之间的倾角保持在30-60°,高炉物料进给设备的物料的实际进给速度为40-400t/h。
然而在实际工作过程中,由于烧结矿区域中的物料形状大多呈现为不规则形状,使得物料在进给过程中很容易与衬板之间发生刮擦情况,造成衬板磨损,为能够有效解决这一问题,如今高炉机械设备中已经大多采用磁性衬板。
相比较传统衬板来看,由于磁性衬板中设置有永久磁铁,所以在高炉机械设备运行过程中,磁性衬板表面将可以吸附一层物料,形成物料保护层,促使在物料进给过程中物料与衬板将会被保护层所阻隔,防止物料与衬板发生直接摩擦,防止衬板产生磨损问题,延长衬板的使用寿命[1]。
另外,为能够解决传统灰绿岩衬板需要进行频繁更换,生产成本高等问题,如今高炉物料进给设备中还采用了复合碳化硅衬板,该衬板通常会被安置在高炉槽下方焦炭系统的焦斗和焦槽等位置,从而起到对该些位置的实际保护作用,相比较传统的灰绿岩衬板来说碳化硅衬板的耐高温、耐高压性能更强,所以其也更加适合在该些位置的实际使用,并可以起到长久持续的保护效果,在长效保护的同时还能够降低衬板的更换频率,降低高炉机械设备的运行成本。
攀钢高炉钒钛磁铁矿冶炼的技术进步
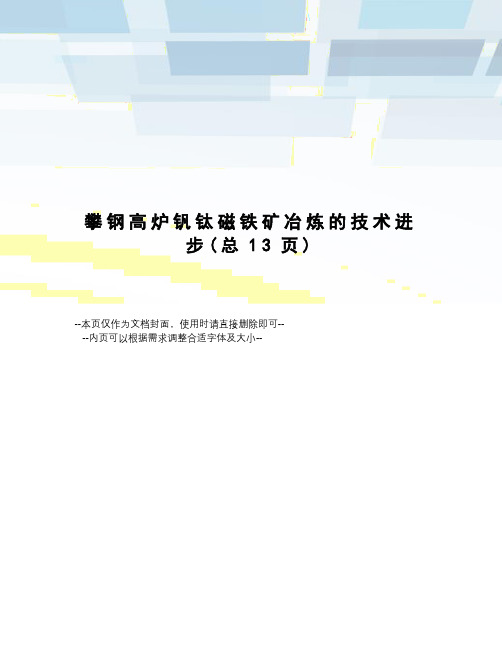
攀钢高炉钒钛磁铁矿冶炼的技术进步(总13页)--本页仅作为文档封面,使用时请直接删除即可----内页可以根据需求调整合适字体及大小--攀钢高炉钒钛磁铁矿冶炼的技术进步付卫国,谢洪恩(攀枝花钢铁研究院,四川攀枝花617000)摘要:攀钢高炉钒钛矿冶炼投产30多年以来,冶炼技术经历了不断的发展和完善,随着精料水平及装备水平的提高,高炉冶炼不断强化,逐步形成了独特的钒钛矿高炉强化冶炼技术。
技术经济指标大幅度提高,在入炉品位仅50%的条件下,高炉利用系数达到了2.5 t/(m3·d)以上。
关键词:钒钛磁铁矿;高炉冶炼;强化技术中图分类号:TF52 文献标识码:A 文章编号:0449—749X(2008)10—0021—04攀钢高炉冶炼的是高钛型钒钛磁铁矿,这种矿石含钛高,高炉冶炼时炉渣中TiO2的质量分数达20%~25%,在冶炼过程中会出现炉渣粘稠,渣铁不分,炉缸堆积等现象,与普通矿相比具有较大的冶炼难度。
从1970年投产以后,高炉利用系数只有1.0t/(m3·d)左右,焦比高达800 kg/t(铁)以上。
在经过30多年的生产实践后,使高炉冶炼钒钛矿的技术逐步完善,钒钛矿的冶炼技术也达到了一个较高的水平,高炉冶炼不断强化,并实现了长期的稳定顺行,部分指标已达到并超过了普通矿高炉的冶炼水平,主要技术经济指标大幅度提高。
年均利用系数逐渐提高到2.4 t/(m3·d)以上,焦比降低到600kg/t(铁)以下[1,2]。
1 装备水平不断提高攀钢高炉投产以来高炉的装备水平不断提高,70年代至80年代投产第1号、2号、3号高炉主要采用的为钟式炉顶、内燃式热风炉;1989年投产的4号高炉以及2005年投产的5号高炉均采用了外燃式热风炉、无料钟炉顶、铜冷却壁及软水密闭循环等先进技术;热风炉采用了助燃空气、煤气双预热以及快速燃烧等技术,使高炉的风温得到显著提高,1990年以后风温的变化见图1。
- 1、下载文档前请自行甄别文档内容的完整性,平台不提供额外的编辑、内容补充、找答案等附加服务。
- 2、"仅部分预览"的文档,不可在线预览部分如存在完整性等问题,可反馈申请退款(可完整预览的文档不适用该条件!)。
- 3、如文档侵犯您的权益,请联系客服反馈,我们会尽快为您处理(人工客服工作时间:9:00-18:30)。
攀钢高炉炉前综合技术开发张志刚(攀钢炼铁厂)摘要介绍了攀钢冶炼钒钛磁铁矿大型高炉近年l0年来,炉内操作技术不断优化,促进了高炉的技术经济指标提高,但高炉的利用系数突破2.2t/(m3.d)以后,传统的有水炮泥,垫沟料、落后的炉前设备和设施的使用,加上传统的炉前操作技术,制约了高炉强化冶炼的持续提高,高炉的经济指标仍在临界点处徘徊。
针对炉前相关技术存在匹配上的缺陷,进行了实验室研究探索与工业试验相结合,对有水炮泥进行改进,并成功地开发出了适用单铁口和双铁口使用的无水炮泥,沟料等新型炉前用料,同时引进国内较先进的炉前设备和设施,改进铁口和主沟等相关设施的维护处理技术,满足了近几年来高炉强化冶炼条件下对炉前工作的适应性要求,促进了高炉技术经济指标进一步提高。
关键词大型高炉铁口炮泥炮泥检测实验室研究工业试验铁水沟0前言2000年以来,随着攀钢高炉冶炼强度不断提高,高风温、大风量、大喷煤、大富氧、精料等强化手段全面用于生产后,炉前加强铁口的维护管理,促进了技术经济指标全面优化。
新型A12O3一SiC—C质有水炮泥和无水炮泥的开发研究应用,和与之相适应的炉前设备和铁口维护处理技术的改进。
实践证明:新型炮泥的应用,并结合炉前设备及设施和铁口维护处理技术的改进,满足了高炉强化冶炼条件下铁口工作需要,推动了炉前生产技术进步。
1高性能有水炮泥的实验室研究探索进入2000年,攀钢高炉铁口使用A12O3一SiC—C质为第四代炮泥。
随着高炉冶炼强度不断提高,高风温、大风量、大喷煤、大富氧、精料等强化手段全面用于生产后,促进了技术经济指标全面优化,铁口排放的渣铁量也逐步增加,铁口冲刷加剧,炮泥在炉内难以形成牢固的“泥包”,出铁时铁口冲刷加剧,铁口通道也易拉大,高温渣铁的侵蚀严重,造成渣铁不能均衡排尽,制约了高炉的稳定顺行,造成深度难涨。
尤其在一期高炉表现较为突出,铁口保护板周围冒瓦斯火严重,对高炉的稳定顺行和安全生产构成威胁。
第四代炮泥很难满足高炉强化冶炼后的铁口工作需要,结合铁口工作状况进行实验室研究探索主要表现在以下几个方面:(1)常温下,炮泥的水分波动在16~21%;体积密度波动范围大,1.975~2.070 g/cm。
;粘性及可塑性低,130~158mm;中温(200~800℃),抗折强度0.8Mpa,耐压强度4.3 Mpa。
中温热震稳定差、剥落、开裂严重。
(2)高温使用性能差,抗渣铁侵蚀冲刷性能差,出铁时易早吹,渣铁不尽,深度难涨,铁口处理、维护难度较大,经常出现潮铁口,出现乱喷溅,炉前活多。
(3)炉内不能形成长期稳定的泥包,铁口深度变化大,铁口合格率只有50%左右。
(4)高炉强化冶炼后,渣铁量增加,炮泥难以担负起大量渣铁的排放任务,对炉况顺行也造成影响。
(5)炮泥的水分波动大,且出铁间隔时间短,在处理铁口时,经常发生喷潮泥等现象,出铁时经常发生“铁口打枪”事故,造成人身伤害和设备损坏。
另外,炮泥水分偏低时,易造成液压炮打不走泥,造成铁口深度波动,使液压炮维护造成极大的困难,影响炉况顺行。
造成上述情况的主要原因是配制炮泥的原料品种质量选择上没有注重其理化性能指标;在炮泥的生产工艺上粗造,渣口泥,打罐泥,不同配比的的炮泥在同一个碾泥机内碾制造成质量偏析;炮泥配比的调整随意性大;炮泥的高温使用性能没有跟上高炉冶炼强度大幅度提高的步伐:炮泥一经生产出来没有质量标准和检测方法对其进行检测,只能凭眼睛看,手摸等经验判断其质量好坏,炮泥送到高炉后堵进铁口导致铁口波动炉前工就认为这斗炮泥有质量问题,改成它用造成浪费。
根据炼铁厂生产发展的需要和强化冶炼不断进行,于2000年7月根据当时炮泥生产条件,在第四代炮泥的基础上迈出了探索性的一步,采取了一系列措施,对炮泥的生产工艺及原料和配方进行了改进,提高其高温使用性能。
2有水炮泥性能改进的研究方法和技术路线2.1探索炮泥在铁口孔道内不同深度的温度变化规律对2BF、3BF铁121出完铁堵口后10分钟对铁口孔道温度进行测试,探索炮泥在铁口孔道内不同深度的温度变化规律,结合实验室研究在氧化气氛条件下对炮泥在不同配比、不同温度、不同烧结时间、使用不同结合剂时的抗折、抗压的强度变化规律,并结合高炉铁口对炮泥的使用情况进行详细跟踪调查,分析研究炮泥在常温和中温条件下的物理性能与铁口工况以及高炉冶炼行程的内在联系规律。
2.2厂自制炮泥检测装置(图一)对炮泥在常温下物理性能指标进行检测分析,并制定检测标准2.3 炮泥质量的改进及稳定性研究(1)探索合理碾泥工艺,优化炮泥配比改善炮泥在常温下的物理性能。
(2)在炮泥中配加2%~3%(云母、减水剂、保存剂、烧结剂、纤维、抗氧化剂)等多种添加剂,改善炮泥中温(200~800℃)物理化学性能(3)在炮泥中配加1%AD添加剂相结合办法提高炮泥的高温使用性能(4)降低炮泥水分,探索合理的困料时间和湿度,在外配加各种添加剂同时,降低炮泥水分至14.8~15.8%,槿索合殚的闲米斗时间为16~48h。
(5)确保炮泥生产用原料质量稳定提高2.4成立生产科炮泥质量检测站依据炮泥常温下检测标准能够快速反映炮泥在铁口使用过程和炮泥的生产工艺以及使用原料的相关关系,炼铁厂成立了炮泥检测站专门对外购和自产的有水炮泥进行质量检测严把质量关,同时对炮泥的生产工艺和使用原料以及铁口的工况进行跟踪,实现了用户、生产厂家、科研所相互沟通技术信息,为炮泥质量的改进、稳定提高,以及高炉根据新型有水炮泥的特性,改进炉前管理和使用方法起到了桥梁作用。
3无水炮泥的配方确定及工业试验3.1无水炮泥配方确定根据攀钢高炉冶炼钒钛磁铁矿的特殊性,以及高炉强化冶炼后铁口工作的现行状况,突出地表现为出铁问隔时间短,从铁口排放的渣铁量增大等情况。
对炮泥的配方在实验室进行研究,确定为单铁口高炉采用复合型结合剂结合的快速烧结无水炮泥,双铁口高炉采用全焦油结合的无水炮泥(炮泥配方见表2,理化性能要求见表3)。
3.2无水炮泥工业试验及应用高炉采用大富氧、大喷煤、高风温、大风量等强化技术,高炉利用系数大幅度提高,99年为2.149t/(m3.d)、2000年为2.25 t/(m3.d)、2001年上半年为2.234 t/(m3.d)。
随着高炉冶炼强度大幅度提高,铁口承担排放渣铁的任务越来越繁重,突出地表现为一期高炉铁口深度难涨,两年来三高炉铁口深度达到2.0米以上还不到5%;一、二高炉铁口周围冒瓦斯火极其严重,危及炉缸工作安全。
四号高炉铁口深度虽然能维持2.1一2.2米,但稳定性差,出铁过程铁口喷溅严重,主沟两旁积渣较多,铁损高,炉前劳动强度大。
为了改善铁口的工作状况,适应高炉强化冶炼。
铁厂从2000年10月以来先后在四高炉南北铁口进行仿昆钢型、仿梅钢型、自制型、同时引进四川峨电、河南中州、攀枝花西区黄河成品炮泥共进行数次摸索性工业试验,根据工业试验中存在的问题对炮泥的配方和生产工艺进行不断改进,同时结合炉前设备(液压炮、开口机)的改进。
于2002年12月开始至2004年7月铁厂四座高炉相继成功地应用了适合目前铁口工作需要的无水炮泥。
高炉铁口合格率达到90%以上,铁量差减小,降低了炉前工人的劳动强度,满足了高炉强化冶炼的要求。
2004年在四高炉进行适合新三高炉三个铁口使用的无水炮泥工业试验取得成功,2005年10月开炉顺利使用上无水炮泥、铁口合格率达90%以上。
4铁口维护与管理(1)根据有水炮泥性能的改进,修订完善《使用有水炮泥铁口操作岗位规程》,固定铁口角度,加强铁口泥套和铁口的维护。
(2)根据无水炮泥的应用,建立健全《使用无水炮泥铁口操作岗位规程》。
固定铁口角度,加强铁口泥套和铁口的维护,单铁口高炉采用复合型结合剂结合的快速烧结无水炮泥,双铁口高炉采用全焦油结合的无水炮泥,并对炮泥的性能指标进行定期检测,确保炮泥质量稳定。
(3)根据有水炮泥性能的改进和无水炮泥的应用,重新修订完善《开口机操作规程》和《液压炮操作规程》,定期对开口机和液压炮进行检查维护,对重要零部件进行定期更换保证其可靠性和稳定性,确保堵铁口和开铁口工作正常。
5进行铁水沟长寿化等相关技术研究随着高炉冶炼的不断强化,长期以来使用的普通垫沟泥铺垫的铁水主沟沟衬已经不能适应强化冶炼的要求,抗侵蚀性、抗冲刷性、热震性差,沟衬粘渣,打水降温后开裂,破损严重使用寿命短为2~3天,通铁量低,仅为5000~6000吨,必须进行沟衬修补和重新垫沟,炉前劳动强度大,吨铁耐材消高,且沟衬修补和重新垫沟时还导致高炉出铁晚点,炉况“受憋”,制约高炉强化冶炼的持续进行。
(1)开发研究用树脂结合的免烘烤铁沟料进行工业试验并取得成功,于2001年在全厂四座高炉推广应用,新垫的主沟使用34天只需对落铁点进行修补外,使用寿命短为6~7天,通铁量达到了16000~18000吨,满足了高炉强化冶炼时对主沟功能的要求。
(2)利用四高炉2004年3~5月大修时机,双铁口便于施工的有利条件,采用快干型浇注料对对北铁口主沟和砂窝子进行整体浇注试验研究。
北铁口主沟和砂窝子开炉投入使用近5个月工作状况正常,其问主沟进行正常维护,砂窝予进行修补两次,通铁量近20万吨取得成功。
在大修其间淘汰传统人工拨“铁闸”,改进为摆动流嘴机械拨闸,同时引进了炉前清渣机械试用取得成功,在2005年10月新三高炉开炉时,进行全面推广运用。
6炉前设备改进(1)结合有水炮泥的改进和无水炮泥在四座高炉应用的同时,炉前液压炮由.BG300型改成用:DDS型,克服了BG300型堵铁口时,打泥压力不足,堵铁口泥量不够,导致铁口深度波动,设备故障多、零部件使用寿命短、维修量大等缺点。
(2)有水炮泥的改进和无水炮泥应用,淘汰使用了30多年的简易钻孔吊挂式开口机,改用YY-F1200型气液式开口机,克服了简易钻孔吊挂式开口机当炮泥强度高时钻孔难,铁口容易钻偏、铁口角度波动大、设备故障多、零部件使用寿命短、维修量大等缺点。
(3)根据YY-F1200型气液式开口机功率大,设备运行稳定,“钻进”、“后退”反应速度快等优良性能,铁厂2003年白行研制开发出透铁口用“专用透杆”和做铁口泥套用“专用工具”安装在开口机上,并应用于生产中,大大降低了炉前工的劳动强度和开口设备消耗,并且工人的安全得到保障。
(4)四号高炉大修时,淘汰了铁水沟拨罐“简易铁闸”,引进采用了摆动流嘴拨罐技术和清渣机械试用取得成功,在2005年10月新三高炉开炉时,进行全面推广运用。
提高了铁水罐的利用率,杜绝了铁水“跑闸”、“漏闸”等事故,同时进一步降低了炉前工的劳动强度。
7结语(1)有水炮泥性能改进和无水炮泥的逐渐推广应用,同时加强铁口的维护处理,铁口合格率和铁量差合格率逐渐上升,均达9096以上,稳定了铁口工作状况,出铁乱喷溅程度减轻铁损降低,改善了炉前工作环境,降低了工人劳动强度。