SPC and Injection Molding
50个模具专业术语
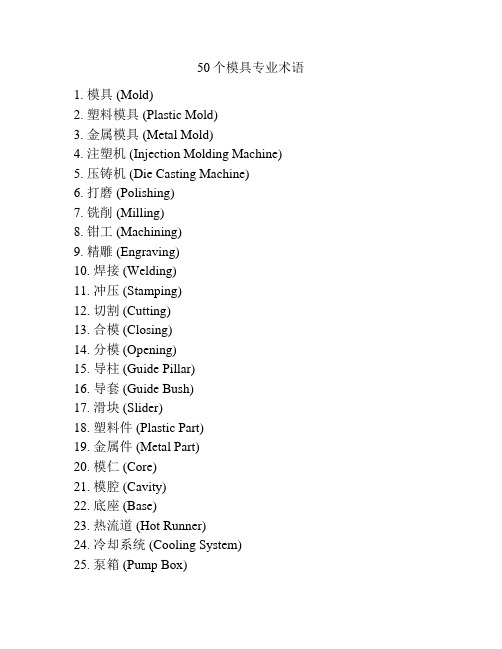
50个模具专业术语1. 模具 (Mold)2. 塑料模具 (Plastic Mold)3. 金属模具 (Metal Mold)4. 注塑机 (Injection Molding Machine)5. 压铸机 (Die Casting Machine)6. 打磨 (Polishing)7. 铣削 (Milling)8. 钳工 (Machining)9. 精雕 (Engraving)10. 焊接 (Welding)11. 冲压 (Stamping)12. 切割 (Cutting)13. 合模 (Closing)14. 分模 (Opening)15. 导柱 (Guide Pillar)16. 导套 (Guide Bush)17. 滑块 (Slider)18. 塑料件 (Plastic Part)19. 金属件 (Metal Part)20. 模仁 (Core)21. 模腔 (Cavity)22. 底座 (Base)23. 热流道 (Hot Runner)24. 冷却系统 (Cooling System)25. 泵箱 (Pump Box)26. 压缩机 (Compressor)27. 水力缸 (Hydraulic Cylinder)28. 模具钢 (Mold Steel)29. 法兰 (Flange)30. 注塑模具 (Injection Mold)31. 放电加工 (Electrical Discharge Machining)32. 模仁巧妙 (Core Pull)33. 螺旋通道 (Spiral Channel)34. 冷却塔 (Cooling Tower)35. 酸洗 (Acid Etching)36. 布胶 (Rubberizing)37. 文字标记 (Texturing)38. 研磨剂 (Polishing Compound)39. 硅胶 (Silicone)40. 硬度测试 (Hardness Testing)41. 射出速度 (Injection Speed)42. 模具寿命 (Mold Life)43. 热流道系统 (Hot Runner System)44. 冷却时间 (Cooling Time)45. 模具设计 (Mold Design)46. 模具制造 (Mold Manufacturing)47. 模具修理 (Mold Repair)48. 模具改造 (Mold Modification)49. 模具试模 (Mold Trial)50. 模具测试 (Mold Testing)。
模具专业英语——兆威机电

thickness *'θɪknɪs+厚度/浓度
(Mould) Release Agent 脱模剂 Release *rɪ'liːs+释放/发射/发布 Agent *'eɪdʒ(ə)nt+ 代理人/代理商/药剂
Spacial *'speɪʃəl+ 空间的/宇宙的 (“Space *speɪs+ 空间/太空”的 衍生词)
Orientation *,ɔːrɪən'teɪʃ(ə)n+ 方向/定位/定向 Plane *pleɪn+ 飞机/平面/水平/平面的
Connecting straight line连接直线
Connect *kə'nekt+ 连接/关联/联合 Straight *streɪt+ 直的/连续的/直接地 Line *laɪn+ 路线/航线/直线/行列
Recess[rɪ'ses]=Deepen ['diːp(ə)n] 变深/下沉 Raise=Exceed [ɪk'siːd] 超过/超出
Title block 标识区域
Characters 字符
Enlarge
一、产品上的英语(English Expression on Product)
4.产品图纸信息—博世(Product Drawing Information—Bosch)
Delivery *dɪ'lɪv(ə)rɪ+ 交付/递送 (Characteristic of Delivery 交付特征/供应商编号)
模具专业英语翻译

单词翻译:PlasticsCompression Molding for PlasticsTransfer Molding and Injection MoldingPressure Die Casting DiesForging DieFundamental of Chip-type Machining ProcessesFundamental of T urning and Boring on LatheMillingElectrodischarge Machines翻译划线的部分T urning is the process of machining external cylindrical and conical surfaces. It is usually performed on a lathe.The depth of cut (DOC), d, represents the third dimension.As the plastic is fed to the rotating screw, it passes through thre e zones as shown: feed, compression, and metering(定量).句子翻译The molds used for compression molding are classified into four basic types, namely, positive molds, landed positive molds, flash-type molds, and semipositive molds.In order to harden and eject thermoplastic parts from the mold, cooling would be necessary.There are seven basic chip formation processes: shaping, turning, milling, drilling, sawing, broaching, and grinding (abrasive machining).In the injection mold, The screw(螺杆)acts as a combination injecting and plasticizing unit .The physcal composition of the workpiece greatly influences the selection of the machining method, the tool composition and geometry, and the rate of material removal.The clamping force that a machine is capable of exerting is part of the size designation and is measured in tons.Proper selection of the die material and of the die manufacturing technique determines, to a large extent, the useful life of forging dies.In compression molding the plastic material as powder or performs is placed into a heated steel mold cavity.The guide pins, or posts, are mounted in the lower shoe.Plastic often contain other added materials called fillers.When applying the electrical discharge machining process, the material is eroded as a result of electrical discharge between tool and work.Parts made by transfer molding have greater strengths, more uniform densities, closer dimensional tolerances, and the parting line requires less cleaning as compared with parts made by compression molding.The die blocks contain the movement mechanisms of the die and the inserts incorporating the casting form so that the assembly can be mounted between the tie bars of the machine.In the early dawn civilization mankind discovered that a heated piece of metal was more easily hammered into different shapes.The tools necessary to produce a given forging cannot be made until the shape of the final forging has been determined.Solid models eliminate most of the problems of the wire frame.1.This process of annealing consists of heating the steel to an elevated temperature fora definite period of time and, usually, cooling it slowly.The pattern is a replica of the part being made but has slightly larger dimensions to allow for shrinkage during solidification and cooling of the casting.This type of mold is widely used because it is comparatively easy to construct and it controls thickness and density within close limits..1.If the surface is unusually hard, the cutting speed on the first roughing cut should bereduced accordinglyWelding is a process in which two materials, usually metals, are permanently jointed together through localized coalescence, resulting from a suitable combination of temperature, pressure and metallurgical conditions.汉译英传递模注射模自由锻Smith forging切削加工过程段落翻译After the feed zone, the screw flight depth is gradually reduced, forcing the plastic to compress. The work is converted to heat by shearing the plastics, making ita semifluid(半流体)mass.In the metering zone, additional heat is applied by conduction from the barrel surface. As the chamber in front of the screw becomes filled, it force the screw back, tripping a limit switch that activates a hydraulic cylinder that force the screw forward and injects the fluid plastic into the close mold.Gas tungsten arc welding is performed with the heat from an electric arc discharged between the workpiece and a nonconsumable(不熔化)electrode made of tungsten.This process, like GNA W(gas metal arc welding), is gas-shielded arc welding, where an atmosphere of inert gas is maintained around the arc and no flux(熔剂)is used.The process is often called tungsten inert(惰性)gas welding.。
注塑ipqc工作流程

注塑ipqc工作流程英文回答:Injection molding IPQC workflow is a crucial process in ensuring the quality of injection molded products. IPQC stands for In-Process Quality Control and it involves inspecting and monitoring the production process at various stages to identify and address any potential issues or defects.The IPQC workflow typically includes the following steps:1. Initial inspection: This involves checking the raw materials, such as the plastic resin pellets, for any impurities or defects. It is important to ensure that the raw materials meet the required specifications before starting the injection molding process.2. Machine setup: Before starting the production, theinjection molding machine needs to be properly set up. This includes calibrating the machine, installing theappropriate mold, and adjusting the parameters such as temperature, pressure, and injection speed.3. First article inspection: Once the machine is set up, the first few molded parts, known as first articles, are inspected to verify their dimensional accuracy and quality. This is done by measuring the dimensions and conducting visual inspections.4. In-process inspection: During the production process, regular inspections are conducted to check the quality ofthe molded parts. This can involve measuring critical dimensions, conducting visual inspections, and performing functional tests if necessary. Any deviations from the required specifications are identified and correctiveactions are taken.5. Statistical process control (SPC): SPC is used to monitor the stability and capability of the injection molding process. It involves collecting and analyzing datafrom the production process to identify any trends or patterns that may indicate potential issues. SPC charts, such as control charts, are used to visualize the data and make informed decisions.6. Final inspection: Once the production is complete, a final inspection is conducted to ensure that the molded parts meet the required quality standards. This can include dimensional measurements, visual inspections, andfunctional tests. Only the parts that pass the final inspection are approved for shipment or further processing.中文回答:注塑IPQC工作流程是确保注塑产品质量的关键过程。
injection molding

Injection MoldingIntroductionInjection molding is a widely used manufacturing process in the field of plastic production. It involves injecting molten material into a mold cavity, allowing it to cool and solidify, before ejecting the molded part. This process is known for its efficiency, accuracy, and versatility, making it suitable for producing a wide range of plastic products. In this document, we will explore the injection molding process, its advantages, limitations, and relevant considerations.The Injection Molding ProcessStep 1: ClampingThe first step in the injection molding process is clamping. The mold cavity is closed and clamped shut, ensuring that it remains tight and secure during the subsequent steps of the process. The clamping force is controlled depending on the size and complexity of the part being molded.Step 2: InjectionOnce the mold is clamped shut, the molten material, typically a thermoplastic polymer, is injected into the mold cavity through a nozzle. The material is heated and liquefied in a barrel before being pushed under high pressure into the mold. The molten material fills the cavity and takes the shape of the mold.Step 3: CoolingAfter the cavity is filled, the molten material is left to cool and solidify. Cooling time is determined by several factors, including material properties, part design, and thickness. It is crucial to control the cooling process to ensure uniform solidification and prevent defects such as warping or shrinkage.Step 4: EjectionOnce the molded part has cooled and solidified, the mold is opened, and the part is ejected. Ejection mechanisms such as pins or ejector plates are used to remove the part from the mold without causing damage.Step 5: Post-processingDepending on the requirements of the final product, additional post-processing steps may be required. This can include trimming excess material, adding surface finishes, or assembling multiple injected parts.Advantages of Injection MoldingInjection molding has numerous advantages over other manufacturing processes, including:EfficiencyInjection molding allows for high-volume production with minimal wastage. The process can produce a large number ofidentical parts within a short period, making it highly efficient for mass production.Cost-effectivenessOnce the initial mold is created, the cost per unit decreases significantly. This makes injection molding cost-effective for large-scale production runs, as the cost is spread over a large number of parts.Design flexibilityInjection molding offers design flexibility, allowing for the creation of intricate and complex parts. It enables the incorporation of features such as undercuts, threads, and varying wall thicknesses.Material optionsInjection molding supports a wide range of material options, including various thermoplastics and thermosetting plastics. This enables the production of parts with different physical properties, colors, and finishes.Limitations and ConsiderationsHigh initial costThe initial cost of tooling and mold creation can be high. However, this cost is typically offset by the cost savings achieved during large-scale productions runs.Design constraintsCertain design constraints apply to injection molding, such as draft angles and uniform wall thickness. These constraints are necessary to ensure proper mold filling, uniform cooling, and easy ejection of the part.Part size limitationsInjection molding is most suitable for producing small to medium-sized parts. Large parts may require special considerations and equipment.Parting line and gate designThe parting line, where the two halves of the mold meet, and the gate design are important considerations in injection molding. Proper placement of the parting line and gate helps prevent defects like sink marks or visible gate scars.Environmental impactInjection molding relies on the use of plastic materials, which can have a significant environmental impact. Proper disposal and recycling of plastic waste are crucial to mitigate these impacts.ConclusionInjection molding is a highly efficient and versatile manufacturing process for producing plastic parts. From the clamping of the mold to the ejection of the final part, each stepin the process is crucial to ensure high-quality parts. Understanding the advantages, limitations, and considerations of injection molding allows manufacturers to make informed decisions and optimize the production process.。
电子厂常用英语词汇.

镊子: TWEEZERS 电容: CAPACITOR顺时针方向:CLOCKWISE锯子: SAW电阻: RESISTOR 逆时针方向: CONTERCLOCKWISE尖嘴钳: NOSE PLIER继电器: RELAY 振动测试: VIBRATION TEST扳手: SPANNER晶振: CRYSTAL 丝印:SPRAY-PAITING鎯头: HAMMER过滤器: FILTER 烫金:METAL-STAMPING电烙铁: SOLDERING IRON 二极管: DIODES 剪钳: WIRE CUTTER三极管: TRIODE老虎钳: PLIERS 发光二极管: LIGHT EMITTING DIODE( LED)电批: TORQUE DRIVER松香: FLUX夹子: CLAMP松香笔: FLUX PEN 正极: ANODE END三角架: CROWFOOD 红胶水: EPOXYB ADHESIVE负极: CATHODE END钢网: STENCIL胶水: GLUE 硬化: CURING刮刀: SQUEEGEE 贴纸: STICKER配线:WIRING刀片: BLADE透明胶纸: OPP TAPE 冷却硬化: OVEN-CURING放大镜: VISIONSCOPE卡板: PALLET间距: PITCH调压器: BOOSTER 手推车: TROLLEYS周期:CIRCLETIME示波器: OSCILLOSCOPE烘干: BAKE 测试: DEBUG测试针: TOGGLE PINS紫外线: ULTRAVIOLET模拟: SIMULATION架子: RACK线圈: WINDING 毛细管现象: CAPILLARY ACTION支架: BRACKETS 涂层: COATING导体:CONDUCTIVEPATTERN溶剂: SOVENT介质材料: DIELETRICMATERIAL隔热板: FELT 镀通孔: PTH( PLATED THROUGH HOLE)锡条: SOLDE BAR 不合格品: NONCONFIRMING UNITS锡膏: SOLDER PASTE原料: DIRECT MATERIAL氧化: OXIDE锡炉: SOLDER-POT 辅料: INDIRECTMATERIAL额定电源: RATEDPOWER浸锡:DIG-SOLDER 试产: PILOT PRODUCTION 量产: MASS PRODUCTION焊点: SOLDERING JOINTS X 光测试: X RAY TEST焊盘: PAD/LAND 跌打测试: DROP TEST焊接: WELDING老化测试: BURN-IN TEST 超声波焊接: ULTRASONIC WELDING回流焊接: REFLOW SOLDERING波峰焊接: WAVE SOLDERING 线路板; PCB(Printed Circuit Board)回焊前: PRE-REFLOW 线路板装配: PCBA( PRINTED CIRCUIT BOARD ASSEMBLY)回焊后: POST-REFLOW 集成电路:IC( INTERGRATED CIRCUIT)回流炉: REFLOW OVEN ESD: ELECTROSTATIC DISCHARGE: 静电放电虚焊: DEWETTING ESD PREVENTION&DAMAGE: 静电防护与损坏假焊: SHORT SOLDER FMEA: FAILURE MODE AND EFFECT ANALYSIS(失效模式分析)少锡: INSUFFICENT SOLDER SPC: STASTICAL PROCESS CONTROL(统计过程控制)偏位: MISALIGNMENT IPC: INSTITUTE OF PACKING AND INTERCONNECTS(电子电路互连与封装协会)阻焊剂:SOLDER-THIEF/MASK 注塑: INJECTION MOLDING层分: DELAMINATION线路: TRACE裂: CRACKED 浮起: LIFTING回路: CIRCUIT内翘: WARPED 静电防护: STATIC SHIELDING短路: BRIGING/SHORT 翘起: LIFT 散静电: STATIC DISSIPATIVE线路开路: BROKEN TRACE 弯: BOW 防静电: ANTISTATIC。
Molding Process Introduce 注塑工艺介绍

Mold Temperature Vicat Softening point plasticization temperature rise plasticization
Process
Valve unit hot water hot water cold water cold water hot water
Advantages Improved Aesthetics Low Pressure Process Lower Part Weight Reduced CycleDefect on Every Part More Complex Process High Tooling Costs 23 Licensing Costs
Process Selection - Injection
Injection Unit The Reciprocating Screw
Ready for Injection
9
Pacific ADS Design Training November 2003
Process Selection - Injection
Pacific ADS Design Training November 2003
12
Process Selection - Injection
Standard Injection Molding
Advantages
•Fast Cycle Times •Complex Parts •High Volume •Aesthetics
Pacific ADS Design Training November 2003
Disadvantages • High Pressure Process • Limited Large Part Capability • High Tooling Cost
毕业设计(论文)-一模多腔的注塑模具结构设计及仿真分析

毕业论文(设计)题目:一模多腔的注塑模具结构设计及仿真分析(英文):The Design of Multi-cavity InjectionMould For Multi-way Buttons andSimulation Analysis院别:机电学院专业:机械设计制造与其自动化(CAD/CAM)姓名:学号:指导教师:日期:2011年5月一模多腔的注塑模具结构设计及仿真分析摘要本次设计主要特点是根据MOLDFLOW软件仿真模流分析来指导模具结构的设计。
MOLDFLOW软件模拟塑料熔体在整个注射过程中的充填、冷却及流动情况,确保获得高质量制件。
打破传统模具结构设计的试模、修模等过程,达到降低成本,提高生产率的目的。
在得到仿真分析最佳质量效果的数据、参数之后用来作为模具结构设计的依据。
本次设计主要包括:(1)模流仿真分析注射成型时熔体在型腔中的流动过程非常复杂,与许多因素如聚合物性能、制件结构、温度、压力、时间、模具结构及注射设备等有关。
仿真定量地给出成型过程的成型窗口状态参数(如压力、温度、速度等)。
(2)依据仿真的成型窗口状态参数进行整个注塑模具的结构设计。
如注射机的选择、浇注系统、成型零件、合模机构、脱模机构和冷却系统的设计,绘制模具零件图和装配图等。
关键词:仿真分析;模具设计;一模六腔;PROE建模The Design of Multi-cavity Injection Mould For Multi-way Buttons and Simulation AnalysisABSTRACTThe main features of the design is based on software simulation flow analysis MOLDFLOW to guide the design of die structure. MOLDFLOW software to simulate the injection of plastic melt in the process of filling, cooling and flow, ensuring access tohigh-quality parts. Breaking traditional mold structure design test mode, the process of repair molds, to reduce costs, improve productivity purposes. Obtained the best quality in the simulation results of the data, parameters after the design used as the basis for the mold.The design includes: (1)Moldflow injection molding simulation of melt flow in the cavity is very complex process with many factors. Such as polymer properties, parts structure, temperature, pressure, time, and injection mold structure and other related equipment. Quantitative simulation of the molding window molding process given the state parameters (such as pressure, temperature, speed, etc.). (2) Simulation based on the parameters of the molding window state the structural design of the injection mold. Such as the choice of injection machine, injection system, molded parts, mold bodies, stripping institutions and cooling system design, drawing die part and assembly drawings, etc..Keywords:Simulation Analysis;Mold Design ;Six-cavity Mold;Proe Modeling目录1绪论 (1)1.1 模具工业在国民经济中的地位 (1)1.2我国模具工业的现状 (1)1.3未来模具发展方向 (1)1.4论文的提出及研究意义 (2)2多向按键工艺分析及模具方案的初步确定 (3)2.1塑件的结构和尺寸精度及表面质量分析 (4)2.2塑件的原材料分析 (4)2.3模具方案的初步确定 (6)2.31 模具结构各个部件的分析确定 (6)2.32 总体结构方案的论证和初步确定 (6)3运用MOLDFLOW进行模具结构有限元仿真分析 (7)3.1介绍其功能 (7)3.2 MOLDFLOW分析的流程 (7)3.3应用MOLDFLOW进行分析 (8)3.31 划分产品网格 (8)3.32 选择成型材料 (9)3.33 确定最佳浇口位置 (10)3.34 创建浇注系统及优化 (11)3.35 创建冷却系统及优化 (13)3.36 成型窗口分析 (16)3.37 选择分析类型 (17)3.38 注射工艺参数的优化 (20)4多向按键的注塑模具结构的最终确定 (24)4.1型腔数目及布局的确定 (24)4.2注塑机的选择 (25)4.3分型面的设计 (27)4.4浇注系统的设计 (29)4.41主流道的设计及计算 (29)4.42定位圈 (30)4.43分流道的设计 (30)4.5浇口的设计 (32)4.51浇口形状的分析与确定 (32)4.52浇口位置的确定 (33)4.6排气系统的设计 (34)4.7模架的确定 (34)4.8推出机构的设计 (34)4.81顶杆的设计及计算 (35)4.82复位杆的设计 (36)4.83推板和推杆固定板的设计 (37)4.9合模导向机构的设计 (37)4.10成型零件的设计 (39)4.101计算成型零件的工作尺寸 (40)4.11冷却系统 (42)4.12模具工作原理 (44)5设计总结 (46)参考文献 (47)致谢 (49)附录 (50)1绪论1.1模具工业在国民经济中的地位模具是制造业的一种基本工艺装备,它的作用是控制和限制材料(固态或液态)的流动,使之形成所需要的形体。
塑胶射出成型工艺流程英文
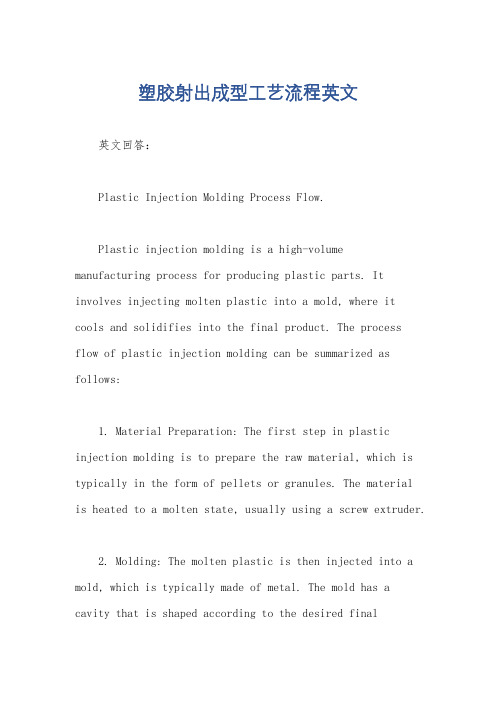
塑胶射出成型工艺流程英文英文回答:Plastic Injection Molding Process Flow.Plastic injection molding is a high-volumemanufacturing process for producing plastic parts. It involves injecting molten plastic into a mold, where it cools and solidifies into the final product. The processflow of plastic injection molding can be summarized as follows:1. Material Preparation: The first step in plastic injection molding is to prepare the raw material, which is typically in the form of pellets or granules. The materialis heated to a molten state, usually using a screw extruder.2. Molding: The molten plastic is then injected into a mold, which is typically made of metal. The mold has acavity that is shaped according to the desired finalproduct. The plastic fills the cavity and is held under pressure until it cools and solidifies.3. Cooling: Once the plastic has solidified, the moldis opened and the part is ejected. The part is then allowed to cool further before being handled.4. Finishing: The final step in the plastic injection molding process is finishing, which may involve various operations such as trimming, decorating, and assembly.中文回答:塑料注塑成型工艺流程。
品质知识竞赛题目
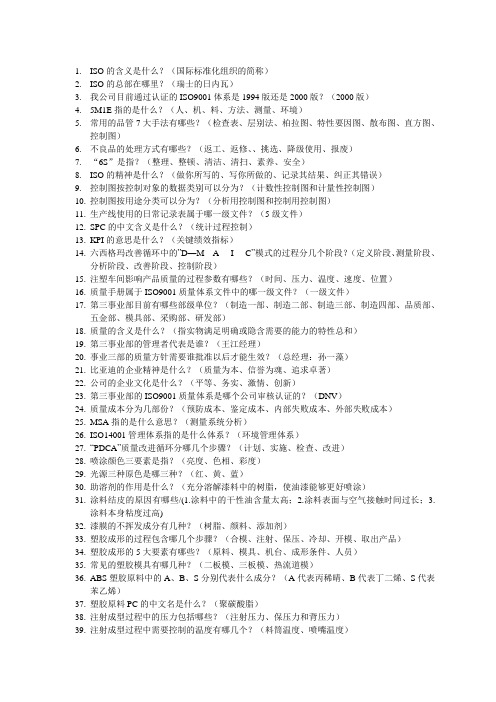
1.ISO的含义是什么?(国际标准化组织的简称)2.ISO的总部在哪里?(瑞士的日内瓦)3.我公司目前通过认证的ISO9001体系是1994版还是2000版?(2000版)4.5M1E指的是什么?(人、机、料、方法、测量、环境)5.常用的品管7大手法有哪些?(检查表、层别法、柏拉图、特性要因图、散布图、直方图、控制图)6.不良品的处理方式有哪些?(返工、返修、、挑选、降级使用、报废)7.“6S”是指?(整理、整顿、清洁、清扫、素养、安全)8.ISO的精神是什么?(做你所写的、写你所做的、记录其结果、纠正其错误)9.控制图按控制对象的数据类别可以分为?(计数性控制图和计量性控制图)10.控制图按用途分类可以分为?(分析用控制图和控制用控制图)11.生产线使用的日常记录表属于哪一级文件?(5级文件)12.SPC的中文含义是什么?(统计过程控制)13.KPI的意思是什么?(关键绩效指标)14.六西格玛改善循环中的”D—M---A----I----C”模式的过程分几个阶段?(定义阶段、测量阶段、分析阶段、改善阶段、控制阶段)15.注塑车间影响产品质量的过程参数有哪些?(时间、压力、温度、速度、位置)16.质量手册属于ISO9001质量体系文件中的哪一级文件?(一级文件)17.第三事业部目前有哪些部级单位?(制造一部、制造二部、制造三部、制造四部、品质部、五金部、模具部、采购部、研发部)18.质量的含义是什么?(指实物满足明确或隐含需要的能力的特性总和)19.第三事业部的管理者代表是谁?(王江经理)20.事业三部的质量方针需要谁批准以后才能生效?(总经理:孙一藻)21.比亚迪的企业精神是什么?(质量为本、信誉为魂、追求卓著)22.公司的企业文化是什么?(平等、务实、激情、创新)23.第三事业部的ISO9001质量体系是哪个公司审核认证的?(DNV)24.质量成本分为几部份?(预防成本、鉴定成本、内部失败成本、外部失败成本)25.MSA指的是什么意思?(测量系统分析)26.ISO14001管理体系指的是什么体系?(环境管理体系)27.“PDCA”质量改进循环分哪几个步骤?(计划、实施、检查、改进)28.喷涂颜色三要素是指?(亮度、色相、彩度)29.光源三种原色是哪三种?(红、黄、蓝)30.助溶剂的作用是什么?(充分溶解漆料中的树脂,使油漆能够更好喷涂)31.涂料结皮的原因有哪些/(1.涂料中的干性油含量太高;2.涂料表面与空气接触时间过长;3.涂料本身粘度过高)32.漆膜的不挥发成分有几种?(树脂、颜料、添加剂)33.塑胶成形的过程包含哪几个步骤?(合模、注射、保压、冷却、开模、取出产品)34.塑胶成形的5大要素有哪些?(原料、模具、机台、成形条件、人员)35.常见的塑胶模具有哪几种?(二板模、三板模、热流道模)36.ABS塑胶原料中的A、B、S分别代表什么成分?(A代表丙稀晴、B代表丁二烯、S代表苯乙烯)37.塑胶原料PC的中文名是什么?(聚碳酸脂)38.注射成型过程中的压力包括哪些?(注射压力、保压力和背压力)39.注射成型过程中需要控制的温度有哪几个?(料筒温度、喷嘴温度)40.APQP的中文含义是什么?(先期产品质量策划和控制计划)41.塑胶原料按性质可以分为哪几类?(热塑性塑料和热固性塑料)42.超声波的频率是多少?(20KHZ以上)43.PPAP的中文含义是什么?(生产件批准程序)44.超声波埋植螺母应控制的参数有哪些?(焊接时间、焊接压力、保压时间、振幅、行程高度、气压?45.目前市场上什么样的产品才具有真正的竞争力?(高品质、低成本的商品)46.QCC是什么意思?(品管圈)47.TQM的含义是什么?(全面质量管理)48.测量系统分析中GR&R值小于多少时该测量系统才是合格的?(30%)49.喷涂车间适宜喷涂作业的温度范围是多少?(18~25℃)50.喷涂车间适宜喷涂作业的湿度范围是多少?(45%~70%)51.目前喷涂车间的洁净度等级要求是多少?(喷柜1万级;其它工作区域10万级)52.喷涂车间前处理工序的设置流程是怎样的?(静电除尘、清洗、粘尘、再次静电除尘)53.目前喷涂车间底漆和中层漆的烘烤工艺采用的参数是多少?(60℃,15分钟)54.特性要因图也称为(鱼骨图、石川图、因果图)55.国际标准化组织成立于哪一年?(1947年)56.AQL的含义是什么?(允收质量水准)57.BOM的意思是什么?(物料清单)58.CPK的意思是什么?(工序能力指数)59.抽样方案可以分为哪几种?(计数性抽样方案和计量性抽样方案)60.最常用的计量性控制图是哪一种?(均值与极差图)61.柏拉图的横轴和纵轴分别代表什么?(不良项、不良比例)62.DOE的含义是什么?(实验设计)63.SOP的含义是什么?(作业指导书)64.SIP的含义是什么?(检验指导书)65.FMEA的含义是什么?(潜在失效模式与效应分析)66.质量审核可以分为几类?(第一方审核、第二方审核、第三方审核)67.不合格可以分为几类?(严重不合格、轻微不合格)68.产品的缺陷可以分为几类?(致命缺陷、严重缺陷、轻微缺陷)69.程序文件属于哪一级文件?(二级文件)70.按照公司的规定,质量体系文件中的一、二级文件需要谁批准后才能生效?(总经理)71.目前三部品质部的组织结构分为?(资源管理、品质规划、质量体系、客户服务、检测中心、文控中心)72.三部质量体系文件中对质量记录的保存期限要求为多久?(两年)73.柏拉图的作用是什么?(识别主要的不良因素)74.在分析问题时采用5W1H法,5W1H是指?(WHY为什么要做、WHO由谁做、WHAT做什么、WHERE哪里做、WHEN什么时候做、HOW如何做)75.控制图的发明者是谁?(休哈特)76.当工序能力达到±3σ时,理论上合格率能达到多少?(99.73%)77.当工序能力达到±6σ时,过程中心偏离规格中心1.5σ时,不良率应该是多少?(3.4PPM)78.在SPC中,USL、LSL分别代表什么意思?(规格上限、规格下限)79.在X-R控制图中,X图、R图分别反映了什么?(分别反映是否存在异常原因和偶然原因)80.IPQC日常工作中的作业依据是什么?(SIP)81.SPC中的σ代表什么意思?(总体标准差,即过程变差)82.按照卡尺的结构分类,可以分为哪几类?(游标类、带表类、数显类)83.颜色产生的三要素是指?(观测者、物体、照明/光源)84.人眼可以接受到的光谱波长范围在多少?(400-750nm)85.颜色按照波长值排列,其顺序应该是怎样的?(红、橙、黄、绿、蓝、靛、紫)86.千分表的最小刻度是多少?(0.001mm即1um)87.不合格的含义是什么?(不满足规范的要求)88.过程的含义是什么?(将输入转换成输出的一组彼此相关的资源和活动)89.实体的含义是什么?(可以单独描述或研究的事物)90.产品的含义是什么?(过程或活动的结果)91.全面质量管理的含义是什么?(一个组织以质量为中心,以全员参与为基础,目的在于通过让顾客满意和本组织所有成员及社会受益而达到长期成功的管理途径)92.全面质量管理的特征有哪些?(1、全面质量;2、全过程;3、全员参与)93.品质控制的发展似分为哪几个阶段?(操作者控制阶段、班组长控制阶段、检验员控制阶段、统计控制阶段、全员质量管理、全员品管)94.抽样检验中的检验水准有哪几级?(Ⅰ、Ⅱ、Ⅲ、S-1、S-2、S-3、S-4)95.抽样检验的严格程度有几种?(正常、加严、放松)96.质量方针的含义是什么?(由组织的最高管理者正式颁发的该组织总的质量宗旨和方向)97.测量系统的组成有哪些?(操作、程序、量具、设备、软件、以及操作人员)98.QS9000质量体系的目标是什么?(持续改进、预防缺陷、减少变差及浪费、顾客满意)99.SPC使用的领域是什么?(大规模生产)100.当工序能力能够达到±6σ时,理论上不良率是多少?(0.002PPM)101.第三事业部主要以塑胶模具、塑胶件、五金冲压件、Keypad产品的设计加工生产为主的。
模具零配件中英文对照解读

常用模具零件中英文对照表2005-12-19 14:51:17 中国注塑网入水:gate进入位:gate location水口形式:gate type大水口:edge gate细水口:pin-point gate水口大小:gate size转水口:switching runner/gate唧嘴口径:sprue diameter流道: runner热流道:hot runner,hot manifold热嘴冷流道: hot sprue/cold runner唧嘴直流: direct sprue gate圆形流道:round(full/half runner流道电脑分析:mold flow analysis流道平衡:runner balance热嘴:hot sprue热流道板:hot manifold发热管:cartridge heater探针: thermocouples插头:connector plug插座:connector socket密封/封料:seal运水:water line喉塞:line lpug喉管:tube塑胶管:plastic tube快速接头:jiffy quick connector plug/socker 模具零件:mold components三板模:3-plate mold二板模:2-plate mold边钉/导边:leader pin/guide pin边司/导套:bushing/guide bushing中托司:shoulder guide bushing中托边:guide pin顶针板:ejector retainner plate托板:support plate螺丝:screw管钉:dowel pin开模槽:ply bar scot内模管位:core/cavity inter-lock顶针:ejector pin司筒:ejector sleeve司筒针:ejector pin推板:stripper plate缩呵:movable core,return core core puller 扣机(尼龙拉勾):nylon latch lock斜顶:lifter模胚(架):mold base上内模:cavity insert下内模:core insert行位(滑块):slide镶件:insert压座/斜鸡:wedge耐磨板/油板:wedge wear plate压条:plate撑头: support pillar唧嘴:sprue bushing挡板:stop plate定位圈:locating ring锁扣:latch扣鸡:parting lock set推杆:push bar栓打螺丝:S.H.S.B顶板:eracuretun活动臂:lever arm分流锥:spure sperader水口司:bush垃圾钉:stop pin隔片:buffle弹弓柱:spring rod弹弓:die spring中托司:ejector guide bush中托边:ejector guide pin镶针:pin销子:dowel pin波子弹弓:ball catch喉塞:pipeplug锁模块:lockplate斜顶:anglefrompin斜顶杆:angleejectorrod尼龙拉勾:partinglocks活动臂:leverarm复位键、提前回杆:earlyreturnbar气阀:valves斜导边:anglepin术语:terms承压平面平衡:partingsurfacesupportbalance模排气:partinglineventing回针碰料位:returnpinandcavityinterference模总高超出啤机规格:moldbaseshuthight顶针碰运水:waterlineinterfereswithejectorpin料位出上/下模:partfromcavith(core)side模胚原身出料位:cavitydirectcutonA-plate,coredirectcutonB-plate. 不准用镶件:Donotuse(core/cavity)insert用铍铜做镶件:useberylliumcopperinsert初步(正式)模图设计:preliinary(final)molddesign反呵:reversecore弹弓压缩量:springcompressedlength稳定性好:goodstability,stable强度不够:insufficientrigidity均匀冷却:evencooling扣模:sticking热膨胀:theroexpansion公差:tolorance铜公(电极):copperelectrodecompre sion molding 压缩成型flash mold 溢流式模具plsitive mold 挤压式模具split mold 分割式模具cavity 型控母模core 模心公模taper 锥拔leather cloak 仿皮革shiver 饰纹flow mark 流痕welding mark 溶合痕post screw insert 螺纹套筒埋值self tapping screw 自攻螺丝striper plate 脱料板piston 活塞cylinder 汽缸套chip 细碎物handle mold 手持式模具encapsulation molding 低压封装成型、射出成型用模具two plate 两极式(模具)well type 蓄料井insulated runner 绝缘浇道方式hot runner 热浇道runner plat 浇道模块valve gate 阀门浇口band heater 环带状的电热器spindle 阀针spear head 刨尖头slag well 冷料井cold slag 冷料渣air vent 排气道welding line 熔合痕eject pin 顶出针punch 冲头insert 入块(嵌入件)deburring punch 压毛边冲子groove punch 压线冲子stamped punch 字模冲子round punch 圆冲子special shape punch 异形冲子bending block 折刀roller 滚轴baffle plate 挡块located block 定位块supporting block for location 定位支承块air cushion plate 气垫板air-cushion eject-rod 气垫顶杆trimming punch 切边冲子stiffening rib punch = stinger 加强筋冲子ribbon punch 压筋冲子reel-stretch punch 卷圆压平冲子guide plate 定位板sliding block 滑块sliding dowel block 滑块固定块active plate 活动板lower sliding plate 下滑块板upper holder block 上压块upper mid plate 上中间板spring box 弹簧箱spring-box eject-rod 弹簧箱顶杆spring-box eject-plate 弹簧箱顶板bushing bolck 衬套cover plate 盖板guide pad 导料块electrical discharge machining (EDM) 电火花加工electrical insulating property 电绝缘性能electrochemical die-sinking machine 电解型腔加工机,电解型腔加工机床electrochemical machine (ECM) 电解加工机床,电化学加工机床electrochemical machining (ECM) 电解加工,电化学加工electro-discharge cutting 电火花加工,电火花切割electro-discharge cutting machine 电火花切割机electro-discharge machine tool 电火花加工机床Electro-discharge Machine 电火花加工机床electro-discharge machining 电火花加工electro-discharge machining process 电火花加工工艺,电火花加工工序epoxy resin 环氧树脂guide bushing 导套guide pillar 导柱,导杆,导柱guide pin 导向销,导杆guide pin cover 导柱盖guide plate 导料板,导板guide plate blanking die 导板式冲裁模,导板式落料模guide post 导柱,导柱guide stock plate 挡料板injection mold 注射模,注塑模injection molding 注射成型,注塑成型injection-molding machine 注塑机,注射机,注塑成形机injection plunger 注射柱塞in-line reciprocating screw 联机往复螺杆,串联往复螺杆,直线排列往复螺杆inner ram 内滑块inserting molding 嵌件成形integrated manufacturing 集成制造internal stress 内应力13.intermediate platen 中间板,隔板塑料成型模具的主要设计要素脱模距stripper distance脱模斜度draft投影面积projected area最大开距maximum daylight;open daylight闭合高度mould-shut height抽芯距core-pulling distance抽芯力core-pulling force脱模力ejector force开模力mould opening force模内压力internal mould pressure;cavity pressure成型压力moulding pressure背压环back-up ring 1 bar = 14.5psi高压接头bite type fitting液压马达hydraulic motor冷却水流量计waterflow regulator打磨器材abrasive material打磨砂轮grinding wheels切割砂轮cutting wheels码模夹(注塑机使用) mould clamps; lifting clamps 小五金工具piping tools高压力软管high pressure hose风管,水软管air .water hose高压油表pressure gauge压力油喉hydraulic hoses光塑检测photoelastic testing吹塑模plastic blow mould注塑模plastic injection mould冲扎复合模blank & form compound die精密冲模precision blanking die熔料流动率MFR=melt flow rate熔料流动指数MET=melt flow index推板导柱guide pin for ejector plater座板clamping plate垫块space block(plate)推板ejector block(plate)afdek plate 档尘板guide stripe 行位后板cavity sub-insert 前模镶件core sub-insert 后模镶件sprue puller insert 扣针镶件stage ejector 顶棍spacer rock(risers) 间隔板变形distortion弯曲warp拖花drag marks火花纹EDM marks困气venting烧黑burns表面缩水shrinkage料位过薄/砸穿thin wall stock走水不平行uneven fill pattern夹水纹/流纹witness line;mismatch;stress marks 走水纹knit lines走水不齐short shotsorifice 料口nozzle seat 热嘴垫圈nozzle plate 射嘴板cross pin 十字头销sled 射台seal ring 封密圈spacer rail 介子座heater groove 发热管槽heater cement 发热管的结合剂soak 浸泡seat 垫圈ream 铰大圆孔直径grind 磨床drill 钻床mill 铣床caliper 卡尺G-caliper 分厘卡Depth Gauge 深厚计hardness tester 硬度计angle gauge 角规marble table 云台石projector 投影仪height gauge 高度仪microscope 显微镜plug gauge 塞规leveller 水平器R gauge R 规Inter caliper 内分厘卡surface 平面仪item number 细目编码catalog number 材料分类编码undercut lip 倒扣口hot tip = hot drop = nozzle 热嘴blow-off strip 放气板blow-off nozzle 吹风口spiral hose 螺旋式的连接喉rust solvent 除锈剂shaft 曲轴ensile strength 拉伸力yield strength 屈服力spark erosion 电火花蚀刻etch(photo-etch) 电蚀harden 淬硬copper electrode 铜公corrosion resistance 耐腐蚀anneal 退火heat treatment 淬火FEM(finite elemnet method) 有限元法preliminary tool design 初期模具设计图zone 热流道区域reverse taper 倒啤把clamp plate 码板toggle clamp 快速夹vacuum furnace 真空炉cavity insert rounds 圆柱镶件cavity insert b0locks 方柱镶件tensile strength 抗张强度,抗拉强度Concept drawing 概念图Assembly drawing 装配图mismatch;witness line 夹纹shut-off(n.) 枕位venting valves 疏气阀venting plug 疏气塞valve casing 阀门罩twist drill 旋钻harden/nitride 碎硬anneal 退火temper 回火stess crack 应力断裂corrosion resistance 防腐,防锈tensile strength 物】抗张强度,抗拉强度split mould (分离)组合式的模具inclined plate 斜面inclined bolt 斜栓jaw (工具,机械等)夹住东西的部分,钳口step change of the P/L 分形面枕位的改变thin steel section 较薄的料位clean-up 清理,清除,清扫Mold Dating Insert 模具日志镶件Hot Sprue Bushing 热浇口套semi-automatic 半自动quick disconnector 快速断开接头full shot 足量注射mismatch 夹痕;夹水纹ejector mark 顶痕screw boss 螺丝孔,螺丝基座sink mark 缩坑15% glass filled ABS 掺有15%玻璃的ABS spraying mold release 脱模剂drag mark 拖痕stress mark 应力痕reinforcement rib 加强筋slght stoning 轻度磨砂soliid line 实线dotted line 虚线internal diameter 内径external diameter 外径nickel-plated 电镀的handling hole;lifting hole 吊装孔parallel 平行块piston 活塞plunger 柱塞carrier 导轨rest 支架item number 项目编号catalog item 商品目录编码dimensional datum 尺寸基准heat treatment certification 淬硬证明文件back-up bushing 支撑导套jacking screw 起重螺丝,千斤顶tapped hole (带有螺旋角度的)螺丝孔diagonal corner 成对角的角落burn mark 烧痕hot runner mainfold (热流道板)分流板texuring 蚀纹clamping screw (注塑机)码模螺丝imperial 英制的metric 公制的puller bushing 水口套puller bar 水口铁drool bushing 防漏胶套筒safety switch 限位制water line connected internally or hard tubing 不可用胶喉连接运水lifter on square rod or locked from rotation 用方形柱或用管钉止转gate insert 入水镶件gate shut-offs 流道开关配件guided ejection 中托司parting line shutoff 前后模接触面waterlines clear tie bars. 运水喉咀接驳位要避开啤机呵林柱. BGV=Balanced Gate Value 平衡入水值spacer 垫块pocket 挖槽rough 粗加工finish 精加工plunge rate 进刀率retract rate 提刀速率splindle rate 主轴转速coolant 冷却液SPLIT RING 开口环(钥匙圈)侧向抽芯力side pulling-core forceconvert.transfer 转图guide pin 边针Tee slot cutter T 形SLOT CUTTER zigzag 双向切削constant overlap spiral 等距环切parallel spiral 环绕切削parallel spiral clean corners 环切并清角morph spiral 依外形环绕true spiral 螺旋切削one way 单向end mill 平铣刀spher mill 球刀bull mill 圆鼻刀face mill 面铣刀rad mill 圆角成型刀chamfer mill 倒角刀slot mill 槽刀taper mill 推拔铣刀dove mill 鸠尾铣刀lot mill 棒状drill 钻孔reamer 纹刀bore bar 搪刀tap RH 右牙刀Tap LH 左牙刀ctr Drill 中心钻spot drill 点钻cntr bore 沉头孔刀c. sink 鱼眼孔钻loft surface 举升曲面coons surface 昆氏曲面ruled surface 直纹曲面revolved surface 旋转曲面swept surface 扫描曲面draft surface 牵引曲面grinding wheel 磨砂使用的轮子quench steel 将...淬火,使冷却stress relieving 应力消除molten 熔热的oxide film 氧化层guide pin and sleeve, locating ring ,导边,司筒,定位圈ejector ,ejector balde, ejector sleeve,顶针,扁顶针,顶针司筒, lifters, wear plate,horn pin,斜坊,磨损板,气顶针,O ring, water baffle, water pipe plug,O 形圈,隔片,运水管道塞, water line connector,wear plate ,运水管道转接头,耐磨板air cylinder,hydraulic cylinder,氯压缸,液压缸micro switch,oil nipple, spring,开关装置,油枪接头,弹弓sprue bushing,early return system,浇口套,早期回撞装置, accelerated ejectors, slied holder,加速顶针,注塑周期计数器, cycle counter,date stamper,滑块固定板,生产日期铭牌,hot runner system ,热流道系统chemical composition 化学成份thermal conductiivity 导热性能thermal diffusivity 热扩散性能dimensonal stablity 尺寸稳定性能cooling effiency 冷却效率easiler ejection 易于脱模alloy insert 合金镶件(cooling) duct 输送管;导管maintenance cost 维护费用ultrasonic testing 超声波检测crack 断裂direct gate 直接浇口ring gate 环形浇口disk gate;disphragm gate 盘形浇口spoke gate;spider gate 轮辐浇口pin-point gate 点浇口edge gate 侧浇口submarine gate;tunnel gate 潜伏浇口fan gate 扇形浇口tab gate 护耳浇口runner plate 流道板(或冷或热)secondary nozzle 二级喷嘴torpedo;torpedo body assembly 鱼雷形组合体catridge heater 管式加热器heat pipe 热管valve gate 阀式浇口force plunger;pot plunger 柱塞flash groove;spew groove 溢料槽impression;cavity block;cavity plate 凹模punch;force 凸模movable insert;loose detail 活动镶件cavity splits;core splits(凹模拼块) (型芯拼块) 拼块side core 侧型芯thread plug;threaded core 螺纹型芯thread ring;threaded cavity 螺纹型环cutting wheel 切割砂轮grinding wheel 打磨砂轮abrasive material 打磨器材mould clamps;lifting clamp 砂模夹(注塑机使用)air (water) hose 风管,水轮管pressure gauge 高压油表hydraulic hose 压力油喉plastic blow mould 吹塑模plastic injection mould 注塑模blandk&form compound die 冲扎复合模precisiion blanking die 精密冲模MFR=melt flow rate 熔料流动率MFT=melt flow index 熔料流动指数handling hole 拉铃孔stop plate 限位块linder bush 衬套spacer block(plate) 垫块,方铁back-up ring 背位环standoff 限位块American Safety Hoist Rings. 英制安全吊装环Mechanical Properties 机械性能Tensile Strength(MPa) 抗拉强度elongation 延伸率hardness(Brinell) 硬度shear stength(MPa) 剪切力impact strength 冲韧性Physical Properties 物理性能solidification shrinkage 凝固收缩率freezing range 凝固与熔范围thermal expansion 热膨胀系数specific heat 比热thermal conductivity 热导率electrical conductivity 电导率micro-structure 金相分析hot work tool steel 热作钢circular motion 环形运动variable 变数,参数graphics window 图形窗口45 degree entry and a zero degree exit. 进刀口45 度,退刀口0 度runner stripper plate 脱料板stripper plate 活动板spacer rock(risers) 间隔板stage ejector 顶棍sprue puller insert 扣针导套guide strip 行位后板afdek plate 挡尘板side gate 大水口pinpoint gate 细水口SHCS 杯头螺丝FHCS 平头螺丝set screw 无头螺丝ball catch 波子螺丝wedge 行位较杯gib 线条,(撑鸡的导轨)latch 拉杆clamp 码仔spring guide pin 弹弓导柱steel pad disc 橙仔方ejector cam insert 斜顶块(screw) nut 螺母taper 嗲把/ 斜度taper interlock 嗲把锁texture 花纹toggle-lok 回撞装置top clamping plate 顶码板unified national coarse (UNC) 美制螺丝(粗牙) unified national fine (UNF) 美制螺丝(幼牙) set screw 喷头螺丝side gate 大水口slide retainer 行位管位water junction 喉咀spacer block 登仔jiffy-matic socket 喉咀套jiffy-tite plug 喉咀公spring plunger 弹弓座sprue puller 勾针/勾粒spring washer 弹簧塑圈stepped ejector pin 有托顶针strippers plate 推板/细水口板submarine gate 潜水口support pin 拉杆support plate 暗板surface finish 光洁度alignment strip 斜锁angle pin 斜针fan gate 扇形入水fillet 圆口ball catch 弹弓波子blade ejector 扁顶bottom clamping plate 底码板free length 自然长度bridge piece 水口铁helix spindle 锅杆hose clip 水喉箍bubbler 隔气运水jiggle 斜顶jiggle witness line 斜顶片位置center distance (CRS) 山打距离(中心线距离)clamp 码仔contour 外形leader pin 导针location ring(flange) 法兰counterbore 拔头,介子托mock-up;prototype 手办die cast 合金压铸national pipe thread(NPT) 美制喉牙overflow 垃圾位ejection sleeve 司筒,顶套epoxy 胶样pin point gate 细水口pressure plug 喉塞pressure spring 压力弹簧parting line flash 披锋burned 烧黑underfilled 缺料insert mismatch 镶件夹口ejector pins not flush 顶针有高低ejector pins skid 顶针滑动insert flash 镶件披锋pressure transducer 压力探测头hydraulic schematic 油积筒油路接驳图jiffy connector recessed 安装喉嘴后不可突出模胚knock out pullback stud -flush with clamp plate 顶棍镶件与底板有否空间safety switches 限位开关stop block 限位块safety strap 安全带drool bushing 防漏胶套筒insert mismatch 镶件夹口EDM visible 明显火花纹lifter scrapes 斜顶拖花short shots 走水不齐wall stock 料位厚薄knit lines 走水纹stress marks 夹水纹uneven fill pattern 走水不平行drag marks 拖花sprue pretrusion 唧嘴突出高度sprue orifice and radil size 唧嘴R 尺寸sprue bushing-keyed 唧嘴有管钉English Chinese program name 产口名称part name 零件名称tool name 模具名称tool source 模具来源tool steel 模具钢材resin 塑料program number 产品编号part number 零件编号tool number 模具编号customer 客户名称No of cavities 内模编号machine size 啤机吨数drum miller 鼓形铣床duplex horizontal miller 复式卧铣床face miller 端面铣床grinding miller 研磨机plain miller 平面铣床planer-type miller 刨式铣床rack miller 齿条铣床slab miller 大型平面铣床slot miller 键槽铣刀spline miller 花键铣刀thread miller 螺纹铣刀vertical miller 立式铣刀,立辊,立辊轧机endmill 立铣刀plastic mould steel 塑料模钢cold work steel 冷作钢hot work steel 热作钢high speed steel 高速钢electric magnetic clutch 电磁离合器pad printer 移印机screen printer 丝印机hot stamper 烫印机solid carbide slitting saw 钻石钢锯片convex cutter 凸锣刀片concave cutter 凹锣刀片side&face cutters,staggered teeth end-mill 锣刀semi-rod 半圆刀split double end 双头刀single end 单头刀2-flute 两辨3-flute 三辨4-flute 四辨reamer 直拈centre drill 中心钻solid carbide drill 钻咀zinc ingot 锌锭aluminium ignot 铝锭tin ignot 锡锭heater cement 发热管的结合剂heater groove 发热管槽spacer rail 介子座cross pin 十字头销nozzle plate 射嘴板nozzle seat 热嘴addendum 齿冠dedendum 齿根air compressor 空气压缩机air exhauster 抽气机air intake 进气口air seal 空气隔离层Mold changing systems 换模系统Mold core 模芯Mold heaters/chillers 模具加热器/冷却器Mold polishing/texturing 模具打磨/磨纹Mold repair 模具维修Molds 模具Pressing dies 压模Quick die change systems 速换模系统Quick mold change systems 快速换模系统三、模具塑料模具mould of plastics注塑模具injection mould冲压模具die模架mould base定模座板Top clamping plate Top plateFixed clamp plate水口推板stripper plateA板A plateB板B plate支承板support plate方铁spacer plate底针板ejector plate面针板ejector retainer plate回针Return pin导柱Guide pin有托导套Shoulder Guide bush 直导套Straight Guide bush动模座板Bottom clamp plate Moving clamp plate基准线datum line基准面datum plan型芯固定板core-retainer plate 凸模固定板punch-retainer plate 顶针ejector pin单腔模具single cavity mould多腔模具multi-cavity mould多浇口multi-gating浇口gate缺料starving排气breathing光泽gloss合模力mould clamping force锁模力mould locking force挤出extrusion开裂crack循环时间cycle time老化aging螺杆screw麻点pit嵌件insert活动镶件movable insert起垩chalking浇注系统feed system主流道sprue分流道runner浇口gate直浇口direct gate , sprue gate轮辐浇口spoke gate , spider gate点浇口pin-point gate测浇口edge gate潜伏浇口submarine gate , tunnel gate料穴cold-slug well浇口套sprue bush流道板runner plate排飞槽vent分型线(面)parting line定模stationary mould,Fixed mould动模movable mould, movable half上模upper mould,upper half下模lower mould,lower half型腔cavity凹模cavity plate,cavity block拼块split定位销dowel定位销孔dowel hole型芯core斜销angle pin, finger cam滑块slide滑块导板slide guide strip楔紧块heel block, wedge lock拉料杆sprue puller定位环locating ring冷却通cooling channel脱模斜度draft滑动型芯slide core螺纹型芯threaded core热流道模具hot-runner mould绝热流道模insulated runner mould熔合纹weld line (flow line)三板式模具three plate mould脱模ejection换模腔模具interchangeable cavity mould 脱模剂release agent注射能力shot capacity注射速率injection rate注射压力injection pressure差色剂colorant保压时间holdup time闭模时间closing time定型装置sizing system阴模female mould,cavity block阳模male mould电加工设备Electron Discharge Machining数控加工中心CNC machine center万能铁床Universal milling machine卧式刨床Horizontal planer车床Engine lathe平面磨床Surface grinding machine去磁机Demagnetization machine万能摇臂钻床Universal radial movable driller 立式钻床Vertical driller超声波清洗机Ultrasonic clearing machine compre sion molding压缩成型flash mold溢流式模具plsitive mold挤压式模具split mold分割式模具cavity型控母模core模心公模taper锥拔leather cloak仿皮革shiver饰纹flow mark流痕welding mark溶合痕post screw insert螺纹套筒埋值self tapping screw自攻螺丝striper plate脱料板piston活塞cylinder汽缸套chip细碎物handle mold手持式模具(移转成型用模具)encapsulation molding低压封装成型(射出成型用模具)two plate两极式(模具)well type蓄料井insulated runner绝缘浇道方式hot runner热浇道runner plat浇道模块valve gate阀门浇口band heater环带状的电热器spindle阀针spear head刨尖头slag well冷料井cold slag冷料渣air vent排气道welding line熔合痕eject pin顶出针knock pin顶出销return pin回位销反顶针sleave套筒stripper plate脱料板insert core放置入子runner stripper plate浇道脱料板guide pin导销eject rod (bar)(成型机)顶业捧subzero深冷处理three plate三极式模具runner system浇道系统stress crack应力电裂orientation定向sprue gate射料浇口,直浇口nozzle射嘴sprue lock pin料头钩销(拉料杆)slag well冷料井side gate侧浇口edge gate侧缘浇口tab gate搭接浇口film gate薄膜浇口flash gate闸门浇口slit gate缝隙浇口fan gate扇形浇口dish gate因盘形浇口diaphragm gate隔膜浇口ring gate环形浇口subarine gate潜入式浇口tunnel gate隧道式浇口pin gate针点浇口Runner less无浇道(sprue less)无射料管方式long nozzle延长喷嘴方式sprue浇口;溶渣根据中文词汇查所关心的技术问题,解决实际工作中的难题例如,在汉语词汇中看到——高速冲孔废料上跳(かす上り、scrap jump )词汇,到网上一搜,中图分类号TG382.6,文章编码:1671-3508-2008-10-07-517,“高速冲压中防止冲孔废料上跳的方法”一文会告诉你引起高速冲孔废料上跳的原因,不外乎有油膜粘连、真空吸附、刃口磨损、磁性未退四个主要方面,解决这些问题有三个方向的思路可以考虑,具体手段有“毛糙面”法、“斜刀口”法、“硅胶顶出”法、“凹模刃口倒退拔”法,等等。
注塑车间管理提案范文

注塑车间管理提案范文英文回答:Title: Proposal for Injection Molding Workshop Management.Introduction:The injection molding workshop plays a crucial role in the manufacturing process. However, there are certain areas that require improvement in terms of efficiency, quality control, and overall management. This proposal aims to address these issues and provide recommendations for enhancing the performance of the injection molding workshop.1. Enhancing Efficiency:To improve efficiency in the injection molding workshop, the following measures can be implemented:a) Optimizing Workflow: Streamlining the workflow by reorganizing workstations, ensuring smooth material flow, and minimizing downtime between production cycles.b) Implementing Lean Manufacturing Principles: Adopting lean manufacturing principles such as 5S, Just-in-Time, and Kaizen to eliminate waste, reduce lead times, and improve overall productivity.c) Automation and Robotics: Introducing automation and robotics in the injection molding process to increase production speed, reduce manual labor, and enhance precision.2. Quality Control:To ensure consistent quality in the injection molding process, the following steps can be taken:a) Regular Maintenance and Calibration: Implementing a preventive maintenance schedule for machines and equipment, along with regular calibration of measuring instruments toensure accuracy.b) Statistical Process Control (SPC): Implementing SPC techniques to monitor and control the injection molding process, identifying and addressing any variations or defects in real-time.c) Training and Skill Development: Providing comprehensive training programs for operators and technicians to enhance their knowledge and skills in injection molding techniques, troubleshooting, and quality control.3. Inventory Management:Efficient inventory management is crucial for the smooth operation of the injection molding workshop. The following strategies can be employed:a) Just-in-Time (JIT) Inventory System: Implementing a JIT inventory system to minimize inventory holding costs, reduce waste, and ensure timely availability of rawmaterials.b) Vendor Management: Establishing strong relationships with reliable vendors to ensure a steady supply of high-quality raw materials at competitive prices.c) Inventory Tracking and Analysis: Utilizing inventory management software to track inventory levels, analyze usage patterns, and make data-driven decisions for procurement and stock control.中文回答:标题,注塑车间管理提案。
模具专业英语术语

中文 模具设计术语 三板模 二板模 高光蒸汽注塑模 气体辅助成型模具 双物料成形模具 叠层模具 低压注塑模具 镁、铝合金压铸模具 SMC热压模具 通用模具 单腔模具 多腔模具 组合模 注射模 热固性塑料模 热塑性塑料模 双色模 试验模 正式模 快速模 英文 3-plate mold 2-plate mold High Class Steam Injection Mold Gas Assisted Injection Mold 2 K Injection Mold Stack Mold Low Presure Injection Mold Mg & AI Die-Casting Mold SMC Mold universal mold single cavity mold multi cavity mold segment mold injection mould mould for thermosets mould for thermoplastics 2-shot molding Trial mold Production mold Prototype mold 欧洲习语 美国习语 备注
浇道系统 冷料井 射料浇口/直浇口 侧浇口 侧缘浇口 搭接浇口 薄膜浇口 闸门浇口 缝隙浇口 扇形浇口 盘形浇口 隔膜浇口 环形浇口 潜入式浇口 隧道式浇口 针点浇口 无浇道 水口形式 进入位 水口大小 转水口 唧嘴口径 主流道 分流道 浇口 护耳浇口 模具号 产品号 产品名称 产品材质 每啤重量 产品重量 成型周期 工程图 装配图 设计任务书 产品开发 目录 设计资料 附件 公制 英制 设计更改
runner system slag well / Cold-slug well sprue gate / Direct gate side gate edge gate tab gate film gate flash gate slit gate fan gate dish gate diaphragm gate ring gate subarine gate (sub marine gates) tunnel gate pin gate / Pin-point gate Runner less gate type gate location gate size switching runner/gate sprue diameter Sprue Runner Gate tab gate Tool number Part number Part Name Part material Shot weight Moulded part weight Cycle time procedure drawing assembly drawing master schedule Product development Contents Design documentation Attachments metric system Imperial Unit design modification
金属注塑成型工艺
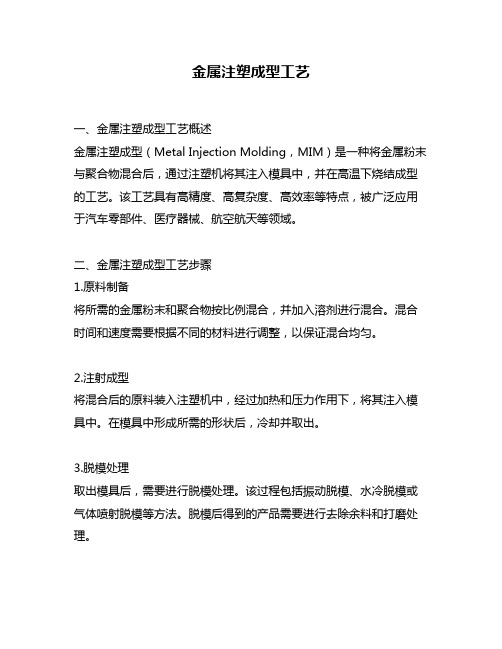
金属注塑成型工艺一、金属注塑成型工艺概述金属注塑成型(Metal Injection Molding,MIM)是一种将金属粉末与聚合物混合后,通过注塑机将其注入模具中,并在高温下烧结成型的工艺。
该工艺具有高精度、高复杂度、高效率等特点,被广泛应用于汽车零部件、医疗器械、航空航天等领域。
二、金属注塑成型工艺步骤1.原料制备将所需的金属粉末和聚合物按比例混合,并加入溶剂进行混合。
混合时间和速度需要根据不同的材料进行调整,以保证混合均匀。
2.注射成型将混合后的原料装入注塑机中,经过加热和压力作用下,将其注入模具中。
在模具中形成所需的形状后,冷却并取出。
3.脱模处理取出模具后,需要进行脱模处理。
该过程包括振动脱模、水冷脱模或气体喷射脱模等方法。
脱模后得到的产品需要进行去除余料和打磨处理。
4.烧结处理将脱模后的产品放入烧结炉中进行高温处理。
该过程需要根据不同材料的特性进行调整,以确保烧结后得到的产品具有所需的物理和化学性质。
5.表面处理经过烧结后,得到的产品需要进行表面处理。
该过程包括抛光、电镀、喷漆等方法,以提高产品的美观度和耐腐蚀性能。
三、金属注塑成型工艺优缺点优点:1.可以制造出形状复杂、精度高的零部件;2.生产效率高,可以大批量生产;3.原料利用率高,可以减少废料产生;4.生产过程中无需加工,可以节约成本。
缺点:1.设备投资较大;2.原料成本较高;3.对模具和设备要求较高;4.生产周期长。
四、金属注塑成型工艺应用领域1.汽车零部件:如变速器齿轮、离合器片等;2.医疗器械:如手术器械、牙科器械等;3.航空航天:如导弹零部件、发动机零部件等;4.电子产品:如手机外壳、电脑散热器等。
五、金属注塑成型工艺未来发展趋势1.材料的多样化:随着技术的不断发展,将会有更多种类的材料被应用于金属注塑成型中;2.精度的提高:随着生产技术的不断提高,金属注塑成型可以制造出更加精密的零部件;3.环保性能的提高:随着环保意识的不断增强,金属注塑成型将会在原料和生产过程中更加注重环保性能。
磁吸充电宝生产工艺流程

磁吸充电宝生产工艺流程英文回答:Magnetic Charging Treasure Production Process Flow.1. Material Preparation.Collect raw materials such as PC materials, ABS materials, electronic components, and magnets.2. Mold Manufacturing.Design and manufacture molds for the charging treasure shell and internal components.3. Injection Molding.Melt the raw materials and inject them into the molds to form the shell and internal components.4. Component Assembly.Assemble the internal components, including the battery, circuit board, and magnetic module, into the shell.5. Magnetic Charging Module Assembly.Assemble the magnets and magnetic charging coilsinto the charging module.6. Testing.Conduct functional testing on the assembledcharging treasure to ensure its performance meets specifications.7. Packaging.Package the finished charging treasure in appropriate packaging for storage and transportation.中文回答:磁吸充电宝生产工艺流程。
塑料常用成形工艺英汉对照资料

各种常用成形工艺英汉对照塑料成型injection molding 射出成形 (注塑成型)extrusion molding 挤出成形 (挤出成型) calendaring molding 压延成形 (压延成型) hollow(blow) molding 中空(吹出)成形matched mould thermal forming 对模热成形 compression molding 压缩成形 (压制成型) transfer molding 转送成形 (传递模塑成型)slush molding 凝塑成形 (搪塑)rotational molding 离心成形 (滚塑)foam forming 发泡成形 (发泡成型)dip mold 浸渍成形encapsulation molding 注入成形 (封装成型)matched die method 对模成形法compound molding 复合成形laminating method 被覆淋膜成形rubber molding 橡胶成形/tips/tips_process_methods.htm Plastic Processing MethodsPROCESS DESCRIPTIONBlow吹塑 An extruded parison tube of heated thermoplastic is positioned between two halves of an open split mold and expanded against the sides of the closed mold via air pressure. The mold is opened and the part ejected. Low tool and die costs, rapid production rates, and ability to mold fairly complex hollow shapes in one piece.Calendering压延 Dough-consistent thermoplastic mass is formed into a sheet of uniform thickness by passing it through and over a series of heated or cooled rolls. Calenders are also utilized to apply plastic covering to the backs of other materials. Low cost, and sheet materials are virtually free of molded-in stresses.Casting Liquid plastic, which is generally thermoset except for acrylics, is poured into a mold without pressure, cured, and taken from the mold. Cast thermoplastic films are produced via building up the material (either in solution or hot-melt form) against a highly polished supporting surface. Low mold cost, capability to form large parts with thick cross sections, goodsurface finish, and convenient for low-volume production.Centrifugal casting离心浇铸 Reinforcement is placed in mold and is rotated. Resin distributed through pipe; impregnates reinforcement through centrifugal action. Utilized for round objects, particularly pipeCoating被覆 Process methods vary. Both thermoplastics and thermosets widely used in coating of numerous materials. Roller coating similar to calendering process. Spread coating employs blade in front of roller to position resin on material. Coatings also applied via brushing, spraying, and dipping.Cold pressure molding冷压力成型 Similar to compression molding in that material is charged into a split mold; it differs in that it employs no heat, only pressure. Part cure takes place in an oven in a separate operation. Some thermoplastic billets and sheet material are cold formed in a process similar to drop-hammer die forming or fast cold-form stamping of metals. Low-cost matched-tool moldings exist which utilize a rapid exotherm to cure moldings on a relatively rapid cycle. Plastic or concrete tooling can be used. With process comes ability to form heavy ortough-to-mold materials; simple, inexpensive, and often has rapid production rate.Compression molding模压成Principally polymerized thermoset compounds, usuallypre-formed, is positioned in a heated mold cavity; the mold is型 closed (heat and pressure are applied) and the material flows and fills the mold cavity. Heat completes polymerization andthe part is ejected. The process is sometimes used forthermoplastics. Little material waste is attainable; large, bulkyparts can be molded; process is adaptable to rapidautomation (racetrack techniques, etc.)Encapsulation 封装成型 Mixed compound is poured into open molds to surround and envelope components; cure may be at room temperature with heated postcure. Encapsulation generally includes several processes such as potting, embedding and conformal coating.Extrusion molding挤出成型 Widely used for continuous production of film, sheet, tube, and other profiles; also used in conjunction with blow molding. Thermoplastic or thermoset molding compound is fed from a hopper to a screw and barrel where it is heated to plasticity then forwarded, usually via a rotating screw, through a nozzle possessing the desired cross section. Production lines require input and takeoff equipment that can be complex. Low tool cost, numerous complex profile shapes possible, very rapid production rates, can apply coatings or jacketing to core materials (such as wire).Filament Excellentstrength-to-weight. Continuous, reinforcedwinding filaments, usually glass, in the form of roving are saturated with resin and machine-wound onto mandrels having shape ofdesired finished part. Once winding is completed, part andmandrel are cured; mandrel can then be removed throughporthole at end of wound part. High-strength reinforcementscan be oriented precisely in direction where strength isrequired. Good uniformity of resin distribution in finished part;mainly circular objects such as pressure bottles, pipes, androcket cases.Injection molding注塑成型 Very widely used. High automation of manufacturing is standard practice. Thermoplastic or thermoset is heated to plasticity in cylinder at controlled temperature, then forced under pressure through a nozzle into sprues, runners, gates, and cavities of mold. The resin undergoes solidification rapidly, the mold is opened, and the part ejected. High production runs, low labor costs, high repoducibility of complex details, and excellent surface finish.Laminating 层合成型 Material, usually in form of reinforcing cloth, paper, foil, metal, wood, glass fiber, plastic, etc., preimpregnated or coated with thermoset resin (sometimes a thermoplastic) is molded under pressure greater than 1000psi (7Mpa) into sheet, rod, tube or other simple shapes. Excellent dimensional stability offinished product; very economical in large production of parts.Matched-die- molding A variation of the conventional compression molding this process employs two metal molds possessing a close-fitting, telescoping area to seal in the plastic compound being molded and to allow trim of the reinforcement. The mat or preform reinforcement is positioned in the mold and the molds is closed and heated under pressures of 150-400 psi (1-3 Mpa). The mold is then opened and the part is removed.Pultrusion This process is similar to profile extrusion, but it does not provide flexibility and uniformity of product control, and automation. Used for continuous production of simple shapes (rods, tubes, and angles) principally incorporating fiberglass or other reinforcement. High output possible.Rotational molding滚塑成型 A predetermined amount of powdered or liquid thermoplastic or thermoset material is poured into mold; mold is closed, heated, and rotated in the axis of two planes until contents have fused to inner walls of mold; mold is then opened and part is removed. Low mold cost, large hollow parts in one piece can be produced, and molded parts are essentially isotropic in natureSlush molding 搪塑Powdered or liquid thermoplastic material is poured into a mold to capacity; mold is closed and heated for apredetermined time in order to achieve a specified buildup of partially cured material on mold walls; mold is opened and unpolymerized material is poured out; and semifused part is removed from mold and fully polymerized in oven. Low mold costs and economical for small production runs.Thermoforming 热成型Heat-softened thermoplastic sheet is positioned over male or female mold; air is evacuated from between sheet and mold, forcing sheet to conform to contour of mold. Variations are vacuum snapback, plug assist, drape forming, etc. Tooling costs are generally low, large part production with thin sections possible, and often comes out economical for limited part production.Transfer molding传递模塑成型Related to compression and injection molding processes. Thermoset molding compound is fed from hopper into a transfer chamber where it is then heated to plasticity; it is then fed by a plunger through sprues, runners, and gates into a closed mold where it cures; mold is opened and part ejected. Good dimensional accuracy, rapid production rate, and very intricate parts can be produced.Wet-lay up or contact molding Several layers, consisting of a mixture of reinforcement (generally glass cloth) and thermosetting resin are positioned in mold and roller contoured to mold’s shape; assembly isusually oven-cured without the application of pressure. Inspray molding, a modification, resin systems and choppedfiber are sprayed simultaneously from a spray gun against themold surface. Wet-layup parts are sometimes cured underpressure, using vacuum bag, pressure bag, or autoclave, anddepending on the method employed, wet-layup can be calledopen molding, hand layup, sprayup, vacuum bag, pressurebag, or autoclave molding. Little equipment required, efficient,low cost, and suitable for low-volume production of parts./classselection/interpretationscontent.aspPLASTICS MANUFACTURING OR PROCESSING Calendering: Plastic Material is compounded in a Banbury mixer, which is a housing around two eccentric rolls. After the material is introduced a weight is applied to the top of the material and the mechanical motion and heating causes the material to soften and become plastic. This material is dumped and usually goes to "warming" rolls which are usually two roll mills similar to those found in making rubber. From here the material is fed into calender rolls and comes out as a uniform thick sheet. It can be passed through embossing rolls to imprint a pattern. It is then passed over a series of cooling cans, and is wound into rolls.Casting: There are several methods and the most common are discussed below:(a) Cold Casting: Liquid plastics or resins are mixed with inert materials such as clays, limestone or marble chips. The plaster-like material is then trowelled, or otherwise applied to a thick shape or mold. After air curing the item is removed, finished by grinding, sawing or filing.(b) Foam Casting: A mixture of plastics such as Urethane and a foaming agent are introduced into the bottom of a mold, which is closed and clamped. They may be passed through an oven or the reaction of the liquid may cause enough heat to expand and fill the mold. The molds are then opened, the pieces removed and cleaned to remove the flash at the mold parting line. Foam casting can also be done by running the mixed liquid onto paper on a moving conveyor. This is then passed through an oven where it rises and loses any volatiles, and cures. At the end of the oven, the material is cut into a sheet or coiled into rolls.c) Sheet Casting: A liquid plastic such as an Acrylic resin is poured between glass panels which acts as a mold. These are placed in hot vats until the plastic polymerizes and solidifies. The glass is removed, the plastic is cut into strips, and stamped, usually in power presses, to form buckles or buttons for ladies dresses.Extrusion: In this process a continuous flow of molten plastic is formed through a shaped opening called a die, and the plastic is then cooled. Depending on the shape of the opening, many different parts can be made. If the opening is like a ring, a tube or pipe can be made. If the opening is a long thin slit, a sheet may be formed. While the die determines the shape of the plastic flow, many different methods are used "down stream" to make different types of parts. In some instances a cooling bath may be used while at other times air jets, water sprays, fans, vacuum pulling conveyor is used to pull the extrusion along the line. As the part leaves the "take off" it may be sawed to special lengths, coiled, spooled, sheared or punched, depending on the requirements of the piece. Fabrication:Cutting, cementing or heat sealing: Plastic sheets are cut on wood working types of machines, then cemented, glued or heat sealed to form final assemblies. Finished sheets can be cut in the dies of various presses such as is used in the leather, textile or metal forming industries. These parts can be glued, heat sealed, or embossed to form a variety of items such as, file folders, panels for auto interiors, tarpaulins, etc.(b) Machining or grinding: Extruded rods, tubes, etc. are machined on lathes, screw machines or grinders to form beads, tubes, balls, etc. as final parts or products.Molding (or Forming): The term "molding" is often applied to operations that do not involve power presses and probably are more accurately described as "forming" or "fabrication." Code 4484 applies to the former; code 4452 to the latter. There are a variety of methods and although not necessarily all-inclusive, the listing below should describe most that would be encountered:(a) Blow Molding: This is a modification of injection molding and presently involves forming in one of two methods. The first involves extruding a tube of heated soft plastic which is gravity fed into the open mold. The operation is timed so that the molds are closed over the material, air is injected into it thereby forcing the plastic to conform to the shape of the mold. The molds are then cooled and the finished part removed. A modification of this is the forming of the soft heated plastic (parison) over a plug through which air is injected forcing the material into the shape of the mold.(b) Cold Molding: This involves coating a mold of metal or wood with a "release" of some type followed by a "gel coat." After this layer of reinforcing material such as glass cloth or fibers and liquid resins are added to build the thickness desired. The items either air dry or cure and are then removed from the mold or form.(c) Compression Molding: Molds are mounted in hydraulic presses, usually with a vertical stroke. Plastic powders, granules, pellets or bricketts are introduced into the lower cavity of the mold, the press is closed and at the end ofthe cycle the press is opened and the parts removed either by hand or by an unloading tray. The parts are finished by cleaning the "flash" at the end of the mold parting line by tumbling, filing, sanding or machining.(d) Dip Molding: This is an outgrowth of the latex dipping industry. Involves dipping a mold into liquid plastic to form a deposit in the shape of the mold. The deposit is then blown from the mold, cut to size and finished.(e) Foam Molding: A set of molds are mounted in a hydraulic or pneumatic press. After the mold is closed, partially expanded beads of polystyrene are blown or sucked into the mold cavities. The molds are heated with steam, the beads expand further to fill the cavities. The molds are then cooled, opened and the finished parts removed.(f) Injection Molding: Hydraulic presses are used to open and close a set of molds. The plastic material in the form of granules or pellets are introduced into the hopper of an extruder. After the press is closed, the extruder forces the molten plastic into the molds through a series of runners and gates to the individual cavities. The molds are cooled by circulating water and opened and the parts removed after sufficient cooling.(g) Rotational Molding: So-called because it involves rotating the molds while in the oven and prior to cooling in a water bath. In the process a measuredamount of liquid is introduced into thin walled metal molds which are then closed and placed in a heated oven. At the same time the molds are rotated so that the liquid comes in contact with the entire inner surface of the mold. After sufficient time, the molds are removed from the oven, opened and the hollow items with an external shape like the inside of the mold are removed. The items are cleaned by using a wire brush and usually decorated with paints or enamels. This method is considered the ideal process for producing completely enclosed hollow parts and used extensively for manufacturing dolls and toys, promotional and premium items, pharmaceutical components, automotive and industrial parts.(h) Slush Molding: See Rotational Molding which is a modification of slush molding and has often replaced it.(i) Transfer Molding: A modified type of compression molding. Instead of loading the thermosetting material directly into the mold, it is first heated to the melting point but below the setting temperature and injected in a liquid state into a closed hot mold. This is accomplished by forcing the liquified material into the orifice of the mold via a pressure cylinder. A big advantage in transfer molding is in the case of complicated parts employing inserts. If a straight compression molding process were employed in such instances, the uneven flow of the compound as pressure is applied would tend to tear inserts from supports. Transfer molding, on the other hand, allows an even flow of the liquified materialthrough the contours of the mold without interference with the position of inserts or other mold parts.(j) Vacuum Molding: Sheets of plastic are softened in an oven, and then placed over a mold of wood or metal. A vacuum is formed in the space between the mold and the plastic sheet, and the plastic is drawn down to take the conformation of the mold. After sufficient cooling time, the piece is removed. The formed part must then be removed from the rest of the sheet by sawing or stamping.Filament Winding: This method is used to produce tanks that can be quite large or ducts for the chemical industry. Usually wooden molds are made and mounted so they can be rotated. Filaments of glass, nylon or other fibrous material are passed through a bath of liquid resin, then spirally wound onto the rotation form until the desired thickness is obtained. After the resin cures, the item is removed from the mold or form.Fluidizing: Low pressure air is passed through very fine solid plastic to cause it to "fluidize." Heated metal parts are then lowered into this plastic. The plastic melts and sticks to the surface of the metal. The temperature and time regulate the thickness of the coating.Plastic Laminating: This process is used in making products such as building panels, kitchen counter tops and restaurant table surfaces, etc. There are twomain processes:(a) High Pressure Laminating: This involves combining together with plastic resins layers of fibrous materials such as fabric, paper, glass fibers or other materials to form a sandwich which is fused in a press under high heat and pressure which serves to cure the plastic and set the laminate into permanent rigid form.(b) Reinforced Materials: This process involves placing pieces of glass fiber cloth or mat, paper or other material, soaked with liquid plastic, on a form or mold the shape of the end product. Although methods differ, it is possible to harden the material into permanent shape at room temperature with little or no pressure. This process makes possible the production of larger plastic products as big as a boat hull or oil truck tank body.Plastisol Processing: Plastisols are dispersions of polyvinyl chloride resin in a plasticizer. Other ingredients include stabilizers, pigments and fillers. There are three methods of molding with vinyl plastisols; rotational, slush and dip. It is possible that some items can be produced by any of the three e.g. bicycle hand grips. Rotational and slush molding are more closely related. Rotational is a modification of slush molding and has often replaced the latter. Dip molding on the other hand is an outgrowth of the latex dipping industry and has come back into being because of the particular qualities of vinyl.Plastic FamiliesThere are two basic families of plastics: Thermoplastic materials and Thermo set materials.Thermoplastics soften and melt upon the addition of heat.Upon removal of heat they then again stiffen and harden into a new shape. The Thermoplastic family is what most people relate to when they think about plastics because of the many domestic products that are produced from them. What red blooded American male does not have first hand experience with this family of plastics when as a child built Revelle models of boats, cars or other objects and then lit them on fire only to end up with an amorphous blob?The injection molding technique was developed to efficiently process this family of plastics into the many useful products we use everyday. Some of the commonly used thermoplastics are polyethylene, polypropylene, polystyrene, PVC, ABS and Nylon to name a few. There are countless other engineered plastic materials and compounds to suit broad varieties of applications.Southwest Plastics has extensive injection molding capabilities for thermoplastic materials.Thermosets harden and cure in the molding process as the molecules actually crosslink in a chemical reaction and set into a final shape. No addition of heat will soften or melt the material. As a result, thermosets have their advantage in any high heat environment where softening or melting cannot be tolerated. Domestically products such as ash trays, cooking utensils and cookware handles are produced from thermosets. Industrially thermosets are used in electrical, electronic and military applications. Some examples of thermoset materials are phenolics, epoxys, melamines and diallylphthalates.Thermosets can be molded using the compression, transfer or injection molding processes.Southwest Plastics has extensive capabilities in molding thermoset materials using all three of these processes.Processing MethodsIn order to transform plastic materials into usable shapes, many methods of processing plastics have been developed including the following: Injection molding, compression molding, transfer molding, blow molding, thermoforming, vaccu-forming, extrusion, and blown film. Each of these processes require specific expertice and skill. Southwest Plastics has expertise in COMPRESSION, TRANSFER, and INJECTION molding.Compression Molding is the first technique developed in the early 1900s to mold Bakelite (phenolic) molding compounds. It is used today to process many varieties of thermoset plastics and composites including phenolic, epoxy, melamine, and diallyl phthalate. The compression molding press is simply a vertically oriented hydraulic press. The compression mold is clamped into the compression molding press, and is simple in that it consists of two halves: the cavity and the force or core on the opposite side. The mold is heated to the temperature as specified by the material manufacturer which is usually around 300° F, and the material is placed directly in the cavity. The mold is then closed under pressure compressing the material and causing it to flow into the void between the cavity and the core. The mold is held closed for several minutes (depending on the material used and the wall thickness of the part) while the material is curing or "setting" into the form of the mold surface. The mold is then opened and the part ejected from the mold cavity. Compression molding lends itself to relatively simple parts, but since there are no sprues, runners or gates through which the material must flow, the material can be heavily loaded with a composite of fillers and fibrous reinforcements which remain in a random orientation in the molded part resulting in superior strength properties.Transfer Molding is another method for molding thermoset materials where the design of the part is too complicated or unsuitable for compressionmolding. Transfer molding is often used when metal inserts, studs, connector pins wear plates, electronic components or other parts are molded into the part. With transfer molding, the mold is clamped closed first. The material charge is then loaded into a loading "pot" which is connected to the cavity with a short runner. The material is then "transferred" from the pot to the cavity via the runner under pressure exerted from a plunger which is hydraulically actuated against the material which has been loaded in the pot.Injection molding is a high production method of producing a vast variety of thermoplastic parts into shapes ranging from fairly simple to quite complex. Injection mold cavities are fed with melted plastic material which is forced under high pressure through a sprue which feeds a runner system then through a gate into the cavity. The material is then cooled to the point that the material is solid and then ejected from the mold as a finished part. Certain thermoset materials can also be injection molded after several modifications to the standard injection molding machine are affected. The injection molding machine consists of two basic components: the clamp unit and the injection unit. The clamp unit holds and clamps the tool into position while the injection unit plasticizes and injects the material into the mold which has been positioned by the clamp unit. The clamp force must be sufficient to hold the mold closed against the hydraulic pressure of the material being injected under high pressure bythe injection unit. The rule of thumb is that there must be three tons of clamp force for every square inch of cavity projected area in the mold. Both units are coordinated by a computer controller on the machine which is programmed to efficiently to produce high quantities of consistent quality parts on an automated cycle.Southwest Plastics has been in business for over 50 years and has extensive experience in both thermoset and thermoplastic materials. We have a state of the art facility and offer molding services using compression, transfer and injection molding techniques. Let us work with you on your next project so we can become your "plastics partner"./subpage.asp?cat=3&id=37Da/Pro Rubber, Inc. offers compression molding of rubber compounds. Compression molding consists of a top and bottom plate mold that is machinedto a custom configuration (fig. 1). An elastomer preform is added between the plates and the plates are compressed under heat and pressure for a specific amount of time. The Da/Pro process monitors variables closely and adjusts to compensate for variable differences during each cycle. After the elastomer is cured properly, the mold is opened, the part is removed, the mold cleaned and the cycle repeated.Fig. 1Da/Pro Rubber, Inc. offers transfer molding of rubber compounds. Transfer molding consists of a mold cavity similar to a compression mold. In addition, the mold contains a transfer pot and a ram, where the rubber material is placed before compression. The mold cavity contains transfer holes, which connect to the transfer pot through sprues (fig. 2). During molding, the ram is compressed and compounded rubber material flows through the sprues into the mold cavity where under heat and pressure the rubber compound cures into the mold cavity configuration. Similar to compression molding, the Da/Pro process monitors all variables and compensates for differences during each cycle. After the elastomer is cured properly, the mold cavity is opened, the part is removed, the sprue is removed, the transfer pot and mold cavity are cleaned and the cycle repeated.Fig. 2Each process has advantages and disadvantages. Our experienced staff of engineers, chemists and salesmen can answer all of your questions and concerns with any of your molding needs - contact us.Compression MoldingCompression Molding has been used for many years and is a common method for thermosetting plastics or permanently hardening plastics by heating them. Compression Molding has been used in the auto industry for over 25 years and is employed in the creation of a wide variety of products including phonograph records, rubber tires, roofs, fenders, spoilers and knee replacements, to name just a few.How Does It Work?The first step in Compression Molding is loading a carefully measured amount of the chosen molding compound, called the Charge, into the bottom portion of your preheated mold. The Charge may take the form of powder, pellets, liquid or preform and should be fully formulated requiring no extra preparation to mold.Once the Charge is in place, the two halves of the mold are brought together, forcing the Charge to conform to the shape of the mold. The Charge is compressed and heated until solidified and cured into the。
全英文注塑资料注塑机结构

全英文注塑资料注塑机结构Injection Molding Machine Structure1. Injection Unit: The injection unit is responsible for melting and injecting the plastic material into the mold. It consists of a hopper, barrel, and screw. The plastic material is fed into the hopper, which then transfers it to the barrel. Inside the barrel, the plastic material is melted by the heating elements and the rotating screw. The screw also serves the purpose of pushing the molten plastic into the mold.2. Mold Clamping Unit: The mold clamping unit is responsible for securely holding the mold in place during the injection molding process. It consists of a clamping system, including a toggle mechanism or hydraulic system, that applies sufficient force to keep the mold closed. The clamping force is crucial to prevent any mold movement or leakage of molten plastic.3. Injection System: The injection system includes the injection unit and the mold clamping unit. It controls theentire injection molding process. The injection system has the capability to regulate and control the temperature, pressure, and speed of the molten plastic.7. Cooling System: The cooling system is essential torapidly cool down the molten plastic after injection. It prevents deformations and ensures the part's dimensionalaccuracy. The cooling system typically consists of cooling channels inside the mold and a cooling water circulation system outside the mold.。
- 1、下载文档前请自行甄别文档内容的完整性,平台不提供额外的编辑、内容补充、找答案等附加服务。
- 2、"仅部分预览"的文档,不可在线预览部分如存在完整性等问题,可反馈申请退款(可完整预览的文档不适用该条件!)。
- 3、如文档侵犯您的权益,请联系客服反馈,我们会尽快为您处理(人工客服工作时间:9:00-18:30)。
Howard AtkinsRevivimIsraelSPC AND INJECTION MOLDING INTRODUCTIONThis paper is based on a study at the "Raviv" injection molding factory. This plant is nowQS9000/ISO 9001 certified and works as a sub-contractor mainly in the automotive and electrical field. The aim was to define those parameters of the injection process which would be most useful for monitoring with SPC and thus reduce the need for post injection tests. As is known one of the main problem with precision injecting is the time taken for parts to acclimatize and reach their final dimensions. The need for on-line checking is vital to prevent hours of work being rejected.The study was written in 1992QUALITY"In the beginning God created......he saw all that he had created and it was good." (Genesis) Despite what should have been perfect planning and execution it was necessary to reject all mankind (apart from Noah). It is hard to say if the planning and execution were better the second time or the customer's requirements were less. Customer requirement is the driving force in today’s world. Increased operational quality reduces costs in the long run by eliminating costly rework. The basic trilogy of quality is planning, control and improvement (1). The experiment was designed to increase the control phase and thus encourage improvement. This is despite the fact that 75% of the problems are caused before the tool reaches the machine (2). SPC (Statistical Process Control) is a growing demand by customers on physical properties thus the logical step is to use SPC on the process itself, isolate the parameters to monitor and thus predict problems in advance, saving scrap and rework.SPC AND INJECTION MOLDINGThe injection process is one of complexity with many parameters of temperature, pressure and time combining dynamically to produce a complete system. The problem is to identify the parameters which will give the clearest indication of potential problems. These parameters can be divided into several groupings:1) Machine; Parameters such as back pressure, rotational speed of the screw, heater bands. These are the set by the operator and are not subject to random variance thus are not useful for SPC.2) Process; Values that are produced as a result of the above parameters, injection or plastification time, cushion or total cycle time. These values are a result of the changes in the machine or the environment and are valid for SPC.3) Product; This returns us to the original dilemma of checking the part and not the process. It has been shown that there is a connection between weight and measurements thus this was used as a control. (3,4)4) Peripheral equipment; This is a valid source of data for SPC. (5)THE EXPERIMENTThe experiment was run on standard injection molding machines in current use at the Raviv plant, Arburg and Kloekner Ferromatik with a clamping force of between 400 kN and 3500 kN and computer control. Current production runs were chosen without any special attempt to optimize conditions. The parts were weighed to an accuracy of 0.01g and the following parameters collected: Cycle, Injection, and Plastification times, Injection and Holding pressures as well as the cushion.Seven separate machines were tested using materials including PA 66 (with and without glass fibers) POM, ABS and PP and at least 100 samples were taken in groups of five from each machine.Control charts were drawn by the normal SPC methods both for groups of Injection, and Plastification times, Injection and Holding pressures as well as the cushion. Seven separate machines were tested using materials including PA 66 (with and without glass fibers) POM, ABS and PP and at least 100 samples were taken in groups of five from each machine. Control charts were drawn by the normal SPC methods both for groups of five further credence to the use of individual charts.RESULTSThe resulting charts were analyzed to find correlation between the parameters of the machine and the weight. They were further examined as to their usefulness as a tool for predicting trends.It was seen that no real correlation could be found between the parameters and the weight and what was more disturbing the control limits were so narrow that most of the charts showed processes out of control. These control limits in some cases were so narrow as to be meaningless, for example, Injection time in one chart was within control limits only 0.006 s wide. The machine can only measure in hundredths of a second, this value is therefore of no practical significance. The control limits in the individual charts are slightly wider but still fail to provide meaningful results. The Table gives some examples (all results show one order smaller than the capability of the machine to measure). The columns UCLx-LCLx and %X show the width of the control charts and that width as a percentage of the mean. Control Limits of selected parametersGROUPS of FIVE. X R UCLx LCLx UCLx-LCLx%XInjection time (s)0.2640.0060.2670.2610.006 2.41%Cycle time (s)18.720.1818.8218.610.210.57%Plastification (s) 4.400.18 4.50 4.300.20 4.59%Cushion (mm)9.040.199.158.930.22 1.21%Weight (g)34.3060.01534.31434.2970.0170.03%IndividualsX R UCLx LCLx UCLx-LCLx%XInjection time (s)0.2640.0030.2720.2560.015 5.76%Cycle time (s)18.720.1018.9818.460.53 2.81%Plastification (s) 4.400.08 4.61 4.190.269.75%Cushion (mm)9.040.099.278.810.47 5.16%Weight (g)34.3060.00734.32534.2860.0390.11%As can been seen the weight is remarkable stable with a control width of 0.11% of the mean in the individual charts. Individual charts because of the small sample size give larger control limits but a reduced range. Despite the consistency of the results , or because of them , all the parameters show that the processes are out of control.REGRESSION ANALYSISDue to these results which are useless in a conventional SPC monitoring system, either as operator drawn charts, on-line computer drawn charts or as a basis for tolerances that can be entered into the press, an attempt was made to use regression analysis. First the coefficient of correlation was obtained for the parameters in respect to the weight, as individual results, and as averages of the parameters representing the different weights.It can be seen that the only parameter that shows a consistent pattern of correlation is that of plastification time. The correlation only exist in the groups of averages and not in the individual results, this is probably due to the reduction of groups. this reduction also is the cause of the positive correlation in the results 101-200 where there are only 6 different weights as opposed to 23 in results 1-100.With this correlation established it is possible to calculate the equation of regression and use this as a basis for control. The equation for the plastification in respect to the weight is:Y = -0.142 X + 34.906Given that the mean weight is 34.35, with tolerances of ±0.1g, this equation gives us tolerances for plastification of 3.21s-4.62s . These tolerances are far more useful than the control limits of the SPC and can be entered into the injection press, to give on-line control.The fact that the plastification time showed a correlation is not surprising as this parameter gives an indication of the state of the melt and uniformity of the raw material.DISCUSSIONThe project which started as an attempt to show the importance of SPC in the control of the machines and to show the ease of using a well tried quality assurance tool in the plant failed. The major problem with SPC is that it was designed for metal workshops where the machinery is far more primitive than in injection molding. The interaction of parameters in molding is such that it is very difficult to build a definite model. A further problem is that SPC cannot deal with no change, this means that a parameter that does not change will be by definition out of control, an absurd situation. The mathematics of SPC can also cause the manufacturer that works within very close tolerances to be penalized. 20 sub-groups of 5 products were weighed , whilst the difference between the parts varied overall by 0.02 g (a part of 9.43 g), there were 2 groups out of control. This can cause rejection of parts. The demands of customers for the use of SPC are likely to cause producers to work between larger tolerances than they are capable, to prevent rejects of good parts.SPC on the parts is useful, because of the nature of polymers the dimensions can not be immediately checked. The weight as an indicator of part size can thus be used. Here again it should not be used blindly but as an indicator of trends. SPC on the weight can certainly show flash or short shots that might escape the naked eye. The control charts should not be used as the sole criteria for scraping parts, rather to ring a warning bell.It has been shown that the use of SPC on the machines themselves is limited. The narrow control limits and the complexity of isolating parameters makes each attempt a shot in the dark. The introduction of closed loop machines means that the self correction of the machines renders the control charts meaningless. In discussions with molding machine manufactures they admit that the trend to produce SPC software is a customer demand that they do not fully agree with. " It should be discussed with the automobile manufacturers and the molding factories if it is appropriate to transfer SPC defined for metal shaping to injection molding." (6). One manufacture told me of customers that bought a computerized machine just for the protocol. The continuous monitoring of computerized machines puts in question the sampling system of SPC. The computer can monitor each and every cycle for the same cost, tolerances of the parameters based on regression analysis or experience will be far more effective. The control limits that we have seen above will not allow the machine to function normally.There are other factors apart from the presses (the classic target for SPC), that affect the quality of the injection. These factors are much more easily controlled and monitored.1) Material: The homogeneity of the mixture that is feed to the machine, its dryness (a good subject for SPC) , and its initial quality.2) Temperature of the tool: The temperature of the mold can be critical. It has been shown that in a specific product 81% of dimensional changes are due to mold temperature. (7) Generally molders set the controllers of their mold heaters to a temperature, maybe check the mold after set-up and then leave it. The change in temperature in the shop between day and night can be seen on products clearly. The importance of increasing control on mold temperature can not be underestimated.3) Melt temperature: Control on this parameter is vital. To often it is not known, modern machines have thermocouples to measure this temperature which is a product of the heater bands and the shear in the cylinder. The value of this parameter is that it can give a broad picture of the functioning of several systems at once, it is also crucial in certain materials which have a very narrow processing window.4) In cavity pressure: This is generally accepted as the best basis for the V-P changeover. This gives another external point to control as well as providing the operator with a far more scientific base for his conditions.5) Optimization of conditions: This is a complex process which can take a long time. Crystalline materials that can take at least 24 hours to reach dimensional stability means that after each adjustment it is necessary to wait.CONCLUSIONS1) SPC. The possibility to control the product through SPC on the machine is very limited. If it is desired to produce SPC control charts it is only worthwhile to use one or two parameters, typically, cycle and plastification times. These will give an overall impression of the machines capabilities. It is worthwhile to control the weight by SPC, not as a rejection tool but as a easily available check on the part.2) Regression analysis : This is an interesting tool that needs to be developed. The results here give a possibility for building a useful method for stating tolerances.3) Other tools. The use of thermocouples and pressure transducers in the molds is recommended. The control of the temperature of the mold is vital to quality injection. This control is especially essential in regions with large temperature changes between day and night or between seasons. The use of thermocouples in the nozzle area of the cylinder is also vital to monitor the actual melt temperature and thus not be dependent on measurements of the temperature of the cylinder.4) Quality environment. This is perhaps the most important factor of all. Management must work to produce an atmosphere were workers are aware of the importance of " right first time ". This can only come with the drive and determination of senior management who have a real commitment to quality. The ISO 9000 qualifying procedures in this instance give a tremendous boost to the company in terms of making the whole team aware and responsible for its actions. Demming's 14 points look good on paper but they look even better when you are part of their applicationDIAGRAMSACKNOWLEDGMENTSI would like to thank all the staff at Raviv for their assistance during the collection of data and their moral and intellectual support. I would also thank Plasson for allowing me to work with Arieh in producing this paper..REFERENCES1) Juran, J.M. and Gryna, F.M. "Juran's Quality Control Handbook" N.Y., McGraw-Hill, 19882) Wortberg, J., and Hanning, D. " SPC and Process Control in Injection Molding", German Plastics, Oct 1991 pp 75-80.3) Bourdon, R. Planning and Optimizing Quality in Injection Molding", German Plastics, Oct 1991 pp 71-75 4) Whipple, B., and Kcoak, M., "Part variation in Injection Molding", Antec 1990 pp 1634-16385) Roth, R.C., Successful control of Processing through SPC Charting of Auxiliary Equipment", ANTEC 1991 pp 2352-23536) Schwab, E., " Computer Aided Quality Assurance in Injection Molding", German Plastics, Feb 1991 pp 5-87) Jaroschek, C., Three steps Towards Automatic Quality Assurance", German Plastics Feb 1992 pp 13-14。