热轧无缝钢管知识大全包括热轧无缝钢管缺陷
轧制无缝钢管常见缺陷和控制措施

轧制无缝钢管常见缺陷和控制措施广东省广州市 510700摘要:无缝钢管是用钢锭或实心管坯穿孔制成毛管,然后经热轧、冷轧或冷拔制成,一般用外径*壁厚毫米数表示。
主要用来输送流体,如输送石油、天然气、煤气、水及某些固体物料。
无缝钢管的用途非常广泛,涉及建筑、石油化工、电力、机械加工、电信、消防、汽车、船舶等行业。
随着使用范围的推广,无缝钢管自身或加工过程中出现的缺陷对安全生产影响也越来越大,本文结合常见缺陷浅析控制措施。
关键词:无缝钢管;常见缺陷;控制措施引言:我国无缝钢管从无到有经过近70年的发展,无缝钢管在产品结构、质量水平、技术装备等方面有了很大的提升,已成为世界钢管制造大国,总产量占全世界60%左右。
同时,因各种缺陷引起的安全事故也是频繁发生,现就无缝钢管缺陷产生的进行思考,进而提出控制措施,以便促进我国钢管行业的发展。
轧制无缝管常见缺陷产生的原因常见缺陷:裂纹、折叠、结巴、扎折、离层、划伤、内翘皮、夹渣等缺陷。
这些缺陷有时会同时出现,原因也是多方面的。
裂纹产生的原因:环形加热炉中管坯或毛管加热温度较高,加热时间较长,从而导致坯料表面氧化脱碳严重,且基体晶粒相对粗大。
由于脱碳层组织成分为强度较低的铁素体,在轧制过程中使管子表面严重脱碳的薄弱环节产生裂纹。
坯料本身存在夹渣、砂眼等缺陷,在轧制过程中使原有缺陷延伸细化进而形成裂纹。
折叠、夹层产生的原因:当管坯存在非金属夹杂、偏析时,有气孔存在夹杂物周边,在穿孔轧制时不能焊合形成内折叠。
管头切飞边残留物(钢屑)带到内壁形成夹层。
划痕、内翘皮产生的原因:在穿孔阶段,顶头变形在内壁形成划痕、凹坑、离层缺陷等缺陷。
钢管退火温度和冷拉余量的控制是否合理,也是形成内翘皮的原因缺陷形成的原因还包含:原材料管胚炼钢水平高低、管胚加工过程控制。
加工制造过程造成包括工艺加工设备落后原因、检测设备设置原因、工作人员工作态度原因。
常见缺陷无损检测手段主要无损检测手段及检测特点:涡流探伤、磁粉探伤、超声波探伤、水压试验。
无缝钢管生产缺陷与预防

无缝钢管生产缺陷与预防1. 引言无缝钢管是一种重要的工业材料,广泛应用于石油、化工、电力、航空、航天等领域。
然而,在无缝钢管的生产过程中存在一些缺陷问题,例如内外壁裂缝、折叠、夹层等。
这些缺陷不仅会降低无缝钢管的质量、性能,还可能导致管道泄漏、事故等安全问题。
因此,如何预防无缝钢管的生产缺陷是非常重要的。
本文将首先介绍无缝钢管生产过程中常见的缺陷问题,然后讨论预防无缝钢管生产缺陷的方法与措施,旨在提高无缝钢管的质量和安全性。
2. 无缝钢管生产过程中常见的缺陷问题2.1 内外壁裂缝内外壁裂缝是无缝钢管生产过程中最常见的缺陷问题之一。
这种裂缝可能是由于原料质量不佳、加工过程中的应力超过了材料的承受范围等原因引起的。
内外壁裂缝会导致无缝钢管在使用过程中易发生断裂,从而造成事故。
2.2 折叠折叠缺陷是指无缝钢管的内外壁出现弯曲、折叠痕迹。
这种缺陷可能是由于轧制过程中的辊形有问题、轧机调整不当等原因引起的。
折叠会使无缝钢管的强度和密封性降低,增加管道泄露的风险。
2.3 夹层夹层是指无缝钢管内外壁之间出现分层或夹杂物。
这种缺陷可能是由于材料不纯、熔炼和浇铸过程中的夹杂物等原因引起的。
夹层会降低无缝钢管的强度和耐腐蚀性,导致管道泄漏和腐蚀。
3. 预防无缝钢管生产缺陷的方法与措施3.1 严格选材要预防无缝钢管生产缺陷,首先需要严格选材。
选择质量优良的原材料可以避免原料本身存在的缺陷问题,降低无缝钢管的生产缺陷风险。
同时,进行严格的材料检测和评估,确保原材料达到相关标准和要求。
3.2 完善加工工艺加工工艺是影响无缝钢管质量的关键因素之一。
应根据钢管的不同用途和要求,制定完善的加工工艺流程。
在轧制、冷拔和热处理等工艺中,要严格控制工艺参数,确保钢管的形状、尺寸和性能达到要求,避免产生裂缝、折叠和夹层等缺陷。
3.3 质量控制与检测质量控制与检测是预防无缝钢管生产缺陷的重要手段。
应建立健全的质量管理体系,从源头控制,严格遵守相关标准和规范。
热轧钢管产品缺陷一览表

热轧钢管产品缺陷一
缺陷名称产生原因
产生工序
管坯表面砸伤,管坯表面有裂
纹
来料单位轧辊表面有异物穿孔导板材质不好
供货单位导板磨损严重或粘钢穿孔导板的形状和轧辊的形状不吻合
工艺设计导向口或受料槽不光穿孔托辊、抱辊、料钩等表面不光
滑穿孔
内孔刮伤顶头或顶杆上有凸起的部分,
束节不光滑或匹配不当
穿孔钢温偏低司炉顶头冷却水太大穿孔顶头位置过后穿孔管坯剪切斜度过大剪切钢温过低、阴阳面司炉、拔料
顶头偏离中心太多
穿孔模子磨损严重打头职工操作不规范
打头尺寸超差
责任心不够,量具不齐全,取
样不及时
穿孔
壁厚不均
打头不好外折叠
导板印
外表碰划
伤内孔折叠
缺陷一览表
预防措施及解决方法备注
严格检查进厂的管坯质量
修磨轧辊
更换供货厂家,确保导板质量
修磨或更换导板
根据辊形设计导板的尺寸
修磨或更换导向口,受料槽,多
在尾部
修磨或更换
修磨或更换
经常观察仪表,保证炉温
把水开小点
进一点顶头位置
更换剪切刀片(头部)
保证钢温、及时拨料
正确调整抱辊,轧辊左右位
置,保证轧辊中心
堆焊或更换模子
加强锻炼,提高责任心
配备各种量具,加强职工责任
心。
热轧无缝钢管质量缺陷与检测研究

热轧无缝钢管质量缺陷与检测研究发布时间:2022-05-25T00:56:30.619Z 来源:《科学与技术》2022年2月第3期作者:刘锦[导读] 本文介绍了热轧无缝钢管质量缺陷,阐述了常规无损检测技术以及各自的优劣点刘锦衡阳华菱钢管有限公司湖南衡阳 421001摘要:本文介绍了热轧无缝钢管质量缺陷,阐述了常规无损检测技术以及各自的优劣点,并对我国目前钢管质量检测方法发展状况进行了概述,希望能对热轧无缝钢管质量缺陷以及检测方法的探讨有所帮助。
关键词:热轧无缝钢管;无损检测技术;质量缺陷;检测研究无缝钢管的制造工艺有热轧、热扩、冷轧、冷拔和锻造等。
对于使用条件苛刻的环境,一般要求以热轧工艺制造,热轧无缝钢管因管体组织与性能分布连续性好、使用可靠性高、产品钢种及壁厚适应范围大,故安全级别要求较高,在使用条件相对特殊或产品径壁比数值偏低等情形下优势明显。
一、热轧无缝钢管的质量缺陷叙述根据传统定义,热轧无缝钢管常见的质量缺陷有裂纹、内折、麻面、凹陷、擦伤、折叠、分层、离层、直道、结疤、夹杂、内螺旋、青线和毛刺等。
随着工业的进步和发展,这种划分实际上已不能满足要求。
比如,对于成品油管和套管,常见的缺陷还有粘扣、丝扣断裂、螺纹超标、挤毁失效、渗漏、理化性能不合格、探伤不合格等,对于油缸用管常见的缺陷还有白点、烂斑等。
未来随着技术标准的加严和客户订货要求的不断提高,新的缺陷名称还将不断出现。
二、热轧无缝钢管常规无损检测无损检测英文全称Non Destructive Testing(NDT),是在不损害或不影响被检测对象使用性能的前提下,采用超声、电磁、射线、红外等原理技术并结合仪器对材料、零件、设备进行缺陷、化学、物理参数检测的技术。
对热轧无缝钢管来说,无损检测主要是以物理检测的方式来对钢管内部或者钢管表面状态进行相应的判断,检查所生产的管材是否达到使用标准。
目前,常用的检测方法有超声波检测(UT)、漏磁检测(MFT)、涡流检测(ET)、磁粉检测(MPT)。
无缝钢管常见缺陷(欠)分析预防及处置
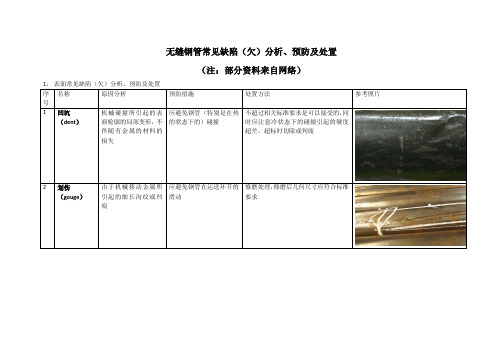
定径孔型设计不合理, 控制定径温度, 定径温度过高或过低 合理设计孔型尺寸 定径机架位置安装不 正确、 成品孔型磨损严 重、 轧制中心线偏移严 重。锯切时,夹紧装置 夹紧力不合理。 矫直辊 压下量或角度调整不 当。 调整安装位置,合理设置 成品孔型轧制量,调整夹 紧装置夹紧力、矫直辊压 下量或角度
3
无缝钢管常见缺陷(欠)分析、预防及处置 (注:部分资料来自网络)
1, 表面常见缺陷(欠)分析、预防及处置 序 号 1 名称 凹坑 (dent) 原因分析 机械碰撞所引起的表 面轮廓的局部变形, 不 伴随有金属的材料的 损失 预防措施 应避免钢管(特别是在热 的状态下的)碰撞 处置方法 不超过相关标准要求是可以接受的, 同 时应注意冷状态下的碰撞引起的硬度 超差。超标时切除或判废 参考照片
6
内直道 ( plug scores)
产生在无缝钢管内部 的细长型的凹槽, 通常 是粘着在精轧用芯棒 上的金属硬碎块引起 的
及时检查芯棒表面质量
钢管内表面允许存在深度不超过壁厚 5%(最大为0.4mm)的内直道;对深 度超标的内直道,应修磨或切除
7
辊 痕 ( rool mark)
由于轧辊调整不当或 轧辊表面有损坏所引 起的钢管表面缺欠
合理设计调质钢种、淬火 液,避免局部冷却
切除或判废
12
拉凹( stretch mill indentation)
连轧时张应力过大引 温度均匀、调整张应力 起,严重时形成拉裂、 空洞
拉凹处的实测壁厚, 不得小于壁厚所允 许的最小值;否则,应切除或判废
13
孔洞(与拉凹 相同)
2, 几何尺寸常见缺陷(欠)分析、预防及处置 序 号 1 2 名称 外径超差 椭圆度超差 原因分析 预防措施 处置方法 超上限时,重新定径; 超下限时,扩径,或改交合同 二次定径、管端定径或切除管端。 参考照片
无缝钢管常见缺陷分析预防及处置

无缝钢管常见缺陷分析预防及处置无缝钢管是一种常用的管道材料,应用广泛于石油、天然气、化工、机械等行业。
在无缝钢管的生产过程中,可能会存在一些常见的缺陷,如裂纹、气孔、夹杂物等。
本文将对这些常见的缺陷进行分析,并提出相应的预防和处置方法。
首先,裂纹是无缝钢管常见的缺陷之一、裂纹的形成可能是由于材料内部的应力超过了其强度极限,或者在加工过程中出现异常。
为了预防裂纹的产生,在生产过程中应严格控制加工温度和冷却速率,以减少应力的产生。
同时,加工过程中应合理选择合金元素的含量和轧制工艺,以提高材料的抗裂性能。
如果发现裂纹,应及时采取措施进行处置,如对裂纹进行修补或剪切。
其次,气孔也是无缝钢管常见的缺陷之一、气孔的形成可能是由于材料中存在气体或金属元素的挥发物,或者在加工过程中入侵了大量的空气。
为了预防气孔的产生,在生产过程中应严格控制材料的熔化温度和气氛的成分,以减少气体的生成。
同时,在加工过程中应加强防护措施,减少空气的侵入。
如果发现气孔,应进行补焊或采用其他方法进行修补。
夹杂物是无缝钢管常见的另一种缺陷。
夹杂物的形成可能是由于材料中存在不溶性的杂质,或者在加工过程中混入了一些外来物质。
为了预防夹杂物的产生,在生产过程中应严格控制原材料的质量,减少杂质的含量。
同时,在加工过程中应严格执行清洁规范,防止外来物质的混入。
如果发现夹杂物,应进行热处理或采用其他方法进行去除。
总结起来,无缝钢管常见的缺陷包括裂纹、气孔和夹杂物。
为了预防这些缺陷的产生,在生产过程中应控制加工温度和冷却速率,合理选择合金元素的含量和轧制工艺,严格控制材料的熔化温度和气氛的成分,加强防护措施,并严格执行清洁规范。
如果发现这些缺陷,应及时采取适当的措施进行修补或去除,以保证无缝钢管的质量和使用效果。
热轧无缝钢管缺陷及修磨
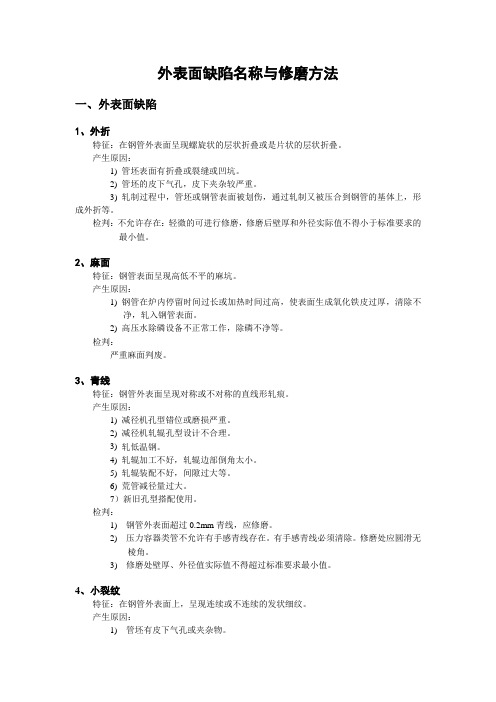
特征:钢管表面呈现高低不平的麻坑。
产生原因:
1)钢管在炉内停留时间过长或加热时间过高,使表面生成氧化铁皮过厚,清除不净,轧入钢管表面。
2)高压水除磷设备不正常工作,除磷不净等。
检判:
严重麻面判废。
3、青线
特征:钢管外表面呈现对称或不对称的直线形轧痕。
产生原因:
1)减径机孔型错位或磨损严重。
2)减径机轧辊孔型设计不合理。
7、指甲印
特征:在钢管表面纵向呈“指甲”直线状分布且每个缺陷间距一米左右。
产生原因:减径机机架在吊运时造成机架辊有撞伤,造成钢管过减径机时造成缺陷。
检判:钢管外表面不允许存在深度超0.02mm的指甲印存在,如存在应完全清除,清除后壁厚、外径实际值不得小于标准要求最小值。
8、精整拉伤
特征:在钢管表面纵向呈直线状分布一条发亮缺陷。
产生原因:精整切管机卡爪调整不当、选用卡爪规格过小及切管机设备问题造成卡
爪退不到位。
检判:钢管外表面不允许存在深度超0.02mm精整拉伤的存在。
9、精整擦伤
特征:钢管表面呈螺旋状,擦伤处表面发亮。
产生原因:矫直机后台与钢管接触后造成。
检判:钢管外表面不允许存在深度超0.02mm精整拉伤的存在。
二、修磨注意点
1、钢管外表面修磨时必需使用抛光片,严禁用磨光片。
2、钢管外表面修磨使用抛光片规格必须用100目以上,保证修磨的缺陷处光滑。
3、钢管外表面缺陷修磨时,保证整体修磨面积是缺陷修磨面积的4到5倍,修磨处应圆滑无棱角。
产生原因:穿孔机导板粘钢或导板磨损严重造成。
检判:钢管外表面不允许存在肉眼可见的导板印存在,如存在应完全清除,清除后壁厚、外径实际值不得小于标准要求最小值。
热轧无缝钢管缺陷及产生原因

热轧无缝钢管缺陷及产生原因1. 离层缺陷特征:位于钢管内表面呈纵向分布,呈凸起螺旋状,块状金属分离或破裂状夹层。
产生原因:材质不良造成有非金属夹杂物,残余缩孔或严重疏松。
2. 直道内折缺陷特征:位于钢管内表面呈纵向分布,呈现对称或单条直线形的折迭有通长,也有局部。
产生原因:芯棒润滑不良,芯棒表面有缺陷或表面附有氧化铁皮,铁屑等使钢管内表面划成沟道,荒管在轧制过程中,在连轧机孔型内过充满。
3. 内孔不规则缺陷特征:位于钢管内表面呈纵向分布,①有一个或二个相差180°的管壁增厚现象,或在钢管内表面与芯棒分离点处有壁厚增厚状,也称内鼓包。
②钢管内园呈六方形的壁厚不均状,也称内六方。
产生原因:内鼓色:连轧压下量分配或张力选择不当,使金属过充满芯棒选用不当。
内六方:张减孔型与张力参数选择不当,张减机单机架减经或总减径率较大。
4. 管壁收缩缺陷特征:位于钢管内表面上,钢管横向断面最薄处钢管内表面凹陷,壁厚局部变薄,严重的收缩几乎撕破。
产生原因:连轧机延伸过大,钢管在孔型侧壁部分,局部被拉薄连轧机各机架压下调整不当和延伸系数分配不合理。
5. 内轧疤缺陷特征:钢管内表面纵向呈指甲状结疤、凸起或块状折迭,钢管内表面压痕。
产生原因:芯棒润滑状态不良,造成芯棒局部磨损、损坏、粘金属,顶头严重磨损、粘金属、缺肉或大裂纹穿孔耳子被压在钢管的内壁上。
6. 内折迭缺陷特征:位于钢管内表面的端部,局部或纵向呈螺旋状半螺旋状或无规律分布的片状折迭。
产生原因:穿孔过程中轧机调整不当,顶头严重磨损,管坯材质不好,芯棒严重损坏。
7. 轧折缺陷特征:位于钢管内表面纵向管壁局部或全长上呈外凹里凸的皱折或在钢管外表面纵向通长有两道对称明显沟痕,一般为直线形,个别为斜线形。
产生原因:连轧荒管外径过大或荒管橢圆度太大,竹节控制强度不够或润滑状态不好,横移装置将连轧荒管碰瘪,连轧机转速错误。
8. 撕破缺陷特征:位于钢管表面纵向上管体呈现不同程度的横向破裂,菱状和椭圆状穿透管体的孔洞。
热轧无缝钢管

热轧无缝钢管热轧无缝钢管:热轧是相对于冷轧而言的,冷轧是在再结晶温度以下进行的轧制,而热轧就是在再结晶温度以上进行的轧制。
热轧无缝钢管优点:可以破坏钢锭的铸造组织,细化钢材的晶粒,并消除显微组织的缺陷,从而使钢材组织密实,力学性能得到改善。
这种改善主要体现在沿轧制方向上,从而使钢材在一定程度上不再是各向同性体;浇注时形成的气泡、裂纹和疏松,也可在高温和压力作用下被焊合。
缺点:1.经过热轧之后,钢材内部的非金属夹杂物(主要是硫化物和氧化物,还有硅酸盐)被压成薄片,出现分层(夹层)现象。
分层使钢材沿厚度方向受拉的性能大大恶化,并且有可能在焊缝收缩时出现层间撕裂。
焊缝收缩诱发的局部应变时常达到屈服点应变的数倍,比荷载引起的应变大得多; 2.不均匀冷却造成的残余应力。
残余应力是在没有外力作用下内部自相平衡的应力,各种截面的热轧型钢都有这类残余应力,一般型钢截面尺寸越大,残余应力也越大。
残余应力虽然是自相平衡的,但对钢构件在外力作用下的性能还是有一定影响。
如对变形、稳定性、抗疲劳等方面都可能产生不利的作用。
3.热轧的钢材产品,对于厚度和边宽这方面不好控制。
我们熟知热胀冷缩,由于开始的时候热轧出来即使是长度、厚度都达标,最后冷却后还是会出现一定的负差,这种负差边宽越宽,厚度越厚表现的越明显。
所以对于大号的钢材,对于钢材的边宽、厚度、长度,角度,以及边线都没法要求太精确。
无缝钢管[1]分热轧和冷轧(拨)无缝钢管两类。
热轧无缝钢管分一般钢管,低、中压锅炉钢管,高压锅炉钢管、合金钢管、不锈钢管、石油裂化管、地质钢管和其它钢管等。
冷轧(拨)无缝钢管除分一般钢管、低中压锅炉钢管、高压锅炉钢管、合金钢管、不锈钢管、石油裂化管、其它钢管外,还包括碳素薄壁钢管、合金薄壁钢管、不锈薄壁钢管、异型钢管。
热轧无缝管外径一般大于 32mm,壁厚2.5-75mm,冷轧无缝钢管外径可以到6mm,壁厚可到0.25mm,薄壁管外径可到5mm,壁厚小于0.25mm,冷轧比热轧尺寸精度高。
无缝管常见缺陷

偏析
钢中各部分化学成分和非金属夹杂物不均匀分布的现象。根据其表现形式可分:树枝状、方框形、点状偏析和反偏析等
22
缩孔残余
在横向酸浸试片的中心部位,呈现不规则的空洞或裂缝。空洞或裂缝中往往残留着外来杂质
23
非金属夹杂物
在横向酸性试片上见到一些无金属光泽,呈灰白色、米黄色和暗灰色等色彩,系钢中残留的氧化物、硫化物、硅酸盐等
无缝钢管常见缺陷名称及详细说明
序号
名称
说明
l
圆度
圆形截面的轧材,如圆钢和圆形钢管的横截面上,各个方向上的直径不等
2
形状不正确
轧材横截面几何形状歪斜,凹凸不平。如六角钢的六边不等、角钢顶角大、型钢扭转等
3
厚薄不均
钢板(或钢带)各部位的厚度不一样,有的两边厚而中间薄,有的边部薄而中间厚,也有的头尾差超过规定
4
弯曲度
轧件在长度或宽度方向不平直,呈曲线状
5
镰刀弯
钢板(或钢带)的长度方向在水平面上向一边弯曲
6
瓢曲度
钢板(或钢带)在长度和宽度方向同时出现高低起伏的波浪现象,使其成为“瓢形”或“船形”
7
扭转
条形轧件沿纵轴扭成螺旋状
8
脱方、脱矩
方形、矩形截面的材料对边不等或截面的对角线不等
9
拉痕(划道)
呈直线沟状,肉眼可见到沟底分布于钢材的局部或全长
27
晶粒粗大
酸浸试片断口上有强烈金属光泽
28
脱碳
钢的表层碳分较内层碳分降低的现象称为脱碳。全脱碳层是指钢的表面因脱碳而呈现全部为铁素体组织部分;部分脱碳是指在全脱碳层之后到钢的含碳量未减少的组织处
14
发纹
表面发纹是深度甚浅,宽度极小的发状细纹,一般沿轧制方向延伸形成细小纹缕
无缝钢管的热轧工艺常见缺陷总结

无缝钢管的热轧工艺常见缺陷总结1. 离层缺陷特征:位于无缝钢管内表面呈纵向分布,呈凸起螺旋状,块状金属分离或破裂状夹层。
产生原因:材质不良造成有非金属夹杂物,残余缩孔或严重疏松。
2. 直道内折缺陷特征:位于无缝管内表面呈纵向分布,呈现对称或单条直线形的折迭有通长,也有局部。
产生原因:芯棒润滑不良,芯棒表面有缺陷或表面附有氧化铁皮,铁屑等使钢管内表面划成沟道,荒管在轧制过程中,在连轧机孔型内过充满。
3. 内孔不规则缺陷特征:位于无缝管内表面呈纵向分布,①有一个或二个相差180°的管壁增厚现象,或在钢管内表面与芯棒分离点处有壁厚增厚状,也称内鼓包。
②钢管内园呈六方形的壁厚不均状,也称内六方。
产生原因:内鼓色:连轧压下量分配或张力选择不当,使金属过充满芯棒选用不当。
内六方:张减孔型与张力参数选择不当,张减机单机架减经或总减径率较大。
4. 管壁收缩缺陷特征:位于钢管内表面上,钢管横向断面最薄处钢管内表面凹陷,壁厚局部变薄,严重的收缩几乎撕破。
产生原因:连轧机延伸过大,钢管在孔型侧壁部分,局部被拉薄连轧机各机架压下调整不当和延伸系数分配不合理。
5. 内轧疤缺陷特征:无缝管内表面纵向呈指甲状结疤、凸起或块状折迭,钢管内表面压痕。
产生原因:芯棒润滑状态不良,造成芯棒局部磨损、损坏、粘金属,顶头严重磨损、粘金属、缺肉或大裂纹穿孔耳子被压在钢管的内壁上。
6. 内折迭缺陷特征:位于无缝管内表面的端部,局部或纵向呈螺旋状半螺旋状或无规律分布的片状折迭。
产生原因:穿孔过程中轧机调整不当,顶头严重磨损,管坯材质不好,芯棒严重损坏。
7. 轧折缺陷特征:位于合金管内表面纵向管壁局部或全长上呈外凹里凸的皱折或在钢管外表面纵向通长有两道对称明显沟痕,一般为直线形,个别为斜线形。
产生原因:连轧荒管外径过大或荒管橢圆度太大,竹节控制强度不够或润滑状态不好,横移装置将连轧荒管碰瘪,连轧机转速错误。
8. 撕破缺陷特征:位于钢管表面纵向上管体呈现不同程度的横向破裂,菱状和椭圆状穿透管体的孔洞。
无缝钢管缺陷与预防
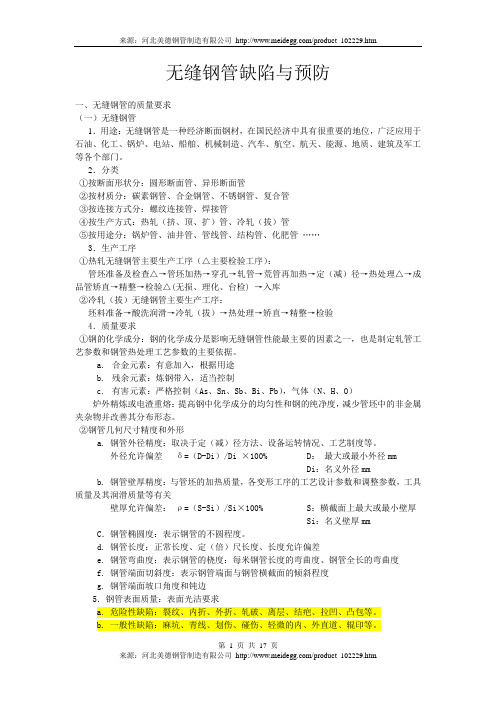
无缝钢管缺陷与预防一、无缝钢管的质量要求(一)无缝钢管1.用途:无缝钢管是一种经济断面钢材,在国民经济中具有很重要的地位,广泛应用于石油、化工、锅炉、电站、船舶、机械制造、汽车、航空、航天、能源、地质、建筑及军工等各个部门。
2.分类①按断面形状分:圆形断面管、异形断面管②按材质分:碳素钢管、合金钢管、不锈钢管、复合管③按连接方式分:螺纹连接管、焊接管④按生产方式:热轧(挤、顶、扩)管、冷轧(拔)管⑤按用途分:锅炉管、油井管、管线管、结构管、化肥管……3.生产工序①热轧无缝钢管主要生产工序(△主要检验工序):管坯准备及检查△→管坯加热→穿孔→轧管→荒管再加热→定(减)径→热处理△→成品管矫直→精整→检验△(无损、理化、台检) →入库②冷轧(拔)无缝钢管主要生产工序:坯料准备→酸洗润滑→冷轧(拔)→热处理→矫直→精整→检验4.质量要求①钢的化学成分:钢的化学成分是影响无缝钢管性能最主要的因素之一,也是制定轧管工艺参数和钢管热处理工艺参数的主要依据。
a.合金元素:有意加入,根据用途b.残余元素:炼钢带入,适当控制c.有害元素:严格控制(As、Sn、Sb、Bi、Pb),气体(N、H、O)炉外精炼或电渣重熔:提高钢中化学成分的均匀性和钢的纯净度,减少管坯中的非金属夹杂物并改善其分布形态。
②钢管几何尺寸精度和外形a. 钢管外径精度:取决于定(减)径方法、设备运转情况、工艺制度等。
外径允许偏差δ=(D-Di)/Di ×100% D:最大或最小外径mmDi:名义外径mmb. 钢管壁厚精度:与管坯的加热质量,各变形工序的工艺设计参数和调整参数,工具质量及其润滑质量等有关壁厚允许偏差:ρ=(S-Si)/Si×100% S:横截面上最大或最小壁厚 Si:名义壁厚mmC.钢管椭圆度:表示钢管的不圆程度。
d. 钢管长度:正常长度、定(倍)尺长度、长度允许偏差e. 钢管弯曲度:表示钢管的桡度:每米钢管长度的弯曲度、钢管全长的弯曲度f. 钢管端面切斜度:表示钢管端面与钢管横截面的倾斜程度g. 钢管端面坡口角度和钝边5.钢管表面质量:表面光洁要求a. 危险性缺陷:裂纹、内折、外折、轧破、离层、结疤、拉凹、凸包等。
热轧钢管的质量缺陷分析

连轧无缝钢管产品缺陷分析1.0壁厚不均壁厚不均是指钢管在同一截面上或沿长度方向上壁厚最薄点、最厚点与名义壁厚偏差较大。
(GB5310、GB3087界定为偏差值超过壁厚公差的80%)。
连轧管机组的壁厚不均主要产生在穿孔机上.其核心问题就是轧件在穿孔过程中与轧制中心线的相吻合程度,包括人口导管、轧辊、导盘(导板)、定心辊、顶杆与轧制中心线对中,以及顶杆不能弯曲;轧件在轧制过程中的稳定性(如厚壁管轧制——因顶杆较细,轧件旋转甩动较大使轧制不稳定);过大的扩径量,另外管坯加热不均(如管坯与炉底接触带即阴暗面)、定心偏斜等都会对壁厚产生不良影响。
除穿孔机外,连轧管机的辊缝调整不当也会造成壁厚不均。
穿孔机产生的壁厚不均呈螺旋状.连轧管机产生的壁厚不均呈直线状或月牙偏。
近些年新建的机组都在穿孔机上采用了机内定心.这对毛管的前端壁厚乃至整管壁厚的改进起到明显的效果。
2.0内折内折是指在钢管的内表面呈片状、直线状或螺旋状的折叠。
关于采用连铸坯轧制产生的内折问题,近年有关专家学者通过试验分析提出:内折的产生与中心疏松、芯部缩孔以及柱状晶在铸坯内呈现的程度有关。
因为严重的管坯中心疏松在穿孔的咬入阶段会造成芯部开裂并在后续的穿孔、辗压过程中形成内折:缩孔由于在加热时内表面被氧化,穿孔过程中又不能被焊合而形成内折,纵向剖开铸坯发现缩孔在铸坯内是不连续的,所以只产生管端内折而管坯内部的缩孔由于穿孔过程中形成的“隔墙”作用不会被氧化而产生内折:对柱状晶来讲,有试验表明柱状晶的粗化度越大其塑性越差,内折率越高。
还有一些研究分析表明,连铸坯的内折除与中心疏松、缩孔和柱状晶有关外,还与中心疏松区偏心有关,中心疏松区偏心的连铸坯其内折率远高于无偏心或偏心小的连铸坯。
另外,统计分析还发现内折率与碳当量大小有关,钢种的碳当量越大.生产出的钢管内折率越高。
内折是与铸坯内在质量以及材料本身有关而定心内折、顶头前压下量过大、椭圆度过大产生的内折以及加热等原因产生的内折这里不加论述。
对热轧无缝钢管生产时产生细微质量缺陷的控制要点分析

对热轧无缝钢管生产时产生细微质量缺陷的控制要点分析摘要:对于热轧无缝钢管的质量缺陷来说,其包含的形式与种类有很多。
对于不同的质量缺陷的检验而言,其标准是有所不同的。
在进行热轧无缝钢管质量缺陷的判定与表述的时候,应该结合实际的生产情况来进行分析,而不同的情况,以及不同的质量缺陷,很可能有不同的界定标准。
关键词:热轧无缝钢管;质量缺陷;控制要点引言检测和判定有缺陷的钢管,能够使企业的产品质量得到有效的保证,增强企业的市场竞争力,这是每一个生产企业需要进行的重要工艺环节。
对于无缝钢管的质量检测方法以及检测设备的改进是目前很多工程人员以及相关的专家学者工作内容的重点。
增强无缝钢管质量检测的准确性的相关研究为绝大多数无缝钢管生产企业带来了信心以及希望。
1、热轧无缝钢管分类根据热轧无缝钢管质量及用途,将其分为以下几类:构造用无缝钢管(GBT8162-1999)。
关键是用在普通结构造及机械构造。
它表示的材质为:碳素钢、20、45号钢;合金钢Q345、20Cr、40Cr、20CrMo、30-35CrMo、42CrMo等。
传送流体用无缝钢管(GBT8163-1999)。
关键是用在工程和体型较大的设备上输送流体的管道。
代表材质为20、Q345等。
低中压锅炉用无缝钢管(GB3087-1999)是用来构建各样类型的低中压锅炉过热蒸汽管、沸水管和机车锅炉用大烟管、小烟管、过热蒸汽管及拱砖管用的优质碳素结构钢热轧及冷拔(轧)无缝钢管。
代表材质为10、20号钢。
高压锅炉用无缝钢管(GB5310-1995)是用于制造高压及其以上压力的水管锅炉受热面用的优质碳素钢、合金钢和不锈耐热钢无缝钢管。
代表材质为20G、12Cr1MoVG、15CrMoG等。
高压化肥设备用无缝钢管(GB1479-2000)是适用于工作温度为-40~400℃、工作压力为10~30Ma的化工设备和管道的优质碳素结构钢和合金钢无缝钢管。
代表材质为20、16Mn、12CrMo、12Cr2Mo等。
热轧无缝钢管质量缺陷与检测方法探讨
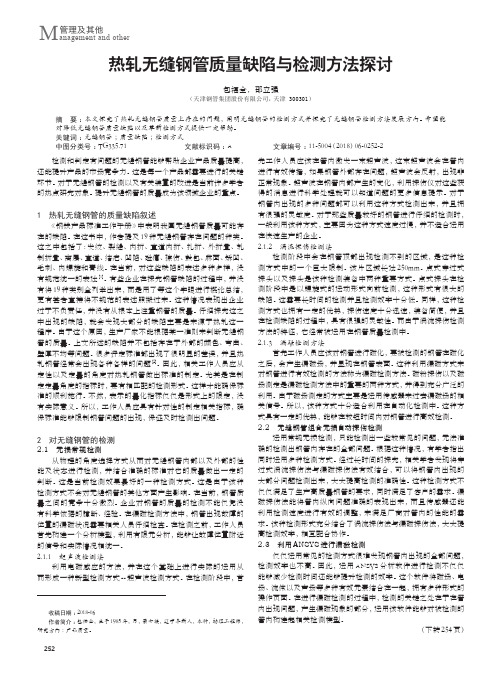
热轧无缝钢管质量缺陷与检测方法探讨包福全,邵立强(天津钢管集团股份有限公司,天津 300301)摘 要:本文探究了热轧无缝钢管质量上存在的问题,阐明无缝钢管的检测方式并探究了无缝钢管检测方法发展方向。
希望能对降低无缝钢管质量缺陷以及革新检测方式提供一定帮助。
关键词:无缝钢管;质量缺陷;检测方式中图分类号:TG335.71 文献标识码:A 文章编号:11-5004(2018)06-0252-2检测和判定有问题的无缝钢管能够帮助企业产品质量提高,还能提升产品的市场竞争力。
这是每一个产品都需要进行的关键环节。
对于无缝钢管的检测以及有关装置的改进是当前许多学者的热点研究对象。
提升无缝钢管的质量成为该领域企业的重点。
1热轧无缝钢管的质量缺陷叙述《钢铁产品标准工作手册》中表明我国无缝钢管质量可能存在的缺陷。
在这书中,作者提及19种无缝钢管存在问题的种类。
这之中包括了:发纹、裂缝、内折、直道内折、扎折、外折叠、轧制折叠、离层、直道、结疤、凹陷、碰瘪、擦伤、鼓包、麻面、矫凹、毛刺、内螺旋和青线。
在当前,对这些缺陷的表述多种多样,没有规范统一的表达[1]。
有些企业在探究钢管缺陷的过程中,并没有将19种类别全列举出来,而是用了等这个字眼进行概论总结,更有甚者直接将不规范的表述照搬过来。
这种情况表现出企业过于不负责任,并没有从根本上注重钢管的质量。
仔细探究这之中出现的缺陷,就会发现大部分的缺陷主要是来源于热轧这一程序。
由于这个原因,生产厂家不能根据某一准则来判断无缝钢管的质量。
上文所述的缺陷并不包括存在于外部的颜色、弯曲、壁厚不均等问题。
很多评定标准都出现了很明显的差误,并且热轧钢管经常会出现各种各样的问题[2]。
因此,相关工作人员应从定性以及定量的角度对热轧钢管做出标准的制定。
尤其是在制定定量角度的指标时,要有相匹配的检测形式。
这样才能确保标准的顺利施行。
不然,表示的量化指标仅仅是形式上的限定,没有实际意义。
所以,工作人员应具有针对性的制定相关指标,确保标准能够限制钢管问题的出现,保证及时检测出问题。
热轧无缝钢管缺陷
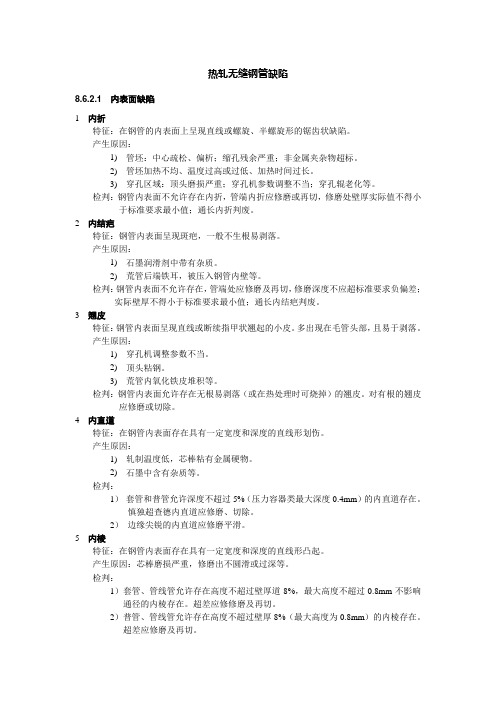
热轧无缝钢管缺陷8.6.2.1 内表面缺陷1 内折特征:在钢管的内表面上呈现直线或螺旋、半螺旋形的锯齿状缺陷。
产生原因:1) 管坯:中心疏松、偏析;缩孔残余严重;非金属夹杂物超标。
2) 管坯加热不均、温度过高或过低、加热时间过长。
3) 穿孔区域:顶头磨损严重;穿孔机参数调整不当;穿孔辊老化等。
检判:钢管内表面不允许存在内折,管端内折应修磨或再切,修磨处壁厚实际值不得小于标准要求最小值;通长内折判废。
2 内结疤特征:钢管内表面呈现斑疤,一般不生根易剥落。
产生原因:1) 石墨润滑剂中带有杂质。
2) 荒管后端铁耳,被压入钢管内壁等。
检判:钢管内表面不允许存在,管端处应修磨及再切,修磨深度不应超标准要求负偏差;实际壁厚不得小于标准要求最小值;通长内结疤判废。
3 翘皮特征:钢管内表面呈现直线或断续指甲状翘起的小皮。
多出现在毛管头部,且易于剥落。
产生原因:1) 穿孔机调整参数不当。
2) 顶头粘钢。
3) 荒管内氧化铁皮堆积等。
检判:钢管内表面允许存在无根易剥落(或在热处理时可烧掉)的翘皮。
对有根的翘皮应修磨或切除。
4 内直道特征:在钢管内表面存在具有一定宽度和深度的直线形划伤。
产生原因:1) 轧制温度低,芯棒粘有金属硬物。
2) 石墨中含有杂质等。
检判:1)套管和普管允许深度不超过5%(压力容器类最大深度0.4mm)的内直道存在。
慎独超查德内直道应修磨、切除。
2)边缘尖锐的内直道应修磨平滑。
5 内棱特征:在钢管内表面存在具有一定宽度和深度的直线形凸起。
产生原因:芯棒磨损严重,修磨出不圆滑或过深等。
检判:1)套管、管线管允许存在高度不超过壁厚道8%,最大高度不超过0.8mm不影响通径的内棱存在。
超差应修修磨及再切。
2)普管、管线管允许存在高度不超过壁厚8%(最大高度为0.8mm)的内棱存在。
超差应修磨及再切。
3)对L2级(即N5)探伤要求钢管,内棱高度不得超过5%(最大高度为0.5mm)。
超差应修磨及再切。
4)边线尖锐的内棱应修磨平滑。
热轧无缝钢管内折缺陷分析
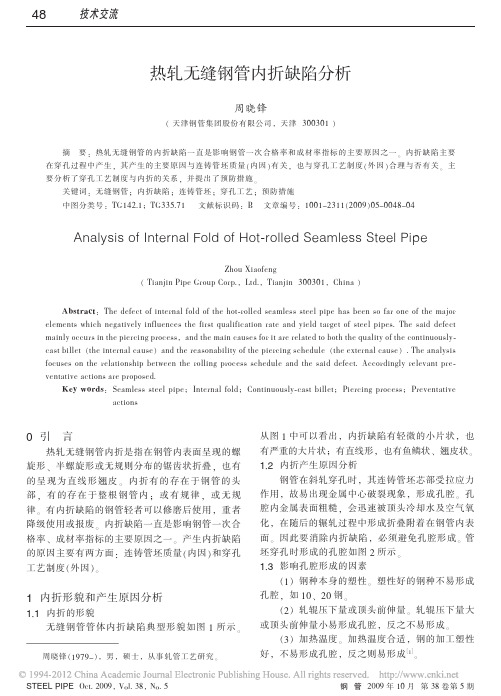
热轧无缝钢管内折缺陷分析周晓锋(天津钢管集团股份有限公司,天津300301)摘要:热轧无缝钢管的内折缺陷一直是影响钢管一次合格率和成材率指标的主要原因之一。
内折缺陷主要在穿孔过程中产生,其产生的主要原因与连铸管坯质量(内因)有关,也与穿孔工艺制度(外因)合理与否有关。
主要分析了穿孔工艺制度与内折的关系,并提出了预防措施。
关键词:无缝钢管;内折缺陷;连铸管坯;穿孔工艺;预防措施中图分类号:TG142.1;TG335.71%%文献标识码:B%文章编号:1001-2311(2009)05-0048-04Analysis of Internal Fold of Hot-rolled Seamless Steel PipeZhou Xiaofeng(Tianjin Pipe Group Corp.,Ltd.,Tianjin300301,China)Abstract:The defect of internal fold of the hot-rolled seamless steel pipe has been so far one of the major elements which negatively influences the first qualification rate and yield target of steel pipes.The said defect mainly occurs in the piercing process,and the main causes for it are related to both the quality of the continuously-cast billet(the internal cause)and the reasonability of the piercing schedule(the external cause).The analysis focuses on the relationship between the rolling process schedule and the said defect.Accordingly relevant pre-ventative actions are proposed.Key words:Seamless steel pipe;Internal fold;Continuously-cast billet;Piercing process;Preventative actions0引言热轧无缝钢管内折是指在钢管内表面呈现的螺旋形、半螺旋形或无规则分布的锯齿状折叠,也有的呈现为直线形翘皮。
无缝钢管缺陷名词解释

折叠
钢管表面局部重叠,有明显的折叠纹
6
锈蚀
表面生成的铁锈,其颜色由杏黄色到黑红色,除锈后,严重的有锈蚀麻点
7
发纹
表面发纹是深度甚浅,宽度极小的发状细纹,一般沿轧制方向延伸形成细小纹缕
8
气泡
表面无规律地分布呈圆形的大大小小的凸包,其外缘比较圆滑。大部是鼓起的,也有的不鼓起而经酸洗平整后表面发亮,其剪切断面有分层
附件2JTZS016
无缝钢管缺陷名词解释
序号
名称
说明
1
壁厚不均
钢管各部位的厚度不一样,有的两边厚而中间薄,有的边部薄而中间厚,也有的头尾差超过规定
2
划道
呈直线沟状,肉眼可见到沟底分布于钢管的局部或全长
3
裂纹
一般呈直线状,有时呈Y形,多与拔制方向一致,但也有其他方向,一般开口处为锐角
4
重皮(结疤)
表面呈舌状或鱼鳞片的翘起薄片:一种是与钢管的本体相连结,并折合到表面上不易脱落;另一种是与钢管的本体没有连结,但粘合到表面易于脱落
12
偏析
钢管中各部分化学成分和非金属夹杂物不均匀分布的现象.根据其表现形式可分:树枝状、方框形、点状偏析和反偏析等
注:列举几种缺陷图示,如下
描述:外裂
描述:内裂
9
麻点(麻面)
表面呈现局部的或连续的成片粗糙面,分布着形状不一、大小不同的凹坑,严重时有类似桔子皮状的,比麻点大而深的麻斑
10
辊印
表面有带状或片状的周期性轧辊印,其压印部位较亮,且没有明显的凸凹感觉
Байду номын сангаас11
疏松
钢管的不致密性的表现.切片经过酸液侵蚀以后,扩大成许多洞穴,根据其分布可分:一般疏松、中心疏松
- 1、下载文档前请自行甄别文档内容的完整性,平台不提供额外的编辑、内容补充、找答案等附加服务。
- 2、"仅部分预览"的文档,不可在线预览部分如存在完整性等问题,可反馈申请退款(可完整预览的文档不适用该条件!)。
- 3、如文档侵犯您的权益,请联系客服反馈,我们会尽快为您处理(人工客服工作时间:9:00-18:30)。
2、热轧钢管生产工艺流程2.1一般工艺流程热轧无缝钢管的生产工艺流程包括坯料轧前准备、管坯加热、穿孔、轧制、定减径和钢管冷却、精整等几个基本工序。
当今热轧无缝钢管生产的一般主要变形工序有三个:穿孔、轧管和定减径;其各自的工艺目的和要求为:2.1.1穿孔:将实心的管坯变为空心的毛管;我们可以理解为定型,既将轧件断面定为圆环状;其设备被称为穿孔机。
对穿孔工艺的要求是:首先要保证穿出的毛管壁厚均匀,椭圆度小,几何尺寸精度高;其次是毛管的内外表面要较光滑,不得有结疤、折叠、裂纹等缺陷;第三是要有相应的穿孔速度和轧制周期,以适应整个机组的生产节奏,使毛管的终轧温度能满足轧管机的要求。
2.1.2轧管:将厚壁的毛管变为薄壁(接近成品壁厚)的荒管;我们可以视其为定壁,即根据后续的工序减径量和经验公式确定本工序荒管的壁厚值;该设备被称为轧管机。
对轧管工艺的要求是:第一是将厚壁毛管变成薄壁荒管(减壁延伸)时首先要保证荒管具有较高的壁厚均匀度;其次荒管具有良好的内外表面质量。
2.1.3定减径(包括张减):大圆变小圆,简称定径;相应的设备为定(减)径机,其主要作用是消除前道工序轧制过程中造成的荒管外径不一(同一支或同一批),以提高热轧成品管的外径精度和真圆度。
对定减径工艺的要求是:首先在一定的总减径率和较小的单机架减径率条件下来达到定径目的,第二可实现使用一种规格管坯生产多种规格成品管的任务,第三还可进一步改善钢管的外表面质量。
20世纪80年代末,曾出现过试图取消轧管工序,仅使用穿孔加定减的方法生产无缝钢管,简称CPS,即斜轧穿孔和张减的英文缩写),并在南非的Tosa厂进行了工业试验,用来生产外径:33.4~179.8mm,壁厚3.4~25mm的钢管,其中定径最小外径为101.6mm;张减最大外径我101.6mm。
经过实践检验,该工艺在产生壁厚大于10mm的钢管时质量尚可,但在生产壁厚小于8mm的钢管时通过定径、张减不能完全消除穿孔毛管的螺旋线,影响了钢管的外观质量。
在随后的改造中不得不在穿孔机于定减径机之间增设了一台MINI-MPM(4机架)来确保产品质量。
2.2各热轧机组生产工艺过程特点我们通常将毛管的壁厚加工称之为轧管。
轧管是钢管成型过程中最重要的一个工序环节。
这个环节的主要任务是按照成品钢管的要求将厚壁的毛管减薄至与成品钢管相适应的程度,即它必须考虑到后继定、减径工序时壁厚的变化,这个环节还要提高毛管的内外表面质量和壁厚的均匀度。
通过轧管减壁延伸工序后的管子一般称为荒管。
轧管减壁方法的基本特点是在毛管内按上刚性芯棒,由外部工具(轧辊或模孔)对毛管壁厚进行压缩减壁。
依据变形原理和设备特点的不同,它有许多种生产方法,如表1所示。
一般习惯根据轧管机的形式来命名热轧机组。
轧管机分单机架和多机架,单机架有自动轧管机、阿塞尔轧机、ACCU-ROLL等,斜轧管机都是单机架的;连轧管机都是多机架的,通常4~8个机架,如MPM、PQF等。
目前主要使用连轧(属于纵轧)与斜轧两种轧管工艺。
表1 轧管减壁的工艺方法2..2.1连续轧管机的几种形式:连轧管机是在毛管内穿入长芯棒后,经过多机架顺序布置且相临机架辊缝互错(二辊式辊缝互错90°,如图1所示;三辊式辊缝互错60°)的连轧机轧成钢管,它是当今被最广泛应用的纵轧钢管方法。
连轧管机轧制过程中,轧件变形实际上是受多组(4~8组)轧辊与芯棒的反复作用从圆到椭圆…椭圆再到圆的过程。
连轧管机的发展历史悠久,早在19世纪末就曾尝试在长芯棒上进行轧管,但种种原因,至1950年世界上仅有6台连轧管机。
1960年后,随着科学技术的进步和生产的发展,特别是电子计算机技术的飞速发展和应用,使连轧管机在生产工艺和设备上日趋完善,得到了迅速的发展和推广。
在浮动芯棒连轧管机的基础上,限动芯棒连轧管机于20世纪60年代中期进行了工艺试验,获得了可喜的成果。
1978年世界上第一套限动芯棒连轧管机(MPM)在意大利达尔明钢管厂建成投产,连轧管工艺发展到了一个新的水准。
20世纪90年代末又推出了三辊连轧管机(PQF)技术,使连轧管工艺装备跃上了更高的台阶。
连轧管机在PQF出现以前,都是两辊式的,即由两个轧辊为一组组成孔型,二辊式的机架既有与地面呈45°交错布置的,也有与地面垂直、水平交错布置的;PQF为三辊式的,即由三个轧辊为一组组成孔型;;MPM与PQF孔型构成见(图2);连轧管时,孔型顶部的金属由于受到轧辊外压力和芯棒内压力作用而产生轴向延伸,并向圆周横向宽展,而孔型侧壁部分的金属与芯棒不接触,但它被顶部轴向延伸的金属对它附加的拉应力作用而产生轴向延伸,并同时产生轴向拉缩。
不论两辊式的还是三辊式的连轧管机,按芯棒的运行方式可分为以下三种形式。
2.2.1.1浮动芯棒连轧管机(或全浮动芯棒连轧管机):简称MM(Mandrel Mill),一般设有8个机架。
轧制过程中对芯棒速度不加以控制,芯棒由被辗轧金属的摩擦力带动自由跟随管子通过轧机,芯棒的运行速度是不受控的;轧制过程中芯棒的运行速度随着各机架的咬入、抛钢有波动,从而引起管子壁厚的波动;轧制结束后,芯棒随荒管轧出至连轧机后的输出辊道,在轧制中、薄壁管时芯棒的几乎全长都在荒管内,见图3;带有芯棒的荒管横移至脱棒线,由脱棒机将芯棒从荒管中抽出以便冷却、润滑后循环使用。
其特点是轧制节奏快,每分钟可轧4支甚至更多的钢管;但荒管的壁厚精度稍低、设有脱棒机其工艺流程较长、芯棒的长度接近于管子的长度;适合生产较小规格(外径小于177.8mm)的无缝钢管。
比较有代表性的浮动芯棒连轧管机有德国米尔海姆厂的RK2机组和我国宝钢的φ140 mm机组。
浮动芯棒连轧管机的工作特点是:由于在轧制时不控制芯棒速度,因此在整个轧制过程中,芯棒速度多次变化。
例如,在一台8机架的连轧管机上,当金属进入第一机架时,芯棒在摩擦力的作用下,以接近第一机架的轧制速度运行;当金属进入第二机架时,芯棒速度就要改变,以第一和第二机架轧制速度之间的某个速度运行;当进入第三机架时,则芯棒速度已变为第一、第二和第三机架轧制速度之间的某个速度;依此类推,直至进入第八机架,芯棒速度便经过了8次变化,已1~8机架间的某个速度运行,进入一个相对稳定的轧制阶段。
在此阶段,前面机架的轧制速度比芯棒速度慢(称为慢速机架),后面机架的轧制速度比芯棒速度快(称为快速机架),如果中间某个机架的轧制速度恰好与芯棒运行速度相同则称为同步机架。
随后当金属逐渐从有关机架中轧出时,在芯棒速度变化为2~8机架间的某个速度;当金属由第二机架轧出,则芯棒速度又变为第三至第八机架间的某个速度,以此类推,直至金属从第八机架轧出为止。
由上可以看出,在钢管的轧制过程中,芯棒的速度至少要变化15次,芯棒速度的变化将导致金属流动条件的改变。
浮动芯棒连轧管机由于轧制过程中芯棒速度改变而使得金属流动发生变化,因金属流动的不规律而引起钢管纵向的壁厚和直径变化,尽管对此采取了不少措施并取得了一定的效果,当轧制条件的变化依然存在,且产品管的尺寸精度始终不如限动芯棒轧机。
此外,芯棒长,使制造费用加大,制造困难,且长芯棒的重量也很大,钢管带着过重的芯棒在辊道上运行将会导致钢管表面损伤。
故目前浮动芯棒连轧管机均用于小型机组。
连轧管时,荒管可以看作是在不同直径的轧辊间连续轧制形成的。
穿在钢管中的芯棒可以看作是曲率半径无穷大的内轧辊。
浮动芯棒轧制时,芯棒除受到轧辊经轧件传递来的作用力外,再无其他外力作用。
当轧件头部经第一机架咬入后,随着轧件逐一走向后面的延伸机架,作用在芯棒上的机架数相继增多,故芯棒速度不断提高,这个阶段称为“咬入”阶段。
当轧件头部进入最末机架后,整个轧件处在连轧管机所有机架的轧制中,芯棒速度维持不变,称为“稳定扎着急”阶段。
当轧件尾部离开第一机架后,芯棒速度友逐级提高,直到轧出延伸,称为“轧出”阶段。
轧辊工作圆周速度是安“稳定轧制”状态下设定的。
轧制过程中轧件又是遵循着体积不变定律的。
然而由芯棒引起的轧件速度的升高,使流入后面机架的金属必然增多,也就是说,后面的机架由芯棒送入了比其设定的轧辊圆周速度所允许的还要多的金属,这就出现了使断面积增大的金属积累。
这种逐步流入的附加金属造成的较大断面,尽管在最后的机架上得到了加工,但仍然导致在荒管的一些部位上直径变大和壁厚变厚,这种现象称为“竹节”。
原则上讲可能在整根钢管上均出现“竹节”。
显然“竹节”现象属纵向壁厚不均,对随后的张减机轧制是不利的,应尽可能防止。
为了防止或减少“竹节”形成,孔型设计分配压下量时,在保证总延伸不变的前提下,适当增加前几架压下量。
这样,就可在后面几个机架中使芯棒速度的跃增得到减弱,从而减轻芯棒速度变化的影响。
良好的芯棒润滑有利于延伸和降低能耗,也可以减少竹节的形成。
还可以采用电控技术防止竹节的产生。
由电子计算机进行预设定,轧辊转速按要求变化,当轧件通过时对轧辊进行校准,使各机架的出口速度与芯棒速度的变化相适应。
70年代盛行浮动芯棒连轧管机机组。
由于受到芯棒重量的限制,至今这种机组仅能生产直径小于177.8mm一下的钢管。
2.2.1.2半浮动(或半限动)芯棒连轧管机:德国人称MRK-S(Mannesmann bohr-Kontimill Stripper);法国人称Neuval-R。
半浮动芯棒连轧管机一般7~8个机架。
德国设计的工艺为:在轧制过程中,前半程,芯棒不是自由地随轧件前进,而是受限动机构的控制,以一恒定速度前进,芯棒与轧件的速差分布是不一致的,第1架的轧件出口速度小于芯棒速度;自第2架开始,轧件的速度快于芯棒的速度,形成稳定的差速轧制状态;当完成主要变形、管子脱离倒数第3架时,限动机构加速释放芯棒,像浮动芯棒一样由钢管将芯棒带出轧机。
德国式的半浮动芯棒连轧管机于20世纪80年代初在日本八幡厂建成投产。
法国研制的工艺为:在钢管由最后一个机架轧出时才松开芯棒,即在轧制过程中具有限动芯棒轧机的工艺特点,而在终轧后松开芯棒;芯棒随荒管至连轧机后的输出辊道。
法国式的半浮动芯棒连轧管机于20世纪70年代后期在法国的圣索夫钢管厂投入生产。
不论德国工艺还是法国工艺,半浮动芯棒轧管机轧制结束后,约有1/3长的荒管(尾部)包住芯棒前端,见图4;带有芯棒的荒管横移至脱棒线,由脱棒机将芯棒从荒管中抽出以便冷却、润滑后循环使用。
其特点是荒管壁厚的精度较高、节奏较快,每分钟可轧3支甚至更多的钢管,芯棒长度虽然比浮动式的短得多,而比限动芯棒轧机略长一些;设有脱棒机工艺其流程较长;适合生产较小规格(外径小于219mm)的无缝钢管。
德国模式的代表机组有日本的八幡厂的φ194 mm机组和我国衡阳的φ89 mm机组;法国模式的机组至今仅有一套,就是法国V&M公司圣索夫厂的φ127 mm机组。