热轧生产线加热炉跟踪仿真实现模式论文
热轧带钢生产线及设备的设计论文
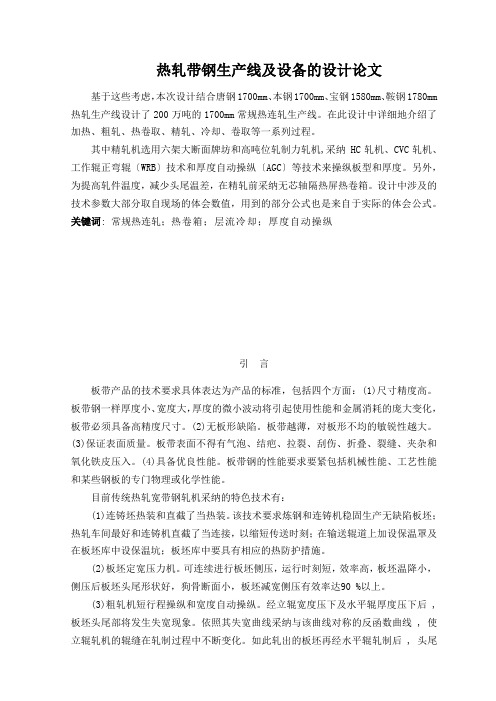
热轧带钢生产线及设备的设计论文基于这些考虑,本次设计结合唐钢1700mm、本钢1700mm、宝钢1580mm、鞍钢1780mm 热轧生产线设计了200万吨的1700mm常规热连轧生产线。
在此设计中详细地介绍了加热、粗轧、热卷取、精轧、冷却、卷取等一系列过程。
其中精轧机选用六架大断面牌坊和高吨位轧制力轧机,采纳 HC轧机、CVC轧机、工作辊正弯辊〔WRB〕技术和厚度自动操纵〔AGC〕等技术来操纵板型和厚度。
另外,为提高轧件温度,减少头尾温差,在精轧前采纳无芯轴隔热屏热卷箱。
设计中涉及的技术参数大部分取自现场的体会数值,用到的部分公式也是来自于实际的体会公式。
关键词: 常规热连轧;热卷箱;层流冷却;厚度自动操纵引言板带产品的技术要求具体表达为产品的标准,包括四个方面:(1)尺寸精度高。
板带钢一样厚度小、宽度大,厚度的微小波动将引起使用性能和金属消耗的庞大变化,板带必须具备高精度尺寸。
(2)无板形缺陷。
板带越薄,对板形不均的敏锐性越大。
(3)保证表面质量。
板带表面不得有气泡、结疤、拉裂、刮伤、折叠、裂缝、夹杂和氧化铁皮压入。
(4)具备优良性能。
板带钢的性能要求要紧包括机械性能、工艺性能和某些钢板的专门物理或化学性能。
目前传统热轧宽带钢轧机采纳的特色技术有:(1)连铸坯热装和直截了当热装。
该技术要求炼钢和连铸机稳固生产无缺陷板坯;热轧车间最好和连铸机直截了当连接,以缩短传送时刻;在输送辊道上加设保温罩及在板坯库中设保温坑;板坯库中要具有相应的热防护措施。
(2)板坯定宽压力机。
可连续进行板坯侧压,运行时刻短,效率高,板坯温降小,侧压后板坯头尾形状好,狗骨断面小,板坯减宽侧压有效率达90 %以上。
(3)粗轧机短行程操纵和宽度自动操纵。
经立辊宽度压下及水平辊厚度压下后 , 板坯头尾部将发生失宽现象。
依照其失宽曲线采纳与该曲线对称的反函数曲线 , 使立辊轧机的辊缝在轧制过程中不断变化。
如此轧出的板坯再经水平辊轧制后 , 头尾部失宽量减少。
热轧带钢生产线及设备的设计论文
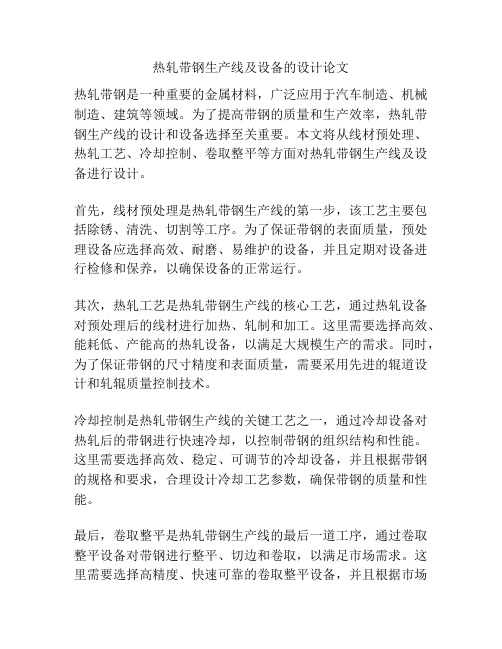
热轧带钢生产线及设备的设计论文热轧带钢是一种重要的金属材料,广泛应用于汽车制造、机械制造、建筑等领域。
为了提高带钢的质量和生产效率,热轧带钢生产线的设计和设备选择至关重要。
本文将从线材预处理、热轧工艺、冷却控制、卷取整平等方面对热轧带钢生产线及设备进行设计。
首先,线材预处理是热轧带钢生产线的第一步,该工艺主要包括除锈、清洗、切割等工序。
为了保证带钢的表面质量,预处理设备应选择高效、耐磨、易维护的设备,并且定期对设备进行检修和保养,以确保设备的正常运行。
其次,热轧工艺是热轧带钢生产线的核心工艺,通过热轧设备对预处理后的线材进行加热、轧制和加工。
这里需要选择高效、能耗低、产能高的热轧设备,以满足大规模生产的需求。
同时,为了保证带钢的尺寸精度和表面质量,需要采用先进的辊道设计和轧辊质量控制技术。
冷却控制是热轧带钢生产线的关键工艺之一,通过冷却设备对热轧后的带钢进行快速冷却,以控制带钢的组织结构和性能。
这里需要选择高效、稳定、可调节的冷却设备,并且根据带钢的规格和要求,合理设计冷却工艺参数,确保带钢的质量和性能。
最后,卷取整平是热轧带钢生产线的最后一道工序,通过卷取整平设备对带钢进行整平、切边和卷取,以满足市场需求。
这里需要选择高精度、快速可靠的卷取整平设备,并且根据市场需求和产品规格,合理设计设备工艺参数,确保产品的尺寸精度和表面质量。
综上所述,热轧带钢生产线及设备的设计需要充分考虑线材预处理、热轧工艺、冷却控制、卷取整平等因素,选择合适的设备和工艺参数,以保障带钢的质量和生产效率。
希望本文的研究能够对热轧带钢生产线的设计和设备选择提供一定的指导和参考。
热轧带钢生产线及设备的设计需要综合考虑多个因素,包括原材料质量、生产工艺、设备性能和工艺参数等。
在原材料的选择上,需要考虑钢种的适用性、含碳量和成分均匀性,以确保带钢的机械性能和化学成分符合要求。
在生产工艺方面,需要根据原材料的性能和要求,合理设计热轧工艺、冷却控制和整平工艺,以保证带钢的尺寸精度和表面质量。
热轧生产线加热炉跟踪仿真的实现模式及其在速度控制中的应用

热轧生产线加热炉跟踪仿真的实现模式及其在速度控制中的应用摘要:跟踪仿真是用数学模型模拟工业加工中物料在生产线上的运动状态,为人机界面(HMI)提供数据支持,同时也是逻辑控制时序信号的重要组成。
跟踪仿真反映速度,也控制速度,因此,它具有积分和逻辑双重意义。
本文以唐钢1810热轧薄板生产线加热炉为例讨论了工业仿真中物料跟踪仿真的一种实现模式。
主要说明了建立跟踪数学模型,定义跟踪数组的数据结构的过程,并用控制逻辑流程图分析了跟踪模型的动态积分和指针移位算法,及其在速度控制中的应用。
关键词:工业仿真,跟踪仿真模型,控制逻辑设计0引言热轧薄板生产线工艺复杂紧凑,设备控制要求响应快速,自动化集中控制程度高,跟踪仿真模型为人机交互操作界面组态提供基础数据,也是PLC程序中触发和连锁信号构成中的重要组成。
在控制模型中起着逻辑、时间、空间上的协调作用,跟踪系统的准确性和可靠性关系顺控程序的有序执行,生产安全,控制精度,产品质量,对节约能源,降低原材料消耗,成本控制也具有非常实际的执行意义。
跟踪仿真模型模拟自动化生产线上物料的运动状态并产生速度控制,以及设备动作的协调同步控制,其时序在整个生产动作周期中是循环但不重复的时序。
跟踪仿真模型的模拟量因此是速度的时间反映,也随着时间产生不同的速度控制,有积分含意义,同时有逻辑意义。
以下是热轧生产线加热炉跟踪仿真的一种实现模式及其在速度控制中的应用。
1跟踪模型分析和实现算法1.1环境模型加热炉跟踪距离长,一线有加热段,横移段,保温段,三个区域;二线有加热段和横移段两个区域,如图1所示,其板坯通过一线或二线横移车输送到一线保温段。
并定义加热炉进口为模型参照0位。
1.2 逻辑算法连铸坯经摆剪剪切后进入加热炉区,加热炉区进口光电开关PHOTOCELL 的关断产生板坯头部,导通产生尾部,同时产生头部占用和尾部占用两个逻辑量。
头部和尾部跟踪点从零开始对速度设定值进行时间积分累加。
PLC通过CC-LINK网络对驱动每组炉辊的变频器进行速度设定,由变频器实现闭环速度控制。
热轧生产线的建模与分析

2002年9月系统工程理论与实践第9期 文章编号:100026788(2002)0920078206热轧生产线的建模与分析卓之兵1,陈文德1,梁启宏2(1.中国科学院数学与系统科学研究院,北京100080;2.北京理工大学自动控制系,北京100081)摘要: 用扩展时间事件图与极大代数方法相结合对一类批量生产的制造系统建立了模型,并在加工时间和存储器数量固定的条件下,用这模型对系统生产周期进行了分析,从而得到了机器的最大利用率Λ关键词: 扩展时间事件图;双子;存储器;离散事件动态系统中图分类号: O231.2;N941.4 文献标识码: A M odels and A nalyses of Ho t2ro lling P rocessZHU O Zh i2b ing1,CH EN W en2de1,L I AN G Q i2hong2(1.A cadem y of M athem atics and System Sciences,A cadem ia Sin ica,Beijing100080,Ch ina;2.D epartm en t of A u tom atic Con tro l,Beijing U n iversity of T echno logy,Beijing100081,Ch ina)Abstract: In th is paper,a linear model is estab lished by the m ethod com b ined betw een Ex tendedT i m ed Even t Graph s and M ax2A lgeb ra fo r a class of batch p rocess m anufactu ring system s.U nder theconditi on of p rocessing ti m e and buffers w h ich are given,w e analyze p rocess ti m e and acqu ire m ax i m alrate of app licati on abou t m ach ines.Key words: ex tended ti m ed even t graph s(ET EG);di o id;buffer;discrete even t dynam ic system1 引言离散事件动态系统能够用极大代数方法来研究,文献[1,2]把时间事件图(一类重要的离散事件动态系统)的分析归结为解极大代数框架下的双子(D i o id)方程Λ扩展时间事件图(ET EG)也是一类重要的离散事件动态系统,文献[3]把它的分析也归结成解双子方程:x=A x w(1)其中x=:[〈t〉1,…,〈t〉2]T,〈t〉i表示第i个变迁激发时间形成的时间序列〈t0,t1,…〉,矩阵A的元素为形如[∃v]3[d1]3[z-m]3[ u]的算子Ζ这里[∃v]为抽样算子,[∃v]〈t0,t1,…〉=:〈t v-1,t2v-1,t3v-1〉;[d1]为加法算子,[d1]〈t0,t1,…〉=:〈t0+d1,t1+d1,…〉;[z-m]为右移算子,[z-m]〈t0,t1,…〉=:〈-∞,…,-∞,t0,t1,…〉,其中-∞重复m次;[ u]为复制算子,[ u]〈t0,t1,…〉=:〈t0,…,t0,t1,…,t1,…〉,其中t i重复u次.“3”为算子复合运算,“ ”与A x中的加法均取极大运算,对两个向量或序列取极大是指对分量或序列各元素取极大Ζ记上述算子集的并集为FΖ定义(f g)〈t〉=:f〈t〉 g〈t〉,(f3g)〈t〉=:f(g〈t〉),Πf, g∈F.则(F,3, )是一个双子Ζ由双子代数的理论易得(1)的解为x=A3w(2)收稿日期:2001202212资助项目:国家自然科学基金(69874040) 作者简介:卓之兵(1972),男,安徽泗县人,博士,主要从事线性系统,控制理论及应用,离散事件动态系统及格序群等领域的研究Λ这里A 3=:6∞k =0A kΖ文献[4]把文献[3]中的变迁延时d 1改为位置延时d 1,给出了扩展时间事件图的严密的双子模型描述,并给出了监控的若干新结果Ζ但文献[4]并未指出这理论如何应用到具体的工程系统中去Ζ本文应用这理论对一类批量生产的制造系统(见文献[5])建立了具体的模型,并用这模型对系统生产周期进行了分析,从而解决了以下从秦皇岛首钢板材公司热轧生产线提出的一个具体问题Ζ问题:两台机器,第一台机器 是加热炉,第二台机器 是轧机,对轧件进行两次加工,其加工时间已固定,两台机器的加工时间也已固定,并且机器 的一批生产个数为M ,机器 前后的存储器数量也固定,问如何组织生产,使得机器 的利用率达最大?这最大利用率是多少?虽然本文研究的系统不很复杂,但本文的建模与分析方法可应用于极为复杂的生产线与制造系统网络,在计算机帮助下可计算出生产周期等重要参数,因此本文的方法有广阔的应用前景Ζ2 热轧生产线的建模扩展时间事件图(ET EG )是一类特殊的Petri 网,它是一个六元集[4],记作〈P ,T ,R 1,w ,T e m p o ,M 0〉,其中T 是变迁集,P 是位置集,R 1=R P T ∪R T P ,R P T ={〈P ,t 〉 p ∈P ,t ∈T }ΑP ×T ,R T P ={〈t ,P 〉 t ∈T ,p ∈P }ΑT ×P ,P ∩T = ,W 是R 1中元素重复次数集,T em po 是一个延时函数,M 0是初始标识集,并且位置的输入、输出均用一个“→”表示,延时在P 上,用“ ”,“○”分别表示变迁和位置Ζ设第一台机器的加工时间为t ~0,一批加热M 个工件.机器 前后存储器个数分别为n ,m ,且它的第一、二两次加工时间分别为t ~1,t ~2两次加工的间歇时间(热轧线中为加工工艺规定的轧件冷却时间)为t ~r Ζ如图1所示.○表示存储器; 表示机器图1 热轧生产线工件首先进入加热炉进行加热,经t ~0时间后出炉进入机器 ,在 上进行两次加工离开生产线.为了简化模型的建立,设t ~r t ~t =N (整数),且(整数)n Εm ΕN ,M N +1=k (整数),t ~1Εt ~2.如上所设的问题中串行生产线可用扩展时间事件图建模与组织生产,并进一步可用双子代数建模成式(1)Ζ首先给出热轧生产系统的Petri 网(ET EG )模型Ζ如图2所示.图2中“-”,“ ”表示变迁,“→”表示弧,“・”表示初始标识,“.”表示位置,u =i 表示由一个复制成i 个,v =i 表示从i 个中抽取最后一个Ζ图中未标出的u ,v 值均表示u =1,v =1,位置p 2n +2m +9,p 2n +2m +10,p n +m +7,p 2n +2m +12中的初始标识为N +1Ζ图2中各参数如下:W (t 1,p 1)=1,T e m p o (p 1)=t ~0,W (p 1,t 2)=1,W (t 2,p 2)=M ,W (p 2,t 3)=N +1W (t 3,p 3)=N +1,W (t 4,p 4)=W (t 5,p 5)=…=W (t n +m +7,p n +m +7)=1W (p 3,t 4)=W (p 4,t 5)=…=W (p n +m +6,t n +m +7)=1,W (p n +m +7,t 3)=N +1T e m p o (p 2)=T e m p o (p 3)=T e m p o (p n +5)=T e m p o (p n +7)=T e m p o (p n +m +5)=0T e m p o (p n +6)=t ~1,T e m p o (p n +m +6)=t ~r ,T e m p o (p n +m +7)=t ~2T e m p o (p n +m +8)=…=T e m p o (p 2n +m +8)=T e m p o (p 2n +m +10)=…=T e m p o (p 2n +2m +9)=0T e m p o (p 2n +m +9)=t ~1,T e m p o (p 2n +2m +10)=t ~2,T e m p o (p 2n +2m +12)=T e m p o (p 2n +2m +13)=0M 0(p n +m +8=M 0(p n +m +9)=…=M 0(p 2n +2m +10)=1,M 0(p n +m +7=N +197第9期热轧生产线的建模与分析图2 热轧生产线的ET EG 模型M 0(p 2n +2m +12)=N +1,M 0(p 2n +2m +13)=1,M 0(p 2n +2m +14)=1W (t 3,p 2n +2m +1)=W (t n +m +8,p 2n +2m +13)=W (t n +m +8,p 2n +2m +12)=1W (p 2n +2m +11,t n +m +8)=k ,W (p 2n +2m +12,t 1)=W (p 2n +2m +13,t 2)=1W (t 1,p 2n +2m +14)=1,W (p 2n +2m +14,t 1)=1,其余初始标识均为0Ζ图2组织生产的过程概述如下:加热炉一次加热M 个工件,它们分成k 个小批进行轧制,每小批中第一个工件J 1轧制后送至最右端存储器,J 1冷却时间内轧制其余N 个工件,依次送至右方各存储器,J 1冷却时间达到后,把它们都移到机器的左方各存储器,再陆续进行第二次轧制,第一小批加工完后再加工第二小批,直到M 个工件加工完Ζ加热炉在送出一个工件后即可在空位中补送入一个工件进行加热Ζ由文献[4]的定理2的结论知〈t 〉1=[z -1][t ~0]〈t 〉1 [z -N -1]〈t 〉n +m +8 uθ〈t 〉2=[t ~0]〈t 〉1 [z -1]〈t 〉n +m +8 0〈t 〉3=[∃N +1][ M ]〈t 〉2 [∃N +1][z -N -1][t ~2]〈t 〉n +m +7 0〈t 〉4=[ N +1]〈t 〉3 0 〈t 〉n +5=〈t 〉n +4 [z -1]〈t 〉n +5 0〈t 〉n +6=〈t 〉n +5 [z -1][t ~1]〈t 〉n +6 0〈t 〉n +7=[t ~1]〈t 〉n +6 [z -1]〈t 〉n +7 0 〈t 〉n +m +6=〈t 〉n +m +5 [z -1][t ~r ]〈t 〉n +m +6 0〈t 〉n +m +7=[t ~r ]〈t 〉n +m +6 [z -1][t ~2]〈t 〉n +m +7 0〈t 〉n +m +8=[∃k ]〈t 〉3 0令x =[〈t 〉1,〈t 〉2,…,〈t 〉n +m +8]T ,则上面式子矩阵形式为λ()08系统工程理论与实践2002年9月其中,v λ=[u θ,0,…,0]T ,A 为下面图3的关联矩阵ΖA 对应的有向图记为G (A ):G (A )中有n +m +8个点,(A )ij ≠[Ε]时,点j 到点i 存在一条弧,其权为(A )ij ;当(A )ij =[Ε]时,点j 到点i 不存在弧Ζ用数字1,2,…,n +m +8表示G (A )中的点Ζ复合算子运算表示弧的权ΖL 1表示1→2→3→n +m +8→1所对应的回路,L 2表示3→4→…→n +m +6→n +m +7→3所对应的回路Ζ则A 所对应的有向图G (A )如图3所示.图3 热轧生产线的双子模型3 生产周期及机器利用率的分析我们已有了两种模型及其对应的两个图,从而可用两种方法来分析生产周期Ζ下面采用两种方法相结合来进行分析Ζ定义3.1[6] 对于序列〈t 0,t 1,…,t j ,…〉,若存在i 0Ε0,使得所有j Εi 0都有t j +N =t j +T ,则称为准周期序列,T 称为周期Ζ把满足上式的最小T 称为最小周期Ζ定理3.1 若图3中点对应的的分量是非有限序列,则L 2上的点对应的x 的分量〈t 〉i 均为准周期序列,且其最小周期为Κ=(2N +1)t ~1+t ~2Ζ证明 图2中,变迁T r 仅在u θr 时刻后才可能激发,现设Petri 网运行时间T 0已大于m ax (u θr 3Φr ΦL 2),由文献[6]的定理1的证明知:x 的分量〈t 〉i 是非有限序列时,变迁T r 均输出标识,N k 1+1-N k 1Ε1Ζ考察时间t 0后,从点i 开始,Petri 网运行k 1周后n 个位置P r 中标识数变化的规律Ζ记P r 后的变迁T r 第k 1次刚激发后的P r 中剩余标识数为m r (k 1),T r 第k 1次激发后的P r 中新标识数为M r (k 1),显然T r 第k 1+1次激发前的P r 中标识数为m r (k 1)+M r (k 1)Ζ不妨设r =3,L 2的回路长为d ,记P =:P (d )=∶7d r =3u r v r ,Αr =∶7ds =r u s v sΖ有M 4(k 1+1)=(M d (k 1)+m d (k 1)-m d (k 1+1))u dv d=(M d -1(k 1)+m d -1(k 1)-m d -1(k 1+1)u d -1v d -1+m d (k 1)-m d (k 1+1)u dv d=…=M d (k 1)P +6dr =3(m r (k 1)-m r (k 1+1))Αr按上式推断k 1次得M 4(k 1+1)=M 4(1)P k 1+6k 1s =1P k 1-s 6d r =3(m r (s )-m r (s +1))Αr 由于P =1,有M 4(k 1+1)=M 4(1)+6d r =3(m r (k 1)-m r (k 1+1))Αr由于0Φm r (k 1)<v r ,0Φm 3(k 1+1)<M 3(1)+6d r =3v r Αr ,于是m r (k 1),M r (k 1+1)只能取有限多个值,18第9期热轧生产线的建模与分析3改为i (3Φi Φn +m +7)后结论类似,由于k 1有∞个,故存在Q ,k 0使k 1Εk 0时,有M r (k 1+Q )=M r (k 1),m r (k 1+Q )=m r (k 1),3Φr Φn +m +7,于是〈t 〉i 为准周期序列Ζ不失一般性,考虑P n +m +7中标识变化规律,P n +m +7中初始标识数为N +1个,当T 3激发时,P n +m +7中标识数变为0,P 3中增加N +1个标识,经过一段时间后,T n +m +7开始激发,输出一个标识,从而P n +m +7中增加一个标识Ζ此时P 3又输出一个标识,经过一段时间后,P n +m +7中增加一个标识Ζ依次下去,当P 3中的N +1个标识全部输出,P n +m +7中标识数增加到N +1时,T 3又开始激发,P n +m +7中N +1个标识全部输出,开始新的周期Ζ由此可见,标识变化的时间周期即为所求的周期Ζ前N 个标识在回路中运行的时间为N t ~1,最后一个标识运行时间为t ~1+t ~2+t ~r ,从而运行的周期Κ=t ~1+t ~2+t ~r +N t ~1=(2N +1)t ~1+t ~2Ζ易知Κ是最小周期Ζ定理3.2 图3的点对应的的分量〈t 〉i 均为准周期序列,其最小周期为m ax {t ~0,k Κ}.其中Κ=(2N +1)t ~1+t ~2Ζ证明 前一结论的证明类似于定理2.2的证明Ζ下面仅证其周期为m ax {t ~0,k Κ}Ζ考虑P 2n +2m +11中标识数变化规律,P 2n +2m +11中的初始标识数为0,当T 3激发后,P 2中减少一个标识,P 2n +2m 中增加一个标识,P 3中也增加一个标识Ζ当P 3中的标识数在L 2中运行一圈后,此时T 3进行第二次激发,P 2又输出一个标识,P 2n +2m +11与P 3各增加一个标识,当P 2n +2m +11中标识数增加到k 个后,此时T n +m +8激发,向P 2n +2m +12输出一个标识,向P 2n +2m +13也输出一个标识Ζ当经过m ax {k Κ,t ~}时间后,T 2激发,输出一个标识,进行又一循环Ζ由上面的分析可知,T 2激发的周期时间为m ax {k Κ,t ~},并且是最小的,而这恰是所要求的周期Ζ因为一个工件在机器上加工时间为t ~1+t ~2,从而M 个工件在机器上加工时间为M (t ~1+t ~2),于是机器的利用率为(t ~1+t ~2)m ax{k Κ,t ~0}Ζ易知,本文组织生产的方法已使机器 的利用率达到最大Ζ4 实际例子设第一台机器的加工时间为45,一批加热18个工件,机器 前后存储器个数分别为4,3,且它的第一、二两次加工时间分别为2,1.5,两次加工的间歇时间(热轧线中为加工工艺规定的轧件冷却时间)为4,上面时间均以分钟为单位Ζ由前面的结论知〈t 〉1=[z -1][45]〈t 〉1 [z -3]〈t 〉13 uθ〈t 〉2=[45]〈t 〉1 [z -1]〈t 〉13 0〈t 〉3=[∃3][ 18]〈t 〉2 [∃3][z -3][1.5]〈t 〉12 0〈t 〉4=[ 3]〈t 〉3 0〈t 〉8=〈t 〉7 [z -1]〈t 〉8 0〈t 〉9=〈t 〉8 [z -1][2]〈t 〉9 0〈t 〉10=[2]〈t 〉9 [z -1]〈t 〉10 0〈t 〉11=〈t 〉10 [z -1][4]〈t 〉11 0〈t 〉12=[4]〈t 〉11 [z -1][1.5]〈t 〉12 0〈t 〉13=[∃6]〈t 〉3 0令x =[〈t 〉1,〈t 〉2,…,〈t 〉13]T ,则上面式子矩阵形式为x =A x vλ式中,v λ=[u θ,0,…,0]T Ζ由定理3.1知,Κ=(2×2+1)×2+1.5=11.5.由定理3.2知,机器 加工完18个工件的最小周期为m ax {3,6×11.5}=69.28系统工程理论与实践2002年9月且机器 的最大利用率=18×(2+1.5)69≈0.913.附记:本文讨论了n Εm Εt ~r t ~1时机器的最大利用率的情况,对于t ~rt ~1>n Εm 的情况并没有给予讨论Ζ利用类似的方法可以得到相似的结果,详略Ζ参考文献:[1] Cofer D D ,Garg V K .Superviso ry con tro l of real 2ti m e discrete system s u sing lattice theo ry [J ].IEEE T ran s on A u 2tom atic Con tro l ,1996,41:199-209.[2] T akai S .A characterizati on of realizab le behavi o r in superviso ry con tro l of ti m ed even t graph s [J ].A u tom atic ,1997,33(11):2077-2080.[3] 戴华平.计算机集成过程控制系统的理论与应用研究[D ].杭州:浙江大学,1998.[4] Zhuo Zh ib ing ,Chen W ende .Superviso ry con tro l of ex tended ti m ed even t graph s [A ].P roceedings of the T h irdW o rld Congress on In telligen t Con tro l and In telligen t A u tom ati on [C ],H efei ,2000.2322-2326.[5] 卓之兵,陈文德,梁启宏.一类存储器的优化问题[J ].系统工程理论与实践,2001,21(5):98-101.[6] 陈文德.扩展时间事件图的分析[J ].应用数学学报(中文版),2002,25(2):132-137.(上接第73页)修正的代理对偶问题(DR s )sup v Ε0v (PR v )的最优解v 3=(0.25,0.75),代理松弛问题(PR v )m in 3x 1+2x 2s .t .0.25(3-5x 1-2x 2)+0.75(1-x 2)Φ0x ∈S的最优解x 3=(0,2),v (DR s )=v (P ),完全弥合了代理对偶间隙Ζ参考文献:[1] Karw an M H ,R ardin R L .Som e relati on sh i p s betw een L agrangean and su rrogate duality in in teger linear p rogram 2m ing [J ].M ath P rogram ,1979,17:320-334.[2] D yer M E .Calcu lating su rrogate con strain ts [J ].M ath .P rogram ,1980,19:225-278.[3] Karw an M H ,R ardin R L .Su rrogate dual m u lti p le search p rocedu re in in teger p rogramm ing [J ].Opn s R es ,1984,32:52-69.[4] Karw an M H ,R ardin R L ,Sarin S .A new su rrogate dualm u lti p lier search p rocedu re [J ].N aval R esearch L ogistics ,1987,34:431-450.[5] 倪明放.解021线性规划Su rrogate 对偶的一个方法[J ].高校计算数学学报,1989,11(3):243-247.[6] 倪明放,徐南荣.求解整数规划代理对偶的一个新方法[J ].计算数学[J ],1993,15(2):156-164.[7] N em hau ser G ,W o lsey L A .In teger and Com b inato rial Op ti m izati on [M ].N ew Yo rk :John W iley &Son s ,1988.[8] Parker R G ,R ardin R L .D iscrete Op ti m izati on [M ].N ew Yo rk :A cadem ic P ress ,1989.[9] 马仲蕃.线性整数规划的数学基础[M ].北京:科学出版社,1995.38第9期热轧生产线的建模与分析。
电加热炉温度控制系统性能的MATLAB仿真

电加热炉温度控制系统性能的MATLAB仿真————————————————————————————————作者:————————————————————————————————日期:电加热炉温度控制系统性能的 MATLAB仿真系别:机电与自动化学院专业班:姓名:学号:指导教师:2013年月日电加热炉温度控制系统性能的MATLAB仿真MATLAB simulation the performance of the control system of heating furnace temperature摘要近年来随着工业的发展,电加热炉在工业控制中的应用越来越广泛。
温度是电加热炉控制系统的一个主要参数,对温度的控制要求也越来越高。
传统控制算法一般要建立在一定的数学模型之上,模型的精确度对控制效果有直接的影响.然而电加热炉是一种具有非线性、纯滞后、大惯性、时变性和升温单向性的控制对象,很难用数学方法建立精确模型.模糊控制不依赖于模型,但由于它的理论并不完善,算法复杂,控制过程会存在稳态误差。
传统PID控制理论成熟,容易实现,虽然大多数情况下可以满足性能要求,但其性能取决于参数的整定情况,且它的快速性和超调量之间的矛盾关系,使它不能同时满足快速升温和超调量小的要求。
鉴于此,本文将模糊算法和常规PID算法结合起来,在手动经验的基础上建立模糊规则,在线自整定PID的参数,提高控制效果。
本文提出了基于模糊PID的箱式电加热炉控制系统的设计方法。
首先介绍了模糊PID 控制器的设计方法,并用MATLAB仿真比较了常规PID控制算法和模糊PID控制算法的性能,分析了模糊PID在电加热炉温度控制中的可行性.最后在二次开发设计的基于组态软件King View开发的系统中,对模糊PID算法和常规PID算法进行了实时调试,并对实验结果进行了分析.关键词:温度控制;MATLAB;模糊PID;常规PIDAbstractWith the development of industry.electric heating furnace is more and more widely used 。
热轧带钢生产线及设备的设计论文

热轧带钢生产线及设备的设计论文引言热轧带钢是一种重要的金属材料,在工业生产和建筑行业中得到广泛应用。
它具有优良的机械性能和成型性能,能够满足各种工程的需求。
为了满足市场对热轧带钢的需求,热轧带钢生产线及设备的设计变得至关重要。
本论文旨在研究和探讨热轧带钢生产线及设备的设计原理和方法。
热轧带钢生产线的设计原则热轧带钢生产线的设计需要遵循一定的原则,以确保生产线的稳定运行和高效生产。
以下是热轧带钢生产线设计的一些原则:1. 按需生产热轧带钢生产线应根据市场需求和订单量进行生产调度。
生产线的设计应能够快速调整生产规模和生产速度,以满足市场的需求变化。
2. 自动化程度高热轧带钢生产线的自动化程度对生产效率和产品质量有着重要影响。
因此,在设计热轧带钢生产线时,应尽可能采用先进的自动化设备和控制系统,以提高生产效率和降低人工操作错误。
3. 设备可靠性高热轧带钢生产线的设备需要具备高可靠性和稳定性,以确保生产过程的连续性和稳定性。
在设备的选择和调试过程中,应注重设备的品质和性能,以避免设备故障和停机时间的影响。
4. 节能减排热轧带钢生产过程中会产生大量的能耗和废气废水。
为了减少对环境的影响,热轧带钢生产线的设计应注重节能和减排,采用先进的能源回收和废气处理设备。
热轧带钢生产设备的设计要点在设计热轧带钢生产设备时,需要考虑以下几个关键要点:1. 轧机的选择轧机是热轧带钢生产线中最核心的设备,对产品的质量和尺寸精度有着重要影响。
在选择轧机时,应考虑轧机的型号、参数和性能指标,以确保其能够满足生产线的需求。
2. 辊道系统的设计辊道系统是热轧带钢生产线中用于输送钢坯和成品钢带的重要设备。
辊道系统的设计应考虑到输送带钢的平稳性、减小辊道磨损和节约能源。
设计时应合理布局辊道,采用合适的辊道材料,并考虑辊道的维护和保养。
3. 冷却系统的设计热轧带钢在轧机上经过高温轧制后需要进行快速冷却,以提高产品的硬度和强度。
冷却系统的设计应能够提供适当的冷却速度和冷却剂,以满足产品的冷却要求。
钢厂PLC热轧感应加热炉系统的实现

钢厂PLC热轧感应加热炉系统的实现随着节能降耗技术的要求越来越高,大功率感应加热炉技术在钢厂热连轧系统中应用越来越广泛。
利用恒远PLC实现对于大功率感应加热炉的自动控制,实现对钢铁热连轧的温度分布控制要求。
在热轧钢球一体化的热连轧生产线中,采用大功率电磁感应加热炉对钢坯进行加热,不仅可以大大提高企业的生产效率,而且还可以极大的减少环境污染和降低能源消耗。
由于加热过程的非线性、时变性、温度分布不均性,以及现场环境的恶劣性、嘈杂性、强磁场分布不均性,人工操控加热炉很难准确、稳定地进行加热,普通的嵌入式控制器很难适应现场恶劣的环境,如果选用PLC作为加热炉的控制器,同时配备上位机组态监控软件,既可以保证系统安全稳定的运行,又可以实时监控整个加热过程。
恒远结合多年的生产实践之经验在新技术PLC控制系统中应用了3种温度控制侧略。
一、控制系统的功能和要求感应加热炉控制系统,根据加热钢坯的需求,加热炉必须具备以下功能:①根据钢坯的实际温度和轧机入口温度要求,加热系统要能够为钢坯提供最大200摄氏度的温度;②由于钢坯温度分布头低尾高,温差大约为50~80摄氏度,控制系统要求能够克服此温差,使加热炉的钢坯温度分布均匀;③系统应具备手、自动控制两种模式;④系统工作在自动控制模式时,能够自动采集钢坯温度,并通过调控中频电压将不同温度的钢坯加热到设定的温度值;⑤系统要具备过载报警、漏电报警等各种报警信息和状态信息。
二、控制系统的硬件实现感应加热炉控制系统的硬件部分主要分为:采样输入部分、PLC控制器和输出执行部分。
其中采样输入部分主要包括钢坯温度测量,钢坯移动速度测量,加热炉电压、电流、频率的测量及报警信息输入等。
恒远感应加热炉钢坯的温度测量部分安装3个测温仪,1号测温仪为提前测温点,位置设在距离加热炉入口略大于钢坯长度的位置。
此测温点主要是扫描采样全钢坯的温度分布;2号测温仪设置在距离加热炉入口500mm前后,此测温点主要是用来记录进入加热炉的确切温度;3号测温仪设置在加热炉出口500mm前后,此测温点主要是用来记录钢坯经过加热炉后出炉温度分布。
加热炉炉温控制策略研究及仿真分析 陆明伟
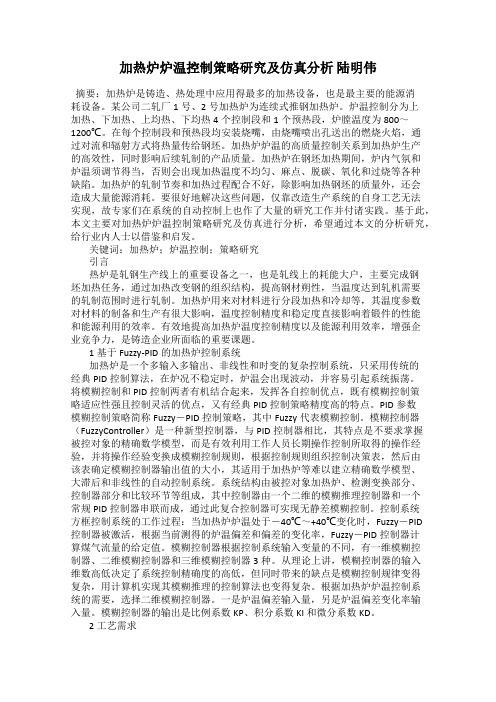
加热炉炉温控制策略研究及仿真分析陆明伟摘要:加热炉是铸造、热处理中应用得最多的加热设备,也是最主要的能源消耗设备。
某公司二轧厂1号、2号加热炉为连续式推钢加热炉。
炉温控制分为上加热、下加热、上均热、下均热4个控制段和1个预热段,炉膛温度为800~1200℃。
在每个控制段和预热段均安装烧嘴,由烧嘴喷出孔送出的燃烧火焰,通过对流和辐射方式将热量传给钢坯。
加热炉炉温的高质量控制关系到加热炉生产的高效性,同时影响后续轧制的产品质量。
加热炉在钢坯加热期间,炉内气氛和炉温须调节得当,否则会出现加热温度不均匀、麻点、脱碳、氧化和过烧等各种缺陷。
加热炉的轧制节奏和加热过程配合不好,除影响加热钢坯的质量外,还会造成大量能源消耗。
要很好地解决这些问题,仅靠改造生产系统的自身工艺无法实现,故专家们在系统的自动控制上也作了大量的研究工作并付诸实践。
基于此,本文主要对加热炉炉温控制策略研究及仿真进行分析,希望通过本文的分析研究,给行业内人士以借鉴和启发。
关键词:加热炉;炉温控制;策略研究引言热炉是轧钢生产线上的重要设备之一,也是轧线上的耗能大户,主要完成钢坯加热任务,通过加热改变钢的组织结构,提高钢材朔性,当温度达到轧机需要的轧制范围时进行轧制。
加热炉用来对材料进行分段加热和冷却等,其温度参数对材料的制备和生产有很大影响,温度控制精度和稳定度直接影响着锻件的性能和能源利用的效率。
有效地提高加热炉温度控制精度以及能源利用效率,增强企业竞争力,是铸造企业所面临的重要课题。
1基于Fuzzy-PID的加热炉控制系统加热炉是一个多输入多输出、非线性和时变的复杂控制系统,只采用传统的经典PID控制算法,在炉况不稳定时,炉温会出现波动,并容易引起系统振荡。
将模糊控制和PID控制两者有机结合起来,发挥各自控制优点,既有模糊控制策略适应性强且控制灵活的优点,又有经典PID控制策略精度高的特点。
PID参数模糊控制策略简称Fuzzy-PID控制策略,其中Fuzzy代表模糊控制。
热轧带钢生产线及设备的设计论文
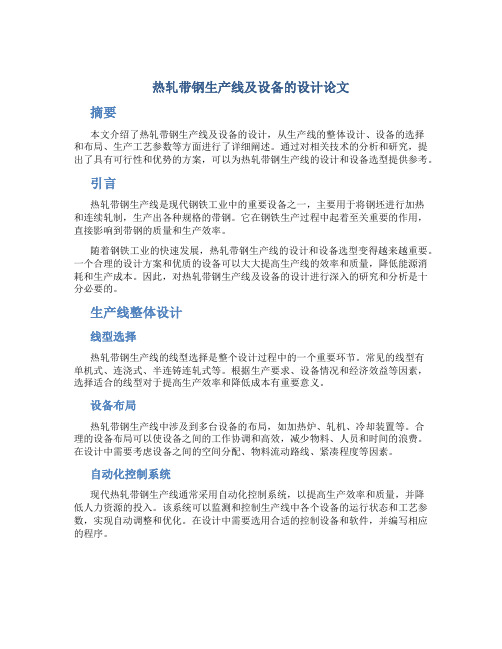
热轧带钢生产线及设备的设计论文摘要本文介绍了热轧带钢生产线及设备的设计,从生产线的整体设计、设备的选择和布局、生产工艺参数等方面进行了详细阐述。
通过对相关技术的分析和研究,提出了具有可行性和优势的方案,可以为热轧带钢生产线的设计和设备选型提供参考。
引言热轧带钢生产线是现代钢铁工业中的重要设备之一,主要用于将钢坯进行加热和连续轧制,生产出各种规格的带钢。
它在钢铁生产过程中起着至关重要的作用,直接影响到带钢的质量和生产效率。
随着钢铁工业的快速发展,热轧带钢生产线的设计和设备选型变得越来越重要。
一个合理的设计方案和优质的设备可以大大提高生产线的效率和质量,降低能源消耗和生产成本。
因此,对热轧带钢生产线及设备的设计进行深入的研究和分析是十分必要的。
生产线整体设计线型选择热轧带钢生产线的线型选择是整个设计过程中的一个重要环节。
常见的线型有单机式、连浇式、半连铸连轧式等。
根据生产要求、设备情况和经济效益等因素,选择适合的线型对于提高生产效率和降低成本有重要意义。
设备布局热轧带钢生产线中涉及到多台设备的布局,如加热炉、轧机、冷却装置等。
合理的设备布局可以使设备之间的工作协调和高效,减少物料、人员和时间的浪费。
在设计中需要考虑设备之间的空间分配、物料流动路线、紧凑程度等因素。
自动化控制系统现代热轧带钢生产线通常采用自动化控制系统,以提高生产效率和质量,并降低人力资源的投入。
该系统可以监测和控制生产线中各个设备的运行状态和工艺参数,实现自动调整和优化。
在设计中需要选用合适的控制设备和软件,并编写相应的程序。
设备选择和布局加热设备热轧带钢生产线中的加热设备主要用于对钢坯进行加热,提高其可塑性和轧制温度。
常见的加热设备有电阻加热炉、感应加热炉和火焰加热炉等。
在选择时需考虑能源消耗、加热速率和加热均匀性等因素。
轧机轧机是热轧带钢生产线中最关键的设备之一,其合理选型和布局对整个生产线的性能和质量有很大影响。
根据产品规格、生产能力和轧制工艺要求等因素,选用适当类型和数量的轧机,并对其布局和调整进行优化。
热轧脉冲式加热炉设计与应用实践探讨

热轧脉冲式加热炉设计与应用实践探讨摘要:热轧加热炉投运以来,充分展示了“脉冲+均热”加热炉的设计优势和特点。
在已投用热轧加热炉设计及应用实践的基础上,新建热轧产线加热炉对已有加热炉的优势点进行了传承,同时对于一些运行过程中发现的不足点及基于产线定位的需求,从加热炉技术方案设计上,进行了优化和改进。
关键词:炉型汽化冷却加热炉纳米材料燃耗1概述宝钢湛江钢铁热轧加热炉采用“脉冲+均热”的智能化加热炉设计方案。
从投产运行以来,节能效果显著,加热炉能力突出,各项指标运行稳定,在同类产线中属于佼佼者。
通过对比两线热轧加热炉运行实际与设计方案,进行理论与实践的研究探索。
2现状2250热轧加热炉投产以来,在能耗及加热质量方面处于高水平,运行过程中还出现过因设计认识制约而产生的一些问题例如氧化烧损、炉墙烧红等问题,给加热炉的正常运行和生产效率带来了不良影响。
结合热轧厂前期加热炉生产运行应用实践,根据当前产线加热炉设计选型特点,从加热炉技术经验传承与技术创新角度进行探索研究。
3加热炉运行主要问题及分析3.1低能耗,高烧损2250热轧加热炉投入生产运行以来,能耗指标优异,吨钢燃耗在34kgce/t左右,处于同类先进产线的领先地位。
但是在氧化烧损控制方面则显得比较被动,平均在0.9~1.2%左右,比同类产线的0.8%左右要高。
一方面统计烧损的边界波动较大,另一方面加热工艺方面,例如在炉时间长,炉内氧含量偏高等。
更主要的是,2250热轧加热炉只有炉尾部一个氧化锆来监测全炉的氧含量。
在工艺控制上进行优化,要想精准控制各段的氧含量和炉温,缺乏有效的硬件设施来促进研究和改进。
3.2加热段能力分布热轧加热炉按照热回收、预热、一加、二加及均热段的供热工艺段设置。
各段的热负荷分配如图1所示。
图1:加热炉炉型及热负荷分布在一热轧投产初期,由于加热炉整体热负荷布置整体偏向于前移,导致在生产过程中,容易出现热负荷自动分配与生产实际需求不匹配,需要人工干预的现象。
加热炉过程控制系统论文
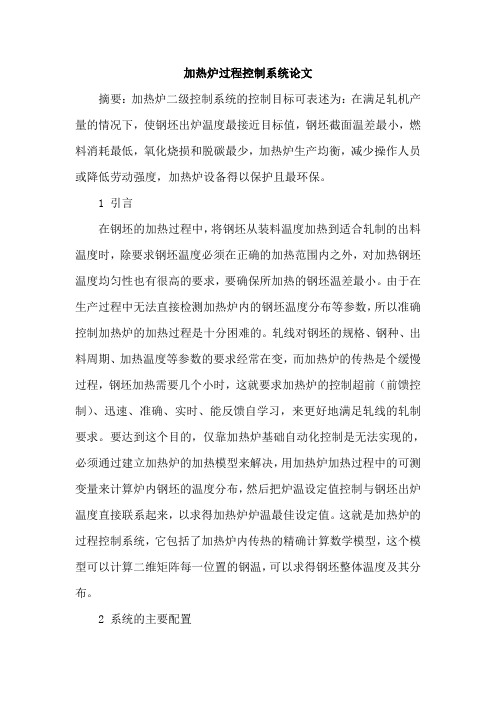
加热炉过程控制系统论文摘要:加热炉二级控制系统的控制目标可表述为:在满足轧机产量的情况下,使钢坯出炉温度最接近目标值,钢坯截面温差最小,燃料消耗最低,氧化烧损和脱碳最少,加热炉生产均衡,减少操作人员或降低劳动强度,加热炉设备得以保护且最环保。
1 引言在钢坯的加热过程中,将钢坯从装料温度加热到适合轧制的出料温度时,除要求钢坯温度必须在正确的加热范围内之外,对加热钢坯温度均匀性也有很高的要求,要确保所加热的钢坯温差最小。
由于在生产过程中无法直接检测加热炉内的钢坯温度分布等参数,所以准确控制加热炉的加热过程是十分困难的。
轧线对钢坯的规格、钢种、出料周期、加热温度等参数的要求经常在变,而加热炉的传热是个缓慢过程,钢坯加热需要几个小时,这就要求加热炉的控制超前(前馈控制)、迅速、准确、实时、能反馈自学习,来更好地满足轧线的轧制要求。
要达到这个目的,仅靠加热炉基础自动化控制是无法实现的,必须通过建立加热炉的加热模型来解决,用加热炉加热过程中的可测变量来计算炉内钢坯的温度分布,然后把炉温设定值控制与钢坯出炉温度直接联系起来,以求得加热炉炉温最佳设定值。
这就是加热炉的过程控制系统,它包括了加热炉内传热的精确计算数学模型,这个模型可以计算二维矩阵每一位置的钢温,可以求得钢坯整体温度及其分布。
2 系统的主要配置(1)过程控制系统的主要设备;以1台服务器和一台高性能的工控机作为该过程的控制主机,共同完成加热炉的板坯跟踪、燃烧设定计算和数据处理及数据通讯、班管理、报表打印等功能。
(2)操作终端(HMI);操作终端采用客户机/服务器方式,在加热炉操作室设置1台HMI PC服务器,另外在加热炉操作室设置1台HMI客户机,用于过程控制的操作。
(3)通讯网络;加热炉过程计算机与轧线过程计算机之间;加热炉过程计算机与基础自动化PLC之间、HMI服务器与客户机之间;HMI服务器与过程计算机之间、基础自动化级PLC之间、基础自动化级PLC与HMI服务器之间均采用以太网通讯,基础自动化级PLC与远程I/O、传动装置之间采用现场总线通讯方式。
加热炉燃烧控制系统设计与仿真_毕业设计(论文)
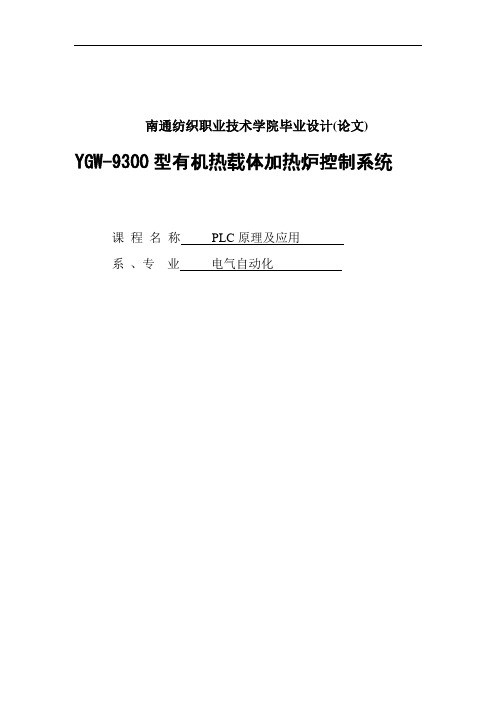
南通纺织职业技术学院毕业设计(论文) YGW-9300型有机热载体加热炉控制系统课程名称PLC原理及应用系、专业电气自动化加热炉燃烧控制系统设计与仿真摘要冶金工业消耗大量的能源,其中钢坯加热炉就占钢铁工业总能耗的四分之一。
自70年代中期以来,各工业先进国对各种燃烧设备的节能控制进行了广泛、深入的研究,大大降低了能耗。
步进式加热炉不仅是轧线上最重要的设备之一,而且也是耗能大户。
钢坯加热的技术直接影响带钢产品的质量、能源消耗和轧机寿命。
因此步进式加热炉优化设定控制技术的推广对钢铁企业意义重大。
步进式加热炉的生产目的是满足轧制要求的钢坯温度分布,并实现钢坯表面氧化烧损最少和能耗最小。
由于步进式加热炉具有非线性、不确定性等特点,其动态特性很难用数学模型加以描述,因此采用经典的控制方法难以收到理想的控制效果,只能依靠操作人员凭经验控制设定值,当工况发生变化时,往往使工艺指标(如空燃比)实际值偏离目标值范围,造成产品质量下降消耗增加。
针对以上情况,本文通过理论和仿真比较说明使用双交叉限幅控制系统是一种比较好的燃烧控制方法。
关键词:步进式加热炉;空燃比;双交叉限幅;系统仿真目录摘要............................................................................................................................. I I ABSTRACT ................................................................................ 错误!未定义书签。
第一章引言 (1)第二章步进式加热炉 (4)2.1步进式加热炉简介 (4)2.2步进式加热炉工艺过程 (5)2.3加热炉控制技术的发展和现状 (8)第三章燃烧控制系统设计及仿真 (9)3.1 步进式加热炉生产工艺和控制要求 (9)3.2燃烧控制系统及仿真 (10)3.2.1 Simulink简介 (10)3.2.2 仿真模型的建立 (11)3.2.3串级比值控制系统设计及仿真 (12)3.2.4 单交叉限幅燃烧控制系统设计及仿真 (17)3.2.5双交叉限幅控制系统设计及仿真 (22)3.2.6偏置单元和炉膛负压控制系统简介 (29)第四章组态软件MCGS在加热炉控制中的应用 (30)4.1 MCGS简介 (30)4.2 MCGS在加热炉控制中的应用 (32)第五章仪表选型 (34)5.1检测元件的选型 (34)5.1.1温度检测 (34)5.2压力和流量的测量 (36)5.3 变送器的选取 (37)5.3.1温度变送器 (38)5.3.2差压变送器的选取 (39)5.4执行器的选择 (40)结束语 (42)参考文献 (43)致谢 (44)第一章引言工业锅炉广泛应用于炼油、冶金、化工、轻工、造纸、纺织与食品等行业。
步进梁式加热炉内板坯跟踪功能的实现

步进梁式加热炉内板坯跟踪功能的实现作者:陈铎来源:《机电一体化》2014年第03期【摘要】本文以某热轧厂步进梁式加热炉为背景,着重介绍了一种炉内板坯跟踪功能的实现方法,该方法逻辑清楚,编程容易,易于实现,在实际使用时未发生板坯数据跟踪错误,保证了生产的顺稳进行。
【关键词】加热炉;板坯;跟踪;实现方法引言炉内板坯跟踪功能是加热炉控制功能中不可缺少的部分,能够提供炉内板坯的真实位置,为板坯出炉温度的准确计算提供前提条件,并确保板坯按计划轧制,对于加热炉的连续性和稳定性生产有十分重要的作用[1]。
由于操作工无法看到炉内板坯的运行状况,一旦出现数据混乱,必须停产呼叫维修人员进行维修,造成一定的停产时间。
本文以某热轧厂步进梁式加热炉为背景,先简述了工艺流程和控制系统硬件配置,然后分四个步骤着重介绍了一种炉内板坯跟踪功能的实现方法。
1 工艺简述某热轧厂加热炉年计划完成400万t板坯的加热任务,拥有三座额定加热能力为 300t/h步进梁式加热炉。
加热炉有效长度是44870mm,板坯规格为厚度230mm、宽度850-1650mm、长度9000-11000mm,设计标准坯规格为230×1250×10500mm。
待加热板坯按轧制顺序进行校验,校验合格板坯由入炉辊道输送、定位到加热炉炉前;装料炉门开启,装钢机将板坯托起来,放到炉内步进梁上;步进梁执行正循环动作将板坯一步步运往出料端;待出钢条件满足后,出料炉门开启,出钢机将板坯从炉内托出来,放到出炉辊道上,最后由出炉辊道将板坯送往轧机轧制。
2 控制系统硬件配置每座炉子独自使用一套板坯输送控制系统。
每个系统均选用西门子416-3系列CPU作为主控制器,通讯网络采用Profibus-DP,包含3个DP主站系统。
其中,主控制器用来完成设备顺序控制、物料跟踪、与其它PLC通讯等功能;DP主站系统1包括4个ET200M子站和按钮盘,用来采集装出钢机、炉门的位置信号和发出控制命令;DP主站系统2包括2个300系列 CPU,分别用来实现对步进梁和液压站的逻辑控制;DP主站系统3用来与变频器通讯,实现对装出钢机电机、炉门电机的控制。
一种应用于加热炉的全范围仿真系统
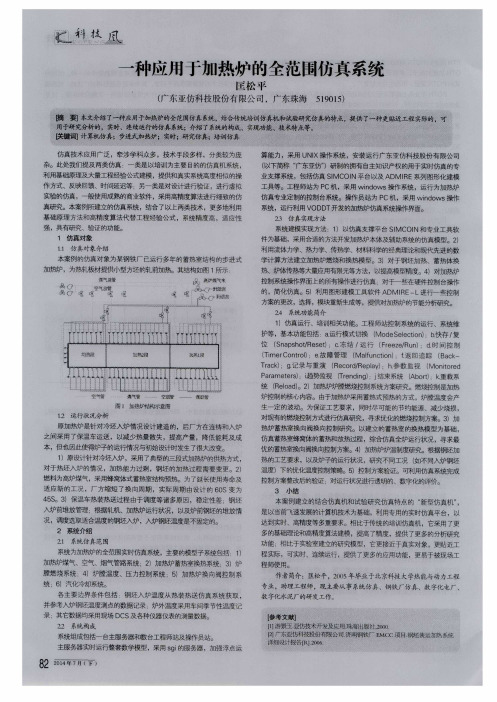
仿真专业定制的控 制台系统。操作员站为 P C机 ,采用 wi n d o ws 操作 系统 , 运: 亍 利用 V O D D T 开发的加热炉仿真系统操作界面。
2 3 仿真实现方法 系统建模实现方法:1 )以仿真支撑平台 S I MC OI N和专业工具软
《甜 披
一
种应用于加热炉 的全范 围仿真系统
匡松 平
( 广东 亚仿科 技股 份有 限公 司 ,广 东珠海 5 1 9 0 1 5 )
≯ l l 《 螽 鼍 圈 本文介 绍了 — 种应用于加 热炉 的全范围 仿真系 统, 结合 传统培训仿真机 和试验 研究仿真 的特点 提供 了 一种更 贴 近工 程实际 的, 可
用于研究分析的,实时、连续运行的仿真 系统;介绍了系统的构成、实现功 能、 技 术特点等。 【 关键i 司 】 计算 【 崩- 真;步进式加热炉;实时; 研究仿真;培训仿真 仿真技术应用广泛 ,牵涉学科 众多,技术手段多样 , 分类较为庞
杂。此处我们提及两类仿真 : 一类是 以 培训 为主要 目的的仿真机系统 , 利用基础原理及大量工程经验公式建模 , 提供和真实系统高度相似 的操
统 ( R e l o a d ) 。2 ) 加热炉炉膛燃烧控制系统方案研究。燃烧控制是加热
炉控制 的核心内容。由于加热炉采用蓄热式预热的方式 ,炉膛温度会产 生一定的波动。为保证工艺要求,同时尽 可能的节约能源、减少烧损 ,
图 1 加热炉结构示意陶
1 2 运 行状 况 分析
对现有的燃烧控制方式进行仿真研究 , 寻求优化的燃烧控制方案。3 )加
控制系统操作界面上的所有操作进行仿真 , 对于一些在硬件控制 台操作
《2024年不锈钢复合板热轧仿真模拟》范文
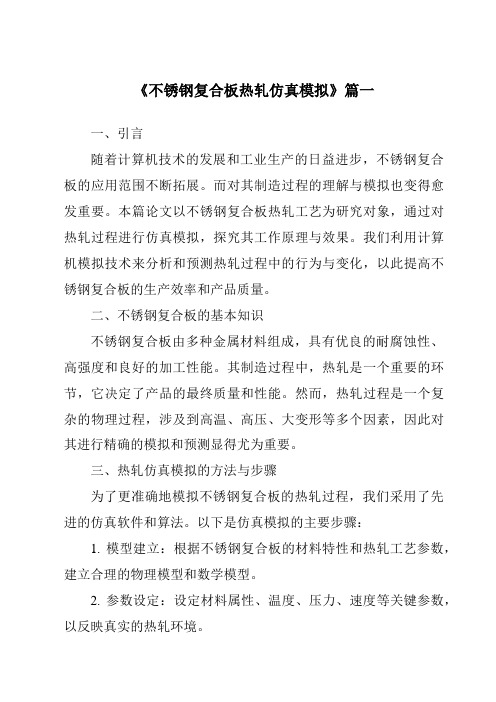
《不锈钢复合板热轧仿真模拟》篇一一、引言随着计算机技术的发展和工业生产的日益进步,不锈钢复合板的应用范围不断拓展。
而对其制造过程的理解与模拟也变得愈发重要。
本篇论文以不锈钢复合板热轧工艺为研究对象,通过对热轧过程进行仿真模拟,探究其工作原理与效果。
我们利用计算机模拟技术来分析和预测热轧过程中的行为与变化,以此提高不锈钢复合板的生产效率和产品质量。
二、不锈钢复合板的基本知识不锈钢复合板由多种金属材料组成,具有优良的耐腐蚀性、高强度和良好的加工性能。
其制造过程中,热轧是一个重要的环节,它决定了产品的最终质量和性能。
然而,热轧过程是一个复杂的物理过程,涉及到高温、高压、大变形等多个因素,因此对其进行精确的模拟和预测显得尤为重要。
三、热轧仿真模拟的方法与步骤为了更准确地模拟不锈钢复合板的热轧过程,我们采用了先进的仿真软件和算法。
以下是仿真模拟的主要步骤:1. 模型建立:根据不锈钢复合板的材料特性和热轧工艺参数,建立合理的物理模型和数学模型。
2. 参数设定:设定材料属性、温度、压力、速度等关键参数,以反映真实的热轧环境。
3. 仿真模拟:利用仿真软件对热轧过程进行模拟,观察材料的变形、温度变化等行为。
4. 结果分析:根据仿真结果,分析热轧过程中的问题与优化方向。
四、仿真模拟结果分析通过仿真模拟,我们能够直观地观察不锈钢复合板在热轧过程中的变化。
在仿真过程中,我们重点关注材料的变形行为、温度分布和应力状态等关键因素。
结果表明,通过合理的参数设置和操作条件,可以有效控制材料的变形和温度分布,从而提高产品的质量和性能。
同时,我们还发现了一些潜在的问题和优化方向,如材料选择、工艺参数调整等。
五、结论与展望通过对不锈钢复合板热轧过程的仿真模拟,我们深入了解了其工作原理和效果。
仿真结果为我们提供了宝贵的参考数据和优化方向。
在实际生产中,我们可以根据仿真结果调整工艺参数和操作条件,以提高产品的质量和生产效率。
同时,仿真模拟还可以帮助我们更好地理解材料的行为和性能,为新产品的研发提供有力的支持。
热轧板厂180th蓄热式步进加热炉设计热能与动力工程毕业设计论文

热轧板厂180th蓄热式步进加热炉设计热能与动力工程毕业设计论文热能与动力工程毕业论文题目:热轧板厂180t/h 蓄热式步进加热炉设计专业:热能与动力工程摘要本设计题目是包钢热轧板厂180t/h 蓄热式连续加热炉,在借鉴已有相关文献的基础上,对加热炉进行了设计和计算,主要包括初步设计和技术设计。
初步设计对加热炉的选型结构做出来初步的选择;技术设计对加热炉设计进行全面的热力计算并确定了加热炉的主要技术参数、结构形式加热炉重要辅助设备进行选择。
通过本次毕业设计,改善蓄热式燃烧技术,节约了燃料,提高炉子热效率,提高了产量及产品质量,同时减少了对环境的污染,达到了节能减排的目标。
由于本设计采用了先进的蓄热式高温空气燃烧技术,该技术拥有多方面的优势,尤其在节能降耗和环保方面取得了很大的成效,相信在国内会拥有广阔的发展前景。
关键词 : 加热炉;高炉煤气;蓄热式燃烧;高效节能热能与动力工程毕业论文ABSTRACTIn this paper, Baogang Hot MILL 180 t / h for Regenerative furnace requirements of a graduation project Reference has been in the literature on the basis of blast furnace gas to fuel the furnace design a comprehensive thermal calculation。
Including combustion, the heating time, the metal structure, masonry design, heat balance calculation. In the projector adumbrate the blast and the air at the same time,not only improve the thermal efficiency,but efficiedcly make use of the blast furnace gas.Focuson the selection process heating furnace, the heating time and load calculation of changes in how the changes in operating parameters were studied and discussed, the furnace important supplementary equipment selection, concluded that the design and the work of the next step Their ideas and perspectives.Through this graduate design and improve regenerative combustion technology, to improve the thermal efficiency of the stove, the goal of improving product quality, while using the stove vaporization cooling system, reducing the water pipes and India to ensure heating quality.Because the design adopted the high temperature air combustion technology,it owned the various advantage, particularly at economized on energy to decline to consume and environmental protection to obtain the very big result, we believed that it will own vast development foreground in the domestic。
热轧板带线加热炉智能燃烧模型的应用

栅镟轉銨0技术论坛戀爾廳能鶴1_驗用丨i f i i r蒙治祥黉W梁-一柳钢2 032热轧板带生产线有3座常规式加 热炉,自2005-10投产以来,燃烧控制模型均 为手动操作,以多年的经验值和理论计算值为 基础,设定空燃比,手动调节加热炉各个加热 段的煤气流量和空气流量,使加热炉内各段炉 气温度达到轧制计划坯料的工艺要求温度。
由于班组对生产工艺的理解和对设备的操作习惯 均有不同,导致在基本满足工艺要求的前提下,每个班组的加热质量均有不同。
且由于2 032生 产线生产品种较多,增加了人工操作的难度,煤气量和空气量的调整次数多,造成炉温波动 频繁,无法保证炉内温度场的稳定性,不但浪 费能源,加热质量也有待优化,还加大了员工 的工作量。
为此,柳钢热轧板带厂与北京科技 大学合作开发加热炉智能燃烧模型。
本文总结 新模型的应用情况。
智能燃烧模型设计与原过程控制系统的各段炉温和最小在炉 时间要求不同,在改造加热炉一级和二级系统 后,智能燃烧模型以坯料升温曲线为基础,以每块坯料出炉目标温度为加热控制最终目标,以每块坯料的加热段段末计算温度为加热控制过程目标。
在坯料进入加热炉的预热段时,智能燃烧 模型开始标记该坯料位置、入炉温度、牌号钢 种和坯料规格等信息,以每个炉子不同的热效 率,按当前坯料出炉节奏推算出一个动态的在 炉时间,使用最合适该坯料的升温曲线,通过 采集该坯料实时的炉温,设定动态目标炉温,操控煤气阀门和空气阀门进行全过程的加热控 制,直至该坯料的计算温度达到出炉目标温度。
整个过程操作工人基本只需进行出钢节奏控制 以及极少的人工温度干预。
应用及优化一二级数据链接在模型离线状态下,进行生产过程的U-L2 的数据通讯模式、电文格式确认,并进行电文 数据组织和通讯测试,实现了双系统数据的异 构同步运行。
制定L2-L3数据接口调试方案,搭建一套调试数据结构并实时同步实际数据,完成L2、L3之间收发数据以及功能测试。
加热炉全自动模型在宝钢热轧各产线的运用

加热炉全自动模型在宝钢热轧各产线的运用王墨南,吕立华(宝山钢铁股份有限公司中央研究院,上海 201999) 摘要:根据宝钢热轧各产线生产的实际情况,优化了加热炉烧钢模型,包括计算加热炉内单块板坯需要温度的必要炉温模型、计算加热炉段内设定温度的设定炉温模型、计算板坯剩余在炉时间的生产节奏模型等。
同时解决了原有加热炉模型冷坯升温慢、降温幅度过大等问题,特别对于质量敏感的钢种进行了针对性设置。
目前,各基地加热炉模型都得到了较高的全自动化率,降低了操作人员的工作强度。
关键词:加热炉;温度;全自动模型中图分类号:TG307 文献标志码:B 文章编号:1008-0716(2021)02-0019-05doi:10.3969/j.issn.1008-0716.2021.02.004ApplicationoffullautomaticmodelforheatingfurnaceinBaosteel’shotrollinglinesWANGMonanandLYULihua(ResearchInstitute,BaoshanIron&SteelCo.,Ltd.,Shanghai201999,China) Abstract:AccordingtotheactualproductionsituationofBaosteel’sproductionlines,thispaperoptimizesthemodeloftheheatingfurnace,includingthenecessaryfurnacetemperaturemodelforcalculatingtherequiredtemperatureofasingleslabintheheatingfurnace,thesetfurnacetemperaturemodelforcalculatingthesettemperatureintheheatingfurnacesectionandtheproductionrhythmmodelforcalculatingtheremainingtimeoftheslabinthefurnace,etc.Atthesametime,thepapersolvestheproblemsoftheoriginalheatingfurnacemodel,forexample,slowheatingofthecoldbilletandexcessivecoolingrange.Especiallyforquality sensitivesteelgrades,targetedsettingshavebeenmade.Atpresent,theheatingfurnacemodelsofallbaseshaveobtainedahighfullautomationrate,whichreducestheworkintensityoftheoperators.Keywords:heatingfurnace;temperature;fullautomaticmodel基金项目:国家重点研发计划重点基础材料技术提升与产业化重点专项项目(项目号2017YFB0304203)王墨南 工程师 1987年生 2012年毕业于上海交通大学现从事冶金热工仿真与自动化研究工作电话 26641071 E mail wangmonan@baosteel.com 加热炉是钢铁生产工艺的重要环节,板坯的加热质量直接影响了钢铁产品的最终质量。
步进式加热炉仿真系统设计
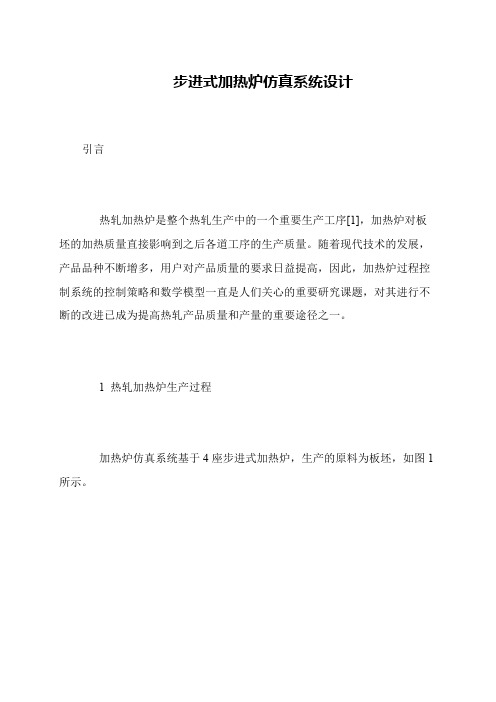
步进式加热炉仿真系统设计
引言
热轧加热炉是整个热轧生产中的一个重要生产工序[1],加热炉对板坯的加热质量直接影响到之后各道工序的生产质量。
随着现代技术的发展,产品品种不断增多,用户对产品质量的要求日益提高,因此,加热炉过程控制系统的控制策略和数学模型一直是人们关心的重要研究课题,对其进行不断的改进已成为提高热轧产品质量和产量的重要途径之一。
1 热轧加热炉生产过程
加热炉仿真系统基于4座步进式加热炉,生产的原料为板坯,如图1所示。
- 1、下载文档前请自行甄别文档内容的完整性,平台不提供额外的编辑、内容补充、找答案等附加服务。
- 2、"仅部分预览"的文档,不可在线预览部分如存在完整性等问题,可反馈申请退款(可完整预览的文档不适用该条件!)。
- 3、如文档侵犯您的权益,请联系客服反馈,我们会尽快为您处理(人工客服工作时间:9:00-18:30)。
热轧生产线加热炉跟踪仿真实现模式论文
摘要:跟踪仿真在数据结构定义的基础上应用二维指针数组和积分算法实现了物料在生产过程中运动状态的监控及模拟,并在速度控制上发挥模型主动,预控,智能,灵活的特点,充分发挥了高速PLC 的性能,表现出了良好的控制效果。
控制集成度高、集中度高的工业控制系统下的其他控制如温度控制,张力控制,压力控制等通过合理运用跟踪仿真模型,从可靠、安全、节能等方面优化跟踪仿真逻辑,都能实现更直观,快速,稳定和开放的控制效果。
0引言
热轧薄板生产线工艺复杂紧凑,设备控制要求响应快速,自动化集中控制程度高,跟踪仿真模型为人机交互操作界面组态提供基础数据,也是PLC程序中触发和连锁信号构成中的重要组成。
在控制模型中起着逻辑、时间、空间上的协调作用,跟踪系统的准确性和可靠性关系顺控程序的有序执行,生产安全,控制精度,产品质量,对节约能源,降低原材料消耗,成本控制也具有非常实际的执行意义。
跟踪仿真模型模拟自动化生产线上物料的运动状态并产生速度控制,以及设备动作的协调同步控制,其时序在整个生产动作周期中是循环但不重复的时序。
跟踪仿真模型的模拟量因此是速度的时间反映,也随着时间产生不同的速度控制,有积分含意义,同时有逻辑意义。
以下是热轧生产线加热炉跟踪仿真的一种实现模式及其在速度控制中的应用。
1跟踪模型分析和实现算法
1.1环境模型
加热炉跟踪距离长,一线有加热段,横移段,保温段,三个区域;二线有加热段和横移段两个区域,如图1所示,其板坯通过一线或二线横移车输送到一线保温段。
并定义加热炉进口为模型参照0位。
1.2 逻辑算法
连铸坯经摆剪剪切后进入加热炉区,加热炉区进口光电开关PHOTOCELL的关断产生板坯头部,导通产生尾部,同时产生头部占用和尾部占用两个逻辑量。
头部和尾部跟踪点从零开始对速度设定值进行时间积分累加。
PLC通过CC-LINK网络对驱动每组炉辊的变频器进行速度设定,由变频器实现闭环速度控制。
该设定值为矢量值,速度的正负区别正反向,该速度的时间累加积分可实现双向可逆跟踪。
1.2.1逻辑信号滤波及跟踪偏差修正
头部和尾部的CREAT和DELET信号采用双PHOTOCELL光电开关保证信号传递,并加入CUT和DISCHARGE的临时信号作为其连锁信号确保信号可靠。
区域内PHOTOCELL在允许偏差范围内对跟踪变量进行修正。
相关逻辑梯形图如图2,控制逻辑流程如图3,图4。
2数据结构
2.1定义数组
物料ID信息G,头部积分累加值H,尾部积分累加值T,头部占用逻辑量Hh,尾部占用逻辑量Tt共同构成一个跟踪数组。
根据加热炉长度,共定义A0~A14共15个数组,跟踪数组初始值是0。
加热炉两侧光电开关等距分布,跟踪数据在实际值偏差范围z内的下降和上升脉冲对跟踪数组的头部和尾部累加值以Li进行修正。
收到轧机区DISCHARGE信号后,保温段SET出钢信号并启动保温段加速区;当出口光电开关组检测到上升脉冲时,RESET出钢信号,同时跟踪数组前移位,末位数组初始复位,数组A0数组物料ID信息G通过level2网络设定跟随轧机继续新的跟踪。
跟踪数组数Ai数据结构定义如表1。
2.2模型的并行合作
二线纵向跟踪模型跟一线相同,两个模型的接口通过嵌入一线模型的手动创建程序模块实现合作。
其横向模型为单变量位置模型,单独的闭环反馈控制器根据测距仪反馈控制变频器实现。
与一线跟踪数组构成准二维意义的跟踪数组模型,这里以一线为例说明跟踪仿真数学模型的算法,相关程序控制逻辑流程如图3。
3速度控制
3.1速度控制功能说明
加热段内定义两个速度区,加速区头部Sah=a(a-区域边界值),尾部Sat=Ty。
(Ty-被加速板坯尾部跟踪数据)。
常速区头部Slh=Ty,
尾部Slt=0。
常速区速度V1=Ve(Ve-连铸出钢速度),剪切后V1=Vc (Vc-小加速拉开头尾间隔),延时后恢复V1=Ve。
加热段第一根板坯尾部到达加速点(其模型数值为b)后,加速区速度为Va=V2。
到达加热段前端(其模型数值为a-w,a-区域界线值,w-考虑光电开关禁区值和减速点以及0速摆动范围)后,保持HOLD为1时,加速区为摆动速度,等效速度为Va=0;HOLD为0时,加速区速度为Va=V2出钢,横移段常速区V3连接加热段加速区V2。
模型模拟,横移段和保温段的速度控制功能相仿,这里以加热段为例讨论跟踪模型在速度控制中的应用。
相关程序控制流程图如图4。
3.2模型模拟0速控制
高温工况下,工艺要求炉辊始终有一定转速,这就要求单组辊道,在没有E-STOP信号时速度总为绝对输出;同时工艺也要求各区域的保持功能,以控制生产节奏。
跟踪模型解决这个矛盾时,用两个时间继电器完成等时正反向转换循环,模拟0速度输出,实现0速度下的非零转速。
3.3速度区控制模型
炉区内辊道电机平均分布,单个变频器控制单组棍道(两个辊为一组,间隔1米),PLC通过CC-LINK网络模块与个变频器通讯,实现跟踪区域与跟踪模型空间上的映射,也为实现速度区域的线性对应和动态移动提供了模型基础。
单个变频器i的外部IP定义为IPi= Li/Lo+ExtendIP (Li-炉辊物理距离,Lo-炉辊间距,ExtendIP-物理
偏移地址,0≤i<81)。
Ty<li≤a,变频器速度设定值vipi=va;0≤li< ty,vipi="V1。
相关程序控制逻辑流程如图5。
4结束语
以上所述跟踪仿真在数据结构定义的基础上应用二维指针数组和积分算法实现了物料在生产过程中运动状态的监控及模拟,并在速度控制上发挥模型主动,预控,智能,灵活的特点,充分发挥了高速PLC的性能,表现出了良好的控制效果。
控制集成度高、集中度高的工业控制系统下的其他控制如温度控制,张力控制,压力控制等通过合理运用跟踪仿真模型,从可靠、安全、节能等方面优化跟踪仿真逻辑,都能实现更直观,快速,稳定和开放的控制效果。