钻,镗,刨,拉削加工
常用加工方法概述
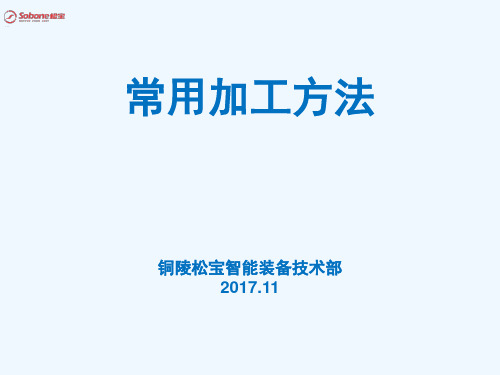
加工范围
车削是以加工回转体为主要加工目的。在车床上可以加工:外圆、端 面、锥度、车成型面、绕弹簧等。
二、钻削 钻孔
定义:钻削刀具与工件作相对运动并作轴向 进给运动,在工件上加工孔的方法。 钻孔是一种最基本的孔加工方 法。钻孔经常在钻床和车床上 进行,也可以在镗床和铣床上 进行。常用的钻床有台式钻床 、立式钻床和摇臂钻床。
刨削加工范围:
由于刨削的特点。维修车间和模具车间应用较多。 刨削主要用在单件小批量生产 中, 刨削主要用来加工平面,也广泛用于加工直槽。 牛头刨床的最大刨削长度一般不超过1000mm,因此只适于加工中、小型工件。龙门 刨床主要用来加工大型工件,或同时加工多个中、小型工件。 插床又称立式牛头刨床,主要用来加工工件的内表面,如键槽、花键槽等,也可用 于加工多边形孔,如四方孔、六方孔等。特别适于加工盲孔或有障碍台肩的内表面。
拉削的工艺特点:
1.生产效率高:由于拉刀是多齿刀具,同时参加工作的刀齿数较多,同时参与 切削的切削刃较长,并且在拉刀的一次工作行程中能够完成粗—半精—精加工, 大大缩短了基本工艺时间和辅助时间。 2.加工精度高,外表面粗糙度小:拉刀具有校准部分,其作用是校准尺寸,修光 表面,并可作为精切齿的后备刀齿。拉削的切削速度较低,切削过程比较平稳, 并可避免积屑瘤的产生。一般拉孔的精度为IT8~IT7,表面粗糙度Ra值为0.4~ 0.8m。 3.拉床结构和操作比较简单:拉削只有一个主运动。但拉削时切削速度较低。刃 磨一次可以加工数以千计的零件,刀具磨损较慢,一把拉刀又可以重磨多次。 4.拉刀成本高:由于拉刀的结构和形状复杂,制造成精度和表面质量要求较高。 5.不能拉削加工盲孔、深孔、阶梯孔及有障碍的外表面,拉削不能纠正孔的位置 误差。
五、拉削
定义:用拉刀在拉力作用下作轴向运动, 加工工件内、外表面的方法。利用多齿 的拉刀,逐齿依次从工件上切下很薄的 金属层,使表面达到较高的精度和较小 的粗糙度值。
孔加工方法有哪些

孔加工方法有哪些孔加工是制造业中常见的加工工艺之一,它在各种机械零部件的制造中起着至关重要的作用。
孔加工的质量和效率直接影响着整个产品的性能和生产效率。
那么,孔加工方法有哪些呢?接下来我们将一一介绍。
首先,最常见的孔加工方法之一是钻削。
钻削是利用钻头在工件上旋转并向下推进的方式来形成孔洞的加工方法。
它可以分为手动钻削和机械钻削两种方式。
手动钻削一般用于小批量生产或修补加工,而机械钻削则适用于大批量生产,具有高效率和一致性的优点。
其次,还有铰削这种孔加工方法。
铰削是利用铰刀在工件上旋转并向下推进的方式来形成孔洞的加工方法。
它一般适用于孔的加工深度较大的情况,能够快速、高效地完成孔的加工。
除了钻削和铰削,还有镗削这种孔加工方法。
镗削是利用镗刀在工件上旋转并在径向移动的方式来形成孔洞的加工方法。
它适用于孔的精度要求较高的情况,能够获得较高的加工精度和表面质量。
此外,还有冲剪这种孔加工方法。
冲剪是利用冲头在工件上冲击的方式来形成孔洞的加工方法。
它适用于对工件表面要求较高的情况,能够快速、高效地完成孔的加工。
最后,还有激光加工这种孔加工方法。
激光加工是利用激光束对工件进行照射的方式来形成孔洞的加工方法。
它适用于对孔的形状和尺寸要求较为复杂的情况,能够实现非常精细的加工。
综上所述,孔加工方法有很多种,每种方法都有其适用的场合和优势。
在实际生产中,我们需要根据工件的具体要求和加工条件来选择合适的孔加工方法,以确保产品质量和生产效率。
希望本文所介绍的内容能够对大家有所帮助,谢谢阅读!。
内孔表面加工常用方法大汇总

内孔表面加工方法较多,常用的有钻孔、扩孔、铰孔、镗孔、磨孔、拉孔、研磨孔、珩磨孔、滚压孔等。
一、钻孔用钻头在工件实体部位加工孔称为钻孔。
钻孔属粗加工,可达到的尺寸公差等级为IT13~IT11,表面粗糙度值为Ra50~12.5μm。
钻孔有以下工艺特点:1.钻头容易偏斜。
在钻床上钻孔时,容易引起孔的轴线偏移和不直,但孔径无显著变化;在车床上钻孔时,容易引起孔径的变化,但孔的轴线仍然是直的。
因此,在钻孔前应先加工端面,并用钻头或中心钻预钻一个锥坑,以便钻头定心。
钻小孔和深孔时,为了避免孔的轴线偏移和不直,应尽可能采用工件回转方式进行钻孔。
2.孔径容易扩大。
钻削时钻头两切削刃径向力不等将引起孔径扩大;卧式车床钻孔时的切入引偏也是孔径扩大的重要原因;此外钻头的径向跳动等也是造成孔径扩大的原因。
3.孔的表面质量较差。
钻削切屑较宽,在孔内被迫卷为螺旋状,流出时与孔壁发生摩擦而刮伤已加工表面。
4.钻削时轴向力大。
这主要是由钻头的横刃引起的。
因此,当钻孔直径d﹥30mm时,一般分两次进行钻削。
第一次钻出(0.5~0.7)d,第二次钻到所需的孔径。
由于横刃第二次不参加切削,故可采用较大的进给量,使孔的表面质量和生产率均得到提高。
二、扩孔扩孔是用扩孔钻对已钻出的孔做进一步加工,以扩大孔径并提高精度和降低表面粗糙度值。
扩孔可达到的尺寸公差等级为IT11~IT10, 表面粗糙度值为Ra12.5~6.3μm,属于孔的半精加工方法,常作铰削前的预加工,也可作为精度不高的孔的终加工。
扩孔方法如图7-4所示,扩孔余量(D-d),可由表查阅。
扩孔钻的形式随直径不同而不同。
直径为Φ10~Φ32的为锥柄扩孔钻,如图7-5a所示。
直径Φ25~Φ80的为套式扩孔钻,如图7-5b所示。
扩孔钻的结构与麻花钻相比有以下特点:1.刚性较好。
由于扩孔的背吃刀量小,切屑少,扩孔钻的容屑槽浅而窄,钻芯直径较大,增加了扩孔钻工作部分的刚性。
2.导向性好。
05第五章 钻削、镗削、铰削与拉削
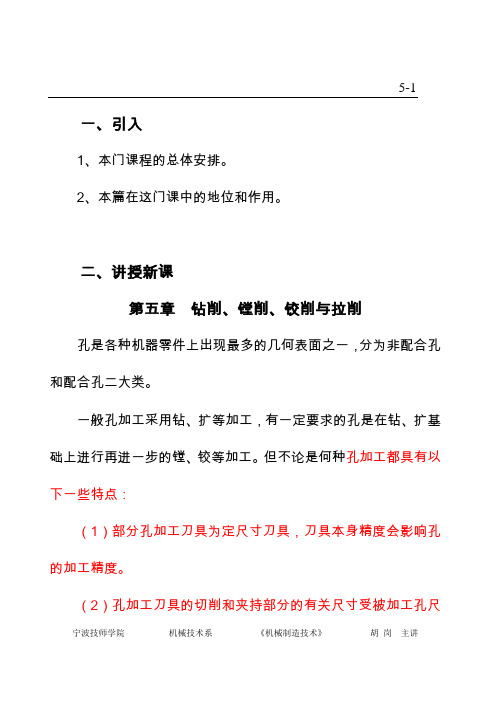
5-1一、引入1、本门课程的总体安排。
2、本篇在这门课中的地位和作用。
二、讲授新课第五章钻削、镗削、铰削与拉削孔是各种机器零件上出现最多的几何表面之一,分为非配合孔和配合孔二大类。
一般孔加工采用钻、扩等加工,有一定要求的孔是在钻、扩基础上进行再进一步的镗、铰等加工。
但不论是何种孔加工都具有以下一些特点:(1)部分孔加工刀具为定尺寸刀具,刀具本身精度会影响孔的加工精度。
(2)孔加工刀具的切削和夹持部分的有关尺寸受被加工孔尺寸的限制,会使刀具的刚性变差。
(3)孔加工时,刀具一般是封闭或半封闭状态下进行工作,对加工质量和刀具耐用度都会产生不利的影响。
宁波技师学院机械技术系《机械制造技术》胡岗主讲5-2 基于以上原因,在机械设计过程中选用孔和轴配合的公差等级时,经常把孔的公差等级定得比轴低一级。
孔加工的方法很多,常用的有钻孔、扩孔、锪孔、铰孔、镗孔、拉孔、磨孔等,还有金刚镗、珩磨、研磨、挤压及特种加工孔等方法。
其加工孔直径Φ0.01~Φ1000mm,加工精度可达到IT13~IT5,表面粗糙度Ra12.5~0.006μm;可在金属或非金属材料上加工,也可在普通材料或高硬度材料上加工。
在加工中可根据不同要求,合理进行选择最佳的加工方案,达到加工质量能符合要求。
第一节钻削加工(一)一、概述用钻头作回转运动,并使其与工件作相对轴向进给运动,在实体工件上加工孔的方法称为钻孔;在已有孔的情况下,用扩孔钻对孔径进行再扩大的加工称为扩孔;钻孔与扩孔统称为钻削。
钻削可以在各种钻床上进行,也可以在车床、铣床、镗床和组宁波技师学院机械技术系《机械制造技术》胡岗主讲5-3合机床、加工中心上进行,但大多数情况下,尤其是在大批量下生产时,主要还是在钻床上进行。
二、钻床主要用钻头在工件上加工孔的机床称为钻床。
通常以钻头的回转运动为主运动,钻头的轴向移动为进给运动。
钻床的分类:坐标镗钻床、深孔钻床、摇臂钻床、台式钻床、立式钻床、卧式钻床、铣钻床、中心孔钻床等八大类。
钻削、车削、磨削、镗孔、拉削的工艺特点

钻削的工艺特点钻削运动构成:钻头的旋转运动为主切削运动,加工精度较低。
钻孔可在钻床上进行,也可在镗床、车床、铣床上进行,常用钻床有台式钻床、立式钻床、摇臂床应用在各类机器零件上经常需要进行钻孔,因此钻削的应用还是很广泛的,但是,由于钻削的精度较低,表面较粗糙,一般加工精度在IT10以下,表面粗糙度Ra值大于12.5μm ,生产效率也比较低。
因此,钻孔主要用于粗加工,例如精度和粗糙度要求不高的螺钉孔、油孔和螺纹底孔等。
但精度和粗糙度要求较高的孔,也要以钻孔作为预加工工序。
单件、小批生产中,中小型工件上的小孔(一般D 13 mrn)常用台式钻床加工,中小型工件上直径较大的孔(一般D<50mm)常用立式钻床加工;大中型工件上的孔应采用摇臂钻床加工;回转体工件上的孔多在车床上加工。
在成批和大量生产中,为了保证加工精度,提高生产效率和降低加工成本,广泛使用钻模、多轴钻的或组合机床进行孔的加工。
一、车削的工艺特点1、易于保证工件各加工面的位置精度a 例如易于保证同轴度要求利用卡盘安装工件,回转轴线是车床主轴回转轴线利用前后顶尖安装工件,回转轴线是两顶尖的中心连线b 易于保证端面与轴线垂直度要求由横溜板导轨,与工件回转轴线的垂直度2、切削过程较平稳避免了惯性力与冲击力,允许采用较大的切削用量,高速切削,利于生产率提高。
3、适于有色金属零件的精加工有色金属零件表面粗糙度大Ra值要求较小时,不宜采用磨削加工,需要用车削或铣削等。
用金刚石车刀进行精细车时,可达较高质量。
4、刀具简单车刀制造、刃磨和安装均较方便。
二、车削的应用在车床使用不同的车刀或其他刀具,可以加工各种问转表面,如内外圆柱面、内外圆锥面、螺纹、沟槽、端面和成形面等,加工精度可达IT8一IT7 ,表面粗糙度Ra 值为1.6~0.8,车削常用来加工单一轴线的零件,如直轴和一般盘、套类零件等。
若改变工件的安装位置或将车床适当改装,还可以加工多轴线的零件(如曲轴、偏心轮等)或盘形凸轮。
常用机械加工方法

拉削的工艺特点:
1.生产效率高:由于拉刀是多齿刀具,同时参加工作的刀齿数较多,同时参与 切削的切削刃较长,并且在拉刀的一次工作行程中能够完成粗—半精—精加工, 大大缩短了基本工艺时间和辅助时间。
6.3m。但当采用宽刀精刨时,即在龙门刨床上进行多件或多刀加工
时,用宽刃刨刀以很低的切削速度,切去工件表面上一层极薄的金属, 平面度不大于0.02/1000,表面粗糙度Ra值可达0.4~0.8m。
精品课件
刨削加工范围:
由于刨削的特点。维修车间和模具车间应用较多。 刨削主要用在单件小批量生产 中, 刨削主要用来加工平面,也广泛用于加工直槽。 牛头刨床的最大刨削长度一般不超过1000mm,因此只适于加工中、小型工件。龙门 刨床主要用来加工大型工件,或同时加工多个中、小型工件。 插床又称立式牛头刨床,主要用来加工工件的内表面,如键槽、花键槽等,也可用 于加工多边形孔,如四方孔、六方孔等精。品课特件别适于加工盲孔或有障碍台肩的内表面。
1.通用性好:根据切削运动和具体的加工要求。价格低,刨床的结构比 车床、铣床简单。调整和操作也较方便。所用的单刃刨刀与车刀基本相 同。制造、刃磨和安装皆较方便。形状简单。可加工垂直、水平的平 面,还可加工T型槽、V型槽,燕尾槽等。 2.生产效率较低:刨削的主运动为往复直线运动。加之刀具切入和切出 时有反向冲击时受惯性力的影响,一个表面往往要限制了切削速度的提 高。单刃刨刀实际参加切削的切削刃长度有限,经过多次行程才干加工 进去。加工不连基本工艺时间较长。刨刀返回行程时不进行切削。 3.加工精度不高:刨削的精度可达IT8~IT7,表面粗糙度Ra值为1.6~
钻床加工,较大的孔(D<50 mm)常用立式钻床加工;大中型工件上的孔应采用摇臂 钻床加工,回转体工件上的孔在车床上加工。
机械制造技术基础第6章 z钻、铰、镗和拉削加工

6.2 钻削加工
立式钻床 立式钻床的外形如图 6-2所示,其特点是 主轴位置垂直布置, 位置固定,加工时通 过移动工件来找正孔 的中心线。适用于中 小型工件的孔加工。
6.2 钻削加工
摇臂钻床 其结构如图6-3所示, 主轴箱可在摇臂上左 右移动,摇臂既可绕 立柱转动,又可沿立 柱垂直升降。加工时, 工件在底座或工作台 上安装固定,通过调 整摇臂和主轴箱的位 置来对正加工孔的中 心线。适用于大型工 件的孔加工。
6.1 概述
二、孔的加工方法
一类是对实体工件进行孔加工,即从实体上加工出孔;另 一类是对已有的孔进行半精加工和精加工 非配合孔一般是采用钻削加工在实体工件上直接把孔钻出 来 对于配合孔则需要在钻孔的基础上,根据被加工孔的精度 和表面质量要求,采用铰削、镗削、拉削、磨削等精加工 的方法作进一步的加工。铰削、镗削是对已有孔进行精加 工的典型的切削加工方法。 要实现对孔的精密加工,主要的加工方法就是磨削。当 孔的表面质量要求很高时,还需要采用精细镗、研磨、珩 磨、滚压等表面光整加工方法;对非圆孔的加工则需要采 用插削、拉削以及特种加工方法。
第六章 钻、铰、镗和拉削加工
本章要点
钻削加工 铰削加工 镗削加工 拉削加工
6.1 概述
钻削、铰削、镗削和拉削加工在机械加工中主要用来进 行孔的加工。它是用相应机床在加工实体材料上钻孔和扩大 已有的孔,并达到一定技术要求的加工方法。
一、孔的类型
按照孔与其他零件的相对连接关系的不同,可分为配合 孔与非配合孔; 按其几何特征的不同,可分为通孔、盲孔、阶梯孔、锥孔 等; 按其几何形状不同,可分为圆孔、非圆孔等。
6.1 概述
三、孔的加工特点
孔加工刀具多为定尺寸刀具,刀具磨损造成的形状和尺寸 的变化会直接影响被加工孔的精度。 由于受被加工孔尺寸的限制,切削速度很难提高,影响 加工生产率和加工表面质量。 刀具的结构受孔的直径和长度的限制,刚性较差。容易 产生弯曲变形和振动,孔的长径比(孔深度与直径之比)越 大,刀具刚性对加工精度的影响就越大。 孔加工时,刀具一般是在半封闭的空间工作,切屑排除困 难;冷却液难以进入加工区域,散热条件不好。切削区热 量集中,温度较高,影响刀具的耐用度和钻削加工质量。
机械加工方法有哪些

机械加工方法有哪些
机械加工方法包括:
1. 切削加工:用刀具对工件进行切削,如车削、铣削、钻削等。
2. 磨削加工:用磨料对工件进行磨削,如平面磨削、外圆磨削、内圆磨削等。
3. 铣削加工:利用铣刀对工件表面进行铣削,如平面铣削、立铣削、平面切削等。
4. 钻削加工:利用钻头对工件进行钻孔,如普通钻孔、深孔钻削、中心孔钻削等。
5. 镗削加工:利用镗刀对孔进行镗削,如普通镗削、精加工镗削等。
6. 锯削加工:用锯条对工件进行切割,如手动锯削、机械锯削等。
7. 拉削加工:利用挤压性状变加工工件,如拉伸、拉拔、拉深等。
8. 攻丝加工:利用攻丝工具对螺纹孔进行攻丝,如内螺纹攻丝、外螺纹攻丝等。
9. 滚削加工:利用滚轮对工件进行滚削,如螺纹滚削、齿轮滚削等。
10. 锻造加工:利用锻压工艺对工件进行变形成型,如冲压、锤击等。
11. 焊接加工:利用焊接工艺将多个工件连接在一起,如电弧焊、气体保护焊等。
12. 铸造加工:利用熔融金属倒入模具中形成工件,如铸铁、铸钢等。
13. 冲压加工:利用冲床对金属板材进行冲裁、折弯、拉深等加工。
14. 拉伸加工:利用拉伸设备对金属材料进行拉伸成型,如拉伸机、拉拔机等。
15. 挤压加工:利用挤压设备将金属材料挤出成型,如挤压机、挤拉机等。
《金工实训》项目八__刨削、拉削与镗削

• 【项目目标】 掌握刨床的种类、主要组成及其使用特点。 掌握刨削工作的基本操作技术。 了解刨削加工的基本知识,工艺特点及加工范围。
能正确选择和使用常用的刀具、量具和夹具。 掌握不同零件的刨削、拉削与镗削工艺及加工方法。
•
加工铸铁工件时,通常采用钨钴类硬质合 金刀头;加工钢制工件时,一般采用高速工具钢弯头 刀。
•
坐标镗床是一种高精度机床,主要用于镗 削高精度的孔,特别适用于相互位置精度很高的孔系, 如钻模、镗模等的孔系。
• •
坐标镗床还可以进行钻、扩、铰孔及精铣加工。 此外,还可以作精密刻线、样板划线、孔距及 直线尺寸的精密测量等工作。
•
镗孔不但能修正上道工序所造成的孔中心线 偏斜误差,而且能够保证被加工孔和其他表面(或中心 要素)保持一定的位置精度,所以非常适合平行孔系、 同轴孔系和垂直孔系的加工。 • 但镗轴采用浮动连接时,孔的尺寸精度和位 置精度则由镗模来保证。
•
根据工件的尺寸形状、技术要求及生产批量 的不同,镗孔可以在镗床、车床、铣床、数控机床和组 合机床上进行。 • 一般回旋体零件上的孔,多用车床加工;而 箱体类零件上的孔或孔系(即要求相互平行或垂直的若 干孔),则可以在镗床上加工。
•
单刃镗刀结构简单,可以校正原有孔轴线偏斜 和小的位置偏差,适应性较广,可用来进行粗加工、半精 加工或精加工。 • 但是,所镗孔径尺寸的大小要靠人工调整刀头 的悬伸长度来保证,较为麻烦,加之仅有一个主切削刃参 加工作,故生产效率较低,多用于单件小批量生产。
第三章 常用金属切削加工方法
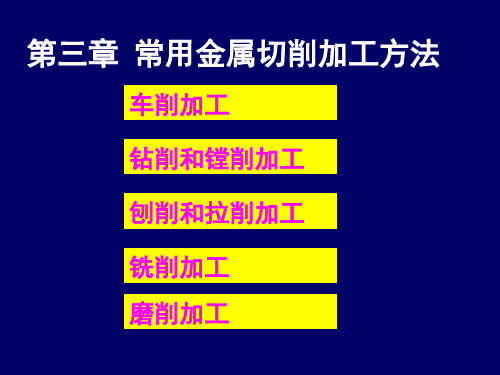
孔中键槽及多边形孔等,有时也用于加
工成形内外表面
二、拉 削
指在拉床上用拉刀进行加工的方法, 拉削可以认为是刨削的进一步发展。
它是利用多齿的拉刀,逐齿依次从工件 上切下很薄的金属层,使表面达到较高 的精度和较小的粗糙度值。
拉削时,一般由拉刀作低速直线运动, 被加工表面在一次走刀中形成
第三章 常用金属切削加工方法
车削加工 钻削和镗削加工 刨削和拉削加工 铣削加工 磨削加工
概述
机械零件种类繁多,但其形状都是由一些基本表面 组合而成。零件的最终成形,实际上是由一种表面 形式向另一种表面的转化,包括不同表面的转化、 不同尺寸的转化及不同精度的转化。转化过程的实 现,主要依靠运动。不同切削运动(主运动和进给 运动)的组合便形成了不同的切削加工方法。常用 的切削加工方法有车削、钻削、镗削、刨削、铣削、 磨削等,对某一表面的加工可采用多种方法,只有 了解了各种加工方法的特点和应用范围,才能合理 选择加工方法,进而确定最佳加工方案
在实际生产中,钻_扩_铰是较精密孔的典型加工工艺
三、镗孔
在镗床上完成孔加工的过程,叫镗孔。
工件安装在工作台上,工作台可作横向和纵向进给, 并能旋转任意角度。镗刀装在主轴或转盘的径向刀 架上,通过主轴箱可使主轴获得旋转主运动、轴向 进给运动,主轴箱还可沿立柱导轨上下移动。
镗削加工所用的刀具
单刃镗刀 浮动镗刀(V=0.08~0.13m/s)
3)减小背吃刀量,增加进给次数,以降低切削力。 (2)偏心工件的车削 偏心工件主要包括偏心轴和偏心套。如图3-8 (3)曲轴的车削 如图3-9
(二)车端面及台阶
(三)孔加工 (四)车槽及切断 (五)圆锥面的车削 常用圆锥面车削的方法有: 宽刀法,小刀架转位法,偏移尾座法和靠模法。
机械制造基础_1.3_机械加工方法

机械与汽车工程学院
1. 车削加工
按工件类型选用车削加工方法: 3) L/D≥20,细长零件 为防止弯曲变形,用中心架或跟刀架作辅助支承。 4) 尺寸较大或形状较复杂工件 采用四爪单动卡盘或花盘装夹工件。 四爪单动卡盘夹紧力较大,但定位精度低,安装 时须反复校正,对于不对称工件需校平衡,且不能高 速,适于单件生产。
机械与汽车工程学院
2. 铣削加工
铣削方式 铣刀 转向 切削过程 切削厚度由大 变小至零,刀 齿易切入工件。 刀具耐用度高, 表面质量高。 切削厚度由零 变大,刀齿不 易切入工件, 产生挤压、滑 移,已加工面 产生冷硬层。 工件受力情况 垂直分力 铣削水平分力 向下,工 与进给同向, 作台和导 丝杠螺母副有 轨紧贴, 间隙,引起工 铣削平稳。 作台窜动,进 给不均匀。 垂直分力 水平分力与进 向上,工 给方向相反, 作台上抬, 丝杠与螺母紧 与导轨有 贴。无窜动。 间隙,引 起振动。
半精车 半精车
精车 精车
磨削 精细车
1. 车削加工 按工件类型选用车削加工方法 1) 长径比L/D≤5,盘类或短而组的轴类零件 三爪自定心卡盘夹持工件,自定心,装夹方便迅 速,可自动化。 2) 5<L/D<20,较长轴类零件 工件两端先钻中心孔;前、后顶尖定位、支承; 采用拨盘和鸡心夹头带动工件转动并承受切削力矩。 适于多工序加工,工件可反复调头,易保证定位 精度,但顶尖刚性差,不适于粗加工。粗加工或半精 加工时,采用“一夹一顶”的方法。
机械与汽车工程学院
1. 车削加工
车削的工艺特点
1. 易于保证各加工面的位置精度:如同轴度、垂直度;
2. 切削过程平稳:连续切削,切削面积不变,切削力变 化小,生产率较高; 3. 适应范围广;适于单件小批生产; 4. 适合有色零件的精加工。 钢铁:粗车 有色金属:粗车 5. 刀具较简单。
4-3钻削、铰削、与镗削与拉削

因此可以看出,钻头的刚性和导向作用差, 因此可以看出,钻头的刚性和导向作用差,切削 时钻头容易弯曲,钻头横刃定心不准, 时钻头容易弯曲,钻头横刃定心不准,钻头开始切入 时仅由横刃进行切削容易造成引偏, 时仅由横刃进行切削容易造成引偏,使孔的轴线容易 偏斜。在钻床上钻孔时,容易产生这种缺陷。 偏斜。在钻床上钻孔时,容易产生这种缺陷。
二、钻削的工艺特点
(1)孔的轴线容易偏斜 所谓偏斜是指加工时由于钻 孔的轴线容易偏斜 头弯曲而引起的孔轴线歪斜。 头弯曲而引起的孔轴线歪斜。 麻花钻受加工孔的限制,其直径较小而长度较长, 麻花钻受加工孔的限制,其直径较小而长度较长, 刚性较差。两条较深的螺旋槽又使钻心变细, 刚性较差。两条较深的螺旋槽又使钻心变细,进一步 削弱了钻头的刚度。为了减少钻头与孔壁之间的摩擦, 削弱了钻头的刚度。为了减少钻头与孔壁之间的摩擦, 钻头的两条导向棱边加工得很窄, 钻头的两条导向棱边加工得很窄,因而其导向作用较 钻头横刃具有很大的负前角, 差。钻头横刃具有很大的负前角,钻削时横刃处发生 严重的挤压从而产生了很大的轴向力,稍有偏斜, 严重的挤压从而产生了很大的轴向力,稍有偏斜,就 会产生较大的附加力矩,使钻头弯曲。 会产生较大的附加力矩,使钻头弯曲。
根据用途和结构的不同,钻床可分为立式钻床、 根据用途和结构的不同,钻床可分为立式钻床、 台式钻床、摇臂钻床、深孔钻床以及中心孔钻床等。 台式钻床、摇臂钻床、深孔钻床以及中心孔钻床等。
2.摇臂钻床 摇臂钻床 摇臂钻床是一种摇臂可绕立柱回转和升降, 摇臂钻床是一种摇臂可绕立柱回转和升降,主轴 箱又可在摇臂上作水平移动的钻床。 箱又可在摇臂上作水平移动的钻床。 摇臂钻床外形图。工件固定在底座1的工作台 的工作台8上 摇臂钻床外形图。工件固定在底座 的工作台 上, 主轴7的旋转和轴向进给运动是由电动机通过主轴箱 的旋转和轴向进给运动是由电动机通过主轴箱6 主轴 的旋转和轴向进给运动是由电动机通过主轴箱 来实现的。主轴箱可在摇臂的导轨上移动, 来实现的。主轴箱可在摇臂的导轨上移动,摇臂借助 电动机及丝杠4的传动 可沿立柱3上下移动 立柱3 的传动, 上下移动。 电动机及丝杠4的传动,可沿立柱3上下移动。立柱3 由内立柱和外立柱组成, 由内立柱和外立柱组成,外立柱可绕内立柱在 ±180°范围内回转。 °范围内回转。 由此主轴很容易地被调整到所需的加工位置上, 由此主轴很容易地被调整到所需的加工位置上, 这就为在单件、小批生产中, 这就为在单件、小批生产中,加工大而重的工件上的 孔带来了很大的方便。 孔带来了很大的方便。
常用机械加工方法
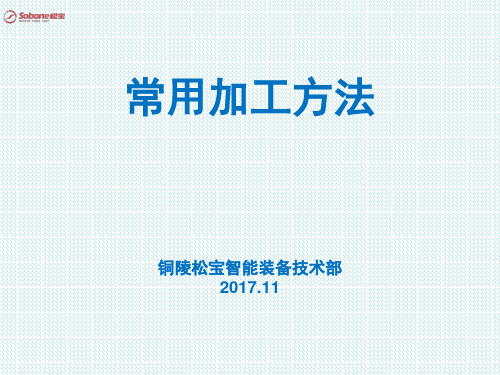
磨削的应用:
1.外圆的磨削:一般在普通外圆磨床或万能外圆磨床上进行,外圆磨削 有纵、横、综合、深磨法等 。
2.孔的磨削:可以在内圆 磨床上进行,也可以在 万能外圆磨床上进行, 它可以加工圆柱孔、圆 锥孔和成形内圆面等。
3.平面的磨削: 周磨——利用砂轮的外圆面进行磨削。端磨——利用砂轮的端面进行磨削。
常用加工方法
铜陵松宝智能装备技术部 2017.11
零件加工方法多种多样,根据被加工零 件的具体情况和要求,在选择加工方法是也 不尽相同。按是否去除材料分为无切削加工 与切削加工,按是否自动化分数控自动加工 与非自动加工,按是否放电分为放电加工与 机械加工。 其中常用的普通切削加工有:车、钻、 镗、刨、拉、铣和磨等,包含数控机械加工, 数控加工是运用CAM计算机控制程序进行自动 化加工。 无切削加工有冲压、钣金、铸造、锻造 等。放电加工有:线切割(分快丝、中丝、 慢丝)、穿孔机、电火花(电脉冲)等。
单刃镗刀在镗铣床上镗孔的方法
粗镗 半精镗 精镗
IT12-IT11 IT10-IT9 IT8-IT7
Ra 25-12.5μm Ra 6.3-3.2μm Ra 1.6-0.8μm
车床上镗孔:工件旋转、镗刀进给,如图下图所示:
在镗床上镗孔:镗刀刀杆随主轴一起旋转,完成主运动;进给运动可由 工作台带动工件纵向移动,也可由主轴带动镗刀杆轴向移动完成, 如下 图。
《机械制造技术基础》第五章钻、镗、刨、插、拉削加工的知识

2.粗精加工一起完成,影响了工件的加工质量;
3.排屑困难,易产生阻塞,导致刀齿损坏。
§5-1 钻削与孔加工刀具 孔加工复合刀具种类较多,按工艺类型分有: 1.同类工艺复合刀具
2.不同类工艺复合刀具
§5-1 钻削与孔加工刀具 二、麻花钻的构造与主要几何参数
是常见的孔加工刀具。一般用于实体材料上的粗 加工。钻孔的尺寸精度为IT11--IT12,Ra为5012.5μm。加工范围为0.1--80mm,以φ30mm以下时最
(3)通常只能单刀加工,不能用多刀同时切削。 所以与铣加工比较,牛头刨床的生产率比较低。 牛头刨床主要用于单件、小批量生产或修理车间。
二、龙门刨床
主要用来加工大平 面,尤其是长而窄的 平面,也可加工沟槽 或同时加工几个中小 型零件的平面。生产
率不如铣削高,主要
用于中小批生产及修 理车间。
§5-4 刨床、插床及其加工范围 三、单臂刨床
§5-1 钻削与孔加工刀具
1.从实体材料上加工出孔的刀具 用于加工精度要求不高,或为精度要求较高的 孔作预加工。 (1)扁钻 (2)中心钻 中心钻用来加工各种轴类工件的中心孔。
§5-1 钻削与孔加工刀具
3、麻花钻
是常见的孔加工刀具。一般用于实体材料上的粗 加工。钻孔的尺寸精度为IT11--IT13,Ra为5012.5μm。加工范围为0.1--80mm,以φ30mm以下时最 常用。
适用于加工宽度较大,而又不需要在整个宽度上加工的零件。
四、插床
插床的生产效率较低,通常只用于单件、小批量生产中插削槽、 平面及成型表面等。
§5-4 刨床、插床及其加工范围
插刀上下运动为主运动,工件 可作纵横两个方向的移动,
工作台还可作分度运动。加工 与安装面垂直的面、沟槽
常用的切削加工方法

常用的切削加工方法
常用的切削加工方法包括:
1. 铣削:使用铣床和铣刀将工件表面上的材料切削掉,形成所需的轮廓和表面质量。
2. 钻削:使用钻床和钻头在工件上进行钻孔加工,形成所需的孔径和孔深。
3. 车削:使用车床和车刀将工件固定在主轴上,通过旋转工件进行切削。
4. 磨削:使用磨床和磨料进行工件表面的修整和加工,以获得更高的精度和光洁度。
5. 刨削:使用刨床和刨刀将工件表面的材料切削掉,用于修整大型平面和表面。
6. 镗削:使用镗床和刀具将工件上的孔加工成所需的精度和尺寸。
7. 拉削:使用拉床和刀具对工件进行拉伸或拉压加工,以改变其形状和尺寸。
8. 搓削:使用搓床和滚轮对工件进行搓削加工,以形成齿轮、花键等零件。
9. 锯削:使用锯床和锯片对工件进行切割和分离,常用于金属材料和木材的加
工。
10. 焊削:使用焊接设备对工件进行切割和加工,常用于金属材料的切割和焊接。
以上方法仅为常见的切削加工方法,实际的切削加工方法还会根据具体的工件材料、形状和尺寸等要求进行选择和组合使用。
切削的基本类型
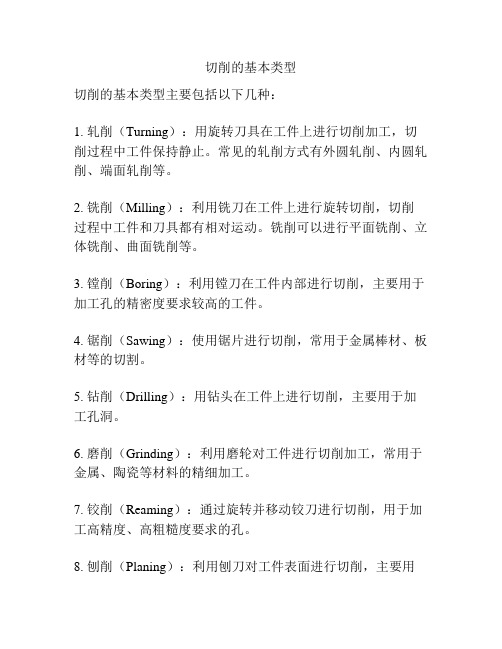
切削的基本类型
切削的基本类型主要包括以下几种:
1. 轧削(Turning):用旋转刀具在工件上进行切削加工,切削过程中工件保持静止。
常见的轧削方式有外圆轧削、内圆轧削、端面轧削等。
2. 铣削(Milling):利用铣刀在工件上进行旋转切削,切削过程中工件和刀具都有相对运动。
铣削可以进行平面铣削、立体铣削、曲面铣削等。
3. 镗削(Boring):利用镗刀在工件内部进行切削,主要用于加工孔的精密度要求较高的工件。
4. 锯削(Sawing):使用锯片进行切削,常用于金属棒材、板材等的切割。
5. 钻削(Drilling):用钻头在工件上进行切削,主要用于加工孔洞。
6. 磨削(Grinding):利用磨轮对工件进行切削加工,常用于金属、陶瓷等材料的精细加工。
7. 铰削(Reaming):通过旋转并移动铰刀进行切削,用于加工高精度、高粗糙度要求的孔。
8. 刨削(Planing):利用刨刀对工件表面进行切削,主要用
于平面的加工。
9. 拉削(Broaching):利用拉刀对工件进行切削,适用于加工孔洞的内轮廓形状。
10. 推削(Pushing):利用推刀对工件进行切削,常用于加工板材、管材等。
这些切削基本类型可以结合使用,互相补充,在不同工件和加工要求下选择合适的切削方法。
钻孔、铰孔、镗孔、拉孔的区别

与外圆表面加工相比,孔加工的条件要差得多,加工孔要比加工外圆困难。
这是因为:1)孔加工所用刀具的尺寸受被加工孔尺寸的限制,刚性差,容易产生弯曲变形和振动;2)用定尺寸刀具加工孔时,孔加工的尺寸往往直接取决于刀具的相应尺寸,刀具的制造误差和磨损将直接影响孔的加工精度;3)加工孔时,切削区在工件内部,排屑及散热条件差,加工精度和表面质量都不易控制。
一、钻孔与扩孔1. 钻孔钻孔是在实心材料上加工孔的第一道工序,钻孔直径一般小于80mm 。
钻孔加工有两种方式:一种是钻头旋转;另一种是工件旋转。
上述两种钻孔方式产生的误差是不相同的,在钻头旋转的钻孔方式中,由于切削刃不对称和钻头刚性不足而使钻头引偏时,被加工孔的中心线会发生偏斜或不直,但孔径基本不变;而在工件旋转的钻孔方式中则相反,钻头引偏会引起孔径变化,而孔中心线仍然是直的。
常用的钻孔刀具有:麻花钻、中心钻、深孔钻等,其中最常用的是麻花钻,其直径规格为Φ0.1 -80mm。
由于构造上的限制,钻头的弯曲刚度和扭转刚度均较低,加之定心性不好,钻孔加工的精度较低,一般只能达到IT13~IT11;表面粗糙度也较大,Ra 一般为50~12.5μm;但钻孔的金属切除率大,切削效率高。
钻孔主要用于加工质量要求不高的孔,例如螺栓孔、螺纹底孔、油孔等。
对于加工精度和表面质量要求较高的孔,则应在后续加工中通过扩孔、铰孔、镗孔或磨孔来达到。
2. 扩孔扩孔是用扩孔钻对已经钻出、铸出或锻出的孔作进一步加工,以扩大孔径并提高孔的加工质量,扩孔加工既可以作为精加工孔前的预加工,也可以作为要求不高的孔的最终加工。
扩孔钻与麻花钻相似,但刀齿数较多,没有横刃。
与钻孔相比,扩孔具有下列特点:(1)扩孔钻齿数多(3~8个齿)、导向性好,切削比较稳定;(2)扩孔钻没有横刃,切削条件好;(3)加工余量较小,容屑槽可以做得浅些,钻芯可以做得粗些,刀体强度和刚性较好。
扩孔加工的精度一般为IT11~IT10 级,表面粗糙度Ra为12.5 ~6.3μm。
七种常用金属加工方法
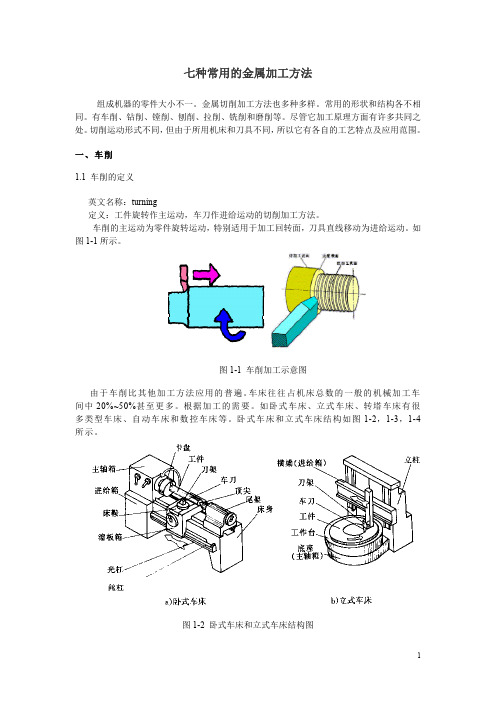
七种常用的金属加工方法组成机器的零件大小不一。
金属切削加工方法也多种多样。
常用的形状和结构各不相同。
有车削、钻削、镗削、刨削、拉削、铣削和磨削等。
尽管它加工原理方面有许多共同之处。
切削运动形式不同,但由于所用机床和刀具不同,所以它有各自的工艺特点及应用范围。
一、 车削1.1 车削的定义英文名称:turning定义:工件旋转作主运动,车刀作进给运动的切削加工方法。
车削的主运动为零件旋转运动,特别适用于加工回转面,刀具直线移动为进给运动。
如图1-1所示。
图1-1 车削加工示意图由于车削比其他加工方法应用的普遍。
车床往往占机床总数的一般的机械加工车间中20%~50%甚至更多。
根据加工的需要。
如卧式车床、立式车床、转塔车床有很多类型车床、自动车床和数控车床等。
卧式车床和立式车床结构如图1-2,1-3,1-4所示。
图1-2 卧式车床和立式车床结构图图1-3 转塔车床示意图图1-4 转塔刀架结构图1.2 车削的工艺特点:1. 易于保证零件各加工面的位置精度零件各表面具有相同的回转轴线(车床主轴的回转轴线)——一次装夹中加工车削时,同一零件的外圆、内孔、端平面、沟槽等。
能保证各外圆轴线之间及外圆与内孔轴线间的同轴度要求。
2. 生产率较高一般情况下车削过程是连续进行的,不易产生冲击,切削力基本上不发生变化。
并且当车刀几何形状、吃刀量和进给量次走刀过程中刀齿多次切入和切出一定时,切削过程可采用高速切削和强切削层(公称横截面积)是不变的切削力变化很小。
车削加工既适于单件小批量生产,生产效率高,也适宜大批量生产。
3. 生产成本较低车刀是刀具中最简单的一种,故刀具费用低,制造、刃磨和安装均较方便。
车床附件多,加之切削生产率高,装夹及调整时间较短,故车削成本较低。
4. 适于车削加工的材料广泛可以车削黑色金属(铁、锰、铬)、有色金属,非金(除难以切削的30HRC(洛氏硬度)以上高硬度的淬火钢件外),塑性材料(有机玻璃、橡胶等),特别适合于有色金属零件的精加工。
- 1、下载文档前请自行甄别文档内容的完整性,平台不提供额外的编辑、内容补充、找答案等附加服务。
- 2、"仅部分预览"的文档,不可在线预览部分如存在完整性等问题,可反馈申请退款(可完整预览的文档不适用该条件!)。
- 3、如文档侵犯您的权益,请联系客服反馈,我们会尽快为您处理(人工客服工作时间:9:00-18:30)。
22
2)麻花钻的几何参数 ) 坐标平面: 坐标平面:
基面 切削平面
23
(1)前角、主偏角 )前角、
24
(2)螺旋角和顶角 )
2Φ=118º
25
(三)钻削的特点
钻削要素
切削速度
进给量
钻削深度
26
钻削力和扭矩
主切削力Fz 主切削力 径向切削力Fy 径向切削力 轴向切削力F 轴向切削力 x
总扭矩M 总扭矩 总切削力F 总切削力
8
扩孔钻
整体式
套式
9
锪钻
10
铰刀
加工精密的圆柱孔和锥孔, 加工精密的圆柱孔和锥孔,加工孔径范围一般 为3~100毫米 ~ 毫米 铰削过程:切削、刮削、挤压、 铰削过程:切削、刮削、挤压、熨平和摩擦 铰孔的尺寸和几何形状精度直接由铰刀决定。 铰孔的尺寸和几何形状精度直接由铰刀决定。
11
12
整体式 套装式
5
扁钻
整体式
装配式
6
麻花钻
螺旋状排屑槽
7
直径: 直径:0.5mm~75mm ~
深孔钻
深孔:孔的深径之比大于 ~ 。 深孔:孔的深径之比大于5~10。 深孔加工特点: 深孔加工特点: 切削热不易传散; ① 切削热不易传散; 排除切屑的通道狭窄; ② 排除切屑的通道狭窄; 钻杆细长,刚度差。 ③ 钻杆细长,刚度差。
机械制造( )(基础) )(基础 机械制造(1)(基础)
《机械制造技术基础》 机械制造技术基础》 第五章 钻、镗、刨、插、 拉削加工
1
内容提要
1. 钻削与孔加工刀具 2. 钻床及其加工范围 3. 镗床及其加工范围 4. 刨床、插床及其加工范围 刨床、 5. 拉床及其加工范围 6. 孔加工技术的发展
锥度绞刀
可调整式
13
丝锥
14
镗刀
大直径孔、孔内环槽、 大直径孔、孔内环槽、孔系加工
单刃镗刀: 单刃镗刀:镗通孔和盲孔
15
浮动镗刀
16
复合刀具
17
同类工艺复合刀具
18
不同类工艺复合刀具
19
孔加工的解决方案
video
20
(二)麻花钻的构造与主要几何参数
1)麻花钻的构造 )
21
两条主切削刃 5个刀刃 个刀刃 两条副切削刃 一条横刃 两个螺旋形前刀面 6个刀面 个刀面 两个经刃磨获得的后刀面 两个圆弧段的副后刀面
32
2
1. 钻削与孔加工刀具
孔加工:孔的形成、 孔加工:孔的形成、扩大与修整
3
加工方法:钻孔、扩孔、锪孔、 加工方法:钻孔、扩孔、锪孔、铰孔和镗孔等
4
(一)孔加工刀具的种类
从实体材料上加工孔:扁钻、麻花钻、 从实体材料上加工孔:扁钻、麻花钻、深孔钻 对已有孔进行加工:扩孔钻、锪钻、铰刀、 对已有孔进行加工:扩孔钻、锪钻、铰刀、镗刀
27
轴向力与扭矩的比例
钻削功率: 钻削功率:Pm=2π· M · n
28
钻头的磨损及耐用度
磨钝标准: 磨钝标准: 塑性材料:VB 塑性材料: 脆性材料: 脆性材料:∆
29
钻削用量的选择
1、根据被加工孔直径选择切削深度 、 2、根据系统强度和刚度选择较大的进给量 、 3、选择钻削速度 、
30
钻削的工艺特点
(1)易引偏 :孔径扩大或孔轴线偏移和不直 ) 横刃定心不准,钻头刚性和导向作用较差 横刃定心不准,
31
钻床: 钻床: 轴线偏移
车床: 车床: 孔径扩大
(2)排屑困难 ) 钻孔的切屑较宽, 钻孔的切屑较宽,在孔内 被迫卷成螺旋状, 被迫卷成螺旋状,流出时 与孔壁发生剧烈摩擦而刮 伤已加工表面
(3)切削温度高,刀具磨损快 )切削温度高, 切削时产生的切削热多, 切削时产生的切削热多,加之钻削为半封闭 切削,切屑不易排出,切削热不易传出, 切削,切屑不易排出,切削热不易传出,使 切削区温度很高。 切削区温度很高。