组件测试曲线异常分析
电池组件IV测试曲线的目的与评估
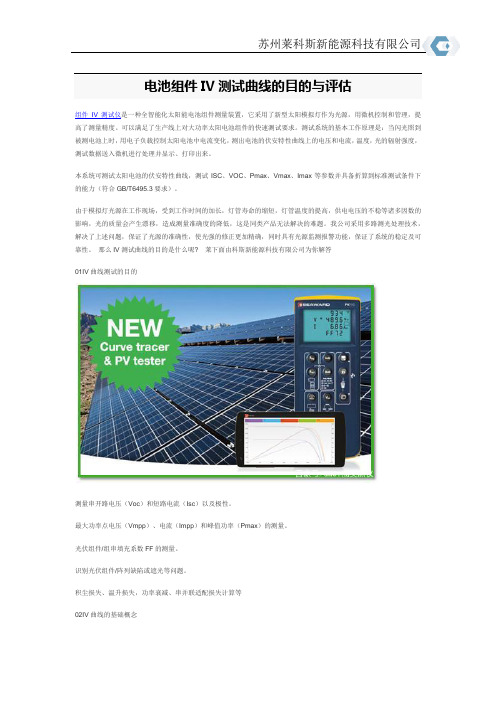
电池组件IV测试曲线的目的与评估组件IV测试仪是一种全智能化太阳能电池组件测量装置,它采用了新型太阳模拟灯作为光源,用微机控制和管理,提高了测量精度。
可以满足了生产线上对大功率太阳电池组件的快速测试要求。
测试系统的基本工作原理是:当闪光照到被测电池上时,用电子负载控制太阳电池中电流变化,测出电池的伏安特性曲线上的电压和电流,温度,光的辐射强度,测试数据送入微机进行处理并显示、打印出来。
本系统可测试太阳电池的伏安特性曲线,测试ISC、VOC、Pmax、Vmax、Imax等参数并具备折算到标准测试条件下的能力(符合GB/T6495.3要求)。
由于模拟灯光源在工作现场,受到工作时间的加长,灯管寿命的缩短,灯管温度的提高,供电电压的不稳等诸多因数的影响,光的质量会产生漂移,造成测量准确度的降低,这是同类产品无法解决的难题。
我公司采用多路测光处理技术,解决了上述问题,保证了光源的准确性,使光强的修正更加精确,同时具有光源监测报警功能,保证了系统的稳定及可靠性。
那么IV测试曲线的目的是什么呢? 莱下面由科斯新能源科技有限公司为你解答01IV曲线测试的目的测量串开路电压(Voc)和短路电流(Isc)以及极性。
最大功率点电压(Vmpp)、电流(Impp)和峰值功率(Pmax)的测量。
光伏组件/组串填充系数FF的测量。
识别光伏组件/阵列缺陷或遮光等问题。
积尘损失、温升损失,功率衰减、串并联适配损失计算等02IV曲线的基础概念Voc 开路电压Isc 短路电流Vmpp最大功率点电压Impp最大功率点电流Pmax峰值功率填充因子FF是太阳能电池品质的量度,定义为实际的最大输出功率除以理想目标的输出功率(IscVoc),FF越大,太阳能电池的质量越高。
FF的典型值通常处于60~85%,并由太阳能电池的材料和器件结构决定。
03影响IV曲线的因素辐照度越大,短路电流越大,辐照度对于开路电压影响不大温度越高,开路电压越小,温度对短路电流影响不大温度一定的情况下,辐照度越高,组件输出功率越大04组件的IV曲线分析STC状态下的组件电参数请点击输入图IV曲线测试仪测试的数值转换到STC条件下的值和厂家出厂的datasheet值进行对比才有意义05IV曲线测试步骤请点击输入图片确保待测组串和逆变器断开被测试组串应该隔离并连接到I-V曲线测试设备。
组件知识考试题目-A
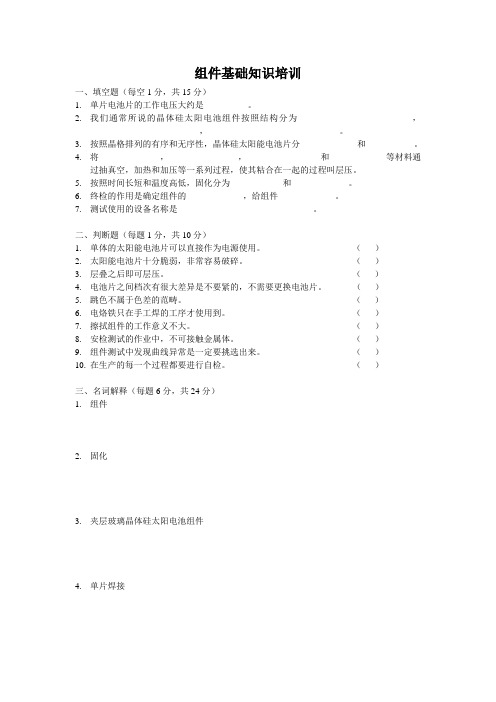
组件基础知识培训一、填空题(每空1分,共15分)1.单片电池片的工作电压大约是__________。
2.我们通常所说的晶体硅太阳电池组件按照结构分为__________________________,_________________________,______________________________。
3.按照晶格排列的有序和无序性,晶体硅太阳能电池片分_____________和___________。
4.将______________,________________,_________________和_____________等材料通过抽真空,加热和加压等一系列过程,使其粘合在一起的过程叫层压。
5.按照时间长短和温度高低,固化分为____________和_____________。
6.终检的作用是确定组件的_____________,给组件_____________。
7.测试使用的设备名称是_______________________________。
二、判断题(每题1分,共10分)1.单体的太阳能电池片可以直接作为电源使用。
()2.太阳能电池片十分脆弱,非常容易破碎。
()3.层叠之后即可层压。
()4.电池片之间档次有很大差异是不要紧的,不需要更换电池片。
()5.跳色不属于色差的范畴。
()6.电烙铁只在手工焊的工序才使用到。
()7.擦拭组件的工作意义不大。
()8.安检测试的作业中,不可接触金属体。
()9.组件测试中发现曲线异常是一定要挑选出来。
()10.在生产的每一个过程都要进行自检。
()三、名词解释(每题6分,共24分)1.组件2.固化3.夹层玻璃晶体硅太阳电池组件4.单片焊接四、简答题(共51分)1.简述组件生产的工艺过程。
(11分)2.简述层压的注意事项。
(10分)3.简述安检的内容。
(10分)4.简述装框的作用。
(10分)5.列举不低于5种太阳能应用实例(10分)。
测试缺陷分析
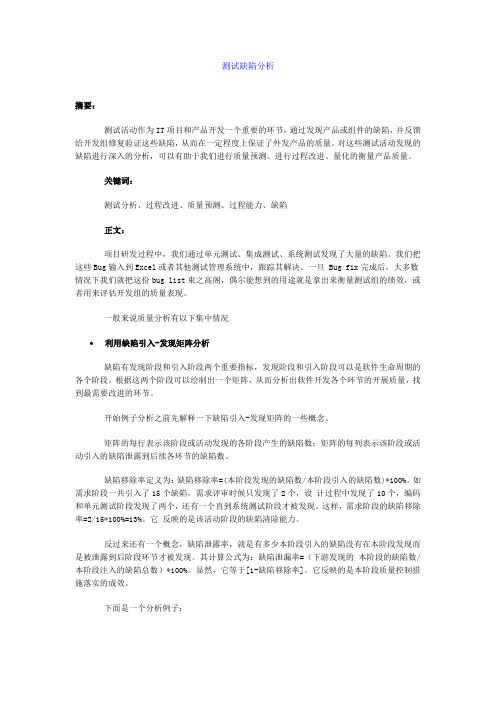
测试缺陷分析摘要:测试活动作为IT项目和产品开发一个重要的环节,通过发现产品或组件的缺陷,并反馈给开发组修复验证这些缺陷,从而在一定程度上保证了外发产品的质量。
对这些测试活动发现的缺陷进行深入的分析,可以有助于我们进行质量预测、进行过程改进、量化的衡量产品质量。
关键词:测试分析、过程改进、质量预测、过程能力、缺陷正文:项目研发过程中,我们通过单元测试、集成测试、系统测试发现了大量的缺陷。
我们把这些Bug输入到Excel或者其他测试管理系统中,跟踪其解决。
一旦 Bug fix完成后,大多数情况下我们就把这份bug list束之高阁,偶尔能想到的用途就是拿出来衡量测试组的绩效,或者用来评估开发组的质量表现。
一般来说质量分析有以下集中情况•利用缺陷引入-发现矩阵分析缺陷有发现阶段和引入阶段两个重要指标,发现阶段和引入阶段可以是软件生命周期的各个阶段,根据这两个阶段可以绘制出一个矩阵,从而分析出软件开发各个环节的开展质量,找到最需要改进的环节。
开始例子分析之前先解释一下缺陷引入-发现矩阵的一些概念。
矩阵的每行表示该阶段或活动发现的各阶段产生的缺陷数;矩阵的每列表示该阶段或活动引入的缺陷泄露到后续各环节的缺陷数。
缺陷移除率定义为:缺陷移除率=(本阶段发现的缺陷数/本阶段引入的缺陷数)*100%。
如需求阶段一共引入了15个缺陷,需求评审时候只发现了2个,设计过程中发现了10个,编码和单元测试阶段发现了两个,还有一个直到系统测试阶段才被发现。
这样,需求阶段的缺陷移除率=2/15*100%=13%。
它反映的是该活动阶段的缺陷清除能力。
反过来还有一个概念,缺陷泄露率,就是有多少本阶段引入的缺陷没有在本阶段发现而是被泄露到后阶段环节才被发现。
其计算公式为:缺陷泄漏率=(下游发现的本阶段的缺陷数/本阶段注入的缺陷总数)*100%。
显然,它等于[1-缺陷移除率]。
它反映的是本阶段质量控制措施落实的成效。
下面是一个分析例子:从上表可以看到,编码过程的缺陷大部分依赖系统测试发现。
太阳能光伏组件IV测试特性曲线分析
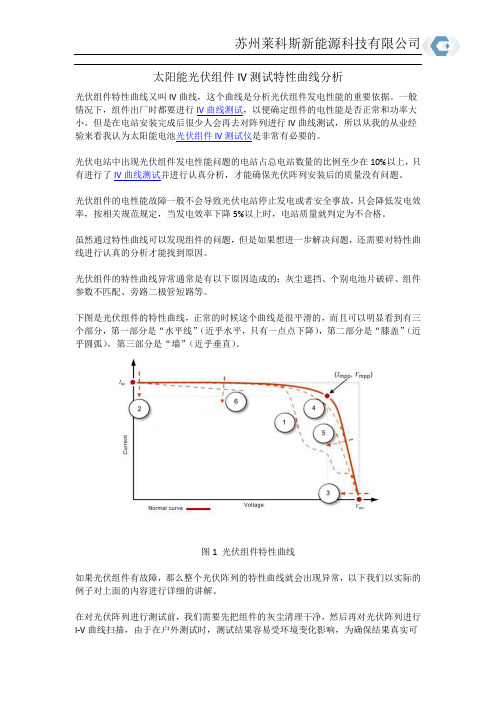
太阳能光伏组件IV测试特性曲线分析光伏组件特性曲线又叫IV曲线,这个曲线是分析光伏组件发电性能的重要依据。
一般情况下,组件出厂时都要进行IV曲线测试,以便确定组件的电性能是否正常和功率大小。
但是在电站安装完成后很少人会再去对阵列进行IV曲线测试,所以从我的从业经验来看我认为太阳能电池光伏组件IV测试仪是非常有必要的。
光伏电站中出现光伏组件发电性能问题的电站占总电站数量的比例至少在10%以上,只有进行了IV曲线测试并进行认真分析,才能确保光伏阵列安装后的质量没有问题。
光伏组件的电性能故障一般不会导致光伏电站停止发电或者安全事故,只会降低发电效率,按相关规范规定,当发电效率下降5%以上时,电站质量就判定为不合格。
虽然通过特性曲线可以发现组件的问题,但是如果想进一步解决问题,还需要对特性曲线进行认真的分析才能找到原因。
光伏组件的特性曲线异常通常是有以下原因造成的:灰尘遮挡、个别电池片破碎、组件参数不匹配、旁路二极管短路等。
下图是光伏组件的特性曲线,正常的时候这个曲线是很平滑的,而且可以明显看到有三个部分,第一部分是“水平线”(近乎水平,只有一点点下降),第二部分是“膝盖”(近乎圆弧),第三部分是“墙”(近乎垂直)。
图1 光伏组件特性曲线如果光伏组件有故障,那么整个光伏阵列的特性曲线就会出现异常,以下我们以实际的例子对上面的内容进行详细的讲解。
在对光伏阵列进行测试前,我们需要先把组件的灰尘清理干净,然后再对光伏阵列进行I-V曲线扫描,由于在户外测试时,测试结果容易受环境变化影响,为确保结果真实可靠,我们对同一个光伏阵列要测试三次以上。
现在市场上有很多仪器可以对光伏阵列的I-V特性曲线进行现场测试,本文提供的光伏曲线案例全部是通过意大利HT公司生产的I-V400测试仪得到的。
01 - 多膝盖“多膝盖”,从这个曲线可以知道光伏阵列中有个别组件的旁路二极管已经短路,原因可能是以下:光伏组件被阴影遮挡、部分电池片损坏、组件旁路二极管损坏、个别组件的功率偏低;图2 第1种异常情况案例02 - 短路电流偏小短路电流偏小,原因可能是组件功率衰减,也可能是测试时操作不当(比如,辐照度计放置倾角不正确,测试时太阳光强变化过快造成的;图3 第2种异常情况案例03 - 开路电压过低开路电压过低,原因可能是以下:PID效应、部分光伏组件被完全遮挡、旁路二极管损坏等,还有可能是测试时操作不当(比如:温度测量不准确)造成的;图4 第3种异常情况案例04 - 膝盖变形“膝盖变形”,表现为开路电压和短路电流都正常,但是填充因子偏低,造成这种情况的原因可能是组件老化,也可能是第5和第6种异常同时发生造成的。
光伏组件失效分析
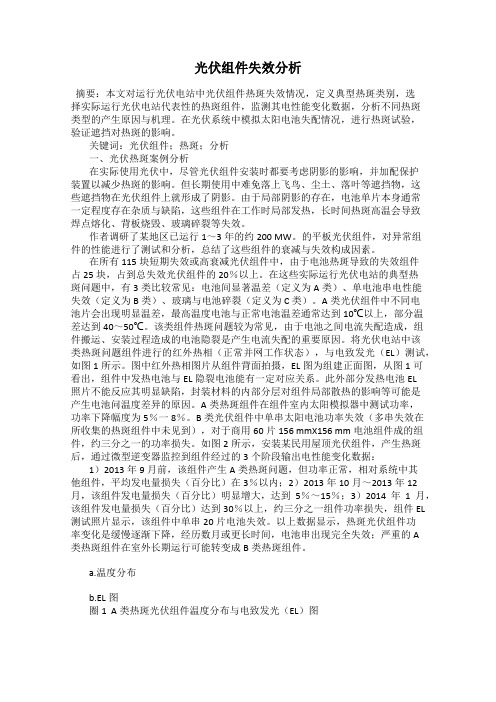
光伏组件失效分析摘要:本文对运行光伏电站中光伏组件热斑失效情况,定义典型热斑类别,选择实际运行光伏电站代表性的热斑组件,监测其电性能变化数据,分析不同热斑类型的产生原因与机理。
在光伏系统中模拟太阳电池失配情况,进行热斑试验,验证遮挡对热斑的影响。
关键词:光伏组件;热斑;分析一、光伏热斑案例分析在实际使用光伏中,尽管光伏组件安装时都要考虑阴影的影响,并加配保护装置以减少热斑的影响。
但长期使用中难免落上飞鸟、尘土、落叶等遮挡物,这些遮挡物在光伏组件上就形成了阴影。
由于局部阴影的存在,电池单片本身通常一定程度存在杂质与缺陷,这些组件在工作时局部发热,长时间热斑高温会导致焊点熔化、背板烧毁、玻璃碎裂等失效。
作者调研了某地区已运行1~3年的约200 MW。
的平板光伏组件,对异常组件的性能进行了测试和分析,总结了这些组件的衰减与失效构成因素。
在所有115块短期失效或高衰减光伏组件中,由于电池热斑导致的失效组件占25块,占到总失效光伏组件的20%以上。
在这些实际运行光伏电站的典型热斑问题中,有3类比较常见:电池间显著温差(定义为A类)、单电池串电性能失效(定义为B类)、玻璃与电池碎裂(定义为C类)。
A类光伏组件中不同电池片会出现明显温差,最高温度电池与正常电池温差通常达到10℃以上,部分温差达到40~50℃。
该类组件热斑问题较为常见,由于电池之间电流失配造成,组件搬运、安装过程造成的电池隐裂是产生电流失配的重要原因。
将光伏电站中该类热斑问题组件进行的红外热相(正常并网工作状态),与电致发光(EL)测试,如图1所示。
图中红外热相图片从组件背面拍摄,EL图为组建正面图,从图1可看出,组件中发热电池与EL隐裂电池能有一定对应关系。
此外部分发热电池EL照片不能反应其明显缺陷,封装材料的内部分层对组件局部散热的影响等可能是产生电池问温度差异的原因。
A类热斑组件在组件室内太阳模拟器中测试功率,功率下降幅度为5%一8%。
B类光伏组件中单串太阳电池功率失效(多串失效在所收集的热斑组件中未见到),对于商用60片156 mmX156 mm电池组件成的组件,约三分之一的功率损失。
组件常见质量问题分析
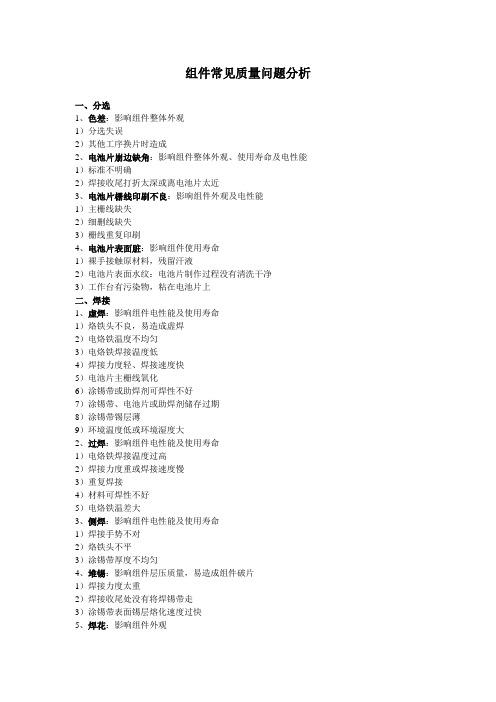
组件常见质量问题分析一、分选1、色差:影响组件整体外观1)分选失误2)其他工序换片时造成2、电池片崩边缺角:影响组件整体外观、使用寿命及电性能1)标准不明确2)焊接收尾打折太深或离电池片太近3、电池片栅线印刷不良:影响组件外观及电性能1)主栅线缺失2)细删线缺失3)栅线重复印刷4、电池片表面脏:影响组件使用寿命1)裸手接触原材料,残留汗液2)电池片表面水纹:电池片制作过程没有清洗干净3)工作台有污染物,粘在电池片上二、焊接1、虚焊:影响组件电性能及使用寿命1)烙铁头不良,易造成虚焊2)电烙铁温度不均匀3)电烙铁焊接温度低4)焊接力度轻、焊接速度快5)电池片主栅线氧化6)涂锡带或助焊剂可焊性不好7)涂锡带、电池片或助焊剂储存过期8)涂锡带锡层薄9)环境温度低或环境湿度大2、过焊:影响组件电性能及使用寿命1)电烙铁焊接温度过高2)焊接力度重或焊接速度慢3)重复焊接4)材料可焊性不好5)电烙铁温差大3、侧焊:影响组件电性能及使用寿命1)焊接手势不对2)烙铁头不平3)涂锡带厚度不均匀4、堆锡:影响组件层压质量,易造成组件破片1)焊接力度太重2)焊接收尾处没有将焊锡带走3)涂锡带表面锡层熔化速度过快5、焊花:影响组件外观1)串焊力度太重2)串焊时烙铁温度过高3)串焊模版槽深不够6、焊接偏移:影响组件外观、电性能及使用寿命1)互联条太软2)互联条扭曲变形3)焊接手势不对4)互联条出现蛇形弯曲5)互联条出现镰刀弯曲7、脱焊:影响组件电性能及使用寿命1)焊接手势太轻或速度太快2)烙铁焊接温度太低3)没有浸泡助焊剂4)电池片或涂锡带可焊性不够8、焊接后电池片翘曲1)电池片拉应力不够2)互联条收缩率大3)电池片热胀冷缩变化大9、焊接破片:影响组件外观、电性能及使用寿命1)电池片自身隐裂2)互联条太硬3)焊接手势太重4)电烙铁温度过高5)堆锡6)电池片焊好后积压过多7)焊接收尾处打折太深或离电池片太近10、电池片氧化:影响组件外观、使用寿命及电性能1)裸露空气中时间过长2)加助焊剂焊接后没有清洗,导致氧化3)电池片来料时间太长,保存条件不符合要求4)空气中湿度大三、层压1、异物:影响组件整体外观、电性能及使用寿命1)生产现场控制不当、工作台面不整洁2)员工在车间整理头发3)工作时必须戴工作帽、穿工作服4)工作的责任心不够5)戴围巾进入操作场所6)人员随便进出车间2、EV A未溶:影响组件外观、电性能及使用寿命1)EV A自身问题交联剂过高2)层压机问题温度不均衡3)EV A熔点过高4)EV A融化速度慢3、真空泡或缺失:影响组件外观、电性能及使用寿命1)EV A自身厚度不均匀2)EV A自身拌料不均匀3)层压时间长、上室压力大4)部分EV A不适合国内层压机5)EV A收缩率大6)层压机温度不均匀或过高4、层压后组件内气泡:影响组件外观及使用寿命1)人员操作失误:工艺参数没有调整准确;自动与手动操作失误;没有及时层压;没有走空循环等2)橡胶毯有裂痕或破损3)不抽真空4)层压机密封圈破损5)不层压导致或层压压力小6)真空速率达不到7)真空泵卡死导致电机烧坏8)层压时间结束不开盖9)真空管路漏气10)真空阀门故障11)EV A保管不善受潮12)EV A过保质期13)EV A融点过高14)绝缘层的结构问题(不是所有背材都能做绝缘条)15)EV A上沾有酒精未完全挥发16)EV A熔化速度过快17)电池片上残留助焊剂和EV A起反映18)工艺参数不符(抽真空时间短、层压温度高、层压时间长)19)焊接工艺问题(虚焊、侧焊、脱焊)导致20)玻璃和EV A边缘收到污染21)异物导致22)停电导致5、层压后破片:影响组件外观、电性能及使用寿命1)电池片自身隐裂:叠层在灯光下仔细检查2)焊接时打折过重导致电池片隐裂:调整焊接方法3)层压前,操作人员抬组件时压倒电池片,进料时不注意4)异物、锡渣、堆锡在电池片上导致层压后破片5)上室压力过大经常出现破片而且在同一位置6)互联条太硬7)叠层人员剪涂锡带时用力过大,电池片产生隐裂8)充气速度或抽真空速度不合适9)叠层人员在倒电池串时产生碰撞,导致电池片隐裂10)引出线打折压破6、EV A交联度不符合要求:影响组件使用寿命1)机器温度过高或太低2)层压时间过长或短3)机器温度不均衡4)EV A自身交联剂质量问题5)EV A储存不当,受光或受热6)EV A过期7、EV A脱层:影响组件使用寿命1)玻璃内部不干净2)EV A受潮或过期或表面有脏污3)层压时间过短或没有层压4)EV A自身内部配方不完善8、EV A发黄:透光率下降,影响组件采光,影响电性能及使用寿命1)EV A自身问题:配方不完善2)EV A与背材之间的搭配性不协调3)EV A与玻璃之间的搭配性不协调4)EV A与硅胶之间的搭配性不协调5)EV A与电池片之间搭配性不协调6)EV A与涂锡带之间搭配性不协调7)EV A受潮氧化9、层压后组件位移:影响组件外观、电性能及使用寿命1)串与串之间位移:没有固定好、EV A收缩率大2)汇流条位移:层压抽真空造成、互联条太软、汇流条太长没有固定好3)整体位移:没有固定或层压放置组件时有倾斜10、焊带发黄发黑:影响组件整体外观、电性能及组件使用寿命1)助焊剂的腐蚀性强或焊带自身抗腐蚀性不强2)EV A的配方体系与焊带不符3)焊带表面镀层的致密程度不够11、背板划伤:影响组件外观及使用寿命1)层压后抬放、修边、装框、测试、清洗及包装都有可能2)装框拆框导致3)背板本身存在划伤12、背板褶皱:影响组件外观1)不层压导致2)EV A收缩率大3)背板自身自量软13、背板鼓包:影响组件外观1)大量鼓包出现在片与片之间,可能是EV A收缩率大:检查每批次EV A2)互联条质地软:更换合适的互联条14、背板脱层:影响组件使用寿命1)背板的毛面部分粘结效果不好:更换背板2)上室压力小调整参数3)不层压导致:检查设备4)EV A的粘结强度不够:调整参数或更换EV A5)组件太热时修边或用手拉角:冷却到室温再修边,在租价安热的时候,禁止用手拉组件的角15、背板凹坑:影响组件外观、电性能及使用寿命1)EV A粘在橡胶毯上:检查橡胶毯,及时清理2)高温布没有清理干净:仔细清理高温布(正反面及大布的正反面)3)上室粘有其他硬物:检查清理16、背板鼓包:影响组件外观及使用寿命1)电池片背膜引起2)3M胶带引起3)返工次数太多或时间长4)层压之后在电池片背面有气泡,经过一段时间后生产5)层压温度过高或层压时间太长17、背板自身脱层:影响组件外观及使用寿命1)背板自身的粘结强度不够;更换背板2)背板耐热不够18、玻璃表面划伤:影响组件外观、使用寿命及安全性能1)抬玻璃时两块玻璃摩擦2)叠层时摩擦3)刀片划伤4)装框拆框时导致5)测试后汇流条打折导致摩擦6)层压返工时摩擦尽量减少7)玻璃本身有划伤没有检出19、玻璃内部划伤:影响组件外观及电性能1)层压返工时刀片划伤2)抬玻璃时两片玻璃摩擦3)玻璃自身存在划伤(包括内部)20、玻璃自爆:1)玻璃自身热应力不够2)玻璃自身内部有杂质颗粒3)玻璃钢化程度不够4)加热板不平5)加热板上有硬物6)堆放不规范7)组件放置数量过多四、测试1、测不出功率1)组件整体正负极接反:仔细检查、责任心、细心2)没有夹好:将夹子夹好3)二极管全部装反2、功率低1)破片或隐裂2)个别电池串正负极接反3)组件被流转单或其他物体遮挡住4)标准件没有校准好5)组件温度高6)氙灯光源不够7)二极管个别装反8)组件内部有虚焊或过焊现象9)组件内部有低电流或低电压的电池片10)电池片串联电阻大,内部有缺陷11)电池片自身短路12)电池片初始光致衰减13)晶体致密程度不够及内在杂质多;3、IV曲线异常1)破片2)电池片中高低档电流混用3)电流电压修正参数不符4)设备出现故障5)电池片中高低档电压混用6)二极管压降问题五、装框1、型材问题:影响组件外观及使用寿命1)型材划伤:来料检查不仔细,装框清洗包装过程中划伤2)型材拼接有出入:在加工时尺寸没有控制好,产生误差3)型材变形:型材加工过程中没有拉直,型材的硬度不够2、型材与组件接缝处漏缝:影响组件外观及使用寿命1)上表面有缝:没有将硅胶溢出,或没有压实型材内部硅胶充足;2)反面有缝:补胶没有补好或硅胶与背板之间粘结性不好;检验硅胶与背板之间的粘结性3、接线盒问题:影响组件电性能及使用寿命1)密封圈脱落:水汽易从盒盖渗入,造成组件短路2)盒盖脚断掉:安装不牢,易被拉掉水汽易渗入3)接线盒没有盖紧:安装不牢,易脱落,水汽易渗入4)连接插头没有插接到位5)安装螺丝没有拧紧6)正负极接反4、硅胶问题1)硅胶固化后发黄2)硅胶固化后与背板不粘结3)硅胶固化后与接线盒不粘结4)在使用中。
光伏组件iv曲线测试要求(一)
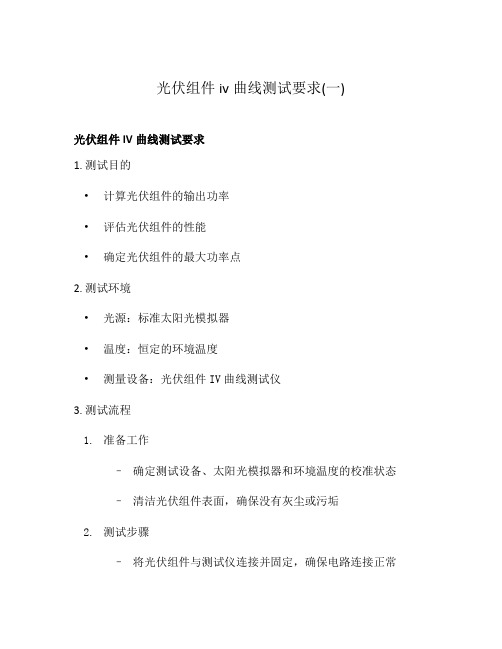
光伏组件iv曲线测试要求(一)光伏组件IV曲线测试要求1. 测试目的•计算光伏组件的输出功率•评估光伏组件的性能•确定光伏组件的最大功率点2. 测试环境•光源:标准太阳光模拟器•温度:恒定的环境温度•测量设备:光伏组件IV曲线测试仪3. 测试流程1.准备工作–确定测试设备、太阳光模拟器和环境温度的校准状态–清洁光伏组件表面,确保没有灰尘或污垢2.测试步骤–将光伏组件与测试仪连接并固定,确保电路连接正常–设置光源输出功率为标准数值–测量光伏组件开路电压和短路电流,记录数据–逐步增加光源输出功率,测量每个功率点下的电流和电压,并记录数据–直到达到光伏组件的最大功率点–逐步减小光源输出功率,同样测量每个功率点下的电流和电压,并记录数据3.数据处理–根据测量得到的电流和电压数据绘制IV曲线图–通过IV曲线图确定光伏组件的最大功率点–计算光伏组件的输出功率4. 举例说明假设我们要测试一块光伏组件,测试结果如下:•开路电压: V•短路电流: A下表为不同光源输出功率下的电流和电压数据:光源输出功率 (W) | 电流 (A) | 电压 (V) ||||| | 0 | 0 | 0 | | 100 | | | | 200 | | | | 300 | | | | 400 | | | | 500 | | | | 600 | | |根据上表的数据绘制IV曲线图后可以发现,光伏组件的最大功率点约在光源输出功率为400W时,电流为,电压为。
通过计算,光伏组件的输出功率为。
根据测试结果,评估光伏组件的性能是否符合要求,进一步验证其在实际应用中的可行性和效率。
以上就是光伏组件IV曲线测试要求的相关要求和举例说明。
通过正确的测试方法和数据处理,可以准确评估光伏组件的性能,为光伏发电系统的设计和优化提供重要参考。
组件效率衰减曲线

组件效率衰减曲线
组件效率衰减曲线是指随着时间的推移,组件的效率逐渐下降的曲线。
在一些电子设备中,如太阳能电池板、发动机等,随着使用时间的增加,组件的性能会受到各种因素的影响,逐渐降低。
通常,组件效率衰减曲线呈现出一个先快后慢的趋势,即初始时期效率下降较快,随着时间的推移,效率下降的速度逐渐减慢。
这是因为在组件使用过程中,一些因素会导致组件性能下降,如材料老化、磨损、电子元件寿命等,但随着时间的推移,这些因素对组件性能的影响逐渐减弱。
具体的衰减曲线形状和速度取决于组件的特性、制造工艺以及使用环境等因素。
因此,不同组件的效率衰减曲线可能存在差异。
对于太阳能电池板来说,效率衰减曲线通常以年份为横轴,效率衰减为纵轴。
根据多项研究和实测数据,太阳能电池板的效率在开始使用后的几年内可能会快速下降,然后逐渐稳定或缓慢下降。
为了延长组件的使用寿命和维持其性能,通常需要定期对组件进行维护和保养。
例如,太阳能电池板需要定期清洗,以去除积尘和污垢,以保持最佳的光吸收效果。
此外,定期检查和更换老化或故障的电子元件也是关键措施。
总之,组件效率衰减曲线对于评估和预测组件性能的变化趋势具有重要意义,对于各种电子设备的维护和优化具有指导作用。
光伏组件故障排查方法

光伏组件故障排查方法光伏组件是太阳能发电系统中的关键部件,其正常运行对于发电效率和系统稳定性至关重要。
然而,由于各种原因,光伏组件可能会出现故障,导致发电量下降甚至无法正常发电。
为了准确、快速地排查光伏组件故障,以下介绍一些常见的排查方法。
1. 可视检查进行一次全面的可视检查,目的是发现是否存在物理损坏、污染、松动等问题。
检查时应注意以下几点:- 是否有明显的裂纹或破损,特别是玻璃表面;- 是否有灰尘、污垢严重影响光吸收;- 是否有电缆接头松动、腐蚀等情况。
2. 温度检测光伏组件的温度异常可能是故障的表现之一。
使用红外热像仪或温度计可以对光伏组件表面的温度进行检测。
若某个组件温度异常明显高于周围组件,可能存在组件失效或局部阻塞的情况。
需要注意的是,温度异常也可能是系统设计或环境因素导致的,因此需要综合考虑。
3. 电压检测通过检测光伏组件的电压情况,可以判断是否存在电池片损坏或连接问题。
可以使用多用电表或专用的光伏电压检测仪进行测量。
需要注意的是,测量时要确保系统处于正常工作状态,并注意电压的稳定性和一致性。
4. 电流检测电流是光伏组件正常发电的关键指标之一。
通过检测光伏组件的电流情况,可以判断是否存在电池片损坏、接线问题或阻塞情况。
可以使用多用电表或专用的光伏电流检测仪进行测量。
需要注意的是,测量时要确保系统处于正常工作状态,并注意电流的稳定性和一致性。
5. IV曲线测试IV曲线测试是一种全面评估光伏组件性能的方法,可以检测出多种故障情况。
通过在不同光照强度和电压下测量光伏组件的电流,可以绘制出IV曲线。
对比理论曲线和实际曲线的差异,可以判断是否存在电池片损坏、接线问题、阴影覆盖等故障。
IV曲线测试需要使用专用的测试设备,操作时需要保持光照稳定和电压控制准确。
6. 隔离诊断若以上排查方法无法准确定位故障,可以通过隔离诊断的方法逐步排查。
将光伏组件逐个隔离,分别测试其电压和电流,以确定具体是哪个组件引起了故障。
光伏组件问题系列总结——电池片串联电阻与并联电阻
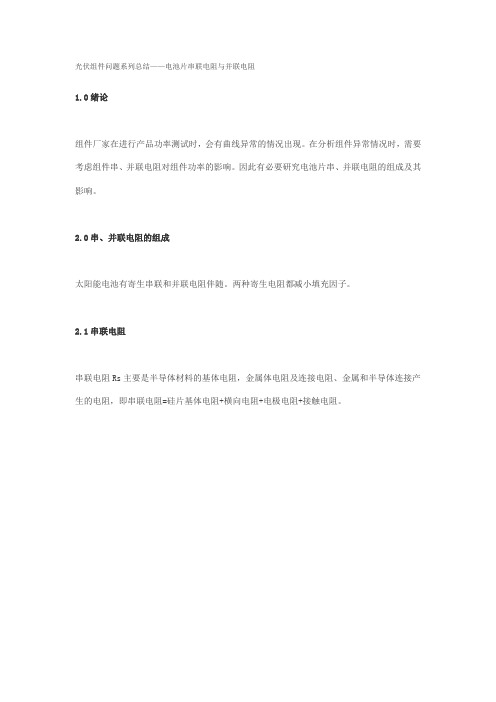
光伏组件问题系列总结——电池片串联电阻与并联电阻1.0绪论组件厂家在进行产品功率测试时,会有曲线异常的情况出现。
在分析组件异常情况时,需要考虑组件串、并联电阻对组件功率的影响。
因此有必要研究电池片串、并联电阻的组成及其影响。
2.0串、并联电阻的组成太阳能电池有寄生串联和并联电阻伴随。
两种寄生电阻都减小填充因子。
2.1串联电阻串联电阻Rs主要是半导体材料的基体电阻,金属体电阻及连接电阻、金属和半导体连接产生的电阻,即串联电阻=硅片基体电阻+横向电阻+电极电阻+接触电阻。
图1串联电阻组成示意图基体电阻由硅片的品质决定。
扩散方块电阻可以调节,但又伴随着结深的变化。
栅线电阻主要靠丝网印刷参数决定,重要的是栅线的清晰度和高宽比(越大越好)。
当然,若单纯的减少串联电阻,栅线可以很宽,但高度较低,这样会增大遮光面积。
接触电阻主要看电极印刷效果、烧结的效果等。
2.2并联电阻并联电阻Rsh主要由于p-n结不理想或在结附近有杂质,这些都能导致结短路,尤其是在电池边缘处。
并联电阻反映的是电池的漏电水平。
漏电流理论上可以归结到并联电阻上。
并联电阻影响太阳电池开路电压,Rsh减小会使开路电压降低,但对短路电流基本没有影响。
并联电阻过小可能由一下原因引起:边缘漏电(刻蚀未完全、印刷漏浆)。
基体内杂质和微观缺陷。
PN结局部短路(扩散结过浅、制绒角锥体颗粒过大)。
3.0 串、并联电阻的影响3.1 串联电阻对填充因子的影响因为填充因子决定着电池输出功率,因此最大输出功率受串联电阻影响,可以近似表示为:如果太阳能电池内阻定义为:串联电阻Rs 影响短路电流,Rs 增大会使短路电流降低,而对开路电压没有影响。
串联电阻的影响如图2。
图2:串联电阻对填充因子的影响3.2 并联电阻对填充因子的影响类似的并联电阻,可以定义为:并联电阻对填充因子的影响如图3.12 所示。
图3 太阳能电池中并联电阻对填充因子的影响在串联和并联电阻都存在情况下,太阳能电池IV 曲线可以用下式表示:(作者微信公众账号:光伏经验网)。
测试图形与测试参数讲解
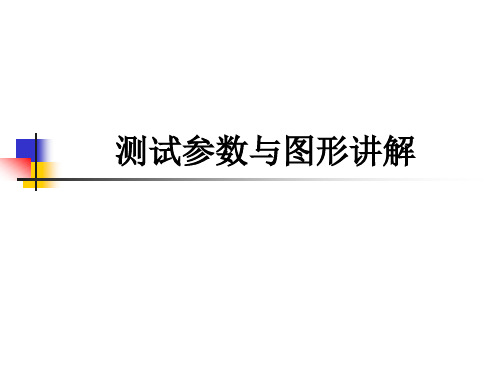
Isc:短路电流,在某种特定温度和幅照度条件下,光伏发电器
在短路状态下的输出电流.
Pm:最大功率,在电流-电压特性曲线上的电流和电压乘
积为最大的点所表示的功率。
Vmp:最大功率点的电压(即工作电压),对应于最大功
1、根据pn结整流的方程.在正向偏置下,通过结的正向电 流为:
IF=Is[exp(qV/KT)-1]
V是光生电压,Is是反向饱和电流.q为电子电量,K是波耳兹曼常 数.T为温度. 太阳能电池与负载接成通路,通过负载的电流是:
I=IF-IL= Is[exp(qV/KT)-1]-IL Is[exp(qV/KT)-1]2、开路电压 开路电压Voc: 开路电压 : 在pn结开路的情况下(R=∞),此时pn结两端的电压即为开路 电压Voc。这时,I=0,即IF=IL,将I=0带入光电池的电压电流方 程: I=IF-IL= Is[exp(qV/KT)-1]-IL,得开路电压为: s[exp(qV/KT)-1]ln( / s+1) Voc=KT/q ln(IL/Is+1)
组件测试参数分解
SerialNu mber Uoc 33.391 29 Isc 8.279 23 9 Pmpp Umpp Impp FF Rs Rsh
D70241
206.47 26.401 7.8206 74.686 0.5064 326.56 39 27 04 4 118 47
Voc:开路电压,在某特定的温度和幅照度条件下,光伏发电器
3.89-3.95
3.83-3.89 7.37-7.60 8.17 0.508 0.610
7.46-7.69 8.23
光伏组件故障分析报告

光伏组件故障分析报告1 引言1.1 光伏组件概述光伏组件,又称太阳能电池板,是光伏发电系统中的核心部件,其作用是将太阳光能转化为电能。
光伏组件主要由硅电池片、玻璃、EVA胶膜、背板、边框等部分组成。
在过去的几十年里,随着光伏技术的不断发展和成熟,光伏组件的转换效率得到了显著提高,成本也在逐渐降低,光伏发电已成为全球新能源的重要组成部分。
我国光伏产业经过多年的发展,已形成了从硅料生产、电池片制造、组件组装到系统集成的完整产业链。
然而,在光伏组件的长期运行过程中,各种故障问题也逐渐凸显出来,对光伏发电系统的稳定性和发电效率产生了影响。
1.2 故障分析的目的和意义对光伏组件进行故障分析,旨在找出故障产生的原因,为故障诊断、防范和维护提供依据。
故障分析的目的和意义如下:1.提高光伏发电系统的稳定性和可靠性,降低故障率。
2.延长光伏组件的使用寿命,降低运维成本。
3.提高光伏发电效率,增加发电收益。
4.为光伏组件的设计、制造和安装提供改进方向。
通过对光伏组件故障的深入分析,有助于推动我国光伏产业的健康发展,提高光伏发电在能源结构中的比重,为实现能源转型和可持续发展贡献力量。
2 光伏组件故障类型及原因2.1 故障类型光伏组件的故障类型多样,主要包括以下几种:1.电池片损坏:电池片是光伏组件的核心部分,其损坏主要包括隐裂、破片、电极脱落等。
2.电路问题:如接线盒内部接线松动、接触不良,或电缆老化导致电阻增大等。
3.封装材料老化:长期受紫外线、温度变化等影响,EVA胶膜、背板等材料会出现老化、变色、龟裂等现象。
4.热斑效应:由于电池片自身或外部阴影导致局部温度升高,影响组件性能。
5.PID效应(潜在诱导性降解):由于组件长期在湿度较大环境下工作,导致电池片出现性能下降。
2.2 故障原因光伏组件故障的原因可以分为以下几类:1.内在因素:–电池片质量:电池片在生产过程中可能存在微裂纹、掺杂不均等问题。
–组件设计:设计不合理,如电池片间距过小,可能导致热膨胀时电池片相互挤压。
光伏组件iv曲线测试要求

光伏组件iv曲线测试要求光伏组件IV曲线测试是评估光伏组件性能的重要手段之一。
通过测试,可以准确了解组件在不同光照和温度条件下的电流-电压特性,从而判断其发电能力和稳定性。
下面将详细介绍光伏组件IV曲线测试的要求和步骤。
首先,进行IV曲线测试需要专业的测试设备和合适的环境条件。
测试设备应具备高精度的测量功能,并能够记录和分析测试数据。
测试环境应保持稳定,避免外界光照和温度的干扰。
测试设备和环境应按照相关标准进行校准和认证,以保证测试结果的准确性和可靠性。
接下来,进行IV曲线测试的步骤包括样品准备、测试前的校准、测试参数设置和测试数据记录与分析。
首先,样品准备要求选择正常的光伏组件,并确保其表面干净、无损伤和灰尘。
其次,测试前的校准包括对测试设备进行校准以及记录和核对测试设备的参数。
然后,设置测试参数时应根据实际情况选择合适的光照和温度条件,并确保参数设置准确和一致。
最后,进行IV曲线测试时要按指定的顺序和程序进行,同时准确记录测试数据,并进行统计和分析,以评估组件的性能。
除了上述基本要求和步骤外,光伏组件IV曲线测试还需要注意以下几点。
首先,测试时应遵循安全操作规程,确保测试人员和设备的安全。
其次,测试周期和频率应根据具体需求进行设置,以确保测试的及时性和充分性。
同时,测试结果应进行多次重复测试,以提高测试结果的可靠性和准确性。
此外,测试结果还应与组件的性能指标进行比对,以判断组件的优劣和合格与否。
综上所述,光伏组件IV曲线测试是评估组件性能的重要手段,其要求和步骤不容忽视。
只有通过科学规范的测试,才能准确了解组件的发电能力和稳定性,为工程应用和产品选择提供有力的指导。
因此,在进行光伏组件IV曲线测试时,我们应严格按照要求操作,并将测试结果与实际需求进行比对和分析,以确保测试结果的准确性和可靠性。
太阳电池组件I-V曲线测试

f) 控制器通过显示器显示经过修正的电流和电压数据并将这些数据存储起来。这个测量过程就 完成了。
相 对 光 谱 能 量
图 1. 氙灯光源光谱分布与 AM1.5 太阳光的光谱分布比较 通常的太阳模拟器,根据光线方向分布的不同,还可以分为直射和散射。所谓的直射太阳模拟器, 是氙灯光线不经过反射从灯直接到达被测量组件;而散射太阳模拟器,是氙灯光线经过多次反射后到 达被测量的组件。两者有着重要的区别。因为我们无法得到完全白色的反射面,经过多次反射的光线, 其中的某些波长成分被反射物体吸收的比例远远大于其它的波长成分,例如短波部分,影响到太阳电 池的光谱响应。另外,对于散射太阳模拟器,射入被测量组件的光线与被测量组件表面法线间的夹角 增大,被测量组件表面形态的变化将影响到组件对光线的吸收。初步的实验也表明,散射光线的增加 有可能影响减少太阳电池组件曲线因子的大小。 4. 测量环境温度的影响 太阳电池的 I—V 特性与温度相关,所以,要达到太阳电池 25℃测试条件的要求,就必须保证环 境温度为 25℃,并且被测量组件需要长时间置放在恒温环境中以保证太阳电池的温度达到 25℃。生产 中使用的温度测量系统,准确度为±1℃。如果使用功率校准的方法,由此而产生的峰值功率测量系统 误差为:
还包括组件实际温度引入的误差;
对于闪光太阳模拟器,往往把光的不稳定性引入的测量误差归于偶然性误差;
上述的误差,实际属于两类,一类是属于系统误差或者是固定误差,另一类属于偶然性误差或者随机
iv曲线测试原理

iv曲线测试原理IV曲线测试原理。
IV曲线测试是太阳能电池组件性能测试的重要手段之一,通过对太阳能电池组件进行IV曲线测试,可以全面了解电池的性能参数,为电池的选型和性能评估提供重要依据。
IV曲线测试原理是基于太阳能电池的工作原理和电学特性,通过对电流-电压曲线的测量和分析,来评估太阳能电池的性能和质量。
在进行IV曲线测试时,首先需要准备好测试设备,包括光源、电源、测量仪器等。
然后将太阳能电池组件置于光源下,接入电路,通过电源对电池进行不同电压的施加,同时测量电流和电压的数值。
根据测量得到的电流-电压数据,绘制出IV曲线图,通过对IV曲线图的分析,可以得到太阳能电池的关键性能参数。
IV曲线图是以电流I为纵轴,电压V为横轴的曲线图,其形状和特征可以直观地反映出太阳能电池的性能。
在IV曲线图中,有一些重要的参数需要特别关注,包括开路电压Voc、短路电流Isc、最大功率点电压Vm、最大功率点电流Im、填充因子FF等。
这些参数可以通过IV曲线测试得到,对于评估太阳能电池的性能和质量具有重要意义。
在IV曲线测试原理中,开路电压Voc是指在太阳能电池输出端口未接负载时的电压值,它是太阳能电池的最大输出电压。
短路电流Isc是指在太阳能电池输出端口短接时的电流值,它是太阳能电池的最大输出电流。
最大功率点电压Vm和最大功率点电流Im分别是太阳能电池在最大功率输出时的电压和电流数值,它们决定了太阳能电池的最大输出功率。
填充因子FF是衡量太阳能电池性能优劣的重要参数,它是最大功率点时的电流和电压之积与开路电压和短路电流之积的比值,填充因子越接近于1,表示太阳能电池的性能越好。
通过对IV曲线测试原理的了解,可以更好地理解太阳能电池的工作原理和电学特性,为太阳能电池的选型和性能评估提供科学依据。
同时,IV曲线测试也是太阳能电池组件质量检测的重要手段,通过对IV曲线的分析,可以及时发现电池组件的质量问题,保障太阳能电池组件的性能和可靠性。
浅析光伏组件电性能测试的影响因素

浅析光伏组件电性能测试的影响因素发表时间:2019-10-18T10:39:33.927Z 来源:《电力设备》2019年第11期作者:伊纪禄袁明翰胡涛王金玉[导读] 摘要:目前,评价光伏组件的发电性能主要还是在试验室进行,因此试验室电性能测试是否准确至关重要。
(中国电子科技集团公司第十八研究所天津 300381)摘要:目前,评价光伏组件的发电性能主要还是在试验室进行,因此试验室电性能测试是否准确至关重要。
本文探寻了室内电性能测试的影响因素,将影响因素归纳为模拟器的状态、组件的状态、测试回路三方面,并对影响光伏组件电性能测试准确度的因素及其影响进行了分析,探究其影响原理,提出相应的解决方法。
关键词:光伏组件;性能测试;模拟器光伏行业经过几十年的蓬勃发展已经非常成熟,光伏组件的电性能作为其主要属性,一直被用来当做评价和交易的基础。
无论是组件生产商还是光伏投资者都希望获得一个准确的电性能数据。
因此,如何提高电性能测试的准确度对第三方检测机构来说至关重要。
对于室内电性能测试来说,可能影响其准确度的方面主要有:模拟器的状态;组件的状态;测试回路。
下面我们分别从以上三方面进行分析。
一、模拟器状态对测试结果的影响对于应用于阳光下的光伏组件来说,对其电性能能产生影响的光源方面的因素主要为光源的光谱辐照度分布和电池的光谱响应。
电池的光谱响应是指在各个波长上的单位辐照度所产生的电流与波长的关系曲线,该曲线与电池自身的工艺材料特性密切相关[1]。
为了反映光伏组件在阳光下的体现(通用标准为AM1.5大气条件),理论上进行电性能测试时,应选取与阳光的光谱辐照度分布与均匀性完全一致的模拟器且选取与被测光伏组件光谱响应完全一致的标准电池来标定辐照度[2]。
然而实际应用中,所用模拟器并不能还原太阳光的状态,模拟器的光谱以及模拟器不均匀度均与室外阳光存在差异,这两方面差异会导致电性能测试出现偏差。
下面我们分别对以上两方面产生的偏差进行分析。
用电结构变化对线损的影响及趋势分析

结 束 语 随着光伏 行业的快 速发展 , 应加 强控制光伏 产品的质量, 当太 阳能 电池组件 中出现 问题电池片, 应针对 问题 电池 片进行更换 并进行控制 分 析, 杜 绝不 合格产品流入下到工序, 提高产 品合格率 。
( >> 上接 第1 8 8 页)
电力企业的 生产经营效 率、 成本, 如何运用科 学合理 的改革用电结 构 , 以 减少输 电过程 中线路 损耗 , 是 每一个 电力企 业必须 面对的 问题 。 由于
过程 中质量 控制 , 可 以在将 电池 片焊接 成串, 在 进行敷设 之前对 电池 串 虚焊 。 在生 产过 程 中严格 检查 异物 。 层压 后 组件转 运 车改 为玻 璃垂直 进行测 试 , 最后在组件 装框之后 进行 的测试 并保存测试 数据 , 太阳电池 放 置 , 搬运 时尽量减少 玻璃 弯曲。 控 制现场 合 适的温 湿度 条件, 组 件不 组件 由于某些 原 因, 功率达 不到预 期 值 , 甚 至比预 期值 小许多 , 测试 曲 允许 >5 0  ̄ C时装框 。 线会 表现 的比较 差 , 为方便查 找其原 因, 对 曲线差 进行统 计归类 , 并通 目 前 曲线异常依然 存在, 很 多组 件都有 不同程度 的热斑 等问题 , 有 过工艺 经验找到 其对于的原 因进行分析。 些措施实 施起来 有些 难度 , 进 展还需 要时 间和相 关设备, 还 有措施 实施 的还不彻底 , 仍 然需要持 续改进 。
其 对于社会 、 企业和 个人 的用 电安全 影响越 来越 大 , 降低线损 既是满 足 企 业节约成 本 的需要 也Байду номын сангаас 科 学发展 关 的要求 。 相 信在 不久的 将来 用电 力线路改 造工作会越 来越完 善, 线 损在科技 不断进步 的情况下, 不断 得
pcr各种异常熔解曲线

PCR和熔解曲线过程中可能出现的一些异常情况包括:
1. 扩增曲线不光滑:这可能是由于PCR反应液有挂壁所致。
2. 扩增抑制:某些情况下,PCR反应可能受到抑制。
3. 扩增曲线断裂或下滑:这可能是由于基线选取范围不对,基线终点大于Ct值。
这通常是由于模板DNA浓度过高所致。
4. 无Ct值出现:这可能是由于模板降解、引物或探针降解、电脑设置了自动休眠等原因。
5. 斜直线型扩增曲线:这可能是由于ROX浓度或程序设置的问题。
建议将仪器上将参比染料设置由ROX改为NONE,取消ROX的校正功能,看扩增曲线是否恢复正常。
6. 扩增曲线末尾起跳:排除污染原因后复检样本,如果复检后曲线为阴性直线则说明之前的末尾起跳为非特异性扩增,如果复检后曲线仍与之前一致则说明末尾起跳表示该样本中待检病毒核酸的浓度偏低。
7. 山域型曲线:这可能是基因丰度低。
8. 无扩增曲线,有熔解曲线:这可能是扩增程序设置错误,未打开荧光采集通道。
只能重新进行实验。
9. 熔解曲线有双峰(左侧有小峰):这可能是引物二聚体导致的。
建议降低引物浓度、适当增加模板量、重新设计引物。
10. 熔解曲线有双峰(右侧有小峰):这可能是可能有基因组污染,可以通过RNA电泳查看是否有基因组污染;也可能是引物非特异性
扩增,可以通过blast检测引物特异性或者重新设计引物。
以上信息仅供参考,建议咨询专业人士获取准确信息。
光伏组件非线性模式功率量测方法研究

/2023.03光伏组件非线性模式功率量测方法研究陈为兴1 冯云峰2 张守才1 林 璋1 黄 征1(1.晶科能源(海宁)有限公司 2.陕西众森电能科技有限公司)摘 要:针对常规瞬态I V测试仪(脉冲时间一般为10~100ms)在高效率、高电容效应引出的瞬时测量误差,本文从电池结构和测试机理出发,分析产生量测偏差的原因。
按照IEC60904 2020中磁滞率≤05%,通过改变扫描速率找到适合的扫描速率,直到所有I V曲线参数在两次连续扫描之前为0 5%或更好。
另一种方法是将I V曲线用于正向和反向扫描,如果两次扫描的所有I V曲线参数一致性优于05%,则证明电容误差是可以接受的。
否则,在达成上述协议之前,应更改测量参数或程序。
根据正向反向扫描进行容性消除验证结果,选择60ms脉冲宽度与非线性高效扫描20ms脉宽方案进行结果验证对比,在获得该类型光伏组件精确量测的同时,可解决长脉冲带来的灯管损耗问题。
非线性高效测量20ms脉宽扫描方案具有以下优势:提出前置开路状态下得到组件真实Voc,Pmax核心区间设置更充分的延时,负载技术单次测试等效倍率约为线性倍率的30~40倍,可有效消除容性影响。
关键词:光伏组件;电容效应;非线性高效模式;量测研究0 引言在过去的30多年里,瞬态I V测试仪以其优异的辐照度均匀性、较短的测试时间、良好的温度稳定性,一直用于光伏组件的批量生产测试。
然而近年来,由于n型光伏组件应用日益广泛,特别是交叉背接触(IBC)光伏组件、带有本征薄膜层的异质结(HIT)光伏组件的出现,其大电容使光伏组件在现有的短脉冲(5~20ms)瞬态I V测试时对光强变化和外路电压变化的响应时间延长,造成测试结果偏离光伏组件的真实值。
太阳电池光电性能是衡量其性能优劣的关键指标,主要体现在伏安特性曲线(即I V曲线)上,参数包括短路电流、开路电压、最大功率、最佳工作电压、最佳工作电流、填充因子和转换效率等[1]。
光伏特性曲线实验报告
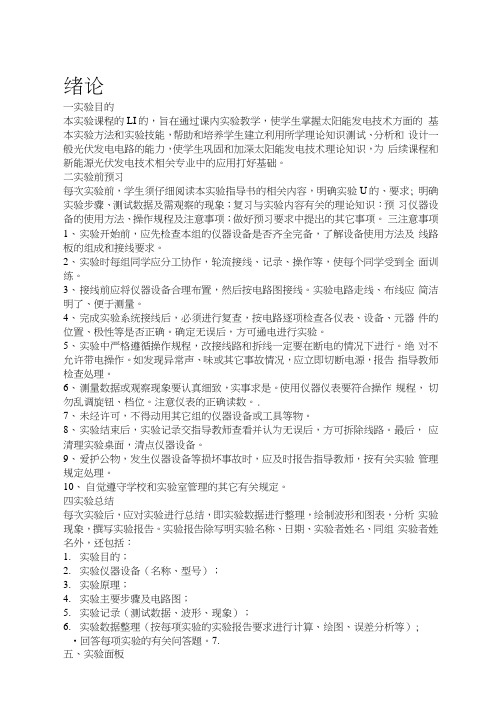
绪论一实验目的本实验课程的LI的,旨在通过课内实验教学,使学生掌握太阳能发电技术方面的基本实验方法和实验技能,帮助和培养学生建立利用所学理论知识测试、分析和设计一般光伏发电电路的能力,使学生巩固和加深太阳能发电技术理论知识,为后续课程和新能源光伏发电技术相关专业中的应用打好基础。
二实验前预习每次实验前,学生须仔细阅读本实验指导书的相关内容,明确实验U的、要求; 明确实验步骤、测试数据及需观察的现象;复习与实验内容有关的理论知识:预习仪器设备的使用方法、操作规程及注意事项;做好预习要求中提岀的其它事项。
三注意事项1、实验开始前,应先检查本组的仪器设备是否齐全完备,了解设备使用方法及线路板的组成和接线要求。
2、实验时每组同学应分工协作,轮流接线、记录、操作等,使每个同学受到全面训练。
3、接线前应将仪器设备合理布置,然后按电路图接线。
实验电路走线、布线应简洁明了、便于测量。
4、完成实验系统接线后,必须进行复查,按电路逐项检查各仪表、设备、元器件的位置、极性等是否正确。
确定无误后,方可通电进行实验。
5、实验中严格遵循操作规程,改接线路和拆线一定要在断电的情况下进行。
绝对不允许带电操作。
如发现异常声、味或其它事故情况,应立即切断电源,报告指导教师检查处理。
6、测量数据或观察现象要认真细致,实事求是。
使用仪器仪表要符合操作规程,切勿乱调旋钮、档位。
注意仪表的正确读数。
.7、未经许可,不得动用其它组的仪器设备或工具等物。
8、实验结束后,实验记录交指导教师查看并认为无误后,方可拆除线路。
最后,应清理实验桌面,清点仪器设备。
9、爱护公物,发生仪器设备等损坏事故时,应及时报告指导教师,按有关实验管理规定处理。
10、自觉遵守学校和实验室管理的其它有关规定。
四实验总结每次实验后,应对实验进行总结,即实验数据进行整理,绘制波形和图表,分析实验现象,撰写实验报告。
实验报告除写明实验名称、日期、实验者姓名、同组实验者姓名外,还包括:1.实验目的;2.实验仪器设备(名称、型号);3.实验原理;4.实验主要步骤及电路图;5.实验记录(测试数据、波形、现象);6.实验数据整理(按每项实验的实验报告要求进行计算、绘图、误差分析等); •回答每项实验的有关问答题。
- 1、下载文档前请自行甄别文档内容的完整性,平台不提供额外的编辑、内容补充、找答案等附加服务。
- 2、"仅部分预览"的文档,不可在线预览部分如存在完整性等问题,可反馈申请退款(可完整预览的文档不适用该条件!)。
- 3、如文档侵犯您的权益,请联系客服反馈,我们会尽快为您处理(人工客服工作时间:9:00-18:30)。
组件测试曲线异常分析
摘要: 太阳电池组件由于某些原因,功率达不到预期值,甚至比预期值小许多,测试曲线会表现的比较差。
为便于查找其原因,本文对差曲线进行统计归类,并通过工艺经验找到其对应原因。
如下图所示:曲线 1 处出 ... 太阳电池组件由于某些原因,功率达不到预期值,甚至比预期值小许多,测试曲线会表现的比较差。
为便于查找其原因,本文对差曲线进行统计归类,并通过工艺经验找到其对应原因。
如下图所示:
曲线 1 处出了问题,如1 处曲线有台阶,则是二极管的问题,基本对组件质量影响不大。
1 处有起伏,而非缓慢下降,则是电流分档问题,此组件中混有电流档偏低或偏高的电池片。
曲线 2 处出了问题,拐弯处略显直角,则是因为组件中有隐裂片,操作过程中产生。
如果是有两次或三次大转折,则是因为组件中有小裂片。
曲线 3 处出了问题,平滑下降中有拱起,则是因为电压分档不均。