QA检验记录报告
QA出货检验报告参考模板
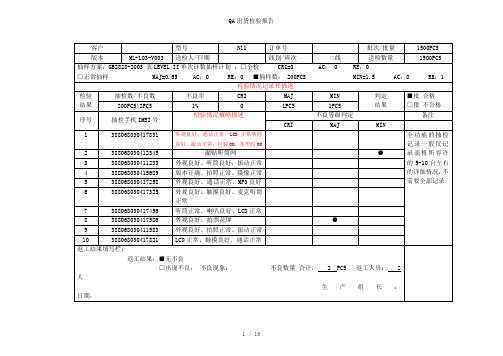
返工结果:■无不良
□出现不良: 不良现象: 不良数量 合计:2PCS 返工人员:2人
生产组长:日期:
OQC二次验收结果:
■合格 □不合格(再次返工) □让步接受(客户有特殊要求执行)
检验员:审核:QR-048-A/0
客户
型号
订单号
批次/批量
1900PCS
版本
ML-L03-V003
送检人/日期
2
388068030486465
漏贴听筒网
●
3
388068030434533
外观良好、听筒良好,振动正常
4
388068036795689
版本正确、拍照正常、摄像正常
5
388068030970258
外观良好、通话正常、MP3良好
6
38806803076625
外观良好、触摸良好、麦克听筒正常
7
388068030557756
□正常抽样 MAJ=0.65 AC:0 RE:0 ■抽样数: 200PCS MIN=1.5 AC:0 RE:1
检验情况记录和描述
检验
结果
抽检数/不良数
不良率
CRI
MAJ
MIN
判定
结果
■批 合格
□批 不合格
200PCS\2PCS
1%
0
1PCS
1PCS
序号
抽检手机IMEI号
检验情况概略描述
不良等级判定
备注
听筒正常、喇叭良好、LCD正常
8
388068030456786
外观良好、拍照花屏
●
9
388068030454883
外观良好、拍照正常、振动正常
QA检验流程

4.1.5.1、如果判定合格,检验员在产品包装盒上贴“QA PASS”标签并在《产品入库报验单》上“OK”区打“√”并签名。若让步接收,检验员在产品包装盒上贴“QA PASS”标签并在《产品入库报验单》上“特采”区打“√”并签名。QA检验员将《产品入库报验单》和检验完毕的产品实物交报验人,报验人入库。
4.1.2、QA检验员对报验产品数量进行确认后方可接收报验产品。
4.1.3、确认报验产品数量无误后,检验员根据相关订单要求检验产品尺寸及出货工单上相关参数及信息,产品尺寸测量记录填写在《QA检验记录表》中.工单检验完毕后,加盖“QA PASS”印章,然后根据对应的外观检验标准进行外观检验.
4.1.4、检验完毕QA检验员填写《QA检验报告》并做出判定后将《QA检验报告》提交QA组长审核,并给出处理意见,品保部经理批准。
4.1.5.2、如果判定不合格,检验员在《产品入库报验单》上“NG”区打“√”并签名。QA检验员将《产品入库报验单》和检验完毕的产品实物退回包装组。如果是一般不符合,包装组做出相应处理并记录结果。如不合格是严重不符,QA组长应填写《纠正和预防措施处理单》,并执行《改进控制程序》中相关内容。
4.2、报表
QA将每次检验的质量情况登记于《QA检验记录表》上,每天统计并在上午之前将前一天检验情况汇报至品质经理及品质文员处,填写《QA出货检验月报告》,交品质经理审核,总监批准。
QA工作流程
文件编号
QA-000
版本号
A0
生效日期
编制
审核
批准
4.3、QA工作流程图:
报验人填写《产品入库报验单》
退回包装组
QA对产品数量进行确认
QA对产品进行100%拆箱核对数量
CMMI QA检查单

验收检查单
1) 转产资料是否完整、正确 2)转产资料是否已顺利交接给供应链 3)是否有转产资料清单 4)转产评审记录检查
1)工程施工启动会议 2)工程施工计划 3)工程文件 4)勘测计划 5)工程勘测报告 7)施工方案 8)验货签收单 9)工程进度计划 10)工程问题记录表 11)工程初验报告 12)工程总结报告
配置管理检查单
2)质量检查结果是否有做记录 3)质量问题是否被处理并做记录,
质量保证检查单
41) )是 是否 否编 做制 度质 量量 计报 划告
2)度量数据收集记录
3)是否做度量分析,度量分析的问题是否做处 理
度量分析检查单
1)是否按决策时机启动决策分析过程
2)是否召开决策分析会议
3) 编制决策分析报告
1)风险识别是否合理 2)是否进行风险评估 3)是否进行风险缓解 4)是否进行风险监控
项目监督与控制检查单 变更管理检查单 风险管理检查单
关键管控点
1)项目需求规格书是否进行评审 2)需求规格书是否能够涵盖客户所需的所有要 求 3)需求规格书功能参数是否符合相关规范及要 求(参考用户要求、国军标等) 4)是否建立需求跟踪矩阵 1)项目总体方案及各分方案是否进行评审 2)总体方案编制是否按需求规格书中的要求 3)各分方案设计是否明确, 能够顺利执行 4)方案评审后需发布
1)变更申请 2)变更评估 3)变更通知 4)变更实施 5)变更验证 6)变更发布
1)项目风险跟踪表 2)项目风险管理报告
研发过程检查(依项目策划
调整)
项目研制阶段
建议检查频度
内容
需求
每节点、里程碑检查,至少一次
1)项目需求规格说明书 2)需求评审
方案设计
QA巡检记录

生 产 结 束 后 检 查
生产完成后生产现场及设备是否及时清洁,生产结束后剩余的物料、废弃物料以及生产用相关文件、记录等受按规定移除生产现场。
□是 □否
检查人/日期: 复合人/日期:
□是 □否
5.是否有与生产无关的人员。
□是 □否
生 产 过 程 检 查
1.生产区域的状态标识是否标明所生产产品的名称、规格、批号、日期等。
□是 □否
2.生产下现场是否整洁,物料、中间品是否码放整齐、标志是否清晰明显。
□是 □否
关 键 工 序 巡 查
巡检时间
巡检内容
□是 □否
□是 □否
□是 □否
□是 □否
工序
批号
检查日期
检查车间
检查
备注
生 产 前 检 查
1.检查生产车间是否有上批清场合格证,是否有与生产无关的器具、物料、设备、文件等。
□是 □否
2.生产环境是否满足生产工艺要求。
□是 □否
3.生产设备是否处于完好状态。
□是 □否
4.生产所使用的原辅料、包装材料,中间产品是否经检验,切名称、批号、数量应与批生产指令一致。
QA检验记录

序号
Hale Waihona Puke 品名/图番制造单位
QA 检验记录
检验日 期:
生产日/班 客户名称 送检数量 AQL值 Ac/Re 抽样数 不良数
判定 OK NG
NO:
处理建议
备注
说明:1、产品标准按《检查标准书》和客户要求的相关项目执行,抽样标准按本公司抽样计划执行;
2、若判定为不合格需返工、返修等处理的,需在返工、返修后按报检程序重新送检,直到合格为止,并在备注栏中注明重检结果;
3、此表一式三份,制造单位、仓库、质审量核部人各一/ 份;每日检验完成后及时提报质量部文确员认统计;
日期:
人/日
检验员/日期:
QA过程检查表

Does the machine have maintenance and inspection?
机器周围是否有安全隐患?
Are there security risks around the machine?
机器参数设定是否正确?
Is the machine parameters set correctly?
OD测试仪是否有校验合格标签?
2
机器/仪器 Machinery /Apparatus
Dose the OD tester have the conformity calibration label? OD测试仪参数设定是否正确? The OD tester parameter settings are correct ? 火花机是否有校验合格标签?
订单号
PO
稽查頻率 Inspection frequency
1次/1天 once/ day 1次/1天 once/day 1次/1天 once/day 1次/1天 once/ day 1次/1天 once/day 1次/1天 once/day 1次/1天 once/ day 1次/1天 once/day 1次/1天 once/ day 1次/1天 once/ day 1次/1天 once/ day 1次/1天 once/ day 1次/1天 once/day 1次/1天 once/ day 1次/1天 once/ day 1次/1天 once/ day 1次/1天 once/ day
1次/1天
Dose the operators implement self-inspection to confirm the spec 、color、appearance and once/ day
海康专用---QA-MAG-004.02A成品出货检验报告

外 线材
观 检
移印
验 压接
1.线身是否无脏污、烧焦、破皮露铜、含杂质、穿孔等; 2.线材安规印字是否正确、无模糊等; 1.内容是否正确;使用颜色是否正确;移印是否无漏印或移位、叠印不良等; 1.排线是否无超长后缩,IDC是否无未压到位; 2.COVER是否无破裂不到位,SR是否无未夹到位、不定位等;
包 装 唛头
不良率
其他
检验 结果
检验 结果
一 式 两
检验结 联
: 第 一 联 ( 白 联 ) 品 保 留 底
第 二 联 ( 红 联 ) 客 人
1. 摆板 栈2.
叠
判定结果
合格
不合格
异常单追溯编号:
附
可靠 性测
核 定 :
记
检 验 员 :
录
表
单
编
号
保存
:
保
期
QA
存
限:
-
部
三年
MA
门
(汽
G-
:
车产
00
日期 :
客户
客户料号
抽 检
采 用:
正常
方
减量
式
免检
检验
电 D项C/目HI-
气
POT COND
性
能
I.R AC/HI-
POT
规格要求
尺
寸
量
测
成品出货检验报告
出货单号 创
亿
品名
NO :
出 货
加严 全检
ATA
样品数 不良级别
主要缺点
次要缺点
F/C
W/H
R/C
接受 POWER
拒收 SATA
医疗器械管理-QA、QC、IQC、IPQC区别

QA、QC、IQC、IPQC区别QA、QC、IQC、IPQC1、QA(QualityAssurance)品质保证:通过建立和维持质量管理体系来确保产品质量。
QA是为满足顾客要求提供信任,即使顾客确信你提供的产品能满足他的要求,因此需从市场调查开始及以后的评审客户要求、产品开发、接单及物料采购、进料检验、生产过程控制及出货、售后服务等各阶段留下证据,证实工厂每一步活动都是按客户要求进行的。
QA的目的不是为了保证产品质量,保证产品质量是QC 的任务。
QA主要是提供确信,因此需对了解客户要求开始至售后服务的全过程进行管理,这就要求企业建立品管体系,制订相应的文件规范各过程的活动并留下活动实施的证据,以便提供信任。
这种信任可分为内外两种:外部的即使客户放心,相信工厂是按其要求生产和交付产品的;内部是让工厂老板放心,因为老板是产品质量的第一责任人,产品出现质量事故他要负全部责任,这也是各国制定产品质量法律的主要要求,以促使企业真正重视质量,因此老板为了避免承担质量责任,就必须以文件规范各项活动并留下证据。
但工厂内部人员是不是按文件要求操作,老板不可能一一了解,这就需要QA代替他进行稽核,以了解文件要求是否被遵守,以便让老板相信工厂各项活动是按文件规定进行的,使他放心。
QA职责:1.负责本部门全面工作,组织实施GMP有关质量管理的规定,适时向企业领导提出产品质量的意见和改进建议。
2.保证本企业产品是在符合GMP要求下生产的。
3.对全企业有关质量的人和事负监督实施、改正及阻止的责任。
4.对有利于生产配置的指令在本部门的指定人员审核签署后进行复核批准。
5.对检验结果进行复审批准。
6.对新产品研制、工艺改进的中试计划及结论进行审核。
7.审核上报药品监督管理部门的有关技术、质量书面材料。
8.审定批记录,作出成品是否出厂的结论。
9.负责组织制定原辅料、包装材料的质量标准和其他文件。
10.审核不合格品处理程序。
11.因质量管理上的需要,会同有关部门组织编写新的技术标准或讨论修正技术标准。
QA出货检验报告出货检验报告

引言概述:正文内容:一、出货检验的目的和意义1. 确保产品符合质量要求:出货检验的首要目的是确保产品在交付给客户之前符合预定质量要求。
这样可以避免将低质量或有缺陷的产品发送给客户,从而提高客户满意度和品牌声誉。
2. 确保产品安全可靠:出货检验还可以通过检测产品的安全性和可靠性,保证产品在使用过程中不会造成任何损害或危险。
3. 检测供应商的表现:通过出货检验可以对供应商的生产能力和质量管理进行评估,为与供应商的合作关系提供依据。
二、出货检验步骤1. 准备工作:在进行出货检验之前,需要明确检验范围和标准,并准备相应的检验设备和工具。
2. 抽样检验:从批次中抽取样本进行检测。
抽样方法应根据产品特点和出货量进行选择,以保证样本的代表性。
3. 检验项目:根据产品的特性和规定的标准,对样本进行外观检验、尺寸检验、功能性能检验等。
4. 记录检验结果:对于每个样本的检验结果,都应进行准确记录,包括合格、不合格或无效等。
三、出货检验所涉及的质量标准1. 外观标准:外观标准是对产品外观质量的要求,包括表面光洁度、颜色、涂层质量等。
根据不同的产品类型和行业标准,可以制定相应的外观标准。
2. 尺寸标准:尺寸标准是对产品尺寸和形状的要求,可以通过测量工具和设备进行精确检验。
3. 功能性能标准:功能性能标准是对产品性能的要求,包括产品的电气性能、机械性能、耐用性等。
可以通过实验室测试、模拟环境测试等方法进行检验。
四、出货检验中的技术要求1. 检验设备和工具:确保检验设备和工具的准确性和可靠性,例如量具、测量仪器、电气测试设备等。
2. 检验人员的技能和资质:检验人员需要具备一定的技术和专业知识,熟悉产品特性和相关标准,能够准确判断检验结果。
3. 检验环境的要求:为了确保检验的准确性和可靠性,需要提供适当的检验环境,包括温度、湿度、光照等条件的控制。
五、出货检验的优势1. 提高产品质量:通过出货检验可以及时发现并解决产品质量问题,提高产品的整体质量水平。
QA检查管理规范(含表格)

QA检查管理规范(IATF16949-2016/ISO9001-2015)1.0目的:为规范QA作业流程,保证出货产品的质量满足客户的需求,特制定本检查指引。
2.0适用范围:适用品保课QA检验。
3.0名词定义:QA:指Quality Assurance 品质保证。
是品保课职能部门之一,其依据内部流程和标准,对产线完成品进行抽样检验。
AQL:Acceptable Quality Level。
指允收品质水准,也可称质量允收水平。
OBA:Out of BOX Assurance,指开箱检验:就是在产线的包装工位前或后一工位,按抽样计划要求,随机抽取样本进行检验。
其特点是:通过在线抽检,能以最快速度检验在线生产完成品,发现异常及时处理,并节约品管人员抽检时打开包装及装箱的时间。
4.0职责:品保课负责落实本指引规定相关事宜,各相关部门配合执行。
5.0作业内容:5.1 抽样计划不同客户的产品抽样计划会有差别,具体选择参照《抽样计划》。
5.2 生产线组批原则为:5.2.1 生产尽量按相同人员、机器、设备、物料、方法、环境、时间生产品集合组成检验批;5.2.2 QA在线进行抽检时所抽检的产品数量依据不同产品进行定义,定义的依据是:a.考虑检验单片产品外观、功能及其它检验项目所需的时间。
所属时间长的,抽检数量适量缩小,反之,抽检数量加大;b.考虑制程品质状况和客户品质要求。
制程品质不理想的,抽检数量适当增加,反之缩小;客户品质要求严格的,抽检数量适当加大,反之减少;c.如客户有明确要求的,须按客人要求进行抽样,但必须在《抽样计划》上加以注明.5.3检验标准及要求5.3.1PCBA检查标准按照《外观检验标准》,未尽事宜,参考IPC-A-610D要求。
5.3.2各检验场的光照度标准:工作台面在自然光或日光灯下,光照度标准应在500LM以上,由QA人员使用照度计每天一次检测当工段所有检验工位的光照度,并记录在【光照度测量记录表】中。
包装成品QA检验报告
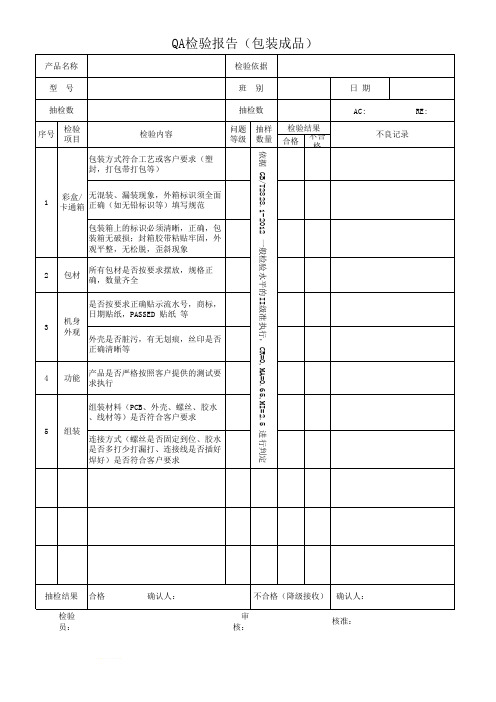
日 期AC:RE:合格不合格包装方式符合工艺或客户要求(塑封,打包带打包等)
无混装、漏装现象,外箱标识须全面正确(如无铅标识等)填写规范
包装箱上的标识必须清晰,正确,包装箱无破损;封箱胶带粘贴牢固,外观平整,无松脱,歪斜现象
2包材所有包材是否按要求摆放,规格正
确,数量齐全
是否按要求正确贴示流水号,商标,日期贴纸,PASSED 贴纸 等
外壳是否脏污,有无划痕,丝印是否正确清晰等
4功能
产品是否严格按照客户提供的测试要求执行
组装材料(PCB、外壳、螺丝、胶水、线材等)是否符合客户要求
连接方式(螺丝是否固定到位、胶水
是否多打少打漏打、连接线是否插好焊好)是否符合客户要求检验员:
审核:核准:QA检验报告(包装成品)
产品名称
检验依据型 号
班 别抽检数
抽检数检验结果不良记录1组装5机身外观3依据 GB/T2828.1-2012 一般检验水平的II级准执行,CR=0,MA=0.65,MI=2.5 进行判定抽检结果合格 确认人:
不合格(降级接收) 确认人:序号检验
项目检验内容
问题等级抽样数量彩盒/卡通箱。
质量管理QA工作总结

持续改进的策略与方法
制定改进计划
根据质量数据分析结果, 制定详细的改进计划,包 括改进目标、实施步骤和 时间表。
推广改进成果
将改进成果推广到整个产 品线或部门,提高整体产 品质量和生产效率。
持续改进文化
建立持续改进的企业文化 ,鼓励员工积极参与质量 改进活动,持续提高产品 质量和客户满意度。
05
CATALOGUE
不合格品处理及改进措施
不合格品的判定与标识
总结词
准确、及时
详细描述
QA团队需确保对不合格品的准确判定,遵循规定的标识方法,避免混淆。
不合格品处理流程
总结词
规范、可追溯
详细描述
制定和遵循不合格品处理流程,包括隔离、评审、处置和追溯等环节,确保问题得到及时、有效的处 理。
改进措施与效果验证
通过案例分享、经验交流等方式,推广优秀质量管理实践,促进质量文化的建设。
04
CATALOGUE
质量检验与控制
来料检验与控制
• 确保供应商提供的产品符合质量标准:通过对供应商进行定期评估和审核,确保其产品质量达到公司要求。- 制定来料检验 计划和标准:根据产品特性和公司标准,制定来料检验计划和标准,明确检验项目、方法、频次和判定准则。- 执行来料检 验:依据检验计划和标准,对进料进行严格检验,确保原材料、零部件及外购件的质量符合要求。- 问题反馈与处理:发现 质量问题时,及时反馈给供应商并要求其整改,同时跟进整改情况,确保问题得到有效解决。
总结词
针对性、有效性
详细描述
针对不合格品产生的原因制定改进措施,并验证其有效性,防止问题再次发生。
QA车间现场检查记录通用版
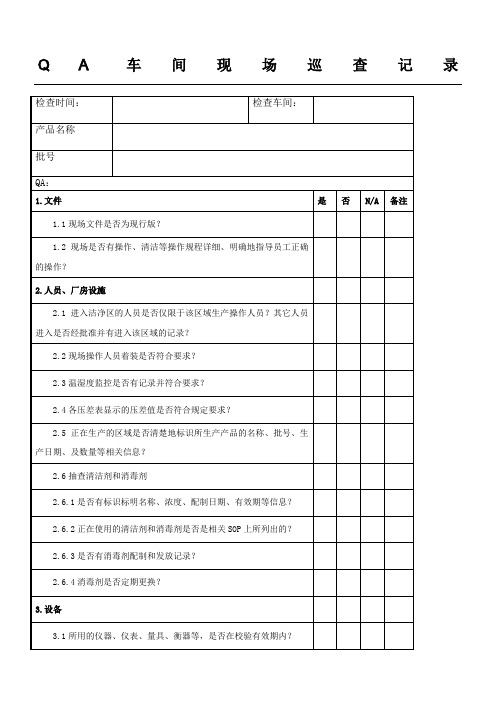
4.6称量是否在专门设计的称量区域内进行?称量是否填写记录?是否有第二个人进行复核?
4.7不同品种、规格的生产操作是否在同一操作间同时进行?
4.8各操作间的生产状态卡是否齐全,且内容是否包含产品名称、生产批号、生产日期等相关信息?
4.9不同的包装线是否有物理分隔以防止混批和交叉污染?
2.3温湿度监控是否有记录并符合要求?
2.4各压差表显示的压差值是否符合规定要求?
2.5正在生产的区域是否清楚地标识所生产产品的名称、批号、生产日期、及数量等相关信息?
2.6抽查清洁剂和消毒剂
2.6.1是否有标识标明名称、浓度、配制日期、有效期等信息?
2.6.2正在使用的清洁剂和消毒剂是否是相关SOP上所列出的?
4.13.4已打印的剩余包装材料:剩余包装材料是否执行了销毁程序?
3.6已清洁的生产设备是否在清洁、干燥的条件下存放?
4.生产操作
4.1进入洁净区的物料是否按规定传入?是否有造成环境污染的风险?
4.2不同名称、规格、工序、批号的物料是否分别存放以避免混淆的风险?
4.3各原辅料、中间产品是否有合格检验报告单,是否在有效/储存期内?
4.4现场检查操作间内盛装物料的容器是否密封?是否有状态标识,内容包含名称、批号(制作号)、数量等相关信息?
4.10生产各相关工艺参数是否符合规定要求?
4.11检查各工序产品质量是否符合规定要求?
4.12生产结束后各生产场地和设备清场是否符合清场规定。洁净区内的地漏是否清洁?
4.13检查现场包装材料:
4.13.1包装材料的名称、规格是否与待包装产品一致?
4.13.2打印的批号、有效期是否正确?
QA成品检验报告

镜头清晰度 无半边模糊、黑点、亮点、暗点 喇叭 复位 充电 连接电脑 回放时喇叭无破音,无声等现象。 复位可以关机或者是重新启动行车记录仪 充电时行车记录仪红灯常亮,关机状态下可以自动开机并进入录像状态 可以正常的连接电脑并做为存储设备和网络摄像头功能 不合格品数量合计:
(
判定结果:
□合格
□不合格
□返工
侧边
底壳 LCD显示屏
二、功能部份
录像 录音 拍照 回放 1,静态录像(测试纸)录像正常,色彩正常。 2,动态录像(移动本机)不会又拖尾现象。蓝灯闪烁! 声音大小一致,声音清晰无破音、杂音。 不能出现黑边,失真现象 无卡死、失真,要求回放画面清淅。
各按键功能 是否正常,是否有错乱、无作用、INT等现象 G-Sensor 移动侦测 实际重力测试,保证文件能够被保护 实际移动图像来进行录像测试能正常开启录像
品质异常审核意见: 备注:“√”代表合格。“×”代表不合格
检验员:
确认:
审核:
QA成品检验报告
客户名称:
检验方式: 序号 □全检
订单编号:
□抽检 □免检
拉别:
机型:
总数量:
检验数量:
日期:
允许水准(AQL):①严重缺陷(CR):0; ②主要缺陷(MAJ):0.65 检验项目 项目要求 一、外观部份
③轻微缺陷(MIN):1.5 不合格品数量 MAJ MIN 第 一 联 品 质 部 ( 白 ) 第 二 联 厂 长 ( 红 ) 第 三 联 生 产 部 黄 ) 原因分析 改善措施 判定
1 2 3 4 5 6 7 8 9 10 11 12刮伤或底色有明显差异的刮痕、手指纹,彩虹、变淡、显示 不全拒收。气泡或污点、杂点>0.20mm拒收;LOGO不能出现断字、不清楚 刮伤:有刮痕,不见底色>2.0mm拒收。 有刮痕,见底色拒收;气泡或污 点、杂点>Φ 0.30mm拒收;面壳和底壳缝隙>0.3mm拒收;USB帽与机身的缝 隙>0.4mm拒收;面壳与底壳的断差>0.3mm拒收;USB和AV插座外凸>0.4mm 拒收;丝印不可出现断字、模糊不清、毛边等现象 刮伤:有刮痕,不见底色>3.0mm拒收。有刮痕,见底色拒收;气泡或污点 、杂点>Φ 0.20mm拒收;丝印不可出现断字、模糊不清、毛边等现象 不失真、没有漏光、漏边现象、不能出现坏点
qa检验报告是什么爱问知识人

引言概述:在软件开发和质量保证过程中,QA(Quality Assurance)检验报告是一种重要的工具,用于评估和记录软件的质量和可靠性。
本文将详细介绍QA检验报告的定义、作用、组成以及编写过程,并对其在软件开发生命周期中的重要性进行阐述。
正文内容:1. QA检验报告的定义(a) QA检验报告是指在软件开发和测试过程中,QA团队根据一系列预定标准和规范,对软件进行全面的评估和测试,并生成一份详细的报告。
(b) QA检验报告旨在帮助开发团队和管理层了解软件的质量状况,以便及时发现和解决问题,提供可靠的软件产品。
2. QA检验报告的作用(a) 评估软件质量:QA检验报告通过执行各种测试和评估方法,评估软件的功能、性能、安全性等方面的质量表现。
(b) 发现问题和缺陷:QA检验报告能够发现软件中存在的问题、错误和缺陷,帮助开发团队及时修复和改进。
(c) 提供决策依据:QA检验报告提供了对软件质量的客观评估,帮助管理层做出相应决策,如是否上线、维护优先级等。
(d) 提高用户满意度:通过QA检验报告,开发团队能够改进软件质量,提高用户的满意度和使用体验。
3. QA检验报告的组成(a) 引言:介绍QA检验报告的目的、范围和方法。
(b) 测试环境和配置:详细说明测试所使用的硬件、软件环境以及配置信息。
(c) 测试方法和策略:阐述QA团队使用的测试方法和策略,包括功能测试、性能测试、安全测试等。
(d) 测试结果和分析:列出测试用例、测试结果和相关数据,对测试结果进行分析和解释。
(e) 问题和建议:列出在测试过程中发现的问题和缺陷,并对其提出改进建议。
4. QA检验报告的编写过程(a) 确定检验范围和目标:明确QA检验报告的范围和目标,确保报告的有效性和准确性。
(b) 收集和分析数据:通过执行各种测试和评估方法,收集和分析软件质量相关的数据。
(c) 编写报告:根据数据分析结果,编写QA检验报告的各个部分,包括引言、测试环境和配置、测试方法和策略、测试结果和分析、问题和建议等。
QA机器验证表

8 机 器 验 证 记 录
不进行 13 使用标准测定器定期进行检验
进行检验,但不是定期 定期进行,但没有记录
定期施行并有记录
能够传达关于QA机器的 技术情报(因为QA机设计 在发生故障时,只不过 可以解析和追究原因,防 分析过去故障,传下 14 以后是不能变更的,所以 不进行故障的解析 让它现状恢复 止故障流出 对策技术 即使人改变了,也不能传 达其设计思想) 用QA机判定合格的,在实 没有作标记 物上做标记 有标记,但不是自动打 自动打标记 上去 自动打标记保管检查 成绩
取措施
验证结果
验证人
整改措施
责任部门 责任人
完成日期
表单编号 整改措施 版本 责任部门 责任人 完成日期
表单编号 版本
整改措施
责任部门 责任人
完成日期
表单编号 版本
表单编号 版本
当产生不良品时,虽然生 产流水线会一时中止,但 有连锁装置,可以在 却不能自动排除。根据 有事发生时起作用 规则可以对不良品记录 和管理,并做上记号
用于QA机上的水,油和气 虽可再利用,但没 虽是一次性的,但没有 定期更换滤器 2 等,会不会影响零件表面 有使用过滤器 使用过滤器 清洁 是否具有连锁装置,当流 水线终止时,如果不排除 完全没有该装置 3 该不良品,则不能再起 动. 零件检验时的装夹方法 4 (位置,角度)是否与实车 与实车完全不同 相同 在必须检查出来的品质 特性上,准备了标准样 5 板,开始操作后,对首件 实施了用标准样板的确 认,同时保留记录
有标准样版,实施确认已 有标准样版,频度也 标准化,但程序不明确, 比较好,实施已确认, 也无记录 并有标准化和记录
QA机器验证表
标准样板规格的依据,通 6 过技术上的考虑,可以得 没有进行 到明确的证明 QA机器是否受环境因素 7 影 响 规格明确,但没有技术 有明确的规格,也有技术 依据明确,数据等也 上的依据 上的依据,但没有整理好 标准化
QA检查作业规定
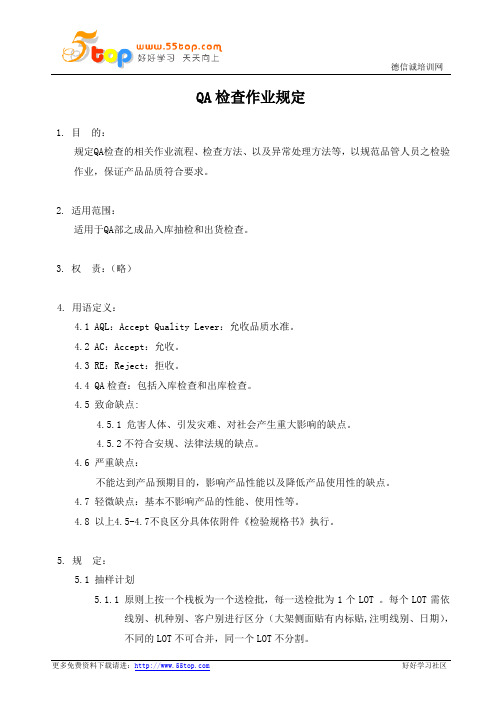
QA检查作业规定1. 目的:规定QA检查的相关作业流程、检查方法、以及异常处理方法等,以规范品管人员之检验作业,保证产品品质符合要求。
2. 适用范围:适用于QA部之成品入库抽检和出货检查。
3. 权责:(略)4. 用语定义:4.1 AQL:Accept Quality Lever:允收品质水准。
4.2 AC:Accept:允收。
4.3 RE:Reject:拒收。
4.4 QA检查:包括入库检查和出库检查。
4.5 致命缺点:4.5.1 危害人体、引发灾难、对社会产生重大影响的缺点。
4.5.2不符合安规、法律法规的缺点。
4.6 严重缺点:不能达到产品预期目的,影响产品性能以及降低产品使用性的缺点。
4.7 轻微缺点:基本不影响产品的性能、使用性等。
4.8 以上4.5-4.7不良区分具体依附件《检验规格书》执行。
5. 规定:5.1 抽样计划5.1.1 原则上按一个栈板为一个送检批,每一送检批为1个LOT 。
每个LOT需依线别、机种别、客户别进行区分(大架侧面贴有内标贴,注明线别、日期),不同的LOT不可合并,同一个LOT不分割。
5.1.2 QA抽样标准依MIL-STD-105D执行,见附件-2。
5.1.3 OQA原则上每批抽检5PCS.5.1.4 AQL:(正常检查)致命不良:AQL=0严重不良:AQL=0.4轻微不良:AQL=1.05.2 检查种类:5.2.1 初期检查:在新产品试产、首次量产、新生产线生产、品质改良后和经品管部QA主管/经理认为必要时实施,以确认产品品质,确保品质早期稳定。
5.2.1.1 初期检查抽样方式:试生产抽取数为全数但不判断。
5.2.1.2 每条生产线首次量产前面一定数量(一般为500台)全检,但不判断,随后进行正常抽检。
如全检合格率在99.6%以下,必须再追加500台全检,直到合格率达到或超过99.6%后,方可转入正常抽检。
5.2.2 正常/加严/缓和检查5.2.2.1 严格度调整依据附表-3 “严格度调整表”。